Привод цепного конвейера (ременная передача + одноступенчатый конический редуктор)




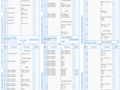
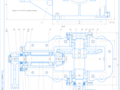
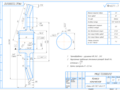
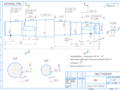
- Добавлен: 24.01.2023
- Размер: 511 KB
- Закачек: 2
Описание
Состав проекта
![]() |
![]() ![]() ![]() ![]() |
![]() ![]() ![]() ![]() |
![]() ![]() ![]() ![]() |
![]() ![]() ![]() ![]() |
![]() ![]() ![]() ![]() |
![]() ![]() ![]() |
![]() ![]() ![]() ![]() |
![]() ![]() ![]() ![]() |
Дополнительная информация
Редуктор.cdw

Расчет валов.cdw

Картер.cdw

Вал ведомый.cdw

Колесо коническое.cdw

Спецификации.frw

Привод.cdw

Рекомендуемые чертежи
- 24.01.2023
- 20.06.2022