Мостовой двухбалочный электрический кран г/п 12, 5т



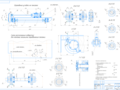
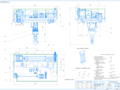
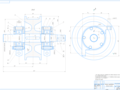
- Добавлен: 25.01.2023
- Размер: 1 MB
- Закачек: 0
Описание
Состав проекта
![]() |
![]() |
![]() ![]() ![]() ![]() |
![]() ![]() ![]() ![]() |
![]() ![]() ![]() ![]() |
![]() ![]() ![]() |
Дополнительная информация
КОЛЕСО СБ.cdw

поз. 4 в подшипниковых опорах.
Подшипники поз. 11 заполнить на 23 свободного объёма корпуса
смазкой литол 24 ГОСТ 21150-75.
*размеры для справок
МЕХ.ПЕРЕДВ.СБ.cdw

для монтажа механизма передвижения тележки
ось электродвигателя
Технические характеристики
Скорость передвижения тележки ммин
передаточное отношение
Рабочие размеры с неуказанным предельным отклонениeм
Размеры* для справок
механизма передвижения
Кафедра ПТМ гр. МЗ-570303
Гайка М32.5 ГОСТ 5916-70
Гайка М16.5 ГОСТ 5915-70
Гайка М12.5 ГОСТ 5915-70
Шайба 16.65Г ГОСТ 6402-70
Шайба 12.65Г ГОСТ 6402-70
Шайба 32.65 ГОСТ 11371-78
Ограждение условно не показано
ТЕЛЕЖКА СБ.cdw

Высота подъёма груза
Группа режима работы
Грузоподъёмность механизма
-передвижения тележки
Электродвигатель механизма
-передвижения тележки:
-передвижения тележки
Канат механизма подъёма
Неуказанные предельные отклонения рабочих размеров
*размеры для справок
Кафедра ГПМиР гр. МЗ-570303
Расчётно-пояснительная
Механизм передвижения
Ограничитель высоты
Подвеска крюковая 4-16-406
Схема навивки канатов
Нагрузки на ходовые колёса
пояснилка.docx
Федеральное государственное образовательное учреждение
высшего профессионального образования
Уральский федеральный университет
имени первого президента России Б. Н. Ельцина
Кафедра «Подъёмно-транспортные машины и роботы»
«Металлургические подъёмно-транспортные машины»
Тема: «Тележка мостового электрического крана
грузоподъёмностью Q = 125 т»
Расчётно-пояснительная записка
Руководитель: Лукашук О.А.
гр. МЗ-570303 Мухамедов Д.А.
Предварительные расчёты механизмов 2
1. Механизм подъёма .2
1.1. Выбор крюковой подвески .2
1.3. Установка верхних блоков . .4
1.4. Установка барабана ..5
1.5. Выбор электродвигателя ..7
1.6. Выбор редуктора .. . ..8
1.7. Выбор соединительных муфт . .9
1.8. Выбор тормоза 10
2. Механизм передвижения .11
2.1. Определение сопротивлений передвижению тележки 13
2.2. Выбор электродвигателя .14
2.3. Выбор передачи ..14
2.4. Выбор тормоза 16
2.5. Выбор соединительных муфт .17
Компонование тележки ..18
Проверочные расчёты механизмов .22
1. Механизм подъёма груза 22
Проверка двигателя на время разгона .. ..22
Проверка двигателя на нагрев . .. ..23
2. Механизм передвижения тележки 28
Проверка двигателя на время разгона .. ..28
Проверка двигателя на время торможения 30
3. Проверка запаса сцепления колёс с рельсами . ..31
Расчёты сборочных единиц 34
Ходовые колёса тележки 34
Список используемой литературы . ..36
Предварительные расчёты механизмов
- Высота подъёма груза15 м;
- Скорость подъёма груза9 ммин;
- Группа режимов работы3М;
Рис. 1. Кинематическая схема механизма подъёма
1.1. Выбор крюковой подвески
По типу крюка подвески бывают с однорогим крюком и с двурогим. Поскольку в задании не указано для перемещения каких грузов предназначен кран то выбираем произвольно подвеску с однорогим крюком.
Выбор типоразмера крюковой подвески производится по двум условиям. Первое – грузоподъёмность крюковой подвески не должна быть меньше заданной грузоподъёмности второе – режим работы крюковой подвески должен соответствовать режиму работы механизма. Группа режимов работы М3 соответствует режиму работы Л (лёгкий) по табл.8 [2].
Выбираем подвеску 4–16–406 с параметрами: т; режим работы – Л; количество блоков ; диаметр блоков по дну ручья мм
масса крюковой подвески кг.
Выбранная подвеска определяет кратность полиспаста:
где- число ветвей каната на которых весит груз;
- число ветвей каната которые навиваются на барабан.
Выбор каната производится по максимальному статическому усилию кН:
где - вес номинального груза и крюковой подвески Н;
где - масса номинального груза (численно равная грузоподъёмности) кг;
- масса подвески кг;
- ускорение силы тяжести.
При выборе типоразмера каната должны быть соблюдены два условия: первое – произведение максимального статического усилия в канате на коэффициент использования каната (коэффициент запаса прочности) не должно превышать разрывного усилия каната в целом т.е.
где – разрывное усилие;
– максимальное статическое усилие;
– коэффициент запаса прочности;
По табл. 9 [2] исходя из режима работы (3M)
Этим условиям соответствует стальной канат двойной свивки диаметром мм с разрывным усилиемН; тип каната – ЛК-Р конструкции 6х19(1+6+66)+1о.с. ГОСТ 2688-80 маркировочная группа 1960 МПа.
Второе условие – должно выполняться соотношение между диаметром
выбранного каната и диаметром блока крюковой подвески:
где - диаметр блока по дну ручья;
- коэффициент регламентируемый нормами ГГТН и зависящий от режима работы (табл.10 [3]);
При режиме работы M3 .
Оба условия выполняются значит канат выбран верно.
1.3. Установка верхних блоков
Минимальный диаметр блока:
где h2 – коэффициент выбора диаметра уравнительного блока по табл.10[3];
dк – диаметр каната мм.
При режиме работы M3 ; ; .
Диаметр по дну канавки:
Размеры профиля ручья должны соответствовать следующим
Рис. 2. Профиль ручья блока
При соблюдении этих условий канат может отклоняться от плоскости симметрии ручья не более 6°. Все блоки полиспастной системы рекомендуется устанавливать на подшипниках качения с применением защитных уплотнителей предотвращающих загрязнение подшипников и утечку смазки.
Блоки должны иметь устройство исключающее выход каната из ручья блока; зазор между указанным устройством и ребордой блока должен составлять не более 20% от диаметра каната.
1.4. Установка барабана
Диаметр барабана по оси навиваемого каната:
где h1 – коэффициент выбора диаметра барабана по табл.10[3];
Полученное значение округлим в большую сторону до стандартного значения из нормального ряда диаметров [1 стр. 24]: мм.
Длина барабана рассчитывается по формуле:
где – длина одного нарезанного участка;
– длина гладкого среднего участка;
– длина одного гладкого концевого участка.
Длина одного нарезанного участка:
где - шаг навивки каната;
– число рабочих витков для навивки половины рабочей
– число неприкосновенных витков ;
– число витков для крепления конца каната ;
где – высота подъёма груза;
Длина одного нарезанного участка
Длина гладкого среднего участка барабана определяется из соотношения
Длина гладкого концевого участка вычисляется по формуле:
Отношение рекомендуется назначать в пределах 35 50.
Полученное значение выходит за пределы рекомендуемого поэтому увеличим диаметр барабана до 400 мм и произведём повторный расчёт.
Число рабочих витков
Полученное значение округлим до ближайшего стандартного значения
Lб = 1600 мм тогда получим
– в пределах рекомендуемого.
Рис. 3. Установка барабана
1.5. Выбор электродвигателя
В крановых механизмах подъёма целесообразно использовать асинхрон-ные двигатели с фазным ротором серий MTF MTH 4AK.
Выбор электродвигателя производится по относительной продолжитель-ности включения ПВ и по необходимой статической мощности при подъёме груза максимального веса. При лёгком (Л ПВ=15%) режиме работы сле-дует применять двигатели серии MTF.
Вычислим необходимую статическую мощность при подъёме груза максимального веса по формуле
где - предварительный КПД механизма.
- вес груза с крюковой подвеской кН;
- скорость подъема груза мс;
Требуемую мощность обеспечит двигатель MTF-411-8 [2 с.59] имеющий следующие параметры:
номинальная мощность двигателя Nдв = 22 кВт;
частота вращения вала двигателя nдв = 685 обмин
максимальный момент Мmax= 580 Нм
масса двигателя mдв = 280 кг.
1.6. Выбор редуктора
Типоразмер редуктора выбирают по расчётному эквивалентному вращающему моменту на выходном валу Ме с учётом режима работы необходимого передаточного числа и частоты вращения быстроходного вала.
Требуемое передаточное число редуктора можно найти по формуле:
где nд – частота вращения двигателя.
Частота вращения тихоходного вала:
Максимальный вращающий момент на тихоходном валу редуктора для механизма со сдвоенным полиспастом:
п б – КПД полиспаста и барабана соответственно.
Эквивалентный момент на выходном валу редуктора:
где N = К1nnWt = 360004814750 = 82080000 = 82·106;
К1 = 3600 – коэффициент для передач с односторонней нагрузкой;
n – частота вращения тихоходного вала редуктора;
nW = 1 – число зубчатых колёс сцепляющихся с тихоходным колесом редуктора;
t – время работы механизма за срок службы для лёгкого режима работы принимаем t = 4750 ч;
= 018 - коэффициент интенсивности режима нагружения.
Базовое число циклов перемены напряжений выбирают исходя из характеристик материала колёс. Твёрдость рабочей поверхности зубьев колёс редуктора HB = 300 NHO =26·106
Окончательно найдём эквивалентный момент:
По всем рассчитанным параметрам выбираем цилиндрический двухступенчатый редуктор типа Ц2-400 с параметрами: ; режим работы – Л (лёгкий); масса 317кг.[2]
1.7. Выбор соединительных муфт
Муфты в механизмах машин применяются для передачи крутящих моментов а так же с целью предотвращения смещения (осевые радиальные угловые) валов возникающие как при монтаже так и при деформации металлических конструкций (рам мостов колонн и т.д.) во время работы машины.
Для соединения валов механизмов передающих основные нагрузки и относящихся к группам режима работы 6К 7К и 8К рекомендуется на мостовых кранах применять зубчатые муфты по ГОСТ 5006-83. Для группы режима 1К-5К применяют втулочно-пальцевые муфты по ГОСТ 2144-75.
Зубчатые муфты 1-го типа (старое название – муфты МЗ) применяются при непосредственном (без промежуточного вала) соединении валов. Зубчатые муфты 2-го типа (старое название – муфты МЗП) – для соединения валов через промежуточный вал для всех групп режима работы. Втулочно-пальцевые муфты применяют только при непосредственном соединении валов.
Передаваемый вращающий момент определяется по формуле
где – расчётный вращающий момент
К – коэффициент запаса прочности
– действующий вращающий момент
– допускаемый вращающий момент для муфты.
где – коэффициент учитывающий степень ответственности соединения (в предварительных расчётах );
– коэффициент режима работы
– коэффициент углового смещения; для муфт 2-го типа .
Произведём выбор муфт:
Для быстроходного вала редуктора:
тогда Нм муфта зубчатая по ГОСТ 5006-55 № 2
Для тихоходного вала применяем вариант установки барабана с внешней опорой как сборочной единицы; в таком случае в качестве внутренней опоры оси барабана используют конец тихоходного вала редуктора имеющий расточку для размещения подшипника.
В механизмах подъёма груза широко используются автоматические нормально замкнутые тормоза с пружинным замыканием и электромагнитным или электрогидравлическим приводом типа ТКТ ТКП ТКГ.
Расчётный тормозной момент определяется по формуле
где – коэффициент запаса торможения = 15 ;
– статический крутящий момент при торможении создаваемый весом номинального груза на валу на котором установлен тормоз.
При режиме работы 3М коэффицент запаса торможения = 15
Величина определяется по формуле
где – КПД механизма ( – КПД редуктора типа Ц2);
– общее передаточное число механизма с учётом кратности полиспаста ().
По рассчитанным параметрам выбираем колодочный тормоз
2. Механизм передвижения
- скорость передвижения тележки465 ммин;
- группа режима работы по ГОСТ 25835-833М;
При выборе кинематической схемы механизма передвижения тележки отдают предпочтение схеме имеющей центральный привод с тихоходным трансмиссионным валом и применением вертикальных редукторов ВК ВКУ. Число ходовых колес тележек зависит от грузоподъёмности. При грузоподъёмности до 160 т предварительно можно принять 4 колеса при большей грузоподъёмности - 8. Предпочтительным является расположение редуктора между приводными ходовыми колесами. При этом обе половины трансмиссионного вала закручиваются под нагрузкой на одинаковую величину что способствует одновременному началу движения приводных колёс и ликвидации перекосов. Тем не менее применяется и схема механизма с боковым расположением редуктора достоинством которой является удобство её монтажа. В этих схемах используются навесные редукторы типа ВКН ЦЗвк.
В механизмах передвижения двухбалочных кранов независимо от места работы применяется как правило раздельный привод. Он лёгок и удобен в изготовлении и монтаже. Однако при раздельном приводе несинхронность движения сторон крана больше чем при центральном. Тормоза часто располагают на вторых концах валов двигателей что обеспечивает удобный подход для ремонтов и обслуживания. Однако при таком расположении тормоза увеличиваются динамические нагрузки действующие на быстроходные валы механизма при торможении.
Число ходовых колес крана может быть 4 8 16. Оно зависит от грузоподъемности пролета режима работы и скорости движения крана. Предварительно число ходовых колес крана можно принять в зависимости от грузоподъемности:
Грузоподъемность механизма
Поскольку грузоподъёмность нашего крана 125 т то число ходовых колёс примем равным 4.
Выбор сборочной единицы «колесо в сборе» производится по максимальной статической нагрузке которая для тележек определяется по формуле
где – вес номинального груза главного подъёма и тележки соответственно;
KH = 125 – коэффициент неравномерности распределения нагрузки на колёса.
Вес тележки в предварительных расчетах можно определить по ориентировочным соотношениям:
при лёгком и среднем режиме работы.
Принимаем диаметр колёс по ГОСТ 24.090.44-82 Dк = 250 мм.
2.1. Определение сопротивлений передвижению тележки
Полное сопротивление W кН передвижению тележки в период разгона приведенное к ободу колеса включает в себя следующие составляющие:
гдеWmр – сопротивление создаваемое силами трения;
Wв – ветром (при работе на открытом воздухе);
Wин –инерцией вращающихся и поступательно движущихся масс тележки;
Wгиб – раскачиванием груза на гибкой подвеске.
Сопротивления создаваемые силами трения определяются по формуле
где - соответственно вес максимального груза и тележки;
– коэффициент трения качения колес по рельсу =04 (по табл.12);
– коэффициент трения в подшипниках колес =0015 (по табл.13);
– диаметр цапфы вала колеса dц = 55;
= 25 – коэффициент дополнительных сопротивлений (трения реборд и токосъёмного устройства [3 7]).
Сопротивление создаваемое уклоном пути
где α- уклон рельсового пути для тележек а = 0002.
Сопротивление создаваемое ветром при рабочем состоянии крана определяется по нормам ГОСТ 1451-77. При работе крана в помещении WB=0.
Сопротивление Wин кН создаваемое силами инерции определяется по формуле
где = 125 – коэффициент учитывающий инерцию вращающихся масс;
– ускорение при разгоне мс2.
Значение а предварительно можно принять равным (05 10)[а] где [а] - допускаемое ускорение при грузоподъёмности в 125 т [а] = 015 мс2 (по табл.14 [2]) следовательно: а = 0075 мс2;
Сопротивление создаваемое раскачиванием груза на гибкой подвеске
где – масса подвески.
Тогда полное сопротивление
2.2. Выбор двигателя
Электрический двигатель выбирается по мощности с учетом относительной продолжительности включения - ПВ %. Необходимую мощность N кВт определяют по формуле
где – скорость тележки мс;
= 087 – предварительное значение КПД механизма;
– кратность среднепускового момента двигателя по отношению к номинальному для асинхронных двигателей с фазным ротором МТН
По этим параметрам при условии ПВ=15% выбираем крановый электродвигатель серии МТF 012-6 с параметрами:
-мощность на валу кВт
-частота вращения обмин
-максимальный момент Нм
-момент инерции ротораJp = 0029 кг·м2
Передачу выбирают исходя из предварительно намеченной кинематической схемы механизма. Как привило в механизмах передвижения тележки удаётся обойтись без открытой передачи применяя стандартный редуктор. Широкое применение находят вертикальные редукторы типа ВКУ ВК закрепляемые на вертикальной плите и навесные редукторы ЦЗвк ВКН устанавливаемые с наружной стороны ходового колеса на приводном вале.
Выбор типоразмера редуктора осуществляют по эквивалентному вращающему моменту на выходном валу с учетом режима работы и передаточному числу.
Необходимое передаточное число редуктора
где – частота вращения вала двигателя обмин;
– диаметр ходового колеса м;
– скорость тележки ммин.
Максимальный момент на тихоходном валу редуктора
Окончательно определим эквивалентный момент:
По всем рассчитанным параметрам выбираем цилиндрический трёхступенчатый редуктор типа Ц3ВК -120 с параметрами:
-передаточное отношение;
-частота вращения на быстроходном валу
-режим работы – Л (лёгкий);
-номинальный вращающий момент ;
Согласно правилам ГГТН РФ тормоза в механизмах передвижения должны устанавливаться в следующих случаях:
–машина работает на открытом воздухе;
–машина предназначенная для работы в помещении передвигается по пути уложенному по полу;
–машина (тележка) предназначенная для работы в помещении на надземном рельсовом пути перемещается со скоростью более 053 мс.
Расчётный тормозной момент механизма при работе крана в закрытом помещении определяется для движения без груза под уклон в предположении что реборды колёс не задевают за головки рельсов:
где – соответственно моменты создаваемые уклоном инерцией и силами трения приведённые к валу тормоза.
Значения этих параметров можно определить по следующим зависимостям:
где - КПД механизма. Принимаем = 085;
– сопротивления передвижению крана (тележки) без груза создаваемые уклоном инерцией и трением соответственно.
Их значения определяются зависимостями
В приведённых зависимостях – коэффициент учитывающий инерцию вращающихся масс механизма (при скорости передвижения меньше 1 мс =125);
[а] – допускаемое ускорение при торможении;
– коэффициент учитывающий сопротивление движению тележки от троллейного токопровода.
По рассчитанным параметрам выбираем тормоз типа ТКГ так как электрогидравлический толкатель являющийся приводом тормоза служит одновременно своеобразным демпфером снижая динамику замыкания тормоза. Это благоприятно скажется на сцеплении колёс тележки с рельсами при торможении.
m = 21 кг DШ = 160 мм.
2.5. Выбор соединительных муфт
Выбор муфт осуществляется в зависимости от передаваемого вращающего момента и условий работы по формуле:
где - коэффициент учитывающий степень ответственности соединения (в предварительных расчётах ); – коэффициент режима работы
- коэффициент углового смещения для втулочно-пальцевых муфт
тогда Нм муфта зубчатая по ГОСТ 5006-83 №1 Нм
Компонование тележки мостового крана
Расположение механизмов на раме тележки должно обеспечить её минимальные габариты и массу равномерную нагрузку на ходовые колёса при номинальном грузе на крюке. Если на тележке устанавливаются два механизма подъёма то равномерности нагрузки на ходовые колёса добиваются при номинальном грузе на крюке главного подъёма. Нагрузку на ходовые колёса тележки в порожнем состоянии с целью улучшения сцепления колес с рельсами стремятся распределить таким образом чтобы на приводные колёса приходилась несколько большая нагрузка чем на неприводные.
В результате компанования тележки должны быть получены:
- схема размещения механизмов на раме с размерами определяющими их положение относительно рамы тележки;
- габаритные размеры тележки;
- положения центров тяжести тележки в порожнем состоянии и при работе с номинальным грузом;
- нагрузки на ходовые колёса тележки в порожнем состоянии и от веса груза.
Схематично предварительная компоновка механизмов на тележке показана на рис. 4.
Рис. 4. Схема предварительной компоновки
Определяем координаты центра тяжести порожней тележки по формулам:
Здесь G веса отдельных сборочных единиц;
X Y координаты точек их приложения.
Рассмотрим равновесие крюковой подвески в плоскости базы тележки и тем самым определим координату приложения равнодействующей от веса груза к раме тележки (точка Огр). Подвеску расположим между барабаном и верхними блоками на наибольшей высоте (рис. 5). В этом положении ось подвески находится от оси барабана на расстоянии
где Нб – высота расположения оси вала барабана над рамой тележки (определяется высотой расположения оси вала редуктора). Поскольку редуктор механизма подъёма мы устанавливаем на платики высотой
hпл = 25 мм то высота расположения оси вала барабана будет равна
Hб = H0+hпл = 265+25 = 290 мм;
Нр – высота рамы тележки; её принимают равной 18 15 от ориентировочно принятой базы тележки
Нр = (18 15)2200 = 280 мм;
Н ≥ 200 мм – расстояние от подвески в её верхнем положении до металлоконструкции тележки (регламентируется «Правилами» ГГНТ); Нп – расстояние от оси до крайней верхней точки подвески
Для установки уравнительного балансира необходимы размеры:
Aв.бл = 08Dбл0 = 08390 = 320 мм
Hmin ур.б 3Dбл0 = 3903 = 1170 мм.
Расстояние от оси приводных колёс до точки ОТ:
Расстояние от оси приводных колёс до центра тяжести груза:
После чего определим положение неприводных колёс:
Рис. 5. Определение равнодействующей от веса груза
Определяем нагрузку на ходовые колёса тележки от веса порожней тележки:
Нагрузка на ходовые колёса от веса груза:
Суммарные статические нагрузки на ходовые колёса:
Максимальная разница в нагрузках на колёса:
Поскольку разница в статической нагрузке на колёса составляет менее 10% то изменение расположения колёс не требуется.
Проверочные расчёты механизмов
1. Механизм подъёма груза
Проверка двигателя на время разгона.
Двигатель должен разгонять механизм за достаточно короткое время иначе уменьшится производительность крана. С другой стороны если оно будет слишком мало то разгон будет сопровождаться большим ускорением что скажется на прочности элементов устойчивости груза и т.д.
Время разгона механизма подъёма принимают 1 2 с [20]. В книге [23] рекомендуется диапазон времени разгона 2 4 с.
Для механизма подъёма груза наибольшее время разгона получается при разгоне на подъём. Его можно получить по приближённой формуле
где дв – угловая скорость двигателя радс; Jмех.р – приведённый к валу двигателя момент инерции при разгоне всех движущихся частей механизма включая поступательно движущиеся массы кгм2; Тп.ср – среднепусковой момент двигателя Нм; Тст.р – момент статических сопротивлений при разгоне приведённый к валу двигателя Нм.
Значение Тп.ср определим по формуле
где п.ср – кратность среднепускового момента двигателя п.ср = 155 (табл. 2.17 [2]);
Тдв.н. = Nдвwдв = 221037174 = 30666 Нм.
Тп.ср = 15530666 = 47533 Нм
Значение Jмех.р определим по формуле
Jмех.р = Jвр+Jпост.р
где Jвр. – момент инерции вращающихся частей механизма приведённый к валу двигателя:
где γ = 11 12 – коэффициент учёта инерции вращающихся масс разположенных на втором третьем и последующих валах механизма;
J1 – момент инерции вращающихся масс разположенных на первом валу равный сумме моментов инерции ротора двигателя (якоря) Jр.дв муфт Jм тормозного шкива Jт.ш.
Jт.ш = mт.шr2т.шт.ш = 254015206 034 кгм2
тогда момент инерции J1 = 0537+005+06 = 1187 кг·м2;
момент инерции вращающихся частей механизма
JВР = 115·1187 = 1365 кг·м2
Окончательно получим
Полученное значение находится в диапазоне рекомендуемых значений времени разгона. Среднее ускорение груза при таком времени разгона равно
Полученное значение превышает допускаемое (табл. 2.16 с. 41) поэтому выберем двигатель с меньшей мощностью:
N = 18 кВт nдв = 700 обмин.
Выполним аналогичный расчёт на выбранный нами двигатель.
Полученное значение не превышает допускаемое значение (табл. 2.16 стр.41 [2]).
Диаметр конца вала двигателя не изменился поэтому выбранная ранее соединительная муфта сохраняется.
Проверка двигателя на нагрев.
Вновь выбранный двигатель должен развивать в период установившегося подъёма номинального груза мощность которая с учётом фактических величин vпод и мех будет равна Nст. max = Gvподмех = 125577015085 = 2216 кВт. Это значение на 23% превышает номинальную мощность двигателя. Следовательно двигатель должен быть проверен на нагрев.
где - эквивалентный момент на валу двигателя при работе с которым его нагрев будет таким же как и при работе с реальными моментами возникающими при подъёме и опускании грузов различного веса Нм;
- номинальный момент двигателя Нм.
Величину следует определять по формуле:
– статический момент на валу двигателя возникающий при подъёме груза
– статический момент на валу двигателя возникающий при опускании груза
– время разгона механизма при работе с грузом
– время установившегося движения при подъёме с;
– время установившегося движения при пускании;
– коэффициент учитывающий ухудшение условий охлаждения двигателя в период пуска.
Под знаком радикала стоят суммы указанных параметров за время рабочего цикла.
По графику на рис. Х. используя значение номинального КПД механизма находится значения КПД при подъёме грузов вес которых соответствует относительной доле от номинального указанной на ординате типового графика. При этом делается допущение что при подъёме и опускании груза КПД одинаковый.
Рис.6. График зависимости КПД от нагрузки
Статические моменты создаваемые на валу двигателя при подъёме и опускании груза i – го веса вычисляются по соотношениям:
– КПД механизма при работе с грузом i-го веса.
При общем количестве подъёмов (опусканий) за цикл равном десяти получается что в нашем случае груз весом G поднимается и опускается четыре раза 0095G – три раза (см. рис. 4.2 б).
Статические моменты при подъёме:
Статические моменты при опускании:
Время разгона при подъёме и опускании груза Gi можно определить
где ДВ – номинальная угловая скорость двигателя радс; С – синхронная угловая скорость двигателя (угловая скорость идеального хода) радс:
где f = 50 Гц – частота промышленного трёхфазного тока; р – число пар полюсов двигателя; в нашем случае р = 4 (MTF 411-8). Тогда
Далее определим моменты инерции Jмех.i для веса Gi
После чего найдём время разгона при подъёме Gi
Время установившегося движения определим по формулам
Фактические скорости движения груза при подъёме и опускании определяют по формулам
Поскольку то примем значение = 067.
Теперь когда известны все параметры входящие в формулу расчёта эквивалентного момента получим следующее значение
Вывод: условие выполняется. Двигатель не перегреется.3.2. Механизм передвижения тележки
Наибольшее время разгона наблюдается когда кран нагружен а уклон пути и ветер препятствуют движению. Поскольку наш кран будет работать в закрытом помещении то ветровая нагрузка не учитывается. В общих чертах расчёт времени разгона двигателя механизма передвижения аналогичен расчёту для двигателя подъёма с тою лишь разницей что здесь нужно принять mпост = mт+mгр; вместо радиуса барабана следует подставить радиус колеса.
Время разгона определяется по формуле
Момент статических сопротивлений
Среднепусковой момент двигателя
Значение Jмех.р равно
По найденному времени вычислим среднее ускорение при разгоне
Полученное значение превышает допускаемое (табл. 2.16 [2]) поэтому выберем двигатель той же серии но с меньшей мощностью.
MTF 012-6: N = 27 кВт n = 840 обмин.
Далее выполним аналогичный расчёт на выбранный нами двигатель.
Значение Jмех.р останется без изменений
с - полученное время не превышает рекомендуемого
Выполним проверку ускорения
Вывод: выбранный предварительно двигатель MTF 012-6 с неоправданно высокой номинальной мощностью N = 31 кВт разгоняет нашу тележку довольно быстро что неудовлетворительно скажется при ручной строповке грузов. Поэтому мы выбрали двигатель той же серии но уже с меньшей мощностью (N = 27 кВт). С такой мощностью тележка будет разгоняться в рекомендуемых для нашего случая диапазонах ускорения.
Проверка времени торможения.
Время торможения должно быть примерно равно времени разгона: tт tр;
где Jмех. т - момент инерции всех движущихся масс механизма и поступатель-но движущихся объектов при торможении приведённый к первому валу механизма кг·м2; Тст. т - момент статических сопротивлений при торможении приведённый к первому валу механизма Н·м.
Данные параметры вычислим по соотношениям
Время торможения равно
Полученное значение превышает рекомендуемые значения и существенно больше времени разгона. Поэтому увеличим расчётный тормозной момент Тт.р. мех путём регулировки замыкающей пружины до 10Н и произведём повторный расчёт:
3. Проверка запаса сцепления колёс с рельсами.
где kсц - коэффициент запаса сцепления колеса с рельсом; [kсц] - допускаемый коэффициент запаса сцепления; [kсц] = 12 (при работе крана в помещении).
Значение kсц определим по выражению
где Тсц.о - момент силы сцепления (трения скольжения) колеса с рельсом когда кран не нагружен; Тдин.р - динамический момент при разгоне возникающий в трансмиссионном валу вследствие ударно-упругого нагружения когда в трансмиссии выбирается зазор; Ту.о.к Тв.о.к Ттр.о.к - соответственно моменты сил: уклона ветра рабочего состояния и трения действующие относительно оси приводных колёс когда кран не нагружен:
где Fсц.о – сила сцепления приводных колёс с рельсом когда кран не нагру-жен:
fсц = 02 (при работе крана в помещении);
С учётом динамики нагружения трансмиссионного вала значение Тдин.р может быть определено по формуле
Момент на оси приводных колёс создаваемый уклоном пути равен
Ту.о.к = Wу. rк = 3185025 = 7962 Нм. Момент на оси приводных колёс создаваемый силами равен Ттр.о.к = Рпр.0( + frц) = 847(04×10-3 + 00150055)= =001 кНм. Здесь rц – радиус цапфы. Далее определяем моменты инерции для порожнего состояния тележки:
Сила статического сопротивления движению равна
кН. Последовательно определим параметры:
Определим коэффициент жесткости тихоходного участка трансмиссии. Максимальный статический момент на тихоходном трансмиссионном валу действующий при передвижении тележки с номинальным грузом на крюке механизма подъёма равен
В качестве материала трансмиссионного вала принимаем сталь 40Х. По табл. 2.19 МПа. Тогда [] = 003в = 003·900 = 27 МПа. Диаметр конца вала определим по формуле
Принимаем диаметр конца вала равным 45 мм. Такой диаметр должна также иметь расточка во втулке полумуфты. Тогда диаметр трансмиссионного вала на наиболее длинном участке можно принять равным 50 мм. Полярный момент инерции поперечного сечения вала будет равен
Так как запас сцепления недостаточен необходимо ввести в схему управления двигателем предпусковую ступень. При этом зазор в передаче нужно выбрать до приложения полного момента двигателя. Динамический момент будет меньше.
Проверим запас сцепления колёс с рельсами при разгоне тележки с номинальным грузом на крюке механизма подъёма. При компоновании тележки была получена нагрузка на ходовые колёса в гружёном состоянии равная Рпр = 654 кН. Определим соответствующие параметры:
Необходимый запас сцепления при разгоне гружёной тележки обезпечивается.
Расчёты сборочных единиц
Ходовые колёса тележки.
Колёса предварительно выбранных колёсных установок проверяем на напряжения в контакте обода и рельса.
k = 0105 при отношении (табл. 5.3 [2])
k1 = 105 при мс (табл. 5.5[2]);
kд = 1+015·0775 = 1116 (табл. 5.4 [2]).
Контактные напряжения
По табл. 5.6 (2) для стали 45 значение допускаемого напряжения при числе циклов нагружения N≤104 [0] = 610 МПа.
Усреднённая скорость движения тележки (при отношении времени неустановившегося движения к полному времени движения k = 06) равна мс.
Полное число оборотов колеса за срок службы при машинном времени Тмаш = 3200 ч (табл. 5.6 [2])
Значение коэффициента определяем по таблице к формуле (5.16) в зависимости от отношения минимальной нагрузки на колесо к максимальной при 818327 = 025 = 016. Приведённое число оборотов колеса за срок службы (5.15 (2))
N = Nc = 0167925×106 127×106.
Допускаемое контактное напряжение определяем по формуле (5.14 (2)):
Поскольку = 346387 МПа [N] = 3561 МПа условия прочности удовлетворяются.
Список используемой литературы
Грузоподъёмные машины: учебно-методическое пособие Ю. В. Наварский. Екатеринбург: ГОУ ВПО УГТУ-УПИ 2003. 100с.
Курсовое проектирование грузоподъёмных машин: Учеб. пособие для студентов машиностроит. спец. вузов С.А. Казак В.Е. Дусье Е.С. Куз-нецов и др.; под ред. С.А. Казака. М.: Высш. шк. 1989.
Грузоподъёмные краны промышленных предприятий: Справочник И.И. Абрамович В.Н. Березин А.Г. Яуре. - М.: Машиностроение 1989. - 360с.
Подъёмнотранспортные машины. Атлас конструкций под ред. М.П. Александрова и Д.Н. Решетова. М. 1973.
Грузоподъёмные машины: Учебник для вузов по специальности «Подъёмно-транспортные машины и оборудование» М.П. Александров Л.Н. Колобов Н.А. Лобов и др.: – М.: Машиностроение 1986 – 400 с.