Проектирование участка для механической обработки детали Корпус




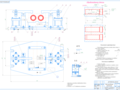
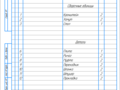
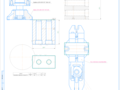
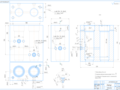
- Добавлен: 24.01.2023
- Размер: 2 MB
- Закачек: 1
Описание
Проектирование участка для механической обработки детали Корпус
Состав проекта
![]() |
![]() |
![]() |
![]() ![]() ![]() |
![]() |
![]() ![]() ![]() |
![]() ![]() ![]() ![]() |
![]() |
![]() ![]() ![]() ![]() |
![]() |
![]() ![]() ![]() ![]() |
![]() ![]() ![]() ![]() |
![]() ![]() ![]() |
![]() ![]() ![]() ![]() |
![]() |
Дополнительная информация
ОК_Корпус.doc
Наименование операции
0 Продольно-фрезерная
Сталь 20ГСЛ ГОСТ 977-88
Оборудование устройство ЧПУ
Обозначение программы
мм мм мм - мммин обмин ммин мин
Установить деталь закрепить
ВИ Приспособление станочное
Фрезеровать поверхность в размер 243-1
РИ Фреза 2214-0061 ГОСТ 9473-80 ВИ Оправка 6220-0128 ГОСТ 13042-83 СИ Штангенглубиномер ШГ-250-005 ГОСТ 162-80
Переустановить деталь закрепить
Фрезеровать поверхность в размер 240-029
РИ Фреза 2214-0061 ГОСТ 9473-80 ВИ Оправка 6220-0128 ГОСТ 13042-83
СИ Штангенглубиномер ШГ-250-005 ГОСТ 162-80
Фрезеровать поверхность в размер 223-1
Фрезеровать поверхность в размер 200-029
Фрезеровать поверхность в размер 123-1
Фрезеровать поверхность в размер 120-022
Открепить деталь снять.
0 Сверлильно-фрезерно-расточная с ЧПУ
мм мм мм - ммоб обмин ммин мин
ВИ Приспособление специальное
Расточить отв.50+064 напроход выдержав размер 60±03
РИ Резец Iscar IHFF40 Пластина Iscar TPGX 110304L
ВИ Головка расточная Iscar BHF MB50 125x114 Удлинитель Iscar EX 50x200 MB50 Оправка Iscar CATM 50 MB50
СИ Штангенциркуль ШЦ-I-005-250 ГОСТ 166-89
Расточить отв.60+064 в размер 230±0575
ГОСТ 3.1418-82 Форма 2а
Расточить отв.60+0046 в размер 230±0575
СИ Штангенциркуль ШЦ-I-005-250 ГОСТ 166-89 Калибр пробка Н8 8133-1104 ГОСТ 14812-69
Расточить отв.69+064 в размер38±031
Расточить отв.70+012 в размер38±031
Полировать отв.60 на длине 210
РИ Круг войлочный полировальный
ВИ Оправка специальная
СИ Образцы шероховатостей по ГОСТ 9378-93
Обработать второе отверстие повторив переходы 1-7 выдержав размер 100±04
0 Вертикально-сверлильная с ЧПУ
Центровать 6 отверстий по программе
РИ Сверло 2317-0105 ГОСТ 14952-7
ВИ Патрон 20-В10 ГОСТ 8522-79 Втулка 50-1 ГОСТ Р 505160-92
Сверлить 4 отв. 139 на глубину 28+1
РИ Сверло 2300-6397 ГОСТ 10902-77
Зенковать 4 фаски 2х45
РИ Зенковка 2353-0103 ГОСТ 14953-80
Нарезать резьбу М16-7Н в 4 отв. на глубину 20
РИ Метчик 2621-1617 ГОСТ 3266-81
СИ Пробка 8221-3067 7Н ГОСТ 17758-72
Сверлить 2 отв.10 до расточенных отверстий
РИ Сверло 2300-3479 ГОСТ 10902-77
Зенкеровать 2 отв.16Н12
РИ Зенкер 2320-2572 ГОСТ 12489-71
ВИ Патрон 20-В10 ГОСТ 8522-79 Втулка 50-1 ГОСТ Р 505160-92 СИ Калибр пробка Н12 8133-0930 ГОСТ 14812-69
Зенкеровать 2 отв.22Н12
РИ Зенкер 2320-2585 ГОСТ 12489-71
ВИ Патрон 20-В10 ГОСТ 8522-79 Втулка 50-1 ГОСТ Р 505160-92
СИ Калибр пробка Н12 8133-0936 ГОСТ 14812-69
Зенковать 2 фаски 15х45
Открепить деталь снять
5 Вертикально-сверлильная с ЧПУ
Центровать 4 отверстия по программе
РИ Сверло 2317-0105 ГОСТ 14952-75
Сверлить 2 отв. 139 на глубину 28+1
Зенковать 2 фаски 2х45
Сверлить отв.10 на глубину 130+5
Зенкеровать отв.16Н12
Зенкеровать отв.22Н12
Зенковать фаски 15х45
Сверлить отв. 5 на глубину 30+2
РИ Сверло 2300-0174 ГОСТ 10902-77
Центровать отверстие по программе
Сверлить отв. 5 на глубину 30
Центровать 2 отверстия по программе
Сверлить 2 отв. 84+03 од резьбу М10 на глубину 30+1
РИ Сверло 2300-3447 ГОСТ 10902-77
Сверлить 2 отв. 15+043 на глубину 6+03
РИ Сверло 2300-6411 ГОСТ 10902-77
Нарезать резьбу М10-7Н в 4 отв. на глубину 20+1
РИ Метчик 2621-1433 ГОСТ 3266-81
СИ Штангенциркуль ШЦ-I-005-250 ГОСТ 166-89 Пробка 8221-3044 7Н ГОСТ 17758-72
Открепить деталь снять.
Сверлить 4 отв. 139 на глубину 28+2
МК_Корпус.doc
МО1 Сталь 20ГСЛ ГОСТ 977-88
Код наименование операции
Обозначение документа
Код наименование оборудования
0 Продольно-фрезерная ИОТ №34-2004
Г606Ф1 18632 4 1 1 1 1 23 14046
5 Слесарная ИОТ №43 - 2004
0 Сверлильно-фрезерно-расточная с ЧПУ ИОТ №78-2000
06ВМФ4 18217 6 1 1 1 1 23 3798
0 Вертикально-сверлильная с ЧПУ ИОТ №69-2005
Р135Ф4 19456 5 1 1 1 1 23 843
Наименование детали сб. единицы или материала
5 Вертикально-сверлильная с ЧПУ ИОТ №69-2005
Р135Ф4 19456 5 1 1 1 1 23 927
Р135Ф4 19456 5 1 1 1 1 23 522
Р135Ф4 19456 5 1 1 1 1 23 811
Р135Ф4 19456 5 1 1 1 1 23 762
5 Контрольная ИОТ №58 – 2004 №89-2002
_Наладки_2.cdw

Вертикально-сверлильная с ЧПУ
Оборудование вертикально-сверлильный с ЧПУ
Сверло 2317-0105 ГОСТ 14952-75
Зенкер 2320-2572 ГОСТ 12489-71
Зенкер 2320-2585 ГОСТ 12489-71
Метчик 2621-1617 ГОСТ 3266-81
Зенковка 2353-0103 ГОСТ 14953-80
Сверло 2300-3479 ГОСТ 10902-77
Удлинитель Iscar EX 80x200 MB80
Головка расточная Iscar
Оправка Iscar CATM 50 MB80
Оборудование продольно-фрезерный
двухстоечный станок 6Г606Ф1
Сверлильно-фрезерно-расточная
Оборудование сверлильно-фрезерно-расточной с ЧПУ
Тисы станочные эксцентриковые
Фреза 2214-0061 ГОСТ 9473-80
Сверло 2300-6397 ГОСТ 10902-77
Расчетно-технологические
Техпроцесс изготовления
Корпуса гидромеханизма
_Корпус_.cdw

Неуказанные предельные отклонения размеров: H14
На поверхности В" допускается наличие 2-х технологических
СП_Присп.spw

Болт М10 х 35 ГОСТ 7798-70
Винт М6 х 14 ГОСТ 1491-80
Гайка М10 ГОСТ 5915-70
Ось 6-14 х 40 ГОСТ 9650-80
Ось 6-14 х 65 ГОСТ 9650-80
Шайба 10 Н ГОСТ 6402-70
Шайба 14 ГОСТ 9649-78
Шайба 10 ГОСТ 11371-78
Шпилька М10 х 25 ГОСТ 22032-76
Шплинт 4 х 25 ГОСТ 397-79
Штифт 5 х 36 ГОСТ 3129-70
Пневмоцилиндр 80х100
_Д_План цеха проектный_2.cdw

расстояний оборудования от проезда относительно друг друга
стен и колонн здания разработаны с учетом оргоснастки на основании типовых проектов
организации рабочих мест и требований ГОСТ 12.3.020-80 Процессы перемещения грузов
на предприятиях. Общие требования безопасности.
механической обработки
Техпроцесс изготовления
Корпуса гидромеханизма
Ведомость оборудывания и объектов участка цеха
ПОДВОД СЖАТОГО ВОЗДУХА
ПОДВОД СРЕДСТВ ОХЛАЖДЕНИЯ
ПОДВОД ЭЛЕКТРОЭНЕРГИИ
КОНТЕЙНЕР ДЛЯ СТРУЖКИ
_Зап_корпус_Дип_3.doc
ПЛАНИРОВКА УЧАСТКА48
ОРГАНИЗАЦИОННАЯ ЧАСТЬ54
КОНСТРУКТОРСКАЯ ЧАСТЬ (ПРОЕКТИРОВАНИЕ СТАНОЧНОГО ПРИСПОСОБЛЕНИЯ)64
ЭКОНОМИЧЕСКАЯ ЧАСТЬ81
БЕЗОПАСНОСТЬ ЖИЗНЕДЕЯТЕЛЬНОСТИ94
В рамках проекта будет рассматриваться деталь «Корпус».
Для детали будет проведён анализ технологичности который позволит оценить её технологичность т.е. возможность рациональной обработки с помощью стандартных инструментов и на существующем оборудовании.
Расчёт коэффициента закрепления операции позволит определить тип производства выбрать соответствующее оборудование способ получения заготовки режущий вспомогательный мерительный инструмент и определить характерный для данного типа производства составы и последовательности выполнения операций.
Будет произведен и проанализирован выбор технологических баз и последовательности обработки заготовки
В проекте будет произведен выбор типа приспособления его расчет на точность усилие зажима и расчет слабого звена на прочность.
В экономической части проекта будет посчитана себестоимость изготовления детали.
Результатом работы будет оформление технологической (маршрутная карта операционная карта карта эскизов маршрут обработки наладки) и конструкторской документации (чертеж детали сборочный чертеж приспособления наладки) согласно ЕСТД и ЕСКД.
1 Анализ исходных данных.
Корпусные детали машин представляют собой базовые детали на них устанавливают различные детали и сборочные единицы точность которых должна обеспечиваться в процессе работы машины под нагрузкой. В соответствии с этим корпусные детали должны иметь требуемую точность обладать необходимой жесткостью и виброустойчивостью.
Деталь «Корпус» гидравлического механизма представляет собой тело прямоугольной формы со сквозными отверстиями и служит для перемещения плунжеров. Относится к типу корпусных деталей
Чертеж детали удовлетворяет всем требованиям предъявляемым стандартами. Он содержит всю необходимую информацию для изготовления контроля. Количество необходимых видов проекций разрезов и сечений достаточно. Технические требования к точности размеров формы и взаимного расположения а также данные о материале шероховатости поверхности и весе детали присутствуют.
Исполнительные поверхности корпуса и их взаимное расположение должны быть выполнены с такой степенью точности чтобы обеспечивать бесперебойную работу гидросистемы в течение всего срока его эксплуатации в соответствии с техническими требованиями к изделию.
Программа выпуска по заданию составляет 2950 штгод.
2 Анализ технических требований к детали
Для разработки технологического процесса представлены: рабочий чертёж детали с техническими требованиями определяющими конструктивные формы и размеры детали точность и качество обработки твёрдость материал и т.п.
Материал детали – Сталь 20ГСЛ ГОСТ 977-88.
Химический состав механические и физические свойства приведены в таблицах ниже.
3 Анализ технологичности детали
Деталь «Корпус» по конструкции относится к классу корпусов. Жесткость детали позволяет применять высокопроизводительные методы обработки с обеспечением требуемой точности. Отсутствие труднодоступных мест для обработки позволяет использовать прогрессивный режущий инструмент. Возможно совмещение конструкторских и технологических баз.
Основные поверхности детали и способы их обработки
Наименование поверхности размеры мм
отверстий резьбовых М16-7H
Резьбонарезание метчиком
отверстия резьбовых М10-7H
Чистовое растачивание
Продолжение таблицы 1
Черновое растачивание
Указанные на чертеже допускаемые отклонения размеров классы шероховатости поверхности позволяют вести чистовую обработку на станках нормальной точности. Технические требования соответствуют назначению детали. Для контроля допусков на радиальное биение поверхностей следует спроектировать контрольное приспособление. Остальные обрабатываемые поверхности с точки зрения точности и чистоты не представляют значительных трудностей. Для обеспечения точности взаимного расположения поверхностей просверлим 2 технологических отверстия на поверхности 4.
Рабочий чертёж содержит все необходимые сведения дающие полное представление о детали и однозначно объясняют её конфигурацию и возможные способы получения заготовки указанны все размеры с необходимыми допусками классы чистоты обрабатываемых поверхностей допускаемые отклонения от правильных геометрических форм а так же взаимное расположение поверхностей чертеж содержит все не обходимые сведения о материале и весе детали простановка линейных размеров обеспечивает минимальное количество операций. Имеются четкие границы между чисто обработанными поверхностями и менее чисто обработанными. Конструкция и материал детали позволяют применять высокопроизводительное оборудование.
Шероховатость обрабатываемых поверхностей соответствует их точности и не требует дополнительных технологических операций.
Возможно применение стандартного режущего и мерительного инструмента. Заданные размеры доступны для контроля.
Технологическая часть
1 Расчеты по объёму выпуска и определение типа производства
В дипломном проекте принимаем пятидневную рабочую неделю с двумя выходными днями при двухсменной работе длительностью 41 час.
Годовой фонд времени работы оборудования определяется исходя из следующих данных:
а)календарных дней в году - 365;
б)продолжительность рабочего дня - 415=8.2 часа;
в)рабочих дней в году - 365-(52*2)-8=253 дня;
Действительный годовой фонд времени работы оборудования:
Металлорежущих станков4015 ч.
Рабочих мест без оборудования4075 ч.
Действительный годовой фонд времени рабочего Рдр=1860 ч.
Продолжительность отпуска 15 дней.
Программа выпуска в год В = 2950 шт.
месячный выпуск Вм = В12; Вм = 295012 = 2458Принимаем 246 шт.
суточный выпуск Вс = Вм22; Вс = 24622 = 112Принимаем 12 шт.
Для предварительного определения типа производства удобнее пользоваться следующей таблицей.
Таблица 2 - Зависимость типа производства и объема выпуска (шт.) и массы детали
При массе детали 40 кг и программе выпуска N=2950 шт.год можно предположить что тип производства будет крупносерийным.
Типы производства характеризуются следующими значениями коэффициентов закрепления операций:
Тип производства K30 ;
Крупносерийное - Св. 1 до 10;
Среднесерийное - Св. 10 до 20;
Мелкосерийное - Св. 20 до 40;
Единичное Св. - 40.
Конфигурация детали позволяет в качестве заготовки использовать отливку в металлические формы по ГОСТ 26645-85 или отливку в песчано-глинистые формы по ГОСТ 26645-85.
Рассмотрим характеристики вариантов получения заготовки.
) отливка в металлические формы по ГОСТ 26645-85
Рассмотрим данный способ для механизированного серийного производства.
Технологический процесс литья: литье под давлением в металлические формы;
Класс размерной точности отливки 8т;
Степень коробления элементов отливки 4;
Степень точности поверхностей отливки 9;
Шероховатость поверхностей отливки Ra 125;
Класс точности массы отливки 5т;
Ряд припусков на обработку отливки 5;
Обозначение точности отливки 8т-4-9-5т ГОСТ 26645-85
Таблица 3 - Припуски и допуски назначенные на поверхности детали по ГОСТ 26645-85 для отливки в оболочковые формы
Допуск на размер (мм)
Шероховатость Ra (мкм)
Припуск на сторону (мм)
Размер заготовки (мм)
Мд - масса детали = 40 кг.
Коэффициент использования материала КИМ = МдМотлм
) отливка в песчано-глинистые формы по ГОСТ 26645-85.
Технологический процесс литья: литье в песчано-глинистые формы из смесей с влажностью от 28% до 35% и прочностью от 120 до 160 кПа со средним уровнем уплотнения до твердости не ниже 80 единиц;
Класс размерной точности отливки 9т;
Степень точности поверхностей отливки 15;
Шероховатость поверхностей отливки Ra 50;
Класс точности массы отливки 15;
Ряд припусков на обработку отливки 9;
Обозначение точности отливки 9т-4-15-15 ГОСТ 26645-85
Таблица 4 - Припуски и допуски назначенные на поверхности детали по ГОСТ 26645-85 для отливки в песчано-глинистые формы
Коэффициент использования материала КИМ = МдМотлп
Результаты расчета по выбору варианта заготовки сводим в таблицу 5.
Таблица 5 - Сравнительная таблица натуральных показателей заготовок
отливка в металлические формы
отливка в песчано-глинистые формы
Вес заготовки на программу кг
Вес деталей на программу кг
Вес отходов на программу кг
Вес отходов на деталь кг
Коэффициент использования материала
Экономическое обоснование выбора заготовки
Стоимость отливки в металлические формы
Sом = (Cом1000·Мотлм·Кт)–(Мотлм – Мд)·Сотх1000 где
Сом = 27000 руб.- цена 1 тн отливки
Мотлм - масса заготовки Мотлм =469 кг.
Кт- коэффициент транспортных расходов Кт=13
Мд -масса детали Мд =40 кг
Сотх -стоимость отходов Сотх=1600 руб. за 1тн
Sом =(270001000·469·13) – (469–40)·16001000 =1635 руб.
Стоимость отливки в песчано-глинистые формы
Sоп= (Cоп1000·Моп·Кт)–(Мпок – Мд)·Сотх1000 где
Спок = 25000 руб.- цена 1 тн отливки
Мотлп - масса заготовки Мотлп =516 кг.
Sпок =(250001000·516·13) – (516–40)·16001000 =1 658 руб.
Отсюда следует что экономически выгодно применять в качестве заготовки отливку в металлические формы.
Результаты расчетов представим в таблице 6.
Таблица 6 - Сравнительная таблица стоимостных показателей заготовок
Наименование показателей
Стоимость материала за 1т руб.
Стоимость 1т. отходов руб.
Стоимость одной заготовки руб.
Стоимость заготовок на программу руб.
Стоимость отходов на программу руб
Экономический эффект на одну деталь руб.
3. Выбор технологических баз
Базирование - придание заготовке или изделию требуемого положения относительно выбранной системы координат.
Согласно теоретической механике требуемое положение или движение твердого тела относительно выбранной системы координат достигается наложением геометрических или кинематических связей.
Общая классификация баз
Все многообразие поверхностей деталей сводится к четырем видам:
) исполнительные поверхности - поверхности при помощи которых деталь выполняет свое служебное назначение;
) основные базы - поверхности при помощи которых определяется положение данной детали в изделии;
) вспомогательные базы - поверхности при помощи которых определяется положение присоединяемых деталей относительно данной;
) свободные поверхности - поверхности не соприкасаемые с поверхностями других деталей.
Конструкторская база - база используемая для определения положения детали или сборочной единицы в изделии.
Основная база - конструкторская база принадлежащая данной детали или сборочной единице и используемая для определения ее положения в изделии.
Вспомогательная база - конструкторская база принадлежащая данной детали или сборочной единице и используемая для определения положения присоединяемого к ним изделия.
Технологическая база - база используемая для определения положения заготовки или изделия в процессе изготовления или ремонта.
Измерительная база - база используемая для определения относительного положения заготовки или изделия и средств измерения.
Исходя из определений можно сделать следующие выводы:
Основными базами детали являются плоскости основания.
Вспомогательными базами являются отверстия под установку отверстия под крепеж.
После черновой обработки установочных поверхностей (базирование в координатный угол) и обработки отверстий в основании наиболее оптимальным представляется базирование в координатный угол так как в этом случае конструкторские технологические и измерительные базы совпадают.
На фрезерных вертикально-сверлильных и расточной операции базирование осуществляем на плоскость в координатный угол.
4 Последовательность обработки заготовки. Сравнение вариантов
При проектировании маршрута обработки определяется последовательность обработки всех поверхностей детали не решая вопросов о способах и средствах обработки. Порядок механической обработки отдельных поверхностей зависит от требуемой точности размерных связей между ними и выбранной схемы базирования. При этом процесс разделяется на черновую и чистовую обработку что вызвано техническими требованиями обеспечения точности размеров относительного положения и качества поверхностей детали.
Каждая проектируемая технологическая операция должна решать конкретную задачу: удалить наибольший слой металла с обрабатываемой поверхности (черновая обработка) или получить более точные размеры и взаимное расположение поверхностей (чистовая обработка) или добиться высокой точности и качество обрабатываемой поверхности (отделочная обработка).
Таблица 7 - Планы обработки наиболее точных поверхностей
Размер после обработки
Получистовое растачивание
Продолжение таблицы 7
Резьбовое отверстие М10-7Н
Резьбовое отверстие М16-6Н
Таблица 8 - Базовый маршрут обработки детали
Наименование операции
Вертикально-фрезерная
Координатно-расточная
Продолжение таблицы 8
Таблица 9 - Проектный маршрут обработки детали
продольно-фрезерный станок 6Г606Ф1
0 Продольно-фрезерная
Фрезеровать поверхность в размер 243-1
Фрезеровать поверхность в размер 240-029
Фрезеровать поверхность в размер 223-1
Фрезеровать поверхность в размер 200-029
Фрезеровать поверхность в размер 123-1
Фрезеровать поверхность в размер 120-022
сверлильно-фрезерно-расточной с ЧПУ станок 2206ВМФ4
0 Сверлильно-фрезерно-расточная с ЧПУ
Расточить отв.50+064 напроход
Расточить отв.60+064 в размер 230±0575
Расточить отв.60+0046 в размер 230±0575
Расточить отв.69+064 в размер38±031
Расточить отв.70+012 в размер38±031
Полировать отв.60 на длине 210
Продолжение таблицы 9
вертикально-сверлильный с ЧПУ
0 Вертикально-сверлильная с ЧПУ
Центровать 6 отверстий по программе
Сверлить 4 отв. 139 на глубину 28
Зенковать 4 фаски 2х45
Нарезать резьбу М16-7Н в 4 отв. на глубину 20
Сверлить 2 отв.10 до расточенных отверстий
Зенкеровать 2 отв.16Н12
Зенкеровать 2 отв.22Н12
Зенковать 2 фаски 15х45
5 Вертикально-сверлильная с ЧПУ
Центровать 4 отверстия по программе
Сверлить 2 отв. 139 на глубину 28
Зенковать 2 фаски 2х45
Сверлить отв.10 на глубину 130
Зенкеровать отв.16Н12
Зенкеровать отв.22Н12
Зенковать фаски 15х45
Сверлить отв. 5 на глубину 30
Центровать отверстие по программе
Центровать 2 отверстия по программе
Сверлить 2 отв. 84+03 под резьбу М10 на глубину 30+1
Сверлить 2 отв. 15+043 на глубину 6+03
Нарезать резьбу М10-7Н в 4 отв. на глубину 24+1
5 Расчёт режимов резания
Фрезерование плоскостей.
К режиму резания при плоском фрезеровании торцом фрезы относятся: диаметр фрезы D число зубьев z глубина резания t скорость подачи sм частота вращения n и время резания до смены инструмента Т.
Глубина резания. Глубина резания равна припуску на обработку:
Скорость подачи. Скорость подачи sм рассчитывается по формуле:
где sм – минутная подача мммин;
s0 – подача на один оборот фрезы ммоб;
n – число оборотов фрезы обмин;
sz – подача на зуб фрезы ммзуб;
z – число зубьев фрезы.
Принимаем по справочнику sz =02 ммзуб.
Скорость резания определяется по формуле
B – ширина фрезерования мм;
Т – стойкость инструмента мин;
D– диаметр фрезы мм;
z – число зубьев фрезы;
Kv – коэффициент определяемый по формуле
где Кmv – коэффициент учитывающий качество обрабатываемого материала;
Кnv – коэффициент учитывающий состояние поверхности заготовки;
Киv – коэффициент учитывающий материал инструмента.
Частота вращения фрезы определяется по формуле
По паспорту станка принимаем ближайшее значение числа оборотов инструмента nф=200 (обмин).
Уточняем фактическую скорость резания по формуле
Сила резания при фрезеровании определяется по формуле:
Обрабатываемый материал
Таблица 13 - Данные для расчета Pz
Крутящий момент на шпинделе (Нм) определяется по формуле
Мощность резания эффективная (кВт) определяется по формуле
sм= szzn=0224200=960 (мммин)
Таблица 14 - Режимы резания при фрезеровании
Значение эффективной мощности резания не превышает мощности привода главного движения станка следовательно процесс резания осуществим.
Сверлильные переходы
Сверление центровочное
Назначаем подачу при диаметре сверла 25 мм.
Рекомендуемая скорость резания - 15-25 (ммин).
Назначаем Vтаб = 15 (ммин).
Км – коэффициент обрабатываемости.
Км = 056 при НВ ≤220.
Vрас = 15 056 = 84(ммин).
Определяем число оборотов сверла.
Nрас = 1000 Vрас ( D) = 100084 31425=668 (обмин).
Ближайшее станочное значение оборотов шпинделя 630 800.
Принимаем Nф = 630 (обмин).
Vф = D Nф1000 = 314256301000 = 79 (ммин).
Крутящий момент при сверлении рассчитывается по формуле:
СM=39 D=25 мм s=002 ммоб y=08; kM==122
Эффективная мощность при сверлении определяется по формуле:
Полученное значение мощности не превышает мощность привода главного движения станка. Процесс резания на данных режимах осуществим.
Предварительное сверление отверстий 10.
Сверло из быстрорежущей стали Р6М5.
Sо = 0.2 (ммоб) (12. т.2. табл. 4.25.)
Стойкость инструмента:
T =Tтабл.×kT=75×1.8=135 мин; (13. т.2. табл. 4.30. табл. 4.7.)
Скорость резания ммин.:
Kmv=1.0;(10. т.2. табл. 4.1.)
Kиv=1.0; (10. т.2. табл. 4.5.)
K (10. т.2. табл. 4.31.)
Частота вращения шпинделя определяется по формуле:
По паспорту станка принимаем n=800 обмин.
Фактическая скорость резания:
Мкр=10·См ·Dq · Sy ·(17)
y=0.8; (10. т.2. табл. 4.32.)
Mкр= 10·0.021 ·102 · 0.20.8 ·1.0=27.6 (Нм);
Мощность резания определяется по формуле:
Таблица 15 - Режимы резания пир обработке отверстий
Зенкерование отверстий диаметром 16Н12.
Подача при зенкеровании определяется:
Sо=KSKHBS=0521=052 (ммоб).
Частота вращения шпинделя станка определяется:
n=(1000 Kv KМ KHBv KT KИ)d(19)
n=(1000 7 1 101 1 1)16=440.
Принимаем по паспорту станка n=400 обмин.
Действительная скорость резания:
Таблица 16 - Режимы резания при зенкеровании
Глубина резания при обработке метчиком равна высоте профиля нарезаемой резьбы обработка резцами осуществляется за несколько проходов.
Врезание на каждом проходе: t0 = 02 03 мм
Скорость резания при резьбонарезании определяется в зависимости от шага резьбы (P=15 мм) и диаметра нарезаемой резьбы (М10).
V=VтабKv=908=72 (ммин).
Рассчитаем частоту вращения шпинделя.
По паспорту станка принимаем n=160 обмин.
Мощность при резьбонарезании метчиком определяется по формуле
Полученные данные занесем в таблицу:
Таблица 17 - Режимы резания при резьбонарезании
Определение режимов резания расточной операции
Определим режимы резания на расточной операции инструментами Iscar.
Обрабатываемый диаметр – 60 мм.
Исходя из рекомендаций по применению режущего инструмента назначаем:
- при предварительной (черновой) обработке – v=140 ммин s=02 ммоб.
Тогда скорость вращения шпинделя будет равна:
По паспорту станка принимаем n=630 обмин.
- при финишной обработке – v=180 ммин s=006 ммоб.
) Обрабатываемый диаметр – 70 мм.
Таблица 18 - Режимы резания при растачивании отверстий инструментом Iscar
Обрабатываемый диаметр мм
Скорость резания ммин
Число оборотов шпинделя обмин
6 Выбор оборудования
Черновую обработку плоскостей производим на продольно-фрезерном станке модели 6Г606Ф1.
Продольно-фрезерные станки модели 6Г606Ф1 предназначены для обработки деталей из черных и цветных металлов различных сплавов и пластмасс. Основным методом обработки на станках является обработка плоскостей торцовыми фрезами.
Кроме этого на станках возможно производить фрезерование плоскостей цилиндрическими фрезами обработку пазов и уступов дисковыми фрезами применять концевые фасонные и угловые фрезы.
Таблица 19- Технические характеристики станка 6Г606Ф1
Технические характеристики
Размеры рабочей поверхности стола мм
Наибольший ход стола мм
Наибольшее расстояние от середины рабочей поверхности стола до торца горизонтального шпинделя мм
Наибольшее расстояние от рабочей поверхности стола до торца вертикального шпинделя мм
Наибольшее расстояние от рабочей поверхности стола до оси горизонтального шпинделя мм
Количество скоростей шпинделя
Пределы частот вращения шпинделя обмин
Количество ступеней подач стола (бесступенчатое)
Пределы рабочих подач мммин
Скорость быстрого перемещения стола мммин
Регулирование подач (бесступенчатое)
Пределы подач шпиндельных бабок мммин
Скорость быстрого перемещения шпиндельных бабок мммин
Скорость перемещения траверсы мммин
Наибольшее перемещение гильзы мм
Мощность главного привода кВт
Габаритные размеры мм:
Масса станка с электрооборудованием кг
Особенности конструкции
Широкие диапазоны рабочих скоростей шпинделя подач стола и шпиндельных бабок высокая жесткость станков позволяют производить на них как обычное так и скоростное фрезерование а также обрабатывать детали из высоколегированных сталей и легких сплавов.
В станках предусмотрены:
бесступенчатое регулирование приводов подач стола и шпиндельных бабок;
автоматический отскок инструмента от обработанной поверхности при быстром ходе стола назад;
возможность работы стола по полуавтоматическому циклу;
быстродействующие гидравлические зажимы подвижных узлов (шпиндельные бабки и гильзы шпинделей);
электромеханическое крепление инструмента;
механизм выборки люфта в приводе подач стола;
механизм уборки стружки вибрационного типа;
автоматическая смазка направляющих;
возможность присоединения гидравлических зажимных приспособлений.
Рисунок 1 - Общий вид станка 6Г606Ф1
Обработку отверстий производим на вертикально-сверлильном станке с ЧПУ 2Р135Ф4.
Рисунок 2 - Общий вид станка 2Р135Ф4
Станок многоцелевой вертикально-сверлильный с крестовым столом и числовым программным управлением предназначен для выполнения следующих операций: сверления зенкерования рассверливания зенкования развертывания нарезания резьбы получистового и чистового прямолинейного и контурного фрезерования деталей чистового растачивания отверствий и канавок в них.
Таблица 20 - Технические характеристики станка 2Р135Ф4
Наибольший условный диаметр сверления
Емкость инструментального магазина
Наибольший крутящий момент на шпинделе Н м
Скорость быстрого перемещения по всем осям ммин
Осевое усилие на шпинделе Н
Наибольшие программируемые перемещения:
Потребляемая мощность кВт
Расточную операцию производим на горизонтально-расточном станке модели 2206ВМФ4.
Станок предназначен для комплексной обработки корпусных деталей средних размеров с четырех сторон без переустановок по заданной программе. На станке можно производить получистовое и чистовое фрезерование плоскостей пазов и криволинейных поверхностей фрезами различных типов а также растачивание сверление зенкерование развертывание нарезание резьбы метчиками в деталях из чугуна стали цветных металлов и пластмасс. Управление станка осуществляется по программе хранящейся в памяти УЧПУ. На станке программируется координатные перемещения стола и шпиндельной головки скорости этих перемещений частота вращения шпинделя смена инструмента выбор коррекции на диаметр и длину инструмента стандартные циклы обработки.
Станок оснащен крестовым поворотным столом лобовой бесконсольной шпиндельной головкой. Инструментальный магазин установлен на самостоятельных опорах возле станка что позволяет значительно увеличить жесткость станка повысить виброустойчивость и свести к минимуму изменения его точностных параметров.
В качестве привода главного движения использован электродвигатель с широким диапазоном регулирования что сокращает длину кинематических цепей и улучшает эксплуатационные качества станка.
Устройство для контроля угла поворота шпинделя позволяет автоматически устанавливать ориентированный по углу инструмент. привод ходовых винтов непосредственно от высоко моментных электродвигателей обеспечивает высокую точность перемещений и гибкость управления подачами. На станке применены замкнутые направляющие качения типа "танкеток" и беззазорные передачи винт-гайка качения что повышает долговечность станка и плавность перемещения рабочих органов. Рабочая зона станка защищена специальной защитой. Станок оснащен устройством термостабилизацией шпинделя. Класс точности станка - В.
Размеры рабочей поверхности стола:
ширина (под заказ) мм
Наибольшее перемещение стола:
продольное (ось "х") мм
поперечное (ось "z") мм
Наибольшее вертикальное перемещение шпиндельной головки мм (ось "y"):
Предельные расстояния от оси шпинделя до рабочей поверхности стола мм:
Предельные расстояния от торца шпинделя до центра стола мм:
Наибольшая масса устанавливаемой заготовки (с учетом массы приспособления) кг:
Пределы частот вращения шпинделя мин-1:
Пределы частот вращения шпинделя с применением быстроходного шпинделя мин-1:
Конусное отверстие в шпинделе:
Пределы рабочих подач по осям "х"y"z" мммин:
Величина ускоренных перемещений по осям "х"y"z" мммин:
Емкость инструментального магазина шт.гнезд (под заказ):
Продолжение таблицы 21
Наибольший диаметр инструментов загружаемых в магазин:
без пропуска гнезд мм
с пропуском гнезд мм
Точность одностороннего позиционирования:
линейного (по осям "х" "y" "z") мкм
углового (поворотного стола ось "В") угл.с
Габаритные размеры станка (вместе с отдельно расположенными сб.единицами агрегатами и электрооборудованием):
Масса станка (без отдельно расположенных сб.единиц агрегатов и электрооборудования) кг:
Масса станка (вместе с отдельно расположенными сб.единицами агрегатами и электрооборудованием) кг:
Род тока питающей сети:
переменный трехфазный
Мощность привода главного движения кВт:
Суммарная мощность всех электродвигателей кВт:
Тип устройства программного управления:
NC-110 SIEMENS 2C-42
7 Выбор средств технологического оснащения
Выбор режущего вспомогательного и мерительного инструмента является основной частью подготовки производства.
Контрольные операции по проверке качества детали на различных стадиях ее изготовления являются частью технологического процесса. У корпусных деталей в процессе их изготовления контролируют главным образом геометрические параметры (диаметр форма прямолинейность осей отверстий расположение отверстий относительно других осей или плоскостей).
Для выбора режущего инструмента составим таблицу.
Таблица 22 - Инструменты
Вспомогательный инструмент
Измерительный инструмент
Фреза 2214-0061 ГОСТ 9473-80
Оправка 6220-0128 ГОСТ 13042-83
Штангенглубиномер ШГ-250-005 ГОСТ 162-80
Головка расточная Iscar BHF MB50 125x114
Пластина Iscar TPGX 110304L
Удлинитель Iscar EX 50x200 MB50
Оправка Iscar CATM 50 MB50
Штангенциркуль ШЦ-I-250-005 ГОСТ 161-80
Калибр пробка Н8 8133-1104 ГОСТ 14812-69
Угломер типа 1-2 ГОСТ 5378-88
Образцы шероховатостей по ГОСТ 9378-93
Круг полировальный войлочный
Сверло 2317-0105 ГОСТ 14952-75
Втулка 50-1 ГОСТ Р 505160-92
Сверло 2300-6397 ГОСТ 10902-77
Патрон 20-В10 ГОСТ 8522-79
Зенковка 2353-0103 ГОСТ 14953-80
Метчик 2621-1617 ГОСТ 3266-81
Пробка 8221-3067 7Н ГОСТ 17758-72
Сверло 2300-3479 ГОСТ 10902-77
Зенкер 2320-2572 ГОСТ 12489-71
Калибр пробка Н12 8133-0930 ГОСТ 14812-69
Зенкер 2320-2585 ГОСТ 12489-71
Калибр пробка Н12 8133-0936 ГОСТ 14812-69
Сверло 2300-0174 ГОСТ 10902-77
Сверлить 2 отв. . 84+03 под резьбу М10 на глубину 30+1
Сверло 2300-3447 ГОСТ 10902-77
Сверлить 2 отв. . 15+043 на глубину 6+03
Сверло 2300-6411 ГОСТ 10902-77
Метчик 2621-1433 ГОСТ 3266-81
Пробка 8221-3044 7Н ГОСТ 17758-72
8 Определение основного технологического времени
Основное технологическое время обработки на переходах определяется по формуле
где s0 – подача ммоб;
n – число оборотов инструмента ммоб;
L – длина обработки мм.
Для определения основного машинного времени составим таблицу:
Таблица 23 - Расчет основного машинного времени мехобработки детали
Расточить отв.69+064 в размер 38±031
Расточить отв.70+012 в размер 38±031
Нарезать резьбу М10-7Н в 4 отв. на глубину 20+1
9 Техническое нормирование
Под техническим нормированием понимается установление норм времени на выполнение отдельной работы или нормы выработки в единицу времени. Под нормой времени понимается время устанавливаемое на выполнение данной операции.
Тшт=То+Твсп + Тоб+Тотд=Топ + Тоб+Тотд(18)
То - основное время;
Твсп – вспомогательное время;
Твсп= Тус + Тзо + Туп + Тизм(19)
Тус – время на установку и снятие заготовки;
Тзо – время на закрепление открепление;
Туп – время на приемы управления;
Тизм – время на измерения;
Топ – оперативное время;
Тоб– время на обслуживание отдых;
Ттех=ТоtсмТ – время на техническое обслуживание рабочего места;
tсм – время на смену инструмента мин;
Торг=Топ3%100 – время организационное мин;
Тотд=Топ6%100 – время на отдых и личные надобности.
Для удобства вычислений составим таблицу.
Штучное время для операций выполняемых на оборудовании с ЧПУ
Тшт=Tца+Tвkв[1+(атех+аорг+аотд)100] где
Tца время цикла автоматической работы станка по программе:
То – основное машинное время выполнения операции;
Tмв – вспомогательное машинное время выполнения операции;
Tв – вспомогательное время выполнения операции:
где tву – время на установку и снятие детали из приспособления;
tва – время не вошедшее в программу;
tки – не перекрываемое время проведения контрольных измерений;
kв – поправочный коэффициент на время выполнения ручной вспомогательной работы kв=098;
атех+аорг+аотд – время на техническое и организационное обслуживание рабочего места на отдых и потребности атех+аорг+аотд=8 мин.
tобс+tотд (атех+аорг++аотд)
Составление управляющей программы для обработки на станке ЧПУ
Для обработки детали на станке с ЧПУ необходимо задать траекторию перемещения инструмента и другие условия обработки. Данную программу называют программой обработки детали или управляющей программой (УП). Программирование обработки детали означает указание траектории движения инструмента и вспомогательных действий станка устройству ЧПУ в соответствии с правилами (языком программирования) ЧПУ. Программы делятся на программы и подпрограммы. При отработке программы УЧПУ будут работать по командам программы однако если в программе встретится команда обращения к подпрограмме то дальнейшее поведение УЧПУ определяется командами подпрограммы. Далее если во время выполнения подпрограммы встретится команда возвращения в программу то дальнейшее поведение УЧПУ определяется командами программы.
Структурную единицу программы (или подпрограммы) составляет кадр. Кадр представляет собой записанную по правилам программирования последовательность символов языка программирования. Последующий кадр от предыдущего отделяется кодами ВК>ПС> (неотображаемые коды “Возврат каретки” “Перевод строки”). Эти коды обычно вставляются автоматически при нажатии клавиши Enter в любом текстовом редакторе.
Элементом кадра является слово. Слово состоит из адреса и последующего числового значения нескольких разрядов (перед числовым значением могут быть записаны знаки "+"-"). При этом знак "+" можно опускать. Х - 1000
Адрес. Числовое значение. Адрес представляет собой одну из алфавитных букв (A - Z) и определяет смысл последующего числового значения. Ниже в таблице перечислены адреса которые используются для данного УЧПУ и их смысл. С использованием этих слов можно составить один кадр причем порядок слов в кадре может быть произвольным.
При одинаковых числовых значениях приведут к одинаковым результатам. Рекомендуется порядок записи по ГОСТ 20999-86.
Схема технологической наладки токарного станка с ЧПУ для чистовой токарной операции приведена на карте наладки.
Часть программы для сверлильно-фрезерно-расточной операции.
N001 G27 S028 M104 T101
N002 G58 Z+000000 F70000
N003 G58 X+000000 F70000
N005 G01 F10200 L131
N006 X-15100 Z-02000 F10600
N008 X+20500 Z+02000 F70000
N012 G01 F10200 L32
N013 X-15100 Z-02900 F10600
N020 X+13000 Z+14000 F70000
N023 G01 F10200 L33
N024 X-16140 Z-07420 F10600
N025 X-00780 Z-00390 F10024
N026 X+00780 Z+00390 F10120
N027 X+16140 Z+07420 F70000
N029 G25 X+99999 F70000
Технологическая планировка является одним из завершающих этапов проектирования механосборочных и вспомогательных цехов машиностроительных предприятий при разработке которой решают комплекс взаимосвязанных технических и организационных задач:
- установление состава производственных участков и отделений
вспомогательных служб санитарно-бытовых и административно-конторских помещений;
- расчет площадей цеха;
- выбор типа объемно-планировочных и конструктивных решений основного производственного и вспомогательного зданий;
- компоновка цеха организация грузопотоков;
- выбор и расчет количества внутрицехового и межцехового транспорта;
- планировка производственных участков поточных механизированных и автоматических (в том числе гибких) линий изготовления деталей сборки узлов и изделий в целом;
- разработка общей технологической планировки цеха и ситуационного плана производственного корпуса.
Технологическая планировка – это графическое изображение на плане и разрезах оборудования поточных и автоматических линий рабочих мест стендов подъемно-транспортных средств и инженерных сетей предназначенных для обслуживания технологических процессов. Планировка является одним из последних этапов разработки рабочего проекта цеха а ее разработка представляет собой многовариантную задачу требующую технико-экономического сравнения конкурирующих вариантов.
Рациональная планировка и организация рабочих мест имеют большое значение для достижения наибольшей производительности и наименьшей себестоимости выпускаемой продукции. В рабочем проекте технологическую планировку оборудования участка цеха малого предприятия (МП) выполняют в масштабе 1:100; для цехов и МП насчитывающих свыше 200 единиц оборудования – в масштабе 1:200; для цехов и МП насчитывающих менее 70 единиц оборудования а также производственных участков – М1:50.
При размещении оборудования на технологических планировках следует обеспечить свободный доступ к рабочим местам удобство работы рабочих и транспортирования заготовок к месту работы близость комнат курения и туалетов раздевалок медпунктов душей комнат приема пищи и столовых хорошее освещение помещений и постоянный воздухообмен удобное расположение фонтанчиков для питья и пожарных гидрантов.
Организация рабочего места должна обеспечить непрерывность работы при соблюдении максимально возможной производительности минимальной себестоимости выпускаемой продукции при обеспечении заданного качества.
Расположение оборудования и рабочих мест координируется относительно колонн. При расстановке станков руководствуются нормальными размерами промежутков между станками в продольном и поперечном направлениях расстояниями от стен и колонн которые устанавливают по нормам технологического проектирования [9]. При этом все расстояния указывают от крайних положений движущихся частей станка и от постоянных ограждений (приспособления включают в габарит станка). При обслуживании технологического оборудования мостовым краном расстояние станков от стен и колонн устанавливают с учетом нормального положения крюка крана над станком.
Размер рабочей зоны по нормам технологического проектирования составляет не менее 800 мм. Транспортируемые изделия не должны выходить за пределы транспортных средств (на площадь прохода). Место расположения рабочего обслуживающего оборудование обозначается кружком диаметром 5 мм с заштрихованной тыльной половиной.
Рисунок 4 - Схемы взаимного расположения универсальных станков друг
Таблица 26 - Нормы расстояний универсальных станков от проезда относительно друг друга от стен и колонн зданий.
Техническая планировка оборудования должна обладать гибкостью. В связи с этим широкое применение находит установка оборудования на виброопорах на общем бетонном полу (плите) производственного корпуса. В этом случае у каждой колонны (а при большой ширине проектов и шаге колонн и между колоннами) располагают краны для подвода сжатого воздуха и смазочно-охлаждающих жидкостей (СОЖ) и воронки в полу для слива в централизованные или групповые системы сбора очистки регенерации и утилизации СОЖ подводы электрокабеля к оборудованию и др.
Технологическую планировку разрабатывают в следующей последовательности:
- наносят продольные и поперечные разбивочные оси унифицированных типовых секций (УТС) производственного и вспомогательного здания; если обслуживаемые помещения располагают на нескольких этажах то на планировке цеха изображают с некоторым интервалом разбивочные оси каждого этажа;
- вычерчивают капитальные стены и колонны производственного и вспомогательного зданий лестничные клетки;
- производят разбивку оконных и дверных проемов в наружных стенах показывают направление открывания дверей;
- на основе компоновки уточняют месторасположение магистральных проездов и проходов производственных механических и сборочных участков технологического оборудования вспомогательных служб трасс подъемно-транспортных средств средств уборки стружки и наносят их на план производственного здания;
- выбирают типовое планировочное решение санитарно-бытовых и административно-хозяйственных помещений и наносят на план соответствующего этажа вспомогательного здания внутренние стенки перегородки дверные проемы;
- выбирают необходимые продольные и поперечные разрезы основного и вспомогательного зданий;
- наносят в верхнем правом углу листа ситуационный план корпуса;
- составляют сводную ведомость площадей цеха и размещают ее на поле чертежа;
- изображают в виде таблицы условные обозначения принятые в планировке;
- на плане и разрезах проставляют все размеры выполняют надписи (наименование участков отделений помещений и размеры их площадей порядковые номера оборудования);
- составляют спецификацию оборудования.
Организационная часть
1 Расчет численности работающих участка.
Расчёт основных работающих участка производится по формуле:
где Фn – полезный фонд одного рабочего в год час.;.
Nв=2950 штгод – размер партии деталей в год;
Тшк – штучно-калькуляционное время изготовления детали на заданной операции мин;
КN – коэффициент многостаночного обслуживания;
Полезный фонд рабочего в год определяется по формуле:
где Дк=366 – максимальное календарное число дней в году;
Дв=104 – число выходных дней в году;
Дп=10 – число праздничных дней в году;
Кn = 09 – коэффициент учитывающий невыходы рабочих.
Тогда количество работающих на участке будет равно:
Кол-во принятых рабочих
Определение необходимого количества оборудования по операциям.
где Тшт – штучное время на выполнение указанной операции
mp – фактически необходимое оборудование
Р – округлённое количество оборудования
з.н. - коэффициент нормальной загрузки оборудования
mp=(NТшт)(60Fдз.н.) (25)
где N – количество деталей в партии
Fд=5445 ч - количество рабочих часов в году при трехсменной работе.
Количество оборудования принято с учетом трехсменной загрузки оборудования.
Распределение рабочих по сменам сводим в таблицу.
Таблица 29 - Распределение рабочих по сменам
Распределение по сменам
Списочный состав основных рабочих - 16 человек явочный – 16 человек из них 7 человек в I смену 7 человек во II смену 2 человека – в III смену.
Общее число вспомогательных рабочих принимается в количестве 30% от числа основных рабочих: Rвсп = 03×16=48 - принимаем 5 человек. Из них: 3 наладчика 6 разряда один в I смену второй во II смену третий – в III смену.
Принимаем 1 контролера 5 разряда который обслуживает проектируемый участок в одну смену а контролер соседнего участка свой и проектируемый – в другую смену.
Общее количество специалистов и управленческого персонала принимается равным 10% от числа рабочих: RС = 01×16=16 - принимаем 3 человека. Мастер в I смену обслуживает два участка: соседний и проектируемый второй мастер обслуживает те же участки во II смену третий - те же участки в III смену.
Также принимается один технолог на участок который работает в I смену.
Составляем общую ведомость работающих участка.
Таблица 30 - Ведомость работающих участка
Распределение разрядов
Итого человеко-разрядов
Итого человеко-часов
Итого работающих участка
2 Транспортировка деталей на участке
Основное назначение транспортной системы участка в основном следующее: доставка с клада в требуемый момент времени к требуемому рабочему месту грузов; доставка заготовок полуфабрикатов или изделий в требуемый момент времени на требуемое технологическое оборудование; доставка полуфабрикатов или готовых изделий с производственных участков на склад.
Транспортировка заготовок из литейного цеха на участок механической обработки осуществляется при помощи электропогрузчика грузоподъемностью три тонны. Транспортировка осуществляется в специальной ячеистой таре которая исключает соударение деталей.
Перемещение деталей от одного рабочего места к другому производится краном-укосиной.
Для перемещения тяжелых деталей или тары с деталями а также для демонтажа отдельных крупногабаритных частей оборудования на участке имеется подвесной кран-балка грузоподъемностью 10 тонн.
3 Организация ремонта оборудования на участке
Система ремонтного и технического обслуживания участка предусматривается для обеспечения работоспособности технологического и подъемно-транспортного оборудования и других технических средств производства.
Основными задачами ремонтной службы являются следующие: уход и надзор за действующим оборудованием; планово-предупредительный ремонт технических средств всех видов; модернизация существующего и изготовление нестандартного оборудования.
Указанные работы выполняет ремонтно-механическая служба участка. Основой организации ремонта оборудования на участке является проведение планово-предупредительного ремонта. Он включает в себя совокупность различного вида работ по техническому уходу и ремонту оборудования и мероприятия межремонтного обслуживания. Межремонтное обслуживание выполняют во время перерывов в работе оборудования без остановки технологического процесса.
Плановые ремонты оборудования: малый средний и капитальный а также изготовление запасных частей возлагаются на ремонтно-механический цех завода т.е. механический участок не располагает собственными службами по ремонту оборудования а привлекает общецеховые и общезаводские службы.
Капитальный ремонт оборудования производится один раз в четыре года. Планово-предупредительный – один раз в два года. Текущий ремонт – один раз в год. Осмотры оборудования проводятся два раза в год. Кроме того ремонт производится внепланово по мере необходимости.
4 Определение потребности в материалах и энергоресурсах
Потребность в основных материалах на год рассчитывается по формуле:
где mз = 469 кг – масса заготовки.
Затраты на основные материалы
Затраты на основные материалы в год определяются по формуле:
Затраты на вспомогательные материалы в год определяются по формуле:
Расчет потребности в холодной воде для технических целей производится по формуле:
где а = 3л – расход воды за один час на один станок; nс = 7– количество оборудования на участке.
Стоимость 1т технической холодной воды составляет 288р. тогда стоимость холодной воды для технических целей будет равна:
Расчет потребности в холодной питьевой воде производится по формуле:
где R = 24чел. – количество работников участка; х = 120л – расход воды на человека в сутки.
Стоимость 1т холодной питьевой воды составляет 352р. тогда стоимость холодной воды будет равна:
Стоимость осветительной электроэнергии составит:
Расчет потребности в сжатом воздухе производится по формуле:
где q = 03м3 – расход сжатого воздуха за 1 час; nС = 7 – количество станков где используется сжатый воздух.
Стоимость 1м3 сжатого воздуха составляет 08р. тогда полная стоимость сжатого воздуха будет равна:
Расчет потребности в горячей воде для отопления производится по формуле:
где V = 3264м3 – объем производственного помещения НОТП = 1800ч. – длительность отопительного периода для средней полосы России в год; h = 40ккалч×м3 – расход тепла.
Стоимость 1т горячей воды составляет 423р. тогда общая стоимость горячей воды для отопительных нужд составит:
Полученные данные занесем в таблицу ниже:
Затраты на основные материалы руб.
Затраты на вспомогательные материалы руб.
Затраты на холодную техническую воду руб.
Затраты на холодную питьевую воду руб.
Затраты на осветительную электроэнергию руб.
Затраты на сжатый воздух руб.
Затраты на горячую воду для отопления руб.
Конструкторская часть (проектирование станочного приспособления)
1 Описание конструкции назначение принцип действия.
В качестве исходных данных конструктор приспособления должен иметь: чертеж заготовки и детали с техническими требованиями их приемки; операционные чертежи на предшествующую и выполняемую операции; операционные карты технологического процесса обработки данной детали.
В результате анализа исходных данных выявляют: последовательность и содержание операций; принятое базирование; используемое оборудование и инструмент; режимы резания; запроектированную производительность с учетом времени на установку закрепление и снятие обработанной детали; размеры допуски шероховатость обрабатываемых поверхностей деталей; марку и вид термической обработки материала.
Служебное назначение приспособления – это максимально уточненная и четко сформулированная задача для решения которой оно предназначено. При формулировании служебного назначения необходимо учитывать данные о закрепляемой детали (количество форма размеры качество поверхностей материал вид термообработки) точности изготовления производительности характеристике привода окружающей среде (температуре влажности запыленности виде энергии и т.д.) о внешнем виде технике безопасности степени автоматизации и т.д.
По целевому назначению приспособления делят на следующие группы:
Станочные для установки и закрепления обрабатываемых заготовок. Эти приспособления подразделяют на сверлильные фрезерные расточные токарные и др. (по группам станков).
Станочные для установки и закрепления рабочего инструмента. К ним относятся патроны для сверл разверток метчиков многошпиндельные сверлильные и фрезерные головки инструментальные державки для токарно-револьверных станков и автоматов и другие устройства. Эти приспособления называются вспомогательным инструментом.
Сборочные используемые для соединения деталей в изделия. Применяют следующие типы приспособлений: а) для крепления базовых деталей собираемого изделия; б) для обеспечения правильной установки соединяемых элементов изделия; в) для предварительного деформирования устанавливаемых упругих элементов (пружин разрезных колец); г) для запрессовки клепки развальцовывания и других операций когда при сборке требуются большие силы.
Контрольные применяемые для проверки заготовок при промежуточном и окончательном контроле деталей а также при сборке машин.
Приспособления для захвата перемещения и перевертывания заготовок деталей и собираемых изделий.
По степени специализации станочные приспособления делят на следующие группы: универсально-безналадочные (УБП) универсально-наладочные (УНП) универсально-сборные (УСП) сборно-разборные (СРП) неразборные специальные (НСП) специализированные наладочные (СНП).
К группе УБП относятся универсальные приспособления общего назначения: центры поводковые устройства оправки токарные патроны цанговые приспособления плиты магнитные и электромагнитные столы и т.д. Они изготовляются как принадлежность к станку заводом изготовителем станков или специализированными предприятиями. УБН применяют в единичном и мелкосерийном производстве; на станках с ЧПУ – в мелкосерийном производстве.
Группа УНП включает приспособления состоящие из постоянной части и сменных наладок. Постоянная часть во всех случаях остается неизменной а сменная наладка заменяется в зависимости от конкретной обрабатываемой детали. Постоянная часть включает в себя корпус и зажимное устройство с приводом (чаще пневматическим). Иногда в нее встраивают делительное устройство и другие элементы кроме опорных и направляющих. Постоянная часть изготавливается заранее и применяется многократно. Перед очередным использованием УНП требуется произвести лишь смену наладки или некоторую дополнительную обработку. Наладка представляет собой сменные опорные и направляющие элементы. Каждый комплект наладки предназначен только для данной детали и конкретной операции ее обработки и в этом случае является специальным. С помощью УНП заготовка устанавливается с такой же точностью и быстротой как и при использовании дорогостоящего специального приспособления. Универсальность УНП несколько ограничена определенными размерами постоянной части которая обычно нормализуется в пределах предприятия или отрасли. К числу нормализованных приспособлений на базе которых собирают УНП относятся машинные тиски скальчатые кондукторы пневматические патроны со сменным кулачками планшайбы с переставными угольниками для растачивания на токарном станке деталей сложной формы и т.д. УНП применяют в серийном производстве; на станках с ЧПУ – в мелкосерийном производстве.
УСП включают приспособления компонуемые из нормализованных деталей и узлов. Каждая компоновка УСП обладает всеми основными свойствами специального приспособления: предназначена для обработки конкретной детали на определенной операции и обеспечивает базирование заготовки без выверки и требуемую точность. По истечении надобности в таком приспособлении оно разбирается на составные детали и узлы которые могут быть многократно использованы для компоновки других приспособлений. Отличительной особенностью УСП является крестообразное взаимно-перпендикулярное расположение на сопрягаемых поверхностях Т-образных и шпоночных пазов. Основные детали и сборочные единицы из которых компонуются УСП условно подразделяются на семь групп: 1) базовые детали (плиты прямоугольные и круглые угольники); 2) корпусные детали (опоры призмы подкладки и т.д.); 3) установочные детали (шпонки штыри пальцы и т.д.); 4) прижимные детали (прихваты планки); 5) крепежные детали (болты шпильки винты и т.д.); 6) разные детали (ушки вилки хомутики оси рукоятки и т.д.); 7) сборочные единицы (поворотные головки кронштейны центровые бабки и др.).
В приборостроении и машиностроении используют комплекты УСП-8 с шириной пазов 8 мм и диаметром крепежных элементов 8 мм для обработки малогабаритных заготовок (220х120х100 мм). УСП-12 предназначены для обработки заготовок размерами 700х400х200 мм а УСП-16 для заготовки размерами 2500х2500х1000 мм.
УСП применяют в единичном и мелкосерийном производстве. При использовании вместо ручных зажимов гидро- или пневмозажимов УСП можно применять и в крупносерийном производстве. На станках с ЧПУ УСП применяются в единичном и мелкосерийном производстве.
Система СРП является разновидностью системы УСП. В компоновках СРП в отличие от УСП количество сборочных единиц преобладает над деталями. Приспособления переналаживаются посредством перекомпоновки регулирования положения базирующих и зажимных элементов или замены сменных наладок. СРП обычно собирают на период выпуска определенного изделия. После обработки партии деталей приспособление снимают со станка и хранят до запуска в обработку новой партии. Разбирают СРП только при смене объекта производства. Компоновки СРП собирают из стандартных деталей и сборочных единиц фиксируемых относительно друг друга системой палец-отверстие. Для этой цели в базовых деталях имеются сетки точных координатно-фиксирующих отверстий. К столу станка детали и сборочные единицы СРП крепятся посредством Т-образных пазов. СРП применяются в единичном и мелкосерийном производстве а на станках с ЧПУ – в мелкосерийном производстве.
Приспособления группы НСП служат для обработки только определенной детали на одной конкретной операции. Специальные приспособления обладают большими преимуществами – позволяют без выверки придать заготовке требуемое положение относительно станка и режущего инструмента и благодаря этому при одной настройке обработать всю партию заготовок. К НСП относятся патроны для токарных автоматов и полуавтоматов мембранные патроны гидропластмассовые приспособления и др. НСП применяются в крупносерийном и массовом производствах. На станках с ЧПУ такие приспособления можно применять лишь как исключение если нельзя применить ни одну из переналаживаемых систем.
К группе СНП относятся специальные приспособления обладающие определенной универсальностью вследствие введения в их конструкцию элементов допускающих наладку приспособления путем регулировки. Благодаря этому одно и тоже приспособление можно применять для обработки ряда деталей одной конструкторско-технологической группы. К СНП относятся переналаживаемые планшайбы патроны оправки кондукторы и т.д. СНП применяют в серийном и крупносерийном производствах; на станках с ЧПУ – в серийном производстве.
Кроме вышеперечисленных групп приспособлений на станках с ЧПУ и обрабатывающих центрах используются и другие группы приспособлений: механизированные универсально-сборные (УСПМ) и универсально-сборные переналаживаемые (УСПО).
Рисунок 5 - Общий вид приспособления
Заготовка устанавливается на плоскость стола поз.2 базируется в координатный угол. Стол закреплен и заштифтован на плите поз. 1. На столе размещены кронштейны поз.3 и пневмоцилиндры поз.4. Закрепление заготовки производится движением штоков пневмоцилиндров посредством рычагов поз.5.
Приспособление базируется на столе расточного станка посредством квадратных шпонок в шпоночные пазы стола станка и закрепляется крепежными элементами.
Спроектировать установочно-зажимное приспособление для детали корпус для операции сверильно-фрезерно-расточная в условиях серийного производства;
-геометрические параметры:
длина х ширина х высота – 1430х890х435
-точность выполняемой операции в мм:
)Точение поверхности диаметром 60Н8 70Н10 (обеспечивается схемой обработки и снимаемым припуском).
)Межцентровое расстояние 100±04 (обеспечивается точностью обработки станка).
)Расстояние от базовой поверхности 60±03 (обеспечивается точностью обработки станка и настройки на размер партии обрабатываемых деталей).
)Размеры А (см. рисунок ниже) (обеспечиваются точностью обработки станка предварительной выставки и выверки - настройкиобкатки на размер партии обрабатываемых деталей).
)Отклонение от параллельности осей обрабатываемых отверстий не более 02 мм (по IT142 при заданном диаметре и длине обработки) (обеспечивается точностью обработки станка и точностью изготовления приспособления)
Способ обеспечения заданной точности - по предварительной настройке станка.
Годовая программа выпуска всех типоразмеров Nг = 2950 шт.
2 Выбор способа установки заготовки в станочном приспособлении. Выбор схемы базирования и описание работы приспособления.
Анализируя техническое задание эскиз детали под выполняемую операцию из ГОСТ 21495-76 выбираем теоретическую схему базирования и из ГОСТ 3.1107-81 возможные схемы практической реализации.
Анализируя различные схемы базирования приходим к выводу что схема базирования детали для обработки группы отверстий предполагает использование в качестве установочной базы наружную поверхность детали которая устанавливается на плоскость в «координатный угол» так как в данном конкретном случае конструкторские технологические и измерительные базы совпадают.
Рисунок 6 - Практическая схема базирования детали "Корпус
3 Силовой расчёт приспособления.
Силовой расчет станочных приспособлений можно разбить на следующие этапы:
- определение сил и моментов резания.
- выбор коэффициента трения f заготовки с опорными и зажимными элементами.
- составление расчетной схемы и исходного уравнения для расчета зажимного усилия Рз .
- расчет коэффициента надежности закрепления К.
- составление расчетной схемы и исходного уравнения для расчета исходного усилия Ри
- расчет диаметров силовых цилиндров пневмо- и гидроприводов.
Определение сил и моментов резания
Определим силы резания при черновом растачивании так как по сравнению с чистовым проходом сила резания будет максимальной. Силы резания будут действовать вдоль трех осей координат x y z и называются соответственно Px Py Pz. Наибольшей из них является сила Pz стремящаяся оторвать заготовку от стола и осевая сила Р0 стремящаяся сдвинуть заготовку. Поэтому дальнейший расчет ведем по ним.
Pz = 10×Cp × tx × Sy × nn × Kp (Н)(33)
где Cp = 92 – коэффициент;
Kp - поправочный коэффициент определяем по формуле:
Kp = Kmp × Kap × Kgp × Klp × Ktp(34)
где Kap - коэффициент зависящий от главного угла в плане;
Kgp - коэффициент зависящий от переднего угла;
Ktp - коэффициент зависящий от радиуса на вершине резца;
Kmp - коэффициент зависящий от материала заготовки определяется как:
где n =1 – показатель степени.
Подставляя известные величины в формулу получим:
Kmp = (980750)1 = 0.81.
По табл. выбираем: Кap = 0.98 ;Kgp = 1.15 ; K Ktp = 0.87.
Kp = 1× 0.98 × 1.15 × 1× 0.87 = 0.81.
Подставив все вычисленные значения в формулу получаем:
Pz = 10 × 92 × 41 × 0.20.75 × 830 × 0.81 890 H.
Pо = 10×Cp × tx × Sy × nn × Kp (Н)(36)
где Cp = 15 – коэффициент;
Kp = Kmp × Kap × Kgp × Klp × Ktp(37)
P0 = 10 × 92 × 41 × 0.20.75 × 830 × 0.81 150 H.
Рассчитаем эквивалентную силу Рэ.
Выбор коэффициента трения заготовки с опорными и зажимными элементами.
В приспособлениях силы трения возникают на поверхностях контакта заготовки с опорными и зажимными элементами. Величина коэффициента трения (зависит от многих факторов). При использовании приспособлений его определение связано с определенными трудностями. В приспособлениях встречается много различных сочетаний контактных поверхностей различающихся по форме состоянию поверхности твердости и т.д. Принимаем коэффициент трения f=0.15.
Находим силу закрепления заготовки. Для этого составляем уравнения сил и моментов.
Проекция сил на ось Х.
где Fтр1 и Fтр2 – силы трения возникающие при зажиме.
где f1 и f2 – коэффициенты трения.
Окончательно получим
Введем понятие коэффициента запаса.
Коэффициент запаса вводится в формулу для обеспечения надежного закрепления заготовки и определяется в зависимости от условий обработки по формуле:
гдеK0 – гарантированный коэффициент запаса принимаем равным 15;
K1 – коэффициент учитывающий возрастание сил обработки при затуплении инструмента принимаем равным 11;
K2 – коэффициент учитывающий неравномерность сил резания обусловленную непостоянством снимаемого при обработке припуска принимаем равным 12;
K3 – коэффициент учитывающий изменение сил обработки при прерывистом резании принимаем равным 10;
K4 – коэффициент учитывающий непостоянство развиваемых приводом сил зажима коэффициент принимаем равным 13;
K5 – коэффициент учитывающий неопределенность положения мест контакта заготовки с установочными элементами принимаем равным 10.
Подставляя числовые значения в формулу определяем коэффициент запаса:
Принимаем коэффициент запаса .
Тогда формула примет вид
Составление расчетной схемы и исходного уравнения для расчета исходного усилия Ри.
Силовые механизмы обычно выполняют роль усилителя. Его основной характеристикой является коэффициент усиления i (передаточное отношение сил).
Наряду с изменением величины исходного усилия силовой механизм может также изменять его направление разлагать на составляющие и совместно с контактными элементами обеспечивать приложение зажимного усилия к заданной точке. Иногда силовые механизмы выполняют роль самотормозящего элемента препятствуя раскреплению заготовки при внезапном выходе из строя привода.
Силовые механизмы делятся на простые и комбинированные. Простые состоят из одного элементарного механизма – винтового эксцентрикового клинового рычажного.
Комбинированные представляют собой комбинацию нескольких простых: рычажного и винтового рычажного и эксцентрикового рычажного и клинового и т.д.
Силовые механизмы используются в приспособлениях с зажимными устройствами как первой так и второй групп. Для приспособлений с зажимными устройствами первой группы силовой механизм следует выбирать совместно с приводом чтобы можно было рационально согласовать силовые возможности механизма (коэффициент усиления i) с силовыми данными привода.
Выбор конструктивной схемы силового механизма производится также с учетом конкретных условий компоновки приспособления.
Для выбранного силового механизма необходимо определить коэффициент усиления i и исходное усилие Ри которое должно быть приложено к силовому механизму приводом или рабочим.
Расчетная формула для нахождения Ри может быть получена на основе решения задачи статики – рассмотрения равновесия силового механизма под действием приложенных к нему сил.
Рисунок 8 - Схема действия сил зажима
Величина усилия зажима определяется формулой
Диаметр пневмоцилиндра определяется по формуле
где D – рабочий диаметр поршня мм;
р – давление рабочее в пневмосистеме Па;
- КПД пневмоцилиндра;
q – учитывается при наличии пружины возврата в системе.
По конструктивным соображениям принимаем диаметр поршня 80мм тем самым обеспечиваем дополнительный запас по усилию прижатия заготовки.
4 Расчёт приспособления на прочность по слабому звену.
Прочность - одно из основных требований предъявляемых к деталям и приспособлениям в целом. Прочность деталей может рассматриваться по коэффициентам запаса или по номинальным допускаемым напряжениям. Расчеты по номинальным допускаемым напряжениям менее точны и прогрессивны но значительно проще.
С помощью расчета деталей (элементов) приспособлений на прочность можно решать две задачи:
а) проверку на прочность уже существующих деталей с определенными размерами сечений путем сравнения фактических напряжений (моментов сил) с допускаемыми - проверочный расчет;
б) определение размеров сечений деталей - предварительный проектный расчет.
Очевидно что наиболее нагруженной частью приспособления является ось рычага проведем проверочный расчет на прочность оси 14 мм по допускаемым напряжениям.
где Р - действующая сила на ось;
t - действующие напряжения на срез;
- допускаемые напряжения на срез;
Напряжения на смятие
s - действующие напряжения на смятие;
- допускаемые напряжения на смятие;
l - длина участка оси на которую действует сила.
Выбранный элемент удовлетворяет всем требованиям прочности.
5 Расчет приспособления на точность [3].
В данном случае необходимо обеспечить:
-отклонение от параллельности осей обрабатываемых отверстий не более 02 мм (обеспечивается приспособлением и точностью обработки станка).
Точность выполнения диаметральных размеров зависти от инструмента линейные размеры зависят от точности станка и его предварительной настройкиобкатки по посадочному отверстию.
При анализе выполняемых размеров схем базирования и установки можно установить что допуск параллельности обрабатываемой поверхности относительно оси детали может быть в пределах допуска. Положение заготовки будет определяться положением рабочих поверхностей установочных элементов относительно поверхностей контактирующих с поверхностями стола станка и определяющих положение приспособления на станке.
Параметр составляющей суммарной погрешности
Погрешность станка в нагруженном состоянии вызываемая погрешностями изготовления и сборки основных деталей и узлов и их износом («технологическая точность оборудования»)
Погрешность расположения приспособления на станке – расположение посадочных поверхностей приспособления относительно посадочных мест станка
Погрешность расположения опорных поверхностей относительно посадочных мест приспособления
Погрешность базирования исходной базы заготовки в приспособлении
Погрешность вызываемая закреплением заготовки в приспособлении
Погрешность расположения направляющих элементов относительно опорных элементов
Погрешность инструмента порождаемая погрешностью его изготовления
Погрешность расположения инструмента на станке
Погрешность возникающая вследствие деформации технологической системы СПИД под влиянием сил резания
Погрешность вызываемая износом инструмента
Выявим составляющие погрешности:
- dс в данном случае вызвана непараллельностью рабочей поверхности стола станка направлению перемещения шпинделя. Для расточных станков с габаритами рабочей поверхности стола до 2500 мм и нормального класса точности в соответствии с ГОСТ 2110-93 (Станки расточные горизонтальные с крестовым столом. Нормы точности) непараллельность указанных поверхностей на длине хода до 1250 мм допускается не более 003 мм. Следовательно dс=003.
- dрп =015 так как расположение приспособления на столе станка влияет на точность получаемого размера;
- погрешность dп.о=002 мм потому что допуск параллельности установочных плоскостей составляет 001 на 100 мм длины а длина обработки составляет 240 мм;
- погрешность dз=0 (принята без расчёта);
- погрешность dп.н. =01мм;
- погрешность dи и dри примем равными нулю так как их влияние устраняется настройкой инструмента на размер;
- погрешность dд=001 (принята без расчёта);
- погрешность dиз=001 – износ резца.
Суммирование составляющих погрешностей рассчитаем по формуле:
Результирующая погрешность 0086 меньше допуска 02 мм. Приспособление обеспечит требуемую точность.
Расчет себестоимости изготовления детали [13].
Расчет удельных капитальных затрат по вариантам сводится к определению затрат на технологическое оборудование производственную площадь и дорогостоящую оснастку.
Исходные данные по базовому варианту
Таблица 33 - Базовый маршрут обработки детали
0 Вертикально-фрезерная
0 Координатно-расточная
Таблица 34 - Проектный маршрут обработки детали
Приведенные затраты на единицу продукции определяются по формуле:
где ПЗ – приведенные затраты на единицу продукции руб.;
С – себестоимость единицы продукции руб.;
К – удельные капитальные вложения в производственные фонды руб.;
Ен – нормативный коэффициент сравнительной экономической эффективности капитальных вложений Ен = 015;
С помощью этого показателя выбирается вариант который обеспечивает оптимальное соотношение между себестоимостью и капитальными вложениями.
1 Расчет удельных капитальных вложений приходящихся на одну деталеоперацию.
1.1 Расчет удельных капитальных вложений в технологическое оборудование.
Коэффициент выполнения норм составляет КВН=105; плановый коэффициент загрузки оборудования КЗО=085.
Действительный годовой фонд времени работы станков: F.=3850 при двухсменной работе.
При определении приведенных затрат рассчитываются капитальные вложения не как таковые а удельные капитальные вложения т.е. вложения приходящиеся на одну деталеоперацию что очень важно так как капитальные вложения могут участвовать в производстве нескольких видов изделий что характерно для всех типов производства кроме массового.
Величина капитальных вложений в оборудование определяется по формуле:
гдеЦ – балансовая стоимость единицы оборудования руб;
Тшт-к – штучно калькуляционное время на выполнение операции мин;
F – действительный годовой фонд времени работы станков ч;
КВН. – плановый коэффициент выполнения норм времени рабочим;
КЗО =085– плановый коэффициент загрузки оборудования.
1.2 Расчет удельных капитальных вложений в производственные площади
В условиях серийного и единичного производства капитальные вложения в производственную площадь приходящиеся на одну деталеоперацию определяется по формуле:
гдеЦПЛ – цена одного квадратного метра производственной площади рубм2;
SОБ – производственная площадь под оборудование м2.
гдеSПЛ – площадь оборудования м2;
КД – коэффициент учитывающий дополнительную производственную площадь на проезды и проходы. КД=5.
1.3 Расчет удельных капитальных вложений в технологическую оснастку
Расчет ведем по формуле:
гдеЦПРИ – цена приспособления руб;
Кз.о. – коэффициент загрузки оборудования.
Расчет производим для оснастки служащей больше года.
Полученные значения капитальных вложений сводим в таблицу .
Таблица 35 - Базовый вариант
Стоимость оборудования Ц руб.
Таблица 36 - Проектный вариант
Сверлильно-фрезерно-расточная с ЧПУ
Вертикально-сверлильная с ЧПУ
Таблица 37 - Капитальные вложения
Вид капитальных вложений
вариант базовый руб.
Отклонения проектный вар.-базовый вар. руб.
Капитальные вложения в оборудование
Капитальные вложения в произв. площади
Капитальные вложения в приспособления
Суммарные капитальные вложения
2 Расчет технологической себестоимости по прямым затратам
2.1 Расчет заработной платы рабочих-станочников
Расчёт заработной платы рабочих станочников с учётом вычетов на социальные программы рассчитывается по формуле:
гдеЧС – часовая тарифная ставка руб.ч;
ТШТ - штучно время на операцию;
К1 – коэффициент учитывающий дополнительную заработную плату;
К2 – коэффициент учитывающий премиальные доплаты;
К3 – коэффициент учитывающий поясные доплаты;
К4 – коэффициент учитывающий отчисления на социальные программы;
К5 – коэффициент учитывающий доплаты за многостаночность работы.
Расчет ведется по операциям.
По данным [9] К1=112 К2=15 К3=12 К4=127.
2.2 Расчет заработной платы рабочих-наладчиков
гдеЧН – часовая тарифная ставка наладчика рубч;
НОБ – норма обслуживания станков наладчиками;
К4 – коэффициент учитывающий отчисления на социальные программы.
По данным завода ЧН=2955 руб. НОБ=5К1=112 К2=15 К3=12 К4=127.
2.3 Расчет затрат на электроэнергию
Затраты на силовую электроэнергию определяются по формуле:
гдеЦЭ – цена 1- го кВт×ч руб(кВтч);
W – мощность электродвигателя привода главного движения кВт;
Квр – коэффициент загрузки электродвигателя по времени;
Кw – коэффициент загрузки электродвигателя по мощности;
Кпот – коэффициент учитывающий потери электроэнергии в сети;
Код – коэффициент учитывающий одновременность работы электродвигателей.
По данным завода ЦЭ=436 руб(кВтч) Кпот=104.
Результаты вычислений занесем в таблицы.
Таблица 38 - Базовый вариант
Часовая тарифная ставка часруб
Зп станочника Зп руб
Таблица 39 - Проектный вариант
Расчёт затрат на технологическое обслуживание и ремонт технологического оборудования эксплуатацию станочных приспособлений режущий инструмент не сильно отражается на определении технологической себестоимости изготовления детали поэтому данными видами расчетов можно пренебречь.
2.4 Расчет амортизации основных фондов
Амортизационные отчисления по оборудованию.
Амортизация на полное восстановление капитальных вложений в оборудование:
гдеНР – норма амортизации оборудования на полное восстановление;
КОБ – удельные капитальные вложения в технологическое оборудование.
По заводским данным НР=15%.
Амортизационные отчисления по производственной площади
гдеНПЛ – норма амортизационных отчислений на реновацию по производственным площадям;
КПЛ – удельные капитальные вложения в производственные площади.
По заводским данным НПЛ=5%.
Результаты расчетов заносим в таблицы.
Таблица 40 - Базовый вариант
Таблица 41 - Проектный вариант
Итоговые полученные результаты занесем в таблицу.
Таблица 42 - Технологическая себестоимость изготовления детали
Затраты на основные материалы руб
Зарплата станочников руб.
Зарплата наладчиков руб
Затраты на электроэнергию руб
Удельная технологическая себестоимость руб
3 Расчет приведенных затрат и выбор варианта.
Расчет удельных приведенных затрат по сравниваемым вариантам выполняется по формуле (51). После чего делается выбор варианта у которого получились наименьшие приведенные затраты.
ПЗ1=265095+0152629103065 руб.(базовый)
ПЗ2=226211+0152313982625 руб.(проектный)
Так как ПЗ2ПЗ1 то проектный вариант выгоднее. Экономический эффект от внедрения проектируемого варианта определяем по формуле:
Э=(ПЗ2-ПЗ1)N=(3065-2625)2950=1298 000 (руб.).
4 Технико-экономические показатели проекта
Завершающим этапом проекта является определение технико-экономических показателей позволяющих видеть преимущества выбранного технологического процесса обработки детали. Технико-экономические показатели сводятся в таблицу.
Таблица 43 - Технико-экономические показатели проекта
Удельная технологическая себестоимость руб.
Удельные капитальные вложения руб.
Удельные приведенные затраты руб.
Безопасность жизнедеятельности
Безопасность жизнедеятельности (БЖД) — наука о комфортном и травмобезопасном взаимодействии человека с техносферой. Дисциплина "БЖД" интегрирует области знаний по охране труда (ОТ) охране окружающей среды (ООС) и гражданской обороне (ГО). Объединяющим ее началом стали: воздействие на человека одинаковых по физике опасных и вредных факторов среды его обитания общие закономерности реакций на них у человека и единая научная методология а именно количественная оценка риска несчастных случаев профессиональных заболеваний экологических бедствий и т.д.
Целью БЖД является снижение риска возникновения чрезвычайных ситуаций по вине человеческого фактора. Существуют три основные задачи БЖД:
Идентификация вида опасности с указанием её количественных характеристик и координат.
Защита от опасности на основе сопоставления затрат и выгод.
Ликвидация возможных опасностей исходя из концентрации и остаточного риска и ликвидация последствий воздействия на человека опасности.
БЖД базируется на достижениях и таких наук как психология эргономика социология физиология философия право гигиена теория надежности акустика и многие другие. В итоге эта дисциплина рассматривает вопросы по БЖД со всех точек зрения т.е. комплексно решает исследуемый вопрос.
Проблемы обеспечения безопасности человека остро проявляются непосредственно на предприятии. Их можно условно разделить на проблемы:
Характерные для любого объекта хозяйственной деятельности.
Связанные со спецификой технологических процессов организации производства и размещением предприятия.
Сложность технологических процессов высокие требования к точности технологических режимов в значительной мере исключают возможность воздействия на технологические процессы для повышения безопасности.
Поэтому центр тяжести мероприятий переносится на создание новых технологий а также устройств снижающих вредное влияние технологических процессов на обслуживающий персонал на создание эффективных организационных и управленческих воздействий.
2 Правовые и организационные основы охраны труда
Охрана труда— система сохранения жизни и здоровья работников в процессе трудовой деятельности включающая в себя правовые социально-экономические организационно-технические санитарно-гигиенические лечебно-профилактические реабилитационные и иные мероприятия.
Законодательство РФ об охране труда основывается на Конституции РФ принятой 12 декабря 1993 года в статье 37 которой провозглашено: “Каждый имеет право на труд в условиях отвечающих требованиям безопасности и гигиены”.
)Основные требования по охране труда изложены в следующих нормативных актах:
)Конституция Российской Федерации (с. 37)
)Трудовой кодекс Российской Федерации (раздел X Охрана труда)
)Административный кодекс РФ
)Гражданский кодекс РФ (части 1 и 2)
)Уголовный кодекс РФ (ст. 8 16 143 145 и др.).
)ГОСТ 12.3.002-75. Процессы производственные. Общие требования безопасности ССБТ.
)ГОСТ 12.2.003-75. Оборудование производственное. Общие требования безопасности ССБТ.
)ПОТ РМ-002-97 Межотраслевые правила по охране труда в литейном производстве (заливка слитков требования к производственным помещениям пожаро- и взрывобезопасность требования к оборудованию разливочные ковши плавильное оборудование требования к размещению оборудования и рабочих мест требования к применению средств защиты работников).
)ПОТ РО-14000-001-98 Правила по охране труда на предприятиях в организациях машиностроения.
Ответственность за состояние охраны труда в организации несет работодатель.
Должностные лица и специалисты виновные в нарушении настоящих Правил несут личную ответственность в соответствии с действующим законодательством за допущенные нарушения независимо от того привели или не привели эти нарушения к аварии или несчастному случаю.
В зависимости от характера нарушений и их последствий должностные лица несут ответственность в дисциплинарном административном и уголовном порядке в соответствии с законодательством Российской Федерации.
Административная ответственность
За нарушение законодательства по охране труда выражается в наложении штрафа на виновное должностное лицо. К административной ответственности привлекаются должностные лица допустившие нарушения трудового законодательства норм и правил охраны труда.
Материальная ответственность
За нарушение законодательства по охране труда работник может быть привлечен к материальной ответственности если по его вине предприятие (учреждение) понесло материальный ущерб (ст. 400 ТК). При определении размера ущерба учитывается только прямой действительный ущерб неполученные доходы не учитываются. Работник причинивший ущерб может добровольно возместить его полностью или частично. С согласия нанимателя он имеет право передавать для возмещения ущерба равноценное имущество или исправить поврежденное.
Материальная ответственность - возмещение ущерба поэтому не исключена возможность одновременного привлечения к дисциплинарной административной или уголовной ответственности (ст. 408 ТК).
Уголовная ответственность
УК РФ предусмотрена ответственность за действия которые грубо попирают положения законодательства о труде и охране труда либо которые повлекли за собой значительные негативные последствия например причинение вреда здоровью либо гибель людей.
3 Опасные и вредные факторы
Основными опасными и вредными производственными факторами в литейном производстве являются:
)повышенная запыленность и загазованность воздуха рабочей зоны;
)нарушения температурного режима воздуха рабочей зоны повышенная температура поверхностей оборудования отливок расплавленный металл;
)повышенные уровни шума и вибрации;
)подвижные части производственного оборудования перемещающееся транспортное и грузоподъемное оборудование и транспортируемые грузы;
)недостаточная освещенность;
)стесненность на производственных площадях;
)перенапряжение зрительного анализатора;
)физические перегрузки и др.
4 Общие требования к материалам производственному оборудованию и организации рабочих мест
Производственные помещения в которых осуществляются процессы обработки резанием должны соответствовать СН и П -2-80 СН и П -89-80 и санитарным нормам проектирования промышленных предприятий СН 245-71. Бытовые помещения должны соответствовать требованиям СН и П -92-76. Все помещения должны быть оборудованы средствами пожаротушения по ГОСТ 12.4.009-83.
По ГОСТ 12.2.009-80 «Станки металлорежущие. Общие требования безопасности» регламентируются требования на все группы изготавливаемых и находящихся в эксплуатации металлорежущих электрофизикохимических станков автоматических линий а также применяемых совместно с ними устройств подключаемых к питающей сети с номинальным напряжением до 660В и частотой до 220Гц.
Станки должны отвечать требованиям безопасности в течение всего периода эксплуатации при выполнении потребителем требований установленных в эксплуатационной документации по ГОСТ 12.2.003-91. Используемые в расчетах характеристики станка (мощность частота вращения шпинделя и т.д.) выбраны из паспорта. Размещение коммуникаций производственного оборудования исходных материалов заготовок готовой продукции и отходов производства в помещениях не должно создавать опасных рабочих условий – в соответствии с ГОСТ 12.3.002-75. Разработанная технологическая документация организация и выполнение технологического процесса резанием соответствует требованиям ГОСТ 3.1102 и 12.3.025-80.
Форма станков и их элементов должны обеспечивать удобный отвод стружки и СОЖ из зоны обработки и удаление стружки от станка.
Для охлаждения поверхности обработки применяется 3-5% эмульсия из Эмульсола Укринол – 1М либо водная эмульсия ВЕЛЛС-1. СОЖ подается в зону резания методом распыления с помощью сопла рекомендуемого ГОСТ 12.3.025-80 для снижения количества аэрозоли. Все зоны резания имеют защитные ограждения в соответствии с ГОСТ 12.2.062-81 но для защиты кожи рабочих от воздействия СОЖ при измерении или уборке станка рабочий использует перчатки и средства индивидуальной защиты соответствующие требованиям ГОСТ 12.4.011-89. Отработанные СОЖ и промывные воды собираются в специальных емкостях и сбрасываются в общую систему канализации только после очистки их от нефтепродуктов.
При разработке технологического процесса предусмотрена рациональная организация рабочих мест удобное расположение инструментов в приспособлении соответствуют требованиям ГОСТ 12.2.029-88. Инструменты и приспособления располагаются в тумбочках и на стеллажах. Станки располагаются в соответствии с требованиями стандартов. Заготовки помещаются в специализированную тару. Эти меры позволяют снизить производственный травматизм.
5 Производственная санитария
Условия труда на рабочих местах производственных помещений складываются под воздействием большого числа факторов различных по своей природе формам проявления характеру действия на человека.
В соответствии с ГОСТ 12.0.003-86 опасные и вредные производственные факторы подразделяются по своему действию на физические химические биологические и психофизические.
6 Анализ опасных и вредных производственных факторов при механической обработке деталей
Выбор технических средств обеспечения безопасности должен осуществляться на основе выявления опасных и вредных факторов специфичных для данного технологического процесса.
Физически вредными производственными факторами являются повышенная запыленность воздуха рабочей зоны в процессе обработке детали; высокий уровень шума и вибраций недостаточная освещенность рабочей зоны; повышенная пульсация светового потока. При отсутствии средств защиты запыленность воздушной среды в зоне дыхания станочников при точении фрезеровании шлифовании может превышать предельно допустимые концентрации.
Аэрозоль нефтяных масел входящих в состав смазочно-охлаждающих жидкостей (СОЖ) может вызвать раздражение слизистых оболочек верхних дыхательных путей способствовать снижению иммунобиологической реактивности.
Движущиеся части производственного оборудования передвигающиеся изделия и заготовки стружка обрабатываемых материалов осколки инструментов высокая температура поверхности обрабатываемых деталей и инструмента повышенное напряжение в электроцепи или статического электричества при котором может произойти замыкание через тело человека – относятся к категории физически опасных и вредных факторов. Участок должен быть защищен от доступа на него посторонних лиц. В соответствии с ГОСТ 12.1.030-81 с целью обеспечения электробезопасности в конструкции электроприводов станков предусмотрена изоляция. На нетоковедущих частях оборудования (корпусах) обязательно применяется заземление контроль которого необходимо проводить не реже чем раз в 2 года.
Металлическая стружка имеющая высокую температуру (400-600°С) и большую кинетическую энергию представляет серьезную опасность не только для работающего на станке но и для лиц находящихся вблизи станка. Наиболее распространенными у станочников являются травмы глаз. Глаза повреждаются отлетающей стружкой осколками режущего инструмента и частицами абразива пылевыми частицами обрабатываемого материала и др.
В процессе механической обработки материалов при работе тупыми режущими инструментами происходит интенсивное нагревание вследствие чего пыль и стружка превращается в парообразное состояние.
Таким образом при обработке материала в воздух рабочей зоны поступает сложная смесь аров газов и аэрозолей являющихся химически вредными производственными факторами.
Концентрация вредных веществ в воздухе рабочей зоны образующихся при обработке резанием не должны превышать предельно допустимых значений (ПДК).
К вредным психофизическим производственным факторам процессов обработки материалов резанием можно отнести физические перегрузки при установке закреплении и съеме крупногабаритных деталей перенапряжение зрения монотонность труда.
К биологическим факторам относятся болезнетворные микроорганизмы бактерии проявляющиеся при работе с СОЖ.
Эффективным средством нормализации воздушной среды является вентиляция.
По характеру организации воздухообмена различают общеобменную и местную вентиляцию в зависимости от назначения: приточную вытяжную приточно-вытяжную.
Действие общеобменной вентиляции основано на разбавлении выделяющихся вредных веществ свежим воздухом до предельно допустимых концентраций.
С целью более эффективного улавливания пыли мелкой стружки и аэрозолей СОЖ образующихся при обработке резанием применяют местные отсасывающие устройства со специальными насадками которые размещают в местах интенсивного выделения вредных веществ. Воздухоотводы для удаления пыли должны иметь гладкие внутренние поверхности без карманов и углублений минимальную длину и число поворотов.
Для снятия зарядов статического электричества пылеприемники и воздухоотводы вентиляционных установок заземляют по ГОСТ 12.3.026-86.
В соответствии с требованиями СН и П. -33-86 ворота двери и технологические проемы механических цехов оборудуют воздушными и воздушно-тепловыми завесами которые защищают работников от охлаждения проникающим в цех холодным воздухом.
Воздухоотводы от местных отсосов и общеобменной вентиляции а также вентиляционные камеры должны очищаться по графику утвержденному администрацией цеха.
Шум и вибрации являются вредными основными производственными факторами в механических цехах и должны соответствовать СН. 2.2.42.1.8.562-96.
Шум на производстве наносит большой экономический и социальный ущерб. Он неблагоприятно воздействуя на организм человека вызывает психические и физиологические нарушения снижающие работоспособности человека.
Источниками шума являются колеблющиеся твердые жидкие газообразные тела. Основные источники шума в металлорежущих станках – это зубчатые передачи электродвигатель и процесс резания.
Основополагающим документом устанавливающий классификацию шумов допустимые уровни шума на рабочих местах общие требования к шумовым характеристикам машин и защита от шума является ГОСТ 12.3.003-83.
Зоны с уровнем звука свыше 80дБА должны быть обозначены знаками безопасности. Станочников постоянно находящихся в этих зонах администрация обязана снабжать средствами индивидуальной защиты органов слуха.
При выборе тех или иных средств борьбы с шумом следует практиковать такие которые уменьшают уровень шума непосредственно в источнике его образования следует использовать глушители звукоизоляцию звукопоглощающие облицовки потолка и стен объемные поглотители подвешиваемые вблизи наиболее шумных станков. Толщина облицовок составляет 20-200мм.
В процессе резания шум можно снизить повышением жесткости инструмента демпфированием колебания заготовки и инструмента.
Самый эффективный метод снижения шума является оснащение станка подвижным звукоизолирующим кожухом герметично закрывающим зону резания.
Причиной возбуждения вибраций при работе станков являются неуравновешенные силовые воздействия.
В одних случаях они возникают при вращении шкивов маховиков и валов в других – при использовании механизмов с возвратно-поступательным движением.
Вибробезопасные условия труда станочников обеспечивают в основном организационно-технологическими мероприятиями которые включают:
- контроль за соблюдением правил и условий эксплуатации станков в соответствии с нормативно-технической документацией;
- контроль технических норм вибрации в соответствии с ГОСТ 12.3.1012-78
- своевременный плановый и предупредительный ремонт станков с обязательным послеремонтным контролем их вибрационных характеристик;
- внедрение мер исключающих возможность контакта станочников с вибрирующими частями оборудования.
9 Электробезопасность
Основными причинами воздействия электрического тока на рабочего являются:
- случайное прикосновение или приближение на опасное расстояние к токоведущим частям;
- появление напряжения на металлических частях оборудования в результате повреждения изоляции или ошибочных действиях персонала;
- шаговое напряжение на поверхности земли в результате замыкания провода и др.
Основными мерами защиты от поражения током являются:
- недоступность токоведущих частей оборудования;
- электрическое разделение сети с помощью специальных разделяющих трансформаторов;
- выравнивание потенциала;
- защитное заземление и зануление;
- защитное отключение;
- применение специальных электрозащитных средств;
- организация безопасной эксплуатации электроустановки.
10 Смазочно-охлаждающие жидкости
Использованные и отработанные СОЖ необходимо собирать в специальные емкости. Водную и масляную фазы можно использовать для приготовления эмульсий. Масляная фаза может поступать на регенерацию или сжигаться. Концентрация нефтепродуктов в сточных водах при сбросе их в канализацию должна соответствовать требованиям СН и П. -32-84. Мелкая масляная стружка и пыль по мере накопления подлежит сжиганию или захоронению на специальной площади.
11 Санитарно-гигиенические требования и условия труда
В таблице приведены санитарно-гигиенические требования и условия труда для категории тяжести труда II б.
Таблица 38 - Санитарно-гигиенические требования и условия труда
Скорость движения воздуха мс
Интенсивность тепловой радиации Втм2
Газовый состав воздуха: Кислород % (по объему)
Углекислота % (по объему)
Вредные примеси ПДК м2м3:1. Аэрозоли масла
Уровень шума общий дБА
Уровень общей вибрации на рабочем месте дБА
Уровень местной вибрации на рабочем месте дБА
Предельный спектр дБ
Естественное освещение при разряде работы –3 К.Е.О. %
Электрическое освещение при разряде работы 3-4 освещенность
12 Пожарная безопасность
Помещение где происходит обработка металлов резанием по СНиП 11-2-80 относится к категории В. Обеспечение пожарной безопасности является одной из важнейших задач охраны труда. Требования пожарной безопасности определяет ГОСТ 12.1.004-85.
Основными причинами пожаров на производстве являются нарушения связанные с технологическим режимом применения горючих и легковоспламеняющихся жидкостей и горючих газов.
Для практической реализации профилактических мер на предприятии организуют постоянно действующую пожарно-техническую комиссию добровольную пожарную дружину утверждают категорию пожарной и взрывной опасности цехов и участков разрабатывают для них противопожарный режим.
Все станочники проходят первичный и повторный противопожарный инструктаж. Мероприятия устраняющие причины пожаров на предприятии подразделяются на строительно-технические и организационные. К первым относятся планировка территории и размещение производственных зданий и сооружений устройство в здании специальных преград препятствующих распространению огня аварийное освещение надлежащая эксплуатация производственного оборудования. К организационным мероприятиям относятся: запрещение курения и пользование открытым огнем при проведении работ в пожароопасных помещениях ограничение запасов сгораемого сырья готовой продукции удаление из производственных помещений легковоспламеняющихся материалов разработка планов эвакуации людей и имущества из помещений.
Для борьбы с пожаром применяются огнегасительные вещества такие как вода водные растворы пена углекислота инертные газы сжатый воздух порошки песок земля и т.д. и средства тушения пожара установленные ГОСТ 12.4.009-91.
В помещении располагают стационарные и первичные средства пожаротушения. На каждых 100 квадратных метрах помещения размещается 1-2 огнетушителя. В каждом помещении имеются эвакуационные выходы.
13 Заключение по разделу
Таким образом рабочее место токаря должно соответствовать действующим нормативным документам нормам и правилам обеспечив индивидуальную и коллективную безопасность.
В ходе дипломной работы был проанализирован вариант производства детали корпус – крупносерийное производство. Был предложен проектный вариант механической обработки детали в результате:
а) выбран маршрут механической обработки с применением станков с ЧПУ
- уменьшилось время на холостые перемещения;
- исключена дорогостоящая вертикально-шлифовальная операция - заменена на полировальный переход в сверлильно-фрезерно-расточной операции так как шлифовать данную поверхность (отверстия) не было необходимости;
б) применен прогрессивный режущий инструмент Iscar
- уменьшилось основное технологическое время механической обработки на сверлильно-фрезерно-расточной операции с ЧПУ;
В ходе дипломной работы для проектного варианта механической обработки
- выбран метод получение заготовки – литье в металлические формы;
- проанализированы варианты базирования заготовки на различных операциях;
- выбрано технологическое оснащение – режущий мерительный вспомогательный инструменты и приспособления;
- рассчитаны режимы резания при механической обработке;
- вычислено технологическое время; разработано приспособление для зажима заготовки при обработке на сверлильно-фрезерно-расточном станке с ЧПУ.
В итоге была разработана технологическая документация – операционный и маршрутный технологический процесс и карта эскизов.
Были посчитаны технико-экономические показатели проекта в ходе которых проектный вариант имеет годовой экономический эффект около 1 млн. руб.
Анухин В. И. Допуски и посадки. Выбор и расчёт указание: Учеб. пособие. 2-е изд. перераб. и доп. СПб.: Изд-во СПбГТУ 2001. 219 с.
Баранчиков В.И. Тарапанов А.С. Харламов Г.А. Обработка специальных материалов в машиностроении: Справочник. Библиотека технолога. – М.: Машиностроение 2002. 264 с.: ил.
Белоусов А.П. Проектирование станочных приспособлений: Учебное пособие для учащихся техникумов. – 3-е изд. переработ. доп. – М.: высш. школа 1980. – 240 с. ил.
Горбацевич А. Ф. Шкред В. А. Курсовое проектирование по технологии машиностроения: - 4е изд. перераб. и доп.-Мн.: Высш. школа 1983.
Дунаев П.Ф. Конструирование узлов и деталей машин: Учеб. пособие для студ. техн. спец. вузовП.Ф. Дунаев О.П. Леликов.– 8-е изд. перераб. и доп.– М.: Издательский центр «Академия» 2003.– 496 с.
Курсовое проектирование деталей машинВ.Н Кудрявцев и др.; под общей ред. В.Н. Кудрявцева: Учебное пособие для студентов машиностроительных специальностей вузов. – Л.: машиностроение 1984. 400 с. ил
Сборник задач и упражнений по технологии машиностроения: Учеб. пособие для машиностроит. вузов по спец. «Технология машиностроения» «Металлорежущие станки и инструменты» В. И. Аверченков О. А. Горленко В. Б. Ильицкий и др.; Под общ. ред. О. А. Горленко.– М.: Машиностроение 1988.– 192 с.; ил.
Справочник нормировщика Стружестрах.
Справочник технолога – машиностроителя. В 2-х т. Под ред. А.М. Дальского А.Г. Косиловой и др. 5-е изд. М.: Машиностроение – I 2003 г. 944 с. ил..
Технология машиностроения. В 2 т. Учебник для вузов В.М. Бурцев А.С. Васильев А.М. Дальский и др.; Под ред. А.М. Дальского. – 2-е изд. стерео-тип. – М.: Издательство МГТУ им. Н.Э. Баумана 2001.
Технология машиностроения (специальная часть): Учебник для машиностроительных специальностей вузовА.А. Гусев Е.Р. Ковальчук И.М. Колесов и др.– М.: Машиностроение 1986.– 480 с.
Технологичность конструкции деталей изготовляемых механической обработкой: Метод. указания. Сост. А.Б. Трухачёв Москва.
Методические указания по выполнению курсовой работы по курсу «Организация планирование и управление предприятием». Сост. Т.В. Янцен.- Москва 1994.
ГОСТ 26645-85. Отливки из металлов и сплавов. Допуски размеров массы и припуски на механическую обработку.
ГОСТ 3.1125-88. Единая система технологической документации. Правила графического выполнения элементов литейных форм и отливок.
_Приспособление расточное_2.cdw

Корпуса гидромеханизма
Техническая характеристика
Приспособление предназначено установки детали Корпус на
столе станка 2206ВМФ4.
Давление в пневмосистеме
Класс загрязненности
сжатого воздуха по ГОСТ 17433-80
Периодичность технического
* Уточняется в процессе эксплуатации при проведении
очередного технического освидетельствования.
Технические требования
Размеры для справок.
Трущиеся поверхности периодически покрывать смазкой
ЦИАТИМ 221 ГОСТ 6267-74.
Приспособление испытать пробным давлением 0
течение 15 минут. Утечки воздуха
деталей пневмосистемы свыше регламентированной температуры
Подвижные части приспособления должны перемещаться
Произвести пробную обработку детали-макета. Произвести
контроль размеров обработанной детали согласно
технологическому процессу.
Маркировать по СТП предприятия-изготовителя:
наименование изделия;
наименование обрабатываемой детали;
Остальные ТТ по СТП предприятия-изготовителя.
Обрабатываемая деталь
Рекомендуемые чертежи
- 24.01.2023
- 05.01.2022
- 15.09.2016