Маслополимерные смолы: Производство олигомеров на основе фракций побочных продуктов производства этилена


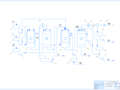
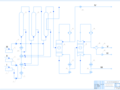
- Добавлен: 25.01.2023
- Размер: 3 MB
- Закачек: 0
Описание
Состав проекта
![]() |
![]() |
![]() |
![]() ![]() ![]() |
![]() ![]() ![]() |
![]() ![]() ![]() |
![]() |
![]() ![]() ![]() |
![]() ![]() ![]() |
![]() ![]() ![]() |
![]() |
![]() |
![]() |
![]() ![]() ![]() |
![]() |
![]() |
![]() ![]() ![]() |
![]() ![]() ![]() |
![]() ![]() ![]() |
![]() ![]() ![]() |
![]() ![]() |
![]() ![]() |
![]() |
![]() |
![]() ![]() ![]() ![]() |
![]() |
![]() ![]() ![]() ![]() |
![]() |
![]() |
![]() |
![]() |
![]() |
![]() ![]() ![]() |
![]() |
![]() ![]() ![]() |
![]() |
![]() ![]() ![]() |
![]() ![]() ![]() |
![]() |
![]() |
![]() ![]() ![]() |
![]() |
![]() ![]() ![]() |
![]() ![]() ![]() |
![]() ![]() ![]() |
![]() |
![]() ![]() ![]() |
![]() |
![]() ![]() ![]() |
![]() |
![]() ![]() ![]() |
![]() ![]() ![]() |
![]() |
![]() ![]() ![]() |
![]() |
![]() ![]() ![]() |
![]() ![]() ![]() |
![]() ![]() |
Дополнительная информация
Аркуш 5.doc
Одержання олігомерів на основі фракцій побічних продуктів етиленових виробництв
НУ «ЛП» ХХТ каф. ТОП гр. ТОР-21с
Вплив концентрації комономеру МА (1) АК (2) ДАФ (3) на вихід
синтезованих РО: 1 – ініційована 2 – термічна
Аркуш 3.doc
Одержання олігомерів на основі фракцій побічних продуктів етиленових виробництв
НУ «ЛП» ХХТ каф. ТОП гр. ТОР-21с
Залежність бромного числа та густини олігомеризату від концентрації
ДАФ та температури процесу коолігомеризації
Аркуш 4.doc
Одержання олігомерів на основі фракцій побічних продуктів етиленових виробництв
НУ «ЛП» ХХТ каф. ТОП гр. ТОР-21с
Вплив концентрації ДАФ та температури процесу
коолігомеризації на густину та ненасиченість олігомеру
Рамка на портретний планшет.doc
Оцінка фінансово-господарської діяльності філії - Долинське відділення № 6343 ВАТ Державний ощадний банк України”
ПРОГНОЗУВАННЯ ВЕЛИЧИНИ КРЕДИТВ КЛНТАМ ТА ДЕПОЗИТВ КЛНТВ НА 2008 РК У ФЛ - ДОЛИНСЬКЕ ВДДЛЕННЯ № 6343 ВАТ «ДЕРЖАВНИЙ ОЩАДНИЙ БАНК УКРАНИ»
Національний університет “Львівська політехніка”
Каф.фінансівгр..ЕК-43
Рамка на альбомний планшет.doc
Одержання композицій на основі епоксидної та вуглеводневих смол
НУ «ЛП» ХХТ каф. ТОП гр. ТОР-21с
Аркуш 2.doc
Одержання олігомерів на основі фракцій побічних продуктів етиленових виробництв
НУ «ЛП» ХХТ каф. ТОП гр. ТОР-21с
Залежність виходу та основних фізико-хімічних характеристик РО від масового співвідношення фракцій С5 і С9
Найменування показника
Густина олігомеризату кгм3
Бромне число г Br2100 г
Бромне число РО г Br2100 г
Колір НПС мг J2100 см3
Експериментальна частина.doc
ОДЕРЖАННЯ ОЛГОМЕРВ РЗНИМИ МЕТОДАМИ
Співолігомеризацію фракції С9 піролізу дизельного палива проводили при оптимальних умовах: температура 453 К тривалість процесу 6 год. концентрація модифікатора 5 20 % мас. (на фракцію) концентрація ініціатора ПДТБ 1 % мас. Процес термічної коолігомеризації технологічно є досить простим його недоліком є невисокий вихід смоли. При ініційованому методі технологія процесу практично аналогічна але вимагає застосуваня пожежо- та вибухонебезпечного ініціатора. У результатi проведених дослiджень встановлено що кожен з методів синтезу реакційно здатних олігомерів (РО) має свої переваги та недоліки і може з успіхом застосовуватится для синтезу таких смол які знаходять дедалі ширше застосування в різноманітних галузях народного господарства. З метою оцінки виходу та фізико–хімічних характеристик РО одержаних ініційованою та термічною коолігомеризацією було проведено дослідження реакції коолігомеризації фракції С9 РПП дизельного палива з наступними комономерами: МА АК і ДАФ в оптимальних умовах проведення реакції: температура 453 К тривалість 6 год концентрація комономеру 15 % мас. (для ініційованого методу концентрація ПДТБ 1 % мас.). У результаті проведених досліджень встановили (рис. 1) що використання ПДТБ забезпечує вищу швидкість реакції коолігомеризації у порівнянні з термічною коолігомеризацією в таких же умовах. Про це свідчать нижчі значення бромного числа олігомеризату (рис. 1 криві 1.1–1.3) у порівнянні з термічним методом (рис. 2 криві 2.1–2.3) відповідно. Спостерігаються також вищі значення густини олігомеризату при використанні у порівнянні з термічним методом синтезу. Позитивний вплив підвищення концентрації комономеру від 5 20 % мас. сприяє більшому виходу РО рис. 2. При цьому використання 1 % мас. ПДТБ забезпечує в середньому на 5 % мас. вищий вихід РО у порівнянні з термічним методом у досліджуваному інтервалі концентрацій комономеру.
Рис.1. Залежність бромного числа олігомеризату від концентрації комономеру МА (1) АК (2) ДАФ (3): 1 – ініційована 2 – термічна
Рис. 2. Вплив концентрації комономеру МА (1) АК (2) ДАФ (3) на вихід синтезованих РО: 1 – ініційована 2 – термічна.
Порівнюючи одержані результати треба відзначити що коолігомерні НПС одержані термічним методом мають більш високу ненасиченість температуру розмякшення та молекулярну масу ніж смоли одержані у присутності ПДТБ. Нижчі значення числа омилення (37 139 і 17 55 35 135 і 14 51 мг КОНг для МА та ДАФ) а також кислотного числа (32 118 29 114 мг КОНг для АК) при термічному методі у порівнянні з ініційованим пояснюються меншою реакційною здатністю комономерів. Зменшення молекулярної маси смол пояснюється більшою швидкістю реакції обривання ланцюга при наявності в реакційній масі джерела вільних радикалів. Загалом вихід цих смол у перерахунку на вихідну сировину зі збільшенням концентрації комономера збільшується але смоли синтезовані шляхом термічної коолігомеризації мають менший вихід що виправдовує застосування ініціатора. На рис. 3 зображена залежність ненасиченості синтезованої смоли від методу одержання та концентрації комономеру. Смоли одержані шляхом термічної коолігомеризації мають більш ненасичений характер як для МА так і для АК і ДАФ.
Рис. 3. Вплив концентрації комономеру на ненасиченість РО МА (1) АК (2) ДАФ (3): 1 – ініційована 2 – термічна.
Процес термічної коолігомеризації технологічно є досить простим його недоліком є порівняно меншиий вихід смоли при задовільних решта фізико–хімічних характеристиках. Технологія ініційованого процесу синтезу смол практично аналогічна але вимагає застосуваня пожежо– та вибухонебезпечного пероксидного ініціатора. Вихід функціоналізованих НПС в присутності ініціатора в середньому на 5 10 % мас. вищий ніж вихід НПС при термічному способі. Підвищення виходу смол при використанні 1 % мас. ПДТБ пояснюється вищою конверсією ненасичених вуглеводнів фракції С9 РПП у порівнянні з конверсією вуглеводнів при термічному методі.
Отже як свідчать отримані дані використання 1 % мас. ПДТБ забезпечує на 5 10 % мас. вищий вихід РО у порівнянні з термічним методом синтезу що зумовлено вищою конверсією основних смолоутворювальних компонентів сировини в реакції коолігомеризації сумарна конверсія основних смолоутворювальних компонентів відрізняється в середньому на 5 %. З врахуванням практично аналогічної технології ініційованого та термічного методу (відмінність полягає лише в наявності вузла приготування та дозування розчину ініціатора при ініційованому методі отримання РО) та незначної відмінності у фізико–хімічних характеристиках РО для подальших досліджень вибираємо метод ініційованої коолігомеризації.
ДОСЛДЖЕННЯ ВПЛИВУ ВИХДНО СИРОВИНИ НА ВИХД ФЗИКО–ХМЧН ХАРАКТЕРИСТИКИ КООЛГОМЕРНИХ СМОЛ
З метою порівняння впливу вихідної сировини на вихід та фізико–хімічні характеристики коолігомерної НПС проведено дослідження з використанням як вихідної сировини окрім фракції С9 РПП дизельного палива також фракцій: С9 і С5 – 9 РПП бензину відповідно. Як комономери використовували: МА АК та ДАФ. Реакцію коолігомризації проводили при температурі 453 К протягом 6 год у присутності 5 20 % мас. комономеру концентрація ПДТБ 1 % мас.
Однією з основних вимог що ставлять до НПС є їх висока ненасиченість. На рис. 4 показано як залежить ненасиченість синтезованих карбоксилвмісних смол від природи вихідної сировини. У результаті проведених досліджень встановлено що смоли одержані на основі С9 мають меншу ненасиченість у порівнянні зі смолами синтезованими шляхом ініційованої коолігомеризації фракції С 5 – 9 РПП бензини це пояснюється вищим вмістом у даній фракції дієнових вуглеводнів.
Рис. 4. Залежність ненасиченості синтезованої смоли від вихідної сировини та концентрації комономеру: МА (1) АК (2) ДАФ (3):
– С5 – 9 фракція РПП бензини 2 – фракція С9 РПП бензини.
На рис. 5 При використанні фракції С9 РПП бензину вихід НПС практично наближується до виходу смоли одержаної на основі фракції С9 РПП дизельного палива і становить 42 54 45 56 37 42 % мас. для МА АК і ДАФ відповідно (див. рис. 4.12) та 30 38 32 40 28 36 % мас. відповідно (рис. 4.15) при використанні фракції К.
Рис. 5. Вплив вихідної сировини та концентрації комономеру на вихід НПС: МА (1) АК (2) ДАФ (3): 1 – фракція С9 2 – С5 – 9 фракція РПП бензину.
Це можна пояснити близьким вуглеводневим складом фракцій С9 РПП дизельного палива та бензину – сумарний вміст реакційноздатних ненасичених вуглеводнів в яких складає: 6577 і 6999 % мас. відповідно. При цьому вміст основних смолоутворюючих компонентів а саме стиролу та його гомологів які характеризуються високою конверсією як у фракції С9 РПП бензину так і у фракції С9 РПП дизельного палива дуже близький. Відмінність є лише у кількості у фракції С5 – 9 РПП бензину дієнових вуглеводнів вищий що й спричиняє вищу ненасиченість смол синтезованих з використанням цієї фракції.
ОДЕРЖАННЯ АЛФАТИЧНИХ ОЛГОМЕРВ НА ОСНОВ ФРАКЦ С5
Аліфатичні РО широко використовують у виробництві дорожніх фарб клеїв-розплавів клейких стрічок пластмасових і каучукових сумішей. На сучасних етиленових установках одержується фракція С5 яка міститься в основному в легких РПП. Дану фракцію доцільно використовувати як сировину для одержання НПС тому що вона містить у своєму складі значну кількість цінних дієнових вуглеводнів. Найбільш поширеним є спосіб каталітичної коолігомеризації фракції С5. Застосовують також і термічну коолігомеризацію яку здійснюють одно- чи двостадійним методами. Одностадійний процес здійснюють коолігомеризацією у присутності ароматичних чи аліфатичних вуглеводнів при температурі 523 573 К протягом 05 10 год. При двостадійному процесі продукт одержаний шляхом попередньої коолігомеризації (температура 373 433 К тривалість 5 год) і який містить кодимери діє нових вуглеводнів фракції С5 далі коолігомеризують при 523К протягом 2 4год. Непрореаговані вуглеводні виділяють обробляючи олігомеризат парою при температурі 423 К. На цій стадії переважно відбувається димеризація дієнів та їх кодимеризація за реакцією дієнового синтезу (реакція Дільса-Альдера).
Каталітична коолігомеризація вуглеводнів фракції С5 здійснюється одно- чи двостадійним методами; як каталізатор найчастіше використовують каталізатори Фріделя-Крафтса. До вихідної фракції С5 можна додавати олефіни та дієни (до початку коолігомеризації) в тому числі і залишки бутадієнової фракції С4. Попередню коолігомеризацію фракції С5 здійснюють протягом 5 год при 373 - 433 К. Для більш повної конверсії ЦПД запропоновано коолігомеризувати вихідну фракцію при температурі 443 - 453К з подальшим пониженням її до 393 - 423 К. Прозорі смоли можна одержати коолігомеризацією фракції С5 зі стиролом чи його похідними в присутності комплексу галогеніду в ароматичному розчиннику. Метою роботи було дослідження впливу вуглеводневого складу вихідної сировини та природи ініціатора на вихід та основні фізико-хімічні характеристики РО. Як ініціатор олігомеризації використано пероксид ди-трет-бутилу (ПДТБ) – ((СН3)3СО)2 вміст активного кисню 10 94 % мас. температура піврозпаду 421 466 К один з найкращих ініціаторів для синтезу РО на основі фракцій РПП. На рис. 6 зображено вплив концентрації комономеру – ДАФ на густину та ненасиченість олігомеризату. Як показують отримані експериментальні дані найменша густина олігомеризату та бромне число синтезованих РО мають місце при температурі 413 К. В інтервалі температур 433 453 К ненасиченість смоли інтенсивно зменшується до кількості ДАФ в реакційній суміші 15 % мас. подальше підвищення концентрації ДАФ не супроводжується значним зменшенням бромного числа олігомеризату а відтак і його густини.
Рис. 6. Залежність бромного числа та густини олігомеризату від концентрації ДАФ та температури процесу коолігомеризації.
Основними кількісними характеристиками РО є ненасиченість або бромне число та вихід. Як видно з рис. 7 вихід РО зростає як при збільшенні температури процесу так і при підвищенні концентрації МА. Хоча зростання температури процесу ефективне до 453 К температура 473 К не забезпечує значного підвищення як виходу РО та його ненасиченості. Концентрація комономеру 20 % мас. не виправдовує себе оскільки бромне число зменшується мало МА повільно вступає в реакцію що підтверджує й незначне збільшення виходу олігомери лише на 2 3 %.
Рис. 7. Вплив концентрації ДАФ та температури процесу коолігомеризації на густину та ненасиченість олігомеру.
Подальші наші дослідження пов’язані з вивченням можливості залучення фракції С5 до коолігомеризації з фракцією С9 з використанням високотермостійких ініціаторів. У зарубіжній практиці для одержання коолігомерних РО використовують каталітичну коолігомеризацію сировини. Більшість патентів по одержанню коолігомерних смол з фракцій С5 і С8 – С10 належать японським фірмам. Встановлено можливість використання коолігомерних смол у лакофарбовій промисловості при виробництві паперу фарб. Одержання РО на основі фракцій С5 і С9 РПП дизельного палива здійснювали двостадійним методом. За результатами попередніх досліджень при одностадійному проведенні коолігомеризації суміші олефінів та дієнів фракції С5 не забезпечуються високі виходи НПС. Незважаючи на високу конверсію мономерів основними є реакції димеризації та коолігомеризації дієнів і олефінів. Невисока середня молекулярна маса олігомеризату підтверджує наявність серед продуктів значної кількості димерів та олігомерів які вилучають на стадії дистиляції при одержанні РО. На першій стадії радикальної коолігомеризації фракції С5 одержують суміш димерів та рідких олігомерів. Після вилучення непрореагованих вуглеводнів одержували фракцію яку в подальшому коолігомеризували з ненасиченими вуглеводнями фракції С9 РПП бензину з одержанням коолігомерних РО. За таких умов зникає необхідність у довготривалому проведенні процесу на першій стадії. Попередню коолігомеризацію вуглеводнів фракції С5 здійснювали при температурі 433 К протягом 5 год. У таблиці представлені результати одержання РО з різним масовим співвідношенням фракцій С5 і С9 у присутності ПДТБ тривалість 6 год температура 473 К).
Залежність виходу та основних фізико-хімічних характеристик РО від масового співвідношення фракцій С5 й С9
Найменування показника
Густина олігомеризату кгм3
Бромне число г Br2100 г
Бромне число РО г Br2100 г
Колір НПС мг J2100 см3
Температура розм’якшення одержаних смол є в межах 343 348 К що приблизно на 15 К нижча ніж для НПС одержаних на основі фракції С9. За показником ненасиченості коолігомерні РО займають проміжне місце між олігомерами синтезованими на основі окремих фракцій С5 і С9. Сировину яка використовується для одержання РО за результатами виходу можна розмістити в ряд:
Фр. С9 > фр. С5 + фр. С9 > фр. С5.
Аналіз впливу масового співвідношення олігомерів фракцій С5 і. С9 на вихід та показники РО показав що із збільшенням вмісту олігомерів фракції С5 зменшується вихід зростає ненасиченість та покращується її колір. При підвищенні кількості фракції С9 зростає густина олігомеризату вихід і молекулярна маса але погіршується їх колір та зменшується бромне число смол. Як бачимо з таблиці оптимальним є масове співвідношення олігомери фракцій С5 : С9 = 1 : 1. Одержані РО характеризуються малоінтенсивним світлим забарвленням високою ненасиченістю та низькою молекулярною масою. Такі олігомери добре розчиняються в уайт-спіриті уміщаються з оксидованими рослинними оліями та оксидованими оливами
SUMMARY-2003.doc
Petroleum resins are used as substitutes for expensive and scarce materials of natural origin. A by-product from making petroleum resins – wastes are used in paint industries as solvents and as a component of boiler fuel. Obtaining of epoxy-petroleum compositions allow to expand their scope.
In the thesis work is proposed technological scheme of obtaining epoxy-petroleum compositions developed measures for safety and security in the chemical laboratory in emergency situations and calculated costs of laboratory experiments.
ВИСНОВКИ.docx
Встановлено що епоксинафтополімерні композиції характеризуються високою тривкістю в нейтральних кислих та лужних середовищах. Водо– та хімстійкість підвищується зі зростанням кількості комономеру у НПС. Встановлено можливість застосовування таких композицій як плівкоутворюючих компонентів що мають виражені антикорозійні захисні властивості.
Запропоновано технологічну схему для одержання епоксинафтополімерних композицій. Проведено розрахунок матеріального та теплового балансів.
У розділі «Охорона праці та безпека в надзвичайних ситуаціях» розроблено заходи з охорони праці і техніки безпеки у лабораторії виконаний розрахунок системи природної вентиляції.
В економічній частині роботи розраховано витрати на проведення досліджень вартість приладів та електроенергії.
ЗМІСТ.docx
1.Вихідна сировина для одержання епоксидних та нафтополімерних смол та їх класифікація
2.Методи одержання епоксидних та нафтополімерних смол
3.Одержання модифікованих нафтополімерних смол
4.Застосування нафтополімерних смол
4.1.НПС в лакофарбовій промисловості
4.2.НПС в целюлозно-паперовій промисловості
4.3.НПС в гумовій промисловості
4.4.Застосування НПС з епоксидними композиціями для
антикорозійних покриттів
4.5.Перспективні області застосування НПС
РОЗДЛ 2. ВИХДН РЕЧОВИНИ МАТЕРАЛИ ТА МЕТОДИКИ ЕКСПЕРИМЕНТУ
1.Вихідні речовини та матеріали
2.Методика одержання зразків
3.Ч-спектроскопічні дослідження одержання епоксинафтополімерних композицій
4.Методи диференційно-термічного та термогравіметричного аналізів
5.Визначення вмісту гель-фракції в полімерних плівках
6.Вмзначення водо- та хімтривкості покриттів
РОЗДЛ 3. ЕКСПЕРИМЕНТАЛЬНА ЧАСТИНА
1.Встановлення співвідношення для одержання епоксинафтополі-мерних композицій
2.Приготування композицій з використанням ангідридів дикарбоно-вих кислот
2.Одержання епоксинафтополімерних композицій на основі твердників амінного типу
РОЗДЛ 4. ТЕХНОЛОГЧНА ЧАСТИНА
1.Опис технологічної схеми процесу одержання композицій на основі епоксидних та нафтополіметних смол
2.Матеріальний баланс даного процесу
3.Тепловий баланс реактора
РОЗДЛ 5. ОХОРОНА ПРАЦ ТА БЕЗПЕКА В НАДЗВИЧАЙНИХ СИТУАЦЯХ
1.Характеристика дослідницької роботи
2.Аналіз загроз в лабораторії
3.Охорона праці при експлуатації обладнання в хімічній лабораторії
5.Санітарно-гігієнічні вимоги
6.Заходи забезпечення безпеки роботи в лабораторії
7.Мікроклімат приміщення лабораторії
8.Розрахунок системи природної вентиляції
РОЗДЛ 6. ЕКОНОМЧНА ЧАСТИНА
1.Обгрунтування доцільності досліджень з економічної точки зору
2.Розрахунок затрат на проведення дослідженнь
3.Розрахунок енергозатрат
4.Розрахунок фонду оплати праці
5.Розрахунок вартості апаратури
7.Загальна вартість лабораторних досліджень
8.Техніко-економічна оцінка результатів
СПИСОК ВИКОРИСТАНО ЛТЕРАТУРИ
АНОТАЦІ1 2003.doc
Нафтополімерні смоли використовують як замінники дорогих та дефіцитних матеріалів природного походження. Побічні продукти виробництва нафтополімерних смол – відгони використовують у лакофарбовій промисловості як розчинники та як компонент котельного палива. Аодержання епоксинафтополімерних композицій дозволяє розширити їх область застосування. Встановлено що епоксинафтополімерні композиції характеризуються високою тривкістю в нейтральних кислих та лужних середовищах. Водо– та хімстійкість підвищується зі зростанням кількості комономеру у НПС.
Також у дипломній роботі запропоновано технологічну схему одержання епоксинафтополімерних композицій та розроблено заходи з охорони праці та безпеки в надзвичайних ситуаціях в хімічній лабораторії при проведенні цих досліджень та розраховано витрати на проведення лабораторних дослідів.
Схема 2 (безперервна).cdw

Схема 1 (періодична).cdw

Характеристика сировини і методика проведення експериментів.doc
1. Характеристика сировини та допоміжних реактивів
1.1.1. Фракція С5 РПП дизельного палива.
1.1.2 Фракція С9 РПП дизельного палива.
1.1.3. Фракція С5-9 РПП (ЗАТ “Лукор” м. Калуш вано-Франківська обл.).
1.1.4. НПС лакофарбова синтетична відповідає вимогам ТУ У 6-05743160.020-96 її фізико-хімічні показники наведені у табл. 2.3.
Основні фізико-хімічні характеристики та вуглеводневий склад цих фракцій наведено в табл.2.1 та 2.2 відповідно.
Фізико-хімічні показники вуглеводневих фракцій
Найменування показників
прозора рідина світло-жовтого
кольору без сторонніх включень
Бромне число г Br2100 г
Колір за ЙМШ мг J2100 см3
Показник заломлення nd20
Вуглеводневий склад (% мас.) фракцій С5 С9 і С5-9 РПП
Найменування вуглеводнів
метилциклопентадієни
неідентиф. насич. вуглеводні
неідентиф.ненасич. вуглеводні
Фізико-хімічні характеристики НПС
кристали жовтого кольору
Температура розм'якшення К
Вміст води % мас. не більше
Вміст сажі % мас. не більше
Вміст сірки % мас. не більше
Кислотність % мас. HCl не більше
Лужність % мас. NaOH не більше
Механічні домішки % мас. не більше
Як сировину для синтезу коолігомерних НПС з функціональними групами використовували фракції С5 і С9 РПП дизельного палива а для порівняння (впливу природи вихідної сировини на вихід і фізико–хімічні характеристики НПС) – фракцію С9 РПП дизельного палива.
1.2.1. Акрилова (пропенова) кислота.
Формула - СН2=СН-СООН.
Розчинність у воді - змішується у всіх співвідношеннях.
Розчинність в органічних розчинниках - добре розчинна в етиловому спирті та етиловому етері.
1.2.2. Малеїновий ангідрид.
Формула - С2Н2(СО)2О.
При кипінні сублімується.
Розчинність у воді - в 100 г води 16 3 г ангідриду при 303 К.
Розчинність в органічних розчинниках - розчинний в ацетоні та хлороформі.
Основні фізико-хімічні характеристики модифікаторів наведені у табл. 2.4 [81 – 84]
Фізико–хімічні показники модифікуючих домішок
1.3. Допоміжні реактиви
1.3.1. ніціатор - ПДТБ.
Формула - (С(СН3)3О)2.
Молекулярна маса - 146.
Температура кипіння Тк = 375 К.
Час піврозпаду t 12 = 1 хв при Т = 466 К.
Час піврозпаду t 12 = 1 год при Т = 421 К.
Час піврозпаду t 12 = 10 год при Т = 399 К.
Енергія активації термічного розкладу – 156 кДжмоль.
Вміст активного кисню - [О]акт. = 1094 %.
Показник заломлення - nd20 = 094.
1.3.2.1. Етиловий спирт використовували технічний із вмістом основного продукту не менше 95 % мас.
1.3.2.2. Ацетон марки ²х.ч.² ²ч.д.а.².
1.3.2.3. Етиловий етер марки ²х.ч.² ²ч.д.а.².
1.3.2.4. Бензол марки ²х.ч.² ²ч.д.а.².
1.3.2.5. Уайт–спірит марки ²х.ч.² ²ч.д.а.².
1.3.2.6. Хлороформ марки ²х.ч.² ²ч.д.а.².
1.3.2.7. ЧХВ марки ²х.ч.² ²ч.д.а.².
Розчинники очищали згідно відомих методик [85].
1.3.3.1. Ацетатна кислота марки ²х.ч.².
1.3.3.2. Хлоридна кислота марки ²х.ч.².
1.3.3.3. Сульфатна кислота марки ²х.ч.².
1.3.4. Гідроксиди металів:
1.3.4.1.Гідроксид калію марки ²ч.д.а.².
1.3.4.2.Гідроксид натрію марки ²ч.д.а.².
Всі перегонки у вакуумі проводили в атмосфері сухого і чистого аргону [86 87].
2. Методики проведення експериментів
2.1. Методика проведення процесу коолігомеризації
Схему експериментальної установки для синтезу коолігомерної НПС зображено на рис.2.1.
Рис. 2.1. Схема лабораторної установки синтезу коолігомерної НПС:
- корпус реактора; 2 - кришка реактора; 3 - вентиль; 4 - термометр; 5 - манометр; 6-контактний термометр; 7 - терморегулятор; 8 - мішалка; 9 - електронагрівач; 10 - термостат.
Коолігомеризацію вуглеводневої фракції з комономером проводили в термостатованому реакторі з нержавіючої сталі (марка Х18Н9Т) обємом 110-3 м3 у середовищі аргону при надлишковому тиску 05 055 МПа який забезпечує перебіг реакції в рідкій фазі. ніціатор коолігомеризації та комономер вводили на початку реакції. Для цього після досягнення необхідної температури реактор із попередньо завантаженими фракцією С5-9 і розрахованою кількістю ініціатора й комономера вміщали в термостат. Після закінчення коолігомеризації визначали бромне число та густину одержаного олігомеризату.
Вуглеводні що не прореагували вилучали проводячи атмосферну (тиск 011 МПа температура 463 К) та вакуумну (залишковий тиск 3 4 гПа температура 473 К) дистиляції олігомеризату.
Одержану модифіковану НПС характеризували наступними фізико-хімічними показниками: колір температура розм'якшення молекулярна маса бромне число кислотне число число омилення.
Атмосферний та вакуумний дистиляти що утворюються при синтезі коолігомерної НПС аналізували хроматографічно.
Достовірність результатів досліджень перевіряли 3 4 експериментами а також на промисловій установці періодичної дії ДП “Орісіл” ВАТ “Лукор” (м. Калуш вано-Франківська обл.).
3. Методики проведення аналізів
Використовували наступні методи аналізу які дають можливість комплексно охарактеризувати вихідну сировину та синтезовані продукти повязати їх зі складом аналізованих продуктів та дати рекомендації для найбільш раціонального їх застосування:
хімічні - використовували титриметричні методи для визначення функціональних чисел: бромного кислотного омилення;
фізичні - визначення: густини кольору розчинності сумісності температури розмякшення молекулярної маси;
фізико-хімічні - ГРХ.
3.1. Хімічні методи аналізу
У хімічних методах аналізу пробу піддають спочатку дії якого–небудь реагенту тобто проводять хімічну реакцію. В залежності від цього їх можна поділити за протіканням реакції на: кислотно–основні комплексоутворення окисно–відновні фазової рівноваги.
3.1.1. Визначення бромного числа
Бромним числом називається число грамів брому що приєднюється до 100 г досліджуваної речовини. Воно характеризує вміст у досліджуваній речовині ненасичених сполук.
Прилади: колби конічні 100 см3 піпетки обємом: 2 5 10 20 см3.
Реактиви: ЧХВ (хлороформ) СH3COOH (конц.) бромід-броматний (КBr+КBrО3) розчин HCl (конц.) KJ 20 %-ий розчин Na2S2O3 01 н розчин крохмал 10 %–ий розчин.
У дві конічні колби з притертими корками обємом по 100 см3 кладуть наважку (масою 02-05 г) аналізованої речовини. Зважують наважки на аналітичних вагах з точністю до 00001 г. В колби додають 5 см3 ЧХВ (хлороформу) вміст колби перемішують до повного розчинення додають ще 10 см3 концентрованої ацетатної кислоти й охолоджують 5-10 хв пізніше – 20 см3 бромід-броматного розчину і далі охолоджують при постійному перемішуванні 20-25 хв. Після чого колби виймають з холодильника додають 5 см3 концентрованої хлоридної кислоти і знову ставлять у морозильну камеру на 5 хв. Для протікання реакції бромування суміш потрібно інтенсивно перемішувати після додавання кожного з вищевказаних реагентів. Відтак до суміші додають 2 см3 20 %-го розчину йодистого калію перемішують та відтитровують 01 н розчином тіосульфату натрію. Крохмаль до титрованих розчинів додають перед закінченням титрування коли жовте забарвлення йоду почне послаблюватися й відтак титрують до знебарвлення суміші. Паралельно проводять контрольний дослід. Бромне число визначають за формулою:
V1 - обєм розчину Na2S2O3 витраченого на титрування контрольної проби см3;
V2 - обєм розчину Na2S2O3 витраченого на титрування робочої проби см3;
Т - поправочний коефіцієнт що показує число грамів брому яке відповідає 1 см3 01 н розчину
К - поправка на 01 н. розчин Na2S2O3.
За результати вимірювань приймають середнє арифметичне значення результатів двох паралельних визначень [84 86].
3.1.2. Визначення кислотного числа
Кислотне число характеризується кількістю КОН (в 1 мг) яка необхідна для нейтралізації вільних кислотних груп які містяться в 1 г речовини що аналізується.
Прилади: колби конічні обємом 100 см3 піпетки обємом: 5 см3.
Реактиви: С2H5ОН С2H5COС2H5 КОН 01 н розчин бромтимоловий синій 01 %-ий спиртовий розчин.
У колбу зважують 05-10 г аналізованого продукту з точністю до 00002 г додають 5 см3 бензолу та перемішують до повного розчинення. Після цього у колбу додають 5 см3 ацетону чекають до утворення однорідної суміші. Відтак титрують 01 н спиртовим розчином КОН у присутності бромтимолового синього до появи темно зеленого забарвлення.
Аналізують дві проби; паралельно в таких же умовах проводять контрольний дослід. З одержаних результатів приймають середнє значення. Кислотне число (1 мг КОН1г) розраховують за формулою:
V1 - обєм 01 н розчину КОH витраченого на титрування робочої проби см3;
V2 - обєм 01 н розчину КОH витраченого на титрування контрольної проби см3;
F - поправочний коефіцієнт 05 н розчину КОH;
6 - кількість КОН що відповідає 1 см3 точно 01 н розчину КОH г;
m - наважка речовини яку аналізують г.
За результати вимірювань приймають середнє арифметичне значення результатів двох паралельних визначень [86 – 88].
3.1.3. Визначення числа омилення
Число омилення характеризує кількість КОН (в 1 мг) яка необхідна для звязування вільних кислотних груп та омилення складних ефірів які містяться в 1 г речовини що аналізується.
Прилади: колби конічні з пришліфованими холодильниками обємом 250 см3 трубки з натронним вапном піпетка обємом 25 см3.
Реактиви: КОН 05 н спиртовий розчин HC фенолфталеїн 1 %-ий спиртовий розчин.
У колбу вміщують 05-10 г аналізованого продукту зваженого з точністю до 00002г доливають 25 см3 05 н розчину лугу і нагрівають зі зворотнім холодильником на водяній бані протягом 3 год. Холодильники закривають зверху трубкою з натронним вапном щоб попередити попадання діоксиду вуглецю з повітря. Якщо досліджувана речовина не розчиняється в спирті її попередньо розчиняють у відповідному розчиннику який не реагує з лугом. По закінченні омилення вмістиме колб не охолоджуючи титрують 05 н розчином хлоридної кислоти у присутності фенолфталеїну до зникнення рожевого забарвлення.
Аналізують дві проби; паралельно в таких же умовах проводять контрольний дослід. З одержаних результатів приймають середнє значення. Число омилення (1 мг КОН1г) розраховують за формулою:
V1 - обєм 05 н розчину HC
V2 - обєм 05 н розчину HC
F - поправочний коефіцієнт 05 н розчину
- кількість КОН що відповідає 1 см3 точно 05 н розчину HC
За результати вимірювань приймають середнє арифметичне значення результатів двох паралельних визначень [87 – 88].
3.2. Фізичні методи аналізу
При фізичних методах аналізу спостереження та вимірювання виконують безпосередньо з аналізованими речовинами причому хімічні реакції або зовсім не проводять або вони відіграють допоміжну роль. Ці методи включають три групи які рунтуються на: взаємодії випромінювання з речовини чи вимірюванні випромінювання речовини вимірюванні параметрів електричних і магнітних властивостей речовини вимірюванні густини чи інших механічних або молекулярних властивостей речовини. Фізичні методи аналізу олі феніло на зміні якого–небудь параметру системи який є функцією складу.
3.2.1. Визначення густини
Густину фракцій та олігомеризатів визначали олі феніловим методом згідно методики [86 87].
3.2.2. Визначення кольору
Колір НПС визначали візуально порівнюючи 10%-ий розчин смоли в бензолі з еталонною стандартною ЙМШ. Аналіз НПС з кольором 80 мг J2100 см3 проводили фотоколоричним методом [89 91] згідно якого вимірювали оптичну густину розчину НПС в бензолі і визначали її колір за градуйованим графіком. Для аналізів використовували фотоколориметр КФК-2-УХЛ 4.2.
3.2.3. Визначення розчинності
Розчинність НПС в уайт-спіриті визначали згідно методики: наважку НПС (60 ± 001г) завантажують в колбу та додають 40г уайт-спіриту. Колбу закривають корком із вставленим холодильником та нагрівають на водяній бані при температурі 343 353 К протягом 1 2 год при періодичному перемішуванні до повного розчинення смоли. Після цього розчин переливають у циліндр закривають корком і охолодивши до температури 293 К розглядають на світлі. Розчин смоли повинен бути прозорим [84 85].
3.2.4. Визначення сумісності
Сумісність розчину модифікованої НПС з оксидованою олією визначали за такою методикою: змішують 17 г 60 %-го розчину НПС в уайт-спіриті (зваженого з точністю ± 001 г) з 15 г 70 %-го розчину оксидованої соняшникової олії в уайт-спіриті. Ця кількість розчинів забезпечує співвідношення модифікованої НПС та оксидованої олії 1:1. Одержану суміш перемішують при температурі 343 353 К протягом 5 10 хв і виливають у циліндр. Після охолодження до температури 293 К розчин повинен бути прозорим протягом 24 год [86 88].
3.2.5. Визначення температури розм’якшення
Визначення температури розм’якшення проводилося за методом кільця та кульки згідно [86].
3.2.6. Визначення молекулярної маси
Визначення молекулярної маси проводили кріоскопічним методом у бензолі згідно методики [88].
3.3. Фізико–хімічні методи аналізу
Фізико–хімічні методи аналізу дозволяють визначити відразу як якісний так і кількісний склад досліджуваних речовин. При проведенні таких аналізів склад речовин визначають на основі вимірювання якої–небудь фізичної властивості за допомогою хімічної реакції.
3.3.1. Хроматографічні дослідження
Хімічний склад фракції С5-9 а також дистилятів визначали методом ГРХ на хроматографі фірми Carle Erba 4100-01Nhp тип 3390A. Детектор ДП. Стальні капілярні колонки типу OV-1(BP-1) з нерухомою фазою:
- сквалан; довжина колонки 100 м діаметр 025 мм; газ-носій - азот; температура колонки 323 398 К температура випарника 493 К; обєм проби 02 мкл;
- феніловий ефір OS-124; довжина колонки 50 м діаметр 025 мм; газ-носій - азот; температура колонки 373 438 К температура випарника 493 К; обєм проби 02 мкл [84 87].
Літературний огляд.docx
РЕАКЦЙНОЗДАТНИХ КАРБОКСИЛВМСНИХ ОЛГОМЕРВ
1.Вихідна сировина для синтезу карбоксилвмісних олігомерів
Різноманітні галузі промисловості України споживають велику кількість дорогих та дефіцитних продуктів природного походження тому їх заміна на дешеві та доступні синтетичні аналоги має важливе народногосподарське значення. Серед синтетичних замінників на даний час широке застосування отримали низькомолекулярні нафтополімерні смоли (НПС) які одержують з дешевої нафтохімічної сировини вуглеводневих фракцій рідких продуктів піролізу (РПП) або крекінгу нафти (РПК) продуктів її переробки чи газу [1].
Більшість нафтополімерних смол - тверді аморфні термопластичні продукти з молекулярною масою 500-2500 температурою розмякшення 70-150°С. Випускають також в'язкотекучі нафтополімерні смоли (молекулярною масою біля 300). Високоякісні нафтополімерні смоли безбарвні або ледь жовтуваті їх колір мало змінюється при нагріванні. Густина смол 093-11 гсм3 зольність світлих НПС не перевищує 01% темних-1% число омилення і кислотне число не перевищує 1-2 йодне число в інтервалі 15-300 [2].
Завдяки збільшенню потужностей піролізних установок утворюється велика кількість РПП кваліфіковане використання яких є необхідною умовою для забезпечення рентабельності та безвідходності етиленових в-в. Вихід РПП в залежності від сировини та режиму процесу піролізу становить 20 40 %. Для синтезу НПС економічно доцільним є використання сировини що містить не менше 30 % мас. ненасичених реакційноздатних вуглеводнів – смолоутворювальних компонентів. Використання РПП для одержання НПС дозволяє суттєво покращити техніко–економічні показники етиленових установок і понизити собівартість етилену на 20 30 % [34].
РПП є сумішшю великої кількості насичених і ненасичених вуглеводнів С5-С14 [5]: ациклічних і аліциклічних алкенів та дієнів (ізопрен диметил–бутадієн ЦПД ДЦПД піперилен тощо) ароматичних (бензол толуол ксилоли) вінілароматичних (стирол метилстироли вінілтолуоли інден метиліндени) конденсованих (нафталін аценафтен флуорен фенантрен антрацен) тощо. РПП поділяють на піроконденсат або ЛПС що википає до температури 473 К та ВПС що википає при температурі вище 473 К [3]. ЛПС має густину 810 - 920 кгм3 вуглеводневий склад (% мас.): 45-70 ароматичних 20-65 парафінових і 5-12 нафтенових при цьому вміст стиролу та його гомологів складає 60-80. З ЛПС виділяють наступні фракції: С5 бензол-толуол-ксилольну чи бензол-толуольну С8–С9 або С9. З ВПС виділяють такі фракції як: нафталіновий концентрат алкілнафталінову аценафтенову флуоренову й антрацен-фенантренову [6].
Для одержання світлих НПС використовується найбільш легка частина РПП - ЛПС або окремі фракції що мають більш вузький інтервал температури кипіння: фракція С5 (303 - 343 К) фракція С5-С9 (303 - 473 К) фракція С8 (403 - 423 К) фракція С8-С9 (403 - 473 К) фракція С9 (423 - 473 К) Оскільки фракція С6-С7 (343 - 403 К) містить небагато дієнів (3 5 % мас.) переважно аліфатичного складу то для в–ва НПС її не застосовують [7].
Всі нафтополімерні смоли класифікують за типом сировини з якої вони отримані. Виділяють:
аліфатичні смоли С5. Смоли отримані полімеризацією фракції С5 що в основному складається з піперилену циклопентадієну ізомерних пентенів і пентанів.
ароматичні смоли С9. Смоли отримувані з фракції С8 — С10 переважно з С9. Основними мономерами тут є стирол α-метилстирол ізомерні вінілтолуоли індени.
смоли на основі дициклопентадієна (ДЦПД). х отримують з технічного ДЦПД сумішей ДЦПД з вищеописаними фракціями або з фракцій що містять деяку кількість ДЦПД.
комбіновані С5-С9 смоли. Отримують з сумішей фракцій С5 і С9.
модифіковані смоли. Отримують співполімеризацією певних фракцій з деякими компонентами (акриловою к-тою малеїновим ангідридомепоксидними смолами). До цієї ж групи іноді відносять смоли що гідруються після їх отримання [8].
Одержання НПС тісно пов’язане з в–вом КС дефіцит коксохімічної сировини для в-ва яких зумовив одержання на базі нафтохімічної сировини синтетичних НПС [9]. Цьому сприяло освоєння та введення в експлуатацію в–в нижчих олефінів методом піролізу нафтопродуктів які забезпечили доступну та дешеву сировинну базу для синтезу НПС [3-6]. Для таких багатотоннажних етиленових установок розроблені ефективні комплексні схеми що дозволяють повністю використовувати РПП для одержання цінної хімічної сировини [10].
Отримання НПС є одним з перспективних і найменш витратних напрямів в переробці РПП - побічних продуктів нафтопереробки що містять необмежені вуглеводні [11] .
Відомі три основні способи отримання нафтополімерних смол :
Каталітична катіонна полімеризація. Цей спосіб є основним при виробництві нафтополімерних смол у всьому світі. Саме цим способом отримують усі аліфатичні ароматичні і комбіновані смоли. сторично першими каталізаторами були протонні сильні кислоти - сірчана і ортофосфатна. В наш час як каталізатори широко використовуються апротонні кислоти Льюїса - хлорид алюмінію фторид бору і комплекси на їх основі. Процес ведеться при температурах 0 – 100°С. Тиск атмосферний або дещо підвищений. Окрім реакційної стадії технологія включає стадію осушення сировини стадію дезактивації і відділення каталізатора і стадію виділення смоли з реакційної суміші. Розробляється нове покоління імобілізованих каталізаторів що є кислотами Льюїса нанесеними на твердий носій (силікагель оксид алюмінію гетерополікислоти катіонообмінні смоли).
Термічна радикальна полімеризація [8]. Технологія процесу термічної полімеризації дуже проста і дозволяє одержувати НПС для різних галузей промисловості [12]. Спосіб полягає у витримці реакційної маси при температурі 230-280°С під тиском до 20 атм впродовж 4 - 8 годин. Має обмежене застосування і використовується тільки для виробництва смол на базі ДЦПД [8]. До недоліків процесу варто віднести низький вихід смол довгу тривалість реакції у порівнянні з каталітичною полімеризацією необхідність застосувння високих температур (вище 473 К) і тиску а також менш темніший колір смоли [12].
ніційована радикальна полімеризація [8]. При радикальній полімеризації реакція ініціюється вільними радикалами. Вільні радикали можуть утворюватися під дією тепла (термічна полімеризація) при поглинанні світлової енергії (фотохімічна полімеризація) під дією іонізуючого випромінювання: α- - γ- або інших частинок високої енергії (радіаційна полімеризація) а також під впливом хімічних ініціаторів які здатні розпадатися з утворенням вільних радикалів (ініційована полімеризація) [6]. Процес ініційованої полімеризації проходить при нижчій у порівнянні з термічною полімеризацією температурі і дозволяє одержувати смоли світлішого кольору. Технологічна схема процесу ініційованої полімеризації сировини багато в чому аналогічна схемі термічної полімеризації відмінність полягає у додатковому вузлі збереження і дозування ініціатора. До недоліків процесу варто віднести пожежо- і вибухонебезпечність ініціаторів що застосовуються у виробництві підвищену тривалість полімеризації і відносно невисокий вихід НПС [12].
Великий інтерес до НПС визначається не лише їх високою якістю і різноманітними властивостями але і значними ресурсами нафтової сировини які можуть бути використані у виробництві смол а також простотою процесів їх отримання що обумовлює їх дешевизну і низьку собівартість.
Щодо джерел сировини для виробництва НПС не можна не згадати про продукти термічного крекінгу а саме про крекінг-бензин у складі якого містяться неграничні вуглеводні аліфатичного і циклічного рядів а також алкеніл - і алкіл - ароматичні. Слід згадати і про продукти каталітичного крекінгу що проводиться зокрема у присутності алюмосилікатних каталізаторів [11].
Варто відзначити що питанням синтезу в–ва й застосування НПС приділялося багато уваги. Так наприклад створення в–в НПС на теренах колишнього Радянського Союзу започатковане ще в 30-і роки ХХ ст. зокрема роботи Зелінського Н. Д. - отримання рідкої смоли при пропусканні ацетилену над активованим вугіллям і Потоловського Л. А. - синтез важкої НПС при очищенні продуктів піролізу сульфатною кислотою [5].
На початку 60-х років нститутом горючих копалин АН СРСР розроблена комплексна схема переробки ЛПС і ВПС яка дозволила отримати ряд цінних нафтохімічних продуктів у тому числі НПС [13] а нститутом хімії Уральської філії АН СРСР запропоновано метод полімеризації ЛПС і комплексна схема переробки смол піролізу в присутності фтороводню в темні та світлі НПС [14].
У подальшому були розроблені та впроваджені процеси отримання світлих смол: Арсолен [7] (ВНДКТ НХО) СПП (НХП АН АзРСР НД –Сланці) [8] Арієн (НХП АН АзРСР) [16] Піропласт-2 (ВНДКТ НХО Черкеське ХВО) [17 18] Піропласт-5 [19] Піропласт-59 [20] Піропласт-2У [21] Стирилен та нділен (ВХН ВВХН) [22 23]. Створені технології в–ва темних смол: СС (НД -Сланці- ВХН ВВХН) зопласт-3 Піропласт (ВНДКТ НХО) [24] а також смол СП (НХП АН АзРСР НД -Сланці-) [3 5 7].
ВПС складається з суміші конденсованих алкіл- і алкенілароматичних вуглеводнів з двома та більше циклами олігомерів і деякої кількості асфальтенів й ВМС. ВПС має густину 1000-1140 кгм3 молекулярну масу 276 –334 коксованість 98-224 % містить біциклічні трициклічні та поліциклічні ароматичні вуглеводні - 51-67 % а також смоли й асфальтени 24-39 % [25-27]. У ВПС є велика кількість висококиплячих вуглеводнів з алкільними замісниками в тому числі конденсованих. Це дає можливість оцінити її як можливу сировину для в-ва синтетичних продуктів – темних нафто полімерних смол ТНПС [6 28] та пластифікаторів [29 30] що в свою чергу дозволяє підвищити техніко-економічні показники піролізних установок. ВПС містить також різні полі-циклоарени і є сировиною для виробництва технічного вуглецю НПС.
Синтезовано НПС з гідроксильними групами (НПСГ) на основі фракції С9 а також НПСГ модифіковані малеїновим ангідридом. Встановлено оптимальні параметри синтезу таких продуктів.
На основі НПСГ та промислової епоксидної смоли ЕД-22 синтезовані блок-співполімери що можуть знайти застосування для одержання захисних і протикорозійних покриттів для металу.
Нафтополімерні смоли з гідроксильними групами синтезовані з дешевої та доступної сировини можуть знайти застосування як компоненти полімерних композицій що широко використовуються в різноманітних галузях промисловості [31].
Проведення подальших поглиблених досліджень в області отримання НПС на основі продуктів переробки нафти удосконалення існуючих процесів використання закінчених у цьому напрямі нових робіт в промисловості є таким чином одним з перспективних і важливих завдань на сучасному етапі розвитку нафтопереробки і нафтохімії [11].
1. 1. Каталітична олігомеризація
У сьогоднішній час в світовій практиці реалізуються як напрям модифікації природних олігомерних продуктів так і спрямований синтез синтетичних матеріалів. Найбільше поширення отримали способи радикальної олігомеризації в яких усунені стадії відділення ініціатора. Проте вони вимагають або високих температур при термічному способі або наявності нестабільних ініціаторів - при ініційованому. При цьому не досягаються високі виходи цільових продуктів і потрібна додаткова переробка вуглеводнів що не прореагували. Частково вищезгадані проблеми вирішуються при реалізації способу іонної олігомеризації з використанням AlCl3 і його комплексів раніше широко представленого в промисловості [32].
Проте сухий алюміній хлорид важко дозувати і неможливо застосовувати в неперервному процесі. Крім цього безводний хлорид алюмінію взаємодіючи з вологою повітря легко гідролізується в результаті чого знижується його каталітична активність і утворюються скупчення. В процесі гідролізу проходить також виділення газоподібного хлороводню що викликає підвищену корозію апаратури і погіршує умови праці. Значно зручніше використовувати хлорид алюмінію в вигляді рідких комплексів з ароматичними вуглеводнями. Такі комплекси легше зберігати і дозувати крім цього вони легко утворюють емульсії з реакційною сумішшю що робить їх більш активнішими ніж хлорид алюмінію. Проте хлорид алюмінію дуже погано розчинний в ароматичних вуглеводнях (менше 1%) і рідкі комплекси AlCl3 з ароматичними вуглеводнями утворюються тільки в присутності таких сполук як хлороводень вода або хлоралкани. Додавання води сприяє утворенню комплексу тільки до певного співвідношення Н2О і AlCl3 подальше збільшення кількості води приводить до поступового розкладу комплексу і при мольному співвідношенні води 1:1 проходить повний його розклад. Тому при проведенні каталітичної полімеризації в присутності AlCl3 дуже важко правильно готувати каталітичний комплекс [5].
Каталізаторами є речовини що володіють електроноакцепторними властивостями. х можна поділити на такі основні групи: протонні кислоти (кислоти-солі Льюїса) - H3PO4 H2SO4 HCl HF апротонні кислоти (каталізатори Фріделя-Крафтса) - AlCl3 BF3 AlBr3 FeCl3 SnCl4 T алкілпохідні металів змінної валентності та галогенпохідні (каталізатори Циглера- Натта) - R3Al-TiCl4 R2Zn-AlCl3 AlCl3-R3Al-TiCl4 [5 23 33].
Хлорид алюмінію характеризується наступними перевагами з іншими каталізаторами процесу полімеризації фракцій продуктів піролізу він доступний і має невисоку вартість забезпечує високий вихід цільових продуктів і швидкість полімеризації дозволяє використовувати в якості вихідної сировини продукти піролізу з широкими межами кипіння і отримувати тугоплавкі смоли [5].
Проте і цей спосіб вимагає стадії приготування комплексу і стадії його утилізації по закінченні процесу. Для ефективного завершення процесів іонної полімеризації потрібне використання сполук при взаємодії з якими компоненти каталітичного комплексу переходять в неактивний стан.
Для досягнення поставленої мети вирішувалися наступні завдання
- розроблений спосіб олігомеризації ароматичних і циклоаліфатичних висококиплячих фракцій РПП з використанням каталітичних систем на основі TiCl4 і Al(C2H5)3 Al(C2H5)2Cl Al(C4H9)3
- підібрано прийнятні умови процесу олігомеризації з використанням каталітичних систем на основі TiCl4 і Al(C2H5)3 Al(C2H5)2Cl Al(з-C4H9)3
- встановлено механізм протікання процесу дезактивації каталітичних систем оксидами олефінів і структури отриманих продуктів методами Ч (інфрачервоної) та ЯМР 1Н- спектроскопії (спектроскопія ядерно-магнітного резонансу).
- встановлені зв'язки між основними параметрами процесу властивостями олігомерів і покриттів на їх основі.
- запропонований спосіб дезактивації каталітичних систем оксидами олефінів що дозволяє усунути стадії центрифугування відстоювання сушки.
Олігомеризація з використанням даних каталітичних систем протікає в гомогенному середовищі що дозволяє точно контролювати параметри проведення процесу і відповідно отримувати смоли потрібної якості. Дослідження що проводяться в даному напрямі дозволяють створити теоретичні передумови для виробництва НПС що забезпечує високу технічну і екологічну ефективність процесу. Також запропонований спосіб безвідходної дезактивації каталітичних комплексів. Спосіб також усуває утворення осмолених вод і шламів.
Встановлено що активність каталітичних систем TiCl4 з різними алюмінійорганічними сполуками залежить від співвідношення стиролу та ДЦПД у досліджуваних фракціях.
Уперше досліджена залежність фізико-хімічних властивостей олігомерів від виду оксиду олефіну. Визначені оптимальні співвідношення каталізатор : дезактиватор для отримання смол з покращеними характеристиками.
Отримані результати є теоретичною основою для створення безперервного безвідходного виробництва синтетичних вуглеводневих олігомерів з використанням каталітичних систем на основі TiCl4 і алюмінійорганічних сполук.
Розроблена принципова технологічна схема неперервного виробництва вуглеводневих олігомерів з РПП
Принципова технологічна схема виробництва НПС з використанням каталітичних систем на основі тетрахлориду титану і алюмінійорганічних сполук.
-реактор полімеризатор-дезактиватор; 2 - підігрівач; 3 - відгінна колона; 4 повітряний холодильник; 5 - холодильник; 6 - збірка-відстійник; 7-збірник розплаву НПС.
I - початкова сировина РПП; II - каталітичний комплекс; III - розчин оксидів олефінів; IV - водяна пара; V - відгін; VI - смола на розчинення або на грануляцію.
Найбільш світлими є НПС отримані з використанням оксиду пропілену (ОП) в якості дезактиватора каталітичної системи тоді як найбільш темний колір мають смоли отримані із застосуванням епіхлоргідрину (ЕПХГ).
Використання гліцидилових ефірів призводить до продуктів з підвищеним кольором в порівнянні з ОП причому істотної різниці між НПС з феніл-гліцидилового (ФГЕ) і з бутил-гліцидилового (БГЕ) ефірів практично немає [32].
Раніше для дезактивації катіонних каталізаторів застосовувалися водні розчини гідроксидів лужних металів або аміаку після чого було потрібним розділення емульсій видалення солей і води з отримуваного олігомеру. Ці операції надзвичайно трудомісткі і приводять до втрати олігомеру і утворення забруднених осмолених вод [33].
Розроблена технологія виробництва ароматичної НПС з кубових залишків ректифікації бензолу (КОРБ) з використанням комплексного каталізатора на основі хлориду алюмінію. Вихід продукту складає 55% від КОРБ. Решта - легкі і важкі ароматичні розчинники. Легкий розчинник використовується для отримання оліфи.
Технологія допускає наступні стадії виробництва НПС : приготування каталізаторного комплексу полімеризація (безперервний процес) нейтралізація промивання і розділення реакційної маси атмосферний і вакуумний відгін важких розчинників сушка і гаряча фільтрація НПС. Час стадії полімеризації 10-15г температура 600-620 °С.
Оліфу отримують розчиненням НПС в атмосферному відгоні з добавками ксилолів. В результаті виходить прозора оліфа без сторонніх включень з наступними показниками: "сухий залишок" = 543% в'язкість за ВЗ-4 (віскозиметр-4) - 18 сек. колірність ~115 мг J2 100см3 міра висихання до міри 3 - 16 годин. Оліфа сумісна з оксидованими рослинними оліями плівка на її основі прозора без сторонніх включень [34].
Розроблений спосіб селективного отримання темних нафтополімерних смол (ТНПС) що мають високі депресорні властивості за допомогою окислення важкої піролізної смоли (ВПС) киснем повітря у присутності солей жирних кислот кобальту і марганцю.
Запропоновано наукове обгрунтування депресорних властивостей ТНПС отриманих у присутності кобальтової і марганцевої солі жирних кислот за рахунок утворення в їх складі смол і асфальтеноподібних компонентів з гідроксильними і карбонільними групами.
Отримані за розробленим способом ТНПС можуть бути використані для зниження температури застигання нафти і нафтопродуктів і запобігання утворенню опадів високомолекулярних з'єднань ВПС в технологічному устаткуванні і трубопроводах.
Ефект отриманих присадок (зниження утворення осаду і температури застигання) на основі продуктів окислення ВПС був підтверджений випробуваннями в лабораторних умовах на нафті Західного Сибіру (родовища «Арчинское» «Соболиное» «Дуклинское») що розрізняються груповим складом і температурою застигання.
Було показано що збільшення температури синтезу і введення каталізатора приводить до росту температури розм'якшення і молярної маси продуктів окислення ВПС. Максимальна температура розм'якшення і молярна маса продуктів окислення були досягнуті для зразків отриманих у присутності кобальтової солі при температурі синтезу 220 °С і його тривалості 35 години.
Зі збільшенням температури синтезу відбувається збільшення вмісту кисню в ТНПС (до 245 % у присутності каталізатора) при цьому в Ч- спектрах спостерігається збільшення інтенсивності смуг гідроксильної (3500 - 3400 см-1) і карбонільної (1710 - 1700 см-1) груп. Особливо інтенсивно відзначається накопичення кисневмісних компонентів в зразках ТНПС отриманих у присутності кобальтового каталізатора.
Для синтезованих ТНПС був встановлений груповий склад. ТНПС отримані у присутності каталізаторів характеризуються великим вмістом смол і асфальтеноподібних компонентів в порівнянні з початковою ВПС або зразками синтезованими без каталізаторів. Вміст смол і асфальтеноподібних компонентів в зразках отриманих у присутності каталізаторів збільшується в 2 - 3 рази в порівнянні з початковою ВПС [35].
У Росії є значні ресурси піпериленової фракції та піперилену [36] що є побічним продуктом в-ва синтетичного каучуку. Практичний інтерес представляє одержання на їх основі розчинних полімерів які є цінними ВМС. Піперилен - реакційноздатний мономер полімеризація якого в залежності від умов проведення реакції сприяє одержанню продуктів з різними фізико-хімічними характеристиками. Олігомеризація піпериленової фракції в присутності комплексних каталізаторів на основі хлориду алюмінію досліджена у роботі [37]. Олігомеризацію проводили використовуючи гомогенні і гетерогенні каталізатори: моноетилалюмінійхлорид комплекс Густавсона (HCl-2AlCl3-3C6H5CH3 C2H5-AlCl2) та безводний хлорид і бромід алюмінію нанесені на силікагель марки КСК шляхом адсорбції з газової фази . Проведені дослідження показали що на таких каталізаторах отримують олігомери піперилену лінійної будови з молекулярною масою 450-500 що задовільняють вимоги як замінника олій для лакофарбової промисловості [38].
Недоліком таких каталізаторів є їх дороговизна та потреба у додатковій стадії - приготування каталітичного комплексу що зумовлює підвищення собівартості НПС.
З протонних кислот до нашого часу достатньо широко застосовували Н2SO4. Проте при полімеризації в присутності Н2SO4 як правило погіршується колір отриманих НПС і вона значно ускладнюється труднощами видалення з полімеризату високомолекулярних сульфокислот та ефірів які сприяють утворенню стійкої емульсії. Тому не зважаючи на високий вихід смол (34-40% в розрахунку на сировину) від використання Н2SO4 при полімеризації відмовились [10].
1.2Термічна олігомеризація
Термічна полімеризація (олігомеризація) олефінів – бімолекулярна реакція що протікає по радикально-ланцюговому механізму : під впливом температури проходить активація молекули олефіну і вона дисоціює на гідроген і радикал останні пізніше приєднуються по місцю подвійного зв’язку до недисоційованої молекули олефіну [10].
Перші роботи по синтезу НПС термічною олігомеризацією фракцій РПП проводились в НХП АН АзРСР; дещо пізніше на основі ВПС у НД – «Сланці» ВХН і ВВХН одержали СС [6 24].
Відомий спосіб отримання світлих НПС термічною полімеризацією ненасичених вуглеводнів продуктів піролізу газу і бензину в присутності низькомолекулярного полімеру що містить 40-45 % ДЦПД ланок при температурі 200-250 °C і тиску 04 - 08 МПа протягом 6 годин. Недолік даного способу полягає в необхідності проведення процесу при високій температурі і тиску.
Відомий також спосіб отримання світлих НПС термічною полімеризацією ненасичених вуглеводнів продуктів піролізу нафтової сировини при 225 – 235°С протягом 6-7 годин під тиском 08 МПа з попередньою термообробкою при 140 – 160 °С протягом 15 – 20 годин. Даний спосіб також має недоліки : необхідність проведення реакції в автоклаві і достатньо висока температура процессу [39].
У ВНДКТ НХО (Росія) розроблений процес одержання НПС Піропласт-2 термічною олігомеризацією фракції С8-С9 який промислово реалізований на Черкеському ХВО (Росія). Олігомеризацію здійснюють при температурі 518 528 К і тиску 08 10 МПа протягом 6 8 год [40 41].
Там же у тих самих умовах але вже на основі фракції С9 РПП бензину синтезована НПС Арсолен [7]. Використання фракції С9 на відміну від фракції С8-С9 дає змогу зменшити при олігомеризації тиск від 10 12 до 06 08 МПа. З огляду на те що смолу Арсолен використовують як замінник олій у лакофарбовій промисловості на АТ «ЛиНОС» (м. Лисичанськ Луганська обл.) налагоджений випуск 60 %-го розчину НПС у гасовій фракції (Піропласт-2У) [40 42]. Для збільшення виходу НПС фракцію С9 олігомеризують у присутності 15 30 % мас. рідких олігомерів одержаних після дистиляції олігомеризату [43] 2 20 % мас. кубових залишків ректифікації стиролу [44] або 5 257 % мас. кубових залишків розкладу диметилдиоксану («зеленого масла») [45].
Використовуючи фракцію С5 РПП бензину там же синтезована НПС Піропласт-5 [46] та на основі фракцій С5 і С9 коолігомерна НПС Піропласт-59 [20]. Процес одержання даних смол двостадійний. НПС такого типу можна використовувати для зменшення витрат олій у в–ві лакофарбових матеріалів [47–49] а також як пом'якшувачі при в–ві гуми для зменшення витрат КС [50].
Технологія процесу термічної полімеризації достатньо проста і дозволяє отримувати світлі НПС для різних галузей промисловості. До недоліків процесу варто віднести більш низький вихід смол та більшу тривалість реакції в порівнянні з каталітичною полімеризацією необхідність застосування відносно вищих температур і тиску [10].
1. 3. ніційована олігомеризація
Значну увагу дослідники приділяють одержанню НПС радикальною коолігомеризацією у присутності ініціаторів що дає можливість одержувати світлі смоли з високим виходом а також смоли з функціональними групами що значно розширює сфери їх використання [51].
З метою зменшення температури процесу покращення фізико–хімічних характеристик та збільшення виходу НПС олігомеризацію вуглеводневих фракцій проводять у присутності ініціатора. Як ініціатори олігомеризації застосовують такі класи органічних сполук : пероксиди гідропероксиди азо- чи діазосполуки поліфункціональні пероксиди та окисно-відновні системи.
З метою пошуку ефективного ініціатора олігомеризації вуглеводневих фракцій досліджена ціла низка пероксидних сполук. Наприклад у праці [52] подані результати олігомеризації алкенілароматичних мономерів фракції 393-473 К смоли піролізу газів і окислювального піролізу бензину з використанням наступних ініціаторів: ПТБ (пероксидитретбутил) пероксид бензоїлу пероксид ізопропілбензолу гіпериз гідропероксид 11-дифенілетану динітрил азо–біс–ізомасляної кислоти (диніз) моногідропероксид диізопропілбензолу (витрата ініціатора 1 % мас. на сировину). Показано що температура 353 393 К тривалість 40 70 год та концентрація ініціатора 01-2 % мас. забезпечує конверсію мономерів – 50-75 %. Використання бінарних систем ініціаторів наприклад суміші ПТБ і гіперизу а також подача їх в систему частинами пришвидшує процес олігомеризації та сприяє більш глибокій конверсії мономерів яка досягає 95 %.
У промисловості для в-ва НПС широко застосовують гіпериз. Зокрема в НХП АН Азербайджану разом з НД «Сланці» (Росія) на основі стиролвмісної фракції С8 з використанням гіперизу розроблена технологія одержання смоли СПП. Для синтезу цієї смоли можна також використовувати алкенілароматичну фракцію С8-С9. Олігомеризацію здійснюють при температурі 473 К і тиску 02 06 МПа протягом 12 год. у присутності 3 % мас. гіперизу. В-во смоли здійснюється на Бакинському заводі «Нафтогаз» (Азербайджан) [3 6] за аналогією одержують олігостирольну смолу на ВО «Сланцехім» (Росія) з додаванням до сировини стиролу (до 20 % мас.) [53].
Досліджені методи та вивчені кінетичні закономірності синтезу НПС з піролізної фракції С9 нафтопродуктів також методом Ч- спектроскопії підтверджена їх будова. Вивчені властивості гумових сумішей модифікованих отриманими НПС.
В даний час у виробництві шин та гумотехнічних виробів у якості підвищувача клейкості гумових сумішей застосовується каніфоль соснова та каніфоль талова. Соснова каніфоль є дефіцитним продуктом з високою ціною. Талова каніфоль практично не забезпечує потрібну конфекційну клейкість гум погіршує технологічні властивості гумових сумішей призводить до їх залипання на устаткуванні утруднюючи технологічний процес збирання шин. Тому проблема створення замінювачів каніфолі актуальна в даний час.
Як ініціюючі системи в радикальній полімеризації для зниження пожежо- і вибухонебезпечності процесу були обрані діазоамінобензол (ДААБ) що виробляється в Україні (м.Шостка завод хімреактивів) та перекис циклогексанону (ЦГ) (виробник ХВС НАН України). Перекис ЦГ одержували «in situ» у фракції С9 при взаємодії перекису водню з ЦГ.
При ініціюванні радикальної кополімеризації діазоамінобензолом отримано НПС що містять вторинні амінні групи котрі дозволяють проводити подальшу модифікацію і таким чином отримувати матеріали з новими властивостями. При ініціюванні процесу полімеризації пероксидом циклогексанону що утворюється «in situ» у фракції при взаємодії пероксиду водню і циклогексанону що робить процес більш технологічним отримано НПС що містять функціональні групи ОН і СООН які дозволяють проводити подальшу модифікацію НПС і відповідно змінювати властивості в необхідному напрямі.
Отримані НПС були використані в якості замінників каніфолі. Проведено порівняльні лабораторні випробування обкладочних шинних гум що містять в якості підвищувачів клейкості каніфоль та зразки НПС отриманих різними методами полімеризації піролізної фракції нафтопродуктів С9.
Порівняльні властивості шинних гум показали що отримані НПС не поступаються за клейкістю та іншими властивостями НПС модифікованих каніфоллю при цьому вони дешевші і перспективніші як замінники каніфолі в якості підвищувачів клейкості для модифікації шинних гум [12].
Розроблено технологію одержання НПС з гідроксильними групами на основі фракції С9 піролізу вуглеводнів з використанням як ініціатора радикальної полімеризації 22'-азо-біс(5-гідрокси-2-метилпентанонітрилу) (АЗП).
Вивчено вплив основних чинників на процес співолігомеризації ненасичених сполук що містяться у фракції С9. Встановлено що оптимальними умовами синтезу НПСГ є: температура 343 К кількість азоініціатора (АЗП) 5 % мас. від вихідної фракції С9 і час співолігомеризації 50 годин.
Розроблено метод одержання НПСГ ініційованою співолігомеризацією фракції С9 зі стиролом. Показано що для одержання таких НПС з гідроксильними групами оптимальний вміст стиролу у сировинній суміші становить 25 % мас. Введення у вихідну фракцію С9 25 % мас. стиролу дозволяє збільшити вихід НПСГ до 45 % мас. при цьому молекулярна маса НПСГ становить 830 гідроксильне число – 550 мг КОНг та ненасиченість 90 %. [31].
Відомий також спосіб отримання НПС ініційованою полімеризацією неграничних вуглеводнів продуктів піролізу нафтової сировини при 180-190°С впродовж 3-35 г у присутності кремнійорганічних пероксидів (наприклад адамантил-1-оксидиметил (третбутилпероксисилану) вихід смоли при цьому складає 46-48%.
До недоліків цього способу відносяться необхідність застосування нових специфічних ініціаторів що генерують вільні радикали при підвищених температурах 180-220°С.
Найбільш близьким до пропонованого є спосіб отримання НПС ініційованою полімеризацією з використанням як ініціатора гіперизу. Полімеризацію проводять при 125-130°С тиску 013-015 МПа впродовж 32-35 г вихід смоли рівний 184%.
Висока тривалість процесу і необхідність використання органічних пожежо- вибухонебезпечних пероксидів є недоліками цього способу.
Поставлене завдання досягається проведенням полімеризації неграничних з'єднань фракції РПП прямогонного бензину з температурою википання 130-200°С у присутності модифікованої смоли отриманої озонуванням НПС (пероксидне число смоли дорівнює 12-18). Проведення процесу вказаним способом дозволяє:
) усунути необхідність використання органічних низькомолекулярних пожежо- вибухонебезпечних пероксидів;
) підтримувати температуру процесу 100-120°С необхідну для розкладання полімерних озонідів;
) проводити процес при атмосферному тиску;
) понизити тривалість процесу до 4-8 годин.
Таким чином використання озонованої смоли як ініціатора полімеризації неграничних з'єднань фракцій РПП дозволяє отримати НПС в м'яких умовах без використання відомих пожежо- вибухонебезпечних пероксидів [54] .
Дослідження ініційованої коолігомеризації алкенілароматичних вуглеводнів фракції С9 дизельного палива засвідчили що найефективнішим ініціатором олігомеризації є монопероксин – суміш 1(1метил1трет бутилпероксиетил)3ізопропілбензолу 1(1метил1третбутилперок–сиетил)4ізопропілбензолу і 113триметил3третбутилпероксиіндану 55] та ПДТБ 56]. Проведені дослідження виявили що на вихід НПС істотно впливає температура реакції тому використання ініціаторів високої термічної стабільності забезпечує одержання НПС із вищим виходом і більшою сумарною конверсією ненасичених вуглеводнів ніж використання ініціаторів меншої термічної стійкості. Процес в–ва НПС ініційованою олігомеризацією фракції С9 впроваджений на ВАТ Оріана (м. Калуш вано–Франківська обл.): температура реакції 473 К тривалість 6 год концентрація ініціатора 1 % мас. Сумарна конверсія мономерів складає 864 % при використанні монопероксину та 889 % у присутності ПДТБ [5758].
Для синтезу НПС можна також використовувати складні системи ініціаторів [59–61] або поліфункціональні ініціатори [62 63]. Такі ініціюючі системи як правило мають більшу термічну стабільність і сприяють утворенню смоли з покращеними фізико-хімічними показниками та сприяють збільшенню її виходу. У працях [64 65] досліджувався синтез НПС у присутності системи ініціаторів: гіпериз - адаманти-1-оксидиметил трет-бутилпероксисилан. Встановлений оптимальний склад ініціюючої системи (1:1) та умови синтезу смоли що включає дві стадії: низькотемпературну (413-423 К 1-3 год) і високотемпературну (455 К 05-1 год) олігомеризацію. Порівняння виходу НПС одержаної при використанні вищезгаданої ініціюючої системи з виходом НПС в присутності окремо взятих ініціаторів засвідчує ефективність її використання для синтезу НПС.
Шляхом ініційованої олігомеризації що містяться у фракції С5 продуктів піролізу переважно дієнових вуглеводнів запропоновано отримувати світлі НПС які можуть бути використані у виробництві паперу і деревоволокнистих плит замість каніфолі і альбуміну. Ринкові умови диктують свої вимоги до впровадження нових наукових розробок : мінімальні капітальні витрати і стислі терміни впровадження висока рентабельність впроваджуваних розробок і ліквідність продукції що обумовлюють мінімальний термін окупності капітальних витрат.
Найбільш адаптованими до ринкових відносин виявилися саме олігомери синтетичні і передусім НПС.
При цьому особливий практичний інтерес представляють процеси отримання на базі рідких РПП нових НПС не лише як замінників рослинних олій і алкідів (для чого в основному і призначається НПС піропласт-2к) але і як дуже дорогих акрилатів в лакофарбових матеріалах що розбавляються водою (водно-дисперсійних) і епоксидних смол в захисних складах. А також фенол-формальдегідних смол у виробництві деревоволокнистих і деревно-стружкових плит.
За екологічно чистою технологією що передбачає ініційовану олігомеризацію ВПС може бути отримана темна нафтополімерна смола для використання як в шинній і гумовій промисловості так і у будівельній індустрії.
Синтез нових НПС таких що відповідають вимогам євро reаch відкриває нові можливості їх застосування у виробництві "зелених" шин а розробка процесу отримання НПС у вигляді нанопорошку свідчить про перспективу їх застосування в нанотехнологіях [66].
2.Одержання модифікованих нафтополімерних смол
НПС при нормальних умовах отримують рідкими або твердими. У більшості випадків температура розмя’кшення твердих НПС знаходиться в межах 323-423 К. Смоли на основі дієнових алкенових циклодієнових фракцій мають більш низьку температуру текучості ніж смоли на основі стирольних та інденових фракцій. Густина НПС знаходиться в межах 1000 - 1140 кгсм3 температура спалаху 413 - 553 К. Зольність НПС не перевищує 03 % мас. – для світлих і 10 % мас. – для темних смол. Для НПС характерна практична відсутність функціональних груп: кислотне число 1 мг КОНг епоксидне число 5 мг КОНг. У залежності від складу вихідних фракцій йодні числа НПС змінюються від 10 до 300 г J2100г. Молекулярна маса НПС зазвичай знаходиться в інтервалі 500-1500. НПС добре розчиняються в ароматичних вуглеводнях скипидарі бутилацетаті частково чи повністю в парафінових вуглеводнях і кетонах не розчиняються у нижчих спиртах. Вони відрізняються високою стійкістю до дії кислот та лугів суміщаються з різними типами ВМС при цьому сумісність визначається хімічною будовою смоли [23].
Загальноприйнятої класифікації НПС не існує їх можна класифікувати у залежності від: походження вихідної сировини; будови ненасичених вуглеводнів які переважають у РПП; методів одержання.
Недоліком НПС є те що вони не містять ніяких функціональних груп крім ненасичених подвійних зв’язків що суттєво обмежує їх подальше застосування у різних галузях промисловості [67].
Покращення характеристик смол можна досягти як в результаті хімічної моди фікації синтезованих олігомерів різноманітними ненасиченими сполуками найчастіше малеїновим ангідридом -ненасиченими багатоосновними кислотами тригліцеридами жирних кислот (рослинними оліями) та ін. [68] так і в результаті модифікації початкової сировини різними мономерами : метилметакрилатом вінілацетатом акриловою і метакриловою кислотами з подальшою співполімеризацією їх з неграничними компонентами фракцій [69]. у тому і в другому випадку модифікація дозволяє ввести в структуру синтезованих олігомерних продуктів активні функціональні групи що надає полімерам ряд нових властивостей : покращені адгезійні і механічні властивості підвищену температуру розм'якшення і можливість подальшої модифікації.
Модифіковані смоли можуть бути отримані як радикальною так і іонною співполімеризацією. Так радикальною співполімеризацією фракції РПП що википає в інтервалі температур 130 190 °С і що містить 50 % неграничних з'єднань з метилметакрилатом під дією гіперизу при температурі 120 °С впродовж 20 30 г отримані полімери з виходом 262 274 % що володіють підвищеною температурою розм'якшення [70]. онна співполімеризація неграничних компонентів фракції С9 РПП прямогонного бензину з метилметакрилатом дозволяє значно скоротити тривалість процесу і збільшити вихід смол [71].
2.2. Модифікація вихідної сировини
Для отримання ефективних замінників продуктів природного походження найбільш перспективним методом є модифікація початкової сировини для синтезу НПС неграничними кислотами їх ангідридами або ефірами.
Співполімеризацією стиролу і ДЦПД з різними мономерами отримані НПС що використовуються у виробництві лакофарбових матеріалів [286972]. Проведена співполімеризація стиролу і ДЦПД присутніх в РПП а також цих же мономерів з гідроксилвмісним низькомолекулярним каучуком бутадієну. Співполімеризацію ініціювали αα'- диоксибензил - пероксидом. Відмінними особливостями αα'- діоксибензилпероксиду є простота отримання пероксиду (взаємодією бензальдегіду з 30 %-м пероксидом водню вихід 90 %) і його низька чутливість до ударів і тертя а також здатність генерувати фенільні і ОН- радикали [73].
Було встановлено що 75 - 139 % толуолу витрачається в процесі олігомеризації ДЦПД і стиролу з гідроксилвмісним низькомолекулярним бутадієновим каучуком. Участь толуолу можна пояснити схемою реакції що включає його взаємодію з радикалами генерованими з пероксиду або з мономерів.
Фенільні або гідрокси - радикали що генеруються пероксидом [73] реагують зі стиролом і далі бензил що утворюється та заміщені радикали приєднуються до циклопентадієну (появу циклопентадієну серед продуктів реакції легко пояснити якщо врахувати що ДЦПД при нагріванні швидко зазнає ретродієнового розпаду [74 75].
Радикал що утворюється взаємодіє з гідроксилвмісним олігомером (ОГ) і потім стає можливий обрив ланцюга при взаємодії з радикалом (легко генерується з розчинника – толуолу при реакції з будь-яким радикалом вказаним в схемі) бензилу.
Отриманий потрійний співполімер використаний у синтезі поліуретану взаємодією гідроксильних груп з поліізоціанатами у присутності дибутилдилаурината олова при кімнатній температурі [76].
Співполімеризацією неграничних компонентів свіжодистильованої ДЦПД фракції з метил і бутилметакрилатом під дією тетрахлориду титану (ТХТ) і каталітичної системи тетрахлорид титану - диетилалюмінійхлорид (ДЕАХ) при температурі 60 °С впродовж 20 30 хв. отримані модифіковані НПС з виходом 27 53 % утворення яких підтверджене Ч-спектроскопією.
Зниження виходу модифікованих смол викликане можливістю утворення нереакційноздатного продукту взаємодії циклопентадієну і акрилового мономеру по реакції Дільса-Альдера [77].
Розроблений спосіб синтезу модифікованих смол що дозволяє в м'яких умовах під дією ТХТ і каталітичної системи Циглера-Натта з високою швидкістю і високою мірою перетворення початкових компонентів фракцій отримувати модифіковані НПС з виходом 37-54 % які по ряду показників значно перевершують немодифіковані.
В якості модифікуючих агентів вибрані ефіри метакрилової і акрилової кислот: метилметакрилат бутилметакрилат бутилакрилат гексилакрилат та ін.
При каталітичній (катіонній) полімеризації активні усі неграничні вуглеводні що входять до складу фракцій РПП тоді як акрилові мономери не здатні полімеризуватися під дією катіонних каталізаторів таких як апротонні кислоти (ТХТ або тетрахлорид олова) або алкілпохідні металів (триетилалюміній діетилалюмінійхлорид). Відомо що ініціаторами багатьох процесів іонної полімеризації можуть виступати донорно-акцепторні комплекси або полімеризація протікає через проміжні стадії їх утворення. У літературних джерелах є відомості про те що метилметакрилат здатний утворювати стійкий комплекс з TiCl4 :
Н2С СС О - - - - - Ti - - - - - OC C CН2
Були отримані комплекси ТХТ і бутилметакрилату (БМА) різного складу і досліджена можливість участі їх в співполімеризації з неграничними з'єднаннями фракцій РПП.
Введення акрилових ланок до складу смол поглиблює забарвлення їх розчинів (200 900 міліграм I2 100 см3 KI) в порівнянні з немодифікованими смолами (60 500 міліграм I2 100 см3 KI). Слід зазначити що використання циклопентадієнових фракцій у співполімеризації або використання ефірів акрилової кислоти (етилакрилату бутилакрилату гектилакрилату) призводить до отримання світліших смол (200 400 міліграм I2 100 см3 KI). Цей же результат досягається при заміні каталізатора ТХТ на каталітичну систему ТХТ-ДЕАХ.
Зразки модифікованих смол на основі фракції С9 представляють олігомерні продукти з молекулярною масою в інтервалі 600-800. Вони характеризуються підвищеною температурою розм'якшення в порівнянні з немодифікованими смолами причому збільшення вмісту БМА у складі початкової фракції і перехід від ТХТ до каталітичних систем ТХТ-ДЕАХ призводить до збільшення температури розм'якшення.
Усі отримані модифіковані НПС сумісні з окисленими рослинними оліями а плівки политі з розчинів синтезованих смол мають більш високу адгезію і еластичність в порівнянні з немодифікованими НПС. Вказані властивості дозволяють використати модифіковані смоли для отримання лакофарбових матеріалів.
Розроблені рецептури пігментованих лакофарбових матеріалів на основі модифікованих НПС і їх композицій з окисленою соняшниковою олією які можуть бути рекомендовані для впровадження в лакофарбовій промисловості [78].
Досліджено закономірності коолігомеризації фракцій С5 і С9 при послідовному додаванні каталітичного комплексу з використанням невеликих кількостей МА. При додаванні в реакційну масу 02 - 05 % мас. МА температура розм’якшення смоли ≥ 373 К. Полімеризацію проводили в присутності інертного газу – аргону при температурі 333 358 К протягом 1 15 год кількість каталізатора – 05 10 % мас. Встановлено що 04 % мас. МА понижує показник кольору смол за йодометричною шкалою (ЙМШ) до 20 40 мг 2100 см3 [79].
Коолігомеризацію МА пропонують проводити також з вуглеводнями С4 нормальної будови чи піпериленовою фракцією в–ва ізопренового каучуку. При цьому МА легко взаємодіє з дієнами утворюючи адукти і перешкоджаючи появі великої кількості побічних маслоутворюючих продуктів.
Замінник каніфолі cмола СК–40 може бути отримана полімеризацією фракції піроконденсату з МА в присутності каталізатора хлориду алюмінію [80].
Співполімеризацією неграничних вуглеводнів фракції С9 РПП з вінілбутиловим ефіром (ВБЕ) під дією каталізаторів ТХТ ДЕАХ і каталітичної системи ТХТ-ДЕАХ отримані модифіковані НПС [81].
Як модифікуючий агент взятий ВБЕ з температурою кипіння 938 °С у кількості 10 %. Перед кожним синтезом мономер очищали дистиляцією.
Співполімеризацію фракції С9 і ВБЕ проводили під дією каталізаторів : TiCl4 TiCl4 - Al(C2H5)2Cl в співвідношенні 1:1 при температурі 80°С тривалістю 180 хвилин. Кількість Al(C2H5)2Cl узята рівною кількості Al(C2H5)2Cl в каталітичній системі TiCl4 - Al(C2H5)2Cl (1:1 моль). Дезактивацію каталізатора здійснювали за допомогою ОП. Виділення смол з реакційної маси проводили видаленням вуглеводнів що не прореагували [82].
Таким чином співполімеризацією неграничних компонентів фракції С9 РПП з в ВБЕ отримані модифіковані НПС вихід яких залежить від типу і концентрації каталізатора і складає 11 - 48 %. Встановлено що використання каталітичної системи TiCl4 - Al(C2H5)2Cl в синтезі модифікованих НПС приводить до максимального виходу за 60 хвилин. Плівки политі з розчинів синтезованих смол мають більш високу адгезію і еластичність в порівнянні з немодифікованими НПС і смолами отриманими з використанням каталізаторів TiCl4 і Al(C2H5)2Cl окремо [81].
2.1.Модифікація нафтополімерних смол
НПС що представляють собою неполярні вуглеводневі олігомери мають обмежену сумісність з полярними полімерами отриманими оксиполімеризацією тригліцеридів жирних кислот. В результаті цього масляно-смоляні композиції утворюють покриття які з часом мутніють. Тому запропоновано замінити немодифіковану смолу на полімерний продукт що містить в складі полярну групу і отриманий співполимеризацією неграничних з'єднань фракції С9 РПП і ВБЕ. Вихід модифікованих НПС значною мірою залежить від умов проведення процесу. В якості каталізатора вибрані TiCl4 у кількості 2 і 5 % і каталітична система TiCl4 що містить і Al(C2H5)2Cl в еквімолярному співвідношенні. Концентрація TiCl4 у каталітичній системі складає 2 і 5 %. Результати дослідження показали що збільшення концентрації TiCl4 сприяє підвищенню виходу модифікованих смол від 1823 % до 3638 %. Заміна TiCl4 на TiCl4 - Al(C2H5)2Cl не дає істотного збільшення виходу проте використання каталітичної системи приводить до утворення смол з покращеними характеристиками: адгезія міцність твердість [83]. Доказом утворення модифікованих смол являється поява смуг поглинання простої ефірної С-О-С групи (1087 см-1) в Ч - спектрі продукту співполімеризації ненасичених з'єднань фракції С9 і ВБЕ.
достатньо багато даних про можливість модифікації НПС малеїновим ангідридом який використовують найчастіше а також α - ненасиченими одно- та багатоосновними кислотами: акриловою метакриливою кротоновою ітаконовою цитраконовою малеїновою фумаровою. Так шляхом модифікації розплаву смоли МА в присутності органічних фосфатів для попередження погіршення кольору смоли отримують смоли з високою температуро- та атмосферостійкістю [68].
Малеїнізація НПС знижує їх окиснюваність. Для повного гальмування окиснення рекомендується обробляти смолу МА (температура процесу 453 - 473 К тривалість - 12 год). Автори роботи [84] вважають що МА приєднується за подвійними зв’язками вихідної НПС запобігаючи таким чином окисненню. Доведено також що для кожної марки НПС здатність до окиснення – різна [85].
Альтернативним і перспективним вирішенням задачі модифікування НПС є озонування [86 87]. Це пов'язано з тим що озон в порівнянні з киснем є енергійнішим окисником здатним з високою швидкістю при низьких температурах селективно реагувати з ненасиченими зв'язками вуглеводневих фрагментів НПС у тому числі і просторово ускладнений ними.
Крім того використання озону дозволяє уникнути утворення великої кількості відходів відділення яких від продуктів реакції і утилізація вимагає великих додаткових затрат [88 89].
Досліджено озонування розчинів циклоаліфатичних НПС в інтервалі концентрацій 10 40 мас. % і температурі 5 60 °С. Показано що в процесі модифікації циклоаліфатичних НПС відбувається збільшення вмісту активного кисню зменшення величини бромного числа характерна наявність подвійних зв'язків збільшення молекулярної маси. Поява полярних груп у структурі НПС призводить до збільшення температури розм'якшення.
Взаємодія озону с ненасиченими фрагментами НПС модифікованої дициклопентадієновою фракцією (НПСДФ) включає ряд послідовних перетворень: 13 диполярне циклоприєднання озону за подвійними зв’зками з утворенням 123 триоксиланів їх розпад на карбонільні сполуки і карбонілоксиди 13 диполярне циклоприєднання з утворенням 124 триоксиланів і продуктів міжмолекулярної взаємодії. [8790]
Збільшення робочої концентрації розчину смол від 10 до 40 мас. % знижує міри озонування (вміст активного кисню) зменшує молекулярну масу і температуру розм’якшення. Зниження температури процесу від 60 до 5 °С не здійснює істотного впливу на степінь озонування але призводить до збільшення молекулярної маси і температури розм'якшення [91].
Озонуванням 10 %-го розчину НПССФ (НПС модифікована стирольною фракцією) і НПСДФ в ксилолі озоно-кисневою сумішшю (витрата О2-О3 - 385 л·г-1 концентрація О3 - 2 об. %) у реакторі барботажного типу при температурі 5 °С і тривалості процесу 20 і 60 хв отримали озоновані НПС (ОНПССФ20 ОНПСДФ20 ОНПССФ60) [87]. Взаємодією НПССФ і НПСДФ з 10 і 20 мас. % МА в розплаві при температурі 180 °С впродовж 4 год отримали малеїнізовані НПС (НПССФМ10 і НПССФМ20). Озонуванням малеїнізованихНПС за наведеною вище методикою отримували комбіновані модифіковані НПС (О60НПССФМ10 і О60НПССФМ20) [92].
Модифіковані НПС характеризуються меншою колірністю а покриття на їх основі володіють властивостями що дозоляють використовувати їх в якості плівкоутворюючих компонентів для економії лакофарбових матеріалів.
Процес модифікації смол за допомогою озоно-кисневої суміші є екологічно чистим зважаючи на використання в якості окислювача - кисню і повної утилізації використаного озону [91].
Модифікація НПС за допомогою озонування дозволить понизити окислюваність смол киснем повітря за рахунок зменшення кількості кратних зв'язків здатна привести до покращення адгезійних властивостей за рахунок введення кисневмісних груп а формування в структурі молекул реакційноздатних груп відкриває можливості подальшої спрямованої хімічної модифікації і спрямованого регулювання цього процесу [88].
Досліджені динамічна в'язкість структурно - механічні властивості і в'язкотекуча стабільність водомасляних емульсій на основі відпрацьованих моторних мастил у присутності невеликих добавок модифікованих НПС. Озоновані і малеїнізовані ароматичні і циклоаліфатичні НПС впливають на міжфазну структуру емульсій як буфери [93].
Здійснюють також модифікацію НПС висихаючими оливами з яких виготовляють оліфи для фарб і будівельних матеріалів. Основна їх перевага полягає в простоті виготовлення економії олій а також здешевленні кінцевого компаунду. Для отримання якісного плівкоутворювача проводять хімічну модифікацію НПС при дії високих температур каталізаторів (ініціаторів) або сумісним окисненням. Наприклад на основі оксидованої олії та модифікованої НПС у присутності гіперизу уайт-спіриту та сикативу одержують оліфу що характеризується незначною тривалістю висихання і підвищеною міцністю плівки [47 94-96].
Використання висихаючих олив особливо таких які містять сполуки зі спряженими подвійними зв'язками [97] сприяє одержанню однорідних композицій. Поширеним є спосіб високотемпературного сплавлення НПС з висихаючими оливами. Одержані продукти рекомендують як зв’язуюче для покриттів з підвищеною атмосферостійкістю стійкістю до корозії та стабільністю властивостей у процесі експлуатації [98-100].
У результаті проведених експериментальних досліджень з аніонної коолігомеризації дієнів і вінілароматичних мономерів з передачею ланцюга на розчинник з використанням модифікованих літійорганічних сполук розроблена високоефективна технологія одержання олігомерів з різною структурою. Здійснено процес модифікації синтезованих олігомерів МА з наступним одержанням на їх основі функціоналізованих олігомерів для використання в клеєвих композиціях антикорозійних покриттях модифікації ЕС тощо [101].
2.2.Синтез нафтополімерних смол з кінцевими функціональними групами
Перспективним є також використання ініційованої олігомеризації фракцій РПП для одержання олігомерів з кінцевими функціональними групами наприклад: епоксидними карбоксильними гідроксильними тощо.
У роботі [102] приведено результати дослідження синтезу НПС з епоксидними групами на основі фракції С9 РПП бензину та дизельного палива з використанням 44-азо-біс-(-23-епоксипропокси(4ціанпентано–нітрилу)). Синтез проводили при температурі 333 363 К протягом 20 60 год та концентрації ініціатора 75 % мас. Одержані НПС з епоксидними групами осаджували петролейним етером та висушували у вакуум–сушильній шафі при температурі 353 К і залишковому тиску 133 266 Па.
Використовуючи вищезгадану сировину у присутності азоініціатора 44-азо-біс-(-4-ціанпентанової) та пероксидиглутарової кислот отримують карбоксилвмісні НПС. Встановлено оптимальні умови синтезу таких смол: температура 343 К тривалість 20 год концентрація ініціатора – 6 % мас. (на вихідну сировину). Створено основи технології їх одержання [103].
На основі фракції С9 РПП бензину та дизельного палива в присутності 22-азо-біс-(-5-гідрокси-2-метилпентанонітрилу) вивчено основні закономірності процесу одержання НПС з гідроксильними групами. Оптимальні умови синтезу таких смол: температура – 343 К тривалість 50 год концентрація ініціатора – 5 % мас.(на вихідну сировину). Розроблено технологію одержання НПС з гідроксильними групами [31]. Показано можливість модифікації таких смол МА – концентрація 1 % мас. (на вихідну сировину) та синтез на їх основі блок–кополімерів які можна застосовувати в композиційних матеріалах.
Незважаючи на те що такі НПС з кінцевими функціональними групами можна синтезувати при невисоких температурах технологія їх одержання має ряд недоліків: чимала тривалість процесу олігомеризації – 20 50 год невисокий вихід смол – 20 27 % мас. До того ж технологія їх одержання передбачає ряд додаткових стадій а саме: синтез ініціатора (його ідентифікація) – ініціатор синтезують з дорогих органічних продуктів що в свою чергу понижує техніко–економічні показники такого в–ва; дистиляція розчинника оскільки запропоновані ініціатори не розчинні у вихідній сировині то для перебігу реакції необхідно застосовувати розчинник.
Підсумовуючи вищесказане функціоналізовані НПС можна класифікувати в залежності від того яка група входить в її склад таким чином (табл. 5).
Класифікація функціоналізованих НПС
Кічура Д.Б. Одержання карбоксилвмісних нафтополімерних смол С9: Автореф. дис. канд. техн. наук: 05.17.04. Держ. ун–т "Львівська політехніка». - Львів. 2003. – 14 с.
Беренц А.Д. Воль–Эпштейн А.Б. Мухина Т.Н. Аврех Г.Л. Переработка жидких продуктов пиролиза.- М.: Химия 1985. -216 с.
Мухина Т.Н. Барабанов Н.Л. Бабаш С.Е. Меньщиков В.А. Аврех Г.Л. Пиролиз углеводородного сырья. - М.: Химия 1987. - 240 с.
Алиев В.С. Альтман Н.Б. Синтетические смолы из нефтяного сырья.- М. - Л.: Химия 1965. - 156 с.
Думский Ю.В. Но Б.И. Бутов Г.М. Химия и технология нефтеполимерных смол. - М.: Химия 1999. - 302 с.
Думский Ю.В. Беренц А.Д. Козодой Л.В. Мухина Т.Н. Нефтеполимерные смолы. - М.: ЦНИИТЭнефтехим 1983. - 65с.
Соколов В.В. Инден–кумароновые смолы.– М.: Металургия 1978. - 215 с.
Думский Ю.В. Нефтеполимерные смолы. М.: Химия 1988. 167 с.
Мухина Т.Н. Лесохина Г.Ф. Гурович Р.Э. Производство бензола.-М.: Госхимиздат 1962. -141 с.
Шиманская Р.И. Плюснин В.Г. Вайсберг Н.С. Использование пиролизной смолы - отхода производства синтетического спирта Химия и технология топлив и масел. -1962. -№9. -С. 34-36.
Оруджов М.Н. Рациональная схема переработки жидких продуктов пиролиза Нефтепереработка и нефтехимия. 1988. № 1. С. 21-24.
Алиев В.С. Алиев С.М. Марданов М.А. Гаджиев Р.К. Касумов К.М. К вопросу рациональной переработки жидких продуктов пиролиза в Азербайджане Сб. тр. ин–та нефтехимических процессов АН АзССР. 1982. №13. С. 221-223.
Думский Ю.В. Беляков М.Е. Сурото А.К. Чередникова Г.Ф. Гринько Л.Б. К вопросу производства нефтеполимерных смол Химия и технология топлив и масел. 1988. №1. С. 68.
Думский Ю.В. Костин Н.И. Беляков М.Е. Разработка и освоение безотходного процесса получения пиропласта–2 в Черкесском ХПО Сб. науч. тр. ВНИКТИнефтехимоборудования. Новые направления использова–ния продуктов нефтепереработки и нефтехимии.– М.: ЦНИИТЭнефтехим 1989. С. 57-62.
Чередникова Г.Ф. Думский Ю.В. Синтез нефтеполимерных смол на базе фракции С5 продуктов пиролиза Сб. науч. тр. ВНИКТИнефтехим –оборудования. Новые направления использования продуктов нефтепере–работки и нефтехимии.– М.: ЦНИИТЭнефтехим 1989. С. 114 -121.
Думский Ю.В. Иволин В. В. Чередникова Г.Ф. Лизунова Т. Ю. Синтез сополимерной НПС пиропласт–59 на базе фракций С5 и С8-С9 Сб. науч. тр. ВНИКТИнефтехимоборудования. Новые достижения в технологии производства продуктов нефтепереработки и нефтехимии. М.: ЦНИИТЭ–нефтехим 1992. - С. 10-14.
Думский Ю.В. Беляков М.Е. Тараканов Г.А. и др. Пуск установки по производству пиропласта-2У заменителя растительных масел Сб. науч. тр. ВНИКТИнефтехимоборудования. Алкилфенольные и нефтеполимерные смолы.– М.: ЦНИИТЭнефтехим 1990. С.14-19.
Коляндр Л.Я. Шустиков В.И. Андреева В.А. Получение смолы «Стирилен» Кокс и химия. 1978. №12. С.29-32.
Жечев С.С. Манеров В.Б. Каверинский В.С. Лившиц Р. М. Применение нефтеполимерных смол в пленкообразующих композициях Лакокрасочные материалы и их применение. 1983. №1. С. 15-20.
Варшавер Е.М. Думский Ю.В. Козодой Л.В Промышленные схемы производства нефтеполимерных смол пиропластов Сб. науч. трудов ВНИКТИнефтехимоборудования. Пластификаторы и воски. М.: ЦНИИТЭ–нефтехим 1978. С.106-111.
Сафиева Р.З. Физикохимия нефти. Физикохимические основы переработки нефти. М.: Химия 1998. 448 с.
Бекиров Т.М. Ланчаков Г.А. Технология обработки газа и конденсата.– М.: Недра 1999. 596 с.
Ковалев Е.Т. Научные основы и технология переработки высококипящих фракций каменноугольной смолы с получением полициклических углеводородов.Харьков: Контраст 2001. 216 с.
Способ получения темных нефтеполимерных смол: А. с. 2158276 РФ МКИ С 08 F 24000 В. Г. Бондалетов С. И. Приходько И. Г. Антонов Л. И. Бондалетова - № 9912448704; Заявл. 22.11.1999; Опубл. 27. 10. 2000. Бюл. № 12. – 4 с.
Грибова Е.В. Моделирование процесса синтеза суперпластификатора на основе тяжелой смолы пиролиза: Автореф. дис. канд. техн. наук: 05.17.08. Полоцкий гос. ун–т. - Новополоцк. 1994. - 20 с.
Имашев Б.У. Разработка технологии переработки смолы пиролиза с получением суперпластификатора: Автореф. дис. канд. техн. наук: 02.00.13. Уфин. гос. техн. ун–т. - Уфа 1999. - 25 с.
Альмаурі Самір Розробка Технології Одержання Нафтополімерних смол з гідроксильними групами : Автореф. дис. канд. техн. наук: 17.09.99. Держ. ун–т "Львівська політехніка». - Львів. 1999. – 21 с.
Фитерер Е. П. Автореф. дис. канд. техн. наук: 05.17.04. Олигомеризация фракций жидких продуктов пиролиза прямогонного бензина под действием каталитических систем тетрахлорид титана – алюминийорганические соединения Томский политехнический университет. - Барнаул. 2006. – 17 с.
Гетьманчук Ю.П. Полімерна хімія: В 3ч.; Ч.2. Йонна полімеризація. – К.: Видавничий центр -Київ. Ун-т 2000. - 160 с.
Копытов М. А. Автореф. дис. канд. техн. наук: 22.10.06. Получение тёмных нефтеполимерных смол и их использование в качестве депрессорных присадок для нефти Томский политехнический университет. –Томск . 2006. – 23 с.
Лонщакова Т.И. Лиакумович А.Г. Перспективы использоваия пиперилена. - М.: ЦНИИТЭнефтехим. 1982. - 54с.
Атаманенко О.П. Нелькенбаум Э. М. Ясман Ю. Б. Сангалов Ю.А. Соколова Н. П. Тайц С.З. Думский Ю.В. Вассерберг В.. Олигомеризация пиперилена и пипериленовой фракции в присутствии комплексних катализаторов на основе хлорида алюминия Нефтехимия. – 1989. – Т. 27 № 1. – С. 87–93.
Способ приготовления катализатора: А. с. 474353 СССР 1975 МКИ B 01 J 1146 В.Б. Копылов В.М. Смирнов А.И. Волкова С.И. Кольцов В.Б. Алесковский – № 187685423–04; Заявл. 22. 01. 1973; Опубл. 25. 06. 1975. Бюл. № 23 - 6 с.
ПатентРоссийскойФедерации Способ получения нефтеполимерных смол Сухов М.С.; Бондалетов В.Г.; Приходько С.И.; Антонов И.Г.; Бондалетова Л.И. Заявл. 13.09.2000; Опубл. 27.12.2001
Думский Ю.В. Технология нефтеполимерных смол термической олигомеризацией фракций продуктов пиролиза углеводородов: Автореф. дис. д–ра техн. наук: 05.17.04. Львов. политех. ин–т. Львов 1992. 45с.
Думский Ю.В. Цахилов З.С. Чередникова Г.Ф. Глуз А.А. Состояние и перспективы производства нефтеполимерной смолы пиропласт2 Лакокрасочные материалы и их применение. 1993. №5. С. 11–12.
Думский Ю.В. Беляков М.Е. Тараканов Г.А. и др. Пуск установки по производству пиропласта2У заменителя растительных масел Сб. науч. тр. ВНИКТИнефтехимоборудования. Алкилфенольные и нефтеполимерные смолы.– М.: ЦНИИТЭнефтехим 1990. С.1419.
Способ получения ненасыщенного олигомерного мягчителя: А.с. 572468 СССР МКИ С 08 F 1000 202 Е.М.Варшавер В.М. Костюченко Л.В.Козодой Ю.В. Думський Н.И.Костин Т.Н. Мухина К.П. Курносов А.Г. Шварц Н.А. Пружанская Н.Я. Васильевых – № 216775805; Заявл. 22. 08. 1975; Опубл. 15. 09. 1977. Бюл. № 34 – 6с.
Способ получения нефтеполимерной смолы: А.с.651009 МКИ С 08 F 24000 Е.М.Варшавер Л.В.Козодой Ю.В.Думський А.Н. Шадрина – № 237772423–05; Заявл. 18. 05. 1976; Опубл. 05. 03.1979. Бюл. № 9 – 8 с.
Способ получения нефтеполимерной смолы: А.с.704949 СССР МКИ С 08 F 24000 Е.М.Варшавер Ю.В.Думский М.В.Кашкина Н.И. Костин А.И Юдаев П.Е. Боруленков – № 234559323–05; Заявл. 12. 04. 1976; Опубл. 25. 12. 1979. Бюл. № 47 – 6с.
Чередникова Г.Ф. Думский Ю.В. Лизунова Т.Ю. Беляков М. Е. Диеновая фракция пиролиза сыръе для получения светлых нефтеполимерных смол Химия и технология топлив и масел 1993. № 2. С. 56.
Лившиц Р.М. Добровинский Л. М. Заменители растительных масел в лакокрасочной промышленности. М.: Химия 1987. 160 с.
Вассерман Л.К. Думский Ю.В. К преодолению дефицита растительных масел Плановое хозяйство. 1990. № 2. С. 123–124.
Каримов Р.Г. Лалаева З.А. Идрисова Т.Ш. Сапунов Г.С. Производство заменителей пищевого сырья для лакокрасочной промышленности на предприятиях Башкортостана в 1960 – 1990 гг. Тез. докл. 12–ой Междунар. конф. по производству и применению химических реактивов и реагентов Химические реактивы реагенты и процессы малотоннажной химии (Реактив – 99). – Уфа 1999. – С. 206 – 207.
Думский Ю.В. Состояние и перспективы развития производства и ассортимента мягчителей защитных восков и смоляных агентов для резин Каучук и резина 1993. № 5. С. 2429.
Магорівська Г.Я. Дзіняк Б.О. ніційована макропероксисиланами олігомеризація фракції С9 піролізу дизельного палива Вопросы химии и химической технологии. – 2003. – № 1. – С. 76–80.
Исмайлов Р.Г. Алиев С.М. Мамедалиев Г.М. Рзаева Ф.Д. Саркисов В.М. Инициированная полимеризация алкенилароматических мономеров фракции 120200 оС смолы пиролиза газов и окислительного пиролиза бензина Химия и технология топлив и масел – 1965. – №3. – С. 410.
Иншаков В.И. Воронков С.Н. Фалалеев Г.А. Опыт освоения и наращивания мощности установки по получению нефтеполимерной лакокрасочной смолы на СПЗ «Сланцы» Нефтепереработка и нефтехимия.– 1983. – №9. – С.23-25.
Способ получения нефтеполимерных смол: А. с. 2191783 РФ МКИ С 08 F 24000 В.Г. Бондалетов Г.Л. Сухих М.В. Кузнецов – № 200111534604; Заявл. 04.06.2001; Опубл. 27.10.2002. Бюл. № 10. - 3 с.
Дзіняк Б. О. Технологія одержання нафтополімерних смол олігомери-зацією фракції С9: Автореф. дис. канд. техн. наук: 05.17.04. Держ. ун–т Львівська політехніка. Львів 1995. 19 с.
Хайр Самер Салім. Технологія одержання нафтополімерних смол співолігомеризацією олефінвмісних фракцій С5 і С9.: Автореф. дис. канд. техн. наук: 05. 17. 04. Держ. ун–т Львівська політехніка.– Львів 1999.– 17с.
Атмаджев В.Е. Интенсификация процесса синтеза соолигомеров на основе бутан–бутиленовой фракции: Автореф. дис. канд. хим. наук: 05.17.04. Волг. гос. техн. ун–т. Волгоград 1993. 22 с.
Ворожейкин А.П. Совместная переработка пиролизной фракции С5 и продуктов двухстадийного дегидрования изопрена: Автореф. дис. канд. техн. наук: 05.17.04. Казан. гос. технол. ун–т. Казань 1994. 26 с.
Но Б.И. Думский Ю.В. Бутов Г.М. Саад К.Р. Синтез нефтеполимерных смол в присутствии сложных систем инициаторов Химия и технология элементоорганических мономеров и полимерных материалов: Межвуз. сб. науч. тр. ВолгГТУ. 1994. С. 8185.
Но Б.И. Бутов Г.М. Мохов В.М. Новые адамантилсодержащие пероксидные инициаторы Тез. докл. V Российской науч.–техн. конф. резинщиков Сырье и материалы для резиновой промышленности.–Москва.– 1998. – С. 176 – 177.
Думский В.Ю. Бутов Г.М. Думский С.Ю. Новые безотходные технологии переработки жидких продуктов пиролиза Тези наук.–техн. конф. Поступ в нафтогазопереробній та нафтохімічній промисловості. Львів. 1999. С. 78.
Бутов Г. М. Пероксидные производные адамантана: синтез свойства и применение: Автореф. дис. д–ра. хим. наук: 05.17.04. Волг. гос. техн. ун–т. Волгоград 1999. 50 с.
Шугурова Н.Н. Антонова Л.А. Григорьев Е.И. Докучаева И.С. Самуилов Я.Д. Лиакумович А.Г. Новые полифункциональные инициаторы радикальной полимеризации: синтез и свойства Тез. докл. Российской конф. с междунар. участием Актуальные проблемы нефтехимии. Москва.– 2001. C. 331.
Саад К.Р. Синтез свойства и применение функциональных кремнийсодержащих с адамантильным радикалом: Дис. канд. хим. наук: 05.17.04. Волг. гос. техн. ун–т. Волгоград 1996. 129 с.
Думский С.Ю. Синтез адамантилсодержащих кремнийорганических пероксидов и применение их в производстве нефтеполимерных смол: Автореф. дис. канд. хим. наук: 05.17.04. Волг. гос. техн. ун–т. Волгоград 1997. 26 с.
Masashiro Ochura Nippon setchaku gakkaishi J.Adhes. Soc. Jap. – 1999. – Vol. 35 № 9. P. 405409.
Думский Ю.В. Чередникова Г.Ф. Кузнецова Н.А. Беля- ков М.Е. Синтез модифицированной нефтеполимерной смол Каучук и резина. – 1988. – № 12. – С. 30–32.
Исмайлов Р.Г. Алиев С.М. Мамедалиев Г.М. Гасанова Ш.И.Сополимеризация алкенилароматических мономеров продук-тов пиролиза с акрилонитрилом винилацетатом и дивинилом Доклады АН Азерб. ССР. – 1968. – Т. 24. – № 1. – С. 11–13.
Шихализаде П.Д. Алиев С.М. Мехтиев С.И. Мурадова М.О.Изучение процесса сополимеризации алкенилароматических углеводородов с эфирами метакриловой кислоты Азербай- джанский химический журнал. – 1977. – № 3. – С. 58–60.
Бондалетов В.Г. Бондалетова Л.И. Акимова Е.В. Сутя- гин В.М. Бондалетов О.В. Синтез модифицированной метил- метакрилатом нефтеполимерной смолы Нефтепереработка и нефтехимия. – 2008. – № 10. – С. 19–24.
Шихализаде П. Д. Изучение процесса сополимери- зации алкенилароматических углеводородов с эфирами метакриловой кислоты П. Д. Шихализаде и [др.] Азер- байджанский химический журнал. – 1977. – № 3. – C. 58–60.
Рахимов А. И. Химия и технология органических перекисных соединений – М.: Химия1979. – 392 с.
Рылова М. В. Взаимодействие дициклопентадиена с элементной серой. Начальные стадии реакции М. В. Ры- лова А. Я. Самуилов Д. Р. Шарафутдинова Ю. Я. Ефре- мов Г. М. Храпковский Я. Д. Самуилов Химия и ком- пьютерное моделирование. Бутлеровские сообщения. –2002. – № 9.
Онищенко А. С. Диеновый синтез А. С. Онищенко. – М.: Изд-во АН СССР. – 1963. – 650 с.
Бондалетов О. В. Сополимеризация жидких продуктов пиролиза и акриловых мономеров. О. В. Бондалетов Л. И. Бондалетова И. В. Тюменцева В. Г. Бондалетов В. М. Сутягин Ползуновский вестник. – 2009. – № 3. – С. 24–28.
Использование циклопентадиеновой фракции жидких продуктов пиролиза в синтезе модифицированных нефтеполимерных смол О.В. Бондалетов Л.И. Бондалетова В.Д. Огородников В.Г. Бондалетов В.М. Сутягин Л.А. Гричневская Известия Томского политехнического университета. – 2010. – Т. 316. – № 3. – С. 77-82 .
Бондалетов О.В. Получение модифицированных нефтеполимерных смол на основе различных фракций жидких продуктов пиролиза углеводородного сырья: Автореф. дис. канд. техн. наук: 11.04.11. Томский политехнический университет. – Томск . 2011. – 25 с.
Зарбов И. Матева В. Кабаиванов В. Полимеризация пироконденсатных фракций С5 и С9 Пластические массы. 1981. № 9. С. 54–55.
Пат. 3890285 США МКИ С 08 F 1502. Pr Заявл. 19. 10. 1973. Опубл. 17. 06. 1975. 8 c.
Бондалетов В.Г. Получение модифицированных винилбутиловым эфиром нефтеполимерных смол на основе фракции С9 В.Г.Бондалетов Л.И.Бондалетова Ю.Б.Варакина Ползуновский весник. 2010. – № 3. С. 148 - 151.
Лившиц М. Л. Технический анализ и кон-трольпроизводства лаков и красок. – М.: Высш. школа. 1987. – 264 с.
Бондалетов В.Г Бондалетова Л.И. Варакина Ю.Б. Получение модифицированных винилбутиловым эфиром нефтеполимерных смол на основе фракции С9 Ползуновский вестник. – 2010. – № 3. – С. 148–151.
Кожанова К.И. Друганова Л.А. Полуйко Е.Г. Окисляемость нефтеполимерных смол воздухом и кислородом. – М. 1976. – 33 с. Деп. в ВНИИВПИЭИлеспром. – 30.05.76. – № 220. – д. 10.
Сухов В.Д. Краснобаева В.С. Делина Е.Н. Ермилова Т.А. Жечев С.С. Каверенский В.С. Манеров В.Б. Окисляемость нефтеполимерных смол молекулярным кислородом Лакокрасочные материалы. 1989. № 2. С. 45–48.
Троян А.А. Бондалетов В.Г. Бондалетова Л.И. Озонирование ароматических нефтеполимерных смол Известия Томского политехнического университета. – 2009. – Т. 315. – № 3. – C. 73–77.
Бондалетов В.Г. Бондалетова Л.И. Троян А.А. Озонирование алифатических нефтеполимерных смол Известия вузов. Хи- мия и химическая технология. – 2003. – Т. 46. – № 2. – С. 43–45.
Разумовский С.Д. Заиков Г.Е. Кинетика и механизм реакции озона с двойными связями Успехи химии. – 1980. – Т. 49. –№ 12. – С. 2344–2376.
Григорьев Е.И. Береснев В.В. Использование озона в химии и технологии синтетического каучука Каучук и резина. – 1999. – № 6. – С 35–41.
Хазова Е.А. Шугурова Н.Н. Григорьева Е.И. Докучаева И.С. Лиакумович А.Г. Самуилов Я.Д. Изменение функціонального состава при озонолизе каучука СКЭПТ Журнал прикладнойхимии. – 2001. – Т. 74. – № 7. – С. 1186–1190.
А.А. Троян В.Г. Бондалетов В.Д. Огородников. Исследование процесса озонирования циклоалифатических нефтеполимерных смол Известия Томского политехнического университета. – 2009. – Т. 315. – № 3. – C. 163–165.
Огородников В.Д. ЯМР спектроскопия как метод исследования химического состава нефтей Инструментальные методы исследования нефти. – Новосибирск: Наука 1987. – С. 49–67.
А.А. Троян В.Г. Бондалетов В.Д. Огородников. Модифицированные нефтеполимерные смолы в образовании и стабилизации водомасляных эмульсий Известия Томского политехнического университета. – 2009. – Т. 315. – № 3. – C. 86–89.
Олифа: А. с. 794051 СССР МКИ С09F 702. Е.М. Варшавер Ю.В.Думский Н.И.Костин Л.В. Козодой Р.А. Мельникова В.К. Сухотин Г.И. Афанасьева В.Ф. Крыжин Р.Ц. Долуханов Е.И. Бемпалов Н.В. Лучнина. - № 265949023–05; Заявл. 06. 09. 1978; Опубл. 07. 01. 1981; Бюл. №1. – 6 с.
Способ получения олифы: А. с. 802343 СССР МКИ С09F 706. К.И. Карасев С.А. Рождественская Г.Н. Далецкая В.Н. Машин А.Г. Кузуб В.И. Цыганов М.В. Курашев А.Е. Шуливейстров. - № 247319423–05; Заявл. 14. 04. 1977; Опубл. 07. 02. 1981; Бюл. №5. – 6 с.
Сорокин М.Ф. Кочнова З.А. Шодэ Л.Г. Химия и технология пленкообразующих веществ.– М.: Химия 1989.– 480 с.
Могилевич М.М. Использование непредельных соединений с сопряженными двойными связями для синтеза пленкообразователей Лакокрасочные материалы и их применение. 1987. №4. С. 8–10.
Способ получения пленкообразующего: А. с.621710 СССР МКИ С09F 706. М.П. Бердников. – № 236816623–05; Заявл. 03. 06. 1976; Опубл. 30. 08. 1978; Бюл. №32. – 8 с.
Способ получения масляно–смоляного лака: А. с. 657050 СССР МКИ С09F 706. М.П. Бердников Г.А. Куклин М.И. Липатников Л.Ф. Подлевских А.Л. Шабалин Н.А. Устюжанинова – № 230854623–05; Заявл. 19. 12. 1975; Опубл. 15. 04. 1979; Бюл. №14. – 8 с.
0. Способ получения масляно–смоляного пленкообразующего: А. с. 704976 СССР МКИ С09F 706. М.П. Бердников Г.А. Куклин Л.В. Обухов.- № 213591523–05; Заявл. 16. 05. 1975; Опубл. 25. 12. 1979; Бюл. № 47. – 6 с.
1.Самоцветов А.Р. Коноваленко Н.А. Полуэктова Н.П. Гусев Ю.К. Олигомеры на основе диеновых и винилароматических мономеров: получение модификация перспективы применения Тез. докл. VII междунар. конф. по химии и физико–химии олигомеров Олигомеры 2000. Пермь. 2000. С.93
2.Гринишин О. Б. Одержання нафтополімерних смол з епоксидними групами: Автореф. дис. канд. техн. наук. 05.17.04. Держ. ун–т Львівська політехніка. Львів. 1997. 17с.
3. Чайківський О. В. Технологія одержання нафтополімерних смол з кінцевими карбоксильними групами: Автореф. дис. канд. техн. наук. 05.17.04. Держ. ун–т Львівська політехніка. Львів. 1999. 18с.
4.СН – 245 – 71. Санитрные нормы проектирования промышленных предприятий – М.: Стройиздат 1972.
5.ОНТП 24 – 86. Определение категорий помещений и зданий по взрывопожарной опасности. – М.: ВНИПО МВД СССР. 1987. -26с.
6.Макаров Г.В. и др. Охран Труда в химической промышленности.- М.: Химия 1989.
7.Правила устройства електроустановок. –М.: Энергоатомиздат 1987.
8.ГОСТ 12.3.002 – 75. ССБТ. Процесы производственные. Общие требования безопасности. – М.: Издательство стандартов 1975.
9.ГОСТ 12.2.003. – 74. ССБТ. Оборудование производственноею Общие требования безопасности. М.: Издательство стандартов 1975.
0.ГОСТ 12.1.010 – 76. ССБТ. Взрывобезопасность. Общие требования. – М.: Издательство стандартов 1977.
1.ГОСТ 12.1.004 – 85. ССБТ. Пожарная безопасность. Общие требования. – М.: Издательство стандартов 1985.
2.СНиП 2.09.02. – 85. Производственные здания. Нормы и проектирования.
3.СН 396 – 74. Указания по расчету рассеивания в атмосфере вредных веществ содержащихся в выбросах предприятий . М.: Стройиздат 1974.
4.Лазарев Н.В. Вредные вещества химической промышленности. – Т.123. – М.: химия 1976.
5.Пожарная опасность веществ и материалов применяемых в химической промышленности : Справочник (Под ред. Рябова В.И.). – М.: Химия 1970.
6.ГОСТ 12.1.011 – 78. ССБТ. Смеси взрывоопасные . Классификация. – М.: Издательство стандартов1978.
7.Захаров Л.Н. Техника безопасности в химической лаборатории. – Л.: Химия 1985.
8.ГОСТ 12.3.020 – 76. ССБТ. Электрооборудование электрозащищенное. Термины и определения. Классификация. Маркировка. – М.: Издательство стандартов 1987.
9.ГОСТ 12.1.009 – 76. ССБТ. Электробезопасность. Общие требования. – М.: Издательство стандартов 1977.
0.ГОСТ 12.1.019 – 79. ССБТ. Электробезопасность. Общие требования. – М.: Издательство стандартов 1987.
1.ГОСТ 12.1.007 – 76. ССБТ. Вредные вещества. Общие требования. – М.: Издательство стандартов 1982.
2.Жидецький В.Ц. Джигерей В.С. Мельников О.В. Основи охорони праці . Навчальний посібник. – Вид. 4-те доповнене. – Львів.
3.СН 396 – 74. Инструкция по проектированию и устройству молнезащиты зданий и сооружений. - М.: Стройиздат 1978.
4.СНиП 2.04.05. 86. Отопление вентиляция и кондиционирование воздуха. Нормы проектирования. – М.: Стройиздат. 1987.
5.СНиП 11 – 4 – 79. Естественное и искусственное освещение. Нормы пректирования. – М.: Стройиздат 1979.
Зведена таблиця мат.балансу.doc
метилциклопентадієни
неідент. ненас. вугл
Табл мат.балансу процесу.docx
неідент. ненас. вугл
Матеріальний баланс.docx
Розрахунок матеріального та теплового балансів процесу ініційованої олігомеризації фракцій С5-С9 потрібний для відтворення загальної картини досліджень яка дає уявлення відносно доцільності наступних конструктивних розрахунків обладнання апаратів та комунікацій дає оцінку економічній ефективності процесу.
Для прикладу матеріального балансу використаємо математичні дані одного із процесів олігомеризації: маса фракції С5-С9 становить 410000 г; маса ініціатора пероксиду дитретбутилу (ПДТБ) - 04100 г як 1 %мас. від даної фракції; маса диалілфталату ДАФ – 61500 г (15%мас. від фракції).
Mфр = Vфр · ρфр = 50 · 0820 = 410000 (г);
Mін = Mфр · Xін = 410000 · 001 = 04100 (г);
Mдаф = Mфр · Xдаф = 410000 · 015 = 61500 (г);
Продукт розпаду ініціатора (100 – 140 °С):
СН3 – С(СН3)2 – ОО – С(СН3)2 – СН3 2СН3 – С(СН3)2 - О
(СН3)2 – С = О + 2СН3
Процес олігомеризації відбувався при температурі 453 К протягом 6-ти год. Одержаний олігомеризат піддавали атмосферній та вакуумній дистиляції.
Продуктивність за сировиною (фракція С5 –С9) становить P = 5000 трік річний фонд робочого часу Z = 8100 год.
Годинна продуктивність:
G = P 1000 Z де 1000 – кількість кг в 1-ій тонні
G = 5000 1000 8100 = 6172839 (кггод).
Кількість вихідної сировини:
Gвих.сир.= 5000 096 = 6430041 (кггод).
Вміст фракції С5-С9 ДАФ та ПДТБ у вихідній сировині:
Gфр = Gвих.вир.· Xвих.сир.; Gфр = 6430041 · 084 = 5401235 (кггод);
Gдаф = 6430041 · 015 = 964506 (кггод);
Gпдтб = 6430041 · 001 = 64300 (кггод).
У перерахунку на об’ємну витрату м3год:
Wфр.= Gфр ρфр.; Wфр.= 5401235 820 = 06587 (м3год);
Wдаф = 964506 1120 = 00861 (м3год);
Wпдтб = 64300 800 = 00080 (м3год);
Сумарна об’ємна витрата реагентів
Wсум. = 06587 + 00861 + 00080 = 07528 (м3год).
Розрахунок об’єму реактора-олігомеризатора необхідного для проведення процесу:
Vр. = (Vг · tг)(mр · φ)
де Vр. – об’єм реактора-олігомеризатора м3;
mр – кількість реакторів-олігомеризаторів;
Vг – годинна продуктивність що дорівнює сумарному об’єму реагентів установки по олігомеризації НПС Vг = Wсум. м3год;
tг – тривалість перебування в апараті год;
φ – об’єм заповнення реактора-олігомеризатора який становить 07.
Vр. = (07528· 6)(2 · 07) = 32263 м3 325 м3;
Зведена таблиця мат.балансу.doc
метилциклопентадієни
неідент. ненас. вугл
Опис технологічної схеми.docx
Процес одержання коолігомерної НПС на основі фракції С5 і С9 зображений на рис. 8 включає такі основні стадії:
димеризація фракції С5;
атмосферна дистиляція вуглеводнів що непрореагували;
коолігомеризація фракції С9 з димерами фракції С5;
атмосферна і вакуумна дистиляція вуглеводнів що не прореагували;
Фракція С5 РПП з установки виробництва етилену поступає в ємність поз. 1 з якої за допомогою насосу поз. 4 через мірник подається в реактор поз. 7 на стадію коолігомеризації. Після завантаження фракції С5 у реактор поз. 7 подачею ВОТ у змійовик при постійному перемішуванні здійснюється нагрів реакційної маси до температури 423 К. При досягненні у реакторі поз. 7 температури 423 К подача ВОТ припиняється. Димеризація вуглеводнів фракції С5 здійснюється протягом 5 год. Реакція екзотермічна. Зняття теплоти реакції здійснюється за рахунок подачі оборотної води в кожух реактора.
Після закінчення реакції димеризат за рахунок надлишкового тиску в реакторі поз. 7 перетискується в колону поз. 8 (обладнану змійовиком та мішалкою) де при атмосферному тиску здійснюють дистиляцію вуглеводнів що не прореагували. Дистиляція здійснюється при температурі куба 418К. Закінчення дистиляції визначається за кількістю і густиною дистиляту що конденсується у холодильнику-конденсаторі поз. 10 і збирається в ємності поз.11. Суміш димерів з кубу колони поз. 8 насосом поз. 9 через мірник подається в реактор поз. 13 (аналог реактора поз. 7) де здійснюється коолігомеризація фракції С9 з олігомерами фракції С5.
Фракція С9 з уcтановки виробництва етилену поступає з ємності поз. 3 з якої подається через мірник на стадію коолігомеризації за допомогою насосу поз. 6. У змійовик реактора поз. 13 подається ВОТ і при постійному перемішуванні здійснюється нагрів реакційної маси. При досягненні в реакторі температури 373 - 393 К з ємності поз. 2 насосом поз. 5 завантажується розчин ініціатора пероксиду дитретбутилу (ПДТБ) та модифікуючого агента диалілфталату ДАФ з ємності поз 15 насосом поз. 14. Реакція коолігомеризації екзотермічна. При досягненні температури 473 К подача ВОТ у змійовик реактора поз. 13 припиняється а подальший ріст температури зупиняється подачею оборотної води в оболонку реактора. За допомогою регулюючих клапанів підтримується необхідна температура процесу в реакторі. Коолігомеризація здійснюється при температурі 473 К і тиску 05 МПа протягом 6 год після чого визначається густина одержаного олігомеризату. При досягненні приросту густини ~ 70 кгм3 процес вважається закінченим. Якщо приріст густини недостатній то процес продовжують до досягнення необхідного його значення.
Рис 4.2. Принципова технологічна схема періодичного процесу виробництва реакційноздатних олігомерів
апарати: 1 2 3 11 15 22 25 ємності; 4 5 6 9 12 14 23 24 27 насоси; 7 13 – реактори; 8 16 апарати для дистиляції; 10 17 холодильники-конденсатори; 19 сепаратор; 20 вакуум-насос;
потоки: фракція С5 ; фракція С9; 50 % розчин ініціатора; V димеризат С5 (димеризат ); V дистилят фракції С5; V димеризат С5 після дистиляції (димеризат ); VII – ДАФ; VIII – олігомеризат фракції С5-С9; IX – реакційноздатні олігомери; – атмосферний дистилят; – вакуумний дистилят; – вакуумний газ.
Після закінчення реакції коолігомеризат перетискується в апарат поз. 16 за рахунок тиску в реакторі поз. 13 де при температурі кубу 493 К здійснюється атмосферна дистиляція непрореагованих вуглеводнів.
Атмосферний дистилят конденсується в холодильнику-конденсаторі поз. 17 і збирається в ємності поз.25. Кінець атмосферної дистиляції визначається за кількістю і густиною атмосферного дистиляту.
Частина атмосферного дистиляту в розмірі 35% повертається в реактор на доолігомеризацію за допомогою насосу поз.24. нша частина атмосферного дистиляту відкачується з установки на розлив за допомогою насосу поз.27. Регуляція потоків атмосферного дистиляту здійснюється за допомогою кранів поз. 21 26.
Після закінчення атмосферної дистиляції в апараті поз. 16 вакуум-насосом поз. 20 поступово створюється вакуум (залишковий тиск 60 кПа) і при температурі кубу 498 К проводиться дистиляція висококиплячих вуглеводнів і низькомолекулярних коолігомерів. Вакуумний дистилят конденсується в холодильнику-конденсаторі поз. 17. При досягненні температури розмякшення НПС 358 - 363 К процес вакуумної дистиляції зупиняють. Конденсат виділяється в сепараторі поз. 19 збирається в ємності поз. 22. Несконденсовані вакуумні гази після очистки викидаються в атмосферу а вакуумний дистилят насосом поз. 23 відкачується з установки на розлив. Співвідношення вакуумного дистиляту до атмосферного становить 12.
Розплав одержаного реакційноздатного олігомеру подається на стадію грануляції і відповідно на пакування та склад готової продукції.
Перевагою даного методу є те що одержані НПС містять в своїй структурі ланки функціональних груп ДАФ що покращує їх властивості. Дане технологічне оформлення процесу у вигляді безперервної технологічної схеми вимагає менших капіталовкладень в порівнянні з безперервною. Особливістю періодичних процесів є те що вони дають можливість краще регулювати технологічні параметри процесів у тих випадках коли доводиться працювати з різною за складом сировиною якими в принципі є фракції С5 і С9.
Серед недоліків слід відмітити наступні: зміна у часі параметрів технологічного режиму періодичної установки погіршує якість продукту; невисока продуктивність; значна тривалість процесів; великі енергетичні затрати повязані з втратою теплоти в періоди завантаження сировини і вивантаження продукту; труднощі з автоматизацією.
Перехід до безперервної схеми виробництва НПС дозволяє усунути недоліки періодичних процесів: забезпечує високу якість кінцевого продукту; стабільність заданого технологічного режиму; дає можливість повністю автоматизувати процес та полегшує працю обслуговуючого персоналу.
3. Матеріальний баланс процесу одержання реакційноздатних олігомерів
Розрахунок матеріального та теплового балансів процесу ініційованої олігомеризації фракцій С5-С9 потрібний для відтворення загальної картини досліджень яка дає уявлення відносно доцільності наступних конструктивних розрахунків обладнання апаратів та комунікацій дає оцінку економічній ефективності процесу.
Для прикладу матеріального балансу використаємо математичні дані одного із процесів олігомеризації: маса фракції С5-С9 становить 410000 г; маса ініціатора пероксиду дитретбутилу (ПДТБ) - 04100 г як 1 %мас. від даної фракції; маса диалілфталату ДАФ – 61500 г (15%мас. від фракції).
Mфр = Vфр · ρфр = 50 · 0820 = 410000 (г);
Mін = Mфр · Xін = 410000 · 001 = 04100 (г);
Mдаф = Mфр · Xдаф = 410000 · 015 = 61500 (г);
Продукт розпаду ініціатора (100 – 140 °С):
СН3 – С(СН3)2 – ОО – С(СН3)2 – СН3 2СН3 – С(СН3)2 - О
(СН3)2 – С = О + 2СН3
Процес олігомеризації відбувався при температурі 453 К протягом 6-ти год. Одержаний олігомеризат піддавали атмосферній та вакуумній дистиляції.
Продуктивність за сировиною (фракція С5 –С9) становить P = 5000 трік річний фонд робочого часу Z = 8100 год.
Годинна продуктивність:
G = P 1000 Z де 1000 – кількість кг в 1-ій тонні
G = 5000 1000 8100 = 6172839 (кггод).
Кількість вихідної сировини:
Gвих.сир.= 5000 096 = 6430041 (кггод).
Вміст фракції С5-С9 ДАФ та ПДТБ у вихідній сировині:
Gфр = Gвих.вир.· Xвих.сир.; Gфр = 6430041 · 084 = 5401235 (кггод);
Gдаф = 6430041 · 015 = 964506 (кггод);
Gпдтб = 6430041 · 001 = 64300 (кггод).
У перерахунку на об’ємну витрату м3год:
Wфр.= Gфр ρфр.; Wфр.= 5401235 820 = 06587 (м3год);
Wдаф = 964506 1120 = 00861 (м3год);
Wпдтб = 64300 800 = 00080 (м3год);
Сумарна об’ємна витрата реагентів
Wсум. = 06587 + 00861 + 00080 = 07528 (м3год).
Розрахунок об’єму реактора-олігомеризатора необхідного для проведення процесу:
Vр. = (Vг · tг)(mр · φ)
де Vр. – об’єм реактора-олігомеризатора м3;
mр – кількість реакторів-олігомеризаторів;
Vг – годинна продуктивність що дорівнює сумарному об’єму реагентів установки по олігомеризації НПС Vг = Wсум. м3год;
tг – тривалість перебування в апараті год;
φ – об’єм заповнення реактора-олігомеризатора який становить 07.
Vр. = (07528· 6)(2 · 07) = 32263 м3 325 м3;
4 Тепловий баланс реактора-олігомеризатора
Згідно технологічної схеми рис. 4.2 реакція олігомеризації проходить при температурі 473 К. Сировина нагрівається за рахунок подачі теплоносія (ВОТ) в змійовик реактора-полімеризатора.
Температура входу фракції С5 – 423 К фракції С9 – 298 К модифікуючого агента ДАФ – 298 К ініціатора ПДТБ – 298 К втрати тепла становлять - 1%.
Загальна теплота яку необхідно підвести в реактор для нагрівання сировини буде становити:
Qпідв = Q1 +Q2 +Q3 + Q4 де
Q1 – теплота підведення для нагрівання фракції С5
Q2 – теплота підведення для нагрівання фракції С9
Q3 – теплота підведення для нагрівання ініціатора ПДТБ
Q4 – теплота підведення для нагрівання модифікатора ДАФ
Як відомо реакція олігомеризації є екзотермічним процесом тому при утворенні реакційноздатних олігомерів РО в реакторі виділяється додаткова теплота яку потрібно відводити. Теплоту утворення олігомерів НПС можна ввважати +70 кДжмоль оскільки вона ідентична теплоті полімеризації стиролу до полістиролу. Втрати у навколишнє середовище теплоти олігомеризації будуть становити 1%.
Вихідні дані для розрахунку:
неідент. ненас. вугл
) Розрахунок теплоти яку необхідно підвести для нагріву фракції С5 у реакторі-полімеризаторі:
G – витрата вуглеводня (кггод)
Mr – молекулярна маса (кгкмоль)
Сp – питома теплоємність (кДжкмоль·К)
Температура завантажених реагентів Т1 – 423 К;
Температура до якої потрібно нагріти реагенти Т2 – 473 К;
Різниця температур T = 473 – 423 = 50 К.
Кількість теплоти яка потрібна для нагрівання фракції С5 розраховуємо за формулою:
Q1 = 1552878 кДжгод.
Втрати у навколишнє середовище становлять:
Qвтр1 = 15529 кДжгод.
Кількість теплоти яку необхідно підвести в реактор для нагріву фракції С5 розраховуємо за формулою:
Q1 = 1552878 + 15529 = 1568407 кДжгод.
) Розрахунок теплоти яку необхідно підвести для нагріву фракції С9 :
T = 473 – 423 = 175 К;
Кількість теплоти яка потрібна для нагрівання фракції С9:
Qнагр2 = 5796220 кДжгод.
Qвтр2 = 57962 кДжгод;
Q2 = 5796220 + 57962 = 5854182 кДжгод.
) Розрахунок теплоти яку необхідно підвести для нагріву ПДТБ:
Т1 та Т2 ідентичні при нагрванні фракції С9 тому:
Qнагр3 = 75577 кДжгод;
Q3 = 75577 + 756 = 76333 кДжгод.
) Розрахунок теплоти яку необхідно підвести для нагріву ДАФ:
Qнагр4 = 784112 кДжгод;
Q4 = 784112 + 784 = 784896 кДжгод.
Розрахуємо загальну кількість теплоти яку потрібно підвести в реактор для нагрівання сировини:
Qпідв = 1568407 + 5854182 + 76333 + 784896 = 8283818 кДжгод.
Підігрів суміші здійснюється водяною парою. Розрахуємо витрату теплоносія в вигляді водяної пари:
r – теплота випаровування води яка становить 1904 кДжкг;
G вод.пари = 8283818 1904 = 435075 кггод.
) Теплота яка виділяється в процесі олігомеризації Q5
Теплоту яка виділяється в процесі олігомеризації розраховуємо за кількістю ненасичених смолоутворювальних компонентів фракцій С5 і С9:
Qол. = (Gc.к.Mс.к.) · Qутв. · 1000.
Сумарна витрата смолоутворювальних компонентів буде становити витраті (метилбутенів пентенів пентадієнів ізопрену циклопентену ЦПД метилциклопентадієнів стиролу алілбензолу вінілтолуолів мезитилену – метилстиролів ДЦПД індену метилінденів неідентифікованих ненасичених вуглеводнів):
Qол. = 1710756 кДжгод.
Втрати в навколишнє середовище будуть становити:
Qвтр5 = 17108 кДжгод.
Кількість теплоти що необхідно відвести:
Qвідв. = Qол. - Qвтр5;
Qвідв. = 1710756 - 17108 = 1693648 кДжгод.
Охолодження реакційної маси здійснюється за рахунок подачі оборотньої води в оболонку реактора-полімеризатора. Тому розрахуємо необхідну кількість холодоагента (води) яка необхідна для охолодження реакційної маси:
Qвідв. – теплота яку необхідно відвести з реактора полімеризатора;
Св – питома теплоємність води (кДжкмоль·К);
T – різниця температур входу і виходу води 298 і 473 К відповідно;
Gв = 1693648 (42 · 175) = 230428 кггод.
Зведена таблиця витрати теплоносіїв і холодоагентів
Назва теплоносія чи холодоагенту
Технічна характеристика параметри
Витрата на одиницю готового продукту
Табл мат.балансу процесу.docx
неідент. ненас. вугл
Розрахунок теплового балансу процесу.docx
Згідно технологічної схеми рис. 4.2 реакція олігомеризації проходить при температурі 473 К. Сировина нагрівається за рахунок подачі теплоносія (ВОТ) в змійовик реактора-полімеризатора.
Температура входу фракції С5 – 423 К фракції С9 – 298 К модифікуючого агента ДАФ – 298 К ініціатора ПДТБ – 298 К втрати тепла становлять - 1%.
Загальна теплота яку необхідно підвести в реактор для нагрівання сировини буде становити:
Qпідв = Q1 +Q2 +Q3 + Q4 де
Q1 – теплота підведення для нагрівання фракції С5
Q2 – теплота підведення для нагрівання фракції С9
Q3 – теплота підведення для нагрівання ініціатора ПДТБ
Q4 – теплота підведення для нагрівання модифікатора ДАФ
Як відомо реакція олігомеризації є екзотермічним процесом тому при утворенні реакційноздатних олігомерів РО в реакторі виділяється додаткова теплота яку потрібно відводити. Теплоту утворення олігомерів НПС можна ввважати +70 кДжмоль оскільки вона ідентична теплоті полімеризації стиролу до полістиролу. Втрати у навколишнє середовище теплоти олігомеризації будуть становити 1%.
Вихідні дані для розрахунку:
неідент. ненас. вугл
) Розрахунок теплоти яку необхідно підвести для нагріву фракції С5 у реакторі-полімеризаторі:
G – витрата вуглеводня (кггод)
Mr – молекулярна маса (кгкмоль)
Сp – питома теплоємність (кДжкмоль·К)
Температура завантажених реагентів Т1 – 423 К;
Температура до якої потрібно нагріти реагенти Т2 – 473 К;
Різниця температур T = 473 – 423 = 50 К.
Кількість теплоти яка потрібна для нагрівання фракції С5 розраховуємо за формулою:
Q1 = 1552878 кДжгод.
Втрати у навколишнє середовище становлять:
Qвтр1 = 15529 кДжгод.
Кількість теплоти яку необхідно підвести в реактор для нагріву фракції С5 розраховуємо за формулою:
Q1 = 1552878 + 15529 = 1568407 кДжгод.
) Розрахунок теплоти яку необхідно підвести для нагріву фракції С9 :
T = 473 – 423 = 175 К;
Кількість теплоти яка потрібна для нагрівання фракції С9:
Qнагр2 = 5796220 кДжгод.
Qвтр2 = 57962 кДжгод;
Q2 = 5796220 + 57962 = 5854182 кДжгод.
) Розрахунок теплоти яку необхідно підвести для нагріву ПДТБ:
Т1 та Т2 ідентичні при нагрванні фракції С9 тому:
Qнагр3 = 75577 кДжгод;
Q3 = 75577 + 756 = 76333 кДжгод.
) Розрахунок теплоти яку необхідно підвести для нагріву ДАФ:
Qнагр4 = 784112 кДжгод;
Q4 = 784112 + 784 = 784896 кДжгод.
Розрахуємо загальну кількість теплоти яку потрібно підвести в реактор для нагрівання сировини:
Qпідв = 1568407 + 5854182 + 76333 + 784896 = 8283818 кДжгод.
Підігрів суміші здійснюється водяною парою. Розрахуємо витрату теплоносія в вигляді водяної пари:
r – теплота випаровування води яка становить 1904 кДжкг;
G вод.пари = 8283818 1904 = 435075 кггод.
) Теплота яка виділяється в процесі олігомеризації Q5
Теплоту яка виділяється в процесі олігомеризації розраховуємо за кількістю ненасичених смолоутворювальних компонентів фракцій С5 і С9:
Qол. = (Gc.к.Mс.к.) · Qутв. · 1000.
Сумарна витрата смолоутворювальних компонентів буде становити витраті (метилбутенів пентенів пентадієнів ізопрену циклопентену ЦПД метилциклопентадієнів стиролу алілбензолу вінілтолуолів мезитилену – метилстиролів ДЦПД індену метилінденів неідентифікованих ненасичених вуглеводнів):
Qол. = 1710756 кДжгод.
Втрати в навколишнє середовище будуть становити:
Qвтр5 = 17108 кДжгод.
Кількість теплоти що необхідно відвести:
Qвідв. = Qол. - Qвтр5;
Qвідв. = 1710756 - 17108 = 1693648 кДжгод.
Охолодження реакційної маси здійснюється за рахунок подачі оборотньої води в оболонку реактора-полімеризатора. Тому розрахуємо необхідну кількість холодоагента (води) яка необхідна для охолодження реакційної маси:
Qвідв. – теплота яку необхідно відвести з реактора полімеризатора;
Св – питома теплоємність води (кДжкмоль·К);
T – різниця температур входу і виходу води 298 і 473 К відповідно;
Gв = 1693648 (42 · 175) = 230428 кггод.
Зведена таблиця витрати теплоносіїв і холодоагентів
Назва теплоносія чи холодоагенту
Технічна характеристика параметри
Витрата на одиницю готового продукту
ОП + ЦЗ (на перевірку).docx
Охорона праці і цивільний захист
1. Характеристика технологічного процесу.
Коолігомеризація фракцій С5–С9 як побічних продуктів етиленових виробництв відноситься до небезпечних процесів органічного синтезу. Тому отримання нафтополімерних смол з цих фракцій вимагає дотримання встановлених правил техніки безпеки. А їхнє порушення неуважність чи неакуратність в роботі може призвести до розгерметизації пожеж вибухів і у свою чергу отруєнь опіків та інших надзвичайних ситуацій.
Залучені у процесі синтезу речовини за своєю природою є горючими токсичними і за певних умов вибухонебезпечними. Ці речовини застосовуються в якості мономерів ініціаторів каталізаторів а також інших допоміжних речовин у процесі синтезу. Проте ті кількості що використовуються під час проведення досліду є недостатніми для створення реальної загрози вибуху.
Санітарна класифікація виробництв проводиться з метою вибору санітарно-захисної зони згідно нормативу СН 245-71 санітарні норми проектування промислових підприємств. Згідно із санітарною класифікацією виробництв науково-дослідна лабораторія належить до V класу (нешкідливе виробництво). Ширина санітарно - захисної зони становить 50м [104105].
Згідно [105] науково-дослідна лабораторія належить до категорії В (пожежонебезпечна) оскільки у ній знаходяться горючі рідини із температурою спалаху яка є вищою ніж 61°С (концентрована сульфатна кислота) і значення тиску вибуху є меншим ніж 5кПа.
Класифікація зон за пожежобезпекою електрообладнання проводилась згідно із Правилами улаштування електроустановок (ПУЕ). Науково-дослідна лабораторія належить до класу П- так як у ній знаходяться горючі рідини температура спалаху яких становить більше ніж 61°С. За вибухонебезпечністю – клас 2 зони розташовані в приміщеннях в яких є недостатня кількість вибухової суміші горючих парів чи газів з повітрям та іншими окисниками для створення вибуху. Проте вибух можливий при аварійних ситуаціях та несправностях як зазначалося вище [106 - 111].
Санітарна класифікація технологічних процесів проводиться в залежності від забруднюючих факторів які можуть розповсюджуватися на одяг та тіло людини у процесі її роботи згідно ДБН та правил з метою вибору санітарно - побутових приміщень що необхідні для забезпечення нормальної життєдіяльності людини. Науково-дослідна лабораторія належить до третьої групи оскільки виконання дослідів передбачало використання кислот лугів розчинників [106 108 112 113].
2. Надзвичайні ситуації та ідентифікація небезпеки в приміщенні лабораторії
Надзвичайна ситуація - наслідок сукупності виняткових обставин що склалися у відповідній зоні в результаті надзвичайної події техногенного природного антропогенного та військового характеру а також під впливом можливих надзвичайних умов.
Надзвичайні ситуації які можуть виникати на території України і здійснювати негативний вплив на функціонування об'єктів економіки та життєдіяльність населення у мирний і військовий час поділяються за наступними основними ознаками:
- за сферою виникнення;
- за галузевою ознакою;
- за масштабами можливих наслідків.
Загальними ознаками надзвичайних ситуацій є:
- наявність або загроза загибелі людей чи значне порушення умов їх життєдіяльності;
- заподіяння економічних збитків;
- істотне погіршення стану довкілля.
Всі надзвичайні ситуації за масштабом можливих наслідків поділяються з урахуванням територіального поширення характеру сил і засобів що залучаються для ліквідації наслідків на НС:
-загальнодержавного рівня
-регіонального рівня
Внаслідок техногенних аварій та катастроф складається надзвичайна ситуація раптове виникнення якої призводить до значних соціально-екологічних і економічних збитків виникає необхідність захисту людей від дії шкідливих для здоров'я факторів проведення рятувальних невідкладних медичних і евакуаційних заходів а також ліквідації негативних наслідків які сталися.
Сьогодні у світі нараховується до 6 млн. хімічних речовин; 90% з них — це органічні сполуки більшість яких токсичні. У промисловій технології щодо токсичних хімікатів вживається поняття «шкідлива речовина»; при контакті з організмом людини вона може викликати травми отруєння захворювання інші відхилення у стані здоров'я.
Ситез НПС ініційованою олігомеризацією фракції С5 – С9 включає стадію розгонки олігомеризату. Характерною ознакою цієї стадії є накопичення рідких відходів у вигляді атмосферного і вакуумного відгонів.
ншими факторами що спричиняють небезпеку в даному методі є :
Наявність токсичних речовин які можуть мати шкідливий вплив на організм людини.
Застосування вибухонебезпечних та легкозаймистих речовин в якості ініціаторів.
Наявність апаратів та трубопроводів що працюють під тиском і при високих температурах
Наявність обладнання що працює під напругою.
Наявність великої кількості скляного посуду як термостійкого так і звичайного.
Як відомо органічні пероксиди які застосовуються в якості ініціаторів в даному випадку коолігомеризації фракції С5 – С9 є речовинами що містять бівалентну групу -О-О- є термічно нестійкими схильні до екзотермічного самоприскорюваного розкладу тобто вибуху. Пероксиди подразнюють шкіру та слизові оболонки.
Певну небезпеку також зумовлює проведення аналізів в проведенні яких застосовуються концентровані кислоти токсичні та вибухонебезпечні речовини.
Дані про токсичність і вибухонебезпечність речовин що беруть участь у процесі представлені в таблиці 5.1 [106 114 115 116 117]:
Дані про токсичність пожежо- та вибухонебезпечність речовин
густинапарів по відн. до повітря
Характер впливу отрути на орг.
група вибухонеб. Сум.
Схильність при н.у. до
Засоби пожежогасіння
Утв.перекисних спол.
Пінні вогнегасникивода
Тонко розпилена вода хім. і пов.-мех.
Хім. піна ропилена вода
Хім. Піна спец. Пара газ
1-2. Фракція С5 – С9. Помірно небезпечна вуглеводнева фракція. Пари фракції при високих концентраціях діють наркотично негативно впливають на нервову систему викликають зміни в крові та погіршують кровообіг. Також пари подразнюють слизові оболонки виявляють подразнюючу сенсибілізуючу дію на шкіру.
МА – малеїновий ангідрид. Поріг подразнюючої дії становить 1мгм3. В результаті вдихання пилу може спричинити гострий кон’юктивіт підвищення температури подразнення верхніх дихальних шляхів в деяких випадках гострий біль у животі. Описані також гострі отруєння в виробництві МА з опіками рогівки очей та слизових оболонок верхніх дихальних шляхів нудотою рвотою задухою і поступовим розвитком спазматичного бронхіту. В деяких випадках відмічалось ураження шлунково-кишкового тракту. Виявлені також пригнічення фагоцитарної активності лейкоцитів легка анемія. Порушення функцій печінки.
Бензол. У великих дозах бензол викликає нудоту і запаморочення а в деяких важких випадках отруєння може спричинити смертельний результат. Пари бензолу можуть проникати через неушкоджену шкіру. Якщо організм людини піддається тривалій дії бензолу в малих кількостях наслідки також можуть бути дуже серйозними. В цьому випадку хронічне отруєння бензолом може стати причиною лейкемії (раку крові) і анемії (недоліку гемоглобіну в крові). Сильний канцероген.
АК - акрилова кислота. Сильно подразнює шкірні покриви та слизову оболонку очей (поріг подразливої дії 004 мгл). При попаданні в очі викликає сильні опіки рогівки ока і може викликати безповоротні ушкодження. Вдихання пари може викликати подразнення дихальних шляхів головний біль при великих концентраціях або експозиції - набряк легенів. Хоча наявність запаху ще не означає загрозу здоров'ю при роботі з нею потрібний моніторинг повітря.
Ацетон. Одна з основних небезпек при роботі з ацетоном - його легкозаймистість. Температура самозаймання 465 °C температура спалаху -20 °C. Повітряні суміші що містять від 25 % до 128 % (за об'ємом) вибухонебезпечні. З цим необхідно рахуватися оскільки ацетон швидко випаровується і хмара що утворюється може поширитися до місця займання (нагрівання або іскра) далеко від місця роботи з ним. Що ж до впливу на організм людини то ацетон має збуджуючу і наркотичну дію вражає центральну нервову систему здатний накопичуватися в організмі у зв'язку з чим токсична дія залежить не лише від його концентрації але і від часу дії на організм. Для людини летальна доза ЛД оцінюється в 1159 гкг.
Етиловий спирт. Етиловий спирт надзвичайно гігроскопічний при концентрації вище 70% (за об'ємом) припікає шкіру і слизові оболонки; при вживанні внутрішньо пригноблює центри гальмування мозку викликає сп'яніння при багатократному вживанні - алкоголізм. Легко займається температура займання 13°С температура самозаймання 404 °С температурні межі вибухонебезпечності 11-41 °С концентраційні 36-19% (за об'ємом).
Оцтова кислота. Характеризується сильною подразнюючою дією. При високих концентраціях у повітрі спостерігається підвищення вмісту лимонної кислоти в тканинах. При концентраціях у повітрі в розмірі 2-3 мгдм3 знаходження у приміщенні можливе тільки до 3-ох хвилин. Поріг відчуття запаху – 0.0006 мгл поріг рефлекторної зміни світлової чутливості ока на рівні 000048 мгл. Хронічна дія парів викликає у працівників спочатку гострі а потім - хронічні риніти як гіпертрофічні так і атрофічні фарингіти ларингіти а також кон’юктивіти і бронхіти. Дія на шкіру проявляється при появі опіків які спричиняються вже при концентрації кислоти 30%. Для очей небезпечними є розчини оцтової кислоти починаючи від 2%.
ЧХВ - . Отрута що володіє різким солодкуватим запахом та сильною наркотичною дією. При потраплянні в організм людини швидко розпадається з утворенням радикалів що в свою чергу веде до ураження легенів печінки нирок.
Пероксид дитретбутилу. Токсично діє на організм при концентрації починаючи від 25 мгкг. Викликає подразнення слизової оболонки очей.
3. Заходи забезпечення безпеки експлуатації технологічного процесу і обладнання
Науково – дослідна лабораторія № 327 навчального корпусу згідно [104105106] належить до класу споруд з невогненебезпечними і невибухонебезпечними процесами виробництва що відбуваються безшумно без великих викидів в атмосферу. Проте аварійна ситуація може виникнути у випадку несправності.
Оскільки приміщення хімічної лабораторії де проводились досліди належить до категорії В тобто пожежонебезпечне приміщення то будівля повинна бути ступеня вогнестійкості. Усі конструкції повинні бути негорючі. Вогнестійкість елементів будівлі (у годинах) повинна бути наступною : несучі стіни стіни сходових кліток колони - 25; зовнішні стіни - 05; плити перекриття - 10; конструкції покриття - 05; протипожежні стіни - 25. максимальна відстань до евакуаційного виходу повинна становити 75м у крилі корпусу де знаходяться лабораторії передбачено два евакуаційних виходи - основний та запасний.
Вибір електрообладнання проводиться згідно ГОСТ 12.2.020-76 ССБТ. «Электрооборудование взрывозащищенное. Термины и опредиления. Классификация. Маркировка» [118]. За способом захисту людей від ураження електричним струмом електричні прилади відносяться до 1-го класу (вироби мають робочу ізоляцію і елемент для заземлення). Заземлення апарату класу 1 відбувається автоматично при включенні вилки в розетку [118-120]. Згідно з вимогами «Правил улаштування електроустановок опір захисного заземлення» в будь-яку пору року не повинен перевищувати: 4 Ом – в установках напругою до 1000 В але якщо потужність джерела струму 100 кВт і менше то опір заземлювального пристрою допускається до 10 Ом; 05 Ом – в установках напругою понад 1000 В з ефективною заземленою нейтраллю; 2503 але не більше 10 Ом – в установках напругою понад 1000 В з ізольованою нейтраллю; якщо заземлювальний пристрій одночасно використовують для електроустановок напругою до 1000 В то опір заземлювального пристрою не повинен перевищувати 1253 але не більше 10 Ом. Тут 3 – струм замикання на землю. Використовується також покриття на підлогу яке не дає іскри [122].
Для будівель у яких розташована хімічна лабораторія класу П- передбачена категорія грозозахисту. Будинки та споруди повинні бути захищеними від прямих ударів блискавки від занесення високих потенціалів через наземні металічні комунікації. Особливістю вторинного прояву блискавки є занесення високих потенціалів у будівлю по металоконструкціях які підведені у цю будівлю. Такі занесення супроводжуються електричними розрядами які можуть стати причиною вибуху чи пожежі. Блискавкозахист будівлі досягається встановленням на будинку блискавковідводів (сітчасті) які складаються із несучої частини (опори) струмовідводу та заземлювача. Опір заземлювача повинен бути меншим ніж 10 Ом згідно з СН 396 – 74. «Инструкция по проектированию и устройству молнезащиты зданий и сооружений. - М.: Стройиздат 1978» [123].
В науково-дослідній лабораторії наявне таке електрообладнання як термостат сушильна шафа аналітична вага УЗДН-2Т рН-метр центрифуга у звичайному виконанні воно надійно захищене струмопровідні частини обладнання - ізольовані а опір ізоляції періодично перевіряється. Корпуси електроустановок повинні бути заземленими а усі струмоведучі частини обладнання - важкодоступними.
В лабораторії обов’язково повинні бути присутні такі засоби пожежогасіння як пісок вовняна чи шерстяна ковдра. Вода і вогнегасники (вуглекислотні порошкові або пінні) [111114]. Вуглекислотний вогнегасник повинен бути в кожному лабораторному приміщенні незалежно від наявності інших засобів пожежогасіння. Такі засоби пожежогасіння є універсальними. Вони зручні при гасінні невеликих осередків запалювання.
По закінченні роботи над дослідами потрібна обов’язкова перевірка стану лабораторії та її підготовка до наступного циклу роботи. Потрібно виконати ряд дій які гарантують безпеку приміщення по закінченні роботи:
Перевірити відключення електричних приладів води газу.
Забезпечити охолодження нагрівальних приладів та прибрати своє робоче місце.
Перевірка кранів газових пальників водяних кранів
Вимкнення вентиляції зачинення вікон.
Перевірка на наявність тліючих предметів та неприбраних просмалених ганчірок.
Вимкнення освітлення та автоматів на груповому електрощиті.
Передача ключів від лабораторії черговому вахтерові.
Працівники лабораторії повинні знати про пожежну небезпеку всіх хімічних реактивів що знаходять у ній. Меблі та обладнання повинні розміщуватися так щоб не перешкоджати евакуації людей в разі аварійної ситуації мінімальна ширина проходу має становити 1 м.
При пожежі спрацьовує протипожежна сигналізація. Крім цьогоукоридорах є протипожежні крани зі шлангами. У випадку пожежі необхідно телефонувати за номером 9-01.
На кожному поверсі на видному і доступному місці знаходиться план евакуації людей у кількох примірниках повинно бути два виходи: один головний для щоденного використання та запасний при виникненні надзвичайних ситуацій а також вивішено план евакуації людей.
4. Мікроклімат робочого місця
Для забезпечення нормальних умов роботи персоналу необхідно створити відповідні санітарно-гігієнічні умови згідно ГОСТ - 12.1.005-88.
Мікроклімат належить до основних факторів які мають прямий вплив на працездатність працівника та його здоров’я. Мікроклімат охоплює сукупність таких показників як : значення температури вологості швидкості руху повітря температури поверхонь обладнання та величину атмосферного тиску. Всі ці фактори ще називають метеорологічними умовами виробничих приміщень.
Оптимальні мікрокліматичні умови - це поєднання параметрів мікроклімату які при тривалому та систематичному впливі на людину забезпечують зберігання нормального теплового стану організму без активації механізмів терморегуляції. Вони забезпечують відчуття теплового комфорту та створюють передумови для високого рівня працездатності табл. 5.2
Оптимальні мікрокліматичні умови Таблиця 5.2
Температура повітря °С
Відносна вологість %
Швидкість руху повітря мс
Відносна вологість температура та швидкість повітря залежить від періоду року (теплого чи холодного) та категорії важкості роботи. Дана робота у лабораторії за важкістю належить до категорії б - легка тобто робота виконується сидячи стоячи або пов’язана із ходінням та супроводжується деякими фізичними навантаженнями.
Для того щоб концентрація шкідливих речовин в повітрі не перевищувала їх ГДК в лабораторії необхідно забезпечити обмін повітря. В лабораторії для цього передбачена проточно-витяжна вентиляція по місцю дії – загально обмінна вентиляція а також локальна (витяжна шафа) [108124]. Також вентиляція приміщення здійснюється за допомогою дверей і вікон. Загальна вентиляція включається в лабораторії за 30 хв до початку роботи і виключається після іі завершення. Кратність повітрообміну К≥7 год-1 . Незважаючи на метеорологічні умови концентрація шкідливих речовин в основному таких що відносяться до 3 класу - речовини помірно небезпечні ГДК 11 – 10 мгм3 та 4 класу - речовини мало небезпечні ГДК > 10 мгм3. У лабораторії ГДК повинно дотримуватися для кожної речовини.
Освітленість у приміщенні регламентується СНиП 11-4-79 [125] залежно від розряду зорової роботи із урахуванням фону контрасту між об’єктом та фоном. Лабораторія повинна забезпечуватися природнім та штучним освітленням. Природне освітлення у лабораторії є боковим (через вікна). Використання лише штучного освітлення у лабораторії заборонене. Штучне освітлення використовується у випадку недостатнього природного освітлення.
Згідно характеристик зорової роботи яка визначається ступінню точності роботу у хімічній лабораторії можна віднести до V розряду (середньої точності) оскільки проводиться робота із предметами розміри яких є не меншими ніж 1-5мм. Тому у лабораторії повинна бути система загального освітлення із рівномірним розміщенням світильників відносно робочих місць. Мінімальна освітленість повинна становити Е=300лк коефіцієнт природного освітлення повинен становити 2%.
Кожен співробітник при використанні для роботи хімічних реактивів повинен добре знати їх властивості та звернути особливу увагу на пожежо- та вибухонебезпечні характеристики речовин та їх здатність до утворення вибухонебезпечних сумішей і які засоби пожежогасіння можна використати.
Не припускається загромадження коридорів та проходів лабораторій а також підходів до засобів пожежогасіння. Забороняється палити зберігати продукти харчування у приміщеннях лабораторій.
Співробітники які починають новий вид вогненебезпечної чи вибухонебезпечної роботи повинні попередньо отримати вказівки із техніки безпеки від свого керівника. Усі роботи повинні проводитися при справному стані приладів апаратів джерел енергії. Лабораторне обладнання повинне використовуватися тільки за прямим його призначенням. Співробітники повинні постійно підтримувати у хімічних лабораторіях чистоту та порядок.
Дана робота у науково - дослідній лабораторії не може призвести до вибухо- чи пожежонебезпечних ситуацій оскільки у ній не використовуються горючі та легкозаймисті речовини.
Джерелом шуму в лабораторії є низькочастотний ультразвуковий генератор УЗДН-2Т робоча частота якого становить 22 кГц. Постійна дія шуму може не лише негативно вплинути на слух але й викликати інші шкідливі наслідки – дзвін у вухах запаморочення головний біль підвищення втоми зниження працездатності. Шум має акумулятивныий ефект тобто акустичні подразнення накопичуючись в організмі людини все сильніше пригнічують нервову систему. Основними засобами уникнення шуму та його зменшення є : застосування малошумного обладнання заміна металевих частин обладнання на пластмасу установка глушників звукоізолюючих кабін акустичних екранів антизвуків правильне архітектурне планування.
Згідно ГОСТу 12. 1. 001-75 при частоті 20000 Гц і більше допустимий рівень звукового тиску на робочому місці становить 105 Дб. Проектом передбачено заходи щодо зниження джерела шуму шляхом встановлення гумових прокладок товщиною 5 мм під обладнання а також застосовувати звукоізолюючі кожухи напівкожухи; розташовувати обладнання в окремі кабіни або використовувати індивідуальні засоби захисту від шкідливої дії ультразвуку.
Науково дослідна лабораторія обладнана витяжною шафою освітлюється вибухобезпечними світильниками містить раковину крани для подачі води.
У лабораторії наявна система водопостачання та каналізації які необхідні для забезпечення технологічного процесу створення нормальних умов праці гасіння пожеж. Крани водо- та газопостачання знаходиться у легкодоступних місцях на лабораторних столах. Також повинні бути загальні крани які у разі необхідності можна було б використати для гасіння пожеж.
У навчальному корпусі де знаходяться дана лабораторія є загальна гардеробна чоловічі та жіночі вбиральні на кожному поверсі а також їдальня на другому поверсі.
5. Ергономіка робочого місця
Основою планування усіх лабораторій є організація і устаткування робочих місць. Від організації робочого місця напряму залежить продуктивність праці та техніка безпеки в приміщенні оскільки робоче місце— це первинна ланка виробництва зона прикладання праці. При цьому необхідно враховувати природне освітлення опалювання вентиляцію розташування конструкції і число витяжних шаф. Лабораторії мають бути обладнані газом електроенергією різної напруги водопостачанням і каналізацією.
При плануванні робочого місця необхідно врахувати такі основні критерії :
) раціональне розміщення у просторі елементів лабораторії зокрема устаткування технологічного та організаційного оснащення а також робітника.
) Робоче місце повинно мати робочу основну і допоміжну зони. В основній зоні яка обмежена досяжністю рук людини в горизонтальній і вертикальній площинах розміщуються засоби що постійно використовуються в роботі у лабораторії. У допоміжній зоні розміщуються предмети котрі застосовуються рідко.
) Предмети інструменти і лабораторний посуд на робочому місці розміщують так щоб під час роботи не доводилось робити зайвих рухів. Предмет який беруть правою рукою повинен лежати справа а той що беруть лівою рукою - зліва.
) Під час виконання робіт обов'язково слід додержуватись усіх правил техніки безпеки і виробничої санітарії.
Непродумане планування збільшує час виконання конкретної роботи. Нормальний розмір робочого місця від 60 х 120 см до 75 х 150 см Такі розміри приймаються при глибині приміщень у світлі 575; 7; 825 м(за даними Лассена); ширина приміщень у світлі приймається 35 м (глибина пристінних робочих столів + середній прохід); висота приміщень у світлі від 33 до 37 м.
Розміри робочого місця уточнюються залежно від найбільшої віддалі ділянок доступних для працюючих і з урахуванням розмірів керамічних плиток (152 -153 мм).
Ширина приміщень 375 (4) і 75 (8) м взаємозв'язана з кроком осей будівлі (вибраному з міркувань конструктивного характеру); збільшення ширини проходів в лабораторіях можливе лише за рахунок площі робочих місць.
Пристінні і здвоєні лабораторні столи роблять головним чином із сталевих профілів з бетонною плитою фанерованою зверху. Під столами розміщені трубопроводи (газовий водопровід і каналізація розріджене і стисле повітря електропостачання і т.д.) приховані в знімальних засувних під столи кожухах-шафках розташованих на цоколі заввишки 8 -10 см із заведеним на цоколь покриттям підлоги. Лабораторні столи що вільно стоять застосовуються дедалі рідше оскільки в випадку пристінних столів створюються кращі умови спостереження і полегшується облаштування проводок без каналів в підлозі.
Підлога в лабораторії повинна бути безшовною стійкою проти хімічних реактивів теплостійкою водонепроникною добре чинити опір стиранню не вимагати забарвлення мати низьку електропровідність; догляд за підлогою і прибирання приміщень не повинні вимагати значних зусиль. Цим вимогам краще за все відповідають рулонні синтетичні покриття які після зварювання рулонних смуг утворюють безшовну підлогу. Пошкоджені або недоброякісні ділянки такої підлоги можуть бути вирізані і відновлені.
Лабораторія де проводились досліди по коолігомеризації фракцій С5 – С9 відповідає всім зазначеним вище вимогам. Експериментальна установка синтезу була розміщена таким чином що вести потрібний візуальний контроль за нею можна було з будь-якої частини лабораторії та розташована під витяжною шафою. Робоче місце було організоване правильно тому ніяких незручностей не виникало.
6. Розрахунок механічної вентиляції для витяжної шафи
Вентиляція - видалення відпрацьованого повітря з приміщення і заміна його зовнішнім. У необхідних випадках при цьому проводиться кондиціонування повітря : очищення від пилу і диму підігрівання або охолодження зволоження або осушення іонізація і так далі. Вентиляція створює умови повітряного середовища сприятливі для здоров'я і самопочуття людини що відповідає вимогам санітарних норм технологічних процесів будівельних конструкцій будівель і технологій зберігання.
Для розрахунку механічної вентиляції витяжної шафи потрібно обчислити її продуктивність - об’єм чистого повітря та кратність повітрообміну у приміщенні.
Продуктивність витяжної шафи розраховують за формулою :
де S – площа перерізу щілини витяжної шафи відкритої на 13 м2; W – швидкість руху повітря в цій щілині (приймається від 05 – 15мс залежно від токсичності газів і парів) мс.
Об’єм повітря яке подають в приміщення при розрахунку механічної витяжної вентиляції приймається від характеру шкідливих виділень а також від швидкості та напряму її руху.
Розраховуємо кратність повітрообміну в лабораторії де встановлена вентиляційна установка :
де abc – довжина ширина і висота приміщення; Vк – об’єм лабораторії м3.
Виходячи з розрахунків повітрообмін в приміщенні можна вважати ефективним.
7. Розрахунок захисного заземлення
Приймаємо що опір рунту рівний Rз = 450 Ом·м.
Вибираємо розмір заземлювача : довжина електрода – 3 м; діаметр електроду – 006 м;
Порядок розрахунку :
Визначаємо розрахунковий питомий опір :
де - питомий розрахунковий опір землі Ом·м; φ – коефіцієнт сезонності який враховує можливі коливання питомого опору при зміні вологості грунту протягом року приймаємо рівним 14 Rз – питомий опір землі Ом·м;
Визначаємо опір розтікання струму по землі одного вертикального заземлювача заглибленого на 1м від поверхні землі за формулою :
де d – діаметр заземлювача м; t – відстань від поверхні землі до середини заземлювача м.
де h – заглиблення заземлювача від поверхні землі м; a – довжина заземлювача м.
Знаходимо приблизну кількість заземлювачів :
Відношення відстані між заземлювачами до їх довжини :
де a1 – відстань між заземлювачами;
По орієнтовному n і k знаходимо коефіцієнт екранування для електродівщо розміщені по контуру = 07.
Визначаємо кількість заземлювачів з врахуванням за формулою :
Знаходимо довжину горизонтального заземлювача L який з’єднує горизонтальні заземлювачі розташовані по контуру за формулою :
Визначаю опір горизонтального заземлювача R2 прокладеного на глибині 1м від поверхні землі за формулою :
де R2 – опір розтікання струму в землі горизонтального заземлювача Ом; h – глибина розташування горизонтального заземлювача м.
Обчислюю загальний опір заземлюючого пристрою за формулою :
де 2 – коефіцієнт використання горизонтального заземлювача який визначають за таблицею залежно від критеріїв та способу їх розташування рівний 045.
Схема заземлюючого пристрою
Розрахований опір не більший від максимально допустимого тому можна вважати що кількість вертикальних заземлювачів та з’єднувальна смуга вибрані правильно.
ohorona_praci-dipl.doc
НАЦОНАЛЬНИЙ ТЕХНЧНИЙ УНВЕРСИТЕТ УКРАНИ
НАЦОНАЛЬНИЙ НАУКОВО-ДОСЛДНИЙ НСТИТУТ ОХОРОНИ ПРАЦ
ДО ВИКОНАННЯ РОЗДЛУ "ОХОРОНА ПРАЦ
В ДИПЛОМНИХ ПРОЕКТАХ
ДО ВИКОНАННЯ РОЗДЛУ "ОХОРОНА ПРАЦ"
ДЛЯ СТУДЕНТЕ ФАКУЛЬТЕТУ ЕЛЕКТРОНКИ
на засіданні кафедри
охорони праці та довкілля
Протокол №3 від 29.10.05 р.
Методичні вказівки до виконання розділу "Охорона праці" в дипломних проектах для студентів факультету електроніки Укл.: С.С. Козлов - К.: НТУУ- -КП" -ННДОП 2005-17с.
ДО ВИКОНАННЯ РОЗДЛУ «ОХОРОНА ПРАЦ»
Укладач:Козлов Сегій Степанович
Відповідальний редакторК.Н. Ткачук
Рецензенти:О.. Полукаров
Темплан 2005 р..Редактор Т. В. Омельчук
Підписано до друку 25.04.05. Формат 60x8412. Папір Xerox Paper (80 gm2). Друк-ризограф. О6л.-вид.арк.-12. Наклад 200 прим.
Національний науково-дослідний інститут охорони праці.
Охорона праці" є обов'язковим розділом дипломного проекту. Обсяг розділу - 12 15 сторінок рукописного тексту.
Змістом розділу є аналіз умов праці на обраному робочому місці (виявлення шкідливих і небезпечних факторів виробничого середовища і порівняння їх з діючими нормативами а також розробка заходів націлених на утворення умов праці що відповідають вимогам усіх норм і стандартів з охорони праці).
Розділ "Охорона праці" складається з підрозділів
Аналіз умов праці на робочому місці.
Розробка заходів з охорони праці.
Пожежна безпека приміщення.
Розрахункова частина.
В середині підрозділів виділяються параграфи. Вибір робочого місця для аналізу умов праці і розробка заходів з охорони праці здійснюється самим студентом-дипломником з урахуванням теми дипломного проекту. Робоче місце може бути обрано:
-на стадії проектування і розробки даного приладу обладнання програмного продукту тощо (наприклад робоче місце інженера-проектувальника в лабораторії НД КБ або інженера-програміста в обчислювальному центрі (ОЦ) на ПЕОМ);
-на стадії експериментального зразка або серійного приладу обладнання зразка що розробляється в науково-дослідній лабораторії або фірмі на підприємстві в виробничому цеху (наприклад робоче місце інженера-конструкгора у вказаній лабораторії 12 корпусу університету або техніка-монтажника зі складання РЕА на заводі або підприємстві);
-на стадії експлуатації розроблювального приладу стенду обладнання або реалізації програмного продукту (наприклад робоче місце інженера-звукооператора в студії інженера-конструктора що працює з використанням обчислювальної та іншої техніки у наукових та виробничих галузях; робоче місце конкретного користувача програмного продукту в приватній фірмі тощо).
З виявлених небезпечних та шкідливих факторів виділяються один-два найбільш несприятливих щодо яких розробляються детальні заходи з охорони праці та робляться необхідні інженерні розрахунки (розрахункова частина). Обсяг розрахункової частини складає 10-15 % від обсягу розділу "Охорона праці".
Студент-дипломник надає викладачу-консультанту спочатку чорновик пояснювальної записки розділу потім після виправлення похибок і зауважень - чистовий варіант. Після цього викладач-консультант підписує розділ "Охорона праці" на титульному аркуші дипломного проекту.
У доповіді на захисті диплому студент-дипломник повинен висвітлити основні положення розроблені в розділі "Охорона праці".
У вступі студенту необхідно висвітлити роль охорони праці для сучасного виробництва та довести необхідність розробки заходів з охорони праці у дипломному проекті. Вказати яке робоче місце обрано для аналізу умов праці на якому підприємстві воно знаходиться. Обсяг вступу - 05 стор.
Окремим параграфом цей пункт у змісті не виділяється.
1 Організація робочого місця
Виявлення та аналіз шкідливих та небезпечних виробничих факторів слід починати з аналізу дотримання вимог встановлених санітарними правилами і нормами [1-3] для виробничих приміщень та робочих місць.
Для цього необхідно вказати геометричні розміри приміщення та кількість робочих місць у ньому. Згідно з характером роботи що виконується вибрати норми за площею та об'ємом приміщення що наведено для одного робочого місця та порівняти їх з фактичними значеннями.
2 Мікроклімат виробничих приміщень
Згідно з ДСТ [456] визначаються категорія важкості робіт що виконуються в приміщенні цеху лабораторії ОЦ та період року. Складається таблиця санітарних норм параметрів мікроклімату які порівнюються з фактичними даними.
3. Шкідливі речовини в повітрі робочої зони
Вказуються джерела виділення шкідливих речовин у виробничому приміщенні лабораторії ОЦ (наприклад пайка ручними електропаяльниками з використанням олов'яно - свинцевих припоїв типу ПОС). Проводиться санітарна характеристика кожної шкідливої речовини - клас небезпечності МДК біологічна дія на організм людини [5] (можливо у вигляді таблиці). Порівнюється фактичний вміст шкідливих речовин у повітрі робочої зони (дані інструментальних вимірювань взяти на преддипломній практиці або розрахунок [478]) з допустимими концентраціями.
Вказуються види та системи освітлення що використовуються в даному приміщенні. Згідно з нормами [3 9] вказуються норми освітлення робочих місць які порівнюються з фактичними даними (розрахунок за [710]).
5. Шум вібрація ультразвук інфразвук
Вказуються джерела шуму у виробничому приміщенні а також якщо вони є вібрації ультразвуку (УЗК) інфразвуку (ФЗ). За [1011] згідно з типом виробничого приміщення наводяться норми за спектральним та загальним рівнем шуму (вібрації УЗК ФЗ [11-24]). Наводяться їх фактичні (розрахункові) значення [7-25]. Проводиться їх порівняння.
6. Виробничі випромінювання
До виробничих випромінювань відносяться:
-випромінювання оптичного діапазону - ультрафіолетові (УФВ) лазерні (ЛВ) інфрачервоні (ЧВ);
-електромагнітні випромінювання (ЕМВ) НЧ ВЧ УВЧ НВЧ діапазонів; іонізуючі випромінювання.
У даному параграфі слід вказати види та джерела виробничих випромінювань на робочому місці згідно з нормативними документами [26 33]. Навести норми по кожному виду випромінювань які порівнюються з їх фактичними значеннями.
Для приміщень з відеотерміналами та ПЕОМ порівнюються фактичні і допустимі норми ЕМВ [334]. Крім цього довільна електронно-променева трубка є джерелом рентгенівського випромінювання що не використовується. Тому при аналізі умов праці на робочих місцях операторів інженерів що працюють з відеотерміналами згідно з [2627] наводяться допустимі норми рентгенівського випромінювання.
7. Небезпека ураження електричним струмом
Вказуються припустимі травмонебезпечні місця та можливі причини ушкодження людей електричним струмом (внаслідок дотику до відкритих струмоведучих частин до струмопровідних неструмоведучих елементів обладнання що опинилися під напругою в результаті порушення ізоляції а також ураження кроковою напругою та через електричну дугу).
Наводиться характеристика електричної мережі живлення із зазначенням кількості фаз проводів роду струму напруги частоти струму режиму нейтралі. При необхідності розраховується сила струму що проходить через тіло людини при можливих включеннях в електричне поле: при однофазному і однополюсному також при двохфазному і двохполюсному дотику до струмоведучих елементів обладнання що знаходяться під напругою при замиканні фази на корпус обладнання або на землю при дотику до обірваного і лежачого на землі проводу повітряної лінії електропередачі.
Розрахункове значення струмів порівнюється з допустимим [35] робиться висновок про небезпеку експлуатації електроустановок.
Називаються речовини матеріали відходи виробництва елементи обладнання що електризуються в процесі виробництва; в окремих випадках (при інженерній розробці захисту від статичної електрики) необхідно розрахувати потенціали струми та енергію розрядів статичної електрики.
Згідно з ПБЕ [39] приміщень цехів лабораторій установки класифікуються за ступенем небезпеки ураження людей електричним струмом (без підвищеної небезпеки; з підвищеною небезпекою і особливо небезпечні).
Розробка заходів з охорони праці
У даному підрозділі розглядаються заходи які забезпечують здоров'я працівника і безпеку умов праці на робочому місці.
1. Нормалізація повітря робочої зони
Здійснюються заходи щодо утворення мікроклімату та забезпечення чистоти повітря робочої зони. Необхідно повністю використовувати можливості вдосконалення технологічних процесів та їх апаратурного оформлення а також вибору схем виробництва сировини палива транспорту з метою зниження тепловиділення і зведення до мінімуму надходження шкідливих речовин у повітря робочої зони.
При недостатності технологічних заходів для нормалізації повітря робочої зони слід використовувати спеціальні методи і засоби включаючи вентиляцію опалення кондиціювання повітря засоби індивідуального захисту екранну ізоляцію теплових агрегатів тощо. В гарячих цехах потрібно передбачити особливий питний режим кімнати відпочинку та повітряні оазиси. Підбираються засоби контролю мікроклімату та чистоти повітря робочої зони.
2. Виробниче освітлення
При проектуванні або реконструкції виробничих приміщень (підрозділів) здійснюються заходи щодо встановлення окремих видів і систем освітлення. Для систем електричного освітлення підбираються типи ламп освітлювачів (вказується використання останніх) напруга освітлювальної мережі джерела живлення [743].
Згідно галузевим нормам передбачається аварійне та ремонтне освітлення. При цьому називаються типи ламп освітлювачів їх виконання номінальна напруга
3. Захист від виробничого шуму та вібрацій
В проектах повинен бути розроблений комплекс заходів застереження зниження та захисту від шуму й вібрацій. При необхідності передбачаються засоби індивідуального захисту погоджується режим праці та відпочинку працюючих а також засоби контролю параметрів шуму й вібрацій [725].
4. Захист від електромагнітних полів і лазерних випромінювань
Залежно від характеристики джерел електромагнітних і лазерних випромінювань обираються і розроблюються заходи захисту персоналу від цих небезпечних і шкідливих виробничих факторів (захист часом відстанню екранами засобами індивідуального захисту). Виконується оцінка прийнятих заходів і вказуються засоби контролю ЕМВ і ЛВ [746].
5. Захист від іонізуючих випромінювань
З урахуванням виду і характеристики випромінювань розробляються заходи захисту персоналу обмеженої частини населення краю області республіки. Оцінюються прийняті заходи і підбираються засоби контролю іонізуючих випромінювань [7].
Безпека експлуатації електрообладнання досягається системою організаційних і технічних засобів і заходів що забезпечують безпеку при нормальному режимі роботи електроустановок а також в аварійному стані [745]
Вказати та описати заходи захисту під час роботи на електроустановках. Необхідно вказати величину прилад і періодичність контролю опору робочої ізоляції захисного заземлення (петлі "фаза-нуль") передбачити заходи попередження електризації речовин і накопичення зарядів статичної електрики а також прилади контролю параметрів статичної електрики.
7. Ергономіка технічна естетика та організація робочого місця
Студентам що розробляють теоретичні дипломні роботи слід відобразити ергономічні вимоги до робіт що виконувались в кабінетах дипломного проектування в лабораторії на ЕОМ або на дослідних установках. В розділі необхідно проаналізувати гігієну розумової праці і передбачити заходи що попереджують нервові захворювання і підвищують працездатність персоналу зайнятого розумовою працею [374748].
Необхідно вказати всі вибухо- та пожежонебезпечні речовини і матеріали що знаходяться на даному робочому місці і в приміщенні загалом навести їх вибухо- та пожежонебезпечні характеристики (можливо у вигляді таблиці). Слід провести короткий аналіз можливих місць і причин загорань і вибухів у приміщенні.
Визначити (розрахувати) категорію приміщення щодо вибухо-пожежонебезпечності вказати вибухонебезпечну зону пожежонебезпечний клас даного приміщення [5051]. Потім слід вибрати засоби пожежогасіння (первинні або автоматичні установки пожежогасіння) засоби пожежної сигналізації.
Перелік тем для детальної розробки заходів з охорони праці в розрахунковій частині
Розрахувати кількість шкідливих речовин що виділяються в робочу зону під час паяння.
Розрахувати інтенсивність газовиділення через нещільність апаратури що працює під тиском визначити вентиляційний повітряний обмін у приміщенні.
Розрахувати тепловий баланс виробничого приміщення.
Спроектувати систему місцевої приточної механічної вентиляції.
Спроектувати систему місцевої витяжної механічної вентиляції.
Спроектувати систему загальної приточної механічної вентиляції.
Обгрунтувати і розрахувати габаритні розміри витяжного зонту та об'єм вилученого ним повітря.
Вибрати і спроектувати прилад для зниження виробничого шуму в цеху лабораторії ОЦ.
Розрахувати екран для захисту від шуму.
Визначити розрахунковим шляхом заходи захисту від ультразвуку.
Розробити комплекс заходів щодо захисту від статичної електрики.
Розрахувати концентраційні межі вибуховості багатокомпонентної суміші горючих речовин з повітрям.
Розрахунковим шляхом визначити категорію приміщення щодо вибухо- та пожежонебезпечності згідно ОНТП 24-86.
Атестувати робоче місце робітника основної професії цеху.
Атестувати робоче місце інженера-дослідника в лабораторії в кабінеті ОТ на дослідній установці
Обрати типи і згідно нормам розрахувати необхідне число первинних засобів гасіння осередків пожеж.
Розробити інструкцію з техніки безпеки під час роботи на дослідній установці лабораторному стенді.
Обрати і розрахувати елементи блискавкозахисту об'єкту.
Розрахувати систему загального рівномірного електричного освітлення цеху методом коефіцієнту використання світлового потоку.
Розрахувати систему загального локалізованого штучного освітлення робочого місця.
Виконати перевірочний розрахунок природного освітлення.
Розрахувати коефіцієнт природнього освітлення графоаналітичним методом.
Розрахувати екран для захисту від електромагнітних випромінювань.
Рекомендована література
СН245-71 Санитарные нормы проектирования промышленных предприятий.-М.1971.
ДСанПіН 3.3-2.007-98 Державні санітарні правила і норми роботи з візуальними дисплейними терміналами електронно - обчислювальних машин. - Київ 1999. - 18с.
ДНАОП 0.00-1.31 -99 Правила охорони праці під час експлуатації електронно -обчислювальних машин. - Київ 1999. - 30 с.
ДСН 3.3.6.042-99 Санітарні норми мікроклімату виробничих приміщень. - Київ 2000.
ГОСТ 12.1.005-88 ССБТ. Общие санитарно-гигиенические требования к воздуху рабочей зоны.- М. 1988.
ДНАОП 003-3.06-80 Санітарно-гігієнічні норми допустимих рівнів іонізації повітря виробничих та громадських приміщень №2152-80 -М. 1980
Справочник по охране труда на промышленных предприятиях. К.Н. Ткачук Д. Ф. Иванчук Р. В. Сабарно и др.-К.: Техника 1991. -286 с.
ГОСТ 12.1.007-76 ССБТ. Вредные вещества. Классификация и общие требования безопасности.
СНиП 23-05-95 Строительные нормы и правила. Естественное и искусственное освещение.-М. 1995.
Справочная книга по светотехнике под ред. Ю. Б. Айзенберг - М.:Энергоатомиздат 1985. - 485 с.
ГОСТ 12.1.003-83 ССБТ. Шум. Общие требования безопасности. - М. 1983.
ДСН 3.3.6.037-99 Санггарні норми виробничого шуму ультразвуку та інфразвуку. - Київ 2000.
ДСН 3.3.6.039-99 Державні санітарні норми виробничої загальної та локальної вібрації.- Київ 2000.
ДНАОП 0.03-3.14-85 Санггарні норми допустимих рівнів шуму на робочих місцях №3223-85.-М 1985.
15 ГОСТ12.1.012-90 ССБТ. Вибрационная безопасность. Общие требования. -М. 1990.
ГОСТ 12.1.028-80 ССБТ. Шум. Определение шумових характеристик источников шума. Ориентировочный метод (СТ СЭВ 1413-78). -М. 1980.
ГОСТ 12.1.029-80 ССБТ. Средства и методы защиты от шума Классификация (СТ СЭВ 1928-79). -М. 1980.
ГОСТ 12.1.036-81 ССБТ. Шум. Допустимые уровни в жилых и общественных зданиях (СТ СЭВ 2834-80). -М 1981.
ГОСТ 12.1.050-86 ССБТ. Методы измерения шума на рабочих местах. -М 1986.
ДСТУ 2300-93 Вібрація. Терміни та визначення. -М. 1993.
ДСТУ 2325-93 Шум. Терміни та визначення.-М. 1993.
ДСТУ 2867-94 Шум. Метода оцінювання виробничого шумонавантаження. Загальні вимоги. -М. 1994.
ДСТУ 2894-94 Пристрої екранувальні для захисту інфрачервоного випромінювання. Параметри та загальні технічні вимоги. - М. 1994.
ДСТУ 3010-95 Обладнання для кондиціонування повітря та вентиляції. Методи визначення шумових характеристик кондиціонерів. - М. 1995.
Борьба с шумом на производстве: Справочник Под общ. ред. Е. Я. Юдина - М.: Машиностроение 1985. - 400 с.
ДНАОП 0.03-1.65-79 Санітарні правила робота з джерелами невикористаного рентгенівського випромінювання №1960-79.
ДНАОП 0.03-1.77-90 Санітарні правила роботи з джерелами низькоенергетичного рентгенівського випромінювання № 5170-90.
ДНАОП 0.03-3.30-96 Державні стандартні норми і правила захисту населення від впливу електромагнітних випромінювань.
ГОСТ 12.1.006-84 ССБТ. Электромагнитные поля радиочастот. Допустимые уровни на рабочих местах и требования к проведению контроля (СТ СЭВ 5801 -86).
ГОСТ 12.1.031-81 ССБТ. Лазеры. Методы дозиметрического контроля лазерного излучения.
ГОСТ 12.1.040-83 ССБТ. Лазерная безопасность. Общие положения.
ГОСТ 111.045-84 ССБТ. Электростатические поля. Допустимые уровни на рабочих местах и требования к проведению контроля.
ГОСТ 12.2.006-87 ССБТ. Безопасность аппаратуры электронной сетевой и сходных с ней устройств предназначеных для бытового и аналогичного общего применения. Общие требования и методы испытаний.
ГОСТ 12.2.091-94 ССБТ. Требования безопасности для показывающих и регистрирующих электроизмерительных приборов и вспомогательных частей к ним.
35.ГОСТ 12.1.038-82 ССБТ. Электробезопасность. Предельно допустимые значения напряжений прикосновения и токов.
ГОСТ 12.1.013-78 ССБТ. Строительство. Электробезопасность. Общие требования.
ГОСТ 12.1.030-81 ССБТ. Электробезопасность. Защитное заземление зануление.
ГОСТ 12.2.025-76 ССБТ. Изделия медицинской техники. Электробезопасность. Общие технические требования и методы испытаний.
ДНАОП 0.00-1.21-98 Правила безпечної експлуатації електроустановок споживачів.
ДНАОП 0.00-1.29-97 Правила захисту від статичної електрики.
ДНАОП 0.00-8.02-93 Перелік робіт з підвищеною небезпекою.
ДСТУ 2817-94 (ГОСТ 12.2.007.6-93) Система стандартів безпеки праці. Апарати електричні комутаційні на напругу до 1000 В. Вимоги безпеки.
Старовертов И. Г. Справочник проектировщика. Часть П. Вентиляция и кондиционирование воздуха -М: Стройиздат 1988. -510 с.
ДСТУ 3191-95 (ГОСТ 12.2.137-96) Обладнання для кондиціонування повітря та вентиляції. Загальні вимоги безпека
Правила усітройства электроустановок.-М.:Энергпромиздат 987.-248с.
Степанов А. Г. Сабарно Р. В. Техника безопасности при эксплуатации лазерных установок. -К.: Техніка 1989. -110 с.
ДСТУ 3038-95 Гігієна Терміни та визначення основних понять.
ГОСТ 12.2.032-78 ССБТ. Рабочее место при выполнении работ сидя. Общие эргономические требования.
ГОСТ 12.2.033-84 ССБТ. Рабочее место при выполнении работ стоя. Общие эргономические требования.
ОНТП 24-86 Общесоюзные нормы технологического проектирования. - М.: Стройиздат -1986.
ДНАОП 0.01-1.01-95 Правила пожежної безпеки в Україні.
ДНАОП 0.05-8.04-92 Порядок проведення атестації робочих місць за умовами праці.
ДНАОП 0.03-8.03-97 Гігієнічна класифікація праці за показниками шкідливості та небезпечності факторів виробничого середовища важкості та напруженості трудового процесу.
ОП і ЦЗ ( Козловська Таня ).doc
Охорона праці і цивільний захист
1.Характеристика технологічного процесу
Дослідження перебігу процесу естерифікації адипінової кислоти (НДК) аліфатичними спиртами проводились у VIII корпусі Національного університету «Львівська політехніка» у хімічній лабораторії кафедри технології органічних продуктів. Сировиною і продуктами процесу є пожежо- і вибухонебезпечні речовини. Пожежа або вибух може відбутися при витоці продуктів і появі відкритого вогню.
Науково-дослідна лабораторія кафедри хімічної технології органічних продуктів відноситься до приміщень із підвищеною небезпечністю через те що тут використовуються вибухонебезпечні речовини. Оскільки в лабораторії знаходяться горючі та важкогорючі речовини та матеріали які здатні взаємодіяти з водою киснем повітря або один з одним а також горіти і в таких кількостях що нездатні при спалахуванні розвивати розрахунковий надлишковий тиск 5 кПа то згідно ОНТП 24-86 приміщення можна віднести до пожежонебезпечної категорії В. Згідно ПУЕ приміщення хімічної лабораторії класифікується як приміщення класу оскільки в приміщенні знаходяться горючі гази та рідини у невеликих кількостях недостатніх для створення з повітрям чи іншими окисниками вибухонебезпечної суміші в об’ємі що перевищує 5% вільного об’єму лабораторії а усі роботи проводяться без застосування відкритого полум’я.
Основою для нормальної роботи в хімічній лабораторії може бути лише свідоме дотримання кожним працюючим правил техніки безпеки. Для забезпечення безпечної роботи потрібні знання класу небезпечності реактивів особливостей їх токсичної дії основних методів надання першої медичної допомоги й методів профілактики отруєнь. При транспортуванні речовин в лабораторії слід уникати їх розливів і розбризкувань оскільки в таких випадках можливе їх попадання в на шкіру людини або в очі. Щоб уникнути опіків потрібно бути уважними і обережними з нагрітим до високої температури хімічним посудом. Бите скло небезпечне тим що ним можна порізатися воно може бути забрудненим реактивами що може спричинити зараження крові.
Згідно санітарних норм СН-245-71 навчальний корпус із хімічними лабораторіями відноситься до V класу шкідливості а його ширина санітарно-захисної зони становить 50 м.
2.Надзвичайні ситуації що можуть виникнути під час процесу
Надзвичайна ситуація (НС) — порушення нормальних умов життя і діяльності людей на об’єкті або території спричинене аварією катастрофою стихійним лихом епідемією епізоотією епіфітотією великою пожежею застосуванням засобів ураження що призвели або можуть призвести до людських і матеріальних втрат.
Причини виникнення НС:
Стихійні і природні явища і особливо небезпечна інфекція.
Старіння і корозія матеріалів конструкцій і споруд.
Проектно-виробничі дефекти споруд.
Порушення технологічних процесів промислового виробництва.
Порушення правил експлуатації споруд і технологічних процесів.
Порушення правил техніки безпеки при проведенні особливо відповідальних робіт.
Для хімічної лабораторії характерними є НС техногенного характеру.
Надзвичайні ситуації техногенного характеру — це наслідок транспортних аварій катастроф пожеж неспровокованих вибухів чи їх загроза аварій з викидом (загрозою викиду) небезпечних хімічних радіоактивних біологічних речовин раптового руйнування споруд та будівель аварій на інженерних мережах і спорудах життєзабезпечення гідродинамічних аварій на греблях дамбах тощо.
Основними небезпечними факторами для персоналу хімічної лабораторії є:
)небезпека гострих або хронічних отруєнь хімічними сполуками;
)ураження електричним струмом при користуванні електричними приладами;
)термічні опіки при роботі з нагрітим до високої температури хімічним посудом і електроприладами;
)можливість ураження очей і ділянок шкіри хімічними сполуками;
)небезпека при роботі з хімічним посудом;
)небезпека виникнення пожеж і вибухів;
Гострі отруєння виникають при надходженні в організм відносно великих кількостей шкідливих речовин за невеликий проміжок часу і проявляються в типових порушеннях нормальної життєдіяльності безпосередньо після отруєння або через невеликий проміжок часу ( кілька хвилин). Гострі отруєння не можуть виникати при нормальній роботі а є наслідком аварійних ситуацій поломок обладнання розливів шкідливих речовин або грубих порушень техніки безпеки.
Хронічні отруєння виникають при тривалій дії на організм відносно невеликих кількостей шкідливих речовин і можуть виникати і при безаварійній роботі як наслідок недотримання правил і норм зберігання реактивів недостатньо ефективній роботі вентиляції недотримання правил особистої гігієни. Важкі наслідки хронічних отруєнь ускладнюються тим що їх симптоми часто бувають
неспецифічними і їх не повязують з істиною причиною до тих пір поки проникнення отрут в організм яке і далі продовжується не приводить до серйозних порушень здоровя.
Електричний струм небезпечний тим що сама людина звикла до постійного його використання і створила дуже неправдиву ілюзію про безпечність електричного струму. Широко поширена думка що струм напругою 220 В і нижче не створює небезпеки для життя. Недооцінка небезпеки призводить до ігнорування правил техніки безпеки.
Хімічна лабораторія за ступенем небезпеки ураження людей електричним струмом відноситься до приміщень з підвищеною небезпекою а нерідко – до особливо небезпечних. Особлива небезпека обумовлена можливістю дії на електрообладнання хімічно активного середовища. В дуже складних умовах експлуатації знаходиться апаратура яка працює всередині витяжної шафи – сушильні шафи електроплитки ЛАТР.
Небезпека ураження людей електричним струмом при роботі в витяжних шафах підвищується у звязку з можливістю одночасного доторкання до металічних корпусів електрообладнання і не заземлених водопровідних і газових комунікацій. Постійне джерело небезпеки в хімічній лабораторії – саморобні електроприбори.
Головними причинами ураження людини електричним струмом є:
Випадковий дотик або наближення на небезпечну відстань до струмоведучих частин які знаходяться під напругою внаслідок недотримань правил техніки безпеки дефектів конструкцій та монтажу електричного обладнання;
Дотик до не струмоведучих частин що опинилися під напругою внаслідок пошкодження ізоляції перехрещування проводів;
Поява напруги на відімкнених струмоведучих частинах на яких працюють люди внаслідок помилкового ввімкнення електричних установок;
Відсутність надійних захисних пристроїв.
При дії електричного струму на людину виникають ураження двох видів: електротравми і електричні удари.
Електротравми – місцеві пошкодження тканин організму викликані дією електричного струму і електричної дуги. Найбільш характерним різновидом електричних травм є електричні опіки електричні знаки металізація шкіри електрофтальмія.
Електричний удар – це різке збудження живих тканин струмом який проходить через організм.
Найбільшу небезпеку представляє змінний струм низької частоти в тому числі струм промислової частоти – 50 Гц. Порогові значення для постійного струму в 3 – 5 разів вищі ніж для змінного частотою в 50 Гц. Але в умовах хімічної лабораторії небезпечна дія на людину будь-якого відчутного струму. Тому електричній безпеці потрібно приділяти велику увагу.
Електроприлади представляють собою небезпеку і тим що їх поверхні нагріваються до високих температур і є потенційна загроза термічних опіків при дорканні до цих нагрітих частин. Таку ж небезпеку представляють всі теплоносії і гарячий хімічний посуд.
Особливо небезпечним при роботі в хімічній лабораторії є можливість ураження очей і ділянок шкіри хімічними сполуками. Неуважність необережність ігнорування правил техніки безпеки при роботі з агресивними сполуками може призвести до їх виливів розбризкувань.
Синтетичний одяг може розчинятися в деяких агресивних речовинах і при змиванні водою полімер буде коагулюватись і покривати тіло ліпкою плівкою це також становить небезпеку.
Більшість робіт в сучасній хімічній лабораторії повязана з використанням скляної посуди. З точки зору техніки безпеки скло має ряд серйозних недоліків основні з яких – крихкість і невисока стійкість до різких перепадів температур. За попередніми підрахунками до 80% від загального числа аварій і нещасних випадків виникає через неправильне поводження зі склом.
Більшість нещасних випадків при порушенні правил роботи зі склом відноситься до категорії мікротравм і легких травм. В першу чергу це порізи рук і опіки рук при необережному поводженні з нагрітими до високої температури скляними деталями. Важкі травми і травми які приводять до інвалідності можуть бути викликані попаданням частинок скла в очі. Крім травм при поломці скляної апаратури і посуди можливі і інші види аварій і нещасних випадків – пожежі і вибухи отруєння і хімічні опіки. Тому так важливо приділяти багато уваги техніці безпеки при роботі зі склом. Потрібно памятати що скляний посуд не призначений для роботи при підвищених тисках не можна допускати нагрівання рідин в закритих колбах які не мають доступу повітря категорично забороняється використання посуду який має тріщини або відбиті краї особливу увагу потрібно приділяти митті посуду.
В приміщенні лабораторії є надзвичайно велика кількість різних горючих і вибухонебезпечних речовин з різними властивостями. Пожежі в лабораторіях виникають у більшості випадків від несправностей обладнання електроустаткування контрольно-вимірювальних та захисних приладів необережного поводження з вогнем та порушення правил пожежної безпеки персоналом.
Для запобігання та успішної боротьби з пожежами необхідно знати фізико-хімічні та пожежонебезпечні властивості вживаних речовин і матеріалів вміти оцінювати пожежну небезпечність речовин і процесів правильно вибирати ефективні засоби запобігання та захисту від пожеж та вибухів.
3. Заходи пожежної безпеки
Протипожежний захист промислових обєктів забезпечується: правильним вибором необхідного ступеню вогнестійкості будівельних конструкцій; правильним обємно-планувальним рішенням будівель і споруд; розташуванням приміщень та виробництв з урахуванням вимог пожежної безпеки; улаштуванням протипожежних перегород в будівлях системах вентиляції паливних системах кабельних комунікаціях; обмеженням витікання та розтікання горючої рідини при пожежі; спорудженням проти димного захисту; забезпеченням евакуації людей; використанням засобів пожежної сигналізації сповіщення та пожежогасіння; організацією пожежної охорони обєкту а також засобами що забезпечують успішне розгортання тактичних дій гасіння пожежі.
Хімічна лабораторія відносяться до приміщень категорії В (пожежонебезпечне приміщення) тому будівля повинна бути ступені вогнестійкості а всі конструкції повинні бути негорючими. Вогнестійкість елементів будівлі повинна відповідати вимогам СниП 2.01.02-85 (мінімальні межі год):
несучі стіни стіни сходових кліток колони – 2 год;
зовнішні несучі стіни та внутрішні не несівні – 025 год;
плити та інші несучі конструкції перекриття – 075год;
сходові площадки самонесівні стіни – 1год;
елементи покриття: плити настили та інші несівні конструкції перекриття – 025 год;
балки ферми рами арки – 025 год.
У коридорі на видному місці знаходиться план евакуації. Для евакуації людей передбачено два евакуаційних виходи – основний та запасний. Максимальна відстань до евакуаційного виходу повинна становити 75 м мінімальна ширина шляхів евакуації – не менше 1 м дверей 08 м.
За характером середовища лабораторія відноситься до нормальних приміщень з хімічно-активним середовищем тому тут рекомендовано використовувати вибухобезпечне обладнання електроприлади класів 1 та 2. Перші мають додатковий захист за допомогою заземлення чи занулення а другі мають подвійну чи посилену ізоляцію і не мають елементів для заземлення.
Усі струмоведучі частини обладнання повинні мати ізоляцію обладнання має бути заземленим а підлога покрита матеріалом який не дає статичної іскри.
Лабораторне приміщення обовязково має бути обладнане вогнегасниками і іншими первинними засобами пожежогасіння: азбестове волокно пісок вода. Обовязково в лабораторії має бути вуглекислотний вогнегасник ним можна гасити електрообладнання горючі рідини і тверді речовини.
Для припинення пожежі важливим є правильно підібрати спосіб і засіб гасіння пожежі:
Горіння можна припинити наступними способами:
охолодженням горючої речовини до температури нижчої ніж температура її займання;
припиненням надходження парів газів горючої речовини в зону горіння;
зниженням концентрації кисню в повітрі в зоні горіння;
Усунення всіх можливих джерел загоряння є головною умовою вибухо- та пожежобезпечності приміщень. Джерелами загоряння можуть бути: відкрите полумя несправність електрообладнання статична електрика розряд блискавки.
Серед найбільш поширених вогнегасних речовин є вода. Однією з важливих переваг води як засобу пожежогасіння є постійна її наявність в будь-якій лабораторії. Особливо ефективне використання води для гасіння звичайних твердих матеріалів – дерева паперу тканини резини а також горючих речовин які добре розчиняються у воді – ацетон нижчих спиртів органічних кислот. Вода ефективний засіб для гасіння одягу. Вогнегасний ефект струменів води полягає у змочуванні поверхні зволоженні та охолодженні твердих горючих матеріалів.
Внутрішнє протипожежне водопостачання здійснюється за допомогою пожежних кранів які встановлюються на висоті 135 м від підлоги всередині приміщень біля виходів у коридорах на сходових клітках.
Кожний пожежний кран споряджається прогумованим рукавом та пожежним стволом. Довжина рукава повинна бути 10 чи 20 м а продуктивність кожного крана – не менше ніж 25 лс.
Корпус в якому знаходиться хімічна лабораторія повинен бути захищеним від прямих ударів блискавки від заносу високих потенціалів через підземні та надземні металічні комунікації від електростатичної індукції.
Для приміщень в яких розташована хімічна лабораторія що відноситься до класу передбачена категорія грозозахисту. Громозахист виконується відповідно до діючого стандарту у вигляді – блискавковідводів що складаються з несучої частини (опори) струмовідводу і заземлювача. У приміщенні використовуються сітчасті блискавковідводи металічна сітка яких заземлюється. Опір заземлювача 10 Ом.
Приміщення лабораторії відноситься до приміщень категорії тобто приміщень де при нормальних умовах праці не утворюються вибухонебезпечні суміші а лише при виникненні аварійних ситуацій чи несправностей обладнання.
У будинках категорії блискавкозахист досягається за допомогою блискавковідводів які мають стержневу чи тросову конструкцію та встановлюються безпосередньо на будинку.
З метою захисту від електростатичної індукції металеве обладнання підключають до контуру захисного заземлення електрообладнання або ж заземлюють.
У випадку пожежі потрібно телефонувати 9-01.
4. Мікроклімат робочого місця
Метеорологічні умови виробничого середовища або мікроклімат виробничих приміщень – це фізичний стан повітря який характеризується такими фізичними параметрами:
- температурою повітря t C;
- відносною вологістю φ %;
- швидкістю руху повітря v мс;
- величиною атмосферного тиску Р Па;
- Тепловиділенням Втм2;
-ступенем іонізації повітря.
Мікроклімат виробничих приміщень залежить від кліматичних умов часу доби і пори року.
Основним нормативним документом що визначає параметри мікроклімату виробничого приміщення є ДСН 3.3.6.042-99 та ГОСТ 12.1.005-88.
Для робочої зони виробничих приміщень встановлюються оптимальні та допустимі мікрокліматичні умови з урахуванням важкості виконуваної роботи та періоду року.
Оптимальні умови мікроклімату встановлюються для постійних робочих місць
Допустимі величини мікрокліматичних умов встановлюються у випадках коли на робочих місцях не можна забезпечити оптимальні величини мікроклімату за технологічними вимогами виробництва технічною недосяжністю та економічно обгрунтованою недоцільністю.
Оптимальні та допустимі параметри мікроклімату лабораторії в теплий та холодний періоди року наведені у табл. 5.1 як для приміщення із незначним надлишком явного тепла – 84 кДж(м3год) і менше.
Таблиця 5.1.Оптимальні та допустимі метеорологічні умови для роботи в хімічній лабораторії
Відносна вологість повітря %
Швидкість руху повітря мс
Нормалізація несприятливих мікрокліматичних умов здійснюється за допомогою комплексу заходів та способів які включають: будівельно-планувальні організаційно-технологічні санітарно-технічні та інші заходи колективного захисту.
Щоб параметри метеорологічних умов рівнялися стандарту у хімічній лабораторії важливим є обрати систему вентиляції. Це система пристроїв для оздоровлення робочої зони з тим щоб концентрація шкідливих речовин у повітрі не перевищувала ГДК. Усі шкідливі речовини задіяні у виробничому процесі за ГДК можна віднести до наступних класів:
клас –ГДК рівне 1-10мгм3 речовини помірно (середньо) шкідливі;
клас –ГДК більше 10 мгм3 – речовини мало шкідливі (малотоксичні).
Ще одним фактором що впливає на умови праці є освітлення. У приміщенні хімічної лабораторії є природне та штучне освітлення. Природнє освітлення має важливе фізіолого-гігієнічне значення для працівників. Воно сприятливо впливає на органи зору стимулює фізіологічні процеси підвищує обмін речовин та покращує розвиток організму загалом і діє тонізуюче. Природнє освітлення не вимагає затрат на експлуатацію. Природнє освітлення поділяють на бокове верхнє і комбіноване. В даному випадку застосовують бокове освітлення крізь віконні отвори. У хімічній лабораторії повинно забезпечуватись природне освітлення для якого коефіцієнт природного освітлення становить КПО=15% (характеристика зорової роботи середньої точності) оскільки в приміщенні постійно перебувають люди.
Згідно СНиП 11-4-79 для штучного освітлення нормована освітленість робочих поверхонь хімічної лабораторії повинна складати Е=300Лк коефіцієнт запасу к=15. Для освітлення лабораторії використовуються світильники типу “Люцетта” які характеризуються коефіцієнтом використання 056 та забезпечують рівномірне освітлення. При використанні ламп розжарювання (газонаповнені) на 200 Вт світловий потік одного світильника Ф=2920 Лм. Витяжна шафа освітлюється електричними лампами у вибухобезпечному виконанні.
У лабораторії знаходиться два можливих джерела шуму – це термостат та хроматограф. Проте за умов їх використання відповідно до правил експлуатації та у випадку їх справності шум що створюється цими приладами знаходиться у межах норм і не перевищує 80 Дб.
При виконанні дослідів в лабораторії слід користуватися засобами індивідуального захисту: халат гумові рукавички протигази окуляри. Хімічна лабораторія повинна мати шафи для зберігання ЗЗ та шафи для одягу. Крім цього повинен бути вмивальний куток з умивальником оснащеним змішувачами для холодної та гарячої води.
Лабораторія відповідає основним вимогам до будівель виробничого приміщення (СНиП 2.09.03-85 ): об’єм приміщення на одного працівника складає не менше 15 м3 площа 45 м2 висота приміщення 32 м.
5. Ергономіка робочого місця
Робоче місце — це зона простору що оснащена необхідним устаткуванням де відбувається трудова діяльність одного працівника чи групи працівників.
Раціональне планування робочого місця має забезпечувати: найкраще розміщення знарядь і предметів праці не допускати загального дискомфорту зменшувати втомлюваність працівника підвищувати його продуктивність праці. Площа робочого місця має бути такою щоб працівник не робив зайвих рухів і не відчував незручності під час виконання роботи. Важливо мати також можливість змінити робочу позу тобто положення корпуса рук ніг. Проте доцільно виключати або мінімізувати всі фізіологічно неприродні і незручні положення тіла.
Проведені дослідження показують що при раціональній організації робочих місць продуктивність праці зростає на 15-25%.
Організація робочого місця передбачає:
— правильне розміщення робочого місця у виробничому приміщенні;
— вибір ергономічно обрунтованого робочого положення виробничих меблів з урахуванням антропометричних характеристик людини;
— раціональне компонування обладнання на робочих місцях;
— урахування характеру та особливостей трудової діяльності.
Загальні принципи організації робочого місця:
— на робочому місці не повинно бути нічого зайвого. Усі необхідні для роботи предмети мають бути поряд із працівником але не заважати йому;
— ті предмети якими користуються частіше розташовуються ближче ніж ті предмети якими користуються рідше;
— предмети які беруть лівою рукою повинні бути зліва а ті предмети які беруть правою рукою — справа;
— якщо використовують обидві руки то місце розташування пристосувань вибирається з урахуванням зручності захоплювання його двома руками;
— робоче місце не повинно бути захаращене;
— організація робочого місця повинна забезпечувати необхідну оглядовість.
Робоча поза — це основне положення працівника у просторі: зручна робоча поза має забезпечувати стійкість положення корпуса ніг рук голови працівника під час роботи мінімальні затрати енергії та максимальну результативність праці.
Найпоширенішими у процесі праці є пози сидячи і стоячи. Проектуючи робоче місце потрібно враховувати що при виконанні роботи з фізичним навантаженням бажана поза стоячи а при малих зусиллях — сидячи.
Проведення дослідів по отриманні дибутиладипінату проводиться як в позах сидячи так і стоячи. Установка естерифікації розташована під витяжною шафою а речовини що використовуються стоять згідно нормативів: токсичні речовини – спирти розташовані в металевій скрині дно якої всипане піском кислота розміщена в шафі каталізатори – на спеціальній поличці. Все скляне обладнання розміщується у шухлядах перед початком досліду вибираємо собі все необхідне. Експериментальну установку розміщують так щоб зручно було спостерігати за процесом контролювати температуру і обєм водного шару в пастці Діна-Старка. Біля установки не розміщують ніяких зайвих предметів.
Робочий стіл і крісло розташовані біля вікна лабораторії якомога далі від установки естерифікації. На ньому розміщені зошит для запису результатів досліджень і вся необхідна література.
Всі потрібні для досліджень пристрої розташовують на лабораторному столі. Загалом лабораторія обладнана таким чином щоб працювати було зручно і приємно. Кожен працюючий має своє робоче місце.
6. Розрахунок штучної вентиляції
Вентиляція – це організований і регульований обмін повітря який забезпечує видалення з приміщення повітря забрудненого шкідливими речовинами (гази пари пил) а також для покращення метеорологічних умов в приміщенні.
Основне завдання розрахунку системи штучної вентиляції – визначити кількість повітря яке необхідно подати і вилучити з приміщення і вибрати потужність електродвигуна вентилятора.
Під час розрахунку вентиляції повітрообмін визначають за допомогою розрахунків за такими даними:
-Кількістю шкідливих виділень;
-За кількістю людей які знаходяться в приміщенні;
-Кратністю повітрообміну;
-Швидкістю руху повітря в повітропроводі.
Оскільки в процесі естерифікації виділяються шкідливі речовини будемо розраховувати вентиляцію за цим методом.
Для приміщень в яких виділяються шкідливі гази чи випари повітрообмін визначають за їх кількістю
де – надлишкова кількість шкідливих речовин (випарів газів пилу) які виділяються в приміщенні мггод;
– ГДК шкідливих виділень у повітрі приміщення мгм3;
Со – концентрація цих виділень у зовнішньому повітрі мгм3 вміст речовини у припливному повітрі можна прийняти
L2 - кількість припливного повітря яке необхідно ввести для зменшення вмісту газу в приміщенні м3год
ГДК бутилового спирту у повітрі 10 мгм3
С0 = С2 ГДК = 02 10 = 2 мг м3
L2 = 187458(10 – 2) = 23432 м3год
Визначивши L для даних умов обчислюємо поперечний переріз повітропроводу:
де vр - швидкість руху повітря в повітропроводі мс (вибирають з діапазону 6-12 мс)
fp = 2343236008 = 0008 м2
Враховуючи розрахункові площі перерізів повітропроводів (fр) за табличними даними підбирають стандартні діаметри при круглому поперечному перерізі або розміри при прямокутному поперечному перерізі.
З таблиці вибираємо d = 100 мм fp = 000785 м2 тоді фактична швидкість руху повітря:
Необхідний тиск для подачі повітря повітропроводами визначають з урахуванням втрат тиску на тертя на ділянках повітропроводу і місцевих опорах пристроїв (фільтр калорифер вентилятор насадки тощо ) .
Втрати тиску на тертя кожної ділянки та у вітках розраховуються за формулою:
де Pтр – втрати тиску на ділянці повітропроводу Па;
R – питомі втрати тиску на 1 м довжини повітропроводу Пам;
l – довжина ділянки або вітки м.
Питомі втрати тиску можуть бути визначені за табличними даними або за формулою:
де – коефіцієнт опору тертя який залежить від шороховатості стінок повітропроводу (для сталевих повітропроводів приймається = 002);
vф – фактична швидкість повітря мс;
d – діаметр повітропроводу м;
– густина повітря кгм3;
– приймають за табличними даними
R = 00283212255012 = 84 Пас
Довжина ділянки повітропроводу дорівнює:
Втрати тиску в місцевих опорах розраховують послідовно для кожної ділянки і у вітках за формулою:
де Z – місцеві втрати тиску в пристроях Па
– коефіцієнт місцевих опорів які приймають за табличними даними.
Загальні втрати тиску на кожній розрахунковій ділянці і у вітках складають
Z = 32 832 12255 2 = 13508 Па
Н =126 + 13508 = 26008 Па
Знаючи необхідний повітрообмін L і загальні втрати тиску Н проводять вибір вентилятора за його аеродинамічною характеристикою .
Необхідна потужність електродвигуна вентилятора визначається за формулою кВт
де Nвент – потужність електродвигуна вентилятора кВт;
L – продуктивність вентилятора м3год.;
Н – тиск створюваний вентилятором Па;
К – коефіцієнт запасу ( К=11–15 );
– коефіцієнт корисної дії вентилятора ( 05–08 ).
Nвент = 23432 26008 12 3600 102 07 = 028 кВт
Визначивши Nвент за довідником (каталогом) вибирають відповідний тип електродвигуна для цього вентилятора.
Вибрали АИР63В4 потужністю 037 кВт.
Документ Microsoft Office Word.docx
Співолігомеризацію фракції С9 піролізу дизельного палива проводили при оптимальних умовах: температура - 453 К тривалість процесу - 6 год. концентрація модифікатора - 5-20 % мас. (у розрахунку на фракцію) концентрація ініціатора - пероксид ди-трет-бутилу - 1 % мас. Основні фізико-хімічні показники та вуглеводневий склад фракції С9 наведено в табл.1. Вуглеводні що непрореагували вилучали проводячи атмосферну та вакуумну дистиляцію олігомеризату.
Рис. 1. Залежність бромного числа олігомеризату від концентрації модифікатора: 1 - ініційована співолігомеризація); 2 - термічна співолігомеризація МА (1) АК (2) КК (3).
Радикальна олігомеризація є одним з найпоширеніших методів синтезу НПС тому в нашому випадку для порівняння впливу методів синтезу ФНПС на фізико-хімічні показники одержуваних продуктів використали термічний та ініційований методи синтезу. У результаті проведених досліджень встановили що смоли одержані термічною співолігомеризацією відрізняються підвищеною ненасиченістю олігомеризату (рис.1) у порівнянні з такими ж смолами отриманими методом ініційованої співолігомеризації. Густина олігомеризату збільшується пропорційно до зростання концентрації модифікуючої домішки в реакційній масі але у порівнянні з методом синтезу смоли одержані шляхом термічної співолігомеризації мають меншу густину ніж ініційованої.
Залежність фізико-хімічних показників ФНПС від концентрації МА
Найменування показників
ініційована співолігомеризація
Температура розм’якшення К
Бромне число г Br2100 г
Колір за ЙМШ г J2100 см3
Молекулярна маса (кріоскопія)
Кислотне число мг КОНг
Число омилення мг КОНг
термічна співолігомеризація
Залежність фізико-хімічних показників ФНПС від концентрації модифікатора
АК - ініційована співолігомеризація
КК - ініційована співолігомеризація
АК - термічна співолігомеризація
КК - термічна співолігомеризація
Рис. 3.Залежність виходу ФНПС від концентрації модифікатора: 1 - ініційована співолігомеризація; 2 - термічна співолігомеризація МА (1) АК (2) КК (3).
При співолігомеризації фракції С9 з МА АК та КК збільшення концентрації модифікуючої домішки призводить до підвищення числа омилення (у випадку з МА) та кислотного числа ФНПС. Ці числа є важливими характеристиками у випадку подальшого застосування синтезованих ФНПС. Вихід цих смол у перерахунку на вихідну сировину зі збільшенням концентрації модифікатора збільшується але термічні ФНПС мають менший вихід (рис. 2). Порівнюючи одержані результати (табл. 2 3) треба відзначити що співолігомерні ФНПС одержані термічним методом мають більш високу ненасиченість (бромне число) та температуру розм’якшення. Молекулярна маса число омилення та кислотне число практично не відрізняються.
Процес термічної співолігомеризації технологічно є досить простим його недоліком є невисокий вихід смоли. При ініційованому методі технологія процесу практично аналогічна але вимагає застосуваня пожежо- та вибухонебезпечного ініціатора. У результатi проведених дослiджень встановлено що кожен з методів синтезу ФНПС має свої переваги та недоліки і може з успіхом застосовуватится для синтезу таких смол які знаходять дедалі ширше застосування в різноманітних галузях народного господарства.
З метою оцінки виходу та фізико–хімічних характеристик НПС одержаних ініційованою та термічною коолігомеризацією було проведено дослідження реакції коолігомеризації фракції С9 РПП дизельного палива з наступними комономерами: МА АК і ДАФ в оптимальних умовах проведення реакції: температура 453 К тривалість 6 год концентрація комономеру 15 % мас. (для ініційованого методу концентрація ПДТБ 1 % мас.). У результаті проведених досліджень встановили (рис. 4.11) що використання ПДТБ забезпечує вищу швидкість реакції коолігомеризації у порівнянні з термічною коолігомеризацією в таких же умовах.
Рис. 3. Залежність бромного числа олігомеризату від концентрації комономеру МА (1) АК (2) ДАФ (3): 1 – ініційована 2 – термічна
Про це свідчать нижчі значення бромного числа олігомеризату (рис. 3 криві 1.1–1.3) у порівнянні з термічним методом (рис. 4 криві 2.1–2.3) відповідно. Спостерігаються також вищі значення густини олігомеризату при використанні у порівнянні з термічним методом синтезу.
Рис. 4. Залежність виходу синтезованих смол від концентрації комономера МА (1) АК (2) ДАФ (3): 1 – ініційована 2 – термічна
Позитивний вплив підвищення концентрації комономеру від 5 до 20 % мас. підтверджує збільшення виходу НПС рис. 4.12. При цьому використання 1 % мас. ПДТБ забезпечує в середньому на 5 % мас. вищий вихід НПС у порівнянні з термічним методом у досліджуваному інтервалі концентрацій комономеру. Вищий вихід НПС при використанні 1 % мас. ПДТБ пояснюється вищою конверсією ненасичених вуглеводнів фракції С9 РПП дизельного палива на відміну від термічної коолігомеризації.
Порівнюючи одержані результати треба відзначити що коолігомерні НПС одержані термічним методом мають більш високу ненасиченість температуру розмякшення та молекулярну масу ніж смоли одержані у присутності ПДТБ.
Нижчі значення числа омилення (37 139 і 17 55 35 135 і 14 51 мг КОНг для МА та ДАФ) а також кислотного числа (32 118 29 114 мг КОНг для АК) при термічному методі у порівнянні з ініційованим пояснюються очевидно меншою реакційною здатністю комономерів у реакції коолігомеризації. Зменшення молекулярної маси смол синтезованих у присутності ПДТБ можна пояснити більшою швидкістю реакції обривання ланцюга при наявності в реакційній масі джерела вільних радикалів спричиненого присутністю ПДТБ. Загалом вихід цих смол у перерахунку на вихідну сировину зі збільшенням концентрації комономера збільшується але смоли синтезовані шляхом термічної коолігомеризації мають менший вихід що виправдовує застосування ініціатора. На рис. 5 зображена залежність ненасиченості синтезованої смоли від методу одержання та концентрації комономеру. Смоли одержані шляхом термічної коолігомеризації мають більш ненасичений характер як для МА так і для АК і ДАФ.
Рис. 5. Вплив концентрації комономеру на ненасиченість функціоналізованих смол МА (1) АК (2) ДАФ (3): 1 – ініційована 2 – термічна.
Процес термічної коолігомеризації технологічно є досить простим його недоліком є порівняно меншиий вихід смоли при задовільних решта фізико–хімічних характеристиках. Технологія ініційованого процесу синтезу смол практично аналогічна але вимагає застосуваня пожежо– та вибухонебезпечного пероксидного ініціатора. Вихід функціоналізованих НПС в присутності ініціатора в середньому на 5 10 % мас. вищий ніж вихід НПС при термічному способі. Підвищення виходу смол при використанні 1 % мас. ПДТБ пояснюється вищою конверсією ненасичених вуглеводнів фракції С9 РПП у порівнянні з конверсією вуглеводнів при термічному методі.
Отже як свідчать отримані дані використання 1 % мас. ПДТБ забезпечує на 5 10 % мас. вищий вихід НПС у порівнянні з термічним методом синтезу що зумовлено вищою конверсією основних смолоутворювальних компонентів сировини в реакції коолігомеризації сумарна конверсія основних смолоутворювальних компонентів відрізняється в середньому на 5 %. З врахуванням практично аналогічної технології ініційованого та термічного методу (відмінність полягає лише в наявності вузла приготування та дозування розчину ініціатора при ініційованому методі отримання НПС) та незначної відмінності у фізико–хімічних характеристиках НПС для подальших досліджень вибираємо метод ініційованої коолігомеризації.
Економіка.docx
1 Обгрунтування доцільності досліджень з економічної точки зору
Важливість скорочення потреб харчової сировини в технічних цілях важко оцінити. Тільки на виробництво лакофарбових матеріалів в світі витрачаються сотні тисяч тонн рослинних олій в тому числі соняшникової для виробництва 1т якої потрібно засіяти 25 га орних земель.
Особливе місце серед синтетичних замінників харчової сировини а саме рослинних олій та альбуміну в лакофарбовій промисловості та виробництві дерево-волокнистих плит займають нафтополімерні смоли (НПС) основною сировинною базою для синтезу яких служать відходи і побічні продукти нафтохімічних виробництв і перш за все рідкі продукти піролізу та крекінгу вуглеводнів (РПП і РПК).
Розвиток хімічної промисловості та розширення областей застосування декоративних і захисних матеріалів ставить перед лакофарбовою промисловістю безліч різноманітних технічних завдань. До них відносяться не тільки покращення якості згідно світових стандартів але і зниження собівартості виробленої продукції. Тому НПС становлять велику перспективу в вирішенні цього питання.
Нафтополімерні смоли як особливий клас низькомолекулярних синтетичних смол що володіють унікальними фізико-хімічними якостями в національній і закордонній практиці знаходять щодалі більше застосування не тільки в якості замінників харчових але і таких продуктів природного походження як каніфоль.
Ринкові відносини диктують свої вимоги у впровадженні нових наукових розробок : мінімальні капітальні витрати і стислі терміни впровадження висока рентабельність впроваджуваних розробок і ліквідність продукції що обумовлюють мінімальний термін окупності капітальних витрат. Найбільш адаптованими до ринкових стосунків виявили саме НПС. При цьому особливий практичний інтерес представляють процеси отримання на базі РПК нових НПС не лише як замінників рослинних олій і алкідів (для чого в основному і призначається НПС пиропласт-2к) але і як дуже дорогих акрилатів в лакофарбовій промисловості в водорозчинних (водно-дисперсійних) матеріалах і епоксидних смол в захисних покриттях. А також для заміни фенол-формальдегідних смол (ФФС) у виробництві зв’язуючих компонентів з різними наповнювачами такими як целюлоза скловолокно деревне борошно деревні плити клеї просочувальні і заливні композиції для фанери тканинних і наповнених волокном матеріалів. Для заміни інден-кумаронових смол (КС). КС використовуються при виробництві побутових фарб покриттів для підлоги друкарських фарб і чорнила клеїв. Також використовуються в якості пом'якшувальних засобів натуральних і синтетичних каучуків. Вироби з використанням НПС за якістю не поступаються виробам з більш дорогих продуктів проте є значно дешевшими
Світовий об’єм виробництва НПС починаючи з 70-их років постійно збільшується і перевищує 600 тис.трік. Це пояснюється з однієї сторони широкою і доступною сировинною базою та низькими затратами на їх виробництво що обумовлює невисоку вартість НПС а з іншої сторони можливістю використання НПС в різних галузях промисловості.
Подальше вдосконалення існуючих виробництв НПС розробка і введення нових високоефективних процесів будуть сприяти більш повному задоволенню потреб в цих цінних продуктах для різних галузей промисловості скороченню витрат значних об’ємів харчової сировини на технічні цілі а також в поглибленні переробки нафти.
2 Розрахунок затрат на проведення досліджень
Вартість затрат на проведення досліджень розраховується укрупнено по основних статтях затрат. Загальна сума затрат пов’язаних з дослідженням визначається як сума окремих статей затрат.
де Ц – ціна на сировину та матеріали;
В – витрата сировини та матеріалів на проведення досліджень.
Результати розрахунку наведені в таблиці 6.1
Вартість речовиннеобхідних для проведення досліджень
Питома вартість витрат %
3 Розрахунок енергозатрат
З енергетичних затрат лабораторних досліджень враховуємо лише технологічні так як опалення освітлення та інше відносяться до загально- університетських витрат.
Час на проведення одного досліду коолігомеризації 1 год. Всього проводилося 6 дослідів. Тому час роботи термостата який служиь для підтримання сталої температури процесу буде становити :
Для нагрівання реагентів відводилося приблизно по 2 години на кожен дослід. Загальний час експлуатації електроплити :
Аналітична вага використовувалася приблизно 1 год на протязі 20 днів тому загальний час роботи ваги:
Час роботи витяжної шафи рівний часу досліду і становить 1 год. В розрахунку на 6 дослідів
Загальний час роботи сушильної шафи становить 6 год. оскільки вона була використана 6 разів протягом 1 год.
Розрахунок енергозатрат
В цю статтю витрат включається також вартість води. Витрата води при проведенні лабораторних досліджень становила 25 м3. Ціна 1 м3 води 450 грн. Отже вартість води:
Ввода =V450 = 25450 = 1125 грн.
Ми використовували дві лампи штучного освітлення потужністю 150 Вт протягом 20 год.
Тоді витрати на освітлення:
Восв= 06320150·21000 = 378грн.
Загальна сума витрат за цією статтею:
Венерг.= Вел.ен.+ Ввода + Восв = 3006+1125+378 = 4169 грн.
Результати розрахунку наведені в таблиці 6.2
Потужність обладнання кВт
Тривалість досліджень год.
Кількість витраченої електроенергії кВтгод
Вага аналітична AXIS AN-50
Шафа витяжна хімічна ШВХ-2 1000Ч750Ч2470
Шафа сушильна 2В-151
Електрична плита Термія -2-25
4 Розрахунок фонду заробітної плати
Заробітна плата наукового керівника:
ЗПнк = Тк Тар = 30·400 =1200 грн.
де Тк = 30 год – кількість годин відведених для консультацій;
Тар =40– тариф грн.год.
На виконання магістерської роботи відводиться 4 місяці. Таким чином стипендія магістранта становить:
Ст = 6730 = 4380 грн.;
де 730 грн. – стипендія магістра за 1 місяць.
Таким чином фонд заробітної плати становить:
ФЗП= Ст + ЗПнк = 4380+1200 = 5580 грн.
Відрахування у пенсійний фонд 2 %:
Пф = ФЗП002 = 5580002 = 1116 грн.
Відрахування у фонд зайнятості 06%:
Фз = ФЗП0006 = 55800006 = 3348 грн.
Прибутковий податок 15% :
ПП= ФЗП·015 = 5580·015 = 8370 грн.
Загальний фонд заробітної плати:
ЗФЗП= ФЗП + Пф + Фз + ПП= 5580 + 1116 + 2472 + 3348 = 656208 грн.
5 Розрахунок вартості апаратури
Невра-ховані витрати на апаратуру грн.
Загаль-на вартість грн.
Час роботи обладнан-ня днів
Амортиза-ційні відрахуван-ня А грн
Термометр ртутний ТЛС-2
Де неврахованих витрати на апаратуру становлять 75% від вартості обладнання а норма амортизаційних відрахувань 15%.
Загальні невраховані витрати на апаратуру:
ЗНВ = Ц0075 = 148050075 = 11107 грн.
Загальна вартість обладнання :
ЗВО = Ц + ЗНВ = 14805 + 11107 = 159157 грн.
Амортизаційні відрахування на обладнання:
А = 05·ЗВОТНА365100%
де Т – фактичний час роботи обладнання дні;
НА – норма амортизаційних відрахувань - 15%
А = 05·127982 · 15 · 30 365 · 100 = 789 грн.
Вартість малоцінного інвентарю та інструментів визначаємо на підставі наведеної специфікації як 20 % від вартості приладів і основної апаратури та терміну їх використання :
Вм.і.і. = С · 20 100 = 159157 · 20 100 = 31831 грн.
6. Розрахунок вартості оренди приміщення
Приймаючи що оплата за оренду приміщення становить 2320 грн. за рік розрахуємо витрати за оренду на час проведення досліджень:
Оп – витрата за оренду приміщення
О – оплата оренди приміщення наведено в таблиці 7.4
Вартість за 1 м2 за 1 рік грн.
Вартість оренди приміщення за рік грн.
Загальна вартість оренди за 6 міс грн.
7 Загальна вартість лабораторних досліджень
Загальна вартість лабораторних досліджень
Сировина і матеріали
Енергозатрати (в т.ч. вода)
Фонд заробітної плати з нарахуваннями
Амортизаційні відрахування обладнання
Накладні витрати (20% прямих)
Отже сумарні витрати проведених лабораторних досліджень будуть становити 1000812 грн.
8 Техніко-економічна оцінка результатів досліджень економічного ефекту
В результаті проведених досліджень на практиці було відтворено процес коолігомеризації фракцій С5-С9 із застосуванням пероксидних ініціаторів. Загальні економічні витрати дослідів становлять 1000812 гр.
Пероксидні ініціатори – це окрема область одержання НПС що відзначається простотою відтворення та більшим економічним ефектом. х застосування дозволяє суттєво підвищити рентабельність виробництва НПС а отже і етиленових виробництв та установок піролізу збільшити раціональність переробки рідких продуктів піролізу та крекінгу що є актуальним питанням сьогодення. Проте робота з цими речовинами вимагає максимальної обережності та безпеки. Слід відзначити також те що в Україні органічні пероксиди не виробляються крім пероксиду бензоїлу та його похідних що теж відноситься до недоліків процесу.
економіяна частина.docx
Обрунтування доцільності досліджень з економічної точки зору
На сьогоднішній день у промисловості велику увагу приділяється застосуванню нафтополімерних смол для зменшення витрати дорогих та дефіцитних продуктів природного походження у виробництві паперу та клеїв у гумовій та лакофарбовій промисловостях.
Рідкі продукти піролізу являються дешевою та найпоширенішою сировинною базою для виробництва нафтополімерних смол. При збільшенні потужності піролізних установок зростає виробництво продуктів піролізу правильне використання яких забезпечує рентабельність і безвідходність виробництва. Комплексна переробка рідких продуктів піролізу з одержанням нафтополімерних смол покращує техніко-економічні показники виробництва та дозволяє зменшити собівартість.
Покращення показників якості та експлуатаційних властивостей нафтополімерих смол здійснюють шляхом модифікації: модифікацією власне нафтополімерних смол; на стадії синтезу внесенням модифікуючих добавок; на стадії синтезу внесенням функціональних груп з ініціатором. Найбільш економічно доцільним є останній спосіб оскільки не вимагає суттєвих змін у технологію виробництва.
Присутність епоксидних смол в нафтополімерних і збільшення їх вмісту веде до покращення еластичності плівок підвищення адгезії і зниження кольору. Варто також відмітити що всі плівки прозорі волого- та водостійкі. Зекономічної точки зору одержання композицій на основі епоксидної та нафтополімерних смол дозволяє зменшити витрати виробництва та полегшити технологію оскільки при цьому утикається використання з’єднань з низькою температурою кипіння спалаху та самозаймання ліквідується стадії зупинки центрифугування та сушіння і відповідно покращується санітарно-гігієнічна та екологічна обстановка на виробництві.
Розрахунок затрат на проведення досліджень
Вартість досліджень розраховуємо за основними статтями затрат. Загальна сума затрат пов’язаних з дослідженням визначається як сума окремих статей затрат.
Вартість сировини та матеріалів необхідних для проведення досліджень здійснюється за формулою:
де Ц – ціна на сировину та матеріали;
А – витрата сировини та матеріалів на проведення досліджень.
Результати розрахунку наведені в таблиці 1:
Вартість речовиннеобхідних для проведення досліджень
Питома вартість витрат %
Нафтополімерна смола
Розрахунок енергозатрат
Оскільки енергетичні затрати на освітлення опалення та інші цілі належать до загально університетських витрат в цьому розділі потрібно визначити лише затрати на технологічні цілі.
На проведення одного досліду необхідно 6 год. Всього проводилось 4 досліди. В процесі досліджень на нагрів сировини за один дослід витрачалося 3год. Отже електрична плита працювала протягом:
Вага аналітична ВЛА-200 на протязі досліджень використовувалася біля 1год. при зважуванні реагентів та продуктів протягом 30 днів. Отже загальний час роботи аналітичної ваги становить:
Тва = 1 30 = 30 год.
Час роботи сушильної шафи приблизно рівний 2 год. Після проведення кожного досліду для сушіння використовуваного хімічного посуду:
В процесі одного досліду якірна мішалка працювала на протязі 3 год. апротягом всіх дослідів:
Апарат Сокслета протягом всіх досліджень працював лише 10 днів по 2год. за 1 день:
Тас = 2 10 = 20 год.
Результати розрахунків наведені в таблиці 2:
Потужність обладнання кВт
Тривалість досліджень год.
Кількість витраченої електроенергії кВтгод
Вага аналітична ВЛА-200
Шафа сушильна 2В-151
В цю статтю витрат включається також вартість води. Витрата води при проведенні лабораторних досліджень становила 16 м3. Ціна 1 м3 води 450 грн. Отже вартість води:
Ввода = V 450 = 16 450 = 720 грн.
В процесі досліджень ми використовували дві лампи штучного освітлення потужністю 150 Вт протягом 45 год.. Отже витрата на освітлення становить:
Восв = 063 45 150 2 1000 = 851 грн.
Загальна сума витрат за цією статтею становить:
Венерг = Вел.ен + Ввода + Восв = 8494 + 720 + 851 = 16545 грн.
Розрахунок фонду заробітної плати
Заробітна плата наукового керівника:
ЗПнк = Тк Тар = 30 400 = 1200 грн.
де Тк = 30 год. – кількість годин відведених для консультацій;
Тар = 40 – тариф грн.год.
На виконання дипломної роботи відводиться 6 місяців. Оскільки стипендія студента становить 730 грн. за 1місяць то за 6 місяців студент отримав:
Ст = 6 730 = 4380 грн.
Таким чином фонд заробітної плати становить:
ФЗП = ЗПнк + Ст = 1200 + 4380 = 5580 грн.
Відрахування у пенсійний фонд - 2 %:
ПФ = ФЗП 002 = 5580 002 = 11160 грн.
Відрахування у фонд зайнятості – 06 %:
ФЗ = ФЗП 0006 = 5580 0006 = 3348 грн.
Прибутковий податок становить 15 %:
ПП = ФЗП 015 = 5580 015 = 8370 грн.
Загальний фонд заробітної плати становить:
ЗФЗП = ФЗП + ПФ + ФЗ + ПП = 5580 + 11160 + 3348 +837 = 656208 грн.
Розрахунок вартості апаратури
Розрахунок вартості приладів та апаратури що необхідні для проведення досліджень здійснюється за таблицею 3:
Вартість приладів та апаратури
Невраховані витрати на апаратуру грн.
Загальна вартість грн.
Час роботи обладнання днів
Амортизаційні відрахування грн.
Шафа сушильна 2В-200
Шафа витяжна хімічна ШВХ-2 1000Ч750Ч2470
Де невраховані витрати на апаратуру становлять 75 % від вартості обладнання а норма амортизаційних відрахувань 15 %.
Загальні невраховані витрати на апаратуру:
ЗНВ = Ц 0075 = 15769 0075 = 1183 грн.
Загальна вартість обладнання :
ЗВО = Ц + ЗНВ = 15769 + 1183 = 16952 грн.
Амортизаційні відрахування на обладнання:
А = ЗВО Т НА 365 100%
де Т – фактичний час роботи обладнання дні;
НА – норма амортизаційних відрахувань%
Розрахунок вартості оренди приміщення наведено в таблиці 4:
Вартість оренди будівлі
Призначення приміщення
Вартість оренди за 1 м2 за 1 міс. грн.
Загальна вартість оренди за 6 міс. грн.
Загальна вартість лабораторних досліджень
Вартість дослідження розраховуємо на підставі розрахованих статей затрат групуючи їх на прямі та накладні витрати в таблиці 5. Одночасно визначаємо структуру витрат.
Сировина і матеріали
Енергозатрати (в т. ч. і вода)
Фонд заробітної плати з нарахуваннями
Амортизаційні відрахування обладнання
Накладні витрати (20% від прямих)
Таким чиномвартість лабораторних досліджень становить 1001238 грн.
Техніко-економічна оцінка результатів досліджень
В даній роботі досліджувались закономірності одержання композицій на основі епоксидних та нафтополімерних смол з використанням різних затверджувачів.
Для одержання вуглеводневих смол використовують дешеву сировину яка є відходами піролізу дизельного палива. Також наявність в композиціях епоксидних смол дозволяє полегшити технологію та знизити витрати виробництва.
Рекомендуемые чертежи
- 06.06.2020
- 24.01.2023