Абсорбция углекислого газа водой


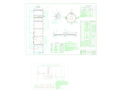
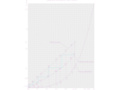
- Добавлен: 25.01.2023
- Размер: 611 KB
- Закачек: 0
Узнать, как скачать этот материал
Подписаться на ежедневные обновления каталога:
Описание
Абсорбция углекислого газа водой
Состав проекта
![]() |
![]() ![]() ![]() |
![]() ![]() ![]() ![]() |
![]() ![]() ![]() ![]() |
![]() |
Дополнительная информация
Контент чертежей
Приложение В и чертеж колонны.dwg

Приложение Б.dwg

Рекомендуемые чертежи
- 30.05.2022
Свободное скачивание на сегодня
Обновление через: 15 часов 3 минуты