Изготовление кровельного материала на основе бутилового регенерата




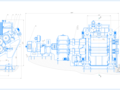
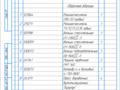
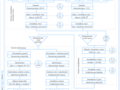
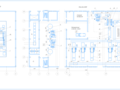
- Добавлен: 25.01.2023
- Размер: 2 MB
- Закачек: 0
Описание
Изготовление кровельного материала на основе бутилового регенерата
Состав проекта
![]() |
![]() ![]() ![]() ![]() |
![]() ![]() ![]() ![]() |
![]() ![]() ![]() |
![]() ![]() ![]() ![]() |
![]() ![]() ![]() ![]() |
Дополнительная информация
Технологическая схема 1.cdw

КП-40461806-240502.65-05-09 СХ
Производство кровельного материала
на основе бутилового регенерата
Схема технологическая
Резиносмеситель 250-20
Прием и листование смеси
Ванна с барабанным накопителем
Резиносмеситель 7123
Подогрев и дозирование смесей
Каландрование смесей
Охладительные барабаны
Закаточное устройство
Вулканизатор "Бузулук
Заматывание в рулоны
Пресс 4-х этажный ПХГ-125
Протягивание готового полотна
Стол для обрезки и контроля
Раскатывание и подогрев рулонов
Раскаточное устройство
Участок каландрования
Участок вулканизации
Раскатывание рулонов
Охладительная этажерка
Нанесение клея и антиадгезива
Клеепромазочная машина
Участок контроля и упаковки
Контроль готовой продукции
Конвейер для осмотра
План цеха.cdw

каландрованной резины
КП-40461806-240502.65-05-09
План цеха по производству
кровельного материала на основе
бутилового регенерата
МДКП окончат.doc
1 Обзор кровельных материалов для скатной кровли
2 Обзор кровельных материалов для плоской кровли
3 Обзор технологии изготовления ..
4 Патентная проработка
1 Обоснование места строительства предприятия .
2 Обоснование проектируемого ассортимента изделий .. ..
3 Технические требования предъявляемые к изделиям .
Технологическая часть
1 Требования к сырью и материалам ..
2 Исследование и обоснование рецептов резиновых смесей
3 Обоснование проектируемого метода производства .
4 Описание технологического процесса .
5 Расчет материального баланса
6 Расчет годовой и суточной потребности в резиновых смесях ..
7 Выбор и расчет оборудования ..
8 Расчет энергозатрат
Экология охрана труда и ТБ . ..
1 Анализ опасных и вредных производственных факторов .
2 Техника безопасности при работе
3 Пожарная безопасность
4 Рекомендации по защите от статического электричества .
5 Средства коллективной защиты работающих от воздействия
опасных и вредных производственных факторов
Список используемой литературы .
В настоящее время в России осуществляется широкомасштабное строительство промышленных и жилых зданий мостов туннелей дорог магистральных трубопроводов гидротехнических и других сооружений. Для обеспечения всех этих видов деятельности необходимо большое количество полимерных строительных материалов причем требования к ним непрерывно повышаются.
Кровля является одним из важнейших и ответственных конструктивных элементов здания. Основное ее назначение - защита здания от проникновения атмосферных осадков. Один из путей решения проблем технологичности устройства кровли повышения ее надежности и долговечности - это применение полимерных материалов.
Поставленные задачи можно решить: созданием новых высококачественных изделий; разработкой современной высокоэффективной технологии и комплекса технологического оборудования для их изготовления обеспечивающих высокую культуру производства и отвечающих требованиям современного производства; совершенствованием методов испытаний и испытательной техники позволяющих дать надежную оценку качества изделий и технологических процессов производства а потому в новых условиях повышение знаний в области проектирования изделий оснастки и оборудования приобретает первостепенное значение. Рост производства резиновой промышленности обусловливает повышенные требования особенно к массовым изделиям которые должны обладать высоким качеством и малой себестоимостью так как в современном производстве стоимость материалов составляет более 70 % себестоимости изделий.
Цель работы – разработка экономичной рецептуры и перспективного технологического процесса производства 500000 квадратных метров современного кровельного материала.
Кровельные материалы предназначены для защиты здания от проникновения атмосферных осадков. Современные здания и сооружения массового строительства имеют главным образом плоские и малоуклонные крыши в то время как в котеджном строительстве в основном применяют скатные кровли. Один из путей решения проблем технологичности устройства кровли повышения ее надежности и долговечности - это применение полимерных материалов. Полимерные кровельные и гидроизоляционные материалы позволяют получать разнообразные по цветовой гамме покрытия способствуют созданию оригинальных конструкций зданий и сооружений внедрению новых форм (куполов оболочек складок сфер и др.).
В мировой практике строительства существует много различных конструкций кровель которые классифицируют по ряду признаков например по используемым материалам конструктивным особенностям геометрии принципам крепления материала назначению и т.д.
В данном курсовом проекте нашли отражение выработанные перспективные конструкции материалов и технологии их изготовления которые представляют наибольший интерес для практики и теоретических исследований основных эксплуатационных характеристик.
Актуальность работы. Эластомерные кровельные и гидроизоляционные материалы находятся в ряду постоянного спроса. Поэтому постановка настоящего исследования направленного на создание производства эластомерных кровельных и гидроизоляционных материалов на существующем оборудовании резиновой промышленности и удовлетворяющих требования потребителей является вполне актуальной.
Выбор того или иного кровельного материала зависит от многих факторов: тип здания тип конструктивных особенностей несущих элементов крыши вкус заказчика традиции и климатические особенности данного региона финансовые возможности заказчика и другие.
1Обзор кровельных материалов для скатной кровли
Архитекторы во многом формирующие вкусы заказчика все больше тяготеют к черепичным или подобным черепичным покрытиям. Это традиционная керамическая черепица а также цементно-песчаная полимер-песчаная металлопластиковая алюминиевая стеклянная так называемая шинглс-гонтовая мягкая кровля под черепицу. В пассажах торговых рядов в зимних садах и оранжереях в фонарях верхнего света промышленных зданий все больше применяются светопрозрачные покрытия из акрилового бикарбонатного стекла стеклопластика кварцевого (закаленного) стекла.
Черепица - широко применяемый штучный кровельный материал. Глиняная или керамическая черепица – это один из старейших кровельных материалов. В последние годы появились новые кровельные материалы такие как относительно дешевая полимер-песчаная черепица и дорогостоящая алюминиевая.
Рис.1.1 Скатная кровля изготовленная из гибкой черепицы
Поскольку черепицу крепят к обрешетке только одним краем кровля обладает способностью свободного перемещения отдельных частей. Это позволяет такой кровле воспринимать деформации вызванные осадкой сооружения ветровым давлением и т.д.
Достоинствами черепичной кровли являются: огнестойкость; долгий срок службы; высокая декоративность.
Недостатками являются: большая масса что требует мощной стропильной конструкции; необходимость придания кровле большого уклона для обеспечения быстрого стока воды; невозможность механизации работ по устройству кровли.
Рис. 1.2 Классическая керамическая черепица
Работа по монтажу такой черепицы сравнима со стоимостью самого материала. К тому же черепица материал хрупкий иногда разбивается градом и камнями. Некачественный обжиг снижает морозостойкость черепицы так как накопленная влага в порах переходя в лёд разрывает черепицу на морозе.
На строительном рынке России можно без труда приобрести современное покрытие для кровли так называемую металлочерепицу. Это листы оцинкованной стали покрытые полимерными составами. Кроме того широко применяются пазогребневые несущие металлопластиковые листы различного профиля.
Такие листы выполняются из стали методом штамповки или роликовой обработки при непрерывном процессе. При этом гарантируется точное повторение рисунка все складки рисунка одинаковы. В металлочерепице сочетаются традиционно красивый черепичный рисунок и экономичность которая достигается за счет низкой материалоемкости (легкости) кровельных длинномерных листов промышленного изготовления и несложного монтажа.
В качестве исходного материала в металлочерепице применяется холоднокатонная сталь толщиной как правило – 05 мм. После прокатки стальной лист подвергается с обеих сторон горячей оцинковке при этом поверхность становится устойчивой к воздействию коррозии и восприимчивой к нанесению следующего слоя методом пассивации. Далее на пассивированную поверхность наносится защитная краска – праймер а затем слой пластика выдерживающий воздействие солнечных лучей и колебаний температур.
Рис. 1.3 Профили металлочерепицы
На рынке кровельных материалов можно приобрести "металлочерепицу" до 30 цветов.1 кв.м такого кровельного покрытия не превышает 5 кг. Стоимость 1 кв.м кровли с учетом ее высокого качества и долговечности вполне сопоставима со стоимостью кровли изготовленной традиционными способами. Такие кровли легко монтируются как из готовых листов длина которых достигает 7 м так и из "картин" производимых на специальной установке непосредственно на строительной площадке.
Эти металлочерепичные покрытия достаточно огнестойки и долговечны. Снег не скапливается на их гладкой поверхности а само покрытие надежно защищает крышу от протечек весной так как талая вода не просачивается сквозь покрытие. Поверхность покрытия остается чистой ни листья ни мох не пристают к кровле. Она отлично противостоит как промышленным выбросам так и суровому климату. Рассчитана она минимум на 50 лет эксплуатации.
Не менее важным техническим решением являются легкие огнестойкие металлические кровельные панели заводской готовности. Они представляют собой многослойную конструкцию из стального профилированного листа приформованного к нему слоя трудносгораемого высокоэффективного пенопласта и припененного рулонного полимерного материала Элон или кровлелон. Применение таких панелей позволяет увеличить срок службы кровельного покрытия до ремонта в 4-5 раз сократить трудозатраты и сроки монтажа покрытия в 5-8 раз уменьшить нагрузку на конструкцию каркаса здания в 3-4 раза производить монтаж покрытия с кровлей в любой климатической зоне в течение всего года.
В последние годы на рынке появились прозрачные и полупрозрачные светопропускающие кровельные волнистые листы и пластины на основе ПВХ в частности марок ондуклер фирмы "Ондулин" (Франция) и валовойма фирмы "Икопал" (Финляндия). Последние изготовляют длиной 3-6 м шириной 20 см и толщиной 15 мм. Материалы характеризуются морозостойкостью и устойчивостью к УФ-излучению. Они выдерживают снеговые нагрузки и соответствуют первому классу по стандарту пожарной безопасности sPs 4190. ПВХ пластины предназначены для устройства кровель в общественных зданиях коттеджах флигелях а также для обустройства балконов стоянок для машин и др.
Рис. 1.4 Полимерные кровельные материалы
Кровельные панели могут быть изготовлены с пенопластовым утеплителем. Долговечность кровельного материала - не менее 30 лет. Плоские листы можно использовать для облицовки стен помещений с повышенной влажностью декорирования балконов для рекламных вывесок и др.
Анализ тенденций в производстве и применении кровельных материалов свидетельствует о том что имеет место устойчивая динамика увеличения производства современных выполненных по новейшим технологиям материалов например таких как цементно-песчаная (бетонная) черепица металлопластиковые кровельные листы "под черепицу" которые значительно более долговечны. Изделия "мягкой кровли" типа Изопласт Филиизол на основе стеклоткани полиэстера и модифицированные битумы вытесняют традиционно применяемый рубероид пергамин толь. Особенность современного кровельного строительства - возврат к традиционно применяемым в России медным кровельным покрытиям деревянному гонту.
2Обзор кровельных материалов для плоской кровли
Мягкая кровля в настоящее время является пожалуй одним из самых популярных вариантов покрытий для плоской крыши. Существуют несколько видов мягкой кровли в зависимости от того материала который используется для ее изготовления:
мягкая кровля из рулонных материалов;
мягкая кровля из бесшовных материалов;
мягкая кровля из полимерных кровельных мембран.
Широко используемые в настоящее время покрытия из рубероида недолговечны и сгораемы. Связано это с тем что у кровельных материалов на битумном связующем - процесс деструкции вызывающий появление трещин в основном связан с окислением составляющих битума (масла переходят в смолы которые в свою очередь превращаются в асфальтены карбены карбоиды - высокомолекулярные соединения с большой атомной массой).
В модифицированном битуме содержащем пластики и эластомеры (приблизительно 70 % битума + 30 % полимера) такие как АПП (атактический полипропилен) ИПП (изотактический полипропилен) СБС (стирол-бутадиен-стирол) процессы деструкции значительно замедлены. В результате по сравнению с традиционно применяемыми кровельными материалами на нефтебитуме (рубероиды пергамины) современные материалы на модифицированном битуме служат в несколько раз дольше (20-30 лет без ремонта).
Изменилась и основа рулонных кровельных материалов (РКМ). На смену бумажному картону пришли стеклохолст (стеклоткань) или полиэстер (в ряде случаев упрочненный стеклотканью). Такие материалы имеют значительно большую массу чем традиционные (3-6 кгкв.м против 1-2 кгкв.м).
Применение высококачественных составляющих увеличение их количества на единицу площади покрытия в несколько раз естественно увеличивает и их стоимость. Однако современные материалы служат значительно дольше. Кроме того вместо нескольких слоев традиционных материалов как правило кладется один слой (максимум 2 слоя). В результате значительные начальные трудозатраты на покупку материалов наплавляемой мягкой кровли окупаются за счет длительной безремонтной эксплуатации.
Рис. 1.5 Рулонные материалы на основе модифицированного битума
В строительстве применяются кровельные материалы на основе эластомеров (полиизобутилена бутилкаучука хлоропрена тройного этилен-пропиленового каучука хлорсульфополиэтилена и др.) и термопластов (поливинилхлорида поливинилфторида этилена его сополимеров и др.).
Выпускаются листовые и пленочные кровельные материалы (толщиной 08-2 мм) изготовляемые на заводах резинотехнических изделий а также жидкие составы (дисперсии мастичные композиции) зачастую состоящие из нескольких компонентов которые смешиваются перед нанесением на кровлю в построечных условиях.
Рулонные материалы на основе полиизобутилена выпускаются за рубежом под названиями репанол преонол опанол неосид и др. Они могут изготавляться армированными и дублированными со стекло- или полимерными основами и формируют кровельное покрытие способом свободной укладки.
Материалы на основе бутилкаучука хлоропренового каучука и хлорсульфополиэтилена (ХСПЭ) выпускаются с упрочнением различными основами (из стеклянного полиэфирного волокна включая нетканые материалы).
Опыт применения этих материалов в строительстве в течение 35 лет подтвердил их превосходные качества: стойкость к озону УФ-излучению химическим реагентам цветостойкость.
Перспективным материалом для устройства кровель является тройной этилен-пропиленовый каучук с диеновым мономером (СКЭПТ за рубежом -ЭПДМ). Вулканизаты на его основе выполненные в виде рулонных материалов обладают комплексом свойств соответствующих современным требованиям к кровельным материалам. По экспертным оценкам СКЭПТ (или ЭПДМ) - один из дешевых и доступных каучуков. Более чем 20-летний опыт эксплуатации однослойных кровель на его основе в США Европе Японии подтвердил их высокую надежность.
Компания Firestone Building Products - мировой лидер по производству однослойных кровельных покрытий изготовляемых из ЭПДМ. Она выпускает полный спектр однослойных систем на базе ЭПДМ который включает широкие резиновые полотнища самоклеящиеся ленты для заделки швов адгезивы герметики очистители стойкие к коррозии крепежные элементы материалы для устройства дополнительной гидроизоляции в местах примыканий и другие изделия удовлетворяющие требованиям самых высоких стандартов в строительной индустрии.
Однослойные мембраны из ЭПДМ развесом 14 кгм2 при толщине 115 мм характеризуются высокими прочностью на разрыв и прокол абразивной стойкостью 300%-м удлинением стойкостью к значительным перепадам температур (от -70 до +100°С) и длительному воздействию озона (при отсутствии каких-либо признаков старения). Кровельные полотнища изготавливают шириной до 15 м и длиной до 60 м.
Компания выпускает кровельные системы ЭПДМ четырех основных типов: балластную (в том числе для инверсионных кровель) полного приклеивания а также системы MAS и BIS с механическим креплением.
В нашей стране также ведутся работы по созданию перспективного ассортимента рулонных и мастичных материалов на основе эластомеров и термопластов: бутилкаучука хлорсульфополиэтилена (ХСПЭ) тройного этиленпропиленового каучука с диеновым мономером (СКЭПТ) поливинилхлорида (ПВХ) и др.
Уникальным комплексом физико-технических и эксплуатационных свойств обладает трудногорючий полимерный материал кровлелон (на основе ХСПЭ и ПВХ) отвечающий современным требованиям пожарной безопасности и являющийся материалом XXI века. Кровлелон отличается легкостью прочностью (12 МПа) влагонепроницаемостью устойчивостью к разрывам и истиранию высокой эластичностью (от -40 до +130°С) стойкостью к химическим биологическим воздействиям. Основное назначение материала – кровли промышленных зданий и сооружений эксплуатирующихся в особо опасных условиях (атомные станции ТЭЦ нефте- и газоперерабатывающие предприятия и др.) а также гидроизоляционная защита сооружений. Посредством термосварки полотнищ из кровлелона монтируются индустриальным способом сборные кровельные и гидроизоляционные ковры.
Наиболее распросраненным и перспективным направлением применения эластомерных кровель из СКЭПТ (ЭПДМ) в США Италии Венгрии являются сборные кровельные ковры изготавливаемые в заводских условиях.
ФПГ "Нефтехимпром" создан рулонный полимерный материал КРОМЭЛ (на основе СКЭПТ) предназначенный для устройства кровельных покрытий и гидроизоляции фундаментов мостов тоннелей мелиоративных систем сантехнических кабин и др. В зависимости от условий эксплуатации могут быть использованы различные модификации материала (однослойный армированный со светоотражающим слоем с клеящим слоем). Наряду с высокими технологическими характеристиками и долговечностью (до 25 лет) КРОМЭЛ вдвое дешевле импортных аналогов. Материал был применен в качестве гидроизолирующего слоя в легких негорючих сэндвич-панелях.
Отечественной компанией 'Термопласт" разработан и внедрен в массовое производство широкий спектр материалов предназначенных для устройства кровельных покрытий гидроизоляции и антикоррозионной защиты.
Рис.1.6 Вид плоской кровли выполненной из полимерного материала
Разработанная компанией технология получения смесевых терпоэластопластов путем переработки термопластов (полиэтилена полистирола полипропилена и др.) каучуков наполнителей и специальных добавок позволяет использовать в качестве исходного сырья как первичные материалы так и отходы.
Создана и внедрена в производство серия термоэластопластов обладающих свойствами термопластов и резин. На их базе производятся рулонные листовые и штучные материалы имеющие срок службы не менее 10-15 лет в любых климатических условиях. Материалы эластичные атмосферостойкие (от -50 до +120°С) и предназначены для устройства и ремонта кровель любого типа.
Бикапол устраивается с помощью мастики или механического крепления рубизэл и арбизэл (армированный негниющей основой) наклеиваются с использованием растворителя. Материалы фольгобикапол и фольгобизэл покрыты с лицевой стороны фольгой (медной алюминиевой и др.) различных оттенков что повышает их декоративные свойства и позволяет использовать при реставрации памятников старины строительстве и ремонте уникальных архитектурных объектов.
Рулонные материалы могут выпускаться с фигурными краями что дает возможность создавать на кровле фактурный рисунок и совершенствовать архитектурный облик здания в целом.
Среди термопластичных полимерных материалов наибольшее распространение получили листы и пленки на основе поливинилхлорида (ПВХ). В мировой практике им отдается предпочтение по сравнению с эластомерными материалами из-за высокой прочности и огнестойкости. Важным технологическим преимуществом является их способность свариваться с образованием прочного водонепроницаемого шва.
Большую популярность получили пленки трокал из пластифицированного ПВХ фирмы "Диамит Нобель" (Германия) а также материалы марок Интертем фирмы "Интерпластика" (Австрия) СРЕ фирмы "Партек" (Финляндия) и сериафил фирмы "Протан" (Финляндия). Материалы вырабатываются цветными армированными дублированными с защитными слоями и без них. Специально разработанные машины фирмы "Динамит Нобель" позволяют осуществлять процесс сварки швов со скоростью 20 ммин (против 1-3 ммин при ручной сварке).
Рис.1.7 Стыковка ЭПДМ мембраны горячим воздухом
К новому поколению следует отнести также рулонные кровельные материалы на основе полиолефинов в частности мембрану GenFlex ТРО фирмы GenFlex Rooffing Systems (США). Основу мембраны составляет смесь этиленпропиленового каучука (70%) и полипропилена (30%) а также армирующий слой стеклоткани. Швы мембран соединяются при помощи горячего воздуха что повышает их прочность а также скорость и безопасность проведения кровельных работ. Мембрана характеризуется высокой прочностью деформативностью и эластичностью при отрицательной температуре (до -55°С) низким водопоглощением и высокой пароизолирующей способностью. Она рекомендуется для устройства однослойных кровель (плоских и с уклоном) в различных климатических зонах (температуроустойчивость от -55 до +100°С). Работы по ее укладке можно производить круглосуточно без потери качества. Мембрана GenFlex ТРО применима для всех известных видов кровельных систем - балластных инверсионных механически закрепляемых и полностью приклеиваемых.
Влагозащитные мембраны фундалин для внешней и внутренней изоляции фундаментов подземных конструкций а также покрытий полов и стен выпускает французская фирма Onduline International.
Фундалин - это упругая жесткая мембрана предназначенная для создания многофункциональной системы защиты от воздействия паров грунтовых вод подвижек вибрации и т.п. Мембрану изготовляют из двухслойного 06-миллиметрового листа на основе полиэтилена высокой плотности. На одной стороне материала имеются выпуклости высотой 8 мм благодаря которым между мембраной и изолируемой поверхностью создается воздушный зазор что способствует эффективному распределению давлений водяного пара или грунтовых вод по всей поверхности. Фундалин характеризуется прочностью стойкостью к воздействию химикатов грибков бактерий температуроустойчивостью (от -30 до +80°С) простотой монтажа (крепится с помощью гвоздей со специальными шайбами). [2]
В настоящее время все большую популярность на рынке кровельных материалов завоевывают бесшовные материалы. Пожалуй самым популярным из них является мастика. Другое название мастики - материалы для наливных кровель. При работе с мастикой не требуется особой квалификации так как покрытие наносится как обычная краска. Важно еще и то что мастики помимо их прямого назначения можно использовать как клеящий состав для кровельного покрытия из рулонных материалов а также для ремонта всех видов старых кровель.
Рис. 1.8 Ремонт кровли мастикой
Мастика – это жидкая вязкая однородная масса которая после нанесения на поверхность и отвердевания превращается в монолитное покрытие.
По составу мастики делят на битумные битумно-полимерные и полимерные мастики. Кроме основного составляющего в мастики могут входить также растворители наполнители и различные добавки.
По составу мастики делятся также на однокомпонентные мастики и двухкомпонентные мастики.
Однокомпонентные мастики основаны на растворителях которые при воздействии воздуха или паров воды (полиуретановая мастика) испаряются и кровля затвердевает.
Двухкомпонентные мастики хранятся дольше так как в них нет растворителей и представляют собой малоактивные в химическом отношении составы.
Преимущества мастичного покрытия:
на поверхности не образуется стыков и швов (отсюда название – кровля из бесшовных материалов);
современные мастики можно наносить на влажную и даже мокрую поверхность или на ржавую поверхность без предварительной зачистки;
мастика обладает высоким уровнем адгезии ко всем видам материалов;
за счет высокой степени адгезии и паропроницаемости пленки при воздействии на мастику водяных паров не происходит вздутия.
Недостатки мастичного кровельного покрытия непросто добиться необходимой толщины изолирующей пленки особенно при неровностях и больших уклонах крыши.
Высокой газонепроницаемостью отличаются резины на основе бутилкаучука (БК) и полиизобутилена но они недостаточно стойки к УФ-излучению. Достоинством резины на основе хлоропрена является их негорючесть но они в связи с диеновой природой менее долговечны чем резины на основе высоконасыщенных эластомеров. Резины на основе ХСПЭ обладают хорошей стойкостью к УФ-излучению и озону огнестойкостью и долговечностью. Однако такие материалы весьма дороги и поэтому используются ограниченно.
Наиболее эффективно проявили себя в качестве кровельных рулонных материалов резины на основе СКЭПТ [1]. Они отличаются высокой газонепроницаемостью водостойкостью и стойкостью к УФ-излучению и озону могут эксплуатироваться в любых климатических зонах вплоть до Арктики их долговечность — не менее 20 лет. Этот каучук наиболее дешевый и хорошо совместим с наполнителями без существенной потери свойств.
Долговечность покрытий на основе эластомерных материалов (по результатам эксплуатации на конкретных объектах) значительно выше чем у битумных и битумно-полимерных кровельных покрытий и составляет 15—30 лет.
Для прогнозирования долговечности рулонных кровельных материалов на основе малонасыщенных эластомеров обычно используют несколько режимов ускоренного старения:
— термическое старение при температуре 80— 116°С в течение 8—4 недель соответственно;
— старение растянутых до определенной фиксированной деформации образцов в условиях УФ-об лучения;
—старение в среде озона при поддержании его постоянной концентрации [2].
Наибольшее влияние на долговечность материалов оказывает строение резинового покрытия — природа эластомера и наполнителя тип образующихся в процессе вулканизации поперечных связей и условия эксплуатации.
3Обзор технологии изготовления
Наиболее привлекательными для нас с точки зрения технологии изготовления являются полимерные кровельные материалы изготавливаемые на существующем полимерном оборудовании.
Рассмотрим известные технологические способы изготовления рулонных материалов способных использоваться для производства полимерных кровельных материалов.
Изготовление резиновых смесей на основе каучуков БК СКЭПТ и регенерата РБП не представляет никаких трудностей на серийных резиносмесителях. Для изготовления термопластичных смесей с использованием полиэтилена – на серийном резиносмесителе применена станция терморегулирования с использованием замкнутого цикла оборота теплоносителя и возможностью его подогрева паром.
Процесс каландрования как однослойных так и двухслойных покрытий без затруднений можно осуществлять на серийном 4-х валковом каландре применяемом в резиновой промышленности. Питание зазоров каландра резиновой смесью можно осуществлять как с подогревательных вальцов так и червячной машиной МЧХВ-160. Последний вариант более предпочтителен по затратам электроэнергии и площади.
Процесс вулканизации кровельных материалов представляет наибольшие затруднения из-за необходимости создания высокой температуры вулканизации и большой длительности процесса.
Непрерывная вулканизация на барабанных вулканизаторах с прессующей лентой
Барабанные вулканизаторы [2] применяемые для вулканизации технической пластины ковриков и других изделий в виде пластин неограниченной длины имеют горизонтальный барабан диаметром от 07 до 2 м и длиной от 125 до 2.0 м обогреваемым паром давлением 05-06 МПа (5-6 кгссм2) или с помощью электрического тока. К поверхности барабана плотно прижимается бесконечная стальная лента охватывающая приблизительно 34 его окружности. Бесконечная стальная лента охватывает также поверхность верхнего и нижнего прижимных валов и натяжного барабана (рис. 1.9).
Рисунок 1.9 – Принципиальные схемы действия барабанных вулканизаторов с одной лентой (а) и с двумя лентами (б) для непрерывной вулканизации транспортерных лент приводных ремней и других плоских изделий:
– обогреваемый барабан; 26 – прессующие барабаны; 3 – изделие; 4 – натяжной барабан; 67 – лента; 8 – инфракрасные лучи.
Техническая пластина с раскаточного устройства подается между поверхностью вулканизационного барабана и лентой и прессуется под действием давления создаваемого лентой. Давление ленты (045-070 МПа) штоком гидравлического цилиндра и могут перемещаться в горизонтальном направлении. Огибая горячую поверхность барабана пластина плотно прижимается к его поверхности лентой нагревается и вулканизуется.
Рисунок 1.10 – Схема установки вулканизатора барабанного типа для вулканизации ремней:
– рулон не вулканизованного ремня; 2 – раскаточная стойка; 3 – компенсатор; 4 – направляющие ролики; 5 – верхний прижимной барабан; 6 – греющий барабан; 7 – редуктор; 8 – нижний прижимной барабан; 9 – станина; 10 – стальная лента; 11 – натяжное устройство; 12 – натяжной барабан; 13 – вариатор; 14 – электродвигатель; 15 – рулон вулканизованного ремня; 16 – закаточное устройство.
Главными органами барабанного вулканизатора является обогреваемый барабан 1 прессующие и натяжные барабаны 2 4 6 и гибкая лента 5 огибающая все барабаны (рис. 1.9а). Изделия подлежащее вулканизации поступает в зазор между поверхностью барабана 1 и поверхностью ленты 5. По мере движения в результате контакта с нагретым барабаном изделие нагревается и вулканизуется. Под прессовка изделия осуществляется за счет вытяжении ленты при помощи натяжного барабана 4 и за счет изменения межцентрового расстояния между осями барабанов 1 и 6 1 и 2. В вулканизаторе с двумя лентами (рис. 1.9 б) число барабанов увеличивается до шести из них два являются обогреваемыми. Изделие размещается прессуется и вулканизуется в пространстве между лентами. С целью интенсификации нагрева изделия через ленту на некоторых вулканизаторах устанавливаются инфракрасные излучатели 5. Вулканизатор с двумя лентами и двумя обогреваемыми барабанами значительно производительнее (12).
Схема установки одного из барабанных вулканизаторов показана на рис. 1.10. Натяжные ленты 10 обеспечивается барабаном 12 и гидравлическим устройством 11. Верхний 5 и нижний. Прижимные барабаны закреплены в подшипниках и с помощью регулировочных винтов могут устанавливаться в нужном положении. Вулканизатор оснащает двумя компенсаторами 3.Давление ленты обеспечивает прессование изделия и предотвращает образование пор.
При выпуске изделий имеющих на поверхности рисунок поверхность барабана гравируют.
Вулканизацию прорезиненных тканей при высокой температуре можно проводить на агрегатах на которых ткани нагревают инфракрасными лучами.
Благодаря значительной проникающей способности инфракрасных лучей создают условия для равномерного прогрева ткани по всей толщине. В результате примерно вдвое сокращается продолжительность вулканизации и улучшается качество продукции.
Непрерывная вулканизация в воздушной атмосфере с применением токов сверхвысокой частоты (СВЧ)
Вследствие низкой теплопроводности резиновых смесей и материалов нагрев всей массы заготовки происходит медленно а теплота не рационально расходуется на возмещение потерь в окружающую среду и на повышение температуры массы оборудования [2]. Указанные недостатки в значительной степени устраняются при использовании электронагрева за счет явления поляризации атомов и молекул диэлектрика помещенного в высокочастотное электрическое поле. Этот способ называют диэлектрическим нагревом высокочастотной электротермией нагревом в микроволновом поле и т.д. В последнее время данный способ нагрева стал внедряться в производстве неформовых изделий. Диэлектрический нагрев обладает значительными преимуществами так как позволяет: концентрировать очень большие мощности в малых объемах материала; получить равномерный нагрев материала с низкой теплопроводностью при большой интенсивности; легко осуществлять избирательный нагрев; легко регулировать температурный режим; осуществить более полную механизацию и автоматизацию технологических процессов.
Суть диэлектрического нагрева состоит в следующем. Под влиянием электрического поля имеющиеся в материале заряды связанные межмолекулярными силами ориентируются или смещаются в направлении поля. Смещение связанных зарядов под действием внешнего электрического поля принято называть поляризацией. Переменное электрическое поле вызывает непрерывное перемещение зарядов молекул вслед за изменениями направлений электрического поля. Это перемещение молекул происходит с некоторым «трением» и нагревом материала. В диэлектриках имеется также небольшое количество свободных зарядов которые создают ток проводимости обусловливающий выделение дополнительной теплоты в материале. Различные материалы нагреваются не одинаково интенсивно так как в зависимости от природы материала изменяется энергия затрачиваемая на поляризацию данного диэлектрика и на создание тока проводимости. Зависимости активной мощности выделяющейся в виде теплоты в теле помещенном в электрическом поле от параметров поля и электрических свойств материала выражается уравнением:
Где Р0 – мощность выделяемое в единице объема диэлектрика Втсм;
f – частота электрического поля МГц;
Е – напряженность электрического поля кВсм;
– относительная проницаемость диэлектрика;
tg – тангенс угла диэлектрических потерь.
Из этого уравнения следует что интенсивность нагрева можно регулировать изменяя параметры электрического поля: частоту и напряженность. Наибольший эффект дает повышение напряженности так как нагрев пропорционален квадрату напряженности поля. Однако напряженность нельзя повышать безгранично вследствие того что при очень высоких потенциалах может произойти пробой. Для обеспечения необходимой надежности напряженность электрического поля устанавливают на уровне 60 - 75 пробивной напряженности. Таким образом реальным путем ускорения разогрева остается повышение частоты поля.
Наряду с преимуществами этот метод обладает и существенным недостатком поскольку в поле токов высокой и сверхвысокой частоты достигается нагрев только полярных каучуков и резиновых смесей обладающих достаточной полярностью. Возможности широкого его использования без специальной корректировки состава резиновых смесей ограничены.
Применяемые в отечественной и зарубежной резиновой промышленности линии [2] для непрерывного изготовления профильных резиновых изделий построены с учетом наиболее эффективного использования сверхвысокочастотного нагрева. Система нагрева в поле токов сверхвысокой частоты (СВЧ) является частью всей вулканизационной установки и предназначена для предварительного нагрева заготовки до температуры вулканизации и создания условий обеспечивающих начало реакции.
Установка подогрева заготовки в поле токов СВЧ (рис. 1.11) состоит из двух последовательно расположенных круглых волноводов подключенных к двум генераторам (магнетронам) мощностью по 25 кВт каждый работающим на частоте 2450 МГц. В волноводах резиновая заготовка подогревается до температуры вулканизации за счет преобразования микроволн в теплоту. Заготовка подлежащая нагреву перемещается внутри волноводов на ленте транспортера из стекловолокна с фторопластовым защитным покрытием выполненной так что имеется возможность регулирования ее положения относительно энергетического центра аппарата. Для защиты персонала работающего на установке от вредного воздействия ультравысокочастотных полей установка снабжается экранами а также фильтрами гасящими радиопомехи. С целью предотвращения вспышек материала в случае обрыва заготовки на входе и выходе в волноводы установлены фотоэлементы блокирующие включение электроэнергии в зависимости от перекрытия луча проходящим профилем. Для удобства обслуживания волноводы имеют продольный разъем и соединены шарнирно подача электроэнергии блокируется концевыми выключателями так что включение возможно только при закрытых волноводах. Удаление летучих газов и паров из материала заготовки при ее нагреве производится путем принудительной циркуляции и продувки воздуха через волноводы (15).
Вулканизатор представляет собой аппарат туннельного типа и служит для завершения процесса вулканизации. Внутри камеры вулканизатора размещена лента транспортера работающего синхронно с транспортером волноводов. В камеру подается горячий (около 200°С) воздух. Вентилятор воздухопроводы и калорифер расположены внизу под камерой. Стенка камеры покрыты тепловой изоляцией.
Вулканизация длинномерных заготовок (типа профильных уплотнителей) на поточной линии можно проводить применяя предварительный подогрев шприцованной заготовки токами сверхвысокой частоты.
Нагревание резиновых заготовок помещенных в электрическое поле сверхвысокой частоты (СВЧ) обеспечивает ряд преимуществ перед обычным медленным нагревом заготовок горячим воздухом:
)регулируемый нагрев заготовок;
)быстрый нагрев позволяющий сократить продолжительность пребывания смеси в вязкотекучем состоянии что способствует сохранению формы сложных профилей.
Интенсивность нагрева резиновых смесей различного состава неодинакова.
Достаточно быстро нагреваются смеси на основе полярных каучуков которые за 30-40с могут нагреется до 200°С в то время как смеси на основе неполярных каучуков нагреваются за 35 мин только до 50-70°С. Для увеличения интенсивности нагревания неполярных каучуков используют в резиновых смесях в сочетании с полярными.
На скорость нагревания влияет тип технического углерода (сажи); при применении печных саж ПМ-50 ПМ-75 ПМ-100 нагревание происходит более интенсивно. Интенсивность нагревания токами СВЧ практически регулируется изменением частоты электрического поля.
Токи СВЧ технически более удобно применять для предварительного нагревания заготовок окончательная вулканизация которых производится в вулканизаторах туннельного типа в среде горячего воздуха. Линия для непрерывного изготовления длинномерных профильных резиновых изделий с подогревом в поле токов сверхвысокой частоты (СВЧ) с вулканизацией в туннельном вулканизаторе горячим воздухом. Основные узлы: вакуумная червячная машина 2 с питателем 1; приемный транспортер 3; микроволновые нагреватели (СВЧ – система) 5; вулканизатор 7; охлаждающая ванна 8; отборочно – режущее устройство 9 – компенсатор и станок для резки готовых изделий на отрезки заданной длины.
Вулканизатор представляет собой аппарат туннельного типа и служит для завершения процесса вулканизации. Внутри короба с надежно изолированными в тепловом отношении стенками размещена лента транспортера работающего синхронно с транспортером волноводов.
В коробе циркулирует горячий воздух. Вентилятор воздухопроводы и калорифер расположены внизу под коробом. Отборочно-режущее устройство скомпоновано с компенсатором; последний необходим в связи с тем что станок для мерной резки готовых изделий в отличие от всех предыдущих работает в дискретном (периодическом) цикле.
Рисунок 1.11 – Линия для непрерывного изготовления профильных изделий с подогревом в поле токов СВЧ:
– питатель для подачи резиновой смеси; 2 – червячная машина4 3 – приемный транспортер; 46 – фотоэлементы; 5 – микроволновые нагреватели; 7 – вулканизатор; 8 – охлаждающая ванна; 9 – отборочно-режущее устройство; 10 – калорифер; 11 – вентилятор; 12 – транспортер; 13 – волноводы; 14 – кожух магнетронов; 15 – вакуумная установка; 16 – пульт управления.
Нагреватель состоит из двух последовательно расположенных трубчатых волноводов мощностью 25 кВт (частота тока 3000 МГц напряжение не выше 8000В). Заготовка перемещается внутри волноводов с помощью транспортерной ленты из стеклянного волокна. Газы и поры из волноводов удаляются с помощью вентиляции. [1].
Непрерывная вулканизация в среде жидкого теплоносителя
Этот способ вулканизации длинномерных изделий получил широкое распространение при изготовлении профильных уплотнителей.
В связи с тем что жидкий теплоноситель одновременно является вулканизационной средой к нему предъявляются следующие требования: стойкость к температурам вулканизации низкое давление паров (для уменьшения потерь теплоносителя и создания благоприятных санитарно – гигиенических условий труда) минимальная токсичность малое воздействие на оборудования и отсутствие вредного влияния на резиновые смеси минимальная пожароопасность низкая стоимость и недефецитность. Кроме того он должен обладать хорошей растворимостью в воде (для обеспечения лёгкой и эффективной отмывки после вулканизации) невысокой плотностью (для облегчения погружения в него вулканизуемых изделий) и низкой температурой застывания (для уменьшения уноса из аппарата с изделиями и связанных с этим потерь теплоносителя).[3].
Наиболее часто в качестве жидкого теплоносителя применяют глицерин ксилитан и расплавы солей. К недостаткам глицерина относится; гигроскопичность окисляемость и способность выделять при высоких температурах акролеин действующий на слизистую оболочку глаз. Глицерин можно применять при температурах вулканизации до 140ºС.
Ксилитан (моноангидрид пятиатомного спирта - ксилитан) представляет собой более вязкую чем глицерин жидкость он более стоек и может применятся при температурах вулканизации до 150 - 155ºС. Глицерин и ксилатин применяют в качестве вулканизационной среды при вулканизации трубок профильных и губчатых уплотнителей.
Расплавы солей являются мало токсичными веществами и могут применяться в открытых вулканизационных аппаратах. Часто для вулканизации в расплаве солей используют эвтектическую смесь нитрат – нитритных солей (СС - 4) с температурой плавления около 141ºС следующего состава: KNO3–53% NaNO3–7% NaNO2–40%. Плотность расплава равна 2000 кгм3 (2гсм3) [2].
Линии для непрерывного изготовления профильных изделий основным аппаратом которых являются вулканизаторы с жидкими теплоносителями работающие без давления в современном резиновом производстве занимают ведущее место. Это обуславливается высокой эффективностью теплообмена между высокотемпературным теплоносителем и нагреваемой резиновой заготовкой и исключительной простотой аппаратурного оформления установки. Поточные линии для вулканизации монолитных длинномерных изделий в жидком теплоносителе независимо от особенностей конструкции и применяемого теплоносителя включают: червячный пресс с системой вакуумирования вулканизационный аппарат (в виде ванны) устройство для отмывки охлаждения протягивания и отбора готовых изделий. Рассмотрим это оборудование на примере линии с вулканизатором 3 в расплаве солей (СС - 4). В состав линии (рис 1.6) входят следующие основные узлы: вакуумная червячная машина 1 промежуточный транспортёр 2 отмывочно – охладительное устройство 4 протягивающее устройство 5 отборочное устройство 6. Заготовка профилируется в головке вакуумной червячной машине. Вакуумирование резиновой смеси в процессе экструзии позволяет устранить порообразование внутри изделия при свободной вулканизации. Таким образом вакуумная червячная машина является неотъемлемой частью линии для изготовления монолитных профилей. При изготовлении пористых изделий использование вакуумной машины не обязательно однако это требует более строгого контроля за содержанием влаги в исходных материалах при изготовлении смеси а также использования влагопоглотителей.
Непосредственно за червячной машиной установлены приёмный ленточный транспортёр и вулканизатор с расплавленной солью. После вулканизатора установлено отмывочно – охлаждающее устройство.
Вулканизатор представляет собой ванну сварной конструкции обычно из нержавеющей стали. С наружной стороны дно ванны обогревается электронагревателями объединёнными в три секции. Контроль работы каждой секции электронагревателей осуществляется термопарами установленными соответственно секциям нагрева по длине ванны. Ванна заполняется сплавом СС – 4 (53% KNO3 + 7% NaNO3 + 40% NaNO2) который расплавляется до температуры 200 - 250ºС. Ванна укреплена на раме сварной конструкции снаружи закрыта кожухами с тепловой изоляцией. С одной стороны кожуха по всей длине установлены остеклённые дверки создающие сквозной доступ к рабочей зоне аппарата. В верхней части кожуха смонтированы два транспортёра (для погружения и перемещения профиля в теплоносителе). Поскольку плотность теплоносителя превышает плотность резины перемещения профиля осуществляется нижней ветвью ленты транспортёра опущенной в расплав на 10 – 40 мм. Диаметр барабанов транспортёров – 500 мм длина каждого транспортёра 4 – 45 м лента из нержавеющей стали толщиной 03 – 05 мм.
Вулканизация на машинах и в аппаратах периодического действия
К аппаратам периодического действия для вулканизации рулонных материалов например конвейерной ленты относят прессы специальной конструкции. Которые имеют специальные приспособления для растягивания ленты и охлаждения концов пресс-формы с целью исключения перевулканизации мест повторно попадающих в пресс-форму при следующем цикле вулканизации.
Прессы для вулканизации транспортерных лент и плоских приводных ремней
Для вулканизации транспортерных лент и плоских приводных ремней конечной длины применяются рамные и колонные гидравлические прессы большой мощности. Такие прессы представляют собой как бы ряд обычных прессов поставленных вплотную и имеющих общие вархние плиты один подвижный стол и общие паровые плиты (рис.1.12). Собранная лента (или ремень) из рулона 1 протягивается между двумя вулканизационными плитами 3 и 6 отпрессовывается с помощью гидравлических приводов 11—12 вулканизуется и закатывается в рулон 9. Для предотвращения вытяжки транспортерной ленты или ремня в процессе эксплуатации перед вулканизацией их подвергают растяжению от 4 до 8% первоначальной длины. С этой целью участок лепты 7 между плитами зажимается посредством гидравлических механизмов 2 и 8 и с помощью гидравлических механизмов 13 и 10 подвергается вытяжке. Верхняя траверса 4 соединяется с гидравлическими цилиндрами 11 посредством рам 5 (или колонн).
Рис.1.12 Схема пресса для вулканизации транспортерных лепт и плоских
а)рулон невулканизованной ленты (ремня); 28 – зажимное устройство; 3- верхняя обогревательная плита; 4- верхняя траверса; 5-рама пресса; 6- нижняя обогревательная плита; 7- участок ленты (ремня);9- рулон вулканизованной ленты(ремня); 1013- растяжное устройство; 11- гидроцилиндры; 12- плунжеры.
Современные прессы подобного рода имеют длину плит 10м. и полезную ширину 12; 16; 20; 25 и 29 м; прессовое усилие составляет соответственно 3200 4200 5200 6500 и 7500 тс; вес прессов равен 125 155 195 267 и 319 тс [2].
Схема установки одноэтажного рамного пресса с размерами плит 2х 10 м. показана на рис.10
Рис.1.13 Схема установки одноэтажного рамного пресса для вулканизации ремней и транспортерных лент
- станины; 2- продольные балки для крепления верхней опорной плиты;3- подвесные стержни; 4- верхняя опорная плита; 5-обогреваемые плиты; 6- секции подъемного стола; 7-рабочие цилиндры; 8-основание пресса; 9-фундаментные балки; 10-фундамент; 11-канал для стока воды; 12- зажимно-растяжное устройство; 13- стол для перезарядки пресса; 14- фундаментные болты; 15-установочные винты; 16-уравновешвающие грузы.
На всех прессах обогрев плит производится с помощью пара подаваемого отдельно для каждых 3—4 м2 плиты. С целью предотвращения перевулканизации участка ленты попадающего дважды между обогреваемыми плитами на одном конце плиты па расстоянии 200—300 мм. устраивают сквозные каналы по которым пропускают охлаждающую воду.
При вулканизации ремней и транспортерных лент с резиновыми прокладками на плиты пресса укладываются стальные линейки шириной от 50 до 100 мм. Эти линейки предотвращают растекание резиновой смеси и обеспечивают отпрессовку боковых сторон ремней и транспортерных лент. Толщина линеек на 03—05 мм меньше толщины изделий поступающих на вулканизацию. Эти линейки после вулканизации в момент раскрытия пресса отодвигаются от ленты в сторону с помощью рычажных механизмов установленных сбоку подвижного стола и неподвижной верхней траверсы по всей их длине. При этом лента освобождается и легче протаскивается между плитами. В момент замыкания плит планки с помощью этих же механизмов возвращаются на свое место.
Электрический или паровой
Электрический (температура до 250° С)
и легко выкатывается
Рис. Х.11. Внешний вид вулкааиза-ционного ттресса с выдвижными раскрывающимися плитами французской фирмы «Э миде к а у».
На рис. 1.14 показан внешний вид рамного пресса для вулканизации ремней и транспортерных лепт. Пресс включает в себя как бы пять рамных прессов с двумя гидроцилиндрами каждый. Между рамами видны механизмы раздвижения боковых планок.
Рис.1.14 Внешний вид рамного пресса дли вулканизации ремней и лент
Для вулканизации состыкованных ремней применяют так называемые челюстные прессы. Рама такого пресса имеет форму кривого бруса и обеспечивает возможность закладки ленты между плитами сбоку.
4 Патентная проработка
Для разработки данного курсового проекта использованы следующие патентные разработки:
Номер патента:2114878 Пластоэластомерная композиция полимерная смесь для вулканизации и способ получения вулканизованной пластоэластомерной композиции.
Суть изобретения:Пластоэластомерную композицию обладающую высоким эластическим восстановлением при сохранении свойств термоэластопластических сплавов получают нагревом полимерной смеси до 160-240oC. Полимерная смесь включает полимерную основу масло вулканизующие агенты вулканизующие добавки. Полимерная основа состоит из полипропилена полиизобутилена этилен-пропилен-диенового тройного сополимера полибутадиена и этилен-пропиленового каучука.
Номер патента:2113445 Способ получения термопластичной резиновой композиции.
Сутьизобретения: Изобретение относится к получению термопластичных резиновых композиций и может быть использовано в резино-технической промышленности. В способе получения термопластичной резиновой композиции смешение ингредиентов осуществляют в две стадии: на первой стадии производят смешение латекса карбоксилсодержащего бутадиеннитрильного каучука с латексом пластика на основе сополимера содержащего 200 - 273 мас.% звеньев акрилонитрила 230 - 311 мас.% звеньев бутадиена и 480 - 520 мас.% звеньев стирола(метилстирола) и антиоксидантом аминного иили фенольного типа в соотношении 1 - 10 : 1 : 002 - 030 по сухому веществу соответственно полимерную смесь выделяют из латекса и обезвоживают; на второй стадии в полимерную смесь вводят на вальцах или в резиносмесителе при 80 - 130oC оксид или гидроксид двухвалентного металла выбранного из группы включающей цинк магний кальций пластификатор и дополнительно бутадиен(изопрен)стирольный термоэластопласт с индексом расплава 4 - 14 г10 мин при 190oC в количестве 1 - 10 мас.ч. на 100 мас. ч. полимерной смеси. На второй стадии можно дополнительно вводить аминный антиоксидант в количестве 05 - 30 мас.ч. на 100 мас.ч. полимерной смеси. В качестве карбоксилсодержащего бутадиеннитрильного каучука можно использовать сополимер содержащий 14-30 мас.% звеньев акрилонитрила 10-30 мас. % звеньев стирола 48-54 мас. % звеньев бутадиена и 2-10 мас. % звеньев метакриловой кислоты. Изобретение позволяет упростить технологию получения термопластичной резиновой композиции и улучшить ее литьевые свойства.
1Обоснование места строительства
На выбор площадки строительства цеха по производству 500 тыс. м2 кровельного материала повлияли следующие факторы:
- наличие сырья в основном потребляемого в больших количествах: это регенерат бутиловый мел и кордное волокно.
2Обоснование проектируемого ассортимента изделий
Ассортимент выпускаемых кровельных материалов подобран из потребности близлежащих регионов в эластомерных рулонных и штучных кровельных материалах.
3Технические требования предъявляемые к изделиям
Кровельные материалы должны соответствовать требованиям ГОСТ 30547 Материалы рулонные кровельные и гидроизоляционные. Общие технические условия.
Общие требования к готовой продукции:
а)Полотно рулонного материала не должно иметь трещин дыр разрывов и складок кроме материалов на перфорированной основе.
б)На кромках полотна рулонного материала на картонной и асбестовой основах допускаются не более двух надрывов длиной 15-30 мм на длине полотна до 20 м. Надрывы длиной до 15 мм не нормируются а более 30 мм не допускаются.
в)Рулонные кровельные материалы с крупнозернистой или чешуйчатой посыпкой должны иметь с одного края лицевой поверхности вдоль всего полотна непосыпанную кромку шириной (85 + 15) мм.
г)Ширина непосыпанной кромки может быть увеличена в зависимости от области применения и приведена в нормативном документе на конкретный материал.
д)Материалы должны быть плотно намотаны в рулон и не слипаться.
е)Торцы рулонов должны быть ровными. Допускаются выступы на торцах рулона высотой не более: 20 мм - для рулонных материалов на волокнистой основе безосновных битумно-полимерных и полимерных материалов.
ж)Линейные размеры площадь полотна рулонного материала и допускаемые отклонения от линейных размеров и площади устанавливают в нормативном документе на конкретный вид материала.
з)Разрывная сила при растяжении рулонных основных битумных и битумно-полимерных материалов должна быть не менее Н (кгс):
5 (22) - для ненаплавляемых материалов на картонной основе;
4 (28) – для наплавляемых материалов на картонной основе;
4 (30) - для материалов на стекловолокнистой основе;
3 (35) - для материалов на основе из полимерных волокон;
2 (40) - для материалов на комбинированной основе.
и)Условная прочность гидроизоляционных безосновных битумно-полимерных материалов должна быть не менее 045 МПа (46 кгссм2).
к)Условная прочность и относительное удлинение при разрыве рулонных полимерных материалов должны быть не менее:
МПа (15 кгссм2) и 300% - для невулканизованных эластомерных;
МПа (41 кгс см2) и 250% - для вулканизованных эластомерных;
МПа (82 кгс см2) и 200% - для термопластичных.
л)Условная прочность и относительное удлинение при разрыве рулонных армированных полимерных материалов должны быть не менее:
МПа (25 кгссм2) и 15% - для невулканизированных эластомерных с армированием из стекловолокон;
МПа (25 кгссм2) и 100% - то же с армированием из полимерных волокон;
МПа (60 кгссм2) и 15% - для вулканизированных эластомерных с армированием из стекловолокон;
МПа (50 кгссм2) и 100% - то же с армированием из полимерных волокон;
0 МПа (120 кгссм2) и 15% - для термопластичных с армированием из стекловолокон;
МПа (90 кгссм2) и 60% - то же с армированием из полимерных волокон.
м)Сопротивление динамическому или статическому продавливанию рулонных кровельных полимерных материалов должно быть указано в нормативном документе на конкретный вид материала.
н)Рулонные материалы должны выдерживать испытание на гибкость в условиях приведенных в таблице 1.
Условия испытания рулонных материалов на гибкость
на брусе с закруглением радиусом мм
при температуре °С не выше
на волокнистой основе
о)Битумные и битумно-полимерные рулонные материалы (кроме беспокровных) должны быть теплостойкими при испытании в условиях приведенных в таблице 2.
Условия испытания рулонных материалов на теплостойкость
при температуре °С не ниже
в течение ч не менее
п)Изменение линейных размеров рулонных безосновных полимерных материалов должно быть не более ±2% при испытании при температуре (70±2) °С в течение не менее 6 ч.
р)Температура хрупкости покровного состава или вяжущего наплавляемых битумных рулонных материалов должна быть не выше минус 15°С битумно-полимерных - не выше минус 25°С.
с)Масса покровного состава или вяжущего с наплавляемой стороны для основных наплавляемых битумных рулонных материалов должна быть не менее 1500 а для битумно-полимерных - не менее 2000 гм2.
т)Водопоглощение рулонных материалов (кроме пергамина) должно быть не более 20% по массе при испытании в течение не менее 24 ч.
у)Рулонные кровельные материалы (кроме пергамина) должны быть водонепроницаемыми в течение не менее 72 ч при давлении не менее 0001 МПа (001 кгссм2).
ф)Гидроизоляционные материалы должны быть водонепроницаемыми при испытании в течение не менее 2 ч при давлении не менее 02 МПа (2 кгссм2) если иные условия испытания не установлены в нормативных документах на конкретные виды материала.
Технологическая часть
1Требования к сырью и материалам
Резиновая смесь для изготовления кровельного материала должна обладать:
- высокой прочностью необходимой для механического крепления на скатных кровлях с большими уклонами;
- морозостойкостью для обеспечения выполнения кровельных работ в любое время года;
- теплостойкостью т.к. во время эксплуатации материал нагревается до 80°С а в отдельных случаях до 110°С;
- стойкостью к озону и УФ-излучению;
- хорошими технологическими свойствами: каландруемостью средней пластичностью заготовки должны иметь низкую усадку гладкую поверхность;
- декоративными и эстетическими требованиями к внешнему виду.
Требования предъявляемые к используемому сырью и материалам представлены в таблицах 2.1 2.2.
Таблица 2.1 – Описание основного сырья и материалов
Наименование основных материалов
№ ГОСТ ТУ ТР инструкция
Показатели обязательные для проверки
Каучуковая основа для верхнего слоя ковра
ТУ 2294-022-05766801-02
Вязкость по Муни МБ1+4 (100°С)
Каучуковая основа для нижнего слоя ковра
ТУ 2511-095-00149073-08
Прочность при разрыве МПа
Потеря массы при сушке %
Ускоритель вулканизации
Белила цинковые БЦО ГОСТ 202-84
Активатор вулканизации
Стеариновая кислота
Продолжение таблицы 2.1
Усиливающий наполнитель
ТУ 5743-114-001492800-93
Усиливающий наполнитель придает анизотропность св-в
Краситель для верхнего слоя ковра
Таблица 2.2 – Описание вспомогательных материалов
Наименование вспомогательных материалов
№ ГОСТ ТУ или ТР инструкция
Ткань прокладочная ЧЛХ-158
Прокладочный материал
ТУ 8318-029-05225011-98
Обработка вулканизованного полотна
Содержание механических примесей влаги
Антиадгезионная обработка резиновых смесей
Антипригарное покрытие
ТУ 2257-082-40245042-04
Пленка полиэтиленовая
2 Исследование и обоснование рецептов резиновых смесей
Рецептуры различаются содержанием и типом наполнителя а также типом ускорителя для вулканизации.
Для обеспечения заданных технологических свойств и получения изделий с заданными техническими свойствами применили наполнители: мел технический или кордное волокно они обеспечивают хорошую обработку хорошо усиливают каучук удешевляют изделие.
Для облегчения распределения ингредиентов и улучшения обработки на оборудовании применен пластификатор битум БНК-5 и масло ПМ.
Чтобы увеличить скорость и снизить время вулканизации применили систему ускорителей в разных комбинациях: из альтакса тиурама диспрактола К-16 этилцимата ДФГ. Применение двух ускорителей обеспечивает высокую скорость вулканизации максимально узкий индукционный период широкое плато вулканизации. Наиболее эффективно ускорители действуют в присутствии первичного активатора – цинковых белил но они трудно распределяются в каучуке поэтому взят вторичный активатор стеариновая кислота. При температурах вулканизации они образуют комплексы которые легко растворяются и распределяются в каучуке.
Наиболее эффективной по скорости вулканизации и себестоимости оказались рецептуры резиновой смеси №9 и 13 в которых применена вулканизующая система из тиурама диспрактола К-16 и серы.
Рецептура №13 выполнена с наполнителем – мел технический как наиболее дешевый наполнитель. Высокая степень наполнения дешевым и плотным наполнителем (120 м.ч мела на 100 м.ч. регенерата) обеспечивает резиновой смеси высокую скорость вулканизации (10 мин) достаточную прочность (36 МПа) большую устойчивость к статическому продавливанию в связи с чем вулканизованный кровельный материал при той же толщине – 16-18 мм имеет туже стоимость что и не вулканизованный.
Рецептура №9 выполнена с наполнителем из распушенных волокон полиамидного хб и вискозного корда образующегося при утилизации изношенных шин. Высокая степень наполнения легким волокнистым наполнителем (120 м.ч волокна на 100 м.ч. регенерата) обеспечивает резиновой смеси низкую плотность (113 гсм3) высокую прочность (64 МПа) большую устойчивость к статическому продавливанию в связи с чем кровельный материал можно изготавливать меньшей толщины – 10 – 12 мм. Высокая теплостойкость материала обеспечивается низкой теплопроводностью наполнителя что не дает нагреться материалу до высоких температур.
Но испытания данного материала на стойкость к озону показали что время до появления первых трещин у него в два раза меньше. Возможно это связано с методикой ускоренных испытаний во время которых образцы подвергают 20% растяжению при котором они и без озона близки к разрушению.
Наибольшей стойкостью к озону и УФ-излучению обладает рецептура №10 изготовленная на основе каучука СКЭПТ-50-ЭНБ который имеет очень малую непредельность что обеспечивает ему высокую стойкость к озону и возможность вулканизации серой.
Для повышения стойкости к озону и УФ-излучению а также для обеспечения привлекательного внешнего вида изделий разработана особая конструкция кровельного материала:
- нижний слой толщиной 14 мм – выполнен из прочной устойчивой к продавливанию резиновой смеси №9.
- верхний слой толщиной 08 мм – выполнен из резиновой смеси на основе СКЭПТ для обеспечения стойкости к атмосферному старению и придания декоративных свойств кровельному материалу;
- выпускная форма кровельного материала выполнена в двух вариантах:
рулоны шириной 15 м длиной 10 м которые применяют для плоских кровель и фигурных листов размером 300х1500 мм укладываемых на скатные кровли с перехлестом и смещением.
Таблица 3.1 Показатели физико-механических испытаний резиновой смеси
Наименование показателей
Условия вулканизации t°Cх'
Условная прочность при разрыве МПа
Относительное удлинение при разрыве %
Остаточное удлинение %
После старения в течении 120 часов при 100°С
Озоностойкость до появления первых трещин мин
Таблица 3.2 Рецепт резиновой смеси
3 Обоснование проектируемого метода производства
Т.к. используемые для изготовления кровельного материала каучуки имеют высокую температуру вулканизации и высокую стойкость к подвулканизации принимаем одностадийный процесс изготовления резиновых смесей в резиносмесителе периодического действия с выгрузкой на листовальные вальцы. Подогрев резиновой смеси осуществляем на вальцах Пд1500 660660 как наиболее распространенное и доступное оборудование а питание зазора каландра выполняем червячными машинами МЧТ-160 по одной на каждый зазор каландра при листовании однослойных смесей на большой скорости обе червячные машины питают один зазор каландра. Формообразование длинномерных и тонких изделий наиболее целесообразно проводить на каландре а в связи с тем что основная марка кровельного материала сдублированная из двух слоев то принимаем четырех валковый каландр позволяющий получить сдублированное полотно за одну операцию. Вулканизацию проектируемых деталей наиболее экономично проводить в барабанных вулканизаторах непрерывного действия а штучные изделия вырезать фигурным гильотинным ножом. Этот способ позволяет выпускать различную номенклатуру кровельных материалов от рулонных до штучных изделий а также быстро переналаживать производство и менять форму кровельных листов за счет быстрой замены вырубного ножа.
Метод нагрева резины с помощью барабанного вулканизатора не самый эффективный метод при котором теплота передается за счет контакта нагретого паром барабана с изделием. Для увеличения эффективности процесса вулканизации двухслойный рулонный материал подается цветным слоем на основе каучука СКЭПТ к барабану что обеспечивает быстрый прогрев. Вулканизация нижнего слоя неравномерна по его толщине что особенно важно для обеспечения адгезии кровельного материала к мастике.
По сравнению с серийно выпускаемым материалом произведено дополнение к технологическому процессу: каландрование материала совмещено с дублированием на четырех валковом каландре и вулканизация на барабанном вулканизаторе.
Для изготовления кровельных фигурных плиток применяем параллельный процесс на спаренной установке из двух гидравлических прессов ПХГ-125 с раскаточными и закаточными устройствами позволяющими производить вулканизацию и смену заготовок с большой скоростью.
Для обеспечения непрерывности ленты после вулканизации отдельных плиток применяем техническое решение по укладке корд-шнура в заготовку при каландровании. Она обеспечивает непрерывность изделий после вулканизации. Готовые рулоны и штучные плитки кровельного материала упаковываются в пленку штабелируются на поддон и вывозятся на склад готовой продукции. Упаковка в пленку обеспечивает устойчивость упаковочного места и дополнительную защиту от атмосферных условий.
4 Описание технологического процесса
Процесс изготовления рулонного кровельного материала состоит из следующих операций:
изготовление резиновых смесей;
разогрев резиновой смеси на вальцах Пд1500 и питание каландра червячной машиной МЧТ-160;
каландрование резинового полотна на 4-х валковом каландре;
вулканизация каландрованных полотен на барабанном вулканизации-онном прессе «Бузулук» или гидравлическом прессе ПХГ-125;
охлаждение полотен рулонного кровельного материала;
вырубка штучных листов из рулонного полотна;
Взвешивание. Маркировка. Упаковка. Хранение.
Технологическая схема производства кровельного материала представлена на рис. 3.1.
Рис. 3.1 Схема технологическая
Обработка и развеска каучука.
Суточный запас регенерата РБП и каучука СКЭПТ-50 со склада погрузчиком в стеллажах или поддонах подают в помещение где производят его подготовку. Резку регенерата на куски осуществляют на пластинчатом ноже с пневматическим приводом (гильотинный нож).
Составленные по рецепту навески регенерата ручной тележкой перевозят в помещение где изготавливают резиновые смеси. Куски навесок каучука из тележки вручную перекладывают на рабочее место машиниста резиносмесителя. Загрузка навески регенерата в резиносмеситель осуществляют вручную. В случае поступления регенерата со склада в замороженном состоянии его до или после резки подвергают декристаллизации в автоклаве с паровым обогревом при температуре 60-90°С в течение 6-8 часа.
Обработка и развеска сыпучих ингредиентов
Для обеспечения необходимого качества изделий применяют кондиционные (доведенное до необходимых параметров сырье и упакованное в тару сохраняющую эти параметры при хранении) материалы: мел и кордное волокно. Ингредиенты со склада подают в расходные бункера на развеску.
Дозирование ингредиентов осуществляют на автоматических весах установленных на отметке +10.800. Развеску материалов производят по выданному рецепту на резиновую смесь.
Подготовка мягчителей
Суточный запас жидких пластификаторов (мягчителей) со склада погрузчиком завозят в помещение где перекачивают в расходные емкости.
Густой мягчитель предварительно разогревается паром и насосом перекачивают в стационарные обогреваемые паром емкости откуда дозируют автоматическими дозаторами в мерную емкость согласно рецепта на резиновую смесь.
Изготовление резиновой смеси в резиносмесителе
Изготовление резиновой смеси осуществляется в резиносмесителе периодического. Навески каучука загружают в смесительную камеру через загрузочную воронку машинистом резиносмесителя а остальные ингредиенты дозируются на автоматических весовых дозаторах. Порядок и время введения продолжительность и температура указаны в тех.карте на резиновую смесь. При одностадийном смешении каждую закладку резиновой смеси изготавливают в один прием при этом ускорители вводят в начале смешения а вулканизующие вещества (серу) за 30 с до окончания смешения. Перемешивание смеси происходит при температуре в камере от 90-100°С при этом температура окружающей среды и температура загружаемых ингредиентов должна быть не ниже +10°С.
Обработка смеси на вальцах
После открытия нижнего откидного затвора разгрузочного устройства смесь из резиносмесителя падает на вальцы. Резиновая смесь обрабатывается на вальцах путем 3-4-х кратного пропуска в зазоре между валками 8-10 мм. Температура переднего валка 55-60°С заднего – 60-65°С.
Затем готовая смесь срезается с вальцев широкой лентой толщиной 8-12 мм и подается на охладительную установку «Жучок».
Охлаждение резиновой смеси
С целью предотвращения подвулканизации при хранении листованную смесь вручную навешивают на вешала охладительной установки с душирующей системой. За период изготовления в резиносмесителе очередной заправки резиновые листы охлаждаются до комнатной температуры и снимаются в стеллаж. Резиновые смеси при укладке пересыпаются опудривающим материалом (каолином мелом и др.).
Контроль качества резиновой смеси
Отбор проб на испытания по ФМП производит ОТК согласно тех. карте на отбираемую смесь. Испытания по ФМП делает ЦЗЛ в соответствии с НТД.
Подогрев резиновой смеси
Резиновая смесь подогревается на вальцах Пд1500 660660 снимается непрерывным листом шириной 200 мм и по конвейеру подается в червячную машину МЧТ-160 откуда по конвейеру направляется в зазор между верхним и выносным валками каландра.
Каландрование резинового полотна
Скорость каландрования - нм 56 - 10 ммин
Температурный режим каландрования оС
-выносного валка 70 ± 5 оС
-верхнего валка 65 ± 5 оС
-среднего валка 60 ± 5 оС
-нижнего валка 55 ± 5 оС
Ширина каландрованного полотна 1470 мм
- Толщина – по регламенту в соответствии с маркой полотна.
Каландрованное полотно охлаждается на холодильных валках и закатывается в прокладочный холст на закаточном конвейере. После чего вылеживается в бобинах перед вулканизацией 2-6 часа.
Диаметр бухты не более 600 мм
Вулканизация в барабанном прессе «Бузулук»
Бобина с каландрованным полотном устанавливается на раскаточное устройство и под натяжением подается в зазор между валком вулканизатора и прессующей лентой при движении вокруг нагретого барабана происходит вулканизация кровельного материала. Для обеспечения заданных свойств кровельный материал подается верхним слоем к греющему валку скорость движения материала подбирают такой чтобы время контакта материала с греющим валком была равна необходимому времени вулканизации изделия. Меньшая температура на нижнем слое кровельного материала обеспечит его недовулканизацию и хорошие адгезионные свойства к кровельной мастике.
- температура валка оС - 170+5
- давление гидравлики МПа - 6-8
- скорость дублирования мчас - 8-12
Готовый вулканизованный кровельный рулонный материал с транспортера вулканизатора поступает на охлаждение и закаточное устройство.
Диаметр бухты не более – 800 мм.
Бухты готового рулонного кровельного материала поставляемого в виде рулонов отправляют с помощью рельсовой тележки на установки для осмотра и резки на мерные рулоны. К рулону приклеивается этикетка и рулон фиксируется скотчем от разворачивания. На деревянный поддон устанавливаются вертикально 25 рулонов и оборачиваются упаковочной пленкой. Поддон с готовыми рулонами вывозится на склад готовой продукции.
Штучные кровельные плитки из рулона нарезаются штанцевым ножом укладываются в картонные коробки и упаковываются полиэтиленовой пленкой. Коробки укладываются на деревянный поддон стопкой высотой не более 1м и заматываются пленкой после чего поддоны вывозятся на склад готовой продукции.
Изготовление штучных плиток на гидравлическом прессе ПХГ-125
Рулоны каландрованного полотна устанавливаются на раскаточную стойку полотно протягивается между тормозными роликами плитами пресса и тянущими роликами и закрепляется в устройстве для закатывания. Полотно натягивается с помощью приводных роликов плиты пресса смыкаются и происходит вулканизация плиток в прессформах по окончании процесса вулканизации плиты пресса размыкаются готовые плитки отделяются от прессформ с помощью деревянных лопаток и все вместе (сомкнутые между собой готовые плитки и невулканизованное полотно) протягиваются с помощью роликов на шаг плит пресса и процесс вулканизации повторяется.
Вулканизованное полотно обрезается ручным ножом по контуру выпрессовочной канавки. Готовые штучные плитки укладываются в картонные коробки оборачиваются упаковочной пленкой. Коробки укладываются на деревянный поддон стопкой высотой не более 1м и заматываются пленкой после чего поддоны вывозятся на склад готовой продукции.
5 Расчет материального баланса
5.1Расчет фонда времени работы предприятия и программы выпуска готовых изделий
Эффективный фонд времени производства зависит от графика его работы. Предприятие работает по пятидневной рабочей неделе с двумя выходными днями. Участки вулканизации работают в три смены а изготовления резиновой смеси и каландрования – в одну. Расчет годового фонда времени представлен в таблице 3.3.
Таблица 3.3 - Годовой фонд рабочего времени
Наименование видов времени
Количество суток часов
Уч. смешения каландрования
Годовой календарный фонд времени в сутках
Выходные дни в том числе 52 дня выходных
Всего рабочих дней в году
Количество смен в сутки
Рабочие часы в сутках
Эффективный годовой фонд времени работы предприятия в часах
Расчет годовой и суточной программ выпуска готовых изделий представлен в таблице 3.4.
Таблица 3.4 - Программа выпуска изделий
Наименование изделия
Задание на проектиро-вание
Программа с учетом потерь
Рулонная кровля в т.ч.:
бутикров (не вулканиз)
кровлен (термопласт)
Фасонная кровля в т.ч.:
6 Расчет годовой и суточной потребности в резиновых смесях и материалах
Расчет годовой и суточной потребности в резиновых смесях на программу производства представлен в таблице 3.5.
Расчет годовой и суточной потребности по маркам резиновых смесей представлен в таблице 3.6.
Таблица 3.5 - Потребность в резиновых смесях
Шифр резиновой смеси
Валовый расход на м.кв кг
Расход резиновых смесей кг
Бутикров (не вулканиз)
Кровлен (термопласт)
Таблица 3.6 - Потребность в резиновых смесях по маркам
272+3751+100838+231379=
290+4755+127826+293303=
Расчет годовой и суточной потребности основных материалов для изготовления резиновых смесей №8 №10 №13 и Бутикров Кровлен представлен в таблицах 3.7 – 3.12.
Таблица 3.7 - Потребность основных материалов для смеси №8
Белила БЦО ГОСТ 202-84
Стеариновая кислота ГОСТ 6484-64
Таблица 3.8 - Потребность основных материалов для смеси №10
Таблица 3.9 - Потребность основных материалов для смеси №13
Таблица 3.10 - Потребность основных материалов для смеси Бутикров
Таблица 3.11 - Потребность основных материалов для смеси Кровлен
Таблица 3.12 – Сводная таблица потребности в основных материалах
Расход в смеси 10 кг
Расход в смеси 13 кг
Расход в Бутикров кг
Расчет годовой и суточной потребности в текстильных вспомогательных и комплектующих материалах представлен в таблицах 3.13 – 3.15.
Таблица 3.13 - Потребность текстильных материалов
Наименование материалов
Расход на одно изделие
Корд-шнур марка 22В (244 текс х1х2)
Таблица 3.14 - Потребность вспомогательных материалов
Потребность в материалах
Для оборота за сутки на год
Таблица 3.15 - Потребности комплектующих материалов
Расход на единицу измерения
7 Выбор и расчет оборудования
7.1Оборудование для транспортирования сырья и материалов
Все виды сырья материалов (за исключением мела и мягчителей) и готовой продукции хранятся в складах в стационарных ячейках расположенных в три этажа. В ячейки с помощью кранов штабелеров грузоподъемностью 3 тонны устанавливаются (и забираются) металлические контейнеры с уложенными в них материалами. Ряды ячеек расположены вдоль помещения складов. Транспортирование поперек рядов в зону действия кранов штабелеров производится рельсовым транспортом с электрическим приводом.
Подача каучуков на участок подготовки производится транспортной системой с предварительным адресованием проходящей по вторым этажам складского корпуса и участка подготовки.
Подъем резаного каучука с первого этажа на второй осуществляется грузовым лифтом Q = 30 тонн. Химикаты с третьего этажа складского корпуса также транспортной системой с предварительным адресованием подаются на третий этаж участка подготовки. Подача осуществляется в металлических транспортных контейнерах V = 10 м3 куда химикаты засыпаются на третьем этаже складского корпуса. Подъем химикатов с первого этажа на третий осуществляется с помощью грузового лифта Q = 30 тонн.
Транспортный материал адресно направляется к соответствующему (по наименованию материалов) стационарному бункеру имеющему начало на третьем этаже участка подготовки а окончание на втором этаже. Бункер заканчивается вибропитателем и автоматическими весами для развески материала.
Технический углерод доставляется на завод в мешках автотранспортом т.к. его годовая потребность не велика. Технический углерод подается для развески на весы в ручную.
Масло ПМ подается на завод в железнодорожных цистернах затем переливается в стандартные специальные цистерны склада мягчителей. Затем масло ПМ со склада мягчителей по трубопроводам закачиваются в промежуточные емкости подготовительного участка. Отсюда оно перекачивается в циркуляционную систему трубопроводов откуда открытием электромагнитных клапанов подается в ковш автоматических весов.
Битум перекачиваются по трубопроводам с паровым подогревом.
Мел доставляется на завод в мешках в железнодорожных вагонах. Из вагона мел доставляется на склад погрузчиком. Суточная потребность мела растаривается из мешков и с помощью скребкового конвейера подается в бункер на подготовительный участок. Далее мел шнековым питателем подается для развески на автоматические весы.
Мелкие транспортные операции осуществляются с помощью электрических погрузчиков с грузоподъемностью 10 тонна.
7.2Обоснование технологического оборудования участка подготовки
Выбор оборудования в основном диктуется объемами изготавливаемой резины и количеством ее шифров (рецептов). В шинном производстве где изготавливается большой объем смесей в ограниченном ассортименте находят применение резиносмесители с большим числом оборотов роторов и большим объемом смесительном камеры с тем чтобы добиться максимальной производительности одной единицы оборудования.
В данном проекте нет необходимости в установке подобного оборудования поэтому для изготовления резиновых смесей выбирается смеситель РСВД 250-20 который исходя из объемов резиносмесительной камеры позволяет в сумме изготовить все «черные» смеси идущие на производство кровельного материала. Для изготовления «цветной» резиновой смеси шифра №10 желательно иметь отдельный резиносмеситель (для обеспечения чистоты цвета резины) исходя из объема ее потребности выбираем резиносмеситель РС 7112172335. Оба резиносмесителя являются распространенным оборудованием.
Процесс смешения резиновых смесей происходит в одну стадию. Резиновые смеси после выгрузки из резиносмесителя идут на доработку. Для работы с резиносмесителем РСВД 250-20 выбираются смесительно-листовальные вальцы СМ 2130 660660 а для смесителя РС 7112172335 - смесительно-листовальные вальцы СМ 1500 660660.
Безопасность работы вальцев обеспечивается автоматическим аварийным устройством. Они также являются типовыми и изготавливаются серийно.
Кроме того на подготовительном участке на третьем этаже устанавливаются три емкости по 8м3 для промежуточного хранения мела и кордного волокна.
Для промежуточного хранения химикатов устанавливаются 8 емкостей по 05м3.
Для промежуточного хранения масла принимается емкость объемом 1м3.
Для хранения резиновых смесей на участке подготовки проектируется автоматизированный склад хранения резиновых смесей с применением кранов штабелеров.
Вся система автоматизированной подачи ингредиентов в промежуточные емкости их подача на автоматизированную развеску и автоматизированная развеска в соответствии с рецептом а также определение порядка загрузки ингредиентов в смесительную камеру с поддержанием режимов смешения производится ЭВМ установленной в пультовом помещении.
7.3Обоснование технологического оборудования для участка каландрования
Для питания каландра применим подогревательные вальцы Пд 1500 660660 и пару червячных машин МЧТ-160. Две машины применены для питания двух зазоров каландра различными смесями а при выпуске однослойных смесей но способных каландроваться на большой скорости обе червячные машины питают один зазор каландра. При каландровании резиновой смеси №8 работает одна червячная машина. После выхода из головки червячной машины разогретая смесь на транспортеру поступает на каландр. Универсальный 4-х валковый каландр 4-710-1800 применен для выпуска дублированного полотна в остальных случаях его применение обеспечивает качество листования особенно для твердых высоконаполненных смесей. Каландрованное полотно охлаждается проходя через охладительные барабаны талькируется или прокладывается тканью и заматывается в рулоны. Закаточное устройство обеспечено механизмом для съема рулонов не останавливая процесс каландрования.
7.4Обоснование технологического оборудования для участка вулканизации
Для вулканизации кровельного материала применили два различных способа вулканизации:
- для рулонной кровли и вырубаемых листов имеющих гладкую поверхность – непрерывной вулканизации в барабанных вулканизаторах «Бузулук»;
- для штучных изделий имеющих сферические выступы на поверхности – вулканизацию в колонных многоэтажных прессах ПХГ-125.
Питание вулканизационных прессов «Бузулук» производится с раскаточных стоек обеспечивающих сматывание прокладочной ткани и подогрев полотна до входа в пресс.
Питание вулканизационных прессов ПХГ производится с раскаточных стоек обеспечивающих равномерное натяжение полотна до входа в пресс. Для автоматизации процесса закладывания заготовки и съема готового изделия в дублированное полотно при каландровании укладываются кордные нити которые обеспечивают связь отдельных вулканизованных изделий в непрерывное полотно вытягиваемое из пресса с помощью приводных роликов. Раскаточное и закаточное устройства протаскивают полотно через два пресса стоящих последовательно тем самым обеспечивают одним механизмом два вулканизационных пресса.
Резка рулонов на мерные куски и упаковка производятся на специальной установке.
Резка рулонов на штучные изделия производится штанцевым ножом в автоматическом режиме сборка изделий в стопки и упаковка в коробки – на автомате для упаковки.
7.5Расчет необходимого количества резиносмесителей
Производительность резиносмесителей Q кгч определяется по формуле:
где t – время смешения одной заправки мин;
V – объем загрузки м3;
d – плотность резиновой смеси кгм3;
k1 = 098 – коэффициент учитывающий потери на ремонт;
k2 = 095 – технологический снижающий коэффициент.
Количество резиносмесителей nрасчопределяется по формуле:
где А – суточный расход резиновой смеси с учетом потерь кгсутки;
Q – производительность резиносмесителя кгчас.
Коэффициент загрузки Кз определяется по формуле:
где nрасч – количество машин рассчитанное теоретически;
nприн – принятое количество машин.
Таблица 3.16 - Расчет количества резиносмесителей
Плотность резиновой смеси
Расчетная произв. кгч
Расход резиновой смеси кгсутки
Под резиносмесителем РСВД 250-20 устанавливаем смесительно-листовальные вальцы .
Под резиносмесителем РС 7112172335 устанавливаем смесительно-листовальные вальцы .
И соответственно для каждых вальцов принимается отдельная система охлаждения резиновой смеси – установка типа «Жучок».
7.6Подбор весов для автоматической развески ингредиентов в резиносмеситель
При подборе типа весов ориентируются на необходимую навеску и диапазон взвешивания весов. Выбор типа весов представлен в таблице 3.17 3.18.
Таблица 3.17 - Выбор типа весов для резиносмесителя РСВД 250-20
Наименование ингредиентов
Технический углерод П 514
Таблица 3.18 - Выбор типа весов для резиносмесителя РС 7112172335
7.7Расчет оборудования для участка каландрования
Расчет количества каландров представлен в таблице 3.19.
Производительность каландра при листовании Q кгчас (резиновые смеси №1 герметизирующий слой и №3 – наружный слой) рассчитывается по формуле:
где V – окружающая скорость выпускающего валка ммин;
k = 08 – коэффициент использования машинного времени.
Таблица 3.19 - Расчет количества каландров
Скорость листования ммин
Расчет машин МЧТ-160 представлен в таблице 3.20.
Производительность червячной машины Q кгчас определим по формуле:
где V – скорость шприцевания ммин;
d – вес погонного метра профиля кг;
n – число потоков шприцевания;
a – коэффициент использования машинного времени.
Таблица 3.20 - Расчет количества червячных машин МЧТ-160
Расчетная производительность кгчас
Расход резиновой смеси на каландре
Принимаем две червячных машины которые работают одновременно при питании двух зазоров каландра и при питании одного зазора каландра с потребностью резиновой смеси больше 780 кгчас а в остальных случаях работает одна червячная машина. Подогрев смеси на вальцах Пд 1500 660660.
7.8Расчет оборудования для участка вулканизации
Расчет необходимого количества вулканизационных прессов представлен в таблице 3.21.
Производительность вулканизационного пресса Q кгчас рассчитывается по формуле:
где n – количество изделий одной загрузки шт;
g – площадь одного изделия м2;
t1 – время вулканизации мин;
t2 – время перезарядки мин.
Таблица 3.21 - Расчет количества вулканизационных прессов
Расчетная производительность м2ч
Кол-во часов работы в сутки час
План выпуска м2сутки
7.9Сводная ведомость технологического оборудования
Полный перечень основного технологического оборудования и его технологические характеристики представлены в таблице 3.22.
Таблица 3.22 - Ведомость технологического оборудования
Наименование оборудования
Технологические характеристики
Резиносмеситель РСВД 250-20
Свободный объем – 250дм3;
Рабочий объем - 140 дм3;
Скорость вращения роторов обормин (быст.тихох.) – 2017;
Рабочее давление воздуха – 7÷9 кгссм2;
Расход охлаждающей воды м3ч - 23
Мощность электродвигателя - 250 кВт.
Резиносмеситель РС 7112172335
Свободный объем – 71дм3;
Рабочий объем - 45 дм3;
Скорость вращения роторов обормин (быстр.) – 12; 17; 23; 35
Рабочее давление воздуха – 6÷8 кгссм2;
Расход воздуха – 25 м3ч.
Расход охлаждающей воды м3ч - 18
Мощность электродвигателя – 6090120200 кВт.
Смесительно-листовальные вальцы
диаметр переднего валка 660 мм
диаметр заднего валка 660 мм
длина рабочей части 2130;
Поверхность валков гладкая;
Рабочая скорость переднего валка 313 заднего – 330
Расход охлаждающей воды – 8 м3ч.
Мощность электродвигателя – 132 кВт.
диаметр переднего валка 660 мм диаметр заднего валка 660 мм длина рабочей части 1500 мм;
Рабочая скорость переднего валка 313 заднего – 330
Расход охлаждающей воды – 6 м3ч.
Мощность электродвигателя – 125 кВт.
Охладительная установка типа «Жучок»
Расход охлаждающей воды – 25 м3ч.
Расход воздуха – 8 м3ч.
Продолжение таблицы 3.22
Подогревательные вальцы
Рабочая скорость переднего валка 289 заднего – 360
Q = 780 кгчас. Мощность электродвигателя 75 кВт.
Диаметр червяка 160 мм.
Длина рабочей части червяка 1560 мм.
Каландр 4-х валковый универсальный
Диаметр валков 710 мм.
Длина рабочей части 1800 мм.
Рабочие скорости валков ммин:
Фрикция между валками 1:15.
Мощность электродвигателя – 350 кВт
Вулканизатор барабанный «Бузулук»
Диаметр вулканизационного валка мм – 1000
Ширина прессующей ленты мм – 1700
Давление пара МПа – 6
Скорость движения прессующей ленты мчас – 8-40
Мощность электродвигателя – 75 кВт
Пресс гидравлический ПХГ-125
Размер прессующих плит мм – 1250х1250;
Количество этажей – 4
Давление пара МПа – 6;
Усилие смыкания плит 600 тонн Мощность электродвигателя – 35 кВт
8 Расчет энергозатрат
8.1Расчет годового расхода силовой электроэнергии
Расчет годового расхода силовой электроэнергии для резиносмесителя
W = Р * п * Ко * Кз * Фэф = 250*1*10*084*2024 = 425040 кВт (3.7)
где : Р = 250 кВтч - расхода электроэнергии в час;
п = 1 – число принятое к установке;
Ко = 10 – коэффициент использования электроэнергии;
Кз = 084– коэффициент загрузки;
Фэф=2024-эффективный фонд работы оборудования.
Аналогично производится расчет расхода силовой электроэнергии для других видов оборудования данные приведены в таблице 3.24
Таблица 3.24 – Расчёт годового расхода силовой электроэнергии
Годовой фонд времени час
Коэф-фициент загрузки
Расход электро-энергии
8.2Расчет годового потребления сжатого воздуха
Расчёт годового потребления сжатого воздуха для резиносмесителя м3
Бп = qп * п * Ко * Кз * Фэф = 145* 1 * 10 * 084 * 2024 = 24652 м3 (3.8)
где : qп = 145 м3ч - расхода сжатого воздуха;
К= 10 – коэффициент использования энергии;
Кз = 084 – коэффициент загрузки.
Аналогично производится расчет сжатого воздуха для других видов оборудования данные приведены в таблице 3.25
Таблица 3.25 – Расчёт годового расхода сжатого воздуха
Годовой расход воздуха м3
8.3Расчет годового потребления воды для охлаждения
Расчёт годового потребления воды для резиносмесителя м3
Бп = qп * п * Ко * Кз * Фэф = 23* 1 * 10 * 084 * 2024 = 39104 м3 (3.9)
где : qп = 23 м3ч - расход воды;
Аналогично производится расчет расхода воды для других видов оборудования данные приведены в таблице 3.26
Таблица 3.26 – Расчёт годового расхода воды
Годовой расход воды м3
8.4Расчет годового расхода пара
Расчет годового расхода пара для вулканизатора «Бузулук»
W = Р * п * Ко * Кз * Фэф = 350*4*10*0865*5819 = 7047 тонн (3.10)
где : Р = 350 кгч - расхода пара в час (при установившемся режиме);
Кз = 0865– коэффициент загрузки;
Фэф=5819-эффективный фонд работы оборудования.
Аналогично производится расчет расхода пара для других видов оборудования данные приведены в таблице 3.27
Таблица 3.27 – Расчёт годового расхода пара
Расход пара в год тонн
Таблица 3.28-Сводная таблица затрат различных видов энергии
Экология охрана труда и ТБ
1 Анализ опасных и вредных производственных факторов
В процессе производства кровельного материала могут возникать следующие опасности:
- вращающиеся части используемого в проекте оборудования и приводные механизмы могут привести к получению работниками производственных травм при отсутствии ограждений или их неисправности;
- при расположении рабочего места на эстакаде при отсутствии ограждений и фиксации рабочего существует опасность падения рабочего и получения им тяжелых травм;
- используемое в производстве электрооборудование создает возможность поражения электрическим током при работе на неисправном оборудовании;
- при приготовлении резиновых смесей в процессе смешения ингредиентов образуется пыль ингредиентов а при вулканизации резиновых смесей выделяются вредные испарения (таблица 4.1). Эти факторы воздействуют на организм человека вызывая заболевания различных органов.
Таблица 4.1 - Свойства токсичных веществ
Наименование вещества
ПДК в рабочей зоне мгм3
Класс точности по СН-24-71
Действие на организм человека
Требования техники безопасности к оборудованию:
- все движущиеся и вращающиеся части оборудования (транспортные ленты агрегат навивочной машины привод электродвигателей) должны иметь ограждения также должны иметь ограждения рабочие места на эстакаде резиносмесителей;
- всё электрооборудование должно иметь заземляющее устройство. Электроприводы имеют блокирующее устройство которое при перегрузке резиносмесителя или неисправности привода блокирует работу резиносмесителя;
Условия безопасности при подъемно-транспортных работах:
- конструкция комплектовка и расположение грузоподъемных механизмов должны обеспечить свободный и удобный доступ к ним;
- приводные и передаточные механизмы располагаются в кожухах;
- грузоподъемные механизмы оборудуются приборами и устройствами безопасности и блокировки.
По степени опасности поражения электрическим током цеха завода можно охарактеризовать следующим образом:
- подготовительный цех относится к классу особо опасных вследствие наличия токопроводящей технологической пыли (уголь сера) которая может проникнуть внутрь машин а также наличия железобетонных токопроводящих полов;
- формовой цех относится к классу помещений с повышенной опасностью что обуславливает наличие токопроводящих железобетонных полов.
В соответствии с этими характеристиками в подготовительном цехе используется взрывозащищенное электрооборудование.
Для защиты людей от поражения электрическим током все оборудование имеет защитное заземление и зануление.
Требования техники безопасности при эксплуатации оборудования:
- к работе на оборудовании допускаются лица не моложе 18 лет прошедши медицинский осмотр теоретическое и практическое обучение по выполнению работы на данном оборудовании правилам техники безопасности и получившие допуск к самостоятельной работе;
- все рабочие и служащие независимо от квалификации и стажа работы по данной специальности должны проходить вводный первичный и периодический инструктаж по безопасности приема и методам работы;
- периодический инструктаж рабочих производится не реже одного раза в квартал с соответствующей регистрацией в журнале инструктажа;
- перед началом работы должны быть проверены состояние и действие аварийного останова оборудования его исправность наличие заземления вентиляции ограждения движущихся частей машины освещения инструмента;
- в процессе работы запрещается производить какие либо исправления в работе оборудования чистка его частей на ходу а в оборудовании предусматривается наличие устройств предупреждающих случайное включение движущихся частей;
- запрещается допуск на рабочее место посторонних лиц отвлечение рабочего посторонними занятиями.
При проведении работы необходимо соблюдать нормы перемещения тяжестей: мужчинами до 25 кг женщинами до 10 кг.
Рабочие места должны содержаться в порядке не допускается загромождать их посторонними предметами полуфабрикатами и отходами [8].
Проходы и проезды должны быть свободными.
3 Пожарная безопасность
Производство резиновых изделий по предложенным в проекте технологиям является пожароопасным в связи с тем что в данном производстве применяются твердые сгораемые вещества и материалы согласно ГОСТ 12.1004-76 и СНиП 2-90-81.
В подготовительном цехе опасность воспламенения пыли образующейся при смешении ингредиентов резиновых смесей при загрузке их в резиносмеситель связана с тем что при непрерывности работы электрической установки резиносмесителя могут возникнуть авария и сильный перегрев электрических пприборов резиносмесителя а также искровой разряд который является импульсом воспламенения пыли.
В цехе вулканизации опасные состояния при нормальной эксплуатации оборудования не возникают а возможны только в результате аварий или неисправностей. Причинами пожаров могут быть: небрежное хранение горючих материалов; искрение рубильников и электродвигателей при их повреждении; небрежное пользование огнем курение.
Основными способами борьбы с пожарами и взрывами от электрооборудования на производстве является правильный уход за ними и правильная его эксплуатация. Используются также защитные устройства пожаротушения.
Для предотвращения пожарной опасности согласно действующих противопожарных норм в производственных корпусах имеются непосредственные выходы наружу. Для подачи воды к различным участкам производства предусматриваем полный противопожарный водопровод объединенный с хозяйственным водозаборные устройства – гидранты на водопроводной линии на расстоянии не более 100 метров друг от друга. По нормам первичных сред пожаротушения для производственных зданий категории В на 500-600 м2 предусмотрен 1 углекислотный ручной огнетушитель ОУ-2 и 4 пенных огнетушителя ОП-5.
В цехах предусматриваем электрическую и телефонную сигнализации. Система электрической пожарной сигнализации – автоматическая. В данном проекте применяются тепловые датчики ДТП реагирующие на повышение температуры воздуха окружающей среды. Тепловые извещатели устанавливаем на потолке или подвешиваем на высоте 6-10 м от уровня пола.
Для отвода атмосферного электричества предусматриваем молнезащиту.
4 Рекомендации по защите от статического электричества.
Все технологическое и вентиляционное оборудование в котором возможно накопление зарядов статического электричества должно быть заземлено. Скорость перемещаемых материалов не должно превышать допустимых норм правил по защите от статического электричества в производствах химической нефтехимической и нефтеперерабатывающей промышленности.
5 Средства коллективной защиты работающих от воздействия опасных и вредных производственных факторов.
Шум. Уровни опасных и вредных производственных факторов в производственных помещениях и на рабочих местах не должны превышать величин определяемых ГОСТ 12.1.003-83 ССБТ. Шум. Общие требования безопасности. СН2.2.42.1.8.562-96 Санитарные нормы.
Вибрация. Уровни предельно-допустимых значений вибрации на рабочих местах не должен превышать величин определяемых ГОСТ 12.1.012-90 ССБТ. Вибрационная безопасность. Общие требования. ГОСТ 12.4.012-83 ССБТ. Вибрация средства измерения и контроля на рабочих местах. СН 2.2.42.1.8.566-96 Санитарные нормы.
Микроклимат. Уровни допустимых величин показателей микроклимата на рабочих местах производственных помещений не должен превышать значений определяемых СанПиН 2.2.4.548-96. Санитарные правила и нормы. Физические факторы производственной среды. Гигиенические требования к микроклимату производственных помещений. Таблица № 14.
Тяжесть и напряженность трудового процесса. Гигиенические критерии оценки тяжести и напряженности трудового процесса не должны превышать величин определяемых ГТР 2.2.755-90 Минздрав России. Москва 1999 г. Выбросы вредных веществ на рабочих местах не должны превышать величины ПДК указанных в таблице № 15.
В помещениях развески взрывоопасных ингредиентов загрузки техуглерода просева и развески мела воздухообмен определяется аспирацией.
В помещении участка изготовления резиновых смесей основная часть вредностей удаляется от вальцов резиносмесителя.
Вентустановки этих систем размещены в отдельном помещении.
Предотвращение выбивания пыли через неплотности создание вакуума внутри элементов транспортной системы предусмотрено пылеуловителями: А1-БПУ.
Удаление пыли отсасываемым воздухом от верхнего и нижнего затворов резиносмесителя предусмотрено системой аспирации.
В помещении загрузки техуглерода создание вакуума внутри элементов транспортной системы предусмотрено пылеуловителями А1-БПУ.
Предусмотрены также системы аспирации от участка развески взрывоопасных ингредиентов просева и развески мела. В отдельных помещениях на ОТМ 4.200:3600 размещены приточные вентустановки – для участка изготовления резиновых смесей загрузки техуглерода подготовки мягчителей отдельно для помещения категории «Б» (развески взрывоопасных ингредиентов) отдельно для развески мела. Раздача приточного воздуха предусмотрена воздухораспределителями в рабочую зону и в верхнюю зону на участке изготовления резиновых смесей.
) Разработана новая рецептура резиновой смеси обеспечивающая получение из нее обособленного класса армированных короткими волокнами вулканизованных эластомерных рулонных кровельных и гидроизоляционных материалов удовлетворяющих требованиям промышленности по технологическим прочностным и адгезионным свойствам и стойкости к продавливанию в статических условиях. В состав полимерной основы резиновой смеси входят два основных продукта – СКЭПТ и бутилрегенерат что позволяет применять кровельные и гидроизоляционные материалы на ее основе по многоцелевому назначению.
) Разработаны научно-технические представления о влиянии степени вулканизации на свойства резиновых смесей на основе бутилрегенерата и этиленпропилендиенового каучука содержащих в своем составе волокнистый наполнитель в количестве до 120 масс.ч. на 100 масс.ч. каучука. Показано что определяющее влияние на свойства таких смесей оказывает тип наполнителя и соотношение входящих в эластомерную композицию полимерных продуктов.
)Впервые показано что введение волокнистого наполнителя как компонента резиновых смесей позволяет повысить и обеспечить их стойкость к продавливанию в статических условиях.
) Разработан технологический процесс изготовления рулонных и штучных кровельных материалов на основе разработанной оригинальной рецептуры.
) Разработан проект цеха по изготовлению 500000 м2 кровельного материала на основе нового технологического процесса.
Список используемой литературы
Власенко Ф. С. «Эластомерные невулканизованные и неармированные рулонные кровельные и гидроизооляционные материалы многоцелевого назначения» Диссертация на соискание ученой степени кандидата технических наук. МИТХТ им. М.В. Ломоносова Москва 2009
Раскина Э. М. Новые эластомерные кровельные материалы. Каучук и резина. №4 2006г.)
Андрашников Б.И. Механизация и автоматизация процессов вулканизации и заключительных операций. М.: Химия. 1976.
Бекин Н.Г. Шанин Н.П. Оборудование заводов резиновой промышленности: Учебное пособие для вузов. Л.: Химия 1973. – 400с.
Машины и аппараты резинового производства. Под ред. Д.М. Барскова. М.: Химия 1975 – 600с.
Захарченко П.И. Справочник резинщика. Материалы резинового производства П.И. Захарченко [и др.] - М.: Химия 1964 - 606с.
Белозеров Н.В. Технология резины - М.: Химия 1964 - 660с.
Куликов И.Г. Техника безопасности и противопожарная техника на заводах резиновой промышленности И.Г. Куликов – М.: Химия 1987.
Шабанова В.П. Методические указания к дипломному и курсовому проектированию: учеб. пособие В.П.Шабанова В.Ф. Каблов С.Н.Бондаренко ВолгГТУ – Волгоград 2008 – 118 с.
Общий вид - 1.cdw

Диаметр робочей частини валков - 710мм.
Длина робочей части валков - 1800мм.
Робочая скорость валков:
а) верхнего и нижнего основных от 8 до 80 ммин.;
б) верхнего и нижнего выносных от 5.85 до 58.5 ммин.
Фрикция между валками:
а) верхним основным и выносным 1.5:1;
б) нижним основным и выносным 1.5:1;
в) верхним и нижним основным 1:1.
Толщина каландрованого материала 0.3-3мм.
Пластичность обробатываемой резины по ГОСТ 415-75 не ниже 0
КП-40461806-240502.65-05-09
Технические требования:
*-Размеры для справок.
Монтаж каландра производить в соответствии с инструкцией по
монтажу. Запуск и опробование каландра в роботе производить в
соответствии с инструкцией по эксплуатации.
Систему установок тепловой автоматики расположить на
расстоянии не больше 10 м от каландра.
Специф оборудования.spw

План цеха по производству
кровельного материала на основе
бутилового регенерата
КП-40461806-240502.65-05-09 ТХ
Вальцы подогревательные
Каландр 4-х валковый
Пресс гидравлический
вулканизационный ПХГ-125
Устройство для охлаждения
резиновой смеси "Жучок
Устройство закаточное
Устройство раскаточное
и закатывания рулонов
Устройство для протягивания
вулканизованного полотна
Рекомендуемые чертежи
- 24.04.2014
- 24.04.2014
- 24.04.2014
- 24.01.2023