Проектирование техпроцесса изготовления детали Стакан




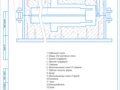
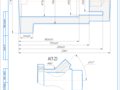
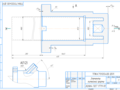
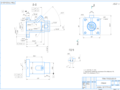
- Добавлен: 24.01.2023
- Размер: 284 KB
- Закачек: 0
Описание
Состав проекта
![]() |
![]() |
![]() |
![]() ![]() ![]() ![]() |
![]() ![]() ![]() ![]() |
![]() |
![]() ![]() ![]() ![]() |
![]() ![]() ![]() ![]() |
![]() ![]() ![]() ![]() |
![]() |
![]() |
![]() ![]() ![]() |
![]() ![]() ![]() |
![]() |
Дополнительная информация
Эскиз песчаной формы.cdw

Вентиляционный канал в стержне
Рабочая полость формы
Вентиляционный канал в форме
Элементы литейной формы.cdw

Чертеж отливки.cdw

Точность отливки 10-7-13-7 ГОСТ 26645-85.
Неуказанные формовочные уклоны 35'
Неуказанные литейные радиусы 3 5 мм.
Ч.cdw

Стакан.cdw

Реферат 1.doc
ТЕХНОЛОГИЯ ЗАГОТОВКА ОБРАБОТКА ЛИТЬЕ ОПЕРАЦИЯ ТЕРМООБРАБОТКА
Объект разработки – деталь «Стакан».
Цель работы – изучить особенности процесса подготовки производства заготовки.
Разработано: заготовка детали «Стакан» общая схема технологии получения заготовки основная операция получения заготовки.
Записка.doc
Полученная в результате разработанного технологического процесса заготовка должна удовлетворять условиям предъявляемым заданием для данной курсовой работы.
Общая схема технологического процесса получения детали
На рисунке 1.1 представлена общая технологическая схема получения и обработки заготовки.
Рисунок 1.1 – Общая технологическая схема получения и обработки заготовки
Выбор марки материала
Выбор материала обеспечивается необходимостью обеспечить требуемую надежность детали при имеющихся экономических ограничениях. То есть при минимальных затратах на изготовление детали получить максимальную выгоду.
В данной курсовой работе исходной деталью для проектирования является деталь “Стакан”. На чертеже ТПЖА.713120. -01 представлены ее внешний вид размеры технические требования на ее изготовление заложенные конструктором.
Таблица 2.1 – Химический состав механические и физические свойства
Механические свойства после то
Выбор материала заготовки определяется следующим требованиями:
предел прочности В ≥ 250 МПа;
относительное удлинение d ≥ 15%;
температура и среда эксплуатации – морская вода
В качестве вариантов рассматриваются материалы: латунь ЛЦ16К4 ГОСТ 17711-80 и ЛЦ30А3 ГОСТ 17711-80. В таблице 2.1 приводится их химический состав а также их механические и физические свойства.
Латунь ЛЦ16К4 – детали работающие в морской воде при протекторной защите арматуры до 250гр.С..
Латунь ЛЦ30А3 – коррозионно-стойкие детали.
Стоимость материала в относительных единицах можно оценить по формуле:
Ci - его стоимость в относительных единицах.
Таким образом окончательно принимается материал заготовки латунь ЛЦ16К4 как наиболее подходящую по свойствам и менее дорогой.
Для получения данного материала применяются индукционные печи с железным сердечником. Сердечник с первичной обмоткой защищен огнеупорной втулкой. Жидкий металл предварительно залитый в канал (кольцевой зазор) создает короткозамкнутый вторичный виток в нем индуктируется ток большой силы нагревающий металл до высокой температуры. За счет его циркуляции происходит быстрый нагрев и плавление загружаемой сверху твердой шихты. Эти печи экономичны имеют высокий тепловой и электрический КПД высокую производительность удобны в обслуживании обеспечивают минимальный угар металла. Схема индукционной печи представлена на рисунке 3.
Рисунок 3 - Схема индукционной печи для выплавки латуни;
- корпус; 2 - сердечник; 3 – кольцевой зазор.
В качестве шихтовых материалов применяют черновую медь (руда) переплавленную стружку литники прибыли Для легирования используют алюминиевокремниевую и другие лигатуры.
Основными особенностями при плавке латунных сплавов являются их склонность к поглощению газов и окисляемость.
Железо выделяется при затвердевании и охлаждении сплава в форме сульфида FeS способствуя образованию газовой пористости в отливках. Включения FeS существенно снижают механические свойства сплава.
Для защиты от поглощения газов и окисления плавку проводят под слоем покровных флюсов в состав которых входят SiO2 O2
Для более полного удаления газов неметаллических оксидных и других включений проводят дегазацию и рафинирование сплава. Для этой цели применяют продувку расплавленного сплава.
Оценка технологичности детали
Деталь “Стакан” изготавливается из материала латунь ЛЦ16К4 литьем в землю.
С точки зрения механической обработки деталь имеет небольшую сложность при обработке. Отверстия менее 15 мм не выливаются так как единичное производство то затраты компенсируются переплавкой сплава. Некоторую сложность представляет обработка внутренней поверхности. Она получается в результате выполнения механической операции.
В единичном производстве проблемы изготовления и обработки решаются использованием универсальной оснастки станков и инструмента.
Выбор способа получения заготовки
Исходными данными для выбора способа получения заготовки являются:
)годовая программа выпуска 15 штгод (единичное производство);
)наличие оборудования и оснастки в заготовительном цехе конкретного предприятия.
Выбранный материал заготовки латунь ЛЦ16К4 литейная и применяются различные виды литья. Ниже рассматриваются два возможных варианта получения заготовки: литье в песчано-глинистые формы и кокиль. Критерием выбора метода получения заготовки является ее стоимость.
Таблица 5.1 - Матрица влияния факторов
литье по выплавляемым моделям
Форма и размеры заготовки
Технологические свойства
Точность изготовления и качество
Механические и эксплуатационные
Время технологической подготовки
Итак для получения заготовки используется литье в песчано-глинистые формы.
Разработка чертежа заготовки и литейной формы
Разработка чертежа отливки литейной формы заключается в:
) выборе рационального положения отливки в форме и назначение разъема модели и формы;
) назначение припуска на механическую обработку формовочные уклоны напуски галтели и литейные радиусы;
) расчете размера стержня;
) разработке эскиза модели.
Прежде чем приступить к разработке технического процесса изготовления отливки необходимо тщательно изучить чертеж детали обратив особое внимание на ее назначение технические условия обработку серийность.
При этом надо руководствоваться следующими положениями:
) способ формовки (машинный или ручной) определяется серийностью производства. При единичном или мелкосерийном производстве применяется ручная формовка; при серийном и массовом - машинная;
) приемы формовки (в двух или более опоках по разъемной модели со стержнями и т.д.) определяется конфигурацией и размерами отливки.
В данном случае имеется единичное производство поэтому для уменьшения себестоимости отливки и детали выбираем ручную формовку так как она дешевле машинной.
При разработке элементов литейной формы и литейного чертежа вначале выберем положение отливки в форме при заливке жидким металлом и определим плоскость разъема модели и формы а затем разработаем все элементы отличающие размеры отливки от размеров детали.
При выборе положения отливки в форме необходимо учесть следующее:
требуется обеспечить равномерное и направленное затвердевание отливки;
наиболее ответственные обычно обрабатываемые поверхности надо делать нижними или боковыми (т.к. получаются более чистыми);
тонкостенные части располагают обычно в нижних частях формы по возможности вертикально или наклонно.
Выбор разъема формы или модели зависит от конфигурации и размеров отливки а также от характера производства. Количество разъемов должно быть минимальным так как наличие разъема приводит к смещению частей отливки относительно друг друга. Большую часть отливки следует помещать в одной части лучше в нижней: не рекомендуется пересекать плоскостью разъема ответственные обрабатываемые или базовые поверхности.
После выбора положения детали при заливке и плоскости разъема переходят к отделению элементов конструирования отливок и моделей. Модель - это прообраз будущей детали от которой она прежде всего отличается размерами на величину припусков на механическую обработку усадку литейных уклонов и наличием возможного напуска. Модель может отличаться от детали и по внешнему очертанию из-за наличия в ней знаковых частей.
Припуском на механическую обработку является слой металла (на сторону) предназначенный для снятия в процессе механической обработки с целью получения требуемой частоты поверхности и размеров заданных чертежом детали.
Величина припусков зависит от материала литейной формы характера производства положения обрабатываемой поверхности в форме и регламентируется ГОСТ.
Припуски на верхние поверхности отливки должны быть больше так как в верхней части отливки могут скапливаться мелкие частицы шлака неметаллических включений и газовые пузыри.
Припуски на механическую обработку отливок из медных сплавов делаются в соответствии с ГОСТ 26645-85.
Припуск на усадку. Величина припуска на усадку выбирается в зависимости от материала. На чертеже отливки величину припуска указывают в примечании или в правом нижнем углу. Модельщик при изготовлении модели использует соответствующий усадочный метр.
Для выбранной латуни линейная усадка при литье деталей большого веса (свыше 10 кг) составляет 14 - 18 %.
Формовочные уклоны служат для удобства извлечения моделей из формы без ее разрушения. Размеры отливки увеличиваются в направлении извлечения модели из формы то есть в сторону плоскости разъема формы. На обрабатываемые поверхности отливки формовочные уклоны задаются поверх припусков на механическую обработку на необрабатываемые - за счет увеличения или уменьшения размеров отливки.
Величину формовочных уклонов выбирают в зависимости от вида литья материала модели и высоты поверхности на которую назначается уклон и обозначается в градусах или в миллиметрах. В таблице 6.1 представлены их значения.
Таблица 6.1 – Значения формовочных уклонов.
Высота поверхности модели мм
Напуски служат для упрощения изготовления отливки. Например отверстия диаметром меньше 15 мм можно не оформлять в отливке так как целесообразно просверлить в процессе механической обработки.
Для данной детали можно не отливать пять отверстий 15 мм а также паз и отверстие 25мм.
Галтели и литейные радиусы определяются по формулам.
где a b - величины сопрягаемых поверхностей мм;
Нормальный ряд радиусов: 1;2;3;5;8;10;16;20;25;40. Таким образом в соответствии с нормальным рядом радиусов можно назначить все галтели.
Так как на отливке не должно быть острых углов которые являются концентраторами напряжений и затрудняют получение четкого контура отливки все острые кромки округляют радиусами размер которых не превышает 3-5 мм. Эти радиусы называются литейными и обозначаются R.
Чертеж отливки выполняют по имеющемуся чертежу детали в соответствии с требованиями ГОСТ 3.1125 - 88 и ведут в определенной последовательности.
Вначале выбирают поверхность разъема отливки далее по ГОСТ 7505-89 назначают припуски допуски напуски литейные уклоны радиусы закругления и указывают основные технические условия на отливку. Затем разрабатывают технологический процесс получения отливки.
Определяем коэффициент использования металла:
где VД – объем детали
VОТЛ – объем отливки
r - плотность материала (r=83 10 6 гм3).
VД= 160 16030 - 4152 304 + 4 1102 190 - 4 802 220 =
= 1446584 мм3 14466 10 -6 м3
VОТЛ= 160 160315 + 4 1132 200 - 4 772 228 =
= 1750440 мм3 17505 10 -6 м3
где МД – объем детали
МОТЛ – объем отливки.
МД =8300 14466 10 -6 = 1108 кг
МОТЛ=8300 17505 10 -6 = 1303 кг.
Разработка технологического процесса получения заготовки
На рисунке 7.1 представлена схема технологического процесса получения заготовки детали “Стакан”.
Рисунок 7.1 – Технологический процесс литья в песчано-глинистые формы
Ниже рассматриваются основные этапы получения заготовки. Формовочными материалами называют материалы применяемые для изготовления литейных форм и стержней.
Стержневые смеси для отливок делятся на пять классов. Для отверстий простой формы к чистоте поверхности которых особых требований не предъявляется применяется смесь четвертого класса. Стержни в процессе заливки используют большие термические и механические нагрузки. Поэтому они должны иметь большую огнеупорность податливость повышенную газопроницаемость и малую газотворность. Наиболее подходящим для смеси является состав состоящий из песка связующего марки ФФ-1С окиси железа графита серебристого. Такая смесь повышает производительность труда устраняет трудоемкую операцию сушки.
В качестве формовочных смесей для отливок применяют сырые и сухие песчаные смеси. В мелкосерийном производстве в основном применяются сухие смеси. Они обладают повышенной прочностью и пониженной податливостью. Для увеличения податливости в смесь добавляют опилки торф асбестовую крошку. Состав смеси: 70 % - отработанной смеси 27 % - свежего материала 3 % - древесных опилок.
Заливочную форму изготавливают в опоках – жестких рамках из стали марок 20Л и 30Л. Форму получают в двух опоках – верхней и нижней. Для точности сборки их центрируют штырями и втулками. В данном случае используются опоки для ручной формовки.
Противопригарные краски и пасты предохраняют поверхность отливки от пригара увеличивают поверхностную прочность уменьшают осыпаемость форм и стержней обеспечивают получение чистых отливок. Нанесение на поверхность формы и стержней краски способствует образованию прочного слоя огнеупорного материала. В данном случае выбирается краска марки ГБ.
Существует следующий порядок изготовления песчаной формы. Устанавливается деревянная модель на модельную плиту устанавливается пустая нижняя опока поверхность модели смачивается раствором керосина и мазута. Затем засыпается просеянная облицовочная смесь и слоями засыпается наполнительная смесь которая периодически уплотняется вручную. Далее опока переворачивается вместе с модельной плитой на 180 и устанавливается вторая половина модели. Устанавливается верхняя опока и процесс наполнения повторяется. Делаются наколы душником.
Далее модель извлекается из формы. Поверхности формы отделывают поврежденные места исправляют. Устанавливают стержни и собирают форму.
Модель состоит из деревянной формы повторяющую форму готовой отливки и литниковой системы. Литниковая система состоит: из воронки (для мелких отливок) предназначенной для приема струи металла; стояка – вертикального канала по которому течет расплавленный металл к другим элементам системы; питателей – каналов передающих метал в полость формы выпора предназначенного для отвода газов из полости формы. В данном случае шлакоуловитель не применяется т.к. он уже есть в устройстве индукционной печи.
Далее отливка охлаждается некоторое время вместе с формой. Затем она извлекается и форма разрушается из отливки извлекают стержни отделяются литники. Производится обрубка и очистка отливки ее первая термическая обработка. Отливка готова.
Термическая обработка заготовки
Термическая обработка представляет собой совокупность операций нагрева выдержки и охлаждения проводимых в определенной последовательности с целью изменения внутреннего строения сплава и получения нужных свойств 3.
Для данной поковки производят следующую термическую обработку: диффузионный отжиг (гомогенизация). При данном отжиге происходит выравнивание химического состава по зерну и происходит повышение пластичности данной бронзы.
Диффузионный отжиг проводят при температуре 7000 – 7500С и охлаждение проводят как в воде так и на воздухе что обеспечивает однородную структуру. Данная термообработка необходима для дальнейшей механической обработки заготовки.
Механическая обработка
Механическая обработка представляет собой совокупность действий направленных на обеспечение нужной формы и размеров заготовки путем снятия слоя металла назначенного на припуски и напуски режущим инструментами. При этом получают заданную точность и чистоту поверхности.
Первая операция представляет собой подготовку баз для дальнейшей обработки детали. Она осуществляется на фрезерном станке. На рисунке 9.1 представлена схема обработки на первой операции.
Рисунок 9.1 – Схема обработки на первой операции
На последующих операциях происходит обработка остальных поверхностей и доведение их до нужной шероховатости и требований по точности. Наружные поверхности и отверстие обрабатывают на токарных фрезерных и расточных универсальных станках. Вначале получают отверстие затем наружный и внутренний контур и доводят эти отверстия.
Таким образом в данной курсовой работе был создан технологический процесс получения детали – стакан. Для заданных механических свойств был подобран соответствующий материал – ЛЦ16К4 для заданной программы 15 штук в год – способ получения – литье в песчано-глинистые формы. Разработан чертеж отливки учитывая припуски на механическую обработку напуски литейные уклоны и радиусы.
Библиографический список
Лахтин Ю.М. Леонтьева В.П. Материаловедение: Учебник для вузов. – М.: Металлургия 1990.
Кочеткова Л.П. Разработка чертежа отливки. Методические указания
Металловедение и термическая обработка цветных металлов. Колачев Б.А. Ливанов В.А. Елагин В.И. Издательство «Металлургия» 1972.
Кнорозов В.В. Технология металлов и материаловедение: Учебник для вузов. – М.: Металлургия1987.
Металловедение и технология материалов: Учебник для вузов Под ред. Ю.П. Солнцева. – М.: Металлургия 1988.
Марочник сталей и сплавов Сорокин В.Г. и др. 1989.
Рекомендуемые чертежи
- 24.01.2023
- 24.01.2023
Свободное скачивание на сегодня
- 24.01.2023