Курсовая работа по расчету аппарата емкостного ВКЭ 1-3-12, 5-1



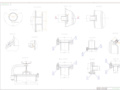
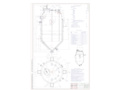
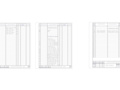
- Добавлен: 25.01.2023
- Размер: 675 KB
- Закачек: 0
Узнать, как скачать этот материал
Подписаться на ежедневные обновления каталога:
Описание
Курсовая работа по расчету аппарата емкостного ВКЭ 1-3-12, 5-1
Состав проекта
![]() |
![]() |
![]() ![]() ![]() |
![]() ![]() ![]() ![]() |
![]() ![]() ![]() |
![]() ![]() ![]() ![]() |
![]() ![]() ![]() |
![]() ![]() ![]() ![]() |
![]() ![]() ![]() |
Дополнительная информация
Контент чертежей
ВКЭ-2.dwg

Спецификация.dwg

ВКЭ-1.dwg

Рекомендуемые чертежи
Свободное скачивание на сегодня
Обновление через: 5 часов 31 минуту
- 22.08.2014
- 29.08.2014
Другие проекты
- 22.08.2014