Прочностной расчет двигателя 12ЧН 15/18



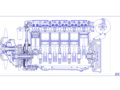
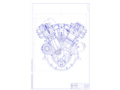
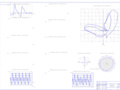
- Добавлен: 25.01.2023
- Размер: 23 MB
- Закачек: 0
Узнать, как скачать этот материал
Подписаться на ежедневные обновления каталога:
Описание
Прочностной расчет двигателя 12ЧН 15/18
Состав проекта
![]() |
![]() |
![]() |
![]() ![]() ![]() |
![]() ![]() |
![]() ![]() |
![]() |
![]() |
![]() ![]() |
![]() ![]() ![]() ![]() |
![]() ![]() ![]() ![]() |
![]() ![]() ![]() ![]() |
Дополнительная информация
Контент чертежей
2.dwg

4.dwg

1.dwg

Рекомендуемые чертежи
- 25.01.2023
- 19.04.2020
- 24.01.2023
Свободное скачивание на сегодня
Обновление через: 6 часов 32 минуты
- 22.08.2014
- 29.08.2014
Другие проекты
- 29.08.2014