Проектирование механического привода




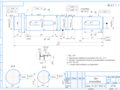
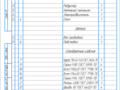
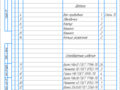
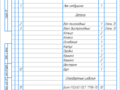
- Добавлен: 04.11.2022
- Размер: 1 MB
- Закачек: 0
Описание
Курсовой проект - Проектирование механического привода
Состав проекта
![]() |
![]() |
![]() ![]() ![]() ![]() |
![]() ![]() ![]() ![]() |
![]() ![]() ![]() ![]() |
![]() ![]() ![]() |
![]() ![]() ![]() ![]() |
![]() ![]() ![]() ![]() |
![]() ![]() ![]() ![]() |
![]() ![]() ![]() ![]() |
![]() ![]() ![]() ![]() |
Дополнительная информация
Редуктор.spw

Болт М10х20 ГОСТ 7798-70
Гайка М12 ГОСТ 5915-70
Кольцо уплот. 60 ГОСТ 9833-73
Кольцо уплот. 100 ГОСТ 9833-73
Манжета 1.1-42 x80-1 ГОСТ 8752-79
Манжета 1.1-28x56-1 ГОСТ 8752-79
Подшипник 7000106 ГОСТ 8338-75
Подшипник 7000109 ГОСТ 8338-75
Шайба 10 ГОСТ 11131-78
Шайба 12 ГОСТ 6402-70
Шпонка 20х12х50 ГОСТ 23360-78
Шпонка 10х8х45 ГОСТ 23360-78
Шпонка 20х12х100 ГОСТ 23360-78
Штифт 4х10 ГОСТ 3128-70
-6g х 120.109.40Х.26 ГОСТ 22034-76
Редуктор.cdw

Вращающий момент на виходнoм валу Т
Частота вращения выходного вала n
Передаточное число редуктора u 4
Технические требования
Залить масло ---68 17479.4-87.
Внутреннюю стенку необработанной части корпуса и крышки
покрасить маслостойкой краской
а снаружи - серой нитроэмалью.
Стыки фланцев корпуса покрыть пастой "Герметик".
Зубчатое колесо.cdw

Неуказанные предельные отклонения H14
Сталь 35 ГОСТ 1133-71
Коэффициент смещения
Межосевое расстояние
Пояснительная записка.docx
«Саратовский государственный
технический университет имени Гагарина Ю.А.»
Кафедра «Техническая механика и детали машин»
Пояснительная записка к курсовому проекту
по дисциплине «Детали машин и основы конструирования» на тему:
«Расчет и проектирование привода с плоскоременной передачей и одноступенчатым цилиндрическим косозубым редуктором»
КИНЕМАТИЧЕСКИЙ РАСЧЕТ4
РАСЧЕТ ПЛОСКОРЕМЕННОЙ ПЕРЕДАЧИ8
РАСЧЕТ ЦИЛИНДРИЧЕСКОЙ ПЕРЕДАЧИ11
РАСЧЕТ ТИХОХОДНОГО ВАЛА18
РАСЧЕТ И ВЫБОР ПОДШИПНИКОВ КАЧЕНИЯ ТИХОХОДНОГО ВАЛА22
ВЫБОР ШПОНКИ. ПРОВЕРОЧНЫЙ РАСЧЕТ ШПОНОЧНОГО СОЕДИНЕНИЯ ДЛЯ НАИБОЛЕЕ НАГРУЖЕННОГО ВАЛА24
КИНЕМАТИЧЕСКИЙ РАСЧЕТ
Кинематический расчет электромеханических приводов является основой проектирования машин и заключается в решении следующих задач:
) выбор электродвигателя (тип мощность частота вращения габариты);
) определение общего передаточного отношения привода U разбивка U по ступеням в соответствии с заданной схемой привода;
) определение мощности частот вращения и крутящих моментов на валах привода.
) Выбор электродвигателя.
Мощность двигателя зависит от требуемой мощности рабочей машины а его частота вращения – от частоты вращения вала приводной машины.
Таким образом исходными данными являются:
– требуемая мощность двигателя
где Pрм – мощность на выходном валу привода (дано в условии);
общ – общий коэффициент полезного действия (КПД) привода.
-коэффициент полезного действия (КПД) привода равный произведению КПД передач входящих в кинематическую схему:
общ = п.п. ц.п. м = 095 096 098 09952 = 089.
Коэффициент полезного действия пары цилиндрических зубчатых колес
Коэффициент учитывающий потери пары подшипников качения п.к. = 0995;
КПД плоскоременной передачи п.п. = 095;
Коэффициент учитывающий потери в муфте М=098 [1 c. 23; 2 c. 5].
– частота вращения приводного вала рабочей машины:
По каталогу в соответствии с найденными значениями окончательно примем двигатель с характеристиками: Рэл.тр и выбираем электродвигатель трехфазный короткозамкнутый серии 4А закрытый обдуваемый 4А112МВ6 У3с асинхронной частотой вращения n =950 обмин (табл. П. 2.1).
Рисунок 1.1 – Двигатели исполнения М100
Таблица 1.1 – Размеры асинхронного электродвигателя мод. 4А112М
Установочные и присоединительные размеры мм
) Определим передаточное число привода отношением номинальной частоты вращения двигателя к частоте вращения приводного вала рабочей машины:
Uобщ = nn = 95066 = 152.
Принимаем согласно таблицы 2 Uц.п.=4.
Вычисляем передаточное число для плоскоременной передачи:
Uп.р. = Uобщ Uц.п. = 1524= 38
что можно признать приемлемым согласно таблицы 2.
Таблица 1.2 - Значения передаточных чисел
Закрытые зубчатые передачи (редукторы) одноступенчатые цилиндрические и конические (ГОСТ 2185— 66):
-й ряд-20; 25; 315; 40; 50; 63
-й ряд-224; 28; 355; 45; 56; 71.
Закрытые червячные передачи (редукторы) одноступенчатые для червяка с числом витков Z1=1; 2; 4 (ГОСТ 2144-75):
-й р я д – 8;1 0; 125; 16; 20; 25; 315; 50
-й ряд-112; 14; 18; 224 28; 355.
Открытые зубчатые передачи
Ременные передачи (все типы)
(Значения 1-го ряда следует предпочитать значениям 2-го ряда)
) Определение параметров привода по валам:
)Число оборотов вращения валов привода (обмин)
Число оборотов вала двигателя nдв = 950;
n= nUп.р. = 95038= 2632 мин;
n= n Uц.п. = 26324 = 66 мин;
)Мощности на валах (кВт)
На валу двигателя: P= 292 кВт;
На быстроходном валу: P= P п.п. = 292 096 0995 = 278 кВт;
На тихоходном валу: P= P ц.п. = 278 096 0995 = 2656 кВт;
На валу рабочей машины: P= P м = 2656 098 0995 = 259 кВт.
)Угловые скорости по валам (радс)
= n1 30 = 314100030 =1046;
= n2 30 = 314263230 =2755;
= n3 30 = 3146630 =69;
= n4 30 = 3146630 =69;
)Крутящие моменты на валах (Нм)
На быстроходном валу:
На валу рабочей машины:
РАСЧЕТ ПЛОСКОРЕМЕННОЙ ПЕРЕДАЧИ
Расчет ременных передач производится в два этапа: первый – проектный расчет с целью определения геометрических параметров передачи второй – проверочный расчет ремней на прочность.
Исходные данные для расчета:
– передаваемая мощность Ртр = 292 кВт
– частота вращения ведущего (меньшего) шкива nдв =950 обмин;
– передаточное отношение
– скольжение ремня = 001.
Диаметр ведущего шкива
Согласно рекомендации [3 с. 77] диаметр шкива
Примем по ГОСТ 17383-73 мм;
Диаметр ведомого шкива
Согласно ГОСТ 17383-73 мм;
Межосевое расстояние
Принимаем мм и определяем длину ремня
Определяем угол обхвата ремня ведущего шкива:
что удовлетворяет условию.
Круговая скорость ремня:
Определим частоту пробегов ремня:
Соотношение условно выражает долговечность ремня и его соблюдение гарантирует срок службы 1000 5000 часов.
Определяем окружную силу:
Удельная окружная сила в передаче:
где С – коэффициенты [табл. 5.3 3]:
Округляем значение до стандартного .
Определяем площадь поперечного сечения ремня:
2 Силовой расчет передачи
Определяем силу предварительного натяжения ремня:
Определим силы натяжения ведущего и ведомого звеньев ремня:
Определим силу давления ремня на вал:
Рисунок 2. Геометрические и силовые параметры передачи
3 Проверочный расчет
Проверим прочность ремня по максимальным напряжениям в сечении ведущего звена:
где- напряжение на растяжение;
- напряжение на изгиб [табл. 5.1 5.2 3];
– напряжение от центробежных сил;
– прочность материала ремня
допустимое напряжение на растяжение
РАСЧЕТ ЦИЛИНДРИЧЕСКОЙ ПЕРЕДАЧИ
Расчет зубчатой цилиндрической передачи производится в два этапа: первый расчет – проектный второй – проверочный. Проектный выполняем по допускаемым контактным напряжениям с целью определения геометрических параметров редукторной пары. Проверочный расчет должен подтвердить правильность выбора табличных величин коэффициентов и полученных результатов в проектном расчете а также определить соотношения между расчетными и допускаемыми напряжениями изгибной и контактной выносливости.
Выбираем материал зубчатых колес и термообработку
Таблица 3 – Рекомендуемый материал для зубчатых колес
Цементация и закалка
На практике в основном применяют следующие варианты термической обработки (т.о.):
I - т.о. колеса - улучшение твердость 235 262 т.о. шестерни - улучшение твердость 269 302 HB. Марки стали одинаковы для колеса и шестерни: 45 40Х 35 ХМ и др. Зубья колес из улучшаемых сталей хорошо прирабатываются и не подвержены хрупкому разрушению но имеют ограниченную нагрузочную способность. Применяют в слабо- и средненагруженных передачах.
II - т.о. колеса - улучшение твердость 269 302 т.о. шестерни - улучшение и закалка ТВЧ твердость поверхности в зависимости от марки стали (см. табл. 1) 45 50 HRCэ 48 53 HRCэ. Твердость сердцевины зуба соотвествует термообработке улучшение. Марки сталей одинаковы для колеса и шестерни: 40Х 40ХН 35ХМ и др.
III - т.о. колеса и шестерни одинаковая - улучшение и закалка ТВЧ твердость поверхности в зависимости от марки сатили: 45 50 HRCэ 48 53 HRCэ. Марки сталей одинаковы для колеса и шестерни: 40Х 40ХН 35ХМ и др.
IV - т.о. колеса - улучшение и закалка ТВЧ твердость поверхности в зависимости от марки стали (табл.1) 45 50 HRCэ 48 53 HRCэ; т.о. шестерни - улучшение цементация и закалка твердость поверхности 56 63 HRCэ. Материал шестерни - стали марок 20Х 20ХН2М 18ХГТ 12ХН3А и др.
V - т.о. колеса и шестерни одинаковая - улучшение цементация и закалка твердость поверхности 56 63 HRCэ. Цементация (поверхностное насыщение углеродом) с последующей закалкой наряду с большой твердостью поверхностных слоев обеспечивает и высокую прочность зубьев на изгиб. Марки сталей одинаковы для колеса и шестерни: 20Х 20ХН2М 18ХГТ 12ХН3А 25 ХГМ и др.
Получаем для шестерни материал Сталь 45 твердость 179 207 НВ1 ; ;
Материал колеса – Сталь 45 твердость 179 207 НВ2 ; .
Окончательно определяем механические характеристики стали 45:
а) для шестерни твердость НВ1=200 термообработка - нормализация;
б) для колеса НВ1≥НВ2+(15 20)=> НВ2=180 термообработка - нормализация.
для шестерни: сталь 45 Термообработка НВ1=200.
для колеса: сталь 45 Термообработка НВ2=180.
1.2 Определение допустимых контактных напряжений.
При расчетах на прочность определяют отдельно для зубьев шестерни и колеса .
Коэффициент долговечности для зубьев по контактным напряжениям
Действительное число циклов перемены напряжений
для шестерни =573*2755*1200=18943380
для колеса =573*69*1200=4744440
Число циклов перемены напряжений соответствующее пределу выносливости
для шестерни 2003=8000000
для колеса 1803=5832000
Т.к. N1 ≥NHO1 то КHL1 =1.
Допускаемое контактное напряжение при числе циклов перемены напряжений
Окончательно допускаемые контактные напряжения (МПа)
1.3 Определение допустимых напряжений изгиба
Проверочный расчет зубьев передач на изгиб выполняется отдельно для зубьев шестерни и колеса
Рассчитываем коэффициент долговечности
- число циклов изменения напряжений для всех сталей соответствующее пределу выносливости 7 с. 56.
Т.к. N1 ≥NFO то КFL1 =1. Т.к. N2 ≥NFO то КFL2 =1
- предел выносливости зубьев при изгибе соответствующий эквивалентному числу циклов изменения напряжений.
Допустимые напряжения смены зубов определяется по формуле:
Проектный расчет служит только для предварительного определения размеров и не может заменить проверочных расчетов на контактную выносливость и выносливость зубов на изгиб
1.4.Основные геометрические параметры передачи
Определяем межосевое расстояние
- вспомогательный коэффициент =43 – для косозубых передач;
=05 – для шестерни расположенной симметрично относительно опор в редукторе который проектируется;
при симметричном расположении 0315-05;
при несимметричном 025-04;
при консольном расположении одного или обоих колес 025-04;
Для шевронных передач ba= 04 - 063; для коробок передач ba= 01 - 02; для передач внутреннего зацепления ba= 02 (u+1)(u-1). Меньшие значения ba- для передач с твердостью зубьев H ≥ 45HRC.
U - передаточное число передачи;
- крутящий момент на тихоходном валу передачи Нм;
- среднее допустимое контактное напряжение;
- коэффициент неравномерности нагрузки по длине зуба;
=1 – для зубов что прирабатываются.
Округляем межосевое расстояние до ближайшего значения по ГОСТ 2185-66 мм:
-й ряд: 40 50 63 80 10 125 160 200 250 315 400 500 630 800 100 1250;
-й ряд: 71 90 112 140 180 224 280 355 450 560 710 900 1120 1400 1800.
Значение из ряда нормальных линейных размеров
Определяем модуль зацепления
где – вспомогательный коэффициент (для косозубых );
– делительный диаметр колеса;
– ширина венца колеса мм;
– допустимое напряжение изгиба материала колеса с менее прочным зубом Нмм2.
По ГОСТ 9563-60 (табл. П. 2.4) принимаем m =225 мм.
Определяем суммарное число зубьев шестерни и колеса
Количество зубьев шестерни
Количество зубьев колеса
Определяем фактическое значение передаточного числа передачи
Определяем погрешность:
условие выполняется.
Фактическое межосевое расстояние
Определяем осевые геометрические параметры передачи.
Делительный диаметр шестерни
Диаметр вершины зубьев шестерни:
Диаметр вершин зубьев колеса:
Ширина венца шестерни
Fa= Fttg = 2135*tg8°=300 Н.
3.1 Проверочный расчет по контактным напряжениям
К – вспомогательный коэффициент К = 376 – для косозубых передач
- коэффициент учитывающий распределение нагрузок между зубцами. Для косозубых - определяют по графику в зависимости от окружной скорости [1 рис. 4.2]:
= n3 30=69 радс; - угловая скорость;
– окружная скорость.
Несмотря на то что окружная скорость составляет всего что соответсвует 9-й степени точности колес в данном расчете принимаем степень – 8. Рекомендуется для редукторов общего назначения [1 с. 330].
- коэффициент учитывающий распределение нагрузки между зубьями согласно [1 с. 65 рис. 4.2];
= 101 – коэффициент динамической нагрузки зависящий от окружной скорости колес степени точности передачи.
=11 – коэффициент учитывающий нагрузки по ширине венца [1 с. 68].
Условие контактной прочности выполняется.
3.2 Проверочный расчет по напряжениям изгиба
где - коэффициент формы зуба: ; ;
- коэффициент учитывающий наклон зуба. Для косозубых колес определяется по формуле:
где - угол наклона зубьев.
m- модуль зазцепления мм;
b- ширина зубчатого венца мм.
- коэффициент учитывающий распределение нагрузки ножки зуба.
- коэффициент учитывающий неравномерности нагрузки по длине зуба [1 с. 69].
– коэффициент динамической нагрузки по длине зуба зависит от окружной скорости [1 с. 66].
То есть условие выполняется.
РАСЧЕТ ТИХОХОДНОГО ВАЛА
1. Ориентировочный расчет вала
Линейные размеры берем из чертежа редуктора (мм): l1 = 008 мм l2=007 мм l2=009 мм d1 = 200 мм d2 = 50 мм. Силы в зацеплении: Ft = 2135 H Fr = 474 H Fоп = 3575 H.
2. Проверочный расчет вала
Проверочный расчет вала выполняется на совместное действие кручение и изгиба. Из этого определяется запас прочности и сравнивается с допустимым Прочность соблюдена при S [S].
Нормальные напряжения определяются по формуле:
где – осевой момент сопротивления наименьшего сечения вала мм3.
Касательные напряжения определяются по формуле:
где – полярный момент сопротивления наименьшего сечения вала мм3.
Далее определяются коэффициент концентрации нормальных и касательных напряжений для вала без упрочнения поверхностного слоя:
где и – эффективные коэффициенты концентрации напряжений при ;
– коэффициент влияния абсолютных размеров поперечного сечения;
– коэффициент влияния шероховатости;
– коэффициент влияния поверхностного упрочнения.
Произведя расчеты получим:
Определение пределов выносливости:
где и – пределы выносливости гладких образцов при сметричном цикле изгиба и кручения Нмм2;
Далее следует определить запас прочности по нормальным и касательным напряжениям:
Общий коэффициент запаса прочности:
515 – условие выполняется.
РАСЧЕТ И ВЫБОР ПОДШИПНИКОВ КАЧЕНИЯ ТИХОХОДНОГО ВАЛА
Предварительно принимаем подшипник 109 ГОСТ 8338-75.
Расчет проводим по реакции опоры .
Осевые составляющие радиальных нагрузок Rs1=Rs2=0. Осевую силу в зацеплении Fa воспринимает подшипник ограничивающий осевое перемещение вала под действием этой силы и испытывающий осевое нагружение Ra равное этой силе.
ВЫБОР ШПОНКИ. ПРОВЕРОЧНЫЙ РАСЧЕТ ШПОНОЧНОГО СОЕДИНЕНИЯ ДЛЯ НАИБОЛЕЕ НАГРУЖЕННОГО ВАЛА
Для соединения валов с деталями и передачи крутящего момента (зубчатыми колесами элементами открытых передач муфтами) применяют шпонки.
В единичном и мелкосерийном производстве используют призматические шпонки. Длину шпонки выбирают из стандартного ряда чтобы они были меньше длины маточной детали на 5 10 мм.
Поперечное сечение шпонки (b × h) выбирают по протяженности диаметра вала.
Выбираем призматические шпонки по ГОСТ 23360-78.
Проверим наиболее нагруженную шпонку на смятие:
Значит выбранная шпонка с С 6 удовлетворяет такие условия прочности.
Смазка применяют в условиях защиты от коррозии уменьшение коэффициента трения уменьшения износа отвода тепла и продуктов износа от трущихся поверхностей уменьшения шума и вибрации.
Сорт масла зависит от величины расчетного контактного напряжения и фактической окружной скорости колес.
Выбираем масло: И-Г-А-68 ГОСТ 17479.4 – 87.
Уровень масла находящегося в корпусе редуктора контролируется жезловым маслоуказателем.
При работе передач масло постепенно загрязняется продуктами износа деталей передач. Со временем оно стареет его свойства ухудшаются поэтому масло налито в корпус редуктора периодически меняют.
Для этого в корпусе предусмотрено сливное отверстие что закрывается пробкой.
Внутреннюю полость редуктора соединяют с окружающей средой путем установления отдушины.
Для смазки зубчатых колес погружением подшипники качения смазываются из картера в результате разбрызгивания масла колесами с образованием масляного тумана и растеканием масла по валам.
Шейнблит А.Е. Курсовое проектирование деталей машин А.Е. Шейнблит. Калининград : Янтарный сказ 2004 - 455 с.
Курсовое проектирование деталей машин С. А. Чернавский [и др.] М. : Машиностроение 1988. 416 с.
Анурьев О.И. Справочник конструктора машиностроителя – М. 1979 – т. .
Д.В. Чернилевский. М. : УМ и «Учебная литература» 1998. 472 с.
Иванов М.Н. Детали машин М.Н. Иванов В.А. Финогенов. М. : Высшая школа 2003. 408 с.
Дунаев П.Ф. Конструирование узлов и деталей машин П.Ф. Дунаев О.П. Леликов. М. : Издательский центр «Академия» 2004. 496 с.
Проектирование механических передач С.А. Чернавский [и др.] М. : Машиностроение. 1984 - 560 с.
Привод звездочек.spw

Манжета 50 ГОСТ 8752-79
Гайка М8 ГОСТ 5915-70
Болт М8х18 ГОСТ 7798-70
Манжета 45 ГОСТ 8752-79
Шпонка 20х12х50 ГОСТ 23360-78
Вал тихоходный.cdw

Комплекс показателей точности устанавливает изготовитель
** - размер обеспечивается инструментом.
Сталь 35 ГОСТ 1050-74
Приводная станция.spw

Гайка М10 ГОСТ 5915-70
Болт М10х20 ГОСТ 7798-70
Болт М14х30 ГОСТ 7798-70
Гайка М14 ГОСТ 5915-70
Ремень 4500 ГОСТ 23831-79
Шайба 10 ГОСТ 6402-70
Шкив 200 ГОСТ 17383-73
Шкив 800 ГОСТ 17383-73
Шпонка 12х8х32 ГОСТ23360-78
Привод.cdw

Вращающий момент на приводном валу Т
Частота вращения приводного вала n
Общее передаточное число привода u 15
Мощность електродвигателя Р
Частота вращения вала електродвигателя n
Технические требования
Осевое смещение валов двигателя и редуктора не больше 1
Перекос валов не больше :
- двигателя и редуктора -1
Кинематическая схема
Привод звездочек.cdw

Вращающий момент на валу Нм 374
Частота вращения вала хв
Технические требования
Подшипниковые камери заполнить пластичным
маслом УТ-1 ГОСТ 1957-73
Рекомендуемые чертежи
- 25.10.2022
Свободное скачивание на сегодня
- 23.02.2023
Другие проекты
- 20.08.2014