Интенсификация процесса дегидрирования изоамиленов




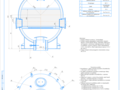
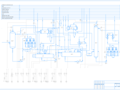
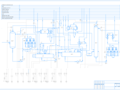
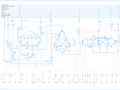
- Добавлен: 25.01.2023
- Размер: 1019 KB
- Закачек: 1
Описание
Состав проекта
![]() |
![]() |
![]() ![]() ![]() |
![]() ![]() ![]() |
![]() ![]() ![]() |
![]() ![]() ![]() |
![]() ![]() ![]() |
![]() ![]() ![]() ![]() |
![]() ![]() ![]() |
![]() ![]() ![]() ![]() |
![]() ![]() ![]() |
![]() ![]() ![]() ![]() |
![]() ![]() ![]() |
![]() ![]() ![]() |
![]() ![]() ![]() |
![]() ![]() ![]() |
![]() |
![]() ![]() ![]() |
![]() |
![]() ![]() ![]() ![]() |
![]() ![]() ![]() |
![]() ![]() ![]() ![]() |
Дополнительная информация
БЖД Каримов.doc
Роль технологии в обеспечении безопасных условий труда и охраны окружающей среды чрезвычайно велика. Соблюдение в технологии предельных значений технологических параметров надежное регулирование процесса позволяет обеспечить надежную и безопасную работу установок для окружающей и природной среды.
Безопасность производственных процессов обеспечивается: выбором технологического процесса а также приемов режимов работы и порядка обслуживания производственного оборудования; выбором производственных помещений и площадок; выбором исходных материалов заготовок и полуфабрикатов а также способов их хранения и транспортирования (в том числе готовой продукции и отходов производства); выбором производственного оборудования и его размещения; распределением функций между человеком и оборудованием в целях ограничения тяжести труда.
Большое значение для обеспечения безопасности имеет профессиональный отбор и обучение работающих безопасным приемам труда правильное применение ими средств защиты.
Производственные процессы не должны представлять опасности для окружающей среды должны быть пожаро- и взрывобезопасными [3].
1 БЕЗОПАСНОСТЬ ПРОЕКТА
1.1. Общая характеристика опасностей проекта
Основными видами опасности являются:
- Токсичные вещества;
- Пожаро- и взрывоопасность;
- Шум и вибрация [5].
1.2. Безопасность производственной деятельности и мероприятия по ее обеспечению
Характеристика токсичных веществ по их действию на организм человека и средства индивидуальной защиты [1 10 17]:
Водород – инертный газ при высоких концентрациях вызывает удушье. Средство – противогаз БКФ шланговый противогаз ПШ-1.
Азот – инертный газ не токсичен при увеличении содержания в воздухе затрудняется дыхание появляется головная боль вызывает удушье. Средство защиты – вентиляция помещения.
Метан – газ наркотического действия. ПДК = 300 мгм3.Класс опасности 4. Средства защиты – противогазы марки «А» ПШ-1 ПШ-2.
Этан – газ наркотического действия. ПДК = 300 мгм3. Класс опасности 4. Средства защиты – противогазы марки «А» ПШ-1 ПШ-2.
Пропан – газ наркотического действия. ПДК = 300 мгм3. Класс опасности 4. Средства защиты – противогазы марки «А» ПШ-1 ПШ-2.
Бутан – газ наркотического действия. ПДК = 300 мгм3. Класс опасности 4. Средства защиты – противогазы марки «А» ПШ-1 ПШ-2.
Изопентан – наркотик действует на нервную систему раздражает слизистые оболочки. ПДК = 300 мгм3. Класс опасности 4. Средства защиты – противогазы марки «А» ПШ-1 ПШ-2.
Пентан – наркотик действует на нервную систему раздражает слизистые оболочки. ПДК = 300 мгм3. Класс опасности 4. Средства защиты – противогазы марки «А» ПШ-1 ПШ-2.
Железооксидный катализатор К-24 «И» – токсичен раздражает слизистые оболочки и кожу. При длительном вдыхании пыли вызывает заболевание легких (сидероз). ПДК =1 мгм3. Класс опасности 2. Средства защиты – респиратор «Лепесток».
Изоамилены – действует угнетающе на нервную систему раздражает слизистые оболочки глаз и верхние дыхательные пути. ПДК =100 мгм3. Класс опасности 4. Средства защиты – противогаз коробка БКФ.
Изопрен – действует угнетающе на нервную систему раздражает слизистые оболочки глаз и верхние дыхательные пути. ПДК =40 мгм3. Класс опасности 4. Средства защиты – противогаз коробка БКФ.
Масло АМГ-10 – горюющая жидкость. ПДК = 300 мгм3. Класс опасности 4. Средства защиты – противогаз коробка БКФ.
Топливный газ – газ наркотического действия. ПДК = 300 мгм3. Класс опасности 4. Средства защиты – противогаз коробка БКФ.
Диоксид углерода – бесцветный газ наркотик раздражает кожу и слизистые оболочки ПДК = 50 мгм3. Класс опасности 4. Средства защиты – противогаз коробка БКФ.
Оксид углерода – ядовитый газ действует на центральную нервную систему и на кровь вызывает потерю сознания судороги одышку удушье. ПДК = 30 мгм3. Класс опасности 4. Средства защиты – противогаз коробка БКФ.
В цехе используются следующие средства защиты органов дыхания:
Фильтрующие- противогазы марки БКФ представляющие собой коробку защитного цвета с белой вертикальной полосой защищает от воздействия кислых газов и паров паров органических веществ мышьяковистого и фосфористого водорода пыли дыма тумана. Он применяется при концентрации кислорода не менее 18 % об. Каждый работающий в цехе имеет свой личный противогаз также в операторной установлен шкаф с аварийным запасом противогазом на каждого работающего в смене.
Изолирующие – шланговые противогазы марки ПШ -1. Он применяется при ведении работ по очистке внутри аппаратов емкостей колонн коммуникаций и арматуры канализационных и других колодцев при выполнении технологических операций в колодцах и приямках [6c.13].
При работе с пылевидными продуктами используются респираторы типа « АРТС 187Г7 ».
Коллективной мерой защиты является – вентиляция.
Пожарная безопасность.
С учетом характеристики производства в проекте предусмотрены мероприятия по безопасным условиям работы определены основные системы пожаротушения.
Важным профилактическим мероприятием по устранению причин возникновения и распространения пожаров и взрывов является правильное категорирование и классификация производств помещений установок электрического и электроосветительного оборудования по их пожаро- и взрывоопасности в соответствии с действующими правилами и нормами.
Установлено что наиболее частыми причинами пожаров и взрывов на предприятиях химической промышленности являются: нарушение элементарных правил пожарной безопасности нарушение режима технологических процессов исправность электрооборудования плохая трудовая дисциплина
Цех дегидрирования изоамиленов относится по НПБ-105-95 к категории «А» и «Б» - взрывопожароопасное [5].
Характеристики пожаро- взрывоопасных свойств сырья [3]:
Водород: tсамовосламенения= 510 С; концентрационные пределы взрываемости: верхний 400 % об нижний 7500 % об.
Метан: tсамовосламенения= 537 С; концентрационные пределы взрываемости: верхний 500 % об нижний 1500 % об.
Этан: tсамовосламенения= 515 С; концентрационные пределы взрываемости: верхний 307 % об нижний 1500 % об.
Пропан: tсамовосламенения= 466 С; концентрационные пределы взрываемости: верхний 231 % об нижний 950 % об.
Бутан: tсамовосламенения= 405 С; концентрационные пределы взрываемости: верхний 180 % об нижний 910 % об.
Пентан: tсамовосламенения= 287 С; концентрационные пределы взрываемости: верхний 147 % об нижний 780 % об.
Изопентан: tвспышки= -52 С; tсамовосламенения= 427 С; концентрационные пределы взрываемости: верхний 136 % об нижний 760 % об.
Изоамилен: tвспышки= -48 С; tсамовосламенения= 273 С; концентрационные пределы взрываемости: верхний 149 % об нижний 830 % об.
Изопрен: tвспышки= -52 С; tсамовосламенения= 400 С; концентрационные пределы взрываемости: верхний 170 % об нижний 1150 % об.
В цехе установлена автоматическая установка пенотушения углекислотная установка огнетушитель ОХП-10 кошма песок. Пожарные краны находятся на всех отметках корпусов. Извещатели пожарной сигнализации установлены на лестничных клетках корпуса у входа в корпуса.
По “Правилам устройства электротехнических установок” в производстве полиэтиленполиаминов используется электрооборудование повышенной надежности против взрыва так помещение по опасности поражения электрическим током относится к категории В-I а.
Защитные средства - приборы аппараты переносные приспособления и устройства служащие для защиты персонала работающего на электроустановках от поражения электрическим током от воздействия продуктов ее сгорания при коротком замыкании.
В данном производстве применяются изолирующие и индивидуальные вспомогательные защитные средства. Изолирующие защитные средства обеспечивают электрическую изоляцию человека от токоведущих частей а также от земли (заземление зануление).
Ограждающие защитные средства предназначены для временного ограждения токоведущих частей а также для предупреждения ошибочных операций с коммутационными аппаратами.
Вспомогательные средства защиты предназначены для индивидуальной защиты обслуживающего персонала от действия электрического тока.
Для обеспечения электробезопасности применяют защитное заземление которое обеспечивает коллективную защиту работающих от поражения электрическим током а также защитное отключение позволяющее быстро отключить электроустановку при возникновении в ней опасности поражения током используются системы сигнализации и блокировки оградительные устройства.
В данном производстве применяются электроустановки с напряжением более 1000 В поэтому сопротивление заземляющих устройств в любое время года не должно превышать 40 Ом. В цехе производства полиэтиленполиаминов для электрооборудования в силовой сети используется напряжение 380 В. в сети освещения 220 В [4].
Защита от статического электричества. Молниезащита.
На химических заводах взрывы и пожары могут возникнуть от статического электричества. Статическое электричество образуется при трении диэлектриков о металл. В случае накопления электрического заряда определенной величины может произойти электрический разряд искра которого может вызвать взрыв и пожар.
Для борьбы со статическим электричеством предусматриваются следующие мероприятия:
– все продуктовые трубопроводы металлические эстакады и аппараты в цехе заземляются; подключение заземленных проводов осуществляется к общему контуру заземления цехового оборудования;
– заземление должно систематически проверяться электролабораторией по графику;
– все оборудование и трубопроводы находящиеся в цехе и соединенные между собой рассматриваются как единая электрическая цепь вследствие чего все фланцевые соединения должны иметь либо приваренные металлические перекидки либо не менее двух тщательно защищенных болтовых соединений;
– сливы и стравливание огнеопасных продуктов из аппаратов свободной струей запрещается слив должен производится по специально оборудованному шлангу; шланги должны иметь наконечники из искронедающего собраны на хомутах и иметь заземление для отвода статического электричества равное 4 Ом.
Сопротивление любой точки неметаллического оборудования относительно контура заземления - 100 Ом [4].
Система мероприятий по защите зданий и сооружений выполняются в соответствии с “Указаниями по проектированию и устройству молниезащиты зданий и сооружений”. Для защиты помещений производства от прямых ударов молний на его крыше устанавливаются стержневые молниеотводы соединенные с заземлителями токопроводящими стержнями. Общее сопротивление заземления 4 Ом.
Повышение уровня шума и вибрации на рабочих местах оказывает вредное воздействие на организм человека. В результате длительного воздействия шума нарушается нормальная деятельность сердечно- сосудистой и нервной системы пищеварительных и кроветворных органов развивается профессиональная тугоухость прогрессирование которой может привести к полной потере слуха. Вибрация воздействует на центральную нервную систему желудочно-кишечный тракт органы равновесия вызывает головокружение онемение конечностей заболевание суставов. Длительное воздействие вибрации вызывает профессиональное заболевание – вибрационную болезнь эффективное лечение которой возможно лишь на ранних стадиях. В соответствии с ГОСТ 12.1.003-83 уровень звука и эквивалентный уровень звука составляет 80 дБ. Для защиты работающих от вредного влияния шума на аппаратах установлены специальные кожухи внутренняя поверхность кожуха обязательно облицовывается звукопоглощающим материалом. Для защиты от вибрации – вибропоглощающие и виброизолирующие материалы. Для уменьшения вибрации кожухов ограждений выполненных из стальных листов на них наносят слой резин пластиков битума которые рассеивают энергию колебаний.
В соответствии с характером и назначением производства помещений цеха предусмотрено освещение: рабочее ремонтное и аварийное.
В цехе применяется комбинированное освещение: общее (производственное помещение освещается однотипными светильниками равномерно расположенными над освещаемой поверхностью и снабженными лампами одинаковой мощности) и местное (освещение непосредственно рабочих мест).
Освещение и световое оформление производственных помещений необходимо выполнить согласно СН и П 23-05-95. В соответствии с нормами в зависимости от характера выполняемых работ освещенность в помещениях при общем постоянном наблюдении за ходом производственного процесса должна быть не менее 75 люкс в помещениях при периодическом наблюдении за аппаратами - не менее 50 люкс на лестничных клетках в бытовых помещениях - не менее 20 люкс [4].
Для общего освещения в проходах и на лестницах устанавливаются стационарные светильники во взрывозащищенном исполнении типа ВЗГ-2000М обеспечивающих освещенность на уровне пола не менее 03 люкс.
Для освещения производственных помещений при внезапном отключении рабочего освещения имеется аварийное освещение. Которое должно быть достаточным для безопасного выхода персонала из помещений и продолжения работы в помещениях и на открытых площадках когда отключение рабочего освещения может повлечь за собой пожар взрыв нарушение технологического режима на довольно длительный срок и сбой работы важнейших объектов.
Аварийное освещение имеет независимый источник питания и обеспечивает освещение рабочих поверхностей не менее 5% от принятых норм для общего освещения но не менее 2 люкс. Система аварийного освещения оснащена аккумуляторными светильниками типа СЗГ.
Для ремонтного освещения следует применять переносные светильники напряжением не выше 12 В [4] .
Насосные и компрессорные - 10 люкс; помещения щитовых КИП и А - 75 люкс; административные помещения - 50 люкс; мастерские - 75 люкс; проходы площадки для обслуживания агрегатов- 10 люкс; туалеты умывальники душевые 30 люкс [4].
Обеспечение нормальных метеорологических условий и чистоты воздуха на рабочих местах в значительной степени зависит от правильного организованной системы вентиляции. В отделении установлена комбинированная система вентиляции предусматривающая общеобменную и местную вентиляцию. Также установлена приточно – вытяжная вентиляция обеспечивающая одновременную подачу и удаление воздуха. Забор свежего воздуха для приточных систем осуществляется через специальные шахты. Размещение приточных и вытяжных систем в одной камере не допускается. Общеобменная вент. система работает круглосуточно.
Основным показателем характеризующим воздухообмен является кратность воздухообмена. Кратность воздухообмена в рабочем помещении К ч -1 вычисляют по формуле [18]:
где L-объем подаваемого (удаляемого) воздуха м3ч;
V- объем вентилируемого помещения м3.
Объем воздуха L м3ч необходимого для разбавления вредных газо- паровыделений попадающих в рабочее помещение до концентрации соответствующей предельно-допустимой вычисляют по формуле [18]:
где G-масса вредных веществ выделяющихся в рабочем помещении в
СПДК -предельно допустимая концентрация вредных веществ по
санитарным нормам мгм3;
СПР - содержание вредных веществ в подаваемом воздухе мгм3.
Вычислим кратность воздухообмена для рабочего помещения:
Выбираем вентилятор типа Ц 9-57 производительностью 26000 м3ч.
Тогда необходимое количество вентиляторов для приточной вентиляции вычислим по формуле [18]:
где nв - производительность вентилятора м3ч.
Принимаем 2 вентилятора.
Кроме основной в цехе имеется аварийная вентиляция предназначенная для интенсивного проветривания помещения в случае внезапного поступления в него больших количеств взрывоопасных и токсичных выделений в результате аварии или нарушения технологического процесса.
При аварийных выбросах необходим сорокократный воздухообмен следовательно надо учесть кратность воздухообмена на величину:
где: 238 ч-1 – кратность воздухообмена в нормальных рабочих условиях.
Количество воздуха подаваемого аварийной вентиляцией Кв м3ч вычисляют по формуле:
следовательно выбираем вентиляторы типа Ц 9-57 производительностью 10000 м3ч. Тогда число аварийных вентиляторов вычисляют по формуле:
Принимаем 3 аварийных вентиляторов.
В производственных помещениях где постоянно или длительно пребывает обслуживающий персонал предусматривает устройство отопления.
В цехе используется воздушное отопление так как оно является наиболее безопасным: нагрев производится в паровых или водяных калориферах. Воздушное отопление сочетается с приточной системой. Для надежности устанавливается не менее двух самостоятельных отопительных систем. Температура на поверхности отопительных приборов центрального отопления не должна превышать 95оС. Отопительные приборы должны быть гладкими и легкодоступными для очистки. Не допускается устанавливать отопительные приборы в нишах. Температура воздуха рабочей зоны поддерживается в холодный и переходный периоды года 18-23оС в теплый 23-25оС. В рабочем помещении температура воздуха должна быть не выше 30 0С и не ниже 10 0С.
Повторное использование теплого воздуха путем рециркуляции желательно для экономии тепла но при наличии ядовитых продуктов и в производственных отнесенных по взрыво- и пожароопасности к категориям А и Б оно противопоказано из-за возможности накопления в помещении ядовитых и токсичных веществ достижения ими взрывоопасных и пожароопасных концентраций.
Льготное обеспечение.
Цех дегидрирования изоамиленов относится к производству с вредными условиями труда. На основании Постановлений Госкомитета по труду и заработной плате работникам производства представляются следующие льготы:
- дополнительный отпуск 12 рабочих дней;
- бесплатное лечебно-профилактическое питание за исключением управлен-
ческого персонала и служащих;
- бесплатная выдача спецодежды спецобуви и защитные приспособления;
- льготное пенсионное обеспечение;
- повышенная оплата за особо-вредные условия труда.
Работающие обеспечиваются путевками в профилакторий и санаторий. Все эти мероприятия предупреждают профзаболевания.
Бытовые помещения предназначены для санитарно-гигиенического обслуживания работников для размещения службы быта.
К бытовым помещениям относят: гардеробная душевые кабины комната приема пищи и личной гигиены. Весь комплекс бытовых помещений находится в административном корпусе цеха. В гардеробной имеются шкафы для хранения рабочей и чистой одежды душевые и умывальные располагаются в смежных комнатах с гардеробными. Допускается размещение умывальников в гардеробных при условии что расстояние от умывальника до шкафов не менее 2 метров. Число душевых сеток и умывальников проектируется: 3 человека на 1 сетку и 15 человек на 1 умывальник. Расчетное количество продолжительности работы душевой 45 минут для 1 смены.
Количество необходимой мебели в бытовых помещениях соответствует численности персонала
Меры безопасности при ведении технологического процесса:
Для безопасного ведения технологического процесса необходимо соблюдать ряд правил:
- не допускать нарушения норм технологического режима;
- соблюдать план аналитического контроля;
- к самостоятельной работе не допускать лиц не прошедших инструктаж и обучение по рабочим местам и без индивидуальных средств защиты;
- фланцевые соединения трубопроводов щелочей должны иметь защитные кожухи;
- не выполнять работу не связанную с прямыми обязанностями и не предусмотренную инструкцией по рабочему месту без проведения целевого инструктажа;
- какие-либо приборы и автоматика должны быть технически исправны;
- работать с исправными защитными устройствами (отсечные обратные предохранительные клапаны);
- не допускать отключения приточно-вытяжной вентиляции кроме случаев пожара;
- не допускать загазованности производственных помещений выше ПДК;
- нельзя работать на неисправном оборудовании с нарушенным заземлением и без исправных ограждений на движущихся частях механизмов;
- ремонтные работы проводить при наличии наряда-допуска и на приготовленном оборудовании. Аппараты должны быть освобождены от продукта промыты водой пропарены продуты азотом воздухом отглушены и при необходимости обесточены;
- ремонтные работы в аппаратах и трубопроводах имеющих контакт с взрывоопасными продуктами должны проводится искробезопасным инструментом;
- при осмотре и ремонте оборудования и трубопроводов на высоте необходимо применять специальные лестницы переносные площадки с ограждениями а также пользоваться предохранительными поясами;
- горячие поверхности аппаратов и трубопроводов должны быть изолированы;
- соблюдать правила эксплуатации аппаратов работающих под давлением;
- огневые работы производить при наличии наряда-допуска в присутствии ответственного лица;
- газоопасные работы производить при наличии наряда-допуска в присутствии ответственного лица;
- все аппараты с взрывоопасными продуктами должны работать под «азотным дыханием»;
- предусмотрена предупреждающая сигнализация максимального и минимального уровня в емкостях сборниках;
- ремонт и чистку устранение неисправности на оборудовании имеющих эл.привод производить после разбора эл.схем и вывешивания плакатов: «Не включать – работают люди!»;
- рабочие места и территорию цеха содержать в чистоте и порядке;
- курение в цехе разрешается только в специально-отведенном месте корпуса
- первичные средства пожаротушения находятся на всех отметках производственных помещений;
- не допускать хранения и прием пищи в производственных помещениях.
К основным опасностям при дегидрировании изоамиленов относятся:
-наличие углеводородов С4 – С5 наркотически и раздражающе действующих на организм человека вызывающих изменения сосудистой и центральной нервной системы обслуживающего персонала;
- наличие азота действующего на человека удушающее;
- возможность поражения электрическим током;
- наличие пара и конденсата высоких температур которые могут вызвать термический ожог;
- наличие движущихся частей машин и механизмов линий механической выгрузки что может привести к травмированию при нарушении эксплуатации и при переходе через линию без соблюдения мер предосторожности;
- наличие аппарата работающего под давлением (10-50) кгссм2 и возможность разрыва аппарата и коммуникаций при нарушении правил эксплуатации.
Меры пожарной безопасности характерные для производства:
- максимальная автоматизация технологического процесса;
- применение для горючих веществ герметичного оборудования;
- установка пожароопасного оборудования на открытых площадках;
- уменьшение массы или объема горючих веществ и материалов находящихся одновременно в помещении или на открытых площадках;
- применение устройств защиты производственного оборудования с горючими веществами от повреждений и аварий (обратные отсечные предохранительные клапаны);
- поддержание концентраций горючих газов паров и окислителя в смеси вне пределов их воспламенения;
- применение оборудования механизмов устройств при эксплуатации которых не образуются источники зажигания;
- применение эл.оборудования соответствующего пожароопасной и взрывоопасной зонам группе и категории взрывоопасной смеси в соответствии с требованиями ПУЭ;
- применение технологического процесса и оборудования удовлетворяющего требованиям электрической искробезопасности;
- устройство молниезащиты зданий сооружений и оборудования;
- применение неискрящего инструмента при работе с ЛВЖ и горючими газами;
- периодическая очистка территории от горючих отходов пыли пуха мусора[5].
Риск – количественная характеристика действия опасностей то есть число сметных случаев число случаев заболевания число случаев временной и стойкой нетрудоспособности (инвалидности) вызванных действием на человека конкретной опасности отнесенной на определенное количество работников за конкретный период времени.
Приемлемый риск – это такой низкий уровень смертности травматизма или инвалидности людей который не влияет на экономические показатели предприятия.
Допустимость риска по международной договоренности принята в пределах от 10-7 до 10-6 (смертельных случаев чел-1·год-1) а величина 10-6 является максимально приемлемой уровнем индивидуального риска. В цехе производства полиэтиленполиаминов реальный риск не превышает приемлемого.
1.3 Мероприятия по защите окружающей природной среды от опасностей
Опасность производства изопрена для окружающей природной среды (ОПС) может возникнуть только при аварийных ситуациях. Причинами аварийных ситуаций могут быть например прекращение подачи электроэнергии пара воды розлив токсичных продуктов разгерметизация трубопроводов оборудования загазованность загорание.
Мероприятия по предотвращению аварийных ситуаций:
- контрольно-измерительные приборы и автоматика должны быть технически исправны;
- не допускать загазованности производственных помещений выше предельно-допустимых концентраций;
- ремонтные работы проводить при наличии наряда-допуска и на подготовленном оборудовании. Аппараты должны быть освобождены от продукта промыты водой пропарены продуты азотом воздухом отглушены и при необходимости обесточены;
- ремонт и чистку устранение неисправности на оборудовании имеющем эл. привод производить после разбора эл. схем и вывешивания плакатов: «Не включать – работают люди!».
Аварийный останов цеха производится в следующих случаях: прорыв углеводородов загазованность помещений и территории цеха загорание.
При загазованности территории или помещений цеха взрыве пожаре в цехе объявляется аварийное положение при этом необходимо:
а) вызывать газоспасательную службу пожарную команду скорую помощь;
б) на месте аварии и в смежных помещениях на установках прекратить все виды огневых ремонтных работ при необходимости отключить электроэнергию на месте аварии непосредственно с подстанции;
в) удалить людей не занятых ликвидацией аварии ведением режима в безопасную зону;
г) отключить повреждённый участок в местах где это не угрожает жизни исполнителей от остальных коммуникаций;
д) произвести аварийный останов отделений и установок цеха;
е) при загазованности усилить естественное проветривание помещений открыв ворота двери окна помещений;
ж) при пожаре все виды вентиляции должны быть отключены окна двери ворота закрыты;
з) по возможности освободить от углеводородов на сырьевой склад или ёмкости вне зоны аварии аппараты с углеводородами находящиеся в опасной зоне аварии;
и) отключить вентиляцию;
к) отмена аварийного положения может быть осуществлена только после полного обследования состояния всего оборудования и коммуникаций на месте аварии и связанных с ней местах.
2. ЭКОЛОГИЧНОСТЬ ПРОЕКТА
Изучение экологической характеристики производства изопрена борьба с вредными воздействиями на человека сточных вод и различных газовых выбросов является частью общей проблемы защиты окружающей среды. При производстве изопрена образуются выбросы в атмосферу сточные воды твердые отходы.
2.1. Выбросы их состав количество влияние на окружающую природную среду и меры по обеспечению ПДВ
Дымовые газы печей поз. 4 103 – выбрасываются в атмосферу через трубу. Установленная норма содержания загрязнений в выбросах – СО отсутсвие.
Газы регенерации после апп. поз. 18 – выбрасываются в атмосферу через трубу. Установленная норма содержания загрязнений в выбросах – содержание пыли катализатора ИМ-2201 - нб 01 гнм3.
Вентиляционные выбросы – выбрасываются в атмосферу через трубу. Установленная норма содержания загрязнений в выбросах – углеводороды - нб 300 мгм3
2.2. Водоснабжение производства и канализация нормы расхода воды.
В цех вода подается для производственно-технических целей хозяйственно-питьевых нужд и для пожаротушения. Для хозяйственно-питьевых нужд количество требуемой воды определяется действующими нормами проектирования промышленных предприятий. Основное количество воды используемой в производстве ПЭПА расходуется в теплообменниках на абсорбции аммиака на разбавление щелочи.
Для питьевой воды в цехе устанавливаются фонтанчики. Качество воды регламентировано ГОСТ 2874-73. Суточная норма расхода питьевой воды составляет 25 литров на одного человека и 180-200 литров на каждый кран-умывальник. Расход воды на душевые 500 лч на человека [ 9 ].
Расход воды на технологические нужды составляет 16206 м3т [ 9 ]
Противопожарный водопровод рассчитывается исходя из предположения что пожар произойдет в часы максимального забора воды другими потребителями. Расчетный расход воды на противопожарные нужды составляет 45 лс [ 9 ].
Для сброса воды предусмотрены системы канализаций: для оборотных промышленных вод для загрязненных промышленных вод для ливневых вод. Сброс токсичных а так же пожаро - взрывоопасных продуктов из емкостей в канализационные системы даже при аварийных ситуациях запрещается. Категорически не допускается соединение сетей хозяйственно-питьевой воды с сетями промышленного водопровода. Расчетный расход воды на противопожарные нужды составляет 45 лс
2.3. Сбросы их состав количество влияние на окружающую природную среду меры по обеспечению ПДС.
Сточные воды представляют собой один из видов жидких отходов и подразделяются на производственные бытовые и поверхностные.
Производственные сточные воды образуются в результате использования воды в технологических процессах. Бытовые сточные воды образуются в раковинах санитарных узлах душевых и т. д. Поверхностные сточные воды образуются в результате смывания дождевыми снеговыми и поливочными водами загрязнений имеющихся на поверхности грунтов на крышах и стенах зданий и т.д.
Водяной конденсат (из контактного газа) – удельная норма выброса на тонну выработанного изопрена 168 м3тн количество образования сточных вод 200 250 м3час. Периодичность образования – постоянно. Условия (метод) обезвреживания утилизации – двухступенчатый отстой и дегазация от углеводородов затем сбрасываются в хим. загрязненную канализацию. Установленная норма содержания загрязнений в стоках – ХПК - 1000 мгО2л нефтепродукты - нб 90 мгл.
Атмосферные осадки (условно-чистые стоки) –периодичность образования – переодически. Количество образования сточных вод 168 м3час. Условия (метод) обезвреживания утилизации – сбрасываются в пром. ливневую канализацию.
Конденсат продувок котлов – количество образования сточных вод 10 12 м3час. Периодичность образования – постоянно. Условия (метод) обезвреживания утилизации – двухступенчатый отстой и дегазация от углеводородов затем сбрасываются в хим. загрязненную канализацию.
2.5 Отходы их состав количество влияние на окружающую природную среду меры по обеспечению ПДС
Отработанный катализатор ИМ-2201 – удельная норма выброса на единицу готовой продукции 23 кгтн количество 20003500 тгод. Периодичность образования –ежесменно. Условия (метод) место захоронения обезвреживания утилизации -- на заводы потребители в цех Д-11-13 на переработку.
Отработанная смесь катализатор-теплоноситель из реакторов – удельная норма выброса на единицу готовой продукции 21 кгтн количество 175 тгод. Периодичность образования – 6 раз год. Условия (метод) место захоронения обезвреживания утилизации – на полигон для захоронения или заводам-потребителям.
Отработанное дизельное топливо и абсорбент – удельная норма выброса на единицу готовой продукции 7 кгтн количество 400 тгод.Переодичность образования –ежесменно. Условия (метод) место захоронения обезвреживания утилизации – сжигаются в печи поз.103 (6 блока).
2.6 Экологическая безопасность проекта для окружающей природной среды
В проектируемом производстве есть выбросы сбросы и отходы.
Выбросы поступают в атмосферу без превышения ПДВ.
Сточные воды подвергаются двухступенчатый отстой и дегазация от углеводородов а затем сбрасываются в химически загрязненную канализацию.
Твердые отходы поступают на заводы потребители для переработки сжигаются в печи или направляются на полигон для захоранения. Поэтому ни выбросы ни сток ни отходы не оказывают вредного влияния на окружающую среду. Следовательно проект экологически безопасен.
3.БЕЗОПАСНОСТЬ И ЭКОЛОГИЧНОСТЬ ПРОЕКТА В ЧРЕЗВЫЧАЙНЫХ СИТУАЦИЯХ
Чрезвычайная ситуация – состояние при котором в результате возникновения источника чрезвычайной ситуации на объекте определенной территории нарушаются нормальные условия жизни и здоровья наносится ущерб имуществу населения народному хозяйству и окружающей природной среде. Под источником чрезвычайной ситуации понимают опасное природное явление аварию или опасное техногенное происшествие широко распространенную инфекционную болезнь людей сельскохозяйственных животных и растений а также применение современных средств поражения в результате чего произошла или может возникнуть чрезвычайная ситуация.
3.1 Причины возникновения ЧС
Чрезвычайные ситуации подразделяются на естественного (природного) и антропогенного происхождения:
ЧС естественного происхождения:
Землетрясения – это подземные удары (толчки) и колебания поверхности земли вызванные естественными процессами происходящими в земной коре. Часто нарушается целостность грунта разрушаются здания и сооружения выходит из строя водопровод канализация линии связи электро- и газоснабжения имеются человеческие жертвы.
Порядок действия при землетрясении [10]:
)если первые толчки вас застали на первом этаже необходимо немедленно покинуть помещение и удалиться как можно дальше от стоящих зданий сооружений столбов они могут упасть и придавить вас;
)если во время толчка вы находились на втором и последующих этажах необходимо встать в дверных проемах и закрыть лицо и голову руками во избежание ранений кусками штукатурки;
)нельзя пользоваться лифтом;
)помните что после первого толчка последуют еще несколько;
)землетрясения сопровождаются пожарами не приближайтесь к веществам воспламеняющимся взрывчатым и токсичным;
)имейте при себе противогаз.
Наводнения – это временное затопление значительной части суши водой в результате действия сил природы. Происходят в результате обильных осадков или интенсивного таяния снега из-за сильных нагонных ветров из-за подводных землетрясений.
Порядок действия при наводнении [10]:
)при угрозе наводнения проводят предупредительные мероприятия позволяющие снизить ущерб и создать условия для эффективных спасательных работ;
)необходимо помнить что времени мало и его надо использовать с максимальной пользой;
)если угроза наводнения будет нарастать на предприятии необходимо позаботиться о безопасности людей работающих на непрерывном производстве;
)необходимо убрать с территории завода в безопасное место все вещества со складов во избежание загрязнения стоков воды.
ЧС антропогенного происхождения [10]:
Основными причинами возникновения ЧС в цехе № 15 могут служить аварийная разгерметизация оборудования для хранения транспортировка и переработка веществ находящихся в газообразном и жидкофазном состояниях. Переработка приводит к выбросу содержимого аппарата в окружающую среду. Другой причиной возникновения ЧС может быть взрыв. Причинами взрыва могут быть не только нарушения ведения технологического процесса но и большие газовые облака образующиеся при утечке или внезапном разрушении герметичных емкостей трубопроводов и т. п.
Авария – это повреждение машины станка оборудования здания сооружения. Происходят аварии на коммунально-энергетических сетях промышленных предприятиях. Если эти происшествия не столько значительны и не повлекли за собой серьезных человеческих жертв – их обычно относят к разряду аварий.
Катастрофа – это крупная авария с большими человеческими жертвами т.е. события с трагическими происшествиями.
Главным критерием в различии аварий и катастроф заключается в тяжести последствий и наличии человеческих жертв.
В результате аварий на предприятии возможны взрывы и пожары а их последствия – разрушение и повреждение зданий и сооружений технологий и оборудования затопление территорий выход из строя линий связи энергетических и коммунальных сетей.
При взрывах ударная волна не только приводит к разрушениям но и человеческим жертвам. Степень и характер взрыва разрушения зависит кроме мощности взрыва от технологического состояния сооружений характера застройки и рельефа местности. Наиболее часто взрывы происходят на предприятиях использующих углеводородные газы в котельных газовых аппаратах при использовании легковоспламеняющихся жидкостей.
Причины – ошибки при изыскании и проектировании низкое качество строительных работ. Пожары возникают в результате перевозок горючего химикатов.
При возникновении ЧС важно своевременно оповестить и организовать защиту рабочих и служащих всего вблизи проживающего населения которому угрожает опасность.
3.2 Оповещение о чрезвычайных ситуациях
В результате чрезмерной концентрации промышленности в отдельных регионах усложнения технических процессов использования значительного числа взрыво- пожаро- радиационно-химически опасных веществ износа оборудования наблюдается рост количеств аварий и катастроф увеличения числа человеческих жертв возрастание материального ущерба от чрезвычайных ситуаций техногенного характера.
Все это вынуждает повысить оперативность и надежность управления процессами как предупреждения так и ликвидации последствий. Разработаны и утверждены специальные программы. В результате её реализации должна появиться единая автоматизированная система предупреждения и действий в чрезвычайных ситуациях (АИЦС НСХС) которая будет сопрягаться с местными и региональными звеньями аналогичных систем. Также намечено внедрить видеоинформационные и другие самые современные средства связи. Все это позволит заранее предупредить организации учреждения о возникновении чрезвычайных ситуаций.
Данная система дополняется развитой сетью электрических сирен расположенных на крышах зданий и шумных цехах. Такая развитая система позволяет оповестить заблаговременно население о возникновении чрезвычайных ситуаций рассказать о правилах действия в конкретно сложившейся ситуации.
В случае опасности людей необходимо немедленно оповестить людей где бы они ни находились. Для этого используют сирены. Завывание сирен означает сигнал «Внимание всем!». Услышав вой сирены надо немедленно включить репродуктор радиовещания и слушать сообщения местных органов власти или штаба по делам ГО и ЧС.
На каждый случай чрезвычайных ситуаций местные органы власти совместно со штабом ГО и ЧС заготавливают варианты текстовых сообщений приближенные к своим специфическим условиям. Информация излагается в течение примерно 5 минут и повторяется по несколько раз.
Ответственность за организацию связи и оповещения несут начальники штабов по делам ГО и ЧС всех рангов. Непосредственное обеспечение и поддержку связи в исправном состоянии и осуществляется начальником служб связи.
3.3. Ликвидация последствий ЧС и защиты в них
Федеральные органы власти располагают специально подготовленными и аттестованными силами и средствами предназначенными для предупреждения и ликвидации чрезвычайных ситуаций. Используя их в рамках единой государственной системы можно до минимума сократить потери.
Силы и средства подразделяются: на силы и средства контроля силы и средства на ликвидацию последствий чрезвычайных ситуаций.
Первый подраздел включает органы надзора контрольно-инспекционную службу службу осуществляющую контроль за потенциально опасными объектами лабораторией контроля за природной средой и др. Второй подраздел включает соединения и части подразделения МЧС МО МВД невоенизированные соединения ГО а также силы и средства принадлежащие другим ведомствам и министерствам.
Территориальные органы Министерства ГО и ЧС создают комиссию с целью: установления источника и причин загрязнения; выявления негативных последствий экстремального загрязнения окружающей среды и оценки нанесенного ущерба; для решения вопроса о приостановке работы источника загрязнения.
Органы Госкомсанэпиднадзора в этой ситуации оценивают возможность и степень влияния экстремального загрязнения на здоровье человека. Органы Росгидромета составляют оперативные прогнозы распространения зоны экстремального загрязнения. Органы Роскомнедры обследуют зону распространения экстремального загрязнения подземных вод. Эта комиссия готовит информационные сообщения. Указывают источник информации дату и время поступления информации о ЧС; место населенного пункта область район или наименование водного объекта где выявляется экстремальная ситуация; характеристика экстремальной ситуации; указывают критерии по которым отмечены экстремальные ситуации с указанием количественных характеристик; оцениваются причины возникновения экстремальной ситуации; указывается виновник возникновения экстремальной ситуации; указываются меры по локализации и ликвидации экстремальной ситуации; дается прогноз распространения зоны экстремального загрязнения и затем ведется наблюдение за тем как меняется эта ситуация.
Основу этих сил составляют войска ГО подразделения поисково-спасательной службы и формирования постоянной готовности МЧС. Существует отряд аэромобильной спасательной службы в силах МЧС.
Работы по ликвидации аварии начинаются без промедления. При этом основные условия направляются на спасение людей предотвращение дальнейших аварий и локализацию образовавшегося очага. В очаг высылается разведка. Одновременно производится оцепление места аварии. Спасательные и медицинские формирования ведут поиск пораженных и оказывают им первую помощь. При авариях задействуются все имеющиеся спасательные пожарные медицинские бригады. Посильную помощь оказывает население. Одновременно производится эвакуация людей причем в первую очередь детей женщин стариков. Затем проводятся работы по локализации аварий. После ликвидации аварий проводятся при необходимости дегазация дорог зданий и т.д.
3.4. Восстановительные работы
Планирование восстановления работоспособности предприятия может предусматривать как первоочередное восстановление так и капитальное. Первое может быть выполнено силами самого объекта создающего для этих целей восстановительные бригады.
В проекте восстановления освещаются следующие вопросы:
-объем работ по восстановлению с расчетом потребностей в рабочей силе материалах строительной технике оборудовании деталях инструменте;
-оптимальные инженерные решения по восстановлению работоспособности предприятия;
-календарный план или сетевой график восстановительных работ очередность восстановления цехов исходя из важности их в выпуске основной продукции;
-состав восстановительных работ и др.
При капитальном восстановлении могут потребоваться городские республиканские и федеральные средства и силы.
Охрана труда в химической промышленности. Г.В. Макаров А.Я. Васин Л.К. Маринина и др. -М.: Химия 1989. 496 с.; ил.
Вредные вещества в промышленности. Под ред. Н.В. Лазарева. –Л.: Химия 1971. – 624 с.
Белов П.С. Голубева И.А. Низова С.А. Экология производства химических продуктов из углеводородов нефти и газа.-М.: Химия 1991.-254с.;
Вихман Г.Л. Круглов Г.А. Расчеты и конструирование аппаратов и машин нефтеперерабатывающих заводов.-М.: Недра 1965.-903с.;
Временный классификатор токсичных промышленных отходов и методические рекомендации по определению класса токсичности промышленных отходов. -М.: Химия 1987.-140с.;
Гжиров Р.И. Краткий справочник конструктора. -Л.: Машиностроение 1983.-464с.;
Касаткин А. Г. Основные процессы и аппараты химической технологии. -М.: Химия 1971.-790 с.;
Контроль химических и биохимических параметров окружающей среды (Справочное пособие).-С.-Пб.1998.-896с
1. ЛИТЕРАТУРНЫЙ ОБЗОР (исправленный) 12.doc
1. Каталитическое дегидрирование углеводородов.
К реакциям каталитического дегидрирования способны углеводороды различных гомологических рядов (парафины нафтены олефины и цик-лоолефины алкилароматические углеводороды). В результате реакции отщепляется водород и образуются более ненасыщенные соединения или происходит циклизация (дегидроциклизация). Катализаторами дегидрирования являются различные металлы и окислы. Основные побочные реакции протекающие при каталитическом дегидрировании: крекинг изомеризация коксообразование. Каталитическое дегидрирование является одним из важнейших промышленных процессов переработки углеводородного сырья [123456].
1.1. Промежуточные продукты реакций дегидрирования.
1.1.1. Олефины как промежуточные продукты ароматизации
Основными продуктами дегидрирования н-парафинов С>6 являются ароматические углеводороды наряду с небольшим количеством олефинов. Питкетли и Стейнер [7] на основании зависимости выхода олефинов и ароматических углеводородов от времени контакта (Сг2О3 475°) высказали предположение что ароматизация н-гептана протекает через промежуточное образование гептена.
Однако против этого мнения был выдвинут ряд возражений. Оболенцев и Усов [8] в близких условиях проведения опыта не наблюдали максимума выходов олефинов в зависимости от времени контакта. По термодинамическим расчетам Левицкого [9] в присутствии больших количеств ароматических углеводородов равновесные выходы олефинов сильно снижаются. На этом основании автор высказал предположение что образование олефинов и ароматических углеводородов происходит параллельно а низкие выходы олефинов в условиях высоких выходов ароматического углеводорода могут быть связаны с близостью к равновесию.
Относительная способность парафинов к дегидрированию в олефины и ароматические продукты существенно не меняется при разбавлении водородом или при уменьшении давления в реакторе [10] а это должно было бы иметь место если бы выходы олефинов были ограничены равновесием.
Вывод о промежуточном образовании олефинов при ароматизации парафинов на окисных и неокисных катализаторах подтверждается также опубликованными в последние годы данными опытов с применением меченых атомов (смеси гептан — гептен при 487° и времени контакта 11 — 4 сек. на алюмохромовом катализаторе и гексан — гексен при 360° в импульсном режиме в токе гелия на платине и никеле).
Расчеты по кинетическому уравнению Панченкова для последовательной гетерогенно-каталитической реакции в потоке дают величину отношения констант скоростей превращения олефинов в ароматические углеводороды 1 и парафинов в олефины 2 [11].
1.1.2. Дегидрирование низших парафинов в моно- и диолефины.
При дегидрировании н-бутана и пентанов в продукте кроме моноолефинов образуется некоторое количество днолефинов. Основным фактором определяющим соотношение моноолефиныдиолефины в продукте является степень удаления от равновесия. Равновесные выходы ди-олефинов сильно возрастают с уменьшением давления и повышением температуры реакции.
Бутилены являются промежуточными продуктами дегидрирования н-бутана в дивинил. К этому выводу приводят работы Баландина и сотр. По дегидрированию бутан-бутиленовых смесей в которых один из компонентов
был мечен 14С. Опыты проводили на окиси хрома и на алюмохромовом катализаторе. Превращению подвергалась смесь бутан : бутилен = 1:1. Опыты с окисью хрома проводили при 635° и разбавлении водой 1:9 [12].
Количественный расчет соотношения скоростей дегидрирования бутана в бутилен 1 и дивинил 2 и бутилена в дивинил 3 дал следующие результаты. Для окиси хрома в указанных выше условиях 1 : 2 : 3 =
=20 : 1 : 1000; для алюмохромового катализатора (600° 250 мм) 1 : 2 : 3 = 18 : 1 : 25 т. е. в обоих случаях образование дивинила из бутана происходит практически целиком через стадию образования бутилена [12].
1.1.3. Дегидрирование олефинов и алкилароматических углеводородов
В катализатах ароматизации н-олефинов C>6 обнаруживаются небольшие количества более ненасыщенных олефинов с тем же числом атомов углерода.
Кривые выходов диенов и ароматических углеводородов в зависимости от времени контакта и других факторов определяющих степень превращения моноолефинов (температура активность катализатора) на различных катализаторах (алюмохромовокалиевом никель платина) носят консекутивный характер. Таким образом можно полагать что дегидроциклизация гексенов и гептенов протекает через промежуточное образование диенов.
Закономерности в выходах продуктов ароматизации гексадиенов и гептадиенов на алюмохромовокалиевом и платиновом катализаторах говорят о том что наряду с образованием промежуточных триенов значительную роль играет непосредственное превращение диенов в ароматический углеводород. При дегидроциклизации триенов С6 и С7 образуются промежуточные циклогексадиены.
Выходы толуола из 1-гептена 13-гептадиена и гептатриена на алюмохромовокалиевом катализаторе при 450° относятся как 1 : 5 : 150 [13] что согласуется с приведенными данными о консекутивном механизме дегидроциклизации олефинов.
Основными продуктами дегидрирования диэтилбензола является этилвинилбензол и дивинилбензол. Закономерности определяющие выходы этих продуктов говорят о том что этилвинилбензол является промежуточным продуктом при образовании дивинилбензола. Реакция дегидрирования диэтилбензола описывается кинетическим уравнением для гетерогенно-каталитической консекутивной реакции в потоке. На смешанном окисном катализаторе при 520—560° и разбавлении диэтил-бензол: вода = 1 : 3 [13] константа скорости стадии дегидрирования этилви-нилбензола в дивинилбензол примерно в 2 раза больше чем стадии дегидрирования диэтилбензола в этилвинилбензол.
1.2. Механизм каталитического денидрирования.
1.2.1. Некоторые элементарные стадии и природа промежуточных
поверхностных соединений.
Если природу объемных промежуточных продуктов дегидрирования можно считать в большинстве случаев установленной то для суждения о поверхностных промежуточных соединениях имеется еще мало данных.
Схема дегидрирования может быть представлена как последовательность объемных и поверхностных промежуточных соединений. Например для ароматизации олефина или нафтена:
(в скобках – поверхностные соединения). Каждая из стадий схемы может в свою очередь состоять из двух или большего числа ступеней. И наоборот не все указанные стадии являются обязательными и при определенных условиях возможно одновременное отщепление более двух атомов водорода от дегидрируемой молекулы или превращение на некоторых стадиях может протекать ступенчато но без выделения в газовую фазу промежуточных соединений.
С увеличением реакционной способности дегидрируемых углеводородов наряду с поверхностными превращениями существенное значение приобретают гомогенные стадии. Так известно что гексатриены уже при 360° термически циклизуются в циклогексадиен а при 300° цикло-гексадиен превращается в бензол [14].
Согласно мультиплетной теории промежуточное поверхностное соединение образуется через двухточечную (дублетную) или шеститочечную (секстетную) адсорбцию дегидрируемой молекулы. При этом должны соблюдаться структурное и энергетическое соответствия между катализатором и реагирующей молекулой.
По дублетному механизму согласно Баландину происходят такие реакции как дегидрирование парафинов до олефинов олефинов до ди-олефинов алкилароматических до алкенилароматических т. е. реакции сопровождающиеся разрывом двух связей С — Н. По секстетному механизму протекает реакция непосредственного дегидрирования циклогексана в бензол сопровождающаяся разрывом шести связей С — Н. С5-Де-гидроциклизация парафинов в нафтены согласно Либерману" в отличие от остальных реакций дегидрирования протекает по секстетно-дублетному механизму: дублетной реакции предшествует секстетный способ адсорбции.
Некоторые сведения о природе поверхностных промежуточных соединений углеводородов были получены в последние годы путем изучения хемосорбции углеводородов на катализаторах методами ИК.- ЭПР-спек-троскопии и др.
По современным представлениям возможны следующие типы адсорбции олефина на металле [15]:
-диадсорбированный :
ассоциативно -адсорбированный:
и диссоциативно адсорбированный олефин образующий соединения -аллильного типа:
Представление об образовании промежуточного соединения через одноточечную адсорбцию не предполагает такой существенной роли геометрического фактора как это имеет место в мультиплетной теории.
При обработке водородом адсорбированного олефина происходят изменения в ИК-спектре которые указывают на образование поверхностных алкильных радикалов:
Адсорбированный алкильный радикал очевидно связан с поверхностью одной -связью.
Образование устойчивой частично гидрированной формы наблюдается также при хемосорбции разветвленных циклических углеводородов на никеле например:
Наоборот в испытанных условиях (комнатная температура остаточное давление 10-5 мм) при гидрировании адсорбированного бензола образуется циклогексан легко десорбирующийся с поверхности. Это по мнению авторов объясняется тем что при адсорбции незамещенного шестичленного циклического углеводорода последний связан с металлом -связыо менее прочной чем -связь.
В условиях более близких к реальным условиям дегидрирования (температура до 200°) при адсорбции циклогексана имеет место образование поверхностного циклогексила. Об этом говорят данные по масс-спектроскопии ионов десорбирующихся с платины под действием импульса поля. Путем изучения спектров ЭПР на поверхности никеля установлено также наличие поверхностного соединения с более высоким содержанием углерода которое как предполагают является промежуточным продуктом коксообразования.
При покрытии около 10% поверхности никеля циклогексан оказывает ускоряющее влияние на орто-пара-конверсию водорода причем каталитическое действие возрастает с температурой предварительной адсорбции углеводорода. Ускорение реакции орто-пара-конверсии водорода связано очевидно с радикалоподобной природой некоторых поверхностных соединений — продуктов частичной диссоциации молекулы углеводорода.
1.2.3. Лимитирующие стадии и кинетические уравнения.
Имеются данные в пользу того что наиболее медленной стадией дегидрирования различных углеводородов является химическое превращение.
Скорость дейтерообмена циклогексена а следовательно и его адсорбции и десорбции на РdАl2О3 и RеАl2О3 значительно больше чем дегидрирования [16]. Такой же вывод можно сделать и о скорости адсорбции и десорбции водорода: пара-орто-конверсия водорода на Ni — ZnО протекает значительно быстрее дегидрирования циклогексана. Расчет стехиометрического числа лимитирующей стадии дегидрирования н-бутана на алюмохромовом катализаторе дает величину близкую к единице [17].
В предположении что скорость мономолекулярной стадии дегидрирования на квазиоднородной поверхности является лимитирующей и адсорбция реагентов описывается изотермой Лэнгмюра для протекания процесса вдали от равновесия были выведены кинетические уравнения вида:
гдеbi — адсорбционные коэффициенты реагентов.
Уравнение в зависимости от относительных величин адсорбционных коэффициентов и концентрационных соотношений реагентов дает эффективные порядки от О до 1 по исходному углеводороду и от — 1 до 0 по продуктам что согласуется с опытом.
Такое толкование кинетических коэффициентов уравнений получило широкое признание. Было проведено довольно много работ по определению адсорбционных коэффициентов реагентов на различных катализаторах в том числе катализаторах дегидрирования. Кинетические адсорбционные коэффициенты возрастают в ряду парафины нафтены ароматические олефины диолефины и сравнительно мало различаются на таких катализаторах как алюмохромовый алюмомолибденовый никель на Аl2О3.
Описанная трактовка кинетических коэффициентов в ряде случаев сталкивается с противоречиями вследствие чего физический смысл их все еще по-видимому остается спорным.
Так согласно величинам относительных адсорбционных коэффициентов дегидрирование парафинов тормозится продуктами — олефинами. Однако эти данные не согласуются с результатами непосредственного измерения адсорбции. Так хемосорбция изопентана оказывается больше чем изоамилена [144]. Представления о сильной адсорбции олефинов не .согласуются также например с кинетическими данными по дегидроцик-лизации. Консекутивное уравнение для дегидроциклизации н-парафинов оправдывается лишь в форме отвечающей сильной адсорбции продукта— ароматического углеводорода но не олефина. В то же время по другим данным кинетические адсорбционные коэффициенты ароматических углеводородов меньше чем олефинов.
В позднее опубликованной работе хроматографическим методом было показано что адсорбция углеводородов — парафинов и олефинов — на алюмохромокалиевом катализаторе в условиях дегидрирования меньше чем адсорбция водорода. Эти результаты дают возможность объяснить литературные данные по торможению дегидрирования парафинов олефинами в рамках механизма торможения реакции водородомИ5. К сказанному можно добавить что иногда при обработке экспериментальных данных по уравнениям типа (2) получаются величины адсорбционных коэффициентов Ь^0 что не согласуется с допущениями принятыми при выводе кинетического уравнения которое в таком случае следует считать полуэмпирическим или оно должно быть выведено из других предпосылок. Действительно положение о том что скорость химического превращения является лимитирующей вряд ли можно считать универсальным так как скорости отдельных стадий могут сильно варьировать в зависимости от реагента и состояния поверхности катализатора.
Кинетические уравнения аналогичные уравнению (2) или его частным формам но с иным физическим смыслом постоянных коэффициентов могут быть выведены также из предпосылок что лимитирующими стадиями являются хемосорбция исходного углеводорода (дегидрирование циклогексана на алюмохромовом катализаторе) или десорбция продуктов (дегидрирование метилциклогексана на Рt— Аl2О3).
В обычно применяемых условиях дегидрирования углеводородов по-видимому значительное влияние оказывают процессы переноса и при достаточно высокой температуре и малых размерах пор катализатора лимитирующей стадией реакции может стать диффузия реагентов.
Исследовалось влияние пористой структуры алюмо-хромового катализатора на превращение п-гексапа. Изменение размера пор достигалось методом замены интермицеллярной жидкости. При температуре выше 470° и преобладающем радиусе пор образцов меньше 40(размер зерен 2—5 мм) [17] наблюдалась зависимость скорости реакции от размера пор т. е. влияние на скорость реакции процессов переноса. Вместе с тем экспериментальные данные достаточно удовлетворительно описываются кинетическим уравнением выведенным при допущении отсутствия диффузионного торможения.
Диффузионное торможение отмечено также другими авторами: дегидрирование н-бутана и дегидроциклизация н-гептана на алюмо-хромовых катализаторах дегидрирование циклогексана на платине нанесенной на окиси алюминия.
При совместном протекании дегидрирования и дейтерообмена циклогексана на Ni—ZпО-катализаторе с повышением температуры от 201 до 298° степень обмена проходит через максимум в то время как дегидрирование возрастает.
Согласно предлагаемой авторами схеме:
реакция Н — D-обмена циклогексана протекает через промежуточное поверхностное соединение С6Н*адс.-r(адс) а дегидрирование циклогексана кроме того — через второе промежуточное поверхностное соединение С6Н*12-т(адс). Стадии 1 3 4 и 5 а также адсорбции и десорбции водорода быстрые стадия (2) превращения одного промежуточного поверхностного соединения в другое является медленной определяющей скорость-Максимум скорости изотопного обмена объясняется влиянием одновременно лротекающего дегидрирования на концентрацию С6Н*адс.-r(адс). Реакции обмена не требуют медленных стадий (2) или (2') и поэтому идут быстро уже при низких температурах. По мере увеличения температуры скорость реакции дегидрирования начинает резко возрастать что ведет к уменьшению степени обмена. В согласии со схемой при введении бензола в систему скорость обмена уменьшается а при добавлении циклогексена существенно не изменяется.
В соответствии сданными соединения С6Н*адс.-r(адс) могут быть диссоциативно адсорбированным циклогексеном связанным двумя -связями а С6Н*12-т(адс). —-комплекс или ряд быстро превращающихся -комплексов. Первое поверхностное соединение может соответствовать реберной (дублетный механизм) а второе — плоскостной (секстетный механизм) ориентации циклогексана на поверхности [18].
1.3. Разновидности дегидрирующего действия катализаторов.
Катализаторы дегидрирования весьма многочисленны и разнообразны по своему химическому составу. Так еще по сводке из книги Плата 31 количество элементов упоминаемых в качестве активных компонентов катализаторов ароматизации парафинов составляло 51 и включало элементы почти всех групп периодической системы а главным образом IV—VI групп. Число известных катализаторов и способов их приготовления непрерывно пополняется.
Один и тот же катализатор если он достаточно активен способен к дегидрированию углеводородов различных гомологических рядов и строения. Так на алюмохромокалиевых катализаторах были получены достаточно высокие выходы продуктов дегидрирования низших парафинов Сз—Сз и ароматизации парафинов Се—Су циклогексана дегидрирования этилбензола олефинов разветвленных парафинов пятичлен-ных нафтенов алкилгидроароматических и других углеводородов[19].
1.3.4. Дегидрирование углеводородов содержащих и не содержащих
Из соотношения продуктов превращения циклогексана в бензол и ме-тилциклопентан и метилциклопентана в бензол и циклогексан Гензель и сотр.186 сделали вывод что при действии сернистых соединений утрачивается активность фторированного алюмоплатинового катализатора по отношению к стадии превращения циклогексена в бензол но не циклогексана в циклогексен и следовательно что указанные реакции протекают на разных активных центрах. Подразделение активных центров катализаторов на такие которые дегидрируют парафины и олефины принимает Пайнс а также некоторые авторы более ранних работ.
Однако при отравлении Рt—F—Аl203-катализатора тиофеном наблюдается более резкое уменьшение выходов бензола при дегидрировании циклогексана чем при дегидрировании циклогексена что не согласуется с данными .
К выводу о том что для разграничения активных центров дегидрирования парафинов и олефинов нет достаточных оснований приходим и при анализе экспериментального материала по влиянию химического состава на активность катализатора. Как правило все активные катализаторы дегидрирования парафинов оказываются активными и в дегидрировании олефинов. О том что это так свидетельствуют хотя бы данные о промежуточном образовании олефинов при ароматизации парафинов которое в противном случае не могло бы иметь места.
Наблюдается параллелизм с одной стороны в относительной реакционной способности насыщенных и ненасыщенных углеводородов на катализаторах различной природы и с другой стороны— в соотношении активностей различных катализаторов по отношению к дегидрированию указанных углеводородов. Так реакционная способность углеводородов возрастает с увеличением ненасыщенности на алюмохромовом алюмо-молибденовом катализаторах платине никеле и др. (см. табл. 1 и 2). Различия в удельных активностях отдельных металлов по отношению к реакциям дегидрирования циклогексана циклогексена и циклогексадиена достигают нескольких порядков. Если пренебречь сравнительно небольшими изменениями (в 2—3 раза) то удельные активности металлов для дегидрирования всех трех углеводородов располагаются в ряд:
Pd Pt Rh Ir > Ni > Ag Cu Co Fe
Естественно представление об однотипности активных центров для дегидрирования насыщенных и ненасыщенных углеводородов не означает того что для обеих реакций оптимальными должны быть одни и те же катализаторы.
Индивидуальные особенности углеводородов могут проявляться в побочных реакциях и вторичных превращениях продуктов. Так например способность к закоксовыванию катализатора у бутадиена значительно больше чем у бутана или бутилена ш. Для уменьшения коксообразования процесс дегидрирования н-бутилена в дивинил проводят в присутствии водяного пара а пары воды отравляют алюмохромовые катализаторы. Поэтому для дегидрирования н-бутиленов применяют не алюмохромовый а другие катализаторы стойкие по отношению к воде например железохромокалиевый.
Разумеется могут иметь значение и другие факторы например соотношение скоростей отдельных элементарных стадий. Так если лимитирующей стадией дегидрирования менее реакционноспособного из двух сравниваемых углеводородов является химическое превращение то на скорость реакции дегидрирования более реакционноспособного углеводорода на том же катализаторе будут возможно оказывать влияние и такие факторы как скорость адсорбции или внутренней диффузии. Поэтому для обоих углеводородов оптимальные катализаторы должны быть разными[151].
1.3.5. С5-Дегидроциклизация
Не наблюдается параллелизма между активностью различных катализаторов по отношению к С5-дегидроциклизации парафинов и к другим реакциям дегидрирования углеводородов. Так активность платины на угле для С5-дегидроциклизации изооктана в 113-триметилцикло-пентан не зависит от изменения температуры формирования катализатора от —10 до 40° а при уменьшении содержания платины в катализаторе от 20 до 5% способность его к С5-дегидроциклизации резко падает [20]. Активность же платиноугольного катализатора к дегидрированию циклогексана в первом случае проходит через максимум а во втором остается практически без изменения.
Эти данные указывающие на то что С5-дегидроциклизация парафиновых углеводородов в нафтеновые протекает на иных активных центрах чем реакция дегидрирования циклогексана находятся в согласии с экспериментальным материалом по подбору катализатора. Известно что на многих активных катализаторах дегидрирования — металлах (палладий осмий и иридий на угле никель на угле и окиси алюминия и др.) и окислах — до сих пор неудалось осуществить реакцию С5-дегидроциклизации парафинов протекающую только на платине.
Сказанное по-видимому не относится к С5-дегидроциклизации оле-финов которая в противоположность парафинам протекает не только на платине по и на алюмохромовом катализаторе (например С5-дегид-роциклизация диметилпентадиена в диметилциклопентадиен).
1.4. Современное представление о природе активной поверхности
Катализаторов дегидрирования.
Окись хрома и некоторые окисные катализаторы
По современным представлениям адсорбированный углеводород на окислах металлов присоединяется к ионам металла а не кислорода16'202. Образование связи между адсорбированным углеводородом и ионом переходного металла происходит за счет незаполненных d-уровней металла или путем образования s — d-связи.
Некоторые авторы установили корреляцию между количеством Сr6+ содержащейся в алюмохромовом катализаторе и его дегидрирующей активностью и в связи с этим высказали предположение что носителем каталитической активности является содержащийся в катализаторе шестивалентный хром.
Это предположение однако недостаточно обосновано так как в условиях реакции восстановление Сr6+ и других возможных соединений с валентным состоянием хрома выше трех происходит быстро [21] а активность алюмохромового катализатора сохраняется продолжительное время. При регенерации алюмохромового катализатора в токе СО2 высшие окислы хрома не образуются а вместе с тем такие катализаторы не менее активны чем регенерированные воздухом.
Количество Сr6+ в катализаторе зависит от условий и продолжительности окисления и природы промотора. Корреляция между активностью и количеством Сr6+ в катализаторе наблюдавшаяся в некоторых случаях могла быть связана с тем что восстановление высших окислов хрома в условиях реакции все же не является достаточно полным и остающийся невосстановленным хром будучи составной частью например шпинели с алюминатом металла-добавки оказывает промотирующее действие.
Ван-Рейн и сотр.из измерений магнитных моментов и сигналов ЭПР алюмохромовых катализаторов подвергавшихся различной окислительно-восстановительной обработке сделали вывод что высшие окислы хрома восстанавливаются в токе сухого водорода т. е. в условиях благоприятствующих получению активного алюмохромового катализатора не только до трех- но и до двухвалентного хрома. Соотношение между 2- и 3-валентными окислами хрома определяется равновесием:
СrO+ Н20 = Сr203 + Н2 (3)
Дальнейшие экспериментальные подтверждения образования двухвалентного хрома при восстановлении алюмохромовых катализаторов были получены Рубинштейном и сотр.206. Так при обработке тщательно восстановленных алюмохромовых катализаторов водой наблюдается выделение водорода. При обработке Н2О катализатора восстановленного дейтерием в газе обнаружен только протий. Это значит что водород образуется при разложении воды ионами Сr2+ обладающими восстановительными свойствами а не выделяется в результате десорбци-онного вытеснения водой.
Вычисленное из объема выделившегося водорода количество Сr2+ приблизительно совпадает с количеством хемосорбированного на катализаторе углеводорода. Количество же содержащегося в катализаторе Сr3+ было примерно в 40 раз больше.
Однако СrСl2 значительно менее активен в реакции дегидроциклиза-ции чем СrСl3. Имеются и другие данные не согласующиеся с предположением о роли ионов Сr2+ как активных центров дегидрирования. Так по условиям равновесия реакции (3) Сr2+ не должен присутствовать в катализаторе при парциальном давлении паров воды в газе выше 1710-3 мм рт. ст. Вместе с тем при давлении паров воды в реагирующем газе 20 мм рт. ст. алюмохромовый катализатор сохраняет значительную активность [21]. Снижение же парциального давления паров воды в газе до 310-4 мм рт. ст. приводило к падению каталитической активности.
Особенно активной катионной структурой в реакциях с участием водорода на полупроводниках является d3. Такую электронную конфигурацию имеет ион хрома в Сr2О3. Согласно Казанскому и Швецу активными центрами дегидрирования являются координационно ненасыщенные ионы Сr3+.
В образцах содержащих адсорбированную воду все ионы Сг3+ находятся в октаэдрической конфигурации. При отщеплении одной молекулы воды координация понижается до квадратной пирамиды:
а отщепление следующих молекул воды может приводить к дальнейшему понижению координации. Для выяснения являются ли присутствующие на поверхности катализаторов десорбировавших воду при высокой температуре координационно ненасыщенные ионы Сr3+ активными центрами дегидрирования необходимы дальнейшие исследования.
Некоторые авторы высказывали предположение что активность алюмохромовых катализаторов обусловлена образованием специфической смешанной структуры между компонентами катализатора.
Крылова Козуненко и Кобозев211 наблюдали максимум содержания стирола в катализате дегидрирования этилбензола и парамагнитной восприимчивости при содержании хрома в катализаторе~2%. Максимум удельной восприимчивости при небольшом содержании хрома связан по-видимому с образованием 6-фазы Сr2О3. Что касается активности катализатора то следует иметь в виду что окись хрома достаточно активна сама по себе и смешанная алюмохромовая структура если бы она играла существенную роль в катализе должна была бы быть весьма активной.
Однако испытанные в работе образцы были мало активными (содержание стирола в катализате было лишь в 2—25 раза больше чем при термическом превращении) и по-видимому обладали значительной кислотностью. Поэтому наблюдавшееся при увеличении содержания хрома свыше 2% снижение выходов стирола могло быть связано с образованием побочных продуктов. Действительно при дегидрировании менее реакционноспособных углеводородов — парафинов — не наблюдалось максимума активности при столь небольших добавках хрома как 2% [21].
Буянов и сотр. связывают активность железохромовоцинковых катализаторов в реакции дегидрирования бутиленов с присутствием в нем хромовой шпинели. Однако значительной дегидрирующей активностью обладают окись железа или окись цинка не содержащие хрома не говоря уже о самой окиси хрома. Поэтому в железохромоцинковых катализаторах активными центрами могут быть по-видимому ионы любого металла входящего в состав катализатора. Образование же твердых растворов и смешанных структур скорее способствует стабильности катализатора препятствуя рекристаллизации и нежелательным химическим превращениям катализатора что может быть особенно важно при дегидрировании бутилена и других олефинов ввиду жесткости условий эксплуатации этих катализаторов.
Имеющиеся данные не дают также оснований полагать что дегидрирующая способность хромовомагниевых или хромосиликагелевых катализаторов обусловлена образованием активных смешанных структур Остается неясной природа активирующего действия малых количеств воды. Полностью обезвоженные катализаторы дегидрирования неактивны. При увеличении содержания воды в сырье активность алюмохромовых катализаторов проходит через максимум.
Можно предположить что вода входит в состав активных центров катализатора оказывая промотирующее действие. Обратимое отравление алюмохромового катализатора более значительными ее количествами может быть объяснено блокированием активных центров. Действительно предварительная адсорбция воды подавляет хемосорбцию н-гексана на алюмохромовом катализаторе. В этом случае происходит только физическая адсорбция н-гексана которая не сопровождается дегидроциклизацией [21].
Носителями каталитической активности в реакциях дегидрирования могут быть атомы металла (в металлических) атомы или ионы металла (в нанесенных металлических) и ионы металла в окисных катализаторах. В состав активных центров входят также по-видимому хемосорби-рованные атомы или молекулы (водород в случае металлического вода в случае окиснохромового катализатора). Дегидрируемая молекула может быть связана с поверхностью одно- двух- или многоточечной адсорбцией с различными типами химической связи (а-связь или разновидности координационных связей).
Тем не менее наблюдается лишь небольшое число разновидностей дегидрирующего действия катализаторов на углеводороды. Имеется достаточно оснований полагать что дегидрирование и ароматизация парафинов протекают на одних и тех же активных центрах и по-видимому то же можно сказать относительно парафинов и олефинов а также нафтенов (кроме случая непосредственного превращения шестичленных нафтенов в ароматические углеводороды).
Для всех этих случаев при которых проявляется аналогия в действии катализаторов различной природы и превращении углеводородов различных гомологических рядов и строения следует предпочесть модель промежуточного соединения с одно- или двух- но не с многоточечной адсорбцией а из существующих гипотез о структуре активных центров те которые связывают активность с самим веществом катализатора п его дисперсностью а не с теми или иными соединениями его с носителями. По-видимому активный катализатор как например платина или окись хрома сохраняет значительную дегидрирующую способность на любом носителе различной природы способном обеспечить стабильность его дисперсности.
Наоборот более специфические реакции дегидрирования (С5-дегид-роциклизация парафинов дегидрирование нафтенов без промежуточного образования циклоолефинов) могут быть объяснены действием многоточечных активных центров или различием типа связи адсорбированной молекулы с поверхностью катализатора по сравнению с другими реакциями дегидрирования [21].
2. Методы получения изопрена.
2.1. Получение изопрена дегидрированием изопентана.
Метод дегидрирования изопентана .представляет большой интерес поскольку процесс дегидрирования н-бутана освоен в крупном промышленном масштабе и кроме того имеются довольно большие ресурсы пентанов от нефтедобычи.
Так же как и в случае бутана процесс дегидрирования изопентана может быть осуществлен по одно- и двухетадийной схеме.
2.1.1. Двухстадийное дегидрирование изопентана
Метод двухстадийного дегидрирования изопентана был разработан НИИМСК совместно с Гипрокаучуком и ИНХП АН АзССР и освоен в промышленном масштабе.
Первая стадия – дегидрирование изопентана в изоамилены – проводится на алюмохромовом катализаторе аналогичном применяемому для дегидрирования н-бутана [19].
В промышленных условиях процесс осуществляется непрерывным способом в кипящем слое катализатора и по технологическому и аппаратурному оформлению принципиально не отличается процесса получения бутадиена из бутана. Процесс проводится при 550—560 °С давлении над кипящим слоем катализатора 013—-016 МПа скорости подачи сырья 120 ч-1 и плотности кипящего слоя 750 кгм3.При таком режиме выход изоамиленов и изопрена составляет в сумме 28—32% (масс.) на пропущенный и 66—71% (масс.) на разженный изопентан.
Как и при дегидрировании бутана большое значение имеет регенерации и подготовка катализатора. Выжигание кокса осуществляется горячим воздухом при 630 °С. Активность регенерированного окисленного катализатора восстанавливается обработкой углеводородным газом при 560—620 °С и объемной скорости углеводородного газа 120—200 нм3(м3 катализатора-ч) примерно в течение 1—2 мин.
После охлаждения и компримирования контактный газ поступает в абсорбер орошаемый тяжелой углеводородной фракцией для отделения метановодородной фракции и затем на трехколонную ректификационную установку где выделяется фракция С5.
По сравнению с получением бутадиена из бутана получение изопрена осложняется образованием большего числа изомеров. Фракция С5 дегидрирования изопентана содержит непрореагировавший изопентан .и три изоамилена: 2-метилбутен-1 (СН2=ССН3—СН2— СН3) с т. кип. 3105 °С 2-метилбутен-2 (СН3—ССН3=СН—СН3) с т. кип. 3848 °С и З-метилбутен-1 (СН2=СН—СНСНз—СН3) с т. кип. 20 °С. Соотношение изоамиленов образующихся в процессе дегидрирования составляет примерно 13-16:55-60:100 и мало зависит от условий проведения процесса.
Вследствие протекания в процессе дегидрирования реакций изомеризации а также из-за наличия в техническом изопентане примесей н-пентана контактный газ содержит три н-амилена — пентен-1 цис-пентен-2 и транс-пентен-2 а также цис- и транс-пиперилен (изопрен циклопентадиен и некоторые другие углеводороды). Выделение изоамиленов из этой смеси довольно сложно. При обычной ректификации требуется применение больших флегмовых чисел и высокий расход пара поэтому процесс нерентабелен [21].
В отечественной промышленной практике для разделения изопентан-изоамиленовых смесей применяется экстрактивная ректификация с диметилформамидом которая по технологическому и аппаратурному оформлению аналогична описанной для выделения бутадиена из фракций С4.
Фракция С5 первой стадии дегидрирования смешивается с ре-цикловыми изоамиленами установки разделения изопрен-изоамиленовых смесей второй стадии что позволяет предотвращать накопление изопентана на второй стадии. Смесь подогревается в теплообменниках горячим диметилформамидом и направляется на экстрактивную ректификацию с безводным диметилформамидом. Содержание воды в диметилформамиде не должно превышать 05%.
Установка экстрактивной ректификации состоит из двух колонн. С верха первой колонны отбирается изопентан содержащий не более 5% изоамиленов н-амиленов и изопрена который возвращается на первую стадию дегидрирования.
Насыщенный диметилформамид содержащий до 6% углеводородов С5 отбирается из куба второй колонны и направляется на десорбцию. Изоамиленовая фракция содержащая до 5% пентанов отводится сверху десорбционной колонны. После конденсации и охлаждения фракция направляется на вторую стадию дегидрирования. Диметилформамид отбирается из куба десорбционной колонны охлаждается в водяном холодильнике и направляется на орошение второй колонны экстрактивной ректификации.
Примерно 3% от циркулирующего диметилформамида выводится на двухколонную установку регенерации где на первой колонне работающей при атмосферном давлении паровым конденсатом отгоняются легкие смолы а на второй — вакуумной колонне отбираются тяжелые смолы [12 22].
Метод синтеза изопрена двухстадийным дегидрированием изопентана имеет те же недостатки которые отмечались при описании процесса получения бутадиена. Относительно высок расход сырья который составляет около 20 т изопентана на 1 т изопрена.
При организации на одном предприятии (производства изопрена двумя методами: дегидрированием изопентана и из изобутилена и формальдегида) — технико-экономические показатели можно улучшить использованием в диоксановом процессе бутилен-изобутиленовой фракции получаемой в качестве побочного продукта при дегидрировании изопентана.
Дальнейшее улучшение технико-экономических показателей процесса очевидно возможно за счет применения (более эффективных катализаторов дегидрирования и более эффективных экстр-агентов разделения углеводородов Сб [23].
2.1.2. Одностадийное дегидрирование изопентана
Так же как и при получении бутадиена из бутана процесс одностадийного дегидрирования изопентана имеет ряд преимуществ по сравнению с двухстадийным. Прежде всего это более простая технологическая схема вследствие исключения стадии разделения изопентан-изоамиленовых смесей. Однако он уступает двухстадийному по выходу целевого продукта.
Процесс одностадийного дегидрирования изопентана разработан в опытно-промышленном масштабе. Дегидрирование изопентана проводится при 635—625 °С и остаточном давлении 199— 266 кПа. Скорость подачи сырья составляет 15—35 объема на 1 объем катализатора. На контактирование подается смесь перегретых паров изопентана и рецикловой изопентан-изоамиленовой фракции.
Контактный газ охлаждается в колонне циркулирующим маслом хомпримируется и .подается на разделение. Установка разделения состоит из абсорбера десорбера и дебутаниаатора. Фракция С5 разделяется ректификацией на возвратную изопентан-изоамиленовую фракцию пиперилен и изопрен концентрацией 995%. Основной примесью в изопрене являются изоамилены.
Из 1 т прореагировавшего изопентана получается 497 кг изопрена 73 кг пиперилеиа 141 кг фракции С4 41 кг ^водорода. Остальной изопентан конвертируется в метан и углеводороды С2 и С3.
Ниже приведены основные расходные коэффициенты сырья и энергетических средств на 1 т изопрена 1в процессе одностадийного дегидрирования изопентана под вакуумом (по данным фирмы «Ноийгу»):
Изопентан т 201 Вода м3 59
Электроэнергия кВт-ч 1492 Топливо 103 кДж 5011
При применении в качестве сырья фракции С5 каталитического крекинга выход изопрена может быть повышен с 50 до 58%.
Проверен также «а опытной установке метод совместного получения бутадиена и изопрена. В этом случае на дегидрирование подается смесь состоящая из 25% изопентана и 75% н-бутана. Выход изопрена на разложенный изопентан повышается до 60— 62%.
Разрабатывается метод одностадийного дегидрирования изопентана под вакуумом на полузаводской установке в присутствии отечественного катализатора ДВ-ЗМ применяемого для дегидрирования бутана. Ведутся исследования по созданию нового более эффективного катализатора применительно к специфике процесса дегидрирования изопентана [8 24].
Процесс одностадийного дегидрирования изопентана пока не внедрен в промышленность.
2.1.3. Окислительное дегидрирование изопентана
Окислительному дегидрированию изопентана уделяется в последние годы такое же большое внимание как и окислительному дегидрированию бутана. Принципиально исследования в этом направлении не отличаются от аналогичных исследовании по деги рированию бутана. Наибольшее число работ посвящено иодно? дегидрированию при котором достигаются высокие выходы. I-опытных установках опробовано уже несколько вариантов проце са — в гомогенных условиях на кварцевой насадке в адиабатич оком полочном реакторе в восходящем потоке твердого акцепте] йодистого водорода на стационарном слое твердого акцептор с использованием комбинации кварцевой насадки и акцепторов.
Техническое осуществление процесса сопряжено с теми я трудностями которые были описаны .выше для процесса иодно дегидрирования бутана. Кроме того осложняется схема выдел ния и очистки изопрена так как фракция С5 выделенная из ко тактного газа содержит некоторое количество иодорганичесю продуктов которые с углеводородами С5 образуют азеотропш смеси.
Американской фирмой «Рего-Тех» предложен метод хлорно дегидрирования изопентана при 450—650 °С в паровой фазе при мольном соотношении изопентан : кислород : хлор = 1 : 025 :001 -т-05 в присутствии катализатора на основе солей оксидов и; гидрокеидов марганца. Выход изопрена в этом процессе не пр вышает 20% на пропущенный изопентан что значительно ни ж чем в процессе йодного дегидрирования.
Для проведения окислительного дегидрирования изопентаа без применения галогенов предложены катализаторы состоят) из омеси молибдата свинца и вольфрамата алюминия и (или) к бальта а также солей цинка хрома магния лантана «ли их см сей [25].
2.1.4. Некоторые новые направления синтеза изопрена из изопентана
Одним из перспективных направлений синтеза изопрена из изопентана является одновременное получение наряду с изопрено других ценных нефтехимических продуктов например окиси проп! лена циклогексаяонокоим^а метакриловой кислоты с использов; нием реакции эпоксидирования. Так разрабатывается метод одш временного получения из изопентана изопрена и окиси пропилен На первой стадии изопентан окисляется кислородом воздуха ; гидроперекиси трег-амила:
Инициаторами реакции служат гидроперекиси например гидроперекись грет-бутила. Процесс проводится при 140 °С и 35 МЛ а.
В этом процессе наряду с гидроперекисью грет-амила образуются третичный амиловый спирт этиловый спирт уксусная шсло-
а ацетон кетоны и некоторые другие. Конверсия составляет 21: при селективности около 50%.
На второй стадии пропилен эпоксидируется концентрированн гидроперекисью грег-амила:
При этом образуются окись пропилена и грег-амиловый спирт. Катализатором процесса служит нафтенат молибдена. Реакция проводится при 45—100 °С и давлении 2 МПа. Наряду .с трет-аммло-вым спиртом образуется метилизопропилкетон который гидрируется в присутствии катализатора — хромата меди — в трет-ами-ловый спирт что повышает общий выход целевого продукта.
На третьей стадии грег-амиловый спирт дегидратируется в изо-амилены:
Процесс дегидратации осуществляется в присутствии катализатора— активного оксида алюминия. Конверсия составляет 95% при селективности 98%. Полученные изоамилены могут подвергаться дегидрированию обычными методами.
Другой процесс получения изопрена из изоамилена с использованием реакции эпоксидироваяия заключается в окислении изо-амиленов в окись изоамиленов и непредельный спирт и их превращении в изопрен.
Окисление проводится в присутствии катализатора при 90 °С и давлении 2 МПа. Превращение окиси изоамиленов и непредельного спирта в изопрен проводится на катализаторе при 400 °С и атмосферном давлении. В качестве побочных продуктов образуются 'метилизопровилкетоя диметилпропаналь изоамилены и изо-пентан.
По одному из вариантов процесса гидроперекись грег-амила используется для эпоксидирования Циклогексиламина или метак-ролеина. При этом вместо окиси пропилена получается соответственно циклогексаноноксим или метакриловая .кислота.
Было предложено использовать вместо изопентана более доступное сырье — н-гексан который предварительно изомеризуют над катализатором — никелем на алюмосиликате при 370 °С и 25 МПа в присутствии водорода. Продукты реакции содержат около 60% смеси 2-метил- и 3-метилпентана. реакционную смесь окисляют кислородом воздуха при 130 °С и 17—18 МПа в лр.и-сутствии инициатора — ди-грег-буталперекиеи. Затем смесью образующихся гидроперекисей эпоксидируют пропилен. При этом получаются окись пропилена и изогексанолы — 2-метилпентанол-2 и З-метилпентанол-3. Изогекеанолы подвергают крекингу в присутствии инициатора — НВг и водяного пара при 675 °С. Выход изопрена составляет 40—42% при селективности 60—61%.
Большой интерес представляет направленный синтез изопрена эпоксидированием изопентана. Процесс включает четыре стадии.
На первой стадии изопентан окисляется кислородом воздуха по приведенной выше схеме. На второй стадии полученной гидроперекисью трет-амила эпоксидируют триметилэтилен являющийся промежуточным продуктом данного синтеза:
Реакция проводится при 100 °С в присутствии катализатора — молибденовой кислоты.
На третьей стадии окись азоамилена изомеризуется в изоами-леновые спирты с одновременной дегидратацией полученных спиртов в изопрен:
Процесс осуществляется на .неподвижном катализаторе пр.и 300 "С с разбавлением азотом. В качестве катализатора применяется оксид тория.
На четвертой стадии происходит превращение образующегося на второй стадии грег-амилового спирта и продуктов его побочных реакций в триметилзтилен. Процесс осуществляется на катализаторе— оксиде алюминия или оксиде вольфрама на .активном оксиде алюминия при 170—200 °С. Реакция проходит с практически полным превращением. Полученный изоамилен направляется на вторую стадию.
Метод получения изопрена эпоксидированием .изопентана характеризуется высокой селективностью на всех стадиях. На стадии получения изопрена не образуется вредных примесей ацетиленовых и диеновых углеводородов. По предварительным данным энергетические расходные коэффициенты существенно :ниже чем при методе дегидрирования. Аппаратурное оформление довольно простое.
К недостаткам процесса следует отнести многостадийность низкую скорость реакции окисления изопентана кислородом воздуха вследствие чего в системе должно находиться одновременно большое количество изопентэна а также образование значительных количеств побочных продуктов для правильного использования которых необходимо сооружение специальных установок разделения и очистки [8 10 18 26].
Интересный принципиально новый метод дегидрирования изопентана разрабатывается ИНХС АН СССР совместно со Стерлитамакским опытным заводом СКИ.
Сущность метода заключается в использовании в качестве катализаторов сплавов палладия в виде очень тонких трубок или фольги. Такой мембранный катализатор обладает проницаемостью для водорода благодаря чему образующийся в процессе дегидрирования водород диффундируя через металл выводится из системы смещая равновесие. Использование мембранного катализатора позволяет одновременно проводить две реакции —дегидрирование и гидрирование с использованием активного атомарного водорода.
На пилотной установке с применением катализатора из сплава палладия с никелем при 558 °С выход изопрена на пропущенный изопентан составляет 186% и изоамиленов—105%. На катализаторе из сплава палладия с родием при 588 °С выход изопрена за проход составляет 239% а сумма изопрена и изоамиленов — около 30%.
Этот процесс запатентован во многих странах. Однако из-за сложности конструирования .аппаратуры в настоящее время трудно оценить перспективы промышленной реализации процесса [8].
2.2. Получение изопрена из изоамиленов.
Так же как в случае дегидрирования бутиленов в бутадиен дегидрирование изоамиленов в изопрен может быть самостоятельным процессом получения изопрена при наличии источников изоамиленов или служить второй стадией двухстадийного метода дегидрирования изопентана.
Дегидрирование изоамиленов может проводиться при разбавлении водяным паром в отсутствие кислорода или как окислительное дегидрирование.
Дегидрирование изоамиленов является первым промышленным методом получения изопрена реализованным в крупных масштабах в США и Голландии. В качестве сырья использовалась фракция С5 получаемая главным образом с установок каталитического крекинга. Из фракции С5 изоамилены извлекаются 65%-ной серной кислотой и затем экстрагируются из насыщенных сернокислых растворов предельными углеводородами.
Следует указать что несмотря на определенные достоинства метода синтеза изопрена дегидрированием изоамиленов он по-видимому не получит дальнейшего развития вследствие ограниченности ресурсов изоамиленов [12].
2.2.1. Дегидрирование изоамиленов при разбавлении паром.
Дегидрирование изоамиленов в изопрен может проводиться на тех же катализаторах и с применением такого же технологического и аппаратурного оформления как при получении бутадиена дегидрированием бутиленов.
Процесс дегидрирования изоамиленов сопровождается многочисленными побочными реакциями в том числе обусловленными частичной изомеризацией изоамиленов в н-амилены и образованием продуктов их дегидрирования.
Процесс проводят в присутствии катализаторов на основе оксида железа и кальций-никель-фосфатных катализаторов [27]. Перегретые пары смеси прямой и возвратной изоамиленовых фракций с температурой до 530 °С смешиваются в соотношении 1 : 20 с перегретым до 750—780 °С водяным паром и поочередно подаются то в один то в другой реактор дегидрирования. По окончании цикла дегидрирования продолжительность которого зависит от применяемого катализатора реактор продувается и переключается на регенерацию катализатора осуществляемую нагретым воздухом.
Выход изопрена составляет 33% при селективности 80%. Некоторое повышение выхода изопрена может быть достигнуто путем сокращения времени пребывания сырья над катализатором и применения быстрого охлаждения контактных газов в нижней части реактора для подавления побочных реакций крекинга и изомеризации.
Проводятся исследования по созданию новых катализаторов более специфичных для процесса дегидрирования изоамиленов вместо используемых в промышленности катализаторов разработанных для дегидрирования н-бутиленов.
Хорошие результаты получаны при испытании нового катализатора марки КИ. По предварительным данным применение этого катализатора позволяет повысить активность и селективность на 15—20% [28].
2.2.2. Окислительное дегидрирование изоамиленов
При окислительном дегидрировании в результате смещения равновесия в сторону образования изопрена за счет связывания кислородом выделяющегося водорода увеличивается выход целевого продукта. Кроме того процесс можно проводить при температурах на 150—200 °С ниже применяемых при обычных методах дегидрирования. Это способствует подавлению побочных реакций и сокращению в несколько раз степени разбавления водяным паром. Кроме того при окислительном дегидрировании отпадает необходимость в периодической регенерации катализатора так как выжиг кокса происходит за счет присутствующего кислорода причем тепло выделяющееся при сгорании кокса в значительной степени или полностью компенсирует эндотермический эффект реакции дегидрирования.
Основными недостатками процесса окислительного дегидрирования являются потери сырья на горение которые составляют до 10% сырья вводимого в реакцию а также образование кислородсодержащих соединений усложняющих и удорожающих очистку изопрена.
Довольно перспективным является окислительное дегидрирование изоамиленов кислородом на гетерогенных катализаторах. В отличие от обычного дегидрирования окислительное дегидрирование изоамиленов протекает практически необратимо. Состав ка-1 тализаторов при этом принципиально не отличается от используемых при окислительном дегидрировании бутиленов.
Наилучшие результаты при синтезе изопрена получены в присутствии сурьмяно-урановых катализаторов. Селективность процесса достигает 90% при конверсии 70%.
Опытные работы по обычному дегидрированию в присутствии кислорода которое осуществляется в более жестких условиях « с большим разбавлением водяным паром по сравнению с окислительным дегидрированием показали что достигаемые выхода и селективность несколько ниже чем при окислительном дегидрировании. Достоинством процесса является отсутствие кислорода в контактном газе и кислородсодержащих соединений в катализаторе [82930].
Литвин О. Б. Соловьев К. С. Яковлев К. А. ЖВХО им. Д. И. Менделеева 1969 т. 14 № 3 с. 313—319.
Федоров В. С. «Каучук и резина» 1972 № 7 с. 1—3.
СЬет. МагЫ. Керой. 1974 v. 205 № 7 р. 18.
СЬет. Магке*. Керог! 1975 v. 208 № 24 р. 5.
КиЬЬ. 1псЦ 1975 v. 9 № 2 р. 68—71.
СЬет. Еп%. N6*5 1974 v. 54 № 16 р. 19.
Федоров В. С. «Каучук и резина» 1974 № 5 с. 1—5.
Огородников С. К. Идлис Г. С. Производство изопрена. Л. «Химия» 1973. 296 с.
СЬет. Есоп. Еп%. Кеу. 1971 v. 3 № 2 р. 35—40.
НуйгосагЬоп Ргосезз. 1972 v. 51 № 2 II р. 28—30.
ОН а. Саз. 1973 v. 71 № 9 р. 37.
Литвин О. Б. Соловьев К. С. Яковлев К. А. Современный промышленный синтез изопрена. М. ЦНИИТЭнефтехим 1968. 96 с.
СЬет. 1псЦ 1967 Ей. 19 № 100 8. 684.
Паушкин Я. М.. Легашин С. В. Хим. пром. 1970 № 8 с. 618— 619.
Та ка 81 К. Ре1го1. Ре^госЬет. Ыегп. 1971 v. 12 № 11 р 62—64 86
СЬет. Еп^. 1972 v. 79 № 3 р. 77.
«Сигать АзЬез! КипзЫоНе» 1972 ВЙ. 25 № 1 5 35
ОН а. Саз 3. 1972 v. 70 № 26 р. 66—67.
Соболев В. М. Щербакова Н. В. Шмарин В. С. ЖПХ 1963 т. 36 А1» 2 с. 428—430.
Михайлов Р. К. и др. Пром. сянт. каучука 1970 №'1 с. 1—2.
Щ е р б а к о в а Н. В. Баснер М. Б. С о б о л е в В. М. Хим. пром. 1965 № 7 с. 495—497.
Павлов С. Ю. и др. Пром. спит каучука 1969 № 2 с. 5—6.
Федоров В. С. Нефтеперерабатывающая и нефтехимическая промышленность СССР в девятой пятилетке. М. «Химия» 1976. 71 с.
Калмыкова Г. В. Баунов А. М. Литвин О. Б. Пром. линт каучука 1972 № 6 с. 20—22.
ОН а. Саз Шегп. 1971 v. 11 № 10 р. 35.
Л иакумович А. Г. Сусеков Л. В. Алекс.андров В. К. Пром. синт. каучука 1969 № 9—10 с. 1—3.
К о т е л ь н и к о в Г. Р. и др. Катализаторы дегидрирования низших парафиновых и олефиновых углеводородов. М. ЦНИИТЭнефтехим 1969. 59 с.
Кир н о с Я. Я. и др. Пром. синт. каучука 1970 № 1 с. 3—5.
Соркин Г. Я- Пер лин Л. Я. «Химия и технология топлив и масел» 1970 № 5 с. 15—17.
Г духов В. Н. Хим. пром. 1970 № 7 с. 70.
Дак Э. У. Экономические и технические перспективы изопреновых каучуков. Доклад на Международном симпозиуме по изопреновому каучуку. Москва 20—241Х 1972. М. ЦНИИТЭнефтехим 1972. 16 с.
Г а л а т а Л. А. и др. Пром. синт. каучука 1970 № 5 с. 1—3.
С а р а е в Б. А. Б о л о х о в а Л. А. Павлов С. Ю. Пром. синт. каучука 1972 № 8 с. 4—6.
Павлов С. Ю. и др. Хим. пром. 1970 № 6 с. 407—408.
ОН а. Сав 1. 1971 у. 69 № 11 р. 80; № 5 р. 40—41.
Фельдблюм В. Ш. О б ещ а лов а И. В. «Кинетика и катализ» 1970 т. И № 4 с. 898—900.
КиЬЬ. АУогИ 1973 у. 166 № 2 р. 37; № 6 р 39
ОН а. Саз Л. 1974 у. 74 № 3 р. 28.
Список использованной литературы 12.doc
К. Керби сб. Химия углеводородов нефти 1958 т.2стр. 189
Г. Стейнер сб. Катализ в нефтехимической и нефтеперабатывающей промышленности. Гостоптехизд 1959 стр.270.
Б.Н. Долгов Катализ в органической химии Ленинград 1959.
И.Я. Тюряев Физико-химические и технологические основы получения дивинила «Химия» 1966.
А.З. Шихмамедбекова Дегидрирование изопентанов в изопрен Азернешр. Баку 1963.
О.Д. Стерлигов Т.Г. Олферьева Н.Ф. Кононов Успехи химии 36 1200 1967
R. Pitkethely H. Steiner Trans. Faraday Soc. 35 979 1939
Р.Д. Оболенцев Ю.Н. Усов ЖОХ 21 1438 (1951)
И.И. Левицкий Изв. АН СССР ОХН 1959 425.
Ю.Н. Плотников Е.А. Тимофеева Н.И. Шуйкин Нефтехимия 4 225 1964
А.А. Баландин М.Б. Нейман и др. Изв. АН СССР ОХН 1957 157.
М.И. Розенгарт Е.С. Мортиков Б.А. Казанский. ДАН 166 619 1966.
А.Л. ЛИберман Кинетика и катализ 5 128 1964.
Д.Бонд П. Уэллс сб. Катализ. Физическая химия гетерогенного катализа. «Мир» М.1967 стр.351.
Г.В. Исангулянц М.А. Ряшенцев Ю.И. Дербенцев и др. Нефтехимия 5 501 1965.
Р. Аткинс Д. Хапел 4-й Международный конгресс по катализу М. 1968 Симп. Механизм икинетика сложных каталитических реакций препр. №4
А.А. Андреев Б.С. Гудков С.Л. Киперман Д.М. Шопов Кинетика и катализ 9 47 1968.
Б.А. Казанский О.Д. Стерлигов А.П. Беленкая сб. Научные основы подбора и производства катализаторов Новосибирск 1964 стр. 336.
А.Л. Либерман Б.А. Казанский К.Х. Шнабель Т.В. Васина Кинетика и катализ 2 446 1961
Ю.И. Печерская В.Б. Казанский Кинетика и катализ 6 357.
Литвин О.Б Основы технологии синтеза каучуков: Учебное пособие. –М.:1972.-528с.
Литвин О.Б. Соловьев К.С. Яковлев К.А. Современный промышленный синтез изопрена.-М.: Химия 1968-496 с.
Краткий справочник физических величин. Л.: Химия 1983-232 с.ил.
6. Автоматизация Каримов 1. doc.doc
Автоматизация и дистанционное управление технологическими процессами позволяет осуществить процессы протекающие при высоких температурах и давлениях агрессивных взрывоопасных и вредных для человека средах.
Автоматизация процессов обеспечивает наибольшую эффективность предприятий. В систему автоматического управления входят различные контрольно-измерительные приборы анализаторы качества и состава а также средства автоматики предназначенные для получения информации о режимных параметрах технологических процессов. Повышения уровня автоматизации процессов и производств осуществляется по следующим основным направлениям:
Управление из одной операторной несколькими однотипны! установками.
Повышение уровня автоматизации установок и произведет: путем применения наиболее совершенных систем автоматизации и достижений науки и техники в этой области.
Внедрение и расширение сети вычислительной техники широкое и всестороннее применение автоматизации труда и снижение себестоимости выпускаемой продукции.
2. Технологический контроль
2.1.Выбор и обоснование параметров контроля
а) Температура продуктов сгорания в топке печи является фактором воздействующим на материалы печи поэтому эта величина должна контролироваться и завышение ее выше 800°С недопустимо.
б) Температура дымовых газов в бороне печи № 103 контролируется т. е завышение ее выше 400°С недопустимо.
Температура в слое катализатора контролируется. Она может меняться от 580 до 600°С в зависимости от заданного режима работы. Контроль необходим для того чтобы оценить работоспособность катализатора во всем объеме катализатора.
Уровень углеводородов в емкости необходимо контролировать т. к при переполнении ее углеводороды могут быть выброшены в атмосферу. Кроме того предельный верхний уровень сигнализируется.
Кроме этого контролируется давление в испарителях поз.102 в реакторах №104 в котлах-утилизаторах №105 в трубопроводах после всех насосов в смесителях пара с кислородом в скрубберах поз.106 106а 110 и пр. Вся система от апп.102 до 105 рассчитана на внутреннее давление 6 кгсм2 узлы конденсации водяного пара на 06 кгсм2.
2.2.Выбор и обоснование средств контроля
Для контроля параметров процесса дегидрирования изоамиленов применяем государственную систему приборов (ГСП) которая позволяет использовать приборы и устройства в необходимых сочетаниях для построения любой системы автоматического контроля регулирования и управления.
а) для регистрации температуры применяем потенциометры типа
ЭПП-09-показывающие и самопишущие. Чувствительным элементом служат термопары:
Для замера температуры от 600 до 1000°С в печи № 103 и реакторе № 104 типа ТХА.
Для замера температуры до 600°С во всех остальных точках типа ТХК.
б)для контроля давления в аппаратах и трубопроводах до 6 кгсм2 применяем манометры типа МС-П1 для контроля давления до 06 кгсм2 –манометры типа МАС-П1.
Для регистрации давления применяем приборы типа ПВ.10-1Э.
в) для контроля уровня применяем приборы типа ПВ.10-1Э первичным прибором которого является уровнемер типа УБ-П.
г) для контроля расхода продуктов применяем приборы типа ПВ.10-1Э ДМПК-100 и диафрагмы камерные ДКН-10.
Для регистрации технологических параметров процесса применяем приборы ПВ.10-1Э системы "СТАРТ
Приборы этой системы находятся на современном техническом уровне. Принцип действия основан на компенсационном методе поэтому перемещение подвижных частей незначительное и ввиду этого обеспечивается высокая точность.
3.Автоматическое регулирование
3.1. Выбор и обоснование параметров управляющих воздействий и
Для регулирования давления уровня температуры применяем схему регулирования по отклонению. Имеются также схемы по возмущению комбинированию. Схема регулирования выбрана по отклонению потому что она вполне обеспечивает проведение процесса дегидрирования имеет объекты регулирования чувствительный элемент регулирующий орган.
В проекте принята схема регулирования уровня продуктов по отклонению. Основными управляющими параметрами при регулировании уровня в котле-утилизаторе № 105 является расход поступающего в котел-утилизатор конденсата. Другим менее сильным управляющим воздействием является действие паро-газовой смеси пара на охлождение. Поэтому для регулирования принят расход конденсата на испарение.
Схема регулирования уровня в аппаратах поз.121 110 1061 1431 несколько иная. Здесь основным управляющим параметром является расход уходящего из аппарата продукта. Другим менее сильным управляющим параметром является расход поступающего в аппарат продукта. Для регулирования принято первое.
Уровень во всех аппаратах не должен превышать 80% их емкости и не быть меньшим чем 5% их емкости. Эти цифры приняты исходя из того чтобы емкости не были переполнены или вовсе опорожнены т.к. это приведет к срыву технологических потоков.
В схемах регулирования уровня датчиками являются уровнемерные приборы типа УБП с которого пневматический сигнал подается на вторичный прибор ПВ.10-1Э и регулирующий блок ПРЗ-21.С регулятора ПРЗ-21 командный сигнал поступает на исполнительный механизм-проходной клапан типа 25с50 нж.
Уровень продукта в аппаратах поз.102105 поддерживается изменением расхода продукта поступающего в эти аппараты. Уровень в аппаратах поз.121 110 1431 1061 поддерживается изменением расхода продукта откачиваемого из этих аппаратов.
Регулирование давления в аппарате 121 осуществляется в пределах 3-5 кгсм2 по отклонению параметра. Регулирование этого параметра необходимо в целях поддержания оптимальных условий процесса дегидрирования.
Основным управляющим воздействием на регулирование давления в аппарате 105 является расход конденсата.
Регулирование давления в апп.105 осуществляется по следующей схеме:
импульс давления с отборного устройства поступает на первичный типа МС-П1 где преобразуется в пропорциональный пневмосигнал (02-10кгсм2) который затем поступает на вторичный прибор типа ПВ. 10-1Э и регулирующий блок типа ПР. 3-21. Обратный сигнал с регулятора подается на исполнительный механизм – клапан проходной типа 25с50нж.
Температуру сырья после печи №103 необходимо поддерживать от 500 до 550°С для достижения оптимальных условий реакции. Регулирование осуществляется подачей водяного пара в сырьевой змеевик т. к. изменение этого параметра наиболее сильно влияет на изменение температуры сырья после печи 103.
Кроме этого возмущающимися воздействиями влияющими на температуру сырья после печи являются:
расход сырья в змеевик печи;
температура сырья перед печью;
температура дымовых газов в печи;
Из всех этих параметров наиболее сильно влияющим на температуру сырья является расход топлива в печь. Однако для регулирования принята другая схема – подача пара в змеевик сырья по той причине что подачей топлива в печь регулируется температура пара после радиантного змеевика этой же печи.
Температуру перегретого пара в радиатном змеевике печи №103 необходимо поддерживать в пределах от 715 до 780 С для поддержания оптимальных условий протекания реакции дегидрирования в реакторе.
Управляющее воздействие для поддержания температуры пара после печи в заданных пределах осуществляется по каналу расхода топлива на сжигание в печи № 103.
Также возмущающими воз действиями влияющими на отклонение температуры пара являются:
расход пара в печь № 103;
температура поступающего пара;
Из всех этих параметров наиболее сильно влияющим на температуру пара является расход топлива в печь что и принято для регулирования.
Температуру в реакторе № 104 в период регенерации один раз в сутки поддерживают в пределах от 600 до 650°С. Завышение температуры выше 700°С приводит к разрушению катализатора.
Температура контактного газа после закалки в пределах 500-510°С поддерживается по каналу подачи конденсата на испарение. Кроме этого возмущающими воздействиями влияющими на отклонение температуры контактного газа являются:
температура газа в реакторе;
расход газа из реактора.
Но ни одно из них так сильно не влияет на температуру газа после реактора. Для регулирования применяют возмущающий параметр по каналу подачи конденсата на испарение.
Регулирование температуры сырья после печи 'ПОЗ осуществляется по следующей схеме:
Термоэлектродвижущая сила (ТЭДС) от термопары поступает на прибор типа ПТ-ТП-68 преобразующий ТЭДС термопары в переменное напряжение которое далее преобразуется в постоянный ток величины 1-5 Ма. Затем этот постоянный ток поступает в электропневматический преобразователь типа ЭПП-63 где постоянный эл.ток преобразуется в пневмосигнал. Пневмосигнал с прибора ЭПП-63 поступает на вторичный прибор типа ПВ.10-1Э и регулирующий блок ПР.3-21 откуда подается на исполнительный механизм – клапан проходной типа 25 с 50 нж.
По такой же схеме осуществляется автоматическое регулирование температуры в аппаратах поз.111 104 106 103 110 106а 102а.
а) Регулируется расход паров продукта в сырьевой змеевик печи № 103. Колебания расхода сырья отрицательно влияют на процесс кроме того необходимо поддерживать оптимальный расход продукта на пять параллельных печей.
б) Регулируется расход пара в радиантный змеевик печи № 103 необходимость регулирования расхода пара вытекает из условий процесса дегидрирования т.е нужно поддерживать соотношение сырье:водяной пар 1:20 мольных.
в) Регулирование расхода воздуха на регенерацию I раз в сутки в пределах 200 кг на тонну катализатора в час диктуется условиями оптимального проведения регенерации катализатора.
Во всех случаях регулирование расхода осуществляется по отклонению.
Регулирование расхода продуктов осуществляется по разности давлений до и после диафрагмы по следующей схеме. Давление Р1 до диафрагмы и Р2 после диафрагмы типа ДКН-10 подаются на первичный прибор типа ДМПК-100 где ΔР= Р1- Р2 преобразуется в пропорциональный пневмосигнал который подается на вторичный прибор типа ПВ.10-1Э и регулирующий блок типа ПР.3-21.Обратный сигнал с регулятора поступает на исполнительный механизм – клапан проходной типа 25 с 50 нж.
По такой же схеме осуществляется регулирование расхода:
паров продукта в сырьевой змеевик печи № 103;
паров воды в паровой змеевик печи № 103;
воздуха и пара в реактор № 104 в период регенерации.
Во всех случаях регулирование осуществляется по отклонению и исполнительные механизмы расположены на потоках продуктов.
3.2. Выбор и обоснование средств регулирования
Используются приборы системы "СТАРТ" построенные на элементах УСЭППА (унифицированная система элементов пневматической промышленной автоматизации) имеющие входные и выходные сигналы.
Регуляторы этой системы находятся на современном техническом уровне и по своим конструктивным и эксплутационным качествам превосходят приборы АУС. Обеспечивается высокая стабильность и постоянство показаний высокая чувствительность.
Лентопротяжный механизм выполнен съемным. Регуляторы в отличие от регуляторов АУС имеют независимую настройку времени изодрома (автоматическая перестановка) и во много раз расширяет диапазон дросселирования (от 5 до 3000).
Вторичные самопишущие малогабаритные приборы ПВ.4-2Э и ПВ.10-1Э с ленточной диаграммой входят в систему приборов "СТАРТ В приборе ПВ.10-1Э встроена станция управления обеспечивающая возможность ведения процесса вручную и на автоматике. К прибору ПВ.10-1Э подключается регулятор ПР.3-21 предназначенный для непрерывного получения регулирующего воздействия в виде сжатого воздуха посылаемого к исполнительному механизму с целью поддержания регулируемого параметра на заданном уровне.
ПР.3-21 по характеру воздействия является регулятором пропорционально-интегральным с диапазоном дросселирования (5-3000) с временем интегрирования от 3 сек. до 100 мин.
МС-П2-пневматический прибор давления входит в общий комплекс унифицированной системы пневматических датчиков и используется в комплекте со вторичными приборами и другими устройствами контроля работающими от стандартного пневматического выходного сигнала 02-10 кгсм .
Прибор предназначен для непрерывного преобразования в пропорциональный пневмосигнал дистанционный передачи абсолютного давления. Принцип действия прибора основан на пневматической силовой компенсации. Давление преобразуется на чувствительном элементе прибора в пропорциональное ему усилие которое через рычажной передаточный механизм автоматически уравновешивается усилием развиваемым давлением воздуха на компенсационном элементе сильфона обратной связи.
При изменении измеряемого давления происходит перемещение рычажной системы связанной с рычагом заслонки индикатора рассогласования управляет через усилитель давления поступающим в компенсационный сильфон обратной связи и одновременно в линию дистанционной передачи являясь мерой измеряемого давления. Предел измерения от 0 до 6 кгсм2.
ДМПК-100-датчик дифманометр мембранный с силовой компенсацией Государственная система приборов и средств автоматизации (ГСП) предназначена для работы в системах автоматического контроля и регулирование параметров промышленных технологических процессов. Датчик используется в комплекте с приборами и регуляторами работающими от стационарного сигнала 02-10 кгсм. Давление сигнала датчика 014-14 кгсм . Расход воздуха не более 3 лмин.
УБП – регулятор буйковый с пневматическим выходным сигналом. Предназначен для оперативного контроля жидкости основано на ареометрическом принципе. Изменение выталкивающей силы вызывает пропорциональное изменение угла закручивания трубки преобразуя в пневмосигнал с помощью пневмообразователя. Прибор работает при 40-200°С и давлении до 40 кгсм2. Нулевому уровню соответствует выходной сигнал 02кгсм2 а 100% уровня – 10 кгсм2.
ЭПП-63 – электрический пневмопреобразователь предназначен для преобразования в стационарный пневмосигнал изменения входного сигнала в виде постоянного тока в диапазоне 1-5 Ма. В контакте с дополнительными блоками ПТ-ТП-68 преобразователь ЭПП-63 используется для получения пневматического сигнала пропорциональному поданному электрическому сигналу малых э.д.с. постоянного тока от 0 до 50 МВ. Допустимая погрешность не более 1%. Порог чувствительности не более 005%.
4.1. Выбор и обоснование параметров предупредительной
Сигнализация необходима для своевременного оповещения о нарушениях параметров процессов.
В данном проекте сигнализируется ряд параметров. Рассмотрим один из них. При завышении уровня в аппарате № 103 выше 50% объема аппарата срабатывает сигнализация по следующей схеме:
Импульс – пневмосигнал от первичного прибора типа УБП поступает на электро-контактный манометр (ЭКМ) .При замыкании контакта ЭКМ подается электрический ток на реле МКУ-48 который замыкает контакты цепи подачи напряжения на сигнальные лампы.
5.СВОДНАЯ СПЕЦИФИКАЦИЯ СРЕДСТВ КОНТРОЛЯ И РЕГУЛИРОВАНИЯ
Таблица I Спецификация приборов
Наименование и краткая характеристика
Iв 4IIв 13в 2г 1г 3д 17д 52в 6в 13в 8в 9в 11в
Пропорцилнально-интегральный регулятор. Давление входного и выходного сигналов02-1 кгсм2. давление питания 14 кгсм2.
г 15г 14г 12г 29г 1ж 28г 25г 27г
Дифманометр мембранный пневматический компенсационный. Давление воздуха питания 14 кгсм2. Погрешность 1%.
а 6е 8а 8е 9а 9е 11а 11е
Уровнеметр буйковой пневматический класс точности 1 . Давление питания 14 кгсм2.
Давление выходного сигнала 02-10 кгсм2. Предел измерения 0-16 м.
Электроконтактный манометр класс точности -16; предел измерения 0-6 кгсм2
Москва «Энерго-прибор»
а 18б 18в 18г 3а 17а
Термопара «хромель – алюмель» прдел измерения 800-1200 ºС
а 20б 222а 221а 23а 23б 23в 21а 32а 16а 16б 16в 16г 16д 16е 16ж 16з 16и.
Термопара «хромель – комель» предел измерения 600-800 ºС
а 1а 26а 27а 28а 7а 14а 17а
б 29б 1б 28б 25б 27б 7б 15б 14б 12б 17б
Передающий преобразователь расхода.
в 1в 3г 17г 13б 52б 6б 8б 9б 13б 11б 4Iб 4IIб
Вторичный самопишущий прибор со станцией управления для автоматического регулирования. Погрешность -1% Давление питания 14 кгсм2 входные сигналы 02-10 кгсм2.
в 7в 28в 25в 15в 14в 12в 17в 18б 20в 222г 221г 23е 21г 16м 12в 19б 24Iб 32г
Вторичный пневматический регистрирующий прибор
б 17б 20б 222б 221б 23г 21б 32б 16к
Прибор для измерения температуры бесшкальный с дистанционной передачей
Измерительный преобразователь давления
Манометр для измерения уровня
в 17в 16л 222в 221в 23д 21в 32в
Преобразователь сигнала измерительный. Служащий для преобразования эл.тока в пневмосигнал
Манометр сильфонный класс точности 16. Предел измерения 0-6 кгсм2 PI
Выбор вспомогательного оборудования.doc
Техническая характеристика
Д=3000 мм V=100 м3 Р=1атм
Q=1700 м3час напор = 70м.ст.ж. эл. двигатель 5000 кВт
Q=126 м3час напор = 30 м.ст.ж. эл. двигатель 20кВт П=1475обмин
Q=65 м3ч напор 445 м. ст. ж
эл. двигатель 20 кВт
Теплообмен-ник 2-х элементный
Р=6 кгсм2 D= 600 мм трубки 25х2х600 мм Fэлем=132 м2
V=106 м3 D=3000 мм L=14424 мм.
Q=135 м3ч напор 98м. ст. ж
эл. двигатель 50 кВт
F=28 м2 Q=750 кгч L=1800 мм.
V=50 м3 D=3000 мм Нц.ч=6500 мм
V=3 м3 D=1620 мм Нц.ч=5000 мм
Q=45 м3час напор = 31 м.ст.ж
Q=130 м3час напор = 90 м.ст.ж
эл. двигатель 75 кВт
Q=30 м3ч напор 44 м. ст. ж
эл. двигатель 28 кВт
Qнас=50 м3ч напор = 30 м.ст.ж
V=08 м3 Qнас=63 лмин
Q=630 лчас напор 30 м. ст. ж
Технологическая схема 1.cdw

Топливный газ + аб.газ
Изоамиленовая фракция
3. ТЕХНОЛОГИЧЕСКИЕ РАСЧЕТЫ.doc
1. Расчет материального баланса.
Производительность 60000 тонн изопрена в год
Состав изоамиленовой фракции
Состав контактного газа со второй стадии дегидрирования
31% – выход изопрена на пропущенные изоамилены.
Эффективный фонд рабочего времени оборудования Тэф=355 дней
Технологические потери 5%
Соотношение сырье : водяной пар 1:6
1.1. Схема материальных потоков
гдеG1 – изоамиленовая фракция;
1.2. Перевод производительности установки в кгч с учетом технологических потерь по формуле:
1.3. Определяем загрузку реактора по формуле:
где03031 – выход изопрена на пропущенные изоамилены;
94 – содержание изоамиленов в сырье.
1.3. Определяем расход водяного пара на разбавление по формуле
1.3. Определяем количество воды необходимое для сжигания кокса
1.4. Определяем количество не прореагировавшей воды
2. Расчет теплового баланса
Исходные данные для расчета:
Расход продуктов реакции
Расход водяного пара
-водяной пар на входе
- водяной пар на выходе
Уравнение теплового баланса дегидрирования изоамиленов имеет вид:
где Q1 – количество теплоты поступающей с сырьем Вт;
Q2 – количество теплоты поступающей с водяным паром Вт;
Q3 – количество теплоты поглощенное в результате реакции
дегидрирования изоамиленов Вт ;
Q4 – потери в окружающую среду Вт
Q5 – количество теплоты отводимое с продуктами реакции Вт.
2.1. Определяем среднюю теплоемкость сырья и продуктов реакции.
Определяем теплоемкость веществ по формуле:
где Т – температура К.
Среднюю теплоемкость определяем по формуле:
хi – массовая доля i-го компонента в долях единиц.
Расчеты сводим в таблицы 2 и 3.
Таблица 2. Теплоемкость сырья
Температуру продуктов реакции ориентировочно принимаем равной 873 К
Таблица 3. Теплоемкость продуктов реакции
2.2. Определяем теплоемкость водяного пара по формуле:
Теплоемкость водяного пара при температуре входа:
2.3. Определяем тепловой эффект реакции
Тепловой эффект реакции находим по закону Гесса:
Изменение теплового эффекта реакции в зависимости от температуры описывается уравнением Кирхгоффа:
Теплоемкость продуктов реакции описывается уравнением:
гдеТ – температура К.
Таблица 4. Расчет теплового эффекта реакции дегидрирования изоамиленов
в расчете на 1 кг полученного изопрена:
2.4. Определяем количество тепла поступающее в реактор
Количество тепла поступающее с сырьем Q1 определяется по формуле:
где сс – средняя теплоемкость сырья ;
Т – температура сырья К.
Количество тепла поступающее с водяным паром Q2 определяется по формуле:
где мв – расход пара ;
Т – температура пара К.
2.4. Определяем количество тепла от водимое из реактора
Потери тепла в окружающую среду составляют 1% от поступающего тепла:
Количество теплоты поглощенное в результате реакции дегидрирования изоамиленов Q3 Вт вычисляют согласно формуле:
гдеq – тепловой эффект реакции
G – производительность по изопрену кгч
Количество теплоты отводимое с продуктами реакции Q4 Вт вычисляют согласно формуле:
где Т – температура продуктов реакции К;
сп – теплоемкость продуктов реакции ;
м – расход продуктов реакции кгч.
Технологическая схема 1 исп.cdw

Топливный газ + аб.газ
Изоамиленовая фракция
2. ТЕХНОЛОГИЧЕСКАЯ ЧАСТЬ 12.doc
1. Выбор и обоснование метода производства.
Из большего числа известных способов получения изопрена промышленное применение получили следующие:
синтез из изобутилена и формальдегида;
дегидрирование изопентана и изоамиленов;
выделение из пиролизных фракций;
димеризация пропилена с последующим крекингом 2-метилпентена-2;
взаимодействие ацетона с ацетиленом.
В связи с большими ресурсами пентанов в нефтедобыче и двухстадийным дегидрированием синтез изопрена двух стадийным дегидрированием изопентана более экономичен. Сырьевая база получения изопрена дегидрированием расширена за счет осуществления процесса изомеризации н-пентана в изопентан. Изопентан получается при каталитическом крекинге при стабилизации нефти. При прямой гонке бензина а так же из газов стабилизации нефти. Изоамилены из пиролизных фракций переработки нефти так же расширяют сырьевую базу данного метода.
Цех дегидрирование изопентана в изопрен введен в действие в 1969. В состав цеха входят две установки:В цехе И-2 дегидрируется изопентан в изоамилены а последние – в изопрен при 600 – 650 ºС и разбавлении водяным паром 1:20.
Исследование температурного режима работы реактора показывает что в реакторе имеется две зоны. Зона 1 Т=605 С Зона с Т=580 С. Т.е. реактор работает не в изотермическом режиме. Это связано со значительным тепловым эффектом реакции. Реакция протекает с поглощением кДжмоль тепла что приводит к снижению температуры нижней зоне реактора на 20-25 С. При снижении температуры значительно уменьшается выход целевого продукта.
В связи с этим в данном проекте для увеличения температуры второй зоны реактора предлагается в нижнюю часть подвести дополнительное количество тепла. Для этой цели установить паровой змеевик. Предлагается направить в этот змеевик часть пара которое идет на разбавление изоамиленовой фракции. Это позволит увеличить температуру нижнего слоя реактора и увеличить выход изопрена.
Технико-экономические показатели процесса из года в год улучшаются благодпря усовершенствованию технологии использованию отходов производства ( абгаза тяжелые отходы и др.) применение более совершенных катализаторов.
Изопрен из изопентана может быть получен двумя способами: одностадийным дегидрированием и двухстадийным.
При двух стадийном процессе в первой стадии на алюмохромовом катализаторе получают три изомера изоамиленов:
Процесс ведут при температуре 530–570 ºС давлении 02–05 кгсм2 в кипящем слое катализатора ИМ–2201.
Вторая стадия поцесса – дегидрирование изоамиленов в изопрен
Процесс ведут при температуре 580–600 ºС на стационарном слое катализатора К-24 «И».
В целях уменьшения парциального давления углеводородов сырье разбавляют водяным паром в соотношении 1:20 что также повышает безопасность процесса.
Катализатор загружают в реактор в смеси с теплоносителем который аккумулирует тепло.
3. Описание технологическое схемы производства.
Принципиальная технологическая схема дегидрирования изоамиленов на железооксидном катализаторе К-24 «И» представлена на рисунке 2.1.
Изоамиленовая фракция со склада поступает в сепаратор поз. 102 под давлением 3924104 Па с начальной температурой 20оС. жидкое сырье из сепаратора поз. 102 поступает в трубное пространство испарителей поз. 101 откуда испаренное сырье поступает в верхнюю часть сепаратора поз. 102. Здесь паровая фаза отделяется от жидкой и направляется в трубное пространство перегревателя поз. 102а где перегревается до температуры от 90 до 120оС.
Из перегревателя поз. 102а испаренное сырье поступает в сырьевой змеевик пароперегревательной печи поз. 103 где перегрев сырья до 520оС осуществляется за счет тепла газов конвекции.
Одновременно на перегревание в паровые змеевики печи поз. 103 через регулятор расхода подается водяной пар в соотношении с сырьем не менее 6:1 который перегревается за счет сжигания топливного и адсорбционного газов до температуры не выше 780оС.
Перегретый пар и перегретое сырье после печи поз. 103 направляются через смеситель в реактор поз. 104 где происходит реакция дегидрирования при температуре от 570 до 660оС.
С целью утилизации тепла парогазовая смесь с нижней части реактора поступает в трубное пространство котлов-утилизаторов поз. 105 последовательно включенных в работу где охлаждается за счет питательной воды до температуры от 230 до 250оС.
Далее контактный газ поступает в скруббер поз. 106 где происходит охлаждение его конденсатом до температуры от 105 до 120оС. конденсат подается вверх скруббера насосом поз. 109.
Из скруббера поз. 106 контактный газ поступает тремя потоками в трубное пространство трех параллельно работающих конденсаторов поз. 11112 1121 в которых происходит конденсация водяного пара и частичное
1 – испаритель; 102 – сепаратор; 102а – пароперегреватель; 103 – печь; 104 – реактор; 105 – котёл-утилизатор; 106 110 – скруббер; 109; 113 – насос; 11112 1121 111д – конденсатор; 121а 1431-3 – емкость.
I – изоамиленовая фракция; II – водяной пар; III – топливный газ; IV – парогазовая смесь; V – шестиатмосферный пар; VI – циркулирующий конденсат VII – промоборотная вода; VIII – циркуляционная горячая вода; IX – паровой конденсат; X – контактный газ; XI – питательная вода.
Рисунок 2.1 – Принципиальная технологическая схема производства дегидрирования изоамиленов
охлаждение контактного газа до 98оС циркуляционной горячей водой подаваемой в межтрубное пространство конденсаторов. Сконденсировавшийся конденсат из конденсаторов поз. 11112 1121 поступает в емкости поз. 1431-3.
Из конденсаторов поз. 11112 1121 контактный газ поступает в скруббер поз. 110 в котором происходит конденсация водяного пара и дальнейшее охлаждение контактного газа циркулирующим конденсатом. Вода на циркуляцию подается насосом поз. 113.
Окончательное охлаждение контактного газа происходит в конденсаторах поз. 111д в трубное пространство которых поступает промоборотная вода. Охлаждение контактного газа происходит до температуры от 45 до 55оС. Здесь также происходит окончательная конденсация водяного пара и водяной конденсат поступает в емкости поз. 1431-3. Контактный газ выводится из цеха и направляется в цех И-3 на дальнейшую переработку.
Переход от контактирования к регенерации заключается вследуещем:
а)отключается реактор 104 от сырьевого змеевика печи 103;
б)отключается котел-утилизатор 105 от скруббера 106 и подключается к системе газов регенерации со сбросом на свечу;
в)для полного удаления углеводородов из системы производится продувка реактора водяным паром в течении 2 минут. Затем проводится регенерация катализатора которая заключается в выжиге кокса отложившегося на катализаторе за время контактирования. Для в реактор подают воздух в течении 11 минут. Температура во время регенерации регулируется подачей насыщенного водяного пара из сети.
Окончание выжига кокса определяется по снижению температуры в реакторе или по отсутствию СО2 в газах регенерации.
Газы регенерации – паровоздушная смесь из реактора 104 через котел утилизатор 105 поступает в общий коллектор и сбрасывается на свечу.
По окончании регенерации реактор вновь переводится на контактирование.
Переключение реакторов осуществляется от электроннологической машины. ЭЛМ установлена отдельно на каждом блоке. ЭЛМ обеспечивает:
Невозможность смешения углеводородов и воздуха;
Исключение воздействий ошибок обслуживающего персонала на исход переклющений;
Переключение осуществляется быстродействующими задвижками и гидроприводами.
4. Характеристика сырья материалов и готовой продукции.
Таблица 4. Характеристика сырья материалов и готовой продукции.
Внешний вид – гранулы красно-коричневого цвета
Насыпная плотность 1116гсм2
Механическая прочность не менее 95%
Удельная поверхность 36 м2г
Каталитическая активность:
конверсия этилбензола не менее 65%
выход стирола на разложенный
этилбензол не менее 88%
массовая доля комков
представляющих слепки
более чем трех гранул не более 40%
размером менее 1мм не более 10%
Продолжение таблицы 4
Инертный теплоноситель
Изделия фарфоровые и корундовые. Поверхность фарфоровых изделий должна быть покрыта ровным слоем прозрачной бесцветной или цветной глазури. Допускаются различия в оттенках глазури плавные натеки. Глазурованная поверхность должна быть гладкой и блестящей. На поверхности не допускаются
выгорки полосы волосяные трещины (цек)вздутия (пузыри бугорки) вмятины и выбоины отбитости слипыши мушки отсутствие глазури (слет глазури) наколы. На рабочей поверхности корундовых изделей не допускаются сколы раковины засорка и трещины.
Кажущаяся плотность изделий изготовленных из корундового не менее 37гсм3
Водопоглащение изделий изготовленных из фарфорового материала не должно превышать 05%
Природный топливный газ
Теплота сгорания низшая при 20оС 101325кПа не менее 318МДжм3 (ккалм3)
Область значений числа Воббе
(высшего) 412545 МДж м3 (ккал м3)
Допустимое отклонение числа Воббе от номинального значения не более ± 5%
Массовая концентрация сероводорода
Массовая концентрация меркаптановой
серы не более 0036 гм3
Объемная доля кислорода не более 10%
Масса механических примесей не более 0001г в 1 м3
Интенсивность запаха газа при объемной доле 1% в воздухе не менее 3 балл.
Изоамиленовая фракция
Выход изопрена на изоамилены+изопрен
по контактному газу в среднем за пробег:
на прпущенные 33%масс
на разложенные 81%масс
Выход изопрена на пропущенные изо-
амилены+изопрен (по матер. балансу)
Выход изопрена на разложенные изо-
Технологическая схема 2 исп.cdw

Контактный газ в И-3
Обратная циркуляционная вода
Прямая циркуляционная вода
Лаб. контроль.doc
Перед испарителем 101
С6 и выше- нб 02% вес.
Комплекс перманганат-колометрический
Масло из гидросистемы
2. ТЕХНОЛОГИЧЕСКАЯ ЧАСТЬ 1.doc
1. Выбор и обоснование метода производства.
Из большего числа известных способов получения изопрена промышленное применение получили следующие:
синтез из изобутилена и формальдегида;
дегидрирование изопентана и изоамиленов;
выделение из пиролизных фракций;
димеризация пропилена с последующим крекингом 2-метилпентена-2;
взаимодействие ацетона с ацетиленом.
В связи с большими ресурсами пентанов в нефтедобыче и двухстадийным дегидрированием синтез изопрена двух стадийным дегидрированием изопентана более экономичен. Сырьевая база получения изопрена дегидрированием расширена за счет осуществления процесса изомеризации н-пентана в изопентан. Изопентан получается при каталитическом крекинге при стабилизации нефти. При прямой гонке бензина а так же из газов стабилизации нефти. Изоамилены из пиролизных фракций переработки нефти так же расширяют сырьевую базу данного метода.
Цех дегидрирование изопентана в изопрен введен в действие в 1969. В состав цеха входят две установки:
Установка дегидрирования изопентана в кипящем слое пылевидного катализатора ИМ-2201 с расположением реактора и регенератора на одном уровне и транспортом катализатора в потоке высокой конденсации.
Установка дегидрирования изоамиленов на неподвижном слое катализатора с разбавлением водяным паром 1:20 в адиабатических реакторах с чередующимися циклами контактирования и регенерации. Установка состоит из 6 блоков
Исследование температурного режима работы реактора дегидрирования изоамиленов показывает что в реакторе имеется две зоны. Зона 1 Т=605 С Зона с Т=580 С. Это связано со значительным тепловым эффектом реакции. Реакция протекает с поглощением кДжмоль тепла что приводит к снижению температуры нижней зоне реактора на 20-25 С. В следствии снижения температуры значительно уменьшается выход целевого продукта.
В связи с этим в данном проекте для увеличения температуры второй зоны реактора предлагается в нижнюю часть подвести дополнительное количество тепла. Для этой цели установить паровой змеевик. Предлагается направить в этот змеевик часть пара которое идет на разбавление изоамиленовой фракции. Это позволит увеличить температуру нижнего слоя реактора и увеличить выход изопрена.
Изопрен из изопентана может быть получен двумя способами: одностадийным дегидрированием и двухстадийным.
При двух стадийном процессе в первой стадии на алюмохромовом катализаторе получают три изомера изоамиленов:
Процесс ведут при температуре 530–570 ºС давлении 02–05 кгсм2 в кипящем слое катализатора ИМ–2201.
Вторая стадия поцесса – дегидрирование изоамиленов в изопрен
Процесс ведут при температуре 580–600 ºС на стационарном слое катализатора К-24 «И».
В целях уменьшения парциального давления углеводородов сырье разбавляют водяным паром в соотношении 1:20 что также повышает безопасность процесса.
Катализатор загружают в реактор в смеси с теплоносителем который аккумулирует тепло.
3. Описание технологическое схемы производства.
Принципиальная технологическая схема дегидрирования изоамиленов на железооксидном катализаторе К-24 «И» представлена на рисунке 2.1.
Изоамиленовая фракция со склада поступает в сепаратор поз. 102 под давлением 3924104 Па с начальной температурой 20оС. жидкое сырье из сепаратора поз. 102 поступает в трубное пространство испарителей поз. 101 откуда испаренное сырье поступает в верхнюю часть сепаратора поз. 102. Здесь паровая фаза отделяется от жидкой и направляется в трубное пространство перегревателя поз. 102а где перегревается до температуры от 90 до 120оС.
Из перегревателя поз. 102а испаренное сырье поступает в сырьевой змеевик пароперегревательной печи поз. 103 где перегрев сырья до 520оС осуществляется за счет тепла газов конвекции.
Одновременно на перегревание в паровые змеевики печи поз. 103 через регулятор расхода подается водяной пар в соотношении с сырьем не менее 6:1 который перегревается за счет сжигания топливного и адсорбционного газов до температуры не выше 780оС.
Перегретый пар и перегретое сырье после печи поз. 103 направляются через смеситель в реактор поз. 104 где происходит реакция дегидрирования при температуре от 570 до 660оС.
С целью утилизации тепла парогазовая смесь с нижней части реактора поступает в трубное пространство котлов-утилизаторов поз. 105 последовательно включенных в работу где охлаждается за счет питательной воды до температуры от 230 до 250оС.
Далее контактный газ поступает в скруббер поз. 106 где происходит охлаждение его конденсатом до температуры от 105 до 120оС. конденсат подается вверх скруббера насосом поз. 109.
Из скруббера поз. 106 контактный газ поступает тремя потоками в трубное пространство трех параллельно работающих конденсаторов поз. 11112 1121 в которых происходит конденсация водяного пара и частичное
1 – испаритель; 102 – сепаратор; 102а – пароперегреватель; 103 – печь; 104 – реактор; 105 – котёл-утилизатор; 106 110 – скруббер; 109; 113 – насос; 11112 1121 111д – конденсатор; 121а 1431-3 – емкость.
I – изоамиленовая фракция; II – водяной пар; III – топливный газ; IV – парогазовая смесь; V – шестиатмосферный пар; VI – циркулирующий конденсат VII – промоборотная вода; VIII – циркуляционная горячая вода; IX – паровой конденсат; X – контактный газ; XI – питательная вода.
Рисунок 2.1 – Принципиальная технологическая схема производства дегидрирования изоамиленов
охлаждение контактного газа до 98оС циркуляционной горячей водой подаваемой в межтрубное пространство конденсаторов. Сконденсировавшийся конденсат из конденсаторов поз. 11112 1121 поступает в емкости поз. 1431-3.
Из конденсаторов поз. 11112 1121 контактный газ поступает в скруббер поз. 110 в котором происходит конденсация водяного пара и дальнейшее охлаждение контактного газа циркулирующим конденсатом. Вода на циркуляцию подается насосом поз. 113.
Окончательное охлаждение контактного газа происходит в конденсаторах поз. 111д в трубное пространство которых поступает промоборотная вода. Охлаждение контактного газа происходит до температуры от 45 до 55оС. Здесь также происходит окончательная конденсация водяного пара и водяной конденсат поступает в емкости поз. 1431-3. Контактный газ выводится из цеха и направляется в цех И-3 на дальнейшую переработку.
Переход от контактирования к регенерации заключается вследуещем:
а)отключается реактор 104 от сырьевого змеевика печи 103;
б)отключается котел-утилизатор 105 от скруббера 106 и подключается к системе газов регенерации со сбросом на свечу;
в)для полного удаления углеводородов из системы производится продувка реактора водяным паром в течении 2 минут. Затем проводится регенерация катализатора которая заключается в выжиге кокса отложившегося на катализаторе за время контактирования. Для в реактор подают воздух в течении 11 минут. Температура во время регенерации регулируется подачей насыщенного водяного пара из сети.
Окончание выжига кокса определяется по снижению температуры в реакторе или по отсутствию СО2 в газах регенерации.
Газы регенерации – паровоздушная смесь из реактора 104 через котел утилизатор 105 поступает в общий коллектор и сбрасывается на свечу.
По окончании регенерации реактор вновь переводится на контактирование.
Переключение реакторов осуществляется от электроннологической машины. ЭЛМ установлена отдельно на каждом блоке. ЭЛМ обеспечивает:
Невозможность смешения углеводородов и воздуха;
Исключение воздействий ошибок обслуживающего персонала на исход переклющений;
Переключение осуществляется быстродействующими задвижками и гидроприводами.
4. Характеристика сырья материалов и готовой продукции.
Таблица 4. Характеристика сырья материалов и готовой продукции.
Внешний вид – гранулы красно-коричневого цвета
Насыпная плотность 1116гсм2
Механическая прочность не менее 95%
Удельная поверхность 36 м2г
Каталитическая активность:
конверсия этилбензола не менее 65%
выход стирола на разложенный
этилбензол не менее 88%
массовая доля комков
представляющих слепки
более чем трех гранул не более 40%
размером менее 1мм не более 10%
Продолжение таблицы 4
Инертный теплоноситель
Изделия фарфоровые и корундовые. Поверхность фарфоровых изделий должна быть покрыта ровным слоем прозрачной бесцветной или цветной глазури. Допускаются различия в оттенках глазури плавные натеки. Глазурованная поверхность должна быть гладкой и блестящей. На поверхности не допускаются
выгорки полосы волосяные трещины (цек)вздутия (пузыри бугорки) вмятины и выбоины отбитости слипыши мушки отсутствие глазури (слет глазури) наколы. На рабочей поверхности корундовых изделей не допускаются сколы раковины засорка и трещины.
Кажущаяся плотность изделий изготовленных из корундового не менее 37гсм3
Водопоглащение изделий изготовленных из фарфорового материала не должно превышать 05%
Природный топливный газ
Теплота сгорания низшая при 20оС 101325кПа не менее 318МДжм3 (ккалм3)
Область значений числа Воббе
(высшего) 412545 МДж м3 (ккал м3)
Допустимое отклонение числа Воббе от номинального значения не более ± 5%
Массовая концентрация сероводорода
Массовая концентрация меркаптановой
серы не более 0036 гм3
Объемная доля кислорода не более 10%
Масса механических примесей не более 0001г в 1 м3
Интенсивность запаха газа при объемной доле 1% в воздухе не менее 3 балл.
Изоамиленовая фракция
Выход изопрена на изоамилены+изопрен
по контактному газу в среднем за пробег:
на прпущенные 33%масс
на разложенные 81%масс
Выход изопрена на пропущенные изо-
амилены+изопрен (по матер. балансу)
Выход изопрена на разложенные изо-
7 ЭКОНОМИЧЕСКАЯ ЧАСТЬ 13.doc
Одной из наиболее важных задач в деле развития нефтехимической промышленности является повышение эффективности общественного производства.
Повышение эффективности производства осуществляется путем повышения производительности труда увеличением нагрузки основных фондов сокращения удельных затрат материалов топлива и электроэнергии.
Вместе с тем эффективность производства во многом определяется осуществлением мероприятий связанных с использованием достижений научно-технического прогресса. Последние обеспечивают сокращение длительности цикла исследования-проектирования производства внедрение прогрессивных форм организации и планирования производства в основных и вспомогательных цехах.
Данный проект предусматривает увеличение выработки изопрена в контакном газе цеха И-2 (2 стадия) с 95000 тгод до 110000 тгод за счет реконструкции 5 блоков второй стадии дегидрирования.
Реконструкция предусматривает монтаж парового змеевика в слое катализатора реактора дегидрирования изоамиленов. В результате которого увеличивается температура в средних и нижних слоях катализатора и выработка изопрена.
2 Расчет производственной программы.
Процесс дегидрирования изоамиленов является непрерывным процессом.
Мощность производство изопрена до реконструкции 95000 тг после реконструкции 110000.
Баланс рабочего времени рассчитывается исходя из данных полученных на производстве по простою оборудования и занесенных в таблицу 6.1
Таблица 7.1 – Эффективный фонд времени основного оборудования.
Продолжительность дни
Календарный фонд времени
Регламентируемые перерывы :
а) на капитальный ремонт
б) на текущий ремонт
в) по технологическим причинам
Эффективный фонд времени
Коэффициент интенсивной загрузки КЭ определяется по формуле
где Тэ - эффективный фонд времени дни;
ТК - календарный фонд времени дни.
3 Расчет расходного контингента сырья материалов топлива энергии в материальном и стоимостном выражении.
Таблица 7.2 – Расчет расходного контингента сырья материалов топлива энергии до внедрения мероприятия.
Норма расхода на единицу готовой продукции
Цена за единицу ресурса
Расходный контингент
Продолжение табдицы 7.2
Итого за вычетом возвратных отходов
Катализатор К-24И кг
Катализатор КД-20 кг
Итого по материалам:
Изобутан-бутановая фракция
Электроэнергия 1000 кВтч
Вода обессоленная 1000 м3
Вода промоборотная 1000 м3
Сжатый воздух 1000 м 3
4. Расчет капитальных затрат
Капитальные вложения в оборудование рассчитывается как сумма затрат на техническое оборудование КИП и средства автоматизации технологические трубопроводы электрооборудование и производственный инвентарь.
В результате реконструкции все имеющееся оборудование сохраняется.
Капитальны затраты на имеющиеся оборудования определяем по инвентарной описи цеха и сводим в таблицу 7.3.
Таблица 7.3 – Расчет стоимости оборудования
Наименование оборудования
Общая сметная стоимость руб.
Аппарат колонного типа
Насосы и компрессоры
Неучтенное оборудование
Капитальные вложения в технологическое оборудование складываются из стоимости его приобретения транспортировки хранения комплектации монтажа.
Стоимость приобретения определяется по прейскурантам исходя из видов и количества оборудования определенного технологическим расчетом. Как правило этот расчет полностью не учитывает потребное для организации процесса оборудования поэтому к нему добавляется неучтенное оборудование рассчитываемое в процентах к учтенному. Стоимость нестандартного оборудования можно принять по аналогии или по его массе и цене за единицу массы с учётом используемого материала (металла сплава и т.п.).
Расходы по доставке оборудования составляют в среднем 5% от стоимости приобретения а по его хранению - 3%. Затраты на монтаж определяются по ценникам на монтажные работы или укрупненно в размере 30 % от стоимости приобретения. Расчет стоимости дополнительного оборудования приведен в таблице 6.4
Таблица 6.4. – Расчет стоимости нового оборудования
Цена за единицу руб.
Стои-мость оборудо-вания руб.
Транс-портные расходы руб.
Заготови-тельно-складские расходы руб.
Затраты на монтаж руб.
Сметная стои-мость руб.
Амортизация (в руб) после внедрения равна сумме амортизаций основного и нового оборудования
А = 28249904+ 242397 = 30673874 руб.
Сводный расчет капитальных вложений и амортизационных отчислений по объекту ведется в таблице 4.
Таблица 4 – Капитальные вложения на создание основных фондов
Виды основных фондов
Продолжение таблицы 4
Измерительные приборы
Прочие основные фонды
Расчет показателей по труду и заработной плате
Баланс рабочего времени составляется для расчета эффективного фонда рабочего времени персонала. В начале определяют номинальный фонд времени как разность между календарным фондом и количеством нерабочих дней в году. Затем рассчитывают эффективный фонд рабочего времени вычитая из номинального фонда общее количество невыходов на работу в течении года.
Процесс непрерывный. График работы при 8 часовом рабочем дне – 4-х бригадная система сменности.
Таблица 5 – Баланс рабочего времени одного рабочего в условиях
непрерывного производства
Для сменного персонала
Для дневного персонала
Календарный фонд времени
Итого нерабочих дней
Номинальный фонд времени
Продолжение таблицы 5
а) очередной и дополнительный отпуск
в) отпуск в связи с родами
г) выполнение государственных и
общественных обязанностей
д) отпуск учащимся вечерней и заочной
Итого невыходов на работу
Эффективный фонд рабочего времени
Таблица 6 –Расчет численности рабочих производства
На именование специальности
Итого основных рабочих
Итого вспомогательных рабочих
зам. Начальника цеха
Продолжение таблицы 6
Итого ИТР служащие МОП
Списочная численность в непрерывных производствах определяется по формуле:
гдеЧС – списочная численность рабочих;
ЧЯ – явочная численность рабочих;
ВК – календарный фонд времени;
ВЭ – эффективный фонд времени.
Фонд заработной платы представляет сумму всех денежных средств предназначенных для оплаты труда работников производственного подразделения предприятия. Фонд заработной платы делится на основную и дополнительную.
В состав основной заработной платы входят все виды оплаты за отработанное время в том числе
a)заработная плата начисленная по сдельным расценкам и тарифным ставкам;
b)премии рабочим за выполнении планового задания;
c)доплата за работу в ночное время;
d)доплата за работу в вечернее время;
e)доплата за работу в праздничные дни;
f)доплата за переработку по графику;
g)надбавки неосвобожденным бригадирам;
h)оплата за обучение учеников;
Дополнительная заработная плата включает в себя выплаты за неотработанное время предусмотренное законом. В ее состав входят:
a)оплата очередных и дополнительных отпусков;
b)оплата ученического отпуска;
c)оплата льготных часов подросткам;
d)оплата перерыва в работе кормящих матерей;
e)оплата за время выполнения государственных обязанностей с отрывом от производства
Оплата по тарифу определяется по формуле:
где Чт – часовая тарифная ставка;
Тэф – эффективный фонд рабочего врамени;
Чсп – списочная численность работников;
Тсм – продолжительность смены.
Оплата премиальных определяется по формуле:
где %пр – процент премии (50%).
Доплата за вредные условия труда определяется по формуле:
где %вр – процент вредности (10%).
Доплата за работу в ночное время определяется по формуле:
Доплата за работу в вечернее время определяется по формуле:
Доплата за работу в праздничные дни определяется по формуле:
гдеТпр – количество праздничных дней;
Чя – явочная численность в сутки.
Основной фонд заработной платы определяется по формуле:
Оплата очередного отпуска определяется по формуле:
гдеТотп – количество дней отпуска.
Оплата ученического отпуска определяется по формуле:
гдеТуо – количество дней ученического отпуска.
Оплата времени выполнения государственных обязанностей определяется по формуле:
гдеТго – количество дней выполнения государственных обязанностей.
Таблица 7. Расчет годового фонда зароботной платы основных и вспомогательных рабочих.
Фонд основной заработной платы руб.
Вспомогательные рабочие
Доплата за вредность
Доплата за работу в веч. Время
Доплата за работу в ноч. время
Доплата за работу в праздники
Часовая тарифная ставка
Списочная числен-ность
Профессия специальность раз-ряд
Апп. дегидри-рования
Продолжение таблицы 7.
Всего годовой фонд зп с учетом районного коэф руб
Фонд дополнительный зп руб.
Оплата ученического отпуска
Оплата дней выполнения
Таблица 8. Расчет годового фонда зароботной платы ИТР и служащих.
Мастер по ремонту оборудования
Продолжение таблицы 8.
Всего годовой фонд зп с учетом районного коэф. руб
Расчет расходов на содержание и эксплуатацию оборудования и цеховых расходов
Расходы на содержание и эксплуатацию оборудования определяется по таблице 9.
Таблица 9 – Расчет затрат на содержание и эксплуатацию оборудования
Амортизационные отчисления
Сумма всех амортизационных отчислений технологического оборудования (из таблицы 3)
Расходы по эксплуатации
% от стоимости оборудования
Расходы на текущий ремонт
Основная и дополнительная
заработная плата вспомогательных
Сумма заработной платы всех вспомогательных рабочих (из таблицы 7)
Отчисления на социальное
% от заработной платы вспомогательных рабочих
% от суммы всех предыдущих затрат
Амортизационные отчисления представляют собой сумму амортизационных отчислений по всем позициям технологического оборудования. Расходы по эксплуатации оборудования принимаются в размере 2-6% от стоимости оборудования а расходы на текущий и капитальный ремонт – 4-8%.
Заработная плата вспомогательных рабочих переносится из таблицы 7.
Отчисления на социальное страхование рассчитываются в размере 26% от фонда заработной платы вспомогательных рабочих. Прочие расходы рассчитываются в размере 05% от суммы всех предыдущих затрат.
Цеховые расходы – это расходы связанные с руководством цеха и обслуживанием цеховых потребностей: зарплата цеховогоруководства содержание цеховой лаборатории амортизационные отчисления по общецеховому оборудованию и зданиям и пр. Для расчета цеховых расходов составляется смета (таблица 10).
Таблица 10 – Смета цеховых расходов
Основная и дополнительная заработная плата инженерно-технического персонала цеха
Отчисления на социальное страхование
Амортизация зданий и сооружений общецехового назначения
Текущий ремонт зданий и сооружений общецехового назначения
Содержание зданий и сооружений общецехового назначения
Расходы по охране труда
Итого цеховых расходов
Затраты по заработной плате инженерно-технического персонала были рассчитаны в таблице 8. Расходы по амортизации содержанию и текущему ремонту зданий и сооружений общецехового назначения инвентаря можно принять в размере 12% от стоимости этих основных фондов. Расходы по охране труда – в размере 15% фонда заработной платы всех работников цеха. Прочие расходы составляют 5-10% от суммы всех цеховых расходов указанных выше.
Расчет себестоимости продукции
Себестоимость продукции отражает технический и организационный уровень проекта. Её расчет производится на проектируемый объем выпуска продукции и на основе предыдущих расчетов. Для отчисления себестоимости составляют проектную калькуляцию типовой формы (таблица 11)
Таблица 11 – Проектная калькуляция себестоимости продукции до
сырьё и основные материалы
вспомогательные материалы
топливо и энергия на технологические цели
основная и дополнительная заработная плата основных производственных рабочих
отчисление на социальное страхование
Расходы на содержание и эксплуатацию оборудования
итого цеховая себестоимость
общезаводские расходы
прочие производственные расходы
производственная себестоимость
непроизводственные расходы
полная себестоимость продукции
Таблица 12 – Проектная калькуляция себестоимости продукции
Отчисления на социальное страхование рассчитываются в размере 26% фонда заработной платы основных рабочих.
Общезаводские и прочие производственные расходы включают затраты на управление предприятием общехозяйственные расходы сборы и отчисления расходы на стандартизацию и др. Величина этих затрат в проектах реконструкции действующих производств определяется по отчетной калькуляции; а в проектах организации новых производств – укрупнено в процентах к расходам по переработке (принимают в размере 15% от разности между цеховой себестоимостью продукции и затратами на сырье и материалы).
Внепроизводственные расходы т.е. расходы по реализации продукции следует принять по данным действующего производства а в проектах по организации новых производств – определить укрупнено в размере 1-4% производственной себестоимости.
Методика распределения затрат на производство между отдельными видами основной продукции должна соответствовать принятой на предприятии в условиях которого предусматривается строительство или реконструкция.
Годовой экономический эффект от внедрения новых реакторов определяли согласно [2 с.22] по формуле:
Э = (С1 – С2)·В2 – Ен·Кд(6.22)
где С1 С2– себестоимость единицы продукции соответственно по базовому и проектному вариантам руб;
В2 – годовой объем производства продукции по проектному варианту т;
Ен – нормативный коэффициент эффективности капитальных вложений;
Кд – дополнительные капитальные вложения.
Э = (2249443 – 2247804)·110000 – 016·242347= 179926480 руб.
Срок окупаемости капитальных вложений определяли по формуле:
где Змод – затраты на модернизацию руб;
Э – годовой экономический эффект руб.
Ток = 242347 17992648 = 0013года
7 Свод технико-экономических показателей проекта.
Произведем сравнение технико-экономических показателей проекта с аналогичными показателями действующего производства.
Производительность труда одного рабочего цеха определяем по формуле:
где В – годовой выпуск продукции т;
Чп – численность персонала цеха.
Птр = 9000074 = 12162 тчел·год;
Птр = 11000074= 14865 тчел·год.
Удельные капитальные вложения:
где Кв – капитальные вложения на модернизацию руб;
В – годовой выпуск продукции т.
Кв.уд = 242347 110000 = 022 рубт.
Прибыль от реализации продукции определяли по формуле:
Пр = (Цопт – С) ·В(6.26)
где Цопт – оптовая цена 1т продукции;
С – себестоимость 1т продукции;
Пр = (24800 – 2249443) ·90000= 207501300 руб;
Пр = (24800 – 2247804) ·110000 = 255415600 руб.
Рентабельность производства рассчитывается по формуле:
где СОПФ – стоимость основного производственного фонда руб.т;
СНОС – стоимость нормативных оборотных средств руб.т.
Стоимость нормативных оборотных средств СНОС рассчитаем по формуле:
где Нсм – норматив по сырью материалам;
Нэ – норматив по энергоресурсам;
Нзп – норматив по запасным частям;
Нгп – норматив по готовой продукции.
Норматив по сырью материалам определим по формуле:
где Ркс – расходный контингент по сырью;
Тэф – эффективный фонд рабочего времени ч.;
Здн – запас количества дней Здн = (3-5) дней.
Норматив по энергоресурсам определим по формуле:
где Ркс – расходный контингент по энергоресурсам руб.;
Здн – запас количества дней Здн = (3-8) дней.
Норматив по запасным частям определим по формуле:
Нзп = (6.11) где Соб – стоимость оборудования руб.
Норматив по готовой продукции определим по формуле:
где М(Q) – объем выпущенной продукции тгод;
Цопт – оптовая цена продукции руб.
Здн – запас количества дней Здн = 015 дней.
Подставив числовые значения в формулы(6.9 – 6.12) получим.
Нсм = = 189844591 руб.т;
Нсм = = 232032278 руб.т.
Нэ = = 40327174 руб.т
Нэ = = 49288768 руб.т;
Нзп = = 56499807 руб.т;
Нзп = = 56984601 руб.т
Нгп = = 9704348 рубт;
Нгп = = 118608696 рубт.
СНОС =189844591+ 40327174+56499807+9704348 = 2455260937руб.т.
СНОС = 232032278 +49288768+56984601+ 118608696 = 2988803757руб.т.
Подставив числовые значения в формулу (7.7) получим
Рентабельность продукции определяли по формуле:
R = (Цопт – С) С·100 % (628)
С – полная себестоимость 1т продукции;
R = (24800 – 2249443) 2249443·100 % = 1024 %;
R = (24800 – 2247804) 2247804·100 % = 1033 %.
Основные технико-экономические показатели проектируемого природоохранного объекта приведены втаблице 7.14
Таблица 7.14 - Основные экономические показатели.
Наименование показателей
Годовая мощность производства тгод
Численность работающих чел
Производительность труда тчел год
Среднемесячная зарплата одного рабочего рмес
Удельные капитальные вложения рт
Полная себестоимость 1 т продукта рт
Прибыль от реализации продукции
Годовой экономический эффект р
Срок окупаемости дополнительных
капитальных вложений год
Вывод: Проведение модернизации привело к увеличение прибыли от реализации продукции на 231% при дополнительных капитальных вложениях равных 242397 руб и небольшой срок окупаемости — 0013 года.
Расчет реактора 1.doc
Температура перед смесителем 520 ºС;
Температура водяного пара перед смесителем 750 ºС;
Температура контактной смеси над слоем катализатора 650÷680 ºС.
Водяной пар снижает парциальное давление а также используется в качестве теплоподводящего агента.
Разлагается водяного пара 27459 кгч
Тепловой баланс реактора
С изоамиленовой фракцией при 680 ºС: ;
С водяным паром при 680 ºС:
Потери тепла в окружающую среду:
Температура в реакторе 650 ºС;
Температура окружающего воздуха 20 ºС;
Толщина торкрет-бетона [24с.24];
Толщина панцирной сетки [24с.25];
Толщина стального корпуса [24с.25] ;
Коэффициент передачи тепла от газа к стенке:
Коэффициент передачи тепла от стенки в окружающую среду:
где – коэффициент теплопередачи излучением
– коэффициент теплопередачи конвекцикй.
гдеС1 – коэффициент излучающей поверхности ;
Тп – температура поверхности аппарата 403 К;
Т0 – температура окружающей среды 293 К.
гдеW – скорость потока 10 мс;
dn – диаметр аппарата 45 м.
Общий коэффициент теплопередачи [24т.4]:
подставляя численные значения получим:
Проверка температуры стенки
Определяем тепловой поток по уравнению [24т.4]:
гдеТр – температура реакции 923 К;
Температура на границе бетон – газ :
Температура на границе раздела бетон – панцирная сетка:
Температура на границе раздела панцирная сетка – корпус аппарата:
Температура на границе стенка аппарата – окружающая среда:
Температура окружающей среды:
Расхождения между принятыми и расчетными величинами незначительны.
Поверхность одного реактора:
Поверхность пяти реакторов:
Тепловой эффект реакции 2866554351 кДжч
На один реактор 57331087 кДжч.
Количество тепла контактной смеси на выходе из всех реактора:
Из одного реактора:
Расчет производиться на основе материального баланса и [14 с.318-319]
Теплосодержание паргазовой смеси на выходе из реактора:
Это соответствует температуре 650 С [24т.3]
Расчет количества конденсата для закалки контакного газа
Закалкой снижается температура контакного газа до 500 С с целью исключения вторичных реакций.
Температура контактного газа перед закалкой как было показано выше равна 650 С. Охлаждение контактного газа происходит за счет испарения конденсата поступающего при температуре 80 С
Количество тепла в контактном газе и водяном паре при 650 С:
Количество тепла в контактном газ и водяном паре при температуре 500 С:
где:14408 – теплосодержание контакного газа при 500 С кДжкг;
757– теплосодержание водяного пара при 500 С кДжкг.
Количество тепла отводимое при закалке:
Количество конденсата необходимое для отвода тепла:
Расчет сопративления слоя катализатора
Падение гидравлического напора паров в слое определяется по формуле [24c.28]:
где:Р – потеря напора кгсм2;
W – скорость паров мсек;
γ – удельный вес паров кгм3;
d – диаметр частиц катализатора см.
d=04 см принимаем что цилиндр 4х4 мм соответствует шарику 4 мм.
Определяем объем реакционной смеси при температуре и давлении процесса по формуле:
гдеР0 – стандартное давление 01 МПа;
Т0 – стандартная температура 273 К;
Р – давление процесса МПа;
Т – температура протекания процесса К
– обьем реакционной смеси при стандартных
Обьем реакционной смеси при стандартных условиях определяется по формуле:
где – количество кмолей реакционной смеси.
Подставив полученное значение в уравнение (12) получим:
Удельный вес газа определяется по формуле:
Скорость газа в реакторе:
Подставляя численные значения в формулу () получим:
Количество водяного пара в контактном газе после закалки:
Расчет контактной массы
Объем непредельных С5 в изоамиленовой фракции поступающей в реактор:
Объем необходимого катализатора:
где10 – насыпной вес катализатора гсм3.
Катализатор загружается в смеси с теплоносителем в соотношении 1:2 весовых.
Насыпной вес теплоносителя 21 гсм3.
Определяем загрузку теплоносителя:
Объем контактной массы:
При диаметре существующего реактора высота контактной массы составит:
Гипрокаучук. Расчетно-пояснительная записка производства СКИ. Часть IV раздел I книга 2. – М.:1966. – 218 с.
Хажилов С.В. практические расчеты тепловой изоляции промышленного оборудования и трубопровобов. – М.: Химия 1964 – 312 с.
Литвин О.Б. Основы технологии синтеза каучуков: Учебное пособие. – М.: Химия 1972 – 528 с.
3. ТЕХНОЛОГИЧЕСКИЕ РАСЧЕТЫ 1.doc
1. Расчет материального баланса.
Производительность 110000 тонн изопрена в год
Таблица 3.1. Состав изоамиленовой фракции
Таблица 3.2. Состав контактного газа со второй стадии дегидрирования
31% – выход изопрена на пропущенные изоамилены.
Эффективный фонд рабочего времени оборудования Тэф=355 дней
Технологические потери 5%
Соотношение сырье : водяной пар 1:6
1.1. Схема материальных потоков
гдеG1 – изоамиленовая фракция;
1.2. Перевод производительности установки в кгч с учетом технологических потерь по формуле:
1.3. Определяем загрузку реактора по формуле:
где03031 – выход изопрена на пропущенные изоамилены;
94 – содержание изоамиленов в сырье.
1.3. Определяем расход водяного пара на разбавление по формуле
1.3. Определяем количество воды необходимое для сжигания кокса
1.4. Определяем количество не прореагировавшей воды
Таблица 3. Материальный баланс
2. Расчет теплового баланса
Исходные данные для расчета:
Расход продуктов реакции
Расход водяного пара
-водяной пар на входе
Таблица 4. Физико-химические свойства веществ.
Уравнение теплового баланса дегидрирования изоамиленов имеет вид:
где Q1 – количество теплоты поступающей с сырьем Вт;
Q2 – количество теплоты поступающей с водяным паром Вт;
Q3 – количество теплоты поглощенное в результате реакции
дегидрирования изоамиленов Вт ;
Q4 – потери в окружающую среду Вт
Q5 – количество теплоты отводимое с продуктами реакции Вт.
2.1. Определяем среднюю теплоемкость сырья и продуктов реакции.
Теплоемкость веществ определяем по формуле:
где Т – температура К.
Среднюю теплоемкость определяем по формуле:
хi – массовая доля i-го компонента в долях единиц.
Расчеты сводим в таблицы 2 и 3.
Таблица 5. Теплоемкость сырья
Температуру продуктов реакции ориентировочно принимаем равной 923 К
Таблица 3. Теплоемкость продуктов реакции
2.2. Определяем теплоемкость водяного пара по формуле:
Теплоемкость водяного пара при температуре входа:
2.3. Определяем тепловой эффект реакции
Тепловой эффект реакции находим по закону Гесса:
Изменение теплового эффекта реакции в зависимости от температуры описывается уравнением Кирхгоффа:
Теплоемкость продуктов реакции описывается уравнением:
гдеТ – температура К.
в расчете на 1 кг полученного изопрена:
Таблица 6. Расчет теплового эффекта реакции.
Продолжение таблицы 6.
2.4. Определяем количество тепла поступающее в реактор
Количество тепла поступающее с сырьем Q1 определяется по формуле:
где сс – средняя теплоемкость сырья ;
Т – температура сырья К.
Количество тепла поступающее с водяным паром Q2 определяется по формуле:
где мв – расход пара ;
Т – температура пара К.
2.4. Определяем количество тепла от водимое из реактора
Потери тепла в окружающую среду составляют 1% от поступающего тепла:
Количество теплоты поглощенное в результате реакции дегидрирования изоамиленов Q3 Вт вычисляют согласно формуле:
гдеq – тепловой эффект реакции
G – производительность по изопрену кгч
Количество теплоты отводимое с продуктами реакции Q4 Вт вычисляют согласно формуле:
где Т – температура продуктов реакции К;
сп – теплоемкость продуктов реакции ;
м – расход продуктов реакции кгч.
Технологическая схема 2.cdw

Контактный газ в И-3
Обратная циркуляционная вода
Прямая циркуляционная вода
4. Механический расчет.doc
1. Характеристика аппарата
Аппарат представляет собой шаровой реактор диаметром 4500 мм двух приваренных к нему обечаек. Верхняя обечайка диаметром 1200 мм закрывается эллиптическим днищем со штуцером диаметром 250 мм для входа сырья и имеет трубу диаметром 920500 мм для входа пара. Нижняя обечайка диаметром 1400 мм служит для выхода продуктов реакции.
Для защиты корпуса от воздействия высоких температур коррозии и уменьшения потерь тепла изнутри аппарат обмуровован.
В нижней части аппарата расположены балки на которых монтируется решетка. На решетку загружается контактная смесь – катализатор с теплоносителем.
В верхней част аппарата расположен отбойник для расположения парогазовой смеси по сечению реактора.
Реактор имеет штуцера для установки термопар и манометров а также люки лазы для ремонтных работ и замены контактной массы.
Все внутренние устройства выполнены из легированных сталей: Х17Н13М2Т Х25Н20С2 и 0Х18Н10Т. Устройства расположенные над слоем катализатора выполнены из легированной стали Х25Н20С2 – во избежании разрушения катализатора окислами металла.
Корпус реактора выполнен из стали 20К ГОСТ 1050-60.
Давление рабочие– 06 МПа;
Температура– 1134 ºС (см. с.61);
Объем аппарата– 587 м3
Среда – пары углеводов и водяного пара
Давление пробное при гидроиспытаниях– 09 МПа
Вес аппарата– 30600 кг;
Вес контактной массы – 18300 кг;
Вес обмуровки и теплоизоляции– 37300 кг;
Вес реактора в рабочем состоянии– 86200 кг.
2 Расчет основных элементов аппарата на прочность
2.1 Расчет толщины обечаек
Диаметр аппарата– 4500 мм.
Диаметр корпуса головки– 1200 мм.
Диаметр эллиптического днища– 1200 мм.
Толщину корпуса головки вычисляют по формуле [33 с.10]
где Р – расчетное давление МПа;
D – диаметр аппарата м;
[s] – допускаемое напряжение материала аппарата МПа;
j - коэффициент прочности сварных швов;
С и С1 – прибавка к расчетной толщине обечайки м.
Коэффициент прочности сварных швов характеризует прочность шва по сравнению с прочностью основного материала. Значение этого коэффициента зависит от метода сварки и типа сварочного соединения. Согласно рекомендациям [8] принимаем для корпуса аппарата сварной шов стыковой с двусторонним сплошным проваром выполненный автоматической сваркой. При контроле 100% длины шва как и для бесшовных аппаратов коэффициент прочности сварных швов принимаем равным 095 [8].
При расчете элементов аппарата допускаемое напряжение определяется по формуле [35 с.127]:
где:* – нормативное допускаемое напряжение МПа;
– поправочный коэффициент в которых обрабатываются пожаро- и
взрывоопасные продукты.
Для стали 20К при 124 ºС * принимаем равным 1185 МПа [33 с.56].
принимаем равным 09 [33 с.8].
Для расчетов принимаем .
Толщину эллиптического днища определяют по формуле [33 с.26]
где: R=Д – для стандартных днищ.
Определяем толщину нижней обечайки по формуле:
Подставив численные значения в формулу получим:
2.2. Расчет сварного шва.
Сварные швы рассчитываются на срез и изгиб.
Напряжение изгиба в сварном шве под действием изгибающего момента [35 с.613] :
где:WСВ – момент сопротивления изгибу сварного шва см3.
Момент сопротивления изгибу сварного шва определяем по формуле[35 с.258]:
Подставив численные значения в формулу () получим:
Дытнерский Ю.И. Основные процессы и аппараты химической технологии. -М.: химия 1991.-464с.
ГОСТ 14249 – 69. Сосуды и аппараты. Нормы и методы расчета на прочность. – М.:
Андрес В.Г. Контроль и автоматизация процессов переработки нефти и газа.
Реактор дегидрирования изоамиленов.cdw

Давление пробное при пневматичес-
Аппарат подлежит инспекции Гостехнадзора.
Аппарат изнутри футурируется жаростойким торкрет-
бетоном. Состав торкрет бетона
подготовку поверхности
под покрытие и технологию гидротерминальной слоя бето-
на проводить согласно иструкции. Объем торкретбетона
вес=3600 кг. Объем жаростойкого кирпича V
Снаружи аппарат теплоизолируется стекломатами толщи-
Технические условия:
Изготовление и сварку реактора произвести всоответсвии
с МН 22-62 и МРТУ 2-04-10-63.
На заводе изготовителе произвести контрольную сварку
первого реактора на прихватах.
Сборку реактора произвести всоответсвии с нормалью
Отверстия в корпусе и сестке для установки люков люков
термопар и манометра вырезать на монтаже
Полная сборка и сварка реактора производится на монтаже
Собранный реактор до проведения работ по токретирова-
нию должен быть подвергнут:
а) гидравлическому испытанию при Р= 9атм;
б) пневматическому испытанию при Р=6 там;
в) пневматическому испытанию при р=3 атм на приварку
Реактор дегидрирования
Экспликация люков и штуцеров
Наименование штуцеров
Вход изоамиленов и пара
Рекомендуемые чертежи
- 30.04.2021
- 25.01.2023
- 24.01.2023
- 24.01.2023
- 17.05.2023
- 10.06.2022
Свободное скачивание на сегодня
- 25.10.2022