Расчет электромеханического привода




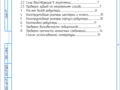


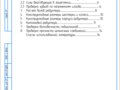
- Добавлен: 24.01.2023
- Размер: 1 MB
- Закачек: 0
Описание
Расчет электромеханического привода
Состав проекта
![]() |
![]() |
![]() |
![]() |
![]() |
![]() |
![]() |
![]() ![]() ![]() |
![]() ![]() ![]() |
![]() ![]() ![]() ![]() |
![]() ![]() ![]() ![]() |
![]() ![]() ![]() ![]() |
![]() |
![]() ![]() ![]() ![]() |
![]() |
![]() ![]() ![]() ![]() |
![]() ![]() ![]() ![]() |
Дополнительная информация
Титульник ПЗ.docx
ИРКУТСКИЙ ГОСУДАРСТВЕНЫЙ ТЕХНИЧЕСКИЙ
Руководитель Китов А.К.
Расчет электромеханического привода
ПОЯСНИТЕЛЬНАЯ ЗАПИСКА
к курсовому проекту по дисциплине
обозначение документа
шифр подпись И.О. Фамилия
подпись И.О. Фамилия
Курсовой проект защищен
РАССЧЕТНАЯ ЧАСТЬ ПРОЕКТА.docx
ИРКУТСКИЙ ГОСУДАРСТВЕНЫЙ ТЕХНИЧЕСКИЙ
Руководитель Китов А.К.
Расчет электромеханического привода
ПОЯСНИТЕЛЬНАЯ ЗАПИСКА
к курсовому проекту по дисциплине
обозначение документа
шифр подпись И.О. Фамилия
подпись И.О. Фамилия
Курсовой проект защищен
РАССЧЕТНАЯ ЧАСТЬ ПРОЕКТА
Выбор электродвигателя и кинематический расчет привода
Схема привода показана на рис. 1.1
Дано:NBB=62 кВт; nBB= 24 обмин
(мощность и обороты на ведомом валу).
1 Выбор электродвигателя по оборотам
nд= nBB *uобщ где uобщ - общее передаточное отношение привода.
Имеется в наличии червячный редуктор с uчр= 20 и цилиндрический редуктор uр = 5.
Тогда uобщ= uр* uчр = 20*5 = 100 . Соответственно
nД= nBB *uобщ = 24*100 = 2400 (обмин). Двигателя с такими оборотами нет. Есть электродвигатели с числом оборотов в минуту: 750; 1000; 1500; 3000 обмин.
Ближе двигатель на 3000 обмин.
Уточняю uобщ = nдnBB = 300024 = 125.
Провожу коррекцию передаточных отношений:
uчр = uобщ uр = 1255 = 25
Таким образом я подобрал электродвигатель по оборотам и определил передаточные отношения на каждой ступени и привода в целом.
2 Выбор электродвигателя по мощности
NД = NBBобщ где общ - общий KПД привода.
общ= 04*р*чр= 0994*097*08= 07454
NД = NBBобщ = 6207454= 832 кВт.
Принимаю электродвигатель 4A132M2 у которого мощность NД =11 кВт nдв=3000 обмин.
A132M2 – 4А - серия асинхронных двигателей; 132 высота центра вала от подошвы; М - тип исполнения; 2 - число полюсов.
Для расчета элементов привода мне потребуются параметры на всех валах привода; мощность – Вт; число оборотов – n обмин;
угловая скорость – с-1; крутящий момент – Т Н*м.
Составлю таблицу этих параметров (таблица 1.1).
Двигаясь от ведомого вала к ведущему вычисляю мощности N Вт; по формулам:
N4= NBB 0 = 6200099 =626262 Вт
N3 = N40*чр = 626262(099*08)=790735 Вт
N2 = N3 0 = 790735 (099*097)=823424 Вт
N1 = N2 0 = 823424 099=831742 Вт
Вычисляю обороты: n обмин:
n3= n4* uчр=24*25=600 обмин
n1= n2* uр=600*5=3000 обмин
Вычисляю угловые скорости с-1:
= П* n130=314*300030=314 с-1
= П* n230=314*60030=628 с-1
= П* n330=314*60030=628 с-1
= П* n430=314*2430=2512 с-1
Вычисляю крутящие моменты: Т= N
Расчет зубчатых колес редуктора
1Расчет зубчатых колес на контактную прочность
Условие контактной прочности имеет вид:
Здесь aw = a – межосевое расстояние; T2- крутящий момент на валу зубчатого колеса; b2- ширина колеса; u — передаточное отношение пары зацепления
KH = KHa*KHB*KHv- комплексный коэффициент KHa - учитывает неравномерность распределения нагрузки между зубьями; KHB - учитывает неравномерность распределения нагрузки по ширине венца; KHv - зависит от скорости и степени точности передачи. Значения коэффициентов приведены ниже. Предварительно принимаем KH = 13
Допускаемое контактное напряжение определяется по формуле: = Hlimb* KHL
где H - коэффициент безопасности; для колес из нормализованной и улучшенной стали а также при объемной закалке принимают = 11 12; при поверхностном упрочнении зубьев =12 13.
Я применили поверхностную закалку48 54HRC( 52 HRC) . Сталь углеродистая и легированная 17HRC +200
В этом случае: Hlimb =17*52+200=1084 МПа
Тогда = Hlimb * KHL = 1084*1115 = 83384 МПа
Определяем межосевое расстояние по формуле:
где Т2 - крутящий момент на валу колеса берется из таблицы 1.1 (для получения требуемой размерности крутящий момент Т2 следует подставлять в Н*мм.); - коэффициент ширины зубчатого венца для косозубых передач = 025 040. Принимаем =035. В результате получим :
После определения межосевого расстояния выбираю стандартный нормальный модуль в интервале
т = тn = (001 002)*= (001 002)*75= 075 15 мм
ряд 1:1; 15; 2; 25; 3; 4; 5; 6; 8; 10; 12; 16;20;
ряд 2:125; 1375; 175; 225; 275; 35; 45; 55; 7; 9; 11; 14; 18
Выбираю модуль mn = 1 мм.
Определяю суммарное число зубьев предварительно задавшись углом наклона зубьев в интервале = 8o 15°.Принимаем = 10°.
Определяю числа зубьев шестерни и колеса
z1= z(u+1)=14772(5+1)=246 =24
z2 = z1*u = 25*5=120
Уточняю угол наклона зубьев.
cos = = (24+120)*1(2*75) = 096
Определяю основные размеры шестерни и колеса:
Диаметры делительные:
Проверка: aw = ( =(25 + 125)2 = 75 мм
Диаметры вершин зубьев:
Ширина колеса =035*75=2625 мм =27 мм
Ширина шестерни =27+4=31 мм
Определяем коэффициент ширины шестерни по диаметру: =3125=124
Определяем окружную скорость и степень точности передачи:
V = = 314*25 (2*103)=3 925 мс здесь - угловая скорость шестерни (таблица 1.1).
(Если V 5 мс - следует принимать 8-ю степень точности; если V > 5 мс - 7-ю степень точности.)
Принимаю 8-ю степень точности
Уточняю комплексный коэффициент нагрузки KH = KHa*KHB*KHv (предварительно принял KH = 13). Симметричное расположение колес.
KHa =105 при 7-й ст.тонн и V5мс; KHa = 11 при V> 5мс;
KHa = 109 при 8-й ст. точн. и V 5 мс; KHa = 113 при V> 5 мс;
KHB = 103 105 при = 08 12 и твердости НВ 350;
KHB = 106 112 при = 08 12 и твердости >НВ 350;
KHv = 10 при V≤ 5(мс); KHv = 105 107 при V> 5мс.
В моем случае KHa = 109; =109; KHv =1.
KH = KHa*KHB*KHv =109*109*1=11881
Проверка контактных напряжений
Условие контактной прочности выполнено.
2 Силы действующие в зацеплении
Окружная = 2*2649*10325=21192 Н.
Радиальная Pr = P*tq α cos = 21192* tq 200 cos 16260 = 80346 Н
(α = 20° - стандартный угол эвольвентного зацепления).
Осевая = 21192*tq16260 = 6181(Н).
3 Проверка зубьев по напряжениям изгиба
Условие прочности имеет вид:
F = YF*Y*KFα*KF*KFv* 2T1(z12*bd*m3) ≤ []F. (2.7)
Коэффициент VF зависит от числа зубьев и имеет следующие значения:
Z 17 20 25 30 40 50 60 80 100 и более
YF 428 409 39 З8 370 366 362 361 360
Y - учитывает угол наклона зубьев. Y =1- 140
KFα - учитывает неравномерность распределения нагрузки между зубьями в курсовом проектировании принимают KFa = 075.
KF - учитывает неравномерность распределения нагрузки по длине зуба
KF = 108 113 при bd = 08 12 и твердости НВ 350;
KF = 113 130 при bd = 08 1.2 и твердости >НВ 350;
KFv - коэффициент динамичности зависит от скорости и степени точности
Способы термохимической обработки зубьев
Нормализация или улучшение
Углеродистая и легированная
Поверхностная закалка
Цементация и нитроцементация
Низкоуглеродистая и легированная
Легированная (38ХМЮА)
передачи KFv == 10 11 при V3мс; КнУ = 11 13 при V> 3мс.
Допускаемое напряжение определяется по формуле = °Flimb [n]F
[n]F - коэффициент запаса прочности. [n]F = [n]F'*[n]F
Значения [n]F' приведены в таблице 2. [n]F" - учитывает способ получения заготовки колеса: для поковок и штамповок [n]F" = 1. Для проката [n]F" =1.15 Для литых заготовок [n]F" =1.3
Принимаю [n]F" =1.15
°Flimb очень сильно зависит от термообработки зубьев. Значения
°Flimb приведены в таблице 2.1.
Поверхностная закалка 49 HRC сталь углеродистая и легированная
°Flimb= 700 Мпа [n]F’ =1.75
В нашем случае: YF = 397 (24 зубьев)
Y = 1 - 140 = 1 – 1626140 =08838
KFα = 075; KF = 133; KFv = 12
[n]F = [n]F'*[n]F"= 175*115 = 20125
[]F = °Flimb [n]F = 70020125 = 3478МПа
F = YF*Y*KFα*KF*KFv* 2T1(z12*bd*m3) =
= 397*08838*075*l33*l2*2*2649*103(242*124*13)=3115 МПа []F Условие прочности выполнено.
Расчет валов редуктора
В курсовом проектировании предлагается производить расчет валов на кручение по пониженным допускаемым напряжениям [] = 25 МПа. Вы можете воспользоваться этим предложением. В нашем пример используем более обоснованный подход. Предположим что для валов применили Сталь 45 имеющую в состоянии поставки B = 598 МПа; T= 363 МПа. Коэффициент запаса прочности возьмем n = 5.
Тогда [] = B5 = 5985 = 1196 МПа 120 МПа
[] = 05 06 [] = 05*120 = 60 МПа
Диаметры валов (ведущего и ведомого) определяются по формуле:
Диаметры выходных концов валов нельзя оставлять в таком виде. Их нужно округлить до ближайших больших стандартных размеров чтобы можно было устанавливать стандартные муфты.
Стандартные диаметры валов и соответствующие им длины валов
Конструктивные схемы валов
Ведущий вал (Рис2.1)
Ближайший больший dв1=14 мм. Между dв1и dп1 (размер под подшипник) необходима ступенька не менее 2-х мм на диаметр то есть
dп1> dв1 + 2 = 14 + 2 = 16 мм. Подшипников с таким диаметром нет. Ближайший больший подшипник имеет диаметр dп1=17 мм. Подшипник должен упираться в бурт.
dб1> dп1+ 3 = 17 + 3 = 20 мм. Оставляю этот диаметр
Ведомый вал (Рис2.2)
Ближайший больший dв2=24 мм
dп2> dв2 + 2=24+2=26 Подшипников с таким диаметром нет. Ближайший больший подшипник имеет диаметр dп2=30мм.
dк2 > dп2+ 2 = 30+2 = 32 мм Оставляю этот диаметр
dб2> dк2 + 3 = 32 + 3 = 35 мм. Принимаю диаметр dб2= 36 мм.
Конструктивные размеры шестерни и колеса
Шестерню выполняем за одно целое с валом ее размеры известны:
d1 = 25 мм; da1 = 27 мм; b1 = 31 мм.
Колесо кованое. Известны размеры:
d2 = 125 мм; da2 = 127 (мм); b2 = 27 (мм)
Эскиз колеса показан на рис. 4
Диаметр ступицы: dст=16*dк2=16*32=512 52(мм)
Длина ступицы: Lст=(12 15)dк2=(12 .15)*32=384 48. Принимаю Lст=40(мм).
Толщина обода: 0 = (25 4)*m = (25 4)*1 = 2.5 4(мм).
Толщина диска: С = 03*b2 = 03*27 = 8.1 (мм). Принимаю C = 10 мм.
Конструктивные размеры корпуса редуктора
Толщина стенок корпуса и крышки:
= 0025 aw + 1 = 0025* 75+ 1 = 2875 мм. Принимаю = 4 мм.
Толщина фланцев поясов корпуса и крышки:
b = 15* = 15*4 = 6 мм.
Толщина нижнего пояса корпуса:
р = 235* = 235*4 =94 мм. Принимаю р = 10 мм.
Диаметр фундаментных болтов:
dф = (003 0036) aw + 12 = (003 0036)* 75 + 12 = 1425 147 мм.
Принимаем болты с резьбой M14. Отверстия под фундаментные болты рекомендуется делать на 2 мм больше диаметра болта.
Диаметр крепежных болтов:
dkp=(05 07)d1=(05 07)*14=7 98
Принимаем болты с резьбой М8. Отверстия под болты рекомендуется делать на 1 мм больше диаметра болта.
Компоновка редуктора
В первую очередь необходимо подобрать подшипники качения.
Поскольку передача косозубая то есть имеются радиальная и осевая нагрузки следует применить радиально-упорные шариковые подшипники. Предварительно принимаем подшипники легкой серии.
Численные значения по пунктам компоновки редуктора для нашего случая:
) d1 = 25 мм; b1 = 31 мм.
) d2=125 мм; b2 = 27 мм.
) dст = 52 мм; Lст = 40 мм.
) d1=14мм; dп1= 17 мм; d61 = 20 мм.
) db2 = 24 мм; dп2 = 30 мм; dk2=32; d62 = 35 мм.
) f > 2dkp > 2*8 = 16 мм принимаю f = 18 мм.
Ведущий вал: DKp= D + 2а + 2b = 47+ 2*8 + 2* 10 = 83 мм.
Ведомый вал: DKp= D + 2а + 2b = 62 + 2*8 + 2* 10 = 98 мм.
) е + =3 + 4 = 7 мм;
) q>2dф >2*14 = 28 мм. Принимаем q = 30 мм.
Проверка долговечности подшипников
Из предыдущих расчетов (см. п. 2.2) имеем:
Окружная Р= 2119.2 Н.
Радиальная Pr = 803.5 Н.
Делительный диаметр шестерни d1 = 25 мм. Кроме того нам потребуется крутящий момент T1 = 2649 Н*м и число оборотов вала n1= 3000 обмин (берем из таблицы 1.1).
Расстояние от центра шестерни до центра подшипника:
Расчетная схема ведущего вала и эпюры изгибающих и крутящего моментов показаны на рис. 7.1
Реакции опор в горизонтальной плоскости равны:
Rx1 = Rx2 = Р2 = 21192 = 10595(Н).
Реакции опор в вертикальной плоскости равны:
Ry1=(Pr*l1 + Pa*d12)2l1 = (8035*36+618.1*(252))(2*36)=509 H
Ry2 = (Pr*l1-Pa*d12)211=(8035*36-618.1*(252))(2*36)=294(H)
Максимальный изгибающий момент в горизонтальной плоскости равен:
Тy= R1x* 11 = 1059.5*36=38124H*мм=38 H*м
Изгибающие моменты в вертикальной плоскости равны:
Тх1 = Ryl* l1 = -509*36=-18 H*м
Tx2=Ry2*l1=-294.2*36=-10 H*м
Суммарные реакция опор равные:
Проверяем подшипники по более нагруженной опоре 1.
Эквивалентная нагрузка определяется по формуле:
Рэ = (X*V*Frl + Y* Fa)* Кб *KT (7.1)
где Fr Fa = Рa = 618 Н; V = 1 (вращается внутреннее кольцо). Кб =
Кб = 13 15 - умеренные толчки; перегрузка до 150%;
Кт =1 при температуре подшипников до 100°
Коэффициенты X и Y зависят от соотношения Fa ( V* Fr) и е - параметр осевого погружения. Параметр е выбирается по таблице и зависит от отношения FaC0 где С0 - статическая грузоподъемность.
Для радиально-упорных подшипников (угол контакта α=12°; е = 041) при Fa(V* Fr)=0526 > е=041 Поэтому X = 045 и Y = 134.
Подставляю полученные данные в формулу (7.1):
Рэ = (X*V*Frl + Y* Fa)* Кб *KT=(045*1*1174+134*618)*115*1=15595 H
Расчетная долговечность млн. об. определяется по формуле
L = (С Рэ)3 = (1610015595)3 =11014 млн. об.
Расчетная долговечность час определяется по формуле:
U = L*106(60*n1) = 11014 *106(60*3000) = 62*103 часов.
Силы в зацеплении такие же как на ведущем валу.:
T2=1311 H*м ; n2=600 обмин;
Расчетная схема ведомого вала и эпюры изгибающих и крутящего моментов показаны на рис 7.2
Rx3 = Rx4 = Р2 = 10595 Н.
Ry3 = (Pr*l2-Pa*d22)212 =(803*38-608*(1252))(2*38)= - 985 H.
Ry4 = (Pr*l2 + Pa*d22)212 =
=(803*38+608*(1252))(2*38)=9015 H.
Ту = Кx3*l2 = 10595 *38=40200 H*мм=40.2 H*м
Тх3 = Ry3* l2 =- 985 *38=-3743 H*м
Tx4=Ry4*l2=9015 *38=34257 H*м
Суммарные реакции опор равны:
Проверяем подшипники по более нагруженной опоре 4.
Fa( V* Fr4) =468(1*13904)=044 > е = 037. Поэтому X = 0.45 и Y = 1.46.
Эквивалентная нагрузка равна:
Рэ - (X*V*Fr4 + Y* Fa)*K6*KT =(0.45 *1*13904 +1.46*618)*135 *1= 20628 H
Расчетная долговечность млн. об.:
L = (С Р)3 =(2190020628)3 = 11966 (млн. об).
Расчетная долговечность час:
Lh = L*106(60*n2) = 11966 *106(60*600) = 332398 часов=33*103 часов.
Проверка прочности шпоночных соединений
Применяем шпонки призматические со скругленными торцами. Размеры сечений шпонок и пазов даны в приложении 5. (см. таблица 8)
Материал шпонок - сталь 45 имеющая в = 598 МПа; т = 363 МПа. Коэффициент запаса прочности возьмем такой же как и для валов n = 5. Тогда [] = вn= 5985 = 1196 МПа 120 МПа.
Шпонки рассчитываются на смятие. Условие прочности имеет вид:
см = 2T[d*(h –t1)*(l - b)] []си (8.1)
Дано: T1 = 265 Н*м; db1 = 14 мм; b = 5 мм; h = 5 мм; t1 = 3 мм; длина шпонки l=lвала-2*(13) - фаска =30-2*2-2=24 мм.
см = 2T1[db1*(h –t1)*(l - b)]=
=2*265*103(14*(5-3)*(24-5))=99 МПа []см=240 МПа.
Условие прочности выполняется.
Ведомый вал (проверяем шпонку под колесом)
Дано: Т2 = 1311 Н*м; dк2 = 32 мм; b = 10 мм; h = 8 мм; t2 = 5 мм; длина шпонки 1 = Lст- 2*(1.. .3) = 40 - 2*2 = 36 мм.
см = 2T2[dk2*(h –t1)*(l - b)]=
*1311*103(32*(8-5)*(36-10)) = 105 МПа []см = 240 МПа.
Условие прочности выполняется.
Список использованной литературы
Чернаевский С.А.и др. Курсовое проектирование деталей машин: учебное пособие. – М.: Машиностроение 1988. – 416 с.
Китов А. К. Прикладная механика. Курс лекций. – Иркутск 2007. –82 с.
Стандарт предприятия СТП ИрГТУ 05-99. Оформление курсовых и дипломных проектов. – Иркутск: Из-во ИрГТУ 199. – 39 с.
Спецификация.spw

Втулка дистанционная
Болт М8 x 1-6g x 16.109.30ХГСА ГОСТ 7805-70
Болт М8 x 1-6g x 25.109.30ХГСА ГОСТ 7805-70
Болт М8 x 1-6g x 95.109.30ХГСА ГОСТ 7805-70
Гайка М8 x 1-6H.04 ГОСТ 5927-70
Манжета 1.1-17 x35-1 ГОСТ 8752-79
Манжета 1.1-30 x50-1 ГОСТ 8752-79
Шайба 8 БрКМц3-1 ГОСТ 6402-70
Гайка М10-7H ГОСТ5972-70
Шайба 10 65Г ГОСТ 6402-70
Манжеты резиновые ГОСТ 8752-79
Подшипники ГОСТ 831 -75
Штифт 6x20 ГОСТ 3129-70
Штифт 6 x 20 ГОСТ 3129-70
Масло индустриальное
Рамка содержание.cdw

Выбор электродвигателя и кинематический расчет
Выбор электродвигателя по оборотам 3
Выбор электродвигателя по мощности 4
Расчет зубчатых колес редуктора 4
Расчет зубчатых колес на контактную прочность 4
Силы действующие в зацеплении 7
Проверка зубьев по напряжениям изгиба 7
Расчет валов редуктора 8
Конструктивные размеры шестерни и колеса 10
Конструктивные размеры корпуса редуктора 10
Компоновка редуктора 11
Проверка долговечности подшипников 11
Проверка прочности шпоночных соединений 14
Список использованной литературы 15
Пояснительная записка
Рамка.cdw

Выбор электродвигателя и кинематический расчет
Выбор электродвигателя по оборотам 2
Выбор электродвигателя по мощности 2
Расчет зубчатых колес редуктора 4
Расчет зубчатых колес на контактную прочность 4
Силы действующие в зацеплении 6
Проверка зубьев по напряжениям изгиба 6
Расчет валов редуктора 8
Конструктивные размеры шестерни и колеса 10
Конструктивные размеры корпуса редуктора 10
Компоновка редуктора 11
Проверка долговечности подшипников 11
Проверка прочности шпоночных соединений 14
Список использованной литературы 16
электро-механического
Чертеж вала.cdw

Общие допуски по ГОСТ 30893.2 - К
Сталь 45 ГОСТ 1050-88
Чертеж колеса.cdw

Общие допуски по ГОСТ 30893.2 - К
Сталь 45 ГОСТ 1050 - 88
Спецификация на печать.spw

Втулка дистанционная
Болт М8 x 1-6g x 16.109.30ХГСА ГОСТ 7805-70
Болт М8 x 1-6g x 25.109.30ХГСА ГОСТ 7805-70
Болт М8 x 1-6g x 95.109.30ХГСА ГОСТ 7805-70
Гайка М8 x 1-6H.04 ГОСТ 5927-70
Шайба 8 БрКМц3-1 ГОСТ 6402-70
Манжета 1.1-17 x35-1 ГОСТ 8752-79
Манжета 1.1-30 x50-1 ГОСТ 8752-79
Подшипники ГОСТ 831 -75
Штифт 6 x 20 ГОСТ 3129-70
Масло индустриальное
Рекомендуемые чертежи
- 09.11.2023