Проектирование нагнетателя природного газа 650-21-21 газоперекачивающего агрегата ГТН-25




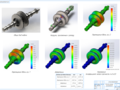
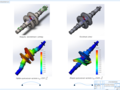
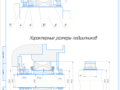
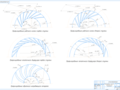
- Добавлен: 24.01.2023
- Размер: 9 MB
- Закачек: 1
Описание
Состав проекта
![]() |
![]() |
![]() |
![]() |
![]() |
![]() |
![]() |
![]() |
![]() |
![]() ![]() ![]() |
![]() ![]() |
![]() |
![]() |
![]() ![]() ![]() ![]() |
![]() |
![]() ![]() ![]() ![]() |
![]() |
![]() ![]() ![]() ![]() |
![]() ![]() ![]() |
![]() |
![]() ![]() ![]() ![]() |
![]() |
![]() ![]() ![]() ![]() |
![]() |
![]() |
![]() |
![]() |
![]() |
Дополнительная информация
!!На прочность.cdw

Критика.cdw

!Чертеж.cdw

Альтернативный вариант магнитных опор.cdw

Нагнетатель.cdw

!Профилирование.cdw

Рекомендуемые чертежи
- 24.01.2023
- 20.10.2020