Проектирование индивидуального привода




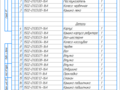
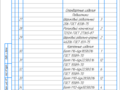
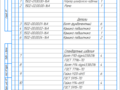
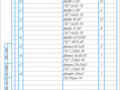
- Добавлен: 24.01.2023
- Размер: 1 MB
- Закачек: 0
Описание
Состав проекта
![]() |
![]() |
![]() |
![]() ![]() ![]() ![]() |
![]() ![]() ![]() ![]() |
![]() |
![]() |
![]() ![]() ![]() |
![]() |
![]() |
![]() ![]() ![]() ![]() |
![]() ![]() ![]() ![]() |
![]() |
![]() ![]() ![]() ![]() |
![]() |
![]() ![]() ![]() ![]() |
![]() |
![]() ![]() ![]() ![]() |
![]() ![]() ![]() ![]() |
![]() |
![]() ![]() ![]() ![]() |
![]() |
![]() ![]() ![]() ![]() |
![]() |
![]() |
![]() ![]() ![]() ![]() |
![]() |
![]() ![]() ![]() ![]() |
![]() |
![]() ![]() ![]() ![]() |
![]() |
![]() ![]() ![]() ![]() |
![]() |
Дополнительная информация
колесо чер.cdw

червяк.cdw

спецификация.cdw

привод индивидуальный.cdw

спецификация продолжение.cdw

привод индивидуальный 1.cdw

спецификация1.3.cdw

спецификация1.1.cdw

дм1.2.cdw

дм1.1.cdw

спецификация1.2.cdw

крышка редуктора.cdw

Спецификация.cdw

рама.cdw

Рекомендуемые чертежи
- 25.10.2022
- 07.12.2021