Коробка скоростей токарно-винторезного станка




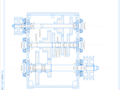
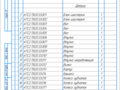
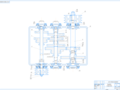
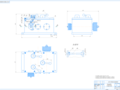
- Добавлен: 25.01.2023
- Размер: 796 KB
- Закачек: 0
Описание
Коробка скоростей токарно-винторезного станка
Состав проекта
![]() |
![]() |
![]() |
![]() |
![]() |
![]() ![]() ![]() |
![]() |
![]() ![]() ![]() |
![]() ![]() ![]() ![]() |
![]() |
![]() |
![]() ![]() ![]() |
![]() ![]() ![]() ![]() |
![]() ![]() ![]() ![]() |
![]() ![]() ![]() |
![]() ![]() ![]() ![]() |
![]() |
![]() |
![]() |
![]() ![]() ![]() |
![]() ![]() ![]() ![]() |
![]() |
![]() |
Дополнительная информация
структурная сетка.frw

Фрагмент.frw

моя коробка скоростей лучше.cdw

Коробка Скоростей ПЗ моя.doc
Основные размеры (параметры) – D=200 мм
Диапазон регулирования частот вращения – Rn=140
Компоновка привода- встроенная
АНАЛИЗ ТЕХНИЧЕСКИХ ХАРАКТЕРИСТИК СТАНКОВ
АНАЛОГИЧНЫХ ПРОЕКТИРУЕМОМУ
Сведем данные о станках в таблицу.
Технические характеристики токарно-винторезных станков с наибольшим диаметром обработки над станиной 200 мм.
ОПРЕДЕЛЕНИЕ ТЕХНИЧЕСКОЙ ХАРАКТЕРИСТИКИ ПРОЕКТИРУЕМОГО СТАНКА.
1 ВЫБОР ТЕХНОЛОГИЧЕСКИХ УСЛОВИЙ ИСПОЛЬЗОВАНИЯ СТАНКА.
Станок универсальный предназначен для выполнения чистовых и получистовых разнообразных токарных работ для нарезания метрической дюймовой модульных резьб (правых и левых) с нормальным и увеличенным шагом одно- и многозаходных резьб копировальных работ при помощи гидрокопировального устройства.
Все перечисленные виды работ выполняются по конструкционной стали (НВ 160-260) и по алюминиевым сплавам.
2 ОПРЕДЕЛЕНИЕ ПРЕДЕЛЬНЫХ ЧАСТОТ ВРАЩЕНИЯ.
Для токарно-винторезных станков при обработке в патроне Dmax определяется по формуле:
dmax=08*Dmaх=08*200=160 мм
Расчетный наименьший диаметр станка определяется по формуле:
dmin=012*dmax=012*160=176 мм
Находим vmax u vmin согласно справочной литературы [4]
vрас. =vтаб*К1*К2*К3
Материал инструмента
Определяем предельные числа оборотов станка:
nmax=(1000*Vmax)(*dmin)=(1000*223)(314*17.6)=4033 обмин
nmin=(1000*Vmin)(*dmax)=(1000*31)(314*160)=62 обмин
3 ОПРЕДЕЛЕНИЕ РЯДА ЧАСТОТ ВРАЩЕНИЯ.
Для данного проектируемого станка назначаем ступенчатый тип регулирования.
Знаменатель ряда назначаем φ=125.
Определим число ступеней частот вращения шпинделя:
Z=1+lg Rn lg =1+ lg140 lg 125=2315
Принимаем число ступеней Z=24.
Принимаем ряд частот вращения шпинделя:
n1=20 n2=25 n3=32 n4=40 n5=50 n6=63 n7=80 n8=100 n9=125 n10=160 n11=200 n12=250 n13=315 n14=400 n15=500 n16=630 n17=800 n18=1000 n19=1250 n20=1600
n21=2000 n22=2500 n23=3125 n24=4000.
4 ВЫБОР ЭЛЕКТРОДВИГАТЕЛЯ.
Анализируя подобные станки принимаем мощность главного привода 4 кВт и согласно справочной литературы [3] табл. [1] выбираем двигатель АИР100S2 с синхронной частотой вращения 3000 обмин.
РАЗРАБОТКА КИНЕМАТИЧЕСКОЙ СХЕМЫ СТАНКА.
1. ПОСТРОЕНИЕ СТРУКТУРНОЙ СЕТКИ.
Определим структурную формулу станка:
Определим число конструктивных вариантов привода:
Ккон=m! q! =4! 3! = 246=4
Определим число кинематических вариантов привода:
Общее количество вариантов:
K= Kкон* Kкин=4*24=96
р1 =2 р2 =3 р3 =2 р4 =2
х1 =3 х2 =1 х3 =6 х4 =124.2 ПОСТРОЕНИЕ ГРАФИКА ЧАСТОТ ВРАЩЕНИЯ.
По структурной сетке привода построим график частот вращения по которому можно определить фактические частоты вращения и передаточные отношения передач в группах.
КИНИМАТИЧЕСКАЯ СХЕМА
МЕХАНИЗМ ПЕРЕБОРА В ДАННОЙ РАБОТЕ НЕ ПРОЕКТИРУЕТСЯ
ОПРЕДЕЛЕНИЕ ПАРАМЕТРОВ ПЕРЕДАЧ.
1 ОПРЕДЕЛЕНИЕ ПЕРЕДАТОЧНЫХ ОТНОШЕНИЙ.
По графику частот вращения определяем передаточные отношения в группах передач.
Значения занесены в таблицу.
2 ОПРЕДЕЛЕНИЕ ДИАМЕТРОВ ШКИВОВ.
Принимаем диаметр шкива электродвигателя D1=63 мм.
Диаметр ведомого шкива:
D2= D1 * iр=63*098083=74 мм
=098(коэффициент проскальзывания)
3 ОПРЕДЕЛЕНИЕ ЧИСЕЛ ЗУБЬЕВ.
После того как определены передаточные отношения всех передач входящих в состав кинематической схемы необходимо определить числа зубьев зубчатых колес.
Для каждой группы передач между валами должно соблюдаться условие:
Da1 + D’a1 = Da2 + D’a2 = Da3 + D’a3 = = Dj + D’j = 2D0 = const.
т.е. сумма диаметров начальных окружностей сопряженных зубчатых колес одной группы должна быть постоянной.
Первая группа колес состоит из трех передач с отношениями:
a1 = 1;b1 = 1;a1 + b1 = 1 + 1 = 2;
a2 = 4;b2 = 5;a2 + b2 = 4 + 5 = 9;
a3 = 7;b3 = 11;a3 + b3 = 7 + 11 = 18.
Наименьшее общее кратное:
K1 = НОК (2 9 18) = 18.
z1 = K1 * a1(a1 + b1) = 18 * 12 = 9;
z2 = K1 * b1(a1 + b1) = 18 * 12 = 9;
z3 = K1 * a2(a2 + b2) = 18 * 49 = 8;
z4 = K1 * b2(a2 + b2) = 18 * 59 = 10;
z5 = K1 * a3(a3 + b3) = 18 * 718 = 7;
z6 = K1 * b3(a3 + b3) = 18 * 1118 = 11.
Для коробок скоростей минимальное число зубьев равно 18
Следовательно количество зубьев необходимо увеличить в n раз:
n > z minz31 = 187 = 257.
Вторая группа колес состоит из двух передач с отношениями:
a6 = 8;b6 = 5;a6 + b6 = 8 + 5 = 13;
a7 = 2;b7 = 5;a7 + b7 = 2 + 5 = 7.
K3 = НОК (13 7) = 91.
z7 = K3 * a6(a6 + b6) = 91 * 813 = 56;
z8 = K3 * b6(a6 + b6) = 91 * 513 = 35;
z9 = K3 * a7(a7 + b7) = 91 * 27 = 26;
z10 = K3 * b7(a7 + b7) = 91 * 57 = 65.
Расчет и проверка фактического ряда чисел оборотов
Допускаемое отклонение в зависимости от знаменателя геометрического ряда:
[Yn ] = ± 10 * ( - 1) % = ± 10 * (125 -1) = ± 25 %.
Стандартные числа оборотов n ст обмин
Фактические числа оборотов n ф обмин
n ф = n эл.дв2. * (D1*)D2 * z5z6 * z9z10 =
= 1500 * 63*09874 * 2133 * 2665 = 31685
n ф = n эл.дв.2 * D1*D2 * z3z4 * z9z10 =
= 1500 * 63*09874 * 2430 * 2665 =39832
n ф = n эл.дв2. * D11*D2 * z1z2 * z9z10 =
= 1500 * 63*09874 * 2727 * 2665 = 4979
n ф = n эл.дв.1 * D1*D2 * z5z6 * z9z10 =
= 3000 * 63*09874 * 2133 * 2665 = 6337
n ф = n эл.дв.1 * D1*D2 * z3z4 * z9z10 =
= 3000 * 63*09874 * 2430 * 2665 = 79665
n ф = n эл.дв.1 * D1*D2 * z1z2 * z7z8 =
=3000 * 63*09874 * 2727 * 2665 = 99581
n ф = n эл.дв2. * D1*D2 * z5z6 * z7z8 =
= 1500 * 63*09874 * 2133 * 5635 = 126739
n ф = n эл.дв2. * D1*D2 * z3z4 * z7z8 * =
= 1500 * 63*09874 * 2430 * 5635 = 159329
n ф = n эл.дв2. * D1*D2 * z1z2 * z7z8 =
= 1500 * 63*09874 * 2727 * 5635 = 199161
n ф = n эл.дв1. * D1*D2 * z5z6 * z7z8 =
=3000 * 63*09874 * 2133 * 5635 = 253478
n ф = n эл.дв1. * D1*D2 * z3z4 * z7z8 =
= 3000 * 63*09874 * 2430 * 5635 = 318658
n ф = n эл.дв1. * D1*D2 * z1z2 * z7z8 =
= 3000 *63*09874 * 2727 * 5635 = 200348
Отклонения значения фактических скоростей вращения лежат в пределах допустимых. Оставляем полученные числа зубьев без изменений.
РАСЧЕТ ДЕТАЛЕЙ И УЗЛОВ ПРОЕКТИРУЕМОГО СТАНКА
Расчету деталей и узлов предшествует определение их нагруженности т.е. определение действующих усилий а на валах привода - расчетных крутящих моментов.
Как правило расчетам на прочность долговечность жесткость подвергаются детали того узла который разрабатывается в проекте в виде сборочного чертежа. Например для коробки скоростей рассчитываются ременные и зубчатые передачи муфты валы и их опоры (в том числе шпиндель и его опоры) и т.д. Расчет производится параллельно с конструированием узла и окончательные размеры конструкции и деталей обосновываются расчетом.
Исходные данные для расчета
Частота вращения вала двигателя
1 ОПРЕДЕЛЕНИЕ МОЩНОСТЕЙ НА ВАЛАХ
При определении мощностей на валах применяются коэффициенты потерь КПД:
зз=099-КПД зубчатого зацепления
рп=098-КПД ременной передачи
пк=0995-КПД подшипников качения
NI= Nэлд* рп* пк2=4*098*09952=376 кВТ
NII= NI* зз*пк2=376*099*09952=361 кВТ
NIII= NII*зз*пк2=361*099*09952=333 кВТ
2 ОПРЕДЕЛЕНИЕ КРУТЯЩИХ МОМЕНТОВ НА ВАЛАХ.
Момент на валу определяется по формуле:
где Тi-искомый момент на i-ом валу
Ni-мощность на i-ом валу
nрасчi-частота вращения на i-ом валу
Приблизительно диаметры валов определяются по формуле:
где Тi-момент на i-ом валу
[]-допускаемое касательное напряжение для материала вала ([]=20Мпа).
Рассчитаем данные параметры и занесем результаты в таблицу.
Значения чисел оборотов моментов и уточненных по ГОСТ диаметров валов.
РАСЧЕТ ЗУБЧАТЫХ КОЛЕС
Желая получить относительно невысокую стоимость и небольшие габариты коробки скоростей выбираем для изготовления колес сталь 40Х ГОСТ 4543-71 (поковка). термообработку зубчатых колес: улучшение и закалка ТВЧ. Свойства материала после термообработки:
-твердость поверхности 48 .. 52
-твердость сердцевины269 .. 302
-предел текучестиsт = 750 МПа.
1 ОПРЕДЕЛЕНИЕ МЕЖОСЕВЫХ РАССТОЯНИЙ.
Расчет производим по допускаемым контактным напряжениям:
где - контактное напряжение
- для станков нормальной точности
МПа - предел контактной выносливости
- коэффициент безопасности
- коэффициент зависящий от вида передачи для прямозубой передачи
- крутящий момент на колесе
- коэффициент ширины зуба
U - передаточное число
- коэффициент учитывающий неравномерность нагрузки
2. Расчет модулей зубчатых колес
Округляем модуль до стандартного значения т.е. =3.5.
Округляем модуль до стандартного значения т.е. =2.5
Затем корректируем по получившимся значениям модулей т.е.
3 ГЕОМЕТРИЧЕСКИЙ РАСЧЕТ ЗУБЧАТЫХ ПЕРЕДАЧ.
Определение делительного диаметра.
Шестерни d1= mt* z1=35*27=945 мм
Колеса d2= mt* z2=35*27=945 мм
Шестерни d3= mt* z3=35*24=84 мм
Колеса d4= mt* z4=35*30=105 мм
Шестерни d5= mt* z5=35*21=735 мм
Колеса d6= mt* z6=35*33=1155 мм
Шестерни d7= m2* z7=25*56=140мм
Колеса d8= m2* z8=25*35=875 мм
Шестерни d9= m2* z9=25*26=65 мм
Колеса d10= m2* z10=25*65=1625 мм
Определение ширины колес.
b1=а*аw=015*81»12 мм
b2=а*аw=015*11375»17 мм
ПРОЧНОСТНЫЕ РАСЧЕТЫ.
1 РАСЧЕТ ВАЛОВ НА ПРОЧНОСТЬ.
Рассчитаем на прочность вал 2(смотри чертёж).
Определим нагрузку в опорах.
Вертикальная плоскость.
Горизонтальная плоскость.
Находим изгибающий момент в горизонтальной плоскости.
My(l1)=-Ray* l1=-575*113=-65 Н*м
My(x)=-Ray*x+Fr6*(x-l1)
My(l1)=-Ray*l1=-65 Н*м
My(l1+l2)=-Ray*(l1+l2)+Fr6*l2=-575*1989+2728*859=12 Н*м
My(х)=Ray*x-Fr2*(x-l1)+Fr7*(х-(l1+l2))
My(х)=-Ray*x+Fr6*(x-l1)-Fr9*(х-(l1+l2))
My(l1+l2+l3)=-Ray*(l1+l2+l3)+Fr6*(l2+l3)-Fr9*l3 =-575*2434+2728*(859+445)-4847*445=0
Находим изгибающий момент в вертикальной плоскости.
Mz(l1)=-Raz*l1=-645*113=-729 Н*м
Mz(x)=-Rax*x+Ft6*(x-l1)
Mz(l1+l2)=-Raz*(l1+l2)+Ft6*l2=-645*198.9+749.4*859=-63.9 Н*м
Mz(х)=-Rаz*x+Ft6*(x-l1)+Ft9*(х-(l1+l2))
Mz(l1+l2+l3)=-Rаz*(l1+l2+l3)+Ft6*(l2+l3)+Ft9*l3 =-645*243.4+749.4*130.4+1331.7*445=0
Суммарный изгибающий момент
Максимальный изгибающий момент М=73.2 Н*м
Крутящий момент Т=43.28 Н*м
Примем что нормальные напряжения изменяются по симметричному циклу
а касательные напряжения- по пульсирующему циклу
Материал вала - сталь 45(т=500 МПа в=750 МПа -1=330 МПа t-1=180 МПа).
tа=tм=05*t=Т(02*d3)=(4328*103)(02*223)=203 МПа
а=М(01*d3)=(732*103)(01*223)=687 МПа
Запас прочности рассчитывается по формуле:
где Кs=17 -для шлицевого соединения
ys=015- для углеродистой стали
es=076-для углеродистой стали
где Кt=14 -для шлицевого соединения
yt=01- для углеродистой стали
et=076-для углеродистой стали
Так как [S]=15 то условие прочности выполняется.
2 ПРОВЕРКА ПОДШИПНИКОВ НА ДОЛГОВЕЧНОСТЬ.
Проведем расчет для второго вала.
Наиболее нагруженной опорой является опора В.
Выбираем подшипник №204-шарикоподшипник радиальный однорядный.
Требуемый ресурс Lh=10000ч
Эквивалентная нагрузка:
P=(X*V* Fr+Y* Fa)*K*K=(1*1*7878)*13*1=102414Н
Эквивалентная долговечность:
Lhe=Lh*Khe=10000*0125=1250часов
Требуемый ресурс на расчетном режиме:
Lе=60*10-6*n*Lhe=60*106*800*1250=60 млн.об.
Расчетная динамическая грузоподъемность:
Подшипник пригоден так как расчетная динамическая грузоподъемность меньше требуемой.
В.И.Анурьев «Справочник конструктора - машиностроителя» том 1. - М.: Машиностроение 1978 - с. 728.
В.И.Анурьев «Справочник конструктора - машиностроителя» том 2. - М.: Машиностроение 1979 - с. 559.
В.И.Анурьев «Справочник конструктора - машиностроителя» том 3. - М.: Машиностроение 1979 - с. 557.
П.Ф.Дунаев О.П.Леликов «Конструирование узлов и деталей машин» - М.: Высшая школа 1985 - с. 416.
Н.С.Колев Л.В.Красниченко и др. «Металлорежущие станки» - М.: Машиностроение 1980 - с. 500.
А.С.Проников «Расчет и конструирование металлорежущих станков» - М.: Высшая школа 1968 - с. 431.
«Справочник технолога-машиностроителя» под ред. А.Г.Косиловой Р.К.Мещерякова том 2. - М.: Машиностроение 1986 - с. 496.
Задание к курсовому проекту 3
Анализ технических характеристик станков
аналогичных проектируемому ..4
Определение технической характеристики проектируемого станка ..4
1. Выбор технологических условий использования станка ..4
2. Определение предельных частот вращения 4
3. Определение ряда частот вращения ..5
4. Выбор электродвигателя .5
Разработка кинематической схемы станка 5
1. Построение структурной сетки ..5
2. Построение графика частот вращения ..7
Определение параметров передач 9
1. Определение передаточных отношений .9
2. Определение диаметров шкивов 9
3. Определение чисел зубьев колес .9
Расчет деталей и узлов проектируемого станка ..13
1. Определение мощностей на валах .13
2. Определение крутящих моментов на валах ..13
Расчет зубчатых колес .14
1. Определение межосевых расстояний ..14
2. Расчет модулей зубчатых колес 15
3. Геометрический расчет зубчатых передач 15
Прочностные расчеты ..17
1. Расчет валов на прочность .17
2. Проверка подшипников на долговечность .20
Список литературы 21
Спецификация.spw

Гайка М16 ГОСТ2524-70
Кольцо 22 ГОСТ13942-86
Кольцо 30 ГОСТ13942-86
Подшипник №202 ГОСТ8338-75
Подшипник №203 ГОСТ8338-75
Подшипник №205 ГОСТ8338-75
Шайба 6 65Г ГОСТ6402-70
Шайба 8 65Г ГОСТ6402-70
Шайба Н.08.01.05 ГОСТ11872-89
Шайба Н.24.01.05 ГОСТ11872-89
моя коробка скоростей.cdw

Уфимский государственный авиационный технический университет.doc
Пояснительная записка
К курсовой работе по дисциплине
«Металлорежущие станки»
(Обозначение документа)
киниматическая схема.frw

эпюра.frw

моя коробка скоростей 2.cdw

Механизм должен работать без рывков и заеданий.
Натяжение ремня обеспечить натяжными роликами.
Рекомендуемые чертежи
- 10.02.2022
- 29.05.2022