Проект системы управления РТК штамповки




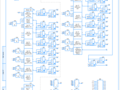
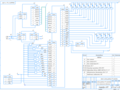
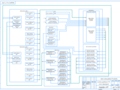

- Добавлен: 24.01.2023
- Размер: 680 KB
- Закачек: 3
Описание
Состав проекта
![]() |
![]() ![]() ![]() ![]() |
![]() ![]() ![]() ![]() |
![]() |
![]() ![]() ![]() ![]() |
![]() |
![]() ![]() ![]() |
![]() ![]() ![]() ![]() |
Дополнительная информация
схема элект подкл.cdw

Магнитный пускатель КМИ-10911
Индуктивный датчик NBB03-8GM16-E2-C-V1
Автоматический выключатель ВА47-29
Межблочный соединитель МБС
Система управления РТК штамповки.
Схема электрическая подключения
Проект системы управления РТК штамповки
Земеров Е.Л. гр. Т-4135С
Циклограмма.cdw

Поворот ПР1 к прессу 1
Поворот ПР1 к накопителю 2
Поворот ПР2 к накопителю 2
Поворот ПР2 к прессу 2
Поворот ПР2 к накопителю 3
Проект системы управления РТК штамповки
Земеров Е.Л. гр. Т-4135С
Программа.cdw

Проект системы управления РТК штамповки
Земеров Е.Л. гр. Т-4135С
Проект системы управления РТК штамповки.docx
РОССИЙСКОЙ ФЕДЕРАЦИИ
Федеральное агентство по образованию
Кафедра автоматизации производственных процессов
Проект системы управления РТК штамповки
расчётно-пояснительная записка
Дисциплина: Автоматизация технологических процессов и производств
Студент: Земеров Е.Л.
Руководитель: к.т.н. доцент Сбродов Н.Б.
В настоящей курсовой работе производиться разработка системы управления РТК штамповки.
Разработка системы управления включает в себя разработку структуры системы управления выбор технических средств автоматизации системы управления разработку электрической схемы подключения разработку программы управления. Система управления РТК штамповки разработана на основе микроконтроллера «Ремиконт Р-130» написана управляющая программа на языке функционально-блоковых диаграмм.
В данной курсовой работе использованы следующие технические решения:
) Загрузочно-разгрузочные операции внутри комплекса осуществляются с помощью промышленного робота.
) Входные и выходные цепи питания промышленного контроллера гальванически разделены с помощью применения двух источников питания.
) В качестве дискретных датчиков положения применены датчики индуктивного типа обладающими высокими эксплуатационными характеристиками надежностью низкой стоимостью по сравнению с остальными типами датчиков положения.
В состав курсовой работы входят расчётно-пояснительная записка и графическая часть.
Обоснование необходимости автоматизации РТК штамповки5
1 Характеристика автоматизируемого технологического объекта5
2 Анализ путей автоматизации7
3. Разработка технического задания.8
3.1 Наименование и область применения системы управления.8
3.2 Основание для разработки.9
3.3 Цель и назначение разработки.9
3.4 Источники разработки9
3.5 Режимы работы объекта9
3.6 Условия эксплуатации системы управления10
3.7 Технические требования10
3.8 Стадии и этапы разработки10
3.9 Порядок контроля и приемки11
Разработка системы управления РТК11
1 Разработка структуры системы управления11
2 Проектирование подсистемы логико-программного управления дискретным технологическим процессом13
2.1 Выбор технической реализации элементов подсистемы13
2.2 Разработка алгоритма управления25
2.3 Разработка программы управления28
Роботы выполняют на сегодняшний день опасную монотонную а значит самую тяжелую работу; промышленные роботы могут поднимать и переносить тяжелые объекты могут использоваться в агрессивной окружающей среде.
Промышленные роботы и построенные на их основе роботизированные технологические комплексы (РТК) являются перспективным средством комплексной автоматизации производственных процессов. Применение РТК позволяет значительно повысить производительность оборудования гибкость производства сократить численность рабочих а значит снизить долю ручного труда и существенно повысить качество и надёжность выпускаемой продукции. Для этого необходимо внедрение в РТК некоторых технических средств автоматизации.
Среди технических средств автоматизации в последнее время широкое распространение получили промышленные контроллеры. Среди данных устройств выделяют две группы: программируемые логические контроллеры и PC-контроллеры.
Целью курсового проекта является разработка системы управления РТК штамповки. Актуальность разработки данной системы управления состоит в том что она позволит снизить прежде всего долю ручного труда что позволит повысить качество выпускаемой продукции и экономические затраты так как РТК внедряется на базе существующих прессов.
Обоснование необходимости автоматизации РТК штамповки
1 Характеристика автоматизируемого технологического объекта
В состав РТК входят (рисунок 1): два пресса два промышленных робота (ПР1 и ПР2) и три накопителя. Обрабатываемые детали размещаются в накопителях. Загрузочно-разгрузочные операции выполняются ПР.
В общем случае отдельными элементами (тактами) технологического цикла работы РТК являются:
Поворот ПР1 к накопителю 1.
Поворот ПР1 к прессу 1.
Поворот ПР1 к накопителю 2.
Поворот ПР2 к накопителю 2.
Поворот ПР2 к прессу 2.
Поворот ПР2 к накопителю 3.
Выдвижение руки ПР1.
Задвижение руки ПР1.
Выдвижение руки ПР2.
Задвижение руки ПР2.
Рабочий ход пресса 1.
Рабочий ход пресса 2.
Рисунок 1 – РТК прессования деталей
Промышленный робот 1
Промышленный робот 2
ПР1 осуществляет захват детали (см. табл. 3) находящейся в накопителе 1 и перемещение ее в рабочую зону пресса 1 (такты 1-4). Выполняются разжим схвата ПР1 (такт 5) и задвижение руки ПР1 (такт 6). Затем выполняется рабочий ход пресса (такт 7) по окончании которого ПР1 перемещает обрабатываемую деталь в накопитель 2 (такты 8-12). ПР1 осуществляет поворот к накопителю 1 одновременно ПР2 – к накопителю 2 (такт 13). ПР1 и ПР2 параллельно выполняют захват деталей из накопителей 1 и 2 соответственно и их перемещение в рабочие зоны прессов 1 и 2 (такты 14-18). После выполнения прессами рабочих ходов (такт 19) ПР1 и ПР2 загружают детали в накопители 2 и 3 соответственно (такты 20-24). После этого цикл работы РТК повторяется начиная с такта 13.
Контроль зажимов (разжимов) схватов ПР1 и ПР2 осуществляются с помощью таймера по времени 15с.
При автоматизации данного технологического объекта с позиции экономики предприятия решаются следующие задачи:
) Высвобождается рабочая сила посредством замены ручных операций зажимаразжима детали на станке и переноса детали вдоль рабочей зоны автоматической операциями;
) Повышается производительность труда т.к. монотонный труд выполняет не человек а автоматизированное оборудование «не знающее» физической усталости и утомления;
) Повышается точность выполнения операций.
Определим вид автоматического устройства управления которое будет управлять объектом.
Данный объект управления – сложный процесс состоящий из отдельных операций. В этом случае возникает задача управления дискретным процессом т.е. связать эти элементы в единую систему обеспечить определенную последовательность работы переход из одного режима в другой при определенных условиях. Вследствие этого в качестве устройства управления дискретным технологическим процессом применяем программируемый логический контроллер.
2 Анализ путей автоматизации
Необходимость автоматизации объясняется следующим:
)Повышением производительности оборудования
)Снижением доли ручного труда
)Сокращением длительности цикла штамповки
)Длительный срок старения прессового оборудования позволяет внедрять РТК на базе существующих прессов что в свою очередь позволяет снизить экономические затраты.
Автоматизация РТК может происходить как на базе прессового оборудования автоматизации (например УЧПУ) так и отдельно от этой базы (например при помощи микроконтроллера).
В первом случае когда система управления РТК связана с системой управления станка непосредственно (система управления роботом внедрена в УЧПУ) задача управления усложняется т.к. количество входных и выходных сигналов УЧПУ заведомо уменьшено (УЧПУ контролирует станок а значит использует входные выходные линии) а так же из-за усложнения программного обеспечения станка что приводит к расширению памяти УЧПУ увеличению стоимости УЧПУ усложнению процесса обработки и как правило к увеличению времени обработки.
Во втором случае используется локальная система управления построенная на промышленном контроллере расположенном в электрошкафу и связанном со всеми внешними датчиками и механизмами. Преимуществом промышленного контроллера является то что это устройство может быть расположено отдельно от станка что обеспечивает дополнительную безопасность в работе оператора и обеспечивает более гибкую систему управления.
3. Разработка технического задания.
3.1 Наименование и область применения системы управления.
Система управления РТК штамповки применяется в кузнечно-штамповом производстве для автоматизации процессов холодной объёмной и листовой штамповки а также в качестве составной части более сложной гибкой производственной системы.
3.2 Основание для разработки.
Основанием для разработки является задание выданное преподавателем для специальности 210200 «Автоматизация технологических процессов и производств» кафедры АПП и соответствующее задание на курсовой проект.
3.3 Цель и назначение разработки.
Целью разработки является повышение производительности оборудования снижение доли человеческого труда и экономических затрат.
Назначение разработки состоит в создании системы управления РТК штамповки на базе микроконтроллера отвечающего за исполнительные механизмы за принятие сигналов с датчиков и пульта оператора.
3.4 Источники разработки
Основными источниками разработки являются:
) Сбродов Н.Б. Применение программируемого контроллера Ремиконт Р-130 в системах управления. Часть 2. Организация ввода-вывода информации: Методические указания к курсовому проектированию по курсу “Системы автоматизации и управления” для студентов специальности 210200. – Курган: Изд-во КГУ 2000.
) Сбродов Н.Б. Применение программируемого контроллера Ремиконт Р-130 в системах управления. Часть 1. Функциональные возможности и архитектура: Методические указания к курсовому проектированию для студентов направления 550200. – Курган: Изд-во КГУ 1998.
3.5 Режимы работы объекта
Предусмотрено два режима работы которые можно переключать с помощью пульта управления. Первый режим – последовательное выполнение цикла штамповки (кнопка “Пуск” на пульте управления). Важно чтобы в это же время от другой системы управления пришел сигнал разрешение цикла (РЦ) только в этом случае начнётся технологический процесс. Работа технологического объекта будет остановлена если сигнал РЦ будет отсутствовать в момент начала нового цикла. Второй режим – остановка выполнения цикла штамповки (кнопка “Стоп” на пульте управления). Также переход на второй режим работы может быть осуществлён программно при неисправности какого-либо механизма РТК штамповки.
3.6 Условия эксплуатации системы управления
Диапазон рабочих температур: 0 50°С.
Влажность: от 40 до 75%.
Атмосферное давление: 860 1080 КПа.
3.7 Технические требования
В состав устройства управления должен входить управляющий контроллер. Управляющий контроллер монтировать внутри электрошкафа с использованием DIN-рейки. Место где устанавливается контроллер должно соответствовать всем требованиям техники безопасности.
Проводной монтаж должен быть выполнен при помощи цельных или крученых проводов сечением не менее 15 мм2. При использовании крученого провода соединение выполнить при помощи обжимного наконечника. Обмотки реле постоянного тока должны быть зашунтированы диодами. Безопасность должна обеспечиваться отсутствием на схеме неизолированных электрически опасных для человека цепей.
3.8 Стадии и этапы разработки
Разработку устройства можно разбить на следующие этапы:
- получение задания на разработку курсового проекта;
- анализ путей модернизации системы управления;
- разработка структуры системы управления;
- выбор устройства управления и других технических средств системы управления;
- разработка электрической схемы подключения устройств;
- составление программы управления;
- сведение расчетов и описаний в расчетно-пояснительную записку.
3.9 Порядок контроля и приемки
Текущий контроль проекта осуществляется руководителем проекта на каждом этапе его разработки. Прием проекта должен осуществляться комиссией в составе которой будет не менее двух человек. При этом следует предоставить расчетно-пояснительную записку и листы графической части (схему планировки РТК циклограмму работы системы управления РТК структурную схему программу управления электрическую схему подключения датчиков и исполнительных устройств).
Разработка системы управления РТК
1 Разработка структуры системы управления
Разработка структурной схемы автоматизации объекта является основой для разработки всей системы. На структурной схеме должны быть указаны взаимосвязи между управляющими устройствами и объектами управления расположения объектов автоматизации а так же необходимо указать какие параметры необходимо контролировать для получения информации.
В данном курсовом проекте устройством управления является промышленный микроконтроллер а объектом управления является промышленный робот.
Промышленный контроллер должен управлять дискретно включениемотключением исполнительных устройств. Контроллер должен иметь модуль дискретного вывода для этой цели.
Модуль дискретного вывода должен выдавать управляющие сигналы на магнитные пускатели поворота промышленных роботов влево на магнитный пускатель поворота промышленного робота вправо на магнитный пускатель движения пресса на магнитные пускатели движения накопителей 1 и 3 гидропривод выдвижения руки промышленного робота 1 и 2 гидропривод задвижения руки промышленного робота 1 и 2 гидропривод зажима детали схватом руки ПР1 и ПР2 гидропривод разжима детали схватом руки ПР1 и ПР2.
Управляющее устройство должно также получать информацию о ходе технологического процесса. Для этой цели служит модуль дискретного ввода куда должны приходить сигналы с датчиков кнопок и т.д. На модуль дискретного ввода должны приходить сигналы с датчиков положения BQ1 BQ2 BQ3 BQ4 BQ5 BQ6 BQ7 BQ8 BQ9 BQ10 BQ11 с кнопок запуска цикла SB1 от устройства управления прессом от другой системы управления.
Промышленный контроллер и блок магнитных пускателей размещаем в электрошкафу с использованием DIN-рейки. Кнопку запуска цикла SB1 и стопа SB2 размещаем на пульте оператора. Промышленный робот будет содержать электроприводы поворота ПР1 и ПР2 гидроприводы выдвижения рук ПР1 и ПР2 гидроприводы задвижения рук ПР1 и ПР2 гидроприводы зажима детали схватом руки ПР1 и ПР2 гидроприводы разжима детали схватом руки ПР1 и ПР2 датчик наличия детали на накопителе 1 BQ1 датчик положения ПР1 BQ2 BQ3 BQ4 датчик выдвижения руки BQ5 датчик задвижения руки ПР1 BQ6 датчик разжима детали схватом руки ПР1 BQ7 датчик наличия детали на накопителе 3 BQ8 датчик положения ПР2 BQ9 BQ10 BQ11 датчик выдвижения руки BQ12 датчик задвижения руки ПР2 BQ13 датчик разжима детали схватом руки ПР2 BQ14.
Структурная схема система управления приведена в графической части лист 1. Как видно в структурной схеме можно выделить информационные устройства (датчики) и исполнительные устройства (магнитные пускатели и электродвигатели). Необходимо осуществить правильный и рациональный выбор всех устройств.
2 Проектирование подсистемы логико-программного управления дискретным технологическим процессом
2.1 Выбор технической реализации элементов подсистемы
Быстроменяющаяся экономическая ситуация и большое разнообразие задач встающих перед предприятиями в современных рыночных условиях изменили старые взгляды на систему автоматизации производства. Сегодня от такой системы требуется уже не только следить за ситуацией и управлять технологическим процессом. Крайне необходимо иметь доступ к постоянному источнику информации целым группам людей и получать информацию в удобной форме чтобы принимать конструктивные решения в вопросах управления в целом.
Современный рынок средств автоматизации предлагает широкий спектр технических и программных средств для построения надежных и удобных в эксплуатации систем.
2.1.1 Путевые выключатели
Путевые выключатели являются важным элементом схем управления манипуляторами и используются для определения положения манипулятора. Для управления манипуляторами применяются только бесконтактные путевые выключатели.
Бесконтактные датчики положения не имеют физической связи с объектами. О присутствии тела они судят с помощью того или иного принципа обнаружения реализуемого в соответствующих преобразователях. Т.к. объект управления (промышленный робот) состоит из металла то следует применить индуктивный датчик положения. Индуктивные датчики по сравнению с другими типами датчиков положения обладают более высокими эксплуатационными характеристиками надежностью и что весьма существенно низкой стоимостью.
В данной курсовой работе для получения информации о положении рабочих органов должны быть использованы 14 путевых выключателей.
В качестве путевых выключателей выбираем датчики положения серии NBB03-8GM16-E2-C-V1 фирмы PEPPERL+FUCHS. Данные путевые выключатели имеют следующие индивидуальные характеристики:
- диапазон срабатывания: 3 мм;
- диаметр корпуса: 8 мм;
- длина датчика: 16 мм.
Все датчики встраиваемые устойчивые к магнитным полям выдерживают вибрацию частотой 10 55 Гц (при амплитуде 1 мм) имеют максимальная величина времени задержки включения: 300 мс. Диапазон рабочих температур данных датчиков: от -25ºС +70ºС.
2.1.2 Управляющий контроллер
В данном курсовом проекте необходимо чтобы управляющий контроллер удовлетворял следующим требованиям:
) Количество входов: 14 количество выходов: 9;
) Контроллер должен быть программируемым логическим;
) Контроллер должен иметь возможность подключения к выходам как нагрузки переменного тока так и нагрузки постоянного тока;
) Контроллер должен быть с жидкокристаллическим дисплеем и кнопками управления;
Отечественный контроллер из серии Ремиконт Р-130 (рисунок 4) удовлетворяет всем вышеперечисленным требованиям. Ремиконт Р-130 – это компактный малоканальный многофункциональный микропроцессорный контроллер предназначенный для автоматического регулирования и логического управления технологическими процессами. Удобство использования этого контроллера является следствием простоты его программирования.
Рисунок 1 – общий вид контроллера Ремиконт Р-130
Ремиконт Р-130 имеет проектную компоновку которая позволяет пользователю выбрать нужный набор модулей и блоков согласно числу и виду входных-выходных сигналов. В контроллер встроены развитые средства самодиагностики сигнализации и идентификации неисправностей в том числе при отказе комплектующих изделий выходе сигналов за допустимые границы сбое в ОЗУ нарушении обмена по кольцевой сети и т.п. Для дистанционной сигнализации об отказе предусмотрены специальные дискретные выходы.
Ниже приведем основные характеристики контроллера. Программируемый логический контроллер Ремиконт Р-130 имеет следующие характеристики:
Аналоговые входные сигналы:
- унифицированные : 0-5 мА (Rb
- термопары: ХЛ ХК ПП ПР ВР;
- разрешающая способность ЦАП: 0025 % (12 разрядов);
- максимальная погрешность АЦП после калибровки: 03 %;
- гальваническая развязка: каждый вход гальванически изолирован от других входов и остальных цепей;
- максимальная нелинейность усилителей для термопар (БУТ-10) и термометров сопротивления (БУС-10): 01 %;
- погрешность АЦП изменения окружающей температуры на 10 градусов Цельсия: максимальное значение - 04 % среднее значение - 02 %;
- максимальная погрешность АЦП при изменении напряжения питания в диапазоне + 10% -10%;
- максимальная погрешность усилителей для термопар (относительно сигнала 10 мВ) и термометров сопротивления (относительно R=10 0м):
при изменении окружающей температуры на 10 градусов Цельсия: 025 %;
при изменении напряжения в диапазоне от +10 до -15 %;
Аналоговые выходные сигналы:
- унифицированные мА: 0-5 (Rh ≤ 2 кОм) 0-20 (Rh ≤ 05кОм) 4-20 (Rh ≤ 05 кОм);
- разрешающая способность ЦАП: 005 % (11 разрядов);
- максимальная погрешность ЦАП после калибровки: 05 %;
- гальваническая развязка: выходы связаны попарно каждая пара изолирована от соседней пары и от остальных цепей;
- максимальная погрешность ЦАП при изменении окружающей температуры на 10 град. Цельсия: 02 %;
- максимальная погрешность ЦАП при изменении напряжения питания от +10 до -10 %;
Дискретные входные сигналы:
- сигнал логического 0: 0-7 В;
- сигнал логической 1: 18-30 В;
- входной ток (при напряжении 24 В): 9 мА;
- гальваническая развязка: входы связаны в группы по 16 входов каждая группа изолирована от других цепей;
Дискретные (импульсные) выходные сигналы:
- транзисторный выход:
- максимальное напряжение коммутации: 40 В;
- максимальный ток нагрузки каждого выхода: 03 А;
- максимальный суммарный ток нагрузки одновременно включенных;
- выходов в пределах одной четверки (с 1 до 4. с 5 по 8 и т.д.): 06 А;
- максимальный суммарный ток нагрузки всех одновременно включенных выходов: 2 А;
- вид нагрузки: активная индуктивная;
- зашита от короткого замыкания в цепи нагрузки: имеется;
- гальваническая развязка: выходы связаны в группы по 16 выходов каждая группа изолирована от других цепей;
- сильноточный релейный выход: тип реле: РПГ-8;
- максимальное напряжение коммутации переменного (действующее значение) или постоянного тока: 220 В;
- максимальный ток нагрузки каждого выхода: 2 А;
- слаботочный релейный выход и аварийный выход: параметры коммутации соответствуют параметрам реле РЭС 54 А.
Общие функциональные параметры:
Максимальное число алгоблоков: 99;
Число алгоритмов в библиотеке: 76;
Время цикла: 02-20 с;
суммирование вычитание: 0;
умножение деление: 001;
извлечение квадратного корня: 01;
Объем памяти: ПЗУ - 32 кбайт ОЗУ - 8 кбайт ППЗУ - 8 кбайт;
Текущее время (таймеры программные задатчики и т.п.) постоянные времени интервалы от 0 до 819 с от 0 до 819 ч.;
Время цикла - от 02 до 2 с.;
Время сохранения информации при отключении питания - 10 лет;
Скорость обмена абонентского канала шлюза по интерфейсной связи ИРПС или RS -232 - 48 кбитс или 96 кбитс.
Чтобы иметь полное представление о контроллере Ремиконт Р-130 его нужно сравнить с другим подобным контроллером. Сравним его с другим подобным контроллером отечественного производства который предложено выбрать в других вариантах данного задания – ПЛК-256. Контроллеры отличаются различным числом входов и выходов. В процессе управления ПЛК-256 осуществляет сбор логическую и арифметическую обработку сигналов в то время как регулирующая модель Ремиконта используется и для решения задач автоматического регулирования. Оба контроллера – и Ремиконт Р-130 и ПЛК-256 просты в программировании составление программ не должно составить труда благодаря простоте и доступности входного языка программирования. Однако принципы по которым составляются программы для этих контроллеров отличаются. На ПЛК-256 программирование осуществляется на языке релейно-контактных схем то есть рабочая программа – это упорядоченная последовательность инструкций. А на Ремиконте процесс программирования сводится к тому что путём последовательного нажатия нескольких клавиш из библиотеки зашитой в постоянной памяти извлекаются нужные алгоритмы эти алгоритмы объединяется в систему заданной конфигурации и в них устанавливаются требуемые параметры настройки. Но и ПЛК-256 также подходит для использования в данной системе управления. Немаловажен тот факт что ПЛК-256 на сегодняшний день морально устарел. Этот и другие факторы говорят нам о том что Ремиконт выглядит более предпочтительным контроллером.
Рассматривая так же Ремиконт Р-130 в сравнении с аналогичным микроконтроллером приходим к выводу что для данных условий Ремиконт Р-130 – оптимальный выбор исходя из ниже следующих условий.
Был проведен сравнительный анализ микроконтроллера Ремиконт Р-130 и микроконтроллера МИК-51. Далее даны характеристики микроконтроллера.
Микропроцессорный программируемый контроллер МИК-51
- Компактный малоканальный многофункциональный высокопроизводительный микропроцессорный контроллер.
- Автоматическое регулирование и логическое управление технологическими процессами
- Построение управляющих и информационных систем автоматизации технологических процессов малого и среднего (по числу входов-выходов) уровня сложности а также построения отдельных локальных и распределенных подсистем сложных АСУТП
- АСУ ТП малой и средней сложности предприятий с непрерывными и дискретными технологическими процессами различных отраслей (энергетические химические машиностроительные сельскохозяйственные пищевые производства предприятия коммунального хозяйства т.п.)
- Системы технологических защит и блокировка аварийных и нештатных ситуаций сигнализация нарушений технологического процесса регистрацию событий архивирование данных
- Территориально распределенные удаленные и локальные системы управления
Функциональные возможности
- Контроллер МИК-51 это - проектно-компонуемое изделие которое позволяет пользователю выбрать нужный комплект модулей и блоков согласно числу и виду входных-выходных сигналов
- Встроенные средства самодиагностики: сигнализация и идентификация неисправностей о выходе сигналов за допустимые границы о сбоях в ОЗУ нарушении обмена по сети и т.п.
В контроллерах МИК-51 имеется развитая система межконтроллерного обмена с помощью которой контроллеры могут объединяться в локальную или распределенную управляющую сеть. В сети контроллеры могут обмениваться информацией как с компьютером так и между собой. Данная функция обеспечивает возможность организации распределенной обработки данных а также увеличения числа каналов ввода-вывода. При использовании функции межконтроллерного обмена значительно снижается информационная нагрузка на сеть.
- Программирование контроллера выполняется с помощью клавиш передней панели или по интерфейсу с помощью специального программного обеспечения - визуального редактора FBD-программ АЛЬФА. В качестве языка программирования в системе реализован язык функциональных блоковых диаграм Fnction Block Diagram (FBD) предоставляющий пользователю механизм объектного визуального программирования. Система программирования реализована в соответствии с требованиями стандарта Международной Электротехнической Комисси (МЭК) IEC 1131-3.
Редактор FBD-программ АЛЬФА имеет встроенный отладчик программ систему логического контроля состояния программы возможности документирования программ печати представления программы в виде таблицы и др.
Математическая обработка информации
Контроллер МИК-51 содержит библиотеку функциональных блоков достаточную для того чтобы решать сравнительно сложные задачи автоматического регулирования и логико-программного управления.
Библиотека функциональных блоков условно разделена на разделы :
- Функциональные блоки ввода-вывода: интерфейсный ввод-вывод аналоговый ввод-вывод дискретный ввод-вывод импульсный ввод
- Математические функциональные блоки: умножение суммирование с маштабированием деление корень квадратный абсолютное значениеинтегрирование дифференциирование с задержкой
- Логические функциональные блоки: Логическое И многовходовое И Логическое ИЛИ многовходовое ИЛИ исключающее ИЛИ мажорирование триггер регистр выделение фронта
- Функциональные блоки управления программой: минимум максимум скользящее средние задержка экмтремум ограничение ограничение скорости переключатель по номеру компаратор таймер счетчик мультивибратор одновибраор импульсатор
- Функциональные блоки управления технологическим процессом: фильтр масштабирование кусочно-линейная функция уставка аналоговая уставка времени программный задатчиктаймер сигнализатор реального времени линейное изменение параметра регулятор аналоговый регулятор каскадный регулятор импульсный пользовательская панель
-Функциональные блоки дельта-регуляторов: регуляторы аналоговые и импульсные с расширенными функциями дельта-регулятор.
Количество входов-выходов контроллера
-Аналоговые входа - 4 (2 универсальных 2 унифицированных).
-Аналоговые выхода -1.
-Дискретные входа -3.
-Дискретные выхода -5.
Модели и коды модулей расширения (УСО):
-МР-51-01: 8 дискретных входов 1 импульсный вход*
-МР-51-02: 4 дискретных входа 4 дискретных выхода 1 импульсный вход*
-МР-51-03: 8 дискретных выходов
-МР-51-04: 8 дискретных выходов
-МР-51-05: 4 дискретных входа 4 дискретных выхода 1 импульсный вход* 1 аналоговый выход
-МР-51-06: 8 дискретных входов 1 аналоговый выход
-МР-51-07: 3 аналоговых входа
Рисунок 2 - Микроконтроллер МИК-51.
Исходя из того что микроконтроллер МИК-51 имеет 12 максимально возможных выходоввходов Микроконтроллер Ремиконт Р-130 удовлетворяет условиям в большей степени.
2.1.3 Магнитные пускатели
Магнитный пускатель – исполнительное устройство предназначенное для включениявыключения трехфазных асинхронных двигателей с короткозамкнутым ротором.
Рука промышленного робота должна выполнять круговые движения по часовой стрелке и против часовой стрелки. Для этой цели необходим реверсивный электропривод. Реверсивный электропривод требует в свою очередь наличия двух магнитных пускателей.
В качестве магнитных пускателей выбираем отечественные недорогие контакторы КМИ-10911 электротехнической компании «ИЭК» (рисунок 2.2).
Рисунок 3 – Магнитный пускатель КМИ-10911
Данный магнитный пускатель имеет следующие технические характеристики:
- номинальное рабочее напряжение переменного тока: 220 В;
- номинальный рабочий ток: 9 А;
- номинальная мощность по категории применения АС-3: 22 кВт;
- номинальное напряжение катушки управления: 220 В;
- мощность потребления катушки: 60 ВА;
- температура окружающей среды: от -40ºС до +50ºС;
- степень защиты по ГОСТ 14254-96: IP20.
Данный контактор имеет возможность установки на 35-мм DIN-рейку.
2.1.4 Гидрораспределители.
Для реализации данной курсовой работы используем 4 гидрораспределителя золотникового типа. Выбираем гидрораспределитель с электромагнитами постоянного тока на 24В. Данный выбор обусловлен следующими факторами: электромагнит постоянного тока имеет высокую эксплуатационную надежность и обеспечивает мягкое переключение. Он не сгорает если во время работы останавливается например из-за заклинивания золотника. Возможна высокая частота переключений.
Так как в настоящее время наиболее распространены маслонаполненные электромагниты их применение предпочтительно особенно для гидроприводов работающих на открытом воздухе или во влажном климате поскольку исключается коррозия внутренних частей. Наличие во внутренней полости масла позволяет снизить износ обеспечить демпфирование ударов и улучшить теплоотдачу.
2.1.5 Автоматические выключатели
Для предотвращения токов короткого замыкания во входной и выходной цепи источника питания необходимо поставить автоматически выключатели.
Рассчитаем токи входных и выходных цепей источника питания и подберем автоматические выключатели.
Внешний вид выключателя представлен на рисунке 4
Рисунок 4 – Автоматический выключатель ВА47-29 1Р 05А
Номинальный выходной ток определим по формуле:
где IВЫХ – номинальный выходной ток А;
P – мощность источника питания постоянного тока Вт;
UВЫХ – напряжение выходной цепи В.
Выбираем автоматический выключатель ВА47-29 1Р 4А на ток 4 А. На основе выбранных технических средств автоматизации строим электрическую схему подключения.
Электрическая схема подключения приведена в графической части расчетно-пояснительной записки (лист 3).
2.1.6 Кнопки управления
В данном курсовом проекте кнопки используются в качестве устройств ручного ввода управляющей информации с пульта оператора. Кнопки необходимы для подачи устройству управления команд «Пуск» и «Стоп».
Используем нормально разомкнутые кнопки без фиксации SB-7 «Пуск» и SB-7 «Стоп» диаметра 22 мм компании «Интерэлектрокомплект» (ООО «ИЭК»).
Рисунок 5 – Кнопки SB-7 «Пуск» и SB-7 «Стоп»
2.2 Разработка алгоритма управления
Когда на микроконтроллер поступает сигнал РЦ (разрешения цикла) сигнал «Пуск» начинается цикл работы системы. Далее идет проверка наличия детали у накопителей 1 и 3. Далее производится одновременное включение магнитных пускателей КМ3 и КМ7 и происходит движение руки ПР1 влево т.е к накопителю 1 а также движение руки ПР2 вправо – к накопителю3. Проверяется наличие детали в накопителе 1 при помощи датчика BQ1 и наличие детали в накопителе 2 при помощи датчика BQ8. Как только рука ПР1 достигает накопителя 1 срабатывает датчик положения BQ2 а при достижении ПР2 накопителя 3 срабатывает датчик положения BQ9. При поступлении сигнала с датчиков BQ2 и BQ9 происходит отключение магнитных пускателей КМ3 и КМ7 а также включение электромагнитов YA3 и YA7 после чего начинается выдвижение руки ПР1 и ПР2. При полном выдвижении руки срабатывает датчик выдвижения BQ5 и BQ12. После срабатывания путевого выключателя BQ5 и BQ12 включаются электромагниты YA4 и YA8 и происходит захват детали. По прошествии 05 секунды производится отключение электромагнитов YA4 и YA8 и начинается задвижение руки т.е срабатывают электромагниты YA1 и YA5. Как только руки задвинутся срабатывают датчики задвижения рук BQ6 и BQ13 а электромагниты YA1 и YA5 отключаются. Затем включаются магнитные пускатели КМ4 и КМ5. Начинается перемещение руки ПР1 к прессу 1 и ПР2 к прессу 2. Как только рука достигнет пресса 1 и 2 сработают датчики BQ3 и BQ10. После этого магнитные пускатели КМ4 и КМ5 отключаются и включаются электромагниты YA3 и YA7 и происходит выдвижение рук. После того как руки выдвинулись срабатывают датчики выдвижения BQ5 и BQ12. Срабатывают электромагниты разжима схвата YA2 и YA6. После срабатывания датчика разжима схвата BQ7 и BQ14 включаются электромагниты YA1 и YA5 и начинается задвижение рук. Как только рука задвинется электромагниты отключатся и сработают датчики задвижения рук BQ6 и BQ13 на систему управления прессами подаётся сигнал ЦП. Выполняется рабочий ход пресса 1 и 2. После срабатывания датчиков задвижения включатся электромагниты выдвижения рук YA3 и YA7 после того как руки выдвинулись срабатывают датчики выдвижения BQ5 и BQ12. Электромагниты отключаются и срабатывают электромагниты зажима схвата YA4 и YA8. После того как схват зажат срабатывают электромагниты задвижения рук YA1 и YA5 после их задвижения срабатывают датчики задвижения BQ9 и BQ10. После того как рука задвинулась включаются магнитные пускатели КМ4 и КМ5 т.е поворот ПР1 к накопителю 2 (вправо) ПР2 – к накопителю 2 (влево). Как только руки достигнут накопителя 2 сработают датчики положения BQ4 и BQ11. Затем включаются электромагниты выдвижения рук ПР1 и ПР2 т.е YA3 и YA7. После того как руки полностью выдвинутся сработают датчики выдвижения BQ5 и BQ12. Затем срабатывают электромагниты разжима схвата т.е YA2 и YA6. После срабатывания датчика разжима схвата BQ7 и BQ14 включаются электромагниты YA1 и YA5 и начинается задвижение рук. Как только руки задвинутся сработают датчики задвижения рук BQ6 и BQ13. После этого цикл работы РТК повторяется.
В соответствии со структурной схемой составим таблицы входных и выходных сигналов.
Таблица 1 – Таблица входных сигналов:
Наличие детали в накопителе 1
ПР1 находится у накопителя 1
ПР1 находится у пресса 1
ПР1 находится у накопителя 2
Наличие детали в накопителе 3
ПР2 находится у накопителя 3
ПР2 находится у пресса 2
ПР2 находится у накопителя 2
Таблица 2 – Таблица выходных сигналов:
2.3 Разработка программы управления
Программа управления составленная для контроллера Ремиконт Р-130 приведена в графической части расчетно-пояснительной записки (лист 5). Программа управления составлена на основании циклограммы работы РТК. В основу программы были положены основные алгоритмы входящие в состав библиотеки алгоритмов для построения логических программ: ВДА – ввод дискретной группы А ДВА – дискретный вывод группы А ЭТП – этап ОКЛ – оперативный контроль логической программы МНИ – многовходовое «И» МИЛ - многовходовое «ИЛИ» УДП – управление двухпозиционной нагрузкой.
В программе был реализован таймер который осуществил задержку длительностью 15 секунд (для контроля разжима схвата промышленного робота левой руки).
Программа состоит из двух этапов. Чтобы обеспечить выполнение более одного цикла (в зависимости от наличия или отсутствия сигнала от другой системы управления) после выполнения всех этапов программы в последнем шаге второго этапа осуществлён переход на начало первого этапа то есть если от другой системы управления придёт сигнал разрешение цикла (РЦ) весь цикл работы технологического объекта повторится заново. Перед тем как перейти на начало цикла все текущие значения алгоблоков сбрасываются посредством предпоследнего шага этапа 2. Так же реализована функция «остановки» системы получающей сигнал от кнопки «Стоп». Реализована эта функция посредством подачи сигнала «стоп» от блока ВДА на соответствующий вход блока ОКЛ а так же на вход «выкл» всех блоков УДП.
В данной курсовой работе была разработана система управления робототехническим комплексом штамповки. Входе выполнения была написана программа для микроконтроллера Ремиконт Р-130 на языке функционально блоковых диаграмм была разработана структурная схема и электрическая схема подключения.
Предусмотрена возможность последующей модернизации и расширения возможностей работы устройства. Модернизация устройства может быть проведена по нескольким путям.
Одним из путей может быть изменение управляющей программы под нужды пользователя. При этом программу можно изменять непосредственно на технологическом объекте с помощью кнопок на лицевой панели контроллера. Другим путем модернизации может быть включение данной локальной системы управления в состав гибкой производственной системы (ГПС) где данный РТК будет какой-то отдельной ячейкой в общем технологическом цикле.
В ходе выполнения данной курсовой работы были получены навыки разработки автоматизированных систем управления технологическими процессами. Были получен опыт выбора технических средств автоматизации опыт построения взаимодействия этих технических средств автоматизации. Так же был осуществлён процесс написания программы для микроконтроллера на языке функциональных блоковых диаграмм.
Сосонкин В.Л. Программное управление технологическим оборудованием: Учебник для вузов по специальности «Автоматизация технологических процессов и производств». – М.: Машиностроение 1991. – 512 с.: ил.
Сбродов Н.Б. Применение программируемого контроллера Ремиконт Р-130 в системах управления. Часть 1. Функциональные возможности и архитектура: Методические указания к курсовому проектированию для студентов направления 550200. – Курган: Изд-во КГУ 1998.
Сбродов Н.Б. Применение программируемого контроллера Ремиконт Р-130 в системах управления. Часть 2. Организация ввода-вывода информации: Методические указания к курсовому проектированию по курсу “Системы автоматизации и управления” для студентов специальности 210200. – Курган: Изд-во КГУ 2000.
Структурная схема.cdw

движения руки ПР1 вправо
движения руки ПР2 влево
движения руки ПР2 вправо
разжима схвата руки ПР2
зажима схвата руки ПР2
разжима схвата руки ПР1
зажима схвата руки ПР1
процессом П2 штамповки
процессом П1 штамповки
движения накопителя 1
движения накопителя 3
Система управления РТК
Промышленный контроллер
Промышленный робот 1
Промышленный робот 2
Блок магнитных пускателей
Проект системы управления РТК штамповки
Земеров Е.Л. гр. Т-4135С
Рекомендуемые чертежи
- 09.03.2022
- 17.03.2025