Проектирование привода к цепному конвейеру




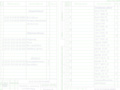
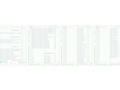
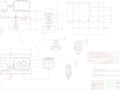
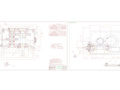
- Добавлен: 24.01.2023
- Размер: 893 KB
- Закачек: 0
Описание
Состав проекта
![]() |
![]() ![]() ![]() ![]() |
![]() ![]() ![]() |
![]() ![]() ![]() ![]() |
![]() ![]() ![]() ![]() |
![]() ![]() ![]() ![]() |
![]() ![]() ![]() |
![]() ![]() ![]() ![]() |
![]() ![]() ![]() ![]() |
![]() |
![]() ![]() ![]() ![]() |
![]() ![]() ![]() ![]() |
Дополнительная информация
Рама спецификая.dwg

Швеллер 14 ГОСТ 1478-75
02.15.01.20.00.000СБ
Швеллер 16 ГОСТ 1478-75
Записка по ДМ.doc
Федеральное государственное образовательное учреждение
высшего профессионального образования
«ПЕРМСКАЯ ГОСУДАРСТВЕННАЯ СЕЛЬСКОХОЗЯЙСТВЕННАЯ
АКАДЕМИЯ ИМЕНИ АКАДЕМИКА
Кафедра деталей машин.
ПОЯСНИТЕЛЬНАЯ ЗАПИСКА
К КУРСОВОМУ ПРОЕКТУ ПО ДЕТАЛЯМ МАШИН
на тему: Проектирование привода к цепному конвейеру.
Расчет энерго-кинематических параметров привода5
1 Выбор электродвигателя5
2 Определение чисел оборотов валов7
3 Определение крутящих моментов на валах8
Расчет цепной передачи9
Проектирование и расчет редуктора15
1 Выбор материала и термообработки15
2 Допускаемые напряжения15
3 Расчет тихоходной передачи24
3.1 Межосевое расстояние24
3.2 Предварительные основные размеры колеса26
3.3 Модуль передачи26
3.4 Суммарное число зубьев и угол наклона27
3.5 Число зубьев шестерни и колеса28
3.6 Фактическое передаточное число28
3.7 Диаметры колес28
3.8 Размеры заготовок колес29
3.9 Проверка зубьев колес по контактным29
3.10 Силы в зацеплении29
3.11 Проверка зубьев колес по напряжениям изгиба30
4 Расчет быстроходной передачи.31
4.1 Межосевое расстояние31
4.2 Основные параметры передачи31
4.3 Размеры червяка и колеса32
4.4 Проверочный расчет передачи на прочность33
4.6 Силы в зацеплении.35
4.7 Проверка зубьев колес по напряжениям изгиба35
4.8 Тепловой расчет36
Проектный расчет валов37
Расчет деталей редуктора40
1.1 Расчет тихоходного вала40
1.2 Расчет промежуточного вала45
1.3 Расчет быстроходного вала50
2 Расчет шпоночных соединений55
Проверочный расчет подшипников57
2 Промежуточный вал59
3 Быстроходный вал61
Смазочный материал и система смазки64
Современные высокопроизводительные машины обеспечивают многократное повышение производительности труда человека.
Самым общим показателем производительности машин может служить их мощность т.е. количество энергии в единицу времени преобразуемое в машине из одного вида в другой или используемое на производственный процесс- обработку или транспортирование изделий. В настоящее время машины-двигатели (турбины) и машины-преобразователи (электрические генераторы) строят мощностью до 500000 кВт и проектируют до 1000000 кВт.
Эффективность транспортных машин может быть охарактеризована грузоподъемностью и скоростью передвижения.
Развитие техники и средств автоматизации обеспечивает возможность автоматической работы отдельных машин групп машин цехов и даже целых заводов с минимальным участием человека.
Машины настолько прочно вошли в жизнь общества что в настоящее время трудно найти такой предмет или продукт потребления который был бы изготовлен или доставлен без помощи машин. Без машин невозможно было бы современное развитие наук медицины искусств требующих совершенных инструментов и материалов были бы невозможны быстрые темпы строительства промышленных и гражданских сооружений а также удовлетворение населения предметами широкого потребления.
Машины в обществе облегчают труд рабочих и снижают вредность и опасность отдельных видов трудовых процессов.
Ведущая роль машиностроения среди других отраслей народного хозяйства определяется тем что основные производственные процессы во всех отраслях промышленности строительства и сельского хозяйства производятся машинами. Технический уровень всех отраслей народного хозяйства тесно связан и в значительной степени определяется уровнем машиностроения.
Расчет энерго-кинематических параметров привода.
1 Выбор электродвигателя.
Потребляемую мощность привода (мощность на выходе) определим по формуле:
где Ft – тяговая сила на звездочке; Ft=300Н
V – скорость цепи; V=02мс
Определим потребную мощность электродвигателя:
Потребную мощность электродвигателя определим по формуле:
где общ. – общий КПД привода;
где цил. – КПД зубчатого цилиндрического зацепления; цил.=097 ([1] табл. 1.1 с. 6)
чер. – КПД червячного зацепления; чер=08 ([1] табл. 1.1 с. 6)
опор. – КПД опор конвейера; опор=099 ([1] табл. 1.1 с. 6)
ц.п. – КПД цепной передачи; ц.п.=093 ([1] табл. 1.1 с. 6)
муф. – КПД муфты; муф.=098 ([1] табл. 1.1 с. 6)
Тогда общий КПД привода будет:
Потребная мощность электродвигателя:
Определим число оборотов приводного вала привода:
где Dз- диаметр звездочки;
гдеpз – шаг приводной звездочки; pз=100мм;
zз – число зубьев приводной звездочки; zз=8;
Тогда диаметр звездочки будет:
Тогда число оборотов приводного вала будет:
Предварительно определим передаточные отношения привода.
По рекомендациям таблицы №1.2 ([1] с. 7) принимаем:
-передаточное отношение тихоходной цилиндрической передачи ;
-передаточное отношение быстроходной червячной передачи ;
-передаточное отношение цепной передачи ;
Тогда предварительное число оборотов вала двигателя будет:
Так как Pпотр. дв.=00857кВт и предварительная частота вращения двигателя то по каталогу подбираем двигатель серии АИР (закрытый обдуваемый) типа АИР71А6 ([1] табл. 24.9 с. 417).
Мощность двигателя: Pдв.=037кВт;
Асинхронная частота вращения ротора: nдв.=915обмин.
Уточним передаточные отношения привода.
Примем передаточное отношение цепной передачи тогда передаточное отношение редуктора будет:
где Uпривода – передаточное отношение привода в целом;
Принимаем передаточное отношение червячной передачи Uчер=12.
Тогда передаточное отношение тихоходной цилиндрической передачи:
Окончательно получаем:
2 Определение чисел оборотов валов.
Число оборотов двигателя:
Число оборотов быстроходного вала редуктора:
Число оборотов промежуточного вала редуктора:
Число оборотов тихоходного вала редуктора:
Число оборотов приводных валов цепных конвейеров:
3 Определение крутящих моментов на валах привода.
Вращающие моменты “Т” на валах:
-на выходном валу привода:
-на тихоходном валу редуктора:
-на промежуточном валу редуктора:
-на быстроходном валу редуктора:
Расчет цепной передачи.
где Т1 – вращающий момент на ведущей звездочке; Т1=Ттих.вал.=2128Нм
z1 – число зубьев ведущей звездочки;
– число рядов цепи; =1
[pц] – допускаемое давление в шарнирах цепи; [pц] =35МПа ([2] табл. 5.8 стр. 91);
КЭ – коэффициент эксплуатации;
где КД КС К Крег. Кр – коэффициенты принимаемые по табл. 5.7 ([2] стр. 90);
КД – коэффициент учитывающий динамичность нагрузки; КД=12
КС – коэффициент учитывающий способ смазки; КС=15
К – коэффициент учитывающий положение передачи; К=1
Крег – коэффициент учитывающий способ регулировки межосевого расстояния; Крег=125
Кр – коэффициент учитывающий режим работы; Кр=1
Тогда шаг цепи будет:
Определим число зубьев ведомой звездочки.
Определим фактическое передаточное число и проверим его отклонение от номинального.
Фактическое передаточное число:
Определим оптимальное межосевое расстояние. Из условия долговечности цепи:
Межосевое расстояние в шагах:
Определим число звеньев цепи lp.
Уточним межосевое расстояние ар в шагах:
Определим фактическое межосевое расстояние.
Монтажное межосевое расстояние.
Определим длину цепи.
Определим диаметры звездочек.
диаметры делительной окружности:
диаметры окружности выступов:
где К=07 – коэффициент высоты зуба ([2] стр. 92)
Кz – коэффициент числа зубьев;
для ведущей звездочки:
для ведомой звездочки:
λ – геометрическая характеристика зацепления;
где d1 – диаметр ролика шарнира цепи; d1=445мм ([2] табл. К32 стр. 419)
Тогда диаметры окружностей выступов звездочек будут:
диаметры окружностей впадин:
Проверим частоту вращения меньшей звездочки:
где n1 – частота вращения меньшей звездочки равная
n1=nтих.вал.=2923обмин
[n]1 – допускаемая частота вращения;
Условие выполняется.
Проверим число ударов цепи о зубья звездочек:
где U – расчетное число ударов цепи;
[U] – допускаемое число ударов;
Определим фактическую скорость цепи:
Определим окружную силу передаваемую цепью
где Р1 – мощность на ведущей звездочке;
где тих.вал. – частота вращения вала;
Проверим давление в шарнирах цепи:
гдеА – площадь проекции опорной поверхности шарнира;
где b3 – ширина внутреннего звена цепи; b3=775мм ([2] таб. К32 стр. 419)
[pц] – допускаемое давление в шарнирах цепи уточненное по рекомендациям ([2] стр. 91); [pц]=30МПа
Проверим прочность цепи.
где [S] – допускаемый коэффициент запаса прочности для роликовых цепей;
[S]=71 ([2] табл. 5.9 стр. 94)
S – расчетный коэффициент запаса прочности равный
гдеFp – разрушающая нагрузка цепи; Fp=18200Н ([2] табл. К32 стр. 419)
F0 – предварительное натяжение цепи от провисания ведомой ветви;
гдеKf – коэффициент провисания; Kf=6 ([2] стр. 94);
q – масса 1 метра цепи; q=075кгм ([2] табл. К32 стр. 419)
а – межосевое расстояние; а=5916мм
g – ускорение свободного падения; g=981мс2
Тогда сила F0 будет равна:
Fv – натяжение цепи от центробежных сил;
Тогда расчетный коэффициент запаса будет
Условие прочности цепи выполняется.
Определим силу давления цепи на вал:
где kв – коэффициент нагрузки вала; kв=115 ([2] табл. 5.7 стр. 90)
Тогда сила давления на вал будет:
Проектирование и расчет редуктора.
1 Выбор материала и термообработки.
Так как в задании не оговаривается о материале и твердости колес то принимаем для зубчатых колес и для червяка нашего привода уровень твердости HB>350 т.е. вариант III ([1] с. 11). Для данного варианта термообработки существуют следующие характеристики:
термообработка колеса и шестерни одинаковая – улучшение и закалка ТВЧ твердость поверхности 45 50 HRCэ;
Марка стали для колес шестерен и червяка одинаковая – сталь 40Х. С такой твердостью с такой термообработкой и из такой же стали будут делаться все валы редуктора.
Выбор материала для червячного колеса связан со скоростью скольжения определим предварительно ожидаемое значение скорости скольжения:
Тогда по рекомендациям ([1] с. 31) принимаем 3-ую группу мягкие серые чугуны по табл. 2.14 ([1] с. 31) принимаем – СЧ15 (литье в песок).
2 Допускаемые напряжения.
Допускаемые контактные напряжения и напряжения изгиба для колес и шестерен тихоходной ступени а также для червяка определяются отдельно.
Допускаемое контактное напряжение определим по формуле:
гдеHRCЭср – средняя твердость для двух предельных значений указанных выше;
что соответствует HBср=450
SH – коэффициент запаса прочности; SH=12 ([1] с. 13)
ZN – коэффициент долговечности;
при условии что 1 ≤ ZN ≤ ZNmax=26 ([1] с. 13)
где NHG – число циклов;
NК – ресурс передачи в числах циклов;
где n – число оборотов колеса; n=nтих.в.=2923обмин
nз – число зацеплений колеса; nз=1
Lh – суммарное время работы передачи; Lh=15000ч.
Тогда ресурс передачи будет:
Тогда коэффициент долговечности будет:
ZR – коэффициент учитывающий влияние шероховатости;
Z – коэффициент учитывающий влияние окружной скорости;
Тогда допускаемое контактное напряжение будет:
Допускаемое изгибное напряжение определим по формуле:
гдеFl Flim=550МПа (([1] табл. 2.3 с. 14)
SF – коэффициент запаса прочности; SF=17 ([1] с. 15)
YN – коэффициент долговечности;
при условии что 1 ≤ YN ≤ YNmax=25 ([1] с. 15)
где NFG – число циклов; NFG=4106 ([1] с. 15)
q – коэффициент; q=9 ([1] с. 15)
NК – ресурс передачи в числах циклов; NК=263107
Так как то принимаем NК=NFG=4106 ([1] с. 15). Тогда YN=1.
YR – коэффициент учитывающий влияние шероховатости;
YA – коэффициент учитывающий влияние двустороннего приложения нагрузки;
YA=1 – для одностороннего приложения нагрузки ([1] с. 15).
Тогда допускаемое изгибное напряжение будет:
где n – число оборотов шестерни; n=nпром.в.=7625обмин
nз – число зацеплений шестерни; nз=1
NК – ресурс передачи в числах циклов; NК=686107
Быстроходная ступень.
гдеHl Hlim=10075МПа (как у тихоходной ступени т.к. твердость ступеней одинакова)
где n – число оборотов червяка; n=nб.в.=915обмин
nз – число зацеплений червяка; nз=1
Так как то принимаем NК=NHG=699107 ([1] с. 13). Тогда ZN=1.
гдеFl Flim=550 (как у тихоходной ступени т.к. твердость шестерен ступеней одинаковая).
при условии что 1 ≤ YN ≤ YNmax=4 ([1] с. 15)
q – коэффициент; q=6 ([1] с. 15)
NК – ресурс передачи в числах циклов; NК=8235107
Допускаемое контактное напряжение.
Допускаемое напряжение при числе циклов перемены напряжений равным 107:
где vск – скорость скольжения; vск =0837мс
Допускаемое напряжение изгиба.
Допускаемое напряжение изгиба равно:
гдеKFL – коэффициент долговечности:
где NFЕ – эквивалентное число циклов нагружения;
где n – число оборотов червячного колеса; n=nпр.в.=7625обмин
nз – число зацеплений червячного колеса; nз=1
КFЕ – коэффициент эквивалентности; КFЕ=004 ([1] табл. 2.15 с.32)
Тогда эквивалентное число циклов нагружения будет:
[]F0 – исходное допускаемое напряжение;
где ви – предел временного сопротивления материала колеса; ви=360МПа ([1] табл. 2.14 с.31).
Тогда исходное допускаемое напряжение будет:
Тогда допускаемое напряжение изгиба будет:
Окончательно принимаем для нашего редуктора следующие допускаемые напряжения:
-допускаемое контактное напряжение [H]=75789МПа
-допускаемое изгибное напряжение; для колеса- [F2]=323529МПа
для шестерни- [F1]=323529МПа
Быстроходная ступень:
-допускаемое контактное напряжение [H]=83958МПа
-допускаемое изгибное напряжение [F]=323529МПа
-допускаемое контактное напряжение [H]=14568МПа
-допускаемое изгибное напряжение [F]=7079МПа
3 Расчет тихоходной передачи.
3. 1 Межосевое расстояние.
Предварительное значение межосевого расстояния:
гдеК – коэффициент принимается в зависимости от поверхностной твердости зубьев шестерни и колеса; К=6 ([1] с. 17);
Uтихс. – передаточное отношение тихоходного зацепления; Uтих.=26
Тпром – вращающий момент на шестерне; Тпром=841Нм
Тогда предварительное значение межосевого расстояния будет:
Определим окружную скорость на колесе:
гдеn1 – число оборотов шестерни; n1= nпром.вал=7625обмин
Тогда окружная скорость будет:
Примем степень точности зубчатой передачи по таблице 2.5 ([1] c. 17) в зависимости от окружной скорости – степень точности 9.
Уточним предварительно найденное значение межосевого расстояния по формуле:
гдеKа – коэффициент; Kа=450 ([1] с.17)
ba – коэффициент ширины; принимаем из ряда стандартных чисел в зависимости от положения колес относительно опор при несимметричном расположении ba=025 ([1] с. 17)
КН – коэффициент нагрузки;
гдеKHv – коэффициент учитывающий внутреннею динамику нагружения;
KHv=103 ([1] табл. 2.6 с.17)
KH – коэффициент распределения нагрузки по длине контактных линий;
где - начальный коэффициент распределения нагрузки принимаем по табл. 2.7 ([1] с. 19) в зависимости от коэффициента
KHw – коэффициент учитывающий приработку зубьев принимаем по табл. 2.8 ([1] с. 19) в зависимости от окружной скорости;
Тогда коэффициент распределения нагрузки по длине контактных линий будет:
KHα – коэффициент распределения нагрузки между зубьями;
где - начальный коэффициент распределения нагрузки между зубьями;
при условии 1 ≤ ≤ 16
гдеnст – степень точности передачи; nст=9
Тогда коэффициент нагрузки будет равен:
Тогда межосевое расстояние будет:
Принимаем аw=112мм.
3.2 Предварительные основные размеры колеса.
Делительный диаметр колеса:
3.3 Модуль передачи.
Максимально допустимый модуль mmax определим из условия неподрезания зубьев у основания:
Минимальное значение модуля mmin определим из условия прочности:
гдеКm – коэффициент; Кm=34103 ([1] с. 20)
КF – коэффициент нагрузки при расчете по напряжениям изгиба;
гдеКFv – коэффициент учитывающий внутреннюю динамику нагружения принимаем по табл. 2.9 ([1] с. 20):
КF – коэффициент учитывающий неравномерность распределения напряжений у основания зубьев по ширине зубчатого венца:
КFα – коэффициент учитывающий влияние погрешностей изготовления шестерни и колеса на распределение нагрузки между зубьями:
Тогда коэффициент нагрузки будет:
[]F – допускаемое изгибное напряжение; []F =323529МПа
Тогда минимальное значение модуля будет:
3.4 Суммарное число зубьев.
Суммарное число зубьев:
3.5 Число зубьев шестерни и колеса.
Число зубьев шестерни:
Принимаем z1=31> z1min=17
Число зубьев колеса:
3.6 Фактическое передаточное число.
Отклонение от заданного передаточного отношения составляет
Делительные диаметры:
Диаметры окружностей вершин dа и впадин df зубьев:
3.8 Размеры заготовок колес.
Для цилиндрической шестерни:
Для колеса c выточками:
Sзаг Сзаг Sпред.- параметры геометрии колеса.
3.9 Проверка зубьев колес по контактным напряжениям.
Расчетное контактное напряжение:
Z – коэффициент; Z=9600 ([1] с. 23)
КН – коэффициент; КН=1223
3.10 Силы в зацеплении.
3.11 Проверка зубьев колес по напряжениям изгиба.
Расчетное напряжение изгиба в зубьях колеса:
КF - коэффициент; КF=1329;
Y – коэффициент учитывающий наклон зубьев;
Y – коэффициент учитывающий перекрытие зубьев; Y=1 т.к. передача прямозубая ([1] с. 24).
YFS2 – коэффициент учитывающий форму зуба; принимается по табл. 2.10 ([1] с. 24) в зависимости от числа зубьев:
Расчетное напряжение изгиба в зубьях шестерни:
YFS1 – коэффициент учитывающий форму зуба; принимается по табл. 2.10 ([1] с. 24) в зависимости от числа зубьев:
Условие прочности по изгибным контактным напряжениям выполнено.
4 Расчет быстроходной передачи.
4. 1 Межосевое расстояние.
гдеКа – коэффициент для эвольвентного червяка Ка=610
KH – коэффициент концентрации нагрузки; при переменном режиме нагружения:
где- начальный коэффициент концентрации нагрузки по графику рис. 2.12 ([1] с. 33) т.к. Uб=12; z1=4 ([1] с.31) – число витков червяка;
4.2 Основные параметры передачи.
Коэффициент диаметра червяка:
Принимаем q=16 ([1] с. 33)
Минимально допустимое значение q из условия жесткости червяка:
Коэффициент смещения:
Углы подъема линии витка червяка.
- на делительном диаметре
- на начальном цилиндре
Отклонение фактического передаточного отношения от заданного:
4.3 Размеры червяка и колеса.
Делительный диаметр червяка:
Диаметр вершин витков:
Длина нарезанной части:
Увеличиваем b1 на 30мм т.е.
Диаметр делительной окружности колеса:
Диаметр окружности вершин зубьев:
Диаметр колеса наибольший:
где k – коэффициент; k=2 ([1] с. 34)
Тогда диаметр колеса наибольший будет:
а=0315 – коэффициент ширины зубчатого венца ([1] с. 34)
4.4 Проверочный расчет передачи на прочность.
Определим скорость скольжения в зацеплении:
где vw1 – окружная скорость на начальном диаметре червяка;
Тогда скорость скольжения будет:
Уточним допускаемое напряжение: [H]=10586МПа
Определим расчетное напряжение:
гдеZ – коэффициент Z=5350 ([1] с.35)
К – коэффициент нагрузки равный
где KHv – скоростной коэффициент; принимаем в зависимости от окружной скорости колеса;
KHv=1 ([1] табл. 2.6 с.17)
KН – коэффициент концентрации нагрузки:
где – коэффициент деформации червяка; =137 ([1] табл. 2.16 с. 35)
X – коэффициент режима; X=05([1] табл. 2.17 с. 11)
Тогда коэффициент нагрузки будет:
Коэффициент полезного действия червячной передачи.
где γw – угол подъема линии витка на начальном цилиндре; γw=14030
ρ – приведенный угол трения; ρ=230=25
4.6 Силы в зацеплении.
Окружная сила на колесе равная осевой силе на червяке:
Окружная сила на червяке равная осевой силе на колесе:
где dw1 – начальный диаметр червяка;
4.7 Проверка зубьев колес по напряжениям изгиба.
Расчетное напряжение изгиба:
где YF2=144 – коэффициент формы зуба ([1] c.36) принимается в зависимости от приведенного числа зубьев zv2:
4.8 Тепловой расчет.
Мощность на червяке:
Температура нагрева:
=03 – коэффициент учитывающий отвод теплоты от корпуса редуктора ([1]. c. 37)
Кт – коэффициент теплоотдачи; Кт=12Вт(м2С0) ([1] с. 37)
А – поверхность охлаждения корпуса; А=016 ([1] с.37)
Тогда температура нагрева масла будет:
Проектный расчет валов.
dм – диаметр вала под звездочку цепной передачи;
dп – диаметр под подшипник;
dК – диаметр под колесо;
dбк – диаметр под буртик колеса;
dбк – диаметр под буртик подшипника;
dш – диаметр под шестерню;
dбш – диаметр под буртик шестерни;
dбп – диаметр под буртик подшипника;
dк – диаметр под колесо;
d – диаметр выходного конца вала;
dман – диаметр под манжету;
dг – диаметр под гайку;
Расчет деталей редуктора.
1.1 Расчет тихоходного вала.
Расчетная схема вала.
Найдем реакции в опорах:
-в горизонтальной плоскости;
-в вертикальной плоскости;
Проверим вал на прочность.
Примем что нормальные напряжения от изгиба изменяются по симметричному циклу т.е. а=и и м=0 а касательные от кручения – по отнулевому (пульсирующему) т.е. а=к2 и m=к2.
Расчет будем вести в наиболее опасном сечении.
Наиболее опасными сечениями являются те сечения где изгибающие моменты максимальны а также если сечения имеют концентратор напряжения (самым наихудшим сечением является сечение с натягом).
Для тихоходного вала опасным сечением является сечение в т. Б (концентратор напряжения натяг).
Пределы выносливости: -1=32108Па; -1=2108Па;
Пределы текучести: Т=5108Па; Т=28108Па;
Коэффициент табл.=005.
Эти исходные параметры применимы для всех валов нашего редуктора для любого сечения. Материал и термообработка валов (см. раздел 3.1).
Рассмотрим сечение в точке Б (т.к. суммарный момент там наибольший).
Найдем суммарный момент:
Момент сопротивления сечению:
где d=40мм – диаметр вала в опасном сечении.
Полярный момент сопротивления:
Найдем амплитудные напряжения цикла а и а и средние напряжения цикла m и m.
Найдем коэффициент долговечности КL:
где N0 – базовое число циклов; N0=4·106 т.к. d50мм
Nц – эквивалентное число циклов;
m – число; m=6 – т.к. напрессовка;
где КЕ – коэффициент эквивалентности; КЕ=063 ([1] с. 108)
t = 15000ч – срок службы в часах;
Т.к. 1≤KL≤17 то принимаем KL=1
Коэффициенты концентрации напряжений:
где К и К – эффективные коэффициенты концентрации напряжений;
и – масштабные факторы;
По таблице 10.13 ([1] с.171):
– коэффициенты влияния шероховатости;
таблица 12.7 ([3] с. 279)
Ку – коэффициент упрочнения; Ку=2 (т.к. улучшение таблица 12.3 ([3] с. 277));
Коэффициенты запаса по нормальным и касательным напряжениям:
Тогда коэффициент запаса будет:
Данные расчета по тихоходному валу говорят о том что вал достаточно прочен.
1.2 Расчет промежуточного вала.
Рассмотрим сечение в точке В. Концентратор напряжения натяг.
где d=27мм – диаметр вала в опасном сечении.
bt1 – параметры шпоночного паза;
b=8мм t1=4мм ([1] табл. 24.29 с.432)
m – число; m=6 – т.к. натяг;
Т.к. 1≤KL≤17 то принимаем KL=1.
Данные расчета по промежуточному валу говорят о том что вал достаточно прочен.
1.3 Расчет быстроходного вала.
Найдем консольную силу FК.
где FtM – окружная сила на муфте.
где TБ – вращающий момент на быстроходном валу;
Выбираем муфту по таблице К21 ([2] с.400) в зависимости от крутящего момента TБ.
Муфта упругая втулочно-пальцевая ГОСТ 21424-75.
Dср. – параметр муфты;
где D и d0 – параметры муфты; D=90мм; d0=20мм.
Рассмотрим сечение в точке В. Концентратор витки червяка.
где df =34 мм – диаметр под подшипник.
где N0 – базовое число циклов; N0=4106 т.к. d50мм
m – число; m=9 – т.к. витки червяка;
Данные расчета по быстроходному валу говорят о том что вал достаточно прочен.
2 Расчет шпоночных соединений.
Для передачи момента с одного вала на другой колеса редуктора садятся на валы редуктора на шпонки.
Принимаем для нашего редуктора призматические шпонки со скругленными концами по ГОСТ 23360-78.
На тихоходном валу мы устанавливаем две шпонки: одну под звездочку цепной передачи другую под колесо. Проверим данные шпонки по напряжениям смятия.
Шпонка под звездочку.
Ширина шпонки b=10мм; высота шпонки h=8мм; длина шпонки l=45мм.
где Ттих. – вращающий момент на тихоходном валу; Ттих.=2128Нм
d – диаметр на котором устанавливается звездочка; d=35мм
[]см – допускаемое напряжение на смятие; для шпонок из стали 40 []см=420МПа.
Ширина шпонки b=14мм; высота шпонки h=9мм; длина шпонки l=40мм диаметр на котором устанавливается колесо d=45мм
На промежуточном валу мы устанавливаем две шпонки: одну под червячное колесо другую под шестерню.
Проверим данную шпонку по напряжениям смятия.
Ширина шпонки b=10мм; высота шпонки h=8мм; длина шпонки l=36мм.
где Тпр.в. – вращающий момент на промежуточном валу; Тпр.в.=841Нм
d – диаметр на котором устанавливается колесо; d=38мм
Шпонка под шестерню.
Ширина шпонки b=8мм; высота шпонки h=7мм; длина шпонки l=22мм диаметр на котором устанавливается колесо d=27мм
На быстроходном валу мы устанавливаем одну шпонку под муфту: ширина шпонки b=5мм высота шпонки h=5мм длина шпонки l=28мм диаметр вала d=16мм момент на этом валу Тб=0876Нм
Проверочный расчет подшипников.
Проверим подшипники по динамической грузоподъемности.
Диаметр под подшипник на валу равен dп=40. Применяем радиальные шариковые однорядные подшипники легкой серии №208. Его данные: динамическая грузоподъемность Сr = 32кН; статическая грузоподъемность С0r =178кН ([1] табл. 24.16 с. 386). Так как вал входит в зацепление с помощью прямозубых колес то осевых сил нет. Определим эквивалентные нагрузки на подшипники.
Эквивалентные нагрузки PEA и PEБ;
где XY – коэффициенты; X=1 Y=0 ([1] с.106).
V – коэффициент вращения; при вращении внутреннего кольца V=1 ([1] с. 108).
Кб – коэффициент безопасности; Кб=13 ([1] c. 107).
Кт – температурный коэффициент; Кт=1 ([1] c. 107).
PEА PEБ расчет будем вести по опоре Б т.к. она более нагружена.
Найдем условную нагрузку:
где КЕ- коэффициент эквивалентности; КЕ=056 ([1] c. 83)
Найдем срок службы подшипников в млн. об.
где а1 а23 – коэффициенты; а1=1 а23=08 (т.к. подшипники шариковые).
р – коэффициент т.к. подшипники шариковые то р=3.
Срок службы в часах:
Подшипники на этом валу пригодны.
2 Промежуточный вал.
Диаметр под подшипник на валу равен dп=25мм. Применяем роликовые конические подшипники легкой серии №7205. Его данные: динамическая грузоподъемность Сr = 292кН; статическая грузоподъемность С0r =21кН ([1] табл. 24.16 с. 386). Факторы нагрузки: коэффициент X=04; коэффициент Y=16; коэффициент e=037.
Схема нагружения подшипников.
Найдем осевые составляющие от действия радиальных сил:
Осевые силы нагружающие подшипники в опорах:
где FА – осевая сила от зацепления; FА=4163Н
Сравним отношения с фактором е=037;
Опора А: Тогда X=1; Y=0
где V – коэффициент вращения; при вращении внутреннего кольца V=1 ([1] с.83).
где XY – коэффициенты их значения приведены выше;
Кб – коэффициент безопасности; Кб=13 ([1] c. 84)
Кт – температурный коэффициент; Кт=1 ([1] c. 83)
Найдем условную нагрузку
где а1 а23 – коэффициенты; а1=1 а23=07 (т.к. подшипники роликовые).
На данном валу установлены два разных подшипника: один шариковый радиальный легкой серии №205 (плавающая опора) и конический роликовый сдвоенный средней серии №7205А (фиксирующая опора). Осевую нагрузку воспринимает только фиксирующая опора. Рассмотрим каждую опору в отдельности.
Подшипник №205. Его данные: динамическая грузоподъемность Сr = 14кН; статическая грузоподъемность С0r =695кН ([1] табл. 24.16 с. 386).
Эквивалентная нагрузка PEБ;
где X=1 Y =0 – коэффициенты;
где а1 а23 – коэффициенты; p=3 а1=1 а23=08 (т.к. подшипники шариковые).
Фиксирующая опора А.
Подшипник сдвоенный №7205А. Его данные: динамическая грузоподъемность Сr = 292кН; статическая грузоподъемность С0r =21кН коэффициенты: X=04; Y=16; e=037 ([1] табл. 24.16 с. 386).
Для сдвоенного подшипника коэффициент «е» будет равен:
Определим отношение и сравним с фактором «е».
где V – коэффициент вращения; при вращении внутреннего кольца V=1 ([1] с.108).
Тогда коэффициенты X и Y будут следующие:
X=067Y=067ctgα=067ctg150=25
Эквивалентная нагрузка PEА;
p – коэффициент; p=333333 (т.к. подшипники роликовые).
Смазочный материал и система смазки.
Для уменьшения потерь мощности на трение и снижение интенсивности износа трущихся поверхностей а также для предохранения их от заедания задирав коррозии и лучшего отвода теплоты трущиеся поверхности деталей должны иметь надежную смазку.
Выбор смазочного материала зависит от контактного напряжения и окружной скорости на колесе. Т.к H тих=22076МПа и =007мс то выбираем по таблице 11.1 ([1] с. 173) вязкость масла - 6010-6 м2с. По таблице 11.2 ([1] с. 173) определяем что марка масла “Индустриальное – И-Г-А-68”.
Смазывание шестерни происходит непосредственно через зубья колеса а также происходит смачивание всех деталей редуктора масляным туманом.
П.Ф.Дунаев О.П.Леликов. Конструирование узлов и деталей машин. – М.: Высшая школа 2000г.
А.Е.Шейнблит. Курсовое проектирование деталей машин. – М.: Высшая школа 1991г.
С.Н. Ничипорчик. Детали машин в примерах и задачах. – Минск.: Высшая школа 1981г.
С.А.Чернавский К.Н.Боков. Курсовое проектирование деталей машин. – М.: Машиностроение 1988г.
О.А.Ряховский С.С.Иванов. Справочник по муфтам. – Л.: Политехника 1991г.
эпюры.dwg

Привод спецификация.dwg

Расчетно-пояснительная
02.15.01.00.00.000ВО
02.15.01.00.00.000ПЗ
Привод общий вид.dwg

Окружная сила на звездочках
Скорость движения тяговой ленты
Число оборотов приводного вала
Общее передаточное число привода
*Размеры для справок.
Перекос валов редуктора и барабана не более
Осевое смещение валов редуктора и барабана
вал.dwg

Редуктор спецификация.dwg

Редуктор общий вид.dwg

покрыть эмалью ЭМПФ-133.
покрыть краской ГРГФ-20
В редуктор залить масло индустриальное
Редуктор обкатать без нагрузки в течении 3ч.
02.15.03.10.00.000СБ
Технические требования.
Плоскость разъема покрыть герметиком
ВГК-18 2 МРТУ 07-6012-63
Коэффициент смещения
Угол наклона линии зуба
Быстроходная ступень.
Передаточное отношение
Максимальный крутящий момент на
Техническая характеристика.
Коэффициент диаметра червяка
Угол подъема линии витка
Направление линии зуба
Чертежи вал_колесо.dwg

Радиусы скруглений 2мм max.
Коэффициент смещения
Нормальный исходный контур
Направление линии зуба
Неуказанные предельные отклонения размеров: валов -t
*Размеры обеспеч. инстр.
кроме мест указанных особо.
Рама общий вид.dwg

Обработка платиков после отжига и рихтовки.
Предельные отклонения крепежных отверстий от номинального
Сварочные швы зачистить
острые кромки затупить.
Сварочный материал - электрод типа Э 42 по ГОСТ 9467-73.
Сварка ручная по ГОСТ 5264-80.
02.17.06.20.00.000СБ
ФЛ-013 А ГОСТ 9109-76.
* Размеры для справок.