Модернизация электропривода механизма режущей головки бесцентрово-токарного станка ВС-160 прокатного цеха №3 ОАО ЗМЗ




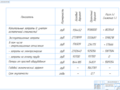
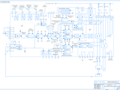
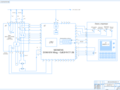
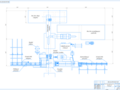
- Добавлен: 25.01.2023
- Размер: 3 MB
- Закачек: 1
Описание
Состав проекта
![]() |
![]() |
![]() |
![]() ![]() ![]() ![]() |
![]() ![]() ![]() |
![]() ![]() ![]() ![]() |
![]() ![]() ![]() |
![]() ![]() ![]() |
![]() |
![]() ![]() ![]() ![]() |
![]() ![]() ![]() ![]() |
![]() ![]() ![]() ![]() |
![]() |
![]() ![]() ![]() |
![]() ![]() ![]() ![]() |
![]() ![]() ![]() |
![]() |
![]() ![]() ![]() |
![]() ![]() ![]() ![]() |
![]() |
Дополнительная информация
6 Результаты VISSIM.cdw

бесцентрово-токарного станка ВС-160
Теоретический чертеж
бланк-задания_1.doc
ВЫСШЕГО И ПРОФЕССИОНАЛЬНОГО ОБРАЗОВАНИЯ
ЮЖНО-УРАЛЬСКИЙ ГОСУДАРСТВЕННЫЙ УНИВЕРСИТЕТ
по дипломному проекту (работе) студента
(фамилия имя отчество)
утверждена приказом по университету от «_27_»__апреля__2006 г. №_82_
Исходные данные к проекту (работе) __материалы преддипломной практики_
Консультанты по проекту (работе) с указанием относящихся к ним разделов проекта:
К А Л Е Н Д А Р Н Ы Й П Л А Н
Наименование этапов дипломного проекта (работы)
Срок выполнения этапов проекта (работы)
Отметка о выполнении
Обзор литературы и постановка задачи
Расчет режима резания и выбор электродвигателя
Расчет динамических параметров системы
Моделирование электропривода в пакете VisSim
Расчет параметров настройки
Оптимизация параметров моделирования
Определение затрат на модернизацию
Оформление пояснительной записки
8 экономика.cdw

остаточной стоимости)
- амортизационные отчисления
Сравнительный экономический
анализ модернизации.
Теоретический чертеж.
Эксплуатационные затраты
- затраты на электроэнергию
- затраты на оплату труда
Потери от простев оборудования
Годовой экономический эффект
Аннотация.doc
Процесс работы бесцентрово-токарного станка смоделирован в пакете динамического моделирования VisSim. Выполнена настройка регуляторов.
Предложена замена существующего двигателя на тихоходный без замены преобразователя.
Произведен расчет затрат и экономического эффекта. Рассмотрены вопросы охраны труда экологии и гражданской обороны.
5 Схема VISSIM.cdw
токарного ВС-160 в пакете
динамического моделирования VisSim
Теоретический чертеж
3 Чертеж схемы.cdw

частота вращения шпинделя
Станок бесцентрово-токарный
Схема электрическая функциональная.
Предварительное управление
Регулятор тока возбуждения
Заданное значение ЭДС
Модуль переключения групп
1 Чертеж общего вида.cdw

7 Результаты VISSIM.cdw

бесцентрово-токарного станка ВС-160
(после модернизации)
Теоретический чертеж
Полный.doc
Структура и технология производственного процесса
Расчет режима резания и выбор электродвигателя
Расчет динамических параметров системы
Моделирование электропривода в пакете VisSim
Расчет параметров настройки
Оптимизация параметров моделирования
Определение затрат на модернизацию
Гражданская оборона
Список используемой литературы
В связи с выходом отечественных производителей металлопродукции на внешний рынок и производством проката по стандартам ASTM DIN и другим к его качеству и геометрическим размерам предъявляются повышенные требования зачастую превышающие требования существующих ГОСТов и технических условий.
Качество металла экспортируемого в другие страны Златоустовским металлургическим заводом большая часть которого производится и обрабатывается в прокатном цехе №3 зависят от многих факторов одним из которых является качество итоговой обработки поверхности проката на бесцентрово-токарном станке немецкой линии ВС-160 фирмы KIESERLING.
При обработке прутков имеющих неоднородную структуру и различные физико-механические свойства возникают броски мощности резания которые отрицательно влияют на качество поверхности металла и точность геометрических размеров. Для различных режимов резания на станке установлен двухскоростной редуктор с коэффициентами передачи 1:209 и 1:462 но в обработке участвуют такие сортаменты и марки сталей что существующие режимы являются неудовлетворительными вследствие того что минимальная скорость обработки бесцентрово-токарного станка ВС-160 выше необходимой.
Снижение скорости обработки осуществляется снижением скорости электродвигателя гораздо ниже номинальной что приводит к увеличению тока в якоре выше номинального более чем в 2 раза и в дальнейшем к сгоранию щеточного механизма
В связи с этим в данном проекте предполагается модернизация системы электропривода со стабилизацией скорости резания на заданном уровне в большом диапазоне что оказывает положительное влияние на качество поверхности обрабатываемого металла.
Обзор литературы и постановка задачи
Станки бесцентрово-токарные предназначены в основном для удаления дефектного и обезуглероженного слоя с поверхности стальных круглых прутков большой длинны.
Принцип работы основан на совмещении двух движений: вращения резцовой головки и подачи прутка. Станки работают в автоматическом цикле. Шпиндельная бабка обеспечивает вращение резцовой головки. Станки оснащаются многорезцовой головкой с набором резцовых блоков. Подающий механизм обычно роликового типа обеспечивает зажим и подачу прутков через центрующий механизм в резцовую головку. Центрующий и поддерживающий механизмы обеспечивают гашение колебаний прутка во время резания.
Станки снабжаются загрузочным и разгрузочным устройствами а также транспортером стружки. Загрузочное устройство обеспечивает поштучную подачу прутков на рольганг подающего механизма или подачу прутка из бунта. Отделяющий механизм отделяет обработанный пруток от обрабатываемого и подает его на разгрузочное устройство которое выгружает обработанный пруток в накопитель. Управление автоматическим циклом работы станков осуществляется программируемыми контроллерами.
Конструкция станков обеспечивает возможность поднастройки резцов на величину износа режущей кромки без остановки процесса обработки. Станки имеют возможность механизированной переналадки механизмов на различные диаметры обработки. Процесс резания осуществляется при обильном охлаждении СОЖ и использовании стружколомателя для размельчения сливной стружки.
Основными технологическими требованиями являются обеспечение:
- самого широкого круга технологических режимов обработки с использованием современного режущего инструмента;
- максимальной производительности;
- наибольшей точности обработки;
- высокой чистоты обрабатываемой поверхности.
Удовлетворение всем этим и другим требованиям зависит от характеристик станка и режущего инструмента мощности главного привода и электромеханических свойств приводов подач и системы управления.
В современных станках с числовым программным управлением (ЧПУ) функции выполняемые электроприводом главного движения значительно усложнены. Помимо стабилизации частоты вращения при силовых режимах резания требуются обеспечение режимов позиционирования шпинделя при автоматической смене инструмента что неизбежно ведет к увеличению требуемого диапазона регулирования частоты вращения.
Динамические характеристики электропривода по нагрузке практически определяют точность и чистоту обработки изделия а также стойкость инструмента. Устойчивый процесс резания при необходимой точности и чистоте поверхности возможен если параметры настройки привода обеспечивают при набросе номинального момента нагрузки максимальный провал скорости не более 40% при времени восстановления не превышающем 025с.
Для выполнения модернизации необходимо рассмотреть несколько вариантов замены электропривода с двигателем постоянного тока. Возможным вариантом может быть система преобразователя частоты с векторным управлением асинхронным двигателем.
Возможность управления частотой вращения короткозамкнутых асинхронных электродвигателей была доказана сразу же после их изобретения. Реализовать эту возможность удалось лишь с появлением силовых полупроводниковых приборов - сначала тиристоров а позднее транзисторов IGBT. В настоящее время во всём мире широко реализуется способ управления асинхронной машиной которая сегодня рассматривается не только с точки зрения экономии энергии но и с точки зрения совершенствования управления технологическим процессом. Асинхронные двигатели широко распространены надёжны имеют относительно невысокую стоимость хорошие эксплуатационные качества но регуляторы скорости их вращения из-за сложности систем электронного регулирования частоты питающего напряжения стоили до начала 80-х годов дорого и не обладали качествами необходимыми для широкого внедрения в индустрию.
Быстрый рост рынка преобразователей частоты для асинхронных двигателей не в последнюю очередь стал возможен в связи с появлением новой элементной базы - силовых модулей на базе IGBT (биполярный транзистор с изолированным затвором) рассчитанный на токи до нескольких килоампер напряжением до нескольких киловольт и имеющих частоту коммутации 30 кГц и выше.
Существует два подхода к внедрению частотно-регулируемых приводов - простая установка преобразователя частоты или создание системы автоматического управления на базе преобразователей частоты.
Для связи с внешними системами управления технологическим процессом практически все преобразователи имеют развитые интерфейсы связи. Это дискретные входы и выходы аналоговые входы и выходы а также сетевые интерфейсы RS232 и RS485 позволяющие работать по известным стандартным протоколам.
Практически все преобразователи могут передавать информацию о величинах тока напряжения и частоты на статоре двигателя определяют момент на валу двигателя частоту вращения ротора развиваемую мощность на валу и много других текущих параметров. Все эти величины необходимы не только для корректного управления технологическим процессом но и для диагностирования как самого двигателя так и рабочего механизма на его валу. Эта и другая информация включая аварийно-предупредительную может передаваться по промышленным сетям к которым могут подключаться несколько десятков преобразователей. Наличие сетевого управления дает системам возможность организации единых управляющих комплексов организующих работу всего энергетического объекта с учетом анализа состояния оборудования и в энергоэффектвном режиме.
Система позволяет не только сообщить оперативному персоналу о случившейся аварии но и предупредить её появление. Она имеет возможность автоматически рекомендовать действия оператору или самостоятельно принять решение об изменении режима и состава работающего оборудования.
Принцип действия преобразователя заключается в преобразовании переменного трехфазного напряжения промышленной частоты в переменное напряжение с регулируемой выходной частотой.
Применение ПЧ позволяет снизить требования к высоковольтной линии питающей предприятие поскольку при пуске очередного электроприводного агрегата не происходит просадки напряжения в линии (пусковой ток в 5-10 раз меньше по сравнению с пуском на прямую); Мощность ПЧ используемого для пуска разгруженного двигателя составляет 20-30 процентов от номинальной мощности электроприводного агрегата что предопределяет высокие технико-экономические показатели пускового ПЧ.
Создание системы с частотно-регулируемыми приводами в которых управление частотой осуществляется наряду с контролем целого комплекса различных технологических параметров позволяет снизить не только потребление электрической энергии но и обеспечивает экономию потребления энергоресурсов всей системы.
В существующем варианте электропривода используются коллекторные двигатели мощностью 160 – 250 кВт номинальная частота вращения которых 1000 – 1500обмин с тиристорным преобразователем SIEMENS Тип: D380850 Mreg–GdGF4V57-3B Input: 380V 697A 5060Hz Output: ±380V 850A. Для различных режимов резания на станке установлен двухскоростной редуктор с коэффициентами передачи 1:209 и 1:462.
В проекте необходимо рассмотреть замену двигателя постоянного тока резцовой головки на двигатель удовлетворяющий техническим требованиям режима резания а также возможность модернизации механической коробки скоростей резцовой головки бесцентрово-токарного станка.
Технические требования к разрабатываемому электроприводу:
Частота вращения резцовой головки должна удовлетворять всем режимам резания.
Мощности резания стабилизированы на заданном уровне в большом диапазоне скоростей.
Технико-экономические показатели
Технические требования должны быть обеспечены при минимальной цене. Конструктивное исполнение устанавливаемого оборудования должно точно совпадать с модернизируемым. Для обеспечения повышенной надежности предусмотреть все возможные степени защиты блока управления и двигателя.
В рамках поставленной цели необходимо решить следующие задачи:
) рассчитать технико-экономические показатели при установке редуктора с большим передаточным числом и замене двигателя с меньшей номинальной частотой вращения.
Прокатный цех №3 состоит из множества участков среди которых можно выделить четыре основных:
- участок зачистки и складирования заготовки;
- участок нагревательных печей;
- участок стана 350500
- участок адъюстажа.
На участке зачистки и складирования заготовки производится завоз железнодорожным транспортом и укладка заготовки в пирамиды с помощью магнитных кранов. Далее металл проходит проверку на наличие поверхностных дефектов которые устраняются там же с помощью кислородных горелок. После снятия дефектов заготовка в соответствии с программой проката укладывается на рольганг для транспортировки к нагревательным печам.
На участке нагревательных печей заготовка постепенно проходя всю длину печи с помощью шагающего пода нагревается до необходимой температуры (750 – 1150Со). После нагрева металл выталкивается на линию проката стана 350500.
На стане металл проходит деформацию путем обжатия в прокатных валках клетей и принимает в итоге готовый профиль разрезается на мерные длины пакуется и транспортируется на участок адъюстажа.
На участке адъюстажа металл подвергается итоговой обработке на правильных машинах токарных станках и проходит конечную проверку на наличие внутренних дефектов на установках ультразвукового контроля.
В цехе осуществляющем деятельность по производству готового проката обработке и отправке заказчику металла организовывается круглосуточное оперативное управление оборудованием задачами которого являются:
- ведение требуемого режима работы;
- производство переключений пусков и остановов;
- локализация аварий и восстановление режима работы;
- подготовка к производству ремонтных работ.
Краткое описание машины.
Расположение оборудования и основные элементы бесцентрово-токарного станка ВС-160 показаны на рисунке 2.1.
Обрабатываемые прутки находятся на загрузочном стеллаже где они катаются к стопорам находящимся перед входным лотком. С помощью подъемного элемента и загрузочного рычага прутки поштучно укладываются на транспортные ролики входного лотка. Транспортные ролики приводятся в движение от привода подачи обточного станка и транспортируют пруток между двумя парами вталкивающих роликов.
Вталкивающие ролики которые также приводятся в движение от привода подачи транспортируют пруток через вращающуюся резцовую головку с четырьмя установленными на ней твердосплавными резцовыми инструментами. Резцовая головка установлена на торцевой стороне полого вала осуществляющего привод головки. Направляющие элементы перед и за резцовым инструментом обеспечивают центрирование и демпфирование прутка. Имеется возможность непосредственной подрегулировки инструмента во время обработки.
Перед тем когда задний конец прутка выходит и вталкивающих роликов их задачу начинает выполнять вытягивающая каретка привод которой осуществляется также от привода подачи.
После выхода прутка из резцовой головки зажимные кулачки вытягивающей каретки открываются и каретка возвращается в исходное состояние. Пруток далее транспортируется с помощью вытягивающих роликов на выходной лоток.
Отделяющий механизм отделяет обработанный пруток от обрабатываемого и подает его на разгрузочное устройство которое выгружает обработанный пруток в накопитель или если это необходимо прутки подаются непосредственно на правильно-полировальную машину. Станки снабжаются транспортером стружки.
В автоматическом режиме прутки загружаются во входной лоток в режиме «пруток за прутком» обеспечивающий повышение стойкости инструмента.
Управление автоматическим циклом работы станков осуществляется программируемыми контроллерами. Наблюдение за ходом всех операций а также управление ими осуществляется через пульт управления оператора находящийся непосредственно у станка. Пульт управления представляет из себя станцию с установленным на ней рабочим компьютером. Все программы управления и визуализации работают в среде операционной системы WINDOWS 3.11. Отображение всей информации производит жидкокристаллический цветной дисплей.
Конструкция станка обеспечивает возможность поднастройки резцов на величину износа режущей кромки без остановки процесса обработки. Станки имеют возможность механизированной переналадки механизмов на различные диаметры обработки. Процесс резания осуществляется при обильном охлаждении СОЖ и использовании стружколомателя для размельчения сливной стружки.
Коробка переключения передач имеет две ступени с передаточными числами 1:209 и 1:462 которые переключаются механически с помощью рычага установленного непосредственно у пульта оператора. Коробка переключения передач имеет электрическую связь с контроллером который производит автоматический расчет скорости обработки.
Рисунок 2.2 Механизм резцовой головки. Кинематическая схема.
Главный привод производит привод резцовой головки через двухступенчатый редуктор.
Привод подачи через передаточный механизм и распределительную коробку приводит:
- транспортные ролики входного лотка;
- две пары вталкивающих роликов;
- вытягивающую каретку через шарнирные валы коническую зубчатую передачу механизм свободного хода и муфту.
Для привода вытягивающих дуо-роликов предусмотрен отдельный двигатель постоянного тока.
Технические характеристики бесцентрово-токарного станка ВС-160:
Мощность двигателя резцовой головки кВт 75-250-250
Номинальная частота вращения обмин 450-1500-2500
Число оборотов резцовой головки
I ступень обмин98-324-542
II ступень обмин217-717-1200
Скорость подачи прутка ммин
(регулирование бесступенчатое)05-30
Исходный диаметр прутков мм42-168
Длина прутка мм3000-9000
Подрегулировка резцов по диаметру мм25
Максимальная глубина резания мм
(стандартным инструментом)25
Диаметр обработанного прутка мм40-160
Рабочий диапазон салазок (диаметр обработанного прутка)
I диапазон (без кассеты) мм40-65
III диапазон мм87-113
IV диапазон мм111-137
V диапазон мм135-160
Таблица 2.1 . Режимы резания для бесцентрово-токарного станка ВС-160
Группа ораба-тывае-мости
Диаметр прутка до обточки мм
Число оборотов резцовой головки обмин
Материал режущей части резца
У7 65Г 40Х 30ХМА 30ХГСА 38ХА ШХ15 12ХН3А О8Х13 А75
ХГСНА 12ТМФ 38Х2М10А 40ХН2МА 20ХН4ФА
Расчет режима резания и выбор электродвигателя
1 Расчет режима резания
В электроприводах главного движения токарных станков согласно 2 мощность электродвигателя определяется требуемой мощностью резания. Для определения мощности резания определим скорость резания V и тангенциальную составляющую силы резания Fz для самого тяжелого варианта работы — для наружной черновой обработке прутка диаметром 165 мм изготовленного из конструкционной стали марки 60ХН резцами из быстрорежущей стали марки Т5К10 согласно 3:
Скорость резания V ммин
где Сv = 340 — эмпирический коэффициент;
Т = 60 мин — стойкость резца;
t = 25 мм — глубина резания;
S = 5 ммоб — подача на один резец;
m = 0.2; y = 0.45 — эмпирические коэффициенты;
Кv - общий поправочный коэффициент определяемый по формуле
К1 - коэффициент влияния физико-механических свойств материала
К2 - коэффициент влияния состояния поверхности К2 = 09
К3 - коэффициент влияния материала инструмента К3 = 14
Частота вращения резцовой головки:
Тогда зная скорость резания V определим тангенциальную составляющую силы резания Рz:
где Сv x y n Kp - коэффициенты и показатели степени для расчета скорости резания
Kp - коэффициент учитывающий фактические условия резания Kp =1485
Крутящий момент М Н·м определяем
Мощность резания эффективная
Мощность резания (эффективная) Ne кВт определяется:
2 Выбор электродвигателя
Двигатель необходимый для данного проекта должен обеспечить все параметры рассчитанные выше а именно номинальную частоту вращения и мощность. Поскольку расчет велся для самого тяжелого режима резания то можно выбирать двигатель который проходит по мощности для этого варианта.
Выбираем двигатель 9 1GG6 – 188 фирмы «SIEMENS» так как он подходит по габаритным и установочным размерам. Двигатель при меньших скоростях обеспечивает больший момент что способствует большему быстродействию системы в целом при данном передаточном отношении и моменте инерции достигается оптимальное соотношение между приведённой массой двигателя и резцовой головкой. Двигатель имеет следующие параметры:
Номинальная мощность двигателя Рн = 100 кВт;
Номинальный ток двигателя Iн = 282 А;
Номинальное напряжение питания Uн = 400 В;
Момент инерции двигателя Jдв = 9.25 кг*м2;
Минимальная скорость вращения nm
Номинальная скорость вращения nн = 900 обмин;
Максимальная скорость вращения nma
Номинальный коэффициент полезного действия hн = 94%.
Сопротивление обмотки якоря Rz = 000956 Ом
Момент номинальный Мном = 640 Н·м
Произведем проверку выбранного двигателя по нагреву согласно 4:
t1 = 5 с — время разгона электродвигателя;
t2 = t4 = 5 с — время работы электродвигателя на холостом ходу;
t3 = 300 с — время работы электродвигателя с номинальной нагрузкой;
t5 = 1 с — межоперационное время;
I1 = 2Iн = 564 А — пусковой ток двигателя
I2 = 01Iн = 282 А — ток холостого хода электродвигателя;
I3 = 095Iн = 268 А — номинальный рабочий ток двигателя;
I4 = 01Iн = 282 А — ток холостого хода электродвигателя;
Поскольку полученный эквивалентный ток меньше номинального тока двигателя следовательно по нагреву данный двигатель подходит и выбран верно.
Рисунок 3.1 – Нагрузочная диаграмма электропривода в автоматическом режиме
Определим по эмпирическим формулам взятым из 6 недостающие данные.
Номинальная угловая скорость вращения двигателя:
Суммарное активное сопротивления якорной цепи электродвигателя определим из условия распределения потерь считая что половина потерь в двигателе идет на нагрев обмоток. Тогда:
Определим значение номинального магнитного потока:
Время регулирования то есть время за которое завершиться переходный процесс составит:
Опираясь на 5 определим коэффициент усиления тиристорного преобразователя как отношение среднего значения выпрямленного напряжения Ud0 к максимальному напряжению управления Uум =10 В.
где Кu = 0.428 — коэффициент схемы выпрямления.
Постоянная времени тиристорного преобразователя :
Постоянную времени тиристорного преобразователя принимаем равной Тп = 0.01 с — время достаточное для восстановления запирающих свойств тиристоров после прохождения полуволны напряжения через 0.
Определим граничный угол отпирания тиристоров:
где Се— коэффициент пропорциональности между скоростью и ЭДС двигателя.
Тогда подставив получим граничный угол отпирания тиристоров равным:
Определим индуктивность якоря двигателя по эмпирической формуле:
Определим постоянные времени полученной системы.
Электромагнитная постоянная якорной цепи двигателя:
Электромагнитная постоянная якоря двигателя:
Электромеханическая постоянная системы:
Массы и моменты приведены к валу двигателя. движущихся частей приведенная к валу двигателя Jm кг×м2
где м = 400кг – масса резцовой головки.
Суммарный момент инерции на валу двигателя JS кг×м2
Моделирование электропривода в пакете VisSim
Оценку качества управления процессом металлообработки целесообразно выполнять методом математического моделирования в программе «VisSim». Данная оценка проводится по показателям качества при переходных процессах которые возникают при изменении управляющих и возмущающих воздействий. Управляющим воздействием в ЭП по системе «управляемый преобразователь-двигатель» является задающие напряжение в зависимости от которого происходит пуск торможение и реверс двигателя. Возмущающим воздействием в частности является изменение по величине или направлению действия (знаку) момента статических сопротивлений.
Структурная схема электропривода с отрицательной обратной связью по скорости в относительных единицах приведена на рисунке 5.1.
Рисунок 5.1 – Структурная схема электропривода с отрицательной обратной связью по скорости в относительных единицах
Из рисунка 5.1 видно что данный электропривод состоит из регуляторов скорости и тока тиристорного преобразователя якорной цепи и двигателя. Регуляторы скорости и тока предназначены для регулирования скорости и тока по оптимальному закону. Звенья «Якорная цепь» и «Двигатель» реализуют реальный двигатель вместе со всей механической частью привода с учетом его электромагнитной и механической инерционности.
Выбор базовых величин приведен в таблице 5.1.
Напряжение питания системы управления тиристорным преобразователем Uу равно 10 В.
Таблица 5.1 – Выбор базовых величин
Для исследования привода в программе VisSim массы и моменты приведены к валу двигателя.
Суммарный момент трения на валу Н·м
Аналогично момент создаваемый силой тяжести Н×м приведённый к валу двигателя:
Момент силы точения Н×м
Ток короткого замыкания Iк.з. А
Момент короткого замыкания Мк.з. Н×м
Угловая скорость холостого хода w0 радс
Скорость точения приведенная к валу двигателя wточ радс
Угловое базовое перемещение вала двигателя lБ рад
Математическая модель для анализа переходных процессов в программе «VisSim» включает в себя все звенья структурной схемы электропривода приведенной на рисунке 5.1 причем момент сопротивления Мс в данной модели представлен суммой расчетных моментов трения тяжести и резания (точения) а для задания силы резания отдельно применён соответствующий блок также применён блок «Задание скорости». Ниже подробнее рассмотрены все блоки входящие в модель для анализа переходных процессов.
Блок «Задание скорости» приведенный на рисунке 5.2 необходим для формирования рассчитанной диаграммы скорости.
Рисунок 5.2 – Модель блока «Задание скорости»
Блок «Двигатель» рисунок 5.3 реализует двигатель вместе со всей механической частью (якорь и редуктор) привода с учетом его электромагнитной и механической инерционности.
Механическая инерционность учитывается механической постоянной якорной цепи электрическая инерционность – электромагнитной постоянной.
Рисунок 5.3 – Блок «Двигатель»
Блок «Преобразователь» представлен на рисунке 5.4 который реализует функцию
Рисунок 5.4 – Блок «Преобразователь»
Блок «Задатчик интенсивности» рисунок 5.5 предназначен для формирования необходимого темпа нарастания напряжения задания для ограничения ускорения двигателя.
Рисунок 5.5 – Структурная схема блока «Задатчик интенсивности»
Блок «Регулятора скорости» представлен на рисунке 3.6 предназначен для регулировки скорости двигателя и реализует функцию вида:
где kрс – коэффициент регулятора скорости равный отношению Т1 к Т2 .
С выхода регулятора скорости подаётся задание на регулятор тока которое необходимо ограничить но с учётом обеспечения двигателем максимального усилия подачи на резцовой головке. Ограничение задано с помощью блока Limit на уровне 023×Iк.з. равном 16×Iном.
Рисунок 5.6 – Блок «Регулятора скорости»
Блок «Регулятор тока» рисунок 5.7 выполняет функцию ограничения и формирования необходимой диаграммы тока и реализует функцию
где T3 и T4 – коэффициенты регулятора тока.
На вход регулятора тока подается сигнал равный разности сигналов UРС и UДТ в относительных единицах на выходе формируется задание для преобразователя.
Рисунок 5.7 – Блок «Регулятор тока»
Рисунок 5.8 – Карта задания силы резания
На рисунке 5.8 блок представляющий файл с расширением .map является картой задания силы резания а умножаемый на него логический блок с использованием X1 и X2 формирует участки на которых сила резания равна нулю. Ненулевая сила резания формируется при сочетании Х1 равном единице Х2 равном нулю при других комбинациях сила резания равна нулю.
Расчет параметров настройки
Настройка контура регулирования тока то есть определение постоянных времени Т3 Т4 произведена по общепромышленной методике согласно 8. Постоянная времени регулятора тока Т4 с
где – частота среза контура регулирования тока равная:
Частота регулятора тока сопряженная Гц
Аналогично настроен контур регулирования скорости (в дальнейшем КРС). Частота среза КРС Гц
Частота регулятора скорости сопряжённая Гц
Тогда постоянная времени:
Коэффициент регулятора скорости КРС
Оптимизация параметров моделирования
Значение коэффициентов для настройки параметров регуляторов выполнено по общепромышленной методике она даёт лишь примерное их значение. Более точные значения подбираются в соответствии с качеством переходных процессов.
Настройку начинают с исключения из блоков нелинейных элементов (ограничений) и силы трения. Сначала настраивают Двигатель с преобразователем по следующей последовательности:
- в двигателе обрывают обратную связь по ЭДС а на его вход подают единичное напряжение преобразователя проверяют соответствие якорной постоянной;
- двигатель соединяют через преобразователь с регулятором тока на который подают единичное возмущение настройкой коэффициентов Т3 Т4 добиваются качественного переходного процесса;
- замыкают обратную связь по ЭДС и подключают пропорционально-нтегральный регулятор скорости. В нём необходимо настроить сначала пропорциональный канал затем интегральный.
Для оптимальности передаточного отношения звеньев период Т3 должен быть равен
График переходного процесса для настроенного двигателя с напряжением задания равным единице представлен на рисунке 7.1.
Рисунок 7.1 – Скорость двигателя при П и ПИ регуляторах скорости
Перерегулирование двигателя по скорости составляет 109%. Настроенный так двигатель будет обеспечивать высокую точность и низкую скорость реакции на возмущения;
- далее подключают задатчик интенсивности и настраивают максимальное ускорение которое должен обеспечить привод т.е. настраивают темп нарастания напряжения задания (при этом перерегулирование привода изменится);
- в регуляторе скорости можно увеличить коэффициент передачи пропорционального канала тем самым повысить быстродействие и эффективность использования двигателя.
Результаты настройки системы:
Значение перерегулирования по скорости составляет 25 % при разгоне до максимальной скорости.
Изначально предполагалось что динамическая сила будет изменяться прямоугольно но в реальности за счёт инерционности цепи якоря она нарастает и спадает постепенно. В существующем режиме работы станка такого темпа разгона и торможения не требуется поэтому задатчиком интенсивности этот параметр доведен до 4 секунд. Следовательно пусковой и тормозной режимы проходят при более низких значениях тока якоря что сказывается на увеличении ресурса электродвигателя.
Качество поддержания скорости при точении обуславливает точность станка в целом так как сила резания зависит от скорости подачи.
На начальном участке (врезание резцов) скорость резко падает из-за большого прироста площади резцовой зоны на максимальную величину 00592 т.е. на 59% по мере увеличения периода вступления в работу всех четырех резцов в работу включается более медленный интегральный канал и скорость восстанавливается.
При выходе прутка из резцовой зоны нагрузка резко пропадает из-за этого возникают всплески скорости на максимальную величину 00528 (53%).
Значение шероховатости обрабатываемой поверхности можно прикидочно оценить разделив скорость вращения резцовой головки на частоту прохождения резцов т.е. это расстояние между соседними неровностями. Глубина неровностей зависит от силы резания и жёсткости всей системы т.е. это перекос резцов относительно прутка. Порядок шероховатости показан на рисунке 7.2.
Рисунок 7.2 – Шероховатость обрабатываемой поверхности
Рисунок 7.3 – Диаграмма тока в относительных единицах
Рисунок 7.4 – Диаграмма нарастания силы резания
Значение тока на пусках и реверсах двигателя не превышает 165 А при обработке максимальное значение равно 280 А. таким образом двигатель не перегружается.
Рисунок 7.5 – Диаграмма тока якоря без учета пульсации резц
Определение затрат на модернизацию
1 Расчет общей суммы затрат
Произведем расчет общей суммы единовременных затрат на модернизацию оборудования бесцентрово-токарного станка ВС-160 – Зк.
Зк = Соб + См + Снал - Др
где Соб – стоимость устанавливаемого оборудования;
См – стоимость монтажа и установки оборудования;
Снал – стоимость пусконаладочных работ;
Др – доход от реализации демонтируемых компонентов системы управления.
Для начала необходимо подсчитать стоимость выбранного оборудования. Список цен на двигатели и редуктора производства фирмы «Siemens» предоставлены московским представительством этой фирмы и сведены в таблицу 8.1.
Таблица 8.1 – Оборудование для модернизации станка.
Наименование изделия
Двигатель постоянного тока с независимым возбуждением мощностью 100 кВт.
Двухступенчатый редуктор
Итого: стоимость всего оборудования = 46890 ЕВРО.
По данным ММВБ от 20 мая 2006г. курс рубля к евро составил = 34руб. 44 коп. за 1 евро. Переводим стоимость оборудования в рубли. Стоимость оборудования в рублях:
где Спк – стоимость оборудования в евро;
К – курс рубля по отношению к евро.
С1 = 47500 3444 = 1615000 руб.
Произведем расчет стоимости оборудования – Соб.
где С1 – стоимость оборудования;
С2 – стоимость неучтенного оборудования.
В соответствии с 10 С2 принимается в размере 20 % от стоимости устанавливаемого оборудования С1:
С2 = C1 02 = 1615000 02 = 323000 руб.
Таким образом стоимость оборудования:
Соб = С1 + С2 = 1615000 + 323000 = 1938000 руб.
Стоимость монтажа и установки оборудования (См) рассчитывается по формуле:
где Соб – стоимость оборудования;
К1 – коэффициент величина которого принимается в соответствии
с 10 в размере 9% от Соб.
См = Соб К1 = 1938000 009 = 174420 руб.
Стоимость наладочных работ определяем по "Прейскурант на экспериментальные пусконаладочные и другие работы на установках" (Номер позиции 2.1.3 пункт 13.2.4 «Установка двигателей мощностью свыше 100 кВт» = 748 руб.
Учитывая что данный прейскурант был выпущен в 1986 году приблизительно посчитать стоимость наладочных работ можно умножая исходную цифру прейскуранта на поправочные коэффициенты:
где Сн – стоимость наладочных работ согласно прейскуранта;
К2 – коэффициент учитывающий увеличение цены с 1986 по 1990 год;
К3 – коэффициент учитывающий увеличение цены с 1990 по 2002 год.
Снал = Сн К2 К3 = 748 155 190 = 2203 руб.
Произведем расчет стоимости демонтажа модернизируемого оборудования и дохода от реализации демонтируемого. Доход от реализации демонтируемого оборудования рассчитывается следующим образом:
где Рсу – остаточная стоимость электрооборудования станка;
Зд – затраты на демонтаж оборудования.
Сначала рассчитаем стоимость демонтажа. Согласно данным БОТ и службы электрика прокатного цеха №3 для демонтажа оборудования станка ВС-160 необходимо задействовать двух рабочих пятого разряда в течение 1 смены. Подсчитаем стоимость затрат на демонтаж системы управления:
Зд = Т5 Тс Кс Кп Ку Кр Фсо
где Т5 = 149 руб. - тариф слесаря-электромонтера 5-го разряда основного цеха;
Тс = 8 – это количество часов в смене (ремонтный персонал работает по восьми часовому графику);
Кс = 11 – это коэффициент учитывающий дополнительную зарплату;
Ку = 115 – районный коэффициент;
Кр = 2 – число рабочих занятых в демонтаже оборудования;
Фсо – коэффициент учитывающий социальные отчисления с фонда оплаты труда принимается Фсо = 1.26.
Теперь подсчитаем затраты на демонтаж оборудования:
Зд = Т5 Тс Кс Кп Ку Кр Фсо =
= 149 8 11 18 115 2 126 = 684 руб.
Ввиду того что станок ВС-160 эксплуатируется в течение 12 лет оценку демонтажа существующего оборудования следует провести исходя из остаточной стоимости оборудования. Остаточная стоимость оборудования станка ВС-160 подсчитывается следующим образом:
гдеPст – остаточная стоимость станка ВС-160 согласно данным бухгалтерии завода на 2006 год составляла Pст = 28361300 руб.;
Кэл – коэффициент учитывающий в стоимости всего оборудования стоимость электрооборудования (для расчетов примем Kэл = 02);
Kсу – коэффициент учитывающий стоимость двигателя в стоимости электрооборудования станка (для расчетов примем Kсу = 02).
Таким образом остаточная стоимость оборудования станка ВС-160 считается:
Pсу = Pст Кэл Ксу = 28361300 02 02 = 1134452 руб.
Итак доход от реализации демонтируемых компонентов системы управления получится:
Др = Pсу – Зд = 1134452 – 684 = 1133768 руб.
В результате общая сумма затрат составит:
Зк = Соб + См + Снал – Др = 1938000 + 174420 + 2203 – 1133768 =
Амортизационные отчисления существующего оборудования определяются по установленным нормам отчислений на стоимость установленного оборудования и неучтенного оборудования:
Са = Сдс Кдс + Сдн Кдн
гдеСдс – стоимость демонтируемого оборудования;
Кдс – коэффициент амортизационных отчислений на установленное
оборудование (согласно [6] = 12% от стоимости установленного оборудования);
Сдн – стоимость неучтенного оборудования = 20% от стоимости
установленного оборудования;
Кдн – коэффициент амортизационных отчислений на неучтенное
оборудования (согласно 10 = 125 % от стоимости неучтенного оборудования).
Таким образом амортизационные отчисления составят:
Са = Сдс Кдс + Сдн Кдн = 1134452 012 + 323000 0125 =
= 13613424 + 40375 = 17650924 руб.
2 Расчет эксплуатационных затрат
Величину эксплуатационных затрат на функционирование оборудования определяем по следующим статьям. Для обеспечения технического обслуживания оборудования нет необходимости вводить новую штатную единицу. Необходимо подсчитать расход электроэнергии потребляемой в новом режиме работы оборудования.
Стоимость эксплуатационных расходов считается так:
Зэ.р. = З + Сэ + Са + Ср
гдеЗ – затраты на оплату труда;
Сэ – затраты на электроэнергию;
Са – амортизационные расходы;
Ср – затраты на ремонт оборудования.
Затраты на оплату труда (с учетом основной дополнительной зарплат и социальных отчислений) вычисляется следующей формулой:
З = Т6 Тм Кс Кп Ку Тг Фсо
где Т6 = 162 руб. - тариф слесаря-электромонтера 6-го разряда основного цеха;
Тм = 168 – месячный фонд рабочего времени (в часах);
Тг = 12 – число месяцев в году;
Фсо = 126 – коэффициент учитывающий социальные отчисления с фонда оплаты труда.
Основная зарплата работника не изменится и составит:
Зо = Т6 Тм Кс Кп Ку Тг Фсо =
= 162 168 11 18 115 12 126 = 93700 руб.
Затраты на электроэнергию составят:
где Nэ – установленная мощность технических средств согласно паспорта составляет 100 кВт. [4];
Тдо – действительный годовой фонд работы оборудования;
Сn – стоимость 1 кВтчаса электроэнергии (на май 2006 года = 12 руб.).
Действительный годовой фонд работы оборудования считается следующим образом:
где Тном – номинальный годовой фонд времени работы оборудования;
kп = 088 - коэффициент учитывающий потери времени на ремонт и текущее планово-предупредительное обслуживание.
Номинальный годовой фонд времени работы оборудования рассчитывается по формуле:
где Dg - число дней работы в году (Dg = 365 при непрерывной работе);
Tc - число часов работы в неделю (Tc = 168 часов при непрерывной
Dn - число дней работы в неделю (Dn = 7 для непрерывно работающих агрегатов).
Таким образом номинальный годовой фонд рабочего времени:
Тном = = = 8760 чгод.
Действительный годовой фонд работы оборудования:
Тдо = Тном kп = 8760 088 = 77088 чгод.
Затраты на электроэнергию потребляемую системой:
Сэ = Nэ Тдо Сn = 100 77088 12 = 925056 руб.
Амортизационные отчисления определяются по установленным нормам на стоимость устанавливаемого оборудования и неучтенного оборудования [6]:
К5 – коэффициент амортизационных отчислений на устанавливаемое
оборудование (согласно [6] = 12% от стоимости устанавливаемого оборудования);
С2 – стоимость неучтенного оборудования;
К6 – коэффициент амортизационных отчислений на неучтенное
оборудование (согласно [6] = 125 % от стоимости неучтенного оборудования).
Са = С1 К5 + С2 К6 = 1615000 012 + 323000 0125 =
= 193800 + 40375 = 234175 руб.
Затраты на текущий ремонт технических средств определяются:
К7 – коэффициент определяющий затраты на ремонт (согласно данных НИИ ЦСУ СССР [6] К7 = 5%).
Ср = Соб К7 = 1615000 005 = 80750 руб.
Таким образом стоимость эксплуатационных расходов:
Зэ.р. = З + Сэ + Са + Ср = 93700 + 925056 + 234175 + 80750 = 1333681 руб.
3 Расчет показателей экономической эффективности
Снижение себестоимости при повышении производительности:
гдеW = 83917 руб.т. - условно постоянные расходы на обработку рассматриваемой марки стали (нержавеющие марки стали.);
dp – коэффициент увеличения производительности труда при модернизации оборудования. Улучшение работы станка позволяет добиться роста производительности на 5-7 %. Для предварительных расчетов принимается dp = 6 %.
Таким образом снижение себестоимости:
dc = W = 83917 = 475 руб.т.
Годовая экономия от снижения себестоимости 1 т. металла считается как:
где dc – снижение себестоимости;
V – годовой план выпуска продукции;
dp – коэффициент увеличения производительности труда.
Годовой план выпуска продукции подсчитывается следующим образом:
где L – действительный годовой фонд работы оборудования;
Ps – часовая производительность станка в тоннах. Производительность станка по данным из паспорта позволяет станку обрабатывать до 17 тонн изделий в час. Для расчетов примем значение = 7 тонн в час (для прутка длиной 7 метров и диаметром 120 мм).
Действительный годовой фонд работы оборудования рассчитывается из следующих данных:
где kp – загрузка оборудования = 97% (по данным БОТ);
Тс – число суток работы станка в год;
Tp – использование рабочего время в сутки с учетом технологических перерывов.
Коэффициент Тр можно рассчитать следующим образом:
Тp = Rc – Rr – Ru – Rp
где Rc – число часов в сутках;
Rr – остановка станка для перестройки на другой размер. Для расчетов примем Rr = 1;
Rp – Уборка станка между сменами и перерыв на обед. При 12-ти сменном режиме работы потери времени на уборку станка между сменами составляют 1 час (05 часа на каждую смену). Первый перерыв на обед – 25 минут 2 перерыв на обед – 20 минут для каждой смены. Итого потери времени на обеденный перерыв = 15 часа. Для расчетов примем Rp = 25 часа.
Таким образом использование рабочего время в сутки с учетом технологических перерывов:
Тp = Rc – Rr – Ru – Rp = 24 – 1 – 25 = 205 часов.
L = kp Tp Tc = 097 205 365 = 7258 часов в год.
Годовой план выпуска продукции:
V = L Ps = 7258 7 = 65322 тонн в год.
Годовая экономия от снижения себестоимости 1 т. металла:
Эр = dс V = 475 65322 = 32889627 руб.
Согласно данным полученным от ремонтных служб 3-го прокатного цеха простои данного станка по причине аварийных ситуаций связанных с внезапным выходом из строя оборудования составляют около 10% рабочего времени. Из времени аварийного простоя на долю поломок механического оборудования приходится – 50% времени простоя а остальные 50% – приходятся на долю поломок электрооборудования (или 5% от рабочего времени станка).
Простой станка по причине выхода из строя электрооборудования также состоит из двух частей: простой по причине выхода из строя электроприводов (60% от времени простоя по причине поломок электрооборудования или 3% от общего времени работы станка) и простой по причине выхода из строя системы управления (40% от времени простоя по причине выхода из строя электрооборудования или 2% от общего времени работы станка).
Годовая экономия от снижения простоев:
где Тэк – экономия рабочего времени;
Ps – часовая производительность станка в тоннах;
W = 83917 руб.т. - условно постоянные расходы на обработку рассматриваемой марки стали (нержавеющие марки стали.).
Произведем подсчет экономии рабочего времени при внедрении новой системы управления:
где Тст – потери рабочего времени при существующей системе;
Тнов – потери рабочего времени при внедряемой системе управления.
Потери рабочего времени при существующей системе управления станка составляют:
где L – действительный годовой фонд рабочего времени;
Рст – коэффициент простоя оборудования при старой системе управления (согласно вышеизложенному = 3%) для расчетов примем = 003.
Тст = L Pст = 7258 003 = 2177 часа.
Потери от простоев оборудования по причине поломки составят:
Пс = Тст Ps W = 2177 9 83917 = 1644185781 руб.
Потери рабочего времени при внедряемой системе управления станка составляют:
Рнов – коэффициент простоя оборудования при внедряемой системе для расчетов примем = 0001.
Тнов = L Pнов = 7258 0001 = 726 часа.
Потери от простоев оборудования по причине поломки программируемого контроллера составят:
Пк = Тнов Ps W = 726 9 83917 = 5483137 руб.
Таким образом экономия рабочего времени составит:
Тэк = Тст – Тнов = 2177 – 726 = 21044 часов.
Годовая экономия от снижения простоев оборудования составит:
Эт = Тэк Ps W = 21044 9 83917 = 158935441 руб.
Итак ожидаемый экономический эффект от внедрения СОР составит:
Sk = Эр + Эт – Зк – Зэр = 22889627 + 158935441 – 980855 – 1333681 = =156378111 руб.
Срок окупаемости оборудования можно посчитать следующим образом:
(или приблизительно 85 месяцев).
ля наглядности эффективности модернизации можно показать таблицу сравнительных показателей для модернизируемой и существующей систем. Сравнительные показатели сведены в таблицу 8.2.
Таблица 8.2 – Сравнительный анализ модернизации
Капитальные затраты (с учетом остаточной стоимости)
Эксплуатационные затраты:
Окончание таблицы 8.2
–амортизационные отчисления
–затраты на электроэнергию
–затраты на оплату труда
Потери от простоев оборудования
Годовой экономический эффект
1 Краткое описание производственного участка
На участке нагревательных печей заготовка постепенно проходя всю длину печи с помощью шагающего пода нагревается до необходимой температуры (750 – 1150 Со). После нагрева металл выталкивается на линию проката стана 350500.
Оперативное управление осуществляет оперативный персонал. Управление всеми агрегатами происходит из специальных помещений машинных станций и машинных залов.
Управление режимом работы тепловых энергоустановок организовывается на основании планов проката.
2 Анализ всех производственных и экологических опасностей
Место расположения прокатного цеха №3 север города Златоуст. Физико-географические климатические условия общие для горнозаводской зоны.
Транспортными путями являются железнодорожный транспорт и автомобильная дорога.
В прокатном цехе №3 имеются электрические сети напряжением: 6 кВ и 04 кВ имеются масляные трансформаторы с трансформаторным маслом представляющие повышенную пожарную опасность.
В цехе могут иметь место следующие опасные и вредные производственные факторы:
- мостовые и электромагнитные краны;
- повышенная температура воздуха рабочей зоны;
- движущийся металл нагретый до высокой температуры;
- повышенное значение напряжения электрической цепи;
- вращающиеся и движущиеся механизмы;
- повышенное значение шума;
- электромагнитные поля;
- взрывопожароопасность;
- сосуды под давлением;
- автомобильный и железнодорожный транспорт.
На станке бесцентрово-токарном линии ВС-160 опасность несчастных случаев возможна:
- движением роликов (подъем и опускание);
- разгрузкой прутков вперед или назад;
- движением цилиндра под выходным лотком;
- движением и транспортировки прутков;
- поворотом выходных роликов;
- прищемлением из-за малого расстояния между прутками или между прутками и входящей воронкой роликами;
- манипуляцией в мульде или вход в мульду.
К работе на данную рабочую профессию допускаются лица не моложе 18 лет прошедшие предварительный медицинский осмотр и не имеющие противопоказаний к выполнению работы.
Рабочий при приеме на работу должен пройти вводный инструктаж. До допуска к самостоятельной работе рабочий должен пройти:
- первичный инструктаж на рабочем месте;
- проверку знаний по Инструкции охраны труда;
- проверку знаний по оказанию первой помощи пострадавшим в связи с несчастными случаями при обслуживании энергетического оборудования;
- проверку знаний по применению средств защиты необходимых для безопасного выполнения работ;
- обучение по программе подготовки персонала;
- ПТБ для рабочих имеющих право подготавливать рабочее место осуществлять допуск быть производителем работ наблюдающим и членом бригады в объеме соответствующем обязанностям ответственных лиц ПТБ.
Допуск к самостоятельной работе оформляется соответствующим распоряжением по предприятию.
Для защиты от воздействия опасных и вредных факторов необходимо применять следующие меры безопасности.
При работе на движущихся и вращающихся машинах и механизмах не должно быть развевающихся участков которые могут быть захвачены движущимися частями механизмов.
При необходимости нахождения вблизи горячих частей оборудования следует принять меры по защите от ожогов и действия высоких температур (ограждение оборудования вентиляция).
При выполнении работ на участках с температурой воздуха выше 33°С необходимо применять режим труда с интервалами времени для отдыха и охлаждения (на таких участках цеха устанавливают аэраторы).
При недостаточной освещенности рабочей зоны следует применять дополнительное местное освещение.
В рабочей зоне станка бесцентрово-токарного станка линии ВС-160 установлено 4 светильника местного освещения.
Для защиты от поражения электрическим током необходимо применить диэлектрические перчатки ковры изолирующие подставки.
Перед каждым пусковым устройством электродвигателей должны находиться диэлектрические коврики или изолирующие подставки.
Электромонтер должен работать в спецодежде и спецобуви и применять другие средства защиты выдаваемые в соответствии с действующими отраслевыми нормами.
Электромонтеру бесплатно должны выдаваться согласно отраслевым нормам следующие средства индивидуальной защиты:
- костюм хлопчатобумажный (на 12 мес.);
- сапоги кирзовые или ботинки (на 12 мес.);
- рукавицы комбинированные (на 3 мес.);
- куртка ватная (на 24 мес.).
При выдаче двойного сменного комплекта спецодежды срок носки должен удваиваться.
В зависимости от характера работ и условий их производства электромонтеру бесплатно временно должна выдаваться дополнительная спецодежда и защитные средства для этих условий.
Требования правил безопасности при ремонтно-наладочных работах
Важной задачей эксплуатации электрооборудования является обеспечение безопасности при его обслуживании. Условия производства работ на действующих электроустановках и необходимые организационные и эксплуатационные технические мероприятия для обеспечения безопасности строго регламентированы «Правилами эксплуатации электроустановок».
Действующими электроустановками считаются такие которые полностью или частично находятся под напряжением или на которые в любой момент может быть подано напряжение. В распределительных устройствах оборудование и ошиновку находящихся под напряжением ограждают или располагают на такой высоте чтобы случайное прикосновение к ним было невозможно.
Пульт управления станком и ящики управления механизмами размещены в удобных для работы оператора местах. Системой управления предусмотрены возможные ошибки оператора при работе станка кроме режима настройки когда любой механизм двигается при нажатии оператором соответствующей кнопки.
Электротехнический и технологический обслуживающий персонал модернизируемой линии должен пройти обучение по правилам безопасности труда. Кроме первоначального обучения необходимо проводить периодическую переподготовку и проверку знаний по правилам техники безопасности.
Необходимо строго и неукоснительно соблюдать все инструкции по технике безопасности в электроустановках напряжением до 380 вольт.
Перед началом работы на станке операторы (которые будут работать на этом станке) должны пройти подготовку для работы на станке под руководством опытных рабочих бригадиров или мастеров. Операторы должны знать особенности управления всем станком и его отдельными механизмами как с центрального пульта управления так и с ящиков местного управления отдельными механизмами. Операторы должны знать технологический процесс и режимы работы станка для исключения возможных аварийных ситуаций. Операторы не прошедшие подготовку на данном оборудовании не могут быть допущены к работе на станке ВС-160.
Перед началом работы оператор обязан проверить общее состояние станка. Запрещается запускать станок в работу в случаях обнаружения при внешнем осмотре неисправностей механизмов. Оператор обязан остановить станок и вызвать специализированный персонал при обнаружении неполадок в системе управления станком или неправильной работе механизмов. Запрещается также пользоваться при работе неисправными инструментом и принадлежностями станка.
Перед началом работы необходимо проверить уровни жидкости в гидросистемах маслостанции и системе охлаждения. Периодически проверяется также уровень смазки в редукторах станка. Перед установкой резцедержателей в резцовые головки шпиндельной бабки необходимо произвести очистку резцовых головок от стружки оставшейся от предыдущего периода работы. Для очистки пользуются крюками щетками или сжатым воздухом (при этом работа естественно ведется в защитных очках). Очистка от стружки осуществляется после остановки станка.
При возникновении во время обработки изделия сильных вибраций необходимо отрегулировать входные и выходные направляющие механизмы станка.
Для защиты оператора от выброса стружки из-под резцов при обработке станком изделия зона резания закрывается кожухом с блокировкой от открытия кожуха при работе шпиндельной бабки.
Персонал работающий на данном станке обязан носить спецодежду предусмотренную нормативом по нормам охраны труда.
Категорически запрещается передавать управление станком лицам специально не обученным для этой цели. Работы по монтажу ремонту обслуживанию электрооборудования проводить при отключенном электропитании.
При работе с электрооборудованием использовать только инструмент прошедший проверку на исправность изоляции. С целью защиты обслуживающего персонала от опасных напряжений все металлические части оборудования которые случайно могут попасть под напряжение необходимо соединить на защитный ноль - для потребителей подключенных к сети с защитным нолем а также к поясу заземления. Все соединения производятся медными проводниками.
На рабочем месте оператора должна быть вывешена инструкция по охране труда. На рабочем месте следует исключить наличие масла на полу либо должен быть предусмотрен деревянный настил.
В целях обеспечения охраны труда обслуживающего персонала системой управления станком предусмотрено наличие следующих элементов:
взаимные блокировки обеспеченные электрической схемой;
элементы ограничения хода (конечные выключатели);
защитные кожухи (с блокировкой) к находящимся в движении элементам.
Кроме вышеуказанного необходимо учесть следующие обстоятельства. Для местного освещения необходимо использовать розетку в 24В переменного тока. Минимальное значение уровня освещенности должно быть не менее 400 люкс.
Обслуживание станка должно производится специально подготовленным квалифицированным персоналом. Ремонт и уход за станками оборудованием и установками осуществляется только специализированным персоналом.
Операторам работающим на станке запрещено устранять выявленные в процессе работы неисправности следует вызвать специализированный персонал.
При выполнении планово-предупредительных ремонтов оборудования необходимо осуществить ремонт всех защитных приспособлений предусмотренных конструкции станка.
При обработке станком изделий из высокопрочного металла или при большом съеме металла с изделия ввиду больших усилий резания резко повышается температура в зоне реза что приводит к испарению эмульсии. Для защиты рабочего от испарений эмульсии предусмотрено подключение станка к цеховой системе вытяжной вентиляции.
Программируемый контроллер как и любое электронное устройство производит при работе электромагнитное излучение. Но в виду того что уровень излучения ничтожно мал а кроме того программируемый контроллер установлен в специальном шкафу в помещении машинных станций то дополнительной защиты рабочего от электромагнитного излучения не требуется.
Рабочее место оператора станка представляет из себя закрытую кабину с установленным в ней пультом управления что значительно снижает воздействие такого вредного производственного фактора как шум. Уровень вибраций и шума производимого станком зависит от правильности настройки входных и выходных поддерживающих роликов а также от правильности заточки резцов и выбора оптимального режима резания. При соблюдении данных условий уровень вибрации и шума не превышает допустимых нормами производственной санитарии пределов. В редких случаях (тяжелый для обработки металл или большой съем металла) в качестве защитного средства от производственного шума применяют наушники.
4 Производственная санитария
В соответствии со статьями 9 и 34 Закона РСФСР “О санитарно-эпидемиологическом благополучии населения” в прокатном цехе №3 осуществляется производственный контроль за соблюдением требований Санитарных правил. Проводятся профилактические мероприятия направленные на предупреждение возникновения заболеваний работающих в производственных помещениях. Осуществляется контроль за условиями труда и отдыха и выполнением мер коллективной и индивидуальной защиты работающих от неблагоприятного воздействия микроклимата.
При проведении работ на электроустановках прокатного цеха №3 необходимо обеспечить соблюдение санитарных норм допустимых уровней освещенности шума и напряженности электромагнитного поля в соответствии с санитарными нормами утвержденными Минздравом России 12.05.85 №3323. Действующие санитарные нормы в цехе приведены в таблице 9.1.
Таблица 9.1 - Санитарные нормы напряженности электромагнитного поля шума и освещенности.
Напряженность электромагнитного поля Е кВм
Рабочее освещение предусмотрено для всех помещений здания а также участков открытых пространств предназначенных для работы прохода людей и движения транспорта. В производственных помещениях освещенность проходов и участков где работа не производится составляет не более 25 % нормируемой освещенности создаваемой светильниками общего освещения.
Очистку светильников замену ламп и плавких вставок ремонт и осмотр осветительной сети производит персонал службы электриков.
Измерение освещенности рабочих мест производится при вводе в эксплуатацию и в дальнейшем по мере необходимости.
Осмотр осветительной сети производиться 1 раз в сутки дежурным персоналом.
Обнаруженные при проверке и осмотре дефекты должны быть устранены в кратчайший срок.
Согласно СНиП 23-05-95 спроектировано искусственное освещение на участке расположения линии ВС-160 прокатного цеха №3. Определим потребность количества светильников для соблюдения санитарных норм в помещении расположения шкафов оборудования и на рабочем месте.
Световой поток Ф лм.
где - нормируемая минимальная освещенность лк;
- площадь освещаемого помещения м2;
- коэффициент неравномерности освещения для люминесцентных ламп (ЛБ - лампы с белым спектром свечения) принимаем z =11;
- коэффициент запаса принимаем k =15;
- число светильников в помещении шт.;
- коэффициент использования светового потока ламп
- коэффициент учитывающий влияние отражающих свойств потолка стен и пола принимаем Кр =08.
где А - длина помещения м;
В - ширина помещения м;
H - высота светильника над рабочей поверхностью м.
Число светильников в помещении Nопределяется из формулы
Для соблюдения санитарных норм в помещении машинных станций и преобразователей линии ВС-160 прокатного цеха №3 установлено 8 светильников ЛБ 40 а непосредственно у станка для освещения рабочей зоны установлено 4 светильника.
4.2 Воздействие шума и вибрации на человека
Шум и вибрация являются причиной снижения работоспособности ослабления памяти внимания остроты зрения что может привести к травматизму и авариям. Длительное воздействие интенсивных шумов может вызвать частичную а иногда и полную потерю слуха. Степень вредности шума и вибрации зависит от частоты уровня (силы) продолжительности и регулярности их воздействия. Классификация шумов допустимые уровни шума на рабочих местах установлены в ГОСТ 12.1.003 – 76 «ССБТ. Шум. Общие требования безопасности» и СН 245 -71.
Источником шума в прокатном цехе №3 являются машинные агрегаты станки и насосные агрегаты. Уровень шума в прокатном цехе №3 составляет 68 ДбА при норме 75 ДбА.
Шум возникает в результате плохой балансировки центровки неуравновешенности роторов муфт маховиков и других вращающихся деталей и вследствие неплотного крепления деталей и перекосов недостаточной смазки а также от централизованной системы сжатого воздуха. Обслуживающий персонал обязан тщательно следить за исправностью и нормальной работой оборудования вовремя устранять подобные неполадки которые к тому же могут явиться причиной аварии.
В число основных мер по предотвращению воздействия шума на персонал входят комплексная автоматизация и дистанционное управление технологическими процессами вызывающих шум.
Для ограничения распространения шума используют звукоизолирующие кожухи полы стены перекрытия. Стены помещений где размещаются вызывающие шум агрегаты не рекомендуется окрашивать масляной краской и облицовывать метлахской плиткой так как это увеличивает отражение звука. В таких помещениях используют акустическую штукатурку акустическую черепицу войлок стекловолокно.
При эксплуатации машин производственных зданий и сооружений а также при организации рабочего места применяются средства и методы коллективной защиты по ГОСТ 12.1.029. А также применяются средства индивидуальной защиты по ГОСТ 12.4.051
Для предотвращения воздействия шума на обслуживающий персонал предусмотрено звукоизоляционное помещение дежурных электриков.
В прокатном цехе №3 вибрация конструкций так же как и шум вредно действуют на человека. Начальные стадии вибрационной болезни при воздействии общей вибрации характеризуются головными болями нарушениями сна повышенной утомляемостью и раздражительностью. Иногда наблюдаются головокружения. Вибрация может быть причиной функциональных расстройств нервной и сердечно-сосудистой систем а также опорно-двигательного аппарата. Основные требования по устранению вибрации изложены в стандарте 12.1.012 – 78 «Вибрация. Общие требования безопасности». Защита от вибрации осуществляется путем устройства упругих элементов размещенных между вибрирующей машиной и основанием на котором она установлена.
4.3 Влияние электромагнитного поля на живые организмы
Непосредственное (биологическое) влияние электромагнитного поля на человека связано с воздействием на сердечно – сосудистую центральную и периферийную нервные системы мышечную ткань и другие органы. Вредные последствия пребывания человека в электрическом поле зависят от напряженности поля Е кВм и от продолжительности его воздействия данные указаны в таблице 6.1.
Согласно СанПиН 2.2.4.1191-03 предельно допустимый уровень напряженности электромагнитного поля на рабочем месте в течение всей смены устанавливается равным 5 кВм.
Контроль за соблюдением требований санитарных правил в прокатном цехе №3 осуществляется органами Госсанэпиднадзора и лицами ответственными за соблюдение правил по безопасным условиям труда в порядке проведения производственного контроля.
4.4 Отопление вентиляция кондиционирование воздуха
Помещения прокатного цеха №3 имеют как искусственную так и естественную вентиляцию. Отопление помещений осуществляется посредством батарей отопления и тепловых регистров. Температура в помещении поддерживается в пределах 200 С при постоянном присутствии обслуживающего персонала. Это соответствует санитарным нормам проектирования промышленных предприятий. Температура наружного воздуха при расчёте систем вентиляции воздуха и воздушного отопления принимаются в соответствии с требованиями СНиП 11-33-75.
Заземление в сети 6 и 04 кВ принято общим. В качестве естественных заземлителей используются металлические каркасы зданий различные трубопроводы. Кроме этого имеется наружный контур заземления. Наружный контур заземления соединен с внутренним контуром. Внутренний контур выполнен полосовой сталью 25 х 4 мм2 и проложенной по стенам на высоте 07 м от уровня пола. Все соединения в сети заземления выполнены сваркой а к корпусам двигателей болтовым соединением. Сопротивление растекания тока заземлителя не превышает 4Ом.
6 Противопожарная безопасность
Руководители прокатного цеха №3 несут ответственность за противопожарную безопасность помещений и оборудования тепловых энергоустановок а также за наличие и исправное состояние первичных средств пожаротушения.
Категория противопожарной безопасности для помещения и оборудования прокатного цеха №3 определена как В по ОНТП 24-86 то есть производство связанное с применением взрывоопасных веществ и материалов. Прокатный цех №3 построен из несгораемых материалов стены сделаны из кирпича и бетона перекрытия – из железобетона пол – из бетона.
Кабели в прокатном цехе №3 проложены в кабельных каналах и тоннелях подвесных металлических лотках и в трубах с соблюдением требований и рекомендаций обеспечивающих пожарную безопасность в кабельном хозяйстве.
Основы пожарной защиты предприятия определены государственными стандартами ССБТ (ГОСТ 12.1.004-85 и ГОСТ 12.1.010-76).
Персонал обслуживающий машинные залы проходит противопожарный инструктаж занятия по пожарно-техническому минимуму участвует в противопожарных тренировках.
В цехе установлен противопожарный режим работы и выполняются противопожарные мероприятия а также разработан оперативный план тушения пожара не допускающий действий которые могут привести к пожару или возгоранию.
На участке вывешен список расчетов и номера телефонов пожарной службы предприятия и муниципальной пожарной службы. Все работники должны пройти инструктаж по действиям в случае пожара. При обнаружении возгорания мастер ставит в известность диспетчера завода проводит оповещение по громкой связи персонала принимает меры по тушению пожара своими силами предварительно отключив электроснабжение участка.
Разработана и утверждёна инструкция о мерах пожарной безопасности и план (схема) эвакуации людей в случае возникновения пожара на тепловых энергоустановках приказом руководителя назначены лица ответственные за пожарную безопасность отдельных территорий зданий сооружений помещений участков создана пожарно-техническая комиссия и система оповещения людей о пожаре.
По каждому происшедшему случаю пожара или загорания проводится расследование комиссией создаваемой руководителем предприятия или вышестоящей организацией. Результаты расследования оформляются актом. При расследовании устанавливается причина и виновники возникновения пожара (загорания) по результатам расследования разрабатываются противопожарные мероприятия.
Цех оборудован сетями противопожарного водоснабжения установками обнаружения и тушения пожара в соответствии с требованиями нормативно-технических документов.
В прокатном цехе №3 предусмотрен набор первичных средств пожаротушения:
- огнетушители ОУ ОХП;
- противопожарный инвентарь (лопаты песок ломы топоры багры);
- на этаже установлены пожарные гидранты с таким расчетом чтобы обеспечить подачу воды в любую точку помещения.
В каждом шкафу находится брезентовый рукав длинной не менее 10 м со стволом.
Окраска составных частей установок пожаротушения включая трубопроводные коммуникации соответствует требованиям ГОСТ 12.4.026—76 и отраслевых стандартов.
Огнетушители размещаются в легкодоступных и заметных местах где исключено попадание на них прямых солнечных лучей и непосредственное воздействие отопительных и нагревательных приборов. Обеспечивается возможность прочтения маркировочных надписей на корпусе а также удобство и оперативность пользования ими.
Руководители прокатного цеха №3 периодически проходят соответствующую подготовку в области экологической безопасности согласно списку составленному и утвержденному руководителем предприятия.
Принимаются меры для предупреждения или ограничения вредного воздействия на окружающую среду выбросов загрязняющих веществ в атмосферу и сбросов в водные объекты шума вибрации и иных вредных физических воздействий а также по сокращению безвозвратных потерь и объемов потребления воды.
В процессе обработки изделия на станке ВС-160 используются различные масла а также водная эмульсия (которая состоит из эмульсина воды и соды). Поэтому полностью выработавшая свой ресурс эмульсия должна сливаться в специальные емкости и отправляться на очистку для повторного использования либо утилизации (при невозможности регенерации эмульсии). Отработанное масло также сливается в специально предназначенные для этого емкости и отправляется на переработку.
При работе станка в режиме больших скоростей подач и при большом съеме стружки с изделия температура в зоне реза резко повышается нагревая эмульсию. Происходит процесс испарения эмульсии с выделением вредных для здоровья человека паров. Для исключения отравления оператора парами эмульсии на станке устанавливается система вытяжной вентиляции которая подсоединена к цеховой сети вытяжной вентиляции.
Программируемый контроллер является микропроцессорным устройством которое при работе производит вредное для организма человека электромагнитное излучение. Для исключения влияния излучения контроллера на оператора программируемый контроллер устанавливают в отдельный шкаф который в свою очередь устанавливается в ПСМ со всем остальным электрооборудованием станка. Оператору во время работы станка доступ в ПСМ запрещен. Доступ имеет только специализированный обслуживающий персонал.
Все демонтируемое оборудование включается в резерв цеха.
Российская система предупреждений и действий в ЧС призвана решать значительно больший круг задач чем ранее ГО.
Центральная задача – проведение мероприятий:
- по предупреждению аварий катастроф и стихийных бедствий;
- по обеспечению безаварийной работы;
- по максимальному снижению разрушений людских и материальных потерь в случае возникновения непредвиденных аварийных обстоятельств;
- по повышению устойчивости.
Они охватывают инженерную радиационную химическую медицинскую защиту.
1 Мероприятиями по повышению устойчивости работы прокатного цеха №3
Основными мероприятиями по повышению устойчивости работы прокатного цеха №3 являются:
- повышение прочности и устойчивости прокатного цеха №3 и совершенствование технологического процесса;
- повышение устойчивости материально-технического снабжения;
- повышение устойчивости управления прокатного цеха №3;
- разработка мероприятий по уменьшению вероятности возникновения вторичных факторов ЧС и ущерба от них;
- подготовка к восстановлению производства после аварии в цехе.
Повышение устойчивости оборудования достигнуто не только путем усиления его наиболее слабых элементов но и созданием запасов этих элементов отдельных узлов и деталей материалов и инструментов для ремонта и восстановления поврежденного оборудования.
Устойчивость систем энергоснабжения прокатного цеха №3 повышено путем подключения его к нескольким источникам питания удаленным один от другого на расстояние исключающее возможность их одновременного поражения.
К организационным мероприятиям повышающим устойчивость управления прокатного цеха №3 относится заблаговременная подготовка руководящих работников и ведущих специалистов к взаимозаменяемости. Для замены недостающих специалистов привлекают квалифицированных рабочих хорошо знающих производство.
2 Радиационное и химическое обеспечение
Основными задачами радиационной и химической защиты являются:
- выявление и оценка радиационной и химической обстановки методом прогнозирования и по данным поста РХН;
- выбор наиболее целесообразных действий производственной деятельности предприятия в условиях радиоактивного и химического заражения;
- организация и проведение дозиметрического и химического контроля;
- обеспечение рабочих и служащих средствами индивидуальной защиты приборами радиационной и химической разведки дозиметрического контроля поддержание их в постоянной готовности.
Рабочим выданы средствами радиационной и химической защиты: противогазы ГП-5 респираторы Р-2. Начальники смен обеспечены газоанализаторами и газосигнализаторами аккумуляторными фонарями.
Ремонт и градуировка средств РХЗ осуществляется в спец. предприятии г. Челябинска.
3 Медицинское обеспечение
Практическое обучение работников прокатного цеха №3 по оказанию первой доврачебной помощи пострадавшему на работе осуществляется по специальной программе.
4 Организация оповещения и связи
В случае возникновения опасности оповещение производится при помощи радио раций сирен находящихся в городе.
Замена электродвигателя позволяет увеличить точность обработки стабилизацию скорости резания на заданном уровне в большом диапазоне что оказывает положительное влияние на качество поверхности обрабатываемого металла. Уменьшить якорный ток двигателя до 90% от номинального на самом тяжелом режиме резания что сказывается на увеличении ресурса работы машины.
В экономической части проекта произведен расчет общей суммы затрат на модернизацию которая составляет 803548 рублей. Годовой экономический эффект от модернизации составляет 1165485 рублей а срок окупаемости капитальных вложений составляет 10 месяцев.
В разделе безопасности жизнедеятельности произведен расчет освещенности рабочей зоны станка. Рассмотрены вопросы экологии и гражданской обороны.
Бесцентрово-токарный станок ВС-160 фирмы KIESERLING. Паспорт.
Справочник технолога-машиностроителя. В 2-х т. Т. 2 под ред. А. Г. Косиловой и Р. К. Мещерякова. – 4-е изд. перераб. и доп. – М.: Машиностроение 1985. 496 с. ил.
Прогрессивные режущие инструменты и режимы резания металлов: СправочникВ. И. Баранчиков А. В. Жаринов Н. Д. Юдина и др.; Под общ. ред. В. и. Баранчикова. – М.: Машиностроение 1990.400 с. ил.
Капунцов Ю.Д. Елисеев В.А. Ильяшенко А.А. Электрооборудование и электропривод промышленных установок: Учебник для вузов Под ред. проф. М. М. Соколова. — М.: Высш. школа 1979г. — 359с. ил.
Сандлер А.С. Электропривод металлорежущих станков. Учеб. пособие для вузов. — М.: Высш. школа 1972г. — 440с.
Справочник по электрическим машинам. В 2-х т. Т. 2 под ред. И. П. Копылова Б. К. Клокова. – М.: Энергоатомиздат 1989. 688 с. ил.
Москоленко В. В. Электродвигатели специального назначения. – М.: Энергоиздат 1981. 104 с. ил.
Усынин Ю. С. Системы управления электроприводов Уч. пособие. – Челябинск: Изд. ЮУрГУ 2001. – 358с. ил.
Электронный каталог продукции департамента A&D фирмы SIEMENS (CD-ROM). – Москва представительство фирмы SIEMENS 2000.
Кириллов В.Е. Некоторые рекомендации студентам электротехнических специальностей для подготовки экономического раздела дипломного проекта (расчета экономического эффекта) Уч. пособие. – Златоуст: Изд. ЮУрГУ 2006.
2 Блочный чертеж схемы 22.cdw

Станок бесцентрово-токарный
Схема электрическая структурная
Содержание.doc
Структура и технология производственного процесса
Расчет режима резания и реализация модели в пакете VisSim
Гражданская оборона
Список используемой литературы
тит-пояс-зап_1.doc
ВЫСШЕГО ПРОФЕССИОНАЛЬНОГО ОБРАЗОВАНИЯ
ЮЖНО-УРАЛЬСКИЙ ГОСУДАРСТВЕННЫЙ УНИВЕРСИТЕТ
Факультет машиностроительный
ПРОЕКТ ПРОВЕРЕНДОПУСТИТЬ К ЗАЩИТЕ
Рецензент Заведующий кафедрой
ПОЯСНИТЕЛЬНАЯ ЗАПИСКА К ДИПЛОМНОМУ ПРОЕКТУ
ЮУрГУ1804.06.696.00.00 ПЗ
Консультанты:Руководитель проекта:
4 Модель VISSIM.cdw

связью по скорости в относительных единицах.
Схема электрическая структурная.
Рекомендуемые чертежи
- 29.07.2014
- 09.06.2018