Проект кузнечно-рессорного отделения РММ


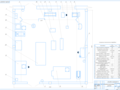
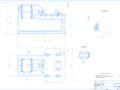
- Добавлен: 25.01.2023
- Размер: 810 KB
- Закачек: 3
Описание
Состав проекта
![]() |
![]() ![]() ![]() ![]() |
![]() ![]() ![]() ![]() |
![]() |
![]() |
![]() ![]() ![]() |
![]() ![]() ![]() |
Дополнительная информация
общий вид.cdw

Рабочее давление воздуха
Максимальное усилие при рабочем давлении
Исправлено.cdw

Огнетушитель углекислотный
Стенд для испытания рессор
Стенд для разборки и сборки рессор
Бабка ладильная для правки рессор
Гидравлический пресс
Обдирочно-шлифовальный станок
Ванна для мойки рессорных листов
Ванна для охлаждения деталей
при закалке листов в масле
Верстак для рессорщика на чугунных ножках
Ванна для охлаждения деталей при
Камерная электрическая печь для нагрева
Машина для формовки и закалки
Стеллаж для рессорных листов
Центробежный вентилятор к горну
Кузнечный горн на один огонь
Наковальня двурогая на подставке
Пневматический ковочный молот
Вертикально-сверлильный станок
Спецификация технологического оборудования
Копия Мой курсач2.docx
Учреждение образования
«Гомельский государственный политехнический колледж»
-360531 “Машины и оборудование лесного хозяйства и
лесной промышленности»
“Диагностика и техническое обслуживание машин лесного хозяйства и лесной промышленности ”
Проект кузнечно-рессорного отделения РММ обслуживающего: МАЗ-53362 - 90МАЗ-630300 - 70трактора МТЗ-80 - 50
Принял руководитель проекта
Председатель цикловой комиссии
фамилия имя отчество
По дисциплине: «Диагностика и техническое обслуживание машин лесного хозяйства и лесной промышленности»
Тема курсового проекта __ Проект кузнечно-рессорного отделения РММ.
Исходные данные 90 автомобилей МАЗ-53362 70 автомобилей МАЗ-630300 и 50 тракторов МТЗ-80. Среднесуточный пробег автомобилей-140 км. Коэффициент технической готовности-aт =09. Категория условий эксплуатации - третья
Содержание проекта Срок выполнения
Пояснительная записка
Дата окончания проекта
Преподаватель-руководитель курсового проекта
Задание принял к исполнению
Перевозки автомобильным транспортом предполагают использование подвижного состава (автомобилей и автопоездов) находящегося в исправном техническом состоянии.
Исправное техническое состояние означает полное соответствие подвижного состава нормам определяемым правилами технической эксплуатации и характеризует его работоспособность.
Работоспособность автомобиля оценивается совокупностью эксплуатационно-технических качеств - динамичностью устойчивостью экономичностью надежностью долговечностью управляемостью и т.д. – которые для каждого автомобиля выражаются конкретными показателями. Чтобы работоспобность автомобиля в процессе эксплуатации находилась на требуемом уровне значение этих показателей длительное время должны мало измениться по сравнению с их первоначальными величинами.
Однако техническое состояние автомобиля как и всякой другой машины в процессе длительной эксплуатации не остается неизменными. Оно ухудшается в следствии изнашивания деталей и механизмов поломок и других неисправностей что приводит результате к ухудшению эксплуатационно-технических качеств автомобиля.
Изменение указанных качеств автомобиля по мере увеличения пробега может происходить также в результате несоблюдения правил технической эксплуатации или технического обслуживания автомобиля.
Основным средством уменьшения интенсивности изнашивания деталей и механизмов и предотвращения неисправностей автомобиля то есть поддержания его в должном техническом состоянии является своевременное и высококачественное выполнение технического обслуживания.
Под техническим обслуживанием понимают совокупность операций (уборочно-моечные крепежные регулировочные смазочные и др.) цель которых – предупредить возникновение неисправностей (повысить надежность) и уменьшить изнашивание деталей (повысить долговечность) а последовательно длительное время поддерживать автомобиль в состоянии постоянной технической исправности и готовности к работе.
Даже при соблюдении всех мероприятий изнашивание деталей автомобиля может приводить к неисправностям и к необходимости восстановления его работоспособности или ремонта. Следовательно под ремонтом понимается совокупность технических воздействий направленных на восстановление технического состояния автомобиля (его агрегатов и механизмов) потерявшего обслуживание и ремонта автомобилей.
Основной документ согласно которому производится ТО и ремонт на автопредприятиях положения о ТО и ремонте ПС автомобильного транспорта. Согласно этого документа ТО производится планово предупредительно через определенный пробег.
Существуют следующие виды ТО и ремонта: ЕО – ежедневное обслуживание направлено в первую очередь на проверку узлов безопасности перед выходом и по возвращению с линии.
ТО-1 – первое техническое обслуживание проводится через 3-5 тыс. км. ТО-2 – второе ТО проводится через 10-15 тыс. км. СО – сезонное обслуживание проводится весной и осенью. ТР – текущий ремонт ремонт направленный на восстановление технически неисправного состояния исключая базовые детали.
Одним из направлений позволяющих повысить техническое состояние парка автомобилей при минимальных расходах на строительство производственной базы для ТО и текущего ремонта является строительство и организация баз централизованного обслуживания и ремонта автомобилей. База централизованного обслуживания обеспечивает ТО и ТР несколько автохозяйств не имеющих собственной производственной базы. Такая форма организации позволяет сконцентрировать средства механизации производственных процессов повысить производительность труда и качеств работ.
Технологический раздел
1 Расчёт годовых производственных трудозатрат на СТО
1.1 Расчет нормативов ТО и ремонта
1.1.1 Определение коэффициентов корректирования нормативов ТО и ремонта
Основными документами определяющими организацию и порядок работы по ремонту двигателей являются: технический кодекс установившейся практики ТКП 248-2010 ” ТЕХНИЧЕСКОЕ ОБСЛУЖИВАНИЕ И РЕМОНТ АВТОМОБИЛЬНЫХ ТРНСПОРТНЫХ СРЕДСТВ. Нормы и правила проведения“ утвержденный постановлением Министерства транспорта и коммуникаций Республики Беларусь 13.05.2010 г.№36 и инструкции заводов - изготовителей. Для расчета используем заданный подвижной состав: МАЗ-630300 – 70МАЗ-53362 – 90трактор МТЗ-80 – 50 шт
Определяем коэффициент корректирования норм периодичности технических обслуживаний в зависимости от условий эксплуатации автомобилей:
К периодичности ТО = К1 К3 (1.1)
Где: К1- коэффициент корректирования норм периодичности технических обслуживаний в зависимости от условий эксплуатации
К1 = 08 – для третей категории эксплуатации
К3- коэффициент корректирования норм периодичности технических обслуживаний в зависимости от природно-климатических условий
где К31=10 – для умеренного климата К32 = 09;
К периодичности ТО = 08 09=072
Определяем коэффициент корректирования норм циклового пробега (до капитального ремонта) в зависимости от условий эксплуатации автомобилей:
Кцикла = К1 К2 К3 (1.3)
где К1- коэффициент корректирования норм норм циклового пробега в зависимости от условий эксплуатации
К1 = 08 – для третей категории эксплуатации (за пределами пригородной зоны булыжник)
К2 - коэффициент корректирования нормативов в зависимости от модификации подвижного состава
К2 =110- для грузовых автомобилей
К3 - коэффициент корректирования нормативов в зависимости от природно-климатических условий
К3 = 09 – для умеренного климата
Кцикла = 08 110 09 =0792
Определяем коэффициент корректирования норм трудоемкости технического обслуживания:
Ктрдоемкости ТО = К2 К42 К5 К6 (1.4)
где К2 - коэффициент корректирования нормативов в зависимости от модификации подвижного состава;
К2 =110- для грузовых автомобилей;
К4 - коэффициент корректирования нормативов в зависимости от пробега с начала эксплуатации;
К42 = 12 –для грузовых автомобилей;
К5 - коэффициент корректирования нормативов в зависимости от количества обслуживаемых и ремонтируемых машин;
К5 = 10 (120 автомобилей две группы технологически совместимых машин);
К6 - коэффициент корректирования нормативов в зависимости от периода эксплуатации (в течение года).
Тогда для грузовых автомобилей МАЗ:
Ктрдоемкости ТО = 110 12 10 1104 =145
Определяем коэффициент корректирования норм трудоемкости текущего ремонта в зависимости от условий эксплуатации автомобилей:
Ктрдоемкости ТР = К1 К2 К3 К4 К5 К6 (1.5)
где К1- коэффициент корректирования норм трудоемкости текущего ремонта в зависимости от условий эксплуатации
К1 = 08 – для второй категории эксплуатации (за пределами пригородной зоны булыжник)
К4 - коэффициент корректирования нормативов в зависимости от пробега с начала эксплуатации
К4 = 12 –для грузовых автомобилей
К5 - коэффициент корректирования нормативов в зависимости от количества обслуживаемых и ремонтируемых машин
К5 = 10 (120 автомобилей две группы технологически совместимых машин)
К6 - коэффициент корректирования нормативов в зависимости от периода эксплуатации (в течение года)
Таким образом для грузовых автомобилей:
Ктрдоемкости ТР =0811009121011375= 1081.
1.1.2 Расчет количества технических обслуживаний в цикле
Таблица 1.1 Нормативные данные по ТО для расчета производственной программы для автомобилей без учета условий эксплуатации
Периодичность ТО в тыс. км.
Трудоемкость ТО в чел. часах
Норма пробега до КР тыс. км.
Грузовой автомобиль МАЗ-53362
Грузовой автомобиль МАЗ-630300
Таблица 1.2 Нормативные данные по ТО для расчета производственной программы для автомобилей с учетом коррекции
Пояснения к таблице 1.2 Нормативные данные по ТО для расчета производственной программы для автомобилей с учетом коррекции определяются путем умножения нормативных данные по ТО для расчета производственной программы для автомобилей без учета условий эксплуатации (таблица 1.1) на соответствующие коэффициенты корректирования нормативов(п. 1.1.1.1)
Количество технических обслуживаний в цикле рассчитываем по следующим формулам:
N2ц = Lц L2ц – 1 ; (1.6)
N1ц = Lц L1ц – ( 1 + N2ц ); (1.7)
где Lц – цикловой пробег т. км;
L1ц L2ц – пробег в километрах или работа в моточасах между ТО-2 и ТО.
Таблица 1.3 Данные для трактора МТЗ-80
Периодичность выполнения ТО и ремонтов мото-ч
Количество ТО и ремонтов в цикле с начала эксплуатации до первого КР
Трудоемкость одного ТО чел.-ч; удельная трудоемкость ТР чел.-ч100 мото-ч
Продолжительность одного ТО ч; удельная продолжительность ТР ч
1.1.3 Расчет количества ТО в году
Определяем коэффициенты перехода от цикла к году.
г = Lг Lц = Дкг Lcc φп Lц ; (1.8)
где Дкг – число календарных дней в году (принимаем 253 дня);
Lcc – среднесуточная пробег автомобилей
Lц – пробег до капитального ремонта
φп – плановый коэффициент использования машины (090 ).
Для МАЗ-53362 и МАЗ-630300:
г = 253 090 140 475200 =00670;
г = 253 090 7 5760 =0277;
Определяем количество тех. обслуживаний в году
Количество сезонных обслуживаний в году:
Количество технических обслуживаний N2 в году:
N2 = N2ц г Мс (1.10)
Количество технических обслуживаний N1 в году:
N1 = N1ц г Мс (1.11)
где Мс – списочное количество машин данной марки.
Для МТЗ-80 рассчитывается ещё и количество технических обслуживаний N3 в году:
N3 = N3ц г Мс (1.12)
N2 = 265 00670 90=159795
N1 = 55 00670 90=25795
N2 = 265 00670 70=159795
N1 = 55 00670 70=25795
N2 = 18 0277 50=2493
N1 = 72 0277 50=9972.
1.2 Расчёт годовых трудозатрат на СТО
1.2.1 Расчет трудозатрат на проведение ТО
Трудозатраты по сезонному обслуживанию:
Тсо.г. = Nсо.г. tсо Пп (1.13)
Трудозатраты по второму техническому обслуживанию:
Т2.г. = N2г. t2 Пп (1.14)
Трудозатраты по первому техническому обслуживанию:
Т1.г. = N1г. t1 Пп (1.15)
где Пп – коэффициент учитывающий повышение производительности труда (Пп = 097);
t2 t1 – нормативы трудозатрат на одно техническое обслуживание соответствующего вида чел. часа (из таблицы 1.2).
tсо – удельная трудоемкость сезонного обслуживания принимается
в объеме 20% от удельной трудоемкости t2
tсо = 02120 =24 чел. часа
tсо = 02175 = 35 чел. часа
Тсо.г. = 180 24 097 = 41904 чел. часа
Т2.г. =159795 120 097 = 186001 чел. часа
Т1.г. = 25795 47 097 = 1176 чел. часа.
Тсо.г. = 140 35 097 = 4753 чел. часа
Т2.г. = 159795 175 097 = 27125 чел. часа
Т1.г. = 25795 903 097 = 22594 чел. часа.
Тсо.г. = 100 80 097 = 776 чел. часа
Т3.г. = 6925 180 097 = 120911 чел. часа
Т2.г. = 2493 120 097 =290185 чел. часа
Т1.г. = 9972 30 097 =290186 чел. часа.
Результаты расчетов сводим в таблицу:
Таблица 1.4 Трудоемкость технического обслуживания
Трудоемкость чел. часов
Автомобиль МАЗ-53362
Автомобиль МАЗ-630300
1.2.2 Расчет трудозатрат на проведение ТР
Расчет скорректированной удельной трудоемкости текущего ремонта автомобилей производим по формуле:
tр =К tн чел-ч1000км (1.16)
где tн – нормативная удельная трудоемкость определенная по таблице 1.2 чел-ч1000км
Таблица 1.5 Расчет удельной трудоемкости текущего ремонта автомобилей
Коэффициент корректирования трудоемкости ТР
Нормативная удельная трудоемкость Чел-ч1000км
Скорректированная удельная трудоемкость Чел-ч1000км
Расчет трудозатрат по текущему ремонту автомобилей производится по норме трудоемкости на каждые 1000 км пробега по формуле:
где Дрг – дни работы в год – 253 дня
lcc – среднесуточный пробег автомобиля в километрах (в мото-ч. для тракторов)
Мс – списочное количество машин данной марки
т - коэффициент технической готовности
tр – удельная трудоемкость по текущему ремонту на 1000 км пробега
(на 100 мото-ч. для тракторов)
Трудозатраты на проведение текущего ремонта равны:
Результаты расчетов сводим в таблицу
Таблица 1.6 Трудозатраты на ТР
Трудозатраты на ТР чел.ч
2 Расчет трудоемкости работ в кузнечно-рессорном отделении
Трудоемкость работ на данном участке расчитывается по формуле:
где -общие трудозатраты на ТР чел. ч;
В-процент вида работ %.
В кузнечно-рессорном отделении кроме работ по текущему ремонту проводятся дополнительные неучтенные работы объем которых составляет до 35% от объема всех ремонтных работ:
Тдоп = 03 чел. ч. (1.19)
Тдоп= 035·31009= 108532
Общий объем трудозатрат ремонтных работ в проектируемом участке кузнечно-рессорных работ:
Т общ = + Тдоп чел. ч. (1.20)
Т общ =31009+108532=418622 чел. ч.
3 Расчет штата рабочих
Явочное количество производственных рабочих рассчитывается по формуле:
где Ря – явочное количество рабочих
Т общ – общие годовые трудозатраты по диагностике чел.ч
Фн – номинальный годовой фонд времени одного рабочего час.
Фонд рабочего времени на год составил 2016часов.
Списочное количество рабочих определяется по формуле:
где Фд – действительный годовой фонд времени рабочего ч.
Действительный фонд времени рабочего называется фонд времени с учетом очередного отпуска и неявки на работу по уважительным причинам.
Действительный фонд времени одного рабочего определяется по формуле:
Фд = (Фн – tот ) (1.23)
где tот – отпуск который равен произведению количества дней отпуска на продолжительность рабочего дня
- коэффициент не выхода на работу по уважительным причинам 096
Фд = (2016-240) 096=1705 чел. ч.
Принимаем 3 человека на отделение.
4 Расчет и подбор оборудования
Основное оборудование рассчитывается а остальное подбирается по технологической необходимости.
Количество основного оборудования определяется по формуле:
где Т общ – общие годовые трудозатраты по диагностике чел.ч;
Фо- годовой фонд рабочего времени оборудования Фо= Фн = 2016 ч;
заг - коэффициент загрузки оборудования (07-09);
т.г. - коэффициент технической готовности оборудования 095
Фо = [365-(52 + 12)]8095 = 2295 ч.
Принимаем 2 единицы основного оборудования.
Для обеспечения качественного проведения работ по ремонту рессор и исходя из технологической необходимости подбираем еще дополнительно необходимое оборудование и сводим его в таблицу.
Таблица 1.5 Перечень технологического оборудования
Габаритные размеры мм
Занимаемая площадь м2
Ларь для кузнечного инструмента
Огнетушитель углекислотный
Стенд для испытания рессор
Стенд для разборки и сборки рессор
Бабка ладильная для правки рессор
Гидравлический пресс
Обдирочно-шлифовальный станок
Ванна для охлаждения деталей при закалке листов в масле
Ванна для мойки рессорных листов
Верстак для рессорщика на чугунных ножках
Ванна для охлаждения деталей при закалке в воде
Камерная электрическая печь для нагрева рессорных листов
Машина для формовки и закалки рессорных листов
Стеллаж для рессорных листов
Центробежный вентилятор к горну
Кузнечный горн на один огонь
Наковальня двурогая на подставке
Пневматический ковочный молот
Вертикально сверлильный станок
Итого площадь всего оборудования в проектируемом кузнечно-рессорном отделении составила 2736 м2.
5 Расчет площади кузнечно-рессорного отделения
Площадь То м2 определяем по формуле:
где fо – площадь занимаемая оборудованием м2;
К – коэффициент учитывающий проходы;
То = 2736 5 = 1368 м2 ;
Принимаем площадь То = 144 м2(12000х12000)
Производим компоновку технологического оборудования и вычерчиваем планировку кузнечно-рессорного отделения.
Организационный раздел
1 Описание технологического процесса ТО
Техническое обслуживание рессор осуществляется по следующей схеме:
Рессору необходимо разобрать в следующем порядке:
Зажать рессору в тиски в непосредственной близости от центрового болта.
Отвернуть гайки болтов хомутов вынуть болты и снять распорные втулки.
Отвернуть гайку центрового болта и осторожно отпускать тиски так как листы в стянутой рессоре находятся в напряженном состоянии.
Промыть керосином все листы рессоры и протереть.
Выявление неисправностей и дефектов рессор
У рессор могут быть следующие дефекты: поломка листов потеря упругости срезание центрового болта износ пальцев и втулок в ушках рессор и кронштейнах износ кронштейнов под торцами ушков рессоры. Для устранения дефектов снятую рессору разбирают листы промывают в щелочном растворе и подвергают контролю и сортировке. Годные для ремонта отправляются на дальнейшее обслуживание и ремонт а не годные в утиль.
Прессовые работы по восстановлению рессор
Прессовые работы по восстановлению и ремонту рессор имеют немаловажную роль на кузнечно-рессорном участке. Эти работы занимают примерно 4% из всех работ по ремонту рессор. Для изгиба полосового материала или изготовления проушин листов рессор на участке применяют различные стенды снабженные зажимным винтом для закрепления полосы. Рихтуют рессоры на специальных установках и прессах а также вручную в специально отведенном для этого месте. Прессовые работы применяются для выравнивания листов и других деталей рессор. Существует два метода прессования холодное и горячее. При горячем прессовании металл (заготовка) предварительно разогревается до высокой температуры после чего подается под пресс. Происходит деформация металла и придание ему нужной формы и размеров. Операций прессования может быть несколько в то числе и с промежуточным подогревом.При холодном прессовании происходит все то же самое но без разогрева металла.Для чего разогревают металл: В горячем состоянии предел прочности металла значительно снижается а предел текучести значительно увеличивается. В результате можно прикладывать гораздо меньшие усилия для пластической деформации заготовки. Недостатком данного способа (кроме энергозатратности) является коробление изделия после деформации - в процессе остывания.
Сверлильные работы по восстановлению рессор
Обработка отверстий занимает в общем объеме механической обработки значимое место так как большинство деталей и механизмов имеют круглые отверстия как крепежные так и посадочные. На сверлильные работы деталей рессор отводится примерно 3% от всего объема ремонтных работ. Сверление и растачивание - наиболее распространенные способы получения отверстия. Для получения отверстий под нарезание резьбы применяется развертывание и зенкерование. Для этих работ на участке устанавливается специальное сверлильное и фрезерное оборудование. На сверлильных станках могут выполнятся работы по сверлению ушек рессор накладок трубок хомутов и т.д. На фрезерных станках выполняются работы по расточке отверстий нарезанию резьбы болтов шайб стремянок и т.д.
Термические работы по восстановлению рессор
Термическую обработку рессорпроводят по одному из трех вариантов:
) нагрев под закалку с помощью ТВЧ с последующей изотермической закалкой; 2) печной нагрев и изотермическая закалка; 3) печной нагрев и обычная закалка в масле с последующим среднетемпературным отпуском.
) ТВЧзакалка происходит следующим образом: деталь которую следует закалить помещается в электромагнитное поле внутри медной трубки которая согнута по форме необходимой детали при этом индуктируются переменные токи высокой частоты они (токи) оттесняются к поверхности детали изнутри возникшим переменным магнитным током. Так как индуктированные токи на поверхности нагреваемой детали имеют очень высокую плотность то происходит быстрый нагрев поверхностного слоя. Изотермическая закалка Нагретую до закалочных температур деталь быстро переносят в закалочную среду имеющую температуру несколько выше температуры начала мартенситного превращения (например 250—300°С для углеродистых сталей) и выдерживают в течение времени необходимого для полного превращения переохлажденного аустенита. В результате получается структура нижнего бейнита.
)Нагрев производится в специальной печи при температуре 830 °С. Далее изотермическая закалка.
)Рессоры накаливают в печи. Температура закалки 830—870° С. После чего опускаются в масло нагретое до температуры не выше 60 °С. После чего рессора достается и происходит отпуск наибольший интервал между закалкой и отпуском допускается не более 4 ч Температура отпуска должна быть в пределах 480—520 °С. Охлаждают в воде температура которой не должна превышать 100 °С или на воздухе в закрытом помещении.
Рихтовочные работы по восстановлению рессор
Рихтовочные работы заключаются в том чтобы убрать все неровности листов и сделать их максимально ровными и пригодными для совмещения. Рихтуют ударами молотка по листу который опирают нанаковальню. Используемая для рихтовки наковальня должна обладать достаточной массой чтобы поглощать удар и иметь форму схожую с формой рихтуемой части детали. Рабочая поверхность наковальни должна быть гладкой чтобы не оставлять следов на поверхности листа.При рихтовке применяютсярихтовочные молотки называемые такжегладилками и молотки-кувалды. Молотки изготовляют из сталей причем их бойки закаливают и полируют. Утончение листа вызываемое обработкой молотком происходит тем быстрее чем сильнее наносимые удары. Так как объем металла остается постоянным то его утончение сопровождается удлинением которому препятствует металл необработанных молотком участков. В результате блокирования этой деформации происходит выпучивание поверхности листовой детали. Лучший эффект достигается в случае рихтовки легкими частыми ударами с малой вытяжкой металла чем при рихтовке сильными разрозненными ударами оставляющими следы на поверхности и сильную вытяжку металла. При наличии на рихтуемой детали складки рихтовку начинают с выправления этой складки до окончательной формы а затем рихтуют остальную часть детали. Качество выполненной рихтовки оценивается визуально и ощупыванием поверхности ладонью руки. Визуально наиболее легко контролируются выпуклые или вогнутые поверхности путем просмотра их под углом или сбоку. Для контроля плоских поверхностей применяют линейки.
Сборка рессор проводится в следующем порядке.
Отобрать требуемый комплект листов. Промазать поверхности листов графитной смазкой;
Подсобрать листы в соответствующем порядке и вставить в отверстие под центровой болт технологический стержень диаметром равным диаметру центрового болта;
Сжать в тисках центральную часть рессоры как можно ближе к стержню и вынуть его;
Вставить вместо стержня центровой болт головкой вниз и затянуть гайку моментом 44-46 Н-м;
Вставить распорные втулки и болты хомутов и затянуть их гайками моментом 12-18 Н-м;
Если хомуты без отверстий загнуть хомуты;
Освободить рессору из тисков и протереть ее от лишней смазки.
Собранные рессоры должны быть испытаны на стенде. Перед испытанием осуществляют осадку рессоры под определенной нагрузкой. Собранную рессору устанавливают на прессе и шпинделем нажимают на середину до полного выпрямления рессоры (стрела прогиба равна нулю). Затем рессору постепенно освобождают измеряют стрелу прогиба и еще раз нажимают на нее до выпрямления. Повторная осадка рессоры той же нагрузкой не должна изменить стрелу прогиба. При уменьшении стрелы прогиба рессора непригодна к эксплуатации. Величина нагрузки стрелы прогиба указана в технических условиях на ремонт сборку и испытание агрегатов и автомобилей.
2 Мероприятия по охране труда в отделении
2.1 Техника безопасности
При организации и выполнении кузнечно-рессорных работ должны соблюдаться требования ГОСТ 12.3.026—81 «ССБТ. Работы кузнечнопрессовые. Требования безопасности.
Рабочие выполняющие кузнечно-рессорные работы пользуются спецодеждой и средствами индивидуальной защиты в соответствии с установленными нормами. Куртка должна перекрывать поясную часть брюк а брюки верхнюю часть ботинок. Ботинки должны быть с гладким верхом и металлическим носком. Работать без рукавиц фартука и головного убора запрещается. Защитные очки применяются с небьющимися стеклами для предохранения глаз от поражения отлетающими частицами. При обработке нагретых добела поковок кузнецы и молотобойцы должны пользоваться очками со светофильтрами.
При ручной ковке должны соблюдаться определенные правила. Наковальню укрепляют на деревянной подставке и устанавливают так чтобы рабочая поверхность ее была горизонтальна. Расстояние между наковальней и горном должно быть не менее 15 м а от наковальни до прохода—не менее 2 м. Наковальню следует проверять на отсутствие трещин. При проверке наковальни «на удар» звук должен быть чистым звонким без дребезжания. Со стороны проходов для предохранения окружающих от возможного поражения отлетающей окалиной или частицами металла следует устанавливать щиты. Клещи выбирают с учетом размеров поковок чтобы при захвате зазор между рукоятками клещей был не менее 45 мм. Для прочного удержания обрабатываемых заготовок на рукоятки клещей следует надевать зажимные кольца (шпандыри).
Перед ковкой следует удалить окалину с заготовки металлической щеткой скребком или легким ударом. Окалину с нижнего бойка удаляют специальной щеткой (метлой). Воздухосдув окалины разрешается производить только тогда когда организованы прием ее в воздуховод и сбор в специальную тару. Наклеп с кузнечного инструмента следует снимать абразивным инструментом.
Перед началом работы на молоте следует проверить холостой ход педали исправность ограждения (блокировки) и прогреть бойки молота куском горячего металла зажимаемого между верхним и нижним бойками. С целью обеспечения более полного соприкосновения поковки с плоскостью нижнего бойка перед началом ковки предварительно на тихом ходу следует наложить на поковку боек бабы.
Во время работы подавать команды следует четко коротко и громким голосом; «Наложи» «Бей сильно» «Бей раз» «Бей до команды стой» «Стой» и др. Команды молотобойцу «Бей» может подавать только кузнец. По команде «Стой» кем бы она ни была подана молотобоец должен немедленно прекратить работу. Первые удары при ковке и последние удары при рубке должны быть слабыми.
При обрубке заготовок или заусенцев необходимо их направлять в безопасную для себя и окружающих сторону. Стоять против обрубаемого конца запрещается. Окончательно отделять отрубаемый кусок металла следует ударом после поворота заготовки на подрубную сторону.
Для изготовления ушков листов рессор или изгиба полосового материала необходимо применять специальные стенды оборудованные зажимными винтами для крепления полос металла. Рихтовать рессоры можно только на специальной установке снабженной концевым выключателем реверсирования электродвигателя. Перед обрубкой листы рессор следует нагревать. При клепочных работах запрещается поправлять заклепку после подачи жидкости в цилиндр плунжера гидравлической склепочной струбцины. Рихтовать рессоры вручную допускается только на специально отведенном для этого участке со средствами звукоизоляции с применением необходимого оборудования.
Ремонт рам должен производиться в устойчивом положении на подставках или на автомобиле с колесами установленном на козелках. Ремонтировать рамы установленные на ребро или вывешенные на подъемных механизмах запрещается.
На кузнечно-рессорном участке заготовки отходы поковки следует укладывать в тару на стеллажи и в штабеля в сторону от рабочего поста не загромождая проходов. Склепочные струбцины следует подвешивать к потолку или к специальному устройству. Рессоры подрессорники и листы рессор необходимо укладывать на стеллажи в горизонтальном положении.
Наковальня для ручной ковки должна быть укреплена на деревянной подставке усиленной железным обручем и установлена так чтобы ее рабочая поверхность была горизонтальной.
Клещи для удержания обрабатываемых поковок следует выбирать по размеру так чтобы при захвате поковок зазор между рукоятками клещей был не менее 45 мм.
Для прочного удержания обрабатываемых заготовок на рукоятки клещей следует надевать зажимные кольца (шпандыри).
Перед ковкой нагретый металл надо очищать от окалины металлической щеткой или скребком.
Заготовку необходимо класть на середину наковальни так чтобы она плотно прилегала к наковальне.
Кузнец должен держать инструмент так чтобы рукоятка находилась не против него а сбоку.
Команду молотобойцу "Бей" может подавать только кузнец. По команде "Стой" кем бы она не была подана молотобоец должен немедленно прекратить работу.
При рубке металла в том направлении куда могут отлететь обрубаемые куски металла должны устанавливаться переносные щиты.
При изгибе полосового материала или изготовлении ушков на рессорных листах должны применяться специальные приспособления (стенды) снабженные зажимными винтами для крепления полос.
Гидравлические струбцины для клепки должны надежно подвешиваться к потолку или специальному устройству.
Горячие поковки и обрубки металла необходимо складывать в стороне от рабочего места.
Перед началом работы на молоте следует проверить холостой ход педали исправность ограждения (блокировки) а также прогреть бойки молота куском горячего металла зажимаемого между верхним и нижним бойками.
Перед ремонтом рама автомобиля должна устанавливаться в устойчивое положение на подставки (козелки).
Рихтовка рессор вручную может производиться на специально отведенном участке с применением мер противошумной защиты.
-обрубать ненагретые листы рессор;
-ставить вертикально у стены листы рессор рессоры и подрессорники;
-поправлять заклепку после подачи жидкости под давлением в цилиндр струбцины;
-работать на станке для рихтовки рессор не имеющем концевого выключателя реверсирования электродвигателя;
-ковать черные металлы охлажденные ниже +800°C;
-ковать металл на мокрой или замасленной наковальне;
-применять не подогретый инструмент (клещи оправки);
-прикасаться руками (даже в рукавицах) к горячей заготовке во избежание ожогов;
-устанавливать заготовку под край бойка молота;
-допускать холостые удары верхнего бойка молота о нижний;
-вводить руку в зону бойка и класть поковку руками;
-работать инструментом имеющим наклеп;
-стоять напротив обрубаемого конца поковки;
-выполнять ремонт рам вывешенных на подъемных механизмах и установленных на ребро. Поднимать транспортировать и переворачивать автомобильные рамы следует только при помощи подъемных механизмов;
2.2 Промышленная санитария
-Высота помещений кузнечно-рессорного участка должна быть не менее 6 м;
-Кузнечно-рессорный участок должен быть размещен в одноэтажном здании выполнен из прочных огнестойких материалов с учетом исключения вибрации при работе молотов;
-Полы в кузнечно-рессорном участке должны настилаться из прочных несгораемых материалов иметь ровную нескользкую поверхность;
-Двери в помещении предусматривают двупольные по ГОСТ 14624-84 "Двери деревянные для производственных зданий" полотна дверей обшивают листовой сталью
-Окна в помещении предусматривают по ГОСТ 12506-81 "Окна деревянные для производственных зданий";
-Двери оконные рамы вентиляционные короба (с наружной и внутренней сторон) металлические конструкции в помещениях должны окрашиваться краской.
-Оптимальные нормы температуры относительной влажности и скорости движения в рабочей зоне:
-Теплый период года: температура 20-21С; относительная влажность 60-40%; скорость воздуха не более 05 мс;
-Холодный и переходный период года: температура 16-18С; относительная влажность 60-40%; скорость воздуха не более 03 мс.
-Отопление рекомендуется воздушное совмещенное с приточной вентиляцией или центральное с местными нагревательными приборами;
-Нагревательные приборы центральных систем отопления устанавливаются у наружных ограждающих конструкций под световыми проемами;
-Для обеспечения нормируемых параметров воздушной среды устраивается приточно-вытяжная вентиляция рассчитываемая на разбавление до предельно-допустимых концентраций выделяемых на участке вредностей удаления тепловыделений на участок;
-Вентиляция выполняется с механическим и естественным побуждением местная и обще обменная;
-Для снабжения водой технологического оборудования и на хоз. питьевые нужды в помещениях участка выполняется водопроводная сеть;
-Система внутреннего водопровода принята раздельная: хозяйственно-питьевая и производственно-противопожарная. Вода питьевого качества по трубопроводам подается к санитарно-техническому оборудованию;
-Сеть водопровода прокладывается открыто с креплениями ка кронштейнах и подвесках по конструкциях здания;
-Все нетоковедущие части электрооборудования но могущие оказаться под напряжением заземлить
-Освещение не должно давать резких теней и бликов и должно иметь правильное наиболее рациональное направление светового потока на рабочие места и объекты. Для создания здоровых условий труда производственных помещений должно быть в дневное время достаточное естественное а в темное время суток искусственное освещение.
2.3 Противопожарная безопасность
-Пожарная безопасность участка обеспечивается: системой противопожарной защиты которая предусматривает применение средств пожаротушения основных строительных конструкций объектов с регламентированными пределами огнестойкости и пределами распространения огня;
-Кузнечно-рессорный участок по взрывной взрыво-пожарной и пожарной опасности относится к категории "Г" "Определение категорий и зданий по взрывопожарной и пожарной опасности" по ОНТП 24-86 МБД СССР; утвержденной 24.П.86г;
-Наружное пожаротушение помещений обеспечивается от существующих пожарных гидрантов оборудованных указательными знаками;
-Эвакуация работающих осуществляется через существующий дверной проем;
-Помещение обеспечивается огнетушителями углекислотными СУ-2 химическими воздушно-пенными ОХВП-10 ящиком с сухим просеянным песком вместимостью 05 совком;
-В соответствии с ГОСТ 12.4.009-83 "Пожарная техника для защиты объектов” введенные в эксплуатацию огнетушители должны иметь учетные (инвентаризационные) номера по принятой на участке системе нумерации;
-Подходы к месту размещения огнетушителей должны быть всегда свободными;
2.4 Охрана окружающей среды
С целью поддержания чистоты атмосферного воздуха в пределах норм в кузнечно-рессорном отделении предусматривают предварительную очистку вентиляционных и технологических выбросов с их последующим рассеиванием в атмосфере.
Воздух удаленный из кузнечно-рессорного отделения с перед выбросом в атмосферу очищают в гидрофильтрах. Очистка в них происходит за счет улавливания загрязняющих воздух веществ водой. Для очистки воздуха удаляемого горнов применяют дожигание или каталитическое зажигание.
Для очистки воздуха от сварочного аэрозоля выделяемого при сварке используют мокрые пылеуловители например барботеры где загрязненный воздух в виде пузырьков проходит через слой жидкости и очищается. Сброс сточных вод от технологического оборудования осуществляется по системе внутренней изолированной канализации. Производственная сеть канализации предназначена для сброса стоков от раковины технологического оборудования мокрой уборки пола. На выпуске из помещения производственной канализации устанавливается колодец с отстойной частью. Канализационные стоки после отстоя направляют на очистные сооружения производственных стоков.
Конструкторский раздел
1Общий вид и описание стенда
Проектируемый стенд для сборки и разборки рессор:
Рама; 2. Пневмоцилиндр; 3. Не подвижный упор; 4. Вильчатый упор; 5. защитный кожух пневмоцилиндра;
Рама проектируемого стенда выполнена из сортового проката на сварке рабочая поверхность рамы выполнена из листа на которой при помощи болтовых соединений устанавливается неподвижный упор который имеет несколько рабочих положений.
Пневмоцилиндр с рабочим диаметром 280 мм установлен на раме при помощи болтовых соединений вильчатый подвижный упор соединен к штоку при помощи оси.
От внешних воздействий пневмоцилиндр закрывают защитным кожухом выполненным из листового проката.
Работа пневмоцилиндра управляется при помощи педали установленной на раме.
Для устойчивой работы пневматизированной оснастки необходимо соответственно подготовить поступающий из сети сжатый воздух. Подготовка в большинстве случаев сводится к очистке его от влаги и механических примесей; при необходимости в нем распыляется масло. Кроме того когда желательно получить стабильное зажимное усилие давление воздуха дополнительно регулируется путем понижения его и автоматического поддержания на заданном уровне.
Техническая характеристика стенда:
Рабочее давление воздуха
(развиваемое при рабочем давлении воздуха)
2 Проверочные расчеты механизмов
Целью проверочных расчетов является определение запаса прочности и ресурса передач.
Проверка штока пневмоцилиндра.
Расчет производим из условия что на шток действует максимальная нагрузка 26000 Н длина штока ориентировочно 500 мм диаметр 65 мм.
Проверим шток на устойчивость при сжатии. Расчетная схема рисунок 2.3 для наихудшего случая.
Расчет произведем по формуле.
где - гибкость стержня (принимаем гибкость максимально возможную для центрально сжатых элементов);
=1 коэффициент приведения длинны;
rmin - см минимальный радиус инерции.
Для штока сечением 65 х 46
где = 95 мм толщина стенки сечения.
Полученная длина 3720 мм намного превышает необходимую 500 мм следовательно условие устойчивости выполняется.
Определим действительный коэффициент гибкости стержня.
Проверим сечение по условию сжатия по формуле:
где F –площадь поперечного сечения трубы;
7 коэффициент центрально сжатых элементов при = 201;
[сжмПа допускаемое напряжение сжатия для стали 20.
0001656*10-697162*106 Па [сжмПа
Условие выполняется прочность штока обеспечена.
Проверочный расчет болтов крепящих заднюю стенку и корпус пневмоцилиндра.
Приняв предварительно для крепления болты М10 и число болтов 16 проверим болты по условию работы на растяжение для этого определим максимальное усилие действующее на крышку.
Pmах = П*D24 * Рр = 314*028024*06*106 = 36945 Н
где Рр =06 мПа расчетное давление;
D = 028 м диаметр поршня.
Проверка болтов на растяжение
где Fр – площадь сечения болта по резьбе;
[р] = 160 мПа - допускаемое напряжение растяжения для болтового соединения;
n = 16 - число болтов.
Fр = П*Dр24 = П*0009224 = 665*10-5 м2
где Dр = 92 мм-диаметр по основанию резьбы.
Условие выполняется.
Проверочный расчет оси крепления рабочего органа.
Рабочий орган крепится к пневмоцилиндру при помощи оси диаметром 20 мм проверим ось по условию работы на срез по формуле.
где [ср] = 90 мПа допускаемое напряжение среза;
Fo- площадь сечения оси;
k = 2 число срезов оси;
Рр = 26 кН сила на рабочем органе.
Fo = П*0022 4 = 314*10-4 м2
Снятую с автомобиля рессору устанавливают на стол стенда для разборки и сборки рессор и закрепляют за боковые поверхности листов затем отвёртывают гайки болтов хомутов рессоры выбивают болты и снимают распорные втулки. Ослабляют крепление рессоры укладывают её боковой поверхностью на стол стенда и закрепляют за верхний и нижний листы. Затем отвёртывают гайку центрового болта ослабляют зажим стенда и снимают разобранную на листы рессору. Подготовленные к сборке листы рессоры надевают по порядку на оправку устанавливают боковой поверхностью листов на стенд и сжимают. Вынимают оправку устанавливают центровой болт и затягивают гайку болта. В проушины хомутов устанавливают стяжные болты и распорные втулки и навёртывают на болты гайки.
После сборки проверяют стрелку прогиба рессоры натягивая тонкую проволоку с грузом по торцевым поверхностям чашек верхнего коренного листа передней рессоры.
Техническое обслуживание стенда.
Техническое обслуживание стенда заключается в своевременном проведении необходимых работ связанных с поддержанием механизма в рабочем состоянии. Производится смазка движущихся частей сливу воды из влагоотделителей. Продувка трубопроводов замена неисправных механизмов.
спец.DOC
Болт М20-6g x 80.ГОСТ 7805-70
Шайба 16.065Г ГОСТ 6402-70
Шайба 20.065Г ГОСТ 6402-70
Гайка М16-6H ГОСТ 5915-70
Гайка М20-6H ГОСТ 5915-70
Стенд для разборки и сборки рессор грузовых автомобилей
Рекомендуемые чертежи
- 19.11.2019