Проектирование комплекта инструментов для обработки ступенчатого отверстия с заданными параметрами




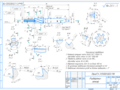
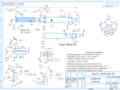
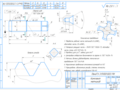
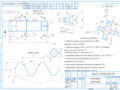
- Добавлен: 24.01.2023
- Размер: 542 KB
- Закачек: 1
Описание
Состав проекта
![]() |
![]() |
![]() ![]() ![]() |
![]() ![]() ![]() ![]() |
![]() ![]() ![]() ![]() |
![]() ![]() ![]() ![]() |
![]() ![]() ![]() ![]() |
![]() ![]() ![]() ![]() |
![]() ![]() ![]() |
![]() ![]() ![]() ![]() |
![]() ![]() ![]() |
![]() ![]() ![]() ![]() |
Дополнительная информация
Поле доgeск1.frw

Развертка.cdw

Разветка.cdw

Сверло перовое.cdw

Развёртка-зенкер.cdw

Метчикq.cdw

Метчик.cdw

Поле доgeск2.frw

Зенкер цельный.cdw
