Расчет двухступенчатого редуктора



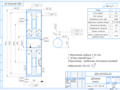
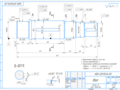
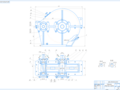
- Добавлен: 24.01.2023
- Размер: 3 MB
- Закачек: 0
Описание
Состав проекта
![]() |
![]() |
![]() ![]() ![]() |
![]() ![]() ![]() ![]() |
![]() ![]() ![]() ![]() |
![]() ![]() ![]() ![]() |
![]() ![]() |
Дополнительная информация
курсовой проект Ермолаева.doc
Кинематический расчет и силовой расчет привода .4
Расчет открытой ступени 7
Расчет зубчатых колес редуктора (закрытой ступени) 8
Предварительный расчет валов редуктора. 12
Конструктивные размеры шестерни и колеса 13
Конструктивные размеры корпуса редуктора 13
Проверка прочности шпоночных соединений 14
Первый этап компоновки редуктора 15
Проверка долговечности подшипника 16
Уточненный расчет валов 21
Список использованных источников 24
Цели и задачи курсового проекта:
Спроектировать и рассчитать привод грузовой лебедки имеющей грузоподъемность G=41 тонны и скорость подъема груза V=15 ммин. Привод двухступенчатый: первая ступень – закрытая (редуктор) цилиндрическая косозубая; вторая ступень – открытая цилиндрическая прямозубая (вариант № 4).
Рис. 1 Схема привода.
) Вторая ступень привода лебедки. 2) Электродвигатель. 3) Муфта.
) Редуктор. 5) Барабан лебедки.
Кинематический расчет и силовой расчет привода.
Выбор грузового каната расчет полиспаста и грузового барабана.
1.1 Расчет наибольшего натяжения каната.
Кратность полиспаста принимаем КПД полиспаста
для блоков с подшипниками качения.
S=4100(2*099)=20701 Н
1.2 Расчет наименьшего допустимого разрывного усилия каната.
Sp=n*S; n=55 для механизмов подъема груза работающих в среднем режиме.
Sp=55*20701=113856 Н
1.3 Выбор грузового каната.
Выбираем канат типа ЛК-Р по ГОСТ 2688-80 с прочностью проволок
Выбранный канат имеет диаметр d=15 мм и Sp=114500 Н.
1.4 Расчет минимального радиуса блока.
e=18 для механизмов подъема работающих в среднем режиме.
1.5 Расчет минимального диаметра грузового барабана.
1.6 Расчет частоты вращения грузового барабана
1.7 Расчет мощности на барабане
1 Выбор электродвигателя.
2.1 Расчет КПД привода
= 098 – кпд редуктора
= 095 – кпд открытой ступени
пп = 099 – кпд пары подшипников
2.2 Расчет требуемой мощности двигателя.
2.3 Оценка максимальной частоты вращения двигателя. Выбор электродвигателя.
Предварительно принимаем ;
2.4 По каталогу (стр. 390 [1]) выбираем электродвигатель. Исходя из полученной максимальной частоты вращения выбираю электродвигатель 4А160S6 c Pном =11 кВт; nдв =1000 обмин
примем передаточное число тихоходной ступени
передаточное число быстроходной ступени
3 Определение мощности частоты вращения и крутящего момента для каждого вала.
Расчет представлен в таблице 1.
Быстроходный вал редуктора
Тихоходный вал редуктора
Частота вращения тихоходного вала:
Угловая скорость быстроходного и тихоходного валов:
Определим мощность тихоходного вала:
Крутящие моменты на валах
Расчет открытой ступени.
Расчет ведем по изгибу.
1. Выбор материалов. Расчет допустимых напряжений.
Выбираем сталь 45 улучшенную для шестерни и колеса с твердостью по Бринеллю соответственно :
где KHL- коэффициент долговечности равен 1 для долговечных передач.
Формула для расчета изгибных напряжений примет вид:
коэффициент запаса SF = 17 для кованых и штампованных зубчатых колес.
2 Расчет модуля зацепления.
KF – коэффициент нагрузки
bm – коэффициент ширины венца
Для консольного расположения шестерни KF = 17
Принимаем Z1=30 bm=10; Т1- момент на тихоходном валу редуктора в Нм.
m=[38(2*374*17*10³)(30*10*278)] 13 =387 мм
YF =38 коэффициент формы для тридцати зубьев.
Найденное значение модуля округляем до стандартного m=4 мм
3 Расчет геометрических размеров зубчатых колес.
d1= Z1*m=30*38=11400 мм
d2= Z2*m=213*38=80900 мм
dа1= d1+2m=114+76=1216 мм
dа2= d2+2m=809+76=8166 мм
df1= d1-25m=114-95=1045 мм
df2= d2-25m=809-95=7995 мм
b2= bm*m=10*38=38 мм
4 Расчет вспомогательных параметров.
5 Расчет сил действующих в зацеплении.
6 Проверочный расчет передачи.
YF2=36 (стр. 42 [1]); Y- учитывает влияние угла наклона. Y=1 для прямозубой передачи.
KF=KFα*KF*KF- коэффициент нагрузки при расчете по напряжениям изгиба.
KFα – коэффициент учитывающий влияние погрешностей изготовления шестерни и колеса на распределение нагрузки между зубьями.
KFα=1 для прямозубых колес
KF - коэффициент учитывающий неравномерность распределения напряжений у основания зубьев по ширине зубчатого венца.
По таблице (таб. 3.7 [1]) находим:
KF=1068 (столбец 2-несимметричное расположение)
KF - коэффициент динамической нагрузки.
Значение KF принимаем по таблице 3.8: KF=125 (восьмая степень точности).
Проверяю зубья по напряжениям изгиба:
Значение напряжения изгиба для шестерни и колеса удовлетворяет условию
Расчет зубчатых колес редуктора (закрытой ступени).
Выбираем материалы со средними механическими характеристиками:
для шестерни сталь 45 термическая обработка- улучшение твердость НВ 230;
для колеса- сталь 45 термическая обработка улучшение твердость НВ-200.
Допускаемые контактные напряжения:
где Hlim b – предел контактной выносливости при базовом числе циклов.
По таблице (таб. 3.2 гл. 3 [1]) для углеродистых сталей с твердостью поверхностей зубьев менее НВ 350 и термической обработкой (улучшением)
где КHL – коэффициент долговечности при числе циклов нагружения больше базового что имеет место при длительной эксплуатации редуктора принимают КHL =1; коэффициент безопасности [SH] =110.
Для косозубых колес расчетное допускаемое контактное напряжение по формуле:
Расчетное допускаемое контактное напряжение равно:
Требуемое условие выполнено.
Коэффициент КH по таб. 3.1 [1] принимаем для симметричного расположения колес относительно опор.
Принимаем для косозубых колес коэффициент ширины венца по межосевому расстоянию
Межосевое расстояние из условия контактной выносливости активных поверхностей зубьев определяем по формуле:
где для косозубых колес Ка=43
Ближайшее значение межосевого расстояния по ГОСТ 2185-66 αw =250 мм
Нормальный модуль зацепления принимаем по следующей рекомендации:
примем по ГОСТ 9563-60 mn=3 мм
Примем предварительно угол наклона зубьев =10 и определим числа зубьев шестерни и колеса по формуле:
принимаем z1=20 тогда z2= z1*u=20*7.1=142
Уточненное значение угла наклона зубьев
Основные размеры шестерни и колеса:
делительные диаметры
диаметр вершин зубьев:
Определяем коэффициент ширины шестерни по диаметру:
Окружная скорость колес и степень точности передачи
При такой скорости для косозубых колес следует принять 8-ую степень точности.
Коэффициент нагрузки
Значения КН берем из таб. 3.5 [1] при твердости НВ≤350 и несимметричном расположении колес относительно опор КН=1.24
По таб. 3.4 [1] при и 8-й степени точности КНα=1.08
По таб. 3.6 [1] для косозубых колес при имеем КН=1.0
Проверка контактных напряжений.
Силы действующие в зацеплении:
Проверяем зубья на выносливость по напряжениям изгиба по формуле:
Где коэффициент нагрузки
По таб. 3.7[1] при твердости НВ350 и несимметричном расположении зубчатых колес относительно опор
По таб. 3.8[1] ; таким образом коэффициент
YF- коэффициент учитывающий форму зуба и зависящий от эквивалентного числа зубьев Z (формула 3.25 [1]):
Допускаемое напряжение находим по формуле:
По таб. 3.9[1] для стали 45 улучшенной при твердости.
- коэффициент безопасности где (таб. 3.9[1])
( для поковок и штамповок);
Допускаемые напряжения:
Дальнейший расчет ведем для зубьев колеса для которого найденное отношение меньше.
Определяем коэффициенты Y и КFα (гл. 3[1]).
для средних значений коэффициента торцового перекрытия α=1.5 и 8-й степени точности .
Проверяем прочность зуба колеса по формуле
Условие прочности выполнено.
Предварительный расчет валов редуктора.
Определим диаметры валов из расчета на кручение по пониженному допускаемому напряжению.
Диаметр выходного конца ведущего вала
У подобранного электродвигателя (таб. П 2[1]) диаметр вала может быть 42 или 48 мм.
Выбираем МУПВ по ГОСТ 21424-75 с расточками полумуфт под и
Диаметр под подшипники ведущего вала . Шестерню выполним за одно целое с валом.
Диаметр выходного конца ведомого вала.
Принимаем ближайшее значение из стандартного ряда:
Диаметр вала под подшипниками примем
Диаметр под зубчатым колесом
Конструктивные размеры шестерни и колеса.
Шестерню выполним за одно целое с валом ее размеры определены выше.
Диаметр ступицы таб. 10.1[1])
Конструктивные размеры корпуса редуктора.
Толщина стенок корпуса и крышки:
Толщина фланцев поясов корпуса и крышки:
нижнего пояса корпуса принимаем
Диаметр болтов: фундаментных ; принимаем болты с резьбой М 20;
крепящих крышку к корпусу у подшипников ; принимаем болты с резьбой М 14 –для ведомого вала болты с резьбой М 12 –для ведущего.
соединяющих крышку с корпусом ;
принимаем болты с резьбой М 12.
Проверка прочности шпоночных соединений.
Для соединений деталей с валами принимаются призматические шпонки со скругленными торцами по ГОСТ 23360-78. Материал шпонок – сталь 45 нормализованная.
Напряжения смятия и условие прочности находим по формуле (ф.8.22[1])
Допускаемые напряжения смятия при стальной ступице при чугунной
Ведущий вал: d=32 мм; b×h=10×8 мм - глубина паза вала; длина шпонки вала (при длине ступицы полумуфты МУВП 60 мм таб. 11.5[1]); момент на ведущем валу :
материал полумуфт МУПВ – чугун марки СЧ 20).
Ведомый вал: d=45 мм; b×h=14×9 мм ;
длина шпонки вала под колесом момент на ведущем валу :
Прочность шпоночных соединений достаточна.
Первый этап компоновки редуктора.
Толщина стенок корпуса и крышки редуктора
= 0025αw+1 = 0025· 250 + 1 = 725 мм. Принимаем = 8 мм
Толщина фланца корпуса и крышки b = 15 = 15·8 = 12 мм
Толщина нижнего пояса корпуса
p = 235 = 235 · 8 = 188 мм. Принимаем р = 20 мм
Диаметр фундаментных болтов
d1=(003÷0036)αw+ 12 = (003÷0036) ·250+12 =195 ÷ 21 мм
Диаметры болтов крепления крышки с корпусом
d2=(005÷06)d1 = (05÷06) ·20=10 ÷ 12 мм
Принимаем d=12 мм для болтов под бобышками d=10 – для остальных.
Очерчиваем внутреннюю стенку корпуса:
принимаем зазор между торцом шестерни и внутренней стенкой корпуса при наличии ступицы зазор берется от торца ступицы;
принимаем зазор от окружности вершин зубьев колеса до внутренней стенки корпуса ;
принимаем расстояние между наружным кольцом подшипника ведущего вала и внутренней стенкой корпуса ;
Предварительно намечаем радиальные шарикоподшипники средней серии; габариты подшипников выбираем по диаметру вала в месте посадки подшипников
Условное обозначение
Для смазки подшипников принимаем пластичный смазочный материал. Сорт смазки – УТ1. Для предотвращения вытекания смазки внутрь корпуса устанавливаем мазеудерживающие кольца. Их ширина составляет
Измерением находим расстояние на ведущем валу
Глубина гнезда подшипника ; примем
Толщина фланца крышки подшипника примерно равна диаметру отверстий под болты 14 мм.
Проверка долговечности подшипника.
Из расчетов имеем: ;;из первого этапа компоновки
Реакции опор: в плоскости xz
Из эпюры видно что самое опасное сечение – сечение под колесом ослабленное шпоночным пазом. Моменты в этом сечении будут равны:
Намечаем радиальные шариковые подшипники 308:
Эквивалентная нагрузка по формуле:
в которой радиальная нагрузка осевая нагрузка ; (вращается внутреннее кольцо); коэффициент безопасности для редукторов всех конструкций (таб. 9.19 [1]); (таб. 9.20 [1]).
Отношение ; этой величине (по таб. 9.18 [1]) соответствует
Расчетная долговечность млн. об
Расчетная долговечность ч
что больше установленных ГОСТ 16162-85.
несет такие же нагрузки как и ведущий вал ;;
Также действуют нагрузки от ведущей шестерни открытой передачи:
Из первого этапа компоновки по замерам примем
Реакции опор: в плоскости xz
Проверка: ; следовательно вертикальные реакции найдены верно.
Проверка: следовательно вертикальные реакции найдены верно.
Из эпюры видно что самое опасное сечение – сечение под подшипником между колесами.
Выбираем подшипники по более нагруженной опоре 4.
Шариковые радиальные подшипники 312 серии (таб. П3 [1]):
d=60 мм D=130 мм B=31 мм C=81.9 мм
Отношение этой величине (по таб. 9.18 [1]) соответствует
Отношение ; следовательно X=1 Y=0.
Отсюда где Кб=12 (учитывая что зубчатое колесо открытой передачи усиливает неравномерность нагружения).
Расчетная долговечность ч где
- частота вращения ведомого вала. Для зубчатых редукторов ресурс работы подшипников может превышать 36000 ч (ресурс самого редуктора) но не должен быть менее 10000 ч (минимально допустимая долговечность подшипника). В нашем случае подшипники ведущего вала 308 имеют ресурс а подшипники ведомого вала 312 имеют ресурс .
Уточненный расчет валов.
Примем что нормальные напряжения от изгиба изменяются по симметричному циклу а касательные от кручения – по отнулевому (пульсирующему).
Уточненный расчет состоит в определении коэффициентов запаса прочности S для опасных сечений и сравнении их с требуемыми (допускаемыми) значениями [S]. Прочность соблюдена при где
Произведем расчет для предположительно опасных сечений каждого из валов.
Материал вала тот же что и для шестерни (шестерня выполнена заодно с валом) т.е. сталь 45 термическая обработка –улучшение.
По таб. 3.3[1] при диаметре заготовки до 90 мм (в нашем случае ) среднее значение .
Предел выносливости при симметричном цикле изгиба
Предел выносливости при симметричном цикле касательных напряжений
Сечение А-А. Это сечение при передаче вращающего момента от электродвигателя через муфту рассчитываем на кручение. Концентрацию напряжений вызывает наличие шпоночной канавки.
Коэффициент запаса прочности
где амплитуда и среднее напряжение отнулевого цикла
При d=32 мм; b=10 мм; t1=5 мм по таб. 8.5 [1]
Изгибающий момент в горизонтальной плоскости
Примем (таб. 8.5 [1]) (таб. 8.8 [1]) (стр. 166 [1]).
Коэффициент запаса прочности по нормальным напряжениям
Результирующий коэффициент запаса прочности
Полученные значения удовлетворяют условию прочности.
Материал вала – сталь 45 нормализованная;
Пределы выносливости
Сечение Б-Б. Диаметр вала в этом сечении 60 мм. Концентрация напряжений обусловлена наличием шпоночной канавки: ;
масштабные факторы (по таб. 8.8 [1]) коэффициенты и .
Изгибающий момент в горизонтальной плоскости
Изгибающий момент в вертикальной плоскости
Суммарный изгибающий момент в сечении Б-Б
Момент сопротивления кручению (d=60 b=18 мм t1=7 мм)
Момент сопротивления кручению
Амплитуда и среднее напряжение цикла касательных напряжений
Амплитуда нормальных напряжений изгиба.
Коэффициент запаса прочности по нормальным напряжениям
Коэффициент запаса прочности по касательным напряжениям
Результирующий коэффициент запаса прочности для сечения Б-Б
Другие сечения не проверяем как менее нагруженные.
Список использованных источников.
С.А. Чернавский и др. «Курсовое проектирование деталей машин» М.: «Машиностроение» 1987 г.
П.Г. Гузенков «Детали машин» М.: Высш. шк. 1986 г.
В.И. Анурьев Справочник конструктора – машиностроителя т.1-3
М.: «Машиностроение» 1980 г.
М.И. Кидрук «Компас -3D» Учебное пособие.
зубчатое колесо Ермолаев.cdw

Нормальный исходный контур
Коэффициент смещения
Допуск на радиальное биение
Неуказанные радиусы 5 мм мах.
Уклоны формовочные 1
Неуказанные предельные отклонения размеров
Сталь 45 ГОСТ 1055-80
вал Ермолаев.cdw

Уклоны формовочные 1
Неуказанные предельные отклонения размеров:
редуктор Ермолаева А.П.cdw

Рекомендуемые чертежи
Свободное скачивание на сегодня
- 23.02.2023