Проектирование привода с одноступенчатым редуктором (узла выходного вала)




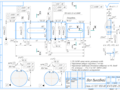
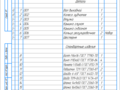
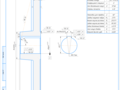
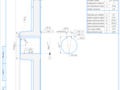
- Добавлен: 24.01.2023
- Размер: 1 MB
- Закачек: 1
Описание
Проектирование привода с одноступенчатым редуктором (узла выходного вала)
Состав проекта
![]() |
![]() |
![]() ![]() ![]() ![]() |
![]() |
![]() ![]() ![]() ![]() |
![]() ![]() ![]() ![]() |
![]() |
![]() ![]() ![]() ![]() |
![]() |
![]() ![]() ![]() ![]() |
![]() ![]() ![]() ![]() |
![]() |
![]() |
![]() ![]() ![]() ![]() |
![]() ![]() ![]() ![]() |
![]() ![]() ![]() ![]() |
![]() ![]() ![]() |
![]() ![]() ![]() |
![]() ![]() ![]() ![]() |
![]() |
![]() |
Дополнительная информация
Узел.cdw

Колесо11.cdw

Коэффициент смещения
Угол делительного конуса
Межосевой угол передачи
Средний окружной модуль
Внешнее конусное расстояние
Среднее конусное расстояние
Средний делительный диаметр
Сталь 45 ГОСТ 1050-88
Неуказанные радиусы скруглений 2 мм max
Неуказанные предельные отклонения отверстий по H14
остальных - IT142 по ГОСТ 30893.1-2002
* Размер обеспечить инструментом.
Узел11н.cdw

Компоновка.cdw

Узел11.cdw

Спецификация11.spw

Кольцо регулировочное
Болт М6х16 ГОСТ 7790-70
Винт М10х60 ГОСТ 11738-84
Манжета 1-55x80-3 ГОСТ 8752-79
Подшипник 7211 ГОСТ 27365-87
Шайба 6 65Г ГОСТ 6402-70
Шайба 7019-0633 ГОСТ 14734-69
Шпонка 14x9x50 ГОСТ 23360-78
Шпонка 16x10x63 ГОСТ 23360-78
Штифт 4x12 ГОСТ 3128-70
Вал11.cdw

Неуказанные радиусы скруглений 2 мм max.
Неуказанные предельные отклонения отверстий по H14
остальных - IT142 по ГОСТ 30893.1-2002.
* Размер обеспечивается инструментом.
Вал.cdw

Неуказанные радиусы скруглений 2 мм max.
Неуказанные предельные отклонения отверстий по H14
остальных - IT142 по ГОСТ 30893.1-2002.
* Размер обеспечивается инструментом.
Колесо.cdw

Коэффициент смещения
Угол делительного конуса
Межосевой угол передачи
Средний окружной модуль
Внешнее конусное расстояние
Среднее конусное расстояние
Средний делительный диаметр
Сталь 45 ГОСТ 1050-88
Неуказанные радиусы скруглений 2 мм max
Неуказанные предельные отклонения отверстий по H14
остальных - IT142 по ГОСТ 30893.1-2002
* Размер обеспечить инструментом.
Титульник.doc
Государственное образовательное учреждение высшего профессионального
Уфимский государственный авиационный технический университет
Кафедра основы конструирования механизмов и машин
ПРОЕКТИРОВАНИЕ ПРИВОДА С ОДНОСТУПЕНЧАТЫМ РЕДУКТОРОМ (УЗЛА ВЫХОДНОГО ВАЛА)
Пояснительная записка
к курсовой работе по дисциплине «прикладная (техническая) механика ОКиП»
(обозначение документа)
«УФИМСКИЙ ГОСУДАРСТВЕННЫЙ АВИАЦИОННЫЙ ТЕХНИЧЕСКИЙ УНИВЕРСИТЕТ»
Тема курсовой работы
Основное содержание:
Рассчитать и спроектировать привод (редуктор) по схеме 05.
Требования к оформлению
1. Пояснительная записка должна быть оформлена в соответствии с требованиями СТО УГАТУ 016-2007
В пояснительной записке должны содержаться следующие разделы:
Выбор электродвигателя. Определение основных кинематических и энергетических параметров редуктора.
Расчет закрытой зубчатой передачи.
Расчет шестерни открытой передачи.
Проектный расчет валов и подбор подшипников.
Расчет элементов редуктора.
Уточненный проверочный расчет валов.
Проверочный расчет подшипников.
Проверочный расчет шпоночных соединений.
Список использованной литературы
Эскизы стандартных деталей и изделий с указанием размеров.
2. Графическая часть должна быть оформлена в соответствии с требованиями СТО УГАТУ 016-2007
Графическая часть должна содержать:
Эскизную компоновку редуктора (узла вала) - формат А1 (А3).
Сборочный чертеж редуктора (узла вала) - формат А1 (А3).
Чертеж детали «Вал выходной» - формат(А2).
Чертеж детали «Колесо зубчатое» - формат(А2).
Пояснилка.doc
1. Определение требуемой мощности.6
2. Определение КПД привода.6
3. Определение требуемой мощности и частоты вращения вала электродвигателя.6
4. Определение передаточного числа редуктора.7
5. Определение крутящих моментов на валах редуктора.7
Проектировочный расчет зубчатой передачи.8
1. Расчет допускаемых контактных напряжений.8
2. Расчет допускаемых изгибных напряжений.9
Проектный расчёт конической передачи11
1. Определение диаметров шестерни и колеса11
2. Проверка зубьев на выносливость по контактными напряжениям.12
3. Проверка прочности зубьев по напряжениям изгиба.14
Расчёт открытой передачи.16
1. Выбор допускаемых напряжений на кручение.18
2. Конструирование быстроходного вала.18
3. Конструирование тихоходного вала.19
Конструирование элементов редуктора.21
1. Общие рекомендации.21
2. Конструктивное оформление внутреннего контура редуктора.21
3. Фиксирующее крепление крышки к корпусу.22
4. Конструктивное оформление опорной части корпуса.23
5. Конструктивное оформление крышки люка.24
6. Конструирование колеса25
Проверочный расчёт шпоночных соединений28
Проверочный расчёт тихоходного вала.29
1. Предварительное назначение подшипников.29
2. Конструирование крышек подшипников.30
3. Конструирование подшипниковых фланцев.31
4. Расчёт усилий в опорах вала.31
5. Проверочный расчёт подшипника по динамической грузоподъёмности.33
6. Построение эпюр моментов и определение максимального момента35
Проверочный расчёт вала на усталостную прочность37
Выбор сорта масла и уплотнений.40
1. Выбор способа и типа смазки подшипников.41
Допуски формы и допуски расположения поверхностей.42
1. Допуски формы и допуски расположения для тихоходного вала.42
2. Допуски формы и допуски расположения для колеса.42
ПРИЛОЖЕНИЕ. Эскизы стандартных деталей.47
Редуктором называют механизм состоящий из зубчатых или червячных передач выполненный в виде отдельного агрегата и служащий для передачи вращения от вала двигателя к валу рабочей машины. Кинематическая схема привода может включать помимо редуктора открытые зубчатые передачи цепные и ременные передачи. Указанные механизмы являются наиболее распространённой тематикой курсового проектирования.
Назначение редуктора - понижение угловой скорости и соответственно повышение вращающего момента ведомого вала по сравнению с ведущим.
Редуктор состоит из корпуса (литого чугунного или сварного стального) в котором помещают элементы передачи - зубчатые колёса валы подшипники и т.д. В отдельных случаях в корпусе редуктора размещают так же устройства для смазывания зацеплений и подшипников (например внутри корпуса может быть помещён шестеренный масляный насос) или устройства для охлаждения (например змеевик с охлаждающей водой в корпусе червячного редуктора).
Редуктор проектируют либо для привода определённой машины либо по заданной нагрузке (моменту на выходном валу) и передаточному числу без указания конкретного назначения. Второй случай характерен для специализированных заводов на которых организованно серийное производство редукторов.
Редукторы классифицируют по следующим основным признакам: типу передачи (зубчатые червячные или зубчато червячные); числу ступеней (одноступенчатые двухступенчатые и т.д.); типу зубчатых колёс (цилиндрические конические коническо - цилиндрические и т.д.) относительному расположению валов редуктора в пространстве (горизонтальные вертикальные); особенностям кинематической схемы (развёрнутая соосная с развёрнутой ступенью и т.д.)
Задание на проектирование.
Спроектировать одноступенчатый редуктор с закрытой конической передачей и цилиндрической шестернёй на выходном 350 Нм - крутящий момент на выходном валу;
0 - частота вращения выходного вала;
000 ч - время работы
- число зубьев шестерни на выходном валу.
Рисунок 1. Одноступенчатый редуктор.
Выбор электродвигателя. Определение основных кинематических и энергетических параметров редуктора.
1. Определение требуемой мощности.
Определяем потребляемую мощность привода:
= = = 14325 кВт (1.1)
Определяем потребляемую мощность электродвигателя по формуле
2. Определение КПД привода.
где - КПД подшипника на входном валу = 099
- КПД подшипника на выходном валу = 099
- КПД муфты на входном конце вала = 098
- КПД зацепления = 095
- КПД открытой передачи = 096
3. Определение требуемой мощности и частоты вращения вала электродвигателя.
Принимаем = 164 кВт.
Определяем частоту вращения вала электродвигателя.
Для частоты вращения ведущего вала одноступенчатого редуктора справедливо
= (700..1750) . (1.3)
Определив мощность и частоту вращения электродвигателя по таблице 24.9 2 подбираем электродвигатель с мощностью N кВт и частотой вращения n ротора ближайшими к = 164 кВт и оборотами (700..1750)
Выбираем двигатель IM1081 ТУ16-525.571-84 синхронная частота 1500 мощностью 185 кВт асинхронной частотой вращения
Рисунок 2. Двигатель.
4. Определение передаточного числа редуктора.
5. Определение крутящих моментов на валах редуктора.
На колесе = = = 36827 Нм; (1.5)
На шестерне = = = 10413 Нм; (1.6)
На конце быстроходного вала = = = 10519 Нм. (1.7)
Проектировочный расчет зубчатой передачи.
По табл. 8.7 выбираем для изготовления шестерни и колеса материал
Материал шестерни Сталь 45 материал колеса Сталь 45 временное сопротивление материала шестерни МПа временное сопротивление материала колеса МПа предел текучести материала шестерни МПа предел текучести материала колеса =450 МПа.
Принимаем средние значения твёрдости для шестерни колеса
1. Расчет допускаемых контактных напряжений.
Определяем допускаемые контактные напряжения для зубьев шестерни и колеса:
где - коэффициент долговечности учитывает режим работы определяется по табл. 8.10 1 - коэффициент безопасности;
предел выносливости контактной поверхности зубьев соответствующий базовому числу циклов переменных напряжений.
Определение базового числа циклов:
= = =154 млн циклов;
Определяем базовое число циклов для контактных напряжений
где c - число зацеплений колеса
n - частота вращения
- срок службы передачи ч.
Определяем эквивалентное число циклов для контактных напряжений; в соответствии с IV режимом нагружения принимаем по табл 8.9 1 = 0125
Определим коэффициент Если то
где - эквивалентное число циклов
- базовое число циклов.
Значение не может превышать 2.6 для колёс с однородной структурой металла и 1.8 - для колёс с неоднородной структурой металла.
= + 70 = 70 = 596 МПа (2.6)
= + 70 = 70 = 502 МПа. (2.7)
Коэффициент безопасности шестерни поскольку структура металла шестерни однородна по объёму
Коэффициент безопасности колеса поскольку структура металла колеса однородна по объёму
Pасчётное контактное напряжение - минимальное из двух найденных: = 4564 МПа
2. Расчет допускаемых изгибных напряжений.
Определяем эквивалентное число циклов для изгибных напряжений;
в соответствии с IV режимом нагружения принимаем по табл 8.9 1 = 0038 и коэффициент a = 6 (структура металла однородна по объёму) в соответствии с IV режимом нагружения принимаем по табл 8.9 1 = 0038 и коэффициент a = 6 (структура металла однородна по объёму)
Определим коэффициент
- базовое число циклов. = циклов.
Значение не может превышать 2.5 для колёс твёрже и 4 - для колёс с твёрдостью менее
Определяем предел выносливости по напряжениям изгиба для зубьев шестерни и колеса :
Определяем допускаемые изгибные напряжения для зубьев шестерни и колеса:
где - предел выносливости зубьев по напряжениям изгиба; Ya - коэффициент учитывающий реверсивность работы передачи при нереверсивной передаче = где - коэффициент учитывающий нестабильность свойств материала зубчатого колеса и ответственность зубчатой передачи (табл. 5.2 1 ). = принимаем = 175. - коэффициент учитывающий способ получения заготовки. Для поковок и штамповок = 1.
= = 175. = = 2705 МПа
- коэффициент концентрации нагрузки по длине зуба зависит от расстояния передачи относительно опор. Назначаем при = 1008 по рис. 2.5 3 = 189
Проектный расчёт конической передачи
Делительный диаметр колеса по внешнему торцу определяется по формуле
E - приведённый модуль упругости. В случае изготовления колеса и шестерни модуль упругости Е = 2100 ГПа.
Округляем по ряду Ra20 = 450 мм
Принимаем по графику 2.6 3 число зубьев шестерни = 25355
При значениях твёрдости и =
Определяем число зубьев колеса = = = 163965
Коррекция частоты вращения тихоходного вала:
Уточняем передаточное отношение
Угол делительного конуса колеса
= = arctg(4) = (3.4)
Угол делительного конуса шестерни = - = - =
Определяем внешний окружной модуль
1. Определение диаметров шестерни и колеса
Делительные диаметры по внешнему торцу рассчитываются по формуле
Определяем внешнее конусное расстояние передачи
Рабочая ширина зубчатого венца
= = = = 72268 мм (3.8)
Расчётный модуль зацепления в среднем сечении
Диаметры в среднем сечении рассчитываются по формуле
Диаметры вершин колёс рассчитываются по формуле
Коэффициенты смещения приняты равными нулю.
Диаметры впадин колёс рассчитываются по формуле
= = = = 72268 мм (3.13)
2. Проверка зубьев на выносливость по контактными напряжениям.
Расчетом должна быть проверена справедливость соблюдения следующего неравенства:
где - рабочая ширина венца колеса
- крутящий момент на шестерне
- Коэффициент расчётной нагрузки при контактных напряжениях
U - передаточное отношение
Определение степени точности передачи
Скорость в зацеплении определяется по формуле:
где d - диаметр колеса мм
n - частота вращения колеса
Скорость в зацеплении:
Согласно скорости по таблице 2.6 степень точности изготовления колёс
= = = 105219 Нм (3.16)
Момент на конце быстроходного вала = = = 106282 Нм
Расчет усилий в зацеплении
Окружное усилие в зацеплении колес рассчитывают по формуле:
= = = 199396 Н (3.17)
= = = 176019 H (3.18)
= = = 70407 H (3.19)
Определение коэффициента расчётной нагрузки
- коэффициент распределения нагрузки между зубьями.
Принимаем по табл 2.8 =
- коэффициент концентрации нагрузки по длине зуба зависит от расстояния передачи относительно опор. Назначаем при = 1 по рис. 2.5 3 = 1879
- коэффициент внутренней динамической нагрузки. Назначаем по табл. 2.7 3 зависимости от скорости и степени точности методом линейной интерполяции.
Коэффициент расчётной нагрузки = (3.20)
Таким образом = = = 1954
3. Проверка прочности зубьев по напряжениям изгиба.
Расчет выполняют отдельно для шестерни и для зубчатого колеса передачи после уточнения нагрузок на зубчатые колеса и их геометрических параметров. Проверяют справедливость соотношений расчетных и допускаемых напряжений изгиба:
- тангенциальная сила в зацеплении
- коэффициент расчётной нагрузки при изгибных напряжениях
- коэффициент формы зуба
- коэффициент концентрации нагрузки для изгибных напряжений по длине зуба зависит от расстояния передачи относительно опор. Вычисляется по формуле
- коэффициент внутренней динамической нагрузки. Назначаем по табл 2.7 3 в зависимости от скорости и степени точности методом линейной интерполяции.
Коэффициент расчётной нагрузки =
Таким образом = = = 2521
Эквивалентные числа зубьев для конических колёс рассчитываются по формуле
где и - числа зубьев зацепляющихся колёс
Коэффициенты формы зуба назначаются по табл 2.9 3
Сопоставление расчетного и допускаемого напряжений
Проверка по напряжениям изгиба: должно выполняться
Расчёт открытой передачи.
По табл. 87 1 выбираем для изготовления шестерни материал
Материал шестерни Сталь 45 временное сопротивление материала шестерни МПа предел текучести материала шестерни МПа.
Принимаем среднее значение твёрдости для шестерни
Определяем базовое число циклов.
Определяем реальное число циклов для напряжений изгиба.
в соответствии с IV режимом нагружения принимаем по табл 8.9 1 = 0038 и коэффициент a = 6 (структура металла однородна по объёму)
Определяем изгибное напряжение для зубьев открытой шестерни:
Определяем допускаемое изгибное напряжение для зубьев шестерни и колеса:
Эквивалентное число зубьев для прямозубых колёс:
Определение модуля открытой передачи:
- коэффициент ширины зубчатого венца колеса относительно модуля
- коэффициент концентрации нагрузки по длине зуба. Назначаем по 1 c 136 = 1641
Определение основных геометрических размеров шестерни
Делительный диаметр рассчитывается по формуле
Диаметр вершины шестерни: коэффициент смещения принят равным нулю.
Диаметр впадины шестерни рассчитывается по формуле
Ширина венца = = = 60 мм (4.2)
Окружное усилие в зацеплении колес:
Таким образом = = = 1951
Проверка по напряжениям изгиба: должно выполняться 24698 МПа 27051 МПа
1. Выбор допускаемых напряжений на кручение.
В проектируемых редукторах для изготовления валов рекомендуется применять термически обработанные среднеуглеродистые и легированные стали.
Для быстроходного вала: Сталь 45 нормализация МПа
Для тихоходного вала: Сталь 45 нормализация МПа
2. Конструирование быстроходного вала.
Рисунок 3. Эскиз быстроходного вала.
Определение минимального диаметра вала исходя из условия прочности по касательным напряжениям.
Скорректируем диаметр входного вала по диаметру вала электродвигателя согласно соотношению = = =(384 48) мм
Принимаем цилиндрический конец вала исполнения 2 по ГОСТ 12080-66 = 40 мм.
Длина конца вала = 82 мм по ГОСТ 6636-69.
Примем диаметр под манжету = 45 мм
Примем в зависимости от диаметр под гайку = 48 мм
Примем в зависимости от диаметр под подшипник = 50 мм
Длина участка под манжету и подшипник = = = 75 мм. При проектировании компоновки уточнится.
Длина участка вала под подшипник В уточняется после подбора подшипника ориентировочно B 20 мм.
Длина участка вала-шестерни равна ширине зубчатого венца рассчитанного выше.
3. Конструирование тихоходного вала.
Рисунок 4. Эскиз тихоходного вала.
Принимаем цилиндрический конец вала исполнения 2 по ГОСТ 12080-66 = 48 мм.
Длина конца вала = 60 мм по ГОСТ 6636-69.
Примем диаметр под подшипник = 55 мм
Длина участка под манжету и подшипник = = = 825 мм. При проектировании компоновки уточнится.
Диаметр вала под колесо: диаметр под колесо должен быть больше диаметра под подшипник для облегчения монтажа колеса на вал.
Диаметр бурта колеса определяется как = +
= + = 56 + = 62 64 мм
Длина участка вала под посадку колеса равна длине ступицы рассчитанной ниже.
Конструирование элементов редуктора.
1. Общие рекомендации.
Размеры корпуса определяются числом и размерами размещёных в них деталей их относительным расположением и величиной зазора между ними. Для удобства сборки корпус выполняют разъёмным.
Плоскость разъёма проходит через оси валов для удобства обработки располагается параллельно оси обработки. Верхняя часть крышки служащая технологической базой для обработки плоскости разъёма также выполняется параллельно оси валов.
2. Конструктивное оформление внутреннего контура редуктора.
Определение зазоров между вращающимися деталями
a = + 3 = + 3 = 1097 мм
Рисунок 5. Компоновка редуктора.
Толщина стенки корпуса
Толщина стенки крышки редуктора
Размеры конструктивных элементов:
Рисунок 6. Сечение корпуса.
3. Фиксирующее крепление крышки к корпусу.
Для крепления используются винты с цилиндрической головкой и шестигранным углублением под ключ.
Диаметр фланцевых винтов крепления крышки корпуса к корпусу определяется по формуле
Принимаем d = 10 мм.
Минимальная ширина фланца редуктора определяется из условия свободного размещения головки винта крепления крышки редуктора и толщины стенки редуктора
Координата размещения оси болта мм принимаем мм.
Рисунок 7. Крепление фланцевым болтом.
Необходимая точность фиксирования достигается штифтами. Используются два конических штифта с внутренней резьбой которые устанавливаются по срезам углов крышки.
Диаметр штифтов = = = (7 8) = 8 мм 2 c 242
Длина штифтов = 40 мм.
Рисунок 8. Фиксирование крышки редуктора штифтом.
4. Конструктивное оформление опорной части корпуса.
Опорная поверхность выполнена в виде четырех расположенных в местах установки болтов платиков. Такое расположение позволяет снизить расход металла и уменьшает время обработки опорной поверхности корпуса снижает нагрузки на резьбовые детали.
Рисунок 9. Опорная поверхность.
Диаметр фундаментных болтов определяется по формуле
5. Конструктивное оформление крышки люка.
Для заливки масла в редуктор и контроля правильности зацепления делают люк. Чтобы удобнее было заливать масло и наблюдать за зубчатыми колесами размеры люка должны быть максимально возможными. Люк закрывается стальной крышкой из листов толщиной
При среднесерийном производстве крышку выполняют штампованной. Для того чтобы внутрь корпуса извне не засасывалась пыль под крышку ставят уплотняющую прокладку. Материал прокладки - технический картон толщиной мм. Крышка крепится к корпусу винтами.
Крышка совмещена с отдушиной. Во внутренней штампованной крышке пробиты 4 отверстия диаметром мм. Наружная крышка - плоская. Вдоль её длинной стороны выдавлены гребня через которые внутренняя полость редуктора соединена с внешней средой.
Пространство между внутренней и внешней крышками заполнено фильтром из тонкой медной проволоки.
Длина крышки L = 492 мм.
= = = (492 59) = 5 мм.
= = = (216 27) = 2 мм.
Рисунок 10. Крышка-отдушина..
Проушина для подъема и транспортировки выполняется в виде ребра с отверстием диаметр которого D = = = 16 мм и шириной S = = = 16 мм.
Рисунок 11. Проушина.
6. Конструирование колеса
Форма зубчатого колеса может быть c плоской или выступающей ступицей.
При среднесерийном производстве заготовки колес получают из прутка свободной ковкой а также ковкой и в штампах.
= + 10= + 10 = 94 мм
Определение длины ступицы.
Поскольку то принимаем = 72 мм
Определяем толщину обода зубчатого венца: S + 2 мм.
Торец зубчатого венца шириной используют для установки заготовки при нарезании зубьев. = 7 мм
внешние углы зубьев притупляются фаской
Толщина обода: С = = = (216..288) = 24 мм
Рисунок 12. Эскиз зубчатого колеса.
Длины шпонок принимаются по ряду предпочтительных чисел по ГОСТ 23360-78. Предварительный подбор параметров осуществляется по табл. 24.29.
Шпонка на конце быстроходного вала
Длина шпонки L = 70 мм
Ширина шпонки b = 12 мм
Высота шпонки h = 8 мм
Рабочая длина шпонки = L - b = 70 - 12 = 58 мм
Глубина паза вала = 5 мм
Глубина паза под колесо = 33 мм
Шпонка на конце тихоходного вала
Длина шпонки L = 50 мм
Ширина шпонки b = 14 мм
Высота шпонки h = 9 мм
Рабочая длина шпонки = L - b = 50 - 14 = 36 мм
Глубина паза вала = 55 мм
Глубина паза под колесо = 38 мм
Шпонка под колесом тихоходного вала.
Длина шпонки L = 63 мм
Ширина шпонки b = 16 мм
Высота шпонки h = 10 мм
Рабочая длина шпонки = L - b = 63 - 16 = 47 мм
Глубина паза вала = 6 мм
Глубина паза под колесо = 43 мм
Расчёт шпонок приведён ниже.
Проверочный расчёт шпоночных соединений
Рисунок 13. Шпоночное соединение.
Из условия прочности на смятие имеем:
Для неподвижных соединений при посадках с натягом принимают = МПа. с 90. Поскольку все вычисленные напряжения смятия ниже допускаемого = 110 МПа то все шпонки удовлетворяют условию прочности.
Проверочный расчёт тихоходного вала.
1. Предварительное назначение подшипников.
Рисунок 14. Подшипник.
Для быстроходного вала назначаем шариковые радиальные подшипники лёгкой серии 210
Внутренний диаметр d = 50 мм
Наружный диаметр D = 90 мм
Динамическая грузоподъёмность С = 35100 Н
Статическая грузоподъёмность = 19800 Н
Диаметр шарика = 127 мм
Для тихоходного вала назначаем роликовые конические подшипники серии диаметров 2 серии ширин 0
Внутренний диаметр d = 55 мм
Наружный диаметр D = 100 мм
Динамическая грузоподъёмность С = 84200 Н
Статическая грузоподъёмность = 61000 Н
Эксцентриситет e = 041 мм
2. Конструирование крышек подшипников.
Рисунок 15. Эскиз крышки подшипников.
Крышка подшипника на быстроходном валу
Стенка крышки при диаметре внешнего кольца подшипника D = 90 по = 6 мм
Установочный поясок принимаем равным толщине крышки S = 6 мм
Канавка для выхода шлифовального круга b = 5 мм - принимается по табл 7.8 при диаметре внешнего кольца подшипника D = 90 мм
Длина пояска сопряжения l b =
Крышка подшипника на тихоходном валу
Стенка крышки при диаметре внешнего кольца подшипника D = 100 по = 7 мм
Установочный поясок принимаем равным толщине крышки S = 7 мм
Канавка для выхода шлифовального круга b = 5 мм - принимается по табл 7.8 при диаметре внешнего кольца подшипника D = 100 мм
3. Конструирование подшипниковых фланцев.
Рисунок 16. Эскиз фланца подшипников.
Диаметры приливов в которых располагаются подшипники определяются по формуле
Фланец подшипника на быстроходном валу:
= + 10 = + 10 = 1125 + 10 = 1225 мм;
Фланец подшипника на тихоходном валу:
= + 10 = + 10 = 125 + 10 = 135 мм;
Минимальная ширина фланца редуктора мм.
4. Расчёт усилий в опорах вала.
Для проверки подшипников на прочность необходимо определить силовые факторы воздействующие на подшипниковые узлы
Расчет усилий в зацеплениях открытой передаче
Расстояния между точками приложения усилий определяются замерами на чертеже: = 13160 мм = 3700 мм = 7650 мм.
Рисунок 17. Расчётная схема.
Расчёт реакций в опорах плоскости XOZ. Уравнение равновесия относительно точки А. M(A)=0.
Уравнение равновесия относительно точки D. M(D)=0.
-301081 + 1260478 - 199396 - 7600 = 0
Расчёт реакций в опорах плоскости YOZ
Реакции в опорах определяем на основании уравнений равновесия относительно точки A. M(A)=0.
Уравнение равновесия относительно точки D. (D)=0.
229 + -300245 - 17602 + 276617 = 0
Определение максимальных усилий.
Опора А принимается плавающей. Осевые силы приложены к опоре С.
Результируюшая осевая сила = 70407 H
5. Проверочный расчёт подшипника по динамической грузоподъёмности.
Требуемый ресурс долговечности подшипников по заданию = 15000 ч
Назначаем по 2 для ведомого вала роликовые конические подшипники серии диаметров 2 серии ширин 0 со следующими характеристиками:
Определяем эквивалентные радиальные нагрузки приводя переменный режим нагружения к эквивалентному постоянному:
здесь = 05 - коэффициент режима работы
Минимально необходимые для работы радиально-упорных подшипников осевые силы:
Находим осевые силы нагружающие подшипники
Примем = = 51707 H. Тогда из условия равновесия вала = + = 70407 + 51707 = 122115 H
Поскольку в таком случае примем = = 220471 H. Тогда из условия равновесия вала = - = 220471 - 70407 = 150063 H
Отношение = = 099. При e = 041 принимаем Х = 04 Y = 08.
Отношение = = 034. При e = 041 принимаем Х = 1 Y = 0.
эквивалентная динамическая радиальная нагрузка
где V - коэффициент вращения; V = 1 (вращение внутреннего кольца подшипника)
= 14 - коэффициент безопасности;
= 1 - температурный коэффициент;
Определяем эквивалентное время работы
где n - частота вращения вала n = 360
Определяем потребную динамическую грузоподъемность выбранного подшипника и сравниваем ее с паспортной.
где - коэффициент корректирующий ресурс в зависимости от надёжности
- коэффициент характеризующий совместное влияние на ресурс особых свойств подшипника и условий его эксплуатации = 075
= = = 6856645 84200 Н
6. Построение эпюр моментов и определение максимального момента
Изгибающие моменты в плоскости XOZ
Изгибающие моменты в плоскости YOZ
Определение результирующих моментов:
Проверочный расчёт вала на усталостную прочность
Для валов расчет на сопротивление усталости является основным. Прежде всего устанавливаем характер цикла напряжений. Так как установить действительный цикл нагрузки машины в условиях эксплуатации трудно расчет выполняем по номинальной нагрузке а циклы напряжений принимаем: симметричный - для напряжений изгиба и отнулевой для напряжений кручения.
Цель расчета - определение запаса сопротивления усталости в опасном сечении. При совместном действии кручения и изгиба запас сопротивления усталости определяем по формуле согласно
где запасы сопротивления по изгибу и кручению согласно
Определение коэффициентов концентрации напряжения согласно
где - масштабный коэффициент
- фактор чистоты поверхности
и - коэффициенты концентрации напряжений для данного сечения вала
и - эффективные коэффициенты концентрации напряжений
По - амплитуды переменных составляющих циклов напряжений - постоянные составляющие.
где - осевой момент сопротивления при изгибе
- осевой момент сопротивления при кручении.
Коэффициенты корректирующие влияние постоянной составляющей цикла напряжений на сопротивление усталости:
Выбор материала вала
Материал вала Сталь 45 нормализация
Временное сопротивление = 610 МПа
Предел выносливости при изгибе = 275 МПа.
Предел выносливости при кручении = 165 МПа.
Расчет вала на выносливость.
Проведём расчёт для опасного сечения
Опасный участок - посадка подшипника с натягом
Назначаем коэффициенты согласно 2
- эффективный коэффициент концентрации напряжений в отношении к масштабному фактору при изгибе. По таблице 10.9 2 при d = 55 мм = 610 МПа принимаем = 333 = 241
Коэффициент чистоты поверхности согласно табл 10.8 2
Опасный участок - галтель
по табл 10.3 2 - масштабный коэффициент для изгиба = 072 для кручения = 08
и - эффективные коэффициенты концентрации напряжений для радиуса галтели r = 16 мм и высоты уступа t = по табл 10.6 2 = 202 = 169
Опасным участком является посадка подшипника с натягом.
Усталостная прочность тихоходного вала обеспечивается поскольку запас прочности превышает минимальное значение s: 223 15
Выбор сорта масла и уплотнений.
Смазывание зубчатого зацепления производится окунанием зубчатого колеса в масло заливаемое внутрь корпуса (картерная смазка).При вращении колёс внутри корпуса образуется взвесь частиц масла которые покрывают поверхность расположенных внутри деталей.
Объём масляной ванны для одноступенчатых цилиндрических редукторов рекомендуется принимать таким чтобы на 1 кВт передаваемой мощности приходилось 035-07 л масла.
V = = = (647..1295). Объём масла V = 12 л
Рекомендуемое значение вязкости масла для зубчатых колёс закрытых передач при контактном напряжении = 37607 МПа и окружной скорости v = 804 = 2028 Руководствуясь вязкостью масла назначаем по ГОСТ 20799-88 Масло индустриальное И-Л-А-22 Принцип назначения сорта масла: чем выше контактные давления в передаче и чем меньше скорость тем более вязкой должно быть масло. Глубина погружения колёс в масло.
Принимаем = 16 105 мм.
Для контроля за уровнем масла в корпусе устанавливают жезловый маслоуказатель (щуп). Для замены масла в редукторе предусматривают сливное отверстие.
У редуктора имеются входные концы валов на быстроходной и тихоходной ступенях. Для предохранения от вытекания смазочного материала из подшипниковых узлов и для защиты их от попадания пыли и влаги извне применяют манжетные уплотнения.
Манжеты подбирают по ГОСТ 8752-79.
Манжета быстроходного вала: d = 50 мм D = 70 мм H = 10 мм.
Манжета тихоходного вала: d = 55 мм D = 80 мм H = 10 мм.
При установке манжетного уплотнения в стенке крышки сверлят 3 отверстия диаметром 3 мм для выпрессовки манжеты в случае необходимости.
1. Выбор способа и типа смазки подшипников.
Подшипники смазывают тем же маслом что и детали передач. Смазывание их другим смазочным материалом применяют редко. При картерной системе смазки подшипники также смазываются брызгами масла. При окружной скорости колёс больше 1 брызгами масла покрыты все детали передач и внутренние поверхности стенок корпуса. Стекающее с колёс валов и со стенок корпуса масло смазывает подшипники.
Допуски формы и допуски расположения поверхностей.
1. Допуски формы и допуски расположения для тихоходного вала.
Допуск цилиндричности на подшипниковую цапфу при значении допуска по JT6 0019 допуск цилиндричности Т = = 00095. Принимаем Т = 0008
Допуск цилиндричности на место посадки колеса при значении допуска по JT6 0019 допуск цилиндричности Т = = 00095. Принимаем Т = 0008
Допуск цилиндричности диаметра конца вала при значении допуска по JT6 0016 допуск цилиндричности Т = = 0008. Принимаем Т = 0008
Допуск соосности на подшипниковую цапфу при роликовых подшипниках диаметре 55 и ширине подшипника 2275 мм допуск по табл 22.5
= 0002275. Принимаем = 0002
Допуск соосности на место посадки колеса при степени точности 6 диаметре колеса 42215 мм и диаметре вала 56 мм допуск по табл 22.8 6 и по табл 22.6 0025
Допуск перпендикулярности на подшипниковую цапфу при роликовых подшипниках (степень точности 7) и диаметре упорного буртика 63 допуск по табл. 22.8 002
Допуски на шпоночный паз вала под колесом. Ширина шпонки 16 мм. Допуск параллельности Т = = = 00215. Принимаем Т = 002 Допуск симметричности Т = = = 0086. Принимаем Т = 008
Допуски на шпоночный паз конца вала. Ширина шпонки 14 мм. Допуск параллельности Т = = = 00215. Принимаем Т = 002 Допуск симметричности Т = = = 0086. Принимаем Т = 008
2. Допуски формы и допуски расположения для колеса.
Допуск цилиндричности на отверстие при значении допуска по JT7 003 допуск цилиндричности Т = = 0015. Принимаем Т = 0012
Допуск перпендикулярности при диаметре ступицы 95 и роликовых подшипниках (степень точности 7) допуск по табл 22.8 002
Допуски на шпоночный паз колеса. Ширина шпонки 16 мм. Допуск параллельности Т = = = 00215. Принимаем Т = 002 Допуск симметричности Т = = = 0086. Принимаем Т = 008
Расчёт длины общей нормали.
Определить величину средней длины общей нормали и её верхнего и нижнего отклонений для прямозубого колеса с внешними зубьями имеющего Z = 164; m = 2574083780424 мм; Х = 0 и выполненного по степени точности ГОСТ 1643-81
По табл.5.30 определяем = 4214997 для = 14 m = 1 мм и Х = 0.
При m = 2574083780424 мм и Х = 0 W = = 108498 мм.
Наименьшее отклонение средней длины общей нормали определяем по табл. 2.5 Слагаемое I равно 26 мкм для вида сопряжения В и степени точности по нормам плавности при d = 42215 мм. Слагаемое II равно 5 мкм по табл. 2.6 при величине допуска на радиальное биение = 0 мкм по табл. 2.2 Тогда = 0 + 5 = 11545082 мкм.
Допуск на среднюю длину общей нормали определяем по табл. 2.7: = 140 мкм для вида сопряжения В и значения = 0 мкм. Нижнее отклонение средней длины общей нормали = - (11545082 + 56) = - 11545222 мкм.
Перед сборкой внутреннюю область полости редуктора тщательно очистить и покрыть маслостойкой краской.
Сборку производить в соответствии со сборочным чертежом редуктора начиная с узлов валов:
-на ведущий вал насадить подшипники предварительно нагретые в масле до 80-100 С;
- в ведомый вал заложить шпонку и напрессовать зубчатое колесо до упора в бурт вала; затем надеть дистанционное кольцо и установить подшипники предварительно нагретые в масле;
Собранные валы уложить в основание корпуса редукторами надеть крышку корпуса покрыв предварительно поверхности стыка крышки и корпуса спиртовым лаком. Затянуть болты крепящие крышку к корпусу.
Установить сквозную и глухую крышки подшипников с комплектом прокладок для регулировки.
Проверить проворачиванием валов отсутствие заклинивания подшипников (валы должны проворачиваться от руки) и закрепить крышки болтами.
Далее на конец ведомого вала в шпоночную канавку заложить шпонку.
Залить в корпус масло.
Собранный редуктор обкатать и подвергнуть испытанию на стенде по программе устанавливаемой техническими условиями.
При передаче момента шпоночным соединением посадка цилиндрического прямозубого колеса принимается
Для сборки предусмотрен направляющий цилиндрический участок вала с полем допуска d11.
Посадка цилиндрического прямозубого колеса открытой передачи осуществляется по
Посадки шпонок регламентированы ГОСТ 23360-78 и принимаются для посадки в паз вала в паз колеса
Посадки шариковых подшипников для соединения с вращающимся валом при режиме работы подшипника осуществляются с натягом исключающим проворачивание и обкатывание кольцом сопряжённой детали вызывающее развальцовку посадочных поверхностей и контактную коррозию. Посадки внешнего кольца неподвижного относительно нагрузки назначают более свободным допускающим наличие небольшого зазора благоприятно влияющего на температурные и монтажные перемещения
Посадка манжетных уплотнений в корпус крышки подшипника не должна осуществляться с применением силы но в то же время она должна быть плотной. Поэтому участок под установку манжеты выполняют по H8. Вследствие прижатия манжеты браслетной пружиной к валу наблюдается износ участка манжеты контактирующей с валом. Поэтому участок посадки вала выполняют c допуском с зазором d9 и полируют.
Посадки глухих крышек подшипников выполняется по сквозных с установленной манжетой - по более точной посадке
Иванов М.Н. Детали машин: Учебник для студентов высших технических учебных заведений. - изд. перераб. - М.: Высшая школа 1998. - 447 с.
Дунаев П.Ф. Леликов О.П. Конструирование узлов и деталей машин: Учеб. пособие для машиностроительных специальностей вузов. - изд. перераб. и доп. - М.: Высшая школа 1998. - 447 с.
Расчет и конструирование одноступенчатого зубчатого редуктора: Учеб. пособие М.Ш.Мигранов О.Ф. Ноготков А.А.Сидоренко Л.Ш. Шустер. - М.: Изд-во МАИ 2002. - 125 с.
Допуски и посадки: Справочник в ч. Под ред. В.Д. Мягкова изд. перераб. и доп. - Л.: Машиностроение. Ленингр. отд-ние 1983.- 447 с.
В.И. Анурьев "Справочник конструктора-машиностроителя" том 1. - 2001. - 920 с.
В.И. Анурьев "Справочник конструктора-машиностроителя" том 2. - 2001. - 912 с.
В.К. Итбаев Р.Г. Ахматвалиев А.А. Сидоренко Б.А. Беляев. Расчет зубчатых передач. Методические указания к выполнению курсового проектирования по дисциплине "Прикладная механика". - Уфа 2009. - 35 с.
Расчет зубчатых передач. Методические указания к выполнению курсового проектирования по дисциплине "Прикладная механика". изд. испр. и доп. Уфимск. гос. авиац. техн. ун-т; Сост.: В.К. Итбаев Р.Г. Ахматвалиев А.А. Сидоренко Б.А. Беляев. - Уфа 2009. - 35 с.
Измерительные размеры зубчатых колес Сост.: О.Ф. Ноготков В.Н. Рубцов С. М. Минигалеев - Уфа 2009. - 33 с.
СТО УГАТУ 016-2007. Графические и текстовые конструкторские документы. Требования к построению изложению оформлению. - Уфа: Уфимск. гос. авиац. техн. ун-т 2007. - 93 с.
ПРИЛОЖЕНИЕ. Эскизы стандартных деталей.
Болт с шестигранной головкой класса точности B (ГОСТ 7790-70)
Винт с цилиндрической головкой класса точности B (ГОСТ 11738-84)
Манжеты резиновые армированные для валов (ГОСТ 8752-79)
Подшипники роликовые конические (ГОСТ 27365-87)
Шайба пружинная (ГОСТ 6402-70)
Шайба на конце вала ГОСТ 14734-69
Шпонки призматические (ГОСТ 23360-78)
Штифт конический (ГОСТ 9464-79)
Штифт цилиндрический (ГОСТ 3128-70)
Компоновка11.cdw

Рекомендуемые чертежи
- 24.01.2023
Свободное скачивание на сегодня
- 23.02.2023