Контрольная работа по проектированию механосборочных участков и цехов



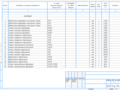
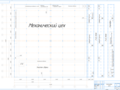
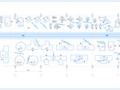
- Добавлен: 24.01.2023
- Размер: 545 KB
- Закачек: 0
Описание
Состав проекта
![]() |
![]() |
![]() ![]() ![]() ![]() |
![]() ![]() ![]() ![]() |
![]() ![]() ![]() |
![]() ![]() ![]() |
Дополнительная информация
План участка.spw

Станок консольно-фрезерный
Станок поперечно-строгальный
Станок горизонтально-расточной
Станок токарно-карусельный
Вертикально-сверлильный
Станок горизонтально-фрезерный
Наименование и техническая характеристика
обозначение документа
Станок вертикально-фрезерный консольный
Станок координатно-расточной
Станок внутришлифовальный универсальный
Плоскошлифовальный станок с прямоугольн.
Станок фрезерно-сверлильно-расточной
Станок продольно-строгальный
Радиально-сверлильный станок
Станок продольно-фрезерный
Кран консольно-поворотный
Автоматизированная напольная
танспортно-складская система
Компоновка цеха.cdw

персонала и инженерно-технических служб
инженерно-технических служб
Отделение ремонта инструмента и оснастки
Заготовительное отделение и склад
и переработки стружки
Контрольное отделение
План участка.cdw

Контрольная 1111ПМУиЦ.docx
по проектированию механосборочных участков и цехов
Ружевича Алексея Сергеевича
Количество деталей в год указано в первой строке в скобках ниже – масса детали в кг. В строках указаны виды станков на операциях; в скобках – штучное время операции (мин). Модели станков выбрать самостоятельно однако не должно быть более двух одинаковых моделей. Детали средних габаритных размеров.
Число станков механического цеха в 7 раз больше чем на участке. Номенклатура такая же. Количество станков заготовительного отделения – 7. Число смен – 2.
План участка механического цеха с расположением станков и другого оборудования в масштабе 1:100.
Общую компоновку всех производственных и вспомогательных отделений (контрольного заточного складов раздаточного инструмента мест мастеров ремонтных бригад и т.д.) административно-конторских и бытовых помещений.
Определение принципа формирования производственных подразделений.
Для выбора принципа формирования производственных подразделений используем такой показатель как степень кооперации которую определяем исходя из среднего числа материальных связей между основным оборудование:
где k N – количество основного оборудования в структуре подразделения.
Данные для расчета ki сводим в таблицу 1.1
Технологический маршрут
На начальном этапе проектирования число однотипных станков N укрупнено рассчитаем по формуле:
где - штучное время на j-ю операцию
F – номинальный годовой фонд времени ч (принимаем 2070 часов);
m – число смен по условию 2;
k – коэффициент использования номинального фонда времени при работе станка в 2 смены – 097.
Результаты расчетов по выбору принципа формирования производственных участков сведем в таблицу 1.2
Материальная связь с другими станками
Степень кооперации равна:
- принцип организации участка – линейный.
Поскольку у деталей 1 2 3 4; и 5 6 7 имеется общность технологических маршрутов обработки то их можно объединить в две поточно-серийные линии:
- линия А включает детали 1 2 3 4;
- линия Б включает детали 5 6 7.
Следовательно получается переменно-поточное производство.
Расчет потребного количество оборудования.
Количество станков для выполнения j-ой операции в переменно-поточной линии определяется по формуле:
где kH – коэффициент учитывающий затраты времени на переналадку линии с одного наименования детали на другое (kH=095).
Общее количество станков в поточной линии Sn обработки группы деталей определяется как сумма принятых на отдельных операциях количеств станков cj
где l – количество операций.
Количество станков в линии А:
Количество станков в линии Б:
Рассчитаем величину такта выпуска. Поскольку линии переменно-поточные то такт выпуска будем определять для каждой детали.
Общая формула такта выпуска:
где D – количество деталей обрабатываемых в год на данной линии.
Данные по расчету станков для линии А сводим в таблицу 2.1 а для линии Б в таблицу 2.2.
рассчитанное количество
Коэффициент загрузки.
Коэффициент загрузки 089
Вертикально- фрезерный
Коэффициент загрузки 085
Общий коэффициент загрузки участка 0864
Проектирование вспомогательных подразделений цеха.
Принимаем нормы удельной производственной площади:
- для малых станков – 10-12 м2;
- для средних станков – 15-25 м2;
- для крупных станков – 25-70 м2.
Результаты расчета сводим в таблицу 3.1
2. Проектирование заготовительного отделения.
Норма удельной площади на оборудование заготовительного отделения принимаем 25-30 м2.
Результат расчета сводим в таблицу 3.1.
2. Проектирование заточного отделения.
Число станков заточного отделения принимаем в процентах от количества металлорежущего оборудования.
Также устанавливаем специальный заточной станок для фрезерных головок.
Кроме основных станков в заточных отделениях устанавливают вспомогательное оборудование в состав которого входят: обдирочно-шлифовальный станок ручной пресс заточной станок для центровочных сверл.
Общая площадь заточного отделения принимаем 10-12 м2 на один основной станок отделения.
Результат расчета сводим в таблицу 3.1
3. Проектирование отделения ремонта инструмента и оснастки.
Число основного оборудования составляет 8 единиц.
Кроме основного оборудования в состав входит вспомогательное в количестве не менее 3 и не более 11 единиц. В число вспомогательного оборудования входят: обдирочно-шлифовальный станок пресса электроэрозионный станок.
Общая площадь определяется по норме 22-24 м2 на один основной станок отделения.
4. Проектирование инструментально-раздаточной кладовой кладовой приспособлений и абразивов.
Норма площади для инструментально-раздаточной кладовой составляет – при массовом производстве – при хранении режущего вспомогательного и измерительного инструмента – 02-03 м2.
Норма площади для кладовой приспособлений составляет – 015-02 м2.
Норма площади для хранения инструментальной оснастки составляет – 035-05 м2.
Площадь кладовой для абразивов принимается из расчета 04 м2 на один шлифовальный заточной или полировальный станок для всех видов производства.
5. Проектирование контрольного отделения.
Площадь контрольного отделения составляет 3-5% от площади станочного отделения.
6. Проектирование ремонтной базы производственного цеха.
Количество станков в ремонтной базе равно 6 единиц. Средняя площадь на единицу основного оборудования составляет 32 м2. Кроме этого требуется площадь для хранения запасных частей её принимают 4 м2 на 1 единицу ремонтной базы.
7. Проектирование участка для приготовления и раздачи СОЖ хранения масел.
Площадь участка для приготовления и раздачи СОЖ определяется в зависимости от числа основного оборудования цеха.
Площадь склада масел составляет 20 м2.
Годовой расход масла для смазки оборудования:
где qM – расход масла на один станок в сутки в кг
Cn – количество станков.
Расход масла в сутки на один металлорежущий станок составляет: для мелкого оборудования 025 кг для среднего оборудования 044 кг для крупного оборудования 07 кг.
Кроме того выделяется площадь 10-20 м2 для шорников и смазчиков.
8. Проектирование отделения и устройств для сбора и переработки стружки.
Площадь отделения для сбора и переработки стружки принимается в зависимости от металлорежущего оборудования цеха.
9. Проектирование цеховых складов.
Проектирование склада заготовок.
В качестве склада заготовок принимаем автоматический склад стеллажного типа с блочными стеллажами с мостовыми кранами-кронштейнами.
10. Сборочное отделение
Площадь сборочного отделения принимается при массовом производстве в размере 30% от площади механического производства.
Подразделение и его оборудование
Производственное отделение (предназначено для механической обработки деталей)
Заготовительное отделение
1 Число основных станков
1 Основное оборудование
Отделение ремонта инструмента и оснастки
1. Основное оборудование
Инструментально-раздаточная кладовая кладовая приспособлений и абразивов.
1. Инструментально-раздаточная кладовая
2. Кладовая приспособлений
3. Кладовая для абразивов
4. Кладовая инструментальной оснастки
Контрольное отделение
1 Контрольное отделение
2. Склад запасных частей
Отделение приготовления СОЖ хранения масле и др.
1 Отделение приготовления и раздачи СОЖ
3. Помещение для персонала
Отделение для сбора и переработки стружки
1. Отделение для сбора и переработки стружки
1. Склад материала и заготовок
2. Склад готовых деталей
Выбор цехового транспорта и грузоподъемных устройств.
В качестве транспортной системы на участке (и в цехе) выбираем автоматизированную напольную транспортно-складскую систему (АНТСС) которая обеспечивает доставку заготовок и деталей к станкам и к контрольному отделению. Транспортные линии принимаем отдельные для каждой обрабатывающей линии для предотвращения путаницы деталей.
В качестве подъемных устройств принимаем мостовые электрические краны служащие для погрузки-разгрузки деталей с АНТСС и установки деталей на места хранения возле станков а для установки деталей на станки принимаем консольно-поворотные краны.
Выбираем потребное количество мостовых кранов как один кран на 50-60 м длины пролета т.е. на цех надо 18 мостовых кранов грузоподъемностью 5 т.
Число тележек АНТСС принимаем три штуки на линию.
Число консольно-поворотных кранов можно определить только после детальной планировке участка когда можно будет увидеть точное расположение оборудования и определить зону обслуживания каждого консольно-поворотного крана.
Проектирование строительной подосновы
Определение требуемой высоты кранового здания.
Общая высота кранового здания Н от пола до нижней выступающей части верхнего перекрытия или до нижней точки стропильной затяжки слагается из расстояния Н от пола до головки подкранового рельса и расстояния h от головки рельса до нижней выступающей части верхнего перекрытия или до нижней точки стропильной затяжки которое зависит только от конструкции крана и его габаритного размера по высоте т.е.
Величина H1 слагается из следующих величин:
где к – высота наиболее высокого станка м; z – промежуток между транспортируемым изделием поднятым в крайнее верхнее положение и верхней точкой наиболее высокого станка этот промежуток принимается равным 05-10 м; е – высота наибольшего по размеру изделия в положении транспортировки м; f – расстояние от верхней кромки наибольшего транспортируемого изделия до центра крюка крана в верхнем его положении необходимое для захвата изделия цепью или канатом и зависящие от размеров изделия принимается не менее 1 м; с- расстояние от предельного верхнего положения крюка до горизонтальной линии проходящей через вершину головки рельса; принимается по стандартам электрических мостовых кранов колеблется в пределах от 05 до 16 м в зависимости от конструкции и грузоподъемности крана.
Вторая часть высоты пролета h определяется в зависимости от конструкции и размеров крана: она равна сумме габаритной высоты крана А и расстоянию m между верхней точкой крана и нижней точкой перекрытия или затяжки стропильной фермы т.е.
Высота электрических мостовых кранов А установлена стандартом (ГОСТ) в зависимости от грузоподъемности крана. Она колеблется в пределах от 2100 мм (для крана грузоподъемностью 10 т.) до 5200 мм (для крана грузоподъемностью 250 т.)
Расстояние между верхней точкой крана и нижней точкой перекрытия m должно быть не менее 100 мм.
Дальнейшее проектирование строительной подосновы и сводим расчет в таблицу 5.1
Здание в виде прямоугольника одноэтажное с полым каркасом УТС основная крановая площадью 5184 м2 площадь цеха 16073 м2; ширина пролета – 24 шаг колонн – 12 высота пролета 108 м. Отопление воздушное.
Элементы конструкции
характеристики эскизы
отдельно стоящий из железобетона
с двухветьевой подкрановой частью 500х1400
железобетонная сегментная составная ферма пролетом 24 м
сборные железобетонные предварительно напряженные
трехслойные железобетонные панели
раздвижные с габаритами 4х42
ширина 15м высота 24 м
скатная покрытие из ячеистого бетона
светоаэроционные с шириной 6 м
железобетонные высотой 3 м.
Определение рабочего состава цеха и расчет его численности.
Расчет численности производим методом расчета по трудоемкости где используется формула:
где Т – трудоемкость механической обработки на годовую программу
ФР – действительный годовой фонд работы рабочего приминается при
-часовой рабочей недели и количестве дней отпуска 24 – 1820 час.
КМ – коэффициент многостаночного обслуживания принимается равным 1.
Поскольку данные о трудоемкости промежуточных работ отсутствуют количество разметчиков и слесарей принимается равным 2% от численности рабочих-станочников.
Данные о расчете основных и вспомогательных рабочих сводим в таблицу 6.1
Категория работающих
Производственные рабочие
(вертикально-сверлильный)
(радиально-сверлильный)
оператор станка с ПУ
разметчики и слесари
Вспомогательные рабочие
кладовщики-раздатчики инструмента и приспособлений
комплектовщики изделий
кладовщик склада заготовок
кладовщик склада готовых деталей
рабочие по межремонтному обслуживанию и ремонту оборудования
рабочие по ремонту приспособлений и вспомогательного инструмента
рабочие по заточке инструментов
рабочие по уборке стружки и производственных помещений
Инженерно-технические работники
Инженерно-технические
Младший обслуживающий персонал
Работники технического контроля
Проектирование обслуживающих помещений цехов
Данные по расчету административно-бытовых помещений сводим в таблицу 7.1.
Помещение (а также инвентарь и устройство)
1 Гардеробные (способ хранения одежды - закрытый число мест – 1170 ширина прохода между лицевой поверхностью шкафов – 06 м)
2. Умывальные (число кранов – 30)
3 Душевые (число кабин для душа - 30)
4.1 Уборная мужская (число унитазов – 9 число писсуаров – 9)
4.2 Уборная женская (число унитазов - 6)
5. Комната для курения
8. Пункт медицинской помощи
1 Рабочие комнаты административно-конторского персонала и инженерно-технических служб.
2. Вестибюли-гардеробные
3. Кабинет техники безопасности
Разработка компоновки
Разработку компоновки выполняем в виде чертежа.
Планировку участка выполняем в виде чертежа.
Расчет данных для проектирования энергетической части
Задание на проектирование энергетического хозяйства должно содержать по каждому цеху суммарную установленную мощность по каждому виду оборудования активную мощность электроприемников и годовой расход электроэнергии. Для этого необходимо все электроприемники каждого цеха разбить на группы по однородности характера работы и для каждой группы подсчитать суммарную установленную мощность исходя из количества единиц оборудования входящего в данную группу.
Затем для каждой группы электроприемников определяем активную мощность. Активная мощность Ра (на шинах низкого потребления) определяется по суммарной установленной мощности и коэффициенту спроса kС учитывающему недогрузку (по мощности) и неодновременность работы электроприемников потери в сети и в электродвигателях по формуле:
Для механических цехов средний коэффициент спроса можно принять равным 04-05.
Годовой расход электроэнергии для цеха на шинах низкого напряжения W в кВт*ч определяют по активной мощности и действительному годовому фонду времени работы оборудования с учетом его коэффициента загрузки (по времени)
где - сумма активных мощностей на шинах низкого напряжения кВт; - действительных годовой фонд времени оборудования одной смены ч; m – количество смен работы оборудования; - коэффициент загрузки оборудования по времени.
Общая активная нагрузка на шинах высокого напряжения равна сумме нагрузок приемников низкого напряжения и активных потерь в трансформаторах и активных нагрузках приемников высокого напряжения.
Годовой расход электроэнергии на освещение принимается по нормам расхода на 1 м2 площади здания.
Трансформаторные подстанции имеют назначение трансформировать переменный электрический ток напряжением порядка 10.000В в ток питающий оборудование напряжением 380 В. Подстанции оборудуются трансформаторами различной мощности наиболее распространенная мощность 1000 кВт.
Активная мощность подстанции Ма рассчитывается по формуле где - установленная мощность 025 – коэффициент учитывающий неодновременность потребления электроэнергии потери в сетях и необходимый резерв.
Расчет сведем в таблицу 10.
Проект пневматического хозяйства завода разрабатывается на основе данных технологических процессов о потребности цехов в сжатом воздухе режиме работы воздухоприемников и местах их расположения. Проект должен содержать расчет общей потребности в сжатом воздухе для каждого цеха и завода в целом выбор типов и определение потребного количества компрессоров указания о месте расположения компрессорной станции разработку схем конструкции и сети воздухопроводов и т.д.
Давление подаваемого воздуха 3-7 атм. Для понижения давления устанавливают редукционные клапаны.
Для укрупненных расчетов можно принимать следующие данные при определении потребности в сжатом воздухе:
- обдувка станков: количество станков подлежащих обдувке принимается 10-15 % от общего числа станков цеха; расход сжатого воздуха 15-20 м3ч станок принимаем для расчета тоже самое;
- обдувка деталей: средний расход на одно установленное сопло 10-12 м3ч для расчета принимаем число сопел равное числу станков;
- пневматические зажимы: на один станок с пневматическим зажимом расходуется до 4 м3ч для расчета принимаем что 50% станков оснащены пневматическими зажимами остальные механическими;
- пневматические инструменты: расход сжатого воздуха 25-45 м3ч на один присоединенный инструмент для расчета принимаем число инструмента равное числу слесарей большей смены.
1 Питание электроприемников
1.1 Электродвигатели станков
1.2 Электродвигатели кранов
Итого электроэнергии
3 Пневматические зажимы
4 Пневматический инструмент
Проектирование механосборочных участков и цехов: методические указания для практических лабораторных работ и дипломного проектирования студентов специальности 1-36 01 01 «Технология машиностроения». Составители: к.т.н. проф. Махаринский Е.И. ст.преп. Беляков Н.В.
Рекомендуемые чертежи
- 24.01.2023