Проект модернизации шагающего манипулятора




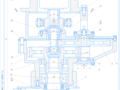
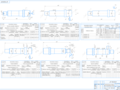
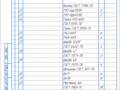
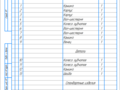
- Добавлен: 24.01.2023
- Размер: 2 MB
- Закачек: 0
Описание
Состав проекта
![]() |
![]() |
![]() |
![]() ![]() ![]() |
![]() ![]() ![]() |
![]() ![]() ![]() |
![]() ![]() ![]() |
![]() ![]() ![]() |
![]() |
![]() ![]() ![]() ![]() |
![]() ![]() ![]() ![]() |
![]() ![]() ![]() ![]() |
![]() ![]() ![]() ![]() |
![]() ![]() ![]() ![]() |
![]() ![]() ![]() ![]() |
![]() ![]() ![]() ![]() |
![]() ![]() ![]() ![]() |
![]() ![]() ![]() ![]() |
![]() ![]() ![]() ![]() |
![]() ![]() ![]() ![]() |
![]() ![]() ![]() ![]() |
![]() ![]() ![]() ![]() |
![]() ![]() ![]() ![]() |
![]() ![]() ![]() ![]() |
![]() ![]() ![]() ![]() |
![]() ![]() ![]() ![]() |
![]() ![]() ![]() ![]() |
Дополнительная информация
Содержание(хорошее).doc
Научно-исследовательский раздел 7
1 Анализ существующих конструкций .7
2 Классификация манипулятора 10
3 Область применения манипуляторов ..13
Конструкторский раздел 15
1 Выбор и обоснование конструкций . 15
2 Обоснования внедрения шагающего манипулятора .15
2.1 Актуальность создание шагающего манипулятора 17
2.2 Возможные типы шагающих движителей .19
2.3 Основные типы движителей машин грунтовой проходимости ..21
3 Постановка задач 26
4 Расчет элементов манипулятора ..31
4.1 Расчет гидроцилиндров ..31
4.2 Расчет гидроцилиндра рукояти .32
4.3 Расчет гидроцилиндра стрелы 33
4.4 Расчет гидроцилиндра захватного органа 34
5 Расчет трубопровода гидросистемы 36
6 Расчет металлоконструкций манипулятора на прочность 37
6.1 Расчет рукояти манипулятора ..37
6.2 Расчет стрелы на прочность ..44
Разработка перспективного графика технического обслуживания и
ремонта шагающего манипулятора 51
1 Разработка мероприятий технического обслуживания машины 51
2 Порядок построения перспективного (годового) графика ТО 52
3 Определение порядкового дня месяца проведения ТО и ремонта .56
4 Определение годовой трудоёмкости технического обслуживания 57
5 Определение числа рабочих для проведения ТО .58
1 Обоснование внедрения средств автоматизации . 60
2 Принцип действия и устройство ограничителя нагрузки манипулятора ..61
Технология восстановления вала . .63
1 Исправление центровочного отверстия .63
2 Токарная обработка под наплавку ..65
4 Токарная (черновая) обработка .70
5 Токарная (чистовая) обработка .71
Безопасность жизнедеятельности .. .. 75
1 Безопасность труда 75
2 Меры безопасности при изготовление шагающего движителя .81
3 Расчет строповки 82
Технико-экономическое обоснование проекта ..85
1 Характеристика базовой и новой техники ..85
2 Определений капитальных вложений ..86
3 Определений годовых и текущих затрат .88
4 Расчет экономического эффекта 99
Список литературы .97
А Манипулятор шагающий (спецификация)
Б Платформа шагающая (спецификация)
В Механизм поворотный (спецификация)
Г Гидроцилиндр (спецификация)
Манипулятор шагающий.doc
Опыт ведения аварийно-спасательных работ позволил определить основные направления: обследование разрушенных сооружений обнаружение пострадавших и оказание им первой помощи; подвод временных коммуникаций (водопровод линия электропередач) и восстановление разрушенных; обрушение опасных зон в поврежденных промышленных и гражданских сооружениях; восстановление этих сооружений и строительство новых объектов; вывод и переработка разрушенных строительных элементов.
Все эти работы требуют большого числа строительных машин различного назначения.
В данном дипломе для решения этих задач был разработан многофункциональный манипулятор на базе высокопроходимого шагающего движителя позволяющий заменить ряд строительных машин за счет использования различного сменного оборудования.
Научно – исследовательский раздел
1 Анализ существующих конструкций
В настоящее время возросшее число природных стихийных бедствий и различного рода аварий требует применение универсальной техники предназначенной для различного рода работ такой как строительные манипуляторы.
Манипулятор – это управляемое устройство или машина для выполнения двигательных функций аналогичные функциям руки человека при перемещении объектов в пространстве оснащенное рабочим органом.
Если буквально придерживаться терминологии то окажется что строители давно с ней знакомы. Такие строительные машины как краны и экскаваторы соответствуют термину «манипулятор» так как их рабочие движения аналогичны двигательным функциям руки человека.
Под определением «строительные манипуляторы» следует понимать как самостоятельные разработки так и новое поколение строительных машин дополненных манипуляционными характеристиками.
Например гидрокрановые установки оснащаемые приводным захватным рабочим органом получают новые качества работы: способность захвата груза без строповки и возможность его ориентированной установки без участия дополнительного рабочего строповщика.
Также примером может служить разработка многоцелевых землеройно-манипуляционных рабочих органов:
–ковш обратной лопаты с челюстным захватом и двух шарнирной вставкой обеспечивающей дополнительную степень свободы с гидравлическим поворотом ковша на рукояти или на вставке ковш с челюстью и ротационным механизмом;
–упрощенный двухпальцевый захват.
Рабочие органы с челюстным захватом (особенно при наличии дополнительной подвижности ковша) выполняют функции руки человека что позволяет
отнести машину к оборудованию манипулятивного типа.
Таким оборудованием помимо операций копания обратной лопаты без смены рабочего органа можно выполнять грейферные работы а также захват груза и ориентацию его в пространстве в любом положении (рис. 1.1).
Рисунок 1.1 – Рабочее оборудование многоцелевого назначения
Одним из перспективных многоцелевых рабочих органов является схват рыхлитель позволяющий значительно расширить функции традиционного зуба-рыхлителя (рис. 1.2).
Оборудование представляет собой шарнирно связанные рыхлительную стойку и челюсть.
Стойка смонтирована на рукояти вместо ковша и управляется гидроцилиндром а челюсть смонтирована на стойке и управляется дополнительным укороченным гидроцилиндром выносной опоры.
Рыхлительная стойка снабжена одним вертикальным зубом а челюсть – двумя наклонными в поперечной плоскости зубьями. Испытания показали что схватом-рыхлителем можно: выполнять послойное рыхление мерзлых грунтов зубьями стойки и челюстью клещевое скалывание (взламывание) асфальтобе-
тонных покрытий и мерзлого грунта; срыв асфальтобетонных покрытий зубом стойки; клещевое разрушение стен одноэтажных зданий с одновременной погрузкой обломков; растаскивание завалов; извлечение бордюрных камней при ремонте дорог; погрузочно-разгрузочные и монтажные работы с грамотными и железобетонными покрытиями трубами и другими штучными грузами.
Рисунок 1.2 – Рабочее оборудование землеройно-манипуляторного рабочего органа в виде двухпальцевого схвата
Благодаря многофункциональности такого рабочего оборудования оно может применяться для ликвидации последствий чрезвычайных ситуаций.
2 Классификация манипуляторов
Строительные манипуляторы и роботы классифицируются по следующим признакам.
Рисунок 1.3 – Классификация строительных манипуляторов и роботов
Ручное управление строительных манипуляторов может осуществляться тремя способами:
–командным с раздельным управлением каждой степенью подвижности манипулятора;
–полуавтоматическим с помощью многостепенной рукоятки с произвольной кинематикой;
–копирующим посредством задающего устройства кинематически подобного манипулятору.
Автоматизированные строительные манипуляторы могут быть с супервизорным управлением когда оператор только включает соответствующую программу автоматического действия.
С комбинированным управлением сочетающим супервизорное и ручное управление; с интерактивным управлением когда возможно принятие как оператором так и управляющим устройством.
По конструкции рабочих органов манипуляторы разделяются на традиционные для выполнения одной типовой операции строительного производства с совмещенным оборудованием когда на одной платформе устанавливается два рабочих органа и более; трансформируемые оборудованные автоматическим захватом и комплексом сменных рабочих органов; адаптируемые оснащенные многоцелевым рабочим органом для выполнения ряда технологических операций.
Классификация также может быть дополнена признаками определяющими число степеней свободы объем рабочей зоны способ программирования вид устройства передвижения конструктивно компоновочную схему и так далее.
Дополнительно можно ввести следующую квалификацию.
Строительные манипуляторы классифицируются по следующим признакам:
–характеру выполняемых операций;
–числу степеней подвижности;
–способу установки на рабочем месте;
–возможностью передвижения;
–типу задающего органа;
–виду систему координат и по системе управления.
По специализации строительные манипуляторы подразделяются на:
–многофункциональные;
–специализированные;
По характеру выполняемых операций подразделяются на:
–погрузочно-транспортные;
По номинальной грузоподъемности манипуляторы подразделяются на следующие группы:
–средние (свыше 10 до 200 кг);
–тяжелые (свыше 200 до 1000 кг);
–сверхтяжелые (свыше 1000 кг).
По числу степеней подвижности манипуляторы подразделяются:
–с тремя степенями подвижности;
–четырьмя степенями подвижности;
–со степенями подвижности более четырех.
По способу установки на рабочем месте манипуляторы подразделяются на напольные подвесные встроенные и другие.
По возможности передвижения манипуляторы подразделяются на стационарные и подвижные.
По виду систем координат манипуляторы подразделяются на работающие:
–в прямоугольной декартовой системе координат;
–в цилиндрической системе координат;
–в угловой системе координат;
–в других системах координат.
По конструктивно компоновочным схемам строительные манипуляторы могут быть:
К напольным относятся манипуляторы обычного исполнения базирующиеся на напольном шасси.
3 Область применения манипуляторов
Манипуляционное многоцелевое оборудование обеспечивает без замены рабочего органа качественное выполнение планировочных рыхлительных откосообразовательных и погрузочно-разгрузочных работ позволит практически исключить ручной труд на земляных работах.
Применение многоцелевого манипуляционного оборудования показало что оно успешно работает как обратная лопата при рытье траншей котлованов при разработке грунта в малообъемных выемках уборке просыпей на обратной засыпке грунта на погрузочно-разгрузочных работах при очистке территорий от мусора при реконструкции строительных объектов многоцелевой манипулятор успешно работает в грейферном и захватно-манипуляторном режимах. При этом не требуется выполнения сложных демонтажных работ обусловленных заменой исполнительных рабочих органов. Оборудование легко осуществляет захват отдельных грузов труб бревен тротуарных плит бордюрных камней и манипулировании ими перемещении и укладывании предметов в соответствии с проектом производства работ эффективно закладывает откосы у траншей и котлованов а также рыхлит мерзлый грунт взламывает асфальтобетонные покрытия.
При разработке манипулятора для примера использовался процесс монтажа коммуникаций. В этом случае многофункциональный манипулятор должен производить операции по отрывке траншей укладке и сборке трубопроводов установке ограждений а также засыпке траншей с утрамбовкой грунта.
В свою очередь манипулятор со сменными рабочими органами может выполнять следующие функции:
–монтаж коммуникаций;
–разборка конструкций;
–бетонные арматурные работы;
–отрывка траншей пазух приямков при устройстве коммуникаций;
–погрузка разгрузка кантование и укладка длинномерных грузов (труб балок бревен и тому подобное).
Конструкция околовка манипулятора позволяет использовать оборудование для распыления различного рода обеззараживающих веществ для обезвреживания отравляющих веществ. Также манипулятор может иметь две параллельные системы управления.
–внутреннюю с рукоятками управления;
–выносную позволяющую управлять манипулятором кабины.
Конструкторский раздел
1 Выбор и обоснование конструкции
Проектируемый манипулятор разработан на базе высокопроходимого шагающего средства.
Применение такой техники позволит сократить число машин в ликвидации последствий чрезвычайных ситуаций что значительно понижает себестоимость спасательных а также ускорит их проведение и сократит потребность в рабочей силе.
Обычно при таких работах используется большее число РАЗЛИЧНОЙ техники учитывая что техники из-за стесненных условий снижается требуется четкая организация . При этом неизбежны потери производительности техники а значит увеличение сроков спасательных работ и ухудшения состояния пострадавших.
Избежать этих негативных факторов позволит внедрения многофункционального манипулятора со сменными рабочими органами. В качестве базовых транспортных средств могут использоваться специализированные высокопроходимые транспортные средства обеспечивающие доступ и работу манипулятора в сложных климатических условиях.
2 Обоснование внедрения шагающего манипулятора
В последние годы в связи с народнохозяйственной потребностью освоения новых труднодоступных территорий внедрения в сельском хозяйстве почвосберегающих технологий и др. повышается интерес к разработке внедорожных транспортных средств с новыми нетрадиционными видами двигателей. Объясняется это тем что в условиях бездорожья движение например по заболоченной местности пескам тундре не может быть эффективно обеспечено традиционными транспортными средствами с колесным и гусеничным двигателями.
Эти обстоятельства заставляют искать новые принципы конструирования транспортных машин в том числе и на базе шагающих двигателей.
В настоящее время имеются лабораторные и опытные образцы шагающих машин. Теоретические и экспериментальные исследования показывают что шагающие машины могут быть лишены недостатков присущих колесным и гусеничным транспортным средствам. В частности за счет достаточно большой площади опорной поверхности (стопы) механизма шагания можно существенно снизить среднее удельное давление на грунт а рациональным выбором кинематической схемы шагающей машины или системы управления реализовать ее поворот без проскальзывания стопы по грунту.
Другое важное преимущество шагающих машин связано с их энергетическими характеристиками. При движении транспортного средства потребляется энергия в конечном счете затрачивается на необратимую деформацию грунта. Если теперь учесть что колесные и гусеничные машины образуют более глубокую колею а шагающие – дискретную и мягкую то достаточно обосновано предложение о меньших энергозатратах при движении рационально спроектированных шагающих машин.
Вместе с тем накопленный опыт исследования динамических характеристик движения шагающих машин обнаруживает целый ряд факторов сдерживающих форсированное внедрение шагающих машин в различные отрасли народного хозяйства. Среди них важнейшими являются сравнительная сложность конструкции а как следовательно и низкая надежность и невысокая скорость передвижения обусловленная высокими динамическими нагрузками действующими на корпус шагающей машины и ее привод при высоких скоростях перемещения неуравновешенных механизмов шагания на этапах быстрого переноса. Однако не игнорируя эти факторы следует иметь в виду что усложнение конструкции в целом есть объективный закон развития техники и в частности транспортного машиностроения. С другой стороны для различных отраслей народно сложности. Так в сельском хозяйстве для производства технологических операций на сравнительно ровном грунте достаточно сохраняя принципы управления
колесными и гусеничными машинами перенести их на шагающие машины.
2.1 Актуальность создания шагающего манипулятора
Преимущества шагающих машин определяют тот интерес который испытывают исследователи со всего мира на протяжении последних десятилетий к проблемам создания шагающих манипуляторов. В настоящее время шагающие машины не нашли широкого применения однако огромное число исследователей данной проблемы заставляет предположить что шагающие машины уже в обозримом будущем займут значительную нишу в различных областях человеческой деятельности. Так весьма популярна идея применения шагающих аппаратов в военных целях. Шагающие машины предполагается использовать для транспортировки грузов контроля последствий ядерного химического и биологического нападения разведки постановки дымовой завесы разборки разрушенных зданий и проведения спасательных операций в городах после ядерной бомбардировки или стихийных бедствий для транспортировки боеприпасов на огневые позиции и работы на складах боеприпасов при минировании и разминировании объектов исследуются возможности применения шагающих двигателей для боевых машин. Прорабатываются вопросы использования машин передвигающихся с помощью ног для проведения исследований на поверхности других планет.
Использование шагающих машин в народном хозяйстве перспективно для транспортировки грузов в местности не имеющих дорог. Например для доставки опор линий электропередач и канатных дорог в горах транспортировки буровых вышек проведения исследований и т.п. Высокая грунтовая проходимость и более слабые по сравнению с колесным и гусеничным транспортом разрушения почвы определяют целесообразность использования шагающих машин при движении по слабым грунтам и легко разрушающемуся почвенному покрову в болотистой местности тундре пустынях и полупустынях в лесу и в горах. Такие машины предполагается использовать например для ремонтных работ на участках нефте- и газопроводов проложенных на труднопроходимой территории.
Трудности создания шагающих машин прежде всего были связаны со сложностью решения проблемы управления их движением. Наиболее простым с точки зрения управления способом перемещения шагающей машины является статически устойчивое шагание.
В частности в алгоритмах управления движением такой машины можно не учитывать динамические факторы. В то же время статически устойчивые режимы движения обеспечивают высокую маневренность и проходимость а также не опрокидывание машины при сбоях и отказах. Система управления должна обеспечивать согласованное (координированное) движение по каждой из степеней подвижности ног за счет одновременного согласованного управления значительным количеством сервоприводов в шарнирах ног в зависимости от состояния машины (показаний датчиков) управляющих сигналов от водителя или верхних уровней системы управления автоматической машины и формы опорной поверхности что обеспечивает реализацию цели перемещения машины и сохранение ее устойчивости.
Если аппарат не имеет значительной по площади управляемой стопы то контакт ноги с опорной поверхностью имеет точечный характер и для статически устойчивой ходьбы минимальное количество ног одновременно находящихся в фазе опоры равно трем. Минимальное же количество ног аппарата равно четырем. При этом четырехногий аппарат имеет только один тип статически устойчивых походок при котором по очереди одна за другой переносятся ноги аппарата. С точки зрения реализации достаточно богатого набора походок обеспечивающих высокую проходимость машины в рамках статической устойчивости количество ног аппарата должно быть не менее шести. Использование большего чем шесть количества ног не дает заметных преимуществ по профильной проходимости или маневренности. Однако увеличение количества ног может быть выгодно при движении по слабым грунтам для снижения удельного давления на грунт.
В силу указанных причин наибольшее продвижение получено в области создания статически устойчивых шагающих машин. А для увеличения проходи
мости проектируемого механизма предлагается ввести в ранее рассмотренную схему движителя управляемый элемент – гидроцилиндр который при движении как будет показано позднее увеличивает положительные качества характеристики траектории движения проектируемого механизма.
2.2 Возможные типы шагающих движителей
Шагающие машины можно условно разделить на два больших класса: статически неустойчивые например двуногие шагающие аппараты и статически устойчивые многоногие машины.
Основная особенность статически неустойчивых шагающих аппаратов состоит в том что их движение обеспечивается развитой системой управления включающей в себя в общем случае систему сбора информации о местности и положении аппарата вычислительные средства переработки полученной информации и исполнительные двигатели реализующие движение конечностей на основе того или иного алгоритма.
Многоногие шагающие машины могут быть как статически устойчивыми так статически неустойчивыми. Это определяется как конструкцией машины так и реализуемой походкой. Для того чтобы шагающая машина была статически устойчивой необходимо чтобы в любой момент времени как минимум три ноги находились в опоре а вертикаль проходящая через центр тяжести пересекала опорную поверхность внутри многоугольника образованного точками контакта опорных элементов ног с поверхностью. Поэтому минимальное количество ног для статически устойчивой машины равно четырем. Для такой машины существует только единственная походка обеспечивающая устойчивость – поочередный перенос каждой ноги в новое положение при взаимодействии с опорной поверхностью остальных трех. С увеличением числа ног шагающей машины увеличивается число вариантов допустимых походок.
Существует достаточно большое количество типов конструкций статически устойчивых шагающих машин. Большинство из них выполнено на уровне технических предложений. Описание которых изложено в авторских свидетельствах и патентах. Однако имеются и действующие модели и экспериментальные образцы. Общим для всех машин является дискретное взаимодействие ног (в дальнейшем стоп или башмаков механизмов шагания) а отличие проявляется в их конструкции кинематических схемах механизмов шагания и движителей приводов курсового перемещения рулевого управления адаптации и др.
Простейшим кинематическим схемам отвечают стопоходящие машины с фиксированной походкой и не имеющие привода рулевого управления адаптации и др. Механизм шагания таких машин – это механическая система с одной степенью свободы. У наиболее сложных статически устойчивых шагающих машин механизмы шагания – это механические системы с тремя и более управляемыми степенями свободы позволяющими стопе перемещаться требуемым образом в пространстве. Управление такими машинами предполагает наличие бортовых вычислительных комплексов.
Целесообразно различать два основных режима эксплуатации статически устойчивых шагающих машин: режим специального маневрирования и маршевый.
Режим специального маневрирования предусматривает реализацию программного движения корпуса шагающей машины при передвижении по грунту где размеры препятствий соизмеримы с характерными размерами машины и обеспечивается согласованным управлением бортовой ЭВМ движением каждого движителя. Реализация режима специального маневрирования решает задачи профильной проходимости шагающей машины состоящей в преодолении таких препятствий как завалы траншеи и др. для этого. Как правило необходимо предусматривать конструкцию движителей шагающей машины обеспечивающих независимое перемещение опор относительно корпуса в трех взаимно перпендикулярных плоскостях т.е. с минимум тремя управляемыми степенями свобод.
Реализация маршевого режима движения целесообразна при перемещении по грунту достаточно гладкого профиля когда размеры преодолеваемых препятствий несоизмеримы с характерными размерами машины и он обеспечивается синхронным управлением движителями как цикловыми механизмами. В отличие
от режима специального маневрирования маршевый режим движения решает более узкую задачу грунтовой (опорной) проходимости состоящей в перемеще
нии по слабым грунтам (заболоченная местность пески и др.) а для сельскохозяйственных машин обеспечивает и экологическое воздействие на почву. В этом случае механизм движителя может быть механической системой с одной управляемой приводом курсового перемещения шагающей машины степенью свободы. Для маневрирования должен быть предусмотрен рулевой привод изменяющий ориентацию плоскостей шагания движителей. Целесообразно также предусматривать и систему адаптации механизмов шагания к микро неровностям грунта. Однако для определения класса машин вместо системы адаптации возможно применение массивного подрессоривания. Таким образом управление шагающей машиной аналогично правлению традиционными колесными и гусеничными машинами и может осуществляться человеком-оператором.
Таким образом в зависимости от эксплутационной ситуации управление шагающей машиной может быть реализовано в одном из двух режимов: режиме специального маневрирования и маршевом. В соответствии с этим целесообразна и концепция проектирования шагающей машины предусматривающая ее эксплуатацию в одном из двух режимов или только в маршевом (например для некоторого класса сельскохозяйственной и транспортной техники возможно применение простейших стопоходящих машин). Как в том так и в другом случаях исследование динамики и устойчивости движения шагающей машины в маршевом режиме является одной из основных задач при проектировании транспортных и технологических машин с шагающими движителями.
2.3 Основные типы шагающих движителей машин
Шагающий движитель машины грунтовой проходимости состоит из следующих узлов: механизм ов шагания механизма адаптации или подрессоривания; приводов курсового движения поворота; системы управления приводами.
По составу функциональных узлов шагающих движителей выделяют
следующие классификационные признаки:
)количество шагающих механизмов в движителе и их расположение;
)структура функциональных приводов шагающих механизмов;
)тип системы поворота шагающего движителя;
)кинематическая схема шагающего механизма;
)система адаптации или подрессоривания шагающих механизмов к рельефу местности;
)система управления шагающим движителем;
)тип сигналов в управляющем устройстве.
Указанные признаки достаточно полно охватывают круг вопросов требующих решения при проектировании шагающих машин и могут служить основой для систематизированного анализа рассмотренных конструкций движителей и схемных решений шагающих машин.
Широкое распространение получили четыре механизма с точки зрения их пригодности в качестве шагающих механизмов транспортно-технологических машин опорной проходимости. Рассматриваемые схемы отобранные из известных с учетом следующих качеств:
Точка на одном из звеньев имеет приближенно прямолинейный участок скорость на котором постоянна;
Требуемая траектория точки образуется при полном обороте ведущего звена механизма;
Обратимость механизма;
Прямолинейный участок траектории опорной точки располагается внешним образом по отношению к звеньям механизма;
Механизм имеет одну степень свободы.
Этим требованиям удовлетворяют механизмы изображенные на рисунках 2.1 – 2.3.
Рисунок 2.1 – Сдвоенный лямбдообразный механизм
Сформулируем критерии на основе которых можно оценивать конструкции движителей построенных на основе рычажных механизмов схемы которых рассмотрены выше.
)Габариты движителя: длина ширина высота. Для сопоставимости результатов конструктивные проработки выполнялись для одного и того же значения размаха траектории – 850 мм.
Сравнение получающихся параметров является простым и наглядным. Вместе с тем объем занимаемый конструкцией является достаточно общим и глубоким показателем ее совершенства т.к. отражает рациональность выбранных кинематических и силовых схем и в значительной степени определяет возможность расположения движителей на корпусе шагающей машины последовательно (один за другим) или объединения их в блоки попарно (поперечная компановка) возможность поворота движителя относительно корпуса шагающей машины и т.д.
Рисунок 2.2 – Четырехзвенный механизм
Рисунок 2.3 – Шестизвенный механизм
)Число подвижных звеньев движителя перемещающих одну опорную стойку.
)Число плоскостей в которых движутся звенья механизма.
Физические направляющие особенно длинные трудно изготавливать с высокой точностью. Нагрузка со стороны ползуна вызывает их изгиб что приводит к росту их сечений и как следствие веса – из-за необходимости обеспечить
жесткость исключающую перекосы и заклинивания пары. Такие направляющие трудно герметизировать в результате чего они работают в условиях сухого или полусухого трения снижающего КПД шагающей машины и увеличивающего износ движителя.
)Удобство подвода вала трансмиссии к входному кривошипу механизма.
)Наличие нагрузок перпендикулярных плоскости прямолинейно-направляющего механизма. При вертикальном расположении прямолинейно-направляющего механизма отсутствие таких нагрузок обеспечивается автоматически.
При горизонтальном или наклонном расположении приводного прямолинейно-направляющего механизма для разгрузки его звеньев от вертикальной реакции требуется введение горизонтальных направляющих.
Отметим что шагающий движитель на основе механизма с одной степенью свободы сочетающий в полной мере компактность и простоту конструкции с хорошей траекторией (форма коэффициент режима скорости ускорения) на сегодняшний день не известен. В связи с этим для экспериментальной отработки был использован наиболее простой четырехзвенный механизм.
Новый тип движителя (рис. 2.4) включает в себя дополнительный управляемый элемент управления который позволяет улучшить характеристики новой шагающей машины в частности в определенный момент времени увеличить высоту шага машины которая необходима нам для увеличения проходимости а также появляется дополнительная возможность горизонтирования машины путем выравнивая положения высоты лап движителя.
По расчетным данным полученным с помощью разработанной программы с применением языка программирования Delphi удалось получить результаты подтверждающие тот факт что высота проседания машины уменьшится а следовательно уменьшатся нагрузки приходящиеся на движитель увеличится плавность хода.
Рисунок 2.4 – Шагающий движитель с гидравлическим приводом
Разработка на базе шагающего движителя многофункционального манипулятора.
Структурно шагающий движитель состоит из пяти элементов: приводного электродвигателя редуктора раздаточного редуктора и двух механизмов шагания. Каждый из этих элементов в общем случае может быть различным по конструкции однако независимо от конструктивных особенностей он должен иметь некоторые общие функциональные свойства выделяющие его в отдельный класс механизмов. Так механизм шагания должен иметь одну степень подвижности ведущее звено должно совершать вращательное движение а выходное звено
должно иметь некоторую точку траектория которой должна отвечать ряду специфических требований определяющих ее пригодность для использования в качестве опорной точки. То есть механизм шагания служит преобразователем вращательного движения ведущего звена в поступательное движение стопы прикрепленной в опорной точке механизма. Раздаточный редуктор должен иметь
одно входное и два выходных звена совершающих вращательное движение.
При этом он может иметь постоянные передаточные отношения или изменяющиеся при движении и служить в этом случае корректором траектории стоп. В частном случае редуктор корректор может вырождаться до жесткой связи между ведущими кривошипами механизмов. Таким образом шагающий движитель представляет собой одностепенную механическую систему с постоянным нахождение в опоре.
Задачей любого механизма шагания является при заданном движении ведущих звеньев отработать заданную траекторию опорной точки механизма. Характеристики этой траектории являются теми параметрами которые отвечают на вопрос пригодности механизма шагания для использования его в движителе шагающей машины.
Рисунок 2.5 – Структурная схема шагающего движителя
В связи с этим для дальнейшего анализа траектория опорной точки условно разделяется на два участка (фазы). Первый участок называется фаза опирания на грунт он начинается с момента опускания стопы на грунт и заканчивается в момент подъема стопы траектория стопы на этом участке должна иметь большую горизонтальную длину и маленькую высоту. Второй участок – фаза переноса начинается с момента схода стопы с грунта и заканчивается в момент опускания стопы на грунт. В независимости от вышесказанного траектория движения стопы разделяется на четыре зоны.
Первая зона – зона гарантированного опирания на грунт границами зоны служат некоторые условные точки между которыми стопа должна находиться в
опоре в штатном режиме движения.
Вторая зона – подъема стопы начинается по окончании зоны гарантированного опирания и заканчивается в некотором условном положении в котором стопа поднята на достаточную высоту для осуществления ее переноса траектория на этом участке должна иметь возможно меньшую горизонтальную протяженность.
Третий участок называется зона гарантированного переноса начинается после окончания зоны подъема и заканчивается на той же высоте с началом зоны опускания. Таким образом самыми низкими точками на участке переноса являются границы этого участка.
Наконец четвертый участок – зона опускания начинается при достижении стопы высоты. На которой закончилась зона подъема и продолжается до постановки стопы на грунт. Таким образом границы фаз опирания и переноса при движении в штатном режиме лежат в зонах подъема и опускания. конкретные значения фаз зависят во-первых от характера объединения механизмов шагания в шагающий движитель во-вторых от профиля опорной поверхности а в-третьих от упругих и пластических свойств грунта. Границы зон являются независимыми от характера местности по которой движется машина а определяются на этапе проектирования как кинематические характеристики механизма шагания. Такой подход на мой взгляд позволяет с одной стороны сформулировать исходные требования к механизму шагания а с другой позволяет рассматривать работу движителя на реальном грунте.
Общие характеристики шагающего манипулятора можно представить следующими параметрами.
Степень подвижности движителя – включает число управляемых (активных) степеней подвижности и число неуправляемых (пассивных) степеней подвижности определяет сложность привода механизма шагающего движителя.
Сложность структурной схемы – комплексный параметр который включает в себя количество звеньев количество кинематических и поступательно движущихся пар количество пространственно движущихся звеньев.
Размах – максимальное расстояние между крайними по горизонтали точками траектории размах не зависит от профиля опорной поверхности и служит базовой величиной к которой относятся все прочие геометрические параметры движителя.
Номинальная высота – от точки опоры до точки подвеса выражается отношением к длине размаха определяется своим минимальным и максимальным значением определяет величину дорожного просвета.
Длина опорного участка – расстояние по горизонтали между границами участка выражается отношением к длине размаха определяет длину шага.
Передаточное отношение от ведущего звена движителя до стопы в горизонтальном положении – определяется как отношение горизонтальной скорости стопы к произведению угловой скорости ведущего звена и длины размаха характеризуется минимальным максимальным и средним значением характеризует горизонтальную скорость движения стопы.
Передаточное отношение от ведущего звена движителя до стопы в вертикальном направлении – определяется как отношение вертикальной скорости стопы к произведению угловой скорости ведущего звена и длины размаха характеризуется минимальным и максимальным значением характеризует скорость вертикальных колебаний стопы.
Максимальное полное ускорение стопы – определяется по модулю характеризует величину кинематически обусловленных динамических нагрузок.
Номинальная высота – определяется отношением расстояния между точкой опоры и точкой подвеса в фазе опускания и подъема к длине размаха характеризуется своим минимальным и максимальным значением определяет возможное уменьшение дорожного просвета при перешагивании.
Доля размаха приходящаяся на фазу опускания или подъема.
Отклонение от нуля скорости опорной точки в момент касания или схода стопы с грунта определяется значениями своей горизонтальной и вертикальной составляющих определяет наличие жесткого удара при постановке или снятии стопы.
Отклонения от нуля ускорения опорной точки в момент касания или схода стопы с грунта определяется значениями своей горизонтальной и вертикальной составляющих определяет наличие мягкого удара при постановке или снятии стопы.
Номинальная высота – определяется отношением расстояния между точкой опоры и точкой подвеса в фазе переноса к длине размаха характеризуется своим минимальным и максимальным значениям определяет величину перешагиваемых препятствий.
Доля размаха приходящаяся на фазу переноса.
Максимальное значение полной скорости стопы.
Максимальное и минимальное (с учетом знака) значения ускорения стопы.
Независимо от вышесказанного определяются основные параметры характеризующие фазовое разбиение траектории опорной точки зависит не только от параметров движителя но и геометрии грунта по которому осуществляется движение. Это означает что само определение данных параметров зависит от профиля опорной поверхности под стопой. Поскольку проектируемые машины предполагаются для ходьбы по относительно ровной поверхности то правомерно при проектировочном расчете ограничится рассмотрением одного основного типа опорной поверхности а именно – плоскости.
Вертикальная координата линия смены ног – вертикальная координата опорной точки в системе координат связанной с движителем в момент постановки или снятия стопы с грунта определяет дорожный просвет машины.
«Глубина приседания» – разница между вертикальными координатами линии смены ног и самой низкой точкой траектории определяет величину вертикальных колебаний корпуса машины при ходьбе.
Длина шага – горизонтальное расстояние между точками постановки стопы на грунт и снятия стопы с грунта.
Горизонтальная скорость в опорной фазе – определяется минимальным максимальным и средним значением определяет курсовую устойчивость маши-
ны выражает неравномерность горизонтальной скорости машины как отношения максимального значения горизонтальной скорости стопы в опорной фазе к ее минимальному значению.
4 Расчет элементов манипулятора
4.1 Расчет гидроцилиндров
Усилие в гидроцилиндре привода оголовка манипулятора. Расчет производится в положении когда рабочий орган находится в крайнем нижнем положении траншеи (рис. 2.6).
Для определения усилия Рц.о. составим сумму моментов всех сил относительно точки поворота оголовка – точки А.
Рц.о.×0255 – Gо×045 – (Gзо+Gгр) ×0855=0
где Gо – вис оголовка; Gо=196 кН
Gзо – вес захватного органа; Gзо=294 кН
Gгр – вес груза; Gгр=19.6 кН.
Внутренний диаметр гидроцилиндра dцо вычислим в зависимости от значений действующего усилия Рц и расчетного давления жидкости в гидросистеме Рр:
При этом с учетом гидравлических потерь от насоса до цилиндра можно принять Р=09Рр.
По ГОСТ 6540-68 dцо=70 мм; dш=30 мм.
Рисунок 2.6 – Расчетная схема для определения усилия в гидроцилиндре оголовка
4.2 Расчет гидроцилиндра рукояти
Расчет ведем в положении когда плечи сил приложенных к рукояти наибольшие (рис. 27).
Определяем усилия в гидроцилиндре рукоятки
где Gр – вес рукояти; Gр=65 кН.
Определяем внутренний диаметр гидроцилиндра
По ГОСТ 6540-68 dц=125 мм; dш=50 мм.
Рисунок 2.7 – Расчетная схема для определения Рцр
4.3 Расчет гидроцилиндра стрелы
Расчет ведем в положении что и для гидроцилиндра рукояти.
Определяем усилия в гидроцилиндре стрелы составляя сумму моментов всех сил относительно точки С.
где Gс – вес стрелы; Gс=71 кН.
Требуемое усилие развиваемое в одном гидроцилиндре стрелы
Определяем внутренний диаметр гидроцилиндра:
По ГОСТ 6540-68 выбираем dц=140 мм; dш=60 мм.
Рисунок 2.8 – Расчетная схема для определения Рцс
4.4 Расчет гидроцилиндра захватного органа
Для проектируемого захватного органа расчетная схема имеет вид (рис. 2.4) где Р – требуемое усилие на штоке гидроцилиндра; N – сила необходимая для удержания объекта манипулирования; l – расстояние до центра захвата.
Для данного вида захватного устройства справедливо равенство
В данном случае чтобы обеспечить удержание объекта необходимо чтобы сила трения пальцев и объекта равнялась весу груза тогда
где m - коэффициент трения сталь о сталь; m=03.
Размеры d и l – определяем конструктивно.
Вычисляем требуемое усилие гидроцилиндра:
Найдем размер гидроцилиндра:
Примем диаметр гидроцилиндра по ГОСТ 6540-68 dц=180 мм; dш=50 мм.
Рисунок 2.9 – Схема работы гидроцилиндра
5 Расчет трубопроводов гидросистемы
Внутренний диаметр трубы нагнетательного трубопровода рассчитываем по формуле:
где q – расход жидкости лмин; q=100 лмин; v=5 МС.
Толщина стенок трубопровода определяется по формуле
где Рu – давление в гидросистеме; Рu=25 Мпа.
s - допускаемое напряжение растяжения для стальных труб; s=784 Мпа.
d – внутренний диаметр трубы;
k – коэффициент безопасности k=2.
Принимаем по ГОСТ 8734-58 стальные толстостенные трубы с внутренним диаметром 17 мм наружным 30 мм d=65 мм.
Аналогично ведем расчет для всасывающей гидролинии:
Толщина стенок трубопровода
Принимаем по ГОСТ 8734-58 стальные трубы с внутренним диаметром 264 мм наружным 30 мм и толщиной стенки 18 мм
–для низкого давления шина Б с внутренним диаметром 32±1.5 мм.
–для высокого давления «РВД» с внутренним диаметром d=20±08 мм.
6 Расчет металлоконструкций манипулятора на прочность
6.1 Расчет рукояти манипулятора
Для расчета рукояти на прочность составим схему расчета для этого представим рукоять как консольную балку закрепленную одним концом в жесткую заделку и приложим все силы действующие на рукоять в вертикальной плоскости.
Для построения эпюр М Q Н необходимо найти реакции в заделе Нв Rв Мв. Для нахождения Мв составим уравнение моментов всех сил относительно точки В.
Мв+Gгр×375+(Gо+Gзо)×Рцо×соs20°×01-Рцо×sin20°×165+
+Рцр×соs45°×02-Рцр×sin42°×17+Gр×18
Мв=25898×067×17+7903×056×165-19.6×375-(196+294)×3225-
-7903×094×01-25898×074×02-65×18=2212 кН ×м.
Для нахождения Нв составим уравнение проекций всех сил на ось Х.
Нв-Рцо×соs20°-Рцр×cоs20°-Рцр×соs42°=0
Нв=7903×094+258.98×074=266 кН.
Для нахождения Rв составим уравнение проекций всех сил на ось Y.
Участок 1. 0z10525 (слева)
При z1=0525; М1=196×0525=-1029 кН×м.
Участок 2. 0z21425 (слева)
Q2×cos22°= Gгр+Gо+Gзо
Н2×sin22°= Gгр+Gо+Gзо
М2=-(Gо+Gзо)×z2-Gгр(0525+z2)
При z2=0; М2=-Gгр×0525= -196×0.525= -1029 кН×м
При z2=1425; М2= -49×1425-196× 10525+1425)= -452 кН×м.
Участок 3. 0z301 (слева)
Q3×cos22°= Gгр+Gо+Gзо+Gр
Рисунок 2 10 – Схема рукояти манипулятора
Н3×sin22°= Gгр+Gо+Gзо+Gр
М3=-Gгр(195+z3)-(Gо+Gзо)(1425+z3)-Gр
При z3=0; М3=-196×195-49×1425= -452 кН×м
При z3=01; М3= -196×205-49×1525-65×01= -483 кН×м.
Участок 4. 0z401 (слева)
Q4×cos78°=-Рцр×sin42°+Gр+Gо+Gзо+Gгр
Н4×sin78°= -Рцр×cos42°
М4=Рцр×sin42°×z4-Gгр(205+z4)-(Gо+Gзо)×(1525+z4)-Gр(G1+z)
При z4=0; М4=-Gгр×205-(Gо+Gзо)×1525= -483 кН×м
При z4=01; М4=25898×067×01-196×215-49×1625-65×02= -2615 кН×м.
Участок 5. 0z516 (справа)
При z5=0; М5=Мв =2212 кН×м
При z5=16; М5= 2212+(-1711)×16= -5256 кН×м.
Участок 6. 0z601 (справа)
М6= Мв+Rв×(16+z6)+Нв×z6×cos12°
При z6=0; М6=-5256 кН
При z3=01; М6= -2615 кН
По полученным данным строим эпюры Н Q и М. Расчет на прочность будем вести в наиболее опасных сечениях I-I и II-II так как в этих местах сечения ослаблены отверстиями.
Из эпюр определяем нагрузки действующие в опасных сечениях.
Изобразим сечения и найдем для них геометрические характеристики: Jx и Wx F.
Jx – момент инерции сечения относительно оси х.
Wx – момент сопротивления сечения нетто.
Для сечения I-I имеем:
Рисунок 2.11 – Сечение балки
F=2×225×1+2×1×(30-6)=98 см2=98×10-4 м2
Момент инерции нетто вычислим по формуле
где d – толщина стенки м;
h – высота сечения м;
В – ширина сечения м;
d – диаметр отверстия м.
Момент сопротивления сечения Wх вычислим по формуле
Нормальное напряжение возникающее в сечении вычислим по формуле
где Mи – изгибающий момент;
Н – наибольшая сжимающая (-) или растягивающая сила.
Касательные напряжения возникающие в сечении вычислим по формуле
где S – статический момент полусечения относительно оси х.
Суммарное напряжение действующее в сечении определим по третьей теории прочности.
При расчете на прочность должно выполняться неравенство
где sт – предел текучести для стали 20 sт =260 МПа;
n – коэффициент запаса прочности n=17.
Условие выполняется следовательно в сечении I-I прочность обеспечивается.
Рисунок 2.12 - Площадь конечного сечения
F=225×1+2×1×(20-6)=53 см2=53×10-4 м2
Момент инерции сечения относительно оси х
Момент сопротивления Wх для нижних волокон
Нормальное напряжение в сечении II-II
Статический момент полусечения Sх.
Касательное напряжение возникающее в сечении II-II
Суммарное напряжение в сечении
Условие выполняется следовательно в сечении II-II прочность обеспечена.
Расчет рукояти в горизонтальной плоскости проводить нецелесообразно но ввиду незначительности действующих в этой плоскости сил (сил инерции) а также запаса прочности.
6.2 Расчет стрелы на прочность
Составим расчетную схему стрелы и приложим в крайней точке В реакции возникающие от действия рукояти а в точке с реакции возникающие в заделке.
Найдем реакции возникающие в заделе.
Для определения Мс составим уравнение моментов всех сил относительно точки С.
Мс+Мв+Нв×057+Rв×255-Рцс×sin32°×22+Рцс×cos32°×1125-Gс×106=0.
Мс=27585×053×22+71×106-2212-266×057-1711×255-27585×085×1125=
Для нахождения реализации Rс составим уравнение проекций всех сил на ось у.
Rс+Gc+Рцс×sin32°-1711=0.
Rс=1711-71-27585×053= 178 кН
Для нахождения Нс составим уравнение проекций всех сил на ось х.
Sх=0; Нс-Нв-Rцс×cos32°=0
Нс=266+27585×085=5005 кН.
Строим эпюры М Н и Q.
Участок 1. 0z1015 (слева)
Н1×sin76°= -Rв×cos14°-Нв×cos76°
М1-Rв×z1-Мв+Нв×sin76×z1×cos76°
При z1=0; М1=Мв=2212 кН×м.
При z1=015; М1=1711×015+2212+2212-2212×097×024×015=23914 кН×м.
Участок 2. 0z202 (слева)
Н2×sin30°= -Rв×cos60-Нв×cos30
М2-Rв (z+015)-Мв+266×sin30°×cos30° (z1-015)
При z2=0; М2=23914 кН.
При z2=02; М2= -1711(02+015)+2212=75 кН×м.
Участок 3. 0z307 (справа)
При z3=0; М3=-Мс = 744 кН×м.
При z3=07; М3= -5005×07+744= 39365 кН×м.
Участок 4. 0z4193 (справа)
М4+Мс+Rс×z4+Нс×(06+z3×sin24)=0
При z4=0; М4=744-178×0-5005×06=39365 кН×м.
При z4=193; М4=744-178×106-5005×(06+106×041) = 2073 кН×м.
М5+Мс+Rс(z+106)+Нс(10346+z5×sin24°)-Gс×z5
При z5=0; М5=744×178×106+5005×10346=2073 кН×м.
При z5=087; М5= 744-178(106+087)-5005(10346+087×036)-71×087=
Участок 6. 0z6027 (справа)
М6+Мс+Rс×(193+z6)+Gк×(087+z6)+Нс(139-z6×sin30)=0
При z6=0; М6=744-178×193-71×08-5005×139=54 кН×м.
М6= 744-178(193+027)-71×(087+027)-5005(139-027×05)= 75 кН
По полученным данным строим эпюры Н Q и М. Расчет на прочность будем вести в наиболее опасных сечениях I-I и II-II так как в этих сечениях присутствуют элементы ослабляющие конструкцию.
Усилия в опасных сечениях.
Рисунок 2.13 – Площадь опасного сечения
F=2×20×2-2×5=70 см2=70×10-4 м2
где b=300-2×20=260 мм.
Момент сопротивления сечения Wх определим по формуле
Нормальное напряжение возникающее в сечении
Касательные напряжения возникающие в сечении данного вида не возникают.
Условие выполняется следовательно в сечении I-I прочность обеспечена.
Рисунок 2.14 – Площадь сечения
F=2×26×1+2×28×1=108 см2=108×10-4 м2
Момент сопротивления:
Нормальные напряжения:
Статический момент полусечения относительно оси х.
Касательное напряжение
Суммарные напряжения действующие в сечении
6.3 Расчет сварного шва
Расчет сварного шва стрелы.
Сварные швы рассчитываются на действие касательных и местных сминающих напряжений. Необходимая толщина шва при этом определяется по формуле
где Sn – статический момент полусечения;
b - коэффициент для ручной сварки b=08;
– расчетное сопротивление условного шва для толщин деталей 20 мм из стали 20 =195 МПа.
Примем толщину шва Кf=8 мм.
Расчет сварного шва щеки стрелы
Расчет шва воспринимающего осевую нагрузку и изгибающий момент ведем по формуле
d - толщина свариваемых деталей d=20 мм;
N – растягивающее усилие N=1001 кН;
М – изгибающий момент М=23914 кН;
81 МПа 195 МПа. Условие выполняется.
Эксплуатационный раздел.
1 Разработка мероприятий технического обслуживания машины
В нашей стране принята система планово-предупредительного технического обслуживания и ремонта землеройно-транспортных машин. Основные положения этой системы в строительстве определены СНиП III-1-76 и «Рекомендациями по организации технического обслуживания и ремонта строительных машин» содержащими виды и периодичность выполнения технических обслуживании и ремонтов планирование и учет данные по трудоемкости технических обслуживании и ремонтов строительных машин.
Виды технического обслуживания ремонта и периодичность их проведения а также состав и порядок выполнения работ по техническому обслуживанию и текущему ремонту указываются заводом-изготовителем в эксплуатационной документации по каждой модели машины.
Техническое обслуживание машин выполняют после каждой смены и через определенные периоды рабочего времени Наработку или время между двумя последовательно проводимыми техническими обслуживаниями одного вида называют периодичностью технического обслуживания. В зависимости от периодичности и объема работ различают ежесменное плановое и сезонное техническое обслуживание.
Виды технического обслуживания периодичность их выполнения и перечни работ для тракторов установлены ГОСТ 20793—75.
В зависимости от конкретных условий использования машин допускается отклонение (±10%) от установленной периодичности выполнения технических обслуживании.
При обслуживании машин работающих в агрегате с тракторами следует пользоваться двумя перечнями работ по техническому обслуживанию: по трактору и по машине.
От работы планово предупредительной системы зависит надёжность работы машин а также качество и сроки выполнения предусмотренных работ машинным парком организации.
Таблица 3.1 – Исходные данные
Расчётная начальная Нф наработка машино-час
На базе шагающего двигателя
2 Порядок построения перспективного (годового) графика ТО
Исходными данными для расчета является и начальная расчетная наработка Нф машины в часах. Перспективный график ТО (план-график) строится на планируемый год. Таким образом построим план-график на июнь 2005 года для шагающего манипулятора.
Для построения план-графика ТО для заданной марки машины необходимо определить наработку Нпл на планируемый год:
где Тн - номинальная наработка машины за год ч.;
Ки - коэффициент использования рабочего времени в течение года.
Коэффициент Ки для машин используемых круглогодично принимается в зависимости от вида машин равным: для бульдозеров - 095.
Номинальную наработку машины за год определяем по формуле:
Тн = (365 - (104 + 10))tсмy(3.2)
где 365 – количество календарных дней в году;
4 – количество воскресных и субботних дней в году;
– количество праздничных дней;
tсм – длительность рабочей смены tсм=8 ч;
y – число смен в сутки у=2.
Таким образом получаем:
Тн = (365 - (104 + 10))8 2 = 4000 ч.
Рассчитаем Нпл для шагающего манипулятора:
Нпл = 4000 095 = 3800 ч;
Фактическую наработку со времени проведения последнего капитального и текущего ремонтов ТО-2 и ТО-1 на начало планируемого года определяют путём деления наработки от последнего капитального ремонта (или с начала эксплуатации для новой машины) Нф на периодичность соответствующего вида технического обслуживания или ремонта Тп.
Тп – периодичность проведения соответствующего вида ТО ч;
Таблица 3.2 – Данные для построения плана-графика ТО машин.
Планируемая наработка Нпл машино-час
Количество технических обслуживаний и ремонтов отдельных видов за год определяем по формуле:
Нпл – планируемая годовая наработка;
Кп – количество всех видов ТО и ремонтов с периодичностью большей периодичности того вида по которому ведётся расчёт (при расчёте капитального ремонта Кп = 0).
Расчёты по формуле (3.4) ведём в последовательности: К Т ТО-2 ТО-1 К=5760м.-ч. Т=960 м.-ч. ТО-2=240 м.-ч.ТО-1=60 м.-ч. Результаты округляем до целых в меньшую сторону. Таким образом для шагающего манипулятора:
Nк = 34005760; т.е. Nк = 3400 ч
Следовательно для данного шагающего манипулятора в течение года требуется провести: капитальный ремонт – 1 текущих ремонтов – 3 ТО-2 – 12 ТО-1 – 48.
После этого строим план-график ТО для заданной марки машины. Для построения плана графика необходимо на оси координат отложить расчётную начальную наработку Нф а на конец каждого месяца по вертикали – плановую наработку для данной машины на конец месяца Нпл.
Для определения Нпл надо готовую плановую наработку распределить по месяцам года пользуясь известными рекомендациями и занести полученные значения в таблицу 3.3 [11].
Таблица 3.3 – Распределение годовой плановой наработки по месяцам
для шагающего манипулятора
Имея данные таблицы 3.3 определим плановую наработку на конец каждого месяца и занесём эти данные в таблицу 3.4.
Таким образом для каждой машины получаем наработки на концы месяцев планируемого года.
По полученным данным строится план график технического обслуживания. На графике шкалы периодичности технического обслуживания и наработки строятся в одинаковом масштабе.
Таблица 3.4 - Распределение годовой плановой наработки на концы месяцев
Фактическую наработку на начало месяца со времени проведения последнего ремонта или ТО определяют аналогично как было показано выше для плана-графика. При этом расчётной формулой будет следующая:
где – фактическая наработка машины за период с начала года до рассматриваемого месяца (июля); если план работы строго выполняется то будет складываться из цифр помещённых в таблице 4 в строке Нпл
По приведённой выше формуле (3.5) рассчитаем наработку машины. Таким образом перспективный график технического обслуживания – это документ для планирования ТО а месячный график ТО – это документ для оперативного учёта наработки и определения фактических сроков проведения отдельных видов технического обслуживания для шагающего манипулятора:
; т.е. NТО-2 = 120 ч
3 Определение порядкового дня месяца проведения ТО и ремонта
Порядковый рабочий день месяца Dтор в котором начинается проведение ТО и ремонта машин определяется по формуле:
где Кдр – число рабочих дней в планируемом месяце;
Nср.м. – наработка со времени проведения ТО или ремонта м.-ч;
Нпл.м. – планируемая наработка м.-ч.
4 Определение годовой трудоемкости технического обслуживания
Для определения трудоемкости необходимо знать количество ТО каждого вида по марке машин и трудоемкости ТО каждого вида.
По установленным нормативам трудоемкости ТО и ремонта и их количеству подсчитывают затраты труда на ТО по каждой марки машин за год и суммируя их получают общие затраты труда (трудоемкости).
Трудоемкость ТО ( чел.-ч.) для каждой марки машин определяется:
где- число машин данной марки;
;;- соответственно числа ТО-1 ТО-2 СОi - машины данной марки i=12 .
;;- соответственно трудоемкость ТО-1 ТО-2 СО – для данной марки машины.
5 Определение числа рабочих для проведения ТО
Потребное число рабочих ПТО подсчитывают по формуле:
где Ф – фонд времени одного рабочего;
КИ – коэффициент использования рабочего времени
Фонд времени (Ф) определяют по выражению
Ф=(ДК – Д) × tсм (3.9)
где ДК – число календарных дней в году (365);
Д – число выходных праздничных и опускных дней;
tсм – продолжительность смены мастера-наладчика.
Фонд времени: Ф=(365 – 140) × 8 = 1800 ч.
Потребное число рабочих:
Коэффициент технической готовности и коэффициент использования машины:
Коэффициент технической готовности КТГ характеризует уровень надежности машины а также качество и своевременность проведения ТО и ремонтов и совершенство применяемой системы обслуживания и ремонта для одной машины
где ДР – число рабочих дней в году;
Дтор – число рабочих дней на техническое обслуживание ремонт и устранение технических неисправностей.
Коэффициент использования Ки определяется по формуле (3.11) Он характеризует уровень организации использования машинного парка предприятия.
Для единичной машины
гдеДР – потери рабочих дней по техническим организационным и др. причинам.
Коэффициент использования находится в приделах:
Коэффициент технической готовности для шагающего манипулятора:
Руководствуясь перспективным графиком можно прогнозировать и устранять неисправности машины вовремя не дожидаясь серьезных поломок. и ТО.
1 Обоснование внедрения средств автоматизации
Широкое распространение электронных систем защиты манипуляторов связано с рядом их эксплутационных достоинств к которым в первую очередь следует отнести простоту настройки обслуживания и ремонта относительно невысокую стоимость. Благодаря развитой и доступной элементной базе обеспечивается работа электронных узлов в широком диапазоне температур не требующая термостатирования.
Использование микропроцессорных средств в аппаратуре систем защиты манипуляторов обеспечивает повышение безопасности и производительности их работы благодаря повышению точности задания грузовой характеристики и снижению психофизических нагрузок на оператора.
Внедрение микропроцессорных ограничителей позволяет снизить стоимость разработки и производства модификации аппаратуры под различные марки манипуляторов с большим набором сменного оборудования повысить информационную насыщенность приборных панелей уменьшить потребляемую мощность размеры обеспечить задание защитных характеристик с погрешностью не более 06% а за счет отображения параметров (вылета стрелы высоты подъема рабочего органа и так далее) с погрешностью 05-1% и почти вдвое увеличить время безотказной работы.
В зарубежной и отечественной практике число разновидностей систем автоматической защиты манипуляторов достаточно велико. Они отличаются функциональными точностными и другими технико-экономическими и эксплуатационными показателями конструктивными особенностями и применяемой элементной базой.
2 Принцип действия и устройство ограничителя нагрузки манипулятора
При ликвидации чрезвычайных ситуаций часто возникают ситуации которые могут привести к перегрузке манипулятора. Для предотвращения таких ситуаций разработан микропроцессорный ограничитель нагрузки манипулятора.
Общие принципы построения микропроцессорных ограничителей манипуляторов представлены структурной схемой на рисунке 4.1. В состав ограничителя входят средства получения информации блок обработки данных БОД блок управления сигнализации и индикации БУИ.
Средства получения информации включают в себя счетчики В1 В4 угла наклона стрелы a или управления гуска b и датчик В2 длины стрелы L. Датчики В3-1 В3-2 нагрузки фиксируют давление Рп в поршневой и Рш в штоковой плоскостях гидроцилиндра подъема стрелы.
Датчик В5 используется для организации автоматического управления (угол g поворота стрелы в плане) а счетчики В6 В7 не задействованы.
Блок обработки данных включает центральный процессор ЦП постоянное запоминающее устройство ПЗУ с программами и табличными данными оперативное запоминающее устройство ОЗУ аналого-цифровой АЦП и дискретно-цифровой преобразователи схемы мультиплексирования: аналоговую МА и цифровую МЦ схемы кодирования вариантов работы и схемы отключающей логики СОЛ с выходными усилителями дискретных сигналов управления.
Кроме того блок обработки данных содержит ряд дополнительных аппаратных средств таких как блок питания с преобразователем и стабилизатором напряжения ПСН входными и выходными фильтрами Ф и схемой контроля СКН систему термостатирования содержащую датчик температуры ДТ терморегулятор ТР и нагревательные элементы ТЭН схему гальванической развязки СГР нормирующие усилители: фильтры НУ калибратор К. Схема управления механизмами манипулятора СУМ осуществляет общее отключение ОО отключение телескопа ОТ поворота ОТ подъема стрелы ОПС.
Блок управления сигнализации и индикации содержит средства управления с помощью которых устанавливаются требуемый вариант работы в зависимости от вида оборудования крана (переключатель ПВ) реализуются режимы автокомпенсации и тестирования выбирается инициируемый параметр (орган управления ОУ). На лицевую панель БУИ выведены также отсчетные цифровые и индикационные средства ИС.
В качестве нормирующего усилителя НУ в схеме используется усилитель марки М2УСЭ0081А с коэффициентом усиления до 200 выполненный на основе прецизионных операционных усилителей типа К140УД14-7.
Технология восстановления детали
В процессе эксплуатации машины происходит износ деталей и узлов. Теряется работоспособность агрегата. Современный технологический уход снижает изнашиваемость деталей но при достижении определенного состояния необходима их замена или восстановление. Процесс восстановления деталей состоит из следующих операций.
–исправление центровочных отверстий;
–термическая обработка – отжиг;
–токарная обработка поверхности детали под наплавку;
–наплавка поверхностей;
–токарная обработка наплавленного слоя под шлифовку;
–термическая обработка – закалка ТВЦ;
–шлифование до номинального размера.
1 Исправление центровочного отверстия
Центральные отверстия на деталях являются базой для ряда операций обтачивания нарезания резьбы шлифования и др.
При ремонтных работах сохранившимися центровочными отверстиями пользуются как базами для обработки из точеных или поврежденных поверхностей.
Скорость резания определяется по формуле
Глубина резания: t= мм.
где Cv – коэффициент зависящий от геометрии и материала сверла Cv=7 [8];
d – диаметр сверла мм;
q – показатель степени q=04;
m – показватель степени m=02;
yv – показатель степени yv=07;
T – стойкость инструмента Т=8 мм;
Кv – общий поправочный коэффициент скорости резания.
Таблица 5.1. Вид дефектов вала
Способ установления дефекта и средство контроля
По рабочему чертежу
Допустимый без ремонта
Вмятины от роликов износ шейки
Подставив в формулу получение значения при n=300 обмин получим
Основное время при центрировании определяется по формуле
где to – основное время мин;
S – подача инструмента ммоб S=02 ммоб;
n – число оборотов детали в мин n=300 обмин = 5 обс.
Определяем вспомогательное время по формуле
tв=tо×13=015×13=0195 мин = 117 с
где 13 – коэффициент.
Для двух отверстий основное время будет равно
t = tо×2 = 015×2 = 03 мин = 18 с.
2 Токарная обработка
До наплавки восстановленные поверхности подвергается черновому точению. Это делается для увеличения шероховатости поверхности и исправления ее геометрии после износа. При обработке применяем токарные резцы из твердого сплава Т15К6 передний угол g=110° задний l=120° резец токарный подрезной.
Выбираем число подходов I=1 подачу S=08 ммоб глубину резания t=15 мм затем определяем скорость резания по формуле
где Cv – коэффициент поперечного сечения Cv=350 [8];
КV – общий поправочный коэффициент.
КV = Кmv × КnV × КUV × КyV × КOV
Кmv – коэффициент на качество обработки материала Кmv =093;
КnV – коэффициент учитывающий состояние поверхностей заготовки КnV =08 [8];
КUV – коэффициент на инструмент материала КUV =09;
КyV – коэффициент учитывающий угол в плане КyV =09;
КOV – вид обработки КOV =10.
КV = 093×08×09×09×10=0602.
Определим необходимое число оборотов шпинделя по формуле
где n – число оборотов шпинделя;
d – диаметр обрабатываемой детали.
Корректируем число оборотов по паспорту станка. Получим фактические обороты:
n1ф = 1600 обмин = 26 обс.
n2ф = 800 обмин = 13 обс.
n3ф = 800 обмин = 13 обс.
Определим фактическую скорость резания по формуле .
Представив фактические значения в формулы получим:
Для первого перехода:
Определим основное время обработки по формуле
где tо – основное время обработки. Мин;
L – длина обрабатываемой поверхности;
n – частота вращения детали обмин;
Тогда Tо=tо1+ tо2+ tо3=0062+02+0023=0285 мин = 171 с.
Определяем вспомогательное время по переходам оно дается на установку и снятие детали на отвод и подвод инструмента и его смену на время связанное с переходом.
Установить деталь весом 088 кг в самоцентрирующийся патрон.
С поджатием центром задней бабки и снять переустановить деталь по карте 51 позиция 8 позиция 2.
Изменить величину подач и одним рычагом карты 61 код 31.
Изменить число оборотов шпинделя двумя рычагами карта 61 позиция 2.
Время на переход карты 60 лист 1 позиция 3.
Продольное перемещение суппорта. Карта 60 позиция 2.
t= 017 мин позиция 30 t= 081 м тогда
Тв1= 054+006+0014+015+017+081=123 мин =738 сек.
Изменить число оборотов шпинделя карта 61 позиция 2 t= 006 мин =36 с.
Изменение детали штангенциркулем карта 61 позиция 16 015 мин.
tв3 = 006+015 = 021 мин = 126 с.
Вспомогательное время операции
tв =tв1+ tв2+ tв3= 123+058+021 =202 мин =1212 с.
Для восстановления выбираем метод автоматической вибродуговой наплавки. Автоматическая вибродуговая наплавка производится на вибрирующую деталь (вращающаяся с помощью специальной наплавочной головки. Выбираем наплавочную головку для автоматической наплавки типа НИИЛТУАНЖ-6.
Для улучшения формовочного направляемого слоя металла и предохранения поверхности от окисления применяем предназначенный для механизированной сварки и наплавки углеродистых и низколегированных сталей флюс и низколегированных сталей флюс марки АН-348-А ГОСТ 9087-69.
Выбираем силу тока 220 А напряжение 20 В размах вибрации – 1. скорость подачи проволоки 15 ммин шаг наплавки 3 ммоб.
Толщина наплавляемого слоя зависит от величины износа и припуска на механическую обработку до наплавки 15 мм и после наплавки 16 мм. Таким образом общая толщина направляемого слоя составит 5 мм на сторону.
Скорость наплавки определяется по формуле
где V – скорость наплавки ммин;
d – диаметр электродной проволоки мм;
Vn – коэффициент перехода проволоки в наплавленном металле к=09;
h – заданная величина наплавляемого слоя;
d – коэффициент учитывающий отклонение фактической площади сечения наплавленного слоя от площади четырехугольника с высотой n:
Число оборотов деталей обеспечивающие получение наплавленного слоя заданной толщины определим по формуле:
где n – число оборотов.
Определим основное время наплавки:
Определим вспомогательное время по формуле:
Тв = То ×13 мин.(5.8)
Первый переход: Тв1 = 13 ×13 =128 мин.
Второй переход: Тв2 = 82 ×13 = 1065 мин.
Третий переход: Тв3 = 27 ×13 = 35 мин.
Тв=Тв1+Тв2+Тв3=128+1065+35=1543 мин.
Операционное штучное время определяем по формуле:
Тш=То+Тв=122+1543=2763 мин.
4 Токарная обработка
Поле наплавки производим токарную обработку поверхности I II.
Оборудование токарной винторезной станок 1К62. Инструмент – резец проходной упорный правый и левый с пластинками твердого сплава Т15К6.
Скорость резания определяем по формуле
Определяем необходимое число оборотов по формуле
Третий переход: n3=100. Назначаем число оборотов для всех переходов nф=800 обмин.
Определяем основное время по переходам
Первый переход: обточить на 355.
Второй переход: обточить под шлифовку на 38е8
Тo=018+163+05=231 мин.
Определим вспомогательное время по переходам
Первый переход: по карте 51 61 позиция 2 tв1=0923 мин;
Второй переход: tв2=025 мин;
Третий переход: tв3=057 мин.
Тв=Тв1+Тв2=131+1743=3051 мин.
5 Токарная (чистовая) обработка
Станок токарно-винторезной 1К62. Инструмент – резец проходной упорный правый и резец канавочный с пластинками твердого сплава Т15К6. классика круглая М2415 ГОСТ 2173-51 из стали У10.
Определим скорость резания:
Определим необходимое число оборотов шпинделя:
Назначаем фактическое число оборотов по паспорту станка:
Первый переход: обточить под нарезание резьбы и снять фаску 1545.
Второй переход: проточить канавку на диаметр 21.
Третий переход: нарезать резьбу М2415 классикой.
Определим основное время по переходам по формуле
где nф – число оборотов станка при нарезке nф =80 обмин;
n1 – число оборотов станка при обратном ходе n1 =125 обмин;
i – число применяемых плашек i = 1.
Основное время операции:
Тo=to1+to2+tо3=0992+021+0535=1737 мин.
Определение вспомогательного времени:
Первый переход: по карте 51 позиция 8 и 2
tуст=057 мин. tв1=223 мин.
Тв=tуст+tв1+tв2+tв3=057+223+0923+2973=6696 мин.
Штучное время операции
Для шлифования детали выбираем круглошлифовальный станок модели 3м153. Диаметр шлифуемой поверхности 35 мм. Выбор шлифуемой поверхности шлифовального круга по карте 2 стр. 623 [7].
Материал детали закаливания – закаленная сталь 35. Выбираем шлифовальный круг диаметром 500 мм с характеристикой абразивного материала: зернистость твердость связка структура.
Круг ПП5003220324А40СМ1-715 ГОСТ 2424-75. Определяем припуск под шлифовку шеек вала по таблице 11-4. Для диаметра 30-50 мм при шлифовке в центрах закаленной стали для длины вала 200 мм для индивидуального производства величина припуска умножается на коэффициент К=12 тогда величина припуска 2а=04×12=048 мм принимаем 05.
Скорость вращения круга 35 ммс. Определим режим резания при окончательном шлифовании с продольной подачей наружных цилиндрических поверхностей деталей из стали по карте 6 стр. 628 [7].
Скорость и число оборотов детали Диаметр шлифовальной поверхности 35 мм.
Скорость вращения Vб=22-35 ммин.
Число оборотов детали nб =250 обмин = 416 обс.
Продольная подача на ход стола Stх в ммхода.
Определим основное время обработки с продольной подачей
где L – длина обработки
где Вк – ширина шлифовочного круга.
n – припуск на диаметр мм;
nj – число оборотов детали в мин;
Sв – подача на ширину шлифования;
К – коэффициент учитывающий время на создание первоначального натяга в системе определяется по карте 9 стр. 633 К=14.
Определим вспомогательное время
Время на установку детали по карте 15 позиция 2 стр. 639 [7] в трехкулачковый патрон с поджатием центром tуст=028 мин.
Вспомогательное время связанное с переходом; измерения микрометром карта 17 tперех=055 мм тогда вспомогательное время равно
Тв=tуст+tперех=028+055=083 мин.
Безопасность и экологичность проекта
1 Безопасность труда
С целью проведения успешного и наиболее эффективного процесса автоматизации и механизации строительных работ необходимо провести надежную подготовку работ. Она включает в себя: подготовку персонала и рабочего места установку и монтаж оборудования.
В строительной организации наметившей применение манипулятора проходят соответствующую квалификационную подготовку инженерно-технические работники и рабочий персонал по обслуживанию и эксплуатации. Обучение проводится на курсах повышения квалификации специалистами НИИ занимающегося решением этой проблемы.
Здесь необходимо отметить что работы по эксплуатации манипуляторов и роботов в строительстве только начинается поэтому многие вопросы существуют только в теоретическом плане но их нужно решать и практически. Это относится и к конструктивным материалам нормативным документам и так далее. Подготовка заключается в изучении и освоении вопросов устройства средств роботизации организации работ по внедрению манипулятора основ эксплуатации и техники безопасности.
Лица не прошедшие специальной подготовки не допускаются к работе. Подготовка рабочего места предусматривает проведение работ по подготовке коммуникаций систем связи оснащения контрольно-информационными устройствами и непосредственно оснащения рабочего места специальными устройствами.
Оснащение контрольно-информационными устройствами позволит соблюдать технику безопасности производства работ и получить необходимые сведения о функционировании манипулятора.
Рабочее место должно обеспечить возможность выполнения манипуляционных действий в соответствии с характерными действиями манипуляторов.
В свою очередь к монтажным работам относятся и работы по замене рабочих органов. В данном проекте многофункционального манипулятора меняют захватные устройства для различных видов работ.
Замена рабочего оборудования отдельных модулей демонтаж перед транспортировкой и монтаж на новом месте осуществляется в соответствии с «Техническим описанием и инструкцией по эксплуатации» или инструкцией по монтажу и демонтажу. Для монтажных и демонтажных работ рекомендуется создавать специальные бригады имеющие опыт работы по монтажу и демонтажу манипуляторов.
Внедрение манипуляторов и роботов в целом способствует снижению числа несчастных случаев на производстве так как они заменяют человека в первую очередь при выполнении опасных и вредных операций. С другой стороны средства роботизации представляют собой устройства повышенной опасности и могут стать причинами травматизма. При изучении причин несчастных случаев связанных с роботами и манипуляторам установлено что в основном они происходят из-за столкновения посторонних рабочих с исполнительными устройствами манипулятора. Во время выполнения операций обучения наладки и при ремонте манипуляторов встречаются ситуации когда в процессе исполнения определенной команды происходят сбои в траектории движения исполнительного устройства. Для таких ситуаций требуется особенно высокая степень обеспечения безопасности. Недостаточность подготовки оператора также может привести к несчастному случаю.
При автоматизации строительства основные мероприятия направлены на предотвращение соприкосновения средств механизации с человеком применения устройства экстренного останова и обучения персонала.
Центральное место в строительстве по созданию безопасной техники и технологии производственных и вспомогательных процессов принадлежит стандартизации.
В совокупности стандарты безопасности классифицируются на четыре группы и все они должны учитываться при создании средств автоматизации строительства.
Первые из них регламентируют санитарно-гигиенические требования к рабочей зоне при работе с веществами с опасными и вредными свойствами.
Во вторую классификационную группу входят стандарты к конструкции оборудования и элементам (рабочим органам средствам контроля сигнализации защитным устройствам и т.п.).
Третья группа относится к размещению элементов технологических систем к рабочим местам и методам контроля выполнения требований безопасности.
Четвертая группа определяет технические требования к конструктивным эксплутационным и гигиеническим свойствам средств защиты.
При эксплуатации манипуляторов на строительно-монтажных работах на работающих воздействуют следующие факторы: двигающиеся устройства и их подвижные части а также объекты манипулирования повышенная запыленность и загазованность рабочей зоны и зоны обслуживания расположение проводов воздушной линии электропередач в рабочей зоне повышенная температура поверхностей расположение рабочего места на высоте повышенная или пониженная температура воздуха в зоне обслуживания повышенный уровень шума и вибрации на рабочем месте недостаточная обзорность опасный уровень напряжения в электрической цепи замыкание которое может произойти через тело человека загроможденность и недостаточная освещенность зоны обслуживания физические и нервно-психологические перегрузки оператора (машиниста).
К работе с манипуляторами и роботами допускаются лица не моложе 18 лет прошедшие медицинское обслуживание специальный курс обучения по безопасности труда и получившие удостоверения на право обслуживания манипуляторов.
Манипуляторы предназначенные для эксплуатации в условиях повышенной запыленности и температуры воздуха при наличии взрыво- и пожароопасных смесей и в других неблагоприятных условиях производственной среды должны иметь соответствующее защитное исполнение. Захватное устройство манипулятора удерживает объект манипулирования при внезапном отключении напряжения (питания) если падение объекта может привести к воздействию на человека опасных производственных факторов.
Манипулятор имеет регулятор снижающий скорость перемещения его исполнительных устройств до 03 мс если операции обучения и наладки манипулятора требуют пребывания обслуживающего персонала в зоне рабочего пространства.
Для повышения безопасности труда оператора в конструкцию манипулятора введены устройства обеспечивающие получение и передачу на пульт управления информации: о режиме работы о срабатывании блокировок манипулятора о наличии сбоя в работе манипулятора о наличии движения исполнительных устройств.
Электрооборудование манипулятора оснащено пусковой аппаратурой исключающей независимо от положения органов управления самопроизвольное включение оборудования при восстановлении внезапно исчезнувшего напряжения.
Манипулятор оснащен средствами защиты (ограничительными предохранительными блокирующими сигнализирующими и др.) исключающими возможность воздействия на обслуживающий персонал опасных и вредных производственных факторов при работе в режимах обучения и использования программы. Эти средства не должны ограничивать технологические возможности манипуляторов и удобство их обслуживания.
В конструкции манипулятора предусмотрены средства обеспечивающие остановку исполнительных устройств: при выходе манипулятора за пределы рабочего пространства. Выход манипулятора за пределы рабочей зоны необходимо ограничить жесткими упорами которые выдерживают нагрузку с учетом динамических и статических усилий.
Блокирующие устройства манипулятора при работе в одном из режимов исключает возможность работы в другом режиме и самопроизвольное переключение с одного режима на другой. Система управления манипулятора имеет устройство аварийного останова срабатывающее орт команды оператора при нарушении работоспособности манипулятора ведущем к возникновению опасных факторов независимо от режима работы в том числе при внезапном отключении любого вида питания которое используют в обслуживаемом оборудовании.
При срабатывании устройства аварийного останова исключается возможность воздействия на обслуживающий персонал опасных производственных факторов. Срабатывание устройства аварийного останова обеспечивается специальной командой подаваемой оператором (машинистом). До начала работы манипулятора за ограждение удаляются посторонние предметы. При невозможности удаления из-за ограждения они должны устанавливаться вне досягаемости их исполнительными устройствами манипуляторов.
Перед началом работы проводится первая проверка функционирования частей комплекса. При этом блокировочные устройства должны срабатывать в соответствии с гидравлической пневматической и электрической схемами.
Обслуживающему персоналу запрещено находиться в рабочем пространстве манипулятора. Неполадки и аварийные ситуации возникающие в процессе эксплуатации ежемесячно регистрируются оператором или наладчиком в специальном журнале форму которого устанавливает предприятие и утверждает главный инженер.
Запрещено выполнять ремонтные работы связанные с обслуживанием манипулятора а также по присоединению и отсоединению рабочего органа манипулятора без отключения питания.
При выполнении работ в рабочем пространстве манипулятора в системе включения питания должен быть вывешен плакат с предупреждающей надписью «Не включать!».
1.1 Требования к условиям труда оператора
Технический уровень машины определяется не только совершенством их технических показателей но и уровнем обеспечения условий труда и безопасности оператора.
К числу регламентируемых показателей относятся уровень концентрации пыли параметры вибрации в вертикальном и горизонтальном направлении на сиденье оператора микроклимата в кабинете (температура влажность скорость движения воздуха в зоне дыхания перепад температур в кабине) освещенность участков поля и дороги внутренние размеры кабины расположение органов управления (рулевого колеса рычагов механизмов поворота опорных площадок часто используемых панелей и др.) силы сопротивления перемещению органов управления средства отображения информации обзорность с рабочего места оператора и др.
1.2 Техника безопасности при эксплуатации шагающей машины
При приеме рабочего он проходит вводный инструктаж при котором ему объясняют общие правила техники безопасности. После вводного инструктажа рабочий проходит первичный инструктаж у инженерно-технического персонала. При этом рабочего знакомят с правилами пуска работы и остановки машины обращению с электрооборудованием средствами огнетушения и индивидуальными приспособлениями. В процессе обучения поступающий знакомится с инструкцией по технике безопасности относящейся к его рабочему месту.
Внеплановый инструктаж проводят для проверки знаний по технике безопасности.
На производительность рабочего очень сильно влияют метеорологические условия:
Температура. Она должна быть оптимальной и должна быть больше 25°С.
Влажность. При большой влажности а если еще повышенная температура то возможен парниковый эффект при котором резко уменьшается работоспособность.
Запыленность. Если в воздухе очень большое количество пыли то возможно получить ряд профессиональных заболеваний.
Скорость движения воздуха и излучение от нагретых предметов также влияют на утомляемость и работоспособность оператора при эксплуатации машины.
Звукоизоляция машины (шагающей) – это прежде всего выхлопная труба.
Безопасная эксплуатация машины на тягово-транспортных работах обеспечивается падением таких мероприятий как создание благоприятных условий труда повышение квалификации обслуживающего персонала обеспечение технического надзора за техникой со стороны инженерно-технических работников и ремонта со стороны обслуживающего персонала.
Для надежности работы систем управления необходимы резервные цепи электропитания от электрогенератора к силовому приводу машины.
Аварии могут произойти вследствие ослабления болтовых соединений потери шплинтов гаек шайб резкое повышение напряжения в участках цепи в следствии короткого замыкания и т.д. необходимо регулярно проверять и подтягивать эти соединения.
Элементы механической конструкции при работе с перегрузками или под воздействиями вибраций могут подвергаться усталостному разрушению.
2 Меры безопасности при изготовлении шагающего движителя
Анализ вредных и опасных факторов возможных при изготовлении проектируемого объекта производится в соответствии с ГОСТ 12.0.003-74 ССБТ.
К вредным и опасным факторам можно отнести:
загрязнение воздушной среды;
неправильно спроектированное освещение;
неблагоприятные метрологические условия;
высокий уровень шума и вибраций; несоответствие нормам безопасности конструкций технологического оборудования и подъемно-транспортных устройств технологической оснастки;
неисправность технологического оборудования технологической оснастки;
опасность поражения электрическим током;
2.1 Пожаробезопасность
На шагающей машине на раме устанавливается огнетушитель а также на корпусе трактора укрепляется шансовый инструмент входящий в состав ЗИПа для первичного пожаротушения.
Выхлопная труба направлена вертикально вверх. На ней предусмотрена установка искро-пламягасителя.
Топливные баки изолированы от корпуса машины резиновым покрытием во избежании утечки электричества.
При ремонте манипулятора а также при монтаже и демонтаже стрелу весом 630 кг поднимают с помощью строп.
В качестве строп применяются стальные проволочные канаты которые. При проектировании и перед установкой на грузоподъемную машину должны быть проверены на прочность расчетом. Расчет производится по формуле
где Р – разрывное усилие каната в целом принимаемое по сертификату Н;
S – наибольшее натяжение ветви каната с учетом КПД полиспаста Н;
k – коэффициент должен соответствовать указаниям таблицы.
Расчет стропов из стальных канатов должен производиться по указанной формуле с учетом числа ветвей канатов n и угла наклона их к вертикали a.
Рисунок 2.1 – Схема строповки
При известном весе G H; натяжение S Н возникающее в каждой ветви определяется по формуле
где при a=45° коэффициент m при a=45° равен 142.
Выбираем k для строп прикрепленных к грузу при помощи крюков серьг колец без его отгибания равным 6.
Диаметр каната выбираем для двух ветвей и угла a=45° равным d=115 мм.
По ГОСТ 3064-80 выбираем канат 11Б-Г-В-Н-МК-Т-87000 ГОСТ 3064-80.
Находим напряжения ветви если G=630 кг.
Проверяем условие прочности если Р=87000 Н
Условие прочности соблюдается следовательно канат выбран верно.
Строительство и эксплуатация магистральных трубопроводов и предотвращение последствий чрезвычайных ситуаций связаны с воздействием на окружающую среду. Во время их строительства и ремонта существенно нарушается поверхность земли в различных формах и активизируются эрозионные процессы на талых грунтах криогенные – на многолетомерзлых русловые деформации – на переходах через реки рельефообразования - на горных участках и в пустынях. В эксплутационный период отрицательное влияние на природу распространяется на более длительное время и проявляется в основном загрязнением окружающей среды вследствие утечки транспортируемых продуктов.
Возникновение криогенных явлений в многолетомерзлых грунтах проявляющихся в нарушении динамики сезонного промерзания и оттаивания в измерении температуры и водного режима мерзлых пород связано с нарушением почвенно-растительного покрова колесами и гусеницами строительной техники ранней весной летом или поздней осенью когда поверхность земли находится в талом состоянии. Следы их не исчезают а с каждым годом разрастаются. Сначала на месте колеи появляется промоина потом канава а впоследствии овраг или озеро. Благодаря использованию в данном проекте широких лыж достигается низкое давление на грунт что позволяет избежать негативных последствий разрушения почвы описанных выше.
Основные транспортные земляные и строительно-монтажные работы надо производить в период устойчивых отрицательных температур во избежании или сведения к минимуму повреждения почвенного покрова. С этой же целью нельзя допускать передвижение транспортных средств и строительной техники по целине и зимним дорогам поздней весной и ранней осенью когда деятельный слой земли либо не оттаял либо не промерз на всю глубину.
По окончании строительных работ поврежденные участки поверхности земли необходимо тщательно рекультивировать.
Технико-экономическое обоснование проекта
При механизации и автоматизации процессов в строительстве в основу эффективности закладываются как экономические так и социальные факторы. При этом автоматизация должна быть не самоцелью а эффективным средством повышения производительности труда улучшения качества производства работ снижения затрат тяжелого монотонного опасного и вредного труда.
Эффективность применения данного манипулятора обуславливается:
–рациональностью выбора объекта автоматизации;
–степенью соответствия конструкции объекта манипулирования условиях их манипулирования;
–наличием и степенью подготовки персонала к эксплуатации манипулятора;
–суммой затрат на приобретение или на разработку и изготовление монтаж наладку и эксплуатацию манипулятора;
–временем внедрения манипулятора;
–коэффициент использования.
1 Характеристика базовой и новой техники
В комплект сменных рабочих органов манипулятора входят: экскаваторный ковш планировочный ковш захват для перемещения цилиндрических объектов захват для подачи к месту монтажа ножницы для перекусывания арматуры устройство для присоединения к рабочему оборудованию гидромолота с трамбующей плитой.
Многофункциональный манипулятор со сменным оборудованием позволит заменить экскаватор погрузчик и др.
Таблица 7.1. Характеристика базовой и новой техники
Многофункциональный манипулятор МЭО-3341 на базе высокопроходимого транспортного средства ТСВ-51 со сменным рабочим оборудованием
Многофункциональный манипулятор МЭО-3341 на базе высокопроходимого шагающего движителя со сменным рабочим оборудованием
Грузоподъемность 5 т.
Скорость передвижения0..20 мс
Мощность двигателя 147 кВт
2 Определение капитальных вложений
2.1 Стоимость новой техники
Збт – стоимость базовой техники – 1200000 руб.;
mбт – масса базовой техники – 10000 кг.;
mнт – масса новой техники – 8000 кг.;
Кудор – коэффициент удорожания – 12.
2.2 Расчет производительности и фонда времени работы
Грузовая производительность техники
П=Эч×Тг×Кпв ед.прод.год (7.2)
Эч – эксплутационная производительность тчас;
Тг – годовой фонд времени работы часгод;
Кпв – внутренние потери времени.
Для новой техники Кпв =09.
Коэффициент Кпв учитывает внутренние потери времени по организационным причинам неучтенные в эксплуатационной производительности.
Годовой фонд времени работы техники
где Дв – число выходных и праздничных дней в году Дв=115;
Дп – количество дней затрачиваемых на перебазирования в течение года;
Дм – средняя продолжительность простоя по метеорологическим условия;
Тсм – продолжительность смены Тсм=8ч – для пятидневной рабочей недели;
Ксм – коэффициент сменности работы техники согласно табл. 2 прил. 1.
Др – время нахождения техники во всех видах технического обслуживания (ТО) текущего (ТР) и капитального ремонта (КР) приходящиеся на 1 час работы бар.дн.ч.
Годовой фонд времени работы техники:
Время нахождения техники во всех видах ТО ТР КР:
где Пр – среднее время пребывания техники в ТО и ТР рабочие дни;
До – среднее время доставки в ремонт и обратно и ожидания ремонта дни (ТР=10 КР=20);
А – количество ТО ТР и КР за межремонтный цикл;
m – число разновидностей ТО и ТР за межремонтный цикл;
Тц – межремонтный цикл Тц=6060 ч.
Время нахождения базовой техники в ТО ТР КР:
Подставляя имеющиеся данные в соответствующие формулы получим.
Годовая производительность базовой техники
П1=554×1577×08=69893 тгод
Годовая производительность новой техники:
П2=554×1577×09=78629 тгод
Годовой объём выполненной работы в рублях определим по формуле
где с – стоимость единицы выполненной работы сБТ =19 руб. сНТ=155 руб.
Подставляя значения в 7.5 получим:
3 Определение годовых текущих затрат
Годовые текущие (эксплутационные) затраты определяем по формуле
И=Зр+Кр+Ар+Эр+Зт+См +Пб (7.6)
где Зр – затраты на заработную плату рабочих;
Кр – затраты на капитальный ремонт;
Ар – амортизационные отчисления на реновацию;
Эр – затраты на технические осмотры и текущий ремонт;
Зт – затраты на топливо;
См – затраты на смазочные материалы;
Мг – затраты на масло;
Пб – затраты на перебазировку.
Затраты на заработную плату рабочих:
Зр1=Кн×Кс×Тг×Чт(7.7)
Зр2=Кн×Кс×Тг×Чт(7.8)
где Кн – накладные расходы по зарплате Кн=11;
Кс – коэффициент учитывающий дополнительную зарплату и отчисления в фонд социального страхования Кс=16;
Чт – часовая тарифная ставка Чт1=74 руб (4 разряд ) Чт=85 руб.( 5 разряд)
Затраты на заработную плату рабочих:
Зр1=11×16×1577×74=205388 руб.
Зр2=11×16×1577×85=235919 руб.
Годовые затраты на капитальный ремонт:
где Нк – норма отчислений на капитальный ремонт Нк=8%.
Годовые амортизационные отчисления на реновацию:
Затраты на технические осмотры и текущий ремонт:
где Кн – нормы отчислений на ТО и ТР Кн=4%.
Годовые затраты на топливо для ДВС:
Зт=103×10-6×Цт×Мн×Тг×Км×Кв×Кд (7.15)
где Цт – цена топлива Цт=18000.рубт;
Мн – номинальная мощность двигателя Мн=147 кВт;
Рт – расход топлива при номинальной мощности.
Км - коэффициент использования мощности двигателя Км = 06;
Кв - коэффициент двигателя по времени Кв = 08;
Кд - коэффициент учитывающий изменение расхода топлива в зависимости от степени использования двигателя по мощности Кд = 106.
Годовые затраты на топливо:
Зт1 = 103×10-6×11×18000×1577×147×240×06×08×106 = 577310 руб.
Зт2 = 103×10-6×11×18000×1577×125×240×06×08×106 = 490910 руб.
Годовые затраты на масло для гидросистемы
Мг = Кн×Ег×Р×Цм×Мд××10-3 (7.16)
где Ег – вместимость гидросистемы дм3;
Р – объемная масса масла кгдм3;
Цм – оптовая цена рубкг;
Мд – коэффициент доливок масла. Мд=15;
Тс – периодичность смены масла.
Годовые затраты на масло:
Мг1 = 11×50×0865×25×15× = 2930 руб.
Мг2 = 11×30×0865×25×15× = 1758 руб.
Годовые затраты на смазочные материалы:
где n – коэффициент перехода от годовой стоимости расхода топлива к стоимости масла n=025.
См1 = 11×025×577310 = 174639 руб.
См2 = 11×025×490910 = 135000 руб.
Годовые затраты на перебазировку зависят от стоимости одной перебазировки количества дней затрачиваемых на перебазировки в течение года и продолжительности одной перебазировки:
гдеСп — стоимость одной перебазировки;
Дп — количество дней затрачиваемых на перебазировку в течение года;
tп — продолжительность одной перебазировки.
Рассчитаем укрупнённо стоимость перебазировки на 10 км при стоимости одной перебазировки Сп = 70 руб. км.
Сп = 700·10 = 700руб.
Тогда по формуле 7.21 имеем:
Годовые текущие (эксплутационные) затраты :
И1 =205388+105600+198000+48000+577310+2930+174639+9800 = 1321667. руб.
И2 =235919+101376+177400+46080+490910+1758+135600+9800 = 1198843 руб.
Вычислим годовые текущие затраты потребителя без учёта отчислений на реновацию:
- для базовой техники:
И1' = 1321667 - 198000=1123667 руб. ;
- для новой техники:
И2' =1198843 – 177400 = 1021443 руб.
Таблица 7.1 – Калькуляция себестоимости эксплуатации техники
Амортизационные отчисления
Масло для гидросистемы
Перебазировка техники
Доля оплаты труда в объёме выполненных работ в процентах определяется по формуле
( 7.19) где Кд – коэффициент учитывающий долю оплаты труда в годовом объёме работ КдБТ =0156; КдНТ = 0 198
Подставляя значения в 7.22 получим:
Фонд оплаты труда определяется по формуле
Фот = V × Фот% (7.20)
Подставляя значения в 7.23 получим:
ФОТБТ = 69893 × 0294 = 205485 руб
ФОТНТ = 78629 × 0301=2366732 руб .
4 Расчет экономического эффекта
Потенциальный экономический эффект в расчёте на одну машину определяем по формуле
где Р = Нр ·10-2 =015 - доля амортизационных отчислений на реновацию;
Ен = 015 - нормативный коэффициент экономической эффективности.
Тогда по формуле 7.24 имеем:
Годовой экономический эффект определяем по формуле
где Ен – нормативный коэффициент экономической эффективности Ен=015;
П1 П2 - годовая производительность базовой и новой техники;
И1 И2 – годовые текущие затраты базовой и новой техники;
З1 З2 – капитальные вложения в базовую и новую технику соответственно.
Срок окупаемости капитальных вложений:
Коэффициент экономической эффективности определяем по формуле
Т – срок окупаемостилет.
Подставляя значения в 7.24 получим
Таблица 7.2 - Технико-экономические показатели
Балансовая стоимость руб
Производительность годовая тгод
Себестоимость продукции годовая руб
Годовой объём работ руб
Фонд оплаты труда рабочих руб
Годовой экономический эффект руб
Срок олупаемости дополнительных капитальных затрвт лет
Коэффициент эффективности
При разработке данного проекта ставилась цель модернизировать шагающий манипулятор а именно возможность применения его в качестве сменного оборудования грузоподъёмного устройства.
Для достижения поставленной цели были решены следующие задачи:
- проведен аналитический обзор существующих конструкций шагающих движителей и на его основе был сделан выбор рабочего органа;
- были рассчитаны рабочие параметры узлов и деталей механизма;
- было произведено экономическое сопоставление с базовой техникой и сделан вывод о целесообразности применения данной разработки;
- разработан технологический процесс восстановления детали;
- разработан комплекс мер обеспечивающих безопасные условия труда.
Технико-экономический анализ показывает что годовой экономический эффект внедрения составляет 288624 руб.при сроке окупаемости 02 года и коэффициент экономической эффективности 5.
Список используемой литературы
Андрианов Н.А. Исследование и диагностирование роботов: учебник для вузов Н.А.Андрианов Д.С. Бальжанов А.Я. Погребняк Н.В. Умнов. – М.: Наука 1980 – 210 с.
Анурьев В.И. Справочник конструктора-машиностроителя. Том 1. В.И.Анурьев. - М.: Машиностроение 1979 - 728 с.
Беркман И.Л. Универсальные многофункциональные манипуляторы: учебник для вузов И.Л.Беркман. – М.: Высшая школа. 1985 – 321 с
Бессонов А.П. Вопросы механики движителей шагающих машин: труды Всероссийской. конференция по механике и управлению движением шагающих машин А.П. Бессонов Н.В Умнов. – Волгоград. 1988 – 345 с.
Богомолов Н.Е. Многомашинная система управления мобильным роботом: сборник научных трудов всероссийской конференции по робототехническим системам Н.Е.Богомолов Ю.М.Лазутин В.С.Ярошевский . – Воронеж. 1984 – 326 с.
Брискин Е.С. Об общей динамике и повороте шагающих машин. Проблемы машиностроения и надежности машин. №6 1997. с. 33-39.
Брискин Е.С.Основы расчета шагающих машин высокой опорной проходимости. Часть 1: учебное пособие Н.Е Богомолов Ю.М.Лазутин В.С.Ярошевский. – Волгоград 1994 - 113 с.
Брислин Е.С.Тяговая динамика шагающих машин с ортогональными движителями. Проблемы машиностроения и надежности машин Е.С. Брислин В.М.Соболев - №3 1990. с. 28-34.
Жога В.В. Исследование динамики шагающего движителя. Совершенствование средств и метод расчета изделий машиностроения: учебное пособиеВ.В.Жога – Волгоград 1988. – 78 с.
Жога В.В. Система показателей качества шагающих транспортных машин: инженерный журнал В.В.Жог.а.- №5. – М.: Машиностроение 1997-142 с.
Панкратов С.А. Основы расчета и проектирования металлических конструкций строительно-дорожных машин: учебник для вузов С.А. Панкратов. – М.: Машиностроение. 1989 – 354 с
Промышленные роботы в машиностроении: альбом схем и чертежей под ред. Ю.М.Соломенцева – М.: Машиностроение 1987 – 237с.
Режимы резания металлов: справочник под ред. Ю.В. Пороновского и др. – М.: НИИТ Автопром 1995 - 456 с.
Релнев В.И. Комплексная механизация и автоматизация строительно-монтажных работ на основе разработки и внедрения в народное хозяйство строительных манипуляторов и роботов: учебник для вузов В.И.Релнев – Л.: Строймздат 1987 - 24 с.
Справочник технолога машиностроителя. Том 1. под ред. Косиловой А.Г. – М.: Машиностроение 1972. 694 с.
Справочник технолога машиностроителя. Том 2. под ред. Косиловой А.Г. и Малова А.Н. – М.: Машиностроение 1972 - 568 с.
Френкель Г.Ю. Роботизация процессов в строительстве:учебник для вузов Г.Ю.Френкель. – М.: Стройиздат 1987 - 173 с.
Заключение.doc
проанализированы существующие конструкции манипуляторов их достоинства и недостатки пути совершенствования и улучшения;
проведен литературный поиск и на его основе сформулированы цели и задачи дипломного проекта;
доказана необходимость внедрения модернизированных узлов;
рассчитан манипулятор и произведён расчёт модернизированных элементов;
разработана принципиальная электронная схема управления шагающим манипулятором;
описаны необходимые условия для обеспечения техники безопасности при работе шагающего манипулятора;
приведён технологический процесс восстановления детали шагающего манипулятора;
рассчитан и приведён примерный экономический эффект от модернизированного манипулятора;
Приведённое технико-экономическое обоснование говорит о том что модернизованный шагающий манипулятор вполне рентабелен и его использование прибыльно а окупаемость манипулятора очень высока. Годовой экономический эффект составил 202073 руб а срок окупаемости 03 года.
тема.doc
Волгоградского государственного архитектурно-строительного университета
Кафедра Строительных
и дорожных машин и оборудования
Заведующий кафедрой
Расчетно-пояснительная записка
к дипломному проекту
Тема: ПРОЕКТ МОДЕРНИЗАЦИИ ШАГАЮЩЕГО МАНИПУЛЯТОРА
Состав дипломного проекта:
Расчетно-пояснительная записка на 95 стр.
Графическая часть на 10 листах.
Руководитель дипломного проекта: к.т.н. доц.
Консультанты: к.т.н. проф.
Нормоконтроль: ст.препод.
ЗАДАНИЕ.doc
Волгоградского государственного архитектурно-строительного университета
Кафедра Строительные и дорожные машины и оборудование
Декан факультета к.т.н.
НА ВЫПОЛНЕНИЕ ДИПЛОМНОГО ПРОЕКТА
Тема дипломного проекта Проект модернизации шагающего манипулятора__
Руководитель проекта
Грузоподъёмность - 6 т.
Высота преодолеваемого препятствия - 1500 мм.
Максимальный вылет стрелы-5000 мм .
Дополнительные данные
Манипулятор.Технические условия
Нормативные документы стандарты (ГОСТы и т.д)
Перечень вопросов подлежащих разработке
Аналитический обзор конструкции манипуляторов
Разработка компоновки поворотного механизма
Разработка автоматической системы ограничения нагрузки манипулятора
Разработка маршрута восстановления детали и наладки
Эксплуатация и техническое обслуживание
Безопасность и экологичность проекта
Технико - экономическое обоснование проекта
Перечень графического материала (с точным указанием обязательных чертежей)
Манипулятор шагающий (общий вид) лист 1 (ф-т А1)
Платформа шагающая (сборочный чертеж) лист 1 (ф-т А1)
Манипулятор. Схема рабочих положений лист 1 (ф-т А1)
Механизм поворотный (сборочный чертеж) листов 2 (ф-т А1)
Гидроцилиндр (сборочный чертёж) лист 1 (ф-т А1)
Деталировка лист 1 (ф-т А1)
Перспективный график ТО и ремонта лист 1 (ф-т А1)
Схема ограничителя грузоподъёмности манипулятора лист 1 (ф-т А1)
Технология восстановления детали лист 1 (ф-т А1)
Технико-экономическое обоснование проекта лист 1 (ф-т А1)
Консультанты по проекту
По какому разделу проекта
Технология восстановления детали
Заключение кафедры о допуске к защите дипломного проекта
гидроцилиндр_спец2.cdw

платформа_шагающая.cdw

гидроцилиндр.cdw

манипулятор_шагающий.cdw

транспортного средства
Скорость передвижения
Габаритные размеры машины
Глубина преодолеваемого борда
Техническая характеристика манипулятора
Максимальный вылет стрелы
Технические требования
Размеры для справок.
Манипулятор шагающий
схема_ограничителя.cdw

механизм_поворота_спец1.cdw

экономика_2вариант.cdw

эксплуатации шагающего манипулятора
Технико-экономические показатели
Балансовая стоимость
Производительность годовая
Себестоимость продукции годовая
Фонд оплаты труда рабочих
2Годовой экономический эффект
Срок окупаемости дополнительных
Коэффициент эффективности
Затраты на оплату труда
Амортизационные отчисления
Затраты на масло для гидросистемы
Затраты на смазочные материалы
Перебазировка техники
Технико-экономическое
экономика.cdw

эксплуатации шагающего
Технико-экономические показатели
внедрения новой техники
Затраты на смазочные
Затраты на перебазировку
Балансовая стоимость
Годовой экономический
Технико-экономическое
лист2.cdw

платформа_шагающая_спецификация.cdw

механизм_поворота.cdw

Частота вращения поворотного круга
Редуктор двухступенчатый
передаточное отношение 28
Гидродвигатель 210.5
Габаритные размеры механизма поворота
Технические требования
Размеры для справок.
Редуктор залить маслом индустриальным
И-Г-А-46 ГОСТ 17479-4-87.
манипулятор_шагающий_спецификация.cdw

ТО.cdw

манипулятора на 2009 год
ПЕРСПЕКТИВНЫЙ ГРАФИК ТО И РЕМОНТА ШАГАЮЩЕГО МАНИПУЛЯТОРА НА 2009 год
восстановление_дет.cdw

Оборудование (наименование
Токарно-винторезный 1К 62
Наименование операции
Зачистка центровых отверстий
Сталь 35 ГОСТ 1050-88
Точение поверхности I
Точение поверхности II
Точение поверхности III
Наименование агрегата
Сварочный преобразователь
Обточить поверхность II
Обточить поверхность III
Нарезать резьбу М24х1
Шлифование поверхности II
Кругло-шлифовальный станок 3М153
Технологический процесс
торсион.cdw

Коэффициент смещения
*Размер для справок.
Манипулятор_раб_положения.cdw

гидроцилиндр_спец1.cdw

механизм_поворота_спец2.cdw

Рекомендуемые чертежи
- 24.04.2014