Дизель v8ЧН 12/13 мощностью 200 кВт для установки на шасси магистрального тягача категории N3



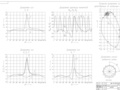
- Добавлен: 25.01.2023
- Размер: 6 MB
- Закачек: 0
Описание
Состав проекта
![]() |
![]() |
![]() |
![]() ![]() ![]() |
![]() |
![]() ![]() ![]() |
![]() |
![]() ![]() ![]() |
![]() ![]() ![]() |
![]() ![]() ![]() |
![]() ![]() ![]() |
![]() ![]() ![]() |
![]() ![]() |
![]() ![]() ![]() |
![]() |
![]() ![]() ![]() |
![]() |
![]() ![]() ![]() |
![]() |
![]() ![]() ![]() |
![]() |
![]() ![]() ![]() |
![]() |
![]() ![]() ![]() ![]() |
![]() ![]() ![]() ![]() |
![]() ![]() ![]() |
![]() |
![]() ![]() ![]() |
![]() ![]() ![]() |
![]() ![]() ![]() |
![]() ![]() ![]() |
![]() ![]() ![]() |
![]() ![]() |
![]() ![]() ![]() |
![]() ![]() ![]() |
![]() ![]() ![]() |
Дополнительная информация
5. уравновешивание(гот).doc
Силы и моменты действующие в кривошипно-шатунном механизме непрерывно изменяются и если они не уравновешены вызывают сотрясение и вибрацию двигателя передающиеся раме автомобиля или трактора.
К неуравновешенным силам и моментам относятся:
а) силы инерции возвратно-поступательно движущихся масс Р
б) продольные моменты Mj = MjI + MjII и MR возникающие в многоцилиндровых двигателях от неуравновешенных сил Рj и KR отдельных цилиндров;
в) крутящий момент Мкр и равный ему но противоположно направленный опрокидывающий момент Mсопр= - Mкр воспринимаемый опорами двигателя.
Двигатель считается полностью уравновешенным если при установившемся режиме работы силы и моменты действующие на его опоры постоянны по величине и направлению. Однако поршневые двигатели не могут быть полностью уравновешенными так как крутящий момент Мкр всегда является периодической функцией угла поворота коленчатого вала и следовательно величина опрокидывавшего момента Мопр всегда переменна.
Условия уравновешенности двигателя с любым числом цилиндров (при соблюдении равенства масс движущихся частей и идентичности протекания рабочего процесса во всех цилиндрах а также обеспечении статической и динамической уравновешенности коленчатого вала) принято записывать в следующем виде:
а) результирующие силы инерции первого порядка и их моменты равны нулю:
б) результирующие силы инерции второго порядка и их моменты равны нулю:
в) результирующие центробежные силы инерции и их моменты равны нулю:
Таким образом решение вопроса уравновешивания двигателя сводится к уравновешиванию лишь наиболее значительных сил и их моментов.
Уравновешивание сил инерции первого и второго порядков слагается подбором определенного числа цилиндров их расположением и выбором соответствующей кривошипной схемы коленчатого вала. Так например в шести- и восьмицилиндровых рядных двигателях полностью уравновешены силы инерции первого и второго порядков и их моменты.
При невозможности подобрать для проектируемого двигателя соответствующего количества и расположения цилиндров для полного уравновешивания сил инерции они могут быть уравновешены противовесами расположенными на дополнительных валах имеющих механическую связь с коленчатым валом.
В рядных двигателях уравновесить силы инерции первого и второго порядков установкой противовесов на коленчатом валу невозможно. При соответствующем выборе массы противовеса можно частично перенести действие силы инерции первого порядка из одной плоскости в другую тем самым уменьшив максимальную неуравновешенность в одной плоскости.
Центробежные силы инерции вращающихся масс практически можно уравновесить в двигателе с любым количеством цилиндров установкой противовесов на коленчатом валу.
В большинстве многоцилиндровых двигателей результирующие силы инерции уравновешиваются без установки противовесов за счет соответствующего числа и расположения колен вала. Однако даже уравновешенные валы часто снабжают противовесами в целях уменьшения и более равномерного распределения нагрузки Rк.ш. на коренные шейки и подшипники а также для уменьшения моментов изгибающих коленчатый вал.
V- образный восьмицилиндровый двигатель :
порядок работы двигателя: 1л-1п-4л-2л-2п-3л-3п-4п; промежутки между вспышками равны 90°; коленчатый вал имеет кривошипы расположенные под углом 90°.
Центробежные силы инерции рассчитываемого двигателя полностью уравновешены:
Суммарный момент центробежных сил действует во вращающейся плоскости составляющей с плоскостью первого кривошипа угол 18°26' величина его:
Силы инерции первого порядка взаимно уравновешены:
Суммарный момент сил инерции первого порядка действует в той же плоскости где и равнодействующий момент центробежных сил величина его:
Силы инерции второго порядка и их моменты полностью уравновешены:
Уравновешивание моментов и осуществляется установкой двух противовесов на концах коленчатого вала в плоскости действия моментов т.е. под углом 18°26' (Рис. 5.1.).
Суммарные моменты и действуют в одной плоскости поэтому:
Масса каждого противовеса определяется из условия равенства моментов:
Расстояние центра тяжести общего противовеса от оси коленчатого вала принимаем
ρ=130 мм. Расстояние между центрами тяжести общих противовесов - b=720 мм. Расстояние между центрами шатунных шеек – а=156 мм.
Масса общего противовеса: =425 кг
согл.doc
Номинальный режим работы двигателя.
Среднее эффективное давление: 0898 MПа
Теоретическое среднее индикаторное давление: 118 МПа
где - механический КПД двигателя;
Значения задается из пределов 07 09 принимаем =08.
- коэффициент скругления диаграммы; принимаем =095
Давление в конце сжатия: 75 МПа
где - степень изохорного повышения давления и -показатели политроп сжатия
и расширения. Согласно эмпирическим данным принимается =151; ρ=126;=137; =122.
Давление в конце впуска: 0168 МПа
Учитывая потери давления на впуске в цилиндры двигателя складывающихся из потерь в агрегатах впуска () потерь в ОНВ () потерь во впускном трубопроводе () и потерь при прохождении впускного клапана () давление будет равным:
Для расчета потерь воспользуемся эмпирическими формулами:
тогда: 00182 МПа итак:
Расход топлива: 8725
где Hu=28800 - низшая теплота сгорания топлива 0365- индикаторный КПД двигателя.
Расход воздуха : 039
где 9061 - теоретически необходимое количество воздуха для сгорания 1 кг топлива
=18– коэффициент избытка воздуха.
Т.к. количество турбокомпрессоров – 2 то одного компрессора:
Давление воздуха перед компрессором: 0098 МПа
Характеристика компрессора
где МПа – давление окружающей среды.
и - расход воздуха на i-м режиме и режиме номинальной мощности
Степень повышения давления в компрессоре: 189
Для установки на проектируемый двигатель выбран турбокомпрессор ТКР 8
Адиабатический КПД при Gв=019 и 189 равен 07 (Рис. 2.1.)
Температура воздуха за компрессором: 377 К
где То=293 К – температура окружающий среды к=14 – показатель адиабаты.
Температура перед впускными клапанами: 323 К
- глубина охлаждения заряда за ОНВ.
Плотность воздуха перед впускными клапанами:
где Rв=287 - газовая постоянная для воздуха.
Уточняется потеря давления во впускном клапане.
где - коэффициент гидравлического сопротивления клапана 16 Wкл=715 мс - средняя скорость заряда в узком сечении клапана.
Уточняется 00179 Мпа
т.е. условие точности расчета выполнено.
Уточняется далее Рк и :
Мощность компрессора: 166 кВт
Давление газов за турбиной: Мпа
где Gвi и GвN– расходы воздуха на i-м и номинальном режимах работы двигателя.
Эффективный КПД турбины: 072
Температура газов перед турбиной: Тт=704 К.
Степень понижения давления в турбине.
Характеристика турбины
где - показатель адиабаты для газов Rг=288 - газовая постоянная
8 - общий КПД турбокомпрессора.
5- механический КПД ТКР = 068- общий КПД турбины
Давление газов перед турбиной.
Согласно условию =64970 мин-1 при u2k= 272 мc т.е. частоты вращения компрессора и ротора турбины равны.
Эффективный КПД турбины (Рис. 2.2.): 071
Nt>Nk т.е. требуется запас мощности и разность мощностей составляет 10 % таким образом баланс мощностей соблюдается.
Режим максимального крутящего момента.
Среднее эффективное давление: 092 MПа
Теоретическое среднее индикаторное давление: 114 МПа
Значения задается из пределов 07 09 принимаем =085.
Давление в конце сжатия: 604 МПа
и расширения. Согласно эмпирическим данным принимается =168; ρ=13; =13; =122.
Давление в конце впуска: 0164 МПа
тогда: 00078 МПа итак:
Расход топлива: 4556
где Hu=28800 - низшая теплота сгорания топлива 0368- индикаторный КПД двигателя.
Расход воздуха : 019
=17– коэффициент избытка воздуха.
Давление воздуха перед компрессором: 01 МПа
Степень повышения давления в компрессоре: 18
Адиабатический КПД при Gв=0097 и 18 равен 069 (Рис. 2.1.)
Температура воздуха за компрессором: 363 К
Температура перед впускными клапанами: 318 К
где - коэффициент гидравлического сопротивления клапана 16 Wкл=39 мс - средняя скорость заряда в узком сечении клапана.
Уточняется 00077 Мпа
Мощность компрессора: 688 кВт
Давление газов за турбиной: 2 Мпа
Эффективный КПД турбины: 071
Температура газов перед турбиной: Тт=681 К.
7 - общий КПД турбокомпрессора.
5- механический КПД ТКР = 067- общий КПД турбины
Согласно условию =61860 мин-1 при u2k= 259 мc т.е. частоты вращения компрессора и ротора турбины равны.
Эффективный КПД турбины (Рис. 2.2.): 072
6.2. Расчет шатунной группы(готово).doc
Шатун является частью кривошипно-шатунного механизма двигателя и служит для передачи усилий от поршня к коленчатому валу и наоборот от коленчатого вала к поршню.
Расчётными элементами шатунной группы являются поршневая и кривошипная головки стержень шатуна и шатунные болты. На рис.6.2.1. приведена расчётная схема шатуна.
При работе двигателя шатун подвергается воздействию знакопеременных газовых и инерционных сил а в отдельных случаях эти силы создают ударные нагрузки. Поэтому шатуны изготовляют из марганцовистых хромистых хромоникелевых сталей с содержанием углерода 030-045%. Для повышения усталостной прочности при достаточной вязкости и пластичности стальные шатуны подвергают в процессе штамповки промежуточной термообработке а после штамповки – полированию обдувке дробью нормализации закалке и отпуску.
Рис. 6.2.1. Расчётная схема шатуна.
2.1. Расчет поршневой головки шатуна
Так как на шатун установлен плавающий палец то в эту головку запрессовывается одна бронзовая втулка. Из-за значительных удельных давлений и ударного характера нагрузки на поршневой палец для изготовления втулки поршневой головки шатуна применена бронза обладающая высокой твердостью и хорошо сопротивляющаяся усталостному разрушениям [1c.156].
Поршневая головка шатуна (рис.6.2.1) рассчитывается на:
- усталостную прочность в сечении I-I от действия инерционных сил (без учёта запрессованной втулки) достигающих максимальных значений при работе двигателя на режиме разносной частоты вращения коленчатого вала;
- напряжения возникающие в головке от воздействия на неё запрессованной втулки;
- усталостную прочность в сечении А-А (место перехода головки шатуна в стержень – заделка головки) от действия (газовых и инерционных) сил и запрессованной втулки.
Расчёт в этом случае производится для того режима работы двигателя при котором амплитуда изменения суммарных сил максимальна.
действительное максимальное давление сгорания Pzma массу поршневой группы = 294 кг; массу шатунной группы = 339 кг;
максимальную (разносную) частоту вращения при холостом ходе = 2400 ;
площадь поршня Fп = 001131 ; = 0274.
Из расчёта поршневой группы имеем:
диаметр поршневого пальца = 45 мм; длина поршневой головки шатуна = 46 мм.
По табличным данным [1] принимаем:
наружный диаметр головки = 646 мм; внутренний диаметр головки d = 49 мм; радиальную толщину стенки головки = () = 8 мм; радиальную толщину стенки втулки = (d-)2 = 2 мм.
Материал шатуна – легированная сталь 40Х; Еш = 22· МПа = 1· 1К. Материал втулки – бронза; Ев = 115· МПа = 18· 1К.
По справочным данным [1] для углеродистой стали 40Х:
- предел прочности = 1050 МПа;
- пределы усталости при изгибе = 350 МПа и растяжении - сжатии = 240 МПа;
- предел текучести = 800 МПа;
- коэффициенты приведения цикла при изгибе = 024 и растяжении – сжатии = 02.
Расчёт детали проводим с учётом переменной нагрузки; определим при изгибе:
при растяжении – сжатии:
Расчёт сечения I -I (см. рис. 6.2.1):
- максимальное напряжение пульсирующего цикла:
где = 008·= 027 кг – масса части головки выше сечения I-I;
- среднее напряжение и амплитуда напряжений:
где 1317 - эффективный коэффициент концентрации напряжений (головка не имеет резких переходов и концентрация напряжения в основном зависит от качественной структуры материала); = 065 – масштабный коэффициент определяется по справочным данным [1] (максимальный размер для сечения I-I составляет 46 мм); = 05 – коэффициент поверхностной чувствительности определяемый по справочным данным [1] (грубое обтачивание);
то запас прочности в сечении I-I определяется по пределу усталости:
Запас прочности соответствует установленным n = 2 5.
Напряжения от запрессованного пальца:
DS = D + Dt DS = 00831 мм;
где D = 004 мм — натяг посадки поршневого пальца; Dt = d·(П-Г)·DT ; Dt = 00431 мм — температурный натяг; DT = 110 K — средний подогрев головки и пальца;
- удельное давление на поверхности соприкосновения пальца с головкой:
где = 03 — коэффициент Пуассона.
Напряжение от суммарного натяга на внутренней поверхности головки:
Напряжение от суммарного натяга на внешней поверхности головки:
Значения ’i и ’а не превышают допустимых значений 100 150 МПа.
Расчёт сечения А-А (рис.6.2.2) на изгиб:
Сечение А-А поршневой головки на режиме или нагружается переменными суммарными силами и постоянной силой от действия запрессованной втулки.
Рис.6.2.2. Распределение нагрузок на поршневую головку шатуна:
а - при растяжении; б - при сжатии.
Суммарная сила растягивающая головку достигает максимального значения при положении поршня в в.м.т. во время начала впуска. Эта сила определяется без учета незначительной в этот момент величины газовых сил.
Максимальная сила растягивающая головку на режиме :
На основании экспериментальных и расчетных данных принимают что радиальное давление от силы распределяется равномерно по внутренней поверхности верхней половины головки (рис.6.2.2 а).
В соответствии с расчетной схемой (рис.6.2.2 а) принимается что нижняя часть головки опирающаяся на стержень большой жесткости не деформируется а действие отброшенной правой части головки заменяется нормальной силой Nj0 и изгибающим моментом Mj0.
Нормальная сила и изгибающий момент в сечении 0-0 (рис.6.2.2 а):
где = 1100 – угол заделки; = ()4 =284 мм – средний радиус головки;
Определяется нормальная сила и изгибающий момент в расчётном сечении от растягивающей силы:
Напряжение на внешнем волокне от растягивающей силы:
где 0882- коэффициент учитывающий совместную деформацию головки шатуна и запрессованной в нее втулки;
где Fв Fг – площади поперечных сечений втулки и головки:
Fг = (dг - d)· Fв = (d - dп)·
Eш = МПа МПа – соответственно модули упругости материалов поршневой головки шатуна и втулки.
Суммарная сила сжимающая головку (рис.6.2.2 б):
где 112 МПа - максимальное давление на номинальном режиме
МПа - давление окружающей среды
м2 – площадь поршня.
Нормальная сила и изгибающий момент в расчётном сечении от сжимающей силы:
Напряжение на внешнем волокне от сжимающей силы:
Запас прочности поршневой головки шатуна в сечении А-А определяется соответствующими соотношениями ([1]с.247). Суммарные напряжения вызываемые в этом сечении газовыми и инерционными силами и запрессованной втулкой изменяются по асимметричному циклу а минимальным запасом прочности обладает наружное волокно для которого:
Максимальное и минимальное напряжения асимметричного цикла:
Среднее напряжение и амплитуды напряжения
Так как = 1.97 > то запас прочности в сечении А-А определяется по пределу усталости:
2.2. Расчёт кривошипной головки шатуна
Подача масла происходит в момент совпадения смазочных отверстий в шатунной шейке коленчатого вала и вкладыша. Кривошипная головка шатуна выполнена разъемной - с плоскость разъема перпендикулярной оси шатуна. Крепление крышки кривошипной головки шатуна осуществляется двумя шатунными болтами.
Кривошипная головка шатуна выполнена с подшипником скольжения. Для уменьшения трения и износа шатунных шеек внутреннюю поверхность подшипников покрыта слоем антифрикционного сплава.
Условия работы верхнего и нижнего вкладышей шатуна неодинаковы. Так как двигатель 4-х тактный то верхний вкладыш нагружают силы давления газов и сил инерции этих масс. Применяются тонкостенные взаимозаменяемые вкладыши изготовленные из стальной ленты покрытые антифрикционным сплавом. Толщина ленты tв = 24 4 мм. Эти вкладыши устанавливаются в кривошипной головке с натягом.
При изготовлении вкладышей на наружной поверхности их отгибаются фиксирующие усики которые предохраняют вкладыши от проворачивания и продольного смещения.
Предварительные размеры кривошипной головки шатуна определяют в зависимости от размеров шатунной шейки dш.ш. коленчатого вала.
Из динамического расчёта и расчёта поршневой головки шатуна имеем:
радиус кривошипа R = 0065 м; массу поршневой группы = 294 кг; массу шатунной группы =+=339 кг; угловую частоту вращения ; = 0274. По табличным данным [1] принимаем: диаметр шатунной шейки = 80 мм; толщину стенки вкладыша tв = 3 мм; расстояние между шатунными болтами Сб = 102 мм; длину кривошипной головки lк = 25 мм.
Точный расчет кривошипной головки весьма затруднен вследствие невозможности полного учета влияния конструктивных факторов.
На крышку давление передается по закону распределения их на вкладыше и что вкладыши и головка деформируется одинаково так как вкладыши сидят в головке всегда с натягом.
Приближенный расчет кривошипной головки шатуна сводится к определению напряжения изгиба в среднем сечении II-II (рис.6.2.1) крышки головки от инерционных сил имеющих максимальное значение в начале впуска (j = 0°) при работе на режиме максимальной частоты вращения холостого хода.
Максимальная сила инерции:
Момент сопротивления расчётного сечения:
где 43 мм – внутренний радиус головки шатуна.
Момент инерции вкладыша и крышки:
Напряжение изгиба крышки и вкладыша
2.3. Расчёт стержня шатуна
Стержень шатуна имеет двутавровое сечение которое по сравнению с другими видами сечений при одинаковых весе и длине стержня обеспечивают шатуну большую жесткость.
Для обеспечения плавных переходов от стержня к кривошипной головке шатуна и для выравнивания напряжений по длине стержня площадь его сечения в направлении кривошипной головки увеличивают (рис.6.2.1)
Для уменьшения сопротивления воздуха при движении шатуна стержню и кривошипной головке шатуна следует придавать обтекаемую форму.
Основными конструктивными параметрами стержня шатуна кроме длины = являются размеры его среднего сечения В-В (рис.6.2.1).
Стержень шатуна рассчитывают на усталостную прочность в среднем сечении В-В от действия знакопеременных суммарных сил (газовых и инерционных) возникающих при работе двигателя на режимах или . Обычно расчёт ведётся для режима максимальной мощности. Запас прочности сечения определяется в плоскости качания шатуна и в перпендикулярной плоскости. Условием равнопрочности стержня шатуна в обеих плоскостях является .
Сила Рсж сжимающая шатун достигает максимального значения в начале рабочего хода. Сила РР растягивающая шатун достигает максимального значения в начале впуска (в в.м.т.). Эти силы определяется по результатам динамического расчёта.
Из динамического расчёта имеем: 10243 кН при =; =-16136 кН при =; = 2372 мм. По табличным данным [1] принимаем: . Из расчетов поршневой и кривошипной головок шатуна: d = 49 мм d1 = 86 мм; характеристики прочности материала шатуна (сталь 40Х).
Площадь и моменты инерции расчётного сечения В-В:
Максимальное напряжение от сжимающей силы:
в плоскости качания шатуна:
где = 1+1089 1050 МПа;
в плоскости перпендикулярной плоскости качания шатуна:
где 1+1046; 1697 мм.
Минимальное напряжение от растягивающей силы:
Среднее напряжение и амплитуда цикла:
где 1317 - эффективный коэффициент концентрации напряжений (головка не имеет резких переходов и концентрация напряжения в основном зависит от качественной структуры материала); = 075 – масштабный коэффициент определяется по справочным данным [1] (максимальный размер для сечения составляет 50 мм); = 13 – коэффициент поверхностной чувствительности определяемый по справочным данным [1] (поверхностное упрочнение стержня шатуна обдувкой дробью).
Так как 181> и 183 > 0143
то запас прочности в сечении В-В определяется по пределу усталости:
2.4. Расчет шатунных болтов
Шатунные болты нагружаются силами инерции масс поршня и шатуна (без нижней крышки) достигающими наибольших значений при положениях поршня около в.м.т. Кроме этих сил шатунные болты подвергаются воздействию значительно больших чем силы инерции сил затяжек. Сила затяжки может быть больше предполагаемой силы в два-три раза что приведет к возникновению текучести материала и затем ослаблению затяжки а также может быть причиной аварии. Также вредное влияние оказывает недостаточная затяжка шатунных болтов приводящая к ударному характеру действия нагрузки и последующему наклепу на стыках кривошипной головки шатуна.
В связи с этим к материалу конструкции и монтажу шатунных болтов предъявляют повышенные требования. Материал болта должен хорошо сопротивляться действию ударной нагрузки и обладать высокими пределами упругости и текучести.
Болты из низкоуглеродистых легированных сталей со временем вытягиваются и их затяжка ослабевает что для шатунов недопустимо.
Болты работают в режиме несимметричного циклического нагружения и требует достаточно большого усилия предварительной затяжки при относительно небольшом диаметре. Потому для обеспечения высокой прочности применяют различные технические решения. Применяют в основном метрическую резьбу с мелким шагом часто обусловлено равной прочностью витков на смятие и стержня на разрыв по впадинам резьбы.
Шатунный болт шлифуется по наружной поверхности в том числе и галтели - переходы от одного диаметра к другому.
Гайка шатунного болта изготовлен из той же стали что и болты. Термическая обработка гаек для повышения твердости граней и для упрочнения резьбы также что и для шатунных болтов.
Следует иметь в виду что при недостаточной жесткости кривошипной головки и возникающих вследствие этого перекосах опорных поверхностей головки и гайки шатунного болта в нем могут возникать не учитываемые расчетом знакопеременные изгибные напряжения. Эти напряжения могут быть значительно снижены повышением жесткости бобышек кривошипной головки уменьшением опорных площадей головок и гаек болтов [3c.164] .
Гайки удерживаются от отворачивания только силами трения в резьбе и на опорной поверхности.
Расчет проводят на режиме максимальных оборотов холостого хода.
Болты стягивающие половинки кривошипной головки шатуна подвергаются растяжению от действия сил инерции поступательно движущихся масс поршня и шатуна и вращающихся масс расположенных над плоскостью разъема кривошипной головки.
Из расчёта кривошипной головки шатуна имеем:
максимальную силу инерции разрывающую кривошипную головку и шатунные болты:
Pjр = 002686 МН. Принимаем номинальный диаметр болта d = 14 мм шаг резьбы t = 15мм число болтов iб = 2.
Для шатунных болтов применена сталь 40ХН с содержанием углерода не менее 03%. По таблице в ([1]с.249) для легированной стали 40ХН определяем:
предел прочности ; предел текучести и усталости при растяжении-сжатии ; коэффициент приведения цикла при растяжении-сжатии .
По формулам ([1]c.248) определим отношение предела усталости при изгибе к пределу текучести:
При работе двигателя силы инерции стремятся разорвать болты. В связи с этим они должны быть затянуты настолько чтобы не была нарушена плотность соединения при действии этой силы.
Сила предварительной затяжки:
где - число шатунных болтов.
Суммарная сила растягивающая болт:
=+·= 002955 МН где = 02.
Максимальные и минимальные напряжения возникающие в болте:
где d - 14·t = 00119 м.
Среднее напряжение и амплитуды цикла:
где 42 - эффективный коэффициент концентрации напряжений (головка не имеет резких переходов концентрация напряжения в основном зависит от качественной структуры материала); 42 – теоретический коэффициент концентрации напряжения определяется по справочным данным [1]; q = 10 - коэффициент чувствительности сталей к концентрации напряжений определяется по справочным данным [1] при 1300 МПа; 096 – масштабный коэффициент; 082 – коэффициент поверхностной чувствительности определяется по справочным данным [1] (обкатка роликом).
Так как 0255 то запас прочности болта определяется по пределу усталости: =3296.
Для современных двигателей для шатунных болтов составляет 2 6.
6.1. Расчет поршневой группы(гот).doc
1. Расчет поршневой группы
К поршневой группе двигателя относятся поршень поршневые кольца и поршневой палец. Эти детали работают при высоких нагрузках от сил инерции и давления газов часто в условиях недостаточной смазки.
Наиболее напряжённым элементом поршневой группы является поршень (рис.6.1.1) воспринимающий высокие газовые инерционные и тепловые нагрузки. Его основными функциями являются: уплотнение внутрицилиндрового пространства и передача газовых сил давления с наименьшими потерями кривошипно-шатунному механизму.
Основными тенденциями совершенствования поршней современных двигателей является снижение их массогабаритных параметров повышение прочности и износостойкости а также снижение коэффициента линейного расширения что очень важно для получения минимального теплового зазора между поршнем и цилиндром без заклинивания.
Поршни автотракторных двигателей изготавливаются в основном из алюминиевых сплавов и реже из чугуна. В качестве алюминиевых сплавов использовались эвтектические сплавы алюминия с кремнием содержание которого в сплаве не превышало 12-13%. Однако постоянно растущий уровень форсирования двигателей требовал перехода на более термопрочные материалы для изготовления поршней. В настоящее время новые двигатели имеют поршни изготовленные из заэвтектических сплавов алюминия с кремнием содержание которого достигает 18% и более. Для улучшения физико-механических свойств заэвтектических сплавов применяется их легирование никелем магнием медью хромом и специальные технологии литья или горячей штамповки.
Чугунные поршни по сравнению с алюминиевыми обладают более высокими показателями твёрдости износостойкости и жаропрочности а также одинаковым коэффициентом линейного расширения с материалом гильзы цилиндра. Однако большая плотность чугунного поршня не позволяет его использовать для высокооборотных двигателей. В настоящее время все серийно выпускаемые двигатели легковых автомобилей имеют поршни из алюминиевых сплавов.
При работе двигателя температура потока горящей топливовоздушной смеси омывающая днище поршня сильно меняется от минимальной при пуске и прогреве двигателя до максимальной на режимах наибольших нагрузок. При этом максимальную температуру имеет днище поршня а минимальную юбка. С учётом такого распределения температуры профиль поршня по высоте выполняется в конической форме.
Значительная часть теплового потока от днища и огневого пояса поршня быстро уходит в стенку цилиндра через поршневые кольца и только часть теплоты передаётся в бобышки а затем и в юбку поршня. При этом отвод теплоты от бобышек значительно меньше чем от стенок юбки которые контактируют со стенками цилиндра. В результате по оси бобышек поршень расширяется значительно больше и становится овальным. Оптимальная форма поршня для вновь проектируемого двигателя подбирается в результате кропотливых и длительных экспериментов.
Наиболее общими конструктивными и технологическими направлениями при разработке поршней современных двигателей является:
- уменьшение расстояния от днища поршня до оси бобышек в целях снижения высоты и массы двигателя;
- уменьшение высоты юбки поршня и снижение веса за счёт вырезов в наименее нагруженных местах (Х-образные поршни);
- нанесение на днище и верхнюю канавку поршня износо- и термостойкого покрытия преобразующего поверхностный слой алюминия в керамику A
- снижение теплового расширения поршня за счёт заливки в его тело стальных терморегулирующих вставок;
- покрытие юбки поршня тонким (0003-0005 мм) слоем олова свинца или оловянно-свинцового сплава в целях быстрой приработки а также уменьшения трения и снижения износа;
- уменьшение внешнего и внутреннего диаметров пальцев;
- переход на плавающие пальцы малой длины с фиксацией шатуна от осевых перемещений в бобышках поршня;
- снижение высоты колец;
- применение конструктивных специальных и технологических элементов улучшающих смазку и уменьшающих износ пары: поршень-цилиндр.
Поверочный расчёт элементов поршня осуществляется без учёта переменных нагрузок величина которых учитывается при установлении соответствующих допускаемых напряжений. Рассчитывают днище стенку головки верхнюю кольцевую перемычку опорную поверхность и юбку поршня.
Для быстроходных дизелей расчетным режимом является режим номинальной мощности когда давление сгорания достигает максимального значения.
Основные конструктивные соотношения размеров элементов поршня выбираются из [1] (табл.12.1.). На основании эмпирических соотношений строится расчетная схема поршня (Рис.6.1.1).
Рис.6.1.1. Схема поршня.
Диаметр поршня: D = 120 мм;
Высота поршня: Н = 123 мм;
Расстояние от днища до оси поршневого пальца: h1 = 76 мм;
Высота кольцевых канавок: a1 = 3 мм a 2 = 3 мм a 3 = 5 мм;
Толщина днища поршня: = 15 мм;
Внешний диаметр пальца: dп = 45 мм; внутренний диаметр пальца: dв = 23 мм;
Расстояние между торцами бобышек: b = 50 мм;
Толщина стенки головки поршня: S = 12 мм;
Высота перемычек: 1 = 14 мм 2 = 9 мм 3 = 6 мм;
Глубина поршня: глубина юбки: высота бобышки:
Длина юбки: h0 = 855 мм; ширина бобышки: Вб = 72 мм;
На основании данных расчётов (теплового скоростной характеристики динамического) получили : диаметр цилиндра D = 120 мм ход поршня S = 130 мм максимальное давление сгорания Рzmax = 112 МПа при n = 2200 обмин площадь поршня Fп = 001131 м3 наибольшую нормальную силу Nмах = 0007946 МН при j = 388° массу поршневой группы mп = 294 кг частоту вращения nх.х.мах = 2400 мин-1 и l = 0274.
Материал поршня – эвтектический алюминиевый сплав с содержанием кремния около 12% 1К; материал гильзы цилиндра – серый чугун 1К.
Днище поршня проверяется на изгиб как свободно опирающаяся на цилиндр равномерно нагруженная круглая пластина.
Напряжение изгиба (МПа) в днище поршня:
где Ми= – изгибающий момент МН·м;
– момент сопротивления изгибу плоского днища м3;
= 112 МПа - максимальное давление сгорания на режиме максимального крутящего момента;
48 м - внутренний радиус днища;
МПа – для алюминиевых поршней с ребрами жёсткости.
Следовательно днище поршня должно быть усилено рёбрами жёсткости. Кроме того в целях повышения износо- и термостойкости поршня целесообразно осуществить твёрдое анодирование днища и огневого пояса что уменьшит возможности перегрева и прогоранию днища.
Толщина стенки уплотняющей части поршня проверяется на сжатие и разрыв:
где - напряжение сжатия и разрыва МПа.
Pzmax - максимальная сила давления газов на днище поршня МН
- площадь опасного сечения x-x без учета ослабления его отверстиями для отвода масла.
Рj - сила инерции головки поршня с кольцами расположение выше сечения x-x Н.
- диаметр поршня по дну канавок:
-площадь продольного диаметрального сечения масляного канала
Тогда напряжение сжатия в сечении х-х:
Рj - сила инерции возвратно-поступательно движущихся масс определяется для режима максимальной частоты вращения при холостом ходе двигателя = 2400 :
где - масса головки поршня с кольцами расположенная выше сечения x-x
где r - радиус кривошипа r = 0065 м; - угловая скорость вращения коленчатого вала при n = nмах = 2400 .
Тогда напряжение разрыва в сечении х-х:
Напряжения в верхней кольцевой перемычке:
Допускаемое напряжение в верхних кольцевых перемычках с учетом значительных температурных нагрузок находятся в пределах для поршней из алюминиевых сплавов
[] = 30 40 МПа ([1]c.261).
Удельное давление поршня на стенку цилиндра:
где - наибольшая нормальная сила действующая на стенку цилиндра при работе двигателя на режиме максимальной мощности и определяемая по данным динамического расчета (» 7946 Н при j = 388°).
Ускорение приработки юбки поршня а также уменьшение трения и снижения износа пары – юбка поршня – стенка цилиндра – достигается покрытием юбки поршня тонким (0003 0005 мм) слоем олова свинца или оловянно - свинцового сплава.
Гарантированная подвижность поршня в цилиндре достигается за счёт установления диаметральных зазоров между цилиндром и поршнем при их неодинаковом расширении в верхнем сечении головки поршня и нижнем сечении юбки .
Диаметры головки и юбки поршня с учетом монтажных зазоров:
где = 0008·D = 096 мм; = 0002·D =024 мм.
Диаметральные зазоры и между стенками цилиндра и поршня в горячем состоянии:
= D·[1+] – Dг·[1+] = 0124 мм;
= D·[1+] – Dю·[1+] = 0036 мм;
где Тц = 388К - температура стенок цилиндра; Тг = 590К - температура головки поршня;
Тю = 473К - температура юбки поршня; То = 293К - температура окружающей среды;
К 1К - соответственно коэффициенты линейного расширения материалов цилиндра (чугун) и поршня (алюминиевый сплав).
Температуры Tц = 388 К Тг = 590 К Тю = 473 К приняты с учетом жидкостного охлаждения двигателя ([1]c.262). Диаметральные зазоры г и ю между стенками цилиндра и поршня в горячем состоянии >0 значит поршень пригоден к работе то есть при достижении максимальных температур поршня и цилиндра не произойдёт их заклинивания. В этом случай нет необходимости увеличивать и и соответственно уменьшать Dг и Dю или предусмотреть разрез юбки поршня обеспечивающий компенсацию недостаточной величины зазора.
1.2. Расчет поршневых колец
Поршневые кольца работают в условиях высоких температур и значительных переменных нагрузок выполняя три основные функции:
- герметизация надпоршневого пространства в целях максимально возможного использования тепловой энергии топлива;
- отвода избыточной доли теплоты от поршня в стенки цилиндра;
- «управление маслом» т.е. рационального распределения масляного слоя по зеркалу цилиндра и ограничения попадания масла в камеру сгорания.
Выполнение этих функций на современных двигателях обеспечивает комплект колец как правило состоящий из трёх колец: двух компрессионных и одного маслосъёмного.
Наиболее нагруженным особенно в тепловом отношении является первое (верхнее) компрессионное кольцо. В качестве материала верхнего компрессионного кольца был принят серый легированный чугун. В целях повышения износостойкости на компрессионное кольцо в обязательном порядке наносится специальное износостойкое покрытие. В качестве такого покрытия используем электролитическое хромирование слоем 01 015 мм твердого хрома. В качестве профиля верхнего компрессионного кольца была выбрана схема с симметричной бочкообразной наружной поверхностью (рис.6.1.2) которая позволяет работать в наиболее тяжелых условиях.
Второе кольцо является компрессионно-маслосъемным. Оно работает в более “мягких” условиях по давлению температуре и смазке чем первое компрессионное кольцо. Кроме уплотнения надпоршневого пространства второе кольцо обеспечивает “управление маслом” снимая его со стенок цилиндра при ходе поршня вниз и осуществляя пропуск некоторого количества масла при ходе поршня вверх. В качестве материала для второго компрессионного кольца применим также серый перлитный чугун. В качестве покрытия поверхности кольца - нанесение слоя тугоплавкого и износостойкого молибдена позволяющего снизить противозадирные свойства. В качестве профиля компрессионно-маслосъемного кольца взят профиль “скребкового” типа (рис.6.1.2).
Третье кольцо – маслосъемное – обеспечивает съем масла с зеркала цилиндра и сброс его в картер через отверстия в канавке кольца. Наиболее важными качествами маслосъёмных колец являются хорошая приспособляемость к форме цилиндра и высокое давление на стенки цилиндра необходимые для эффективного съёма масла. В качестве схемы маслосъемного кольца выбрана схема коробчатого типа в виде спиральной пружины. Коробчатые кольца изготовляются из серого легированного чугуна способного длительное время работать в паре с чугунной гильзой цилиндра без специальных покрытий хотя некоторые двигатели имеют маслосъёмные кольца с хромированной наружной поверхностью. Профиль маслосъемного кольца на (рис.6.1.2).
Рис. 6.1.2. Профили компрессионных и маслосъёмных колец.
Расчёт колец заключается:
а) в определении среднего давления кольца на стенку цилиндра которое должно обеспечивать достаточную герметичность камеры сгорания и не должно резко увеличивать потери мощности двигателя на трение колец о стенки цилиндра;
б) в построении эпюры давления кольца по окружности;
в) в определении напряжений изгиба возникающих в сечении противоположном замку при надевании кольца на поршень и в рабочем состоянии;
г) в установлении монтажных зазоров в прямом замке кольца.
Силы действующие на кольцо изображены на рис.6.1.3.
Рис.6.1.3. Силы действующие на кольцо.
Материал кольца - серый легированный чугун Е = 1× МПа;
Среднее давление кольца на стенку цилиндра:
где А0 = 3·t = 165 мм;
Давление кольца на стенку цилиндра в различных точках окружности определяется по формуле:
где - переменный коэффициент определяемый изготовителем в соответствии с принятой формой эпюры давления кольца на зеркало цилиндра. Результаты расчета Р а также для различных углов приведены в таблице 6.1.1 и на рисунке 6.1.3.
По этим данным строим эпюру давлений кольца на стенку цилиндра (рис.6.1.4).
Напряжение изгиба кольца в рабочем состоянии:
Напряжение изгиба при надевании кольца на поршень:
Допустимое напряжение при изгибе кольца [] = 220 450 МПа.
Рис.6.1.4. Эпюра давлений кольца.
Монтажный зазор в замке поршневого кольца мм:
где =008 мм Тц = 388 К Тк = 493 К То = 293 К.
1.3. Расчет поршневого пальца
Поршневой палец предназначен для шарнирного соединения поршня с шатуном и является осью колебательного движения шатуна.
Во время работы двигателя поршневой палец подвергается воздействию переменных нагрузок приводящих к возникновению напряжения изгиба сдвига смятия и овализации. Вследствие высоких температур в бобышках поршня и благодаря переменному вращению поршневой палец работает в условиях полужидкостного трения что в свою очередь вызывает повышение температуры ухудшение смазки и повышенный износ трущихся пар (палец - бобышки поршня и палец - верхняя головка шатуна). В соответствии с указанными условиями работы к материалам применяемым для изготовления пальцев предъявляются требования высокой прочности и вязкости. С другой стороны палец работает в условиях высоких циклических нагрузок что требует применения вязких материалов обладающих высокой усталостной прочностью. Этим требованиям удовлетворяют цементированные малоуглеродистые и легированные никелем и хромом стали с твёрдой поверхностью и вязкой основой.([1]c.273).
В настоящее время наибольшее распространение получили плавающие поршневые пальцы которые во время работы двигателя могут проворачиваться как в бобышках поршня так и в поршневой головке шатуна. Это обеспечивает уменьшение износа плавающего пальца и его опорных поверхностей поскольку относительная скорость трущихся поверхностей примерно вдвое меньше чем при других креплениях поршневого пальца.
От осевых перемещений плавающие пальцы удерживаются стальными стопорными кольцами.
Расчёт поршневого пальца включает определение удельных давлений пальца на втулку верхней головки шатуна и на бобышки а так же напряжений от изгиба среза и овализации.
Размеры поршневого пальца намечают из условия сохранения на нём масляной плёнки а основные конструктивные соотношения размеров поршневого пальца приведены в ([1] табл.12.1.с.258).
Максимальные напряжения в пальцах бензиновых двигателей возникают при работе на режиме максимального крутящего момента.
Действительное максимальное давление сгорания Рzмах = 112 МПа при = 2200 наружный диаметр пальца =45 мм внутренний диаметр пальца = 23 мм длина пальца = 102 мм длина втулки шатуна = 46 мм расстояние между торцами бобышек =50 мм (рис.6.1.5).
Рис.6.1.5. Расчётная схема поршневого пальца.
Материал – сталь 12ХНЗА Е = 22· МПа.
Расчётная сила действующая на поршневой палец:
Удельное давление пальца на втулку поршневой головки шатуна:
Удельное давление пальца на бобышки:
Напряжение изгиба в среднем сечении пальца:
Касательные напряжения среза в сечениях между бобышками и головкой шатуна:
Наибольшее увеличение горизонтального диаметра пальца при овализации:
Рис.6.1.6. Распределение нагрузки по внешней поверхности поршневого пальца.
Напряжения овализации на внешней поверхности пальца:
в горизонтальной плоскости (точки 1 = ):
в вертикальной плоскости (точки 3 = ):
Напряжения овализации на внутренней поверхности пальца:
в горизонтальной плоскости (точки 2 = ):
в вертикальной плоскости (точки 4 = ):
Наибольшее напряжение овализации возникает на внутренней поверхности пальца в горизонтальной плоскости. Это напряжение не должно превышать = 300 350 МПа что соответствует вычисленному значению.
Расчет коленчатого вала гот.doc
Коленчатый вал – наиболее сложная в конструктивном отношении и наиболее напряжённая деталь двигателя воспринимающая периодические нагрузки от сил давления газов сил инерции и их моментов. Действие этих сил и моментов приводит к возникновению в материале коленчатого вала значительных напряжений скручивания изгиба и растяжения – сжатия. Кроме того периодически изменяющиеся моменты вызывают крутильные колебания вала которые создают дополнительные напряжения кручения.
Таким образом из-за исключительно сложных и тяжелых условий работы коленчатого вала предъявляются высокие и разнообразные требования к механическим свойствам материалов применяемых для их изготовления. Материал коленчатого вала должен обладать высокой прочностью и вязкостью большой сопротивляемостью износу и усталостным напряжениям сопротивлением действию ударных нагрузок и твердостью. Такими свойствами обладают правильно обработанные углеродистые и легированные стали а также высококачественный чугун. Коленчатые валы отечественных автомобильных бензиновых двигателей довольно широко используются литые валы из высокопрочного чугуна. Преимуществом чугунных валов является их меньшая стоимость и возможность снижения припусков на механическую обработку. Поверхности шеек чугунных валов в целях повышения их твёрдости и износостойкости обрабатываются токами высокой частоты а стальные - подвергаются азотированию на глубину 05 08 мм ([1]c.307).
Прочность коленчатого вала определяется:
- размерами и формой отдельных элементов кривошипа – коренных и шатунных шеек и щек;
- влиянием факторов понижающих прочность концентрацией напряжений возникающих в галтелях (в местах перехода от шеек к щекам) и у краев масляных отверстий в шейках;
- характеристиками прочности материала вала – пределом текучести пределами выносливости при изгибе и знакопеременном кручении;
- методами упрочнения - механическими химико-термическими и термическими обработками;
- расположением волокон зависящих от способа формирования кривошипов;
- несоосностью коренных опор картера и биением коренных шеек вызывающих упругие деформации вала и перегрузку подшипников с последующими усталостными разрушениями вала и антифрикционного слоя.
Размеры коленчатого вала рядного двигателя зависит от следующих факторов:
- числа коренных и шатунных подшипников;
- конструкции блока цилиндров (отдельные цилиндры или блоки цилиндров);
- конструкции головок цилиндров;
- типа сочленения шатунов;
- способа изготовления и материала вала ([3]c.458).
Сложная форма коленчатого вала многообразия действующих на него сил и моментов характер изменения которых зависит от жесткости вала и его опор а также ряд других причин не позволяют провести точный расчет коленчатого вала на прочность. В связи с этим используют различные приближенные методы расчета позволяющие получить условные напряжения и запасы прочности в отдельных элементах коленчатого вала ([1]c.308).
Коленчатый вал является прецизионной деталью. Все поверхности скольжения коленчатого вала должны иметь высокую частоту которая достигается суперфинишной обработкой – полированием после шлифования. Диаметр шеек вала и хвостовик обычно выдерживаются с точностью до 0015 мм а взаимное биение коренных шеек не превышает 0005 0008 мм. Для работоспособности шатунных подшипников наиболее важным является перекос осей шатунных и коренных шеек который не должен превышать 003 005 мм на длине вала. Общие требования ко всем шейкам – овальность и конусность не более 0005 мм. Для нормальной работы упорных подшипников необходимо обеспечить биение соответствующих торцевых поверхностей коленчатого вала не более 001 мм и заданный размер между ними с точностью до 0015 0025 мм.
Помимо работоспособности подшипников должна быть обеспечена и герметичность манжетных уплотнений вала. Это достигается чистотой и точностью выполнения поверхностей под передний и задний сальники (биение не более 001 мм относительно коренных шеек). Шероховатость поверхности под кромку сальника не должна быть больше Ra 016 мкм.
Задний фланец коленчатого вала и центрирующий поясок (для посадки и крепления маховика) также должны иметь допуск на биение относительно коренных шеек не более 001 мм. В противном случае маховик получает большой дисбаланс и становится невзаимозаменяемым с коленчатым валом что является нетехнологичным для ремонта.
Размеры коренных и шатунных шеек выбирают с учетом получения необходимой прочности жесткости вала и допустимых значений удельных давлений на подшипники. Сокращение длины шеек и увеличение их диаметра повышает жесткость вала и уменьшает габариты и массу двигателя. Перекрытие шеек dш.ш. + dк.ш.>2·R также повышает жесткость вала и увеличивает прочность щек.
Радиус галтелей коленчатого вала во избежание возникновения больших концентраций напряжений не должен быть менее 2 3 мм от диаметра коренной или шатунной шейки. Согласно статическим данным ширина щек коленчатого вала автомобильных двигателей изменяется в пределах (1 125)·D а толщина щек - в пределах (02 022)·D .
Сложная форма коленчатого вала многообразие действующих на него сил и моментов характер изменения которых зависит от жёсткости вала и его опор а также ряд других причин не позволяют провести точный расчёт коленчатого вала на прочность. В связи с этим используют различные приближённые методы расчёта позволяющие получить условные напряжения и запасы прочности в отдельных элементах коленчатого вала.
На основании данных динамического расчёта имеем:
коленчатый вал с симметричными коленами и с противовесами расположенными только на концах вала; центробежная сила инерции вращающихся масс КR = -27646 кН; радиус кривошипа R = 65 мм. С учётом анализа существующих двигателей а также анализа эмпирических соотношений принимаем следующие основные размеры колена вала (рис.6.3.1): коренная шейка – наружный диаметр dк.ш. = 95 мм внутренний диаметр кш = 0 мм длина шатунная шейка - наружный диаметр dш.ш. = 80 мм внутренний диаметр шш =0 мм длина расчетное сечение А-А щеки – ширина b= 129 мм толщина h= 266 мм. Материал вала – углеродистая сталь 50Г.
По таблицам справочных данных [1] определяем:
пределы прочности в = 800 МПа и текучести (условные) т = 370 МПа и т = 250 МПа;
пределы усталости (выносливости) при изгибе -1 =360 МПа
растяжении – сжатии -1р =270 МПа и кручении -1 = 198 МПа;
коэффициенты приведения цикла при изгибе α = 018 и кручении α = 008.
Определяем коэффициенты:
при изгибе: 097 и 2633;
при растяжении – сжатии: 073 и 219.
при кручении: 079 и 342.
Рис.6.3.1. Расчетная схема коленчатого вала
Величина удельного давления на рабочую поверхность шейки определяет условия работы подшипника и срок его службы. При работе подшипников стремятся не допускать выдавливания масляного слоя разрушения антифрикционного материала и ускоренного износа шеек вала.
Расчёт шеек ведётся от действия средних и максимальных результирующих всех сил нагружающих шейки. Максимальные (Rш.ш.мах и Rк.ш.мах) и средние (Rш.ш.ср и Rк.ш.ср.) значения определяют из развёрнутых диаграмм ( см. динамический расчёт).
Среднее и максимальное удельное давление на шатунную шейку:
где = 21366 Н и 93232 Н – соответственно средняя и максимальная нагрузки на шатунную шейку; 295 мм - рабочая ширина шатунного вкладыша; - радиус галтели принят равным 3 мм.
Среднее и максимальное удельное давление на коренную шейку:
где = 59466 Н – средняя нагрузка на 4-ю коренную шейку которая является наибольшей; = 99624 Н - максимальная нагрузка на 4-ю коренную шейку которая является наибольшей; 28 мм - рабочая ширина коренного вкладыша; где 0035·= 3 мм.
3.1. Расчёт коренной шейки
Коренные шейки рассчитывают только на кручение. Максимальные и минимальные значения скручивающих моментов определяют с помощью составления таблиц набегающих моментов последовательно подходящих к отдельным коренным шейкам. Для составления таблиц используют данные динамического расчёта.
Набегающие моменты скручивающие коренные шейки рассчитаны и показаны в таблице 6.3.1. Значения и взяты из таблицы 4.3. с учётом порядка работы двигателя 1л-1п-4л-2л-2п-3л-3п-4п. Порядок определения набегающих моментов показан на рис.6.3.2.
Рис.6.3.2. Схема определения набегающих моментов
на коренные шейки коленчатого вала.
Набегающие моменты и крутящие моменты отдельных цилиндров алгебраически суммируют с учётом порядка работы двигателя начиная от первого цилиндра.
Момент сопротивления коренной шейки кручению:
Максимальное и минимальное касательные напряжения знакопеременного цикла для наиболее нагруженной 3-й коренной шейки (табл.6.3.1) на которую воздействуют крутящий момент имеющий наибольший размах :
Среднее напряжение и амплитуды напряжений:
где 145- коэффициент концентрации напряжений определённый по справочным данным [1]; q = 071 - коэффициент чувствительности материала к концентрации напряжений принятый по справочным данным; = 3 - теоретический коэффициент концентрации напряжений определённый по справочным данным с учётом наличия в шейке масляного отверстия;= 06 - масштабный коэффициент определённый по справочным данным при = 95 мм; =13 - коэффициент поверхностной чувствительности определённый по справочным данным с учётом закалки шеек токами высокой частоты на глубину 2 3 мм.
Так как = 676 > = 342то запас прочности коренной шейки определяют по пределу усталости:
Полученный запас прочности соответствует требуемым значениям (n = 3 5).
3.2. Расчёт шатунной шейки
Шатунные шейки рассчитывают на кручение и изгиб. Скручивание шатунной шейки происходит под действием набегающего момента Мш.ш.i а изгиб – под действием изгибающих моментов в плоскости кривошипа Мz и в перпендикулярной плоскости Мт. Так как максимальные значения скручивающего и изгибающих моментов не совпадают по времени запасы прочности шейки от кручения и изгиба определяют независимо друг от друга а затем их суммируют определяя общий запас прочности.
Скручивающий момент действующий i-ю шатунную шейку: для двухпролётного симметричного вала Мш.ш.i = Мк.ш.i + 05(Мкр.ц.л.i+ Мкр.ц.п.i)
Для определения максимально нагруженной шейки составляют таблицу 6.3.2 набегающих моментов для каждой шатунной шейки.
Момент сопротивления кручению шатунной шейки:
На основании данных таблицы 6.3.2 определяют значения максимальных Мш.ш.i.мах и минимальных Мш.ш.i.min скручивающих моментов для наиболее нагруженной шейки.
Максимальное и минимальное касательные напряжения знакопеременного цикла для наиболее нагруженной 3-й шатунной шейки:
= 32097 Н*м =-19141 Н*м
где = 1452 и = 087 - определены при расчёте коренной шейки = 065 - масштабный коэффициент определённый по справочным данным при = 80 мм.
Так как = 10132 > = 342 то запас прочности шатунной шейки от касательных напряжений определяется по пределу усталости:
Моменты изгибающие шатунную шейку приведёны в таблице 6.3.3:
Изгибающий момент действующий на шатунную шейку в плоскости перпендикулярной плоскости колена для сечения – по оси масляного отверстия:
для среднего сечения В - В:
В плоскости колена для сечения – подсчет не производят т.к. на основании анализа полярной диаграммы и диаграммы износа масляное отверстие на шатунной шейке целесообразно сделать в горизонтальной плоскости (φм=90°) и следовательно =
Для среднего сечения В-В:
= 100821 Н*м =1473 кН
Расчет моментов и приведен в таблице 6.3.3.
Максимальные и минимальные нормальные напряжения в шатунной шейке:
=83182 Н*м =-138657 Н*м
=375481 Н*м =49509 Н*м
Среднее напряжение и амплитуда напряжений:
где 242; q = 071; = 30 и ==087 - определены при расчёте коренной шейки =069 масштабный коэффициент определённый по справочным данным при = 80 мм.
где 242; q = 071; = 30 и ==13 - определены при расчёте коренной шейки =069 масштабный коэффициент определённый по справочным данным при = 80 мм.
Запас прочности шатунной шейки от нормальных напряжений определяется:
для сечения – – по пределу усталости (при 0)
для сечения В-В – по пределу текучести т.к
Общий минимальный запас прочности шатунной шейки для наиболее нагруженного среднего сечения В-В:
Необходимый запас прочности nш.ш.= 2 3.
Щёки коленчатого вала воспринимают сложные переменные напряжения: касательные от кручения и нормальные от изгиба и растяжения – сжатия. Наибольшие напряжения возникают в местах перехода шейки в щёку в галтелях (сечение А-А рис.6.3.1).
Максимальный и минимальный моменты скручивающие щеку:
где = 13559 Н и = -22601 Н определены по табл.6.3.3.
Максимальное и минимальное касательные напряжения знакопеременного цикла щеки:
где == 265· момент сопротивления кручению прямоугольного поперечного сечения щеки - сечение А-А щеки (= 029 определён при = 485).
где =0808; q = 063 - коэффициент концентрации напряжений определённый по справочным данным [1]; =155 - теоретический коэффициент концентрации определённый по справочным данным с учётом наличия концентрации напряжений у галтели (радиус галтели принят равным 3 мм) при 011; =055 масштабный коэффициент определённый по справочным данным при = 129 мм; =07 - коэффициент поверхностной чувствительности определённый по справочным данным для необработанной щеки.
Запас прочности от касательных напряжений определяют по пределу усталости (при 0):
Максимальное и минимальное нормальные напряжения щеки:
=05· () = -277694 Н;
где значения и взяты из таблицы 4.6;
где 135; q= 063; =155 и ==07 - определены при подсчёте касательных напряжений; =062; по табл.[1] при = 129 мм.
Так как = 3039 > = 2633 то запас прочности щеки от нормальных напряжений определяют по пределу усталости:
Суммарный запас прочности щеки:
Таблица 6.3.1.(продолжение)
Таблица 6.3.2.(продолжение)
Таблица 6.3.3.(продолжение)
7 Описание конструкции .doc
Блок цилиндров отлит из легированного чугуна как одно целое с верхней частью картера в перегородках которого предусмотрены гнезда для верхних половин коренных подшипников. Картерная часть связана с крышками коренных опор поперечными болтами-стяжками образуя прочную конструкцию. Бобышки болтов крепления головки цилиндров выполнены в виде приливов к поперечным стенкам образующим рубашку охлаждения равномерно распределены вокруг каждого цилиндра.
Гильзы цилиндров "мокрого" типа легкосъемные. В соединении гильза - блок цилиндров полость охлаждения уплотнена резиновыми кольцами круглого сечения. В верхней части установлено кольцо под бурт в проточку гильзы в нижней части два кольца установлены в расточки блока.
Гильзы цилиндров отлиты из специального чугуна с перлитной структурой. Рабочая поверхность гильзы закаливается токами высокой частоты и тщательно шлифуется и полируется. Хонингованием на зеркало гильзы наносится редкая сетка впадин и площадок под углом к оси гильзы. При работе двигателя масло удерживается во впадинах что улучшает прирабатываемость цилиндро-поршневой группы.
В верхней части гильзы имеется упорный бурт нижней плоскостью которого гильза устанавливается на соответствующий упорный торец блока цилиндров. Верхний торец бурта имеет выступ предохраняющий прокладку головки цилиндров от непосредственного воздействия на нее горячих газов а выступание бурта над плоскостью блока обеспечивает надежное уплотнение газового стыка. Центрирование гильзы осуществляется при помощи двух обработанных поясов - верхнего и нижнего размещенных на ее наружной поверхности.
Нижний пояс гильзы уплотняется двумя резиновым кольцами которые устанавливаются в прокладках блока предотвращая тем самым попадание воды из водяной рубашки блока в полость масляного картера двигателя. В верхней части резиновое кольцо установлено под бурт в проточку гильзы.
Картер маховика - изготовлен из специального серого чугуна повышенной прочности и крепится болтами к заднему торцу блока цилиндров через уплотнительную прокладку из паронита. Картер представляет собой жесткую конструкцию в середине нижней части которой имеется отверстие под сальник коленчатого вала с маслоотражателем. Верхняя половина картера маховика частично закрывает детали привода механизма газораспределения и жидкостного насоса системы охлаждения.
В верхней части выполнена расточка для установки опоры привода механизма управления коробкой передач. Вверху на нижней части картера маховика справа установлены: сапун с фланцем в сборе маслозаливная горловина индукционный датчик частоты вращения и углового положения коленчатого вала фиксатор применяемый для регулирования тепловых зазоров в газораспределительном механизме. Ручка фиксатора при эксплуатации установлена в верхнем положении. В нижнее положение ее устанавливают при регулировочных работах при этом фиксатор находится в зацеплении с маховиком.
Кривошипно-шатунный механизм. КШМ включает в себя поршневые комплекты шатуны коленчатый вал и маховик. Поршень воспринимает силу давления газов кривошипно-шатунный механизм преобразует возвратно-поступательное движение поршня во вращательное движение коленчатого вала при помощи шатуна шарнирно соединённого с поршнем и кривошипом коленчатого вала.
Коленчатый вал изготовлен методом горячей штамповки (заодно с противовесами) из высокоуглеродистой стали и упрочнен азотированием. Вал предназначен для восприятия усилия передаваемого от поршней шатунами и преобразования его в крутящий момент который затем через маховик передается агрегатам трансмиссии. Коленчатый вал имеет пять коренных опор и четыре шатунных шейки которые связаны между собой щеками и сопрягаются с ними переходными галтелями. В шатунных шейках вала выполнены внутренние полости которые сообщаются с масляными каналами в коренных шейках. В этих полостях под действием центробежной силы оседают загрязнения моторного масла. Загрязняющие частицы скапливаются во втулках. Полости снаружи закрыты заглушками. На заднем конце коленчатого вала прессовой посадкой закреплена шестерня привода механизма газораспределения и масляного насоса.
Задний конец коленчатого вала в торцевой части имеет два отверстия для запрессовки штифтов фиксации маховика одно осевое отверстие для опорного подшипника первичного вала коробки передач а также резьбовые отверстия для болтов крепления маховика.
От осевых перемещений коленчатый вал зафиксирован четырьмя полукольцами установленными в проточках крышки задней коренной опоры и блока.
Полукольца изготовлены из бронзы имеют по торцам профрезерованные смазочные канавки и от проворачивания предохраняются двумя усиками имеющимися в нижних полукольцах. Усики входят в пазы которые расположены на крышке заднего коренного подшипника.
Хвостовик и носок коленчатого вала уплотнены резиновыми самоподжимными сальниками установленными соответственно в передней крышке блока цилиндров и картере маховика.
Маховик изготовлен из специального чугуна и крепится на заднем торце коленчатого вала восемью болтами из легированной стали. Момент затяжки болтов 190-200 Н*м. Болты от самоотворачивания предохраняются стопорными пластинами каждую из которых устанавливают под два болта. Точная фиксация маховика осуществляется двумя штифтами и установочной втулкой. На обработанную цилиндрическую поверхность маховика напрессован зубчатый венец нагреваемый перед напрессовкой до температуры 230°С. Зубчатый венец маховика служит для пуска двигателя стартером и изготовлен из низкоуглеродистой стали цементирован и закален. При изготовлении маховик балансируется. Максимальная несбалансированность составляет 30 г·см.
На заднем торце маховика устанавливается сцепление. На наружной поверхности маховика имеется отверстие под фиксатор маховика который используется при регулировках двигателя.
Шатун - стальной двутаврового сечения; нижняя головка выполнена с прямым и плоским разъемом. Шатун окончательно обрабатывают в сборе с крышкой поэтому крышки шатунов невзаимозаменяемые. На крышке и шатуне нанесены метки спаренности в виде трехзначных порядковых номеров. Кроме того на крышке шатуна выбит порядковый номер цилиндра. Подшипниками скольжения служат бронзовая втулка верхней головки шатуна и съемные вкладыши устанавливаемые в нижнюю головку шатуна. Крышка шатуна закреплена двумя шатунными болтами с гайками.
Вкладыши коренных и шатунных подшипников изготавливаются из стальной ленты покрытой слоем свинцовистой бронзы и тонким слоем свинцовистого сплава. Верхний и нижний вкладыши коренного подшипника невзаимозаменяемы. В верхнем вкладыше имеется отверстие для подвода масла и канавка для его распределения. Оба вкладыша нижней головки шатуна взаимозаменяемы. Для предотвращения вкладышей от проворачивания и осевых перемещений в гнездах на краях вкладышей выдавлены усы которые входят в соответствующие пазы выполненные в постелях блока и крышках коренных и шатунных подшипников.
Окончательно обработанные вкладыши перед сборкой проверяются с помощью контрольного приспособления. Прилегание наружной поверхности вкладыша к гнезду контрольного приспособления при проверке с помощью краски под соответствующей нагрузкой на стык должно обеспечивать минимальное пятно контакта 90%. Неперпендикулярность боковых торцов относительно наружной поверхности должна быть не более 02 мм. Допустимая разница вдоль оси вкладыша не должна превышать 0003 мм. Вся поверхность вкладыша и постели под ним не должна иметь вмятин забоин царапин следов коррозии.
Крышки коренных и шатунных подшипников. Изготавливаются из ковкого чугуна и закрепляются при помощи болтов. Крышки коренных подшипников кроме вертикально расположенных болтов крепления имеют и горизонтально расположенные стяжные болты. Болты крепления крышек коренных подшипников затягивают строго регламентированным моментом равным 245-250 Н*м.
Поршни отлиты из алюминиевого сплава АК-18 с вставкой из износостойкого чугуна под верхнее компрессионное кольцо. На поршне установлены два компрессионных кольца и одно маслосъемное кольцо. Компрессионные кольца в своем сечении представляют одностороннюю трапецию. Рабочая поверхность верхнего компрессионного кольца покрыта хромом нижнего - молибденом. Маслосъемное кольцо - коробчатого сечения с витым пружинным расширителем и хромированной рабочей поверхностью. В головке поршня выполнена цилиндрическая камера сгорания.
Поршень с шатуном соединены пальцем плавающего типа осевое перемещение пальца в поршне ограничено стопорными кольцами. Поршневой палец изготовлен из хро-моникелевой стали 12ХНЗА в виде пустотелого цилиндрического стержня.
Наружная поверхность поршневого пальца цементируется на глубину 10-14 мм и закаливается с нагревом токами высокой частоты. Твердость внутренней поверхности пальца HRC 20-40 и наружной - HRC 56-65.
Механизм газораспределения предназначен для управления процессами впуска в цилиндры свежего воздушного заряда и выпуска из них отработавших газов. Открытие впускных и выпускных клапанов происходит в определенных положениях поршня что обеспечивается совмещением меток на шестернях привода при его сборке.
Механизм газораспределения проектируемого двигателя - верхнеклапанный состоит из распределительного вала цилиндрических толкателей штанг коромысел возвратных пружин и клапанов.
Кулачки распределительного вала в соответствии с фазами газораспределения приводят в действие толкатели и штанги а последние через коромысла преодолевая сопротивление пружин открывают клапаны. Закрытие клапанов происходит под действием силы сжатых пружин.
Регулирование теплового зазора осуществляется регулировочными винтами установленными в коромыслах.
Распределительный вал - откован из стали 18ХГТ и установлен в развале блока цилиндров на пяти подшипниках скольжения. Привод вала осуществляется от шестерни установленной на заднем конце вала на сегментной шпонке.
Толкатели - плоские пустотелые со съемными цилиндрическими направляющими которые крепятся к блоку цилиндров.
Клапаны - впускные и выпускные - выполнены из жаропрочных сталей. Впускной клапан изготовлен из высоколегированной стали 4Х10С2М с последующей закалкой до твердости HRC 35-40. Торец стержня клапана в точке контакта с коромыслом закален на глубину 2-4 мм до твердости HRC 50-55. Выпускной клапан изготовлен из высоколегированной стали 5ХЕОН4АГ9М (ЭП-303М) с последующей закалкой до твердости HRC 30-35. К торцу стержня выпускного клапана приварен встык наконечник из стали 40ХН поверхность которого закалена на глубину 2-4 мм до твердости HRC 50-55. Поверхность рабочей фаски головки выпускного клапана наплавлена стеллитом ВЗК; твердость наплавленного слоя HRC 40-49. Диаметр головки выпускных клапанов 43 мм впускных - 45 мм.
Стержни клапанов на длине 125 мм от торца при сборке покрывают графитом для улучшения приработки. Клапаны перемещаются в металлокерамических направляющих втулках.
Для предотвращения попадания масла в цилиндр по зазору стержень клапана - направляющая втулка на втулках клапанов установлены резиновые манжеты.
Пружины клапанов - цилиндрические с равномерным шагом витков и разным направлением навивки изготовлены из пружинной стали 50ХФА. На каждом клапане установлено две пружины. Нижними торцами пружины опираются на головку через стальную шайбу верхними - в тарелку. Тарелка упирается во втулку соединенную со стержнем клапана двумя конусными сухарями. Клапанные сухари зажимаются не непосредственно верхней тарелкой пружин а через дополнительную цианированную коническую втулку. Разъемное соединение втулка - тарелка дает возможность клапанам поворачиваться относительно седла.
Привод механизма газораспределения - двухступенчатый осуществляется от хвостовика коленчатого вала блоком шестерен. От вала промежуточной шестерни привода механизма газораспределения дополнительно приводятся компрессор пневматической тормозной системы автомобиля насос гидроусилителя рулевого управления и ТНВД. От ведущей шестерни привода механизма газораспределения дополнительно приводится масляный насос системы смазки. Привод механизма газораспределения закрыт картером маховика закрепленным на заднем торце блока цилиндров.
Головки цилиндров - индивидуальные для повышения ремонтопригодности двигателя имеют полости для охлаждающей жидкости сообщающиеся с рубашкой охлаждения блока. Стык головки цилиндра и гильзы уплотнен прокладкой. В расточенную канавку на нижней плоскости головки установлено опорное кольцо которое деформируя стальную прокладку образует надежный газовый стык между головкой и блоком. Перепускные отверстия для охлаждающей жидкости и масла а также головка по контуру уплотнены формованной резиновой прокладкой.
Впускные и выпускные каналы расположены на противоположных сторонах головки. Впускной канал тангенциальный кроме подачи воздуха формирует в цилиндре проектируемого двигателя вращательное движение воздушного потока определенной конфигурации. В головку запрессованы чугунные седла и металлокерамические направляющие втулки клапанов. Головка закреплена на блоке четырьмя болтами. Механизм газораспределения закрыт крышкой через уплотнительную прокладку.
Основные системы проектируемого двигателя:
Система смазки - комбинированная с "мокрым" картером. Масло под давлением подается к коренным и шатунным подшипникам коленчатого вала к подшипникам распределительного вала компрессору пневматической тормозной системы автомобиля турбокомпрессорам системы газотурбинного наддува.
Система смазки включает масляный насос полно-поточный и частично-поточный фильтры очистки масла масляный картер двигателя водомасляный радиатор масляные каналы в блоке и головке цилиндров передней крышке и картере маховика клапаны для обеспечения нормальной работы системы контрольные приборы масляные трубопроводы и маслозаливную горловину.
Из картера через маслоприемник масло поступает в секцию масляного насоса. Из секции через канал в правой стенке блока масло направляется в полно-поточный фильтр очистки масла где очищается фильтрующим элементом а оттуда в масляный радиатор затем в главную магистраль откуда по каналам в блоке и головке цилиндров к коренным подшипникам коленчатого вала подшипникам распределительных валов к форсункам охлаждения поршней. Форсунки охлаждения поршней охлаждают днище поршня струей масла одновременно стекающее масло смазывает опоры поршневого пальца в бобышках и подшипник верхней головки шатуна. Масло снимаемое со стенок цилиндра маслосъемным кольцом отводится в поршень и также смазывает опоры поршневого пальца в бобышках и подшипник верхней головки шатуна у которой есть два отверстия для этой цели. К шатунным подшипникам коленчатого вала масло подается по отверстиям внутри вала от ближайшей коренной шейки. Остальные детали и узлы проектируемого двигателя смазываются разбрызгиванием и масляным туманом.
Масляный насос закреплен на нижней плоскости блока цилиндров.
В корпусе секции установлен предохранительный клапаны отрегулированный на давление открытия 85-95 кгссм2 и предназначенный для ограничения максимального давления на выходе из секции насоса и клапан системы смазки поддерживающий давление 40-55 кгссм2 в главной магистрали двигателя.
Фильтры очистки масла установленные на правой стороне блока цилиндров состоят из корпуса двух колпаков и сменных фильтрующих элементов соответственно. В корпусе фильтров установлен перепускной клапан с сигнализатором засоренности фильтроэлементов имеются два резьбовых отверстия для установки датчиков давления и сигнализации о недопустимом понижении (менее 07 кгссм2) давления масла в главной магистрали. Клапан пропускает неочищенное масло в масляный радиатор минуя полно-поточный фильтр при низкой температуре масла или значительном засорении фильтрующего элемента при перепаде давления на элементе 25-30 кгссм2.
Масляный картер закреплен на нижней плоскости блока цилиндров болтами. Между картером и блоком установлена прокладка для обеспечения герметичности соединения. Для предотвращения быстрого перетекания масла при ускорениях движения автомобиля в картере имеются перегородки. В нижней части картера имеется отверстие закрытое пробкой.
Система охлаждения – жидкостная с принудительной циркуляцией. Система закрытого типа т.е. сообщение с атмосферой происходит через специальные клапаны которые открываются при определенном давлении или разрежении в ней. Для компенсации изменения объема охлаждающей жидкости служит расширительный бачок.
Наиболее выгодный температурный режим работы дизеля лежит в пределах 75 98°С. Система охлаждения состоит из водяной рубашки блока и головок цилиндров водяного насоса радиатора термостатов вентилятора отключаемой гидромуфты привода вентилятора расширительного бачка соединительных трубопроводов и шлангов датчика термометра ременного привода водяного насоса. Система охлаждения заполняется антифризом ТОСОЛ-А40.
При работе дизеля охлажденная жидкость из нижнего бачка радиатора центробежным насосом подается в рубашку блока цилиндров. Омывая наружные поверхности гильз охлаждающая жидкость через отверстия в верхней плоскости блока поступает в водяные рубашки головок охлаждая в первую очередь выпускные каналы. Нагретая жидкость из головки поступает в водосборный трубопровод а затем через открытые клапаны термостатов направляется в радиатор. В радиаторе жидкость охлаждается за счет интенсивного обдува воздухом радиатора а затем вновь подается водяным насосом в рубашку охлаждения блока.
Когда дизель холодный жидкость циркулирует по малому кругу не поступая в радиатор. В этом случае обеспечивается ускоренный прогрев дизеля. Когда температура охлаждающей жидкости увеличивается и клапаны термостатов полностью открываются обеспечивается циркуляция жидкости по большому кругу т.е. через радиатор.
Система питания двигателя топливом предназначена для размещения запаса топлива на автомобиле очистки его и равномерного распределения по цилиндрам строго дозированными порциями. В ее состав входят: топливный бак фильтр грубой очистки топлива топливный насос высокого давления с топливоподкачивающим насосом фильтр тонкой очистки топлива топливопроводы форсунки указатель количества топлива в баке.
В разрабатываемом двигателе системой впрыска является аккумуляторная система Common Rail главным преимуществом которой является широкий диапазон изменений давления топлива и момента начала впрыскивания. Все это реализуется путем разделения процессов создания давления и обеспечения впрыскивания. Требования по впрыску топлива:
расширенные границы применяемости;
повышенное давление впрыскивания (до 1600 бар);
изменяемый момент начала впрыскивания;
обеспечение предварительного и дополнительного впрыскивания (даже очень позднего);
регулирование давления впрыскивания (230-1600 бар) в зависимости от условий эксплуатации автомобиля.
Аккумуляторная система Common Rail включает в себя:
контур низкого давления а также агрегаты подачи топлива;
контур высокого давления включая ТНВД топливный аккумулятор высокого давления форсунки и магистрали высокого давления;
система электронного регулирования работы дизеля датчики управления и исполнительные механизмы;
системы подачи воздуха и отвода ОГ.
Важнейшим элементом аккумуляторной системы впрыска является форсунка с быстродействующим электромагнитным клапаном. Он открывает и закрывает распылитель регулируя процесс впрыскивания топлива в каждом цилиндре. В отличие от прочих систем впрыска с управлением электромагнитными клапанами в аккумуляторной системе Common Rail впрыскивание топлива в камеру сгорания происходит при открытом электромагнитном клапане. Все форсунки подсоединены к топливному аккумулятору высокого давления отсюда и название системы. Ее модульное исполнение облегчает адаптацию к конкретному двигателю.
Действие аккумуляторной системы впрыска топлива основано на том что процессы создания высокого давления и обеспечения впрыскивания разделены. Система электронного регулирования работы дизеля раздельно управляет работой всех узлов.
Непрерывно работающий ТНВД с приводом от дизеля создает потребное давление впрыскивания обеспечивая некую постоянную величину давления в топливном аккумуляторе независимо от частоты вращения коленчатого вала и расхода топлива. Это означает что ТНВД работает в постоянном режиме с меньшими пиками крутящего момента и меньшей пиковой производительностью чем в традиционных системах впрыска. Соответственно его размеры также могут быть существенно компактнее. Регулирование давления происходит с помощью клапана регулирования давления иили управлением на входе в ТНВД. Находящееся в аккумуляторе высокого давления топливо подготовлено к впрыскиванию.
Топливо из аккумулятора по коротким магистралям высокого давления поступает к форсункам которые впрыскивают его непосредственно в камеры сгорания цилиндров двигателя. Каждая форсунка состоит в основном из распылителя и быстродействующего электромагнитного клапана который управляет распылителем через механический привод. Электромагнитные клапаны приводятся в действие сигналами от блока управления работой дизеля. Количество впрыскиваемого топлива при постоянном давлении в топливном аккумуляторе пропорционально времени включения электромагнитного клапана и не зависит при этом от частоты вращения коленчатого вала двигателя или частоты вращения вала ТНВД (регулирование впрыскивания по времени).
Основной функцией системы электронного регулирования является управление впрыскиванием дизельного топлива в нужный момент в необходимом количестве и с необходимым давлением что обеспечивает умеренный расход топлива и малый уровень шума работы дизеля.
Излишки топлива а вместе с ними и попавший в систему воздух отводятся через жиклер фильтра тонкой очистки и сливные топливопроводы в топливный бак. Просочившееся через прецизионные детали форсунок топливо по сливным топливопроводам отводится в топливный бак.
Фильтр грубой очистки топлива предназначен для предварительной очистки топлива от механических примесей относительно крупного размера. Таким образом предотвращается возможное повреждение этими частицами фильтроэлементов тонкой очистки и отрицательные последствия попадания в прецизионные детали форсунок и ТНВД неочищенного топлива.
Фильтр тонкой очистки топлива расположен на верхней правой стороне проектируемого двигателя и предназначен для очистки топлива от мелких частиц. В качестве фильтра тонкой очистки применен фильтр типа ЭТФ-3.
Система пуска включает агрегаты и отдельные детали создающие необходимую для начала работы двигателя частоту вращения коленчатого вала предусмотренную в эксплуатационных условиях.
Система вентиляции картера обеспечивает отсос из картера газов во впускной трубопровод.
Содержание.doc
Описание конструкции проектируемого двигателя ..
Тепловой расчет проектируемого двигателя .
Кинематический и динамический расчет проектируемого двигателя .
Расчет уравновешивания двигателя.
Расчет на прочность деталей двигателя .
1.Расчет поршневой группы
1.2.Расчет поршневого кольца ..
1.3.Расчет поршневого пальца ..
2.Расчет шатунной группы
2.1.Поршневая головка шатуна ..
2.2.Кривошипная головка шатуна
2.3.Стержень шатуна .
2.4.Расчет шатунных болтов
3.Расчет коленчатого вала
3.1.Расчет коренной шейки ..
3.2.Расчет шатунной шейки .
Список использованной литературы ..
Тепловой.doc
Тепловой расчёт позволяет с достаточной степенью точности аналитическим путем определить основные параметры вновь проектируемого двигателя. Тепловой расчёт даёт исходные данные для кинематического динамического расчётов а также расчётов теплонапряжённого состояния основных деталей двигателя.
1. Выбор недостающих исходных данных
Исходя из требования обеспечить приемлемые динамические качества грузового автомобиля примем что на 1 тонну его массы должна приходиться мощность 17 26 кВт. Тогда требуемая мощность двигателя:
Рабочий объём двигателя: iVh' = 1176 л.
Таким образом требуемая литровая мощность двигателя:
Полученный показатель литровой мощности может быть обеспечен только при использовании наддува. Оценим потребные давления за компрессором Рк для номинального режима и режима максимального крутящего момента приняв в соответствии с современными требованиями:
Зададимся номинальной частотой вращения .
Основные расчетные частоты вращения для дизелей:
режим минимальной частоты: .
режим наибольшего крутящего момента: .
Промежуточный режим:
Максимальная частота вращения коленчатого вала на режиме холостого хода ограниченная регулятором:
Примем степень сжатия двигателя = 16 что с одной стороны позволит избежать чрезмерных значений Рz а с другой стороны обеспечит надёжный запуск двигателя. Будем считать что в двигателе реализуется объёмное смесеобразование в неразделённых камерах сгорания.
У дизелей для обеспечения выгодного протекания ВСХ применяют прямой корректор подачи топлива с которым коэффициент избытка воздуха α возрастает по мере увеличения частоты вращения. Наименьшим значениям α соответствует частота nм при которой развивается наибольший крутящий момент. Для снижения дымности при частотах вращения n nм используется обратный корректор обедняющий смесь.
У дизелей с наддувом значения α следует задавать на 10 20% выше чем у безнаддувных – во избежание чрезмерных тепловых нагрузок на детали ЦПГ.
Характер зависимости Тr(n) формируется в основном под влиянием изменения цикловых подач топлива прямым и обратным корректорами.
Основные свойства дизельного топлива – средний элементарный состав молекулярная масса mт низшая теплотворная способность Нu теоретически необходимое количество воздуха для сгорания 1 кг топлива l0 (или L0) приведены в таблице 3.1.
Потребные значения давления Рк за компрессором для обеспечения заданной мощности Ne дизеля и характера кривой крутящего момента ориентировочно определяют в следующем порядке:
а) для номинального режима работы двигателя :
Исходя из эмпирических данных при среднем наддуве давление за компрессором:
Температура за компрессором :
=155 - показатель политропы сжатия в компрессоре
Глубина охлаждения заряда в ОНВ:
б) для режима наибольшего крутящего момента:
Давление за компрессором :
Далее строим графики потребного изменения в зависимости от частоты вращения (рис.3.1). Через полученные точки для номинального режима и режима максимального крутящего момента проводим прямые линии дающие ориентировочную форму зависимостей .
Для расчёта процессов газообмена необходимо задаться некоторыми параметрами впускной и выпускной систем. Для лучшего наполнения и очистки на каждый цилиндр устанавливается по два впускных и выпускных клапана.
Диаметр и высота подъема впускных клапанов соответственно:
Общая площадь сечения клапанных щелей:
Коэффициент гидравлического сопротивления впускного клапана:
Коэффициент расхода впускного клапана: .
Диаметр каждого выпускного клапана:
Общая площадь сечения выпускных клапанов:
Коэффициент гидравлического сопротивления выпускного клапана:
Коэффициент расхода выпускного клапана: .
2. Определение параметров рабочего тела.
Количество горючей смеси: .
Количество () отдельных компонентов продуктов сгорания обогащенной смеси (α > 1):
Общее количество продуктов сгорания ():
3. Расчёт основных процессов цикла.
Процессы газообмена.
Основная задача расчёта газообмена состоит в определении количественных и качественных показателей наполнения цилиндров свежим зарядом и очистки их от отработавших газов. Степень очистки и наполнения цилиндра определяется потерями давления свежего заряда в различных элементах впускной трассы.
Принципиальная схема впускной трассы и её важнейшие гидравлические сопротивления показаны на рис.1. Обозначения: ВО воздухоочиститель АЦП – агрегат центрального впрыска топлива Тр – впускной трубопровод Кл – впускной клапан.
Гидравлическая схема впускной системы:
Потеря давления в воздухоочистителе (МПа):
где для дизелей при работе на номинальной мощности здесь и далее .
Давление за воздухоочистителем (МПа): .
Плотность заряда за воздухоочистителем (кгм3):
Степень повышения давления в компрессоре:
- принятое значение давления за компрессором (МПа)
Температура за компрессором:
где nк – показатель политропы сжатия в компрессоре. Ориентировочно для центробежных компрессоров nк = 16 18.
Снижение давления в ОНВ:
Давление за охладителем наддувочного воздуха :
Температура заряда за ОНВ :
Потеря давления во впускном трубопроводе (МПа):
Давление во впускном трубопроводе перед клапаном (МПа): .
Средняя за процесс впуска скорость в узком сечении впускного клапана (мс): .
Плотность заряда во впускном трубопроводе перед клапаном (кгм3):
Потеря давления во впускном клапане (МПа):
Давление в цилиндре в конце впуска (МПа):
Давление остаточных газов (МПа): - давление в выпускной системе:
Зададимся подогревом заряда при впуске ΔТ от стенок впускного трубопровода (коллектора) стенок цилиндра и днища поршня. При значения ΔТ составляют: 20 30 К – у дизелей с наддувом. При подогрев ΔТ: 10 15 К у дизелей с наддувом. Изменение подогрева по частоте вращения принимается линейным.
Зададимся значением коэффициента дозарядки для каждой из расчетных частот вращения.
Коэффициент остаточных газов: .
Температура заряда в цилиндре в момент окончания впуска (К):
где - коэффициент учитывающий различие теплоемкости свежего заряда и остаточных газов.
Коэффициент наполнения характеризующий качество процессов теплообмена:
Процессы сжатия и сгорания.
Коэффициент молекулярного изменения горючей смеси: .
Коэффициент молекулярного изменения рабочей смеси: .
Теплота сгорания рабочей смеси кДжкмоль:
Средняя мольная теплоёмкость продуктов сгорания при температуре tx°C определяется выражением кДж(кмоль*К):
Мольная теплоёмкость смеси свежего заряда и остаточных газов кДж(кмоль*К):
Показатель политропы сжатия: .
Расчетное давление окончания сжатия в точке с2 (ВМТ) МПа: .
Температура окончания сжатия (К): или (°С): .
Коэффициент использования тепла при сгорании определяем основываясь на статистических данных для двигателей различных типов. Эта величина учитывает потери тепла при сгорании вызванные теплообменом со стенками цилиндра и днищем поршня диссоциацией продуктов сгорания утечками рабочего тела и др. У дизелей более высокие значения выбираются при газотурбинном наддуве способствующем созданию наивыгоднейших условий для смесеобразования и сгорания.
Задаемся максимальным давлением цикла Рz по статистическим данным. У дизелей с наддувом значения Рz увеличивают на 20 40%. Дальнейший рост Рz нежелателен по соображениям тепловой и механической напряженности деталей ЦПГ.
Степень повышения давления в цикле:
Температура ТZ в конце сгорания определяется из уравнения первого начала термодинамики записанного в виде:
Обозначив: получаем квадратное уравнение относительно tz °C:
Решение этого уравнения: ; .
Степень предварительного расширения :
Процессы расширения и выпуска.
Задаемся разностью Δ коэффициентов использования тепла в точке b() и точке z() учитывающей интенсивность подвода тепла при догорании топлива по линии расширения z-b.
Внутренняя энергия рабочего тела в точке z (кДжкмоль):
Внутренняя энергия рабочего тела в точке b (кДжкмоль): .
Степень последующего расширения :
Показатель политропы расширения:
Уравнение для показателя политропы расширения решается методом последовательных приближений с точностью до 3-го знака после запятой. В качестве начального приближения в правую часть уравнения подставляются значения n2 = 121 125 для дизелей.
Давление (МПа) и температура (К) в конце расширения:
Температура остаточных газов (К): .
Проверка совпадения с выбранными в начале расчёта значениями температуры остаточных газов Тr:
Допустимая погрешность [Δ] не должна превышать 15%.
4.Показатели цикла и двигателя в целом.
Индикаторные показатели.
Теоретическое среднее индикаторное давление цикла (МПа):
. Действительное среднее индикаторное давление (МПа) с учетом скругления диаграммы рабочего цикла: .
Индикаторный КПД: .
Удельный индикаторный расход топлива (гкВт*ч): .
Индикаторная мощность (кВт):
где iVh’ – полный рабочий объем двигателя (л) имеющего i цилиндров.
Индикаторный крутящий момент (Н*м): .
Механические потери.
Механические потери в ДВС оцениваются средним давлением механических потерь Рm которое в зависимости от средней скорости поршня Сп рассчитывается по формуле:
Значения коэффициентов ам и bм для дизелей различных типов приведены в таблице 3.2.
с неразделенными камерами сгорания
Механический коэффициент полезного действия:
Эффективные показатели.
Среднее эффективное давление цикла (МПа):
Эффективный коэффициент полезного действия:
Удельный эффективный расход топлива (гкВт*час):
Эффективная мощность (кВт):
Эффективный крутящий момент (Н*м):
Часовой расход топлива (кгчас):
Результаты вычислений представлены в таблице 3.3.
Параметры рабочего тела и остаточных газов.
Процессы впуска и выпуска.
Процесс сжатия и сгорания.
5.Построение характеристики ТНВД.
Для построения характеристики ТНВД рассчитывается массовая подача топлива в диапазоне частот вращения nmin nх nр (мгцикл):
На максимальной частоте вращения холостого хода:
- рабочий объем цилиндра
=17 ..20мг(цикл*литр) - цикловая подача топлива на режиме холостого хода в расчете на литр рабочего объема цилиндра
Характеристика ТНВД показана на Рис3.2.
6. Построение и анализ ВСХ
По результатам теплового расчета двигателя строится внешняя скоростная характеристика (ВСХ). Характер протекания ВСХ оценивается:
Коэффициентом приспособляемости:
где Меmax – максимальный крутящий момент МеN – крутящий момент при номинальной мощности.
Скоростным коэффициентом:
где nM и nN – частоты вращения коленчатого вала соответствующие максимальному крутящему моменту и номинальной мощности.
Литровой мощностью двигателя:
Чем выше Кm и ниже Кс тем лучше двигатель приспосабливается к изменению внешней нагрузки а автомобиль обладает высокими динамическими характеристиками.
Также по результатам теплового расчета строятся графики параметров процесса впуска параметров процесса сжатия и сгорания индикаторных показателей и механических потерь эффективных показателей. Строится индикаторная диаграмма цикла. Графики теплового расчета показаны на Рис. 3.3.-3.8.
Характеристика ТНВД .
Внешняя скоростная характеристика дизеля 8V 1213
Параметры процесса впуска
Параметры процессов сжатия и сгорания
Индикаторные показатели и механические потери
Эффективные показатели
Индикаторная диаграмма цикла
анализ выбора.doc
В настоящее время основным типом силовой установки грузового автомобиля или автобуса является двигатель внутреннего сгорания с воспламенением от сжатия или с принудительным воспламенением при применении газообразного топлива. Как правило это четырёхтактные двигатели с числом цилиндров до 8 и рядным или V-образным расположением цилиндров.
Основное преимущество V-образных двигателей перед однорядными такой же мощности - меньшие размеры и в первую очередь меньшая длина вследствие чего увеличена жесткость таких ответственных деталей как картера (блок – картера) крышки (головки) цилиндров и коленчатого вала. Наиболее часто применяемый угол между осями цилиндров 45-90°. Он определяется назначением двигателя требованиями к размерам и порядком работы цилиндров расположенных в одном ряду. Там где основное требование – уменьшение размеров и в первую очередь высоты этот угол может быть и больше 90°.
Современные грузовые автомобили имеют двигатели высокой мощности. Для получения таких мощностей применяется форсирование по эффективному давлению. В настоящее время наибольшее распространение среди агрегатов наддува нашли турбокомпрессоры или иначе газотурбонагнетатели. Двигатели с наддувом обладают рядом преимуществ по сравнению с безнаддувными двигателями. К ним относятся:
- низкий расход топлива
-снижение шума выхлопа так как турбина сама является хорошим глушителем шума
-применение нетрадиционных видов топлив
-меньшая токсичность по сравнению с безнаддувными двигателями и др.
Имеется также ряд недостатков:
-высокие механические и тепловые нагрузки
-менее благоприятное протекание кривой крутящего момента особенно при высоких степенях наддува
-худшая приемистость
Рост автомобильного парка неизбежно сопровождается увеличением потребления жидкого топлива нефтяного происхождения и значительным загрязнением атмосферного воздуха. В настоящее время транспорт нашей страны потребляет более половины светлых нефтепродуктов что составляет около 13 % всех энергоресурсов. Поэтому оптимизация структуры потребления автомобильным транспортом топлива нефтяного происхождения представляет одну из наиболее важных народнохозяйственных задач. Не менее острой является проблема уменьшения загрязнения окружающей среды особенно в крупных промышленных центрах. Решению этих вопросов способствует более широкое применение на автомобильном транспорте газобаллонных автомобилей работающих на сжиженном нефтяном сжатом и сжиженном природном газах а так же применение электронных систем впрыска.
В развитых капиталистических странах Европы в США и Японии суммарные энергетические затраты на эксплуатацию всех видов транспортных систем составляют от 133 до 245% совокупного потребления энергии всеми отраслями национальной экономики. В США доля потребляемого автомобилями нефтяного топлива составляет около 50 %.
Наибольшее распространение на автомобильном транспорте СНГ и СПГ получили в Японии США Новой Зеландия и Канаде а в европейских странах — в Италии ФРГ Франции Бельгии и Великобритании.
Использование СПГ является одним из важнейших направлений применения альтернативных видов топлива Национальные программы многих стран (Италии Новой Зеландии США Канады и др.) располагающих собственными месторождениями ПГ или импортирующих газовые топлива из-за рубежа предусматривают перевод значительной части автомобильного парка на топливо этого вида. Широкое распространение СПГ находит и на автомобильном транспорте стран — членов СЭВ.
Масштабы использования ПГ в качестве топлива для автомобильных двигателей в зарубежных странах зависят от соотношения цен на жидкое и газовое топливо а также от требований максимального использования собственных ресурсов и сведения к минимуму зависимости от конъюнктуры рынка на нефтепродукты.
Анализируя выше сказанное выбираем восьмицилиндровый V-образный двигатель. Такая схема поможет нам уменьшить длину двигателя не меняя его объем.
Применим систему впрыска непосредственно в цилиндр и электронное управление системой впрыска. Характерной особенностью систем впрыска с электронным управлением является относительно малое количество подвижных частей что обеспечивает их высокую надёжность и стабильность работы.
В качестве прототипов выбираем двигатели автомобилей параметры и показатели которых представлены в таблице 1.1.
При выборе прототипов были соблюдены следующие условия:
- рабочий объем аналога
- аналоги представляют заводы производители из разных стран;
- показатели рабочего процесса прототипов отражают современный уровень двигателестроения.
Аналогом проектируемого двигателя является двигатель зарубежного или отечественного производства имеющий такой же или близкий рабочий объём и назначение. Рабочий объём рассчитываемого двигателя iVh' = 11760 см3.
Исходя из его назначения в качестве аналогов выбираем двигатели:
Kenwqrth T400B – рядный 6-цилиндровый жидкостного охлаждения рабочим объёмом iVh' = 10824 см3.
KD3744.10 – V-образный 8-цилиндровый типа 8V 12125 воздушного охлаждения рабочим объёмом iVh' = 11310 см3.
F8L 413F- V-образный 8-цилиндровый типа 8V 12513 воздушного охлаждения рабочим объёмом iVh' = 12763 см3.
КАМАЗ-820.53-260- V-образный 8-цилиндровый типа 8V 1213 жидкостного охлаждения рабочим объёмом iVh' = 11760 см3.
TV8.640- V-образный 8-цилиндровый типа 8V 11761207 жидкостного охлаждения рабочим объёмом iVh' = 10500 см3.
Технические данные прототипов представлены в таблице 1.1.
Наименование обозначение
Номинальная мощность Ne
Номинальная частота вращения nN
Максимальный крутящий момент Меmax
Частота вращения соответствующая Меmax nM
Коэффициент приспособляемости Km
Скоростной коэффициент Kс
Удельный расход топлива на номинальном режиме ge
Среднее эффективное давление Ре
Средняя скорость поршня на номинальном режиме Сп
Литровая мощность Nел
Удельная поршневая мощность Nеп
динам..dwg

Полярная диаграмма сил
действующих на шатунную шейку
Графики динамического
ДВС ПК 2504.05.00.00.
тепл. расч..dwg

Показатели процесса впуска
сгорания и расширения
Эффективные показатели
Индикаторная диаграмма цикла
и механические потери
ДВС ПК 2504.05.00.00
крит костина.doc
в горизонтальной плоскости (точки 2 = ):
в вертикальной плоскости (точки 4 = ):
Наибольшее напряжение овализации возникает на внутренней поверхности пальца в горизонтальной плоскости. Это напряжение не должно превышать = 300 350 МПа что соответствует вычисленному значению.
1.4. Критерий Костина
Вычислим критерий Костина позволяющий оценить удельную тепловую напряженность поршня в зависимости от параметров рабочего процесса и режима работы двигателя:
где b = 424 – коэффициент при неразделенной КС;
сm = 64 мс – средняя скорость поршня;
hv = 0982 – коэффициент наполнения;
рК = 0194 МПа – давление перед впускными органами;
ТК = 325 К – температура перед впускными органами;
ре = 1089 МПа – среднее эффективное давление;
gе = 0389 кгкВт·ч – удельный эффективный расход топлива;
Т0 = 293 К – начальная температура.
кин.1.doc
1. Кинематический расчёт двигателя
Кинематический и динамический расчет проводится для номинального режима при n = 2200 мин-1 так как на данном режиме сумма сил инерции от возвратно - поступательно движущихся масс и газовых сил наибольшая.
Диаметр поршня: D = 120 мм;
Ход поршня: S = 130 мм;
Радиус кривошипа: r = 65 мм;
Частота вращения коленчатого вала: n = 2200 обмин.
Рис.4.1. Схема кривошипно-шатунного механизма.
На рис.4.1. приведены основные обозначения центрального кривошипно-шатунного механизма: s φ — угол поворота кривошипа (ОВ) отсчитываемый от оси цилиндра (А`О) в направлении вращения коленчатого вала по часовой стрелке (точка О — ось коленчатого вала; точка В — ось шатунной шейки; точка А` — ВМТ); — угол отклонения оси шатуна (АВ) от оси цилиндра; — угловая скорость вращения коленчатого вала; R = ОВ — радиус кривошипа; S = 2R = A`A`` — ход поршня (точка А``— НМТ); Lш = АВ — длина шатуна; λ = RLш — отношение радиуса кривошипа к длине шатуна; R+Lш = А`О — расстояние от оси коленчатого вала до ВМТ.
Недостающие исходные данные:
Отношение радиуса кривошипа к длине шатуна: 029.
Длина шатуна: l = 223 мм.
Площадь поршня: = 001131
Перемещение поршня: м
График перемещения поршня SX показан на Рис.4.2.
Скорость поршня: мс
График скорости поршня VП показан на Рис.4.3.
где – угловая скорость вращения коленчатого вала: =23038 радс
Ускорение поршня: мс2
График ускорения поршня j показан на Рис.4.4.
Результаты кинематического расчета приведены в таблице 4.1.
2. Динамический расчёт
Анализ сил действующих в кривошипно-шатунном механизме необходим для расчета деталей двигателя на прочность и для определения нагрузок на подшипники. Его проводят для определенного режима работы двигателя.
Динамический расчет кривошипно–шатунного механизма заключается в определении суммарных сил и моментов возникающих от давления газов и сил инерции. По этим силам рассчитывают основные детали на прочность и износ а также определяют неравномерность крутящего момента и степень неравномерности хода двигателя. Во время работы двигателя на детали кривошипно–шатунного механизма действуют силы давления газов в цилиндре силы инерции возвратно–поступательно движущихся масс центробежные силы давление на поршень со стороны картера и силы тяжести (пренебрегаем).
Приведение масс частей кривошипно-шатунного механизма.
Для дизелей конструктивная масса шатуна:
0 ..400 примем 300 .
Конструктивная масса поршня:
В массу поршневого комплекта входит масса поршня поршневых колец поршневого пальца.
Масса шатуна и поршня (вместе с массой колец и пальца):
Приведённая масса неуравновешенных частей одного колена:
0 400 кгм2 примем 320 кгм2
Масса неуравновешенных частей одного колена: =362 кг
Масса шатуна сосредоточенного на оси поршневого пальца: =093 кг
Масса шатуна сосредоточенная на оси кривошипа: =246 кг
Массы совершающие возвратно-поступательные движения: =387 кг
Массы совершающие вращательное движение: = 854 кг
Полные силы инерции.
Сила давления (МН) газов на поршень: Н
где P – давление газов в цилиндре МПа [из теплового расчета];
Р0 – атмосферное давление P0 = 01013 МПа.
Сила инерции от возвратно-поступательно движущихся масс: H
Суммарные силы действующие в кривошипно-шатунном механизме: Н
Графики силы инерции силы давления газов суммарной силы PΣ показаны на Рис.4.5.
Центробежная сила инерции вращающихся масс:
Центробежная сила инерции вращающихся масс шатуна:
Центробежная сила инерции вращающихся масс кривошипа:
Результаты расчетов сил и сведены в таблицу 4.2.
График боковой силы N показан на Рис.4.6.
где - угловое перемещение шатуна: градусов
Сила действующая вдоль шатуна: Н
График силы действующей вдоль оси шатуна S показан на Рис.4.6.
Сила направленная по радиусу кривошипа: H
График радиальной силы K показан на Рис.4.7.
Тангенциальная сила направленная по касательной к окружности радиуса кривошипа:
График тангенциальной силы T показан на Рис.4.7.
Сила К считается положительной если она сжимает щёки колена.
Сила Т принимается положительной если направление создаваемого ею момента совпадает с направлением вращения коленчатого вала.
Результаты расчетов сил сведены в таблицу 4.3.
По величине Т определяют крутящий момент одного цилиндра:
Результат расчета крутящего момента одного цилиндра сведен в таблицу 4.3.
Для построения кривой суммарного крутящего момента Mкр двигателя графически суммируют кривые моментов каждого цилиндра сдвигая одну кривую относительно другой на угол поворота кривошипа между вспышками. Так как величина и характер изменения крутящего момента по углу поворота коленчатого вала всех цилиндров двигателя одинаковы и отличаются лишь угловыми интервалами равными угловым интервалам между вспышками в отдельных цилиндрах то для подсчета суммарного крутящего момента двигателя достаточно иметь кривую крутящего момента одного цилиндра.
Период изменения крутящего момента четырехтактного двигателя с равными интервалами между вспышками с числом цилиндров i = 8:
Расчет крутящего момента двигателя сведен в таблицу 4.4.
Графики крутящего момента одного цилиндра Мкр ц крутящего момента двигателя Мкр и среднего крутящего момента двигателя показаны на Рис 4.8.
Максимальное и минимальное значения крутящего момента двигателя (Рис 4.8.):
Мкр.max=2407 Н*м Мкр.min= -221 Н*м
Силы действующие на шатунные шейки коленчатого вала от одного шатуна.
Полярную диаграмму силы S действующей на шатунную шейку строят графическим сложением векторов сил К и Т (Рис 4.9.). Диаграмма силы S с центром в точке Ош является полярной диаграммой нагрузки Rш.ш на шатунную шейку от действия одного шатуна. По значениям силы Rш.ш для различных φ снятых с полярной диаграммы или вычисленных по формуле строят диаграмму Rш.ш в прямоугольных координатах (Рис 4.10.).
Результирующая сила действующая на шатунную шейку: Н
Результаты расчета результирующей силы сведены в таблицу 4.3.
По развернутой диаграмме Rш.ш (Рис 4.10.)определяют Rш.ш ср Rш.ш max Rш.ш min:
Rш.ш ср = 2136551 Н Rш.ш max = 9323186 Н Rш.ш min= 848 Н
По полярной диаграмме строят диаграмму износа шатунной шейки (Рис. 4.11.). По диаграмме износа определяют положение оси масляного отверстия (90°).
Условные силы действующие на шатунные шейки от двух смежных шатунов.
В соответствии с порядком работы двигателя на 1 2 и 3-ю шатунные шейки одновременно действуют силы от левого и правого шатунов смещенные одна относительно другой на 90° а на 4-ю шейку действуют силы от левого и правого шатунов смещенные на 450°.
Суммарные тангенциальные силы действующие на шатунные шейки от двух смежных шатунов: кН
Суммарные силы действующие на шатунные шейки по радиусу кривошипа от двух смежных шатунов: кН
Условные нагрузки на 1 2 и 3-ю шатунные шейки - и на 4-ю шатунную шейку - рассчитываются по формулам:
Расчет сил сведен в таблицу 4.5. а - таблицу 4.6.
По значениям сил и для различных φ вычисленных по формуле строят диаграммы и в прямоугольных координатах (Рис. 4.12.)
По развернутым диаграммам определяют:
15 кН 8396 кН 1078 кН
78 кН 8451 кН 1931 кН
Силы действующие на колена вала.
Суммарные силы действующие на колена вала по радиусу кривошипа:
Нагрузки на колена вала рассчитывают по формулам:
Силы действующие на коренные шейки.
Силы действующие на 1-ю и 5-ю коренные шейки:
Силы действующие на 2-ю и 3-ю коренные шейки и ориентированные относительно первого кривошипа:
В соответствии с порядком работы двигателя силы действующие на 2-й кривошип смещены относительно сил действующих на 1-й кривошип на 270° УПКВ а силы действующие на 3-й кривошип – на 450° УПКВ.
Сила действующая на 4-ю коренную шейку:
Результаты расчетов сил сведены в таблицу 4.7.
По значениям сил для различных φ вычисленных по формуле строят диаграммы в прямоугольных координатах (Рис.4.13.)
По этим диаграммам определяют:
для 1-й коренной шейки
48 кН 3681 кН 264 кН
для 2-й коренной шейки
09 кН 5373 кН 259 кН
для 3-й коренной шейки
48 кН 5845 кН 293 кН
для 4-й коренной шейки
47 кН 9962 кН 678 кН
для 5-й коренной шейки
23 кН 3647 кН 941 кН
кин.3.doc
(23)-я шатунная шейка
Таблица 4.5.(продолжение)
Таблица 4.6.(продолжение)
Таблица 4.7.(продолжение)
кин.2.doc
Таблица 4.4.(продолжение)
Полярная диаграмма нагрузки на шатунную шейку.
Диаграмма износа шатунной шейки
Рекомендуемые чертежи
- 29.07.2014
- 06.06.2023