Проектирование, исследования механизма литьевой машины




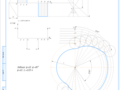
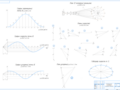
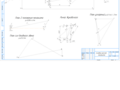
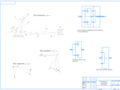
- Добавлен: 24.01.2023
- Размер: 371 KB
- Закачек: 0
Описание
Состав проекта
![]() |
![]() |
![]() ![]() ![]() ![]() |
![]() ![]() ![]() ![]() |
![]() ![]() ![]() |
![]() ![]() ![]() |
![]() ![]() ![]() ![]() |
![]() ![]() ![]() |
Дополнительная информация
исл6.cdw

кин6.cdw

кул6.CDW

сил6.cdw

Рекомендуемые чертежи
- 25.01.2023
- 25.01.2023
- 18.12.2021
Свободное скачивание на сегодня
- 22.08.2014
- 29.08.2014