Проектирование цилидрического двухступенчатого редуктора с ременной передачей вертикальное расположение




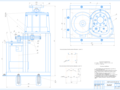
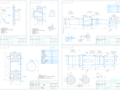
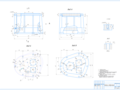
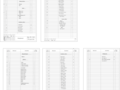
- Добавлен: 24.01.2023
- Размер: 435 KB
- Закачек: 0
Описание
Состав проекта
![]() |
![]() ![]() ![]() ![]() |
![]() ![]() ![]() |
![]() ![]() ![]() ![]() |
![]() ![]() ![]() ![]() |
![]() ![]() ![]() ![]() |
![]() ![]() ![]() ![]() |
Дополнительная информация
корпус.cdw

литейные радиусы-3 5мм.
Неуказанные предельные отклонения размеров:
Поверхность корпуса очистить и красить
маслоотпорной краской.
Внутреняя поверхность покрытия-0
Наружная поверхность покрытия-0
РПЗ.doc
Полоцкий государственный университет
Кафедра технологии конструкционных
по курсу «Детали машин»
«Проектирование механического привода
согласно схемы и исходных данных »
Выбор электродвигателя и кинематический расчет привода 4
Определение мощностей и передаваемых крутящих моментов 6
Прочностной и геометрический расчет передач. 7
1 Расчет цепной передачи 6
2Расчет материалов и допускаемых напряжений быстроходной зубчатой передачи. 8
3Расчет быстроходной зубчатой передачи. 10
4Расчет материалов и допускаемых напряжений тихоходной зубчатой передачи. 14
5Расчет тихоходной зубчатой передачи. 16
Проектный и проверочный расчет валов. 20
1 Расчет второго вала. 20
2 Расчет первого вала. 23
3Расчет третьего вала. 27
Выбор и проверочный расчет подшипников качения 32
1Подбор подшипников по динамической грузоподъемности на первом валу. 32
2Подбор подшипников по динамической грузоподъемности на втором валу. 34
3Подбор подшипников по динамической грузоподъемности на третьем валу. 36
ВЫБОР И ПРОВЕРОЧНЫЙ РАСЧЕТ МУФТ. 38
ВЫБОР СИСТЕМЫСМАЗКИСМАЗОЧНЫХ МАТЕРИАЛОВ И УПЛОТНЕНИЙ. 40
Определение размеров корпусных деталей кожухов ограждений и установочной
Список используемой литературы 42
Совершенствование конструкции деталей машин методов их расчета и введение новых стандартов должно находить отражение в курсовом проектировании.
Цель курсового проектирования по деталям машин – приобретение навыков проектирования. Работая над проектом мы выполняем расчеты учимся рационально выбирать материалы и форму деталей стремясь обеспечить их высокую экономичность надежность и долговечность. В проектировании широко используются ГОСТы учебная и справочная литература. Приобретенный в результате проектирования опыт будет являться основой для выполнения курсовых проектов по специальным дисциплинам и для дипломного проекта а также для всей дальнейшей конструкторской деятельности.
Проект состоит из пояснительной записки спецификации и графической части. Объем этих документов этих документов зависит от объема всего проекта установленного учебной программой. Объем графической части составляет четыре листа формата А1.
Техническое задание на курсовой проект включает схему объема привода исходные данные (силовые кинематические и геометрические факторы срок службы характер нагрузки) и указания об объеме расчетной и графической части проекта.
По СТ СЭВ 208 75 устанавливаются следующие стадии разработки конструкторской документации.
Техническое задание являющегося исходным документом для разработки конструкторской документации проектируемого изделия.
Техническое предложение содержащее уточненные основные и дополнительные данные изделия и обоснование принятых решений.
Эскизный проект содержащий принципиальные решения.
Технический проект окончательное техническое решение дающее представление о принципах работы и устройстве изделия.
Рабочая документация содержащая необходимые данные для изготовления контроля приемки эксплуатации и ремонта изделия.
Выбор электродвигателя и кинематический расчет привода 1. Определяем коэффициент полезного действия привода.
где подш = 0993 – подшипник качения
пц = 0965 – передача цилиндрическая закрытая
пр = 0945 – передача клиноременная
= 094·09652·09933 = 086
Расчетная мощность электродвигателя:
Ртр = 55 086 = 639 кВт.
Угловая скорость определяется пропорционально:
nвых = 30·10 314 = 9554 мин –1
Предварительное значение передаточных чисел для цилиндрической и клиноременной передачи:
Uр.м. = 2 Uц.п. = 25
Расчетная частота вращения вала электродвигателя:
nэд р = 9554·125 = 1194 мин –1.
Выбор электродвигателя:
Рэд = 75 кВт – мощность
nэд = 1455 мин –1 – частота вращения
Действительное общее передаточное число привода:
Uo = 1455 955 = 1522
Действительное передаточное число ременной передачи:
Uрем = 1522 252 = 2.43
Определение мощностей и передаваемых крутящих моментов
Силовые и кинематические параметры валов привода:
Расчет мощностей на каждом валу:
Р2 = 75·094·0993 = 7 кВт
Р3 = 7·0965·0993 = 67 кВт
Р4 = 67·0965·0993 = 642 кВт.
Расчет угловой скорости:
= 314·1455 30 = 15229 с –1
= 15229 243 = 6267 с –1
= 6267 25 = 2506 с –1
= 2506 25 = 1000 с –1.
Расчет частоты вращения:
n1 = 30·15229 314 = 1455 мин – 1
n2 = 30·6267 314 = 59875 мин – 1
n3 = 30·2506 314 = 2394 мин – 1
n4 = 30·1000 314 = 9554 мин – 1.
Расчет крутящих моментов:
Т1 = 7500 15229 =4924 Н·м
Т2 = 7000 6267 = 11169 Н·м
Т3 = 6700 2506 = 26735 Н·м
Т4 = 6420 1000 = 642 Н·м.
Прочностной и геометрический расчет передач.
1 Расчет клиноременной передачи
Р1 = 750 кВт Р2 = 7 кВт
n1 = 1455 мин – 1 n2 = 59875 мин – 1.
Т1 = 4924 Н·м Т2 = 11169 Н·м.
Сечение ремня и размеры сечения:
сечение ремня = f(Т1р);
Т1р = Т1Ср – расчетный передаточный момент
Ср = 12 – коэффициент учитывающий динамичность нагружения передачи и режим ее работы
Т1р = 4924·12 = 5908 Н·м;
Обозначения сечения ремня – кордшнуровой (узкого сечения α=34 ) УА -900 IV ГОСТ 1284.1-89
Размеры и параметры поперечных сечений клиновых ремней:
d1 min = 90 мм – минимальный расчетный диаметр ведущего шкива
Вр = 11 мм В = 13 мм Нр = 10 мм Н = 2.8 мм.
Расчетный диаметр ведомого шкива:
d2 = 90·243 = 218.7мм;
Действительный диаметр: d2 = 224 мм;
Действительное передаточное число проектируемой передачи:
где = 0015 – коэффициент упругого скольжения
Uд = 224 [90(1 – 0015)] = 2.5
Минимальное межосевое расстояние:
аmin = 055(d1 + d2) + Нр
аmin = 055(90 + 224) + 10= 182.7мм принимаем а = 183 мм.
Расчетная длина ремня:
LP = 2a + 05(d1 + d2) + 025(d2 – d1)2 a
LP = 2·183 + 05·314(90 + 224) + 025(224 – 90)2 183 = 883.51 мм
Действительная длина ремня LP ≥ LP:
Межцентровое расстояние:
а = 183 + 05(900 – 883.51) = 191.24 мм.
Коэффициент учитывающий длину ремня:
СL = f(Lp сечение ремня)
Угол обхвата ремнем меньшего шкива:
α10 = 1800 – 570(d2 – d1) a;
α10 = 1800 – 570(224 – 90) 191.1 = 140.04.
= 314·90·1455 (60·103) = 7.61 м с.
Число ремней передачи:
z = Р1Ср (Р0СLCαCk);
где Р0 = f(сечение ремня ) – мощность передаваемая одним ремнем
Сk = 10 – коэффициент учитывающий число ремней в передаче
z = 75·12 (5.35·087·089·1) = 2.17 принимаем z = 2.
Сила нагружающая валы передачи:
где F0 = 05Ft φ – предварительное натяжение ремня
Ft = 2·103T1 d1 – окружное усилие
φ = 05 – коэффициент тяги
Ft = 2·103·4924 90 = 7872 Н
F0 = 05·7872 05 = 7872 Н
F = 2·7872 sin(140 2) = 152075 Н.
Расчет долговечности резинотканевого клинового ремня
у- предел выносливости ремня у = 9МПа maxнапряжение в ремне
2Расчет материалов и допускаемых напряжений быстроходной зубчатой передачи.
частота вращения n1 = 59875 мин-1 n2 = 2394 мин-1
передаточное число u = 25
продолжительность работы передачи: nгод = 5 лет; кгод = 07; ксут=06
Материал шестерни и зубчатого колеса
1. Материал шестерни – 55 НВ1 = 320 в1 = 850 т1 = 540 Мпа.
2. Материал колеса – 55 НВ1 = 300 в1 = 750 т1 =500 Мпа.
Допускаемые контактные напряжения.
1. Базовое число циклов соответствующее пределу выносливости для шестерни и зубчатого колеса NH lim1(2).
NH lim1(2)=f(HB1(2))
для шестерни NH lim1 =30 106
для колеса NH lim2 = 27106
2. Эквивалентное число циклов
NHE1(2)=60n1(2)LhcKHE
где Lh= 365кгод24·ксут·nгод – продолжительность работы передачи
Lh= 36500724·06·5 = 18396 час.
с = 1 – число зацеплений зуба за один оборот колеса
KHE = Σ[(ТiТ1)0.5qн(tiLh)] – коэффициент учитывающий изменение нагрузки передачи в соответствии с циклограммой
KHE = (115)305+(0515)305 = 0166
qH = 6 – показатель степени кривой усталости при расчете на контактную выносливость
NHЕ1 = 60598751839610166 = 1097106
NHЕ2 = 6023941839610166 = 4386106
3. Коэффициент долговечности.
т.к. NН lim NНE то YN1(2) = 1
4. Предел контактной выносливости.
H lim1=f(350)=2320 + 70 = 710 МПа
H lim2=f(320)=2300 + 70 = 670 МПа
5. Допускаемые контактные напряжения.
H 1(2)=09 H lim1(2)ZN1(2)SH1(2)
где SH=1.1 – коэффициент запаса прочности
H 1=09710111 = 580.9 МПа
H 2=09670111 = 548.18 МПа
6. Расчетные допускаемые контактные напряжения.
Допускаемые изгибные напряжения.
1. Базовое число циклов напряжений NFlim = 4106 цикл.
2. Эквивалентное число циклов.
NFЕ1 = 60598751839610166 = 1097106
NFЕ2 = 6023941839610166 = 4386106
т.к. NF lim NFE то YN1(2) = 1
4. Предел выносливости зубьев при изгибе.
F lim1(2) = f(HB1(2))
F lim1 = f(320) = 175320 = 560 МПа
F lim2 = f(300) = 175300 = 525 МПа
5. Допускаемые изгибные напряжения.
FР 1(2) = 04 F lim1(2)YN1(2) YA
где YA = 1.0 – коэффициент учитывающий двухстороннее приложение нагрузки
FР 1=0456011 = 224 МПа
FР 2=0452511 = 210 МПа
Допускаемые напряжения при действии максимальной нагрузки.
3Расчет быстроходной зубчатой передачи
крутящий момент Т1 = 11169 Нм Т2 = 26735 Нм
1.Расчет межосевого расстояния и выбор основных параметров передачи.
1.1. Расчетное межосевое расстояние мм
где ka = 43 мПа13 – для косозубой передачи
ba – коэффициент ширины шестерни относительно межосевого
ba = baw = 2bd (u + 1) = 20.8 (25 + 1) = 0.45
bd – коэффициент ширины шестерни относительно ее диаметра
bd = b d1 = f(HB) = 0.8
kH – коэффициент учитывающий неравномерность распределения нагрузки по ширине венца
kА – коэффициент внешней динамической нагрузки
- зубчатого колеса b2 = b = ba= 045·76.9= 34.605 35 мм;
- шестерни b1 = b2 + 4 = 35 + 4 = 39 мм;
Величину округляют до ближайшего значения = 100 мм в соответствии с ГОСТ .
Принимая предварительно = 19 и = 150 определяется модуль зацепления
m = 2awcos [z1(u+1)]
m = 2·100·cos 15 [19(25 + 1)] =2.92 округляем до ближайшей величины mn =3мм в соответствии с ГОСТ .
Суммарное число зубьев передачи
z = 2·100·cos 15 3 = 64.82округляем до ближайшего целого числа z = 65.
Действительный угол наклона зуба
cos = 65· 3 (2·100) = 0975
Число зубьев шестерни
z1 = 65 (25 + 1) = 18.57 округляем до ближайшего целого числа z1 = 18
Число зубьев зубчатого колеса
Действительное передаточное число
Диаметры зубчатых колес мм
начальных dw1(2) = mnz1(2) cos
dw1=318 0975 = 55.4 мм
dw2=347 0975 = 144.6 мм
вершин зубьев da1(2) = mn (z1(2) cos + 2)
da1=3(18 0975 + 2) = 61.4 мм
da2=3(47 0975+ 2) = 150.6мм
проверка aw = 05(dw1+ dw2) = 100 мм
2. Проверка расчетных контактных напряжений.
2.1. Окружная сила в зацеплении Н
Ft = 210311169 55.4 = 4032.12Н
2.2. Окружная скорость колес мс
= 31455.45985 (60103) = 1.73 мс
2.3. Степень точности – 9
Удельная окружная динамическая сила
где H – коэффициент учитывающий влияние вида зубчатой передачи и модификации профиля на динамическую нагрузку
H = f(350 140 24 24) = 002
g0 – коэффициент учитывающий влияние разности шагов зацепления зубьев шестерни и колеса
g0 = f(степень точности m)
Удельная окружная сила в зоне ее наибольшей концентрации
WHtp = 4032.12 ·113 35 = 130.17Н
Коэффициент учитывающий динамическую нагрузку в зацеплении
KHv = 1 + (WHv WHtp)
KHv = 1 + (1.56 130.17) = 1.011
Удельная расчетная окружная сила
WHt = 4032.12 ·113·1011·1 35 = 131.61Н
Расчетные контактные напряжения МПа
где ZH – коэффициент учитывающий форму сопряженных поверхностей зубьев
ZH = 177·0975 = 1725
ZE – коэффициент учитывающий механические свойства материалов колес
Z – коэффициент учитывающий суммарную длину контактных линий
α = [188 – 32(1z1 + 1z2)] cos
α = [188 – 32(118 + 147)]·0975 = 1.635
Условие не удовлетворяется следовательно изменим b2=50
WHt = 4032.12 ·113·1011·1 50 = 92.12
Расчет и корректировка параметров передачи.
= 50·02222 (314·3) = 1.04 данное значение является ближайшим к значению = 1.04 = 1 ± 5%
Рекомендуется проектировать передачи с коэффициентом осевого перекрытия = 1.
Коэффициент учитывающий форму зуба
YFS 1(2) = f(z1(2) E x 1(2)) (x1(2) = 0) где
z1(2) E = z1(2) cos3
z1 E = 18 (0975)3 = 19.42
z2 E = 47 (0975)3 = 50.71
Расчетные напряжения изгиба зуба
F1(2) = YFS 1(2) Y Y WFt mn ≤ FP1(2)
Y = 1 – 0 1400 = 0.9 – Коэффициент учитывающий наклон зуба
Y = 1 α = 061 – коэффициент учитывающий перекрытие зубьев (α = 155 – коэффициент торцевого перекрытия
F1 = 42· 09·061·92.12 2 = 106.205 МПа
F2 = 374·09·061·92.12 2 = 94.57 МПа
Проверка прочности зубьев при перегрузках.
Максимальные контактные напряжения МПа
Hmax = 580 = 710МПа ≤ 1350 МПа
4.2. Максимальные напряжения изгиба МПа
Fmax1(2) = F1(2)(TmaxTnom) ≤ FPmax1(2)
Fmax1 = 106.205·15 = 159.30 МПа ≤ 432 МПа
Fmax2 = 94.57·15 = 141.85 МПа≤ 400МПа
Силы в зацеплении зубчатых колес
Уточненный крутящий момент на колесе
Т2 у = 26735·2.61 25 = 279.11 Н·м
Ft1(2) = 2·103 T1(2) dw1(2)
Ft1 = 2·103 ·11169 55.4 =4032.12 Н
Ft2 = 2·103 ·279.11 144.6 =3860.44 Н
Fr1(2) = Ft1(2) tg α cos
Fr1 = 4032.12·0324 0975 = 1339.9Н
Fr2 = 3860·0324 0975= 1282.70Н
Fa1 = 4032.12·0.2279= 918.92Н
Fa2 = 3860.44·0.2279 = 879.79Н
4Расчет материалов и допускаемых напряжений тихоходной зубчатой передачи
частота вращения n1 = 2394 мин-1 n2 = 9554 мин-1
продолжительность работы передачи: nгод = 5 лет кгод = 07 ксут = 06
1. Материал шестерни – 55 НВ1 = 350 в1 = 850 т1 = 540 Мпа.
2. Материал колеса – 55 НВ1 = 320 в1 = 750 т1 =500 Мпа.
для шестерни NH lim1 = 30106
для колеса NH lim2 = 25106
Lh= 3650724·06·5 = 18396
NHЕ1 = 6023941839610166 = 4386106
NHЕ2 = 6095541839610166 = 1756106
т.к. NН lim1 NНE1 то YN1 = 1
4. Предел контактной выносливости МПа.
H lim1(2) = f(HB1(2))
H lim1 = f(320) = 2350 + 70 = 770 МПа
H lim2 = f(300) = 2320 + 70 = 710 МПа
5. Допускаемые контактные напряжения МПа.
H 1(2) = 09 H lim1(2)ZN1(2)SH1(2)
где SH = 1.1 – коэффициент запаса прочности
H 1 = 09770111 = 630МПа
H 2 = 097101.1212 = 650.6МПа
6. Расчетные допускаемые контактные напряжения МПа.
NFE1(2) = 60n1(2)LhcKFE
где Lh = 365кгод24·ксут·nгод – продолжительность работы передачи
Lh= 3650724·06·5 = 18396 час
KFE = Σ[(ТiТ1)0.5qн(tiLh)] – коэффициент учитывающий изменение нагрузки передачи в соответствии с циклограммой
KFE = (115)305+(0515)305 = 0166
NFЕ1 = 6023941839610166 = 4386106
NFЕ2 = 6095541839610166 = 1756106
4. Предел выносливости зубьев при изгибе МПа.
F lim1 = f(350) = 175350 =612.5 МПа
F lim2 = f(320) = 175320 =560 МПа
5. Допускаемые изгибные напряжения МПа.
FР 1=04612.511 = 245 МПа
FР 2=0456011 = 224 МПа
5Расчет тихоходной зубчатой передачи. Исходные данные:
частота вращения n1 = 239.4мин-1 n2 = 9554 мин-1
крутящий момент Т1 = 267.35 Нм Т2 = 642 Нм
где ka = 49 МПа13 – для прямозубой передачи
ba = baw = 2bd (u + 1) = 21.2 (25 + 1) = 0.68
bd = b d1 = f(HB) = 09
- зубчатого колеса b2 = b = ba= 068·93.79 = 63.7 мм 64 мм;
- шестерни b1 = b2 + 4 =64+ 4 =68 мм;
Прямозубые передачи.
Принимая предварительно z1 = 19 aw = 120 мм определяем модуль зацепления
m = 2·120 [19(25 + 1)] = 3.6мм
4. Значение модуля округляем до ближайшего значения mn m = 3.5мм
5. Число зубьев шестерни
z1= 2120 [3.5(25 + 1)] = 19.5 принимаем z1 = 20
6. Число зубьев зубчатого колеса
z2 = 2025 = 50 принимаем z2 = 50
7. Расчетное межосевое расстояние мм
awo = 053.5(18+45) =122.5 принимаем awo = 120 мм
8. Действительное передаточное число
dw1 = 3.520 cos 0 = 70 мм
dw2 = 3.550 cos 0 = 175 мм
da1 = 3.5(20 cos 0 + 2) =77 мм
da2 = 3.5(50 cos 0 + 2) = 182мм
проверка aw = 05(dw1 + dw2) = 122.5 мм
Ft = 210326735 70 = 7638.57 Н
= 314702394 (60103) = 0.87 мс
WHtp = 7638.57·11 64 = 131.28 Н
KHv = 1 + (2.66 131.28) 1.02
WHt = 7638.57·11·102·1 64 = 133.91Н
Z = 1 – коэффициент учитывающий суммарную длину контактных линий
Условие не удовлетворяется следовательно изменим b2=70
WHt = 7638.57·11·102·1 70 = 122.43 Н
Проверка расчетных напряжений изгиба.
Удельная окружная динамическая сила
H = 016 – коэффициент учитывающий влияние вида зубчатой передачи и модификации профиля на динамическую нагрузку
Удельная расчетная окружная сила в зоне ее наибольшей концентрации
WFtp = 7638.57·11 70 = 120.03Н
KFv = 1 + (WFv WFtp)
KFv = 1 + (7.11 120.03) = 1.059
WFt = 7638.57·11·1059·1 70 = 127.11 Н
Y = 1 – коэффициент учитывающий наклон зуба
Y = 1 – коэффициент учитывающий перекрытие зубьев
F1 = 415·1·1·127.11 3.5 = 150.71МПа
F2 = 365·1·1·127.11 3.5 = 132.55МПа
Hmax = 650.6 = 796.81 МПа ≤ 1350 МПа
Fmax1 = 150.71·15 = 226.06 МПа ≤ 520 МПа
Fmax2 = 132.55·15 = 198.82МПа ≤ 416 МПа
Т2 у = 642·25 25 = 642Н
Ft1 = 2·103 ·26735 70 = 7638.57 Н
Ft2 = 2·103 ·642 175 = 7337.14 Н
Fr1 = 7638.57·0364 cos 0 = 2780.43 Н
Fr2 = 7337.14·0364 cos 0 = 2670.72Н
Проектный и проверочный расчет валов.
1 Расчет второго вала.
Вал передает момент:
Со стороны шестерни первого вала на зубчатое колесо действуют силы:
Со стороны зубчатого колеса третьего вала на шестерню действуют силы:
Расстояние между средними подшипниками:
l Lст2 + Lст3 + 3x +
Lст2 =– длина ступицы зубчатого колеса
x – расстояние между ступицей и подшипником
[] = 10 15 МПа – допускаемое напряжение
Принимаем dв = 46 мм
Lст3 = 74 – длинна ступицы шестерни
l 74 + 50 + 3·7 + 26 = 171мм
Расстояние между левым подшипником и серединой зубчатого колеса:
l1 = Lcт2 2 + x + 2 = 50 2 + 7 + 26 2 =45 мм
Расстояние между серединой шестерни и правым подшипником:
l2 = Lcт3 2 + x + 2 = 74 2 + 7 + 26 2 =57 мм
Расстояние между серединами зубчатого колеса и шестерни:
l3 = Lcт3 2 + Lcт2 2 + x = 50 2 + 74 2 + 7 =69 мм.
Опорные реакции в вертикальной плоскости
МС = RDy l + Fa12d2 2 – Fr12l1 + Fr32(l1 + l3) = 0
RDy = (– Fa12d2 2 + Fr12l1 – Fr32(l1 + l3)) l
RDy = (-879.79·175 2 + 1282.7 ·45– 2670.72 (45 + 69)) 171 = -1893.11
= Н (обратное направление)
МD = – RСy l + Fa12d2 2 + Fr12 (l3 + l2) – Fr32l2 = 0
RCy = (Fr12 (l3 + l2) + Fa12d2 2 – Fr32l2) l
RCy = (1282.7 (69 + 57) + 879.79 ·175 2 – 2670.72 ·57) 171=505.09Н
y = – RDy + RCy – Fr12 + Fr32 = -1893.11+505.09 – 1282.70 + 2670.72 = 0
Опорные реакции в горизонтальной плоскости:
МС = RDxl – Ft32(l1 + l3) – Ft12l1 = 0
RDx = (Ft32 (l1 + l3) + Ft12l1) l = (7638.57 (45 + 69) + 3860.44 ·45) 171 = 6108.28
МD = – RCxl + Ft12(l3 + l2) + Ft32l2 = 0
RCx = (Ft12(l3 + l2) + Ft32l2) l = (3860.44(69 + 57) + 7638.57·57) 171=5390.72 Н
x = Ft32 + Ft12 – RСx – RDx = 7638.72 + 3860.44 – 6108.28 – 5390.72 = 0
В вертикальной плоскости
М2y = RCyl1 = 505.09 ·45 = 22729.05·мм
M2y = – RDy l2 = – 1893.11·57 = –107907.27·мм
В горизонтальной плоскости:
МCx = RCxl1 = 5390.72·45 = 301026.15·мм
МDx = RDxl2 = 6108.28·57= 348171.96·мм
Суммарный изгибающий момент в сечении под шестерней (это сечение наиболее нагруженное)
Диаметр вала с учетом суммарного изгибающего момента под шестерней:
мм выбранное ранее сечение подходит dв =46 мм.
Диаметр цапф под подшипники принимаем dп = 40 мм (кратен 5).
Буртик между зубчатым колесом и шестерней dб = 52 мм
Материал вала сталь 40Х
Пределы выносливости стали:
Нормальные напряжения в сечении под шестерней:
момент сопротивления
W = d3 32 – bt(d – t)2 2d
b = 14 – ширина канавки t = 55 – глубина канавки.
W = 314·463 32 – 14·55(46 – 55)2 2·46 = 817828мм3
a = 364510.20 817828 = 44.57 МПа
Касательные напряжения:
Момент сопротивления при кручении:
Wк = d3 16 – bt(d – t)2 2d
Wк = 314·463 16 – 14·55(46 – 55)2 2·46 = 1772938 МПа
а = 267350 2·1772938= 753 МПа
Эффективные коэффициенты концентрации напряжений для сечения со шпоночной канавкой для стали 40Х с пределом прочности 900 МПа:
Масштабные факторы при d = 46 мм:
Для углеродистой стали коэффициент учитывающий влияние постоянной составляющей цикла на усталость вала:
Коэффициент запаса прочности по нормальным напряжениям
Коэффициент запаса прочности по касательным напряжениям:
Общий коэффициент запаса прочности:
где s – расчетный коэффициент запаса прочности;
[s] = 13 15 – требуемый коэффициент запаса для обеспечения прочности;
[s] = 2.5 4 – требуемый коэффициент запаса для обеспечения жесткости;
Прочность и жесткость обеспечены.
2 Расчет первого вала
Неуравновешенная составляющая силы передаваемая ременной передачей.
Расстояние от левого подшипника до центра шестерни:
Расстояние от правого подшипника до центра зубчатого колеса:
Lст1 = 14·dв – длина ступицы
Принимаем dв = 36 мм
Lст1 = 14·29 = 50 мм
Расстояние от ременной передачи до левого подшипника
Мв = – RAy l + Fa21d1 2 – Fr21l2 = 0
RAy = (Fa21d1 2 – Fr21l2) l
RAy = (918.92·55.4 2 – 1339.9 ·126 ) 171 = – 838.44 Н (обратное направление)
МА = RВy l + Fa21d1 2 + Fr21l1 = 0
RВy = (– Fr21l1 – Fa21d1 2) l
RВy = (–1339.9·45– 918.92·55.4 2) 171= -501.46 Н (обратное направление)
y = RВy + RAy – Fr21 = 501.46 + 838.44 – 1339.9 = 0
МВ = S(f + l) – RAxl + Ft21l2 = 0
RAx = (S(f + l) + Ft21l2) l
RAx = (152075(150 + 171) + 4032.12·126) 171 = 5825.78Н
МА = Sf – Ft21l1 + RВxl = 0
RBx = (Ft21l1 – Sf) l = (4032.12·45– 152075·150) 171 = –272.90Н
x = S + Ft21 – RAx – RBx = 1520.75 + 4032.12 – 5825.78–(–272.9) = 0
М1y = RAy l1 = 838.44·45 = 37729.8Н·мм
M1y = RBy l2 =501.46 ·126 = 63183.96Н·мм
Вертикальной плоскости:
МАx = Sf = 152075·150 = 228112.5Н·мм
МВx = RBx l2 = 272.9·126 =34385.4 Н·мм
Суммарный изгибающий момент в сечении под шестерней:
Изгибающий момент в сечении под левым подшипником:
Наиболее нагруженным является сечение под левым подшипником:
Диаметр выходного конца вала:
[] = 20 30 МПа – допускаемое напряжение
Принимаем dк = 26 мм.
Диаметр цапф под подшипниками должны быть несколько больше dк = 26 мм и кратны 5. Принимаем dп = 30 мм.
Диаметр участка вала между выходным концом и цапфой под подшипник должен занимать промежуточное значение между данными диаметрами. Принимаем dк-п = 28 мм.
Диаметр буртика должен быть больше dв = 36 мм. Принимаем dб = 42мм.
Диаметр вала с учетом суммарного изгибающего момента под левым подшипникам:
мм выбранное ранее сечение подходит dп = 36 мм.
Нормальные напряжения в сечении под левым подшипником:
W = 314·363 32 = 457812мм3
a = 228112.5 457812 = 49.82 МПа
Wк = 314·363 16 = 915624 МПа
а = 111690 2·915624 = 6099МПа
Эффективные коэффициенты концентрации напряжений
Масштабные факторы при d = 36 мм:
[s] = 2 4 – требуемый коэффициент запаса для обеспечения жесткости;
3Расчет третьего вала.
Силы действующие на колесо со стороны шестерни.
Сила передаваемая муфтой
S = 037337 = 2201.14 Н
Расстояние от левого подшипника до центра зубчатого колеса:
Расстояние от левого подшипника до муфты:
Lст4 = 09·dв – длина ступицы
Принимаем dв = 60 мм
Lст4 = 09·60 = 54 мм
Мв = RAy l – Fr34l2 = 0
RAy = 2670.72·114 171 = 1780.48Н
МА = – RВy l + Fr34l1 = 0
RВy = 2670.72·57 171 = 890.24 Н
y = RВy + RAy – Fr34 = 890.24 + 1780.48 – 2670.72 = 0
МВ = RAxl – Ft34l2 + S(l + l3) = 0
RAx = (Ft34l2 – S(l + l3)) l
RAx = (7337.14·114 – 2201.14(171 + 70)) 171 =1789.24 Н
МА = Sl3 + Ft34l1 – RВxl = 0
RBx = (Ft34l1 + Sl3) l
RBx = (7337.14·57 + 2201.1470) 171 = 3346.76 Н
x =S – Ft34 + RAx + RBx = 2201.14 – 7337.14 + 1789.24+3346.76 = 0
М1y = RAy l1 = 1780.48·57 = 101487.36Н·мм
M1y = RBy l2 = 890.24·114 = 101487.36 Н Н·мм
МАx = Sl3 = 2201.1470 = 154079.8 Н·мм
МВx = RBx l2 = 3346.76·114 = 381530.64 Н·мм
Принимаем dк = 48 мм.
Диаметр цапф под подшипниками должны быть несколько больше dк = 48 мм и кратны 5. Принимаем dп = 55 мм.
Диаметр участка вала между выходным концом и цапфой под подшипник должен занимать промежуточное значение между данными диаметрами. Принимаем dк-п = 52 мм.
Диаметр буртика должен быть больше dв = 60 мм. Принимаем dб = 64 мм.
Диаметр вала с учетом суммарного изгибающего момента под зубчатым колесом:
мм выбранное ранее сечение подходит dв = 60 мм.
b = 18 – ширина канавки t = 7 – глубина канавки.
W = 314·603 32 – 18·7(60 – 7)2 2·60 = 1824555 мм3
a = 394797.81 1824555 = 21.63 МПа
Wк = 314·603 16 – 18·7(60 – 70)2 2·60 = 3944055 МПа
а = 642000 2·3944055 = 813 МПа
Эффективные коэффициенты концентрации напряжений для сечения со шпоночной канавкой для 40Х с пределом прочности 900 МПа:
Масштабные факторы при d = 60 мм:
[s] = 25 4 – требуемый коэффициент запаса для обеспечения жесткости;
Прочность и жесткость обеспечены.
Выбор и проверочный расчет подшипников качения
1Подбор подшипников по динамической грузоподъемности на первом валу.
Подбор подшипников по динамической грузоподъемности на первом валу.
RAy = 83844 Н RВy = 50146 Н RA
Внешняя осевая сила:
Частота вращения кольца:
Диаметры посадочных поверхностей вала:
Требуемая долговечность подшипника:
Роликовый радиально упорный Обозначение подшипника – 7306А
Данные данного подшипника:
d = 30 мм – внутренний диметр
D = 72 мм – внешний диаметр
Сr = 52800 Н – динамическая грузоподъемность
Сor = 39000Н – статическая радиальная грузоподъемность.
Определяем осевые составляющие S и осевые силы Fа.
Определяем радиальные нагрузки:
Более нагруженным является левый подшипник.
где e = 034 – коэффициент минимальной осевой нагрузки
S = 03458858 =2001172 Н
Значение коэффициента радиальной осевой нагрузок и коэффициента осевого нагружения определяем в зависимости от значения отношения:
iFa C0r = 1918.92 39000= 0023.(i =1 – число рядов тел качения)
X = 1 Y = 0 e = 034.
Сравниваем отношение FA VFr и значение е и окончательно принимаем значения коэффициентов X Y
где V = 1 – коэффициент вращения
FA VFr = 918.92 158858= 0157 е значит X = 1 Y = 0.
Вычисляем эквивалентную динамическую нагрузку:
Рэ = (VXFr + YFA)KбKт
где Kб =1– коэффициент безопасности
Kт =11– температурный коэффициент.
Рэ = (1158858+ 0918.92)11 = 58858
Определяем требуемую динамическую грузоподъемность:
2Подбор подшипников по динамической грузоподъемности на втором валу
RAy = 189311 Н RВy = 50509 Н RA
Роликовый радиально упорный Обозначение подшипника – 7208А
d = 40 мм – внутренний диметр
D = 80 мм – внешний диаметр
Сr = 58300Н – динамическая грузоподъемность
Сor = 40000 Н – статическая радиальная грузоподъемность.
где e = 035 – коэффициент минимальной осевой нагрузки
S = 035639491 = 223821 Н
Значение коэффициента радиальной осевой нагрузок и коэффициента осевого нагружения определяем в зависимости от значения отношения: iFa C0r = 879.79 40000 = 0.021.(i =1 – число рядов тел качения)
FA VFr = 879.79 1639491= 0127 е значит X = 1 Y = 0.
Kт =1– температурный коэффициент.
Рэ = (11639491 + 0879.79)11 = 639491 Н
3Подбор подшипников по динамической грузоподъемности на третьем валу.
RAy = 178048 Н RВy = 89024 Н RA
Тип подшипника: Роликовый радиально упорный Обозначение подшипника – 7211
d = 55 мм – внутренний диметр
D = 100 мм – внешний диаметр
Сr =65000 Н – динамическая грузоподъемность
Сor = 46000 Н – статическая радиальная грузоподъемность.
Более нагруженным является правый подшипник.
где e = 0 – коэффициент минимальной осевой нагрузки
FA VFr = 0 1346313 = 0 е значит X = 1 Y = 0.
где Kб – коэффициент безопасности
Kт – температурный коэффициент.
Рэ = (11346313 + 00)11 = 346313 Н
ВЫБОР И ПРОВЕРОЧНЫЙ РАСЧЕТ МУФТ.
Для передачи вращающего момента от редуктора будем использовать муфту упругую втулочно-пальцевую (МУВП). Эти муфты общего назначения применяют для передачи вращающих моментов со смягчением ударов с помощью упругих рези6новых втулок надеваемых на пальцы.
На работу муфты существенно влияют толчки удары и колебания обусловленные характером работы приводимого в движение машины. Поэтому расчеты муфты ведут не по номинальному моменту Т а по расчетному Тр.
где кр = 15 – коэффициент режима работы
Т = 64200 Нм – вращающий момент.
Тр = 15642 = 7704 Нм. (770400 Нмм)
Пальцы проверяем на изгиб:
где – наибольшее напряжение при изгибе в опасном сечении пальца мПа; – диаметр окружности на которой расположены пальцы;
– допускаемое напряжение при изгибе пальцев.
Окончательно вычисляем
условие прочности выполняется.
Условие прочности втулки на смятие:
где – длинна втулки;
– допускаемое напряжение на смятие для резины.
Окончательно вычисляем:
- условие прочности выполняется.
Расчет показал что принятая нами муфта полностью удовлетворяет условиям прочности.
Выбор системы смазки смазочных материалов и уплотнений.
Для уменьшения потерь мощности на трение и снижение интенсивности износа трущихся поверхностей а также для предохранения их от заедания задиров коррозии и лучшего отвода теплоты трущихся поверхностей детали должны иметь надежную смазку.
Выбираем смазочный материал. Требуемая вязкость масла зависит от контактного напряжения и окружной скорости колес. По определенным скорости и контактным напряжениям находим требуемую кинематическую вязкость и марку масла – индустриальное И – 40А.
Подшипники расположенные снизу смазываются той же смазкой маслом верхние подшипники смазываем литолом или солидолом через прессмасленки .
При работе передач масло постепенно загрязняется продуктами износа. С течением времени оно стареет свойства его ухудшаются. Поэтому масло необходимо периодически менять. Для этой цели в корпусе предусматриваем сливное отверстие закрываемое болтом. Болт создает герметичное соединение.
При длительной работе в связи с нагревом масла и воздуха повышается давление внутри корпуса что приводит к просачиванию масла через уплотнения и стыки. Чтобы этого избежать внутреннюю полость корпуса сообщают с внешней средой путем установки отдушины в его верхних точках.
Уплотнительные устройства применяем для предохранения от вытекания смазочного материла из подшипниковых узлов а так же для защиты их от попадания извне пыли и влаги. Используем манжетные уплотнения. Манжету устанавливаем открытой стороной внутрь корпуса. В этом случае к рабочей кромке манжеты обеспечен хороший доступ
Определение размеров корпусных деталей кожухов ограждений и установочной плиты.
Толщину стенки для двухступенчатого цилиндрического редуктора:
d = 0025аw цил2 + 3 = 00252225 + 3 = 85 мм принимаем d = 8 мм.
Расстояние от внутренней поверхности стенки редуктора до:
боковой поверхности вращающейся части:
с = (10 12) d = 118 = 88 мм.
боковой поверхности подшипника качения:
Расстояние в осевом направлении между вращающимися частями смонтированными на одном валу.
Минимальное значение зазора между зубчатым колесом одной ступени и валом другой ступени:
с3 = 15 d = 158 = 12 мм.
Радиальный зазор от поверхности вершин зубьев:
до внутренней поверхности стенки редуктора:
с4 = 12 d = 96 мм принимаем с4 =10мм.
Расстояние от боковых поверхностей элементов вращающихся вместе с валом до неподвижных частей редуктора:
Ширина фланцев S соединяемых болтом диаметром dбол = 15 = 158 = 12 мм к = f(dбол) = 24 мм:
S = к + + 6 = 24+8+6=38 мм.
Толщина фланца боковой крышки:
Высота головки болта:
h = 08h1 = 088 = 64 мм.
Длина цилиндрической части крышки:
«Детали машин» Курмаз Л.В. Скойбеда А.Т. Минск УП «Технопринт» 2001.
«Детали машин» Решетов Д.Н. «Машиностроение» 1974.
«Детали машин» Кузмин А.В. Чернин И.М. Минск «Высшая школа» 1986
«Детали машин в примерах и задачах» Ничипорчик С.Н Минск «Высшая школа» 1981.
«Детали машин курсовое проектирование » П.Ф Дунаев О.П ЛеликовМосква «Высшая школа»
деталировка.frw

Радиусы закруглений - 3мм.
Неуказанные предельные отклонения размеров: охватываемых
Точность зубчатого колеса в соответствии с ГОСТ
Формовочные уклоны - 3
литейные радиусы - 3 5 мм.
Неуказанные предельные отклонения размеров:
- охватываемых - h14
- охватывающих - H14
Отв. центр. B4 ГОСТ 14034-74
КПДМ 36.03.37.04.002.09
КПДМ 36.03.37.04.002.03
КПДМ 36.03.37.04.002.07
КПДМ 36.03.37.04.002.05
SСпецификация.frw

Промежуточный вал-шестерня
Мазеудерживающее кольцо
Паста "Герметик-прокладка
Болт фундаментный M16
Шайба концевая 7019-0622
Шайба концевая 7019-0621
Редуктор.frw

Техническая характеристика
P =3 кВт; n =1415 мин ; U =14
Прогиб ветви ремня под воздействием силы 100 Н не
более 6 мм (ГОСТ1284.3-96)
непараллельность осей шкивов не более 0
0 мм. Смещение рабочих поверхностей шкивов не более
Привод обкатать без нагрузки в течение не менее 1
часа. Стук и резкий шум не допускаются.
После обкатки мосло из редуктора слить и залить масло
индустриальное И-40А ГОСТ 20799-75 в количестве 2л.
Ограждения условно не показаны. Ограждения ременной
передачи и муфты установить и окрасить в оранжевый
Схема расположения болтов крепления к раме (1:3)
Схема расположения болтов крепления редуктора к раме (1:4)
Ось электродвигателя
Технические требования
КПДМ 04.22.01.000.СБ
Привод.cdw

P =7.5 кВт; n =1455 мин ; U =15.22; U =2.5; U =2
Прогиб ветви ремня под воздействием силы 100 Н не
более 6 мм (ГОСТ1284.3-96)
непараллельность осей шкивов не более 0
0 мм. Смещение рабочих поверхностей шкивов не более
Привод обкатать без нагрузки в течение не менее 1
часа. Стук и резкий шум не допускаются.
После обкатки мосло из редуктора слить и залить масло
индустриальное И-40А ГОСТ 20799-75 в количестве 2л.
Ограждения условно не показаны. Ограждения ременной
передачи и муфты установить и окрасить в оранжевый
КПДМ 36.03.37.04.001
Технические требования
Схема расположения болтов крепления редуктора к раме (1:4)
Схема расположения болтов крепления двигателя к раме( 1:4)