Усовершенствованная газотурбинная установка типа ГПА-25 мощностью 25 МВт для привода нагнетателя природного газа




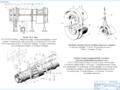
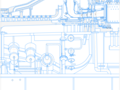
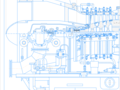
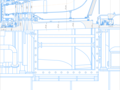
- Добавлен: 24.01.2023
- Размер: 5 MB
- Закачек: 4
Описание
Состав проекта
![]() |
![]() |
![]() ![]() ![]() |
![]() |
![]() ![]() ![]() ![]() |
![]() ![]() ![]() ![]() |
![]() ![]() ![]() |
![]() ![]() ![]() |
![]() ![]() ![]() ![]() |
![]() ![]() ![]() ![]() |
![]() ![]() ![]() |
![]() ![]() ![]() ![]() |
Дополнительная информация
Диплом ГТК-25М.doc
БРЯНСКИЙ ГОСУДАРСТВЕННЫЙ ТЕХНИЧЕСКИЙ УНИВЕРСИТЕТ
Кафедра Тепловые двигатели’’
ВЫПУСКНАЯ КВАЛИФИКАЦИОННАЯ РАБОТА
Руководитель: доцент к.т.н.
БРЯНСКИЙ ГОСУДАРСТВЕННЫЙ ТЕХНИЧЕСКИЙ
на выпускную квалификационную работу
Спроектировать усовершенствованную газотурбинную установку типа ГПА-25
мощностью 25 МВт для привода нагнетателя природного газа.
Утверждён приказом по БГТУ № от 2015г.
Срок сдачи законченного проекта 2015г.
Исходные данные для проектирования
Мощность турбины 25 МВт начальная температура 288К
температура газа перед турбиной 1293K. Частота вращения 60005500 обмин тепловая схема - простейшая
Содержание папки текстовых документов (перечень разделов подлежащих разраб.)
Технико-экономическое обоснование
Конструкторская часть
Технологическая часть
Исследовательская часть
Список использованной литературы
Перечень графического материала с точным указанием обязательных чертежей:
Газотурбинная установка типа ГТН-25М (вид общий 4 листа)
Технологическая часть (2 листа)
Исследовательская часть (2 листа)
доцент к.т.н. Рогалёв В.В.
Руководитель проекта
доцент к.т.н. Шилин М.А.
Задание принял к исполнению
Газотурбинная установка типа ГТК-25М продольный
Исследовательская часть
Технология монтажа и демонтажа корпуса осевого
В выпускной квалификационной работе разработана двухвальная газотурбинная установка мощностью Ne = 25 МВт для привода нагнетателя природного газа.
Дано технико-экономическое обоснование выбора параметров и конструкции установки ее сравнение с аналогичными агрегатами.
Выполнены необходимые тепловые расчёты турбины и определены напряжения в основных деталях и узлах.
Большое внимание уделено: оптимизации проточной части путем постановки сотовых уплотнений; расчёту технико-экономических показателей и экономического эффекта от эксплуатации спроектированной ГТУ.
Исследовательская часть включает в себя рассмотрение преимуществ использования сотовых уплотнений. По результатам исследований в спроектированной установке внедрены сотовые уплотнения.
Пояснительная записка и графическая часть выполнены в соответствии с нормами и требованиями ЕСКД ЕСТД и других нормативно-технических документов.
Технико-экономическое обоснование6
1. Технико-экономическое обоснование выбора параметров и типа конструкции6
Конструкторская часть6
1. Описание конструкции6
2. Тепловые расчёты6
3. Расчёты прочности6
Технологическая часть6
1. Последовательность технологического процесса6
2. Демонтаж верхней половины впускного патрубка6
3. Демонтаж верхней половины корпуса ОК6
4. Демонтаж верхней половины напорного патрубка ОК6
5. Монтаж верхней половины напорного патрубка ОК6
6. Монтаж верхней половины корпуса ОК6
7. Монтаж верхней половины впусконого патрубка6
Исследовательская часть6
1. Исследование физических процессов в ступенях газовых турбин с сотовыми уплотнениями6
2. Уплотнение радиального зазора безбандажных рабочих лопаток газовой турбины6
3. Внедрение результатов исследования в ГТН-256
4. Результаты модернизации6
Список использованной литературы6
Одно из основных мест в топливном балансе нашей страны занимает природный газ как наиболее удобное дешёвое и чистое топливо.
Наиболее экономичным способом доставки газа от мест добычи к потребителю является транспортировка его по трубам.
В связи с этим необходимо увеличить как число новых магистральных газопроводов с высокой степенью автоматизации и эксплуатационной надежности так и осуществить серийное производство газоперекачивающих агрегатов к газопроводам на давление 100 ата (981 МПа). Предполагалось и осуществлено внедрение на газопроводах труб для транспортировки газа диаметром 1420 мм а так же новые перспективные газоперекачивающие агрегаты мощностью 254 МВт.
Современная тенденция в развитии ГТУ состоит в том чтобы повысить температуру и давление рабочих газов при простых схемных решениях совершенствование системы охлаждения и применение более жаростойких материалов. При проектировании турбины типа ГТН – 25 были учтены все современные достижения в решении этих вопросов.
В данном дипломном проекте произведены тепловой расчет ГТУ с номинальной мощностью на муфте нагнетателя 25 МВт температурой рабочего тела перед турбиной 1293 К (1020 оС).
В ходе дипломного проектирования для повышения КПД ГТУ ее экономичности при эксплуатации была применена установка сотовых уплотнений.
Проектируемая турбина рассчитана для изготовления в блочном исполнении. Принцип блочного проектирования ГТУ заключается в разбивке всей установки на минимальное количество конструктивных законченных узлов в виде легко поддающихся стыковке осмотру и замене монтажных блоков вписывающихся в допустимые транспортные габариты не подлежащие разборке не требующие подгонки наладки и других операций при монтаже. Такое решение существенно снижает затраты на монтаж и ремонт.
1 Технико-экономическое обоснование выбора параметров и типа конструкции
Агрегат ГТН-25 головной образец которого изготовлен в 1987 году на ПО ТМЗ является однотипным в ряде бесподвальных ГПА 6 16 25 МВт. Исходя из этого было решено выполнить его по той же конструктивной схеме а увеличение мощности и тепловой экономичности обеспечить необходимым повышением параметров. Такой путь позволяет в максимальной степени использовать накопленный заводом опыт в создании высоконапорных одновальных осевых компрессоров.
Величина быстроходности турбокомпрессорной группы (n=6000 обмин) определялась заданной мощностью и использованием как и в ГТН–16 лопаточного аппарата компрессора газотурбинной установки ГТ-6-750 с надстройкой последнего двумя трансзвуковыми ступенями спереди. При этом достигается высокая степень унификации с ГТН–6 и ГТН–16[8]. При такой быстроходности ТВД удаётся сохранить двухступенчатой с изменённым диаметром дисков (104 м) несмотря на увеличение изоэнтропийного перепада.
Скорость вращения силовой турбины определяется оптимальной быстроходностью одноступенчатого нагнетателя и прочностными характеристиками ТНД. Варианты расчётов показывают что сохранение частоты вращения на уровне ГТН–16 (1038 с-1) невозможно: рост перепада энтальпий в ТНД (из-за увеличения начальной температуры) не позволяет ограничиться одной ступенью прежнего диаметра а дальнейшее увеличение окружной скорости приводит к недопустимым напряжениям в диске. Поэтому турбина низкого давления выполняется двухступенчатой с корневым диаметром dк=0904 м и частотой вращения 5500 обмин. При этом удельная быстроходность нагнетателя Н-25-76 получилась на 6% выше чем в ГТН-16 у нагнетателя Н–16–76 что позволило выполнить его одноступенчатым и соединить с ТНД непосредственно (без редуктора).
Некоторое снижение быстроходности ТНД (на 38% ниже) получено из-за повышения температуры продуктов сгорания в конце процесса расширения.
Комплексное повышение всех параметров в ГТН-25 позволило увеличить его тепловую экономичность. А компоновка агрегата позволяет выполнить его на общей раме в виде транспортабельного блока.
На рисунке 1.1. показан рост тепловой экономичности приводных ГТУ: 1- ГТН-6; 2- ГТК-16; 3- ГТН-16; 4- ГТН-25.
В нашем случае при выборе начальной температуры газа Т1 будем ориентироваться на исходные данные соответствующие базовой ГТУ. Для ГТН-25 производства ТМЗ Т1=1293 К (1020°С).
Расчётную степень повышения давления принимаем равной к =132 как и в базовой ГТН–25 т.к. оптимальную степень повышения давления к opt = 22 в однокаскадном компрессоре получить невозможно. Это ведёт к существенному снижению КПД компрессора (см. тепловые расчеты).
Данное значение расхода является приближенным. Принимаем ориентируясь на заводской вариант расход воздуха В дальнейших расчетах значение расхода теплоперепадов ТВД ТНД будут уточнены.
Применение регенерации обеспечивает повышение КПД ГТУ на при увеличении её стоимости на . Кроме того по мере эксплуатации ГТУ происходит постепенное загрязнение проходных сечений регенератора как по воздуху так и по газу что увеличивает сопротивление регенератора снижает коэффициент теплопередачи и эффективность регенерации в целом. Снизить загрязнение регенератора можно путём установки дополнительных фильтров тонкой очистки по воздуху и по топливу что также повысит сопротивление входного и выходного трактов ГТУ и повышает стоимость установки. По причине значительного увеличения капитальных затрат мы вынуждены отказаться от использования регенерации в данной схеме. В связи с отсутствием потребителя в данной схеме будет отсутствовать котел-утилизатор (в нашем случае есть необходимость отопления поселка численностью 150-200 чел. когда рациональные потребители тепла в таком случае должны быть крупными: большие города крупные животноводческие комплексы энергоемкое производство). Учитывая вышеперечисленные факторы будет использоваться простейшая схема ГТУ.
Таким образом на основе изложенного технико-экономического анализа принимаем следующие исходные данные:
Эффективная мощность ГТУ: Nе=25 МВт.
Начальная температура воздуха: Т3=288 К.
Начальная температура газа: Т1=1293 К.
Частота вращения роторов: n=(60005500) мин-1.
Назначение и тип: газотурбинный газоперекачивающий агрегат (ГГПА).
Вариант тепловой схемы: простая.
1. Описание конструкции3
1.1. Проточная часть турбины3
1.2. Проточная часть компрессора4
1.3. Система охлаждения элементов турбины6
1.4. Конструкция агрегата8
1.5.Показатели ГТН-259
2. Тепловые расчёты12
2.1. Определение расчетного значения степени повышения давления в цикле12
2.1.2. Расчёт компрессора14
2.1.3. Расчёт камеры сгорания15
2.1.4. Расчёт газовой турбины15
2.2. Расчёт проточной части газовой турбины.17
2.2.1.Выбор исходных параметров.17
2.2.2. Распределение перепада энтальпий по ступеням турбины19
2.2.3. Расчёт проточной части газовой турбины высокого давления23
2.2.4. Расчёт проточной части турбины низкого давления32
2.3. Определение потерь энергии и КПД ступеней33
2.4. Технико- экономические показатели ГТУ35
3. Расчёты прочности36
3.1. Расчёт рабочей лопатки первой ступени ТВД36
3.3. Расчёт на вибрацию рабочих лопаток второй ступени ТВД37
3.4. Определение критической частоты вращения ротора ТВД.40
3.5. Расчёт на прочность диска второй ступени ТВД40
3.6. Расчет опорного подшипника ТВД42
3.7. Расчет упорного подшипника ТВД43
1 Описание конструкции
1.1 Проточная часть турбины
Увеличение степени повышения давления в компрессоре агрегата ГТН-25 (132 вместо 115 в ГТН-16) при двухступенчатом исполнении ТВД потребовала увеличения корневого диаметра последней ступени (до 750 мм вместо 700мм в ГТН-16). Несмотря на отличающиеся абсолютные размеры в ТВД ГТН-25 применен тот же тип лопаточного аппарата что и в ГТН-16 первая ступень с низким отношением и большой циркуляцией . Вторая ступень имеет направляющий аппарат с большой конусностью периферийного обвода и малым углом входа (около 400).
Умеренные числа маха М в ТНД (благодаря применению вторых ступеней и повышенной температуры газа) позволяют использовать традиционные для завода высокореактивное облапачивание. При этом первая ступень ТНД получена из второй методом периферийной подрезки.
Сравнительные характеристики турбин ГТН-16 и ГТН-25 приведены в таблице 2.1.
Сравнительные характеристики турбин
1.2 Проточная часть компрессора
В соответствии с данными расчёта тепловой схемы ГТУ типа ГТН–25 компрессор должен обеспечить следующие характеристики на расчётном режиме (при параметрах атмосферного воздуха =1013кПа =288 К): массовый расход воздуха 118 кгс; степень повышения давления 132; адиабатический КПД 87%; коэффициент запаса устойчивой работы 12; рабочий диапазон изменения приведённого расхода от расчётного значения 75..106%.
Создание компрессора предусматривает использование в качестве основы проверенного в эксплуатации лопаточного аппарата осевого компрессора ГТ-6-750 путем подстройки его спереди новыми высоконапорными ступенями. Для пропуска заданного расхода принят вариант формирования проточной части путем замены двух первых ступеней осевого компрессора турбины ГТН-16 на более высоконапорные.
Применение этих ступеней при трансзвуковом лопаточном аппарате оправдано и с точки зрения обеспечения приемлемой аэродинамической эффективности так как при оптимальном профилировании доля потерь в уплотнениях может быть снижена.
Увеличение степени повышения давления в рассматриваемых ступенях осуществлено устранением (до нуля) закрутки потока перед рабочими лопатками. При профилировании предвключенных ступеней использован закон постоянства циркуляции как наиболее близкий к на основе которого сделана проточная часть основного прототипа.
В полученном четырнадцатиступенчатом компрессоре первые четыре направляющих венца включая ВНА выполняются поворотными - для обеспечения выхода ГТУ на рабочие режимы и регулирования компрессора при частичных нагрузках.
Расчетная характеристика этого компрессора представлена на рисунке 2.1.
Регулирование компрессора осуществляется следующим образом:
На режимах запуска – поворотом четырех направляющих аппаратов первых ступеней при открытом противопомпажном клапане;
При частичных нагрузках – только одновременным прикрытием четырех ПНА на разные углы но от одного сервомотора.
На рисунке 2.2. приведены основные результаты расчета на переменные режимы работы газотурбинной установки ГТН-25 полученные с использованием характеристики компрессора на рис. 2.1 позволяющие сделать выводы:
Предусмотренное регулирование компрессора позволяет обеспечить его устойчивую работу в диапазоне изменения числа оборотов силового вала 075 105(приведенного числа оборотов компрессора 085 104).
Мощность пускового устройства (600 кВт) достаточна для вывода ГТУ на самоходный режим и обеспечения требуемой скорости пуска.
1.3 Система охлаждения элементов турбины
Для двигателя с начальной температурой 1293 К при заданном ресурсе 100 тысяч часов разработка системы охлаждения является одной из важнейших задач.
В агрегате ГТН–25 эта проблема усложняется ещё и тем что при большой степени повышения давления в компрессоре (132) и отсутствии промежуточного охлаждения воздуха температура охладителя достигает 663 К (390°С).
Защита основных элементов турбины от воздействия высоких температур выполнена следующим образом: камера сгорания в головной части имеет экран для создания повышенных скоростей воздуха у жаровых стенок после которого вторичный воздух сбрасывается на стенки газохода. Несмотря на малую конвективность охлаждения такое решение необходимо в связи с высокой начальной температурой и неустойчивым характером плёнки вблизи горелочного устройства (вихревое течение в шаровом пространстве).
Для защиты газоходов предусмотрена вторая ступень ввода воздуха с образованием на его стенках плёнки. Непосредственно перед сопловым аппаратом из корпуса за компрессором организована третья ступень ввода – для пленочного охлаждения потоком направляющих лопаток первой ступени турбины (а так же частично ротора и вставок над рабочими лопатками).
Статор турбины имеет двухъярусное охлаждение. Собственно корпус охлаждается воздухом из промежуточной ступени компрессора. Одновременно приняты меры для уменьшения к нему потока тепла от проточной части путём «трёхэтажной» конструкции крепления направляющих лопаток: сегменты–обойма–корпус. Все эти элементы имеют малые сечения в местах контакта причём последние продуваются воздухом.
Для защиты обоймы от излучения проточной части и возможного прорыва газа между вставками (над рабочими лопатками первой ступени) между сегментами вставлены экраны.
Направляющие лопатки первой ступени проектируются литыми полыми с внутренним дефлектором и охлаждаются воздухом после компрессора с температурой 594 К. Воздух подаётся внутрь дефлектора откуда выпускается в районе входной кромки спинки лопатки и в корневой части. Охлаждение направляющих лопаток второй ступени аналогично. Рабочие лопатки первой ступени ТВД выполнены конструктивно в двух вариантах: с продольными охлаждающими каналами и петлевой схемой прохода воздуха. В обоих вариантах воздух подаётся из ротора к хвостовым соединениям каждой лопатки и выпускается в радиальный зазор.
Схема охлаждения ротора ТВД параллельная (с подпиткой свежим воздухом перед второй ступенью) и независимой подачей охлаждающего воздуха (через сверления в роторе) к каждой рабочей лопатке первой ступени.
Дефлекторным диском – спереди дроссельным – сзади и промвставками под направляющими лопатками второй ступени ротор ТВД полностью изолируется от проточной части. Между покрывающими и несущими лопатки дисками течёт охлаждающий воздух поступающий из центральной расточки ротора куда он подаётся из компрессора через радиальное отверстие. Покрывающие диски защищаются протечками воздуха из уплотнений.
Оценочные расчёты показали что представленная система охлаждения обеспечивает температуры в области гребней ротора около 703 733 К.
Ротор ТНД выполнен охлаждаемым продувкой воздуха из промежуточной ступени компрессора под дефлекторным диском и под полками рабочих лопаток.
Дефлекторный диск и торец несущего диска последней ступени защищены протечками воздуха из концевых уплотнений.
Столь развитая система защиты ротора ТНД оправдана его большой напряжённостью и повышенным уровнем температур в проточной части. Максимальная температура в гребнях дисков для принятой схемы охлаждения достигает не более 673 К.
1.4 Конструкция агрегата
Газотурбинная установка типа ГТН–25 представляет собой единый блок массой 90 тонн включающий следующие основные части: газотурбинный двигатель нагнетатель раму–маслобак с установленным на ней и встроенным в неё вспомогательным оборудованием и маслопроводами.
Корпус ГТУ выполнен максимально жёстким и состоит из двух независимых друг от друга частей: несущего цилиндра и выхлопной части турбины.
Несущий цилиндр в передней части образует осевой входной патрубок компрессора с четырьмя стойками на которые опирается корпус переднего подшипника с расположенными в нём опорно-упорными вкладышами муфтой свободного входа и коническим редуктором пускового устройства.
Цилиндр ГТУ имеет горизонтальный и четыре вертикальных разъёма открывающих доступ к основным узлам агрегата: подшипникам проточной части компрессора и турбин камере сгорания.
Выхлопная часть турбины жёстко не связанная с цилиндром устанавливается на раму-маслобак на четырёх гибких опорах и стыкуется с корпусом среднего подшипника и заднего лабиринтового уплотнения ТНД при помощи эластичных контактных колец (уплотнений). Заднее уплотнение крепится к корпусу заднего подшипника ТНД только в нижней половинке.
Диффузор за турбиной низкого давления крепится к несущему цилиндру и корпусу заднего подшипника (в нижней половине). Такой принцип разделения статора на две независимые части кроме повышенной жёсткости цилиндра и стабильности размеров проточной части исключает передачу к несущему цилиндру (корпусу) усилий от горячих газоходов.
Передняя часть корпуса выполнена безобоймовой. Непосредственно в неё установлены направляющие аппараты первых шести ступеней компрессоров. Входной направляющий и последующие три направляющие аппарата выполнены поворотными с приводом от одного сервомотора через качающийся рычаг.
Камера сгорания кольцевого типа в виде жарового пространства ограниченного двумя листовыми оболочками установленными в каркасе размещается между радиальным диффузором компрессора и обоймой ТВД.
Конструкция выполнена из двух половин имеет горизонтальный разъем и крепится к обойме ТВД.
Подвод топлива к камере сгорания осуществляется по наружному трубопроводу с двух сторон четырьмя патрубками к верхней и нижней половинам внутреннего коллектора. Последний (раздельно в верхней и нижней половинах) осуществляет раздачу газа к двадцати струйным горелкам типа «грибок» выполненных в центре лопаточных завихрителей. Встроенные запальные устройства со свечой СП–08 установлены в двух горелках.
Роторы выполнены сборными дисковыми. В агрегате ГТН-25 вместе с более высоким уровнем температур окружные скорости в компрессоре и ТВД увеличены до 245 мс. В этих условиях применение дискового ротора стало неизбежным. Конструкция ротора турбокомпрессора с центральной стяжкой в первых трёх ступенях компрессора такова из-за их малым втулочным диаметром и стремлением уменьшить диаметр пояса жёсткости в остальной части ротора где применяются десять периферийных болтов. Болты служат для крепления между собой дисков промежуточной части барабанного типа и хвостовиков ротора.
Сборным из двух дисков и двух хвостовиков стянутых болтами по периферии выполнен и ротор турбины низкого давления.
Нагнетатель природного газа Н–25–76 (Н-25-100) выполнен для степеней сжатия (125; 137; 145) одноступенчатым с консольным расположением рабочего колеса.
Упорный подшипник нагнетателя (ТНД упорного подшипника не имеет) выполнен с двумя упорными гребнями что позволяет значительно снизить удельные нагрузки на любых режимах работы агрегата.
Соединения нагнетателя и турбины низкого давления осуществляется с помощью промежуточного вала и включает две гибкие муфты с упорными сухарями.
Установка уплотнений и опорного вкладыша в общей обойме горизонтального разъема обеспечивает стабильность радиальных зазоров. К корпусу эта обойма крепится разбитым вертикальным фланцем в котором размещены каналы подвода и отвода газа.
1.5 Показатели ГТН-25
КПД расчетный при 310%
КПД нагнетателя (политропический)
Применение для резервирования вентиляторов ВОМ компоновки совмещенной с воздухозабором полностью решает вопрос автономности в случае исчезновения напряжения переменного тока.
Технический проект ГТН-25 базируется на отработанных и серийно выпускаемых по ТМЗ турбинах ГТ-6-750; ГТН-6; ГТК-16 и предусматривает широкую унификацию с агрегатом ГТН-16. Техническое решение большинства узлов явилось дальнейшим развитием инструкций этих машин а некоторые узлы (профили лопаток компрессора вкладыши среднего подшипника) частично или полностью унифицированы. Многие узлы имеют конструктивную и технологическую унификацию.
Время необходимое для полной ревизии всего двигателя с выемкой роторов турбин при капитальном ремонте составляет две восьмичасовых смены бригады из трех слесарей.
Техническими средствами для максимального снижения этих показателей явилось главным образом повышение быстроходности и параметров цикла а так же выполнение нагнетателя с консольным ротором.
Достигнутые результаты показаны в таблице 2.2 в сопоставлении с бесподвальными ГПА ПО ТМЗ ГТН-16 и моделью 5000(В) Джениралл Электрик(США).
Сопоставление показателей ГТН-25 с другими ГПА
Сравнительные величины
Вес в объеме поставки
Всего на 1кВт мощности
Число основных блоков
Занимающая площадь на 1 агрегат
Объем помещения на 1 агрегат
Габаритные размеры ГПА с нагнетателем длина
2.1 Определение расчетного значения степени повышения давления в цикле
Расчёт тепловой схемы ГТУ (рис.2.3.) начинается с определения зависимости .
Для вариантов безрегенеративного исполнения (простейшей и теплофикационной) эту зависимость рассчитывают по следующей формуле:
где – КПД соответственно турбины и компрессора;
– коэффициент потерь давления в ГТУ;
– температурный коэффициент.
В расчётах принято: ;;;
– осреднённое для всего цикла (рис.2.2.2.);
Расчёт производим для пяти значений температурного коэффициента . В данном случае принято: и ;
Температурные коэффициенты:
Расчёт выполнен на ЭВМ в программном приложении Microsoft Excel. По результатам расчетов максимальное значение КПД получилось при (рис.2.4) Такую степень повышения давления в однокорпусном компрессоре без заметного снижения его КПД получить невозможно. Поэтому исходя из поставленного условия выполнения ГТУ по простейшей схеме принимаем расчётное значение ориентируясь на уже имеющийся компрессор базовой ГТУ с такой же величиной и приемлемым значением КПД
На основании полученных зависимостей и графиков изменения максимальных значений внутреннего КПД в зависимости от начальной температуры (состояние атмосферы) и от начальной температуры газа для безрегенеративных ГТУ.
Расчётное значение температуры атмосферного воздуха принимаем равным нормальной (стандартной ) так как не оговариваются дополнительные условия.
Выбор начальной температуры газа независимо от варианта исполнения тепловой схемы ГТУ диктуется только жаропрочностью применяемых материалов лопаток и дисков турбины и способа их охлаждения. Исходя из условий рабочая температура .
Принимаем – атмосферное давление.
Тогда давление за компрессором: .
Давление перед турбиной:
Степень расширения в турбине:
Давление за турбиной:
2.1.2 Расчёт компрессора
Удельную работу компрессора и температуру за ним определяем в следующей последовательности. Находим:
Средняя температура изоэтропийного сжатия:
Показатель изоэнтропы и теплоёмкость воздуха при этой температуре .
Изоэнтропийный перепад энтальпий в компрессоре:
Действительный перепад энтальпий при :
Температура воздуха за компрессором:
– равна температуре воздуха поступающего в камеру сгорания.
2.1.3 Расчёт камеры сгорания
В качестве топлива применяется стандартный углеводород для которого и .
Теплотой топлива вносимой в камеру сгорания пренебрегаем.
Принимаем КПД камеры сгорания .
Тогда для простейшей и теплофикационной схемы относительное содержание воздуха в продуктах сгорания:
Значения теплосодержания воздуха и и продуктов сгорания при соответствующих температурах взяты по графикам.
Коэффициент избытка воздуха: .
2.1.4 Расчёт газовой турбины
Для простейшей схемы коэффициент потерь давления будет иметь наименьшее значение. В частности примем .
Температура газа за турбиной при изоэнтропийном расширении найдём из выражения:
Изоэнтропийный перепад энтальпий в турбине:
где – теплоёмкость газа принятая по средней температуре процесса изоэнтропийного расширения в турбине.
Действительный перепад энтальпий в турбине:
где - внутренний КПД турбины с учётом аэродинамических потерь от охлаждения потока в проточной части турбины;
Температура газа за турбиной:
Расход газа через ТНД ГТУ определяется по соотношению:
Эффективная удельная работа ГТУ с учётом охлаждения:
- механический КПД турбины и компрессора;
- относительный расход воздуха на охлаждение;
; G газа среднее для
- относительный расход топлива;
- коэффициент возврата работы для охлаждающего воздуха;
Расход газа через ТНД:
Расход топлива определяем по выражению:
что удовлетворительно совпадает с принятым ранее значением.
2.2 Расчёт проточной части газовой турбины
2.2.1 Выбор исходных параметров
Число ступеней в турбине выбирается по варианту 2 + 2 (2 ступени в ТВД и две ступени в ТНД).
Расходную составляющую скорости потока примем равной .
Коэффициент возврата тепла:
где z=4 – число ступеней;
- коэф-т возврата для бесконечного числа ступеней.
Полный изоэнтропийный перепад энтальпий с учётом коэффициента возврата тепла:
Ометаемая площадь рабочих лопаток последней ступени газовой турбины:
– удельный объём газа за турбиной.
С целью уменьшения потерь с выходной скоростью за турбиной предполагаем установку осерадиального диффузора с КПД и степенью диффузорности . При этом скорость потока газа за диффузором:
Изоэнтропийный перепад энтальпий в диффузоре (рис.2.5)
Потери энергии в диффузоре:
Потери энергии с выходной скоростью за диффузором:
Температура газа за последней ступенью в точке В:
Давление газа перед диффузором:
Удельный объём газа за последней ступенью:
Уточнённое значение ометаемой площади:
Перепад энтальпий соответствующий расходной составляющей скорости потока за последней ступенью турбины:
2.2.2 Распределение перепада энтальпий по ступеням турбины
Поскольку расширение газа в турбине происходит до давления Рz РII то перепад энтальпий в турбине возрастёт на величину изоэнтропийного перепада энтальпий в диффузоре тогда:
Перепад энтальпий на ТВД определяется из выражения:
Располагаемый перепад энтальпий на одну ступень в ТВД при равном распределении его по ступеням:
Полный перепад энтальпий на каждую ступень ТВД в предположении полного использования выходной кинетической энергии газа из предыдущей ступени:
Перепад энтальпий на ТНД:
Располагаемый перепад энтальпий на ступень ТНД:
Полный перепад энтальпий на первую ступень ТНД будет равен:
Диаграмма состояния газа рассчитана и построена в предположении расширения газа от полных параметров перед турбиной до давления за последней ступенью (рис.2.6).При этом принято:
; число участков диаграммы .
Давление удельный объём и перепад энтальпий на участках определены по формулам:
Результаты расчётов представлены в табл.2.2.1. На диаграмме состояния газа показано распределение перепадов энтальпий по ступеням ТВД и ТНД и обозначены расчётные точки параметров газа перед и за ступенями а также в осевых зазорах ступеней по среднему диаметру.
Параметры газа на политропе расширения в турбине
Обозначение и размерность
Точки на политропе расширения
Отношение температур
Температура конца участка
Средняя температура участка
Разность температур на участке
Средняя теплоёмкость участка (по Тср)
Показатели изоэнтропы (по Тср)
Давление в конце участка
Перепад энтальпий на участке
2.2.3 Расчёт проточной части газовой турбины высокого давления
Вся мощность развиваемая ТВД идёт на привод компрессора . Из этого перепада затрачивается на создание расходной скорости потока сz перед ТВД. Располагаемый перепад на каждую ступень ТВД а полный . Закрутку лопаток будем считать близкой к закону постоянной циркуляции. Принятые условия для ТВД запишутся следующим образом:;;;;.
Примем расход рабочего тела по лопаточным венцам ТВД следующим:
Удельный объём газа за рабочими лопатками второй ступени ТВД:
Ометаемая площадь рабочих лопаток второй ступени ТВД:
Удельный объём газа за рабочими лопатками первой ступени ТВД:
Ометаемая площадь рабочих лопаток первой ступени ТВД:
Расчёт второй ступени ТВД
Расчёт второй ступени ТВД начинаем с корневого диаметра.
Окружная скорость у корня ступени из условия осевого выхода потока:
Корневой диаметр ступени:
Внешний диаметр рабочих лопаток:
Средний диаметр рабочих лопаток:
Высота рабочих лопаток:
В корневом сечении окружная составляющая абсолютной скорости потока в предположении осевого выхода потока из ступени:
Абсолютная скорость выхода потока:
Перепад энтальпий в направляющем аппарате:
Перепад энтальпий в рабочем колесе:
Степень реактивности у корня ступени:
что соответствует рекомендуемым пределам ().
Относительная скорость газа на входе в рабочее колесо:
Угол входа потока в рабочее колесо:
Относительная скорость газа на выходе из рабочего колеса:
Угол выхода потока из рабочего колеса:
Условие 2 ≤ 1 выполняется.
Окружная составляющая абсолютной скорости выхода газа из рабочего колеса:
а т.е. у корня ступени обеспечивается практически осевой выход потока.
Среднее сечение ступени рассчитывается в предположении обеспечения закрутки потока по закону постоянной циркуляции то есть . Средний диаметр направляющего аппарата при условии будет несколько меньше диаметра рабочего колеса (вследствие меньших значений удельного объёма газа в зазорах ступени по сравнению с его значением за рабочим колесом). Примем в первом приближении:
Окружная скорость на этом диаметре:
Окружная составляющая абсолютной скорости потока:
Перепад энтальпий в направляющем аппарате на среднем диаметре:
Перепад энтальпий в рабочем колесе второй ступени ТВД:
Степень реактивности на среднем диаметре:
Зная h22 по диаграмме состояния газа определим параметры газа в осевом зазоре второй ступени ТВД на среднем диаметре отложив от конца процесса второй ступени отрезок h22 (рис.2.6):
Найденному удельному объёму соответствует площадь кольца занятого направляющими лопатками второй ступени ТВД:
Внешний диаметр направляющего аппарата второй ступени ТВД:
Средний диаметр направляющего аппарата:
что совпало с ранее принятым значением.
Высота направляющих лопаток:
Окружная составляющая относительной скорости выхода газа из рабочего колеса:
Окружная скорость на среднем диаметре рабочего колеса:
Периферийное сечение
Расчёт периферийного сечения второй ступени ТВД ведём в той же последовательности что и для среднего сечения с учётом различных значений окружных скоростей в осевом зазоре и за рабочим колесом а именно:
По найденным в трёх сечениях второй ступени ТВД значениям величин строим графики изменения по высоте лопаток всех параметров потока (рис.2.7.абв.) и треугольники скоростей (рис.2.8.г).
Расчёт первой ступени ТВД
Расчёт первой ступени ТВД при принятых условиях (;; однотипные направляющие и рабочие лопатки) сводится к определению параметров потока по среднему диаметру за рабочим колесом и за направляющим аппаратом и высоты направляющих и рабочих лопаток.
Параметры газа за первой ступенью ТВД определяем по диаграмме состояния (рис.2.6):
Высота рабочих лопаток первой ступени ТВД составляет от высоты рабочих лопаток второй ступени ТВД.
Принимая с достаточной для расчётов точностью найдём из (рис.2.7.): ;
и по (рис.2.6) параметры потока по среднему диаметру за направляющими лопатками первой ступени ТВД:
Ометаемая площадь направляющих лопаток первой ступени ТВД:
Внешний диаметр направляющего аппарата первой ступени ТВД:
Значения параметров потока в контрольных сечениях первой ступени ТВД на диаметрах ; и находим по характеристикам второй ступени ТВД для соответствующих значений ;; (рис.2.2.8.). В частности значения скоростей С1 = 460 мс и W2 = 385 мс необходимые для определения потерь энергии в ступени.
2.2.4 Расчёт проточной части турбины низкого давления
Расчёт второй ступени ТНД
Из ранее проведённых расчётов имеем: располагаемый перепад энтальпий на ступень ТНД:
Полный перепад энтальпий на вторую ступень ТНД равен:
Расчёт второй ступени ТНД производится в той же последовательности что и второй ступени ТВД. С целью сокращения объёма работы он не заносится в пояснительную записку.
Основные параметры рассчитанных ступеней представлены в табл.2.4.
Основные параметры ступеней
Внутренний диаметр d' мм
Средний диаметр НА d мм
Внешний диаметр НА d" мм
Высота направляющих лопаток l мм
Высота рабочих лопаток l2 мм
Изоэнтропийный перепад энтальпий в ступени h0 кДжкг
Полный изоэнтропийный перепад энтальпий в ступени h0* кДжкг
Окружная скорость на среднем диаметре НА U1 мс
Условная скорость C0 мс
Характеристическое отношение UC0
Полный перепад энтальпий в направляющем аппарате h1* кДжкг
Перепад энтальпий в рабочем колесе h2 кДжкг
Степень реактивности на среднем диаметре ρ
Коэффициент потерь энергии в направляющем аппарате 1
То же в рабочем колесе 2
Скорости и углы потока на среднем диаметре
2.3 Определение потерь энергии и КПД ступеней
Потери энергии в направляющих и рабочих решётках определяются по формулам:
причём значения 1 и 2 берутся осреднёнными по высоте лопаток т.е. с учётом вторичных перетеканий на концах лопаток (в корневой и периферийной областях межлопаточных каналов). В настоящем расчёте принято 1 = 006 и 2 = 008.
Для ступеней с бандажом потери от протечек через осевые зазоры определяются по формулам
где - коэффициент расхода щели осевого зазора;
- площадь щели осевого зазора у периферии ступени м2 ;
- удельный объем за рабочим колесом ;
- степень реактивности у периферии ступени;
- число щелей уплотнения по бандажу;
- коэффициент расхода щели над бандажного уплотнения.
Для уплотнения нового типа с уплотняющими осевыми зазорами
где - коэффициент расхода через щели;
- давление торможения перед ступенью МПа;
- давление в осевом зазоре у корня ступени;
- число щелей уплотнения шт;
- удельный объем торможения перед ступенью ;
- коэффициент учитывающий искажение потока из-за подмешивания к нему протечек через корневое уплотнение.
Потери на трение диска о газ вычисляются по формулам:
где - потери энергии на трение диска кВт;
- средний диаметр ступени м;
- окружная скорость на среднем диаметре ;
- удельный объем газа в осевом зазоре по среднему диаметру .
К.п.д. ступени определяется по формуле:
Результаты расчетов потерь энергии и КПД сведены в таблицу 2.5.
Значения соответствующих расчетных величин принимались для средних диаметров ступеней (таблица 2.4.).
Потери энергии и КПД ступеней
Теоретическая скорость выхода потока из направляющего аппарата С1t мс
Потери энергии в направляющем аппарате Δh1 кДжкг
Теоретическая скорость выхода потока из рабочего колеса W2t мс
Коэффициент потерь энергии в рабочем колесе 2
Потери энергии в рабочем колесе Δh2 кДжкг
Радиальный зазор по рабочим
Потери энергии у периферии ступени Δhl" кДжкг
Давление перед ступенью P0 МПа
Давление в осевом зазоре Р1’ МПа
Коэффициент расхода .
Число гребней уплотнения по Н.А. z шт.
Радиальный зазор по гребням направляющего аппарата Δ' м
Диаметр уплотнения в направляющем аппарате dу' м
Площадь радиального зазора в направляющем аппарате fу' м2
Величина утечек у корня ступени
Потери энергии от протечек у корня ступени Δhl' кДжкг
Потери энергии на трение диска Δhтр кДжкг
Сумма потерь энергии в ступени Δh кДжкг
Использованный перепад энтальпий в ступени h кДжкг
Располагаемый перепад энтальпий в ступени h0 кДжкг
Использованный перепад энтальпий в турбине составляет:
H = Σh = 629788 кДжкг.
Внутренний к.п.д. турбины:
2.4 Технико- экономические показатели ГТУ
Удельный расход газа
- расход теплоты в камере сгорания.
Удельный расход тепла ГТУ
Удельный расход условного топлива
3.1 Расчёт рабочей лопатки первой ступени ТВД
Расчёт рабочей лопатки на растяжение
Проводим расчёт рабочей лопатки первой ступени так как эта ступень несёт наибольшую температурную нагрузку.
Лопатка по высоте имеет переменное сечение. Средний диаметр рабочего колеса . Длина лопатки . Площадь корневого сечения лопатки . Площадь периферийного сечения лопатки . Отношение . Отношение . Число оборотов ротора . Материал лопатки Сталь 2Х13. Плотность материала . Предел текучести материала .
Растягивающее напряжение у корня лопатки от центробежной силы пера лопатки:
Допускаемые растягивающие напряжения:
где к – коэффициент запаса прочности согласно [11].
Лопатка по растягивающим напряжениям проходит так как напряжения:
Расчёт лопатки на изгиб
Число рабочих лопаток . Средний диаметр рабочего колеса . Длина рабочей лопатки . Момент сопротивления профиля . Расход газа через рабочее колесо . Абсолютная скорость выхода потока из направляющего аппарата . Абсолютная скорость выхода потока из рабочего колеса . Угол выхода потока из направляющего аппарата . Угол входа потока в направляющий аппарат . Давление перед рабочим колесом . Давление за рабочим колесом . Допускаемые изгибные напряжения .
Окружная составляющая силы действующая на лопатку:
Осевая составляющая силы действующей на лопатку:
Сила действующая на лопатку:
Лопатка по изгибающим напряжениям проходит так как:
3.3 Расчёт на вибрацию рабочих лопаток второй ступени ТВД
Периодическое воздействие возмущающих сил на лопатку может вызвать резонансные колебания при которых резко возрастает прогиб лопатки что приведёт к её поломке .
Во избежание возникновения подобных явлений производим расчёт рабочих лопаток на вибрацию с целью определения резонансных частот вращения.
Плотность материала лопатки r=8000 кгм3. Модуль упругости Е=21×109 МПа. Длина лопатки l=104 м. Площадь корневого сечения лопатки Fк=0002625м2. Площадь периферийного сечения лопатки Fп=000207 м2. Момент инерции корневого сечения лопатки Iк=038×10-8 м4. Момент инерции периферийного сечения лопатки Iп=022×10-8 м4. Диаметр рабочего колеса dср= 096 м.
Частота собственных колебаний единичной лопатки переменного сечения без бандажа будет составлять:
Отсюда статическая частота колебаний: fc=56584 Гц.
Динамическая частота колебаний:
где nc - секундное число оборотов ротора;
B - коэффициент определяемый по формуле (для переменного сечения профиля) .
Строим график зависимости fд=F(nc) и из начала координат проводим лучи кратности. Данные по которым строится график представлены в табл. 2.6.
Зависимость динамической частоты колебаний лопатки от nc
График изменения динамической частоты (диаграмма Кемпбелла) представлен графически на рис. 2.9.
Как видно из диаграммы на рис. 2.9 лучи кратности i=5 i=6 пересекают кривую fд. Абсциссы точек пересечения лучей с кривой fд соответствуют резонансным числам оборотов.
Как видно из диаграммы на рис. 2.9. лучи кратности i=5 i=6 пересекают кривую fд. Абсциссы точек пересечения лучей с кривой fд соответствуют резонансным числам оборотов.
Для i=5 Dn= (nраб-nрез)nрез = (11833-126)126 ×100% = -611 %>5% что соответствует требованиям.
Для i=6 Dn= (nраб-nрез)nрез = (11833-98)98 ×100% = 207 %>4% что соответствует требованиям.
Следовательно вибрационная надежность облопачивания рабочего колеса второй ступени ТВД обеспечена.
3.4 Определение критической частоты вращения ротора ТВД
В связи с тем что в конструкцию ротора не вносились изменения его критическая частота вращения должна остаться практически неизменной по сравнению с критической частотой ротора ГТУ – прототипа. Поэтому критическую скорость вращения оцениваем приближённо по формуле Звягинцева:
где d0=0773 м – максимальный диаметр вала l=38 м G=63700 Н – сила тяжести ротора турбокомпрессора. В результате подстановки исходных данных в формулу получаем:
Таким образом nкр на 268% больше чем nраб. что удовлетворяет условию надёжности жёстких роторов (nкр>nраб на 20..25 % ).
3.5. Расчёт на прочность диска второй ступени ТВД
Диск второй ступени ТВД произвольного профиля поэтому при его расчёте заменяем заданный профиль ступенчатым состоящим из ряда колец произвольной толщины.
Расчет осуществляется методом двух расчетов от втулки к ободу для диска составленного из участков постоянной толщины. Первое кольцо считается втулкой диска последующие 6 колец – элементами полотна диска.
Расчетные зависимости :
sr=k1×sri+k2×sti+k3×sui
st=k1'×sri+k2'×sti+k3'×sui
здесь sti – радильные и тангенциальные напряжения на внутреннем радиусе каждого участка (xi).
sui=08×ui – напряжение в тонком стальном вращающемся кольце внутреннего радиуса x для i-го кольца где
К1К2К3 К1'К2'К3' – коэффициенты определенные по [18] в зависимости от отношения xнаружнxвнутр xнаружн и xвнутр соответственно внутренний и наружний радиусы участка.
Напряжения на стыке участков определяются по формулам перехода:
sr(n+1) = srn× yn yn+1
st(n+1) = stn+m×srn×(ynyn+1-1).
Расчет первого участка который имеет профиль диска постоянной толщины производится по формулам :
Здесь suв = 08×uв2 – для наружного радиуса первого кольца.
g = 0412×( 1- g' = 0412×( 1- 0575×x2rв2 ).
На оси втулки где х=0sro = sto.
Таким образом радиальные sro и тангенциальные sto напряжения во втулке без отверстия одинаковы и принимаются в первом и втором расчетах произвольно.
Первый расчет производится при следующих условиях: n = nраб = 7100 обмин; sto1 = 100 МПа; sro1 = 100 МПа – принято произвольно.
Второй расчет производится при условиях: su = 0; n = 0; sto2 = 150МПа; sro2 = 150 МПа – принято произвольно.
Величины коэффициентов необходимые для расчета диска приведены в табл. 2.8. Расчёт выполнен с использованием программы Microsoft Excel.
Коэффициенты для расчёта диска
Расчет показывает что критерии прочности диска удовлетворяют нашим требованиям.
3.6 Расчет опорного подшипника ТВД
Исходные данные для расчета:
Частота вращения ротора ТВД
Грузоподъемность подшипника
Пользуясь таблицей 15-1 (Г.С. Жирицкий) [11] примем величину диаметрального зазора
Окружная скорость шейки
Задаемся средней температурой масла в подшипнике
Коэффициент динамической вязкости для этой температуры (рис. 16-1 Г.С. Жирицкий)[11].
Определяем коэффициент грузоподъемности
Используя рисунок 15-9 (Г.С. Жирицкий) [11] определяем коэффициент
Подсчитываем минимальную толщину масляной пленки:
Жидкостное трение в подшипнике осуществляется при коэффициенте запаса надежности
Определяем величину по графику 15-10 (Г.С. Жирицкий)[11]
Коэффициент трения в нижней половине подшипника
Коэффициент трения в верхней половине подшипника
Мощность затрачиваемая на трение
Коэффициент расхода масла через нижний вкладыш находим из графика (рис. 15-11 Г.С. Жирицкий)[11]
Расход масла вытекающего через торцы подшипника под действием давления масляного клина
Под действием избыточного давления масло подводится к подшипнику и вытекает через торцы подшипника расход его определяется из уравнения
Полный расход масла
Повышение температуры масла в подшипнике
где - удельная теплоемкость масла ().
Температура масла на входе в подшипник
Температура масла на выходе из подшипника
Обе величины являются приемлемыми.
3.7 Расчет упорного подшипника ТВД
Центральный угол охвата
Осевая нагрузка на подшипник
По величинам и определяем коэффициенты
Рабочая поверхность одной колодки
Усилие приходящееся на одну колодку
Среднее удельное давление
при допустимом давлении .
Примем среднюю температуру масла в подшипнике
Повышение температуры масла в подшипнике
Температура масла на выходе из подшипника
Минимальная толщина масляной пленки
Работа трения одной колодки
Расход масла через все колодки
Расчет упорного диска
Диск рассматривается как круговая пластина заделанная по радиусу r и нагруженная равномерным давлением Р’ср
Для rR=01500270=056 - =09;=063.
Примем толщину диска h=50 мм.
Максимальное напряжение:
Максимальный прогиб:
1 Последовательность технологического процесса
В данной операции рассматриваются два варианта разборки в зависимости от конструкции корпуса ОК:
Вариант I – корпус состоит из 2-х частей (передней и задней)
Вариант II – цельный корпус ОК
2 Демонтаж верхней половины впускного патрубка
Примечание - На установках с отдельными передним и задним корпусами ОК (Вариант I) прежде чем производить разборку впускного патрубка следует произвести разборку корпуса осевого компрессора
Демонтаж верхней половины впускного патрубка
1 См. рис. 3.1. Отвернуть и снять 15 болтов 1 и 15 пружинных шайб 2 крепления верхней половины кожуха регулирующего кольца 3. Снять верхнюю половину кожуха.
Примечание – Операция выполняется если корпуса ОК цельные (вариант II). Если корпуса ОК раздельные – после демонтажа верхней половины корпуса ОК.
2 Маркировать взаимное положение шестерён и рейки.
3 Установить под низ регулирующего кольца опору 4.
4 Отвернуть два болта 5 и снять ограничитель хода кольца ВНА 6.
5 Отвернуть болт 7 и снять пластину 8.
6 Отвернуть и снять два болта 9.
7 Отвернуть и снять четыре гайки 10.
8 Маркировать призонные шпильки 11 согласно их местоположения на пластине 12. Снять шпильки 11 и пластину 12.
9 См. рис.4. Отвернуть два болта 28 и снять две пластины 29.
10 Отвернуть и снять две гайки 30.
11 Маркировать и снять призонную шпильку 31.
12 См. рис. 3.1. Выпрессовать три контрольных штифта 16. 1.13 Отвернуть и снять 29 болтов 13 на вертикальном фланцевом соединении впускного патрубка 14 и корпуса компрессора 15.
14 Отвернуть и снять восемь гаек 17.
15 Маркировать и выпрессовать четыре призонные шпильки 18.
16 См. рис. 3.2. Отвернуть и снять шесть болтов 19 на горизонтальном разъёме впускного патрубка.
17 См. рис. 3.1. Отвернуть и снять шесть болтов 20.
18 См. рис. 3.2. Застропить впускной патрубок и выбрать натяжение стропов.
19 Вставить направляющие штифты 21 на место призонных шпилек 18.
Примечание – Направляющие лопатки ВНА необходимо привести в закрытое положение.
21 См. рис. 4.2. Отделить верхнюю половину впускного патрубка 14 от нижней с помощью тали 22.
22 Установить верхнюю половину впускного патрубка на брусья. Снять таль стропа и скобы.
Примечание – Впускной патрубок установить вертикальным разъёмом со стороны компрессора вверх (для последующего демонтажа лопаток).
1 Переместить ротор ОК в направлении всаса до упора в рабочие колодки.
2 На горизонтальном разъёме впускного патрубка 14 замерить осевой зазор "д". Данные занести в ремонтный формуляр.
Зазор "д"=496÷520 мм
3 Замерить зазоры "в" и "г" по лопаткам ВНА. Данные занести в ремонтный формуляр.
Зазор "в"=108÷156 мм
Зазор "г"=047÷105 мм
Очистить от грязи ржавчины; промыть и продуть сжатым воздухом.
Произвести дефектацию лопаточного аппарата ВНА.
3 Демонтаж верхней половины корпуса ОК
Полная последовательность операций разборки корпуса ОК выглядит следующим образом:
Демонтаж верхней половины корпуса ОК (вариант I)
1 См. рис.3.4. Выпрессовать с помощью приспособления три контрольных штифта 1.
2 Отвернуть и снять 29 болтов 2 на вертикальном фланцевом соединении впускного патрубка и верхнейполовины переднего корпуса ОК 3.
3 Отвернуть и снять четыре гайки 4. Снять 2 призонные шпильки 5.
4 Выпрессовать с помощью приспособления три контрольных штифта 1 на вертикальном фланцевом соединении переднего 3 и заднего 6 корпусов компрессора.
5 Отвернуть и снять 29 болтов 2 на вертикальном фланцевом соединении переднего 3 и заднего 6 корпусов компрессора.
6 Отвернуть и снять 14 болтов 7 на горизонтальном разъёме переднего корпуса компрессора.
7 Установить четыре направляющих штифта 8 на место шпилек 5.
8 Застропить верхнюю половину переднего корпуса компрессора.
9 С помощью четырёх отжимных болтов 9 отжать верхнюю половину переднего корпуса компрессора.
10 Отделить верхнюю половину переднего корпуса компрессора 3 и установить на брсья..11 Выпрессовать с помощью приспособления три контрольных штифта 10 на вертикальном фланцевом соединении заднего корпуса 6 и напорного патрубка ОК.
12 Отвернуть и снять 30 болтов 11 на вертикальном фланцевом соединении заднего корпуса и напорного патрубка.
13 Повторить п. 1.6-1.10 для заднего корпуса компрессора.
Проверка зазоров осевого компрессора
1 Переместить ротор осевого компрессора до упора в рабочие колодки 2 Проверка зазоров осевого компрессора (в направлении всаса). Положить свинцовую проволоку на ротор осевого компрессора для замера радиальных зазоров "а" "б" по рабочим и направляющим лопаткам на 0 1÷3 ступенях.
3 См рис. 5. Отвернуть и снять отжимные болты 9 на верхней половине передней части компрессора.
4 Используя направляющие штифты 8 установить верхнюю половину 3 на место; ослабить стропа.
5 Завернуть 14 болтов 7 горизонтального разъёма.
6 Отвернуть 14 болтов 7 снять и уложить верхнюю половину 3 на брусья.
7 Замерить по свинцовым оттискам радиальные зазоры по рабочим и направляющим лопаткам осевого компрессора на 0 1÷3 ступенях. Данные занести в ремонтный формуляр.
Зазор "а"=090÷140 мм
Зазор "б"=090÷140 мм
8 Замерить щупом радиальные зазоры на 0 1÷3 ступенях слева и справа по рабочим и направляющим лопаткам осевого компрессора. Данные занести в ремонтный формуляр.
9 Застропить верхнюю половину заднего корпуса компрессора. Отделить верхнюю половину заднего корпуса компрессора и отвести в сторону.
10 Положить свинцовую проволоку на ротор осевого компрессора для замера радиальных зазоров "а" "б" по лопаткам на 4÷9 ступенях.
11 Повторить п. 2.3÷2.6 для верхней половины заднего корпуса компрессора.
12 Замерить по свинцовым оттискам радиальные зазоры по рабочим и направляющим лопаткам осевого компрессора на 4÷9 ступенях. Данные занести в ремонтный формуляр.
Зазор "а"=090÷150 мм
13 Замерить щупом радиальные зазоры на 4÷9 ступенях слева и справа по рабочим и направляющим лопаткам осевого компрессора. Данные занести в ремонтный формуляр.
14 Замерить щупом радиальные зазоры на 4÷9 ступенях слева и справа по рабочим и направляющим лопаткам осевого компрессора. Данные занести в ремонтный формуляр.
Демонтаж верхней половины корпуса ОК (вариант II)
1 См. Рис. 3.1. Выпрессовать три контрольных штифта 23 на фланцевом соединении корпуса компрессора 15 и напорного патрубка 24.
2 Отвернуть и снять 30 болтов 25.
3 Отвернуть и снять восемь гаек 26 на четырёх призонных
Демонтаж верхней половины корпуса ОК
4 Снять призонные шпильки 27.
5 Отвернуть и снять 28 болтов 28 на горизонтальном разъёме корпуса компрессора 15.
6 Установить четыре направляющих штифта на место призонных шпилек.
7 Установить четыре отжимных болта в соответствующие резъбовые отверстия и отжать верхнюю половину корпуса компрессора.
8 См. Рис. 2. Застропить верхнюю половину корпуса компрессора.
9 Отделить верхнюю половину корпуса компрессора и отвести в сторону.
Проверка зазоров осевого компрессора
1 Переместить ротор осевого компрессора в направлении всаса до упора в рабочие колодки.
2 Положить свинцовую проволоку на ротор осевого компрессора для замера радиальных зазоров "а" "б" по рабочим и направляющим лопаткам на 0 1÷9 ступенях.
3 Отвернуть и снять отжимные болты на верхней половине корпуса компрессора.
4 Застропить и установить верхнюю половину на место используя направляющие штифты; ослабить стропа.
5 Завернуть 28 болтов 28.
6 Повторить п. 3.5 3.7 3.9 данной операции (вариант II) и уложить верхнюю половину корпуса компрессора на брусья.
7 Замерить по свинцовым оттискам радиальные зазоры по рабочим и направляющим лопаткам осевого компрессора на 0 1÷9 ступенях. Данные занести в ремонтный формуляр.
8 Замерить щупом радиальные зазоры на 0 1÷9 ступенях слева и справа по рабочим и направляющим лопаткам осевого компрессора. Данные занести в ремонтный формуляр.
4 Демонтаж верхней половины напорного патрубка ОК
Демонтаж верхней половины напорного патрубка ОК
1 См. рис. 3.5. Выпрессовать четыре контрольных штифта 1 на горизонтальном разъёме напорного патрубка 2.
2 Отвернуть и снять 36 болтов 5 на горизонтальном разъёме напорного патрубка 2.
3 Отвернуть и снять 12 болтов 6 на вертикальном фланцевом соединении верхней половины напорного патрубка 2.
4 Отвернуть и снять четыре болта 7 крепления воздушной обоймы 8 к верхней половине напорного патрубка 2.
5 Отвернуть и снять четыре гайки 12 на двух призонных шпильках 13.
6 Выпрессовать две призонных шпильки 13.
7 Установить четыре направляющих штифта и четыре отжимных болта в соответствующие отверстия.
8 Застропить верхнюю половину напорного патрубка 2.
9 Отделить верхнюю половину напорного патрубка 2 и отвести в сторону.
10 Отвернуть и снять четыре отжимных болта.
Замер зазоров См. рис. 5
1 Положить свинцовую проволоку на ротор ОК и на воздушную обойму для замера радиальных зазоров "а" и "б" по рабочим и направляющим лопаткам на 10÷15 ступенях осевого компрессора и зазоров "л1" и "л2" по лопаткам выходного направляющего аппарата на I и II ступенях.
2 См. рис. 6. Используя направляющие штифты установить верхнюю половину напорного патрубка 2 на место и ослабить стропа.
3 Установить на место четыре контрольных штифта 1.
4 Завернуть 18 болтов 5 (через один).
5 Повторить п. 1.2 1.9 и уложить верхнюю половину напорного патрубка на брусья.
6 Замерить по свинцовым оттискам радиальные зазоры по рабочим и направляющим лопаткам осевого компрессора "а" и "б" на 10÷15 ступенях осевого компрессора и зазоров "л1" и "л2" по лопаткам выходного направляющего аппарата на I и II ступенях. Данные занести в ремонтный формуляр [10].
Зазор "а"=114÷178 мм–10÷13
ст. 140÷191 мм–14÷15 ст.
Зазор "б"=114÷165 мм–10÷13
ст. 140÷191 мм–14 ст.
Зазоры "л1" "л2"=005÷074 мм
7 Замерить щупом радиальные зазоры на 10÷15 ступенях слева и справа по рабочим и направляющим лопаткам осевого компрессора и зазоры "л1" и "л2" по лопаткам выходного направляющего аппарата на I и II ступенях. Данные занести в ремонтный формуляр.
8 Замерить осевой зазор между ротором осевого компрессора и воздушной обоймой 8. Данные занести в ремонтный формуляр.
Демонтаж воздушной обоймы
1 См. рис. 4.5. Завернуть в верхнюю половину воздушной обоймы 8 три рым-болта 9.
2 Застропить обойму.
3 Отвернуть и снять шесть болтов 10 на горизонтальном разъёме воздушной обоймы 8.
Примечание – В воздушной обойме 8 предусмотрены четыре установочных штифта 11; без необходимости снимать их не рекомендуется.
4 Отделить верхнюю половину воздушной обоймы 8 от нижней половины отвести в сторону и уложить на брусья.
Примечание – Зазоры по воздушным уплотнениям обоймы 8 определить методом обмера после снятия ротора ОК-ТВД.
Зазоры "и к"=142÷157 мм
Очистить от грязи ржавчины; продуть сжатым воздухом верхние половины ОК.
Произвести дефектацию лопаточного аппарата ОК.
5. Монтаж верхней половины напорного патрубка ОК
Технические требования:
) Произвести осмотр проточной части; исключить попадание посторонних предметов.
) Все крепёжные болты установочные штифты и сопрягаемые поверхности смазать смазкой.
) При сборке на фланцах крышках и других деталях сверять маркировку.
) Очистить рабочие поверхности фланцев устранить заусенцы.
Монтаж воздушной обоймы.
1 См. рис. 3.5. Застропить верхнюю половину воздушной обоймы 8 подвести к месту установки и установить на нижнюю половину.
Примечание – Предварительно смазать смазкой четыре установочных штифта_11.
2 Расстропить обойму отвернуть и снять три рым-болта 9.
3 Завернуть шесть болтов 10.
Монтаж верхней половины напорного патрубка.
1 См. рис. 3.5. Застропить верхнюю половину напорного патрубка 2 поднять и подвести к месту установки.
2 Положить свинцовую проволоку на ротор осевого компрессора и на воздушную обойму для замера радиальных зазоров по рабочим и направляющим лопаткам на 10-15 ступенях ОК и зазоров по лопаткам выходного направляющего аппарата на I и II ступенях.
3 Установить четыре направляющих штифта.
4 Установить верхнюю половину напорного патрубка 2 на нижнюю половину используя направляющие штифты и ослабить строп.
5 Поднять верхнюю половину напорного патрубка 2 и отвести в сторону.
6 Замерить по свинцовым оттискам радиальные зазоры на 10-15 ступенях ОК и зазоры по лопаткам выходного направляющего аппарата на I и II ступенях. Данные занести в ремонтный формуляр. См. гл 3.3 п. 2.6
7 Нанести на фланцы горизонтального разъёма напорного патрубка 2 тонкий слой уплотняющей мастики "Перматекс" и смазки.
Примечание – Мастику "Перматекс" наносить узкими полосками шириной 254 мм с двух сторон от резьбовых отверстий под болты горизонтального разъёма. На остальные участки разъёма нанести смазку "Фел-Про С102".
8 Повторить п. 2.4 данной операции и установить верхнюю половину патрубка на место. Расстропить.
9 Установить две призонные шпильки 13 смазав их предварительно смазкой.
10 Завернуть четыре гайки 12.
11 Установить четыре контрольных штифта 1 на горизонтальном разъёме патрубка.
12 Завернуть 12 болтов 6 на вертикальном фланцевом соединении опорного кольца соплового аппарата 1-ой ступени и напорного патрубка.
13 Завернуть 36 болтов 5 на горизонтальном разъёме патрубка 2.
14 Завернуть четыре болта 7 крепления верхней половины воздушной обоймы 8 к напорному патрубку 2.
6. Монтаж верхней половины корпуса ОК
Монтаж заднего корпуса компрессора (вариант I).
1 См. рис. 3.4. Завернуть в верхнюю половину заднего корпуса компрессора 6 два рым-болта 14.
2 Застропить верхнюю половину 6 и подвести к месту установки.
3 Положить свинцовую проволоку на ротор осевого компрессора для замера радиальных зазоров по рабочим и направляющим лопаткам на 4-9 ступенях.
4 Установить четыре направляющих штифта 8 для сборки заднего корпуса компрессора 6.
5 Установить верхнюю половину заднего корпуса на нижнюю половину ослабить стропа.
Примечание – В случае неплотного прилегания верхней и нижней половин выполнить затяжку болтов 7 (через один).
6 Поднять верхнюю половину заднего корпуса 6 и отвести в сторону.
7 Замерить по свинцовым оттискам радиальные зазоры по рабочим и направляющим лопаткам ОК на 4-9 ступенях. Данные занести в ремонтный формуляр.
Зазор "а"=089÷152 мм
Зазор "б"=089÷140 мм
8 Нанести на фланцы горизонтального разъёма корпуса компрессора 6 тонкий слой уплотняющей мастики "Перфект Сийл" а на вертикальные разъёмы смазку "Фел-Про С102". Мастику "Перфект Сийл" нанести полосками (шириной 254 мм) с двух сторон от резьбовых отверстий
9 Повторить п. 1.5 данной операции. Снять направляющие штифты 8.
10 Установить три контрольных штифта 10 и четыре призонные шпильки 13 смазав их смазкой.
11 Расстропить задний корпус 6 вывернуть два рым-болта 14 снять грузоподъёмные скобы.
12 Завернуть восемь гаек 12 на призонных шпильках 13.
13 Завернуть 30 болтов 11 на вертикальном разъёме.
14 Завернуть 14 болтов 7 на горизонтальном разъёме.
Монтаж переднего корпуса компрессора (вариант I)
1 См. рис. 3.3. Застропить верхнюю половину переднего корпуса 3 и подвести к месту установки.
2 Положить свинцовую проволоку на ротор осевого компрессора для замера радиальных зазоров по рабочим и направляющим лопаткам на 0 1-3 ступенях.
3 Повторить п. 1.4-1.7 для переднего корпуса 3 и определить зазоры на 0 1-3 ступенях ОК. Данные занести в ремонтный формуляр.
Зазор "а"=089÷140 мм
4 Нанести на фланцы горизонтального разъёма переднего корпуса ОК 3 тонкий слой уплотнительной мастики "Перфект Сийл" а на вертикальные разъёмы смазку "Фел - Про С102". См. п. 1.8
5 Установить верхнюю половину переднего корпуса компрессора 3 на нижнюю половину используя направляющие штифты 8.
6 Снять направляющие штифты 8 расстропить корпус компрессора.
7 Установить три контрольных штифта на вертикальном фланцевом соединении переднего и заднего корпусов ОК.
8 Установить шпильки 5.
9 Завернуть гайки 4 на призонных шпильках 5.
10 Завернуть 29 болтов 2 на вертикальном фланцевом соединении переднего и заднего корпусов ОК.
Примечание – Если корпус осевого компрессора цельный (вариант II) то пункты 2.7 и 2.10 не выполнять.
11 Завернуть 14 болтов 7 на горизонтальном разъёме переднего корпуса_3.
7 Монтаж верхней половины впусконого патрубка
Монтаж верхней половины впускного патрубка
1Замерить зазоры по лопаткам ВНА. Данные занести в ремонтный формуляр.
2 См. рис. 3.2. Застропить впускной патрубок 14 поднять и подвести к месту установки.
Примечание – Операция выполняется если корпуса ОК цельные (вариант II).
Если корпуса ОК раздельные – до операций технологической карты № 48.
3 Нанести на фланцы горизонтального разъёма впускного патрубка 14 тонкий слой уплотняющей мастики "Перматекс" а на вертикальный разъём смазку "Фел-Про С102".
4 Застопорить регулирующее кольцо входного направляющего аппарата (ВНА) ОК во избежание проворачивания направляющих лопаток.
Примечание – Лопатки ВНА необходимо привести в закрытое положение.
Мастику "Перматекс" нанести полосками (шириной 254 мм) с двух сторон от резьбовых отверстий
5 Установить направляющие штифты на место призонных шпилек 18.
6 Установить верхнюю половину впускного патрубка 14 на нижнюю половину. Убедиться что маркировка на зубчатой рейке и шестернях совпадают.
7 Расстропить впускной патрубок снять направляющие штифты.
8 См. рис. 3.1.3.2. Установить три контрольных штифта 16 и четыре призонные шпильки 18 согласно
9 Завернуть крепёж на вертикальном и горизонтальном разъёмах смазав его предварительно смазкой "Фел – Про С102": восемь гаек 17; 29 болтов 13 шесть болтов 19 и шесть болтов 20.
Сборка регулирующегокольца ВНА
1 См. рис. 3.3. Соединить регулирующее кольцо ВНА ОК по горизонтальному разъёму установив призонную шпильку 31 и затянув крепёж: две гайки 30 две пластины 29 два болта 28 (с двух сторон).
2 См. рис. 3.1. Соединить регулирующее кольцо ВНА ОК с приводом: установить на место пластины 12
запрессовать согласно маркировке призонные шпильки 11 затянуть крепёж (четыре гайки 10 два болта_9 пластина 8 болт 7).
3 Снять все блоки используемые для стопорения кольца и опору 4.
4 Установить ограничитель хода кольца 6 и завернуть два болта 5.
5 Установить кожух регулирующего кольца 3 и завернуть 15 болтов 1 установив предварительно 15 пружинных шайб 2.
1 Исследование физических процессов в ступенях газовых турбин с сотовыми уплотнениями
Опыт освоения и эксплуатации газовых турбин обозначил ряд проблем решение которых остается актуальным в настоящее время.
При работе маневренных газотурбинных установок с частичной нагрузкой а также в процессе их пуска и останова в ряде случаев создаются такие условия обтекания лопаточного аппарата которые способствуют возникновению в периферийных сечениях рабочих лопаток локальных зон трансзвуковых течений а также зон характеризующихся явлениями отрыва пограничного слоя oт поверхности лопатки. Наличие указанных зон может оказывать существенное влияние на напряженное состояние лопаток в значительной степени определяющее надежность работы турбины.
Установка сотовых уплотнений в радиальных зазорах газовых турбин позволяет получить определенный эффект при соблюдении оптимальной геометрической структуры ячеек. При этом обеспечивается сокращение утечек рабочего тела через зазор и следовательно повышение эффективности работы ступени. Экспериментальные данные полученные при испытаниях турбинных ступеней с сотовыми уплотнениями используются в настоящем проекте тем самым увязываются критерии качества и надежности уплотнения с его гидродинамическими показателями учитываются при этом эксплуатационные факторы работы уплотнения.
2 Уплотнение радиального зазора безбандажных рабочих лопаток газовой турбины
Во избежание задевания ротора о статор между рабочими лопатками и корпусом турбины должен быть предусмотрен определенный радиальный зазор. Необходимая величина этого зазора в холодном состоянии обычно определяется условием исключения возможности задевания лопаток о корпус на рабочих режимах а также при пуске-останове двигателя. Отметим что на установившихся режимах работы величина зазора меньше монтажной вследствие большей тепловой деформации в рабочих условиях ротора по сравнению со статором. В периферийной области турбинной ступени происходят очень сложные по своей природе процессы течения рабочей среды которые имеют здесь ярко выраженный трехмерный характер [16].
Целью данной серии экспериментальных исследований являлось сравнение по эффективности работы гладких и сотовых уплотнений при различных величинах радиальных зазоров а также сопоставление двух конструктивно различных типов сотовых уплотнений между собой при их использовании в составе турбинной ступени. Представлены результаты эксперимента поставленного на модели одноступенчатой газовой турбины.
Схема проточной части турбины а также схема измерений в ступени представлены на рис.4.1. В таблице приведены некоторые геометрические параметры исследуемой ступени.
Исследования эффективности работы ступени турбины проводились при использовании в ее конструкции сотовых и гладких уплотнений в качестве периферийных для безбандажного рабочего колеса. По своей геометрии ячейки уплотнения имели профиль правильного шестиугольника и изготовлялись из стальной фольги толщиной 025 мм при этом глубина ячеек составляла значение hя = 5 мм. Испытывались сотовые уплотнения с диаметрами ячеек dя = 4 мм и dя = 25 мм (соотношения hяdя при этом соответственно hяdя 1 и hяdя = 2). Величина радиального зазора изменялась путем расточки обечайки над рабочим колесом ступени. Это обусловливало постоянство значения положительной перекрыши в течение проведения всех опытов которая оставалась равной Δ=12 мм. Диапазон изменения величины радиального зазора составил = 05 3 мм (относительный зазор = l=06 4%).
Геометрические параметры экспериментальной ступени
Направляющий аппарат
Диаметр средней окружности Dср
Толщина выходной кромки увых
На рис.4.2 представлены зависимости относительного внутреннего КПД ступени от параметра uС0 при различных значениях радиального зазора для конструкции с гладким уплотнением.
Аналогичные зависимости для ступени с сотовыми уплотнениями различной геометрии показаны на рис.4.3.
Из представленных графиков (рис.3.2 3.3) видно что КПД ступени с сотовым уплотнением в области оптимальных значений uС0((uС0)opt-=06 07) выше чем КПД ступени с уплотнением «гладкая стенка». Однако при этом в зоне очень маленьких величин радиальных зазоров ( = 05 мм) КПД ступени с гладким уплотнением оказался выше чем КПД ступени с сотовым уплотнением с dя= 25 мм но все же ниже чем при использовании сотового уплотнения с dя = 4 мм. Указанное явление объясняется некоторыми особенностями течения потока через радиальный зазор при различных конструктивных параметрах сотового уплотнения
Наличие более высокого КПД ступени с сотовым уплотнением по сравнению с гладким подтверждается результатами выполненного нами траверсирования потока за рабочим колесом (рис.4.4). Обнаружена также характерная особенность работы ступени с сотовым уплотнением которая состоит в явлении «запирания» потока утечки рабочего тела через радиальный зазор. При уплотнении «гладкая стенка» в периферийной части лопаки и в зоне радиального зазора наблюдаются значительное изменение параметров потока и наличие больших осевых скоростей (см. рис.4.4) что объясняет дополнительные утечки рабочего тела и следовательно рост величины потерь от радиального зазора. Напротив для ступеней с сотовыми уплотнениями такие резкие изменения параметров не характерны чем по нашему мнению и объясняется повышение КПД этих ступенях.
На рис.4.5 представлена зависимость изменения относительного КПД ступени (=0i0i=0) от величины относительного радиального зазора ( = l) при оптимальных значениях параметра uC0 для различных вариантов уплотнения радиального зазора. Отметим более высокий темп снижения КПД при увеличении радиального зазора характерный для ступени с гладким уплотнением. Указанную особенность работы сотовых уплотнений необходимо учитывать при определении влияния увеличенных радиальных зазоров образующихся в процессе длительной эксплуатации двигателя.
Таким образом на основе анализа результатов экспериментальных исследований модели турбинной ступени с сотовым уплотнением на периферии рабочего колеса можно сделать следующие выводы:
КПД исследованной ступени при использовании сотовых уплотнений с характеристикой hяdя 1 оказался выше чем при уплотнении «гладкая стенка» во всем исследованном диапазоне изменения величин радиальных зазоров.
Результаты траверсирования потока за рабочим колесом подтверждают вывод о снижении потерь с утечкой рабочего тела через периферийный радиальный зазор при использовании сотовых уплотнений.
Существует возможность оптимизации конструктивных параметров сотовой структуры уплотнения для получения максимального воздействия на поток утечки через радиальный зазор с целью снижения его количественной величины.
При использовании в турбинной ступени сотового уплотнения возможно уменьшение величины радиального зазора по сравнению с номинальным без опасности разрушения рабочей лопатки в случае задевания о сотовую структуру в процессе работы.
Итак в результате проведенных экспериментальных исследований на статических и динамических стендах представляется возможным сделать вывод что оптимизация конструктивных параметров сотового уплотнения должна проводиться с учетом влияния следующих факторов:
формы ячейки сотового уплотнения;
геометрических размеров ячеек;
величины и формы радиального зазора;
особенностей конструктивных характеристик ступеней турбин;
режимных характеристик движения потока;
пульсационных явлений в сотовой структуре.
3 Внедрение результатов исследования в ГТН-25
Полученные результаты позволяют нам сделать вывод о рациональности установки сотовых уплотнений. Целесообразно будет установить сотовые уплотнения на периферию второй ступени ТВД.
4 Результаты модернизации
Уточненная эффективная мощность
где - расход теплоты в камере сгорания.
Сравнение технико-экономических показателей ГТУ ГТН-25 и ГТН-25М приведены в таблице 4.2.
Технико-экономические показатели ГТУ ГТН-25 и ГТН-25М
Номинальная мощность ГТУ
Эффективный КПД ГТУ
Удельный расход условного топлива
Температура газа перед турбиной
Частота вращения ротора
Число часов работы в год
Результатом выполнения ступени ТВД усовершенствованного типа явилось следующее:
- КПД установки увеличился на 05%
- удельный расход топлива снизился на 00063 кгкВт*ч
Модернизацию турбины по результатам следует принять целесообразной.
Арсеньев Л.В. Тырышкин В.Г. и др. Газотурбинные установки. Справочное пособие.- Л.: Машиностроение 1978.- 232 с.
Арсеньев Г.В. Трубилов М.А. Паровые и газовые турбины.- М.: Энергоатомиздат 1985.- 352 с.
Бауман Н.Я. Яковлев М.И. Свечков И.М. Технология производства паровых и газовых турбин.- М.: Машиностроение 1973.- 320 с.
Бронштейн Л.С. Ремонт стационарной газотурбинной установки.- Л.: Недра 1987.- 143 с.
Газотурбинные установки Уральского турборемонтного завода. Осипенко В.Н. Ковалевский М.М. и др.- Теплоэнергетика. 1975 №6- 289 с.
Гоголев И.Г. Методические указания к выполнению курсового и дипломного проектов газовых турбин и газотурбинных установок для оформления чертежей и пояснительной записки.- Брянск.: БИТМ 1970.- 98 с.
Головко В.А. Экономика и организация производства в дипломных проектах.- Тула: ГПИ 1979.– 59 с.
Дейч М.Е. Трояновский Б.М. Исследование и расчеты ступеней осевых турбин.- М.: Машиностроение 1956.- 168 с.
Демиденко И.А. Организация и планирование машиностроительного производства. Управление. Методические указания по выполнению организационно-экономической части дипломных проектов для специальности 1602 – «Турбостроение».- Брянск: БИТМ 1993.- 27 с.
Единая система конструкторской документации. Основные положения.- М.: Издательство стандартов 1982.- 150 с.
Жирицкий Г.С. Стрункин В.А. Конструкция и расчет на прочность деталей паровых и газовых турбин.- М.: Машиностроение 1968.- 520 с.
Зольф Г.А. Тепловой расчет стационарных газовых турбин.- М.: Машиностроение 1960.- 210 с.
Инструкция по планированию учету и калькулированию себестоимости продукции на предприятиях тяжелого энергетического и транспортного машиностроения. Свердловск: НИИ экономики и организации производства 1972.- 100 с.
Кирилов И.И. Автоматическое регулирование паровых турбин и газотурбинных установок: Учебник для студентов вузов обучающихся по специальности «Турбостроение». 2-е изд. перераб. и доп.- Л.: Машиностроение. Ленинградское отделение 1988.- 447 с.
Кирилов И.И. Газовые турбины и газотурбинные установки. М.: Машиностроение 1956.- 168 с.
Кирилов И.И. Теория турбомашин.- Л.: Машиностроение 1972.- 318 с.
Костюк А.Г. Шерстюк А.Н. Газотурбинные установки.- М.: Высшая школа 1979.- 620 с.
Кузьмичев Р.В. Повышение надежности энергетических машин. Дроконов А.М. Прочность турбомашин: Учеб. Пособие.- Брянск: БИТМ 1992.- 132 с.
Кузьмичев Р.В. Гоголев И.Г. Коэффициент расхода надбандажного уплотнения турбинной ступени. Энергомашиностроение 1985. №12.- 88 с.
Кузьмичев Р.В. Паровые и газовые турбины. Методические указания к выполнению курсового и дипломного проектов газовых турбин и газотурбинных установок для студентов специальности «Турбостроение».- Брянск: БИТМ 1981.- 88 с.
Николаева Т.А. Промышленная экология. Методические указания.- Брянск: БГТУ 2001.- 18 с.
Ольховский Г.Г. Энергетические газотурбинные установки.- М: Энергоиздат 1985.- 304 с.
Препкин Ю.М. Камеры сгорания газотурбинных двигателей.- М.: Машиностроение 1973.- 391 с.
Ревзин Б.С. Газотурбинные газоперекачивающие агрегаты.- М.: Недра 1986.- 215 с.
Ревзин Б.С. Тарасов А.В. Марковский В.М. Тепловой расчет схем приводных газотурбинных установок на номинальный и переменный режимы работы: Учебное пособие.- Екатеринбург: ГОУ УГТУ-УПИ 2001.- 61 с.
Свойство сталей и сплавов применяемых в котлотурбостроении.- Л: ЦКТИ 1967.- 159 с.
Скроткин Я.Н. Аэродинамический расчет лопаток осевых турбомашин.- М: Машиностроение 1972.- 159 с.
Ситчиков М.Ф. Металлы в турбостроении.- М: Машиностроение 1974.- 154 с.
Слубачевский Г.С. Авиационные газотурбинные двигатели.- М: Машиностроение 1976.- 520 с.
Шварц В.А. Конструкции газотурбинных установок.- М: Машиностроение 1970.- 243 с.
Юдин Е.Я. Охрана труда в машиностроении.- М: Машиностроение 1976.- 106 с.
Скрипты для страниц. Активируются через alt+F9
Продольный 4.cdw

Тепловая схема.cdw

КС- камера сгорания;
ТВД- турбина высокого давления;
ТНД- турбина низкого давления;
) при различных значениях
Принципиальная схема ГТУ ГТН-25М
Цикл в T-S диаграмме ГТУ ГТН-25М
Цикл в P-V диаграмме ГТУ ГТН-25М
Продольный 2.cdw

Продольный 1.cdw

Спецчасть 2.cdw

- гладкое уплотнение;
- сотовое уплотнение
Зависимость относительного КПд от величины радиального зазора
- гладкое уплотнение; 2 - сотовое уплотнение d
Номинальная мощность ГТУ
Эффективный КПД ГТУ
Удельный расход условного топлива b
Температура газа перед турбиной Т
Частота вращения ротора
Число часов работы в год
Результатом выполнения ступени ТВД усовершенствованного
типа явилось следующее:
- КПД установки увеличился на 0
- удельный расход топлива снизился на 0
Иследование физических процессов
в ступенях газовых турбин с
сотовыми уплотнениями
Сравнение технико-экономических показателей ГТН-25 и ГТН-25М
Спецчасть 1.cdw

Схема проточной части и измерений
Направляющий аппарат
Диаметр средней окружности
Толщина выходной кромки
Зависимость ступени с гладким
Зависимость ступени с сотовым
Геометрические параметры
экспериментальной ступени
Исследование физических процессо
в в ступенях газовых турбин с
сотовыми уплотнениями
Продольный 3.cdw

Технология.cdw

-опора; 6-ограничитель хода кольца ВНА; 8
-призонная шпилька; 14-впускной патрубок; 15-корпус компрессора;
-контрольный штифт; 24-напорный патрубок
Демонтаж (монтаж) верхней половины впускного патрубка
-впускной патрубок; 17-гайка; 18-призонная шпилька; 1
-болт; 21-штифт; 22-таль
Разборка (сборка) трубопроводов в пределах
агрегата-трубопровод топливного газа
-коллектор отбора воздуха; 6
-хомут; 7-противопомпажный клапан;
-трубопровод; 11-компенсатор; 16
-воздуховод; 21-коллектор подачи
охлаждающего воздуха; 23-трубопровод подвода воздуха на диски;
-компенсатор; 27-воздухосборник; 29-пластина; 31-шпилька;
Монтаж и демонтаж корпуса
Рекомендуемые чертежи
- 24.01.2023