Конический редуктор


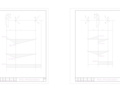
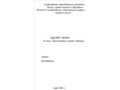
- Добавлен: 24.01.2023
- Размер: 708 KB
- Закачек: 0
Узнать, как скачать этот материал
Подписаться на ежедневные обновления каталога:
Описание
Конический редуктор
Состав проекта
![]() |
![]() |
![]() ![]() ![]() |
![]() |
![]() |
![]() ![]() ![]() |
![]() ![]() ![]() |
![]() |
![]() ![]() ![]() ![]() |
![]() ![]() ![]() |
![]() ![]() ![]() ![]() |
![]() |
Дополнительная информация
Контент чертежей
▌я■Ё√ шчушср■∙шї ш ъЁєЄ ∙шї ьюьхэЄют.dwg

╥шЄєы№э√х ышёЄ√.dwg

Рекомендуемые чертежи
Свободное скачивание на сегодня
Обновление через: 8 часов 42 минуты