Двухсупенчатый червячно-цилиндрический редуктор




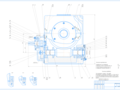
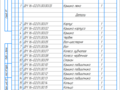
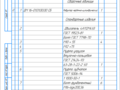
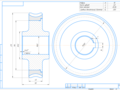
- Добавлен: 24.01.2023
- Размер: 757 KB
- Закачек: 0
Описание
Двухсупенчатый червячно-цилиндрический редуктор
Состав проекта
![]() |
![]() |
![]() ![]() ![]() ![]() |
![]() ![]() ![]() ![]() |
![]() ![]() ![]() ![]() |
![]() ![]() ![]() ![]() |
![]() ![]() ![]() ![]() |
![]() ![]() ![]() ![]() |
![]() ![]() ![]() |
![]() ![]() ![]() ![]() |
Дополнительная информация
спецификация ВО.spw

Общий вид.cdw

ВАЛ.cdw

КОЛЕСО.cdw

2 вид.cdw

Спецификация.spw

1 вид.cdw

Рекомендуемые чертежи
- 16.03.2019