Проектирование предприятия по капитальному ремонту топливной аппаратуры комбайнов


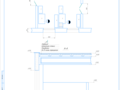
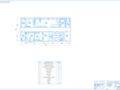
- Добавлен: 04.11.2022
- Размер: 712 KB
- Закачек: 0
Подписаться на ежедневные обновления каталога:
Описание
Курсовой проект - Проектирование предприятия по капитальному ремонту топливной аппаратуры комбайнов
Состав проекта
![]() |
![]() ![]() ![]() ![]() |
![]() ![]() ![]() |
![]() ![]() ![]() |
Дополнительная информация
Контент чертежей
План предприятия.cdw

Наружной очистки и мойки
Разборочно-сборочный
Дефектовочно-комплектовочный
Административные помещения
СГАУ Б-АИ-41.04.000 ПП
по капитальному ремонту
топливной аппаратуры
План участка.cdw
цементно-песчанного раствора
СГАУ Б-АИу-41.04.000
разборочно-сборочного
Условные обазначения
- отвод в канализацию
- подвод холодной воды
Проектирование предприятий КП РПЗ.docx
ФГБОУ ВО Саратовский ГАУ
Кафедра «Техническое обеспечение в АПК»
по дисциплине: «Проектирование предприятий технического сервиса»
Проектирование предприятия по капитальному ремонту топливной аппаратуры комбайнов
Обоснование и расчет организационных параметров предприятия 6
Расчет и компоновка главного корпуса предприятия .24
Проектирование строительных элементов 27
Технико-экономическое обоснование проекта . 30
Список литературы . ..34
Рост машинотракторного парка сельского хозяйства при интенсификации его использования предъявляет большие требования к дальнейшему развитию ремонтной базы сельского хозяйства которая призвана обеспечить качество ремонта и обслуживания техники постоянную работоспособность всего парка машин.
На ремонтно-технических предприятиях предусматривается как правило проведение всех капитальных ремонтов и технических уходов машин. Все ремонтно-технические предприятия и мастерские хозяйств должны быть обеспечены современными металлорежущими станками ремонтно-технологическим оборудованием приборами приспособлениями и инструментам. На ремонтно-технических предприятиях необходимо внедрять индустриальные методы ремонта совершенствовать организацию труда все это обеспечивает высокое качество ремонта и высокую производительность труда.
В ремонтно-технических предприятиях должны быть четко налажены планирование контроль и учет всех работ объектов их загрузки. Ремонт машин необходимо производить с равномерной загрузкой в течение всего года. Главными направлениями в развитии ремонтной базы сельского хозяйства являются:
- развитие специализации – создание ремонтных предприятий не только по ремонту тракторов автомобилей комбайнов их агрегатов и узлов но и по ремонту свеклоуборочных силосоуборочных машин и других сложных сельскохозяйственных машин.
- внедрение широкой кооперации между ремонтно-техническими предприятиями по ремонту агрегатов и машин создание межобластных и межреспубликанских связей кооперирования по ремонту двигателей тракторов комбайнов и других объектов а также восстановлению деталей.
- широкое внедрение агрегатного метода ремонта машин за счет внедрения механизированного инструмента автоматизации отдельных технологических процессов. Техническое обслуживание машинно-тракторного парка осуществляется общими силами и с помощью районных ремонтно-технических предприятий на основе хозяйственных договоров. Применение современных средств технического обслуживания машинно-тракторного парка позволяет значительно улучшить условия труда механизаторов повысить производительность труда и снизить себестоимость ремонта.
В данном курсовом проекте необходимо спроектировать предприятие по ремонту топливной аппаратуры комбайнов: Енисей-1200 в количестве 470 штук СК-5М-1 – 490 штук Дон-1500 – 480 и обосновать его экономическую эффективность.
ОБОСНОВАНИЕ И РАСЧЕТ ОРГАНИЗАЦИОННЫХ ПАРАМЕТРОВ ПРЕДПРИЯТИЯ
1 Годовая программа предприятия технического сервиса
Годовая производственная программа проектируемого предприятия в рублях произведенной продукции представлена в Таблице 1.
Таблица 1. Годовая программа и стоимость ремонта
Наименование объекта ремонта
Комплект топливной аппаратуры комбайна Енисей-1200
Комплект топливной аппаратуры комбайна СК-5М-1
Комплект топливной аппаратуры комбайна Дон-1500
Специализированные предприятия или цехи по ремонту комбайнов и
других сложных сельскохозяйственных машин и их частей проектируют и
строят сравнительно небольшими. Это объясняется тем что число этих
машин невелико а транспортировка их на большие расстояния представ-
ляет известные трудности. Предприятия выполняют текущий и капиталь-
ный ремонт используя преимущественно готовые агрегаты получаемые
по кооперации с других ремонтных предприятий. Эти специализированные предприятия капитально ремонтируют отдельные агрегаты и узлы машин для нужд текущего ремонта который проводят сами хозяйства в ЦРМ.
Кроме того такие предприятия обычно оснащены оборудованием для ре-монта и других сложных машин и их составных частей а не только тех на
которых они специализируются.
Характеристика объектов ремонта.
Дизельная топливная аппаратура разделяется на приборы двух групп из которых первая предназначена для хранения и очистки топлива вторая – для его подачи дозирования и впрыска. К первой группе относятся расходный топливный бак отстойник с фильтром грубой очистки топлива фильтр тонкой очистки и топливопроводы низкого давления. Сюда же входит и подкачивающий насос с насосом ручной подкачки.
Ко второй группе относятся топливный насос с регулятором форсунка и топливопроводы высокого давления.
Комплект топливной аппаратуры Енисей-1200 Дон-1500 СК-5М-1.
В систему питания топливом дизелей СМД-23(Енисей-1200) СМД-31(Дон-1500) и СМД-21(СК-5М-1) входят топливный бак фильтры грубой и тонкой очистки топливоподкачивающий насос и топливный насос с регулятором и ограничителем дымления форсунки топливопроводы высокого и низкого давления. Унифицированы (применяются на обоих типах дизелей) фильтр грубой очистки топлива (ФТ-75) фильтр тонкой очистки топлива (ФТ-150А) форсунка 39.1112010 и ограничитель дымления.
Рис.1. Схема системы питания топливом дизеля СМД-23: 1 – топливный насос; 2 – перепускной клапан в сборе; 3 – топливопроводы высокого давления; 4 – форсунки; 5 – топливопровод слива дренажного топлива из первой форсунки; 6 – впускная труба; 7 – топливопровод подвода чистого топлива к топливному насосу; 8 – топливопровод подвода топлива от топливоподкачивающего насоса к фильтру тонкой очистки; 9 – фильтр тонкой очистки топлива; 10 – клапан удаления воздуха (в сборе); 11 – топливопровод слива избыточного топлива и выпуска воздуха в бак; 12 – топливопровод слива дренажного топлива из второй третьей и четвертой форсунок; 13 – впускной коллектор; 14 – трубка подвода воздуха к ограничителю дымления; 15 – топливный бак; 16 – фильтр грубой очистки топлива; 17 – топливопровод перепуска топлива из головки топливного насоса в топливоподкачивающий насос; 18 г топливопровод от фильтра грубой очистки к топливоподкачивающему насосу; 19 – топливоподкачивающий насос
Рис. 2. Схема питания топливом дизеля СМД-31: 1 – клапан-демпфер; 2 – топливопровод перепуска избыточного топлива из головки топливного насоса; 3 – топливопровод подвода топлива от подкачивающего насоса к фильтру тонкой очистки; 4 – топливопровод слива топлива из первой и второй форсунок; 5 – впускная труба турбокомпрессора; 6 – топливопровод подвода чистого топлива к топливному насосу; 7 – фильтр тонкой очистки топлива; 8 – топливопровод слива дренажного топлива из третьей четвертой пятой и шестой форсунок; 9 -впускной коллектор; 10 – форсунка; 11 – трубка подвода воздуха к ограничителю дымления; 12 – топливопровод слива топлива и выпуска воздуха в бак; 13 – топливный бак; и – топливопровод от топливного бака к фильтру грубой очистки; 15 -фильтр грубой очистки; 16 – топливопровод от фильтра грубой очистки к подкачивающему насосу; 17 – подкачивающий насос; 18 – топливный насос высокого давления; 19 – топливопроводы
Устройство топливной системы двигателя СМД-21(СК-5М-1) аналогично системе двигателя СМД-23. Из бака топливо поступает в фильтр грубой очистки где освобождается от воды и механических примесей размером более 009 мм. Далее с помощью топливоподкачивающего насоса оно направляется в фильтр тонкой очистки где происходит окончательная фильтрация топлива. После этого оно поступает в топливный насос высокого давления (ТНВД) откуда по топливопроводам топливо поступает к форсункам и впрыскивается в камеру сгорания.
2 Схема технологического процесса ремонта
При разработке схемы технологического процесса учитываются конструктивные и технологические особенности обслуживаемого или ремонтируемого объекта значение годовой производственной программы предприятия. Ремонт деталей приборов системы питания в АТП сводится к работам по их восстановлению не требующим сложного оборудования. К ним относятся притирка рабочих поверхностей клапанов и их седел запорных игл и распылителей форсунок плунжерных пар замена потерявших упругость пружин восстановление целости трубопроводов резьб заделка трещин в корпусах поплавках и др. Схема технологического процесса ремонта топливной аппаратуры комбайнов представлена на схеме. Здесь мы имеем следующие операции по ремонту: слесарные станочные кузнечно-термические сварочно-наплавочные и гальванические. Слесарный и станочный ремонт предполагаетпроверку и регулировку элементов топливной аппаратуры. В кузнечно-термических операциях проводят кузнечные работы по ремонту а так же необходимую закалку. Для восстановления определенных деталей сваркой и наплавкой производят сварочно-наплавочные операции и на гальванических операциях производят ремонт детали нанесением гальванического покрытия.
3 Производственная структура предприятия технического сервиса
Производственная структура предприятия технического сервиса зависит от годовой производственной программы марки обслуживаемого или ремонтируемого объекта особенностей организации производственного процесса и применяемой технологии в соответствии с которыми составляется перечень подразделений основного и вспомогательных производств.
На основании схемы технологического процесса определяем состав предприятия (см. Табл. 2)
Таблица 2. Производственная структура предприятия
Наименование участка
Сборочно-разборочный
Дефектовочно-комплектовочный
Кузнечно-термический сварочно-наплавочный
Административные помещения
4 Расчет годового объема работ по предприятию
Годовая трудоемкость ремонтных работ по предприятию определяется по формуле:
Туд – удельная трудоемкость одного ремонта (см. [1] Туд =105чел.-ч);
Rг – годовая производительность программы (см. исходные данные);
K – поправочный коэффициент зависящий от программы (см. Прил. К=1).
Тг =105·1440· 1= 15120 чел-ч
Общая годовая трудоемкость по всем маркам будет равна
Тг = Тi = 15120 чел-ч.(1.2)
Годовые объемы работ по участкам в процентах от общего сведем в таблицу (см. Табл. 3). Распределение по видам работ осуществляется в соответствии с процентным распределением (см. Прил. 3). Операции схожие по выполнению объединяем в одно наименование работ и складываем их процентное распределение.
Таблица 3. Распределение ремонтных работ по видам
Сборочно-разборочные
5 Режимы работы предприятия и расчет фондов времени
Режим работы предприятия зависит от продолжительности рабочей смены (в часах) и количества смен.
Для расчетов принимаем следующие режимы работы предприятия: смен – одна продолжительность рабочей смены – 8 ч. количество рабочих дней в неделе – 5.
Фонд времени рабочего определяется планируемым временем работы одного человека в течении определенного периода. Различают номинальный и действительные фонды.
Номинальный фонд времени рабочего (Фнр) характеризуется максимально возможным временем его работы в течении определенного периода и рассчитывается по пятидневной рабочей неделе по формуле:
Фнр = (dк – dв – dп) t – dпп (1.3)
где dK dB dП dП.П – соответственно число календарных выходных праздничных и предпраздничных дней;
t – продолжительность рабочей смены ч.
Принимаем число выходных дней – 104 праздничных – 11 предпразднечных – 8. Отсюда:
Фнр = (365 – 104 – 11) 8 – 8 = 1992 ч.
Действительный фонд рабочего времени (Фдр) является временем фактической его работы в течении определенного периода и рассчитывается при пятидневной рабочей неделе по формуле:
Фдр = (dк – dв – dп – dо) tk – dппk (1.4)
где dо – продолжительность отпуска рабочего за планируемый период дней;
k = 096 – коэффициент учитывающий вынужденные потери времени по болезни и другим уважительным причинам.
Длительность отпуска рабочих зависит от их специальности и рода работ. В соответствии с действующим законодательством при обычных ремонтных операциях полагается отпуск в течение 24 рабочих дней в году. В горячих отделениях (сварочном кузнечном и др.) длительность отпуска увеличивается до 36 рабочих дней в году.
Фдр = (365 – 104 – 11 – 24) 8 096 – 8 096 = 1728 ч;
Фдр = (365 – 104 – 11 – 36) 8 096 – 8 096 = 1696 ч.
Фондом рабочего времени оборудования называют время в течении которого оно может быть занято работой.
Действительный фонд рабочего времени оборудования (Фо) определяют по выражению:
Фо = [(dK – dB – dП) t – dП.П] n kO (1.5)
где kO = 095 – коэффициент учитывающий простой оборудования;
n – количество смен.
Фо = [(365 – 104 – 11) 8 – 8] 1 095 = 1892 ч.
Фонд времени рабочего места участка отделения предприятия (ФРМ) – это плановое число часов их работы в течении определенного периода:
ФРМ = [(dK – dB – dП) t – dП.П] n (1.6)
ФРМ = [(365 – 104 – 11) 8 – 8] 1 = 1992 ч.
6 Определение штатов предприятия
Списочный состав производственных рабочих определяется по формуле:
Явочный состав производственных рабочих определяем по формуле:
Необходимое количество производственных рабочих по профессиям на каждом участке определяется по формуле:
где ТГ – годовая трудоемкость на участке ч.;
ФДРП – действительный годовой фонд времени рабочего данной профессиич.
Данные по расчету количества рабочих заносятся в Табл. 4
Таблица 4. Расчет количества производственных рабочих
Количество вспомогательных рабочих рассчитывается по формуле:
P1 = (014 017) PП (1.10)
где РП – число производственных рабочих чел.
P1 = 015 11 = 165 2 чел.
Число младшего обслуживающего персонала (МОП) составляет 1 3% от общего числа производственных рабочих число счетно-конторского персонала (СКП) – 3 4% число инженерно-технических работников (ИТР) – 13 15% количество контролеров ОТК определяется в соответствии с нормой: один человек на 15 20 производственных рабочих.
Структура предприятия принята безцеховая так как количество рабочих менее 200 следовательно начальников цехов не будет.
Данные по расчету сотрудников предприятия сведены в Табл. 5
Таблица 5. Штаты предприятия
Категория работающих
Количество работающих чел.
Производственные рабочие
Вспомогательные рабочие
7 Расчет количества оборудования и рабочих постов
Количество оборудования и рабочих мест рассчитывается в соответствии с технологическим процессом трудоемкостью выполняемых работ тактом работы и фондом времени.
Расчет количества оборудования для моечно-очистительных работ
Число моечных машин для наружной очистки определяют по формуле:
Количество моечных машин для очистки сборочных единиц и деталей:
где R – суммарное количество единиц проходящих наружную очистку в течении года;
Q – суммарная масса сборочных единиц и деталей подлежащих очистке в течении года m=15кг;
qm – производительность моечной машины едч;
qч – годовая производительность моечной машины тч;
Км – коэффициент учитывающий использование моечной машины по времени (Км = 085);
Кзв – коэффициент учитывающий степень загрузки и использования моечной машины по времени (Кзв = 065 075).
Принимаем для очистки сборочных единиц и деталей машин установку М-204
Принимаем для наружной очистки машину ОРГ-5361-03
Расчет рабочих мест для разборочно-сборочных работ
Для разборки и сборки топливной аппаратуры при годовой программе 1440 штук целесообразно применить ремонт без поточной линии так как такт ремонта слишком высок. При такой организации труда число рабочих мест определяется по формуле:
где Tразб(сб) – суммарная трудоемкость разборных и сборочных работ в год чел-ч.
Количество рабочих мест разборки-сборки определяется по формуле:
Расчет количества рабочих мест дефектации и комплектации
Количество рабочих мест дефектации и комплектации определяется по формуле:
где Тдеф(Комп) – общая годовая трудоемкость дефектовочно-комплектовочных работ чел-ч;
РСР – средняя плотность работ (РСР = 12 16).
Расчет количества оборудования для слесарно-станочных работ
В случае когда известна трудоемкость по видам работ расчет числа станков ведут по формуле:
гдеТст - общая годовая трудоемкость станочных работ чел-ч;
Кст - коэффициент загрузки станка по времени (Кст=085.. .09).
Расчет количества оборудования для термических работ
Количество оборудования для термических работ определяется по формуле:
где ТТ – общая трудоёмкость термических работ чел-ч.
Расчёт количества оборудования для гальванических работ
Количество оборудования для гальванических работ определяется по формуле:
где ТГ – общая трудоёмкость ремонта гальваническими материалами чел-ч.
Расчет числа испытательных стендов
Расчет количества оборудования для окрасочных работ
Количество оборудования для окрасочных работ определяется по формуле:
гдеТок - общая трудоёмкость окрасочных работ чел-ч
Принимаем один комплект оборудования для малярных работ.
Таблица 6.Ведомость оборудования
Наименование оборудования
Участок очистки и мойки топливной аппаратуры
Ларь для обтирочного материала
Шкаф для хранения моечных средств
Тележка для перевозки агрегатов
Разборочно-сборочный участок
Стенд для разборки-сборки ТНВД
Верстак слесарный на 1 рабочее место
Шкаф для инструмента и монтажных приспособлений
Участок дефектации и комплектации
Комплект средств измерения
Стол для дефектаци и комплетации деталей
Тележка грузоподъёмная
Шкаф с набором дефектовщика
-0-630-400 ГОСТ10905-86
Ларь для обтирочных материалов
Слесарно-станочный участок
Комплект приспособлений
ОРГ-1468-060А ГОСНИТИ
Стеллаж для узлов и деталей
Тележка для перевозки узлов
Станок для прогонки резьбы
Станок токарно-винторезный
Станок фрезерный универсальный
Станок точильно шлифовальный
Стеллаж для инструмента и приспособлений
Тумба для инструмента
Ларь для обтирочных материалов
Верстак для жестяницких работ
Вибрационные ножницы
Вентилятор кузнечный
Трансформатор сварочный
Сварочный полуавтомат
Выпрямитель 715×605×950 механизм подачи 435×220×340
Гальванический участок
Гальваническая установка
Ванна для промывки и обезжиривания
Универсальный стенд для испытаний и регулировки
Стенд для обкатки и притирки форсунок
Стенд для испытания ТНВД
Установка пульверизаторной окраски
Установка передвижная сушильная
РАСЧЕТ И КОМПОНОВКА ГЛАВНОГО КОРПУСА ПРЕДПРИЯТИЯ ТЕХНИЧЕСКОГО СЕРВИСА
Расчет площадей главного корпуса осуществляется по площади пола занятого оборудованием умноженной на переходный коэффициент:
где fоб - площадь пола занятого оборудованием м2 (см. Табл.6. Ведомость оборудования);
α - переходный коэффициент.
Площадь административных помещений определяют по числу служащих и ИТР из расчета 5 м2 на одного человека.
Площади бытовых помещений определяют из расчета:
- гардероб: 075 08 м2 на одного рабочего;
- умывальники: один умывальный кран с площадью 05 м2 планируется на 10 человек;
- душевые: одна кабина площадью 2 25 м2 на 5 человек;
- туалеты: один унитаз с площадью 3 м2 на 15 человек;
Площадь закрытого склада для хранения запасных частей материалов метизов и прочего определяют по формуле:
где Fх - площадь для хранения м2;
Для определения Fх используется формула:
гдеН1 - норма расхода материалов запасных частей и топлива на один ремонтируемый объект (таб.23);
а - норма хранения запаса дни;
Dр – число рабочих дней в году;
Kx - коэффициент использования площади хранения.
Площади всех подразделений предприятия сводятся в Табл. 7.
Таблица 7. Расчет площадей по подразделениям предприятия
Наименование отделения участка
Наружной очистки и мойки
Разборочно-сборочный
Принимаем общую площадь проектируемого
ремонтного завода 495 м2 .
Далее производится компоновка главного корпуса проектируемого предприятия. Задача компоновки заключается в рациональном размещении в корпусе производственных и вспомогательных участков и служб в обеспечении наилучшей технологической взаимосвязи между ними наиболее коротких грузопотоков с минимальным количеством их пересечений а также соблюдении норм технологического и строительного проектирования. При компоновке производственных подразделений следует принимать во внимание то что:
- производственные и вспомогательные участки целесообразно размещать в одном здании;
- следует строить так чтобы контур здания был близок к квадрату или прямоугольнику;
- отделять участки только пожароопасные или те которые необходимо изолировать в соответствии с правилами безопасности и охраны труда.
В соответствии с полученной площадью принимаем шаг колонн -6м ширину пролетов принимаем 6 и 9м высота колон 526 м.
Планировку всех подразделений выполняют в соответствии с компоновочным планом здания используя принятые условные обозначения.
ПРОЕКТИРОВАНИЕ СТРОИТЕЛЬНЫХ ЭЛЕМЕНТОВ
Проектирование строительных элементов главного корпуса предприятия начинается с привязки колонн к стенам разбивочным осям. Несущие опоры или колонны в строительных планах обозначаются взаимным пересечением разбивочных основных линий. Привязка выполняется при помощи двух или трех координатных размеров в зависимости от типа здания
Стены зданий подразделяются на несущие и каркасные. Несущие стены бескаркасных промышленных зданий выполняются из кирпича. Толщина стен зависит от климатических условий и характера нагрузки.
При проектировании производственных помещений для выполнения стен рекомендуется использование панелей. Раскладку панелей по фасаду различают ленточную с простенками и ленточную без простенков с толщиной 200.. .250 мм.
Несущими элементами здания являются колонны. Колонны зданий имеют квадратные прямоугольные и двухветьевые сечения. Колонны сплошного квадратного и прямоугольного сечений применяют для зданий высотой до 108 м с мостовым краном и без него. Колонны двухветьевого сечения используются как правило для зданий высотой от 108 до 18м.
Для проектируемого предприятия принимаем колонны квадратного сечения 500500 мм. Наружные стены проектируем толщиной в 2 кирпича (510 мм) перегородки внутри корпуса между подразделениями - толщиной 250 мм.
При проектировании геометрический центр сечения колонн средних рядов совмещается с пересечением модульных разбивочных осей следующим образом:
- у колонн крайнего ряда наружная грань и внутренняя поверхность стен совмещаются с модульной разбивочной осью идущей вдоль крайнего ряда;
- парные колонны в местах деформационных швов примыканий или перепадов высот зданий размещают таким образом чтобы модульная разбивочная ось совмещалась с геометрической осью деформационного шва.
В зависимости от нагрузок действующих на фундамент структуры грунта основания глубин промерзания и типа здания фундаменты выполняют ленточными столбчатыми свайными и сплошными.
Для проектируемого предприятия выбираем столбчатый фундамент.
Основные несущие конструкции покрытий чаще всего балки и фермы.
Односкатные и двухскатные балки из предварительно напряженного железобетона имеющие двутавровое поперечное сечение применяются для покрытия пролетов 6 и 9 м. Они могут опираться и на стены и на колонны.
Для пролетов больших размеров используют строительные фермы из предварительно напряженного железобетона или сварные из профильного проката. Для покрытия пролетов принимаем железобетонные балки. На строительные балки укладывается ограждающее покрытие.
Кровлю настилают рулонными гидроизоляционными материалами.
Устройство окон зависит от температурно-влажностного режима и особенностей технологического процесса. Оконные проемы выполняют с железобетонными металлическими или деревянными переплетами. Конструкция проемов определяется требуемой естественной освещенностью. Размеры оконных проемов принимаются кратными по высоте 06 и ширине 05 м высота от пола до подоконной доски 10 15 м. В нашем случае принимаем ширину окна 15 м а высоту 3 м. Расстояние от наиболее удаленного выхода из помещения до рабочего места должно быть не более 50 м. Здание должно иметь не менее двух выходов. При этом двери должны открываться по направлению выхода из здания. Высоту дверей принимаем 25 м ширину 15 2 м. Размеры ворот определяются габаритами транспортных средств и ремонтируемых объектов.
Полы в подразделениях и участках главного корпуса предприятий технического сервиса проектируют в зависимости от специфики технологических операций ремонтно-обслуживающих воздействий требований охраны труда и окружающей среды. Принимаем бетонные плиты по прослойке из цементно-песчаного раствора.
ТЕХНИКО-ЭКОНОМИЧЕСКИЕ ПОКАЗАТЕЛИ ПРОЕКТА
Технико-экономические показатели работы предприятия технического сервиса характеризуются абсолютными и относительными показателями .
К абсолютным показателям относятся: годовая производительная программа себестоимость выпускаемой продукции стоимость основных фондов количество производственных рабочих мощность электродвигателей .
Относительные показатели: производительность годовой выпуск продукции на 1 руб. основных средств фондовооруженность общий уровень рентабельности стоимость основных средств предприятия на одного производственного рабочего.
Стоимость основных средств:
Сос = Сз + Соб + Спр + Си (4.1)
где СЗ – стоимость здания руб.;
СОБ – стоимость оборудования руб.
СПР – стоимость приспособлений и инструмента руб.;
СИ – стоимость инвентаря руб.
Стоимость зданий и сооружений:
где См - стоимость одного м3 здания руб.;
Cз = 15000 495 6= 44550 тыс. руб.
Стоимость станочного и технологического оборудования стоимость приспособлений и инструмента стоимость инвентаря определяют по соответствующим каталогам ценникам и усредненным показателям аналогичных действующих предприятий.
Соб = 06 С3 = 26730 тыс. руб.
Спр = 012 С3 =5346 тыс. руб.
Си = 005 С3 = 22275 тыс. руб.
Сос= 44550 + 26730 + 5346 + 22275 = 788535 тыс. руб.
Себестоимость ремонта машины определяется как:
где Сп - прямые затраты руб.;
Сн - косвенные (накладные) расходы руб.
Прямые затраты упрощенно определяются по формуле:
СП = (03 04) СНИ N(4.4)
где Сни - цена нового изделия принимаем Сни -60000 руб. ;
N - годовая программа предприятия шт.
Сп = 03 60000 1440 = 25920 тыс. руб.
Косвенные (накладные) расходы определяются как:
Сн = Снп + Снх (4.5)
где Снп - общепроизводственные расходы руб.;
Снх - общехозяйственные расходы руб.
Снп = 05 Сп = 12960 тыс. руб.
Снх = 017 Снп = 22032 тыс. руб.
По формуле (4.5) определяем косвенные (накладные) расходы:
Сн = 12960 + 22032 = 151632 тыс. руб.
Тогда по формуле (4.3) определим себестоимость ремонта аппарутуры:
С = 25920 + 22032 = 281232 тыс. руб.
Себестоимость единицы продукции (одного ремонта):
Сед = 281232 1440 = 1952 тыс.руб .
Производительность труда то есть выработку на одного рабочего рассчитывают по формуле:
где Вп - годовой выпуск продукции руб.;
Ч - число производственных рабочих чел.
В = 281232 30 = 93744 тыс. рубчел.
Годовой выпуск продукции на один руб. основных средств рассчитывается по формуле:
где Сос - стоимость основных средств руб.
Вр =28123.2 788535 = 035руб.
Фондовооруженность рассчитывается по формуле:
Ф = 788535 30 = 262845 тыс. рубчел
Общий уровень рентабельности рассчитывается по формуле:
где Пг - годовая прибыль равная разности годового выпуска продукции (тыс. руб.) и себестоимости годового выпуска (тыс. руб.).
Разработана схема технологического процесса капитального ремонта топливной аппаратуры с программой 1440 штук в год.
На основании расчетов установлено что для организации ремонта топливной аппаратуры Енисей-1200 Дон-1500СК-5-М с годовой программой 144 штук необходимо строительство корпуса площадью 495 м2.
Рассчитаны режимы работы предприятия и фонды времени.
Для выполнения годового объема работ необходимо наличие производственных рабочих в количестве 11 человек всего на предприятии работает 17 человек.
Рассчитано и подобрано оборудование необходимое и достаточное для выполнения в полном объеме капитального ремонта топливной аппаратуры.
Выполнена компоновка здания предприятия с наиболее рациональным расположением всех подразделений.
Спроектирован главный корпус предприятия технического сервиса. Спланированы все производственные участки и показано расположение технологического и подъемно-транспортного оборудования.
Технико-экономический анализ деятельности предприятия ТС свидетельствует о целесообразности и экономической эффективности проекта (уровень рентабельности составил 35%).
Бабусенко С.М. Проектирование ремонтно-обслуживающих предприятий. -М.: Агропромиздат 1990.
Матвеев Е.А. Пустовалов И.И. Техническое нормирование ремонтных работ в сельском хозяйстве. -М.: Колос 1979.
Оборудование ремонтных предприятий Курчаткин В.В. Ачкасов К.А. Тельнов Н.Ф. и др. под ред. Курчаткина В.В. - М.: Колос 1999.
Козлов Ю.С. Оборудование для ремонта сельскохозяйственной техники. Справочник. - М.: Россельхозиздат 1987.
Методические указания по проектированию ремонтных предприятий. А.Л. Шашкин Ф.Я. Рудик. - Саратов: СХИ 1986.
И.С. Серый А.П. Смелов В.Е. Черкун Курсовое и дипломное проектирование по надежности и ремонту машин. - М.: Агропромиздат 1991.-184с.
Рекомендуемые чертежи
- 09.07.2014
- 27.04.2015
Свободное скачивание на сегодня
Обновление через: 10 часов 6 минут