Кран с вращающейся колоной 6.3 т




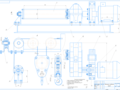
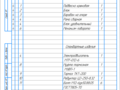
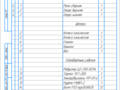

- Добавлен: 25.01.2023
- Размер: 701 KB
- Закачек: 1
Описание
Кран с вращающейся колоной 6.3 т
Состав проекта
![]() |
![]() |
![]() ![]() ![]() |
![]() ![]() ![]() ![]() |
![]() ![]() ![]() ![]() |
![]() ![]() ![]() ![]() |
![]() ![]() ![]() ![]() |
![]() ![]() ![]() ![]() |
![]() ![]() ![]() ![]() |
Дополнительная информация
Кран с вращ колоной.doc
Поворотный стреловой кран с вращающейся колонной представляет собой колонну несущую стрелу 5 с грузовым полиспастом 4 механизм подъёма груза 2 механизм поворота крана 6.
Колонна опирается на один упорный и 2 радиальных подшипника 1. Стрела поддерживается жёсткой тягой и полиспастом или полиспастом 3.
Поворотные краны выполненные по данной схеме называются стационарными стреловыми кранами с вращающейся колонной (с не вращающимся механизмом поворота).
Рассчитаем поворотный стреловой кран с вращающейся колонной при следующих исходных данных:
-грузоподъёмность 6.3т
-скорость подъёма груза 13ммин
-скорость перемещения тележки 23 ммин
-частота вращения крана 2.1 обмин
-режим работы тяжёлый (ПВ40%)
Расчёт механизма подъёма.
1.Выбор полиспаста диаметра барабана и блоков.
Для проектируемого крана принимаем механизм подъёма схема которого представлена на рис. 1.
В применяем простой полиспаст при использовании которого обеспечиваются вертикальное перемещение груза одинаковая нагрузка на подшипники барабана и на ходовые колёса тележки независимо от высоты подъёма груза. Для крана грузоподъёма Q=6.3Н принимаем простой полиспаст (а=1) кратностью u=4.
Максимальное натяжение в канате набегающем на барабан при подъёме груза : Н
где z –количество ветвей на которых висит груз
При сбегании каната с подвижного блока К.П.Д. полиспаста:
где - К.П.Д. блока с учётом жесткости каната для блока на подшипниках качения .
Канат выбираем по разрывному усилию согласно Правилам Госгортехнадзора:
где - коэффициент запаса прочности каната принимаемый по табл.11.
Из приложения 1 выбираем канат стальной двойной свивки типа ЛК-3 конструкции 6х25(1+66+12)+1 о.с. ГОСТ 7665-69 диаметром 14.5мм при расчётном пределе прочности проволок площадью сечения всех проволок 77мм2 и с разрывным усилием 12500 Н.
Диаметр блока и барабана по центру наматываемого каната
Диаметр блока и барабана по дну канавки
где е – коэффициент зависящий от режима работы и типа грузоподъёмной машины (табл.12). Для тяжёлого режима е= 20.
Диаметр блока крюковой подвески (по центру наматываемого каната) принимаем 300 мм
Диаметр уравнительного блока 300=240 мм.
2.Выбор и проверочный расчёт крюковой подвески.
По номинальной грузоподъёмности Q= 6.3тс и режиму работы выбираем крюк однорогий тип Б № 15 ( ГОСТ 6627-74).
Крюк изготовлен из стали 20 имеющей предел прочности предел текучести предел выносливости
. Резьба шейки крюка – метрическая М52 с внутренним диаметром dв= 46.5мм. На прочность крюк проверяем в сечениях 1-1 А-А и А’-A’ .
В сечении 1-1 крюк рассчитываем на растяжение:
кгссм2[ ]=500 600 кгссм2.
В сечении А-А крюк рассчитываем как кривой брус нагруженный эксцентрично приложенным усилием. Наибольшее напряжение растяжения внутренних волокон сечения А-А:
где F – площадь сечения А-А. После замены действительного сечения равновеликой трапецией имеем:
где е2 – расстояние от центра тяжести сечения до внутренних волокон
k – коэффициент зависящий от кривизны и формы сечения крюка
r – расстояние от центра приложения нагрузки до центра тяжести сечения
D= 95 мм – диаметр зева
е1 – расстояние от центра тяжести сечения до наружных волокон
Напряжение в сечении А’-А’ определяем при условии когда стропы расположены под углом 450 к вертикали.
Усилие разгибающее крюк
Наибольшее напряжение растяжения внутренних волокон в сечении А’-А’:
Касательное напряжение в сечении А’-А’:
Суммарное напряжение в сечении А’-А’:
Допускаемое напряжение кгссм2.
Расчётные напряжения в сечениях А-А и А’-А’ меньше допускаемых.
Высота гайки должна быть не менее:
где t =0.5см – шаг резьбы
р=300 350 кгссм2 – допускаемое напряжение на смятие сталь по стали (материал гайки сталь 45)
Для метрической резьбы высота гайки
Высота гайки с учётом установки стопорной планки Н= 65 мм.
Наружный диаметр гайки
4.Упорный подшипник.
Для крюка диаметром шейки d1=55 мм выбираем упорный однорядный подшипник лёгкой серии 8211 ГОСТ 6874-75 со статической грузоподъёмностью С0= 12900 кгс.
Расчётная нагрузка на подшипник должна быть равна или меньше статической грузоподъёмности:
где коэффициент безопасности.
Она изготовлена из стали 45имеющей предел прочности предел текучести предел выносливости .
Траверсу рассчитываем на изгиб при допущении что действующие на неё силы сосредоточенные кроме того считаем что перерезывающие силы незначительно влияют на изгибающий момент. Расстояние между осями крайних блоков 266мм. Расчётная нагрузка на траверсу Qp= 7560 кгс.
Максимальный изгибающий момент (сечение А-А)
Момент сопротивления среднего сечения траверсы
где - допускаемое напряжение на изгиб кгссм2.
Момент сопротивления среднего сечения траверсы ослабленной отверстием:
ширина траверсы назначается с учётом наружного диаметра D1 посадочного гнезда для упорного подшипника
Изгибающий момент в сечении Б-Б:
Минимальный диаметр цапфы под подшипник
6.Выбор подшипников блоков.
Поскольку подшипники блоков работают при переменном режиме нагрузки то эквивалентную нагрузку определим по формуле:
где Р1 Р2 Р3 Р4 – эквивалентные нагрузки
L1 L2 L3 L4 – номинальные долговечности.
С учётом графика загрузки механизма подъёма при режиме работы радиальные нагрузки на подшипник составляют:
Эквивалентные нагрузки при каждом режиме:
Долговечность подшипника номинальная и при каждом режиме нагрузки:
где Lh- ресурс подшипника Lh = 5000 ч.(XII)
n – частота вращения подвижного блока крюковой подвески с которого канат сматывается на барабан при установившемся режиме
Dбл – диаметр блока по центру наматываемого каната. Эквивалентная нагрузка:
Динамическая грузоподъёмность кгс.
Для данного диаметра цапфы по динамической грузоподъёмности выбираем шарикоподшипник радиальный однорядный лёгкой серии 212 (ГОСТ 8338-75) внутренний диаметр d= 60мм наружный диаметр D= 110мм ширина подшипника В=22 мм динамическая грузоподъёмность С= 4110 кгс (приложение XIII).
7.Расчёт узла барабана.
Принимаем барабан диаметром D=300 мм по дну канавки.
Расчётный диаметр барабана Dб= 314.5 мм (по центру наматываемого каната).
Длина каната наматываемого на одну половину барабана
Число витков нарезки барабана
где 1.5 2 – число запасных витков.
Длина нарезки на одной половине барабана
где tн – шаг нарезки барабана (приложение XIV) для каната dк=14.5мм tн=17мм.
Полная длина барабана
где l3=4tн – длина участка с каждой стороны барабана используемая для крепления для закрепления каната
Барабан отлит из чугуна СЧ15-32 с пределом прочности на сжатие .
Толщину стенки барабана определяем из расчёта на сжатие:
где к – коэффициент запаса прочности для крюковых кранов k=4.25 (приложение XV).
Толщина стенки проектируемого чугунного барабана
Принимаем толщину стенки 16 мм.
Кроме сжатия стенка барабана испытывает деформацию изгиба и кручения.
Крутящий момент передаваемый барабаном
Сложное напряжение от изгиба и кручения:
где W – экваториальный момент сопротивления поперечного сечения барабана
D= 30см D2= 26.8 см
-коэффициент приведения напряжений .
8.Расчёт узла крепления каната к барабану.
Принимаем конструкцию крепления каната к барабану прижимной планкой имеющей трапециевидные канавки. Канат удерживается от перемещения силой трения возникающей от зажатия его между планкой и барабаном болтами (шпильками).начиная от планки (точка Б) предусматривают дополнительные витки (1.5 2) способствующие уменьшению усилия в точке закрепления каната.
Натяжение каната перед прижимной планкой (точка Б)
где е=2.72 – основание натурального логарифма
f – коэффициент трения между канатом и барабаном (f=0.1 0.16)
- угол обхвата канатом барабана принимаем .
Суммарное усилие растяжения болтов
где f1 – приведенный коэффициент трения между планкой и барабаном при угле заклинивания каната
- угол обхвата барабана канатом при переходе от одной канавки к другой.
Суммарное напряжение в болте при затяжке крепления с учётом растягивающих и изгибающих усилий:
где - коэффициент запаса надёжности крепления каната к барабану
кгс – усилие изгибающее болты
7 мм – внутренний диаметр болта М20 изготовленного из стали Ст3
Допускаемое напряжение для болта
9.Расчёт оси барабана.
Ось барабана изготавливают из стали 45 (ГОСТ 1050-88) с пределом прочности кгссм2. После конструктивной проработки узла производим расчёт усилий действующих на ось а также минимального допускаемого диаметра оси.
При номинальном грузе на крюке равнодействующая от усилий в ветвях каната находится на расстоянии мм от правой оси В.
Усилия действующие со стороны ступиц на ось:
Строим эпюры изгибающих моментов и перерезывающих сил:
При известном изгибающем моменте диаметр оси приближенно вычисляем по формуле
см. принимаем =6.5см.
10.Выбор подшипников оси барабана.
Ось устанавливаем на ролико- или шарикоподшипники радиальные сферические двухрядные.
Подшипник опоры В вставляем в выточку тихоходного вала редуктора Ц2- 350 имеющего следующие размеры: диаметр 110 мм глубина 60 мм. Поскольку ос барабана не вращается относительно вала редуктора то подшипник опоры В выбираем по статической нагрузке.
Расчётная нагрузка на подшипник
По этой нагрузке для диаметра цапфы 50 мм выбираем подшипник который должен иметь наружный диаметр 110 мм.
Таким условиям удовлетворяет роликоподшипник радиальный сферический двухрядный № 3610 (ГОСТ 5721-75) со статической грузоподъёмностью 10300 кгс.
Учитывая что динамическая грузоподъёмность определённого подшипника выше статической и для соблюдения принципа унификации принимаем в качестве опоры А такой же подшипник № 3610.
Расчёт мощности двигателя и выбор редуктора.
При подъёме номинального груза мощность двигателя механизма подъёма
где - кпд механизма (приложение XXXIII).
Предварительно до проверки мощности двигателя на нагрев принимаем ближайший по каталогу двигатель меньшей мощности. Из приложения XXXIV выбираем электродвигатель переменного тока с фазовым ротором типа MTF312-6 мощностью N=15 кВт частотой вращения n= 955 мин-1 (радс) максимальным моментом Мп.max= 48 кгс·м моментом инерции ротора Jp= 0.0318 кгс·м·с2. Номинальный момент на валу двигателя кгс·м. Отношение максимального к номинальному
Передаточное число редуктора
Редуктор механизма подъёма выбираем исходя из расчётной мощности частоты вращения двигателя передаточного числа и режима работы.
По каталогу (приложение XLI XLVI) выбираем редуктор типа Ц2-350—16.3(суммарное межосевое расстояние А=350мм передаточное число и=16.3 схема сборки 4 вал тихоходный с концом под зубчатую муфту) .
Предельная консольная нагрузка на конце тихоходного вала редуктора Ц2-350 При тяжёлом режиме работы принимается 1800 кгс (приложение XLVI). Действующая нагрузка от оси барабана на конец тихоходного вала редуктора составляет 933 кгс которая меньше предельной.
Допустимая величина предельного момента передаваемого редуктором
где Nред= 24.1кВт – табличное значение мощности при тяжёлом режиме и n= 955 мин-1
Мред – табличное значение момента выбранного редуктора
- кратность пускового момента принимаемая в зависимости от режима работы (табл.14).
Средний момент электродвигателя в период пуска
Для выбранного двигателя кратность максимального пускового момента
Поскольку то редуктор удовлетворяет условиям перегрузки двигателя в период пуска.
Статический момент на валу двигателя при подъёме грузов различных по весу определяем по формуле
где - усилие в навиваемом на барабан канате при подъёме груза кгс
а – число ветвей навиваемых на барабан
- кпд механизма подъёма принимаемый в зависимости от поднимаемого груза по графику (рис.36).
При подъёме номинального груза определяем статический момент на валу двигателя :
Усилие в канате свиваемом с барабана при опускании груза Q:
Статический момент на валу двигателя при опускании номинального груза
Время пуска привода при подъёме и опускании груза
где Jпр – момент инерции движущих масс приведенный к валу двигателя при подъёме и опускании груза
- угловая скорость двигателя
Мст. – статический момент на валу двигателя при подъёме или опускании груза Мст. =Мп или Мст=Моп.
Момент инерции кгс·м·с2 движущихся масс механизма приведенный к валу двигателя при подъёме груза:
0318 кгс·м·с2 -момент инерции ротора 0.0474 кгс·м·с2 – момент инерции зубчатой муфты с тормозным шкивом (приложение XLVII) выбранной предварительно по Мпред
-коэффициент учитывающий моменты инерции масс деталей вращающихся медленнее чем вал двигателя
2 кгс·с2м 481.5 кгс·с2м 321 кгс·с2м - масса поднимаемого груза
- общее передаточное число механизма .
кпд механизма (рис 36)
157 м –радиус барабана по центру наматываемого каната.
При подъёме номинального груза:
Время пуска при подъёме и опускании груза соответственно равно:
Усилия в канате статические моменты на валу моменты инерции движущихся масс механизма приведенные к валу двигателя время пуска при подъёме и опускании Q и Q приводим в табл.1
Грузоподъёмность кгс
Усилие в канате навиваемом на барабан при подъёме груза Sп кгс
Кпд механизма подъёма
Усилие в канате свиваемом с барабана при опускании груза Sоп кгс
Статический момент кгс·м при
-опускании груза Моп
Приведенный момент инерции при подъёме и опускании груза Jпр.п кгс·м·с2
Ускорение мс при пуске
Ускорение при пуске поднимаемого номинального груза
Среднеквадратичный момент эквивалентный по нагреву действительному моменту возникающему от заданной загрузки электродвигателя механизма подъёма в течении цикла
Строим график загрузки в течении цикла работы. Статические моменты развиваемые электродвигателем в течении цикла загрузки определяем согласно стр.82:
Для крана работающего в машиностроительном цехе средняя высота подъёма груза Нс= 1.5м.
Время установившегося движения:
Суммарное время за цикл работы:
-установившегося движения =55.5 с
- неустановившегося движения с.
Время пауз за цикл работы при ПВ= 40 %:
Число включений в час .
Эквивалентная мощность по нагреву: кВт.
Следовательно выбранный двигатель удовлетворяет условию нагрева (NЭ NН).
Тормоз устанавливаем на быстроходном валу редуктора. Расчётный тормозной момент кгс·м
где - коэффициент запаса торможения по Правилам Госгортехнадзора для тяжёлого режима 2 (табл. 18)
Мст.т – статический момент на валу двигателя при торможении
По таблице (приложение LI) выбираем двухколодочный тормоз типа ТКТ- 300 с наибольшим тормозным моментом МТ=50 кгс·м отрегулированным на расчётный момент.
Время торможения механизма подъёма:
где Jпр – момент инерции движущих масс приведенный к валу тормоза торможении
- при опускании груза
Выбираем диаметр шкива D= 300мм.
Тормозной шкив изготавливаем из стального литья марки 45Л
Тормозные колодки футерованы фрикционной лентой типа Б ГОСТ 1198-69 с коэффициентом трения f=0.3 допускаемое давление =6 кгссм2.
Между двигателем и редуктором устанавливаем зубчатую муфту с тормозным шкивом DТ =300 мм (прил. XLVII) имеющую следующую характеристику: наибольший передаваемый крутящий момент 320кгс м момент инерции Jм = 0047 кгс· м · с2.
Крутящий момент передаваемый муфтой в период пуска двигателя при опускании номинального груза
где - суммарный момент ротора электродвигателя и полумуфты насаженной на вал электродвигателя
0318+0.0121=0.0439 кгс·м·с2.
Момент инерции полумуфты насаженной на вал электродвигателя
Крутящий момент передаваемый муфтой в период торможения двигателя при подъеме номинального груза
Максимальный крутящий момент при пуске двигателя
М ПП = МП.max— MП1 =48-18.16=30 кгс ·м.
Крутящий момент от сил инерции передаваемый муфтой
где —момент инерции машины (за исключением момента инерции ротора и полумуфты насаженной на вал двигателя)
097-0.0439=0.053 кгс ·м· с2.
Крутящий момент передаваемый муфтой в период пуска :
Из вычисленных значений моментов выбираем момент Мтях= 34.5 кгс ·м.
Определяем расчетный крутящий момент для муфты
М расч = k1Мтах= 1.3·34.57=44.94 кгс ·м.
где k1 — коэффициент учитывающий степень ответственности муфты (прил. LIV).
Выбранная муфта удовлетворяет условию передачи максимального крутящего момента. При расчете по номинальному моменту расчетный момент
М расч = k1k2 МН(182)
где k2— коэффициент учитывающий условия работы муфты (прил. LIV).
Необходимо чтобы максимальный кратковременный момент не превышал двукратного момента допускаемого муфтой (приведенного по ГОСТ 5006—55).
Расчетные моменты для упругих втулочно-пальцевых муфт:
при расчете по номинальному моменту
при расчете по максимальному моменту
Между барабаном и редуктором установлена зубчатая муфта. Крутящий момент передаваемый муфтой
Расчётный момент для выбора муфты
М расч = k1k2 МН= 1.55·1.2· 513 =955 кгс·м
По таблице (прил.LV) выбираем стандартную зубчатую муфту ГОСТ 5006-55 №9 с модулем m=6мм числом зубьев z=46 шириной зуба b=35 мм толщиной зуба S1=8.91 мм наибольшим моментом передаваемым муфтой равным 300 кгс·м.
Расчет механизма поворота.(рис.2)
Вес крана G = 4 тс расстояние от оси вращения до центра тяжести
с = 3 м расстояние между подшипниками h = 3 м .
Определяем действующие нагрузки и реакции в опорах. Вертикальная реакция
V=Q+G =6.3 +4 =10.3 тс.
Расчетная нагрузка на подшипник
Qp = kV = 1.4· 10.3 =14.4 тс
где k =1.4 — коэффициент безопасности (прил. X).
По расчетной нагрузке (ГОСТ6874—75 прил. IX) выбираем упорный шарикоподшипник 8213 с допускаемой осевой статической грузоподъемностью 15300 кгс внутренним диаметром d= 65 мм наружным диаметром D= 100 мм.
Горизонтальную реакцию Н определяем из равенства нулю суммы моментов всех действующих сил относительно точки В1:
Qp = kH =1.4 ·10.4=14.5 тс
где k = 14 —коэффициент безопасности (прил. X).
По этой нагрузке выбираем однорядный шарикоподшипник [4] №322 (ГОСТ 8338 — 75 прил. XIII) с допускаемой статической грузоподъем-ностью 17 тс внутренним диаметром d =100 мм наружным диаметром D= 240 мм высотой В=49мм.
Статическая грузоподъемность выбранного подшипника больше расчётной.
Общий статический момент сопротивления повороту равен сумме моментов сил от ветра уклона и трения:
где - сумма моментов сил трения в подшипниках опор
MTp=M Tp(dl) + M TP(d2)+M Tp(d3).
Момент сил трения в верхнем подшипнике (точка A1)
где f=0.015 0.02 – приведенный коэффициент трения шарикоподшипника
d1 = 0.175 м – средний диаметр подшипника.
Момент сил трения в нижнем радиальном подшипнике (точка В)
Момент сил трения в упорном подшипнике
M Tp(d3)=Vf0015 кгс·м.
Для упорных подшипников скольжения в расчетах принимают средний диаметр трения d3cp = .
Момент сил ветра состоит из двух моментов действующих на
Момент сил ветра действующий на кран
МКр = FKpqonвc = 6 · 15 · 1 · 15 · 1 · 4 = 540 кгс м
где FKР = м2 — наветренная площадь крана;
кгсм2; nв = 1; с = 15; = 1;
= 4. м — расстояние от оси вращения крана до центра действия
ветровой нагрузки м.
Момент сил ветра действующий на груз
МГP = FГРq0cA = 10· 15· 1· 8 = 1200 кгс м
где Frp =10м2 — наветренная площадь груза;
Тогда Мв = 540+1200=1740кгс м.
Момент сил возникающих от наклона крана
Му = (QA + Gc)sin = (6300· 8 +4000·3 ) 002 =1248 кгс м
где — угол наклона принимаем = 1°12'. Общий статический момент
МCT =1740+1248+13.65+13.65+6.37= 1787 кгс м.
Момент сил инерции масс при пуске привода
где — суммарный момент инерции масс груза крана механизма поворота приведенный к оси вращения крана
JB = (J'гр + J'кр) = 12(41088+ 3672) =53712 кгс . м . с2;
Jr'p = mгр A2 =642·82=41088 кгс м с2;
J’кр =mкр c2 =408·82=3672 кгс м с2;
— угловая скорость поворота крана
tn = 23 с — время пуска принимаемое согласно рекомендациям ВНИИПТмаш (линейное ускорение конца стрелы должно быть не более 1 мс2):
Расчетная мощность двигателя
= 15 18 — средний коэффициент перегрузки для асинхронных двигателей с фазовым ротором. Принимаем = 165.
По каталогу выбираем электродвигатель типа MTF112-6мощ-
ностью N =5.8 кВт при ПВ=40 % п=930мин-1 (= 97.4 радс)
M n.max = кгс м кгс м с2 (прил. XXXIV).
Общее передаточное число механизма поворота
Принимаем передаточное число зубчатой передачи ив =20 Тогда передаточное число червячного редуктора
Выбираем стандартный редуктор Ц2-250-19.88 и уточняем ив =
Проверку выбранного двигателя по условиям нагрева выполняем с использованием метода номинального режима работы.
Суммарный момент статического сопротивления повороту приведенный к валу двигателя
Номинальный момент выбранного двигателя
Мн = 975= 975 =6 кгс м.
Коэффициент загрузки двигателя при установившемся движении
Пользуясь графиком (рис. 79 а) при 0.78 находим относительное время пуска t n.o = 24 с. Определяем время разгона привода при повороте крана с номинальным грузом
где Jпр — суммарный момент инерции вращающихся масс механизма поворота крана массы груза и массы вращающейся части крана приведен- ный к валу двигателя;
- угловая скорость двигателя. Суммарный момент инерции масс приведенный к валу двигателя
Jпр =Jмех + Jгр+ J.кр
где Jмех — момент инерции вращающихся масс механизма поворота крана
Jмех = (Jp + JM) = 12 (0.0069+0.00763) =0.0174
Jгр — момент инерции массы груза приведенный к валу двигателя
Jкр — момент инерции массы вращающейся части крана приведенный к валу двигателя
Тогда Jпр = 0 0174 + 00.246+0 0.022= 0285 кгс м с2.
Время разгона привода
Ускорение конца стрелы при пуске
что меньше допускаемого [a] = 06 1 мс2.
Время рабочей операции при среднем угле поворота α = 90° (14 оборота)
Определяем отношение
По графику (рис. 45) находим
Необходимая мощность
Эквивалентная мощность
Номинальная мощность
Следовательно выбранный электродвигатель MTF 112-6 удовлетворяет условиям нагрева.
При перегрузке электродвигатель должен удовлетворять условию
где Мп и МH — пусковой и номинальный моменты двигателя. Пусковой момент:
где М’СТ — суммарный статический момент сопротивления вращению;
М”Д — динамический момент от вращательно движущихся масс механизма и крана;
М’”Д — динамический момент от вращательно движущейся массы груза
тогда Мп = 4.74+ 3.18 = 7.92 кгс м. Коэффициент перегрузки двигателя при пуске
Определение тормозного момента и выбор тормоза.
Принимаем время торможения tT = 5 с; линейное замедление конца стрелы
а = еТA = 0044 · 8 =0.352 мс2
где ет —угловое замедление
МT = МB.T + МУ.Т + M”Д.Т + M’”Д.Т —M’ТР
где МB.T+ МУ.Т= кгс·м
сумма моментов сил от ветра и уклона приведенных к валу тормоза;
M”Д.Т + M’”Д.Т= кгс·м.
МT = 13.65 +13.65 + 6.37 = 33.67 кгс·м
Выбираем двух колодочный тормоз ТКТ-200 с тормозным моментом Мт = 16 кгс м (прил. LI) который обеспечит торможение крана за более короткое время как было принято вначале (5 с). Следовательно его надо отрегулировать на нужный тормозной момент.
З. Расчет металлоконструкций крана.
Действующие нагрузки; вес груза собственный вес металлоконструкций силы инерции
усилия в грузовом канате (рис. ). Нагрузка от веса поднимаемого груза
Q' = Qka =6300· 12 =7560 кгс
где kд — динамический коэффициент.
Рис.4 Расчетная схема Рис.5 Схема к расчету металлокон-
определения размеров фрик- струкций крана
Вес стрелы изготовленной из трубы с наружным диаметром Dн = 200 мм толщиной стенки 15 мм Go =360 кгс. Материал — сталь ВМ СтЗсп.
Определяем усилие сжимающее стрелу при условии Mb = 0 по формуле
Усилие сжимающее стрелу от действия грузового каната
Суммарное сжимающее усилие
Рсж = Рсж + Р’сж = 14 +1.9=15.9тс.
Момент изгибающий стрелу в вертикальной плоскости посередине стрелы
Напряжения в крайних волокнах сечения трубы от действия сжимающих нагрузок и изгибающего момента от собственного веса стрелы
где F — площадь поперечного сечения трубы;
F = DСP = 314 ·18.5·15 =87.13 см2
WИ — момент сопротивления изгибу трубы;
— коэффициент продольного изгиба.
Коэффициент продольного изгиба определяют табличным спо собом в зависимости от гибкости стрелы. Гибкость стрелы
Рис.6 Схема соединения колонны и стрелы
где Lc — расчетная длина стрелы; принимаем Lc= 8м (рис. 4);
г — радиус инерции сечения стрелы
см — момент инерции сечения
F — площадь поперечного сечения стрелы см2.
Тогда ; величина коэффициента продольного изгиба φ = 045. При повороте крана возникает сила инерции масс груза и стрелы которые также изгибают стрелу в горизонтальной плоскости. Линейное ускорение конца стрелы при пуске определено ранее а =0.4 мс2.
Масса стрелы постоянного сечения приведенная к головке а релы.
Масса груза приведенная к головке стрелы при условии что груз поднят в крайнее верхнее положение
Сила инерции от массы груза и стрелы приложенная к головке стрелы
Fин = mа = (642+9)·0.4 =260.4 кгс.
Считая колонну абсолютно жесткой принимаем что у основания стрела полностью будет воспринимать изгибающий момент от силы инерции
Ми = Fин A=260.4·8= 2083 кгс·м
Напряжения в крайних волокнах в горизонтальной плоскости
Сила давления ветра на груз WB =150 кгс. Момент от силы ветра изгибающий стрелу в горизонтальной плоскости
Ми.в = WBLC = 150·8 = 1200 кгс м.
Напряжение в крайних волокнах сечения в горизонтальной плоскости от ветровой нагрузки
Суммарные напряжения в горизонтальной плоскости кгссм2
Колонна крана состоит из двух швеллеров №16 а связанных поперечными листами по длине и по торцам (рис. 5). В торцовых листах с обеих сторон закреплены оси на которые посажены упорный и радиальные подшипники. К полкам швеллеров приварены проушины для крепления стрелы зубчатого колеса и механизма подъема.
Рси.7 Опорный узел колонны поворотного крана
Площадь поперечного сечения одного швеллера F=19.5 см2 моменты инерции сечения относительно осей: 1Х = 823 см4; 1Y =78.8 см4
Моменты сопротивления сечения: Wx=103см3 Wy =16.4см3.
Определяем нагрузки действующие на колонну. Горизонтальная реакция
Н = 10.4 тс была определена ранее. Сжимающей нагрузкой при такой конструктивной схеме можно пренебречь так как основная нагрузка воспринимается нижним опорным узлом.
Горизонтальное (окружное) усилие возникающее при работе механизма поворота
где где Мкр =1787кгс м — крутящий момент относительно оси вращения крана;
D н. о = 2000 мм — диаметр зубчатого колеса. Реакция в точке В (рис. 8)
Наибольший момент изгибающий колонну
Мн = RВh1 =11658 · 0.16=1865 кгс м
так как можно принять h1 = 0 16 м.
Рис. 8. Схема к расчету колонны Рис. 9. Сечение колонны
Необходимый момент сопротивления сечения колонны изготовленной из стали ВМ СтЗ (рис. 9)
Фактический момент сопротивления сечения двух швеллеров
Напряжение в опасных сечениях
кгссм2 - 2100 кгссм2.
Спецификация мех-ма поворота-.spw

Электродвигатель МТF-011-6
Болт М12-6gх50.88.05
Болт М16-6gх50.88.05
Общий вид крана.cdw

Общее передаточное отношение привода
Частота вращения крана
Скорость подъёма груза
Высота подъёма груза
Скорость перемещения тележки
Режим работы средний.
Механизм подъёма .cdw

Общее передаточное отношение привода 1060 .
Скорость подъёма груза
Крутящий момент на выходном валу
Спецификация мех-ма подъёма .spw

Механизм поворота.cdw

Общее передаточное отношение привода .
Частота вращения крана обмин 0.8
Крутящий момент на выходном валу
Спецификация крана .spw
