Проектирование участка мехобработки




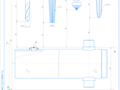
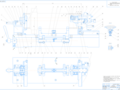
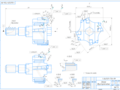
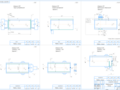
- Добавлен: 24.01.2023
- Размер: 1 MB
- Закачек: 3
Описание
Состав проекта
![]() |
![]() |
![]() ![]() ![]() |
![]() ![]() ![]() |
![]() ![]() ![]() |
![]() |
![]() ![]() ![]() ![]() |
![]() ![]() ![]() ![]() |
![]() ![]() ![]() ![]() |
![]() ![]() ![]() ![]() |
![]() ![]() ![]() ![]() |
![]() ![]() ![]() |
![]() ![]() ![]() ![]() |
![]() ![]() ![]() |
![]() ![]() ![]() ![]() |
![]() ![]() ![]() ![]() |
![]() ![]() ![]() ![]() |
![]() ![]() ![]() |
![]() ![]() ![]() ![]() |
![]() |
![]() ![]() ![]() ![]() |
![]() ![]() ![]() |
![]() ![]() ![]() |
![]() ![]() ![]() |
![]() ![]() ![]() |
![]() |
![]() ![]() ![]() |
![]() ![]() ![]() |
![]() ![]() ![]() |
![]() ![]() ![]() |
![]() ![]() ![]() |
Дополнительная информация
Бланк задания.doc
Факультет: машиностроительный
Кафедра технологии машиностроения
Заведующий кафедры Драган А.В.
по дипломному проектированию
Студенту Рожкову Валерию Анатольевичу.
Тема проекта: Проект участка механического цеха по изготовлению корпуса 503А-8603512-02 .(Утверждена приказом по ВУЗу от № )
Сроки сдачи студентом законченного проекта .
Исходные данные к проекту:
Чертеж детали корпус 503А – 8603512 – 02.
Объем выпуска 10 тыс.в год ..
Режим работы двухсменный .
Материалы преддипломной практики .
Содержание расчетно-пояснительной записки (перечень подлежащих разработке вопросов):
Разработка технологического процесса изготовления детали. 1.1 Назначение и конструкция детали. 1.2 Анализ технических условий изготовления детали. 1.3 Анализ технологичности конструкции детали. 1.4 Определение типа производства (по таблице). 1.5 Выбор метода получения заготовки 1.6 Анализ базового технологического процесса изготовления детали. 1.7 Выбор методов обработки. 1.8 Выбор технологических баз. 1.9 Разработка технологического маршрута обработки детали. 1.10 Разработка технологических операций. 1.11 Расчет припусков на механическую обработку двух поверхностей аналитическим методом. 1.12 Расчет режимов резания. 1.13 Определение норм времени технологических операций. 1.14 Определение типа производства по коэффициенту закрепления операций. 1.15 Расчет технологической размерной цепи. 1.16 Определение количества основного технологического оборудования. .
Расчет и проектирование средств технологического оснащения. 2.1 Расчёт и проектирование приспособления для сверления отверстия в бонке. 2.1.1 Описание работы станочного приспособления. 2.1.2 Силовой расчёт станочного приспособления. 2.1.3 Расчёт сверлильного приспособления на точность. 2.1.4 Расчёт приспособления на прочность. 2.2 Расчёт и проектирование приспособления для контроля радиального биения внутренних канавок. 2.2.1 Разработка и краткое описание конструкции контрольного приспособления. 2.2.2 Расчёт контрольного приспособления на точность. 2.3 Расчёт и проектирование комбинированного зенкера. 2.4 Разработка и проектирование манипулятора для подъёма детали. 2.4.1 Назначение манипулятора. 2.4.2 Устройство и принцип работы.
Технико-организационная часть.. 4. Технико-экономическое обоснование процесса. .
Приложения: комплект технологической документации (МК ОК КЭ) спецификации к сборочным чертежам. .
.Перечень графического материала (с точным указанием обязательных чертежей и графиков):
1 Чертеж детали – 1л. ф. А1; 5.2 Операционные эскизы – 2л. ф. А1; 5.3 Карта инструментальной наладки токарного станка с ЧПУ – 1л. ф. А1; 5.4 Сборочный чертеж приспособления для сверления отверстия в бонке – 05л. ф. А1; 5.5 Чертеж зенкера ступенчатого – 05л. ф. А1; 5.6 Сборочный чертеж приспособления для контроля биения внутренних канавок отонсительно сквозного внутреннего отверстия – 25л. ф. А1. 5.7 Общий вид манипулятора – 1л. ф. А1; 5.9 Планировка производственного участка – 1л. ф. А1; 5.10 Технико-экономические показатели – 1л. ф. А1. .
Консультанты по проекту:
по конструкторской технологической и организационной части – доцент Медведев О.А. .
по экономической части – ст. преподаватель Мартиновская О.В. .
по охране труда – доцент Драган А.В. .
выдачи задания 8.02.06г. .
Календарный график работы над проектом на весь период проектирования (с указанием сроков выполнения и трудоемкость отдельных этапов):
Технологическая часть пояснительной записки – 5.04.06г. (15%) .
Конструкторская часть пояснительной записки охрана труда – 20.04.06г. (20%) .
Организационная и экономическая часть пояснительной записки – 30.04.06г. (10%) Чертеж детали чертеж заготовки операционные эскизы – 15.05.06г. (15%) .
Инструментальная наладка станка сборочные чертежи технологической оснастки чертеж средства межоперационного транспортирования планировка – 7.06.06 (30%)
Оформление пояснительной записки – 15.06.06 (10%) .
Руководитель Медведев О.А. .
Задание принял к исполнению (дата) 8.02.05г. .
(подпись студента) Рожков В.А. .
Примечание: Задание прилагается к законченному проекту и вместе с проектом предоставляется при сдаче в ГЭК.
Аннотация.doc
«Проект участка механического цеха по
изготовлению корпуса 503А-8603512-02»
2. в том числе илл.16 10 листов чертежей 1 плакат
Брестский государственный технический университет 2007г.
В дипломном проекте дано описание объекта производства указаны конструктивные особенности машины в которую входит обрабатываемая деталь. Проведен анализ служебного назначения детали где выявлено назначение поверхностей детали. В проекте была разработана заготовка – отливка. Определено количество переходов механической обработки исходя из требуемой точности размеров детали и требуемых допусков формы и расположения детали. Разработан маршрутно-операционный технологический процесс. Установлена последовательность переходов дано обоснование выбора технологических баз выполнены аналитические расчеты припусков на две поверхности и режимов резания.
Разработаны средства технологического оснащения:
Спроектировано приспособление для сверления отверстия в бонке и определена допустимая погрешность этого приспособления.
Спроектирован ступенчатый зенкер.
Спроектировано контрольное приспособление для контроля биения внутренних канавок относительно сквозного внутреннего отверстия.
Решен комплекс вопросов организации и экономики производства. Разработана планировка участка и произведен расчет экономической эффективности участка. Произведены расчеты цеховых расходов и себестоимости изготовления корпуса. Произведен расчет освещения.
Ведомость.doc
Технологический процесс
механической обработки
Спецификации к сборочным
чертежам и планировке
Карта наладки инструмента
для обработки детали
на сверлильном станке с
Чертеж приспособления
для обработки отверстия
относительно сквозного
внутреннего отверстия
Приспособление контрольное(А2) лист 2.cdw

Станочное приспособление(А1).cdw

для обработки отверстия
* Размеры для справок
Оборудование: станок сверлильный с ЧПУ 2Р135Ф2
Номинальное давление в пневмосети 0
Планировка (А1).cdw

участка по изготовлению
Корпус 503А-8603512-02
Условные обозначения
Тара для заготовок и деталей
Шина электрическая на опоре
Манипулятор(А1).cdw

Наладка(А1).cdw

для обработки детали
на сверлильном станке с ЧПУ 2Р135Ф2
СП Планировка.doc
по изготовлению детали
Корпус 503А-8603512-02
Планировка производственного
участка по изготовлению
Операционные эскизы 1(А1).cdw

Вертикально-сверлильная
СП Контрольное приспособление.doc
Приспособление контрольное(А0).cdw

Радиальное биение поверхностей Л
для контроля биения
внутренних канавок относительно
сквозного внутреннего отверстия
должны покачиваться плавно боковые люфты
заедания не допускаются.
Несоосность шарикоподшипников поз. 92 не более 0
Несимметричность перемещения опоры поз. 4 относительно
оси контрольной втулки не более 1мм.
При сборке направляющие стойки поз. 18;9 и скалки поз. 39
смазать приборным маслом МВП ГОСТ 1805-51.
* Размеры для справок
Станочное приспособление(А0).cdw

для обработки отверстия
* Размеры для справок
Оборудование: станок сверлильный с ЧПУ 2Р135Ф2
Номинальное давление в пневмосети 0
Зенкер(А2).cdw

СП Станочное приспособление.doc
для обработки отверстия
Пневмоцилиндр 1011-63х80
Операционные эскизы 2(А1).cdw

-36.01.01-Т128-Т128-КЭ
Разностенность корпуса не более 2мм.
Деталь(А1).cdw

И37160.079-73. На поверхности Н брызги не допускаются
Разностенность корпуса поз.2 2мм не более
На участке Л поверхность И допускается выполнять
Ось отверстия М должна лежать в одной плоскости с осями
отверстий Д. Допустимое отклонение 5мм не более.
Поверхность Е допускается выполнять
Содержание .DOC
1Назначение и конструкция детали 7
2Анализ технических условий изготовления детали 9
3Анализ технологичности конструкции 10
4Определение типа производства .10
5Выбор метода получения заготовки 11
6Анализ базового варианта технологического процесса
изготовления детали .13
7Выбор методов обработки 17
8Выбор технологических баз .18
9Разработка технологического маршрута обработки детали .22
10Разработка технологических операций .24
11Расчет припусков на механическую обработку двух
поверхностей аналитическим методом ..26
12Расчет режимов резания .34
13Определение норм времени технологических операций 40
14Определение типа производства по коэффициенту
закрепления операций .42
15Расчет технологической размерной цепи .45
16 Определение количества основного технологического
Расчет и проектирование средств технологического оснащения 51
1Расчет и проектирование приспособления для сверления
отверстия в бонке . 51
1.1 Описание работы станочного приспособления ..51
1.1Служебное назначение и описание конструкции
фрезерного приспособления ..62
№ докум. оцонооокуруеркоомрсггааангагндаподокумента
Датаааааааааааааааааааа
Техпроцесс изготовления корпуса 503А-8603512-02
1.2 Силовой расчёт станочного приспособления .52
1.3 Расчет сверлильного приспособления на точность 54
1.4 Расчет приспособления на прочность .55
2 Расчёт и проектирование приспособления для контроля
радиального биения внутренних канавок 55
2.1 Разработка и краткое описание конструкции контрольного приспособления .56
3.2 Расчёт контрольного приспособления на точность ..56
3 Расчёт и проектирование ступенчатого зенкера 57
4 Разработка и проектирование манипулятора для подъёма
4.1 Назначение манипулятора 60
4.2 Устройство и принцип работы 61
Технико-организационная часть 63
Расчет технико-экономических показателей обработки детали ..68
1 Определение потребности в материально-технических и
трудовых ресурсах 69
2 Расчет технико-экономических показателей .72
3 Расчет себестоимости продукции 76
4 Оценка экономической эффективности варианта
технологического процесса 83
Охрана труда и окружающей среды 87
2 Охрана окружающей среды 93
3 Обеспечение безопасности в чрезвычайных ситуациях. 97
Пояснительная записка.DOC
Целью дипломного проектирования является подтверждение знаний и умений полученных в результате обучения в Брестском государственном техническом университете.
Дипломное проектирование по технологии машиностроения следует проводить учитывая разработку ресурсосберегающих технологий повышение качества продукции внедрение новых технологических и конструкторских разработок прогрессивные методы обработки усовершенствованный режущий и вспомогательный инструмент и так далее.
Разработка технологического процесса изготовления детали
1Назначение и конструкция детали
Деталь «Корпус 503А-8603512-02» входит в состав гидроцилиндра 503А - 8603510-03 позиция 1 (рисунок 1.1).
Рисунок 1.1 – Эскиз гидроцилиндра 503А-8603510-03
Гидроцилиндр 503А-8603510-03 предназначен для подъёма кузова автомобилей серии МАЗ-5551. Крепится гидроцилиндр на автомобиле с помощью цапф Б. Вместо транспортной пробки 11 завинчивается штуцер гидросистемы через который подаётся масло в гидроцилиндр. Происходит выдвижение ступеней I-III – кузов поднимается. Опускание кузова и соответственно складывание гидроцилиндра происходит под действием собственного веса кузова автомобиля.
Корпус предназначен для направления движения и ограничения крайних положений второй ступени гидроцилиндра. В конструкции корпуса присутствуют приваренные цапфы с помощью которых корпус крепится к кузову и бонка к которой присоединяется штуцер гидросистемы.
Рисунок 1.2 - Основные поверхности детали
Исполнительными поверхностями (поверхности с помощью которых деталь выполняет свою функцию в узле) являются:
13 14 15 – внутренние цилиндрические поверхности – служат направляющими для движения 2 ступени цилиндра.
Основными конструкторскими базами (поверхности точки линии определяющие положение данной детали в узле) являются:
6 – поверхности отверстий под цапфы.
Вспомогательными конструкторскими базами (поверхности линии или точки определяющие положение других деталей относительно данной) являются:
– отверстие в стенке корпуса – определяет положение бонки под штуцер гидросистемы;
и 10 – резьбовая и торцевая поверхности – определяют положение днища;
13 14 15 - внутренние цилиндрические поверхности – определяют положение 2 ступени цилиндра;
16 17 18 – поверхности канавок – определяют положение уплотнителей.
Остальные поверхности являются свободными.
Материал детали – конструкционная сталь 35 (среднеуглеродистая сталь). Этот материал применяется для изготовления самых разнообразных деталей во всех отраслях машиностроения. Заменители – стали 30 40 35Г.
Таблица 1.1 – Химический состав стали 35
Таблица 1.2 – Механические свойства стали 35
2 Анализ технических условий изготовления детали
В ходе этого анализа необходимо установить в какой мере состав и численные показатели технических условий указанных на чертеже детали соответствуют её назначению и условиям работы.
Исходя из назначения и условий работы детали наиболее важными и ответственными поверхностями являются внутренние диаметры для хождения полуколец и для установки направляющих и уплотнений.
Внутренний диаметр для хождения полуколец B127 выполняется по 10 квалитету точности с параметром шероховатости Ra125 внутренние диаметры для установки направляющих и уплотнений B130 и B132 выполняется по 10 квалитету точности с параметром шероховатости Ra125 и допуском на биение относительно диаметра для хождения полуколец B127 равным 008мм и 006мм соответственно.
3 Анализ технологичности конструкции
Анализ технологичности проводится с целью выявления элементов конструкции которые вызовут затруднения при изготовлении изделия (необходимость сложной заготовки дорогостоящих методов обработки и оборудования сложной и дорогой оснастки больших затрат времени и т.д.).
Конструкция сборочной единицы усложнена имеющимися на ней приваренными цапфами и бонкой.
Большинство поверхностей легко доступны для режущего инструмента. В основном используется стандартный режущий инструмент однако имеются поверхности для обработки которых необходимо использовать специнструмент (внутренние диаметры для установки направляющих и уплотнений). Обработка возможна на станках нормальной точности. Необходимо применение специальных приспособлений так как есть поверхности получить которые очень сложно. Материал хорошо обрабатывается резанием т.к. коэффициент обрабатываемости стали 35 равен 10. Контроль поверхностей детали не составляет большого труда однако есть поверхности контроль которых требуют применения специальных приспособлений. Канавки для выхода инструмента отсутствуют. Отсутствует большая разностенность и незамкнутость контуров.
Вывод: конструкция детали является средней технологичности.
4 Определение типа производства
Исходя из таблицы ориентировочного определения типа производства по годовому объёму выпуска (N=10000штгод) и массе (m=188 кг) определим что производство деталей среднесерийное. После разработки технологического процесса механической обработки изделия а так же основного оборудования тип производства подлежит уточнению по коэффициенту закрепления операций.
5 Выбор метода получения заготовки
Метод получения заготовки ее качество и точность определяет объем механической обработки который в свою очередь устанавливает количество рабочих ходов (операций) технологического процесса.
В базовом варианте в качестве заготовки используется горячекатаный трубный прокат повышенной точности. Этот вид заготовки подходит для принятого типа производства.
Коэффициент использования материала:
где mдет - масса готовой детали кг;
mзаг - масса заготовки кг. (массы заготовок определяем с помощью системы КОМПАС-3D 5.11 путем построения твердотельной модели заготовки).
Так как КИМ1>06 то данная заготовка приемлема для среднесерийного типа производства.
Стоимость базовой заготовки можно определить по следующей формуле:
где SМ – стоимость материала руб;
SЗО – стоимость заготовительных операций руб.
Стоимость материала SМ:
Q – масса одной штучной заготовки с учетом потерь на концевые обрезки толщину резцов и некратность кг;
q – масса детали кг;
SОТХ – стоимость 1т стружки руб.
Прокат поступает на заготовительные операции длиной 22м (масса 847кг). После резки получаем 4 заготовки.одной штучной заготовки с учетом потерь на концевые обрезки толщину резцов и некратность будет 21175кг.
Для трубного проката (труба):
В качестве альтернативной замены трубного поката можно использовать заготовки получаемые центробежным литьем т.к. деталь имеет форму вращения. Данный вид заготовки приемлим для среднесерийного типа производства.
Стоимость альтернативной заготовки можно определить по следующей формуле:
кт – коэффициент зависящий от класса точности;
кс – коэффициент зависящий от группы сложности;
кв – коэффициент зависящий от массы;
км – коэффициент зависящий от марки материала;
кп – коэффициент зависящий от объема производства;
Q – масса заготовки кг;
Sотх – стоимость одной тонны отходов руб.
Сравнивая два вышеприведенных варианта заготовки по стоимости материала и коэффициенту использования материал (Sзаг1Sзаг2 КИМ1КИМ2) можно сделать вывод что более выгодным является первый вариант заготовки т.к КИМ почти одинаков а стоимость заготовки из трубного проката ниже чем заготовок полученных центробежным литьем на 12%.
6 Анализ базового варианта технологического процесса изготовления детали
Критический анализ базового техпроцесса изготовления заданного изделия проводится с целью выявления его недостатков что позволит разработать более эффективный техпроцесс в соответствии с новыми данными.
Таблица 1.3 – Анализ базового техпроцесса обработки детали «Корпус 503А-8603512-02»
Наименование и краткое содержание операции
Измерительный инструмент
Продолжение таблицы 1.3
Подрезать торец в размер с двух сторон. Точить фаски
Патрон 7102-0072 ГОСТ 24351-80; центр вращающийся ГОСТ 8742-75
Резец левый 03215-02 Т15К6
Штангенциркуль ШЦ II-250-630-0.1
Токарная. Обточить B144
Центр передний ГОСТ 13214-79; центр вращающийся ГОСТ 8742-75
Резец сборный 2109-7987 Т15К6
Сверлильная. Цековать отверстия B62 с двух сторон
Зенковка торцовая 62.26
Контрольное приспособление
Токарная. Зенкеровать отверстие насквозь зенкеровать ступенчатое отверстие
Приспособление 9075-3875
Зенкер 9346-735; зенкер двухступенчатый 9346-788 Т14К8
Нутромер НИ 100-160 ГОСТ 868-82; штангенциркуль ШЦ I-125-0.1 ГОСТ 166-89; контрольное приспособление 9801-3639
Токарная. Раскатать отверстие B127
Приспособление 9675-3875
Раскатка 1412-4032; ролик 1181-0014
НИ 100-160; профилометр
Сверлильная. Сверлить отв. снять фаску нарезать резьбу.
Кондуктор 9671-10715
Сверло B22.75 ГОСТ 10903-77; развертка коническая 2973-0036; зенковка ГОСТ 14953-80; метчик КГ34
Пробка резьбовая КГ34" 8258-4006 8259-4006; штангенциркуль ШЦ I-125-0.1 ГОСТ 166-89; пробка конусная 05544-6
Токарная. Проточить поверхность B142 нарезать резьбу
351-80; центр грибковый 9460-130-I
Резец сборный Т15К6; резец резьбовой сборный ТV02-035-884-82 Т15К6
Кольцо резьбовое М140×1.5-6g 8212-0293 8212-1293; скоба B139.968 – скоба B1879.65-0.12; скоба B142-016
Токарная. Расточить 4 канавки
Оправка цанговая 9677-1245
Резец фасонный круглый 9320-890
Штангенциркуль ШЦ I-125-0.1 ГОСТ 166-89; шаблон на размер 18+0.14; пластина на размер 2.6+0.25; приспособление для замера B133+1.0 B131+1.0 B137+1.0 B132+0.26; контрольное приспособление 9661-623653
В базовом техпроцессе каждый метод обработки резанием соответствует требуемой форме качеству точности и положению получаемой поверхности.
Состав методов обработки каждой поверхности соответствует требуемому коэффициенту уточнения параметров точности заготовки до уровня точности детали.
Производительность методов обработки в целом соответствует кпупносерийному производству. На каждой из операций задействовано не более одного станка что свидетельствует о том что принятые в техпроцессе методы достаточно производительны о рациональном выборе оборудования и режимов резания.
Во всех случаях при выдерживании диаметральных размеров соблюдается принцип единства баз. При выдерживании некоторых линейных размеров принцип единства баз не соблюдается. Это объясняется тем что большинство линейных размеров получаются по настройке инструментов.
В качестве черновых технологических баз на первых операциях используется торец трубы и наружная цилиндрическая поверхность. Такой комплект технологических баз позволяет подготовить чистовые базы для последующей механической обработки.
Технологический маршрут базового техпроцесса в целом соответствует принципу постепенного формирования точности отдельных поверхностей и их взаимного расположения а также соответствует хронологическому порядку подготовки технологических баз и принципу первоочередного выполнения переходов на которых снимаются наибольшие припуски и напуски.
Стоимость технические характеристики оборудования соответствуют габаритам и сложности заготовки требуемой точности обработки типу производства кроме применяемых на операциях 010 055 токарно-винторезных станков и на операции 040 вертикально-сверлильного станка не свойственных среднесерийному типу производства.
Станочные приспособления соответствуют данному типу производства. В базовом техпроцессе в основном применяются неразборные специальные и специализированные наладочные приспособления.
Конструкция режущих и вспомогательных инструментов в целом соответствует массовому типу производства. В базовом техпроцессе в основном применяется специальный инструмент а также многоинструментальные наладки что даёт возможность сократить набор формообразующих движений и за один рабочий ход обработать максимальное количество поверхностей. Благодаря применению специального вспомогательного инструмента сокращается время на смену и подналадку режущего инструмента.
Средства контроля также соответствуют типу производства. В базовом техпроцессе применяются специальные средства контроля что позволяет сократить время контроля. Точность контрольных приспособлений соответствует точности контролируемых размеров.
Возможные пути улучшения базового техпроцесса:
- вместо токарной операции 005 ввести центровально-подрезную операцию которая позволяет сократить количество установов;
- объединить токарные операции 030(зенкерование насквозь) 035 и 045 в одну токарную с ЧПУ;
- объединить токарные операции 030(зенкерование ступенчатой части отверстия) и 055 в одну токарную с ЧПУ;
- заменить вертикально-сверлильный станок 2Н135 на операции 055 на сверлильный с ЧПУ 2Р135Ф2.
7 Выбор методов обработки
Выбор и обоснование методов обработки проведем для наиболее ответственных поверхностей. Обоснование выбора методов обработки будем производить на основе требуемых величин уточнения Ку рассчитанных по допускам линейных размеров соответствующих поверхностей.
При выборе методов обработки будем пользоваться справочными таблицами экономической точности обработки в которых содержатся сведения о технических возможностях различных методов обработки.
Выберем методы для обработки наружной цилиндрической поверхности B144+0.16 (IT10):
- черновое точение (IT12);
- чистовое точение (IT10).
Требуемый коэффициент уточнения:
где Ку - требуемая величина уточнения;
dзаг - допуск размера формы или расположения поверхностей заготовки;
dдет - допуск размера формы или расположения поверхностей детали.
Расчетная величина уточнения по выбранному маршруту обработки:
где К1 К2 Кn - величины уточнения по каждому переходу или операции при обработке рассматриваемой поверхности. Точность на черновом переходе обработки сталей обычно повышается на 1 3 квалитета размерной точности. Точность на каждом чистовом и отделочном переходе при обработке сталей повышается на 1 2 квалитета точности. Единая система допусков и посадок ЕСДП построена так что для одного интервала номинальных размеров допуски в соседних квалитетах отличаются в 16 раз. Поэтому расчетные величины уточнений для сталей будут равны:
К = 16 163 = 16 41 – для черновой обработке;
К = 16 162 = 16 256 – для чистовой обработки.
Так как соблюдается условие Ку. расч. ≥ Ку значит требуемая точность будет обеспечиваться выбранными методами обработки.
Выбранные методы сведем в таблицу 1.4.
Таблица 1.4 - Выбор методов обработки
Поверхность B144-0.16
Отверстие с резьбой КГ34”
Нарезание резьбы метчиком
Поверхность М140×1.5-6g
Нарезание резьбы резцом
8 Выбор технологических баз
Выбор баз для механической обработки производим с учётом достижения требуемой точности взаимного расположения поверхностей детали по линейным и угловым размерам обеспечения доступа инструментов к обрабатываемым поверхностям.
Сначала производим выбор чистовых баз.
При зенковании двух поверхностей под цапфы требуется выдержать линейные размеры при этом используется следующий комплект чистовых баз (рисунок 1.3): точки 1234 располагаются на центральной оси детали точка 5 располагаются на левом торце детали при этом соблюдается принцип единства баз для получаемых линейных размеров. Эту схему базирования можно осуществить устанавливая заготовку в равномерно-сходящиеся призмы по наружной цилиндрической поверхности и левому торцу используя специальное приспособление.
Рисунок 1.3 – Схема базирования при зенковании поверхностей под цапфы
При зенкеровании раскатке сквозного отверстия и при точении цилиндрической поверхности под резьбу и нарезании резьбы базирование осуществляется по левому торцу детали (точка 5) с помощью упора и по наружному цилиндру (точки 1234) с помощью патрона. Такая схема базирования позволяет совместить измерительную и технологическую базы для диаметральных размеров выдерживаемых на данной операции. Для продольных размеров получаемых на данной операции принцип единства баз не соблюдается.
Рисунок 1.4 – При зенкеровании раскатке сквозного отверстия и при точении цилиндрической поверхности под резьбу и нарезании резьбы М140
При зенкеровании внутреннего ступенчатого отверстия и растачивании канавок базирование осуществляется по правому торцу детали (точка 5) с помощью откидного упора и по внутреннему сквозному отверстию (точки 1234) и поддерживается люнетом (точка 6). Такая схема базирования позволяет совместить измерительную и технологическую базы всех размеров выдерживаемых на данной операции. Осуществить эту схему базирования можно с помощью специального токарного приспособления.
Рисунок 1.5 – Схема базирования при зенкеровании раскатке внутреннего ступенчатого отверстия и растачивании канавок
При обработке отверстий КГ34" базирование осуществляется по левому торцу детали (точка 5) с помощью упора и по наружному цилиндру (точки 1234) с помощью нижней призмы и прижима. Такая схема базирования позволяет совместить измерительную и технологическую базы для линейных размеров выдерживаемых на данной операции. Осуществить эту схему базирования можно с помощью специального сверлильного приспособления которое будет спроектировано в конструкторской части проекта.
Рисунок 1.6 – Схема базирования при обработке отверстий КГ34
Произведем выбор черновых баз.
Схемы базирования будут выглядеть следующим образом (рисунок 1.7). Такая схема базирования может быть реализована при помощи приспособления на основе равномерно сходящихся призм и откидного упора при центровании и трехкулачкового токарного патрона закрепляющего деталь по внутреннему отверстию при обтачивании по наружной поверхности. Такая схема базирования позволяет совместить измерительную и технологическую базы для выдерживаемых радиальных и продольных размеров.
Рисунок 1.7 – Схема базирования при обработке торцев и наружного цилиндра детали
9 Разработка технологического маршрута обработки детали
Запишем технологические переходы обработки детали в хронологическом порядке учитывая следующие требования:
- каждый последующий переход должен уменьшить погрешность обрабатываемой поверхности и улучшить ее качество;
- в первую очередь должны обрабатываться те поверхности которые будут использоваться в качестве технологических баз на последующих переходах;
- не рекомендуется совмещение черновой и чистовой обработки немерным инструментом на одном и том же станке;
- обработка легкоповреждаемых поверхностей должна выполнятся в конце техпроцесса.
Составим порядок переходов обработки детали «Корпус 503А-8603512-02»:
Подрезка торцев центровка с одновременной обработкой короткого участка внутренней цилиндрической поверхности;
Черновое точение наружной цилиндрической поверхности заготовки;
Чистовое точение наружной цилиндрической поверхности заготовки;
Цекование верхнего отверстия под цапфу;
Цекование нижнего отверстия под цапфу;
Зенкерование внутренней цилиндрической поверхности насквозь;
Раскатка внутреннюю цилиндрическую поверхность после зенкерования насквозь;
Нарезание резьбы М140х15;
Зенкерование ступенчатого отверстия;
Растачивание одной канавки;
Растачивание второй канавки;
Растачивание третьей канавки;
Растачивание четвертой канавки;
Сверление отверстия под КГ34";
Развертывание отверстия под КГ34";
Нарезание резьбы КГ34";
Предварительно выберем оборудование:
- для подрезки торцев и центровки выбираем центровально-подрезной;
- для точения заготовки по наружной цилиндрической поверхности выбираем токарно-винторезный станок;
- для зенкерования насквозь раскатки внутреннего отверстия и нарезания резьбы выбираем токарный станок с ЧПУ;
- для зенкерования ступенчатого отверстия растачивания канавок выбираем токарный станок с ЧПУ;
- для обработки отверстия КГ34" – вертикально-сверлильный станок с ЧПУ;
По общим признакам (одинаковое оборудование схемы базирования режущий инструмент и др.) объединим переходы в операции. Выделим следующие операции:
Операция 005 – центровально-подрезная (переходы 1).
Операция 010 – токарная с ЧПУ (переход 2-3).
Операция 015 – вертикально-сверлильная (переход 4-5).
Операция 020 – сварка (переход 6).
Операция 025 – токарная с ЧПУ (переход 7-9).
Операция 030 – токарная с ЧПУ (переход 10-15).
Операция 035 – сверлильная с ЧПУ (переход 16-19).
Операция 040 – слесарная.
Операция 045 – контрольная.
10 Разработка технологических операций
На этом этапе окончательно определяется состав и порядок выполнения переходов в пределах каждой технологической операции производится выбор моделей оборудования станочных приспособлений режущих и измерительных инструментов.
Состав вертикально-сверлильной операции 015:
Установить и закрепить деталь в кондукторе.
Зенковать одну поверхность под цапфу.
Переустановить деталь.
Зенковать вторую поверхность под цапфу.
Произведем выбор приспособлений режущего и измерительного инструмента СОЖ для вертикально-сверлильной операции 015 на которой производится обработка отверстия под установку цапф.
Для установки и закрепления детали на данной операции используется специальное сверлильное приспособление – кондуктор.
Зенкование осуществляется зенковкой 9348-446 материал режущей части - быстрорежущая сталь Р6М5.
В качестве СОЖ используется Эмульсол ЭМ-1 в основном применяющийся при лезвийной обработке сталей.
Выберем измерительный инструмент. После зенкования отверстие контролируется штангенглубиномером ШГ-160 ГОСТ 162-90.
В качестве станочного оборудования выбираем вертикально-сверлильный станок 2Н150.
Состав сверлильной операции с ЧПУ 030:
Сверлить отверстие КГ34".
Развернуть отверстие КГ34".
Зенковать фаску в отверстии КГ34".
Нарезать резьбу КГ34".
Контролировать размеры.
Произведем выбор приспособлений режущего и измерительного инструмента СОЖ для сверлильной операции с ЧПУ 030 на которой производится обработка отверстия КГ34".
Для установки и закрепления детали на данной операции используется специальное сверлильное приспособление – кондуктор которое будет спроектировано в конструкторской части проекта.
Сверление осуществляется сверлом 2301-0077 2275 ГОСТ 10903-77 материал режущей части - быстрорежущая сталь Р6М5. Развертывание осуществляется разверткой конической 2373-0036 материал режущей части - быстрорежущая сталь Р6М5. Зенкование осуществляется зенковкой 2353-0136 ГОСТ 14953-80 материал режущей части - быстрорежущая сталь Р6М5. Нарезание резьбы осуществляется метчиком КГ34" 2680-4055.
Выберем измерительный инструмент. После развертывания отверстие контролируется пробкой конусной 05544-6 после резьбонарезания – пробкой резьбовой КГ34" 8258-4006; 8259-4006.
В качестве станочного оборудования выбираем сверлильный станок с ЧПУ 2Р135Ф2.
Разработку остальных технологических операций производим аналогично и результаты сводим в операционные карты (см. приложение).
Все применяемое оборудование и его характеристики сведем в таблицу 1.5.
Таблица 1.5 - Ведомость станочного оборудования
Категория ремонтной сложности
Центровально-подрезной
Вертикально-сверлильный станок
Вертикально-сверлильный
11 Расчет припусков на механическую обработку двух поверхностей аналитическим методом
Рассчитаем припуски и межоперационные размеры для переходов на обработку отверстия корпуса B127Н10(+0.16) мм.
Исходные данные: заготовка – прокат труба B148×12 из стали 35 масса заготовки 206 кг.
Деталь базируется в приспособлении по торцу и наружной поверхности.
Пользуясь рабочим чертежом детали выберем технологический маршрут обработки отверстия B127Н10 и определим Rz и h для заготовки по переходам:
–й переход – однократное зенкерование квалитет 12 Rz = 20 мкм h = 4 мкм;
– й переход – раскатка квалитет 10 Rz = 5 мкм h = 5 мкм.
Пространственное отклонение формы поверхности заготовки ρз:
где ρк – отклонение учитывающее коробление заготовки мкм;
ρэкс – отклонение учитывающее несоосность отверстия по отношению к наружному контуру заготовки мкм.
где Δк – удельная кривизна заготовки мкммм;
l – длина обрабатываемой поверхности мм.
Δк = 25 мкммм; ρк = 000252665 = 665 мкм; ρэкс = 500 мкм.
Остаточное пространственное отклонение по переходам определяем по формуле:
где ку – коэффициент уточнения формы.
После зенкерования ρ1 = 004ρз = 004832 = 3328 мкм;
После раскатки ρ2 = 003ρз = 003832 = 2496 мкм.
Погрешность установки детали на выполняемом переходе у определим по формуле:
где б – погрешность базирования.
В нашем случае б = 0 так как имеет место совмещение технологической и измерительной баз.
Погрешность закрепления корпуса в приспособлении з = 200 мкм.
Расчёт минимальных значений межоперационных припусков производим по формуле:
zmin = 2 (Rz i-1 + hi-1 + )(1.11)
Тогда минимальный припуск по переходам будет следующим:
-й переход: 2z1min = 2 (200 + 300 +) = 21356мкм.
-й переход: 2z2min = 2 (20 + 4 + ) = 257мкм.
Вычислим расчётный размер:
-й переход (раскатка): Dp2 = 12716 – 0114 = 127046 мм;
-й переход (зенкеровка): Dpз = 127046 – 2712 = 124334 мм.
Допуски на размер назначаем и заносим в таблицу 1.5.
Рассчитаем минимальные диаметры отверстий:
Заготовка: Dзmin = 1243 – 22 = 1221 мм.
Минимальные значения припусков zminпр находим как разность наибольших предельных размеров выполняемого и предшествующего переходов а максимальные значения zmaxпр как разность наименьших предельных размеров:
-й переход: = 12716 – 127 = 016 мм;
= 127 – 1266 = 04 мм;
-й переход: = 127 – 1243 = 27 мм;
= 1266 – 1221 = 45 мм.
Предельные значения общих припусков определим суммируя промежуточные припуски:
= 110 + 2750 = 2860 мкм = 286 мм;
= 110 + 4790 = 4900 мкм = 49 мм.
Таблица 1.6 – Аналитический расчёт припусков
переходы обработки отверстия B127Н10
Элементы припуска мкм
Расчётный припуск 2zmin мкм
Расчётный размер Dp мм
Предельный размер мм
Предельные значения припусков мм
Продолжение таблицы 1.6
Общий номинальный припуск вычисляется по формуле:
где Вз и Вд – соответственно верхнее отклонение допуска заготовки и детали.
= 286 + 11 – 016 = 38 мм.
Следовательно номинальный диаметр отверстия заготовки будет равен:
Dзном = Dном – (1.13)
Dзном = 127 – 38 = 1232 мм
Производим проверку правильности выполнения расчётов по формуле:
-й переход: 110 – 110 = 160 – 160 0 = 0;
-й переход: 4500 – 2700 = 2200 – 160 1800 = 1800.
Общий припуск: 4900 – 2860 = 2200 – 160 2040 = 2040.
Значит расчёты межоперационных припусков произведены правильно. Все расчёты сведены в таблицу 1.6.
На основании данных таблицы строим схему графического расположения припусков и допусков на обработку отверстия B127Н10.
Рисунок 1.8 – Расположение полей припусков и допусков на отверстие B127Н10
Рассчитаем припуски и межоперационные размеры для переходов на обработку поверхности B144h10(-0.16) корпуса.
Обработка корпуса в центрах.
Составим технологический маршрут получения поверхности B144h10 с указанием Rz и h по переходам:
-й переход – чистовое обтачивание квалитет 10 Rz = 32 мкм h = 30 мкм;
-й переход – черновое обтачивание квалитет 12 Rz = 50 мкм h = 50 мкм;
Заготовка – Rz = 200 мкм h = 300 мкм.
Значение пространственных отклонений формы для заготовки данного вида ρз определяем по формуле:
где ρк – коробление (кривизна) заготовки.
Δк = 1 мкммм; ρк = 00012665 = 2665 мкм
ρц – погрешность центрирования определяем по формуле:
где d – допуск на наружный базирующий диаметр при центрировании d=22мм.
Погрешность установки детали на выполняемом переходе у равна нулю (базирование по центровым отверстиям).
zmin = 2(Rz i-1 + hi-1 +) ()
-й переход: 2zmin2 =2(50 + 50 +58)= 2158 мкм.
Результаты сведём в таблицу 1.7.
Расчётный размер диаметра корпуса dр вычислим начиная с конечного минимального чертёжного размера путем добавления припуска.
-й переход: d2 = 14284мм.
-й переход: d1 = 14384 + 20158 = 144156 мм.
Заготовка: dзагот = 144156 + 21661 = 147478 мм.
Назначаем допуски на переходы и заготовку.
Предельный размер dmin определяем округляя dр до большего значения в пределах допуска на данном переходе а dmax определяем прибавлением к dmin допусков соответствующих переходов:
-й переход: dm dmax 2 = 14384 + 016 = 144 мм
-й переход: dm dmax 1 = 14416 + 04 = 14456 мм.
Заготовка: dm dmax заг = 1475 + 22 = 1497 мм.
Максимальные значения припусков находим как разность наибольших предельных размеров выполняемого и предшествующего переходов а минимальные значения – как разность наименьших предельных размеров выполняемого и предшествующего переходов:
-й переход: = 1497 – 14456 = 514 мм;
= 1475 – 14417 = 334 мм;
-й переход: = 14456 – 144 = 056 мм;
= 14416 – 14384 = 032 мм;
Общий минимальный припуск находим как сумму минимальных промежуточных припусков а общий максимальный припуск – как сумму максимальных припусков:
= 334 + 032 = 366 мм;
= 514 + 056 = 57 мм.
Общий номинальный припуск 2 вычисляется по формуле:
где Нз и Нд – соответственно нижнее отклонение допуска заготовки и готовой детали: Нз = 1100 мкм Нд = 160 мкм
= 3660 + 1100 – 160 = 4600 мкм = 46 мм.
Зная значение находим номинальный диаметр заготовки:
dном = ddном + 2(1.18)
dном = 144 + 35 = 1475 мм.
Для рассматриваемого случая имеем:
-й переход: 4600 – 2560 = 2200 – 160840 = 840.
Общий припуск: 4600 – 2560 = 2200 – 160840 = 840.
Следовательно расчёты межоперационных припусков произведены правильно. Все расчёты сведены в таблицу 1.7.
Таблица 1.7 – Аналитический расчёт припусков
переходы обработки отверстия B144h10
-й переход (черновое обтачивание)
-й переход (чистовое обтачивание)
На основании данных таблицы строим схему графического расположения припусков и допусков на обработку B144h10.
Рисунок 1.9 – Расположение полей припусков и допусков на поверхность B144h10
12 Расчёт режимов резания
Расчёт режимов резания на два перехода производится по эмпирическим формулам согласно [2]:
Режимы резания при чистовой проточке поверхности B144-0.16:
Глубина резания будет составлять t = 05 мм.
Подачу выбираем из таблиц согласно [2]: S = 05ммоб.
Материал режущей части – твердый сплав Т15К6.
Скорость резания находим по формуле:
где Т – период стойкости инструмента Т = 60 мин;
Сv = 340 х = 015 у = 045 m = 02 – коэффициенты и показатели степени по [2];
Кv = Кмv Кuv Кпи (1.20)
где Кuv = 10 Кпи = 09 – коэффициенты согласно [2]
Определим частоту вращения по формуле:
Получаем: n = = 579 мин-1.
Согласно характеристикам выбранного оборудования принимаем частоту вращения шпинделя:
nф = 630 мин-1 тогда vф = ммин.
Определим силу резания по формуле:
где Ср = 300 х = 10 у = 075 n = -015 – показатели степени согласно таблиц [2]:
где = 10 = 10 = 10 = 10 – коэффициенты согласно таблицам [2];
где n = 075 – показатель степени.
Отсюда = 378 Н = 038 кН.
Определим мощность резания по формуле:
где N – мощность резания.
Определим основное время по формуле:
где L = 539 мм – длина рабочего хода
SM – минутная подача.
Отсюда SM = 06630 = 378 мммин;
Определим режимы резания при сверлении отверстия B
Глубина резания при сверлении равна половине диаметра:
T = 052775 = 114 мм.
Подачу выбираем максимально допустимую S = 043 ммоб.
Материал режущей части – быстрорежущая сталь Р6М5.
Скорость резания при сверлении определяем по формуле:
где Сv – поправочный коэффициент;
D – диаметр обработки мм;
Т – период стойкости инструмента мин;
q m y – показатели степени из таблиц [2];
Кv – коэффициент обрабатываемости
Кv = КмvКuvКlv(1.31)
где Киv = 10 – коэффициент учитывающий инструментальный материал;
Кмv – коэффициент характеризирующий обрабатываемый материал;
где Кr – коэффициент характеризирующий группу стали по обрабатываемости;
nv – показатель степени.
Коэффициенты определены по таблицам 1-24 стр. 261-276 согласно [2]:
Сv = 98 q = 04 у = 05 m = 02 отсюда
Кv = 13411 = 134 отсюда
Получаем: n = = 429 мин-1.
nф = 430 мин-1 тогда vф = = 307 ммин.
Определим крутящий момент и осевую силу:
где Cм = 00345 Ср = 68 q = 20 у = 08 – поправочные коэффициенты согласно таблиц [2]:
где Nс – мощность резания.
Определим величину рабочего хода L по формуле:
L = l + l1 + l2 (1.38)
где L = 15 мм – длина обработки;
l1 = l2 = 55 мм – длина врезания и перебега отсюда:
L = 15 + 55 + 55 = 26 мм.
На остальные операции по обработке поверхностей режимы резания назначаем по таблицам 1-37 приведенным на стр. 261-283 в [2] и [3].
Таблица 1.8 – Режимы резания при обработке «Корпус 503А-8603512-02».
Наименование операции или перехода
Подрезать торцы в размер 533 и точить 2 фаски 2×30
Обточить начерно B145
Обточить начисто B144
Продолжение таблицы 1.8
Цековать отв. B62 с одной стороны
Цековать отв. B62 с другой стороны
Зенкеровать отверстие B127
Раскатать отверстие B127
Точить поверхность под резьбу 139.85
Нарезать резьбу М140
Зенкеровать ступенчатое отверстие B130 B132
Расточить канавку B137
Расточить канавку B133
Расточить канавку B131
Расточить канавку B132
Расточить фаску 1×45
Сверлить отверстие B2275
Развернуть отверстие под резьбу
Зенковать фаску 2×45
Нарезать резьбу КГ34”
13 Определение норм времени технологических операций
Нормирование операций производим согласно [4]:
Расчёт штучного времени для центровально-подрезной операции 005. Основное время То составляет 06 мин. производство среднесерийное. Рассчитываем норму штучно-калькуляционного времени по формуле:
где Тшт – штучное время определяется по формуле:
где Тп-з – подготовительно-заключительное время мин;
n – количество деталей в настроечной партии шт;
То – основное время мин;
Тв – вспомогательное время мин;
Тоб – время на обслуживание рабочего места мин;
Тотд – время перерывов на отдых и личные надобности мин.
Вспомогательное время определяем по формуле:
где Ту.с. – время на установку и снятие детали мин;
Туп – время на приёмы управления мин;
Тиз – время на измерение детали мин.
Ту.с = 013 мин – при установке детали массой до 20кг в призмах
Туп = 006 мин – при включениивыключении станка рычагом 004мин при подведенииотведении инструмента 002мин.
Тиз = 012 мин – при измерении штангенциркулем.
Время на обслуживание рабочего места и отдых составляет 7% (при длине стола до 750мм) от оперативного времени:
Тоб + Тотд = 007Топ (1.43)
Тоб + Тотд = 007091 = 003 мин.
Тогда штучное время равно:
Тшт = 06 + 031 + 003 = 094 мин.
Подготовительно-заключительное время состоит из времени на наладку станка инструмента; при обработке в специальном приспособлении – 14 мин установка инструмента – 2 мин установка упора – 2 мин получение инструмента до работы и сдача его по окончании смены – 7 мин.
Тп-з = 14 + 2 + 2 + 7 = 25 мин.
Тогда штучно-калькуляционное время:
Результаты расчётов по остальным операциям произведенные аналогично вышеприведенным занесём в таблицу 1.9.
Таблица 1.9 – Нормирование операций технологического процесса обработки детали «Корпус 503А-8603512-02»
Наименование операции
Центровально-подрезная
Вертикально-сверлильная
14 Определение типа производства по коэффициенту закрепления операций
Тип производства по ГОСТ 3.1119-83 характеризуется коэффициентом закрепления операций:
Кз.о. = 1 – массовое;
Кз.о. 10 – крупносерийное;
Кз.о. 20 – среднесерийное;
Кз.о. 40 – мелкосерийное производство
В единичном производстве Кз.о. не регламентируется.
В соответствии с методическими указаниями [5] определим Кз.о.:
где О – количество всех технологических операций выполняемых в течение месяца;
Р – число рабочих мест необходимых для выполнения месячной программы.
Число рабочих мест для выполнения определённой i-ой операции определяется по формуле:
где NM – месячный объём выпуска деталей шт;
Тшт-к – штучно-калькуляционное время на выполнение операции мин;
Кмз = 1 – коэффициент подготовительно-заключительного времени;
FM – месячный фонд времени работы оборудования 388 час;
Кb – коэффициент выполнения норм времени Кb = 12.
Рассчитаем количество рабочих мест по операциям:
Рассчитываем коэффициент загрузки рабочих мест по формуле:
где РрI – рассчитанное число рабочих мест;
РI – округлённое число рабочих мест.
Определим количество операций выполняемых на рабочем месте при его нормативной загрузке по формуле:
где н – нормативный коэффициент загрузки.
Определим общее количество операций и рабочих мест по формулам:
О = 20 + 6 + 16 + 3 + 7 + 16 = 68;
Отсюда рассчитаем коэффициент загрузки операций:
Согласно рекомендациям [5] производство среднесерийное.
15 Расчёт технологической размерной цепи
Технологическую размерную цепь составляем для чертежного размера 28+2 получаемого без соблюдения принципа единства баз.
Любой размер можно представить как расстояние между двумя точками (его границами) на условной координатной оси. Это расстояние зависит от координат границ размера то есть от двух размеров связывающих начало координат с этими границами.
Аналогичная зависимость имеет место при формировании размеров деталей в процессе их механической обработки партиями на заранее настроенных станках. При этом используется контактное базирование деталей и режущий инструмент настраивается относительно установочных элементов приспособления контактирующих с технологическими базами детали. В этих условиях начало координат для отсчёта положений границ формируемого размера детали следует принимать на технологической базе ориентирующей деталь в направлении этого размера так как она контактирует с неизменными установочными элементами приспособления и занимает стабильное положение для всех деталей партии. Таким образом исходный размер АΔ в общем случае зависит от двух размеров (А1 и А2) которые связывают его границы с соответствующей технологической базой. Один из этих размеров А1=533мм связывающий технологическую базу с формируемой режущим инструментом границей исходного звена сформирован на предшествующей операции без соблюдения принципа единства баз поэтому для него так же необходимо составлять размерную цепь (рисунок 1.10). Второй размер А2=505мм связывает технологическую базу и вторую границу исходного звена является настроечным.
Рисунок 1.10 – Технологическая размерная цепь для размера АΔ
Решим проектную задачу методом неполной взаимозаменяемости т.е. определим допуски составляющих звеньев по известному допуску замыкающего звена.
Допуск замыкающего звена ТАΔ=2мм
Определим единицы допуска ij для каждого из составляющих звеньев
где АСГ – среднее геометрическое границ интервала номинальных размеров в таблице допусков в который попадает j-е составляющее звено.
где Аjmin и Аjmax – минимальная и максимальная величина размера входящие в данный интервал.
Определим среднее число единиц допуска составляющих звеньев при условии равноточности этих допусков:
где n – число всех звеньев.
По таблице допусков определяем что данные величины допусков соответствуют 1415 квалитету.
Назначаем допуски на все составляющие звенья:
А1=505мм; ТА1=2800мкм. – по 15кв.
А2=533мм; ТА2=1750мкм. – по 14кв.
Правильность назначенных допусков проверяем по условию:
Составим условие точности для размерной цепи:
ТАΔ=2000мкм>1905мкм – условие точности выполняется.
Определяем координаты середин полей допусков всех составляющих звеньев кроме одного – корректирующего в качестве которого принимаем звено А2 – уменьшающее.
ЕсрА1=ЕIА1+TА22=-1400+28002=0мкм (1.54)
ЕсрАΔ=ЕIАΔ+TАΔ2=0+20002=1000мкм (1.55)
Определяем координаты середины поля допуска корректирующего звена из условия:
Определяем предельные отклонения всех составляющих звеньев:
EIА1=ЕсрА1–TА12=0–28002=–1400мкм
ESА1=ЕсрА1+ТА12=0+28002=1400мкм; (1.57)
EIА2=ЕсрА2–TА22=–1000–17502=–1875мкм
ESА2=ЕсрА2+ТА22=–1000+17502=–125мкм.
16 Определение количества основного технологического оборудования
Определим количество оборудования по формуле:
F – действительный годовой фонд времени работы оборудования час;
F = 4015 ч Ni = 10000 шт.
Коэффициенты загрузки оборудования определим как отношение расчётного количества единиц оборудования к принятому:
По полученным расчётным данным построим график загрузки оборудования.
Рисунок 1.12 – График загрузки оборудования
Т.к. на трех операциях используется токарный станок с ЧПУ 16К20Ф3С32 и при этом загрузка не превышает нормативно допустимой то операции будем выполнять на одном станке. При этом загрузка станка составит 76% что не превышает нормативно допустимой для серийного типа производства. Тогда график загрузки оборудования примет вид:
Рисунок 1.12 – График загрузки оборудования после объединения операций
Расчёт и проектирование средств технологического оснащения
1 Расчёт и проектирование приспособления для сверления отверстия в бонке
1.1Описание работы станочного приспособления
Приспособление предназначено для базирования и закрепления при сверлении отверстия в бонке. Устанавливается на вертикально-сверлильном станке с ЧПУ марки 2Р135Ф2.
Заготовка в приспособлении базируется по наружному диаметру и торцу трубы.
Принцип работы приспособления.
Труба устанавливается на призмы и упирается торцем в упор. При повороте рукоятки пневмокрана в рабочую полость пневмоцилиндра подается воздух из пневмосети при этом плунжер цилиндра давит на прижим который при этом действует как коромысловый механизм и прижимает трубу к призмам. После закрепления осуществляется сверление.
После окончания обработки рукоятка пневмокрана переключается в другую позицию сжатый воздух поступает в другую полость цилиндра. Плунжер опускается тем самым отжимается труба.
Приспособление возможно переналаживать только при замене установочных элементов.
Приспособление удобно разбирать и собирать так как большинство элементов конструкции крепятся на резьбе или винтами и болтами. Приспособление имеет большие габаритные размеры и в конструкцию приспособления входит много металлических деталей. Поэтому конструкцию приспособления можно считать металлоёмкой и сложной. Заготовку удобно устанавливать в данное приспособление так как для этого не требуется много времени и больших усилий. Для очистки и смазки некоторых деталей необходима полная разборка приспособления.
1.2Силовой расчёт станочного приспособления
Составим схему сил действующих на заготовку.
Рисунок 2.1 – Схема для расчета силы закрепления заготовки
Под действием крутящего момента Мсв заготовка стремиться вывернуться из призм при этом возникает силы реакции между призмами и заготовкой R1 и R2. Так же на заготовку действует прижимающая осевая составляющая силы резания Ро. Определим какой величины необходимо приложить силу прижима W чтобы предотвратить выворачивание.
Условие равновесия будет иметь вид:
где - вертикальные составляющие сил реакций в призмах;
К – коэффициент запаса.
где - половина угла в призме (=450).
Горизонтальные составляющие сил реакций в призмах :
Рассчитаем коэффициент запаса:
К=К1·К2·К3·К4·К5·К6 (2.4)
где К1=15 – гарантированный коэффициент запаса;
К2=12 – коэффициент учитывающий колебание силы резания из-за непостоянства припуска;
К3=11 – учитывает увеличение силы резания в результате износа инструмента;
К4=10 – учитывает постоянство силы зажима (механизированный зажим);
К5=10 – учитывает удобство расположения рукояток;
К6=11 – учитывает наличие момента стремящегося повернуть заготовку на плоскости.
К=15·12·11·1·1·11=2178
Из () находим R1Г и R2Г:
Из рассчитанного следует что прижима осевой силой от сверления хватает для предотвращения выворота заготовки из призм.
Поэтому выбираем самый малый пневмоцилиндр с односторонним штоком со следующими характеристиками D=63 мм; d=16 мм который развивает усилие:
где D – рабочий диаметр цилиндра мм;
р – давление в пневмосети МПа;
– КПД пневмоцилиндра.
1.3Расчёт сверлильного приспособления на точность
Произведем расчет приспособления для обеспечения допуска на расстояние от торца 11 мм используя следующую формулу:
где Т – допуск на выполняемый размер Т=01 мм;
Кm – коэффициент учитывающий отклонение рассеяния значений составляющих величин от закона нормального распределения Кm=12;
ЕБ – погрешность базирования заготовки в приспособлении (ЕБ = 0 т.к. соблюдается принцип единства баз);
ЕЗ – погрешность закрепления заготовки в приспособлении ЕЗ=006мм;
ЕУ – погрешность установки приспособления на станке (ЕУ=0 т.к. осуществляется надежный контакт установочной плоскости приспособления с плоскостью стола станка);
ЕИ – погрешность рабочих поверхностей приспособления в результате их изнашивания в процессе эксплуатации:
где b – постоянная зависящая от вида установочного элемента и условия контакта (b = 0005 мкм);
N – количество контактов заготовки с опорой (установок в приспособление снятий с него) в год.
ЕИ = 0005·10000=50мкм;
ЕП = 0 – погрешность перекоса т.к. применяется укороченный осевой инструмент повышенной жесткости.
– погрешность обработки исходя из экономической точности обработки =0035мм;
Кm1 – коэффициент учитывающий уменьшение предельного значения погрешности базирования при работе на настроенных станках Кm1=08;
Кm2 – коэффициент учитывающий долю погрешности обработки в суммарной погрешности Кm2=06.
Приспособление обеспечивает требуемую точность.
1.4Расчёт приспособления на прочность
Рассчитаем на прочность опасное звено приспособления. Из рассмотрения данного приспособления можно прийти к выводу что наиболее нагруженными деталями является: ось коромысла.
Ось работает на срез она изготовлена из стали Ст5.
Расчет на прочность:
где Р – сила реакции действующая на ось Р =2Q=2·1500=3000 Н ;
d – диаметр оси мм. ;
– допускаемое напряжение растяжения = 100 Мпа ;
Тогда необходимый размер опасного сечения:
Принимаем стандартный больший диаметр оси d=8мм.
2Расчёт и проектирование приспособления для контроля радиального биения внутренних канавок
2.1Разработка и краткое описание конструкции контрольного приспособления
Данное контрольное приспособление представляет собой основание со стойками с закрепленными на них подшипниками и штативом с измерительным прибором индикаторного типа. Деталь устанавливается на подшипники и проворачивается и скалка устанавливается на поверхности на которой нужно измерить биение. Показания индикатора часового типа является показаниями биения отверстий относительно искомого отверстия. В приспособлении имеется механизм для приподнимания детали при закладке и съёмке детали с приспособления так как у детали большой вес.
2.2Расчёт контрольного приспособления на точность
Для того чтобы контрольное приспособление обеспечивало правильность контроля требуется чтобы его погрешность была не более 13 допуска на контролируемый параметр:
TD – допуск контролируемого размера мм.
Погрешности в процессе измерения:
у – погрешность установки;
З – погрешность закрепления;
И – погрешность в результате износа установочных элементов;
пер. мех – погрешность передаточных механизмов;
изм. средства – погрешность средств измерения (индикатора).
Найдем погрешности возникающие в процессе измерения допуска перпендикулярности торца Б относительно наружного диаметра шлицевого отверстия:
у = 0014мм т.к. возникает биение между наружным и внутренним кольцом подшипника 4 класса;
З = 0 так в нашем случае не происходит закрепление детали на контрольном приспособлении;
И = 0 так как износ установочных подшипников невелик и при установке детали на контрольное приспособление индикатор каждый раз выставляется на “0”;
мм т.к. рычаг крепится на оси с посадrой H5g6 в которой максимальный зазор равен 14мкм.
изм.средства = 001 мм так как в качестве средства измерения используется индикатор часового типа (ИЧ 1-10) у которого цена деления равна 001мм.
Допустимая погрешность при измерении допуска перпендикулярности в 200мкм:
что равно допустимой погрешности ΔПР = 002мм и позволяет применять для измерений в рассматриваемом случае данное контрольное приспособление.
3 Расчёт и проектирование ступенчатого зенкера
Режущий инструмент – ступенчатый – зенкер необходим для обработки ступенчатого отверстия B132 и B130. Применение комбинированного инструмента позволяет сократить время обработки детали и повысить точность обработки отверстий.
Диаметр зенкера применяем с учётом допуска обрабатываемого отверстия согласно ГОСТ 12509-75.
D1 = 13005-003 D2 = 13205-003.
Диаметр направляющих зенкера D3 = 13205-0.05.
Геометрические и конструктивные параметры рабочей части зенкера задний угол α на задней поверхности лезвия 20 на калибрующей части – 5. Передний угол γ = 0. На зубьях ступени B130: задний угол = 20 на калибрующей части – 15. Главный угол в плане φ = 90. Обратную конусность на длине пластины из твердого сплава принимаем 009 мм.
К станку зенкер крепится посредством резьбы ленточной двухзаходней 36×10. Ширина ленточки при заточке 02+0.1 мм. Твердый сплав пластины для обработки конструкционной стали марки Т30К4 форму 2515 по ГОСТ 2209-82. Для корпуса зенкера применяется сталь 40Х ГОСТ 4543-71.
Технические требования к зенкерам оснащенными пластинами из твердого сплава по ГОСТ 12509-75.
Выполним проверку резьбового соединения на смятие:
Из условия износостойкости резьбы по напряжениям смятия:
где F – сила действующая на резьбу винта и гайки H;
d2 – средний диаметр резьбы винта и гайки d2 = 3373 мм;
h – высота резьбы h = 3 мм;
z – число рабочих витков.
Число рабочих витков находится следующим образом:
где Н – глубина ввинчивания винта Н = 50 мм;
P – шаг резьбы для резьбы М36х10 р = 10 мм.
[см] – допускаемое напряжение при смятии допускаемое напряжение при смятии находится по формуле:
где [т] – предел прочности материала для стали 40Х [т] = 200 Нмм2;
n – коэффициент запаса n = 15
Получим напряжениям смятия:
Напряжение смятия полностью удовлетворяет условию износостойкости резьбы по напряжениям смятия и имеет достаточный ресурс работы.
Выполним проверку резьбового соединения на растяжение:
Площадь поперечного сечения стержня болта по заданному внешнему усилию определяют по формуле:
где d1 – внутренний диаметр резьбы винта d1 = 32 мм;
Р – растягивающее усилие действующее на хвостовик;
[в]р – допускаемое напряжение на растяжение; допускаемое напряжение при растяжении находится по формуле:
где в – предел прочности материала винта в = 980 Нмм2;
n – коэффициент запаса n = 15.
[в]р= 98015 = 653 Нмм2
Из результатов расчета видно что площадь поперечного сечения стержня хвостовика гораздо больше площади необходимой для сохранения целостности хвостовика при нагрузке Р = 1645Н. Это означает что прочность при растяжении хвостовика удовлетворяет условию прочности при данных условиях эксплуатации.
4 Разработка и проектирование манипулятора для подъёма детали
4.1 Назначение манипулятора
Манипулятор предназначен для подъёма и перемещения грузов массой до 60 кг. При подключении его к пневмосети стрела и рукоять находятся в состоянии безразличного равновесия в любой точке пространства зоны обслуживания как с грузом так и без него. Манипулятор позволяет производить плавную и точную установку деталей на межоперационных передачах при усилии оператора не более 65 Н. конструкция манипулятора дает возможность использовать различные грузозахватные устройства: клещевого типа захваты с пневмоуправлением захваты закрепленные на оси жесткие захваты позволяющие транспортировать груз с ориентированным положением захваты консольно-штырьевого типа. Обеспечивает транспортировку хрупких вещей таких как стекло земляные формы.
Технические характеристики:
Номинальная грузоподъёмность кг 60;
Максимальный грузовой момент Нм 400;
Число степеней подвижности 4;
Максимальный радиус обслуживания
по горизонтали мм не менее 3150;
Минимальный радиус обслуживания
по горизонтали мм не менее 400;
Максимальная высота обслуживания мм не менее 1700;
Минимальная высота обслуживания мм не менее 200;
Габаритные размеры мм4700×580×3750;
Масса кг не более 530;
Масса без колонны кг не более 425.
4.2 Устройство и принцип работы
Стрела 8 шарнирно закреплена в стойке 7 которая крепится к вертлюгу 5.
Вертлюг крепится к колонне 9 и обеспечивает стреле 8 возможность неограниченного поворота вокруг вертикальной оси колонны. Систему уравновешивает противовес 4.
Пневмоцилиндр 1 закреплен на тяге 3 и штоком опирается на кронштейн 6 стойки 7. При подаче воздуха в рабочую полость пневмоцилиндра 1 он опускаясь вместе с тягой 3 и стрелой 8 поднимает рукоять 10 вверх обеспечивая перемещение блока. При стравливании воздуха рукоять опускается вниз.
Рассчитаем конструкцию манипулятора по максимальному грузовому моменту от поднимаемого груза.
Грузовой момент от поднимаемого груза:
М=QL≤[M]=400Нм (2.16)
где Q=Pg – вес поднимаемого груза Н;
L – плечо приложения груза м.
Q=Pg=20698=20188Н (2.17)
М=QL=201880486=9811Нм400Нм (2.18)
Следовательно данная конструкция манипулятора пригодна для перемещения заготовки корпуса.
Т.к. плечи манипулятора равны 360мм и 1800мм то усилие развиваемое пневмоцилиндром больше веса заготовки в 5 раз.
Определим диаметр цилиндра:
Выбираем пневмоцилиндр с односторонним штоком со следующими характеристиками D=50 мм; d=12 мм.
Технико-организационная часть
Спроектируем планировку механического участка по обработке корпуса 503А-8603512-02.
Состав и количество оборудования участка будет следующим:
– станок центровально-подрезной 2А911 – 1 шт.;
– станок вертикально-сверлильный 2Н150 – 1 шт.;
– станок сверлильный с ЧПУ 2Р135Ф2 – 1 шт.;
– станок токарный с ЧПУ 16К20Ф3С32 – 1 шт.
Определим предварительную площадь участка по формуле:
где Спр – принятое количество станков по участку;
Sуd – удельная площадь на один станок; для средних станков –18 22 м2.
Выполняем планировку участка.
Производим расчёт рабочих станочников по формуле:
где Спр – принятое количество станков;
Фо – эффективный годовой фонд времени работы оборудования (в год 4015 часов при 2-х сменном режиме работы);
Кз – коэффициент загрузки;
Ки – коэффициент использования оборудования;
Фр = 1840 часов – эффективный годовой фонд времени рабочего;
Км – коэффициент многостаночности.
Для среднесерийного производства:
КзКи = 085; Км = 13 15.
Число станочников участка принимаем равным 6.
В состав производственных рабочих входят наладчики. Принимаем на 1 смену по 1-му наладчику исходя из количества оборудования значит число наладчиков – 2 человека. Количество работников ОТК принимается 1 человек на 3 6 станков в 1 смену; принимаем по 1-му контролёру ОТК в смену. Количество контролёров ОТК – 2 человека.
Произведем расчет вспомогательных рабочих: ремонтники инструментальщики транспортные рабочие складские – принимаем в количестве 20 25% от производственных рабочих и принимаем 3 человека.
Количество ИТР принимаем в зависимости от количества оборудования; для среднесерийного производства принимаем 22 16%. Принимаем ИТР 1 человек. Определяем количество служащих (бухгалтеры кассиры учётчики) для среднесерийного производства – 0.9 1.9% от общего числа производственных рабочих получаем 1 человек.
Младший обслуживающий персонал (МОП) (уборщики сторожа) принимаем 1 человек.
Произведем описание вспомогательных служб участка.
К вспомогательным службам относятся: инструментальное хозяйство ремонтное хозяйство складское хозяйство эмульсионное хозяйство масляное хозяйство службы по сбору и переработке отходов контрольная служба.
Инструментальное хозяйство в своём составе имеет инструментально-раздаточную кладовую кладовую. Приспособлений и абразивов контрольно-проверочный пункт заточное отделение и мастерскую по ремонту приспособлений и инструмента. Проверка эталонов а также точного сложного инструмента и приспособлений осуществляется в центральной измерительной лаборатории. Заточное отделение занимается эксплуатационной переточкой режущего инструмента за исключением сложного и точного который затачивают в инструментальном цехе.
Мастерская по ремонту приспособлений и инструмента предназначается для производства несложного текущего ремонта приспособлений и инструмента.
В состав ремонтного хозяйства входит мастерская предназначенная для межремонтного обслуживания и производства отдельных ремонтов.
Складское хозяйство состоит из комплекса складов необходимых для обеспечения нормального хода производства. Сюда относятся склады металла заготовок и полуфабрикатов межоперационные склады склады готовых деталей.
Для уборки стружки может иметься в наличии стружкоуборочный конвейер. Для целесообразности его применения произведём расчёт. Расчёт ведём по формуле:
Следовательно применять стружкоуборочный конвейер не будем. Стружка будет собираться в короба и вывозиться из цеха автотранспортом.
На участок заготовки доставляются карой и складируюся в начале участка. Установка и снятие заготовок со станков производится манипулятором т.к. заготовка достаточно тяжелая а перемещение коробов с заготовками между станками производится кран-балкой. После операции 015 заготовки карой доставляются на сварку. После сварки заготовки возвращают на участок. В конце участка складируются готовые детали которые потом отправляют на сборку.
СОЖ передают по трубопроводам из центральной установки к разборным кранам установленным на участках. В процессе работы станка используется автономная система охлаждения станка которая ежесуточно пополняется из разборных кранов для восполнения потерь жидкости вследствие ее разбрызгивания уноса со стружкой и обработанной заготовкой.
Предприятия обеспечиваются электроэнергией от передач напряжением 110кВ. Для понижения напряжения используют следующий каскад: открытая понижающая станция 11035 кВ затем открытые центральные распределительные подстанции 3510-6кВ и цеховые закрытые трансформаторные подстанции 6-100.4кВ. Подстанции приближают к основным потребителям электроэнергии для уменьшения потерь в сети.
При производстве корпуса широко используют сжатый воздух для приводов пневматических зажимных устройств. Давление сжатого воздуха в сети составляет 04 06 МПа. Компрессорные станции размещены в изолированном помещении вследствие высокого уровня создаваемого ими шума.
Исходными данными для составления плана расположения оборудования являются: разработанный проект технологического процесса ведомость требуемого оборудования габариты применяемого оборудования.
При разработке плана учитываем следующее:
) длина пути грузопотоков обрабатываемых деталей должна быть как можно короче;
) следует обеспечить возможность установки демонтирования и транспортировки любого станка;
) иметь в виду возможность многостаночного обслуживания;
) должны быть предусмотрены средства доставки заготовок на участок их погрузки и выгрузки передачи деталей от станка к станку а также средства транспортировки готовых деталей на сборку или склад;
) необходимо предусмотреть средства для уборки стружки от станка транспортировки его по участку;
) должны быть решены вопросы:
- ремонта оборудования; технологической оснастки;
- обеспечение станков смазочно-охлаждающей жидкостью;
- охраны труда и техники безопасности; эстетики чистоты и порядка на участке.
По результатам расчетов с учетом рекомендаций литературы выполняем компоновочный план цеха. Наиболее распространенной конструкцией здания цехов механосборочного производства является здание прямоугольной формы с полом на бетонном основании с системой колонн. Колонны соединены стропильными и подстропильными фермами на которые сверху укладываются перекрытия. Для машиностроения приблизительно 85% зданий являются одноэтажными как более экономичные и не имеющие ограничения по размещению тяжелого оборудования.
Основными параметрами производственных зданий являются:
L – ширина пролета (расстояния между продольными осями колонн образующими пролет);
t – шаг колонн (расстояние между поперечными осями колонн);
При реализации требований к типизации и унификации производственных зданий разработаны производственные помещения габаритами 72x72 м сеткой колонн 24х12 м. И общей площадью 1728 м2.
Поскольку в данном цехе имеются грузовые краны грузоподъемностью 10т то высоту пролета принимаем 84 м.
Расчет технико-экономических показателей обработки детали
Для расчета экономической эффективности вариантов технологического процесса прежде всего необходимо заполнить приведенную ниже таблицу исходных данных.
Таблица 4.1 – Исходные данные для выполнения экономического раздела дипломного проекта (базовый вариант).
Трудоемкость программы выпуска час
вертикально-сверлильная
Подъемно-транспортное оборудование:
- манипулятор – 8 шт.
Годовая программа выпуска – 10 000 штук.
Масса заготовки - 206 кг.
Масса детали - 188 кг.
Производственная площадь участка 176 м2.
Таблица 4.2 – Исходные данные для выполнения экономического раздела дипломного проекта (проектируемый вариант).
центровально-подрезная
Продолжение таблицы 4.2
- манипулятор – 4 шт.
Годовая программа выпуска 10 000 штук.
Производственная площадь участка 88 м2.
1 Определение потребности в материально-технических и трудовых ресурсах
Состав оборудования и дорогостоящей оснастки сведем в 2 таблицы по вариантам базовому и проектируемому.
Таблица 4.3 – Состав оборудования и оснастки (базовый вариант).
Модель оборудо-вания
Количество на программу шт.
Коэффи-циент загрузки оборудо-вания
Мощ-ность приводов кВт
Цена единицы оборудо-вания млн.руб.
Продолжение таблицы 4.3
Таблица 4.4 – Состав оборудования и оснастки (проектируемый вариант).
Количество основных материалов на годовую программу рассчитывается по нормам расхода материалов:
где qн – нормы расхода материалов на одно изделие кг;
Q – годовой объем выпуска продукции Q = 10000шт.
Количество вспомогательных материалов:
Мвсп = qоб. ОП (4.2)
где qоб – нормы расхода материалов на единицу оборудования кг;
ОП – количество принятого производственного оборудования шт.
Мс = 206×10000 = 206000 кг.
Мвсп =435×8 = 3480 кг.
Проектируемый вариант:
Мвсп =435 ×4 = 1740 кг.
Количество производственных рабочих (кроме производственных рабочих автоматических линий и наладчиков-операторов оборудования) определяется по формуле:
где Чр – расчетное количество производственных рабочих;
Тст – трудоемкость механической обработки на годовую программу станко-часы;
Фэ.р – эффективный годовой фонд времени рабочего Фэ.р = 1860 ч;
Кмн – коэффициент многостаночного обслуживания – количество станков обслуживаемых одним рабочим.
Расчеты сведем в таблицы 4.5 и 4.6.
Таблица 4.5 – Количество работающих (базовый вариант)
Таблица 4.6 – Количество работающих (проектируемый вариант)
Число производственных рабочих в первой смене принимаем 55% от общего количества производственных рабочих.
Предусматриваем наличие следующих вспомогательных рабочих:
- базовый вариант: 1 слесарь-механик 1 слесарь-электрик 1 слесарь по общему ремонту 1 смазчик;
- проектируемый вариант: 1 слесарь-механик 1 слесарь-электрик 1 слесарь по общему ремонту 1 смазчик.
Инженерно-технические работники:
- базовый вариант: 1 мастера 1 технолог 1 инженер-нормировщик;
- базовый вариант: 1 мастера 1 технолог 1 инженер-нормировщик.
2 Расчет технико-экономических показателей
Расчет капитальных вложений рассчитываем по следующей формуле:
К = Коб+Кзд+Косн+Кинв+Кмонип+ОбС (4.4)
где Коб – капиталовложения в оборудование (техническое энергетическое подъемно-транспортное средства контроля и управления) млн. руб.;
Кзд – капиталовложения в здание млн. руб.;
Косн – капиталовложения в дорогостоящую оснастку (приспособления штампы модели режущий и мерительный инструмент и тому подобное) млн. руб.;
Кинв – капиталовложения в инвентарь млн. руб.;
Кмонип – капиталовложения в манипуляторы млн. руб.;
ОбС – капиталовложения в запасы материалов (оборотные средства) млн. руб.
Капиталовложения в оборудование:
где h – количество типоразмеров (моделей) оборудования;
mi – значение коэффициента занятости оборудования i-го типоразмера (вида) изготовлением рассматриваемой продукции.
где Тгод – трудоемкость программы выпуска рассматриваемой продукции часгод.;
Тобщ – эффективный годовой фонд времени работы оборудования часгод.
Коб = 12·(14300·018+16400·038+6500·006+14400·05+14400·017+
+5700·012+14300·016+14300·012)=26352 тыс.руб.
Коб = 12·(16500·005+52000·079+6500·006+34000·008)=52146 тыс.руб.
Капиталовложения в здание определяются следующим образом:
Кзд = (Sц + Sтс) mср Цзд (4.6)
где Sц – производственная площадь занимаемая участком цехом м2 ;
mср – средний коэффициент занятости площади при изготовлении рассматриваемой продукции:
Sтс – площадь потребная для размещения транспортных средств и устройств систем управления станков с ЧПУ м2;
Цзд – стоимость 1 м2 площади механического цеха руб.
Кздб = 176×330×021 =12197 тыс.руб.;
Кздп = 88×330×0245 =6970 тыс.руб.
Капиталовложения в дорогостоящую оснастку (Косн) определяются по формуле:
Косн = 01× Коб (4.8)
Коснб = 01×26352=2635 тыс.руб.;
Коснпр = 01×52146=5215 тыс.руб.
Капиталовложения в запасы материалов охватывают вложения в запасы основных комплектующих изделий и рассчитываются следующим образом:
где w – число видов материалов необходимых для производства продукции;
Q – необходимое количество материалов с-го вида на объем выпуска продукции т (шт.- если учитывать количество заготовок);
Дп – длительность рассматриваемого периода дни;
Доб – длительность одного оборота оборотных средств дни;
Доб = (Stшт i ·k) (60 · 24) + Тз (4.10)
где tшт – штучное время выполнения операций технологического процесса мин;
k – коэффициент учитывающий длительность операций связанных с перемещением маркировкой оформлением документов и др. (k = 15 – 25);
Тз – количество дней на которое создается текущий страховой транспортный запасы принимается в зависимости от частоты поставок материалов дн (Тз = 5-30 дн).
Цм.с – оптовая цена заготовок с-го вида с учётом способа их получения (материала) рубт;
kтз.с – коэффициент учитывающий транспортно-заготовительные расходы по приобретению материалов с-го вида.
Коэффициент kтз с может быть принят в первом приближении равным 104 - 108 для основных материалов и 108 - 110 - для вспомогательных материалов.
Определим длительность одного оборота оборотных средств и капиталовложения в запасы материалов для базового варианта:
Найдем те же величины и для проектируемого варианта:
В первом приближении вложения в производственный инвентарь определяются по следующим укрупненным показателям: 1 - 2% от стоимости основного оборудования.
Кинв = 015×Коб (4.11)
Кинвб = 0015×26352 = 395 тыс.руб.;
Кинвпр = 0015×52146 = 782 тыс.руб.
Капиталовложения в манипуляторы:
где ЦБ – балансовая стоимость манипулятора с учетом затрат на доставку монтаж и устройство фундамета (если исходных сведений о таких затратах нет то не более 20% от стоимости оборудования) руб;
n – количество манипуляторов на участке.
Кмонипб=12×8×4500=43200 тыс.руб.;
Кмониппр=12×4×4500=21600 тыс.руб.
Рассчитанные величины сведем в таблицу 4.7.
Таблица 4.7 – Состав капитальных вложений.
Проекти- руемый вариант
Капиталовложения в оборудование
Капиталовложения в здание
Капиталовложения в оснастку
Капиталовложения в запасы материалов (оборотные средства)
Капиталовложения в инвентарь
Капиталовложения в манипуляторы
Капиталовложения – всего
3 Расчет себестоимости продукции
Затраты на материалы:
где w – число видов материалов применяемых при изготовлении изделия;
Цм с – оптовая цена на материал с-го вида с учетом транспортно-заготовительных расходов рубкг;
Мс – потребности в материале с-того вида кг;
Мотх. с – реализуемые отходы материалов с-того вида кг;
Цотх.с – цена отходов материала руб кг.
С= С= 206000·1086–18000·60 = 22264 млн. руб.
Основная заработная плата рабочих-сдельщиков:
С= Тгод·Сз сч· kот·kм (4.14)
где Тгод – суммарная трудоемкость изготовления продукции за год чел.-ч;
Сз сч – средняя часовая тарифная ставка заработной платы в цехе (на участке) рубчел.-ч.;
kот – отраслевой коэффициент kот=12;
kм – коэффициент доплат за многостаночное обслуживание (10-16).
Фонд заработной платы рабочих-повременщиков:
С= nФр· Сз сч·kзан· kот·kм (4.15)
где n– потребное количество рабочих-повременщиков чел.;
Фр – эффективный фонд времени одного рабочего ч;
kзан – коэффициент занятости работника выпуском рассматриваемой продукции (определяется также как mi).
Среднечасовая тарифная ставка рассчитывается как средневзвешенная величина:
где n n n – количество рабочих соответственно I II III разрядов чел.;
С С С – тарифные часовые ставки этих рабочих руб.
СБ = 6826·1028·12·1 = 84 млн. руб.;
СПР = 3801·1048·12·1 = 48 млн. руб.
СБ = СПР = 4·1860·1100·1·12·1 = 98 млн. руб.
Дополнительная заработная плата рабочих:
где kдз – коэффициент учитывающий дополнительную плату с учетом премиальных выплат (принимается от 10 до 50%).
СБ = 84 ·035= 294 млн. руб.;
СПР = 48·035 = 168 млн. руб.;
СБ = СПР = 98·035= 343 млн. руб.
Отчисления на социальное страхование с заработной платы рабочих:
где kсс – коэффициент учитывающий отчисления на социальное страхование.
СБ = (84+294) ·035 = 397 млн. руб.;
СПР = (48+168) ·035 = 227 млн. руб.;
СБ = СПР = (98+343) ·035 = 463 млн. руб.
Годовой фонд заработной платы ИТР и служащих с отчислением на соцстрах находящихся на штатно-окладной системе:
С итрз = С слз = nи · Зм · kзан · (1+kдз) · (1+kсс) (4.19)
где nи – количество работающих определенной специальности чел.;
Зм – месячный оклад работающего определенной специальности рубмес;
kзан – коэффициент занятости работника выпуском рассматриваемой продукции.
С Б = 3·300000 ·12·021·135·135 =41 млн. руб.;
С ПР = 3·300000 ·12·0245·135·135 =48 млн. руб.
Затраты на амортизацию оборудования транспортных средств и дорогостоящей оснастки:
где h – количество моделей оборудования;
На – норма годовых амортизационных отчислений на замену оборудования (транспортных средств и дорогостоящей оснастки) i –го вида.
С= (143·1·(018+016+012)+164·1·038+144·1·(05+017)+65·1·006+
+57·1·012)·1·+45·8·1·= 65млн. руб.;
С=(165·1·005+65·1·006)·1·+(52·1·079+34·1·008)·1·+45·4·1·= =767млн. руб.
Затраты на ремонт оборудования:
С = 008·2635= 21 млн. руб.;
С = 008·5215= 42 млн. руб.
где Стэ – затраты на силовую и технологическую электроэнергию руб;
Ссж – затраты на сжатый воздух руб;
Спар – затраты на пар руб;
Стоп – затраты на топливо руб.
Затраты на силовую и технологическую электроэнергию определяют по следующей формуле:
kод– коэффициент спроса электроэнергии (103 – 107);
kп – коэффициент учитывающий потери в сети (103 – 105);
Цэ – цена 1 кВт.ч электроэнергии рубкВт.ч.
С = (11·727+12·1522+75·255+15·2034+15·674+4·492+11·642+11·480+
+8·15·4015·021)·105·104·200 = 204 млн. руб.;
С = (10·199+10·3056+75·239+37·307+4·15·4015·0245)·105·104·200= 9 млн. руб.
Затраты на сжатый воздух (Ссж) определяют по формуле:
Ссж = Нсж · FдΣ ·kп · Цсж (4.24)
где Нсж – среднечасовая норма расхода сжатого воздуха на один станок (1 3 м3час);
FдΣ –действительный суммарный фонд времени работы оборудования использующего сжатый воздух ч;
kп– коэффициент учитывающий потери сжатого воздуха (равен 15);
Цсж – цена 1 м3 сжатого воздуха рубм3.
СБсж = 2·6826·15·20=041 млн. руб.;
СПсж = 2·3801·15·20=023 млн. руб.
Затраты на приготовление СОЖ(из базового варианта):
СБСОЖ = СПСОЖ =17 тыс.руб.
Затраты на воду для бытовых нужд (Св.б):
Св.б = Нв.б · kзан ·Драб· nΣ ·Цв.б· (4.26)
где Нв.б – норма расхода воды на одного работающего в смену (006м3);
nΣ – количество работающих чел.;
Драб – количество рабочих дней в году;
Цв.б – стоимость 1 м3 воды для бытовых нужд рубм3;
СБв.б = 006 · 9 · 569 ·1360 · 021 = 877 тыс.руб.
СПв.б = 006 · 5 · 569 ·1360 · 0245 = 569 тыс.руб.
Затраты на смазочно-обтирочные (вспомогательные) материалы для оборудования:
– средняя величина затрат на смазочно-обтирочные материалы за год в расчете на единицу оборудования
Оп – количество принятого производственного оборудования i–го вида шт.
С = 250000·8 = 2 млн. руб.;
С = 250000·4 = 1 млн. руб.
Затраты по приспособлениям режущему и мерительному инструменту и прочей оснастке:
Синстр.= 18%·Косн (4.28)
С= 018·264=048 млн. руб.;
С= 018·522=094 млн. руб.
В первом приближении расходы по содержанию зданий и сооружений за год можно принять в процентах от их стоимости:
Ссод. зд.= 2%·Кзд (4.29)
С= 002·122=024 млн. руб.;
С= 002·697= 014 млн. руб.
Затраты на амортизацию зданий и инвентаря:
С = 001·122= 012 млн. руб.;
С = 001·697= 007 млн. руб.
Расходы на охрану труда:
Сохр.тр.= 5%· С (4.31)
С= 005·182=091 млн. руб.;
С= 005·146=073 млн. руб.
На основании произведенных расчетов заполняем таблицы 4.8 4.9 4.10.
Таблица 4.8 – Смета расходов на содержание и эксплуатацию оборудования.
Наименование статей расходов
Проектируемый вариант
Амортизация оборудования транспортных средств и ценного инструмента и приспособлений
Затраты на эксплуатацию оборудования всего
- стоимость вспомогательных материалов;
- основная и дополнительная зарплата вспомогательных рабочих с отчислениями на соцстрах(с учетом уборщиков производственных помещений);
- затраты на энергию для технологических целей;
- затраты по приспособлениям режущему и мерительному инструментам и прочей оснастке.
Затраты на текущий ремонт оборудования и транспортных средств
Таблица 4.9– Смета цеховых расходов.
Содержание аппарата управления цехом (участка) (фонд заработной платы служащих с отчислениями)
Испытания опыты и исследования рационализация и изобретательство
Прочие расходы (3% от суммы затрат пунктов 1-6)
Таблица 4.10 – Калькуляция цеховой себестоимости продукции.
Стоимость основных материалов за вычетом возвратных отходов
Основная заработная плата основных рабочих
Дополнительная заработная плата основных рабочих
Налоги и отчисления в бюджет и внебюджетные фонды с зарплаты производственных рабочих
Расходы на содержание и эксплуатацию оборудования
4 Оценка экономической эффективности варианта технологического процесса
Общая экономическая эффективность проекта оценивается показателем (коэффициентом) характеризующим величину прироста чистой прибыли предприятия на каждый рубль необходимых для получения этой прибыли капиталовложений:
где Пч – чистая прибыль предприятия от реализации годового объема производственных изделий млн. руб.;
К – капиталовложения необходимые для производства годового объема изделий млн. руб.
Как следует из формулы (4.32) для определения коэффициента общей экономической эффективности надо знать размер чистой прибыли которая определяет цель деятельности предприятия по выпуску продукции.
Пч = Q– (С+Ннед+Нпр) (4.33)
где Q – годовой объем выпуска продукции в стоимостном выражении млн. руб.
Q = С+Пбал+ННДС (4.34)
где С – себестоимость годового выпуска продукции млн. руб.;
Пбал – балансовая прибыль по выпускаемой продукции млн. руб.;
где R – реальная или введенная норма рентабельности базового проекта %.
ННДС – сумма налога на добавленную стоимость руб.
где – ставка налога на добавленную стоимость %;
Ннед – сумма налога на недвижимость млн. руб.:
Ннед = (Коб+Кзд) · (4.36)
где Тнед – годовая ставка налога на недвижимость %.
Нпр – сумма налога на прибыль млн. руб.:
где Пнал – прибыль предприятия облагаемая налогом на прибыль млн. руб.;
Тпр – ставка налога на прибыль %.
Пнал = Пбал –Ннед (4.38)
Подставив численные значения в формулы получим:
Пбал Б = 29581· = 7395 млн. руб.
Н=(29581+7395) ·=6656 млн. руб.
QБ = QПР = 29581+7395+6656 = 43632 млн. руб.
Пбал ПР= – 28075 = 8901 млн. руб.
Н= (2635+122) · = 039 млн. руб.;
Н= (5215+697) · = 059 млн. руб.
ПналБ = 7395 – 039= 7356 млн. руб.;
ПналПР = 8901 – 059= 8842 млн. руб.
Н= 7356 · = 1765 млн. руб.;
Н= 8842 · = 2122 млн. руб.
Пч Б = 43632 – (29581+039+1765) = 12247 млн. руб.;
Пч ПР = 43632 – (28075 +059+2122) = 13376 млн. руб.
Таблица 4.11 – Основные технико-экономические показатели проекта.
Наименование показателя
Годовой выпуск продукции:
- в натуральном выражении
- в стоимостном выражении по цене базового предприятия
Общая стоимость основных производственных фондов всего
Производственная площадь цеха (участка)
Продолжение таблицы 4.11
Численность производственных рабочих всего
- основных производственных рабочих
- вспомогательных рабочих
Трудоемкость изготовления единицы продукции
Выпуск продукции на одного производственного рабочего:
- в стоимостном выражении
Фондовооруженность труда
Средняя загрузка оборудования
Цеховая себестоимость годового объема выпуска продукции
Размер чистой прибыли
Абсолютная (общая) эффективность капиталовложений
Охрана труда и окружающей среды
Охрана труда – это система правовых социально-экономических организационных технических санитарно-гигиенических и других мероприятий направленных на обеспечение здоровых и безопасных условий труда на производстве. Создание здоровых и безопасных условий труда полная ликвидация травматизма и профессиональных заболеваний является важнейшей государственной задачей охраны труда в РБ. Она установлена и регулируется Конституцией РБ Трудовым Кодексом и различными правилами и нормами а так же инструкциями по охране труда. Основным законодательным актом который регулирует отношения в области охраны труда для работника и нанимателя независимо от формы собственности и ведомственного подчинения является Трудовой Кодекс РБ.
В целях охраны произведения Трудовой Кодекс возлагает на администрацию предприятия во-первых проведение инструктажа рабочих и служащих по технике безопасности производственной санитарии противопожарной охране и другим правилам охраны труда во-вторых организацию работы по профессиональному отбору и в-третьих осуществление постоянного контроля над соблюдением работниками всех требований инструкции по охране труда. На главного инженера возлагается оперативное руководство организацией инструктажа (обучения) и ответственность за его проведение в целом на предприятии. Непосредственный контроль над своевременным проведением инструктажа осуществляет инженер по охране труда. Начальник цеха и мастер участка несут ответственность за своевременное проведение инструктажа. Инструктажи бывают: вводный первичный на рабочем месте повторный внеплановый целевой. Рабочие и служащие обязаны соблюдать инструкции по охране труда установленные требования обращения с машинами и механизмами а также пользоваться выдаваемыми им средствами индивидуальной защиты.
Одним из необходимых условий здорового и высокопроизводительного труда является обеспечение чистоты воздуха и нормальных условий микроклимата в рабочей зоне помещения. Оптимальные и допустимые значения микроклимата а именно: температуры относительной влажности и скорости движения воздуха устанавливаются согласно ГОСТ 12.1.005-76 «Воздух рабочей зоны. Общие санитарно-технические требования» в зависимости от тяжести выполняемой работы и сезона года. Для обеспечения микроклимата и чистоты воздушной среды участок оборудован приточно-вытяжной вентиляцией которая удаляет загрязненный или нагретый воздух из помещения и подает в него свежий воздух. Источники интенсивных выделений пыли при точении паров при мойке и другие оборудованы устройствами для местных отсосов. Загрязненный воздух перед выбросом в атмосферу очищают с помощью фильтров или специальных устройств (пылеосадочные камеры циклоны ротоклоны). Для подогрева воздуха в холодное время года предусмотрены калориферы.
В производственных условиях не всегда удается устранить все опасные и вредные производственные факторы путем проведения общетехнических мероприятий (устройство вентиляции экранирование источников теплового излучения и др.). В этих случаях применяют средства индивидуальной защиты. Органы зрения защищаются очками не только от механических повреждений но и от теплового излучения. Органы дыхания защищают фильтрующими средствами (респираторы и противогазы). Защита кожи лица шеи и рук при работе с едкими различными веществами осуществляется применением защитных мазей и паст которые наносятся на кожу перед началом работы а по окончании ее легко смываются.
Сохранность зрения человека состояние его центральной нервной системы и безопасность на производстве производительность труда и качество выпускаемой продукции зависят от условий освещения. При освещении производственного помещения (участка) используют естественное создаваемое светом неба и искусственное осуществляемое электрическими лампами освещение. При выполнении слесарной (040) токарных с ЧПУ (010025030) сверлильной с ЧПУ (035) контрольной (045) к общему освещению добавляется местное концентрирующее световой поток непосредственно на рабочих местах (электрические лампы). Для защиты глаз от ультрафиолетового и инфракрасного излучения слепящей яркости видимого излучения на операциях сварки (020) применяют защитные очки щитки шлемы.
Увеличение производительности рост мощностей и быстроходности оборудования при одновременном снижении его материалоемкости сопровождается усилением вибраций. Особенно желательно снизить воздействие вибраций на операциях с ЧПУ (010025030035). Воздействие вибраций не только ухудшает самочувствие работающего и снижает производительность труда но и приводит к виброболезни. Основными методами борьбы с вибрацией машин и оборудования являются: снижение вибраций воздействием на источник возбуждения (посредством снижения или ликвидации вынуждающих сил); отстройка от режима резонанса путем рационального выбора массы или жесткости колеблющейся системы; вибродемпфирование (процессе уменьшения уровня вибрации путем превращения энергии механических колебаний данной колеблющейся системы в тепловую энергию-использование композиционных материалов пластмасс дерева резины полимеров); динамическое гашение колебаний; изменение конструктивных элементов машин; виброизоляция (виброизолирующие опоры типа упругих прокладок или пружин).
На слесарной операции (040) при работе с ручной пневматической шлифовальной машинкой применяют средства индивидуальной защиты рук от воздействия вибраций: рукавицы перчатки виброзащитные прокладки. В целях профилактики вибрационной болезни для работающих с вибрирующим оборудованием рекомендуется специальный режим работы.
Шум на производстве который возникает при механической обработки наносит большой ущерб вредно воздействует на организм человека (ухудшение слуха глухота нарушается процесс пищеварения) вследствие чего снижается производительность. Утомление рабочих и операторов из-за сильного шума увеличивает число ошибок при работе способствует возникновению травм. Для снижения шума используют такие методы как: изменение в конструкции шумообразующего источника; заключение его в изолирующие кожухи; использование глушителей шума при выпуске сжатого воздуха из пневмосистемы (на сверлильных операциях 015035); размещение наиболее мощных источников шума в звукоизолирующих помещениях; использование звукопоглощающей облицовки потолков и стен штучных звукопоглотителей и звукопоглощающих экранов виброизолирующих фундаментов и амортизаторов под оборудование. К средствам индивидуальной защиты от шума относят вкладыши наушники и шлемы.
В связи с тем что при производстве корпуса на всех операциях технологического процесса применяется электричество большое значение уделяется электробезопасности. Основными мерами защиты от поражения током являются:
а) обеспечение недоступности токоведущих частей находящихся под напряжением для случайного прикосновения (изоляция токоведущих частей ограждения);
б) электрическое разделение сети; устранение опасности поражения при появлении напряжения на корпусах кожухах и других частях электрооборудования что достигается применением малых напряжений использованием двойной изоляции защитным заземлением занулением защитным отключением; организация безопасной эксплуатации электроустановок (медосмотр обучение и квалификация);
в) применение специальных электрозащитных средств – переносных приборов и приспособлений (диэлектрические резиновые перчатки инструмент с изолирующими рукоятками диэлектрические галоши и коврики указатели напряжения предупредительные плакаты временные переносные ограждения-щиты).
На участке предусмотрены защитные ограждения возле основного и вспомогательного оборудования и пульты аварийного его отключения.
Так как вес детали «Корпус 503А-8603512-02» равен 188 кг то для установки и снятия её на всех операциях используются манипуляторы. Для обеспечения безопасности эксплуатации манипуляторов применяют: концевые выключатели автоматически отключающие механизмы подъема детали; ограничители грузоподъемности предохраняющие манипулятор от перегрузки путем выключения механизма подъема; звуковую и световую сигнализацию предупреждающую о наступлении аварийной ситуации.
Подробно распишем меры безопасности при работе с манипуляторами используемыми для поднятия корпуса.
К работе допускаются лица не моложе 18 лет закрепленные за механизмом знающие устройство и правила его эксплуатации имеющие навыки по управлению манипулятором и строповки грузов и пошедшие инструктаж по технике безопасности для работы с ним.
Перед началом работы на манипуляторе необходимо:
– проверить исправность труб пневмосети манипулятора;
– при случайном повреждении пневмомагистрали после обратного клапана (свободное истечение воздуха в атмосферу) грузозахватный орган с грузом резко опускается;
– осмотреть наружное состояние механизма;
– осмотреть закрепление противовеса;
– проверить состояние захватного устройства надежность закрепления захвата в блоке управления.
При работе с манипулятором необходимо следить за тем чтобы груз был надёжно закреплен грузозахватным устройством. Запрещается освобождать захват от груза при неполном стравливании воздуха из системы. Для полного стравливания необходимо воздействовать на рукоятку астатического управления вниз.
Запрещается работать с манипулятором при любой его неисправности. Полное техническое освидетельствование манипулятора находящегося в эксплуатации производить один раз в 3 года частичное не реже одного раза в год согласно «Правилам устройства и безопасной эксплуатации грузоподъёмных кранов». При замене несущих расчётных конструкций манипулятора находящегося в эксплуатации проводить внеочередное полное техническое освидетельствование.
Планировка участка выполнена в соответствии с требованиями ГОСТов и СНиПов о безопасном расположении оборудования на участке механической обработки деталей: ширина проходов (проездов) – 4.5 м не менее; расстояние между оборудованием и коробами – 0.3 м не менее; оборудование участка расположено в одну линию на соответствующем расстоянии друг от друга что обеспечивает хороший доступ к станкам рабочих (основных и вспомогательных).
Спроектируем общую систему освещения. (Кноринг Г.М. Справочник для проектирования электрического освещения)
Выбираем тип светильников с учетом характеристик светораспределения по экономическим показателям условиям среды а также с учетом требований взрыво- и пожаробезопасности.
Световой поток ряда ламп (Фл лм) светильников при люминесцентных лампах рассчитывается по формуле:
Фл =Ен·S·z·kзап (n·h)(4.1)
где Ен – нормативная минимальная освещенность лк; выбираем исходя из СНиП II-В.6-59;
S – площадь освещаемого помещения м2 S = 88 м2 (согласно планировки участка);
z – коэффициент минимальной освещенности z = 11 по СНиП II-В.6-59;
kзап – коэффициент запаса для люминесцентных ламп kзап = 15. согласно ГОСТ 6825-61;
n – количество рядов светильников в помещении (принимаем согласно площади участка и минимального практического расстояния расположения рядов светильников между собой – 8);
h – коэффициент использования светового потока ламп зависящих от КПД и кривой распределения силы света светильника высоты подвеса светильников и показателей помещения принимаем h=40 60%.
Фл = 200·88·11·15 (8·045) = 8067 лм.
При расположении в ряду 5-и ламп определяем световой поток одной лампы Фл1:
Фл1 = 8067 5=1613 лм.
По световому потоку Фл = 1600 лм выбираем по ГОСТ 6825-61 стандартную лампу ЛДЦ-80 со световым потоком 1600 лм и световой отдачей 34 лмВт.
2 Охрана окружающей среды
С экологической точки зрения технологический процесс обработки детали корпус передняя является относительно безопасным. На производстве не используются вещества процессы способные нанести значительный ущерб окружающей среде. Однако несоблюдение элементарных правил эксплуатации производственного оборудования применения смазочно-охлаждающих технологических сред (СОТС) может привести к загрязнению окружающей среды ухудшению здоровья рабочих.
Для обеспечения чистоты воздушной среды цех оборудован приточно-вытяжной вентиляцией которая удаляет загрязненный воздух из помещения и подает в него свежий воздух. Источники интенсивных выделений паров при мойке вредных аэрозолей при окраске сварочные кабины и другие оборудованы устройствами для местных отсосов. Загрязненный воздух перед выбросом в атмосферу очищается с помощью фильтров и специальных устройств (пылеосадочные камеры циклоны ротоклоны).
При осуществлении мойки изделий используется водно-щелочной раствор. При этом с деталей удаляется остаток СОЖ стружка. Для уменьшения вредных выбросов используется рециркуляция воды предварительно очищенной в отстойниках и циклонах.
Отработанная СОЖ собирается в специальные емкости при станках. Водная и масляная фаза используется в качестве компонентов для приготовления эмульсий. Масляная фаза эмульсий поступает на регенерацию. Концентрация нефтепродуктов в сточных водах при сбросе их в канализацию должна соответствовать требованиям СНиП 11-32-74. Водную фазу СОЖ очищают до ПДК или разбавляют до допустимого содержания нефтепродуктов и сливают в канализацию. Контроль качества СОЖ на масляной основе производится одного раза в месяц эмульсий – одного раза в неделю синтетических и полусинтетических жидкостей – не реже одного раза в две недели. Не реже одного раза в неделю должен производиться анализ СОЖ на отсутствие микробов вызывающих кожные заболевания. Дополнительный контроль СОЖ должен проводиться при появлении запаха или раздражения рук.
3 Обеспечение безопасности в чрезвычайных ситуациях
Проанализировав используемое оборудование при производстве детали «Корпус 503А-8603512-02» и техпроцесс приходим к выводу что на данном предприятии чрезвычайная ситуация может возникнуть в результате пожара.
Для предотвращения возникновения пожаров большое значение имеет противопожарная профилактика. Она предусматривает ряд мероприятий по предупреждению возникновения пожаров и их ликвидации:
Для пожароопасных цехов на промышленной площади отводят определённые участки и располагают с подветренной стороны по отношению к открытым складам ЛВЖ сжиженные газы и т.п. Внутризаводские дороги должны обеспечивать беспрепятственный удобный проезд пожарных автомобилей к любому зданию. Одна из сторон предприятия должна примыкать к дороге общего пользования или сообщаться с ней проездами.
Эффективное мероприятие в рамках предотвращения пожаров – разделение здания на противопожарные отсеки противопожарными преградами. Они выполняются из несгораемых материалов и не должны иметь проёмов и отверстий через которые могут проникать продукты горения при пожаре.
Для предупреждения распространения пожара с одного здания на другое между ними устраивают противопожарные взрывы величина которых зависит от степени огнестойкости здания.
Эвакуационные выходы должны давать возможность людям безопасно и в короткий срок покинуть помещение в случае пожара. Эвакуационные выходы располагаются рассредоточено и имеют световые указатели с надписью «ВЫХОД». Ширина путей эвакуации – 1 м не менее а дверей на путях эвакуации – 0.8 м не менее.
Удаление дыма из помещений при пожаре производится через оконные проёмы аэрационные фонари а также с помощью специальных дымовых люков легко сбрасываемых конструкций.
При коротком замыкании возможно возникновение пожара поэтому необходимо предусмотреть наличие устройств для выключения оборудования в данном экстренном случае.
Необходимо обеспечить защиту от молнии и защиту от электростатической индукции. Для защиты от электростатической индукции металлические корпуса оборудования присоединяют к защитному заземлению а для защиты от молнии производят монтаж молниеотводов которые в свою очередь состоят из молниеприёмника токоотвода и заземления.
Также необходима установка сигнализации которая обеспечивает подачу полного и быстрого сообщения о пожаре с указанием места и его возникновения.
Соответствующим приказом по предприятию или распоряжением устанавливается порядок проведения противопожарного инструктажа а именно:
– рабочие служащие вновь принятые на работу могут быть допущены к работе только после прохождения первичного противопожарного инструктажа;
– повторный инструктаж проводится не реже 1 раза в год или при переводе с одного участка работы на другой;
– в соответствии с действующим ПУЭ проектируемое производство относиться к категории Д и к зоне класса Б-1а в котором обращаются горючие вещества и материалы в холодном помещении и взрывоопасные смеси не образуются при нормальных условиях эксплуатации. По огнестойкости данное помещение относится к II степени.
Антонюк В.Е. Конструктору станочных приспособлений.: Справочное пособие. - Мн.: Беларусь 1991.
Горбацевич А.Ф. Шкред В.А. Курсовое проектирование по технологии машиностроения. - Мн.: Высшая школа 1983.
Горохов В.А. Проектирование и расчет приспособлений. - Мн.: Высшая школа 1983.
Демиденко Г.П. Защита объектов народного хозяйствования. – Киев: Высшая школа 1987.
Мельников Г.Н. Вороненко В.П. Проектирование механосборочных цехов. - М.: Машиностроение 1990.
Методические указания по выполнению курсового проекта по курсу “Технология машиностроения” для студентов специальности Т 03.01.00. - Брест 1996.
Методические указания по расчету припусков расчетно-аналитическим методом. - Брест 2000.
Справочник технолога - машиностроителя в двух томах.Под ред. Косиловой А.Г. М. Машиностроение 1985г. Т.2.
Г.Н.Кирсанов и др. Руководство по курсовому проектированию металлорежущих инструментов: Учебное пособие для ВУЗов. - М.: Машино-строение 1986.
Проектирование технологических процессов механической обработки в машиностроении: Учебное пособиеПод ред. В.В.Бабук - Мн.: Высшая школа 1978.
Титульник.doc
Учреждение образования
Брестский государственный технический университет
Кафедра технологии машиностроения
РАСЧЕТНО-ПОЯСНИТЕЛЬНАЯ ЗАПИСКА
К ДИПЛОМНОМУ ПРОЕКТУ НА ТЕМУ:
ПРОЕКТИРОВАНИЕ УЧАСТКА МЕХАНИЧЕСКОГО ЦЕХА ПО ИЗГОТОВЛЕНИЮ КОРПУСА 503А-8603512-02
по технологической и
конструкторской части Медведев О.А.
по экономической части Мартиновская О.В.
по охране труда Драган А.В.
Руководитель проекта Медведев О.А.
Контрольная карта, лист2.doc
Контролируемые параметры
Наименование средств ТО
Пробка КГ34’’ 8258-4006
Пробка КГ34’’ 8259-4006
Спецнутромер 8146-345
Приспособление контрольное
Технический контроль
Oперационные карты 1.doc
Наименование операции
Центровально-подрезная
Сталь 35 ГОСТ8731-87
Оборудование устройство ЧПУ
Обозначение программы
Эмульсол ЭМ-1 ТУ РБ 00203358.007-97
При выполнении операции соблюдать инструкцию по охране труда №22
Установить и закрепить заготовку
Приспособление подрезное специальное
Подрезать и центровать одновременно два торца выдерживая размеры 533-1752х300
Зенкер торцовый 2321-5185-01; ножи 2020-5096 Т15К10
Штангенциркуль ШЦ-II-250-630-01 ГОСТ 166-89
ГОСТ 3.1404-86 Форма 2
При выполнении операции соблюдать инструкцию по охране труда №145
Установить и закрепить заготовку в патроне и поджать задним центром
Патрон 7102-0072 ГОСТ 24351-80 центр 7032-0035 Морзе 5 ГОСТ 13214-79
Точить поверхность 145 начерно
Державка 9412-2265 резец К01.4933.000-21 пластина 02114-120612 Т15К6
Точить поверхность 144-016
Скоба 144-016 05523-581
ГОСТ 3.1487-82 Форма 5
Оборудование устр-во ЧПУ
Кодирование информации содержание кадра
- режимы резания выбор инструмента
- быстрый подвод резца
- наружная обработка с автоматическим отскоком и возвратом на быстром ходу в нач.точку
Для разработки управляющих программ
Вертикально-сверлильная
При выполнении операции соблюдать инструкцию по охране труда
Установить и закрепить заготовку в кондукторе
Зенковать две поверхности выдерживая размеры 6+02 35-062 62+04 92±03 последовательно
Стойка поворотная 9673-1642 зенковка 9348-446
Штангенглубиномер ШГ-160 ГОСТ 162-90
Установить и закрепить заготовку в приспособлении
Приспособление 9675-3875
Зенкеровать отверстие 127+012
Зенкер 9346-735 Т14К8
Нутромер НИ100-160-1 ГОСТ 868-82
Раскатать отверстие 127+016
Точить поверхность 13985-012 выдерживая размер 28+2
Резец К-01-4912-000-06 ТУ 02-035-892-82
Пластина 4-х гр. 03114-120408 Т15К6 ГОСТ 19052-80
Скоба 13985-012 05523-457 штангенглубиномер ШГ-160 ГОСТ 162-90
ГОСТ 3.1404-86 Форма 2а
Нарезать резьбу М140х15-6g
Резец К-01-4904-0008 ТУ 02-035-884-82
Пластина 04112-080400 Т15К6 ГОСТ 19055-80
Кольцо 0212-0293 6g ГОСТ 17765-72 кольцо 8212-0293 6g ГОСТ 17765-72
- цикл глубинного сверления
- цикл черновой обработки
- задание контура обработки
- цикл чистовой обработки
L01F15W-28X140A0C0P05
- цикл нарезания резьбы
Оправка цанговая 967-1245 люнет ПЦ 1326
Зенкеровать 2 отверстия выдерживая размеры 130+016 132+016 415+20 одновременно
Зенкер ступенчатый Т14К8
Расточить 4 канавки выдерживая размеры 26+025 137+053 8±02 3+025 131+10 18+014 3+025 133+10 175±02 R25+012
2+026 68-074 последовательно
Державка 9415-170 резцы канавочные Т15К6
Калибр 18+014 8423-6093 калибр 26+025 8154-6226 спецнутромер 8146-7654
Расточить фаску 1х450 в отверстии 132
Штангенциркуль ШЦ-I-125-01-2 ГОСТ 166-89.
- цикл точения канавки
- точение внутренней фаски
При выполнении операции соблюдать инструкцию по охране труда №113
Приспособление 9671-10715
Сверлить отверстие насквозь выдерживая размеры 2275 93±11
Патрон 04740-5 втулка 04740-2
Сверло 2275 2301-0077 ГОСТ 10903-77
Развернуть коническое отверстие под резьбу КГ34”
Патрон 04740-5 втулка 9464-174
Развертка коническая 2373-0036
Зенковать фаску 2х450 в отверстии КГ34”
Зенковка 2354-0136 ГОСТ 14953-80
Нарезать резьбу КГ34”
Патрон 04740-5 втулка 9472-77
Метчик КГ34” 2680-4055
Пробка КГ34” 8258-4006 пробка КГ34” 8259-4006
- отмена постоянного цикла абсолютные координаты подача ммоб выбор инструмента
- режимы резания направление вращения смена инструмента
- смещение начала координат относительно трех осей
- задание коррекции для инструмента №1
- быстрое позиционирование
- постоянный цикл формальный параметры цикла
-отмена постоянного цикла отмена коррекции инструмента выбор инструмента
- задание коррекции для инструмента №2
- задание коррекции для инструмента №3
- задание коррекции для инструмента №4
-отмена постоянного цикла отмена коррекции инструмента
Комплект документов(титульник).DOC
Министерство образования Республики Беларусь
Брестский государственный технический университет
Кафедра технологии машиностроения
на технологический процесс изготовления детали:
«Корпус 503А-8603512-02»
Контрольная карта, лист1.doc
Наименование марка материала
Сталь 35 ГОСТ8731-87
Наименование оборудования
Стол контрольный Р684
Контролируемые параметры
Наименование средств ТО
Образец шероховатости 32-Р
Образец шероховатости 125-РПЦ
Нутромер НИ100-160-1 ГОСТ 868-82
Кольцо 8212-0293 6g ГОСТ 17765-72
Кольцо 8212-1293 6g ГОСТ 17765-72
Технический контроль
ГОСТ 3.1302-85 Форма 2
Маршрутная карта.DOC
Сталь 35 ГОСТ8731-87
Код наименования операции
Обозначение документа
Код наименования оборудования
Доставить заготовку в цех
Центровально-подрезная
Вертикально-сверлильная
ГОСТ 3.1118-82 Форма 1а
Наименование детали сб. единицы или материала
Рекомендуемые чертежи
- 08.01.2024
- 02.06.2021