Нормирование точности и технические измерения




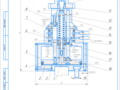
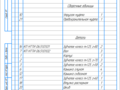

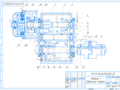
- Добавлен: 24.01.2023
- Размер: 532 KB
- Закачек: 0
Описание
Состав проекта
![]() |
![]() ![]() ![]() ![]() |
![]() ![]() ![]() ![]() |
![]() ![]() ![]() ![]() |
![]() ![]() ![]() |
![]() ![]() ![]() ![]() |
![]() ![]() ![]() ![]() |
![]() ![]() ![]() ![]() |
Дополнительная информация
Чертеж Сборочный 1.cdw

Задание 2.cdw

Зубчатое колесо.cdw

Неуказанные предельные отклонения размеров:
-Сталь 40Х ГОСТ 4543-71
Курсовой по НТТИ.doc
Учреждение образования ”Полоцкий государственный университет“
По дисциплине «Нормирование точности и технические измерения»
Задание на курсовую работу3
Расчет и выбор посадок с натягом5
Расчет и выбор посадок подшипников качения9
Выбор посадок для гладких цилиндрических cоединений методом подобия12
Выбор посадок шлицевого соединения15
Выбор параметров резьбового соединения.16
Выбор степеней точности и вида сопряжения зубчатой передачи17
Определение допусков и предельных отклонений размеров входящих в размерную цепь.19
Список используемой литературы28
Задание на курсовую работу
Требование к зубчатой передачи
С сильными толчками и вибрацией до 300%
материал венца зуб. колеса
материал втулки(ступицы) зуб. колеса
диаметр соединения мм
шероховатость сопрягаемых
Размеры размерной цепи мм
Одной из главных целей конструктора в ходе проектирования и конструирования новых и усовершенствования устаревших изделий является разработка чертежной документации для чертежей обеспечивающей необходимую технологичность и высокое качество изделий.
Цель курсовой работы по дисциплине “Нормирование точности и технические измерения”:
)Приобретение студентом необходимых знаний и навыков для расчета и выбора допусков и посадок типовых соединений деталей машин:
расчет и выбор посадки с натягом;
расчет и выбор посадок подшипников качения;
выбор посадок для гладких цилиндрических соединений методом подобия;
выбор допусков и посадок шлицевого соединения;
выбор степеней точности и посадок резьбового соединения;
выбор и расчет точности зубчатых колес и передач;
)Определение допусков и предельных отклонений размеров входящих в размерную цепь
)Нормирование точности формы и расположения шероховатости поверхностей узла.
Достоинствами курсовой работы по сравнению с другими видами обучения являются практически полная самостоятельность студента во время её выполнения необходимость использования знаний из других параллельных областей.
Расчет и выбор посадок с натягом
Посадки с натягом предназначаются для образования неподвижных соединений. Величина натяга N складывается из деформации сжатия и деформации растяжения контактных поверхностей соответственно вала и отверстия. Упругие силы возникающие при деформации создают на поверхности деталей напряжение препятствующее их взаимному смещению.
Расчет посадки с натягом в курсовой работе выполняется по типовой методике приведенной в литературе (2стр. 222). Порядок расчета:
Определяются минимальный и максимальный функциональные натяги по формулам:
T – вращающий момент Нм;
DL – диаметр и длина соединения м;
CD Cd – коэффициенты жесткости конструкции;
ED = 21011 Ed = 11011 – модули упругости материалов охватывающей детали и вала Нм2 (1 т.1 табл.1.106 стр.335);
f = 015 - коэффициент трения при нагреве или охлаждении сопрягаемых деталей (2 табл.9.2 стр.225);
Pдоп – наибольшее допустимое давление на поверхности контакта вала и охватывающей детали при котором отсутствуют пластические деформации Нм2.
Коэффициенты жесткости конструкции (2 стр.223):
мм - наружный диаметр охватывающей детали (зубчатого колеса);
D1 = 20мм – внутренний диаметр полого вала (ступицы зубчатого колеса);
D = 030; d = 025 – коэффициенты Пуассона (1 табл.1.106 стр.335);
Наибольшее допустимое давление Pдоп (2 стр. 224):
а)для охватывающей детали
Т – предел текучести материалов охватывающей детали и вала
Т = 34108 Нм2 – охватывающей детали
Т = 21108 Нм2 – вала.
В формулу Nmax ф подставляется меньшее допустимое давление Pдоп = 082107 Нм2.
Определяем коэффициенты жесткости:
Определяем минимальный и максимальный функциональные натяги:
Определяем поправки к найденным значениям Nmin ф и Nmax ф:
а)поправка u учитывает смятие неровностей контактных поверхностей вала и охватывающей детали (2 стр. 224):
Kd = 08 и KD = 02 – коэффициенты учитывающие величину смятия неровностей на поверхности вала и охватывающей детали (приложение 2 таблица 3 методических указаний к выполнению курсовой работы);
Rzd и RzD – высота неровностей поверхностей вала и охватывающей детали.
б)поправка ut учитывает различие рабочей температуры и температуры сборки и различие коэффициентов линейного расширения материалов вала и отверстия (2 стр 225):
αD = 1210-6 и αd = 10510-6 – коэффициенты линейного расширения материала деталей (приложение 2 таблица 2 методических указаний к выполнению курсовой работы);
tрD и tрd – рабочие температуры деталей;
t = 20C – температура сборки деталей.
Определяем Nmin ф и Nmax ф с учетом поправок (1 стр. 335):
При и поправка берется со знаком «минус».
Находим функциональный допуск посадки
Распределим функциональный допуск между эксплуатационным и конструктивным таким образом чтобы
Определяем число единиц допуска а и соответствующий квалитет (2 стр. 15):
где i – единица допуска мкм
Выбираем квалитет – IT8 (3 стр.34).
Выбираем стандартную посадку по ГОСТ 25347-82 (СТ СЭВ 144-75) при этом соблюдаем следующие условия:
Проверяем выполнение этих условий:
Выбираем посадку 70:
Итоговые данные по выбору посадки с натягом.
Данные по выбору ст. посадки
Параметры стандартной посадки
Поля допусков и предельные отклонения мкм
Схема полей допусков
Расчет и выбор посадок подшипников качения
Выбор класса точности подшипника.
Выбор класса точности подшипника производят в зависимости от условий работы проектируемого механизма. При ограниченной информации об условиях работы механизма что имеет место в задании на курсовую работу точность подшипника можно выбрать исходя из заданной окружной скорости ().
При рекомендуется использовать подшипники 4-го класса точности то назначаем 4-ый класс точности (1 стр. 805).
Выписываем отклонения на средние значения диаметров колец - для внутреннего диаметра и - для наружного.
Для – ES = 0 EI = -6 мкм (1 табл.4.71 стр.807)
для – es = 0 ei = -7 мкм (1 табл.4.72 стр.808).
Определяем вид нагрузки (1 стр. 813). Т.к. происходит вращение вала то вращающееся кольцо подшипника должно быть смонтировано с натягом исключающим возможность обкатки и проскальзывания этого кольца по посадочной поверхности вала такой вид нагружения внутреннего кольца – циркуляционный. Наружное кольцо должно быть установлено в корпусе с небольшим зазором. При этом наружное кольцо будет воспринимать нагрузку лишь ограниченным участком. Такой вид нагружения называется местным .
Предварительно рассчитываем интенсивность нагрузки подшипника(1 стр.814):
R = 25 кН – радиальная реакция опоры на подшипник.
мм– рабочая ширина кольца подшипника;
k = 18 – динамический коэффициент посадки зависящий от характера нагрузки ( в нашем случае – с сильными толчками и вибрацией перегрузка до 300%) (1 стр. 814).
F = 1 – коэффициент учитывающий степень ослабления натяга при полом вале (1 стр. 814).
FА =1 – коэфициент неравномерного распределения радиальной нагрузки между рядами подшипника для радиальныхи радиально упорных с одним внутренним или наружным кольцом (1 стр. 814).
По (1 табл. 4.82 с.818) заданным условиям соответствует поле допуска для внутреннего кольца – k6.
По (1 табл. 4.84 с.821) выбираем поле допуска отверстия корпуса (под наружное кольцо подшипника) K7.
Итоговые данные по расчету и выбору посадок
Схемы полей допусков:
Выбор посадок для гладких цилиндрических cоединений
Выбор посадки для соединения «крышки подшипников – корпус».
Поле допуска центрирующей поверхности (буртика) привертной глухой крышки принимают согласно ГОСТ 18511-73 d11 а имеющей отверстие для прохода вала принимают по ГОСТ 18512-73 h8.
Соединение буртика крышки подшипника с корпусом должно быть выполнено с зазором.
Соединение с глухой крышкой считаем неответственным. Принимаем посадку крышки подшипника в корпус (1 стр. 309).
Крышка со сквозным отверстием должна обрабатываться по более высокому квалитету чем глухая и должна более точно центрироваться. Это необходимо для надежной работы сальника или иного защитного уплотнения. Принимаем посадку крышки со сквозным отверстием и вала(1 стр. 309).
Для обеспечения вращения вала во втулке муфты выбираем “ходовую” посадку (1 стр. 306).
Посадку штифта предохранительной муфты выбираем (1 стр. 300).
Итоговые данные по выбору посадок для гладких цилиндрических
соединений методом подобия.
Предельные отклонения и допуски мкм
Предельные зазоры и натяги допуски посадок мкм
Штифт – корпус муфты
Выбор посадок шлицевого соединения
Выбор посадок шлицевого соединения необходимо проводить с учетом назначения соединения его конструкции и способа центрирования.
Выбор способа центрирования определяется эксплуатационными и технологическими требованиями. Выбираем центрирование по наружнему диаметру D так как этот способ центрирования рекомендуется в случаях повышенных требований к точности сосности элементов соединения когда твердость втулки не высока и допускает обработку чиставой протяжкой а вал обрабатывается фрезерованием и окончательным шлифованием по наружнему диаметру D. Применяется для подвижных соединений передающих малый крутящий момент (1 стр. 783).
Для подвижных соединений работающих при малых нагрузках центрируемых по D выбираем посадку для наружного диаметра D – (1 табл. 4.59 с.784) для ширины шлица b – (1 табл. 4.59 с.784)
Обозначение посадки . Допускается не указывать в обозначении допуски нецентрирующих диаметров (1 с.787).
Итоговые данные выбора допусков и посадок шлицевого соединения.
Обозначения шлицевого соединения на сб. чертеже
Предельные отклонения мкм
Выбор параметров резьбового соединения.
Тип посадки рассматриваемых соединений определяется характером заданной нагрузки. Поскольку для узла задана нагрузка с сильными толчками и вибрацией перегрузка до 300% следует принимать переходную посадку с целью уменьшения возможного самосвинчивания деталей (1 стр. 702).
Принимаем длину свинчивания N = мм (1 табл. IV.2 c.984)
где d – номинальный диаметр резьбы мм.
Выбираем переходную посадку (1 табл. IV.7 c.987) как предпочтительную.
Итоговые данные по выбору посадок.
Наименование деталей
Номинальные размеры параметров резьбы мм
Предельные отклонения диаметров резьбы мкм
Обозначение метрической резьбы на чертеже:.
Выбор степеней точности и вида сопряжения зубчатой
Выбор степеней точности зубчатого колеса
По степени точности зубчатые колеса и передачи подразделяются в порядке убывания точности на 12 степеней. При выборе степеней точности зубчатого колеса учитывается назначение передачи режим ее работы требования к надежности и долговечности и т.п. Все показатели точности сгруппированы в три нормы: норму кинематической точности норму плавности работы и норму контакта зубьев. Т.к. по условию необходима «бесшумность работы» то мы должны будем выбрать степень точности необходимую для бесшумности работы зубчатой передачи (1 стр. 855).
В зависимости от окружной скорости выбираем степень плавности работы равную 6 (высокая) так как (1 табл.5.12 с. 857). Нормы плавности работы зубчатых колес и передач могут быть не более чем на две степени точнее или на одну степень грубее норм кинематической точности; нормы контакта зубьев могут назначаться по любым степеням более точным чем нормы плавности работы зубчатых колес и передач (1 стр. 861).
Расчет бокового зазора и выбор вида сопряжения
Гарантированный боковой зазор находится по формуле (1.стр. 873):
V – толщина слоя смазки между зубьями
– межосевое расстояние
и – коэффициенты линейного расширения материала колеса и корпуса
и – отклонение температур колеса и корпуса от 20°С
– угол профиля исходного контура (1 стр. 837).
Величина толщины слоя смазки зависит от способа смазывания и окружной скорости колес. Ориентировочно ее можно определить по формуле (1 стр. 873):
где m – модуль зубчатого колеса мм.
Межосевое расстояние мм;
Из условия выбираем вид сопряжения зубьев B (1 табл. 5.16 с. 863) для которого мкм.
Наибольший боковой зазор получаемый между зубьями в передаче не ограничен стандартом. Принимаем вид допуска соответствующий виду сопряжения т.е. виду сопряжения В соответствует вид допуска b (1 табл. 5.23 с. 874).
Наибольший боковой зазор определяется по формуле (1. стр.873):
TH1 = 200мкм и TH2 = 200мкм – соответственно допуск на смещение контура колес зубчатой передачи (1 табл. 5.18 с.866)
fa = 260=200мкм – алгебраическая разность верхнего и нижнего отклонений межосевого расстояния зубчатой передачи (1 табл. 5.16 с.863)
Итоговые данные по выбор и расчёту точности зубчатой передачи
Норма точности и вид сопряжения
Наименование и обозначение контрольного параметра
Числовое значение параметра
Допуск на радиальное биение зубчатого венца
Допуск на накопленную погрешность шага по зубчатому колесу
Плавности работы - B
Предельные отклонение шага
Допуск на погрешность профиля
По высоте не менее 50
По длине не менее 70
Допуск на параллельность осей
Допуск на перекос осей
Условное обозначение зубчатой передачи
Ширина зубчатых колес b=15 мм.
Числовые значения параметров взяты из (1.табл.5.7 5.8 5.9 5.10 стр.845-852).
Определение допусков и предельных отклонений размеров входящих в размерную цепь.
Расчет размерной цепи методом на максимум-минимум.
)Составляем размерную цепь.
Для этого необходимо на основе анализа взаимосвязи и взаимозависимости между размерами деталей узла установить какие размеры влияют на размер замыкающего (исходного) звена указанного на чертеже узла. Размеры с предельными отклонениями стандартизованных деталей которые входят в размерную цепь (ширина B колец подшипников) необходимо установить по соответствующим стандартам.
Определяем какие из составляющих звеньев размерной цепи являются увеличивающими а какие уменьшающими (1. стр. 552).
Увеличивающие звенья – Б7.
Уменьшающие звенья – Б1 Б2 Б3 Б4 Б5 и Б6.
В качестве зависимого звена принимаем Б7.
Составим основное уравнение размерной цепи (1. стр. 559) и определим номинальный размер замыкающего звена Б:
Б1 Б2 Бm+n – номинальные значения всех звеньев размерной цепи
2 m+n – коэффициенты характеризующие расположение звеньев по величине и направлению или передаточные отношения.
Номинальный размер замыкающего звена Б определяется по следующей формуле (1. стр. 560):
Определяем среднее число единиц допуска ac составляющих звеньев кроме зависимого звена по формуле (1 с.561):
ТБ - допуск замыкающего (исходного) звена мкм
ТВ – допуск ширины кольца подшипника
к1 – число подшипников размер В которых входит в размерную цепь
i – значения единиц допуска составляющих звеньев.
Применим способ допусков одного квалитета так как все составляющие цепь размеры могут быть выполнены с допуском одного квалитета. Значения i выбираем из (1 табл.3.3 с.564).
По (1 табл. 1.8 с.43) принимаем 7-й квалитет.
)Назначаем допуски на составляющие звенья по установленному квалитету кроме зависимого звена (1 табл. 1.8 с.43).
ТВ = 120 мкм (стандартизированное изделие).
Допуск зависимого звена определяем по формуле:
где ТБj – допуски составляющих звеньев.
Устанавливаем предельные отклонения размеров составляющих звеньев кроме зависимого звена.
Б7 – охватывающий размер а Б1 Б2 Б3 Б4 и Б6 – охватываемые. Соответственно предельные отклонения для них назначаются как для основного отверстия и основного вала.
Звено размерной цепи
)Определяем координаты середин полей допусков составляющих звеньев и замыкающего звена.
Координата середины поля допуска зависимого звена входящего в число увеличивающих звеньев определяется по формуле:
- координаты середин полей допусков увеличивающих звеньев размерной цепи
- координаты середин полей допусков уменьшающих звеньев размерной цепи.
)Определяем предельные отклонения зависимого звена по формуле:
Расчет размерной цепи вероятностным методом.
Порядок расчета размерных цепей теоретико-вероятностным методом тот же что и методом по максимум-минимум.
Условия для расчёта размерной цепи вероятностным методом следующие:
процент риска принят р=027%
кривая рассеяния действительных размеров звеньев цепи имеет нормальный закон распределения
центр группирования действительных отклонений размеров звеньев цепи совпадает со средними отклонениями табличных полей допусков размеров.
)Принимаем закон рассеивания размеров деталей – нормальный (закон Гаусса) отсюда .
Определяем среднее число единиц допуска ac составляющих звеньев кроме зависимого звена по формуле (1 стр.583):
где t=3 (1 табл.3.8 стр 580) – коэффициент нормального распределения
По таблице (1 табл. 1.8 с.43) принимаем 10-й квалитет.
)Устанавливаем предельные отклонения размеров составляющих звеньев кроме зависимого звена.
Данные расчёта размерной цепи.
Замыкающее звено цепи Б
Составляющие звенья цепи Бj с указанием их предельных отклонений
Выбор шпонки производится по ГОСТ 23360-78 (Соединения шпоночные призматическими шпонками. Размеры шпонок и сечения пазов. Допуски и посадки). В нашем случае – призматическая шпонка (исполнение А) размеры которой выбираем из (1 табл.4.52 c.773) в зависимости от диаметра вала.
Размеры сечения шпонки
Интервалы длин шпонок мм
Длину шпонки принимаем l = 40мм.
Для размеров шпонок установлены следующие поля допусков(2 стр. 334):
Для размеров пазов на валу установлены следующие поля допусков(1 стр. 773):
Размер сечения паза для призматической шпонки (исполнение А).
Микрокатор (измерительная головка пружинная ИГП) предназначен для точных относительных измерений линейных размеров а также отклонений от заданной геометрической формы и может быть использован в универсальных стойках типов CI и СII или в измерительных приспособлениях с присоединительным диаметром 28мм.
Микрокатор применяют для линейных имерений относительным контактным методом. Первые микрокаторы были изготовлены в 30-х гг. 20 века фирмой «Иогансон» (Швеция).
В настоящее время выпускаются микрокаторы с ценой деления шкалы 02; 05; 10 и 2 мкм с нормальным (100-150гс) и уменьшенным (50гс) измерительным усилием. Микрокаторы с уменьшенным усилием позволяют контролировать нежесткие тонкостенные или изготовленные из мягких материалов детали. Микрокаторы имеют пружинный механизм и обладают высокой износостойкостью и отсутствием погрешности обратного хода.
Рис. Схема механизма микрокатора: 1 — пружина; 2 — стрелка; 3 — узел крепления стрелки; 4 — демпфирующий рычаг; 5 — измерительный стержень.
Специальная ленточная пружина завитая от середины в разные стороны закреплена на угольнике и консольной пружине. К середине пружины приклеена стрелка которая поворачивается при растяжении пружины. Измерительный стержень подвешен на мембранах и связан с угольником. Перемещение измерительного стержня вызывает поворот угольника вокруг точки а что в свою очередь изменяет растяжение пружины. Угол поворота стрелки пропорционален величине растяжения пружины. Головки оснащены механизмом для точной установки на размер в пределах шести делений шкалы. Измерительные наконечники головок оснащены корундом. Головки укомплектованы измерительным наконечником со сферической измерительной поверхностью и арретиром.
Цена деления шкалы мкм
Предел измерений мкм
; 2; 05: 02; 01; (005; 002 — опытные образцы)
± (300: 150; 60; 30; 15; 6; 4)
±. 05% от цены деления
Данная курсовая работа закрепила теоретические знания о дисциплине мною были приобретены навыки расчёта размеров я научился правильно определять точность типовых соединений назначать допуски научился анализировать конструкцию узлов механизма на практике столкнулся с указаниями стандартов ЕСКД и успешно применил их.
Список используемой литературы
Допуски и посадки. Справочник в 2-х частях. Под ред. Мягкова В.Ф. 5-ое изд. Ленинград «машиностроение» 1978.
Якушев А.И. Воронцов Л.Н. Федотов Н.М. Взаимозаменяемость стандартизация и технические измерения. Учебник для вузов шестое издание переработанное и дополненное. Москва «машиностроение» 1987.
Методические указания к курсовой работе по дисциплине ВСТИ для студентов спец. 1201. Новополоцк 1991.
Единая система допусков и посадок СЭВ в машиностроении и приборостроении: Справочник: В 2 т. – 2-е изд. перераб. и доп. – М.: Издательство стандартов 1989.
Вал.cdw

Сталь 40Х ГОСТ 4543-71
Спецификация.spw

Зубчатое колесо m=1.25
Болт М4 ГОСТ 7708-70
Болт М6 ГОСТ 7708-70
Винт установочный М4 ГОСТ 1476-75
Мaнжета 1.1-28х42-1 ГОСТ 8752-79
Мaнжета 1.1-35х50-1 ГОСТ 8752-79
Подшипник 1000807 ГОСТ 8338-75
Подшипник 7000106 ГОСТ 8338-75
Подшипник 108 ГОСТ 8338-75
Шайба А.2.0Х30Н12 ГОСТ 11371-78
Шайба А.1.08Х32Н12 ГОСТ 11371-78
Шпонка А 12х8х60 ГОСТ 23360-78
Штифт 6h9х18 ГОСТ 12850.1-93
Спецификация 2.spw

Болт М5X1-6gx25.58X.01 ГОСТ 7808-70
-6gх25.58.35Х.01 ГОСТ 11738-84
Винт М5х1.5-6g х 25.58.35Х.01 ГОСТ Р 11738-84
Кольцо020-025-30-2-1 ГОСТ 18829-73