Проектирование сборочного узла зубчатой передачи


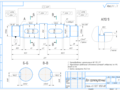
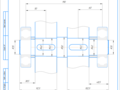
- Добавлен: 04.11.2022
- Размер: 2 MB
- Закачек: 0
Узнать, как скачать этот материал
Подписаться на ежедневные обновления каталога:
Описание
Курсовой проект - Проектирование сборочного узла зубчатой передачи
Состав проекта
![]() |
![]() ![]() ![]() |
![]() ![]() ![]() |
![]() ![]() ![]() |
Рекомендуемые чертежи
- 24.01.2023
- 21.05.2023
Свободное скачивание на сегодня
Обновление через: 15 часов 12 минут