Модернизация фрезерно-центрирующего полуавтоматического режима. МРИ1-М




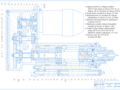
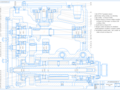
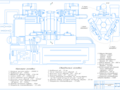
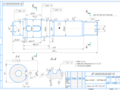
- Добавлен: 25.01.2023
- Размер: 1 MB
- Закачек: 1
Описание
Состав проекта
![]() |
![]() |
![]() ![]() ![]() |
![]() ![]() ![]() |
![]() |
![]() ![]() ![]() ![]() |
![]() |
![]() |
![]() ![]() ![]() ![]() |
![]() |
![]() |
![]() ![]() ![]() ![]() |
![]() |
![]() |
![]() |
![]() ![]() ![]() ![]() |
![]() |
![]() |
![]() |
![]() ![]() ![]() ![]() |
![]() |
![]() |
![]() ![]() ![]() ![]() |
![]() ![]() ![]() |
![]() ![]() ![]() |
![]() ![]() ![]() |
![]() ![]() ![]() |
![]() ![]() ![]() |
![]() |
![]() ![]() ![]() |
![]() ![]() |
![]() ![]() ![]() |
![]() ![]() ![]() |
![]() ![]() ![]() |
![]() ![]() |
![]() ![]() ![]() |
Дополнительная информация
3_Формоутворення.doc
1 Аналіз конструктивно - технологічних властивостей деталі.
Деталь вал КС6В 120916018 виготовляється з сталі 40Х ГОСТ 4543-81. вихідною заготовкою для виготовлення деталі є штамповка. Діаметри шийок вала за виключенням 45к6 зменшується до торця вала. В конструкції даної деталі немає фланців з великими перепадами діаметрів по відношенню до основної частини.
В конструкції вала передбачено шпонковий паз на шийці 60к6 на яку встановлюється зубчасте колесо. Також передбачена шліцева поверхня -
Д: 45х259р ГОСТ 6033-80.
Для забезпечення необхідної твердості треба провести термообробку. Щоб забезпечити шорсткість поверхонь 125 і 32 необхідно здійснити шліфування цих поверхонь.
Деталь є досить високої точності так як є велика кількість ділянок з 6-м квалітетом. Вал є досить жорстким що дозволяє забезпечити необхідну точність.
З точки зору технологічності дану деталь можна вважати технологічною.
Конструкція вала не має поверхонь для обробки яких необхідно було б використовувати дороге обладнання. Обробку поверхонь вала можна проводити прохідними різцями.
Так як діаметри шийок вала зменшуються до торця вала то є можливість проводити обробку на гідрокопірувальних або багаторізцевих напівавтоматах. Використання цього високопродуктивного обладнання дозволяє зменшити час на обробку поверхонь тобто збільшити продуктивність.
Даний вал використовується в редукторі для передачі крутного моменту.
Основні механічні властивості матеріалу:
границя текучості = 80кг-смм2;
границя витривалості =100 кг-смм2.
2 Аналіз схем формоутворення та вибір комплексу рухів.
Будь-яку поверхню можна уявити у вигляді сукупності декількох простих: плоских циліндричних конічних сферичних торових евольвентних гвинтових.
Кожна поверхня уявляється як слід руху однієї лінії (твірної) по іншій (направляючій). Ці лінії називають відтворюючими.
Для виконання будь-яких поверхонь необхідно здійснити формоутворюючі рухи тобто рухи інструмента і заготовки узгоджені між собою.
Проаналізуємо які методи формоутворення можна використати для утворення торцевих поверхонь деталі і центрових отворів.
Фрезерування торців вала.
Рисунок 3.1 - Схема обробки торцевими фрезами з рухомою (б) і нерухомою (а) заготовкою
Рисунок 2.2. - Схема обробки циліндричними фрезами з рухомою (б) і нерухомою (а) заготовкою
Рисунок 3.3 - Схема обробки конічними фрезами з рухомою (5) і нерухомою (а) заготовкою
Рисунок 3.4 – Схема обробки прохідними різцями
Обробка центрових отворів
Рисунок 3.5 - Схема обробки центрувальними свердлами з рухомою (б) і нерухомою (а) заготовкою
Рисунок 3.6 - Схема обробки циліндричними свердлами з рухомою (б) і нерухомою (а) заготовкою
Рисунок 3.7 - Схема обробки методом пластичної деформації
Проаналізувавши приведені вище схеми обробки вала і центрових отворів а також враховуючи рекомендації вимоги до оброблюваних поверхонь призначаємо обробку по схемах рис. 3.1(а) і рис. 3.5 (а).
Визначимо набори виконавчих рухів.
Технологічний модуль ТМ=ОСУ
Модульний комплект МК=ОСУw
Матриця можливих компоновок по ТМ
- твірна. Метод формоутворення - дотику Ф=2 (Ф1(О1) Ф5(П2)).
- направляюча . Метод формоутворення - сліду Ф=1 (Ф5(П2)).
Технологічний модуль ТМ= ОСZ Модульний комплект МК=ОС2w
-твірна. Метод формоутворення - копіювання Ф=0 (Вр(П2))
- направляюча. Метод формоутворення - сліду Ф=1 (Ф4(Оі)).
3 Розробка структурно - кінематичної схеми верстата.
У відповідності з вибраними схемами обробки та необхідними наборами виконавчих рухів складаємо структурно-кінематичну схему верстата.
Рисунок 3.8 - Структурно-кінематична схема.
ВИСНОВКИ.doc
Проектування складних агрегатів якими являються сучасні металорізальні верстати проводиться як правило на основі наявних прототипів чи конструкторських рішень. При створенні нового верстату використовують відпрацьовані і всесторонньо випробувані конструкції майже всіх його вузлів.
Конструювання верстату починається з підбору необхідних для виконання проекту креслень технічних описів і архівних матеріалів.
Однією з основних вимог які ставляться до сучасних металорізальних верстатів являється точність їх роботи. Під цим розуміється стабільність забезпечення верстатом заданої геометричної форми оброблюваної деталі якість її поверхні і точність розмірів які визначають основні параметри форми.
В цьому курсовому проекті:
Проведено аналіз схем формоутворення та запропоновано оптимальну структурно-кінематичну схему.
Проведено кінематичний розрахунок свердлильної головки шпиндельного вузла та запропоновано оптимальну кінематичну схему.
Проведено силовий розрахунок шпиндельного вузла на жорсткість. Запропоновано оптимальну конструкцію шпиндельної головки.
Вал _А3.cdw

А1(готово).cdw

Схема_А1.cdw

Схема_А1.cdw

А1(готово).cdw

А1(готово).cdw

4_Конструювання свердлильної головки.doc
1.1 Опис конструкції та принципу роботи вузла
Свердлильні головки з самостійними вузлами і змонтовані зверху на коробках приводу. Шпинделі свердлильних головок приводяться в обертання від індивідуальних фланцевих електродвигунів змінного струму. Шпиндель свердлильної головки має 6 ступенів чисел обертів в межах 238 - 1125 обхв. Зміна швидкостей обертання шпинделя здійснюється змінними зубчастими колесами розміщеними в торці задньому свердлильної головки.
Подача пінолей здійснюється від гідроциліндрів і забезпечує цикл роботи що включає швидкий підвід робочий хід і швидкий відвід. Зміна здійснюється від своїх гідропанелей. Центрувальні свердла затискуються в самоцентруючі затискні цанги.
По розрахованій потужності по каталогу вибираємо двигун А02-21-4
для якого N = 11 кВт n = 1400 обхв = 087.
Проведемо перевірку двигуна по нагріву методом еквівалентної
Рисунок 4.1.1 – Графік потужності
Потужність холостих ходів:
Робоча потужність Р3 = 05 кВт
Потужність врізання Р2 = 14·Р3 = 14 ·05 = 07 кВт.
Еквівалентна потужність - Р0
РеР0 отже двигун вибрано вірно.
1.3 Кінематичний розрахунок вузла.
На даному верстаті передбачається обробляти центрові отвори свердлами 4x11 - 6x15 мм. Тому для розрахунку приймаємо:
Dmax = 6 мм dmin = 4 мм. Тоді швидкості різання Vmax = 141 мхв Vmin=45мхв..
Мінімальна частота обертання свердлильної головки визначаються за формулою :
Максимальна частота обертання:
Діапазон регулювання частот обертання:
Для визначення числа ступеней частот обертання шпинделя
приймаємо φ = 126. Тоді:
де t - число ступеней швидкості різання.
Для переналадки верстата на інший режим буде використовуватись гітара змінних коліс так як верстат спеціальний. Виходячи з цього будуєм структурну сітку.
Рисунок 4.1.2 - Структурна сітка.
Так як сітка симетрична то кожна пара коліс може використовуватись
два рази: як прискорююча і як сповільнююча.
З структурної сітки:
тоді і3 = φ = 126; і2 = φ2 = 158; і1 = φ3 = 20;
і4 = 1φ = 1126; і5 = 1φ2 = 1158; і6=1φ3 =12.
Вибрані значення передаточних віношень задовольняють умову
≤ і ≤ 2. Приймаємо іо= 1φ4 = 1126.
Для визначення чисел зубів знаходимо по таблиці таку суму Z яка б задовольняла три передаточних відношення: і1(і6) і3(і5) i3(i4) Σ=108
Для передаточного відношення іо Σz=111
Результати вибору чисел зубів коліс зводимо в таблицю 4.1.1:
Таблиця 4.1.1 - Числа зубів коліс
Маючи числа зубів будуємо графік чисел обертів:
Рисунок 4.1.3 - Графік чисел обертів.
1.4 Розрахунок осьової жорсткості шпиндельного вузла
Рисунок 4.1.4 - Схема навантаження
Проаналізувавши проведену вище схему бачимо що гілка К6 К8 К9 розвантажується тобто осьове зусилля сприймається гілкою К1 К2 К3 К5 К6 К7. Осьова деформація шпинделя визначається за формулою:
де Р – осьова сила Н;
К – жорсткість стику;
N – кількість стиків.
Осьова жорсткість шпиндельного вузла
Обчислимо податливість кожного стику. Для плоских нерухомих стиків 1 2 4 5 7 лінійна податливість:
де С = 19·10-9 - для контакту сталь-сталь;
Р - осьова сила Н; Р = 200 Н;
F - площа контакту мм2.
Площі стиків: F1 = 1500 мм2; F2 = 1688 мм2; F4 = 1394 мм2;
F5 = 1825 мм2; F7= 1320 мм2.
Підставляючи значення в формулу для визначення податливості отримаємо: ; ;;
Для підшипника 3 лінійна податливість
де Ку = 15·10-6 - коефіцієнт контактної податливості для упорного підшипника.
Осьова жорсткість шпиндельного вузла :
2 Конструювання фрезерної головки
2.1Опис конструкції та принципу роботи вузла.
Фрезерні головки змонтовані на направляючих коробках привода і при допомозі шліцевого вала шестерні і рейок отримують рух від одного гідроциліндра. Шпинделі фрезерних головок приводяться в рух від індивідуальних фланцевих двигунів змінного струму. Ліва фрезерна головка вздовж станини не переміщається. Переміщення правої головки проходить разом з коробкою привода. Зміна швидкостей обертання шпинделів здійснюється змінними шестернями які розміщені біля заднього торця. Цикл роботи головки забезпечується системою електромагнітів та кінцевих вимикачів і включає швидкий підвід робочий хід і швидкий відвід.
По розрахованій потужності по каталогу вибираємо двигун. А02-42-4 для якого N = 55 кВт; n = 1440обхв; = 087.
Проведемо перевірку двигуна по нагріву методом еквівалентної потужності. Графік потужності зображений на рисунку 4.6.
Рисунок 4.2.1 – Графік потужності
Потужність врізання:
Р2=14· Р3=14·55 = 77кВт
Робоча потужність Р3=55кВт.
Еквівалентна потужність згідно [3с.315]
Ре Рпом отже двигун вибрано правильно.
2.3 Кінематичний розрахунок вузла.
На даному верстаті передбачається обробляти заготовки діаметром від 25 мм до 80 мм. Тому приймаємо розміри фрез:
Dmах=130м i Dmin = 90мМ.
Тоді швидкості різання Vmin =110 мхв Vmax = 354 мхв.
Мінімальну частоту обертання визначаємо за формулою:
nmin= (1000·Vmin)(·Dmax) [7 с.90]
Dmax - максимальний діаметр фрези мм.
nmin= (1000·110)(314·130)=270 обхв.
nmax= (1000·Vmax)(·Dmin) [7 с.90]
Dmin - мінімальний діаметр фрези мм.
Rn=nmaxnmin =1250270 = 463
Для визначення числа ступеней частот обертання шпинделя приймаємо =126
Тоді Z=1 + (lgRnlg) = 1 + (lg46lg126) = 7
де Z - число ступеней швидкості різання.
Для переналадки верстата на інші режими буде використовуватись гітара змінних коліс так як верстат спеціальний. Виходячи з цього будуємо структурну сітку.
Рисунок 4.2.2 – Структурна сітка
Так як сітка симетрична то кожна пара коліс може використовуватись два рази: як прискорююча так і сповільнююча.
і1; і2; і3; і4; і5; і6; і7=
і4 = 1 тоді із = = 126; і2 = 2 = 158; і1 = 3 = 20; і5 = 1 2 = 1126;
і6 = 1 2 = 1158; і7=1 3 =12.
Вибрані значення передаточних відношень задовольняють умову 14≤і≤2.
Приймаємо іо та і6 рівними 12 =1158
Для визначення чисел зубів знаходимо по таблиці таку суму Z. Яка задовольнила б три передаточних відношення: і2(і6) і3(і5) і4. ΣZ= 82. Для передаточних відношень і0 та і8 ΣZ= 59 і ΣZ= 101 для відношення і1(і7) ΣZ= 81.
Результати вибору чисел зубів коліс зводимо в таблицю 4.2.1
Таблиця 4.2.1 - Числа зубів коліс.
Маючи числа зубів будуємо графік чисел обертів
Рисунок 4.2.3 - Графік чисел обертів.
2.4 Характеристики вузла.
Для спеціальних верстатів точність обертання залежить від необхідної
точності обробки :Δ=ΔД3
Де Δ- биття шпинделя;
ΔД - допуск на лімітуючий розмір виробу
Для нашого випадку ΔД =052 = 025 мм
Тоді Δ= 0253 = 0083 мм.
Жорсткість шпиндельного вузла визначається по деформації шпинделя під навантаженням. При цьому жорсткість на передньому кінці шпинделя Нмкм.
де F - сила прикладена на передньому кінці шпинделя
Y – прогин переднього кінця шпинделя.
При визначенні жорсткості шпинделя виходячи з вимог до точності обробки визначаю прогин Y від сил різання і моменту привода при відповідних режимах обробки. Він обмежуються допуском на лімітуючий розмір деталі:
Виходячи з нормальної роботи підшипників жорсткість на ділянці між опорами лежить в межах 250-500 Нмкм.
Дана характеристика також справляє значний вплив на якість обробки. Вібрації які виникають в шпиндельному вузлі негативно позначаються на точності і чистоті обробки стійкості інструмента і продуктивності верстата. Згідно рекомендації [1 с.209] власна частота коливань шпинделя повинна бути не нижче 400-600 Гц
Тепловиділення і температурні деформації шпиндельного вузла необхідно зводити до мінімальних значень так як вони впливають на точність обробки і роботоздатність опор. Допустимий нагрів на зовнішньому кільці підшипника складає 70°С.
2.5 Вибір конструктивної схеми шпиндельного вузла.
Для створення шпиндельного вузла у вигляді окремих агрегатних модулів зменшення трудоємкості конструювання виготовлення і експлуатації шпиндельних вузлів і експлуатації шпиндельних вузлів доцільно використовувати типові конструктивні схеми їх особливістю є те що осьове навантаження сприймається передньою опорою задня опора при цьому плаваюча тобто не закріплена в соьовому напрямку. Це підвищує радіальну жорсткість вузла зменшує теплові деформації переднього кінця шпинделя.
Рисунок 4.2.4 - Конструктивна схема шпиндельного вузла.
2.6 Вибір геометричних характеристик шпиндельного вузла.
Діаметр шпинделя в передній опорі приймаємо d = 80 мм.
Міжопорна відстань l = 270 мм.
Діаметр переднього кінця шпинделя dк = (1 - 12) d = 90 мм.
Діаметр шпинделя в задній опорі dк = (1 - 08) d = 70 мм.
Діаметр шпинделя в міжопорній частині dм = (1 - 09) d = 75 мм.
Виліт шпинделя С = (1 - 21) d = 75 мм.
2.7 Розрахунок оптимальної міжопорної відстані.
Конструктивні параметри шпиндельного вузла в значній мірі впливають на його жорсткість. Для отримання оптимальних жорсткісних характеристик вузла необхідно зробити раціональний вибір цих параметрів. При наближених проектних розрахунках шпиндель заміняють балкою на двох опорах з силою F прикладеною до консолі тобто на відстані С від передньої опори.
Рисунок 4.2.5 - Розрахункова схема.
Радіальну деформацію робочого кінця шпинделя можна представити в вигляді:
де Yпш - зміщення викликане прогином тіла шпинделя;
Yоп - зміщення викликано податливістю опор;
Yзс - зміщення зсуву від дії поперечних сил.
Рисунок 4.2.6 - Схема деформації шпинделя
Так як зміщення у = (3 - 6) у1·YΣ то при наближених розрахунках не враховуємо. Сумарну деформацію визначаємо за формулою [5с.92]
де Е - модуль пружності матеріалу шпинделя;
I1 2 - осьовий момент інерції січення шпинделя на консолі і між опорами;
k1 k2 - податливість передньої і задньої опор;
- коефіцієнт защемлення
Загальна податливість шпиндельного вузла:
Оптимальне значення міжопорної відстані визначаєм з рівняння:
Розв’язок кубічного рівняння дає значення оптимальної міжопорної відстані 10ПТ. Розрахунки здійснені з допомогою ЕОМ.
Вихідні дані для розрахунку представлені в таблиці 4.2.2.
Таблиця 4.2.2 - Вихідні дані для розрахунку.
Діаметр шпинделя в міжосьовій частині
Діаметр отвору в шпинделі
Діаметр кінця шпинделя
Податливість передньої опори
Податливість задньої опори
Виліт робочого кінця шпинделя
Коефіцієнт защемлення l опори
Таблиця 4.2.3 - Результати розрахунку
Розрахункова між опорна відстань
Оптимальна міжопрна відстань
Жорсткість шпиндельного вузла
2.8 Розрахунок радіальної жорсткості шпиндельного вузла.
Радіальну жорсткість даного шпиндельного вузла визначимо як для статично-визначеної системи прийнявши пару підшипників передньої опори за одну опору центр якої знаходиться на осі першого підшипника.
Рисунок 4.2.7 - Розрахункова схема.
Як бачимо зі схеми даний вал складений з трьох ділянок з різними моментами інерції. Так як перепади 6у то всі моменти інерції можна звести до приведеного з формулою:
Момент інерції окремої ділянки знаходимо за формулою:
де D - зовнішній діаметр мм;
d - діаметр отвору в шпинделі мм.
I1 = 314(704- 304)64 = 1 138 250 мм4 ;
I2= 314(754- 304)64 = 1 512 6275 мм4;
I3= 314(804 - 304)64 = 1 969 8595 мм4.
Тоді пр= (4553 · 104 + 27984 · 104+ 26593 · 104)360 = 1642 · 104мм4
Для визначення зміщення викликаного прогином тіла шпинделя необхідно представити систему як пружну балку на жорстких опорах:
Рисунок 4.2.8 - Розрахункова схема.
Зміщення кінця шпинделя знаходимо за правилом Верещагіна:
Wi – площа ділянки епюри моментів від заданої сили
Мі - координата центру ваги на епюрі від одиничної сили для відповідної ділянки.
Необхідні епюри представлені на рис. 4.2.9
Рисунок 4.2.9 - Епюри моментів.
М1 = Р · 75 = 910 · 75 = 68250 Н·мм
W1 = 23 · 75 · lH = 50 Н·мм
R2 = (Р · 75) 270 = (1 · 75)270 = 0277 Н
Тоді W2 = R2 · 23 · 270 = 0277 · 23 · 270 = 50 Н·мм Обчислимо значення шп:
Визначення зміщення викликаного податливістю опор представимо систему як жорстку балку на пружних опорах.
Р = 910Н; 1 = 2070 мм; а =75 мм.
Рисунок 4.2.10 - Розрахункова схема.
(оп+2)(1+2) = (1 + а)1.
звідси 0П = ((1 + а)1)(1+ 2) - 2 = ((1 + а)1) + (а1) 2
Користуючись законом Гука знайдемо зміщення в передній і задній опорах (1 і 2)
Реакція в опорах : R1 = Р(1 + а)1; R2 = Ра1.
Тоді 1 = (Р(1 + а)1)С1; 2 =( Ра1)С2
де Сi - податливість і-ї опори.
Прогин шпинделя знаходимо сумуючи 0П і щп
Σ=оп+ шп=179·10-3+168·10-3=34·10-3мм.
Жорсткість шпиндельного вузла:
Кшп=РΣ = 91034·10-3 = 2676 Нмкм.
Обчислимо податливість кожного стику.
Для плоских нерухомих стиків 2 3 5 6 10 лінійна податливість:
де С = 19-10-9 - для контакту сталь-сталь;
Площі стиків: F2 = 1460 мм2; F3 = 1055 мм2; F5 = 4082 мм2;
F6 = 4082 мм2; F10 = 2120 мм2.
Підставляючи значення в формулу отримаємо:
e^2 = 176·10-6 ; e^3 = 21·10-6 ; e^5 = 1·10-6 ; e^6 = 1·10-6; e^10 = 15·10-6;
Для плоского затягнутого стику 1 лінійна податливість:
де С=15·10-12 м3 ·H1
Лінійна податливість : е^1 = 125·10-12
Для підшипника 4 лінійна податливість е^ = Кр
де Кр=2·10-6 - коефіцієнт контактної податливості для роликових
3 Конструкція та принцип роботи привода.
Ліва і права коробки привода встановлюються на направляючих
Ліва коробка закріплюється жорстко а права може переміщуватись
вздовж станини в залежності від довжини оброблюваної деталі.
Переміщення здійснюється вручну з допомогою гвинта. Кріпиться
коробка в потрібному положенні за допомогою гвинтів і планок.
В розточках правої і лівої коробок встановлений шліцевий вал який
служить опорою двом тригранним барабанам. З допомогою
гідроциндрів розміщених в коробках привода здійснюється фіксація
затиск розфіксація і розтиск барабанів.
В лівій коробці привода розміщений сферичний мальтійський хрест за
допомогою якого через додаткову пару шестерень здійснюється поворот барабанів. Приводом служить окремий електродвигун. Керування двигуном забезпечує система кінцевих вимикачів та електромагнітів.
В розроблюваній коробці привода використовується електродвигун
А041-4 частота обертів вала n = 1450 обхв потужність 17 кВт.
2_Формування вихідних даних на проект.doc
1 Розрахунок режимів різання по операціях і переходах.
Розрахуємо аналітично режими різання для першого переходу операції 005.
Фрезерувати торці вала в розмір 1
нструмент - торцеві фрези з встановленими ножами з швидкоріжучої сталі ГОСТ 26695-85.
Розміри фрези; D=100мм; d=50мм; В=50мм; t=8.
Період стійкості фрези 180 хв.
Глибина різання: В=50мм;
Довжина робочого ходу Lрх =230мм;
Подача St=015мм [2 с.23 ]
Швидкість різання визначаємо за формулою:
де Сvg уm - коефіцієнт і показники степенів;
х = 01; р = 0; u = 015; Сv= 142;
е = 0.25; у =0.4; т = 0.2; [2 с. 29 ]
D - діаметр фрези мм;
Т - період стійкості фрези хв;
Z - кількість зубів фрези;
Кv =089 - коефіцієнт що враховує умови різання
V = ((142-1000025)(18002·501 ·01504·500'15)) · 089 = 143 мхв
-Число обертів шпинделя:
n= (1000·V)(·D) = (1000·143)(314·100) = 456 обхв
-Сила різання визначається за формулою:
Рz = ((10·Ср ·tх·Szy Вzy·z)(Dg·nw))·Кмр
де Ср=825; х = 095; у = 08;
n - частота обертів фрези обхв.
Рz= ((10· 825 ·5095 ·50 11 · 8 ·01508)(100 11 · 4560))· 075 = 2335Н
Мкр = (Рz·V)(1020 · 60) = (2335 ·100)(1020 · 60) = 1168 Н·м
-Потужність різання визначаємо за формулою:
N = (Рz·V)(1020 · 60) = (2335 ·143)(1020 · 60) = 53кВт
Таблиця 2.1 - Зведена таблиця режимів різання
Вступ.doc
В даний час і в майбутньому необхідне створення нових моделей верстатів штучних виробничих систем тому майбутні спеціалісти верстатобудівники повинні володіти основами конструювання верстатів і найважливіших вузлів. Для успішного застосування обчислювальної техніки при конструювання необхідно добре знати зміст процесу проектування всіх видів верстатного обладнання володіючи методами його моделювання і оптимізації.
В сучасних верстатах використовують велику кількість засобів вимірювання деколи дуже точних наприклад лазерні інтерферометри і т. д.
Сучасні металорізальні верстати забезпечують виключно високу точність виконання оброблювальних деталей.
1_ АНАЛІЗ ЗАВДАННЯ НА ПРОЕКТУВАННЯ.doc
1 Аналіз завдання на проект і обрунтування напрямків
Метою даного проекту є розробка конструкції спеціального фрезерно-центрувального верстата-автомата. Вихідними даними на проект є:
-робоче креслення деталі;
-технічні умови на виготовлення деталі;
-орієнтований тип виробництва.
Виходячи з програми випуску серійного виробництва і визначаємо ступінь автоматизації верстата.
Робоче креслення деталі дає нам уявлення про поверхні деталі та їх взаємне розміщення. Виходячи з конструкції деталі ми можемо визначити як буде розміщуватись деталь на верстаті та способи її базування і закріплення. При обробці валів послідовно з двох сторін необхідно здійснювати переустановку деталі. Це призведе до здійснення похибки базування. Тому при розробці верстата доцільно використати одночасну обробку торців з незмінним закріпленням вала як при фрезеруванні гак і при центруванні. Виходячи з цього ми можемо орієнтовно намітити компоновку верстата.
Фізичні властивості матеріалу деталі будуть визначати спосіб обробки і застосовуваний ріжучий інструмент. Звідси ми визначаємо режим різання і пропонуємо технологічний процес механічної обробки. Виходячи з режимів різання проводимо кінематичний розрахунок верстата та силовий розрахунок окремих вузлів.
Для аналізу уже розроблених на теперішній час верстатів та встановлення їх можливостей проводимо огляд спеціальної літератури. На основі аналізу проведеного в попередньому пункті за базовий верстат приймаємо фрезерно-центрувальний напівавтомат мод. МРТ1-М. Технічна характеристика
Діаметр оброблюваної заготовки мм25-125
Довжина оброблюваної заготовки мм200-500
Число швидкостей шпинделя фрези6
Межі чисел обертів шпинделя фрези обхв125-712
Найбільший хід фрезерної головки мм220
Межі подач ммхв20-40
Число швидкостей свердлильного шпинделя6
Межі чисел обертів свердлильного шпинделя обхв238-1125
Хід свердлильної головки мм75
Межі робочих подач свердлильної головки ммхв20-300
Тривалість холостих ходів хв03
Потужність електродвигунів кВт:
-фрезерної головки7510
-свердлильної головки 223
Габарити верстата мм
-довжина - ширина3140-1630
Категорія ремонтоскладності 7
Зміст.doc
1 Аналіз завдання на проект і обрунтування напрямків
Формування вихідних даних на проект 9
1 Розрахунок режимів різання по операціях і переходах .9
Оптимізація схем формоутворення 11
1 Аналіз конструктивно - технологічних властивостей деталі 11
2 Аналіз схем формоутворення та вибір комплексу рухів 12
3 Розробка структурно - кінематичної схеми верстата ..15
Конструювання верстатного обладнання ..16
1 Конструювання свердлильної головки 16
1.1 Опис конструкції та принципу роботи вузла ..16
1.2 Вибір двигуна 16
1.3 Кінематичний розрахунок вузла 17
1.4 Розрахунок осьової жорсткості шпиндельного вузла 20
2 Конструювання фрезерної головки ..21
2.1Опис конструкції та принципу роботи вузла 21
2.3 Кінематичний розрахунок вузла 22
2.4 Характеристики вузла .25
2.5 Вибір конструктивної схеми шпиндельного вузла 26
2.6 Вибір геометричних характеристик шпиндельного вузла ..26
2.7 Розрахунок оптимальної міжосьової віддалі .27
2.8 Розрахунок радіальної жорсткості шпиндельного вузла ..31
3 Конструкція та принцип роботи привода ..36
Перелік посилань .38
свердлильна3.doc
Кільце 112 ГОСТ 13942-80
Шпонка 10х8х20 ГОСТ 23360-78
Шпонка 6х6х32 ГОСТ 23360-78
Шпонка 8х7х20 ГОСТ 23360-78
Гвинт М8х22 ГОСТ 11738-72
Болт М8х25 ГОСТ 7808-70
Шайба 865 ГОСТ 6402-70
Болт М10х45 ГОСТ 7808-70
Шайба 1065 ГОСТ 6402-70
Гвинт М6х15 ГОСТ 11738-72
Шпилька М1045 ГОСТ 2203476
Гайка М10 ГОСТ 2524-70
Підшипник №50205 ГОСТ 2893-73
Гайка М90х2 ГОСТ 11871-80
Шайба 90 ГОСТ 11871-80
Штифт 6х40 ГОСТ 3129-70
Штифт 6х6х20 ГОСТ 3128-70
свердлильна2.doc
КП МОО 06О50.02.00.021
КП МОО 06О50.02.00.022
КП МОО 06О50.02.00.023
КП МОО 06О50.02.00.024
КП МОО 06О50.02.00.025
КП МОО 06О50.02.00.026
КП МОО 06О50.02.00.027
КП МОО 06О50.02.00.028
КП МОО 06О50.02.00.029
КП МОО 06О50.02.00.030
КП МОО 06О50.02.00.031
КП МОО 06О50.02.00.032
Підшипник №208 ГОСТ 8338-75
Підшипник №206 ГОСТ 8338-75
Підшипник №305 ГОСТ 8338-75
Підшипник №207 ГОСТ 8338-75
Підшипник №210 ГОСТ 8338-75
Підшипник №8110 ГОСТ 2533-79
Підшипник №7210 ГОСТ 333-79
Ущільнення 21-40 ГОСТ 1832-78
Ущільнення 1-125 ГОСТ 4862-78
Ущільнення 18-85 ГОСТ 3314-81
Ущільнення 18-115 ГОСТ 3314-81
Манжета 1-55-80 ГОСТ 8752-79
Кільце 30 ГОСТ 13942-80
Кільце 62 ГОСТ 13942-80
свердлильна1.doc
Складальне креслення
КП МОО 06О50.02.00.001
КП МОО 06О50.02.00.002.
КП МОО 06О50.02.00.003
КП МОО 06О50.02.00.004
КП МОО 06О50.02.00.005.
КП МОО 06О50.02.00.006
КП МОО 06О50.02.00.007
КП МОО 06О50.02.00.008.
КП МОО 06О50.02.00.009.
КП МОО 06О50.02.00.010
КП МОО 06О50.02.00.011
КП МОО 06О50.02.00.012
КП МОО 06О50.02.00.013
КП МОО 06О50.02.00.014
КП МОО 06О50.02.00.015.
КП МОО 06О50.02.00.016.
КП МОО 06О50.02.00.017.
КП МОО 06О50.02.00.018
КП МОО 06О50.02.00.019
фрезерна головка1.doc
Складальне креслення
КП МОО 06О50.03.00.001
КП МОО 06О50.03.00.002
КП МОО 06О50.03.00.003
КП МОО 06О50.03.00.004
КП МОО 06О50.03.00.005
КП МОО 06О50.03.00.006
КП МОО 06О50.03.00.007
КП МОО 06О50.03.00.008
КП МОО 06О50.03.00.009
КП МОО 06О50.03.00.010
КП МОО 06О50.03.00.011
КП МОО 06О50..03.00.012
КП МОО 06О50..03.00.013
КП МОО 06О50..03.00.014
КП МОО 06О50.03.00.015
КП МОО 06О50.03.00.016
КП МОО 06О50.03.00.017
КП МОО 06О50.03.00.018
КП МОО 06О50..03.00.019
КП МОО 06О50.03.00.020
КП МОО 06О50.03.00.021
КП МОО 06О50.03.00.022
фрез 3.doc
Шайба 1065 ГОСТ 6402-70
Гвинт М8х20 ГОСТ 11738-72
Гвинт М10х25 ГОСТ 11738-72
Гвинт М8х20 ГОСТ 1491-80
Гвинт М6х12 ГОСТ 1491-80
Кільце 70 ГОСТ 13942-80
Шайба 33 ГОСТ 11872-80
Шайба 48 ГОСТ 11872-80
Шайба 36 ГОСТ 11872-80
Гвинт М12х20 ГОСТ 1478-75
Гвинт М10х12 ГОСТ 1478-75
фрез 2.doc
КП МОО 06О50.03.00.024
КП МОО 06О50.03.00.025
КП МОО 06О50.03.00.026
КП МОО 06О50.03.00.027
КП МОО 06О50.03.00.028
КП МОО 06О50.03.00.029
КП МОО 06О50.03.00.030
КП МОО 06О50.03.00.031
КП МОО 06О50.03.00.032
Підшипник 36211 ГОСТ 831-85
Підшипник 36208 ГОСТ 831-85
Підшипник 7216 ГОСТ 333-79
Підшипник 214 ГОСТ 8338-75
Підшипник 207 ГОСТ 8338-75
Шпонка 8х7х42 ГОСТ 23360-78
Шпонка 10х8х40 ГОСТ 23360-78
Шпонка 10х8х35 ГОСТ 23360-78
Шпонка 8х7х38 ГОСТ 23360-78
Шпонка 10х8х135 ГОСТ 23360-78
Шпонка 6х6х18 ГОСТ 23360-78
Гайка М48х15 ГОСТ 11871-80
Гайка М36х15 ГОСТ 11871-80
Гайка М33х15 ГОСТ 11871-80
Гайка М90х2 ГОСТ 11871-80
Гайка М12 ГОСТ1 2524-70
Шпилька М12 60 ГОСТ22034-76
Шайба 1265 ГОСТ 6402-70
Перелік посилань.doc
Справочник технолога – машиностоителя в 2-х томах. Под ред. Р.К. Мещерякова и А.Г. Косиловой. М. «Машиностроение» 1984 – 495с.
Ф.М. Абрамов довідник по обробці деталей різанням” К. Техніка 1982.
Дубиняк С. А. Нагорняк С. Г. Дубецький .Д Шпинделі МРВ” Тернопіль 1980.
Иванов И. М. Детали машин” М. Вища школа 1971.
Дубиняк С. А. Нагорняк С. Г. Дубецький .Д Розрахунок передач валів муфт МРВ” Тернопіль 1980.
Дубиняк С. А. Нагорняк С. Г. Дубецький .Д Основи кінематичного розрахунку верстатів” Тернопіль 1980.
Металлорежущие станки и автоматы: ученик для машиностроительных втузов под ред. А.С. Проникова. – М.: Машиностроение 1981. – 479с.
Металорежущие станки под ред. Н.С. Ачеркана в 2т. - М.: Машиностроение 1965.
Металорежущие станки под ред. В.Э. Пуша. - М.: Машиностроение 1986. – 576с.
Н.С. Колев Л.В. Красниченко Н.С. Никулин. - Металорежущие станки. - М.: Машиностроение 1980. – 500с.
Детали и механизмы металорежущих станков том 1 под редакцией Д.Н. Решетова. – М.: Машиностроение. – 664с.
Анурьєв А. М. Справочник конструктора – машиностроителя в 3-ох т. М.: Машиностроение 1978.
С.А. Чернавский и др.. Курсовое проетирование деталей машин – 2-е узд. перераб и доп. – М.: Машиностроение 1988. 416с.
Підшипники кочення: Справ очник-каталог под ред. В.Н. Нарышкина и Р.В. Коросташевского. – М.: Машиностроение 1984. – 280с.
Режимы резания металлов. Справочник. Под ред. Ю.В. Барановського. М. «Машиностроение»1972.-260с.
Б.Л. Богуславский А.Н. Малов М.П. Новиков и др. Справочник металлиста в 5 томах т.2 М.: Машиностроение 1976. – 720с.
В.Т. Павлище Основи конструювання та розрахунок деталей машин: Київ «Вища школа» 1993. – 560с.
С.А. Дубиняк С.Г. Нагорняк И.В. Луців и И.Д. Дубецький Расчет деталей и узлов металорежущих станков с использованием ЭВМ”. Киев. УМКВО 1989.
Курсовое проектирование по технологии машинистроения под общей редакцией А.Ф. Горбацевича. Издательство «Высшая школа» Минск 1975.
Дипломное проектирование по технологии машинистроения под общей редакцией В.В. Бабука. Издательство «Вышэйшая школа» Минск 1975.
М.Е. Егоров В.И. Дементьев В.И. Дмитриев Технология машиностроения. Москва «Высшая школа» 1976.
Единая система допусков и посадок СЭВ в машиностроении и приборостроении. Справочник в 2 томах. Москва «Издательство стандартов» 1989.
С. Посацький Опір матеріалів – Видавництво Львівського університету 1973.
Рекомендуемые чертежи
- 30.05.2021