Проектирование и исследование механизма двигателя внутреннего сгорания




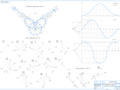
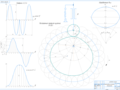
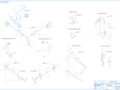
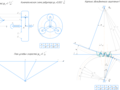
- Добавлен: 24.01.2023
- Размер: 1 MB
- Закачек: 0
Описание
Состав проекта
![]() |
![]() |
![]() ![]() ![]() |
![]() |
![]() ![]() ![]() |
![]() |
![]() ![]() ![]() ![]() |
![]() ![]() ![]() ![]() |
![]() |
![]() ![]() ![]() ![]() |
![]() ![]() ![]() ![]() |
Дополнительная информация
TMM 3-4.doc
с роликовым толкателем
Построить в произвольном масштабе заданный закон изменения второй производной перемещения толкателя по углу поворота кулачка
Методом графического интегрирования построить графики
Графически исключив параметр φ из графиков
построить совмещенный график
Определить минимальный радиус кулачка.
Методом обращения движения построить практический (он же рабочий) профиль кулачка.
1 Задание и данные для расчетов
Задание. Спроектировать кулачковый механизм с роликовым толкателем. Дано:
схема кулачкового механизма (рис. 3.1);
закон изменения аналога ускорения толкателя кулачкового механизма (рис. 3.1);
исходные данные в таблице 1.
Наименование параметра
Ход толкателя в кулачковом
давления в кулачковом
Рисунок 3.1 – Схема кулачкового механизма и закон аналога ускорений
2 Построение диаграмм движения толкателя
На фазе удаления толкателя кулачкового механизма движение по синусоидальному закону.
Рассчитываем экстремальное значения ординат графиков аналогов ускорений и скоростей:
На фазе возвращения толкателя кулачкового механизма движение по синусоидальному закону.
Построение графиков начнем с графика аналога ускорений толкателя.
На оси абсцисс откладываем фазовые углы:
После соответствующего расчета принимаем масштабный коэффициент по оси ординат графика аналога ускорений равным:
Он будет таким же и для графиков аналогов скоростей и перемещений толкателя:
Длину ОХ по оси абсцисс соответствующую одному обороту кулачка принимаем равной 170 мм.
Следовательно угол φу=170° изображаем отрезком 85 мм угол φв=170° изображаем отрезком 85 мм.
Делим фазовые углы φу и φв на несколько равных частей:
Определяем масштабный коэффициент по оси абсцисс
График аналога скоростей строим используя метод графического интегрирования графика аналога ускорений выходного звена.
Проверка: площади кривых (фазы φу и φв) должны быть одинаковыми.
На оси абсцисс графика аналога скоростей и из середины участков восстанавливаем перпендикуляры до пересечения с линиями графика. Точки пересечения проектируем на ось ординат и соединяем точки полученные на оси ординат с полюсом Р2 лучами 12 6.
Определяем полюсное расстояние:
Под диаграммой аналога скоростей строим график перемещения толкателя.
Ось абсцисс делим на участки от 0 до 12.
В пределах участка 0 – 1 поводим хорду параллельную лучу 1 из конца этой хорды в пределах участка 1 – 2 проводим хорду параллельную лучу 2 и т.д.
Ординаты фазы φу симметричны ординатам фазы φв.
Проверка: максимальная ордината графика перемещений толкателя 6 должна получится равной величине хода толкателя 14 мм. (в масштабе М 1:10).
Используя графики перемещения и аналога скоростей толкателя сводим значения ординат этих графиков в таблицу 2.
3 Определение минимального радиуса
Для определения минимального радиуса кулачка Rmin строится дополнительная диаграмма методом исключения угла φ
в масштабе по данным таблицы 2.
Для этого проводим взаимно перпендикулярные оси. Ось ординат обозначим через S а ось абсцисс через S. По оси S производим разметку пути толкателя. В направлении перпендикулярном движению толкателя откладываем для каждого положения величины S вправо при движении толкателя вверх. Построенные точки соединяем плавной кривой.
Строим вторую половину диаграммы откладывая величины S влево при движении толкателя вниз.
По диаграмме определяем допустимую область центров вращения кулачка. Для этого из концов отрезков максимальных значений S проводим лучи под углом доп=30° к направлению движения толкателя.
Эти лучи пересекаются в точке О1 которая определяет положение оси вращения кулачка при его минимальных размерах.
ОО1 представляет собой минимальный радиус профиля кулачка Rmin= ОО1= 100 мм. Этот размер берется прямо с чертежа так как диаграмма была построена в масштабе
4 Построение профиля кулачка
Начинаем построение профиля кулачка (без ролика).
В произвольной точки О (ось вращения кулачка) проводим окружность радиусом Rmin= 100 мм. то есть построение производим в масштабе . Через ось О проводим линию 0 – 0 движение толкателя.
В соответствии с разметкой фазовых углов на графике S" откладываем начиная от действительной линии движения толкателя в направлении противоположном вращению кулачка фазовые углы φу=170° и φв=170°.
Отмечаем на окружности Rmin точки 612.
Делим фазовые углы на шесть равных частей (каждая часть равна 2833°). Точки деления на окружности Rmin соединяем радиусами (лучами) с центром вращения кулачка – точкой О.
От окружности радиуса Rmin вдоль этих радиусов от соответствующей точки откладываем перемещения толкателя из таблицы 2 для .
Эти перемещения показаны толстыми линиями.
Соединяем полученные точки плавной кривой получаем центровой (теоретический) профиль кулачка. Этот профиль является рабочим профилем кулачка с толкателем без ролика.
Определяем минимальный радиус кривизны центрового профиля кулачка ρmin как радиус вписанной окружности выпуклого участка профиля кулачка где кривизны окажется наибольшей. На этом участке произвольно выбираем три точки 345 и соединяем их двумя хордами. В середине хорд восстанавливаем к ним перпендикуляры точку пересечения которых М принимаем за центр вписанной окружности. Получаем ρmin=155 мм. в масштабе М 10:1.
Действительный профиль кулачка найдем как эквидистантную кривую отстоящую от центрального профиля на расстоянии равном радиусу ролика.
Радиус ролика выбирается наименьшим из условий:
Для получения действительного (рабочего) профиля кулачка на его центровом профиле выбираем ряд точек из которых проводим окружности радиусом равным радиусу ролика rp.
Огибающая этих окружностей (внутренняя) и является действительным (рабочем) профилем кулачка.
IV. Проектирование кинематической схемы
планетарного редуктора и построение
картины эвольвентного зацепления зубчатых колёс
По передаточному отношению модулю т учитывая условия соосности соседства и равных углов между сателлитами подобрать числа зубьев всех колёс планетарного механизма заданной схемы считая что Zmin>17 и колёса нулевые.
Рассчитать начальные диаметры и вычертить схему механизма в двух проекциях.
Построить картину скоростей и план угловых скоростей механизма (редуктора).
Рассчитать внешнее зацепление пары прямозубых колёс эвольвентных профилей с неподвижными осями нарезанных стандартной инструментальной рейкой модуля m. При выборе коэффициентов смещения рейки обеспечить отсутствие подреза ножек зубьев.
Построить картину эвольвентного зацепления. Изобразить по три зуба каждого колеса линию и дугу зацепления рабочие участки профилей зубьев.
Аналитически и по данным картины зацепления определить коэффициент перекрытия.
1 Описание схемы зубчатого механизма
На рисунке 4.1 изображена схема зубчатого механизма с планетарной ступенью. Механизм состоит из подвижного звена Н (водила) блока сателлитов Z2 опорного колеса Z3 зубчатого колеса Z1.
Угловая скорость коленчатого вала
(зубчатого колеса 1)
Передаточное отношение редуктора
Модуль зубчатых колес
Рисунок 4.1 – Схема зубчатого механизма с планетарной ступенью
2 Подбор чисел зубьев планетарного редуктора
Подбор чисел зубьев планетарного редуктора проводим в такой последовательности.
Запишем формулу передаточного отношения планетарной ступени редуктора:
Запишем условие соосности для данного планетарного редуктора:
Определим число зубьев колеса Z3 Z2:
После подбора чисел зубьев планетарного редуктора проверяем данную схему на:
заданное передаточное отношение (с допустимой точностью);
условие соседства (размещение нескольких сателлитов);
условие сборки (условие равных углов между сателлитами);
условие правильного зацепления.
Заданное передаточное отношение:
Расчетное передаточное отношение редуктора равно заданному.
Условие выполняется.
Условие соседства выполняется.
где К – число сателлитов;
Условие правильного зацепления:
3 Построение схемы редуктора
Определяем радиусы делительных окружностей всех зубчатых колёс редуктора:
Выбираем масштабный коэффициент схемы редуктора
Тогда масштабные радиусы колёс определятся как частное от деления действительных радиусов колёс на масштабный коэффициент схемы редуктора
Строим кинематическую схему редуктора в указанном масштабе.
4 Построение картины скоростей и плана
угловых скоростей редуктора
Для построения картины скоростей проводим линию ординат и проектируем на неё все характерные точки редуктора.
Определяем скорость точки А принадлежащей колёсам 1 и 2
Определяем масштабный коэффициент картины скоростей :
От точки А откладываем отрезок Аа = 50 мм изображающий вектор скорости точки А колеса 1. Соединяя точку а с точкой О (скорость точки О равна нулю) получим прямую 1 которая является линией распределения скоростей колеса 1.
Переходим к колесу 2. У этого колеса известны скорость точки А (она такая же как и скорость точки А колеса 1) и скорость точки С (её скорость равна нулю ). Поэтому соединяя точки а и С получим прямую 2 которая является линией распределения скоростей колёса 2
Переходим к водилу Н. Из точки В проведём горизонтальную прямую до пересечения с линией распределения скоростей 2. Получим точку b - конец отрезка скорости оси сателлита 2. Одновременно это скорость оси водила Н. Соединяя точки b и О; (скорость точки О равна нулю - ось вращения водила) получим прямую Н которая является линией распределения скоростей водила Н.
Для построения плана угловых скоростей определяем масштабный коэффициент:
Проводим прямую перпендикулярную линии и откладываем на ней отрезок 01 = 168 мм. Из точки 1 проводим луч параллельный линии 1 картины скоростей до пересечения с вертикальной прямой ОР. Из точки Р – полюса плана угловых скоростей проводим лучи параллельные линиям 2 3 и Н. Полученные отрезки 0-1 0-2 0-3 и О-Н пропорциональны соответствующим угловым скоростям:
С помощью плана угловых скоростей можно графически определить передаточное отношение редуктора:
Определим процент расхождения в расчётах:
Допустимая погрешность не должна выходить за пределы точности инженерных расчетов которые составляют 6-8%.
5 Построение картины эвольвентного зацепления
Выбираем масштабный коэффициент картины эвольвентного зацепления
или 4:1 с соответствием ГОСТ.
В нормальных колесах делительная окружность совпадает с начальной.
Откладываем межосевое расстояние и из центров колес О1 и О2 проводим делительные окружности радиусами r1 и r2.
Точка Р касания делительных окружностей называется полюсом зацепления.
Через полюс зацепления Р проводим общую касательную Т – Т и под углом зацепления - линию зацепления N – N (производящую прямую). Касательную Т – Т необходимо строить строго перепендикулярно к линии центров О1 - О2.
Определяем радиусы основных окружностей зубчатых колес Z1 и Z2 по формулам:
Проводим основные окружности радиусами и .
Проверка: эти окружности должны касаться линии N – N (но не пересекаться). Из центров колес О1 и О2 опускаем на линию зацепления N – N перпендикуляры О1А и О2В. Получаем точки А и В. Отрезок АВ линии зацепления называется теоретической линией зацепления.
Для более точного определения положения точек А и В воспользуемся формулами:
Определяем радиусы окружностей вершин зубчатых колес Z1 и Z2 по формулам:
Пересечение окружности вершин радиуса с линией зацепления N – N дает точку а а пересечение окружности вершин радиуса с линией зацепления N – N дает точку b.
Отрезок ab линии зацепления N – N называется активной линией зацепления. При указанном направлении вращения зубчатых колес 1 и 2 зацепление пары зубьев начинается в точке a и заканчивается в точке b.
Проводим окружности впадин указанными радиусами.
Профили зубьев очерчиваются по эвольвентам. Чтобы вычертить эвольвенту надо иметь основную окружность производящую прямую и чертящую точку на ней. Обычно за чертящую точку берется полюс зацепления Р.
При перекатывании производящей прямой N – N по первой основной окружности (радиус) получается эвольвента (профиля зуба) первого колеса. При перекатывании производящей прямой N – N по второй основной окружности (радиус) получается эвольвента (профиль зуба) второго колеса.
Для построения эвольвента (профиля зуба) второго колеса отрезок РВ делим на равные части например на четыре. Пусть длина каждой части равна h. Маленькие отрезки откладываем от точки В по дуге основной окружности вправо и влево. Обозначим точки деления 1234 7.
Точки 1234 7 соединяем радиусами с центром колеса О2 и в каждой из полученных точек 1234 7 проводим касательные к основной окружности радиуса . От точки 1 по касательной откладываем один маленький отрезок h от точки 2 – 2h и т.д. Соединяем полученные точки плавной кривой получаем эвольвенту которая строится от основной окружности до окружности вершин.
Неэвольвентная часть зуба (от основной окружности радиуса до окружности впадин радиуса ) очерчивается сначала по радиусу делается округление радиусом.
Определяем толщину зуба по делительной окружностям по формуле:
Отложим от полюса зацепления Р по делительной окружности r2 расстояние равное половине толщины зуба S22 и найдем ось симметрии зуба. Проводим ось симметрии и относительно этой оси строим правый зуба симметричный вычерченному.
Вычисляем величину окружного шага по делительной окружности
и угловой шаг колеса Z2 по формуле:
Для построения второго зуба откладываем от оси симметрии первого зуба величину углового шага по значению тангенса угла. Получим ось симметрии второго зуба. Имея ось симметрии не трудно построить в торой зуб.
Строим третий зуб второго колеса аналогично построению зуба.
Методика построения первого зуба шестерни аналогична методике построения первого зуба колеса. Только на равные части нужно поделить отрезок РА.
Строим второй и третий зуб шестерни откладывая от осевой линии первого зуба величину углового шага определяемого по формуле:
Величину углового шага строим по значению тангенса угла.
Определяем рабочие участки профилей зубьев. Радиусом равным отрезку О2b из центра О2 проводим дугу до пересечения с боковым профилем зуба. Точка пересечения является концом рабочего участка профиля зуба большого колеса. Рабочий участок выделим штриховкой. Аналогично определяем рабочий участок профиля зуба шестерни.
Определяем дугу зацепления одного из колес (второго).
Изображаем боковой профиль зуба (показан штриховыми линиями) в начале и в конце активной линии зацепления т.е. проходящий через точки a и b. Дуга cd начальной окружности отсеченная боковым профилем является дугой зацепления.
6 Определение коэффициента перекрытия
При указанном направлении вращения колес в момент начала зацепления профиль зуба колеса 2 занимает положение I. Профиль зуба пересекает начальную (делительную) окружность в точке с и основную окружность в точке е.
В момент конца зацепления той же пары зубьев профиль зуба колеса 2 находится в положении II. Профиль зуба в положении II пересекает начальную окружность в точке d и основную в точке l.
Дуга cd есть дуга начальной окружности которую проходит точка профиля зуба от начала зацепления одной пары зубьев в точке а до конца зацепления этой же зубьев в точке b.
Дуга - дуга зацепления.
Отношение дуги зацепления к величине окружного шага называется коэффициентом перекрытия :
Коэффициент перекрытия характеризует плавность зацепления. Он показывает среднее количество пар зубьев находящихся одновременно в зацеплении.
Активный участок линии зацепления ab равен дуге проходимой зубом за время зацепления по основной окружности (по свойству эвольвенты).
Дуги же проходимые зубом по различным окружностям пропорциональны радиусам. Поэтому можно записать:
- по свойству эвольвенты
Подставляя это значение в формулу для определения коэффициента перекрытия получим
Из треугольников О1Ab и О1AP определим
Подставив в (2) получим:
Подобным же образом находим отрезок aP
Артоболевский И. И. Теория механизмов и машин: Учеб . для втузов. - 4-е изд. перераб. и доп. - М.: Наука 1988. - 640 с.
Федотов Г.Д. Адакин В.А. Задания для курсового проекта по ТММ. Ульяновск ГСХА 2008 52С.
Попов С. А. Тимофеев Г.А. Курсовое проектирование по теории механизмов и машин. - М.: Высшая школа 2003-280 с.
Федотов Г.Д. Краткий курс лекций по теории механизмов и машин. Ульяновск ГСХА 2008 63с.
Федотов Г.Д. Адакин В.А. Практикум по теории механизмов и машин. УГСХА 2008 110с.
Федотов Г.Д. Киреева Н.С. Методические указания по изучению дисциплины и выполнение курсового проекта по ТММ. УГСХА 2006 72с.
TMM 1-2.doc
«Ульяновская государственная сельскохозяйственная академия»
Инженерный факультет
Кафедра технической механики
Расчетно-пояснительная записка к курсовому проекту по ТММ
на тему: «Проектирование и исследование механизма двигателя внутреннего сгорания»
I. Структурный анализ и кинематическое исследование рычажного механизма 3
1 Структурный анализ механизма ..3
2 Синтез механизма ..5
3 Построение схемы и исследование движения звеньев механизма 5
4 Построение планов скоростей .. 6
5 Построение планов ускорений .9
6 Построение кинематических диаграмм 12
II. Силовой расчет механизма 13
1 Определение нагрузок на звенья механизма 13
2 Определение реакций в кинематических парах механизма 15
2.1 Силовой расчет группы звеньев 4 – 5 15
2.2 Силовой расчет группы звеньев 2 – 3 17
2.3 Силовой расчет ведущего звена ..19
3 Определение Ру методом жесткого рычага Н.Е. Жуковского . 20
III. Проектирование кулачкового механизма ..22
1 Задание и данные для расчетов .. 22
2 Построение диаграмм движения толкателя .. 23
3 Определение минимального радиуса профиля кулачка ..25
4 Построение профиля кулачка .26
IV. Проектирование кинематической схемы планетарного редуктора
и построение картины эвольвентного зацепления зубчатых колёс ..28
1 Описание схемы зубчатого механизма . .28
2 Подбор чисел зубьев планетарного редуктора . 29
3 Построение схемы редуктора . 30
4 Построение картины скоростей и плана угловых скоростей редуктора 31
5 Построение картины эвольвентного зацепления ..32
6 Определение коэффициента перекрытия . .35
I. Структурный анализ и кинематическое исследование рычажного механизма.
1 Структурный анализ механизма
Механизм включает в себя 5 звеньев:
– кривошип 24 – шатун 35 – ползун 0 – стойка.
Всего 5 подвижных звеньев в данном механизме.
Соприкосновение звеньев и их относительное движение образуют кинематическую пару (КП).
(стойка – кривошип) это вращательная КП низшая 5 класс.
(кривошип шатун) это вращательная КП низшая 5 класс.
(кривошип – шатун) это вращательная КП низшая 5 класс.
(шатун – ползун) это вращательная КП низшая 5 класс.
(ползун – стойка) это вращательная КП низшая 5 класс.
Всего 7 кинематических пар в данном механизме.
Определяем степень подвижности механизма по формуле П.Л. Чебышева:
где n=5 – число подвижных звеньев;
p5=7 – число кинематических пар пятого класса;
p4=0 – число кинематических пар четвертого класса.
Определяем класс механизма. Для этого разложим механизм на группы Ассура на начальный механизм (W=1) состоящие из 1-го входного звена и
-й кинематической пары. И простейшие структурные группы (W=0) состоящие из 2-х звеньев и 3-х кинематических пар.
Разложение механизма на группы Ассура и определение класса механизма выполнено согласно классификации Ассура – Артоболевского.
В таблице 1 приведен рычажный механизм V-образного двигателя внутреннего сгорания разложенный на группы Аcсура (при разложении на группы Ассура следует обязательно соблюдать взаимное расположение звеньев).
Структурное исследование механизма
Схема структурной группы
и механизма 1-го класса
Класс механизма определяется наивысшим классом группы Ассура которая входит в состав механизма.
Рассматриваемый механизм 2-го класса.
Формула строения механизма запишется в следующем виде:
На рисунке 1 показана схема рычажного V-образного четырехтактного механизма двигателя внутреннего сгорания.
Кривошип ОА (звено 1) вращается вокруг оси т.О со средней угловой скоростью 1.В то время как т.А кривошипа перемещается из положения А0 в положение А'0 тогда т.В ползун-3 перейдет из положения В0 (верхняя мертвая точка) в положение В'0 (нижняя мертвая точка) т.е. пройдет путь равный S.
Определим длину шатунов:
Из условия известно что длина звена LОА=004 м. Также известны отношение АВОА=4 (отношение длины шатуна к длине кривошипа).
Определим расстояние до центров тяжести шатунов:
Из условия известно AS2=AS4=AB3
LAS2=LAS4=0163=00533 м.
3 Построение схемы и исследование движения
Выбираем масштабный коэффициент кинематической схемы
Определим масштабные длины звеньев механизма:
положение центров тяжести шатунов
В принятом масштабе длин L по заданным размерам звеньев вычерчиваем кинематическую схему механизма.
На чертеже помечаем положение т.О – центра вращения кривошипа и положение неподвижных направляющих ОВ и ОВ'. Проводим траекторию т.А. Это окружность радиуса ОА. Делим траекторию т.А на 12 равных положений получим т.А1 А12. Номеруем точки А в направление 1.
Определим методом засечек положение точек В и В' на их траекториях. Из каждой точки т.А откладываем отрезки равным АВ=АВ'=160 мм. делаем засечку на направляющих ОВ и ОВ' получим т.В1 В12 и В'1 В'12.
4 Построение планов скоростей
Определение линейных скоростей точек механизма начинаем с входного звена 1(ОА). Так модуль скорости точки А кривошипа совершающего вращательное движение определим из выражения:
А= 1·LОА=430·004=172 мс
Направлен вектор скорости перпендикулярно кривошипу ОА в сторону его вращения.
Далее определяем скорости точек структурной группы. Для этого составляем систему векторных уравнений связывающих искомую скорость точки с известными скоростями точек.
Из уравнения (1) известно что вектор скорости направлен перпендикулярно кривошипу ОА в сторону его вращения и вращается с угловой скоростью 1 вектор скорости направлен перпендикулярно ВА.
Из уравнения (2) известно что вектор скорости направлен перпендикулярно кривошипу ОА в сторону его вращения и вращается с угловой скоростью 1 вектор скорости направлен перпендикулярно В'А.
В уравнениях четыре неизвестных параметра которые могут быть определены в результате графического решения векторных уравнений т.е. путем построения планов скоростей.
Изображая скорость точки А отрезком Ра=86 мм определим значение масштабного коэффициента:
Последовательность графоаналитического способа решения задачи рассмотрим на примере построения плана скоростей для второго положения механизма.
На чертеже выбираем т. Р – полюс плана скоростей проводим вектор Ра2 перпендикулярно кривошипу ОА2 в сторону его вращения. Конец вектора обозначим а2.
Согласно уравнению (1) через точку а2 проводим линию действия - перпендикулярно В2А2 до пересечения линии действия - параллельно к ОВ2 получим т. b2.
Согласно уравнению (2) через точку а2 проводим линию действия - перпендикулярно В'2А2 до пересечения линии действия - параллельно к ОВ'2 получим т. b'2.
Для определения скалярной величины любого из полученных векторов достаточно умножить соответствующий отрезок в мм на масштабный коэффициент плана скоростей:
Для нахождения скоростей точек S2 и S4 – центров тяжести звеньев 2 и 4 воспользуемся теоремой подобия:
Скорости всех звеньев механизма и их отрезки в миллиметрах представлены в таблице 2.
Планы скоростей для остальных положений механизма строим аналогично.
Угловые скорости звеньев определяются с помощью построенных планов скоростей.
Угловая скорость первого звена задана в исходных данных и равняется
Модуль угловой скорости второго звена для второго положения механизма можно найти по формуле:
Абсолютные и относительные скорости точек звеньев
механизма и их отрезки в миллиметрах
Значение угловых скоростей звеньев 2 и 4 представлены в таблице 3.
Таблица 3. Значение угловых скоростей шатуна АВ и АВ' в с-1
Направление угловой скорости звена АВ определяется следующим образом. Переносим мысленно вектор с плана скоростей в точку В шатуна 2 и наблюдаем направление поворота этого звена вокруг точки А.Во втором положении механизма угловая скорость 2 направлена против часовой стрелки. Аналогично получим направление угловой скорости 4 звена 4 оно будет направлено против часовой стрелки.
5 Построение планов ускорений
Построение планов ускорений рассмотрим для второго положения механизма. Так как кривошип ОА вращается с постоянной угловой скоростью то точка А будет иметь только нормальное ускорение величина которого равна:
а направленно оно параллельно звену ОА от точки А к точке О.
Определяем масштабный коэффициент плана ускорений:
Последовательность построения плана ускорений рассмотрим для второго положения механизма.
Из произвольной точки – полюса плана ускорений откладываем вектор параллельно звену ОА от точки А к точке О.
Для построения точки В и В' составим и решим графические уравнения:
Ускорение направлено параллельно ОВ проведенное через полюс .
Ускорение направлено параллельно ОВ' проведенное через полюс .
Определим модули нормальных ускорений:
Нормальное ускорение направлено параллельно звену АВ от точки В к точке А (центру вращения).
Нормальное ускорение направлено параллельно звену АВ' от точки В' к точке А.
Определяем длину отрезков в миллиметрах изображающие нормальные ускорения:
Тангенциальные составляющие ускорений и по абсолютной величине неизвестны но известны по направлению. Они направлены перпендикулярно соответствующим звеньям механизма АВ и А'В или перпендикулярно нормальным составляющим.
Согласно первому векторному уравнению через точку а плана ускорений проводим прямую направленную вдоль звена АВ в направлении от точки В к точке А и на ней откладываем отрезок anb=14 мм величина которого в масштабе соответствует величине вектора нормальной составляющей ускорения .
Через точку nb перпендикулярно звену АВ (или тоже самое что перпендикулярно ) проводим направление вектора тангенциального ускорения до пересечения с линей действия вектора (параллельно к ОВ проведенный через полюс ). Получим точку В.
Согласно второму векторному уравнению через точку а плана ускорений проводим прямую направленную вдоль звена АВ' в направлении от точки В' к точке А и на ней откладываем отрезок anb'=484 мм. величина которого в масштабе соответствует величине вектора нормальной составляющей ускорения .
Через точку nb' перпендикулярно звену АВ' проводим направление вектора тангенциального ускорения до пересечения с линей действия вектора (параллельно к ОВ' проведенный через полюс ). Получим точку В'.
Для определения ускорений точек S2 и S4 – центров тяжести звена 2 и звена 4 воспользуемся теоремой подобия. Замеряем отрезки и
Откладываем полученные значения отрезков от точки а по векторам и получим точки S2 и S4 соединяем их с полюсом .
Определяем действительное значение ускорений:
План ускорений для положений механизма 1 и 10 строим аналогично. Ускорение всех точек звеньев механизма и их отрезки сводим в таблицу 4.
Таблицу 4. Абсолютные и относительные ускорение точек
звеньев механизма и их отрезки в миллиметрах
Угловые ускорения звеньев определяются на основе построенных планов ускорений.
Входное звено 1 вращается равномерно с постоянной угловой скоростью. Следовательно его угловое ускорение равно нулю:
Модули угловых ускорений второго и четвертого звеньев для второго положения механизма можно найти по формулам:
Таблица 5. Значение угловых ускорений шатуна АВ и АВ' в с-2
Определим направления угловых ускорений звеньев 2 и 4. Чтобы определить направление углового ускорения 2 необходимо вектор относительного тангенциального ускорения с плана ускорений (на плане ему соответствует вектор ) перенести в точку В механизма а точку А условно закрепить. Вектор будет вращать точку В звена 2 относительно А по часовой стрелки а следовательно и угловое ускорение будет направленно по часовой стрелке.
Угловое ускорение звена 4 будет направленно против часовой стрелки т.к. вектор будет вращать точку В звена 2 относительно А против часовой стрелки.
6 Построение диаграммы перемещения S(t) скорости (t) и ускорения a(t) точки В ползуна 3
По оси t откладываем отрезок L=240 мм. Данный отрезок соответствует времени оборота кривошипа.
Делим отрезок L на 12 равных частей и получаем точки 01 1112. Для построения диаграммы S(t) нужно из точек 01 1112 отложить ординаты соответствующие перемещению точки В. Полученные точки 1' 11' соединяем плавной кривой.
Для построения диаграммы (t) воспользуемся методом дифференцирования (метод хорд). Криволинейные участки графика S(t) соответствующие интервалам оси t заменяем хордами. Выбираем произвольной длинны полюсное расстояние Н1=60 мм. Из полюса P1 проводим лучи параллельные соответствующий хордам участков заданной кривой до пересечения с осью ординат. Из середины интервалов проводим перпендикуляры к оси абсцисс до пересечения с соответствующими линиями. Полученные точки 1'' 11'' соединяем плавной кривой.
Диаграмму a(t) построим аналогичным способом (методом хорд) путем дифференцирования диаграммы (t). Выбираем произвольной длинны полюсное расстояние Н2=50 мм.
II. Силовой (кинетостатический) расчет механизма.
Для кинетостатического исследования механизма строим кинематическую схему механизма во втором положении (перечерчиваем с первого листа). Масштабный коэффициент схемы
перечерчиваем с первого листа план скоростей в масштабе
и план ускорений в масштабе
1 Определение нагрузок на звенья механизма
Определим силы инерции и моменты от пар сил инерции действующие на звенья механизма:
Силы инерции РИ2 и РИ4 направляем в стороны противоположные соответствующим ускорениям и . Момент МИ2 и МИ4 прикладываем к звеньям 2 и 4 противоположно условным ускорениям 2 и 4.
Заданными внешними силами являются также силы веса звеньев которые определяются по формуле:
G2=m2·g =035·10=35 Н
G4=m4·g =035·10=35 Н
Векторы сил тяжести прикладываем в центрах тяжести звеньев и направим вертикально вниз.
Для удобства расчетов силу инерции РИ2 и момент МИ2 приведем к одной результирующей силе а также приведем к одной результирующей силе момент МИ4 и силу инерции РИ4. Для этого вычислим плечи сил h2 и h4 по формулам
Силы давления газов на поршень:
Для поршней 3 и 5 строим диаграммы в масштабе
Поршень 3 совершает расширение и J3=97 мм а поршень 5 совершает выхлоп следовательно давление в цилиндре равно атмосферному. Определим давление в цилиндре 3:
Определим давление газов на поршень 3:
Прикладываем силу в точку В звена 3 в направлении скорости .
Определим давление газов на поршень 5:
2 Определение реакций в кинематических парах механизма
Порядок силового расчета рассмотрим для второго положения механизма.
Силовой (кинетостатический) расчет начинается с наиболее удалённой от входного звена группы Ассура т.е. производится в порядке обратном кинематическому расчету и заключается в последовательном рассмотрении условий равновесия (по принципу Даламбера) всех входящих в механизм групп.
2.1 Группа звеньев 4 – 5
Изображаем группу звеньев 4 – 5 в масштабе L=0001 ммм.
Рассмотрим силы действующие на группу звеньев 4 – 5.
В центре тяжести звеньев S4 и S5 приложены силы веса G4 G5 направлены вертикально вниз.
Силу инерции PИ4 прикладываем в точке Т4 и направляем противоположно вектору ускорения центра тяжести звена 4. Точку Т4 находим откладывая от направления линии действия силы инерции PИ4 приложенной в центре тяжести S4 плечо h4 таким образом чтобы сила инерции PИ4 приложенная в точке Т4 создавала момент относительно S4 того же направления что и момент MИ4.
Силу инерции PИ5 прикладываем в точке Т5 и направляем противоположно вектору ускорения центра тяжести звена 4.
Освобожденные связи заменяем реакциями.
В шарнире А со стороны звена 1 действуют реакции связи. Обозначим её R14. Она не известна ни по величине ни по направлению. Для упрощения решения задачи разложим эту реакцию на две составляющие: нормальную направленную вдоль линии AB' звена 4 и касательную направленную перпендикулярно линии AB' звена 4.
Под действием всех внешних сил сил инерции и реакций связей структурная группа находится в равновесии. Исходя из условий равновесия составим уравнение моментов всех сил действующих на группу относительно точки В' (при этом для звена 4) и определим касательную составляющую силы .
Будем считать моменты действующие против часовой стрелки положительными а по часовой – отрицательными. Плечи сил определяются непосредственным замером на чертеже в миллиметрах и обозначаются буквой h с индексом соответствующей силы.
Момент сил относительно точки В' образуют силы Исходя из условия равновесия звена 4 запишем:
Составим векторное уравнение равновесия сил действующих на группу 4 – 5 ().
Полученное векторное уравнение имеет два неизвестных и может быть легко решено графическим методом путем построения многоугольника сил. Равенство говорит о том что этот многоугольник сил должен быть замкнутым.
Построение плана сил начинаем с реакции которую откладываем из произвольной точки «1» в масштабе Р удобном для построения.
Принимаем масштабный коэффициент плана сил равным
Тогда масштабные (на чертеже) отрезки сил в миллиметрах определятся как частное от деления абсолютной величины силы на масштабный коэффициент:
Затем строим по порядку силы геометрически складывая их. Из конца построения точки «8» проводим линию действия реакции и соединяем с точкой «1».
Определим реакцию в шарнире B' – R54. Для этого рассмотрим условие равновесия четвертого звена:
Воспользуемся планов сил для звеньев 4 – 5 строим вектор R54.
2.2 Группа звеньев 2 – 3
Изображаем группу звеньев 2 – 3 в масштабе L=0001 ммм.
Рассмотрим силы действующие на группу звеньев 2 – 3.
В центре тяжести звеньев S2 и S3 приложены силы веса G2 G3 направлены вертикально вниз.
Силу инерции PИ2 прикладываем в точке Т2 и направляем противоположно вектору ускорения центра тяжести звена 2. Точку Т2 находим откладывая от направления линии действия силы инерции PИ2 приложенной в центре тяжести S2 плечо h2 таким образом чтобы сила инерции PИ2 приложенная в точке Т2 создавала момент относительно S2 того же направления что и момент MИ2.
Силу инерции PИ3 прикладываем в точке Т3 и направляем противоположно вектору ускорения центра тяжести звена 2.
В шарнире А со стороны звена 1 действуют реакции связи. Обозначим её R12. Она не известна ни по величине ни по направлению. Для упрощения решения задачи разложим эту реакцию на две составляющие: нормальную направленную вдоль линии AB звена 2 и касательную направленную перпендикулярно линии AB звена 2.
Под действием всех внешних сил сил инерции и реакций связей структурная группа находится в равновесии. Исходя из условий равновесия составим уравнение моментов всех сил действующих на группу относительно точки В (при этом для звена 2) и определим касательную составляющую силы .
Момент сил относительно точки В образуют силы Исходя из условия равновесия звена 2 запишем:
Составим векторное уравнение равновесия сил действующих на группу 2 – 3 ().
Определим реакцию в шарнире B – R32. Для этого рассмотрим условие равновесия второго звена:
Воспользуемся планов сил для звеньев 2 – 3 строим вектор R32.
2.3 Силовой расчёт входного звена механизма
Вычерчиваем входное звено 1 в масштабе L=0001 ммм с соблюдением заданного положения показав все действующие силы. Рассмотрим эти силы. В точке А на звено 1 со стороны звена 2 действует сила (приведённая сила) равная по величине но противоположная по направлению. Также в точке А на звено 1 со стороны звена 4 действует сила (приведённая сила) равная по величине но противоположная по направлению.
Силы и были определены из планов сил групп 2 – 3 и 4 – 5 равны по абсолютной величине:
Сила инерции РИ1=0 так как центр тяжести звена 1 – точка S1 лежит на оси вращения звена 1 (точка О).
Силой веса звена 1 G1 пренебрегаем.
Момент от силы инерции МИ1=0 так как 1=0.
Под действием реакций и звено 1 в равновесии не находится. Найдём уравновешивающую силу из условия равновесия входного звена.
Исходя из условия равновесия входного звена запишем:
Для определения реакции в шарнире О - составляем векторное уравнение равновесия сил действующих на входное звено 1:
Строим план сил входного звена в масштабе:
Из полученного плана сил видим что вектор изображает в масштабе реакцию R01. Определим величину реакции R01:
3 Определение уравновешивающей силы методом жесткого рычага Н.Е. Жуковского. Проверка кинетостатического исследования механизма
В практических инженерных расчетах часто требуется определить уравновешивающую силу без определения реакций в кинематических парах. Тогда целесообразно с целью упрощения расчетов воспользоваться теоремой профессора Н.Е. Жуковского о жестком рычаге.
Основной смысл теоремы заключается в том что алгебраическая сумма моментов всех внешних сил действующих в механизме и приложенных в соответствующих точках повёрнутого на 90 градусов в любую сторону плана скоростей относительно полюса плана равна моменту уравновешивающей силы или иначе сумма моментов всех сил относительно полюса будет равна нулю. Сам же план скоростей рассматривается здесь как жесткий рычаг с опорой в полюсе Р. Действительно если мы составим уравнение моментов то уравновешивающая сила РУ будет единственной неизвестной в этой системе.
Как видно определив уравновешивающую силу методом жёсткого рычага мы тем самым сможем одновременно проверить правильность проведенного нами кинетостатического расчета.
Определим величину уравновешивающей силы методом жесткого рычага Н.Е. Жуковского и сравним её с величиной силы (или момента) полученной в процессе кинетостатического расчёта.
Повернём план скоростей на 90 градусов против часовой стрелки (можно повернуть и по часовой стрелке) и построим его в масштабе =02 Нмм.
Перенесем все внешние силы действующие на механизм параллельно самим себе на план скоростей в те точки которые соответствуют точкам приложения сил на схеме механизма.
К внешним силам относятся веса звеньев – G2 G3 G4 G5 главные векторы сил инерции – РИ2 РИ3 РИ4 РИ5 и величины сил давление газов на поршень – F3 F5.
Составим уравнение моментов всех сил (внешних) относительно точки
Р - полюса плана скоростей. Плечи всех сил относительно полюса замеряем непосредственно на чертеже независимо от масштаба в котором построен повернутый план скоростей подставляя их значения в уравнение в миллиметрах. Обозначим величину плеча сил на рычаге Н.Е. Жуковского через h с индексом соответствующей силы.
Искомое уравнение будет иметь вид:
Сравним значение уравновешивающих сил полученных методом планов сил и методом жесткого рычага Н.Е. Жуковского. Определим процент расхождения в расчетах:
Допустимая погрешность не должна выходить за пределы точности инженерных расчетов которая составляет 6-7%.
ТММ - Лист 2.cdw

План сил звена 2 - 3
План сил входного звена
ТММ - Лист 4.cdw

План угловых скоростей
Картина эвольвентного зацепления М 4:1
ТММ - Лист 1.cdw

ТММ - Лист 3.cdw

Приоектирование кулачкового
Рекомендуемые чертежи
- 24.01.2023