Проектирование цилиндрического зубчатого редуктора цепной передачи




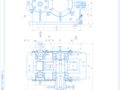
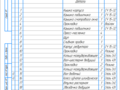
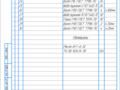
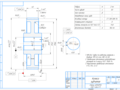
- Добавлен: 24.01.2023
- Размер: 358 KB
- Закачек: 0
Описание
Проектирование цилиндрического зубчатого редуктора цепной передачи
Состав проекта
![]() |
![]() ![]() ![]() ![]() |
![]() ![]() ![]() ![]() |
![]() ![]() ![]() |
![]() ![]() ![]() ![]() |
![]() ![]() ![]() ![]() |
![]() ![]() ![]() ![]() |
Дополнительная информация
Чертеж шестерня.cdw

Коэффициент смещения
Степень точности по ГОСТ 1643-72
2. Зубья по рабочему профилю и
Предельные отклонения штамповочных
размеров по II классу ГОСТ 7505-74.
Неуказанные предельные отклонения
Спецификация 2.cdw

Подшипник 308 ГОСТ 8338-75
Болт М6 ГОСТ 7798-70
Шайба пружинная 6 ГОСТ 6402-70
Болт М10 ГОСТ 7798-70
Шайба пружинная 10 ГОСТ 6402-70
Гайка М10 ГОСТ 5915-70
курсовой по деталям машин.doc
потребительской кооперации
Кафедра оборудования предприятий торговли
и общественного питания
ПРОЕКТИРОВАНИЕ ЦИЛИНДРИЧЕСКОГО
ЗУБЧАТОГО РЕДУКТОРА ЦЕПНОЙ ПЕРЕДАЧИ
Пояснительная записка
к курсовой работе по деталям машин
Техническое задание на проектирование3
Расчет одноступенчатого цилиндрического прямозубого редуктора3
1.Выбор электродвигателя и кинематический расчет4
2.Расчет прочностных параметров зубчатой передачи6
3.Расчет параметров зубчатой передачи8
4.Проверочные прочностные расчеты10
5.Предварительный расчет валов редуктора11
6.Конструктивные размеры шестерни колеса и корпуса редуктора14
7.Расчет цепной передачи14
8.Первый этап компоновки редуктора16
9.Расчет долговечности подшипника и проверка диаметров валов17
10.Второй этап компоновки редуктора23
11.Проверка прочности шпоночных соединений24
12.Посадки зубчатого колеса звездочки и подшипников25
13.Выбор сорта масла25
Список использованной литературы26
Техническое задание на проектирование
Спроектировать одноступенчатый цилиндрический редуктор и рассчитать цепную передачу для привода ленточного конвейера (рис. 1).
Редуктор должен работать 8ч в сутки 300 дней в году в течение 10 лет режим нагружения (средний вероятный) кратковременная перегрузка не превышает двух номинальных моментов. Редуктор изготовлен в отдельном закрытом корпусе смазка – погружением колес в масляную ванну. Цепная передача расположена под углом 45° к горизонту.
Рис. 1 Схема привода конвейера
Расчет одноступенчатого цилиндрического прямозубого редуктора
Исходные данные для проектирования:
тяговое усилие ленты F=15 кН;
скорость ленты =13 мс;
диаметр приводного барабана D=300 мм;
прямозубая цилиндрическая передача;
режим работы: 8 ч в сутки 300 дней в году в течение 10 лет режим нагружения (средний равновероятный) кратковременная перегрузка не превышает двух номинальных моментов;
цепная однорядная роликовая передача расположена между зубчатым редуктором и барабаном ленточного конвейера под углом 45°.
1.Выбор электродвигателя и кинематический расчет
Потребляемая мощность электродвигателя:
где Ft – окружная сила на барабане ленточного конвейера Н; – скорость движения ленты мс.
где ц – КПД цепной передачи; з – КПД зубчатой передачи; м – КПД муфты; оп – КПД опор приводного вала (одной пары подшипников качения) (КПД определяем по табл. 1 прил. 1 [1]).
Требуемая мощность электродвигателя:
Угловая скорость барабана:
где D – диаметр барабана м.
Частота вращения приводного вала конвейера:
Требуемая частота вращения вала электродвигателя при одноступенчатом редукторе:
где и1 и2 - передаточные числа кинематических пар привода рекомендуемые значения которых (ирек) приведены в табл. 2 [1] (выбраны ицеп=225 – для цепной передачи и итих=43 – для зубчатой пары одноступенчатого редуктора).
По табл. 3 [1] выбираем электродвигатель типа АИР100L6945 мощностью 22 кВт и асинхронной частотой вращения n=945 обмин. (При подборе электродвигателя по мощности допускается его перегрузка до 8% при постоянной и 12% при переменной нагрузке).
Уточнение передаточных чисел привода.
Общее передаточное число привода:
Передаточное число цепной передачи ицеп=225 тогда передаточное число редуктора:
(принимается равным иред=5 из стандартного ряда табл. 4 [1]).
Определяем частоты вращения и угловые скорости валов редуктора и барабана:
для вала шестерни муфты и вала электродвигателя:
)для вала зубчатого колеса и быстроходной звездочки цепной передачи:
)для вала барабана ленточного конвейера и тихоходной звездочка цепной передачи:
Рассчитываем вращающие моменты:
)на приводном валу барабана ленточного конвейера:
)на валу зубчатого колеса:
)на валу шестерни и электродвигателя:
2.Расчет прочностных параметров зубчатой передачи
Желая получить сравнительно небольшие габариты и невысокую стоимость редуктора выбираем для изготовления колеса и шестерни сравнительно недорогую легированную сталь 40Х (поковка). По табл. 5 [1] назначаем для колеса термообработку: улучшение твердости поверхности до 230 260 НВ с пределом прочности В=850 МПа пределом текучести Т=550 МПа для шестерни – улучшение 260 280 НВ В=950 МПа Т=700 МПа. При этом обеспечивается приработка зубьев обеих ступеней по формуле
где Н1 Н2 – соответственно твердости шестерни и колеса (т.е. твердость шестерни рекомендуется назначать больше твердости колеса не менее чем на 101 15 единиц).
Определение допускаемых напряжений
Допускаемые контактные напряжения
По табл. 5 [1] для зубчатого колеса предел выносливости по контактным напряжениям:
Число циклов напряжений или ресурс передачи для зубчатого колеса определяем по формуле
где n2=189 обмин – частота вращения выходного вала
tΣ=10лет·300дней·8ч=24000ч – срок службы передачи.
По табл. 7 [1] определяем коэффициент КНЕ=025 для 2-го режима работы. Для колеса циклическая долговечность или эквивалентное число циклов до разрушения:
Базовое число циклов соответствующее перелому кривой усталости определяем по средней твердости поверхности зубьев колеса:
Сравнивая NНЕ и NОН отмечаем что для колеса NНЕ ≥ NОН (675·107≥205·107). Так как шестерня вращается быстрее то аналогичным расчетом получим и для нее NНЕ ≥ NОН. При этом для всех колес передачи коэффициент долговечности:
Допускаемые контактные напряжения определяем по материалу колеса как более слабому:
где НО=550 МПа – предел выносливости зубчатого колеса SH=11 – коэффициент безопасности.
Допускаемые напряжения изгиба
Определяем допускаемое напряжение изгиба при расчете на усталость по формуле:
где F0 – предел выносливости зубьев по напряжениям изгиба (табл. 6 [1]) SF – коэффициент безопасности (рекомендуется SF=155 175) КFC – коэффициент учитывающий влияние двустороннего приложения нагрузки (в наших расчетах КFC=10 – односторонняя нагрузка КFC=070 08 – реверсивная нагрузка) КFL – коэффициент долговечности методика расчета его аналогична расчету КHL (для наших расчетов КFL=1 для колеса и шестерни).
По табл. 6 [1] для колеса
Предварительно по табл. 7 [1] находим КFЕ=014 для 2-го режима нагрузки (и m=6 при твердости 350НВ) и эквивалентное число циклов:
По табл. 6 [1] коэффициент безопасности SF=175.
Допускаемые напряжения при кратковременной нагрузке
По табл. 6 [1] предельные контактные напряжения:
Предельные напряжения изгиба:
3.Расчет параметров зубчатой передачи
Предварительный расчет межосевого расстояния (аW) выполняем по формуле:
где и=5 – передаточное отношение редуктора;
(при Е1=Е2=21·105) – приведенный модуль упругости Е1 Е2 – модули упругости зубчатых колес Т2=109·103 Нмм [Н]=500 МПа. По рекомендациям табл. 8 [1] принимаем коэффичиент ширины колеса (при симметричном расположении колес относительно опор) и рассчитываем коэффициент ширины шестерни:
По табл. 9 [1] находим коэффициент Кнb=111.
Подставляя эти значения получаем межосевое расстояние:
Принимаем стандартное межосевое расстояние (аW=100мм) из ряда (табл. 10 [1]) и находим ширину зубчатого колеса:
Ширину колеса округляем до стандартного ближайшего значения (табл. 11 [1]): b2=40мм.
Ширину шестерни принимаем на 5 мм больше:
Определяем модуль зубчатой передачи:
Из нормализованного ряда (табл. 13 [1]) выбираем стандартный ближайший модуль меньшего значения: m=20 мм.
Суммарное число зубьев:
Число зубьев шестерни:
Проверка: (по условию недопущения подрезания зубьев принимаем число зубьев ).
Число зубьев колеса:
Фактическое передаточное число:
(находится в пределах допустимого отклонения 3% от номинального).
Делительные диаметры шестерни и колеса:
Проверка межосевого расстояния:
Диаметры вершин зубьев шестерни и колеса:
Диаметры впадин зубьев шестерни и колеса:
4.Проверочные прочностные расчеты
Выполняем проверочный расчет зубчатого колеса по контактным напряжениям как более слабого по допускаемым контактным напряжениям.
Частота вращения зубчатого колеса n2=189 обмин окружная скорость:
По табл. 14 назначаем 9-ю степень точности: nст=9.
Определяем коэффициент расчетной нагрузки:
где КН определяем по табл. 15 [1] (принимаем КН=11) а коэффициент КНa определяем по формуле:
Учитывая что для нашего редуктора угол зацепления находим расчетное контактное напряжение:
Условие контактной прочности выполняется поэтому ширина колес не изменяется.
Силы в зацеплении для прямозубых колес:
Радиальная сила (для стандартного угла a=20°):
Выполняем проверочный расчет по напряжениям изгиба:
По табл. 16 [1] находим коэффициент формы зуба: для шестерни (количество зубьев ) для колеса (количество зубьев ) .
Расчет выполняем по тому колесу у которого меньше .В нашем случае для шестерни: для колеса: . Расчет выполняем по шестерне.
Рассчитываем коэффициент: По табл. 15 [1] для 9-й степени точности . Принимаем .
Рассчитываем коэффициент нагрузки:
Определяем напряжение изгиба по формуле:
Отмечаем что для данной пары колес основным критерием работоспособности является контактная а не изгибающая прочность.
Итак мы определили параметры зубчатой передачи редуктора:
5.Предварительный расчет валов редуктора
Предварительные значения диаметров стальных валов редуктора определяем по прочности на кручение:
где t - касательные напряжения Мk = Т – крутящий или вращающий момент на валу - допускаемые касательные напряжения - полярный момент сопротивления вала.
Из этого условия прочности определяется допускаемый диаметр вала:
Для быстроходного (входного) вала
Для тихоходного (выходного) вала
Эти значения округляем до стандартных размеров (табл. 11 [1]): и проверяем на соответствие диаметров концов валов (табл. 18 [1]). Из этой же таблицы определяем стандартные длины концов быстроходного и тихоходного валов: .
Размеры диаметров участков валов:
для выходного вала:
где высоту заплечика (tцип) координату (r) фаски подшипника определяем по табл. 19 [1].
Округляем данные значения диаметров участков валов до стандартных (табл. 11 [1]):
а)под подшипники: для входного вала для выходного вала ;
Так как размеры валов под подшипники должны быть меньше размеров валов под шестерню и под колесо из условия сборки и конструктивных соображений:
По полученным данным рисуем эскизы ведущего и ведомого валов
Рис. 2а. Эскиз ведущего вала шестерни
Рис. 2б. Эскиз ведомого вала
6.Конструктивные размеры шестерни колеса и корпуса редуктора
Шестерню выполняем заодно с валом. Ее размеры:
Зубчатое колесо кованое. Его размеры: Диаметр ступицы: принимаем 70мм; длина ступицы: принимаем 60мм.
Толщина обода принимаем равной 8мм.
Толщина диска С=03b2=03·40=12 мм.
Толщина стенок корпуса и крышки редуктора:
Толщина фланцев поясов корпуса и крышки:
б)нижний пояс: принимаем
принимаем болты с резьбой М15;
б)крепящих крышку к корпусу у подшипников:
принимаем болты с резьбой М10;
в)соединяющих крышку с корпусом:
принимаем болты с резьбой М10.
7.Расчет цепной передачи
Выбираем приводную роликовую однорядную цепь.
Вращающий момент на ведущей звездочке (на вале зубчатого колеса): . Передаточное число ранее было принято: .
Число зубьев ведущей звездочки: (проверка выполнена). Число зубьев ведомой звездочки: (принимается четным) (проверка выполнена).
Расчетный коэффициент нагрузки: где - динамический коэффициент при спокойной нагрузке (передаче к ленточному конвейеру) - учитывает влияние межосевого расстояния (при t – шаг цепи) - учитывает влияние угла наклона цепи ( при углах не более 60°) - при периодическом регулировании натяжения цепи - при капельной смазке - при односменной работе. Принимаем по табл. 20 [1] среднее значение допускаемого давления в шарнирах цепи при частоте вращения вала малой звездочки
Определяем шаг однорядной цепи:
Принимаем стандартный ближайший шаг (табл. 21 [1]) ().
Скорость цепи определяем по формуле:
Межосевое расстояние:
от центробежных сил: где - коэффициент учитывающий расположение передачи - масса 1м цепи.
Расчетная нагрузка на валы:
Основные размеры ведущей звездочки:
Основные размеры ведомой звездочки:
Ступица ведущей звездочки: . Длина ступицы: принимаем 45мм. Толщина диска звездочки где - расстояние между пластинами внутреннего звена (табл. 21 [1]).
8.Первый этап компоновки редуктора
На межосевом расстоянии вычерчиваем упрощенно шестерню и колесо в виде прямоугольников шестерня выполнена заодно с валом длина ступицы колеса равна ширине венца и не выступает за пределы прямоугольника.
Очерчиваем внутреннюю стенку корпуса:
а)принимаем зазор между торцом шестерни и внутренней стенкой корпуса ;
б)принимаем зазор от окружности вершин зубьев колеса до внутренней стенки корпуса ;
в)принимаем расстояние между наружным диаметром подшипника ведущего вала и внутренней стенкой корпуса где - толщина стенки корпуса редуктора.
Предварительно намечаем радиальные шарикоподшипники средней серии. Габариты подшипников выбираем по диаметру валов в месте посадки подшипников (см. рис. 2): . По табл. 23 [1] выбираем подшипники: 305 (для ведущего вала) и 308 (для ведомого вала).
Принимаем для подшипников пластичную смазку. Устанавливаем мазеудерживающие кольца шириной .
Находим конструктивные расстояния (расчетом или непосредственно замером на чертеже):
где - ширина подшипника 305 (табл. 23 [1]);
Принимаем окончательно:
Глубина гнезда подшипников: .
Толщину фланца крышки подшипника принимаем равной .
Диаметр отверстия в крышке . Высоту головки болта примем . Длина соединительного пальца цепи .
Замером устанавливаем расстояние определяющее положение звездочки относительно ближайшей опоры ведомого вала.
9.Расчет долговечности подшипника и проверка диаметров валов
Ведущий вал (рис. 3).
Из предыдущих расчетов для прямозубой шестерни имеем: окружная сила радиальная сила из первого этапа компоновки
Определяем реакции опор:
в горизонтальной плоскости xz^
в вертикальной плоскости yz:
Строим эпюры изгибающих и крутящих моментов (см. рис. 3) и определяем наиболее опасное сечение по условию максимума моментов.
Рис. 3. Эпюры моментов для ведущего вала
Им является сечение вала в точке С в котором изгибающие и крутящие моменты составляют:
Определяем эквивалентный момент в наиболее опасном сечении С вала:
Рассчитываем допускаемый диаметр вала исходя из допускаемого напряжения на изгиб :
Принятый нами ранее диаметр ведущего вала составляет 20мм что более допускаемого диаметра следовательно условие прочности выполняется.
По диаметру вала подбираем подшипник серии 305 с параметрами (табл. 23 [1]):
Условие статической грузоподъемности выполняется так как радиальная нагрузка на подшипник (полная реакция опоры): .
Расчетная долговечность составляет:
Расчетная долговечность в часах составляет:
где n1 – частота вращения вала шестерни обмин.
Для зубчатых редукторов ресурс работы принят равным 36000 ч что на порядок ниже ресурса подшипника 305 серии (538136 ч) поэтому выбираем подшипник серии 105 (табл. П3 [2]):
Расчетная долговечность подшипников серии 105 превышает ресурс работы редуктора 36000 ч.
Ведомый вал (рис. 4).
Ведомый вал несет те же нагрузки что и ведущий: окружная сила радиальная сила но на этот вал добавляется нагрузка от цепной передачи Составляющие нагрузки от цепной передачи при угле наклона цепи 45°:
Из первого этапа компоновки: .
а)в горизонтальной плоскости xz:
относительно точки С:
относительно точки А:
б)в вертикальной плоскости yx:
Строим эпюры изгибающих и крутящих моментов (см. рис. 4) и определяем наиболее опасное сечение по условию максимума моментов. Им является сечение вала в точке С в котором изгибающие и крутящие моменты составляют:
Рассчитываем допускаемый диаметр вала исходя из допускаемого напряжения на изгиб для колеса :
Принятый нами ранее диаметр ведущего вала составляет 32 мм что более допускаемого диаметра следовательно условие прочности выполняется.
Выбираем подшипник по наиболее нагруженной опоре С серии 308 с параметрами (табл. 23 [1]):
Условие статической грузоподъемности выполняется так как радиальная нагрузка на подшипник в точке С (полная реакция этой опоры) .
Расчетная долговечность подшипников составляет:
Рис. 5. Эпюры моментов ведомого вала
где n2 – частота вращения ведомого вала обмин.
Для зубчатых редукторов ресурс работы принят равным 36000 ч что на порядок ниже ресурса подшипника 308 серии (408730 ч) поэтому выбираем подшипник серии 208 (табл. П3 [2]):
Расчетная долговечность подшипников серии 208 превышает ресурс работы редуктора 36000 ч.
10.Второй этап компоновки редуктора
Вычерчиваем шестерню и колесо по конструктивным размерам найденным раннее. Шестерню выполняем заодно с валом.
Конструируем узел ведущего вала:
а)наносим осевые линии удаленные от середины редуктора на расстояния L1. Используя эти осевые линии вычерчиваем в разрезе подшипники качения;
б)между торцами подшипником и внутренней поверхностью стенки корпуса вычерчиваем мазеудерживающие кольца их торцы должны выступать внутрь корпуса на 1-2 мм от внутренней стенки;
в)вычерчиваем крышки подшипников с уплотнительными прокладками (толщиной 1мм) и болтами;
г)переход ведущего вала от диаметра 25мм к диаметру 20мм на концевом участке выполняем на расстоянии 10-15мм от торца крышки подшипника так чтобы ступица муфты не задевала за головки болтов крепления крышки.
Аналогично конструируем узел ведомого вала.
Отложив от середины редуктора расстояние L2 проводим осевые линии и вычерчиваем подшипники мазеудерживающие кольца крышки подшипников с прокладками и болтами.
Отложив от середины редуктора расстояние L3вычерчиваем звездочку цепной передачи. От осевого перемещения звездочка фиксируется на валу торцовым креплением шайба прижимается к торцу ступицы одним или двумя винтами. Следует обязательно предусмотреть зазор между торцом вала и шайбой 2-3мм для натяга.
11.Проверка прочности шпоночных соединений
На ведущем и ведомом валах применяем шпонки призматические со скругленными торцами. Их размеры зависят от диаметров валов и принимаются по табл. 24 [1]. Материал шпонок – сталь 5 нормализованная.
Напряжения смятия и условие прочности:
Допускаемые напряжения смятия при стальной ступице из малоуглеродистой стали из среднеуглеродистой стали при чугунной ступице .
Диаметр вала сечение шпонки: длина шпонки (при длине ступицы муфты 36мм) момент на ведущем валу
Определяем напряжение смятия:
(полумуфты МУВП изготавливают из чугуна).
Из двух шпонок – под зубчатым колесом и под звездочкой – больше нагружена вторая (меньше диаметр вала и соответственно размеры шпонки) поэтому проверяем на смятие вторую шпонку.
Диаметр вала сечение шпонки: длина шпонки (при длине ступицы звездочки 58мм) момент на валу
(звездочка выполняется из термообработанной среднеуглеродистой или легированной стали).
12.Посадки зубчатого колеса звездочки и подшипников
Посадки назначаем в соответствии с табл. 25 [1].
Посадка зубчатого колеса на вал Н7р6 посадка звездочки цепной передачи на вал редуктора Н8h8.
Шейки валов под подшипники выполняем с отклонением вала k6. Отклонения отверстий в корпусе под наружные кольца по H7.
Остальные посадки назначаем в соответствии с табл. 25 [1].
13.Выбор сорта масла
Смазывают зубчатое зацепление окунанием зубчатого колеса в масло заливаемое внутрь корпуса до уровня обеспечивающего погружение колеса примерно на 10мм. Объем масляной ванны определяем из расчета 025дм3 масла на 1кВт передаваемой мощности:
По табл. 26 [1] устанавливаем вязкость масла в зависимости от окружной скорости. В нашем случае окружная скорость составляет 164мс и рекомендуемая кинематическая вязкость при контактном напряжении 530МПа по табл. 26 [1] составляет 34мм2с. По табл. 27 [1] определяем для этой вязкости тип масла
Подшипники смазываем пластичной смазкой типа Литол-24 которую закладываем в подшипниковые камеры при сборке. Периодически смазку пополняем шприцем через пресс-масленки.
Список использованной литературы
Детали машин. Проектирование цилиндрических зубчатых редукторов: Методические указания по выполнению курсовой работы Сост. А.А. Ордин. – Новосибирск: СибУПК 2001. – 76 с.
Курсовое проектирование деталей машин: Учеб. пособие для техникумов С.А. Чернавский Г.М. Ицкович К.Н. Боков и др. – М.: Машиностроение 1980. – 351 с. ил.
Курсовое проектирование деталей машин: Учеб. пособие для учащихся машиностроительных специальностей техникумов С.А. Чернавский К.Н. Боков И.М. Чернин и др. – 2-е изд. перераб. и доп. – М.: Машиностроение 1988. – 416 с. ил.
Спецификация.cdw

Пояснительная записка
Крышка смотрового окна
Кольцо мазеудерживающее
Вал-шестерня ведущий
Колесо зубчатое цилиндрическое
Чертеж1.cdw

Чертеж вал.cdw

Клеймить клеймом ОТК.
Рекомендуемые чертежи
- 09.05.2024
- 24.01.2023
- 23.10.2021