Производство цветного портландцемента



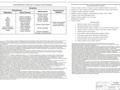
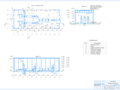
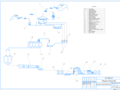
- Добавлен: 24.01.2023
- Размер: 578 KB
- Закачек: 0
Описание
Состав проекта
![]() |
![]() |
![]() ![]() ![]() ![]() |
![]() ![]() ![]() |
![]() ![]() ![]() ![]() |
![]() ![]() ![]() ![]() |
Дополнительная информация
Лист 3.dwg

Сцеп из 2Г 125х14; l100
Железобетонная стеновая панель
Насадка I №20; l1230 100 l 60 150 l 220
Ж-б сегментная ферма с раскосами для малоукровной кровли
Фартук из оцинкованой кровельной стали
Три дополнительных слоя руберойда-верхний слой бронированый
Архитектура промышленных зданий
Промышленное одноэтажное здание
Упор подкрановой балки -200х8; L400 612пл; L250 220; L100 Гайка М12
Опора подкрановой балки -400×8; L550 4·20пл; L450 4·12пл; L250 2 гайки М16 Сетка из ·6 с ячеей 50х50
Закладной элемент для крепления вертикальных продольных связей
Стройка торцевого фахверка из 2-160х8;-184х6
Доборный угловвой блок площ. сечения 300х550
-150х8; l250 через 1200
Ж.-б. ребристая плит
Обмазочная пароизоляция
Плиты из крупнозернистого керамобетона 100-120
Выравнивающий слой из цементно-песчаного состава (15 мм)
Основной четырехслойный рубероидный ковер
Гравий втопленный в битум (g=15 мм)
Цементно-песчаный раствор
Утеплитель - пенополистирол
Керамзитобетонная стеновая панель
Генеральный план предприятия М 1:500
Производство цветного портландцемента
Минеральные пигменты - их характеристики и применение в технологии цемента
Классификация пигментов по природе происхождения
авгит. 2. Оксиды: гётит
окислы марганца (псиломелан
магнетит. 3. Сульфиды: киноварь
реальгар. 4. Карбонаты: церуссит (природные свинцовые белила)
сидерит. 5. Сульфаты: ярозит
барит (баритовые белила). 6. Фосфаты: вивианит
дельвоксит. 7. Вольфраматы: вульфенит. 8. Хроматы: крокоит.
Пригодные для использования в качестве пигментов минералы относятся к различным кристаллохимическим классам:
охры красные. 2. Оранжевый: реальгар
ванадинит. 3. Жёлтый: аурипигмент
светлый лимонит. 4. Зелёный: глауконит
керченит. 5. Голубой: азурит (в тонком помоле). 6. Синий: лазурит
азурит (в крупном помоле)
рибекит. 7. Фиолетовый: лазурит (после специального прокаливания). 8. Красно-коричневый: гематит
темный лимонит. 9. Коричнево-чёрный: окислы марганца (псиломелан
вад). 10. Чёрный: каменный уголь
Пигменты - это сухие красящие порошки
являющиеся также наполнителями системы; нерастворимые в воде
масле и других растворителях. В зависимости от происхождения пигменты классифицируются на минеральные и органические. А по способу получения - на природные и искусственные. Для получения природных минеральных пигментов производят механическую обработку природных материалов: помол
просев или отмачивание. b0.25
Цветные пигменты ( красители)
должны быть устойчивы по отношению к агрессивной среде
создаваемой сильнощелочным вяжущим цементом. Кроме того
они должны быть свето и атмосферостойкими. Пигменты не должны растворяться в воде для затворения. В процессе изготовления окрашенного бетона они должны равномерно и устойчиво распределяться в нём. Неорганические пигменты
а в особенности оксидные
невероятно хорошо отвечают этим требованиям. Этим требованиям отвечают пигменты производимые таких фирмой как: Lanxess
Bayferrox и IOX. Именно эти пигменты обладают вечным качеством. b0.41667
Искусственные минеральные пигменты получают путем термической обработки минерального сырья (например
умбра). Помимо традиционных сухих порошковых пигментов получают пигменты в виде паст-концентратов
эмульсий и микрокапсул. Запрещено применение токсичных пигментов
содержащих в своем составе
свинец. Свойства пигментов: b0.25
Пигменты ( красители ) обладают определенным цветом
т.к. они способны избирательно отражать лучи дневного цвета. Когда на пигмент падает световой луч
то часть лучистой энергии поглощается
окрашивая пигмент в цвет отраженных лучей. Пигмент
отражающий почти весь падающий на него свет
поглощающий падающие на него световые лучи - черным. b0.41667
Химический состав пигмента обуславливает его главные свойства: термостойкость
коррозионную и химическую устойчивость
цвет. Содержание водорастворимых солей в пигментах должно быть минимальным
т.к. под действием воды они вымываются. b0.25
Дисперсность пигмента влияет на все его основные свойства. Чем меньше размер частицы
тем выше укрывистость и красящая способность пигмента. Полидисперсный состав пигмента позволяет получить плотное покрытие при минимальном расходе связующего. Укрывистостью называют способность пигмента при равномерном нанесении на одноцветную поверхность делать невидимым цвет последней. Наилучшая укрывистость достигается при использовании частиц пигмента (0
- 10) мкм. Укрывистость выражается в граммах пигмента
необходимой для того
чтобы сделать невидимым цвет закрашиваемой поверхности площадью 1 квадратный метр. Укрывистость пигментов считают хорошей
если она составляет (20-60) гкв.м. Например
у железного сурика она составляет 35 гкв.м.
а у охры - 180 гкв.м. Красящая способность - способность пигмента передавать при смешивании окраску смеси с белым пигментом. Интенсивность окрашивания - Интенсивность окраски является важным показателем качества пигмента. Показатели окрашивающей способности являются решающими для оценки экономичности данного пигмента. Под интенсивностью окрашивания понимается способность пигмента окрасить в свой цвет окружающую его среду. b0.41667
Стандарт DIN 53 237 является основным для исследования пигментов марки Bayferrox
и в первую очередь для оценки их окрашивающей способности. При этом сухая смесь исследуемого пигмента и тяжёлого шпата сравнивается со смесью соответствующего пигмента Bayferrox - стандарт и тяжёлого шпата. Относительная окрашивающая способность рассчитывается следующим образом: Относительная окрашивающая способность равна отношению: весовой части пигмента - эталона к весовым частям исследуемого пигмента умноженного на 100 процентов. Маслоемкость - это способность частиц пигмента удерживать на своей поверхности определенное количество масла. Выражается она в граммах на 100 г пигмента и колеблется обычно (40-100)г. Поскольку стоимость связующего масла (олифы) обычно выше
более экономичны пигменты с малой маслоемкостью. Кроме того
чем меньше связующего требуется для получения краски рабочей консистенции
тем более долговечным будет покрытие.
Светостойкость характеризуется способностью пигмента сохранять свой цвет при действии ультрафиолетовых лучей. Большинство природных пигментов - светостойки. Некоторые органические пигменты обесцвечиваются в процессе эксплуатации. b0.25
Щелочестойкость нужна
т.к. некоторые пигменты изменяют свой цвет при соприкосновении с щелочными растворами (цементные системы). Их не применяют для изготовления окрасочных составов
наносимых на поверхность бетона. Щелочестойкими являются почти все природные пигменты
а также многие искусственные пигменты (титановые белила
оксид хрома; органические пигменты алый> и оранжевый>). b0.41667
Пигменты для окраски бетона не должны вступать в реакцию с цементом и выцветать под действием света и погодных явлений. Они должны быть устойчивы по отношению к агрессивной среде
создаваемой сильнощелочным цементным вяжущим. Пигменты не должны растворяться в воде для затворения. Этим требованиям соответствуют неорганические оксидные пигменты. До настоящего времени не имеется данных о несовместимости цемента и оксидных пигментов. Поэтому для производства цветных бетонов могут без ограничения использоваться все типы цементов. Собственный цвет цемента оказывает влияние на цвет готового изделия: серый цвет цемента приглушает все цвета и оттенки
поэтому при окраске бетона
который производится на основе обычного портландцемента
бывает невозможно добиться такой яркости и сочности цвета
которая достигаются при использовании белого цемента. Поэтому для производства бетона светлых тонов
а также зеленого бетона рекомендуется использовать белый цемент. Степень насыщенности и чистоты цвета
которая достигается благодаря применению белого цемента
зависит и от самого пигмента. В том случае
если речь идет о черном пигменте
то окрашенный им бетон на основе серого цемента
практически не отличается от окрашенного им же бетона
в состав которого входит белый цемент. В случае использования темно-коричневого или красного пигмента это отличие является незначительным. Что касается желтого и синего пигментов
то в данном случае это отличие значительно. Чем выше степень чистоты желаемого оттенка
тем возникает большая необходимость использования белого цемента. Различные виды цемента имеют
различные оттенки серого цвета. Даже цвет цементов одного типа различается в зависимости от завода-производителя. Эти различия могут проявиться на окрашенном бетоне. Причем бетон
окрашенный в светлые тона
более чувствителен к подобным изменениям
окрашенный в более темные тона. Таким образом
образующие оптически цельную поверхность (например: фасады зданий
тротуарная плитка) должны быть изготовлены из цемента одного типа
произведенным одним и тем же цементным заводом.
Экспликация зданий и сооружений
Производственный цех 18х144
Производственный цех 24х144
Ремонтно- механический цех
Административный корпус
Условные обозначения и изображения
КП ПЗ.doc
Пояснительная записка к курсовой работе состоит из 34 страниц текста 14 таблиц 2 патентов. Использовано 5 источников информации. В ней приведены: характеристика выпускаемого вяжущего; характеристика сырьевых материалов; выбор и обоснование способа производства; режим работы предприятия; расчет производительности цеха; расчет состава сырьевой смеси; расчет потребности предприятия в сырье; выбор технологического оборудования; расчет основных механизмов; расчет расходных бункеров; расчет складов сырьевой продукции; расчет потребности в энергетических ресурсах; штатная ведомость цеха; контроль технологического процесса и качества продукции; безопасность технологического процесса; технико–экономические показатели; вывод; заключение; список используемой литературы.
Графическая часть представлена на 3 листах формата А1 на которых изображены план помольного отделения его разрез и технологическая схема производства.
Ключевые слова: ПОРТЛАНДЦЕМЕНТ КЛИНКЕР ПИГМЕНТЫ ВЯЖУЩЕЕ СМЕСЬ.
Номенклатура продукции
Минеральные пигменты их характеристики и применение в строительстве
Технологическая часть
выбор и обоснование способа производства
режим работы предприятия
расчет производительности цеха
расчет состава сырьевой смеси
расчет потребности предприятия в сырье и полуфабрикатах
выбор и расчет основного технологического и транспортного оборудования
ведомость оборудования
расчет потребности в энергетических ресурсах
Безопасность технологического процесса
Технико-экономические показатели
Список использованной литературы
Цвет и фактура сооружений во все времена имели большое значение для архитектурного оформления зданий и ансамблей. Неслучайно потому что производство белого и цветных цементов возникло почти одновременно с началом применения железобетона в строительстве.
В настоящее время производство и применение белого и цветных портландцементов в том или другом объеме налажено в ряде стран – в России США Англии Мексике КНДР Венгрии Польше Германии и других. Во многих странах он является предметом экспорта.
Опыт применения белого и цветных цементов в строительстве в виде раствора и бетона при изготовлении облицовочных плит полов ступеней скульптуры показал высокое их качество. Начиная с 1936 года эти цементы применялись на важнейших строительствах страны.
Примеры использования цветных цементов для отделки крупных панелей в заводских условиях также свидетельствуют о высоком качестве изделий и значительной экономии времени и средств по сравнению с применением например облицовочной керамики. Ограниченный ассортимент отделочных цементов и недостаточное производство все еще препятствуют широкому их внедрению на заводах железобетонных и домостроительных деталей способствуют удорожанию отделочных работ за счет применения менее эффективных и более дорогих материалов. Создавшееся положение объясняется в частности известной недооценкой значения цветных портландцементов для индустриализации отделочных работ и снижения себестоимости железобетонных изделий и является той причиной которая в свою очередь сдерживает развитие их производства и применения.
Технические требования
По цвету портландцемент подразделяют на: красный желтый зеленый голубой розовый коричневый и черный.
По механической прочности портландцемент подразделяют на марки: 300 400 и 500.
Портландцемент должен изготовляться в соответствии с требованиями настоящего стандарта по технологическим регламентам утвержденным в порядке установленном министерством-изготовителем.
Портландцемент должен содержать не менее 80% клинкера не более 6% активной минеральной добавки не более 15% минерального искусственного или природного пигмента или не более 05% органического пигмента от массы цемента.
Белый клинкер должен быть белизной не менее 68% абсолютной шкалы по ГОСТ 965-78.
Допускается для портландцемента желто-красной гаммы и коричневого цвета применять отбеленный клинкер белизной не менее 40% абсолютной шкалы а для черного - обыкновенный клинкер.
Активные минеральные добавки осадочного происхождения белизной не менее 68% абсолютной шкалы должны удовлетворять требованиям ОСТ 21-9-74.
Допускается для портландцемента желто-красной гаммы и коричневого и черного цветов применять добавки белизной не менее 40% абсолютной шкалы.
Красящие пигменты должны обладать щелоче- и светостойкостью не должны содержать примесей оказывающих вредное влияние на морозостойкость и прочность цементного камня и соответствовать нормативно-технической документации на пигменты и красители.
Гипсовый камень должен удовлетворять требованиям ГОСТ 4013-74.
По согласованию с потребителем допускается введение в портландцемент при его помоле поверхностно-активных пластифицирующих и гидрофобизирующих добавок в количестве не более 03% его массы в пересчете на сухое вещество.
Допускается вводить в портландцемент специальные добавки улучшающие его декоративные свойства в количестве не более 2% массы цемента.
Содержание окиси магния (MgO) в клинкере не должно быть более 5% содержание свободной окиси кальция (CaOсв.) не должно быть более 15% по массе.
Содержание ангидрида серной кислоты (SO(3)) в портландцементе не должно быть более 35% массы цемента.
Портландцемент должен быть однородным по цвету в пределах отгружаемой партии и сохранять свой цвет при тепловлажностной обработке и воздействии ультрафиолетовых лучей.
Цвет портландцемента должен соответствовать эталону утвержденному Минстрой материалов СССР.
Эталоном служит образец портландцемента или цементная окраска. Образцы-эталоны утверждаются для каждого завода.
Предел прочности образцов из цемента изготовляемых и испытанных по ГОСТ 310.4-81 через 28 сут с момента изготовления должен быть не менее значений указанных в таблице.
Предел прочности кгссм²
Начало схватывания цемента должно наступать не ранее 45 мин а конец - не позднее 12 ч от начала затворения.
Портландцемент должен показывать равномерность изменения объема при испытании образцов кипячением в воде.
Тонкость помола цемента должна быть такой чтобы при просеивании пробы сквозь сито с сеткой № 008 по ГОСТ 6613-86 проходило не менее 90% массы просеиваемой пробы.
Цемент высшей категории качества должен удовлетворять следующим дополнительным требованиям:
обладать стабильными показателями прочности при сжатии коэффициент вариации прочности для цемента марок 300 и 400 должен быть не более 5% а для цемента марок 500 - не более 3%.
Красящие пигменты должны удовлетворять следующим нормативно-техническим документам:
для цементов красного и розового цвета - руда железная красковая гематитовая по ТУ 14-9-71-74;
для цементов голубого цвета - голубой фталоцианиновый пигмент по ГОСТ 6220-76;
для цементов желтого цвета - желтый железоокисный пигмент по ГОСТ 18172-80;
для цементов зеленого цвета - зеленый фталоцианиновый пигмент по ТУ 6-14-488-76;
для цементов коричневого цвета - смесь руды железной красковой гематитовой по ТУ 14-9-71-74 и пероксида по ТУ 14-9-50-73.
Архитектурные достоинства и долговечность изделий из цветных портландцементов в равной степени зависят как от качества цементного клинкера – белизны активности так и от технических свойств пигментов и красковых руд введенных в состав цветного цемента.
Однако выбор надлежащего качества пигментов для производства цветных портландцементов осложняется слабым развитием их производства.
Принято различать два основных вида пигментов:
)минеральные в том числе синтетические и природные получаемые тонким измельчением красковых руд;
В отличие от красителей пигменты нерастворимы в воде масле и других растворителях и способны придавать окраску другим веществам и материалам при тесном смешении в дисперсном состоянии с другими дисперсными материалами или образовывать тонкозернистые суспензии с водой маслом и т. д. для покрытия окрашиваемой поверхности.
Среди большого числа минеральных неорганических пигментов в состав хромофора которых часто входят более редкие элементы такие как например свинец цинк кобальт хром кадмий титан и другие наиболее доступны и перспективны для производства цветных портландцементов железоокисные пигменты.
По цвету железоокисные пигменты подразделяются на желтые красные коричневые черные. Хромофором во всех случаях являются различные окислы и гидроокислы железа. Так носителем желтого цвета пигмента является в основном трехводный гидрат окиси железа – Fe2O3 3H2O. Красный железоокисный пигмент представляет собой почти чистую окись железа – Fe2O3 преимущественно в виде мельчайших кристаллов гексагональной формы. Черный железоокисный пигмент представляет собой в основном соединение FеO Fe2O3 соответствующее магнетиту (Fe3O4) и имеет кристаллы кубической системы.
Технологический процесс в целом достаточно сложен и по состоянию на данное время еще не гарантирует получения вполне стабильного по цвету продукта. Объясняется это тем что на форму и размеры кристаллов количество гидратной воды от которых в значительной мере зависит цвет пигмента в сильной степени влияют условия их осаждения температура прокаливания и другие факторы.
Красный железоокисный пигмент называемый редоксайд содержит до 95% Fe2O3. Цвет его в зависимости от небольших изменений в технологическом процессе приобретает различимые глазом оттенки.
Красный железоокисный пигмент характеризуется большой красящей способностью щелочестойкостью светостойкостью. Для получения цветных портландцементов красной гаммы от светло-красного (розового) до красного и терракотового цвета к клинкеру белого цемента при помоле добавляют редоксайд от 05 до 08%
Основными и широко распространенными природными минеральными пигментами являются: охра от светлого до темно-желтого цвета; сурик железный – вишнево-красный; мумия – розовая и красная; менее распространены: сиена – темно-желтая; умбра – коричневая а также коричневый и черный марганцовый пигменты.
Хромофором перечисленных пигментов являются водные и безводные окислы железа и марганца. Пигменты этой группы отличаются большой стойкостью к свету щелочам и атмосферным воздействиям и хорошей красящей способностью. Небольшие добавки их к цементу не оказывают вредного влияния на прочность цементного камня.
Добавка природных пигментов в количестве от 1 до 15% позволяет получать широкую гамму цветных портландцементов. Производство природных пигментов несложное и сводится в основном к рудоразборке дроблению сушке и измельчению породы – красковой руды.
Ввиду небольшого объема производства молотые природные пигменты так же как синтетические железноокисные и органические пигменты для производства цветного портландцемента в ближайшее время смогут предоставляться лишь в ограниченном количестве. Поэтому для массового производства цветных цементов необходима равноценная замена указанных пигментов. Практическое значение в этом отношении имеют красковые руды.
Выбор и обоснование способа производства
В зависимости от приготовления сырьевой смеси различают два основных способа производства портландцемента: мокрый и сухой. При мокром способе сырьевые материалы измельчают и смешивают в присутствии воды и смесь в виде жидкого шлама обжигают во вращающихся печах. При сухом способе материалы измельчают смешивают и обжигают в сухом виде. В последнее время все шире начинает применятся комбинированный способ приготовления сырьевой смеси по которому сырьевую смесь подготовляют по мокрому способу затем шлам обезвоживают и из него приготовляют гранулы которые обжигают по сухому способу.
Каждый из способов имеет положительные и отрицательные стороны. В водной среде облегчается измельчение материалов и быстро достигается однородность смеси но расход топлива на обжиг смеси в 15-2 раза больше чем при сухом способе. Развитие сухого способа длительное время ограничивалось вследствие низкого качества получаемого клинкера. Однако успехи в технике помола и гомогенизации сухих смесей обеспечили качество портландцемента.
В настоящее время получает всемирное развитие сухой способ производства цемента с печами оборудованными циклонными теплообменниками и реакторами – декарбонизаторами. Производительность такой линии составляет 3000 тонны клинкера в сутки. При этом способе производства цемента расход топлива снижается на 30-40% по сравнению с мокрым а металлоемкость в 25-3 раза.
Производство цемента по сухому способу экономичнее чем по мокрому отсутствует: процесс образования шлама можно совместить отдельные звенья технологической схемы в одном агрегате – мельница самоизмельчения «Аэрофол» усреднительные склады мельницы помола сырьевых материалов с подсушкой и др. При сухом способе поступающие на завод сырьевые материалы в виде мергеля известняка и глины подвергают дроблению в дробилках типа С–776 до зерен крупностью 25мм. Приготовленный дробленый материал ленточными транспортерами подают на склад сырья где сырьевые компоненты усредняют с помощью усреднительных машин до установленного норматива по химическому составу и подают и подают далее в бункера мельниц. Из последних сырьевые компоненты вместе с добавками через дозаторы по массе поступают в приемную устройства помольных агрегатов где их измельчают до требуемой фракции подсушивают за счет тепла отходящих газов из вращающихся печей и подвергают сепарации.
Измельченный в мельнице материал выгружают потоком газов через циклоны – разгружатели с помощью мельничного вентилятора. Далее мука поступает в коррекционные силосы где она гомогенизирует и перегружается в расходные силосы. Из силосов сырьевую смесь подают пневмоподъемниками в загрузочное устройство оснащенное дозаторами по массе и далее в циклонные теплообменники вращающейся печи. В теплообменниках сырьевая смесь нагревается встречными горячими газами вращающейся печи до t=750-800°C и частично декарбонизируется после чего поступает в печь на обжиг.
Обжиг клинкера при сухом способе производства осуществляется во вращающихся печах состоящих обычно из четырех соединенных циклов через которые направляются отходящие из печи газы; навстречу газам сверху вниз через циклоны поступает сухая измельченная сырьевая шихта; за 25-30 секунд она нагревается до 750-800°C и декарбонизирует на 30-40%.такая современная печь имеет производительность 3000 тс при удельном расходе тепла 32 - 34 МДжкг клинкера.
Также стали известны вращающиеся печи полусухого способа производства в них печь соединены с конвейерной решеткой на которой через слой гранулированной сырьевой шихты дважды просасываются горячие печные газы; в результате в загрузочный конец печи поступает подогретая и частично декарбонизированная сырьевая шихта. Расход тепла в этой печи размерами 4×60 м. – около 35 МДж при производительности 42 тчас.
При комбинированном способе сырьевые материалы подготовленные по мокрому способу и шлам имеющий влажность около 40% обезвоживаются на фильтрах до влажности 16 - 18%. Из полученного «сухаря» приготовляют гранулы и обжигают их по схеме сухого способа.
Отправным материалом для расчета технологического оборудования потоков сырья состава персонала является режим работы цеха. Он определяет количество рабочих дней в году количество смен в сутки и рабочих часов в смене.
Режим работы устанавливают в соответствии с трудовым законодательством РФ по нормам технологического проектирования предприятий вяжущих веществ.
Расчетный годовой фонд времени работы технологического оборудования в часах на основании которого рассчитывается производственная мощность предприятия в целом и отдельных линий установок определяют по формуле:
где Вр - расчетный годовой фонд времени работы технологического оборудования в часах;
Ср - расчетное количество рабочих суток в году;
Ч - количество рабочих часов в сутки;
Ки - среднегодовой коэффициент использования технологического оборудования.
Годовой фонд работы оборудования в часах составляет:
oпри круглогодичной непрерывной трехсменной работе:
oпри прерывной неделе в две смены:
oпри трехсменной работе:
3*23*52+52*8=62325 час.
Режим работы предприятия
Кол-во рабочих дней в году
Годовой фонд экспл. времени
Использования эксплутационного времени
Годовой фонд рабочего времени в часах
Расчет производительности цеха
В этом разделе исходя из принятого режима работы цеха дается расчет объема производства по сырью полуфабрикатам и готовой продукции для каждого из технологических переделов в час смену сутки.
При расчете производительности следует учитывать возможный брак и другие производственные потери размер которых принимается по соответствующим нормативам.
Для заводов по производству вяжущих веществ средние величины возможных производственных потерь обычно принимаются 1-3%.Производительность цеха по готовой продукции определяется по формулам:
где Пгод – заданная годовая производительность цеха
Ср – расчетное количество рабочих суток в году;
где Вр – расчетный годовой фонд рабочего времени в час.
Производительность каждого технологического передела рассчитывается по формуле:
ППч=ПчРУм(1+(С=Б)100)
где Пч – производительность цеха в час по готовой продукции
РУм – удельный расход сырья полуфабриката в достигаемом переделе на единицу готовой продукции определяемый на основании материального баланса
Б – потери на данном переделе в %.
Аналогично рассчитывается производительность в смену сутки год.
Расчет производительности предприятия
Расчет состава сырьевой смеси
Рациональное содержание %
Принятое содержание %
% Fe2O3=0033*C4AF=0033*12=04;
% CaO=0737*С3S+0656*C2S+0623*C3A+0461*C4AF= 0737*57+0656*25+0623*6+0461*12=67679;
Силикатный модуль n=S
Глиноземистый модуль p=Al2O3 Fe2O3=11955.
Наименование компонентов
Содержание оксида по массе
Расчет потребности сырья и полуфабрикатов
Потребность проектируемого цеха в сырье и полуфабрикатов в час смену сутки год с учетом потерь при их транспортировании определяют по формуле:
где Рм – расход сырья полуфабрикатов в час смену сутки и год в тоннах;
П – производительность цеха соответственно в час смену сутки год в тоннах;
Ру – удельный расход сырья и полуфабрикатов в тоннах на тонну готовой продукции;
п – потери при транспортировании %принимаются по нормам технологического проектирования (1-15%).
Потребность цеха в сырье и полуфабрикатах
Потребность в сырье т
Материальный баланс технологических операций
Технологическая операция
Транспорт цемента на силосный склад
Помол клинкера гипса с добавками
Красковая руда – 10%
Транспорт гипса от дробильного отделения
Транспорт гипса до дробильного отделения
Транспорт красковой руды от дробильного отделения
Дробление красковой руды
Транспорт красковой руды до дробильного отделения
Транспорт диатомита от дробильного отделения
Транспорт диатомита до дробильного отделения
Транспорт клинкера к помольному отделению
Транспортирование клинкера до дробильного отделения
Обжиг сырьевой смеси для получения клинкера
Транспорт. сырьевой смеси из помольного отделения
Совместный помол и сушка сырьевых материалов
Транспортирование материала из дробильного отделения
Транспортирование материала со склада в дробильное отделение
Расчет основного технологического и транспортного оборудования
Необходимое количество машин и другого оборудования определяют по формуле:
гдеМ – количество машин подлежащих установке;
Ппч – требуемая часовая производительность по данному технологическому переделу;
Пп – паспортная или расчетная часовая производительность машин выбранного типоразмера;
Кп – нормативный коэффициент использования оборудования во времени (принимается обычно равным 092).
Дробильное оборудование: М1=391(50*092)1;
Оборудование для тепловой обработки: М2=28289(50*092)1;
Помольное оборудование: М3=391(20*092)2;
Оборудование для транспортировки: М4=391(20*092)2;
Расчет расходных бункеров
Требуемый геометрический объем бункера определяют по формуле:
гдеVполезн – требуемая полезная емкость бункера м³;
– коэффициент заполнения принимается равным 085-09.
Известняк:Vизв=24313=187;
Vполезн=187*15=2805;
Глина:Vглина=72523=3152;
Vполезн=3152*15=4728;
Гипс:Vгипс=0809=088;
Красковая руда:Vкр.р.=33413=256;
Диатомит:Vкр.р.=12813=098;
Расчет складов сырьевой продукции
Емкость силосного склада рассчитывается по формуле:
гдеА - фактическая годовая производительность завода;
Сн - число суток нормированного запаса (принимаем 15);
ρн - насыпная плотность материала тм3;
Кз - коэффициент заполнения силоса (принимаем 09).
ИзвестнякV=1018585*15365*13*09=3620133;
ГлинаV=304212*15365*23*09=60395;
ГипсV=3232*15365*09*09=163977;
Красковая рудаV=139986*15365*13*09=4917;
ДиатомитV=53833*15365*13*09=18908.
Расчет складов готовой продукции ведется по формуле:
V=101000*15365*09*09=51243;
L=506884627*36=5215;
V=10100*15365*1*09=461187.
Расчет помольного оборудования
Производительность шаровых мельниц чаще всего применяемых для помола сырья и полуфабрикатов на заводах вяжущих веществ рассчитывают по формуле:
Q=645V√D(pv)^08kbq тчас
гдеQ – производительность мельницы по сухому материалу тчас;
V – внутренний полезный объем мельницы м³;
P – масса мелющих тел т;
k – поправочный коэффициент который принимается равным 10 при помоле по открытому циклу и 11-22 – по замкнутому циклу;
b – удельная производительность мельницы ткВт час полезной мощности;
q – поправочный коэффициент на тонкость помола.
Значения b и q принимаются по справочникам Массу мелющих тел определяют по формуле:
где V – внутренний объем мельницы м³;
– степень заполнения объема мельницы мелющими телами % (обычно принимают 25-30%);
γ0 – насыпная объемная масса мелющих тел тм³.
При мокром помоле производительность мельниц повышается примерно в 15 раза.
Ведомость оборудования цеха
Результаты проведенного подбора оборудования представляют в виде ведомости в которой перечисляют все основное и транспортное оборудование принятое к установке.
Наименование оборудования
Техническая характеристика
Сдвоенный рукавный фильтр
Число секций в фильтре 8
Фильтрующая поверхность 224 м²
Производительность по высушенному материалу 21-51 тч
Длина транспортера 5 м
Скорость ленты 15 мсек
Производительность 60 м3ч
Мощность двигателя 18 кВт
Число об. двиг. в мин. 1000
Мощность двигателя 30 кВт
Трубная шаровая мельница
Число оборотов в мин. 2083
Производительность 10-56 тч
Загрузка мелющими телами 32 т
Внутренний диаметр 400-800 мм
Высота выхлопной трубы с фланцем 174D м
Высота всего циклона 456D м
Коэффициент гидравлического сопротивления 1025 Нм²
Скорость передвижения 29 ммин
Ширина колеи 1520 мм
Установленная мощность 68 кВт
Расчет потребности в энергетических ресурсах
К энергетическим ресурсам относятся: топливо пар электроэнергия и сжатый воздух необходимые для выполнения технологических операций.
Расчет расхода электроэнергии
Наименование оборудования с электродвигателем
Количество единиц оборудования
Продолжительность работы в смену час
Коэффициент использования во времени
Коэффициент загружения по мощности
Часовой расход электроэнергии с учетом коэффициента использования и загрузки по мощности кВтчас
Коэффициент загрузки по мощности отражает использование мощности двигателя установленного при данном оборудовании в зависимости от степени его загрузки в период работы. Если оборудование загружается полностью в соответствии с технической производительностью и двигатель работает на полную мощность то он равен 1 а если полностью не используется то он будет меньше единицы. Величину этого коэффициента условно можно определить по формуле:
где Квм – коэффициент загрузки мощности двигателя;
Пф и Пт – производительность оборудования: фактическая и техническая;
α – коэффициент зависящий от степени использования производительности оборудования. Значение коэффициента α принимают:
Расход электроэнергии в смену в сутки и в год устанавливают умножением соответствующего количества рабочих часов в смену сутки год. Удельный расход электроэнергии подсчитывается по формуле
гдеЭуд - удельный расход электроэнергии на товарную единицу продукции;
Эгод – годовой расход электроэнергии в кВтчас.
Эуд=3016475100000=3016
Потребность цеха в энергетических ресурсах
Наименование энергетических ресурсов
Технический контроль качества сырья
Контролируемые параметры
Периодичность контроля
Наименование методики контроля или контрольного прибора
Место отбора пробы или установки датчика контрольного прибора
Предел прочности Нм3
Коэффициент размоло-способности
Содержание активного СаО
Предел прочности при сжатии мНм3
Технический контроль технологического процесса
Крупность фракций мм
Помол сырьевых материалов
Остаток на сите № 008
Остаточная влажность
Технический контроль качества готовой продукции
Контролируемый параметр
Цветной портландцемент
Склад готовой продукции
Тонкость помола на сите № 008
Прочность при сжатие на 28 сутки
Перед отправкой партии
Объемная масса в рыхлом состоянии
Объемная масса в уплотненном состоянии
Новые технические решения
К этому курсовому проекту на тему «Белые и цветные портландцементы» найдено два патента: 2 169 715 (13)C2 и 2 147 016 (13)C1 (смотрите приложения 1 и 2).
Формула изобретения:
Способ приготовлении шихты для получения клинкера белого цемента включающий дозирование и сухой или мокрый помол карбонатного компонента глинистого компонента и кремнеземистой добавки - кварцевого песка отличающийся тем что кварцевый песок измельчают отдельно до удельной поверхности не менее 400 м2 кг и затем перемешивают с измельченными глинистым и карбонатным компонентами.
Способ приготовления шихты по п.1 отличающийся тем что карбонатный и глинистый компоненты измельчают совместно.
Способ приготовления шихты по п.1 отличающийся тем что карбонатный и глинистый компоненты измельчают раздельно.
Способ приготовления шихты для получения клинкера белого цемента включающий дозирование и сухой или мокрый помол карбонатного глинистого компонента и кремнеземистой добавки - кварцевого песка отличающийся тем что осуществляют совместный помол карбонатного и глинистого компонентов и при помоле в ту же сырьевую мельницу вводят кварцевый песок предварительно измельченный до удельной поверхности не менее 400 м2 кг.
Способ получения белого портландцементного клинкера включающий приготовление сырьевой смеси перемешиванием карбонатного и кремнеземистого компонентов с последующим обжигом сырьевой смеси и охлаждением полученного клинкера отличающийся тем что в качестве карбонатного компонента используют отход производства аммиачных удобрений а в качестве кремнеземистого компонента - отход производства фосфорных удобрений при следующем расходе компонентов в кгт клинкера:
Отход производства аммиачных удобрений - 128955 - 133239
Отход производства фосфорных удобрений - 16095 - 30020
Способ получения белого портландцементного клинкера по п.1 отличающийся тем что при приготовлении сырьевой смеси в нее дополнительно вводят алюмосиликатный компонент в количестве 48124 - 16895 кгт клинкера.
Способ получения белого портландцементного клинкера по любому из пп.1 - 3 отличающийся тем что осуществляют резкое охлаждение в воде или на воздухе.
При большой насыщенности предприятий цементной промышленности сложными механизмами и установками по добычи и переработки сырья обжигу сырьевых смесей и измельчению клинкера перемещению складированию и отгрузки огромных масс материалов наличие большого количества электродвигателей особое внимание должно уделяться созданию благоприятных и безопасных условий для работы трудящихся. Охрану труда следует осуществлять в соответствии с «Правилами по технике безопасности и производственной санитарии на предприятиях цементной промышленности».
Поступающие на предприятия рабочие должны допускаться к работе только после обучения их безопасным приемам работы и инструктажа то технике безопасности. Ежеквартально необходимо проводить дополнительные инструктаж и ежегодно повторное обучение по технике безопасности непосредственно на рабочем месте.
На действующих предприятиях необходимо оградить движущиеся части всех машин механизмов и двигателей а также электроустановки приемки люки площадки. Должны быть заземлены электродвигатели и электрическая аппаратура.
Большое внимание следует уделять обеспыливанию воздуха и отходящих газов печей и сушильных установок для создания нормальных санитарно–гигиенических условий труда. В соответствии санитарными нормами проектирование промышленных предприятий концентрация в воздухе помещений цементной и остальных видов пыли не должно превышать 004 мгм3. содержание в воздухе СО не допускается более 0003 сероводорода – более 002 мгм3. В воздухе выбрасываемом в атмосферу концентрация пыли не должна быть более 006 гм3. При нормальной эксплуатации пылеочистных систем содержание пыли в выбрасываемом воздухе составляет 004 – 006 гм3.
Для создания нормативных условий труда все помещения цементных заводов надо обеспечить системами искусственной и естественной вентиляции. Этому в большей мере способствует герметизация тех мест где происходит пылевыделение а также отсос воздуха из бункеров течек дробильно-помольных механизмов элеваторов и т.п.
Воздух отбираемый из цементных мельниц очищают с помощью рукавных или электрофильтров. Важно не допускать просасывание через 1 м2 ткани фильтров более 60 – 70 м3 воздуха в 1 час. Для очистки воздуха отсасываемого из камер сырьевых мельниц обычно устанавливают циклон и электрофильтр.
Отходящие газы цементных печей необходимо очищать для предотвращения загрязнения окружающей среды. Для этого устанавливают электрофильтры. Если же отходящие газы содержат значительное количество пыли то их сначало пропускают через батарею циклонов.
Шум возникающий при работе на цементных заводах характеризуется зачастую высокой интенсивностью превышающей допустимую норму в 90 дБ. К числу мероприятий по снижению шума у рабочих мест относят применение демпфирующих прокладок между внутренней стенкой мельничных барабанов и т.п. При этом звуковое давление снижается на 5 – 12 дБ.
Производительность труда
Под производительностью труда понимают количество продукции приходящееся в год на одного списочного рабочего. Производительность труда является важнейшим показателем экономичности запроектированного производства.
Баланс времени одного рабочего вычисляют исходя из следующих соображений:
количество календарных дней в году – 365;
Нерабочее время в году:
a)выходные дни – 104;
b)очередной отпуск – 24 (по КЗОТу).
Если некоторым категориям рабочих представляется по действующему законодательству дополнительный отпуск то количество рабочих дней по этой статье (Dн2) должно исчисляться по формуле:
Dн2=12+(КдопКя)*Dдоп
где Кдоп – количество рабочих по штатной ведомости пользующихся дополнительным отпуском;
Кя – общее количество явочных рабочих по штатной ведомости;
Dдоп – длительность дополнительного отпуска в днях.
Общее количество нерабочих дней в году Dн.
Количество дней отрабатываемых одним рабочим в году
Списочное количество рабочих
где Кя – количество производственных рабочих.
Общее списочное количество производственных рабочих определяется по формуле:
где Кяв – явочное количество вспомогательных производственных рабочих.
Производительность труда в натуральном выражении:
Съем с 1м² производственной площади (Ср) характеризует компактность запроектированных компоновочных решений и уровень использования производственных площадей.
где Пг – годовая производительность запроектированного цеха в принятых расчетных единицах;
F – суммарная площадь всех этажей.
Наименование показателей
Количество единицы измерения
Показатели других заводов
Расход энергетических ресурсов (электроэнергии)
Списочное количество рабочих
Количество производственных рабочих
Объем готовой продукции с 1м² произв. площади в год
В данном курсовом проекте было запроектировано производство цветного портландцемента.
Были произведены такие необходимые расчеты как расход сырьевых компонентов; состав сырьевой смеси; расчет складов и необходимого оборудования. При заданной производительности предприятия 100000 тгод необходимо:
oкрасковой руды 139986
В курсовом проекте принято производство цемента по сухому способу что обусловлено необходимостью экономии топливно-энергетических ресурсов.
Графическая часть представлена тремя чертежами формата А1 на которых представлены чертежи технологической схемы производства вяжущего плана и разрезов помольного цеха со всем необходимым оборудованием.
Череповский С.С. Алешина О.К. Производство белого и цветного портландцемента. - М.: Стройиздат1964.
Бауман В.А. Строительные машины Справочник в двух томах. – М.: Машиностроение 1977.
Справочник по проектированию цементных заводов под редакцией С.И. Докишевского. – Л.: 1986.
Волженский А.В. Минеральные вяжущие вещества - М.:Стройиздат 1986.
Бутт Ю.М. Технология цемента и других вяжущих материалов - М.: Стройиздат 1964.
Лист 2.cdw

Обмазочная пароизоляция
Плиты из крупнозернистого керамобетона
Выравнивающий слой из цементного раствора
Основной 4-х слойный рубероидный ковер
Асфальтобетон (б=30мм)
Трубная шаровая мельница
Цех помола по сухому способу
План на отм. 5.000; разрез 1-1;
разрез 2-2; спецификация
План на отметке 5.000
Лист 1.cdw

тарельчатые питатели
воздушно-проходной сепаратор
гомогенизационные силосы
запасные силосы сырьевой муки
отбеливающий холодильник
красковой руды и клинкера
Красный портландцемент
Рекомендуемые чертежи
- 24.01.2023