Механизация устройства основания автодорог с конструктивной разработкой автогрейдера с гидростатической трансмиссией




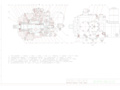
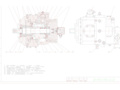
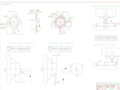

- Добавлен: 24.01.2023
- Размер: 5 MB
- Закачек: 0
Описание
Состав проекта
![]() |
![]() |
![]() |
![]() ![]() ![]() |
![]() |
![]() ![]() ![]() |
![]() |
![]() ![]() ![]() |
![]() |
![]() ![]() ![]() |
![]() |
![]() ![]() ![]() |
![]() |
![]() ![]() ![]() |
![]() ![]() ![]() |
![]() ![]() ![]() |
![]() ![]() ![]() |
![]() ![]() ![]() |
![]() ![]() ![]() |
![]() |
![]() ![]() ![]() ![]() |
![]() ![]() ![]() ![]() |
![]() ![]() ![]() ![]() |
![]() ![]() ![]() ![]() |
![]() ![]() ![]() ![]() |
![]() ![]() ![]() ![]() |
![]() ![]() ![]() ![]() |
![]() ![]() ![]() ![]() |
![]() ![]() ![]() ![]() |
![]() ![]() ![]() ![]() |
![]() ![]() ![]() ![]() |
![]() ![]() ![]() ![]() |
![]() ![]() ![]() ![]() |
![]() ![]() ![]() ![]() |
Дополнительная информация
ЭКОНОМИКА.doc
Экономический анализ даёт возможность выбрать наиболее эффективный вариант новых изделий способствует внесению в создаваемые конструкции таких улучшений которые позволяют получить лучшие результаты при наименьших материальных трудовых и финансовых затратах. При этом окончательное решение о целесообразности запуска гидростатической трансмиссии автогрейдера в производство может быть принято только после расчёта её стоимости. В условиях нестабильной экономической ситуации предприятие изготовитель заинтересовано прежде всего в обеспечении по возможности большей загрузки имеющихся в распоряжении производственных мощностей на длительный срок. Иначе говоря для получения прибыли предприятие должно выпускать изделие в достаточно большом объёме.
Таким образом количество изделий которые могут быть куплены у предприятия определяется их ценой и заинтересованностью потенциальных покупателей в их приобретении.
В связи с этим в экономической части дипломного проекта рассчитывается полная себестоимость гидростатической трансмиссии автогрейдера.
2 Расчёт и анализ себестоимости изделия
Себестоимость продукции – это текущие затраты на производство и реализацию продукции выраженное в денежной форме.
Себестоимость – это инструмент оценки технико-экономического управления производства и труда. Она выступает исходной базой для формирования цены.
Их расчёт по отдельным статьям в денежном выражении на единицу продукции принято называть калькуляцией. Себестоимость изделия по этому методу определяется по следующим статьям затрат:
покупные комплектующие изделия полуфабрикаты;
возвратные отходы (вычитаются);
топливо и энергия на технологические цели;
основная заработная плата производственных рабочих;
отчисления на социальное страхование;
расходы на подготовку и освоение производства новых видов изделий;
износ инструмента и приспособлений;
прочие производственные и внепроизводственные расходы.
В статью “Сырьё и материалы” включаются затраты на сырьё и материалы которые входят в состав продукции или являются необходимыми компонентами для её изготовления на покупные изделия общепромышленного назначения (например различные подшипники) на вспомогательные материалы используемые для технологических целей. Затраты по этой статье включаются в себестоимость отдельных изделий прямым путём. Затраты на вспомогательные материалы для технологических целей относят на себестоимость изделия прямым путём.
Стоимость сырья и материалов определяется на основании норм расхода каждого вида материалов и прейскурантных цен за вычетом стоимости отходов которые также определяются по прейскурантам. Под возвратными отходами понимаются остатки сырья материалов или полуфабрикатов утратившие полностью или частично потребительские свойства исходного материала и неиспользуемые по прямому назначению. Размер возвратных отходов зависит от степени прогрессивности применяемого технологического процесса.
Расходы по статье “Покупные изделия полуфабрикаты и услуги кооперативных предприятий” определяются в соответствии с ведомостью покупных изделий требующих дополнительных затрат труда на их сборку и обработку при укомплектовании выпускаемой продукции и действующих оптовых цен на них.
В статью “Топливо и энергия на технологические цели” включаются затраты на все виды топлива и энергии расходуемые в производстве.
В статье “Основная заработная плата производственных рабочих” планируется и учитывается основная заработная плата как производственных рабочих так и инженерно-технических работников непосредственно связанных с изготовлением продукции. В состав этой статьи включаются оплата повременщиков по тарифным ставкам доплаты до часового фонда: по прогрессивно- премиальным системам за работу в ночное время не освобожденным бригадирам за обучение учеников и т. д. Доплаты до часового фонда включаются в себестоимость косвенным путём – в процентах к прямой заработной плате. Этот процент определяется как отношение суммы всех доплат до часового фонда к фонду прямой заработной платы по плановым или фактическим данным предприятия.
В статье “Дополнительная заработная плата производственных рабочих” планируются и учитываются следующие выплаты:
оплата очередных и дополнительных отпусков;
компенсация за неиспользованный отпуск;
оплата льготных часов подросткам;
оплата перерывов в работе кормящих матерей;
оплата времени связанного с выполнением общественных и государственных обязанностей;
выплата вознаграждений за выслугу лет.
Дополнительная заработная плата определяется в процентах от основной заработной платы.
Статья “Отчисления на социальное страхование” включает отчисления по установленным нормам от суммы основной и дополнительной заработной платы производственных рабочих.
Статья “Отчисления на подготовку и освоение производства” включает расходы на комплексное опробование вновь вводимых в действие предприятий цехов затраты на освоение производства новых изделий.
В статье “Расходы на содержание и эксплуатацию оборудования” отражаются затраты на содержание амортизацию и текущий ремонт оборудования рабочих мест а также затраты на амортизацию износ и восстановление специальных инструментов и приспособлений. Расходы на содержание и эксплуатацию оборудования распределяются с помощью сметных ставок рассчитываемых методом коэффициенто-машино-часов’ работы оборудования. Исходными показателями являются расходы на час работы оборудования и её продолжительность при изготовлении единицы соответствующего вида продукции.
Статья “Цеховые расходы” в большинстве случаев относится на себестоимость отдельных устройств пропорционально основной заработной плате производственных рабочих. Она включает в себя:
заработную плату цехового персонала;
амортизацию зданий и сооружений цеха;
затраты на содержание и текущий ремонт зданий сооружений и инвентаря общецехового назначения.
Затраты по статье “Общезаводские расходы” связаны с организацией производства в целом и его управлением. В неё входят:
заработная плата персонала заводоуправления;
расходы на командировки;
расходы на подготовку кадров;
расходы на охрану предприятия и др.
По статье “Внепроизводственные расходы” учитываются только затраты предприятия по реализации продукции. Они устанавливаются в процентах от производственной себестоимости.
Произведём расчёт всех статей затрат.
НАИМЕНОВАНИЕ ИЗДЕЛИЯ
Датчик положения люльки насоса
Датчик положения люльки мотора
Соединительные трубопроводы
Соединительные кабели
Ресурсозатраты на приобретение материалов в исходном варианте завода изготовителя остались на прежнем уровне.
В проектном варианте в результате антикризисных мероприятий
Транспортно – заготовительные расходы.
где tp-процент транспортно – заготовительных расходов руб;
M0 - стоимость основных материалов руб;
Mn-стоимость покупных полуфабрикатов руб;
Индексом И.-обозначен исходный вариант (прототип)
Индексом ПР.-обозначен проектный вариант
Основная заработная плата производственных рабочих.
З 1590170 руб (в исходном варианте заработная плата осталась на уровне 2009года завод заработную плату не повышал)
Дополнительная заработная плата Зд руб;
где d-процент дополнительной заработной платы;
Отчисление на социальное страхование Зс руб;
где а процент отчисления;
Расходы на освоение и подготовку производства Зосв руб;
где b-процент от основной заработной платы;
Расходы на содержание и эксплуатацию оборудования Po руб;
где m-процент затрат к основной заработной плате;
Цеховые расходы Цp руб;
где B-процент затрат к основной заработной плате;
Общезаводские расходы Оp руб;
Производственная себестоимость Sn руб;
Sn=Ззатр+Tp+Зо+Зд+Зс+Зосв+Po+ЦP+Ор
S99327+695289+159017+238526+589953+95410+3482472+ 2226238=20319921руб.;
S85221+596574+1613068+241960+598445+96784+3532619+ 1548545+2258295 = 19008363 руб;
Коммерческие расходы Рк руб;
где F - процент к производственной себестоимости;
Полная себестоимость Sполн руб;
S 20319921+142641=20519962 руб;
S 19008363+133058 = 19141421 руб;
Предполагаем что рентабельность изделия составляет 25%. Тогда исходное уравнение оптовой цены без НДС будет являться
тогда оптовая цена будет складываться
Р20319921+5094330=25471651 руб.
Р19008363+4752090 = 23760453 руб.
3 Расчёт оптовой цены гиростатической трансмиссии автогрейдера
ЧИСЛЕННОЕ ЗНАЧЕНИЕ руб.
Стоимость основных материалов.
Стоимость покупных изделий.
Транспортно-заготовительные расходы.
Дополнительная зарплата.
Отчисления на социальное страхование.
Расходы на содержание и эксплуатацию оборудования.
Расходы на освоение и подготовку производства
Общезаводские расходы.
Производственная себестоимость.
Коммерческие расходы
Полная себестоимость.
Цены указаны по состоянию на 1 квартал 2010г.
4 Технико-экономическое обоснование
Наименование проекта
Создание автогрейдера с гидростатической трансмиссией
Народнохозяйственное значение проекта ожидаемые конечные результаты
Создание отечественного изделия удовлетворяющего потребность на Российском рынке.
Обоснование целесообразности проведения работ по проекту
Создание высоконадёжной системы удобной в эксплуатации основанной на современных разработках. Невысокая цена.
Краткая характеристика положения в данной области в стране и в мире
Основные аналоги представлены российскими производителями. Отечественные изделия близкие по типу но по назначению отличны.
Место и срок освоения проекта
Механизация .doc
1.Общие требования к механизированным работам при устройстве
основания автомобильных дорог
К механизированным работам в дорожном строительстве относятся работы выполняемые как с частичной так и с комплексной механизацией. При этом к комплексно-механизированным работам относят работы выполняемые комплектом машин механизмов и установок обеспечивающих механизацию всех тяжелых и трудоемких процессов и подобранных таким образом чтобы в результате их совместной работы достигалась наивысшая для современного уровня техники производительность труда.
В основу технологических правил дорожно-строительных работ
положена комплексная механизация с увязкой работы всех машин
механизмов и в соответствии с заданной производительностью потока
исходя из наилучшего использования каждой машины. Для этого
необходимо наиболее правильно осуществлять комплектование машин в
отряды чтобы обеспечить установленную скорость потока. При поточном
строительстве дорог особое значение имеют строгое выполнение
утвержденных графиков и учет выполненных работ.
Технологическая последовательность выполнения работ в потоке
) устройство телефонной связи; строительство временных жилищно-
бытовых и производственных помещений и выполнение других
подготовительных работ;
) выполнение сосредоточенных работ;
) строительство дорожных эксплуатационных зданий;
) строительство труб малых и средних мостов;
) устройство земляного полотна и водоотвода;
) устройство основания;
) устройство покрытия.
Прочность и устойчивость основания в значительной степени
предопределяющие дальнейшую работу покрытия зависят от правильной
оценки строительных свойств грунтов и водно-теплового режима земляного
полотна правильной проектировки последнего и качественного возведения
с соблюдением надлежащего уплотнения и обеспечения водоотвода как
поверхностных так и грунтовых вод с учетом перераспределения влаги в
результате воздействия градиентов температур.
2.Технология устройства оснований и используемые машины
При устройстве гравийных щебеночных и грунтовых оснований дорожных покрытий используют автогрейдеры или бульдозеры и наконец при устройстве дорожных покрытий обработанных и необработанных вяжущими асфальтобетонных и цементно-бетонных применяют автогрейдеры бульдозеры автосамосвалы асфальтоукладчики гудронаторы бетоноукладчики. Таким образом устройство основанией автодорог осуществляется при совместной комбинированной работе различных землеройных и дорожных машин. При этом для каждого участка и вида работ важно правильно oпределить состав машин специализированного звена а также ведущую машину предназначенную для выполнения основных операций и влияющую на производительность всего звена.
В качестве материала для основания обычно применяют щебень и гравий которые распределяют с помощью автогрейдеров по дну корыта. Гравий — это обломочная горная порода состоящая из окатанных зерен размером от 2 до 40 мм с примесью песка пыли и глины. Используют гравий для устройства гравийных покрытий или оснований под усовершенствованное покрытие. Щебень — это раздробленные горные породы из неокатанных остроугольных зерен от 5 до 75 мм. Материал для основания завозят любыми транспортными средствами (самосвалами землевозами скреперами) и разгружают на одной из сторон проезжей части или вдоль оси корыта таким образом чтобы не мешать проезду этих машин. Материал разравнивают послойно круговыми проходами автогрейдера. Отвал устанавливают под углом захвата 45° углом резания до 50° и углом наклона равным заданному поперечному профилю. При этом отвал приподнимают на высоту разравни-ваемого слоя. После этого поверхность профилируют для чего отвал устанавливают под углом захвата 60—90° а угол резания — 60°. Профилирование ведут круговыми проходами начиная от бровки . Длина захваток для укладки материала оснований — не менее 300 м. Для обеспе- чения разворотов автогрейдеров в конце участка организуют съезды с на-сыпи.
.В общий состав работ входят:
- разбивка трассы дороги;
- планировка поверхности земляного полотна;
- устройство корыта и уплотнение его;
- устройство подстилающего слоя из песка;
- устройство щебеночного основания и верхнего слоя (покрытия).
Ниже рассмотрены особенности выполнения указанных работ.
. Работы по строительству дороги начинаются с грубой планировки
поверхности полотна дороги создания поперечных и продольных уклонов
устройства канавы для отвода поверхностных вод автогрейдером типа Д-
. Корыто для дороги устраивается автогрейдером : срезается
грунт на глубину по проекту (условно - на глубину 30 см) и ширину больше
чем ширина покрытия на 05 м. Дно корыта уплотняется прицепным
вибрационным катком.
. Песок для подстилающего слоя подвозится к месту работ на автосамосвалом
автомобилях-самосвалах КАМАЗ- 6520 и распределяется автогрейдером
ДЗ-122 . Поверхность подстилающего слоя планируется так чтобы при
прикладывании 3- метровой рейки величина просвета не превышала ± 10 мм.
Уплотнение производится прицепным катком или моторным вибрационным
катком ДУ-96. Движение транспорта по готовому подстилающему
. Покрытие из щебня или гравия (нижнего или верхнего слоя)
обработанных битумом способом перемешивания автогрейдером на дороге
производится следующим образом: предварительно разравнивается
гравийный материал перед разливом жидкого битума материал сложенный
в виде валика разравнивается на ширину несколько меньшую чем ширина
проезжей части (на 05 м с каждой стороны). Розлив жидкого битума
осуществляется в несколько приемов. При первом розливе назначается
небольшая норма расхода битума: до 25 л на 1 м2. Перемешивание
осуществлять собиранием минерального материала в валик и последующим
его разравниванием. Готовая смесь из валика после проверки ее по качеству
и объему распределяется по проезжей части дороги с соблюдением заданной
ширины толщины и с приданием соответствующего профиля после чего
производится окончательная укатка катком ДУ-96. Толщина
основания (нижнего слоя) или покрытия принимается 100 мм в плотном теле.
Свойства гравийного материала входящего в состав смесей должны
удовлетворять требованиям ГОСТ 25607-94 «Смеси щебеночно-гравийно-
песчаные для покрытия и оснований автомобильных дорог и аэродромов»;
ГОСТ 8267-93 «Щебень и гравий из плотных горных пород для
строительных работ».
В качестве органических вяжущих применяют жидкие битумы марок МГ
130 и СТ 70130; дорожные битумные эмульсии марок ЭБК-2; ЭБК-3
ГОСТ22245-90 «Битумы нефтяные дорожные вязкие .Технические
Смешение на дороге автогрейдером выполняют для устройства покрытий на
автомобильных дорогах IV категории а также верхних слоев оснований на
дорогах III - IV категорий. Слои дорожной одежды построенные способом
смешения на дороге имеют толщину 8 - 10 см. При большей толщине
смешение делают в два приема.
Состав бригады для выполнения работ :
бульдозерист 4 разр. - 1 чел.
машинист автогрейдера 4 разр. - 1 чел.
шоферы 4 разр. - 7 чел.
машинист катка 4 разр. - 1 чел.
Потребность в машинах
Моторный виброкаток
Потребность в материалах на 1000 м автодороги.
3.Операционный контроль качества устройства автодороги
Наименование операций подлежащих контролю
Контроль качества выполняемых операций по устройству дорог с покрытием из щебня дорожных плит асфальта
Устройство земляного полотна (корыта) песчаного подстилающего слоя
степень уплотнения грунта и песчаного подстилающего
слоя. ровность основания соответствие отметок профилей проектным
Устройство основания из щебня или гравия
равномерность распределения материала битумоминеральной смеси соблюдение заданной толщины слоя с учетом коэффициента уплотнения ровность поверхности основания (при прикладывании 3-метровой рейки просвет не должен превышать 5 м) достаточность уплотнения основания (при проходе тяжелого катка на поверхности не должно оставаться следа от вальцов)
Допускаемые отклонения от проектных размеров
Допускаемая величина отклонения
Отклонение в сумме измеренных горизонтальных углов при « n » измеренных углов
Относительная разность между длиной трассы по проектным материалам и при выносе трассы на местность (или по двум промерам):
в равнинной местности
Основания и покрытия из грунтов щебня и гравия
Ширина основания под покрытие капитального типа
Высотные отметки по оси
Допускаемый просвет под 3-метровой рейкой
СХЕМА РАБОТ ПО УСТРОЙСТВУ ЩЕБЕНОЧНОГО ОСНОВАНИЯ ДОРОГИ
БЖД.doc
Наиболее часто несчастные случаи при устройстве основания автодорог происходят из-за неправильно организованных рабочих мест недостаточности обучения и психологического состояния человека.
Поэтому механизация работ при устройстве основания автодорог(конструктивная разработка автогрейдера с гидростатической трансмиссией) позволит значительно облегчить труд уменьшить число несчастных случаев как среди дорожных рабочих в зоне устройства основания дорог так и среди самих водителей автогрейдера.
Разработка автогрейдера с гидростатической трансмиссией осуществлялась в конструкторском бюро.
1. Выбор объекта анализа.
В качестве объекта анализа при решении задач охраны труда выбрано конструкторское бюро где происходит инженерная разработка конструкции автогрейдера с гидростатической трансмиссией машинная обработка результатов. Объектом исследования с точки зрения безопасности является техническое обеспечение автоматизированного рабочего места разработчика представляющее собой персональный компьютер типа IBM PC с выводом информации через печатающее устройство - цветной струйный плоттер модели HP.
2. Анализ потенциальной опасности конструкторского бюро для работающих и для окружающей среды.
2.1 Анализ потенциально опасных и вредных производственных факторов.
В соответствии с ГОСТ 12.0.002-80 опасным производственным фактором воздействие которого на человека в определенных условиях приводит к травме или другому внезапному резкому ухудшению здоровья а вредным – фактор воздействие которого приводит к заболеванию или снижению
работоспособности человека. Согласно ГОСТ 12.0.003-74 опасные и вредные по природе действия подразделяются на следующие группы: физические химические биологические и психологические.
Для конструкторского бюро опасные и вредные факторы представлены на рис. 5.1
Рис. 5.1 Физические и психологические опасные и вредные производственные факторы.
Основные опасные и вредные производственные факторы
места их возникновения нормы ПДУ и ПДК.
Возможные последствия
Повышенное значение напряжения электрической цени замыкание которой может произойти –через тело человека при режиме глухо заземленной нейтрали.
Конструкторское бюро
При длительном воздействии (более1сек.)
Распределительный щит.
Повышенная напряженность электрического поля и электромагнитного излучения.
Электроустановки частоты выше 50000 Гц. Конструкторское бюро
ПДУ при частоте 60 КГц – 3 МГц
Профессиональные заболевания электротравмы пожары.
Повышенный уровень статического электричества.
Трубопроводы. Эл. установки.
Повышенная или пониженная температура воздуха влажность подвижность воздуха рабочей зоны.
Скорость воздуха менее 01 мс
Перегрев или переохлаждение организма.
Недостаточная освещенность рабочей зоны.
Конструкторское бюро.
Утомляемость дискомфорт опасность травматизма ухудшение зрения
Повышенный уровень шума.
Уровень по полосам частот не менее 315
Нервно-психическая перегрузка
2.2. Анализ производственных воздействий вычислительного центра на окружающую среду.
От работающего оборудования возникает шум и тепловыделения в небольших количествах.
В результате работы возникают бумажные отходы в виде испорченных листов из-за возможности остановки программы плохого качества красящей ленты неисправности принтера неисправности плоттера.
Электромагнитное излучение и ионизация воздуха при работе монитора персонального компьютера.
Возможно загрязнение окружающей среды соединениями ртути в случае неправильной утилизации отслуживших свой срок люминесцентных ламп.
2.3. Анализ возможности возникновения чрезвычайных
При работе электрического оборудования возможны короткие замыкания. Из-за того что часть работы проводится с бумажной документацией есть вероятность возникновения пожара.
Существует возможность воздействия молнии на здание в результате чего может возникнуть искрение в воздушных промежутках между металлическими конструкциями здания.
2.4. Категория помещения по пожароопасности.
Категория помещения по пожарной опасности относится к категории производства «В» поскольку в помещении находятся твердые горючие вещества (дерево бумага пластмассы и т.п.) которые могут гореть в сочетании с кислородом воздуха.
2.5. Степень огнестойкости здания.
Степень огнестойкости III-б исходя из категории помещения по пожарной опасности «В» – количество этажей здания в котором размещено конструкторское бюро - 5 фактическая площадь этажа между противопожарными стенами здания – 3600 м2.
2.6. Классификация помещения в зависимости от окружающей среды.
Помещение конструкторского бюро относится к классу сухих т.к. среда помещения нормальная помещение сухое влажность не более 60 % нет активных выделений пыли и химических вредных веществ.
2.7. Классификация помещения по степени опасности поражения электрическим током.
Поскольку в помещении есть возможность одновременного прикосновения человека к заземленным металлическим частям с одной стороны и к металлическим корпусам внутри которых есть опасное для жизни напряжение с другой стороны то КБ относится к помещению с повышенной опасностью поражения электрическим током.
2.8. Классификация помещения по заданной зрительной работе.
Поскольку инженерами-программистами производится различение
объектов зрительной работы при фиксированном направлении линий зрения на рабочую поверхность то помещений относится к I группе по задачам зрительной работы.
3. Организация рабочего места операторов.
На каждого работающего должна приходиться площадь не менее 4.5 м2 и объем не менее 15 м3. Интерьер отделывается голубым или светло-зеленым цветом как благоприятно действующим на зрение снижающим нервное возбуждение и усталость. Надписи предупреждающие об опасности рекомендуется выделять красным цветом.
Основная поза инженеров-программистов – сидя поэтому:
Высота рабочей поверхности – 700 мм.
Высота пространства для ног – 600 мм.
Высота рабочего сидения – 420 мм.
Высота средств отображения информации – 110 мм.
Зона выполнения ручных операций используемых часто – 400 мм.
4. Требования к воздуху рабочей зоны и мероприятия по их обеспечению
Предполагаются следующие оптимальные нормы температуры влажности и скорости движения воздуха в рабочем помещении.
Относительная влажность %
Скорость движения воздуха (не более) мс
Работа выполняется сидя без физического напряжения и подъема тяжести и требуемые затраты энергии до 133 Ккал поэтому категория
работ – легкая – 1-а.
Помещение конструкторского бюро оборудовано техникой которая нагреваясь во время работы повышает температуру воздуха. В связи с этим для поддержания необходимой температуры в теплое время года в КБ установлены кондиционеры типа БК –2300 в количестве 2 штук которые подключаются к электросети и устанавливаются в наружных ограждениях для отведения тепла на улицу.
В холодное время года для поддержания оптимальной температуры в вычислительном центре помещение снабжается водяной отопительной системой. Система кондиционеров поддерживает относительную влажность на уровне 40 – 60 %. Поддерживание скорости движения воздуха 01 мс обеспечивается конструктивными особенностями: двери и окна располагаются таким образом чтобы дверной проем не располагался на противоположной стороне от окон (чтобы не было сквозняков).
5. Размещение средств отображения информации.
Общие требования к размещению средств отображения информации по ГОСТ 12.2.032-78.
Используемые средства отображения информации (монитор) требующие точного и быстрого считывания показаний расположены в вертикальной плоскости под углом 30 градусов от нормальной линии взгляда и в горизонтальной плоскости под углом 30 градусов от сагиттальной плоскости. под углом 60 градусов от сагиттальной плоскости.
Допустимые уровни звукового давления уровни звука и эквивалентные уровни звука на рабочих местах предполагаемые проектом представлены в таблице 2.
Уровни звукового давления дБ в октавных полосах со среднегеометрическими частотамиГц
Уровни и эквивалентные уровни звука дБА
Стены КБ отделаны слоями звукопоглощающих покрытий изготовленных из асбоцементных перфорированных листов и гипсовых листов типа АГП АГШБ.
7. Меры безопасности при повышенном напряжении в электрической сети замыкание которой может произойти через человека.
В помещении где эксплуатируется дисплей персонального компьютера применяется трехфазный ток с частотой 50 Гц напряжением – 220 В. Режим нейтрали питающей трансформатор с глухозаземленной нейтралью.
В КБ рассматриваемом в качестве объекта анализа устанавливается электрооборудование которое имеет открытые токоведущие части. Для обеспечения безопасности поражения током предусмотрено расположение токоведущих частей внутри корпусов с запирающимися дверцами и блокировкой. При соблюдении этих рекомендаций случайное прикосновение человека к токоведущим частям становится практически невозможным но при работе электрооборудования не исключается возможность пробоя напряжения на корпусе. В связи с этим предусматривается проведение мероприятий по обеспечения безопасности:
Устройство защитного отключения поврежденного оборудования от сети (рис.5.2):
Рис.5.2 Устройство защитного отключения поврежденного оборудования от сети.
В качестве исполнительного органа применены автоматические выключатели.
8. Обеспечение требуемой освещенности.
Для обеспечения требуемой освещенности предусмотрена общая система искусственного освещения при которой светильники располагаются в верхней зоне помещения равномерно.
Работа инженеров-программистов связана с прочтением машинного текста и текста светящегося на экране. Наименьший размер объекта различения 1-5 мм. поэтому предусматриваются следующие нормированные значения коэффициента естественной освещенности.
Характеристика зрительной работы высокой точности.
Разряд зрительной работы IIIб.
Контраст различения с фоном – средний.
Освещенность при общем освещении – 200 лк.
При верхнем освещении коэффициент естественной освещенности –5 %.
Нормирование значений
коэффициента естественной освещенности на рабочих поверхностях при естственном и совместном освещении по СНиП 23-05-95указана в таблице 5.3
Разряд зрительной работы
Расчет освещенности конструкторского бюро.
Важным вопросом охраны труда является освещение рабочего места. Правильно устроенное освещение обеспечивает хорошую видимость и создает благоприятные условия труда. Искусственное освещение по способу расположения источников света делятся на: общее местное и комбинированное.
Светотехнические расчеты являются основополагающими при проектировании осветительных установок. Задачей расчета обычно является определение числа и мощности светильников необходимых для получения заданной освещенности. Реже производятся проверочные расчеты т.е. определяется освещенность в определенных точках при заданных параметрах осветительной установки.
Порядок расчета освещения по методу коэффициента использования светового потока сводится к следующему:
Определяется нормированное значение освещенности для общего освещения (E0).
Выбирается тип источника и светильника согласно требованиям.
Определяется высота подвеса светильников.
Находится расстояние между рядами светильников (L) крайним радом и стеной (I).определяется необходимое количество светильников N.
Требуется рассчитать освещение помещения вычислительного центра по следующим данным:
Длина помещения А – 6 м.
Ширина помещения В = 4 м.
Потолок покрашен белой краской стены - светлой краской.
Нормативная освещенность для такого помещения составляет 600 лк для газоразрядных ламп и 300 лк для ламп накаливания по СниП 23.05-95.
Согласно СниП 23.05-95 в общественных административных и подобных им зданиях из числа газоразрядных ламп должны применяться только люминесцентные лампы.
Люминесцентные лампы неизбежно применяются при повышенных требованиях к цветопередаче независимо от разряда работ.
Согласно этому для освещения вычислительного центра берем люминесцентные лампы которые имеют ряд существенных преимуществ в числе которых:
Высокая световая отдача достигающая 75 лмВт.
Большой срок службы доходящий до 10.000 часов.
Возможность иметь источники света различного спектрального состава при лучшей для большинства типов цветопередачи чем лампы накаливания.
Относительно малая (хотя и создающая ослепленность) яркость что в ряде случаев является достоинством.
Так как условия среды нормальные то исходя из этого выбираем светильники с люминесцентными лампами (ЛБ-40) серии ЛСП02 условный номер группы 3.
Высоту свеса светильников принимаем равной hс = 0.25 м высота рабочей поверхности hр = 0.8 м (столы) тогда высота подвеса светильников:
h = H - hс – hр =3 –0.25 – 0.8 = 1.95 м.
Расстояние между рядами светильников по ширине здания:
где lc - светотехнические наивыгоднейшее расположение рядов светильников (находится по таблице).
Расстояние l между светильниками и стеной обычно принимается равным (025 03)L если рабочие места расположены у стен.
Число рядов светильников по ширине помещения:
М=(В – 2I)L+1=(4 – 2*0?68)273+1=1967
Определим коэффициент использования светового потока h характеризующий отношение потока падающего на расчетную поверхность к суммарному потоку всех ламп в функции индекса помещения и коэффициентов отражения стен рс и потолка рп рабочего оборудования ро по таблицам.
Индекс помещения вычисляется по формуле:
I=S[h*(A+B)] где S – площадь помещения.
l=4*6[195*(6+4)]=123
По таблице находим коэффициент использования светового потока
Для лампы ЛБ-40 (мощностью 40 Вт) световой поток составляет Фл = 2850 лм (данные берутся из таблицы «Технические данные люминесцентных ламп»).
Необходимое число светильников N=Ko*K*S*Zh*n*Ф
где К – коэффициент запаса характеризующий снижение освещенности при эксплуатации (данные из таблицы) для помещений с нормальной воздушной средой при газоразрядных лампах К = 15;
Z – коэффициент неравномерности характеризующий отношение средней освещенности к минимальнойZ=1.
n – число ламп в светильнике n = 2 шт.
Размещение светильников:
)Число светильников в ряду:
)Общая длина светильников в ряду Iобщ:
где lc – длина одного светильника по справочнику.
) Расстояние между светильниками в ряду ln (в том числе расстояние между столбом и крайним светильником в ряду)
ln=(A – lобщ)nn=(6-3711)4=057 м
где nn - число всех промежутков в ряду nn=4.
В результате проведенных расчетов получим что для требуемой освещенности вычислительного центра размерами 6*4*3 требуется 6 светильников ЛСП02 с лампами ЛБ-40 (в каждом светильнике 2 лампы) расположены в два ряда (рис. 5.3).
Рис.5.3 План расположения светильников.
9. Обеспечение санитарно-гигиенических условий труда.
Для обеспечения санитарно-гигиенический условий труда для персонала предусмотрен следующий состав и количество санитарно-бытовых устройств:
В гардеробной число отделений в шкафах или крючков для одежды принято равным списочной численности работающих.
установлен один умывальник.
предусмотрена одна уборная для мужчин и одна уборная для женщин.
10. Мероприятия по защите окружающий среды.
Работа инженеров-программистов связана с бумагой т.к. выходная информация имеет вид распечаток которые выдают печатающие устройства.
Предусмотрена утилизация бумажных отходов в целях экономии ресурсов: бумагу следует собирать в отдельные контейнеры и по мере накопления отправлять на переработку или сдавать в пункт приема макулатуры. Работа принтеровплоттера вентиляторов также вызывает шум. Предлагаются следующие нормы по шуму для окружающей среды:
11. Мероприятия и средства по обеспечению безопасности в чрезвычайных ситуациях.
11.1. Обеспечение пожаробезопасности.
Для пожарной безопасности предусматривается наличие системы пожарной защиты в виде автоматических извещателей (комбинированный) расположенных на потолке помещения. Во избежания пожаров предлагаются нормы первичных средств пожаротушения на действующих предприятиях и помещении категории В к которой относится вычислительный центр так как в помещении находятся твердые горючие вещества которые могут гореть в сочетании с кислородом:
Наличие двух огнетушителей углекислого ручного типа ОУ2-5-8.
Наличие пенных огнетушителей ОХП-10.
Система извещения о пожаре – автоматическая пожарная сигнализация с извещателем.
Расстояние от наиболее удаленного рабочего места до эвакуационного выхода 35 м (СниП 2.09.02-85).
11.2. Обеспечение молниезащиты.
КБ находится в г. Коврове - местности со среднегрозовой деятельностью большей или равной 20 часов поэтому предусмотрена система молниезащиты третьей категории. (СО 153-34.21.122-2003).Молниеприемник представляет из себя металлическую сетку с ячейками 12х12 мм которая покрывается антикоррозийным покрытием (оцинковкалужение).Молниеприемник располагается на крыше сооружения и связан с заземляющим контуром. Импульсное электросопротивление каждого заземления не должно превышать 20 Ом.
11.2.1. Расчет стержневого молниеотвода
Определим ожидаемое количество поражений молний в год зданий и сооружений прямоугольной формы:
N=[(А+6*h)*(В+6* h)-77*h]*n*10
А и В длина и ширина здания
А=84 м; В=72м; h=12м
n-среднегодовое число ударов молнии на 1 км земной поверхности;
N=[(84+6*12)*(72+6*12)-77*12)*4*10=0085 (ударов молний в год).
Определяем зону защиты молниеотвода из условия :
Так как N=0085то выбираем зону защиты Б (категория
Для создания зоны защиты применим одиночный стержневой молниеотвод. Для зоны Б действует следующее условие:
r=)(A2)= )(842)=886м
h =092*663=609м; r=15*663=995 м
Расчет заземляющего устройства:
Сопротивление вертикально забитой трубы
Количество электродов из соотношения :
Электроды установлены в ряд (=091; =094)
11.3. Инженерная разработка по обеспечению безопасности труда.
12. Инженерная разработка по защите окружающей среды.
Для защиты окружающий среды от шума исходящих от принтеров и кондиционеров предусмотрено однослойное ограждение конструкторского бюро. Проектируемое ограждение следует выполнить со слоем звукопоглощающими и вибропоглощающими покрытиями и имеющими отверстия. В общем случае звукоизоляция рассчитывается как:
Rогр=R + R1 + R2 - R0
где R - звукоизоляция ограждения 50 дБ;
R1 - добавочная звукоизоляция за счет нанесения слоев ЗПМ;
R2 – добавочная звукоизоляция за счет нанесения слоев ЗПМ;
R0 –добавочная звукоизоляция за счет отверстий и щелей.
R1 = 87*b*j+20*lg[(mn + mnc) mn ]
где b - коэффициент затухания b = 30 (1м);
j - толщина слоя ЗПМ j = 100 мм;
mnс - поверхностная плотность слоя mnс = 250 кгм2;
mn - поверхностная платность перегородки mn = 220 кгм2;
R1 =87*30*100+20*lg[(220+250)220]=261 дБ
где fp1 - резонансная частота ограждения со слоем ВПМ
fp -резонансная частота ограждения без слоя ВПМ
q1- коэффициент внутренних потерь
q - коэффициент внутренних потерь
mn1= mn +mnc= 220+250 = 470 кгм3.
R0 = 10*lg[1 – S0S + S0S + 1001*R]
где S0 - площадь отверстия S0 = 001 м2;
S – площадь всего ограждения S = 147 м2;
R0 = 10*lg[1 –001147+001147* 105] = 21 дБ.
Окончательно рассчитываем Rогр:
Rогр = 50+261+146 – 21 = 697 дБ.
Уровень шума в зале исходящий от работающих принтеров машин и кондиционеров достигает 80 дБА.
Следовательно величина снижения шума:
L R следовательно рассчитанная звукоизоляция эффективна.
В разделе «Безопасность и экологичность проектных решений» при инженерной разработке автогрейдера с гидростатической трансмиссией проанализированы потенциально опасные и вредные факторы при работе конструктора за персональным компьютером и возможности возникновения чрезвычайных ситуаций в конструкторском бюро проанализировано воздействие КБ на окружающую среду.
Произведена классификация помещения по взрывоопасности и пожароопасности по степени огнестойкости и степени опасности поражения током по задачам зрительной работы.
Разработан комплекс мероприятий по обеспечению безопасности труда и санитарно - гигиенических условий труда:
Определены требования к воздуху рабочей зоны.
Предложены меры борьбы с шумом.
Разработаны меры безопасности при повышенном напряжении в электросети.
Приведены нормы освещенности.
Также в разделе предложены мероприятия по защите окружающей среды и произведены инженерные расчеты по обеспечению безопасности труда : система грозозащиты; система звукоизоляции.
Технология.DOC
1 Описание назначения и конструкции детали
В технологической части этого дипломного проекта прорабатывается процесс производства на торцевой распределитель который является одной из основных деталей аксиально-поршневых гидронасосов.
Рис. 4.1 Аксиально-поршневой насос
вал; 2 корпус; 3 блок цилиндров; 4 поршень; 5 распределитель;
крышка; 7 диск; 8 уплотнительный узел; 910 кольца; 1112 подшипники; 13 коробка золотникова.
Назначение детали заключается в распределение потока рабочей жидкости в напорный и всасывающий трубопровод.
Один из торцов детали работает в паре трения «стальной распределитель – латунное накладное дно блока цилиндров» другой торец плотно прижат к задней крышке гидронасоса поэтому торцы сделаны плоскими и на них дан жесткий допуск неплоскостности. Исходя из условий наилучшей работы распределителя в паре трения с латунным блоком цилиндров данный распределитель делают из стали. Для разгрузки распределителя от сил прижима – отжима на торце распределителя делают разгрузочные канавки.
Так как распределитель работает в паре трения то на торцы распределителя задают высокий класс точности. Распределитель также имеет отверстие под подшипник которое одновременно является базовым отверстием.
2 Анализ технологичности конструкции
Технологичность конструкции - совокупность свойство конструкции изделия определяющих ее приспособленность к достижению оптимальных затрат при производстве эксплуатации ремонте для заданных показателей качества объема выпуска и условий выполнения работ.
Обобщенными показателями технологичности является трудоемкость изготовления изделия технологическая себестоимость и материалоемкость.
Рассматриваемая деталь изготавливается из стали Х12Ф1Ш что обусловлено наличием трения с ответными деталями
Получение внешнего контура детали не вызывает больших затруднений и может быть выполнено на токарных станках. Возможно также применение высокопроизводительных станков в частности на станках с ЧПУ (числовым программным управлением).
Трудность в изготовлении детали может представлять соблюдение допусков форм и расположений поверхностей обусловленных конструктивными особенностями.
Для контроля размеров в основном можно применить стандартный инструмент. Изготовление детали не требует большого количества нестандартного режущего инструмента и приспособлений.
Из сказанного можно сделать вывод что рассматриваемая деталь в целом технологична.
3 Расчет по программе выпуска
Определим действительный годовой фонд времени работы оборудования:
где Fн - номинальный фонд времени работы оборудования;
S - число смен в сутки;
Bн - коэффициент учитывающий потери времени на настройку и наладку оборудования во время рабочих смен;
Bр - коэффициент учитывающий потери времени связанные с проведением плановых ремонтов.
При 8-ми часовой смене за 256 календарных рабочих дней в году номинальный фонд времени работы оборудования будет равен:
Fн = 60 × 8 × 256 = 122880 мин.
Тогда действительный годовой фонд времени работы оборудования:
Такт выпуска детали определяется по следующей формуле:
где Fд - действительный годовой фонд времени;
N - годовая программа выпуска детали.
Принимаем что годовая программа выпуска 10000 деталей.
Определим коэффициент серийности при средне штучном времени Тшт.ср= 23 мин.:
По коэффициенту серийности определим тип производства:
Кс 10 20 следовательно тип производства среднесерийный.
Определяем оптимальное количество деталей в партии n:
где F - количество рабочих дней в году F = 256;
a - число дней на которые необходимо иметь запас деталей на складе принимаем 5 дней ;
Метод получения заготовок определяется назначением и конструкцией детали материалом техническими требованиями масштабностью и серийностью выпуска а также экономичностью изготовления заготовки и дальнейшей ее обработки.
С учетом геометрической формы линейных размеров материала детали в качестве заготовки применяют прокат. Для получения поковок и штамповок а также для непосредственного изготовления деталей гидропривода механическим путем применяют заготовки из проката.
Годовой экономический эффект рассчитывается по формуле:
Эзаг = (S заг1 - Sзаг2)N
где Sзаг1 и Sзаг2 - стоимость сопоставляемых заготовок руб.;
N - годовая программа выпуска шт.
Найдем стоимость заготовки из стандартного проката по следующей формуле:
где Q - масса заготовки кг;
Цм - цена 1 тонны материала заготовки руб.;
Цотх - цена 1 тонны отходов руб.;
q - масса готовой детали кг.
При этом получим коэффициент использования материала равный
Стоимость заготовки полученной поковкой вычисляется следующим образом:
где Kт Kс Kв Kм KП - коэффициенты зависящие от класса точности группы сложности массы марки материала и объема производства заготовок;
Ci - базовая стоимость 1 тонны заготовки руб.
По рассчитанным стоимостям заготовок можно определить годовой экономический эффект:
Эзаг = (31169 – 5127)10000 = 99950 руб.
Исходя из этого можно сделать вывод о наиболее экономичном виде заготовки для детали торцевой распределитель.
При конкретных производственных условиях для данной детали наиболее экономически выгодным является прокат.
5 Расчет режимов резания
5.1 Операция 020 Токарная
Выбираем станок марки 16К20 (токарно-винторезный). Выбираем резец проходной с пластиной из твердого сплава марки Т15К6. По таблице 11 определяем подачу суппорта на один оборот шпинделя.
y = 045 табл.17 стр.269 [ 3 ] ;
T – среднее значение стойкости инструмента T = 30 – 60 мин ;
t - глубина резания t = 10 мм ;
S – подача S = 1 мм об;
Kn - коэффициент скорости резания Kn = Kmn × Knn × Kun
где Kmn - коэффициент учитывающий качество обрабатываемого материала:
Knn - коэффициент отражающий состояние поверхности заготовки:
Kun - коэффициент учитывающий качество материала инструмента:
Отсюда скорость резания:
Число оборотов шпинделя:
где d - диаметр обрабатываемой поверхности; d = 94 мм;
По паспорту станка принимаем 240 обмин;
Уточнение скорости резания:
V = = 3.14 94 240 1000 = 78 ммин
Основное машинное время обработки:
где Lрх = Lрез + y- длина рабочего хода суппорта
Lрез - длина обрабатываемой поверхности;
y - расстояние подхода резца;
n - частота вращения вала.
To = (47 + 2) 1 240 = 0.2 мин.
Подача суппорта в минуту
S’ = S n = 1 240 =240 мммин.
Рис.4.2токарнаяоперация020
5.2 Операция 050 сверлильно-фрезерная
Фрезеровать паз в размеры. Определяем параметры фрезерования.
Глубина фрезерования t = 4.3 мм.
Ширина фрезерования В=6.5 мм.
Выбираем фрезу концевую с цилиндрическим хвостовиком (по ГОСТ 18372-73) и материал режущей части ВК 8.
длинна рабочей части
- число зубьев Z = 4.
Определение подачи на зуб.
Принимаем Sz = 0.05 ммзуб .
T m × t x × S z y × B u× Z p
где Sz – подача на зуб мм;
Z – число зубьев фрезы.
По табл. 39 (стр. 286) определим численные значения для формулы.
014 × 45 02 × 005 03 × 8 02× 4 01
По паспорту станка принимаем n = 100 обмин.
Продольное перемещение стола станка:
Подача фрезы на оборот
S = Sz Z = 0.05 4 = 0.2 ммоб.
To = 15 02 100 = 0.75 мин.
Sм = Sz Z n = 0.05 4 100 =20 мммин.
Рис. 4.3 Фрезерная операция 050
Патентные исследования с рамкой.doc
“Гидростатической трансмиссия автогрейдера”
Задача патентных исследований – получение сведений достаточных для исследований технологического уровня тенденций развития объектов техники.
Цель поиска информации: получение исходных данных для обеспечения высокого технического уровня.
Задание на проведение патентного поиска
Название предмета поиска подлежащего патентной разработке:
Гиростатическая трансмиссия автогрейдераустройство управления гиростатической трансмиссией автогрейдера».
Страны: РФ Великобритания США Германия Япония Франция.
Глубина поиска: с 2000 по 2010 гг.
Подпись руководителя проекта
Подпись консультанта
1. Результаты проведения патентных исследований
которым проводился поиск
(изобретения модели).
Библиографические данные достаточные для их нахождения
Гидросистема мобильной машины.
Электрогидравлическая система управления.
Пат. 2162551 БИ №16 2001г.
Пат. 2115911 БИ № 8 2003 г.
Аналогов не обнаружено
Аналогов не обнаружено.
2. Результаты проведения информационных исследований.
Белецкий Б.Ф.Булгакова И.Г. Строительные машины и оборудование.-Ростовн Д.:2005-608с.
Добронравов С.С.Дронов В.Г. Строительные машины и основы автоматизации. -М.:Высшая школа2001-575с.
Полноприводной грейдер «Сюйчжоу»GR215A(Китай).Руководство по эксплуатации (на русском языке) 2009г.
Motor Grader 24 M Caterpiller (USA) 2009г.(Каталог :Технические характеристики и краткое описание )(на английском языке).
Сравнительный анализ
В информационных источниках [12] описан комплект аппаратуры автоматизации управления функций дорожно-строительных машин «АКА-Дормаш» В комплект аппаратуры входят устройства I-«Стабилоплан»для скреперовканавокопателейдреноукладчиков и т.п.;II-«Автоплан» для бульдозеров;III-«Профиль» для автогрейдеров и профиловщиков;IV-«Стабилострой» для различных укладочных машин. В комплекте аппаратуры используются следующие автономные системы управления:
-маятниковые датчики установленные на борту машины для контроля положения рабочего органа;
-копировальные системы обеспечивающие контроль положения по внешнему копиру-проволоке(тросу) колесу лыже радио и световому лучу и т.п.;
-комбинированные системы в которых контроль углового осуществляется автономными датчиками а определение по высоте –копиром.
Все системы используемые в системах различного назначения комплектуются
в основном двумя типами автономных маятниковых датчиковотличающимися типами установочного приспособления и разрешающей способностью преобразователя. а также копирным (щуповым) датчиком подъемным устройством двумя типами электрогидрозолотниковунифицированным пультом дистанционного управления и вспомогательным блоком. Вместо щупового (копирного) и маятникого датчика может использоваться следящая система с дискретным регулированием. В этом случае дополнительно применяется унифицированное согласующее устройство световой (лазерный ) луч вместо копира и фотоэлектрический приемник.
Системы автоматического управления разделяются на одно-двух- и трехканальные.При одноканальной системе управления рабочий орган машины удерживается в заданном положении в одной плоскости: продолной у скреперов и бульдозеров;поперечной –у автогредеров.Это системы «Стабилоплан-1» «Стабилоплан-10» «Копир-Стабилоплан» -для скреперов «Автоплан-1» «Копир-Автоплан-10» «Комбиплан-10ЛП» для бульдозеров «Профиль-1» «Профиль-10» для легких и средних автогрейдеров. При двухканальной системе управления стабилизация рабочего органа машины обеспечивается в поперечной и продольной плоскостях. К таким системам относятся «Комбиплан» для бульдозеров «Профиль-2» и «Профиль-20» для средних и тяжелых автогредеров. «Стабилослой-1» и «Стабилослой-10» для укладчиков покрытий. «Профиль-20»-двухканальная комбинированная копирная по жестким направляющим Унифицированная система «Профиль-30»- двухканальная комбинированная по лазерным направляющим.(автогрейдеры скреперы бульдозерыасфальтоукладчики профиловщики дреноукладчики.)
К недостаткам копировальных системам управления по жесткому копиру относятся повышенная трудоемкость при выполнении точных работ по установке копира (тросапроволоки) и постоянным поддержанием его в заданном положении. В лазерных системах управления обеспечивается управление курсом машины и толщиной укладываемого слоя дорожного покрытия. В лазерных системах управления обеспечивается управление курсом машины и толщиной укладываемого слоя дорожного покрытия.
В каталоге [3] приведена фотография и краткое описание рукоятки управления типа джойстик содержащая корпус и полый шток на одном конце которого закреплена рукоятка с установленной в ней клавишей управления микровыключателями а другой конец которого кинематически соединен с установленной в корпусе парой поворотных взаимно перпендикулярных поводков связанных с электромеханическими задающими устройствами.
К достоинствам данного механизма можно отнести:
– небольшая и простая кинематическая схема которая приводит к упрощению изготовления и сборки рукоятки;
– малые габариты и вес рукоятки;
– электронный блок управления встроен в рукоять что уменьшает погрешность в выходном сигнале вследствие уменьшения внешних электромагнитных наводок.
К недостаткам можно отнести:
– применение контактных конечных выключателей значительно уменьшает надежность устройства.
Известна «Электрогидравлическая система управления» (Пат. №2115911) содер-
жащая гидродвигатель два гидрораспределителя электромагнит регулировочный клапан гидронасос пульт управления.
Достоинством данной системы является:
– возможность плавного регулирования давления;
– постоянный расход жидкости при изменении внешней нагрузки.
Недостатком данной системы является:
– является возможность управления только одним приводом;
– усложнение схемы за счет введения дополнительного элемента (гидродвигателя) результатом которого стало снижение быстродействия системы управления.
Наибольшее распространение в гидросистемах тракторов дорожно-строительных подъемно-транспортных и других мобильных машин получило
техническое решение “Гидросистема мобильной машины” (Пат.2158861) содержащая регулируемый реверсивный насос приводимый в действие двигателем машины выходы которого через двухпозиционные четырехлинейные гидрораспределители соединены со входами гидроцилиндров являющихся исполнительными механизмами гидросистемы введены пропорциональный золотниковый клапан с электроуправлением датчик положения люльки насоса датчик давления в рабочей полости насоса устройство управления пропорциональным золотниковым клапаном причем входы пропорционального золотникового клапана и датчика давления соединены с магистралью которая подключается к поршневой полости каждого исполнительного механизма гидросистемы а выход пропорционального золотникового клапана – со сливом входы устройства управления соединены с выходами датчика давления и датчика положения люльки насоса а выход с управляющим входом пропорционального золотникового клапана.
Введение в гидросистему пропорционального золотникового клапана с электроуправлением датчика давления датчика положения люльки насоса и устройства управления обеспечивает гидравлическое замыкание регулируемого насоса и гидроцилиндров во всем диапазоне изменения скоростей и нагрузок. При этом за счет изменения положения люльки а следовательно подачи насоса и давления в поршневой полости гидроцилиндра создается режим обеспечивающий минимальный необходимый перепад давления на пропорциональном золотниковом клапане что обеспечивает минимизацию потерь в гидросистеме. Это позволяет значительно расширить область применения объемно-замкнутых приводов в мобильных машинах и снизить энергопотребление приводов.
Гидросистема включает в себя гидрообъемную передачу приводимую в действие двигателем машины содержащую регулируемый реверсивный насос с датчиком положения люльки насоса вспомогательный насос к его напорной магистрали подключен сливной клапан и через подпиточные клапаны подключены рабочие магистрали насоса .
К рабочим магистралям насоса подключены двухпозиционные гидрораспределители выходные магистрали гидрораспределителей подключены к штоковым и поршневым полостям гидроцилиндров являющихся исполнительными механизмами гидросистемы. К магистрали насоса которая соединяется с поршневыми полостями гидроцилиндров подключен вход пропорционального золотникового клапана с электроуправлением а его выход соединен со сливом.
К рабочей магистрали насоса подключен датчик давления выход которого соединен с входом устройства управления к другому входу подключен выход датчика положения люльки насоса . Выход устройства управления соединен с управляющим входом пропорционального золотникового клапана . Устройство управления содержит суммирующий усилитель и усилитель мощности. На суммирующем усилителе реализуется вычитание сигналов датчика положения люльки насоса и датчика давления . Разностный сигнал поступает на вход усилителя мощности а сего выхода на вход пропорционального золотникового клапана .Для работы гидроцилиндра включается гидрораспределитель при этом штоковая полость гидроцилиндра подключается к рабочей магистрали а поршневая – к магистрали насоса.
Для выдвижения штока гидроцилиндра рабочая жидкость по магистрали насоса подается в поршневую полость гидроцилиндра . Сливаемая из штоковой полости гидроцилиндра рабочая жидкость поступает в магистраль насоса . Однако сливаемый объем рабочей жидкости меньше на величину объема штока чем нагнетаемый объем. Восполнение недостающего объема производится вспомогательным насосом через подпиточный клапан .
Для втягивания штока гидроцилиндра рабочая жидкость по магистрали насоса нагнетается в штоковую полость гидроцилиндра а слив из поршневой полости осуществляется в магистраль насоса . Однако поступающий в гидроцилиндр объем жидкости меньше на величину объема штока чем вытесняемый из него объем. Сигнал с выхода датчика положения люльки насоса поступает на вход устройства управления в котором формируется электрический сигнал пропорциональный углу отклонения люльки насоса . Этот сигнал усиливается и поступает на вход пропорционального золотникового клапана состоящего из пропорционального электромагнита золотника и пружины. Электрический сигнал с выхода устройства управления поступающий на вход пропорционального золотникового клапана увеличивает ток в обмотке электромагнита - в результате якорь электромагнита перемещает золотник пропорционально току при этом сжимается пружина. Золотник в соответствии с управляющим сигналом открывает окно регулируя тем самым величину дроссельного отверстия которое соединяет магистраль со сливом. При уменьшении электрического сигнала с выхода устройства управления ток в обмотке электромагнита уменьшается усилие развиваемое якорем электромагнита также уменьшается и пружина перемещает золотник в сторону закрытия уменьшая тем самым расход сливаемой рабочей жидкости. Выходной сигнал с устройства управления формируется таким образом что при увеличении угла отклонения люльки насоса то есть при увеличении скорости движения штока гидроцилиндра золотниковый пропорциональный клапан открывается и сливает объем жидкости который необходимо скомпенсировать при заданной скорости движения штока гидроцилиндра .
При увеличении нагрузки на шток гидроцилиндра увеличивается давление в поршневой полости гидроцилиндра которое регистрируется датчиком давления его сигнал поступает на вход суммирующего усилителя и уменьшает сигнал с датчика положения люльки насоса и тем самым уменьшает открытие пропорционального золотникового клапана поддерживая постоянный расход сливаемой жидкости при заданной скорости движения штока гидроцилиндра .
Таким образом за счет управления пропорциональным золотниковым клапаном в штоковой полости гидроцилиндра всегда поддерживается давление подпитки а сливается такой излишек жидкости какой необходим при заданной скорости движения штока гидроцилиндра .
Из всех выявленных технических решений лучшим является:
“Электрогидравлическая система управления” Пат. №2162551 которая состоит (рис.1.) из пульта управления (ПУ) включающего в себя элемент управления 1 кинематически связанный с датчиком положения (ДП) 2 преобразующими перемещение в электрический сигнал и блока З кнопочных переключателей (КП) распределителя 4 состоящего из распределительных секций с пропорциональным управлением (СПУ) и распределительных секций с дискретным управлением (СДУ) причем каждая распределительная секция связана с одним гидродвигателем насоса переменной производительности 5 электрогидравлического регулятора насоса 6. Выход насоса 5 соединен с напорными магистралями 7 распределителя 4 и датчиком давления 8 выход LS- канала 9 распределителя соединен с датчиком давления 10. Управляющие входы распределительных секций подключены к соответствующим выходам пульта управления. Кроме того система содержит функциональный блок управления (ФБУ) состоящий из сумматора 11 первый инвертирующий вход которого подключен к выходу звена ограничителя 12 вход которого соединен с выходом датчика давления 10 LS-канала третий не инвертирующий вход сумматора 11 подключен к управляющему входу электрогидравлического регулятора насоса 6.
– универсальность: система обеспечивает работу в трех режимах;
– применение системы приводит к снижение энергетических потерь;
– относительно невысокая стоимость из-за использованием в системе более простых гидрораспределителей.
Электрогидравлическая система работает следующим образом. При задании одного или нескольких сигналов от пульта управления на соответствующие распределительные секции распределителя 4 золотник или золотники перемещаются напорная магистраль насоса 5 через открытые золотники распределительных секций подсоединяется к гидроцилиндрам а напорная магистраль гидроцилиндра к LS-каналу датчик давления 10 формирует электрический сигнал который через звено ограничения 12 поступает на второй вход сумматора 11 при этом в системе замыкается положительная обратная связь по давлению что приводит к увеличению давления на выходе насоса 5 до тех пор пока не начнется движение двигателя то есть не установится величина давления на выходе LS-канала а соответственно и величина сигнала на выходе датчика давления 10. При этом насос устанавливает такую подачу которая поддерживает установленную разность давлений между выходами насоса 5 и LS- канала 9. При повышении допустимого давления на гидроцилиндре звено ограничения 12 ограничивает величину выходного сигнала датчика давления 10 при этом в системе устанавливается давление срабатывания предохранительного клапана что экономит энергию и уменьшает разогрев рабочей жидкости в гидросистеме при повышении нагрузки. При необходимости ограничения нагрузки в отдельных приводах системы звено ограничения 12 может быть построено с регулируемой величиной ограничения по сигналу подаваемому на управление конкретной распределительной секции. В этом случае отпадает необходимость установки разгрузочного LS-клапана в конкретной секции что упрощает ее конструкцию и стоимость.
Рис. 1. Электрогидравлическая система управления. Пат. №2162551
За основу при проектировании была взята “Электрогидравлическая система управления” (Пат. 2162551) В разрабатываемой системе управления расходом и поддержания давления использован тот же принцип управления давлением и расхода при помощи регулируемого коаксиально-плунжерного насоса с электрическим управлением которое осуществляется с блока управления при этом использована обратная связь по давлению при помощи датчика давления. Проектировочная система отличается от аналога: низкой себестоимостью высокой точностью достигнутым главным образом из-за применения быстродействующей элементной базы качественной и надежной гидроаппаратуры.
Конструкторская часть.doc
1. Цель разработки и назначение системы
Трансмиссией называется силовая передача осуществляющая связь двигателя с ведущими колесами автомобиля. Трансмиссия предназначена для передачи крутящего момента с коленчатого вала двигателя на ведущие колеса а также для изменения величины этого момента. Кроме того трансмиссия обеспечивает движение автомобиля задним ходом.
Устройство трансмиссии зависит от количества ведущих мостов и их расположения. Трансмиссия может иметь:
Один задний ведущий мост;
Два ведущих моста – передний и задний;
Два задних ведущих моста и один передний управляемый;
Три ведущих моста: два задних и один передний;
Четыре ведущих моста.
По принципу действия трансмиссии могут быть механическими гидравлическими электрическими или комбинированными.
Гидравлическая трансмиссия в качестве основного элемента имеет гидравлическую передачу. Под гидравлической передачей понимают устройство предназначенное для передачи механической энергии посредством жидкости.
Гидравлические передачи делят на гидростатические (или объемные) и гидродинамические.
Гидравлическая трансмиссия с гидростатической передачей состоит из насоса распределительного устройства гидролиний и моторов расположенных на ведущих колесах. Масло под рабочим давлением от гидронасоса приводимого двигателем поступает в распределительное устройство от которого направляется к приводным моторам ведущих колес. Такая трансмиссия позволяет бесступенчато в большом диапазоне регулировать частоту вращения ведущих колес автомобиля.
Конструкция трансмиссии зависит от типа автомобиля его назначения и взаимного расположения двигателя и ведущих колес. Характер изменения передаваемого крутящего момента в разных типах трансмиссий различен. Трансмиссия и ее техническое состояние значительно влияют на эксплуатационные свойства автомобиля. Так при ухудшении технического состояния механизмов трансмиссии и нарушении регулировок в сцеплении главной передаче и дифференциале повышается сопротивление движению автомобиля и ухудшаются тягово-скоростные свойства проходимость экологичность автомобиля снижается топливная экономичность.
Целью данного дипломного проекта является разработка автогрейдера с гидростатической трансмиссии .
2. Описание автогрейдера
Автогрейдер предназначен для землеройно-профилировочных работ и служит для эксплуатации в дорожном строительстве. Автогрейдер Д3-98А как мощную и высоко эффективную дорожно-строительную машину целесообразно применять при выполнении особо энергоемких земляных работ большого объема или работ в тяжелых дорожных условиях.
Автогрейдером выполняются следующие работы:
Строительство и капитальный ремонт грунтовых и гравийных дорог.
Устройство в грунтовом полотне нароста под основание дороги.
Перемещение грунта в насыпь.
Разравнивание насыпного грунта и планировка поверхности.
Перемещение инертных материалов со стабилизирующими добавками при смешивании их на дороге.
Киркование (разрыхление грунта и изношенных полотен дорог).
Планировка поверхности больших территорий.
Очищение дорог и территорий от снежного заноса.
Автогрейдер представляет собой трехосную машину и состоит из двигателя трансмиссии ходовой части рабочего оборудования механизмов и систем управления рабочего места машиниста. Двигатель преобразует химическую энергию топлива сгорающего в его цилиндрах в тепловую энергию а затем в механическую передаваемую коленчатому валу.Трансмиссия автогрейдера : представляет собой группу механизмов предназначенных для передачи вращательного движения коленчатого вала ведущим колесам. Механизмами трансмиссии производится трогание автогрейдера с места и остановка изменение скорости и направления движения. В трансмиссию входят: муфта сцепления коробка передач ведущий мост карданная передача.
Преимущество гидростатической трансмиссии — это возможность плавно изменять передаточное отношение в большом диапазоне обеспечивать плавное трогание и разгон автогрейдера простое реверсирование и быстрое изменение скоростного режима движения благодаря малым вращающимся массам. Исключительная управляемость особенно в стеснённых пространствах и на уклонах. Гидростатическое торможение с полным контролем скорости без применения тормозов. Автоматическое изменение скорости и тяги в зависимости от внешних нагрузок. Ходовая часть-– совокупность элементов с помощью которых осуществляется передвижение автогрейдера и реализация его силы тяги. К ходовой части автогрейдера относят основную раму с механизмами подвески ведущего моста переднюю ось с колесами а также колеса средней и задней осей конструктивно объединенных в заднюю тележку.
Рабочее оборудование- предназначено для непосредственного выполнения операций автогрейдера – резание и перемещение грунта или других материалов.
Рабочее оборудование делится на основное постоянно установленное на машине и дополнительное – сменное предназначенное для вспомогательных операций. К основному рабочему оборудованию относится отвал с тяговой рамой и механизмом ее подвески к дополнительному – кирковщик .
Механизмы и системы управления предназначены для выбора машинистом направления движения автогрейдера изменения положения рабочего оборудования в процессе работы быстрой остановки двигателя автогрейдера или удержания его на месте запуска двигателя освещения и сигнализации. Механизмы и системы управления включают в себя : рулевое управление гидросистему тормоза и электрооборудование.
К рабочему месту машиниста относится: кабина с сидением пультами управления система обогрева вентиляция.
Различают рабочий и транспортный режимы автогрейдера. Основной рабочий
режим заключается в срезании и перемещении грунтавыравниваниие полотна
При транспортном режиме необходимом для передвижения машины к месту работы отвал максимально поднимают. Работа автогрейдера в этом режиме практически не отличается от работы обычных транспортных средств.
3.Тяговый расчет автогрейдера.
У автогрейдеров преобладающим режимом работы является тяговый что обусловливается особенностями его рабочего процесса. В среднем 80—85% общего времени работы автогрейдера приходится на тяговый режим. Транспортный режим не является составной частью рабочего цикла поскольку автогрейдеры относятся к землеройно-транспортньш машинам непрерывного резания грунта. Вследствие этого максимальные расчетные транспортные скорости современных автогрейдеров составляют 32—42 кмч. Поэтому тяговый расчет автогрейдеров будет заключаться в определении основных параметров в первую очередь полностью отвечающих требованиям тягового режима работы при выполнении различных технологических операций.
Основные параметры автогрейдера: полный и сцепной вес колесная схема весовые нагрузки на оси максимальная мощность двигателя минимальная расчетная скорость движения на низшей рабочей передаче максимальная расчетная транспортная скорость число передач и ряд передаточных чисел трансмиссии размеры отвала. Для нормальной работы автогрейдера необходимо соблюдение следующего условия
Pк ≥ Wраб ≤ φсц × Gсц (2.1)
где Pк – сила тяги на ведущих колесах кН;
Wраб – общее сопротивление при установившемся рабочем режиме кН;
φсц – коэффициент сцепления ведущих колес с грунтом
Gсц – сцепной вес автогрейдера кН.
Общее сопротивление при установившемся рабочем режиме складывается из следующих составляющих
Wраб = Wр + Wп + Wв + Wт (2.2)
где Wр – сопротивление грунта резанию ножом кН;
Wп – сопротивление поступательному перемещению перед отвалом
призмы волочения грунта кН;
Wв – сопротивление грунта при движении его вверх по отвалу кН;
Wт – сопротивление перекатыванию колес кН;
Определим сопротивление Wр
где к – удельное сопротивление грунта резанию кНм2;
F – площадь поперечного сечения вырезаемой стружки м2.
F = × φсц × G ( кк × m ) (2.4)
где – коэффициент использования сцепного веса автогрейдера;
G – сила тяжести автогрейдера кН;
кк – удельное сопротивление грунта копанию кНм2;
m – коэффициент учитывающий неравномерность сечения стружки при
Определим сопротивление Wп
где Qгр – вес призмы грунта перед отвалом кН;
f – коэффициент внутреннего трения грунта.
где Vф – объем призмы волочения перед отвалом м3 ;
λ – насыпной вес призмы волочения кНм3 .
Vф = ( H – hср)2 × l × кз (2 × tgφ ) (2.7)
где Н – высота отвала м;
hср – среднее значение глубины резания м;
кз – коэффициент заполнения отвала;
φ – угол естественного откоса грунта град.
Определяем сопротивление Wв
Wв = Qгр × cos2 × f1 (2.8)
где – угол резания ножа град. ;
f1 – коэффициент трения грунта об отвал.
Определяем сопротивление Wт
где – коэффициент сопротивления качению колес по грунту;
Максимальная сила тяги автогрейдера определяемая по сцепному весу автогрейдера равна
φсц × Gсц = φсц × 0 × G (2.10)
где φсц – коэффициент сцепления ведущих колес с грунтом;
Определяем величину тяговой силы
Рк = Me × iт × м ( rc × 1000 ) (2.11)
где Me – максимальный крутящий момент на валу двигателя Н×м;
м – коэффициент полезного действия трансмиссии;
rc – силовой радиус колеса м.
3.1.Исходные данные для проектирования.
Длина отвала =4250 мм
Высота отвала =720 мм
Масса автогрейдера =190000н
Колесная формула 1 х 3 х 3
Общий вес автогрейдера G связан со сцепным весом следующим образом:
-коэффициент определяемый колесной формулой.
В свою очередь сцепной вал автогрейдера определяет тяговое усилие на ведущих колесах.
- коэффициент использования сцепного веса.
Коэффициент данный – величина переменная и зависит в основном от коэффициента буксования ведущих колес. При отсутствии буксования () коэффициент близок к нулю; при 100% буксовании (=100%) он достигает своего максимального значения
Рис.2.1. Схема сил действующих на автогрейдер.
Исследованиями установлено что существует такой коэффициент использования сцепного веса при котором мощность развиваемая автогрейдером на отвале имеет максимальное значение .
Величина в естественных условиях работы автогрейдера колеблется в пределах при этом коэффициент буксования .
Наиболее эффективное использование автогрейдера будет в том случае когда тяга на ведущих колесах равна оптимальной:
Оптимальное сечение стружки разрабатываемой автогрейдером за один
К=220000()-расчетное значение сопротивление грунта копанию
учитывающий как резание так и перемещение грунта.
Мощность на отвале Вт:
- фактическая скорость движения автогрейдера при выполнении им заданной рабочей операции.
Наблюдения за работой автогрейдеров в эксплуатационных условиях показывает что при вырезания кювета фактическая рабочая скорость машины без применения автоматов не может превышать 4 .
Примем фактическую рабочую скорость =35() при =02.
=93467 (Вт)=9347(кВт) (2.19)
Потери мощности на буксование кВт:
где: =009-коэффициент сопротивления перекапыванию в естественных условиях.
Потери мощности на буксование объясняется тем обстоятельством что ведущее колесо развивая тяговое усилие обязательно буксует.
Потери мощности на перекатывание кВт:
Суммарная мощность на ведущих колесах кВт:
Потребная мощность двигателя кВт:
9–коэффициент уменьшения мощности двигателя из-за неустанно-
=085 –коэффициент полезного действия трансмиссии.
Выбираем двигатель модели У1Д6-250ТК-С4-четырехтактный шестицилиндрический дизельный с непосредственным впрыскиванием топлива мощностью =184 (кВт) с номинальной частотой вращения =1500 (об.мин.).
Номинальный момент двигателя Hм
4.Расчет объемного гидропривода
4.1.Исходные данные для расчета объемного гидропривода.
Привод вращательного движения
Номинальное давление гидропривода Рном МПа
Крутящий момент на валу гидромотора М кН м
Частота вращения вала гидромотора nм обс
Длины гидролиний м:
Местные сопротивления:
присоединительный штуцер
угольник с поворотом на 900
Температура рабочей жидкости tж 0С
Температура окружающей среды tв 0С
Для расчета гидропривода необходимы следующие основные исходные данные: выходные параметры гидродвигателей исполнительного механизма (величины крутящих моментов и скоростей вращения вала); режимы работы принципиальная гидравлическая схема; номинальное давление в гидросистеме; граничные температуры окружающего воздуха и др.
При расчете гидропривода принимается ряд допущений основными из которых являются следующие: рабочая жидкость считается несжимаемой; температура жидкости основные физические свойства жидкости (плотность вязкость и др.) принимаются постоянными; рассматривается установившийся режим работы гидропривода; коэффициенты гидравлических сопротивлений постоянны; разрыва потока жидкости при работе гидропривода не происходит; подача насоса питающего гидросистему.
4.2.Определение мощности гидропривода и насоса
Мощность гидропривода определяют по заданным нагрузкам и скоростям гидродвигателей обеспечивающих привод исполнительных механизмов.
Полезную мощность гидродвигателя вращательного действия (гидромотора) определяют по формуле:
где - Мощность гидродвигателя кВт; М – крутящий момент на валу гидромотора кН м; - угловая скорость вращения вала гидромотора с-1; nм – частота вращения вала гидромотора с-1(обс).
= 035 · 2 · 314 · 25 = 55 кВт (2.28)
Полезную мощность насоса определяют исходя из мощности гидродвигателя с учетом потерь энергии при ее передаче от насоса к гидродвигателю по формуле:
где Nнп – мощность насоса кВт; kзу - коэффициент запаса по усилию kзу = 11 12; kзс – коэффициент запаса по скорости kзс = 11 13; Nгдв – мощность гидродвигателя кВт.
Nнп = 115 · 12 · 55 = 758 кВт (2.30)
Меньшие значения коэффициентов следует выбирать для гидроприводов работающих в легком и среднем режимах а большие в тяжелом и весьма тяжелом режимах эксплуатации.
Зная необходимую полезную мощность насоса определяемую по формуле (2.29) и учитывая что полезная мощность насоса связана о номинальным давлением и подачей зависимостью Nнп = pном Qн можно найти подачу или рабочий объем насоса по формулам:
где Nнп - мощность насоса кВт; Qн - подача насоса дм3с Qн = qн nн; Pном - номинальное давление МПа; qн - рабочий объем насоса дм3 (дм3об); nн - частота вращения вала насоса с -1 (обс).
Qн = 758 16 = 474 дм3с (2.33)
qн = 758 16 · 32 = 014 дм3об (2.34)
Для того чтобы найти рабочий объем насоса по формуле (2.32) необходимо задаться частотой вращения вала насоса которая зависит от типа приводного двигателя (двигатель внутреннего сгорания электродвигатель и др.). Для мобильных машин в качестве приводных двигателей насосов чаще всего используют дизели с номинальной частотой вращения 1500 1600 1700 обмин и т.д.
Номинальные частоты вращения установленные ГОСТом 12446-80 следующие: 750; 960; 1200; 1500; 1920; 2400 обмин и т.д. Для насосов с приводом от электродвигателей принимаются значения частот вращения соответствующих электродвигателей.
Принимая частоту вращения 1920 обмин будем иметь :
nн =192060= 32 с -1 (обс). (2.35)
Подставляем значение из формулы (2.35) в формулу (2.34) и производим расчет.
Насос выбирают из технической литературы по двум параметрам ближайшим к расчетным: номинальному давлению рном и рабочему объему насоса qн .
Насос выбирают из технической литературы по двум параметрам ближайшим к расчетным: номинальному давлению рном и рабочему объему насоса qн
Техническая характеристика насоса
Давление на выходе МПа:
Давление на входе в насос МПа:
Частота вращения вала обмин:
Номинальная объемная подача дм3мин
Номинальная потребляемая мощность кВт
КПД насоса (не менее)
Объемный КПД (не менее)
При выборе насоса следует учитывать что насосы рассчитанные на высокое давление могут быть использованы в гидроприводах имеющих более низкое давление. Если значения рабочего объема насоса в результате расчетов оказываются большими то возможно применение двух и более насосов устанавливаемых параллельно. При этом с целью унификации целесообразно использовать один тип насосов.
По технической характеристике выбранного насоса производят уточнение действительной подачи насоса:
где Qнд - действительная подача насоса дм3 с; qнд - действительный рабочий объем насоса дм3 (дм3об); nнд - действительная частота вращения вала насоса nнд = nн с -1 (обс); - объемный' КПД насоса.
Qнд = 0162 · 32 · 094 = 48 дм3 с (2.37)
Действительная частота вращения вала насоса nнд в формуле (2.26) может отличаться от номинальной частоты вращения вала насоса из его технической характеристики и берется равной частоте nн принятой в формуле ().
Насос предназначен для передачи механической энергии приводного двигателя к исполнительным органам изделия посредством регулируемого по величине и направлению потока рабочей жидкости.
Выбранный насос конструктивно состоит из следующих узлов:
- механизма управления (ручного и электрогидравлического)
- насоса подпитки: героторного насоса
- других вспомогательных элементов.
Ходовая часть насоса представляет собой аксиально-плунжерную машину бескарданного типа с гидростатическими опорами и состоит из блока цилиндров 1 в котором размещены поршни 2 с пятами 3.
Ходовая часть размещена в корпусе 4 насоса на валу 5 имеющему шлицевое соединение с блоком цилиндров 1 которое позволяет блоку самоустанавливаться при прогибе вала 5. Сам вал установлен в подшипниках 6 и 7.
Пружина 8 опираясь одним своим концом через кольцо 9 на вал 5 а другим через кольцо 38 и 39 осуществляет поджим блока цилиндров 1 вместе с латунным распределителем 10 к стальному распределителю 11 опирающемуся на силовую крышку 12 и центрируемого по подшипнику 7 с помощью штифта 13. Поджим уравновешивает моменты центробежных сил поршней массы блока цилиндров и сил трения стремящихся опрокинуть блок цилиндров относительно края распределителя 11.
В зоне высокого давления поршни с пятами прижимаются к опорной поверхности люльки 14 давлением рабочей жидкости. В зоне же всасывания силы давления жидкости в цилиндрах блока 1 могут оказаться меньше сил трения и сил инерции действующих на поршень с пятами поэтому для предотвращения отрыва пят 3 от опорной поверхности люльки в конструкции ходовой части предусмотрен сепаратор 15.
Люлька 14 совместно с подшипниками 16 установлена в корпусе 4 насоса и посредством рычага 35 и пальца 36 связана с цилиндром управления 37 насоса.
Ручной механизм управления насосом представляет собой однокаскадный гидроусилитель золотникового типа (сервоклапан) 17 имеющий механическую посредством рычага 38 обратную связь люльки 14 насоса с золотником. Пружина сервоклапана осуществляет установку золотника в нейтральное положение при неработающем насосе или при отсутствии усилия на рычаге сервоклапана. Воздействием на рычаг 38 в ту или другую сторону осуществляется управление насосом.
Электрогидравлический механизм управления является пропорциональным однокаскадным гидрораспределителем 18 золотникового типа и предназначен для регулирования потока рабочей жидкости пропорционально подаваемому на него электрическому сигналу управления. Обратная связь в этом случае осуществляется при помощи датчика положения 26 через блок управления .
Переключение режимов управления насосом (механическое или электрогидравлическое) осуществляется при помощи гидрораспределителя 19 ручного управления установленного на корпусе 4 насоса.
Вспомогательный героторный насос 20 расположен в корпусе 21 фильтра который крепится к силовой крышке 12 насоса. Валик 22 героторного насоса связан с валом 5 насоса шлицевым соединением.
Фильтр 23 предназначен для очистки рабочей жидкости и содержит фильтроэлемент и предохранительный клапан предохраняющий фильтроэлемент от разрушения при повышении давления сверхдопустимого для фильтроэлемента.
Также в корпусе 21 фильтра расположены датчик давления 24 управления насосом и датчик загрязненности 25 фильтроэлемента.
Датчики давления 30 служат для контроля давления в силовых магистралях насоса и обеспечивают обратную связь по давлению.
В расточках силовой крышки 12 размещены два обратно-предохранительных клапана 27 и предохранительный клапан 28 насоса подпитки.
Заправка насоса рабочей жидкостью выполняется через дренажные отверстия «Т1» или «Т2» на корпусе 4 насоса. Для выпуска воздуха из внутренних полостей насоса на корпусе 4 предусмотрена пробка 29.
Герметичность выходного вала насоса обеспечивается постановкой уплотнительного узла 31 во фланец 32 насоса.
Выбранный насос обеспечивает необходимую подачу рабочей жидкости для нормального функционирования системы.
4.4.Определение внутреннего диаметра гидролиний скоростей движения жидкости.
Расчетные значения внутренних диаметров всасывающей напорной и сливной гидролиний определяют из уравнения неразрывности потока жидкости с учетом размерностей по формуле:
где dр - расчетное значение внутреннего диаметра гидролинии м; Qнд - действительный расход жидкости (подача насоса) дм3с; vж - скорость движения жидкости в гидролинии мс.
Скорости движения рабочей жидкости выбирают в зависимости от назначения гидролинии таким образом чтобы для уменьшения потерь давления на гидравлическое трение режим движения был ламинарным или близким к нему.
для всасывающей гидролинии vж = 12 мс
для напорной гидролинии vж = 5 мс
для сливной гидролинии vж = 2 мс тогда
для всасывающей гидролинии (2.39)
для напорной гидролинии (2.40)
для сливной гидролинии (2.41)
По расчетному значению внутреннего диаметра гидролинии dр производят выбор трубопровода по ГОСТу 8734-75 при этом действительное значение диаметра трубопровода d должно быть больше расчетного т.е. d ≥ dр . Значение толщины стенки трубопровода принимают конструктивно равным 2 4 мм.
После выбора трубопроводов производят определение действительных скоростей движения жидкости во всасывающей напорной и сливной гидролиниях по формуле:
где vжд - действительное значение скорости движения жидкости мс; d - действительное значение внутреннего диаметра гидролинии м; Qнд - действительный расход жидкости дм -3с.
для всасывающей гидролинии
для напорной гидролинии
для сливной гидролинии
4.5.Выбор гидроаппаратуры кондиционеров рабочей жидкости
Гидроаппаратуру (распределители обратные клапаны гидрозамки предохранительные клапаны и др.) выбирают по условному проходу и
номинальному давлению. Дополнительным параметром для гидроаппаратуры является номинальный расход рабочей жидкости.
Под условным проходом dу го ГОСТу 16516-80 понимается округленный до ближайшего значения из установленного ряда диаметр круга площадь которого равна площади характерного проходного сечения канала устройства или площади проходного сечения присоединяемого трубопровода.
Соотношения между условными проходами и действительными внутренними диаметрами по ГОСТу 16516-80 приведены в табл.1.
Условный проход dу мм
Диапазон действительных внутренних диаметров d мм
В данном случае принимаю dу = 320 мм.
Так как dу = 320 мм и номинальное давление рном = 16 МПа то выбираем гидрораспределитель Р-32.160-20-01-02.1-10.4-07-30 ГОСТ 22-829-74.
Техническая характеристика секционного гидрораспределителя
Условный проход 32 мм
Расход рабочей жидкости дм3мин
Внутренние перетечки рабочей жидкости при нейтральной позиции золотника и номинальном давлении см3мин не более:
для всех рабочих секций кроме 05.2
для рабочих секций 05.2
Утечки рабочей жидкости через обратные клапаны напорных и промежуточных секций при номинальном давлении см3мин не более
Максимальное усилие для перемещения золотника из нейтральной позиции в рабочие при номинальных давлении и расходе Н
Количество всех секций собираемых в одном блоке не более
Давление в сливной гидролинии МПа не более
Потери давления в гидрораспределителе при нейтральной позиции золотников и номинальном расходе рабочей жидкости МПа не более:
Потери давления при рабочей позиции золотника МПа не более
зависит от числа секций
Основные параметры обратного клапана типа 61
Номинальный расход дм3мин
Характеристика предохранительного клапана прямого действия
Условный проход гидрораспределителя мм
Диапазон регулирования давления МПа
Характеристика предохранительного клапана и блоков предохранительного клапана непрямого действия
Предохранительный клапан (см. Рис. 3) служит для предохранения гидросистемы и ее элементов от перегрузок.
Рис. 1. Предохранительный клапан.
78–кольцо уплотнительное.
Расчет предохранительного клапана.
Определить параметры предохранительного клапана обеспечивающие заданные характеристики насоса.
Клапан срабатывает не вызывая пика давления в системе если время t1 подъема давления насосом оказывается меньше или равно времени срабатывания клапана t2
Условие (t1 « t2) выполняется в пределах заданного показателя чувствительности %
Где P – величина пика давления МПа (кгссм²)
= (25 + 24.4) 25 · 100 = 197
Fк =314 · (33² - 28² ) 4 = 2394
Pпр =25 ·2394 = 59866
Величина подъема клапана мм
X = Qн (K · ·dк √Pн · Pсл )
Где K – коэффициент проводимости клапана
Ккл – коэффициент расхода жидкости через клапан
g – ускорение свободного падения мс²
K = 09 · √2 · 981 8600 = 0042
X = 150 (0042 · 314 · 33 · √25 – 244) = 882
Время открывания клапана определяется из условия равноускоренного движения клапана без начальной скорости под действием среднего значения P с
T2 = √2 mкл · X (P · Fкл – R)
где R – сила сопротивления движения клапана Н
P · Fкл – K = (0125÷025) P · Fкл
Время нагнетания давления насосом с
Где W – предохранительный объем см³
Результаты расчетов занесены в таблицу .
Наименование параметра
Высота подъема клапана мм
Усилие удержания клапана Н
Время срабатывания клапана с
Выбранные параметры клапана обеспечивают требования по быстродействию.
В качестве кондиционеров для очистки рабочей жидкости от загрязняющих примесей в гидроприводах применяют фильтры или сепараторы.
Техническая характеристика линейного фильтра
Типоразмер 1.2.32-40
Номинальный расход через фильтр при вязкости рабочей жидкости 20 30 сСт дммин
Номинальная тонкость фильтрации мкм
Номинальное давление МПа
Номинальный перепад давления при номинальном расходе и вязкости рабочей жидкости не более 30 сСт МПа
Перепад давления на фильтроэлементе при открывании перепускного клапана МПа
Ресурс работы фильтроэлемента до замены или промывки ч
Масса сухого фильтра кг
Кондиционеры выбирают в зависимости от требований; предъявляемых к чистоте рабочей жидкости по следующим параметрам: условному проходу номинальной тонкости фильтрации номинальной пропускной способности и номинальному давлению. Поэтому перед их выбором необходимо установить требования к тонкости фильтрации обуславливаемые типом выбранного насоса.
Выбор рабочих жидкостей производят на основе анализа режимов работы и условий эксплуатации гидропривода с учетом конструктивных особенностей установленного гидравлического оборудования главным
образом конструктивных особенностей используемого насоса. Рабочая жидкость должна удовлетворять требованиям.
Техническая характеристика масла
Плотность при 20 0С кгм3
Вязкость при 50 0С сСт
Температура застывания 0С
Температура вспышки 0С
4.6.Расчет потерь давления в гидролиниях
Определение потерь давления при движении жидкости в гидролиниях необходимо для более точного расчета гидродвигателя а также для определения гидравлического КПД гидропривода.
Потери давления определяют отдельно для каждой гидролинии (всасывающей напорной сливной) при определенной температуре рабочей жидкости.
Потери давления в гидролинии определяют по формуле:
где Δp - потери давления в гидролинии МПа; - сумма путевых потерь МПа; - сумма потерь в местных сопротивлениях МПа.
Потери давления по длине гидролинии определяют по формуле:
где Δp λ - коэффициент путевых потерь (коэффициент Дарси); d - внутренний диаметр гидролинии м; vжд - скорость движения жидкости в гидролинии мс; ρ - плотность рабочей жидкости кгм3.
При подстановке в формулу (9) длины гидролинии l следует учитывать что для всасывающей гидролинии l = lвс для напорной гидролинии l = lнап + lисп а для сливной гидролинии l = lсл + lисп. Коэффициент путевых
потерь зависит от режимадвижения жидкости его определяют по формулам: а) для ламинарного режима (Rе 2320):
б) для турбулентного режима (Rе > 2320):
Число Рейнольдса определяют по формуле:
где vжд - скорость движения жидкости в гидролинии мс; d - внутренний диаметр гидролинии м; v - кинематический коэффициент вязкости рабочей жидкости мс2 ( = 03*10-4 м2с).
Для всасывающей (турбулентный) тогда
Для напорной (турбулентный) тогда
Для сливной (турбулентный) тогда
Потери давления в местном сопротивлении определяют по формуле:
где Δpм - потери давления в местном сопротивлении МПа; - коэффициент местного сопротивления; vжд - скорость движения жидкости мс;
ρ - плотность рабочей жидкости кгм3.
Ориентировочные значения коэффициентов местных сопротивлений некоторых элементов гидропривода
Тип местного сопротивления
Сверленый треугольник
Присоединительный штуцер
Угольник с поворотом на 900
= 1·2+1·015+2·15+1·2+1·015 = 73
Потери давления в местном сопротивлении для напорной гидролинии
Потери давления в гидролинии Δр = 0087 + 0080 = 0167 МПа
Потери давления в местном сопротивлении для сливной гидролинии
Потери давления в гидролинии Δр = 00096 + 00114 = 00021 МПа
4.7.Расчет гидромотора
Основными параметрами гидромотора являются рабочий объем qм номинальное давление рном частота вращения вала nм расход рабочей жидкости Qм .
Мощность потребляемая гидромотором определяют по его основным параметрам:
где Nм - мощность гидромотора кВт; рм - перепад давления на гидромоторе МПа рм = (рном - Δрн) – Δрс здесь рном - номинальное давление Δрн Δрс - потери давления в напорной и сливной гидролиниях; Qм - расход жидкости через гидромотор дм 3с; qм - рабочий объем гидромотора дм3 (да3 об); nм - частота вращения вала гидромотора с -1 (обс).
рм = (16 – 0167) – 0021 = 158
Nм = 158 · 0139 · 25 = 55 кВт
Рабочий объем гидромотора определяют из равенства полезной мощности гидромотора определяемой по формуле (1) и потребляемой мощности т.е. по формуле:
где qм – рабочий объем дм3 (дм3об); М – крутящий момент на валу
гидромотора кН м; рном – номинальное давление МПа; Δрн – потери давления в напорной гидролинии МПа; Δрс – потери давления в сливной гидролинии МПа.
Но значение рабочего объема гидромотора должно еще удовлетворять следующему соотношению:
Из формулы (16) вторично определяют рабочий объем гидромотора:
где qм – рабочий объем дм3 (дм3об); Qнд - расход жидкости дм3с; nм – частота вращения вала гидромотора с -1 (обс).
По среднему значению рабочего объема и остальным параметрам производят выбор гидромотора.
Техническая характеристика нерегулируемых гидромоторов типа 210
Давление на входе МПа:
Частота вращения обмин:
Крутящий момент Н м:
Номинальная эффективная (полезная) мощность кВт
КПД в номинальном режиме при вязкости рабочей жидкости 33 сСт:
Допускаемая температура рабочей жидкости 0С:
с корпусом из чугуна
После выбора гидромотора определяют действительные значения частоты вращения вала и крутящего момента развиваемого гидромотором.
Действительные значения крутящего момента и частоты вращения вала гидромотора определяют по формулам:
где qмд - действительный рабочий объем гидромотора дм3 (дм3об); гм об - гидромеханический и объемный КПД гидромотора из его технической характеристики.
Далее приводят сравнение действительных и заданных параметров по относительным величинам:
Допускаемая величина отклонения не превышает ± 10%.
Гидромотор предназначен для преобразования энергии потока рабочей жидкости изменяемого по величине в механическую энергию вращения выходного вала с ограничением давления рабочей жидкости.
Выбранный гидромотор конструктивно состоит из следующих узлов:
- механизма электрогидравлического управления
Ходовая часть гидромотора представляет собой аксиально-плунжерную машину бескарданного типа с гидростатическими опорами и состоит из блока цилиндров 1 в котором размещены поршни 2 с пятами 3.
Ходовая часть размещена в корпусе 4 гидромотора на валу 5 имеющему шлицевое соединение с блоком цилиндров 1 которое позволяет блоку самоустанавливаться при прогибе вала 5. Сам вал установлен в подшипниках 6 и 7.
Пружина 8 опираясь одним своим концом через кольцо 9 на вал 5 другим через кольцо 29 и 30 осуществляет поджим блока цилиндров 1 вместе с латунным распределителем 10 к стальному распределителю 11 опирающегося на силовую крышку 12 и центрируемого по подшипнику 7 с помощью штифта 13. Поджим уравновешивает моменты центробежных сил поршней с пятами массы блока цилиндров и сил трения стремящихся опрокинуть блок цилиндров относительно края распределителя 11.
В зоне высокого давления поршни с пятами прижимаются к опорной поверхности люльки 14 давлением рабочей жидкости. В зоне же всасывания силы давления жидкости в цилиндрах блока 1 могут оказаться меньше сил трения и сил инерции действующих на поршень с пятами поэтому для предотвращения отрыва пят 3 от опорной поверхности люльки 14 в конструкции ходовой части предусмотрен сепаратор 16.
Люлька 14 совместно с подшипниками 15 установлена в корпусе 4 гидромотора и посредством рычага 31 и пальца 27 связана с цилиндром управления 28 гидромотора.
Электрогидравлический механизм управления гидромотором является пропорциональным однокаскадным гидрораспределитель 17 золотникового типа и предназначен для регулирования потока рабочей жидкости пропорционально подаваемому на него электрическому сигналу управления.
Датчик положения 19 расположенный на корпус 4 гидромотора обеспечивает обратную связь по углу отклонения люльки 14 через блок управления.
Блок прокачки 18 гидромотора осуществляет прокачку рабочей жидкости из магистрали низкого давления с целью её охлаждения и очистки через фильтры гидросистемы а также создает давление для управления гидромотором при помощи предохранительного клапана КП3.
Датчик скорости 20 служит для контроля частоты вращения выходного вала гидромотора.
Заправка гидромотора рабочей жидкостью выполняется через заправочный клапан 21 представляющий собой предохранительный клапан шарикового типа.
Для выпуска воздуха из внутренних полостей гидромотора на корпусе 4 предусмотрена пробка 22.
Герметичность выходного вала 5 гидромотора обеспечивается постановкой уплотнительного узла 23 во фланец 24 гидромотора.
Вал насоса приводится во вращение от двигателя. Поршни установленные в блоке цилиндров вращаются вокруг оси блока и одновременно совершают возвратно-поступательное движение при этом за одну половину оборота поршень всасывает рабочую жидкость а за другую - нагнетает её в гидросистему. Давление на выходе из насоса определяется нагрузкой на рабочий орган и ограничивается предохранительным клапаном гидросистемы. Подача определяется частотой вращения вала и рабочим объемом насоса. Если гидромотор не нагружен (давление рабочей жидкости минимально) подача насоса полностью воспринимается камерами гидромотора.
Выбранные насос и гидромотор обеспечивают работоспособность системы управления изделием в целом.
4.8.Тепловой расчет гидропривода
Тепловой расчет гидропривода приводится с целью определения температуры рабочей жидкости объема гидробака и выяснения необходимости применения специальных теплообменных устройств.
Основными причинами выделения тепла в гидроприводе являются: внутреннее трение рабочей жидкости дросселирование жидкости при прохождении различных элементов гидропривода трение в гидрооборудовании и др.
Количество тепла выделяемое в гидроприводе в единицу времени эквивалентно теряемой в гидроприводе мощности.
Тепловой расчет гидропривода ведется на основе уравнения теплового баланса:
где Qвыд - количество тепла выделяемого гидроприводом в единицу времени (тепловой поток) Вт; Qотв - количество тепла отводимого в единицу времени Вт.
где Qвыд - количество тепла выделяемого в единицу времени Вт; Nн - мощность привода насоса (потребляемая) Вт; гм - гидромеханический КПД гидропривода; kв - коэффициент продолжительности работы гидропривода; kд - коэффициент использования номинального давления; рном - номинальное давление Па; Qнд - действительная подача насоса м3с; н - полный КПД насоса из его технической характеристики.
Гидромеханический КПД гидропривода находят по формуле:
где гмн гм гдв - гидромеханические КПД насоса и гидродвигателя соответственно; г – гидравлический КПД гидропривода учитывающий потери давления в гидролиниях.
Гидравлический КПД гидропривода равен:
где рном – номинальное давление МПа; Δрн Δрс Δрвс – потери давления в напорной сливной и всасывающей гидролиниях соответственно МПа.
Следует отметить что в технических характеристиках насосов и гидромоторов обычно приводят значения полного и объемного КПД. Поэтому гидромеханический КПД определяют из выражения для полного КПД гидромашины:
где н – полный КПД насоса (или гидромотора); гн - гидравлический КПД; мн - механический КПД; обн - объемный КПД; гмн - гидромеханический КПД.
Значения коэффициентов продолжительности работы гидропривода и использования номинального давления приведены в табл.2.
Режим работы гидропривода
Коэффициент продолжительности работы гидропривода kв
Коэффициент использования номинального давления kд
Скреперы трубоукладчики рыхлители
Бульдозеры автогрейдеры автокраны погрузчики
Экскаваторы катки машины непрерывного действия тягачи и др.
Коэффициент продолжительности работы гидропривода kв определяют отношением времени действия гидропривода tгп к времени работы машины tм т.е. kв = tгп tм .
Коэффициент использования номинального давления kв равен отношению рабочего давления в гидроприводе р к номинальному рном т.е. kв = р рном .
Количество тепла отводимого в единицу времени от поверхностей металлических трубопроводов гидробака при установившейся температуре жидкости определяют по формуле:
где Qотв - количество отводимого в единицу времени тепла Вт; kмп - коэффициент теплопередачи от рабочей жидкости в окружающий воздух Вт(м2 град); tж - установившаяся температура рабочей жидкости °С tж ≤ 0 70 °С; t0 - температура окружающего воздуха °С; - суммарная площадь наружной теплоотводящей поверхности трубопроводов (всасывающей напорной сливной гидролиний) м2 Sr l Sб - площадь поверхности гидробака м2 .
для всасывающей Sri в = 314(0073 + 2·3) ·090 = 171
для напорной Sri н = 314(0035 + 2·3) ·770 = 1459
для сливной Sri с = 314(0057 + 2·3) ·860 = 1635
= Sri в +Sri н + Sri с = 171 + 1459 + 1635 = 3265
Для практических расчетов рекомендуется принимать значения kмп = 10 15 Вт(м2 град) причем минимальные значения коэффициента kмп
берутся при затрудненной циркуляции воздуха максимальные - при свободном обтекании воздухом элементов гидропривода.
Площадь поверхности гидробака определяют из уравнения теплового баланса (21) после подстановки в него выражений (22) и (26).
Расчетная площадь поверхности гидробака связана с его объемом следующей зависимостью:
где Sб - площадь поверхности гидробака м2 ; V - объем гидробака дм3.
Из формулы (27) определяют объем гидробака. Этот объем не должен превышать 08 30 минутной подачи насоса. Если это условие не удовлетворяется то необходима установка теплообменника.
В этом случае задаются объемом гидробака исходя из рекомендуемого соотношения 08 30 минутной подачи насоса. Затем по формуле (27) определяют площадь гидробака а площадь теплоотводящей поверхности теплообменника находят из уравнения теплового баланса гидропривода с теплообменником (отвод тепла через наружную поверхность трубопроводов не учитываем):
где Qвыд - количество тепла выделяемого в единицу времени Вт; Qб - количество отводимого в единицу времени тепла от поверхности гидробака Вт Qб = kmn (tж – t0)Sб ; Qт - количество отводимого в единицу времени тепла от теплоотводящей поверхности теплообменника Вт Qт = kmnт(tж– t0)Sт здесь kmnт - коэффициент теплопередачи теплообменника Вт(м2 град); Sт - площадь теплоотводящей поверхности теплообменника м2.
При расчете теплообменника зная kmnт принимают равным 110 175 Вт(м2 град) .
Qб = 12 (60 – 10) ·0103 = 618 Вт
Qт = 140(60– 10) ·Sт
59618 = 618 + 7000· Sт => Sт = 279 м2.
По расчету принимаем площадь теплоотводящей поверхности теплообменника 279 м2.
5. Описание работы гидросистемы гидростатической трансмиссии
Система управления ГСТ обеспечивает бесступенчатое изменение скорости движения автогрейдера вперед и назад на двух режимах в зависимости от положения рукоятки управления.
Электрогидравлическое управление: при нахождении рукоятки управления в среднем (нейтральном) положении вал гидромотора вращаться не должен. При отклонении рукоятки управления вперед (назад) частота вращения вала гидромотора плавно изменяется от нуля до максимального значения.
Ручное управление: включение ручного управления производится переключением управляющего распределителя. При ручном режиме управления изменение частоты вращения вала гидромотора производится только за счет регулирования подачи насоса.
Гидросистема ГСТ предназначена для управления движением автогрейдера посредством потока рабочей жидкости регулируемого по направлению и скорости.
В состав гидросистемы входят: насос А1 мотор А2 а так же пополнительный бак Б1 и гидромонтажный комплект которые в состав гидростатической трансмиссии не входят.
По схеме соединения насоса и исполнительного двигателя гидросистема является замкнутой по виду регулирования – объёмной т.к. основной насос является регулируемым и работает в режиме объёмного регулирования расхода рабочей жидкости.
При вращении вала приводного двигателя и связанного с ним валов насоса Н1 и героторного насоса Н2 масло нагнетаемое героторным насосом очищенное через фильтр Ф1 поступает к гидрораспределителю Р31 и сервоклапану Р32 а также через обратно-предохранительные клапана КОП1 и КОП2 в силовые полости гидронасоса. Излишки нагнетаемого масла сливаются через клапан КП2 и поступают в корпус.
Вариант 1 – гидростатическая трансмиссия работает в режиме ручного управления.
Без внешнего воздействия на рычаг управления насос Н1 подачу масла не производит. При отклонении рычага управления и перемещении связанного с ним посредством рычага и тяг золотника масло от героторного насоса Н2 поступает через гидрораспределитель Р34 переключенный на режим ручного управления (электрогидравлическое управление отключено) в полость цилиндра ЦУ1.
Поршень цилиндра ЦУ1 под действием сил давления масла отклоняет связанную с ним люльку насоса Н1 и рабочая жидкость поступает в магистральную полость и далее в силовые полости гидромотора М1 и под золотник ЗП1 блока прокачки БП.
Под воздействием перепада давления рабочей жидкости между магистралью высокого и низкого давления золотник ЗП1 перемещается и соединяет магистраль низкого давления с линией управления гидромотора. Давление управления создается при помощи предохранительного клапана КП3. Излишки рабочей жидкости отводятся в корпус гидромотора.
При этом люлька гидромотора удерживается пружиной цилиндра управления ЦУ2 на максимальном углу.
Другая полость цилиндра ЦУ1 соединяется со сливом сервоклапана Р32 и масло сливается в корпус насоса.
Каждому углу поворота рычага соответствует определенная подача насоса Н1.
При отклонении рычага в обратную от нейтрального положения сторону люлька отклоняется в противоположном направлении. Происходит смена направления потока рабочей жидкости а следовательно и направления вращения вала мотора.
В среднем (нулевом) положении при отсутствии внешнего воздействия рычаг удерживается пружиной входящей в состав сервоклапана Р32.
Вариант 2 – гидростатическая трансмиссия работает в режиме электрогидравлического управления.
Нагнетаемое героторным насосом Н2 масло пройдя через фильтр Ф и очистившись по магистралям поступает к пропорциональному золотниковому гидрораспределителю Р31. Управляющий электрический сигнал действует на электромагнит гидрораспределителя Р31 которые заставляют золотник гидроцилиндра Р31 перемещаться при этом поток рабочей жидкости поступает в гидрораспределитель ручного управления Р34 переключенный на электрогидравлическое управление (ручное отключено) и оттуда попадает в одну из полостей цилиндра управления ЦУ1 заставляя поршень цилиндра управления отклонять люльку насоса на заданный угол. Вторая полость цилиндра ЦУ1 через гидрораспределители РЗ4 и РЗ1 соединяется со сливом в корпус насоса Н1.
При подаче «отрицательного» электросигнала – люлька насоса поворачивается в противоположную относительно нормали сторону. Происходит смена направления потока рабочей жидкости а также смена направления вращения вала мотора.
Датчик положения ДП1 совместно с гидрораспределителем Р31 обеспечивает обратную связь по углу отклонения люльки насоса Н1.
При работе гидромотора рабочая жидкость нагнетаемая из гидросистемы поступает в силовые полости гидромотора М1 и под золотник ЗП1 блока прокачки БП1.
Под воздействием перепада давления рабочей жидкости между магистралью высокого и низкого давления золотник ЗП1 перемещается и соединяет магистраль низкого давления с линией управления гидромотора. Давление управление создается при помощи предохранительного клапана КП3. Излишки рабочей жидкости отводятся в корпус гидромотора.
При отсутствии сигнала управления люлька гидромотора удерживается пружиной цилиндра управления ЦУ2 на максимальном углу.
Датчик положения ДПЛМ гидромотора отслеживает угол наклона люльки и совместно с гидрораспределителем РЗ3 обеспечивает обратную связь по углу отклонения люльки.
При подаче управляющего электрического сигнала на электромагнит гидрораспределителя РЗ3 и после его согласовании с сигналом получаемым с датчика положения ДПЛМ и датчика скорости ДС1 золотник гидрораспределителя РЗ3 перемещается и поток рабочей жидкости под давлением поступает в пружинную полость цилиндра управления ЦУ2 или в другую полость ЦУ2 соединяя противоположную полость через гидрораспределитель РЗ3 со сливом в корпус гидромотора М1.
Датчики давления ДД1 и ДД2 служат для контроля давления в силовых магистралях насоса и обеспечивают обратную связь по давлению в силовых магистралях насоса Н1.
При перегрузке насоса Н1 срабатывает один из обратно-предохранительных клапанов КОП1 или КОП2 и рабочая жидкость из полости нагнетания перетекает в полость низкого давления.
Датчик давления (см. Рис. 4.) предназначен для контроля давления в силовых магистралях насоса и обеспечивает обратную связь по давлению.
Требования по надежности:
Рабочая температура окружающей среды от минус 50°С до +140 °С;
Ускорение синусоидальной вибрации в диапазоне частот от 1 до 500 Гц до 10 g.
Рис. 4. Датчик давления.
-блок электроэлементов;
-тензопреобразователь;
9-кольцо уплотнительное;
Датчик давления состоит из корпуса 1 внутри которого размещены блок электроэлементов 2 и тензопреобразователь 3. Датчик давления вворачивается в гидравлический прибор или переходник. Выходной сигнал с датчика снимается с контактов разъема.
При подаче масла в штуцер тензопреобразователь 3 формирует электрический сигнал который поступает на блок электроэлементов 2 обрабатывается и выдается на разъем.
5.1. Вывод дифференциальных уравнений насос – гидромотор
Система насос – гидромотор должна соответствовать ряду допущений:
подача насоса пропорциональна углу поворота люльки;
утечки пропорциональны перепаду давления;
расход деформаций жидкости прямо пропорционален скорости жидкости в объемном тракте скорости изменения давления и обратно пропорционален модулю упругости жидкости;
гидродвигатели жестко (без люфтов) соединены с нагрузкой.
Вывод передаточной функции гидропривода базируется на двух основных уравнениях: уравнений расхода и уравнений нагрузки на валу гидромотора.
Имея в виду что скорость гидромотора умноженная на его характерный размер дает Q можно почленённым делением уравнения (1) на получить
Y – потеря скорости из-за утечек;
C - изменение скорости из-за деформации жидкости.
Геометрические подачи насоса и гидромотора определяются:
QН = FНRγzН 2 см3сек (3)
Q = FНRγz 2 см3сек (4)
FН – поперечное сечение поршня;
R – радиус окружности на которой размещаются центры цилиндров;
Н и - угловые скорости насоса и гидромотора.
Приравнивая (3) и (4) получим
X = Хγ где Х = Н γН – коэффициент пропорциональности.
Принимаем Y = сур где су - экспериментально определенный коэффициент.
Имея в виду что по закону Гука
QC = - dVV = V ·dpdt - расход определяемый деформацией рабочей жидкости.
QC = C тогда C = сс dpdt где сс = V
Следовательно уравнение расхода может быть записано
Хγ = dαdt + суp + сс dpdt
α – угол поворота вала гидромотора.
М = р – индикаторный момент развиваемый гидромотором;
МС = F = F dαdt – линеаризованный момент активного сопротивления;
МД = I d 2αdt 2 = (IO + (1i2)IН) d 2αdt 2
IН – момент инерции нагрузки;
i – передаточное отношение от гидромотора к нагрузке.
Следовательно р = I d 2αdt 2 + F dαdt
Получим систему линейных дифференциальных уравнений с постоянными коэффициентами
Хγ = dαdt + суp + сс dpdt
р = I d 2αdt 2 + F dαdt
Заменим производные оператором дифференцирования sddt – оператор Лапласа.
Хγ = I сс s3 α + (I + F сс) s2 α + (Fсу + ) s α
Отношение A(s) и Г(s) называется передаточной функцией гидропривода и имеет вид:
Находя изображение по Лапласу данного дифференциального уравнения решая его в изображениях и беря отношение изображения выходной величины к изображению входной получим выражение передаточной функции насос-гидромотор которое при нулевых начальных условиях совпадает с полученным соотношением α γ.
Используя каноническую форму записи получим
– постоянная времени;
– коэффициент затухания;
кг Х – коэффициент усиления.
6.Описание функциональной схемы системы управления
гидростатической трансмиссии автогрейдера
Гидростатическая трансмиссия предназначена для изменения направления и скорости движения автогрейдера в транспортном и рабочем режимах.
Описание работы гидростатической трансмиссии представлено на функциональной схеме системы управления гидростатической трансмиссией автогрейдера .
На схеме приняты следующие условные обозначения:
ПУ – пульт управления;
ППУ – преобразователь пульта управления;
МУ – модуль управления;
БУН – блок управления насосом;
ПВС – преобразователь входных сигналов;
МУ – механизм управления;
ДД – датчик давления;
ДПЛН – датчик положения люльки насоса;
ДПЛМ – датчик положения люльки мотора;
ИЗ – индикатор загрязненности;
ДС – датчик скорости.
Управление гидростатической трансмиссией (ГСТ) производится от пульта управления (ПУ) размещенного в кабине водителя. В состав ПУ входят: механизм управления преобразователь пульта управления (ППУ) и кнопка включения привода. Включение ГСТ осуществляется при нажатии кнопки ПУ «Привод» при этом загорается индикатор ПУ «Привод». При отклонённой от нейтрального положения рукояти и нажатии кнопки ПУ «Привод» соответствующий индикатор не должен загораться и привод ГСТ не должен включиться. При отклонении рукояти ПУ вперёд-назад при включённом приводе ГСТ формируется сигнал управления ГСТ величина которого пропорциональна углу отклонения рукояти.
Управляющий сигнал с ППУ поступает на преобразователь входных сигналов в блоке управления (БУ).
БУ функционально состоит из модуля питания который включает в себя два блока: блок питания (БП) и блок управления насосом (БУН) и преобразователя входных сигналов (ПВС).
БП формирует напряжения ±15В для питания микросхем в БУН и в ПВС а также формирует питающее напряжение для датчиков положения.
ПВС обеспечивает сбор и обработку сигналов с информационных датчиков формирование сигнала управления насосом и мотором.
БУН обеспечивает режимы управления насосом и мотором в зависимости от управляющих сигналов преобразование сигналов обратных связей от датчика положения люльки насоса и люльки мотора и датчиков положения золотников механизмов управления (МУ) насосом и мотором их суммированием с управляющим сигналом и усиление их по мощности.
6.1.Пульт управления
Пульт Управления предназначен для формирования сигналов управления системы управления гидростатической трансмиссией. Элементы схемы управления расположены в корпусе поз.1. Механизм пульта управления поз.3 установлен на корпусе поз.1 так же блок электроэлементов поз.4 крепится к корпусу поз.1 через прокладку поз.8 на проставке поз.6. Преобразователь пульта управления крепится на крышке поз.2.
Внешние блоки и приборы соединяются с пультом управления через разъём Х1 входящим в состав пульта управления и крепящегося к крышке поз.2.
В состав пульта управления входят механизм управления преобразователь пульта управления и кнопка включения привода.
На рис. 5. представлен общий вид пульта управления.
Рис. 5. Пульт управления.
-блок электроэлементов
Когда рукоятка пульта управления находится в среднем (нейтральном) положении величина выходного напряжения составляет (0±005)В. При отклонении рукоятки пульта управления вперед или назад до упора вал резистора начинает вращаться и напряжение изменяется от (5±05)В до (-5±05)В соответственно.
Характеристики Пульта Управления:
- ПУ представляет собой рукоятку типа “джойстик” с возможностью отклонения вперед и назад;
- Конструкция ПУ предусматривает крепление его в составе изделия;
- Рукоятка ПУ имеет четкую фиксацию нейтрального положения и во всех промежуточных положениях;
- Рукоятка ПУ имеет два направления – вперед и назад;
- Переключение направлений производится перемещением рукоятки в поперечной плоскости;
- Фиксация рукоятки пульта управления осуществляется в любом положении хода;
- Цвет корпуса и рукоятки черный надписи и знаков – светло-серый.
6.2.Механизм пульта управления
Схема механизма пульта управления представлена на рис. 6.
Рис. 6. Механизм пульта управления.
Ось поз. 8 резистора управления поз. 3 жестко связана валом поз. 10 с рычагом управления поз. 2. После регулировки резистора управления поз. 3 корпус резистора через накладки поз. 57 винтами жестко крепится к корпусу поз. 1 механизма пульта управления. При перемещении рычага управлении поз. 2 вперед и назад в соответствии с изменением сопротивления резистора управления поз. 3 плата преобразователя пульта управления формирует выходной сигнал от +5В до -5В. Внутренние полости механизма пульта управления защищены манжетой поз. 4.
6.3. Разработка и описание электрических схем пульта управления
Электрическая схема пульта управления является составной частью системы управления гидростатической трансмиссии . Функционально она включает в себя:
6.3.1. Преобразователь пульта управления.
Преобразователь пульта управления состоит из формирователя питания и двух формирователей сигналов управления один из которых является резервным. Управляющий сигнал с преобразователя пульта управления поступает на преобразователь входных сигналов в блоке управления (БУ).
Рис. 7. Генератор прямоугольных импульсов.
Входное напряжение 27В поступает на предварительный стабилизатор напряжения. Это напряжение является питающим для мостовой схемы управление которой осуществляется с задающего генератора DA 1. На выходе мостовой схемы формируется переменное прямоугольное напряжение которое является питающим для резистора механизма управления. Номиналы резисторов R4 R5 R6 выбираем одинаковыми и равными 10 кОм С3=001 мкФ.
Рис. 8. Мостовая схема.
Мостовая схема предназначена для усиления сигнала поступающего с генератора до уровня ±15В импульсов прямоугольной формы необходимого для питания системы. Усиление производится по току с помощью применения транзисторов VT2 VT3. Номиналы резисторов выбираем равными R7=R8=33 кОм R9=R10=360 кОм R11=R12=10 кОм.
Инвертирующий усилитель состоит из операционного усилителя DA 2.2 резисторов R24 R25 R26 и конденсатора С8. На операционный усилитель поступает сигнал от резистора механизма управления. Номиналы резисторов R8 R9 R10 R18 принимаем равными 47 кОм R2 -10кОм конденсатор С2 имеет емкость 0022 мкФ.
6.3.2.Кнопка включения привода.
Перед включением гидростатической трансмиссии необходимо запустить приводной двигатель и включить электропитание гидростатической трансмиссии.
Для включения гидростатической трансмиссии на пульте управления необходимо установить рукоять управления в нейтральное положение а затем нажать кнопку «Привод» при этом должен загореться индикатор «Привод».
6.3.Блок управления.
Блок управления состоит из модуля питания (блок питания блок управления насосом) и преобразователя входных сигналов.
Блок управления предназначен:
- для управления режимами работы насоса и мотора;
- выработки вторичных питающих напряжений для запитки электронных схем и информационных датчиков;
- обработки управляющего сигнала с пульта управления сигналов обратной связи и информационных датчиков.
На рис.10. представлен общий вид блока управления.
Рис. 10. Блок управления.
-блок управления насосом
-преобразователь входных сигналов
-держатель вставки плавкой
А2-преобразователь входного сигнала;
А3-блок управления насосом;
Х1 Х4 Х5 – КПА – разъемы.
Элементы схемы управления расположены на печатных платах поз.4 5 6. Внешние блоки и приборы соединяются с блоком управления через разъёмы Х1 Х4 Х5 – КПА закрепленные на основании поз.7. контрольно-проверочная аппаратура подключается к блоку через розетку Х5 – КПА расположенную на основании поз.7. Органы контроля и регулировки поз.10 11 индикаторы поз.2 3 находятся на основании поз.7 под крышкой.
Эксплуатационные регулировочные резисторы имеют следующее назначение:
РЕГ.М – регулировка максимальной частоты вращения вала мотора;
РЕГ.Н – регулировка максимальной частоты вращения вала насоса;
БАЛ.М – регулировка начального положения люльки мотора;
БАЛ.Н – регулировка начального положения люльки насоса.
Работа блока управления заключается в следующем:
Питающее напряжение борт сети В поступающее на блок управления через разъём Х3 и блок предохранительный подаётся на блок питания А1 который формирует напряжение ±15В к пульту управления через разъём Х2 к информационным датчикам и к электромагнитам механизмов управления насоса и мотора через разъём Х1.
Блок предохранительный снабжен информационным индикатором который загорается при перегорании предохранителя.
Включение блока питания осуществляется по команде от пульта управления нажатием кнопки «Привод» и загоранием соответствующего индикатора. При повторном нажатии кнопки «Привод» блок питания выключается и индикатор гаснет.
Блок управления насосаи преобразователь входного сигнала А2 обеспечивают задание требуемых режимов работы насоса и мотора в соответствии с командой управления от пульта управления.
В преобразователе входного сигнала осуществляется обработка и суммирование сигналов датчиков давления с сигналом управления идущем с пульта управления.
В блоке управления насоса откорректированный сигнал управления поступивший с преобразователя входного сигнала А2 складывается с сигналами поступившими с датчиков положения механизмов управления и датчиков положения люльки насоса и мотора. После всех преобразований сигнал управления поступает на механизмы управления с разъёма Х1.
Для поиска неисправностей контрольные точки из схемы блока управления выведены на разъём Х5 – КПА.
6.3.1. Разработка и описание электрических схем
В состав блока управления входят: модуль питания (блок питания и блок управления насосом) и преобразователь входных сигналов. При разработке электрических плат входящих в состав блока управления была применена технология поверхностного монтажа которая предполагает использование ЧИП-компонентов. Это позволяет значительно снизить трудоемкость сборки узлов снизить габариты и вес аппаратуры увеличить надежность быстродействие и качество аппаратуры. ЧИП-элементы имеют небольшие габариты крепятся непосредственно на дорожках не имея при этом выводов на обратную сторону платы поэтому монтаж их может осуществляться и с двух сторон.
Блок питания служит для преобразования входного сигнала +27В в напряжение выхода ±12 В. Сигнал +27В подается на преобразователь постоянного тока DA 6.1 который формирует стабилизированное напряжение питания ±12 В.
Рис .11 .Блок питания
Блок питания формирует напряжения для питания микросхем в блоке управления насосом и в преобразователе входных сигналов а также формирует питающее напряжение для датчиков положения.
Блок управления насосом состоит из следующих основных блоков:
Блок управления насосом обеспечивает режимы управления насосом и мотором в зависимости от управляющих сигналов преобразование сигналов обратных связей от датчика положения люльки насоса и люльки мотора и датчиков положения золотников механизмов управления насосом и мотором их суммирование с управляющим сигналом и усиление их по мощности.
Сигнал датчика угла 6.1. поступает на операционный усилитель DA 1.1 через резисторы R6 (на инвертирующий вход) и R7 (на неинвертирующий вход). Резистор R17 в цепи обратной связи определяет коэффициент усиления по напряжению. Номиналы резисторов R5 R6 R7 R17 выбираем одинаковыми и равными 47 кОм. Напряжение инвертирующего входа операционного усилителя определяется выражением: Uи = Uвх* R7 R5 = Uвх; напряжение неинвертирующего входа определяется выражением: Uи = Uвх* (R7 R5+1) = 2*Uвх. Отсюда коэффициент усиления по напряжению на инвертирующем входе равен 1 а на неинвертирующем – 2. К неинвертирующему входу операционного усилителя DA 1.1 подключен ключ DA 2.1. На вход ключа подается положительная составляющая прямоугольного сигнала питания датчиков. Когда вход ключа отличен от нуля и на операционный усилитель приходит положительный сигнал ключ SW размыкается и на входы операционного усилителя DA 1.1 подается одинаковое напряжение. Исходя из этого на выходе операционного усилителя появляется положительный сигнал равный Uвх (так как сигналы датчика угла и входа ключа SW находятся в одной фазе). Когда же на вход приходит отрицательный сигнал ключ коммутирует неинвертирующий вход с корпусом. В результате этого операционный усилитель работает как инвертор с единичным коэффициентом усиления. Когда сигнал датчика угла меняет фазу операционный усилитель работает следующим образом. На вход операционного усилителя приходит отрицательный сигнал датчика угла а на ключ SW – положительный (то есть ключ размыкается). Исходя из этого получаем на выходе операционного усилителя напряжение Uвх. Когда на DA 1.1 поступает положительный сигнал от датчика угла ключ SW коммутирует неинвертирующий сигнал с корпусом и операционный усилитель работает как инвертор с единичным коэффициентом усиления. На выход операционного усилителя поступает сигнал с фазочувствительного выпрямителя датчика угла. Емкость конденсатор С1 выбираем равной 0022 мкФ. Резистор R1 равным 10 кОм. Сигнал поступает на суммирующий усилитель.
Рис. 12. Инвертирующий усилитель.
Инвертирующий усилитель состоит из операционного усилителя DA 1.2 резисторов R2 R8 R9 R10 R18 конденсатора С2 и ключа DA 2.2. Работает этот блок аналогично предыдущему. На операционный усилитель поступает сигнал от датчика положения люльки (ДПЛН) и сигнал с фазочувствительного выпрямителя ДПЛН. Номиналы резисторов R8 R9 R10 R18 принимаем равными 47 кОм R2 -10кОм конденсатор С2 имеет емкость 0022 мкФ. Сигнал поступает на суммирующий усилитель.
Инвертирующие усилители на которые поступают сигналы с датчика угла 6.2. и датчика положения люльки мотора (ДПЛМ) работают аналогично усилителю изображенному на рис. 12.
На операционный усилитель поступают сигналы: от инвертирующего усилителя DA 1.1 (сигнал ДУ 6.1.) через резистор R24 и от инвертирующего усилителя DA 1.2 (сигнал ДПЛН) через резистор R25. Блок осуществляет суммирование входных сигналов и выдает усиленный сигнал на компаратор DA 1.4. Конденсатор С6 является фильтром благодаря которому выходное напряжение изменяется более плавно. Номиналы элементов принимаем равнымиR25= R37=10 кОм R36=470 кОм С6=2200 пкФ.
Рис. 14. Генератор треугольного сигнала.
Здесь генератор сигналов треугольной формы DA 1.1 – это классический релаксационный RC-генератор. Работает он следующим образом: примем что при начальном включении питания выходной сигнал операционного усилителя выходит на положительное насыщение. Конденсатор начинает заряжаться до напряжения +15В. Когда напряжение на конденсаторе достигнет половины напряжения источника питания операционный усилитель переключается в состояние отрицательного насыщения и конденсатор начинает разряжаться до напряжения -15В с той же самой постоянной времени. Этот цикл повторяется бесконечно и сигналы получаются хорошей треугольной формы. Номиналы элементов принимаем равными: R42=R52=47 кОм R51= 220 кОм С9=001 мкФ. С инвертирующего входа треугольный сигнал подается через делитель напряжения R41-R48 на неинвертирующий вход компаратора.
Рис. 15. Компаратор.
Состоит из инвертирующего усилителя DA 1.4. На инвертирующий вход операционного усилителя через делитель напряжения R40-R47 номиналы которых равны 300 кОм и 150 кОм соответственно подается сигнал от блока сумматор. На неинвертирующем входе – треугольный сигнал от генератора. Компаратор сравнивает напряжения на входах и выдает инвертированный сигнал в виде прямоугольных импульсов длительность которых зависит от величины входного напряжения поступающего от сумматора. Чем больше величина линейно изменяющегося напряжения тем короче длительность импульсов выходного прямоугольного сигнала. Сигнал с компаратора через делитель напряжения R53-R59 поступает на полевой транзистор VP1.
Рис. 16. Генератор прямоугольных импульсов.
Здесь генератор сигналов прямоугольной формы DA 5.2 – классический релаксационный RC-генератор. Работает он следующим образом: примем что при начальном включении питания выходной сигнал операционного усилителя выходит на положительное насыщение. Конденсатор начинает заряжаться до напряжения +15В. Когда напряжение на конденсаторе достигнет половины напряжения источника питания операционный усилитель переключается в состояние отрицательного насыщения и конденсатор начинает разряжаться до напряжения -15В с той же самой постоянной времени. Этот цикл повторяется бесконечно получаются сигналы хорошей треугольной формы. Номиналы элементов выбираем равными: R32=R34=47 кОм R33=220 кОм С10=001 мкФ. С выхода операционного усилителя прямоугольный сигнал подается на мостовую схему.
Рис. 17. Мостовая схема.
Мостовая схема предназначена для усиления сигнала поступающего с генератора до уровня ±15В импульсов прямоугольной формы необходимого для питания системы. Усиление производится по току с помощью применения транзисторов VT2 VT3 VT4 VT5. Номиналы резисторов выбираем равными R45=R46=51 кОм R55=R56=470 кОм R57=R58=100 кОм. Прямоугольный сигнал ±15В служит для запитки датчиков системы.
Рис.1 8. Формирователь сигнала.
Через диод VD1 включенного в цепь таким образом что через него проходит только положительная составляющая прямоугольного сигнала питания датчиков системы происходит формирование управляющего сигнала.
Блок преобразователь входных сигналов состоит из следующих основных блоков:
Преобразователь входных сигналов обеспечивает сбор и обработку сигналов с информационных датчиков формирование сигнала управления насосом и мотором.
Инвертирующий усилитель состоит из операционного усилителя DA 1.1 резисторов R77 R78 R88 R92 и конденсаторов С19 и С20. На операционный усилитель поступает сигнал управления. Номиналы резисторов R77 R78 R88 R92 принимаем равными 10 кОм конденсаторы С19С20 имеют емкость 15 мкФ.
Блок состоит из микросхемы КР 590 DA 2.1. Работает этот блок следующим образом. Положительный сигнал поступает на ключ SW с которого сигнал поступает на информационные датчики.
Рис. 21. Компаратор.
Состоит из инвертирующего усилителя DA 14.3. На инвертирующий вход операционного усилителя через делитель напряжения подается сигнал от блока сумматор. На неинвертирующем входе – треугольный сигнал от генератора. Компаратор сравнивает напряжения на входах и выдает инвертированный сигнал в виде прямоугольных импульсов длительность которых зависит от величины входного напряжения поступающего от сумматора. Чем больше величина линейно изменяющегося напряжения тем короче длительность импульсов выходного прямоугольного сигнала. Номиналы резисторов выбираем равными R109=R110=R115=R116=47кОм.
На операционный усилитель поступают сигналы: от инвертирующего усилителя DA 15.3 через резистор R159 и от инвертирующего усилителя DA 14.3 через резистор R160. Блок осуществляет суммирование входных сигналов. Номиналы элементов принимаем равными R159=82 кОм R160=51 кОм R161=510 кОм R162=24 кОм
Остальные элементы электрической схемы блока управления работают аналогично выше рассмотренным.
7. Расчет надежности
При анализе надёжности сложных систем их разбивают на отдельные элементы с тем чтобы вначале рассмотреть параметры и характеристики этих элементов а затем оценить работоспособность всей системы в целом.
Каждый элемент системы выделяется в зависимости от поставленной задачи и может состоять из деталей и сборочных единиц. При исследовании надёжности системы элемент не разделяется на составные части а показатели безотказности и долговечности работы каждого элемента можно производить независимо от других элементов и частей схемы.
Каждый i-тый элемент схемы характеризуется значением Pi(t)— вероятностью его безотказной работы в течение заданного периода времени.
Вероятность безотказной работы системы при последовательном соединении элементов:
Если известны интенсивность отказов и наработка до отказа элементов системы подчиняющиеся экспоненциальному закону распределения то для определения вероятности безотказной работы системы состоящей из n элементов можно воспользоваться формулой:
ni — количество равнонадёжных элементов одного типа шт.
li интенсивность отказов i-ого элемента 1ч.
t - время наработки на отказ ч.
При расчете показателей безотказности принимаются следующие допущения:
- отказы элементов статически независимы;
- функция вероятности безотказной работы подчиняется экспоненциальному закону.
Данные для расчета приведены в таблице
Общая интенсивность отказов
Модуль питания МПВ10ВВ
Вставка плавкая ВП1-1 5А
Суммарная интенсивность отказов элементов:
λ = ni × λi =(014+006+10+03+04+04+36+05+024+022+006+03+006 +004+001+012+016+012+008+0008+08+012+008+004+0006+003+003+01 +003+003+02+02+04+04+001+001+003+01+01+01+01+004+004+003) =10604 -1
Средняя наработка на отказ:
Т0 = 1 λ = 1 10604×10-6 = 94304 ч.
Вероятность безотказной работы за 1000 часов равна:
Р (1000) = е(λ *1000) = 0995
Из приведенного расчета надежности следует что пульт и блок управления за время работы 1000 часов в 99% случаев остаются работоспособны
Таблица 1.doc
Песок супесь растительный грунт торф
Ручной (лопаты) машинами
Легкий суглинок лёсс гравий песок со щебнем супесь со строймусором
Ручной (лопаты кирки) машинами
Жирная глина тяжелый суглинок гравий крупный растительная земля с корнями суглинок со щебнем или галькой
Ручной (лопаты кирки ломы) машинами
Тяжелая глина жирная глина со щебнем сланцевая глина
Ручной (лопаты кирки ломы клинья и молоты) машинами
Плотный отвердевший лёссдресва меловые породысланцы туф известняк иракушечник
Ручной (ломы и кирки отбойные молотки) взрывным способом
Граниты известняки песчаники базальты диабазы конгломерат с галькой
ГОСТ 22-829-74 Гидропривод объемный. Распределители секционные золотниковые с ручным управлением на номинальное давление 160 кгссм.кв. (16 МПа) -Действующий
Соответствие гидравлических масел по настоящему стандарту принятым в нормативно-технической документации
Обозначение масла по настоящему стандарту
Принятое обозначение масла
Нормативно-техническая документация
Список литературы .doc
Алексеева Т. В. Галдин Н. С. Шерман Э. Б. - Гидравлические машины и гидропривод мобильных машин: Учеб. Пособие. – Новосибирск: - Изд-во Новосиб. Ун-та 1994. – 212 с. – ISBN 5-7615-0228-3.
Васильченко В.А. Гидравлическое оборудование мобильных машин: Справочник- М.: Машиностроение 1983.- 301 с.
Обработка металлов резанием. Справочник технолога.Изд.3-е
под.ред. Г.А.Монахова.М.:Машиностроение1974.
Т. М. Башта И. З. Зайченко В. В. Ермаков Е. М. Хаймович. “Объемные гидравлические приводы”. М.: Машиностроение. 1969г.
В. А. Хохлов В. Н. Прокофьев Н. А. Борисова В. И. Гусаков В. М. Чуркин. “Электрогидравлические следящие системы”. М.: Машиностроение. 1971г.
К. Л. Навроцкий. “Теория и проектирование гидро- и пневмоприводов”. М.: Машиностроение. 1991г.
В. Н. Прокофьев. “Машиностроительный гидропривод”. М.: Машиностроение. 1978г.
А. П. Пехальский И. А. Пехальский. “Устройство автомобилей”. М.: Академия. 2005г.
А. М. Гуревич А. К. Болотов В. И. Судницын. “Конструкция тракторов и автомобилей”. М.: Агропромиздат. 1989г.
Ю. М. Соломенцев. “Методы и средства обеспечения безопасности труда в машиностроении”. М.: Высшая школа. 2000г.
Л. П. Боброва-Голикова. “Эргономика и безопасность труда”. М.: Машиностроение. 1985г.
Гоберман Л. А. Теория конструкция и расчёт строительных и дорожных машин.- Москва «Машиностроение» 1979г.
Ранеев А. В. Устройство и эксплуатация дорожно-строительных машин.-Москва 2000 г.
Добронравов С. С. Строительные машины и основы автоматизации. Москва Высшая школа 2001г.
Мелкозеров П.С. Энергетический расчет систем автоматического управления и следящих приводов. - М.: Энергия 1968. – 304 с
Справочник технолога - машиностроителя. В 2-х т.:под ред. А.Г.Косиловой и Р.К.Мещерякова Название: Справочник технолога-машиностроителя. В 2-х т.М.: Машиностроение .- 1986
Косилова А. Г. Мещеряков Р. К. Калинин М. А.Точность обработки заготовки и припуски в машиностроении. Справочник технолога . М.: Машиностроение.- 1976
Малов А.Н. Справочник технолога - машиностроителя. В 2-х т. М.: Машиностроение.- 1972
Барановский Ю.В Режимы резания металлов. Справочник.М.: Машиностроение-1972.
А.А. Панов В.В. Аникин и др.Название: Обработка металлов резанием: Справочник технолога. М.:Машиностроение 2004
ГОСТ 2.704-76. ЕСКД. Правила выполнения гидравлических и пневматиче
ских схем. М.: Изд-во стандартов 1982. 17 с.
ГОСТ 2.781-68. ЕСКД. Обозначения условные графические
ГОСТ 2.780-68. ЕСКД. Обозначения условные графические. Элементы гидравлических и пневматических сетей. М.: Изд-во стандартов 1984. 5 с.
ГОСТ 23000-78. Система человек-машина. Пульты управления. Общие эргономические требования.
ГОСТ 21753-76. Система человек-машина. Рычаги управления. Общие эргономические требования.
Иванов В.А. Фалдин Н.В. Теория оптимальных систем автоматического управления. – М.: Наука. Главная редакция физико-математической литературы 1981. – 336 с.
Справочник по полупроводниковым диодам транзисторам и интегральным схемам Под ред. Н.Н. Горюнова. – М.: Энергия 1979. – 831 с.
Резисторы: справочник В.В. Дубровский Д.М. Иванов Н.Я. Пратусевич и др. Под общ. ред. И.И. Четвертакова. – М.: Радио и связь 1987. – 263 с.
Полупроводниковые приборы: Учебник для вузов Под ред. В.А. Лабунцова. – М.: Энергоатомиздат 1990. – 576 с.
Заключение.doc
проведен тяговый расчет автогрейдера расчет гидроаппаратуры трансмиссии.
Разработана и описана функциональная схема системы управления трансмиссией а также схемы электрических соединений блока и пульта управления. Провен расчет надежности электронных схем управления изделия. В технологической части рассмотрен вопрос контроля и проверки основных характеристик гидростатической трансмиссией автогрейдера. В экономической части приведен расчет калькуляции себестоимости и цены изделия.
Разработанная гиростатическая трансмиссия позволяет увеличить срок эксплуатации оборудования значительно упрощает работу водителя – оператора.
Приложение.doc
Конденсатор К10-17а-М1500-0022 мкФ ±10%-В ОЖО.460.172.ТУ
Конденсатор К73-11-М1500-2200 пФ ±10% АДПК.673633.013ТУ
Конденсатор К13-11-63В-22 мкФ ±10% АДПК.673633.013ТУ
Конденсатор К10-17а-М1500-2200 пФ ±10%-В ОЖО.460.172.ТУ
Конденсатор К10-17а-М1500-001 пФ ±10%-В ОЖО.460.172.ТУ
Конденсатор К10-17а-Н90-022 мкФ-В ОЖО.460.172.ТУ
Конденсатор К50-29-63В-100 мкФ-В ОЖО.464.181.ТУ
Конденсатор К50-29-29В-22 мкФ-В ОЖО.464.181.ТУ
Конденсатор К10-17а-Н90-15 мкФ-В ОЖО.460.172.ТУ
Конденсатор К10-17а-Н90-1 мкФ-В ОЖО.460.172.ТУ
Конденсатор К73-11-63В-1 мкФ ±10% АДПК.673633.013ТУ
Микросхема КМ544УД7 АДБК.431130.555ТУ
Микросхема КР590КН13 бКО.348.209-10ТУ
Модуль питания VDG10DD ТУ 6589-014-40039437-99
Микросхема К561ТЛ1 бКО.348.457-16ТУ
Микросхема К561ТМ2 бКО.348.457-11ТУ
Резистор С2-33Н-0125 -10кОм±5%-А ОЖО.467.173ТУ.
Резистор С2-33Н-0125 - 47кОм±5%-А ОЖО.467.173ТУ.
Резистор С2-33Н-0125 -240кОм±5%-А ОЖО.467.173ТУ.
Резистор С2-33Н-0125 -27кОм±5%-А ОЖО.467.173ТУ.
Резистор С2-33Н-0125 -36кОм±5%-А ОЖО.467.173ТУ.
Резистор С2-33Н-0125 -20кОм±5%-А ОЖО.467.173ТУ.
Резистор С2-33Н-0125 -47кОм±5%-А ОЖО.467.173ТУ.
Резистор С2-33Н-0125 -220кОм±5%-А ОЖО.467.173ТУ.
Резистор С2-33Н-0125 -51кОм±5%-А ОЖО.467.173ТУ.
Резистор С2-33Н-0125 -470кОм±5%-А ОЖО.467.173ТУ.
Резистор С2-33Н-0125 -300кОм±5%-А ОЖО.467.173ТУ.
Резистор С2-33Н-0125 -150кОм±5%-А ОЖО.467.173ТУ.
Резистор С2-33Н-0125 -2кОм±5%-А ОЖО.467.173ТУ.
Резистор С2-33Н-0125 -100кОм±5%-А ОЖО.467.173ТУ.
Резистор С2-33Н-0125 -1кОм±5%-А ОЖО.467.173ТУ.
Резистор С2-33Н-025 -3кОм±5%-А ОЖО.467.173ТУ.
Резистор С2-33Н-0125 -30кОм±5%-А ОЖО.467.173ТУ.
Резистор С2-33Н-0125 -510кОм±5%-А ОЖО.467.173ТУ.
Резистор С2-33Н-025 -2кОм±5%-А ОЖО.467.173ТУ.
Резистор С2-33Н-0125 -22кОм±5%-А ОЖО.467.173ТУ.
Резистор С2-33Н-0125 -3кОм±5%-А ОЖО.467.173ТУ.
Резистор С2-33Н-0125 -680кОм±5%-А ОЖО.467.173ТУ.
Резистор С2-33Н-0125 -24кОм±5%-А ОЖО.467.173ТУ.
Резистор С2-33Н-0125 -3МОм±5%-А ОЖО.467.173ТУ.
Резистор С2-33Н-0125 -43кОм±5%-А ОЖО.467.173ТУ.
Резистор С2-33Н-0125 -715кОм±5%-А ОЖО.467.173ТУ.
Резистор С2-33Н-0125 -270кОм±5%-А ОЖО.467.173ТУ.
Резистор С2-33Н-0125 -18кОм±5%-А ОЖО.467.173ТУ.
Резистор С2-33Н-0125 -12кОм±5%-А ОЖО.467.173ТУ.
Резистор С2-33Н-0125 -91кОм±5%-А ОЖО.467.173ТУ.
Резистор С2-33Н-0125 -82кОм±5%-А ОЖО.467.173ТУ.
Резистор С2-33Н-0125 -221кОм±5%-А ОЖО.467.173ТУ.
Резистор С2-33Н-0125 -681кОм±5%-А ОЖО.467.173ТУ.
Резистор С2-33Н-0125 -360кОм±5%-А ОЖО.467.173ТУ.
Резистор С2-33Н-0125 -169кОм±5%-А ОЖО.467.173ТУ.
Диод КД510А ТТ3.362.100ТУ
Диод КД257А АДБК.432121.034ТУ
Диод КД247А аАО.336.838ТУ
Диод КД213А аАО.336.176ТУ
Стабилитрон КС156А СМ3.362.812ТУ
Стабилитрон КС133А СМ3.362.812ТУ
Транзистор КП723Г АДБК.432140.415ТУ
Транзистор КТ3117А аАО.336.262ТУ
Транзистор КТ313А аАО.336.131ТУ
Транзистор КТ816Г аАО.336.186ТУ
Транзистор КТ817Г аАО.336.186ТУ
Вилка ГРПМШ-1-45ШУ2 НЩ0.364.006ТУ
Перечень элементов к схеме электрической принципиальной пульта управления.
Конденсатор К10-17в-Н90-047 мкФ -В ОЖО.460.107.ТУ
Конденсатор К10-17в-М1500-001 мкФ ±10% ОЖО.460.172.ТУ
Конденсатор К53-46-32В-68 мкФ -В АДПК.673546.002.ТУ
Микросхема КМ544УД2 бКО.348.257ТУ
Резистор Р1-12-025 -200Ом±5%-А ОЖО.467.169ТУ.
Резистор Р1-12-025 -360Ом±5%-А ОЖО.467.169ТУ.
Резистор Р1-12-025 -1кОм±5%-А ОЖО.467.169ТУ.
Резистор Р1-12-025 -10кОм±5%-А ОЖО.467.169ТУ.
Резистор Р1-12-025 -33кОм±5%-А ОЖО.467.169ТУ.
Резистор Р1-12-025 -10Ом±5%-А ОЖО.467.169ТУ.
Резистор Р1-12-025 -47кОм±5%-А ОЖО.467.169ТУ.
Резистор СП3-19Б-05 -22кОм±10%-А ОЖО.467.169ТУ.
Резистор Р1-12-025 -2МОм±5%-А ОЖО.467.169ТУ.
Резистор Р1-12-025 -24кОм±5%-А ОЖО.467.169ТУ.
Резистор Р1-12-025 -270кОм±5%-А ОЖО.467.169ТУ.
Резистор Р1-12-025 -47Ом±5%-А ОЖО.467.169ТУ.
Резистор Р1-12-025 -24Ом±5%-А ОЖО.467.169ТУ.
Набор диодов КД803АС9 АДБК.432120.644ТУ
Стабилитрон Д818Д СМ3.362.045ТУ
Набор диодов КД707АС9 АДБК.432120.644ТУ
Стабилитрон 2С512А1 СМ3.362.823ТУ
Введение.doc
Целью данного дипломного проекта является разработка автогрейдера с гидростатической трансмиссии . Трансмиссия предназначена для передачи крутящего момента с коленчатого вала двигателя на ведущие колеса а также для изменения величины этого момента. Кроме того трансмиссия обеспечивает движение автомобиля задним ходом. Гидравлическая трансмиссия в качестве основного элемента имеет гидравлическую передачу.
Гидравлические передачи делят на гидростатические (или объемные) и гидродинамические. Гидравлическая трансмиссия с гидростатической передачей состоит из насоса распределительного устройства гидролиний и моторов расположенных на ведущих колесах. Главным достоинством гидростатической трансмиссии является возможность плавного изменения передаточного отношения в широком диапазоне частот вращения что позволяет гораздо лучше использовать крутящий момент двигателя. Большим достоинством гидростатической трансмиссии является простота реверсирования которое обеспечивается гидравлически изменением потока рабочей жидкости. Это позволяет обеспечить исключительную маневренность автомобиля. В дипломной проекте разрабатывается регулируемая гидростатическая трансмиссия. Это позволит дополнительно увеличить точность маневрирования и скорости движения. Разрабатываемая система является универсальной. Даёт возможность оснащать другую дорожную технику улучшая их характеристики.
07.Преобразователь входных сигналов 1л..dwg

Преобразователь входных сигналов
Схема электрическая принципиальная
10.02.НС.dwg

Теплообменный аппарат
Предел измер.(0-100) C
установка насосная МКРН.063234.015
Гидромотор БС2.957.000001
Манометр ГОСТ 2405-88
Гидромотор испытуемый
N>1.5кВт n=1500обмин
Насос МКРН.063234.001 или
Балансирный динамометр
Клапан для отбора проб ОСТ 3-3270-85
Гидроклапан предохранительный Г54-22
Термометр любого типа
Гидропривод МКРН.303364.004
Клапан МКРН.306577.016
Клапан предохранительный МКРН.306577.046
Клапан редукционный МКРН.306577.048
Фильтр МКРН.061146.006
Установка насосная МКРН.
Гидромотор МКРН.382213.005
Распределитель золотниковый
Клапан предохранительный МКРН.306577.005-01
Аппарат теплообменный
Принятые условные обозначения: ДД - датчик давления; ДС - датчик скорости; ДТ - датчик температуры; ДУ - датчик угла; ЦУ - цилиндр управления.
Клапан предохранительный
Клапан предохранительный
Блок прокачки МКРН.306569.015
Гидрораспределитель МКРН.306154.021
Клапан предохранительный МКРН.306577.078
Датчик давления МКРН.406233.005-01
Индикатор загрязненности МКРН.406239.008
Фильтроэлемент 340.099А
Клапан предохранительный МКРН.306577.070
Фильтр МКРН.061146.035
Датчик положения МКРН.402312.011
Датчик давления МКРН.406233.009-04
Клапан заправочный ПБ5.890.046-1
Гидромотор МКРН.382212.001
Гидромотор аксиально-поршневой
Гидрораспределитель МКРН.306155.003
Насос героторный МКРН.063621.009
Гидрораспределитель МКРН.306154.191
Клапан обратно-предохранительный МКРН.306577.018
Насос МКРН.063234.019
Принятые условные обозначения: ДП - датчик положения; ДЗ - датчик загрязненности; ДТ - датчик температуры; ДС - датчик скорости; ЦУ - цилиндр управления.
Схема гидравлическая принципиальная
- блок цилиндров; 2 - поршень; 3 - пята; 4 - корпус; 5 - вал; 6
- подшипник; 8 - пружина; 9
- распределитель латунный; 11 - распределитель стальной; 12 - силовая крышка; 13 - штифт; 14 - люлька;
- сепаратор; 16 - подшипник; 17 - сервоклапан; 18
- гидрораспределитель; 20 - героторный насос; 21 - корпус;
- валик; 23 - фильтр; 24
- датчик давления; 25 - датчик загрязненности; 26 - датчик положения;
- предохранительный клапан; 29 - пробка; 31 - уплотнительный узел; 32 - фланец; 33 - стопорное кольцо;
- уплотнительное кольцо; 35 - рычаг; 36 - палец; 37 - цилиндр управления; 39 - рычаг.
05.Блок управления Сбор.чер.А1-1л.dwg

клеем герметиком силиконовым "Полисил" оксимный ТУ 2252-001-512214350-00.
периметру. Концы шнура соединить
ВК-9 по ОСТ 4Г 0.029.204.
Крышку поз.34 подвязать к лепестку поз.107 нитью поз.155.
Компаунд ЭЗК-6 ОСТ 107.460007.007-92
Перед установкой лепестка поз.107 контактную поверхность на
основании зачистить до металлического блеска диаметром 10мм.
ГОСТ 9640-85 на выступающую резьбовую часть с переходом на торец гайки.
Гайку держателя поз.141 стопорить нанесением эмали ЭП-51
Взам. инв.N° Инв.N° дубл. и дата
не более 200 В. Меры защиты по ОСТ 11.073.062-2001.
Остальные ТТ по БСО.005.004 ТУ.
настройки блока в составе изделия.
ставить на герметике ВГО-1 ТУ 38.303-04-04-90.
Винты крепления вилок поз.134 137
Лист регистрации изменений
Номера листов ( страниц )
Инв.N°подл. Взаим.инв.N° Инв.N дубл. и дата
Надписи на блоках поз.7
Справ. N° Перв. примен.
Электромонтаж производить в соответствии с МКРН.468364.094 МЭ.
Стопорить по ОСТ 4Г О.019.200: винты поз.69
Планку фирменную поз.56
втулки поз.26 и шарниры поз.21
Приклеить клеем 88-НП ТУ 38 105540-85 или клеем 88-СА ТУ 38.1051760-89:
шнур поз.52 к основанию поз.35 по всему
методом вулканизации.
ставить на клее ВК-9 по ОСТ 4Г О.029.204. Выступание клея над поверхностью Ж
винты розеток поз.149
Пломбировать по ГОСТ 18680-73. Пломбу поз.109 ставить после
-Пр3 РД107.26.001-90. Допускается маркировать эмалью МКЭ черной по
Надписи маркировать эмалью ЭП-572 черной ТУ 6-10-1539-76
кгссм ) в течение1-2 мин. Утечка воздуха не допускается.
Элементы на блоках ЭРИ не показаны.
Испытать на герметичность воздухом под избыточным давлением
- транспортировочные.
Давление подавать через вилку Х1.
*Размеры для справок.
Допустимое значение потенциала статического электричества
Электромонтаж производить в соответствии с МЭ.
клеем герметиком силиконовым Полисил" оксимный ТУ 2252-001-512214350-00.
09.02.ГМ.dwg

Теплообменный аппарат
Предел измер.(0-100) C
установка насосная МКРН.063234.015
Гидромотор БС2.957.000001
Манометр ГОСТ 2405-88
Гидромотор испытуемый
N>1.5кВт n=1500обмин
Насос МКРН.063234.001 или
Балансирный динамометр
Клапан для отбора проб ОСТ 3-3270-85
Гидроклапан предохранительный Г54-22
Термометр любого типа
Гидропривод МКРН.303364.004
Клапан МКРН.306577.016
Клапан предохранительный МКРН.306577.046
Клапан редукционный МКРН.306577.048
Фильтр МКРН.061146.006
Установка насосная МКРН.
Гидромотор МКРН.382213.005
Распределитель золотниковый
Клапан предохранительный МКРН.306577.005-01
Аппарат теплообменный
Принятые условные обозначения: ДД - датчик давления; ДС - датчик скорости; ДТ - датчик температуры; ДУ - датчик угла; ЦУ - цилиндр управления.
Клапан предохранительный
Клапан предохранительный
Блок прокачки МКРН.306569.015
Гидрораспределитель МКРН.306154.021
Клапан предохранительный МКРН.306577.078
Датчик давления МКРН.406233.005-01
Индикатор загрязненности МКРН.406239.008
Фильтроэлемент 340.099А
Клапан предохранительный МКРН.306577.070
Фильтр МКРН.061146.035
Датчик положения МКРН.402312.011
Датчик давления МКРН.406233.009-04
Клапан заправочный ПБ5.890.046-1
Гидромотор МКРН.382212.001
Гидромотор аксиально-поршневой
Гидрораспределитель МКРН.306155.003
Насос героторный МКРН.063621.009
Гидрораспределитель МКРН.306154.191
Клапан обратно-предохранительный МКРН.306577.018
Насос МКРН.063234.019
Принятые условные обозначения: ДП - датчик положения; ДЗ - датчик загрязненности; ДТ - датчик температуры; ДС - датчик скорости; ЦУ - цилиндр управления.
Схема гидравлическая принципиальная
- палец; 28 - цилиндр управления; 31 - рычаг.
- фланец; 25 - стопорное кольцо; 26 - кольцо уплотнительное;
- пробка; 23 - узел уплотнительный;
- датчик положения; 20 - датчик скорости; 21 - клапан заправочный;
- сепаратор; 17 - гидрораспределитель; 18 - блок прокачки;
- силовая крышка; 13 - штифт; 14 - люлька; 15 - подшипник;
- распределитель латунный; 11 - распределитель стальной;
- подшипник; 8 - пружина; 9
- блок цилиндров; 2 - поршень; 3 - пята; 4 - корпус;
10.Крепление гидронасоса.dwg

с конструктивной разработкой автогрейдера с
гидростатической трансмиссией
*Размер для справок.
Неуказанные предельные отклонения размеров по
11.Технология общий.dwg

Фрезерная 050 операция
ДП-МГОУ-190205-05-02-ЧТ
Механизация устройства основания автодорог с конструктивной разботкой автогрейдера с гиростатической трансмиссией
Фрезерование 060 пазов
02.Полотно дороги.dwg

лающего слоя с разравни-
ванием автогрейдером
Устройство щебенчетого
Устройство щебенистого основания автомобильных дорог
Механизация устройства основания
автодорог с конструктивной
разработкой автогрейдера с
гидростатической трансмисии.
ДП-МГОУ-190205-02-02 ПЗ
03.ГСТ.Гидравлическая схема А1-1л.dwg

Клапан МКРН.306577.016
Клапан предохранительный МКРН.306577.046
Клапан редукционный МКРН.306577.048
Фильтр МКРН.061146.006
Установка насосная МКРН.
Гидромотор МКРН.382213.005
Распределитель золотниковый
Клапан предохранительный МКРН.306577.005-01
Аппарат теплообменный
Принятые условные обозначения: ДД - датчик давления; ДС - датчик скорости; ДТ - датчик температуры; ДУ - датчик угла; ЦУ - цилиндр управления.
Клапан предохранительный
Клапан предохранительный
Блок прокачки МКРН.306569.015
Гидрораспределитель МКРН.306154.021
Клапан предохранительный МКРН.306577.078
Датчик давления МКРН.406233.010-01
Индикатор загрязненности МКРН.406239.008
Фильтроэлемент 340.099А
Клапан предохранительный МКРН.306577.070
Фильтр МКРН.061146.035
Датчик положения МКРН.402312.011
Датчик давления МКРН.406233.010-04
Клапан заправочный ПБ5.890.046-1
Гидромотор МКРН.382212.001
Гидромотор аксиально-поршневой
Гидрораспределитель МКРН.306155.003
Насос героторный МКРН.063621.009
Гидрораспределитель МКРН.306111.006
Клапан обратно-предохранительный МКРН.306577.018
Насос МКРН.063234.019
Принятые условные обозначения: ДД - датчик давления; ДП - датчик положения; ДТ - датчик температуры; ДС - датчик скорости; ЗП - золотник прокачки; ИЗ - индикатор загрязненности; ЦУ - цилиндр управления.
Схема гидравлическая принципиальная
Механизация устройства основания автодорог
с конструктивной разработкой автогрейдера с
гидростатической трансмиссией
12.ЭконПлакат..dwg

Грунтовка АК-070 ГОСТ 25718-83(1); Эмаль ЭП-140 черная ГОСТ 24709-81(2)
или эмаль ЭП-51 черная ГОСТ 9640-85(2).
Дет. поз. 18 затянуть с усилием на сбег резьбы.
Сопрягаемые поверхности секций поз. 2
покрыть смазкой ЦИАТИМ-221 ГОСТ 9433-80.
Сборка распределителя должна производиться в условиях отвечающих
общим техническим требованиям БСО.005.032
категория помещения 2.
Болт М8-6ех20.48.019
жидкости к потребителям
Полости отвода рабочей
Полости подвода рабочей
ленного на ось Е относительно плоскости симметрии Д
рабочих секций не должно превышать#2.4`
(#17 мм на конце рычага).
жидкости выполнены в соответствии с ГОСТ 9833-73.
Посадочные места полостей для подвода рабочей
Суммарное отклонение рычага длинной 400 мм. установ-
Гидрораспределитель
КГТА ДП.1211.06.00.13
Инв.N подл и дата Взаим.инв N Инв.N дубл. и дата
Электромагнит с датчиком положения
Гидравлическая схема
Основная заработная плата производственных рабочих
Расходы на содержание и эксплуатацию оборудования
Производственная себестоимость
Общезаводские расходы
Коммерческие расходы
Полная себестоимость
Дополнительная зарплата
Отчисления на соцстрахование
Калькуляция разработки устройства
основные материалы и покупные изделия
Транспортно-заготовительные расходы
Расходы на освоение и подготовку производства
Расчет себестоимости
Механизация устройства основания автодорог с конструктивной разработкой автогрейдера с гидромеханической трансмиссией.
Экономический эффект
06.Пульт управления СБ А1-1л.dwg

Планку фирменную поз.19 и линзу поз.11 ставить на клей ВК-9
ОСТ 4Г 0.029.204 с обеспечением герметичности места вклеивания линзы поз.19.
Клей 88-НП ТУ38 105540-85 или клей 88-СА ТУ 38 1051760-89.
Прокладку поз.17 приклеить к проставке поз.13.
Головки винтов поз.23
уплотнить герметиком ВГО-1 ТУ
стопорить по ОСТ 4Г 0.019.200 вид 25Г.
Головки винтов поз.23 покрыть эмалью ЭП-51 черной ГОСТ 9640-85.
Крышка поз.9 - транспортировочная.
Пломбировать по ГОСТ 18680-73.
Клеймо представителя ОТК.
Допустимое значение уровня статического электричества не более
0В. Меры защиты согласно ОСТ 11.073.062-84.
Остальные ТТ по БС0.005.004 ТУ.
01.Автогрейдер А1- 4 листа.dwg

мм 8950х2460х3360 грейдера
кг 16000 Двигатель: - модель Д-260.4 - мощность
кВт(л.с.) 147(200) - частота вращения коленвала
обмин 2100 Привод хода (гидростатическая трансмиссия): насос: - рабочий объем
см3об 112 - номинальное давление
МПа 25 - максимальное давление
МПа 43 - тип управления электрогидравлическое и ручное(аварийное) - напряжение питания
В 27 гидромотор: - рабочий объем (максимальный)
см3об 112 - рабочий объем (миниимальный)
см3об 40 - номинальное давление
МПа 43 - тип управления электрогидравлическое Отвал: - длинахвысотахширина
мм 3740х620х16 - дорожный просвет
мм 350 - глубина врезания
мм 400 - угол резания
град 30 70 Управлениефункциями отвала: - подъем левого края; - продольное перемещение вдоль по направляющим; - фронтальный наклон; - поворот круга; - боковой сдвиг тяговой рамы; - подъем правого края. Рулевое управление: - двухцилиндровая система управления поворотом с приводом от гидростатического нуля; - угол поворота колес
град 37 - угол "перелома" рамы в сочленении
Механизм выноса отвала
Механизм поворота круга
Гидроцилиндр подъема отвала
Механизм поворота колес
Гидромотор трансмиссии
Пульт упарвления приводом хода
ТП - транспортная передача
НП - нейтральная передача
РП -рабочая передача
СТ - служебный тормоз
СТТ - стояночный тормоз
Схема кинематическая
Схема кинематическая принципиальная трансмиссии автогрейдера
Механизация устройства основания автодорог
с конструктивной разработкой автогрейдера с
гидростатической трансмиссией
08.Преобразователь пульта управления.dwg

Теплообменный аппарат
Предел измер.(0-100) C
установка насосная МКРН.063234.015
Гидромотор БС2.957.000001
Манометр ГОСТ 2405-88
Гидромотор испытуемый
N>1.5кВт n=1500обмин
Насос МКРН.063234.001 или
Балансирный динамометр
Клапан для отбора проб ОСТ 3-3270-85
Гидроклапан предохранительный Г54-22
Термометр любого типа
Гидропривод МКРН.303364.004
Клапан МКРН.306577.016
Клапан предохранительный МКРН.306577.046
Клапан редукционный МКРН.306577.048
Фильтр МКРН.061146.006
Установка насосная МКРН.
Гидромотор МКРН.382213.005
Распределитель золотниковый
Клапан предохранительный МКРН.306577.005-01
Аппарат теплообменный
Принятые условные обозначения: ДД - датчик давления; ДС - датчик скорости; ДТ - датчик температуры; ДУ - датчик угла; ЦУ - цилиндр управления.
Клапан предохранительный
Клапан предохранительный
Блок прокачки МКРН.306569.015
Гидрораспределитель МКРН.306154.021
Клапан предохранительный МКРН.306577.078
Датчик давления МКРН.406233.005-01
Индикатор загрязненности МКРН.406239.008
Фильтроэлемент 340.099А
Клапан предохранительный МКРН.306577.070
Фильтр МКРН.061146.035
Датчик положения МКРН.402312.011
Датчик давления МКРН.406233.009-04
Клапан заправочный ПБ5.890.046-1
Гидромотор МКРН.382212.001
Гидромотор аксиально-поршневой
Гидрораспределитель МКРН.306155.003
Насос героторный МКРН.063621.009
Гидрораспределитель МКРН.306154.191
Клапан обратно-предохранительный МКРН.306577.018
Насос МКРН.063234.019
Принятые условные обозначения: ДП - датчик положения; ДЗ - датчик загрязненности; ДТ - датчик температуры; ДС - датчик скорости; ЦУ - цилиндр управления.
Схема гидравлическая принципиальная
Система управления ГСТ
Схема функциональная
ДС - Датчик скорости
ИЗ - Индикатор загрязненности
ДД - Датчик давления
ДПЛМ - Датчик положения люльки мотора
ДПЛН - Датчик положения люльки насоса
ПВС - преобразователь входного сигнала
Преобразователь пульта управления
МУ - Механизм управления
БУ - Блок управления
ПУ - Пульт управления
Принятые условные обозначения:
ДС - датчик скорости;
РЗ - гидрораспределитель;
ДТ - датчик температуры.
Апарат теплообменный
Гидрораспределитель
Клапан обратно-предохранительный
Индикатор загрязненности
Схема электрическая соединений
Схема электрическая принципиальная
09.Крепление гидромотора.dwg

с конструктивной разработкой автогрейдера с
гидростатической трансмиссией
04.Сист.управления.Схема функциональная.dwg

Теплообменный аппарат
Предел измер.(0-100) C
установка насосная МКРН.063234.015
Гидромотор БС2.957.000001
Манометр ГОСТ 2405-88
Гидромотор испытуемый
N>1.5кВт n=1500обмин
Насос МКРН.063234.001 или
Балансирный динамометр
Клапан для отбора проб ОСТ 3-3270-85
Гидроклапан предохранительный Г54-22
Термометр любого типа
Гидропривод МКРН.303364.004
Клапан МКРН.306577.016
Клапан предохранительный МКРН.306577.046
Клапан редукционный МКРН.306577.048
Фильтр МКРН.061146.006
Установка насосная МКРН.
Гидромотор МКРН.382213.005
Распределитель золотниковый
Клапан предохранительный МКРН.306577.005-01
Аппарат теплообменный
Принятые условные обозначения: ДД - датчик давления; ДС - датчик скорости; ДТ - датчик температуры; ДУ - датчик угла; ЦУ - цилиндр управления.
Клапан предохранительный
Клапан предохранительный
Блок прокачки МКРН.306569.015
Гидрораспределитель МКРН.306154.021
Клапан предохранительный МКРН.306577.078
Датчик давления МКРН.406233.005-01
Индикатор загрязненности МКРН.406239.008
Фильтроэлемент 340.099А
Клапан предохранительный МКРН.306577.070
Фильтр МКРН.061146.035
Датчик положения МКРН.402312.011
Датчик давления МКРН.406233.009-04
Клапан заправочный ПБ5.890.046-1
Гидромотор МКРН.382212.001
Гидромотор аксиально-поршневой
Гидрораспределитель МКРН.306155.003
Насос героторный МКРН.063621.009
Гидрораспределитель МКРН.306154.191
Клапан обратно-предохранительный МКРН.306577.018
Насос МКРН.063234.019
Принятые условные обозначения: ДП - датчик положения; ДЗ - датчик загрязненности; ДТ - датчик температуры; ДС - датчик скорости; ЦУ - цилиндр управления.
Схема гидравлическая принципиальная
Система управления ГСТ
Схема функциональная
ДС - Датчик скорости
ИЗ - Индикатор загрязненности
ДД - Датчик давления
ДПЛМ - Датчик положения люльки мотора
ДПЛН - Датчик положения люльки насоса
ПВС - преобразователь входного сигнала
Преобразователь пульта управления
МУ - Механизм управления
БУ - Блок управления
ПУ - Пульт управления
Принятые условные обозначения:
ДС - датчик скорости;
РЗ - гидрораспределитель;
ДТ - датчик температуры.
Апарат теплообменный
Гидрораспределитель
Клапан обратно-предохранительный
Индикатор загрязненности
Схема электрическая соединений
Схема электрическая принципиальная
Механизация устройства основания автодорог
с конструктивной разработкой автогрейдера с
гидростатической трансмиссией
Рекомендуемые чертежи
- 24.01.2023
- 22.08.2014
- 22.08.2014
- 22.08.2014
Свободное скачивание на сегодня
- 24.01.2023
Другие проекты
- 22.08.2014
- 04.11.2022