Привод ленточного транспортера с двухступенчатым редуктором




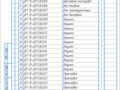
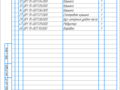
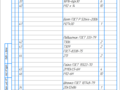
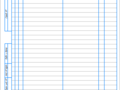
- Добавлен: 04.11.2022
- Размер: 4 MB
- Закачек: 0
Описание
Состав проекта
![]() |
![]() |
![]() ![]() ![]() |
![]() ![]() ![]() ![]() |
![]() |
![]() ![]() ![]() |
![]() ![]() ![]() |
![]() ![]() ![]() |
![]() ![]() ![]() |
![]() |
![]() ![]() ![]() ![]() |
![]() ![]() ![]() |
![]() ![]() ![]() ![]() |
![]() ![]() ![]() ![]() |
![]() ![]() ![]() |
![]() ![]() ![]() ![]() |
![]() |
![]() ![]() ![]() |
![]() ![]() ![]() |
![]() ![]() ![]() |
![]() ![]() ![]() |
![]() ![]() ![]() |
![]() ![]() ![]() |
![]() ![]() ![]() |
Дополнительная информация
Редуктор.cdw

Шестерня.cdw
коэффициент смещения
Неуказанные предельные отклонения размеров: отверстия H14
валов h14 остальное
Сталь 45 ГОСТ 1050-74
3y.cdw

1y.cdw

5y.cdw

Привод.cdw

Содержание.docx
РАСЧЁТ НАГРУЗОЧНЫХ И КИНЕМАТИЧЕСКИХ ПАРАМЕТРОВ ТРАНСПОРТЁРА 5
1 Выбор типа конструктивного исполнения электродвигателя 5
2 Определение передаточных чисел механического привода 6
3 Выходные данные для расчёта привода 7
РАСЧЁТ ДОПУСКАЕМЫХ НАПРЯЖЕНИЙ 10
РАСЧЁТ ЗУБЧАТЫХ ЗАЦЕПЛЕНИЙ РЕДУКТОРА 21
1 Проектировочный расчёт цилиндрической прямозубой передачи 22
2 Проверочный расчёт цилиндрической прямозубой передачи 24
3 Расчёт соединений зубчатых колёс и валов передачи 28
4 Расчёт элементов зубчатых колёс 29
5 Проектировочный расчёт косозубой цилиндрической передачи 30
6 Проверочный расчёт косозубой цилиндрической передачи 32
7 Расчёт соединений зубчатых колёс и валов передачи 37
8 Расчёт элементов зубчатых колёс 39
ПРОЕКТИРОВОЧНЫЙ РАСЧЁТ ВАЛОВ РЕДУКТОРА 40
ПРОВЕРОЧНЫЙ РАСЧЁТ ВАЛОВ РЕДУКТОРА 43
РАСЧЁТ ПОДШИПНИКОВ РЕДУКТОРА НА ДОЛГОВЕЧНОСТЬ 69
1 Расчёт подшипников радиально упорных-конических
2 Расчёт шарикоподшипников радиальных однорядных 73
КОНСТРУИРОВАНИЕ И РАСЧЁТ ЭЛЕМЕНТОВ КОРПУСА РЕДУКТОРА 76
ПРОВЕРОЧНЫЙ РАСЧЁТ СОЕДИНЕНИЙ ПЕРЕДАЮЩИХ КРУТЯЩИЙ МОМЕНТ 81
1 Выбор муфты входного вала 84
2 Выбор муфты выходного вала 86
ТЕПЛОВОЙ РАСЧЁТ ЦИЛИНДРИЧЕСКОЙ ПЕРЕДАЧИ В ЗАКРЫТОМ ИСПОЛНЕНИИ 88
1 Проверочный тепловой расчёт зубчатой передачи 89
2 Смазка цилиндрических редукторов 91
Реферат.docx
Объект исследования: привод ленточного транспортера с двухступенчатым редуктором.
Цель работы: выбрать приводной электродвигатель спроектировать двухступенчатый редуктор подобрать соединительные муфты.
В курсовом проекте выполнен расчет нагрузочных и кинематических параметров транспортера. Определены исходные данные для выполнения проектирования двухступенчатого редуктора: передаточные числа частоты вращения валов вращающие моменты сил мощности на валах.
Проведены проектировочные и проверочные расчеты зубчатых передач редуктора валов подшипников соединительных элементов. Сконструирован корпус редуктора выбраны и проверены муфты. Подобраны стандартизованные детали тип смазки элементов привода.
В графической части проекта разработаны: чертеж общего вида транспортера сборочный чертеж двухступенчатого редуктора рабочие чертежи деталей редуктора.
ПРИВОД ЭЛЕКТРОДВИГАТЕЛЬ РЕДУКТОР МУФТА РАМА ВАЛ КОЛЕСО ПОДШИПНИК СМАЗКА.
VVedenie.docx
Весьма различные машины и механизмы в большинстве своем состоят из однотипных по служебным функциям деталей и сборочных единиц. Отсюда следует что одни и те же методы анализа расчета и проектирования находят применение казалось бы в далеких друг от друга отраслях техники. Поскольку большинство деталей машин общего назначения используется в приводах то они выбраны одним из объектов курсового проектирования. Привод машины или механизма – система состоящая из двигателя и связанных с ним устройств для приведения в движение рабочих органов машины.
При проектировании привода производят кинематические расчеты определяют силы действующие на детали и звенья сборочных единиц выполняют расчеты изделия на прочность решают вопросы связанные с выбором материала и наиболее технологических форм деталей освещаются вопросы сборки и разборки отдельных сборочных единиц и привода в целом.
Основной задачей на этапе конструирования привода является минимизация его стоимости и габаритных размеров при обеспечении надежности и технологичности. Это достигается оптимальным соотношением параметров привода и электродвигателя по рекомендуемым значениям передаточных чисел всех его элементов которые основаны на инженерном опыте. Исходным документом при проектировании является техническое задание отступление от которого недопустимо.
Выполнение курсового проекта по деталям машин – самостоятельная творческая работа по решению комплексной инженерной задачи. Знания и опыт приобретенные при выполнении этого проекта являются базой для выполнения дипломного проектирования. Вместе с тем работа над курсовым проектом по деталям машин подготавливает к решению более сложных задач общетехнического характера с которыми будущий инженер встретится в своей практической деятельности по окончании университета.
Курсовая работа ДМ (Клюхин).docx
Параметры рабочего органа механического привода:
- угловая скорость барабана
- частота вращения барабана
- крутящий момент на барабане
- полезная мощность на барабане
Общий КПД привода механического привода
где КПД муфты; КПД первой ступени редуктора; КПД второй ступени редуктора; КПД пары подшипников [с.151].
Максимальная мощность на валу электродвигателя
Определяем диапазон возможных значений передаточного числа привода
Диапазон частоты вращения вала электродвигателя
1.Выбор типа конструктивного исполнения
В качестве электродвигателя применим промышленный трехфазный асинхронный электродвигатель с короткозамкнутым ротором. Эти двигатели имеют простую конструкция наименьшую стоимость просты в обслуживании.
Принимаем электродвигатель серии 4А с чугунным корпусом типа У категории З по ГОСТ 19523-81. Крепление электродвигателя на лапах.
Эквивалентный крутящий момент
где коэффициент эквивалентности
Значение среднеквадратичной мощности на валу электродвигателя
Принимаем электродвигатель 4А132S8УЗ с минимальной массой и оптимальной частотой вращения вала.
Таблица 1.1 - Параметры электродвигателя
Проверяем двигатель на пуск по условию
Условие выполняется выбранный электродвигатель оставляем.
2.Определение передаточных чисел
механического привода
Передаточное число привода
Для двухступенчатой развёрнутой схемы редуктора передаточное число быстроходной (первой) ступени равно
Принимаем согласно ГОСТ 21426-75 передаточного число
Передаточное число тихоходной (второй) ступени редуктора равно
Действительное передаточное число редуктора
Относительная ошибка передаточного числа
Ошибка допустима передаточные числа подобраны удовлетворительно.
3.Выходные данные для расчёта привода
Определяем время эксплуатации привода транспортёра
где Lгод = 45 – длительность эксплуатации привода коэффициент использования привода в течении года коэффициент использования привода в течении суток.
Определяем нагрузочные и кинематические параметры на валах привода.
Вал электродвигателя
Угловая скорость вала двигателя
Крутящий момент на валу двигателя
Вал 1 (быстроходный вал).
Крутящий момент на валу
Вал 2 (промежуточный вал).
Вал 3 (тихоходный вал).
Вал 4 (вал рабочего органа).
Входные данные для кинематического динамического расчета привода показаны в таблицах 1.21.31.4.
Таблица 1.2 – Входные данные для расчета редуктора
Быстроходная (первая)
Режим работы привода
Спокойный нереверсивный
Таблица 1.3 – Нагрузочные и кинематические параметры привода
Угловая скорость с-1
Частота вращения обмин
Таблица 1.4 – Основные геометрические размеры электродвигателя мм
Установочные и присоединительные размеры
РАСЧЁТ ДОПУСКАЕМЫХ НАПРЯЖЕНИЙ
Назначаем материалы: - шестерня сталь 45 по ГОСТ 1050-74. Заготовка – поковка . Термообработка – улучшение. Колесо сталь 40 по ГОСТ 1050-74. Обработка - нормализация. Механические свойства материалов записаны в таблицу 2.1 и 2.2
Расчёт допускаемых напряжений шестерни -3 и колеса-4
Таблица 2.1 - Механические свойства материалов
Допускаемые контактные напряжения при проектировочном расчете согласно ГОСТ 21354 – 87 определяют по формуле
Базовое число циклов перемен напряжений для шестерни 3 и колеса 4 определяют по графику 3.16 (стр.72 Киркач 1)
Пределы контактной выносливости соответствующие базовому числу циклов перемен напряжений
Срок (суммарный) службы передачи
Продолжительность действия нагрузок в часах
Эквивалентное число циклов перемен напряжений для шестерни и колеса
- коэффициент долговечности учитывает срок службы и режимы нагрузок передачи
Так как принимаем ;
- коэффициент учитывающий шероховатость поверхностей зубьев таблица 3.18 (стр.72 Киркач 1).
- коэффициент учитывающий окружную скорость график 3.17 (стр. 72 Киркач 1).
- коэффициент безопасности (стр.72 Киркач 1).
Допускаемые контактные напряжения при проектировочном расчете определяют по формуле
Для цилиндрических передач за расчетное допускаемое контактное напряжение берут напряжение
Для расчёта по максимальной нагрузке допускаемого контактного напряжения принимаем:
Допускаемые напряжения изгиба при проектировочном расчете согласно ГОСТ 21354 – 87 определяют по формуле
Предел изгибной выносливости соответствующий базовому числу циклов перемен напряжений табл. 3.19 (стр. 74 Киркач 1).
- коэффициент учитывающий шероховатость поверхностей зубьев (формула 3.58 стр.75 Киркач 1).
- коэффициент учитывающий чувствительность материалов к перегрузкам при проектировочном расчете (формула 3.57 стр. 75 Киркач 1).
При известном модуле выбирают по графику 3.19 (стр. 75 Киркач 1).
- коэффициент учитывающий характер нагрузки при нереверсивной передаче (Табл. 3.20 стр.75 Киркач 1). При реверсивной передаче по таблице 3.20 (стр. 75 Киркач 1).
- коэф. безопасности формула 3.56 (стр. 75 Киркач 1).
- коэф. учитывающий характеристики материалов табл. 3.19 (стр. 75 Киркач 1).
- коэф. способа получения заготовок и условий эксплуатаций табл. 3.21 (стр. 75 Киркач 1).
- показатель степени кривой усталости при расчета на изгиб.
- базовое число циклов перемен напряжений при изгибе.
Допускаемые напряжения изгиба для шестерни и колеса
Для расчёта принимаем
Для расчёта max нагрузки:
Расчёт допускаемых напряжений шестерни -1 и колеса-2
Таблица 2.2 - Механические свойства материалов
Срок (суммарный) службы передачи и продолжительность действия нагрузок в часах берём из расчёта прямозубого зацепления
РАСЧЕТ ЗУБЧАТЫХ ЗАЦЕПЛЕНИЙ РЕДУКТОРА
Рисунок 3.1 – Кинематическая схема привода транспортера
– электродвигатель; 2 – редуктор; 3 – муфта пружинная ; 3.1 – цилиндрическая закрытая прямозубая передача; 3.2 – цилиндрическая закрытая косозубая передача; 6 – ведущий вал; 7 – муфта зубчатая; 10 – рама привода; 11– барабан транспортёра.
В – входной быстроходный вал редуктора 2;
С – промежуточный вал редуктора 2;
Д – тихоходный вал редуктора 2;
Е – вал рабочего органа.
1 Проектировочный расчет прямозубой цилиндрической
Исходные данные из результатов кинематического расчета таблица 1.1.
Р2 = 3886 кВт; Р3 = 3732 кВт; n2 = 160 мин-1; n3 = 40 мин-1; u3-4 = 40;
Назначаем коэффициенты.
Для прямозубых зубчатых колес коэффициент ширины зубчатого колеса относительно межосевого расстояния ba =ba назначается в пределах 020 040 и выбирается из ряда по ГОСТ 2185-76 (табл.30) [3].
Принимаем ba = 0315.
КН - коэффициент учитывающий распределение нагрузки по ширине венца. При b4d3 = ba (u34+1)2 = 0315(4+1)2 = 078; (колесо прирабатывается; положение колеса – в близи одной из опор) КН = 105.
КН – коэффициент динамичности нагрузки. В проектировочных расчетах принимается равным КН = 12 [3 стр.96].
КНα – коэффициент учитывающий распределение нагрузки между зубьями. Для прямозубых передач принимается КНα = 1.
Рассчитываем межосевое расстояние.
Принимаем из таблицы межосевое расстояние а = 280 мм.
Назначаем модуля mn = (001 0025)a – (001 0025)280 = 28 7 мм.
Принимаем из таблицы m = 3 мм.
Назначение чисел зубьев. Определим суммарное число зубьев.
(Z3 +Z4) = (2a)mn =(2280)3 = 18666. Принимаем 187.
Число зубьев шестерни 3
Z3 = (Z3 +Z4)(U3-4+1) = 187(4+1) = 374. Принимаем Z3= 37.
Число зубьев колеса 4
Z4 = (Z3 +Z4) - Z3 = 187 – 37 = 150.
Действительное передаточное число передачи
U3-4д = Z4 Z3 = 15037 =405
Относительная ошибка
Расчет геометрических размеров зубчатых колес.
Ширина венца колеса: b4 = b baa = 0315 · 280 = 882 мм.
По таблице 8 (стр. 130) принимаем b4 = 90 мм.
Ширину шестерни принимаем на 2 5 мм больше для компенсации неточностей монтажа.
b 3 = b4 +3 = 90 + 3 = 94 мм.
d3 = m z3 = 337 = 111 мм – диаметр делительной окружности шестерни.
da3 = d3 + 2m = m(z3+2) = 111 + 2·3 = 117 мм – диаметр окружности выступов шестерни.
d3 = d3 – 25m = m(z3+25) = 111 – 25·3 = 1035 мм – диаметр окружности впадин шестерни.
d4 = m z4 = 3·150 = 450 мм. - диаметр делительной окружности колеса.
da4 = d4 + 2m = 450 + 2·3 = 456 мм.
d4 = d4 – 25m = 450 – 25·3 = 4425 мм.
Проверяем межосевое расстояние
а3-4 = (d3 + d4)2 =(111 + 450)2 = 2805 мм.
Назначаем степень точности колес. Основанием для назначения степени точности зубчатых колес является окружная скорость
Степень точности колес 9В.
2 Проверочный расчет прямозубой цилиндрической
Проверка на контактную усталостную прочность.
Расчетное условие н ≤ [] н. [] н = [] н расч = 37504 МПа.
Формула контактных напряжений при проверочном расчете
где Zм = 275 МПа – коэффициент учитывающий механические свойства материалов сопряженных зубчатых колес [1 стр.71].
Zн - коэффициент учитывающий форму сопряженных поверхностей зубьев для прямозубых колес при α = 20о
Z - коэффициент учитывающий суммарную длину контактных линий.
Для зацепления с прямыми зубьями колес
Коэффициент перекрытия колес
Приведенный коэффициент КН = КНα КН КН = 1 106 107 = 1134
КНα – коэффициент учитывающий распределение нагрузки между зубьями. Для прямозубых передач принимается КНα = 1[3 стр.95].
КН - коэффициент учитывающий распределение нагрузки по ширине венца. При b4d3 =90111 = 081; (колесо прирабатывается; положение колеса – возле одной из опор) КН = 106.
КН = 107 – коэффициент динамичности нагрузки. При окружной скорости V= 0929 мс и классе точности 9В и твердости Н3 350 HВ.
н = 32263 [] н = 37504 МПа – контактная усталостная прочность обеспечена.
Проверка на контактную прочность при действии максимальных перегрузок. н max ≤ [] н max. Максимальное контактное напряжение
Допустимое контактное напряжение []H max = 28T = =1260 МПа
H max = 39514 []H max = 1260 МПа – контактная прочность при действии максимальных перегрузок обеспечена.
Проверка на усталостную изгибную прочность.
Расчетное условие F ≤ [] F.
Определим по какому из зубчатых колес пары вести расчет для чего и для шестерни и для колеса рассчитываем отношение [] FYF.
Допускаемое изгибное напряжение
где F limb3 = 360 МПа – предел выносливости зубьев при изгибе.
KFc – коэффициент учитывающий направление приложения нагрузки к зубьям. Для нереверсивных зубчатых передач KFc =1.
SF =175 – коэффициент запаса прочности при изгибе [3].
KFL – коэффициент долговечности. Рассчитываем по формуле
Принимаем равным KFL3=1.
где m – показатель степени кривой усталости. Для зубчатых колес с твердостью поверхности НВ>350 m = 9 [3 стр.110].
NFO – базовое число циклов перемен напряжений соответствующее длительному пределу выносливости. Для всех сталей NFO = 4106 [3 стр.110].
NFE – эквивалентное число циклов перемен напряжений. Рассчитывается с учетом данных режима нагружения. Для шестерни
Находим YF3 – безразмерный коэффициент величина которого зависит от формы зуба. Число зубьев Z3 = 37; Z4 = 150.
Находим по таблице 24[3 стр.77]. YF3 = 372; YF4 = 3619.
Более «слабым» элементом является колесо по которому ведется дальнейший расчет.
Действительное изгибное напряжение
где YF3 = 3 72 YF4 =3619 – коэффициенты формы зуба;
Y 1- коэффициент учитывающий совместную работу точных зубьев;
Y = 1- коэффициент учитывающий наклон зуба для прямозубых передач равен 1.
KFα = 1 – коэффициент учитывающий распределение нагрузки между зубьями.
KF - коэффициент учитывающий распределение нагрузки по ширине венца. По табл.37 [3 стр.104] при b4d4 = 90450 = 02; (колесо прирабатывается; положение колеса – возле одной из опор) КF = 102.
KFV - коэффициент динамичности нагрузки. Класс точности 9В. Н2 ≤350 НВ. КF = 113.
F4 = 6118 [] F = 1975 МПа – изгибная усталостная прочность обеспечена.
Проверка на изгибную прочность при действии максимальных перегрузок. F max ≤ [] F max. Максимальное изгибное напряжение
F max = F4 Кпер = 6118 15 = 9177 МПа.
Допустимое максимальное изгибное напряжение
[] F max = 28· T = 28 450 = 1260 МПа.
F max = 9177 [] F max = 1260 МПа - изгибная прочность при действии максимальных нагрузок обеспечена.
На рисунке 3.1 показана схема зубчатой передачи с указанием размеров
Рисунок. 3.1 схема зубчатой передачи с указанием размеров
3 Расчет соединений зубчатых колес и валов передачи
Диаметр вала для установки ведущей шестерни 3 передачи
Размер диаметра впадин шестерни равен мм. Учитывая этот размер и диаметр вала мм выполняем шестерню 3 заодно с промежуточным валом. На рисунке 8.7 показан вал-шестерня 3.
Диаметр вала для установки ведомого колеса 4 передачи
На консоли тихоходного вала Е передачи диаметром мм. Устанавливаем шпонку для соединения вала со ступицей ведомого колеса сечением мм. Глубина шпоночного паза на валу мм во втулке ступицы мм. Рабочая длина шпонки при допускаемом напряжении смятия материала вала []=80МПа.
Устанавливаем шпонку 20×12×86 ГОСТ 10748 – 79 (табл. 5.10 стр.60).
4 Расчет элементов зубчатых колес
Для ведущей шестерни 3. Толщина ступицы.
Для ведомого колеса 4. Толщина обода зубчатого венца.
Диаметр обода колеса мм.
Толщина диска зубчатого колеса
Диаметры вспомогательных отверстий
Фаски на колесах 3 4 мм. При угле .
5 Проектировочный расчет косозубой цилиндрической
Данные выбираем из результатов кинематического расчета таблица 1.1.
Р1 = 4047 кВт; Р2 = 3886 кВт; n1 = 720 мин-1; n2 = 160 мин-1; u1-2= 45.
Назначаем угол наклона зубьев = 16о.
Для косозубой передачи.
Коэффициент ширины зубчатого венца колеса относительно межосевого расстояния ba = 0315 (табл.30[3]).
КНα=113 – коэффициент неравномерности нагрузки между зубьями (ожидается 8-я степень точности и окружная скорость до 10 мс).
КН = 106 - коэффициент учитывающий распределение нагрузки по ширине венца. При bd1 = ba (u1-2+1)2 = 0315(45+1)2 = 0866; (колесо прирабатывается; положение колеса – вблизи одной из опор).
КН = 12 – коэффициент динамичности нагрузки для проектировочных расчетов.
По конструктивным соображениям и принимаем мм.
Назначение модуля. mn = (001 0025) a =(001 0025)160=(16 4) мм.
Принимаем модуль для колес 1 и 2 m = 20 мм.
Назначение чисел зубьев.
(Z1 +Z2) = (2a cos) mn =(2160 cos16) 20 = 1538.
Принимаем (Z1 +Z2) =154.
Рассчитываем угол наклона зубьев колес
= arcos[mn2а(Z1 +Z2)] = arcos [20(2 160) 154] = 15740о.
Z1 = (Z1 +Z2)(U1-2+1) = 154(45+1) = 28. Принимаем 28.
Z2 = (Z1 +Z2) - Z1 = 154 – 28 = 126.
U1-2ф = Z2 Z1 = 12628 = 45
Ширина колеса: b2 = b ba a = 0315 160 = 504 мм.
По табл.34 принимаем b2 = 52 мм.
Проверяем на торцевое перекрытие
b2 ≥ 4mnsin =420sin1574о = 295 – торцовое перекрытие обеспечено.
b1 = b2 + 3 = 52+ 3 = 55 мм.
d1 = mz1cos = 20 28cos1574о = 581816 мм – диаметр делительной окружности.
da1 = d1+2m = 581816 + 2 20 = 621816 мм – диаметр окружности выступов.
d1 = d1 – 25m = 581816 – 25 20 = 531816 мм– диаметр окружности впадин.
d2 = m z2 cos = 20 126 cos 1574о = 2618174 мм.
da2 = d2 + 2m = 2618174 + 2 20 = 2658174мм.
d2 = d2 – 25m = 2618174 – 25 20 = 2568174 мм.
Проверка: а = d12 + d22 = 5818162 +26181742 = 160 мм.
Назначение степени точности
Основанием для назначения степени точности зубчатых колес является окружная скорость
Назначаем степень точности 9В.
6 Проверочный расчет косозубой цилиндрической
Проверка на контактную усталостную прочность
Расчетное условие н ≤ [] н . [] н = [] н расч = 37504 МПа.
Для косозубой передачи расчетное контактное напряжение равно
где Zм = 275 МПа12 – коэффициент учитывающий механические свойства материалов сопряженных зубчатых колес [3 стр.71].
Zн - коэффициент учитывающий форму сопряженных поверхностей зубьев для шевронных колес при α = 20о
Z - коэффициент учитывающий суммарную длину контактных линий. Для косозубых и шевронных колес
Коэффициент перекрытия для косозубых колес
КНα = 113– коэффициент учитывающий распределение нагрузки между зубьями. Для косозубых передач принимается по табл.31 для скорости 14 мс и степени точности 9В [3 стр.95].
КН = 108 - коэффициент учитывающий распределение нагрузки по ширине венца. При b2d1 = 52581816=0894; (колесо прирабатывается; положение колеса - вблизи одной из опор)
КН = 108 – коэффициент динамичности нагрузки. [3 табл.38].
Класс точности 9В; Н2 350 HВ; V=14 мс.
н = 357245МПа [] н. = 37504МПа – контактная усталостная прочность косозубого зацепления обеспечена.
Расчетное условие: F ≤ [] F.
Выясняем по какому из зубчатых колес пары вести расчет для чего и для шестерни и для колеса рассчитываем [] FYF.
Допускаемое изгибное напряжение для косозубого зацепления
где F limb = 360 МПа – предел выносливости зубьев при изгибе.
KFc =1 – коэффициент учитывающий направление приложения нагрузки к зубьям. Для нереверсивных передач.
SF =175 – коэффициент запаса выбираем из таблицы 41 [3].
KFL – коэффициент долговечности для шестерни
Для зубчатых колес с твердостью поверхности НВ≥350 показателе степени кривой усталости m = 6.
При таком величине m = 6. Коэффициент долговечности имеет пределы возможных значений 1≤ KFL ≤ 163. Принимаем равным KFL = 1.
NFE – эквивалентное число циклов перемен напряжений. Рассчитывается с учетом данных режима нагружения.
KFL – коэффициент долговечности для колеса
Принимаем равным KFL = 1.
Предел допускаемых изгибных напряжений
[] Flimb2=18ННВ2 = 18 192 = 3456 МПа.
Определяем безразмерные коэффициенты YF1 и YF2 величины которых зависят от формы зуба. Число зубьев Z1 = 28; Z2 = 126. Рассчитываем эквивалентное число зубьев шестерни и колеса
Z1E = Z1(cos3) = 28(cos31574о) = 314
Z2E = Z2(cos3) = 126(cos31574о) = 1413
По таблице 24 [3 стр.77] находим YF1 = 374 и YF2 = 3614.
Рассчитываем отношения
Более «слабым» элементом является колесо по которому ведется дальнейший расчет. Расчетное изгибное напряжение для колеса 2
Y - коэффициент учитывающий наклон зубьев колес
Y= 1 - о140о = 1 – 1574о140о = 08875.
KFα – коэффициент учитывающий распределение нагрузки между зубьями. Для шевронных и косозубых цилиндрических передач
где n =9 – степень точности колес по нормам контакта ГОСТ1643-72.
При степени точности выше 5-й принимается n = 5.
– торцевой коэффициент перекрытия.
КF = 103 - коэффициент учитывающий распределение нагрузки по ширине венца. По табл.37 [3 стр.104].
При b2d2 = 522618174 = 020; (колесо прирабатывается; положение колеса – вблизи одной из опор).
КF = 103 - коэффициент динамичности нагрузки [3 табл.38]. Класс точности колес 9В. Твердость колеса 2 Н2 ≤ 350 HВ.
F = 2899 МПа []F = 1975 МПа – изгибная усталостная прочность обеспечена.
Проверка на контактную прочность при действии максимальных перегрузок.
Контактное напряжение при действии максимальных перегрузок
Коэффициент перегрузки
Максимальное допускаемое контактное напряжение
[]H max = 28T = 28·450 =1260 МПа
H max = 43753 []H max = 1260 МПа – контактная прочность при действии максимальных перегрузок обеспечена.
Проверка на изгибную прочность при действии максимальных перегрузок.
Изгибное напряжение при действии максимальных перегрузок
F max = F Кпер = 2899 15 = 4348 МПа.
Максимальное допускаемое изгибное напряжение
Fmax = 4348 []F max = 1260МПа - изгибная прочность при действии максимальных нагрузок обеспечена.
8 Расчет соединений зубчатых колес и валов передачи
Диаметр вала для установки ведущей шестерни 1 передачи
Размер диаметра впадин шестерни равен мм. Учитывая этот размер и диаметр вала мм выполняем шестерню 1 заодно с быстроходным валом. На рисунке 8.8 показана схема зубчатой передачи с указанием размеров и вал-шестерня 1.
Рисунок 3.2 – Схема зубчатой передачи с указанием размеров
Диаметр вала для установки ведомого колеса 2 передачи
На консоли промежуточного вала С передачи диаметром мм. Устанавливаем шпонку для соединения вала со ступицей ведомого колеса сечением мм. Глубина шпоночного паза на валу мм во втулке ступицы мм. Рабочая длина шпонки при допускаемом напряжении смятия материала вала []=80МПа.
Устанавливаем шпонку 14×9×50 ГОСТ 10748 – 79 (табл. 5.10 стр.60).
8 Расчет элементов зубчатых колес
Для ведущей шестерни 1. Толщина ступицы.
Для ведомого колеса 2. Толщина обода зубчатого венца.
Диаметр обода колеса
Принимаем мм. Число отверстий .
Фаски на колесах 1 2 мм. При угле
Проектировочный расчет валов редуктора
Рассмотрим двухступенчатый редуктор у которого одна ступень цилиндрическая косозубая а другая цилиндрическая прямозубая.
Быстроходный вал редуктора. На рисунке 16.7 представлен эскиз компоновочной схемы вала.
Рисунок 4.1 – Эскиз компоновочной схемы вала
Ориентировочный диаметр вала в опасном сечении при пониженном допускаемом напряжении кручения МПа.
Принимаем размеры консольного участка вала мм; мм.
Диаметр вала под подшипники мм.
Диаметр вала под уплотнение мм.
Шестерня изготовлена заодно с валом.
Назначаем тип подшипников на которых установлен быстроходный вал.
Опоры № 1 и № 2. Роликоподшипник радиально-упорный конический однорядный № 7307 ГОСТ 333 – 79. Посадочный диаметр мм наружный диаметр мм ширина мм. Каталожная динамическая грузоподъемность Н статическая грузоподъемность Н.
Промежуточный вал редуктора. На рисунке 16.8 представлена эскизная компоновочная схема промежуточного вала.
Рисунок 4.2 Эскизная компоновочная схема промежуточного вала
Диаметры вала под шестерней и колесом мм.
Диаметры вала между шестерней и колесом мм.
Назначаем тип подшипников для установки промежуточного вала.
Опоры № 3 и № 4. Роликоподшипник радиально-упорный конический однорядный № 7309 ГОСТ 333 – 79. Посадочный диаметр мм наружный диаметр мм ширина мм. Каталожная динамическая грузоподъемность Н статическая грузоподъемность Н.
Тихоходный выходной вал. На рисунке 16.9 представлена эскизная компоновочная схема выходного вала.
Рисунок 4.3 Эскизная компоновочная схема выходного вала
Принимаем размеры выходного консольного участка вала мм; мм с учетом установки зубчатой муфты.
Диаметры вала под колесом мм.
Диаметры упорного участка вала для колеса мм.
Назначаем тип подшипников для установки тихоходного вала.
Опоры № 5 и № 6. Шарикоподшипник радиальный однорядный № 213 ГОСТ 8338 – 75. Посадочный диаметр мм наружный диаметр мм ширина мм. Каталожная динамическая грузоподъемность Н статическая грузоподъемность Н.
1 Проверочный расчет валов редуктора
Для расчёта валов составляем расчётную схема (см.рис. ). При этом принимаем что детали передают валу силы и моменты посередине своей ширины. Собственную массу вала и массу установленных на нём деталей а также силы трения возникающие в опорах не учитываем.
Быстроходный входной вал
Назначаем материал вала
К материалам машинных валов предъявляются требования достаточной прочности жёсткости ударной вязкости при минимальной чувствительности к концентрации напряжения. Этим требованиям отвечают малоуглеродистые стали марок Ст. 5 Ст. 6 (ГОСТ 380-88) среднеуглеродистые стали - Сталь 35 Сталь 45 (ГОСТ 1050-88) легированные стали - 40Х 40ХН 20Х 12ХНЗА 18ХГТ 30ХГТ (ГОСТ 4543-88).
Для изготовления вала назначаем материал Сталь 45 ГОСТ 1050-88:
- предел прочности по нормальным напряжениями ;
- предел текучести по нормальным напряжениям ;
- предел текучести по касательным напряжениями ;
- предел выносливости по нормальным напряжениям
при симметричном цикле для образца ;
- предел выносливости по касательным напряжениями
Определяем силы действующие на вал
К этим силам относится силы возникающие в деталях передач и от веса этих деталей внешние силы на валу от действия шкивов звёздочек муфт.
1 Рассчитываем силы в зацеплении цилиндрической косозубой передачи.
где - угол зацепления в нормальном сечении ;
- угол наклона зуба
2 Рассчитываем силу действующую со стороны упругой втулочно-пальцевой муфты
где - окружное усилие на диаметре расположения пальце муфты
Рисунок 4.4- расчётная схема и эпюры нагружения быстроходного вала
Расчёт опорных реакций и изгибающих моментов
Расчётная схема приведена на рисунке
1 Вертикальная плоскость
составляем уравнение равновесия относительно опоры 1:
составляем уравнение равновесия относительно опоры 2:
следовательно расчёт выполнен правильно.
Рассчитываем изгибающие моменты в сечениях:
2 Горизонтальная плоскость
Определяем опасные сечения
концентрация напряжения обусловлена нарезкой эвольвентных зубьев
концентрация напряжения обусловлена посадкой с гарантированным натягом
Проверочные расчёты
Часто разрушение вало носит усталостный характер поэтому расчёт валов на усталость является основным. Он сводится к определению действительных коэффициентов запаса прочности S для предположительной опасных сечений вала и сравнения их с допускаемым коэффициентом запаса прочности [S].
Запас прочности S при совместном действии нормальных и касательных напряжений может быть рассчитан по формуле:
где - запас прочности по нормальным напряжениям
где - запас прочности по касательным напряжениям
- переменные составляющие циклов напряжений;
- постоянные составляющие циклов напряжений.
Так как внешние нагрузки по положению относительно вала неизменны
Так как режим работы вала не реверсивный
где и - момент сопротивления сечения при изгибе и кручении соответственно.
Суммарные коэффициенты учитывающие влияние всех факторов на сопротивление усталости при изгибе и кручении определяются по формулам
где - эффективные коэффициенты концентрации при изгибе и кручении;
- коэффициенты влияния абсолютных размеров поперечного сечения;
- коэффициент влияния шероховатости на поверхности (при шероховатости Ra=25);
- коэффициент влияния упрочнения (поверхностное упрочнение не предусмотрено).
Как правило выполняется также проверка на статическую прочность при максимальных перегрузках. Расчёт ведётся в предположении что во время кратковременных напряжения во всех сечениях вала возрастают сравнительно с напряжениями номинального нагружения.
Проверочный расчёт на выносливость в сечении (А-А)
Суммарные коэффициенты учитывающие влияние всех факторов на сопротивление усталости при изгибе и кручении:
- моменты сопротивления сечения при изгибе и кручении
- переменные и составляющие циклов напряжений
Для среднеуглеродистых сталей
- коэффициент запаса прочности по нормальным напряжениям
- коэффициент запаса прочности по касательным напряжениям
- общий коэффициент запаса прочности (отношения предельного напряжённого состояния к действительному)
О работоспособности вала судят по выполнению расчётного условия
- требуемый коэффициент запаса для обеспечения прочности
- следовательно выносливость вала в сечении (А-А) обеспечена.
Проверочный расчёт на статическую прочность при максимальных перегрузках в сечении (А-А)
- коэффициент перегрузки в пиковых значениях нагрузки
- максимальное значение нормальных напряжений
- максимальные значения касательных напряжений
- эквивалентное максимальное напряжение
- допускаемое напряжение
- следовательно статическая прочность вала в сечении (А-А) обеспечена.
Проверочный расчёт на выносливость в сечении (Б-Б)
- эффективные коэффициенты концентрации при изгибе и кручении;
-коэффициент влияния шероховатости на поверхности
(при шероховатости Ra=25);
- коэффициент влияния упрочнения
(поверхностное упрочнение не предусмотрено).
- Суммарные коэффициенты учитывающие влияние всех факторов на сопротивление усталости при изгибе и кручении:
- следовательно выносливость вала в сечении (Б-Б) обеспечена.
Проверочный расчёт на статическую прочность при максимальных перегрузках в сечении (Б-Б)
- следовательно статическая прочность вала в сечении (Б-Б) обеспечена.
Промежуточный вал редуктора
Для изготовления вала назначаем Сталь 45 ГОСТ 1050-88;
1 Рассчитываем силы в зацеплении цилиндрической косозубой передачи
2 Рассчитываем силы в зацеплении цилиндрической прямозубой передачи
Расчёт опорных реакций и изгибающих моментов
Расчётная схема вала приведена на рисунке.
составляем уравнение равновесия относительно опоры 3:
составляем уравнение равновесия относительно опоры 4:
Рисунок4.5 - расчётная схема и эпюры нагружения промежуточного вала
Рассчитываем изгибающие моменты в сечениях
концентрация напряжения обусловлена наличием шпоночной канавки
где b - ширина шпоночного паза мм;
t - глубина шпоночного паза на валу мм;
Выходной(тихоходный) вал редуктора
1 Рассчитываем силы в зацеплении цилиндрической прямозубой передачи
2 Рассчитываем силу действующую со стороны зубчатой муфты
где - окружное усилие на делительном диаметре муфты
Рисунок 4.6 - расчётная схема и эпюры нагружения тихоходного вала
. Расчёт опорных реакций и изгибающих моментов
составляем уравнение равновесия относительно опоры 5:
составляем уравнение равновесия относительно опоры 6:
Изгибающих моментов нет.
Расчет подшипников редуктора на долговечность
Расчет подшипников выполняем для скорректированной долговечности при повышенном уровне надежности с учетом качества металла и условий эксплуатации.
Расчетное условие пригодности подшипника .
- скорректированная расчетная долговечность с учетом качества металла и условий эксплуатации.
- требуемая долговечность заданная в техническом задании.
1 Расчет роликоподшипников радиально-упорных конических однорядных
Тип подшипников на которых установлен вал.
Опора 1 и 2. Роликоподшипники радиально-упорные конические однорядные № 7209 по ГОСТ 333 – 79. Геометрические размеры подшипника мм; мм; мм. Каталожная динамическая грузоподъемность Н статическая грузоподъемность Н.
Рассчитываем радиальные нагрузки действующие в опорах
Определяем эквивалентные нагрузки в опорах вала
На опоры действует осевая сила Н.
где - суммарная радиальная нагрузка действующая на подшипник в опоре ( );
Определяем дополнительные параметры подшипников
- угол наклона роликов подшипника;
- расчетный параметр;
Определяем минимальные осевые нагрузки для подшипников.
Условие равновесия всех осевых сил действующих на вал
Для опоры 1 принимаем осевую нагрузку Н.
Тогда из условия равновесия для опоры 2 осевая нагрузка
Следовательно реакции найдены верно.
следовательно X=1;Y=0
- коэффициент вращения вращается внутреннее кольцо подшипника (при вращении наружного кольца );
- коэффициент безопасности
- коэффициент учитывающий рабочую температуру нагрева подшипника ( до 100oС )
- коэффициент радиальной динамической нагрузки;
- коэффициент осевой динамической нагрузки.
- коэффициент осевой динамической нагрузки из таблицы подшипников.
Расчет показывает что опора 2 является более нагруженной. Дальнейший расчет выполняем по опоре 2.
Рассчитываем скорректированную долговечность подшипника в млн.об. с учетом качества металла и условий эксплуатации
С - динамическая грузоподъёмность подшипника;
- коэффициент учитывающий вероятность отказов для степени надежности ;
- коэффициент подшипников для роликоподшипников;
- показатель степени для роликоподшипников.
Рассчитываем скорректированную долговечность подшипника в часах
где обмин – частота вращения вала.
ч. – подшипники пригод
Опора 3 и 4. Роликоподшипники радиально-упорные конические однорядные № 7209 по ГОСТ 333 – 79. Геометрические размеры подшипника мм; мм; мм. Каталожная динамическая грузоподъемность Н статическая грузоподъемность Н.
- расчетный параметр.
Для опоры 3 принимаем осевую нагрузку Н.
Для опоры 4 осевая нагрузка
Расчет показывает что опора 4 является более нагруженной. Дальнейший расчет выполняем по опоре 4.
ч. – подшипники пригодны.
2Расчет шарикоподшипников радиальных однорядных
Опора 5 и 6. Шарикоподшипники радиальные однорядные № 213 по ГОСТ 8338 – 75. Геометрические размеры подшипника мм; мм; мм. Каталожная динамическая грузоподъемность Н статическая грузоподъемность Н.
- суммарная осевая нагрузка действующая на подшипник в опоре ( );
Расчет показывает что опора 5 является более нагруженной. Дальнейший расчет выполняем по опоре 5.
- коэффициент подшипников для шарикоподшипников (для роликоподшипников );
- показатель степени для шарикоподшипников (для роликоподшипников ).
ч. – подшипники пригодны
Конструирование и расчет элементов корпуса редуктора
Толщина стенки основания корпуса
Нм – максимальный вращающий момент на тихоходном валу.
Толщина стенки крышки корпуса мм.
Для расчета поясов фланцев корпуса используем рисунок 6.1.
Рисунок 7.1 – Размеры верхнего и нижнего поясов фланцев корпуса
Толщина верхнего пояса фланца корпуса
Толщина нижнего пояса фланца крышки
Толщина нижнего фланца корпуса
Диаметр и количество фундаментных болтов
Ширина фланца мм. Координата стяжного болта фланца мм.
Ширина опорной поверхности нижнего фланца корпус
Диаметры болтов расположенных у подшипниковых гнезд
Диаметры стяжных болтов фланца .
Принимаем мм. Число определяется графически.
Диаметры болтов крепления смотровой крышки мм
Принимаем мм. Число .
На рисунке 7.2 показаны размеры приливов для размещения болтов у подшипниковых гнезд. Размеры приливов в таблице 6.1.
Рисунок 7.2 – Размеры приливов у подшипниковых гнез
Таблица 7.1 – Размеры приливов у подшипниковых гнезд
Гнезда подшипников входного вала
Гнезда подшипников промежуточного вала
Гнезда подшипников выходного вала
Размер болтов крепления крышек
Диаметр расточки под подшипник мм
Диаметр винтов крепления крышки к корпусу мм
Диаметр окружности болтов крышки
Диаметр бобышки под крышкой мм
Минимальное расстояние от оси отверстия болта подшипниковых гнезд до расточки под подшипник мм.
Торцы приливов для подшипниковых гнезд выступают за фланцы плоскости разъема на величину мм.
Размеры литейных переходов между стенкой корпуса и фланцами:
- толщина перехода . Принимаем мм;
- высота перехода мм.
Радиус сопряжения элементов корпуса мм.
Для исключения смещения крышки относительно корпуса устанавливаются два конических штифта на разных сторонах разъема. Штифты установить до расточки отверстий под подшипники.
Диаметры штифтов мм. По ГОСТ 3129-70.
Толщина проушины мм.
Диаметр отверстий в проушинах мм.
Толщина ребер жесткости основания корпуса мм.
Толщина ребер жесткости крышки корпуса мм.
Опорные поверхности под крепежные детали должны быть обработаны размер элементов поверхностей для размещения болтов зависит от диаметра крепежных болтов. Размеры элементов опорных поверхностей в таблице 7.2.
Таблица 7.2 – Размеры элементов опорных поверхностей
Опорные поверхности для крепления редуктора к основанию
Опорные поверхности для соединения основания и крышки корпуса со стороны подшипников
Опорные поверхности для соединения основания и крышки корпуса со стороны стяжных болтов
Диаметр отверстия под фундаментный болт мм
Диаметр отверстия под стяжной болт мм
Проверочный расчет соединений передающих
Расчёт шпоночного соединения быстроходного вала и упругой втулочной-пальцевой муфты. Исходные данные: крутящий момент Нм; посадочный диаметр под шестерню мм; консольный диаметр длина ступицы мм; муфта – тип 1.
Устанавливаем шпонку для соединения вала со ступицей ведомого колеса сечением мм. Глубина шпоночного паза на валу мм во втулке ступицы мм. Рабочая длина шпонки при допускаемом напряжении смятия материала вала []=80МПа.
Устанавливаем шпонку 10×8×45 ГОСТ 10748 – 79
Материал шпонки – сталь 6 предел текучести МПа.
По ГОСТ устанавливаем шпонку призматическую с размерами:
Рассчитываем напряжение смятия на рабочей грани шпонки
Рассчитываем допускаемое напряжение смятия
- коэффициент запаса прочности.
МПа МПа следовательно шпоночное соединение работоспособно.
Устанавливаем шпонку 8×7×70 ГОСТ 10748 – 79
Расчет шпоночного соединения промежуточного вала и упругой втулочно-пальцевой муфты. Исходные данные: крутящий момент Нм; посадочный диаметр мм: длина ступицы колеса мм;. шестерни
МПа и МПа МПа следовательно шпоночное соединение работоспособно.
Расчет шпоночного соединения тихоходного вала и зубчатого колеса Z4. Исходные данные: крутящий момент Нм; посадочный диаметр мм: длина ступицы зубчатого колеса Z4 мм.
Для консольного участка тихоходного вала диаметром
1 Выбор муфты входного (быстроходного) вала
Для соединения вала двигателя и входного вала редуктора применим (рисунок 21.1) муфту упругую втулочно-пальцевую (МУВП).
Рисунок 9.1 - Муфта упругая втулочно-пальцевая (МУВП)
На работу муфты очень влияют толчки удары и внезапные изменения нагрузки обусловленные характером работы проектируемого транспортера.
Выбор муфт производят не по номинальному моменту на валу а по расчетному моменту с учетом коэффициента перегрузки.
Расчетный момент для выбора муфты
Принимаем муфту упругую втулочно-пальцевую по ГОСТ 21424- 75 Тип-1. МУВП-32 номинальный крутящий момент передаваемый муфтой Нм. Диаметр вала мм. Диаметр отверстия муфты мм
Геометрические размеры для проверочного расчета (рисунок 21.1 21.2).
- диаметр расположения пальцев мм;
- диаметр пальцев мм; число пальцев ;
- длина резиновой втулки пальца мм;
- зазор между полумуфтами мм.
Рисунок 9.2 – Пальцы муфты с втулками
Проверочный расчет муфты. Работоспособность муфты определяют по работоспособности пальцев и резиновых втулок.
Усилие приходящееся на один палец
Прочность пальцев по напряжениям изгиба
Прочность пальцев обеспечена МПа МПа.
Условие прочности втулки на смятие МПа.
Прочность резиновых втулок обеспечена
Проверяем муфту по скорости вращения
2 Выбор муфты выходного (тихоходного) вала
Применяем зубчатую муфту типа МЗ. Зубчатая муфта наиболее применяемый вид жестких компенсирующих муфт. Применяются для соединения горизонтальных соосных валов способны компенсировать любые смещения осей (рисунок 21.3)
Рисунок 9.3 – Зубчатая муфта типа МЗ
Выбор муфты производят не по номинальному моменту на валу а по расчетному моменту с учетом коэффициента перегрузки.
Принимаем зубчатую муфту по ГОСТ 5006-55 номинальный крутящий момент передаваемый муфтой Нм. Диаметр вала мм.
Геометрические размеры для проверочного расчета (рисунок 21.3).
- модуль зацепления мм;
- длина зуба муфтымм.
Работоспособность муфты определяет прочность зуба на смятие
Прочность муфты обеспечена МПа МПа.
Тепловой расчет цилиндрической передачи в закрытом исполнении
Вследствие значительных потерь мощности за счет низкого КПД червячной передачи происходит нагревание элементов передачи корпуса и масла которое в нем находится. При повышенных температурах масло теряет свои смазочные свойства что может привести к выходу передачи из строя.
Поэтому для червячной передачи выполняют проверочный тепловой расчет. Записывают уравнение теплового баланса системы в виде
Из этого уравнения определяют расчетную температуру масла которая должна быть меньше допускаемой температуры.
где - мощность на тихоходном валу кВт;
- КПД червячной передачи;
м2 - площадь поверхности корпуса передачи соприкасающаяся с воздухом рекомендуется м2;
- межосевое расстояние м;
- температура окружающего воздуха;
кВт() - коэффициент теплопередачи.
Допускаемая температура для обычных редукторных масел . Для авиационных масел .
Если температура необходимо либо увеличить поверхность охлаждения (применяя охлаждающие ребра).
Либо применить искусственное охлаждение (рисунок 12.8) обдувание корпуса воздухом с помощью вентилятора.
Посредством размещения в картере редуктора змеевика с циркулирующей водой помещаемого в масло.
1 Проверочный тепловой расчет зубчатой передачи
Основная цель определение расчетной температуры нагрева масла в процессе работы червячного редуктора. Температура масса не должна превышать допустимой температуры для выбранного сорта масла. Рисунок 13.3 позволяет определить ориентировочную площадь поверхности охлаждения.
Расчетная температура нагрева масла в редукторе
°С – температура воздуха окружающей среды.
- мощность на червяке редуктора в кВт.
- коэффициент полезного действия червячной передачи.
Вт(м 2·град) – коэффициент теплоотдачи поверхности.
- коэффициент переменности режима нагружения.
- площадь поверхности охлаждения корпуса редуктора без учета поверхности ребер охлаждения. Определяем приближенно как сумму площадей шести граней прямоугольного параллелепипеда (рисунок 13.1) который условно представляет корпус червячного редуктора.
Поверхность охлаждения корпуса редуктора .
Площадь поверхности профиля редуктора
- расстояние от днища корпуса редуктора до оси зубчатого колеса ; м
- диаметр червячного колеса;мм
мм - толщина стенки крышки и корпуса редуктора;
мм – зазор между внутренней стенкой крышки редуктора и колесом при толщине стенки корпуса редуктора мм;
- межосевое расстояние редуктора; м
Верхняя площадь редуктора
мм - расстояние от боковой стенки редуктора до средней части опорного подшипника;
Площадь боковой поверхности
Площадь поверхности охлаждения корпуса редуктора
Количество тепла выделяемого в червячном редукторе за секунду
Количество тепла отдаваемого корпусом червячного редуктора в окружающую среду за секунду
Расчеты показывают что площадь поверхности редуктора достаточна для естественного охлаждения червячного редуктора.
2 Смазка цилиндрических редукторов
Для смазывания цилиндрических и конических редукторов применим картерную систему смазки. Для расчета уровня и объема масла в картере редуктора составим (на рисунке 13.2) кинематическую схему зацеплений редуктора с использованием масштабного коэффициента длин .
Масштабный коэффициент длин ммм.
В таблице 13.3 приведены действительные размеры диаметров зубчатых колес и их размеры в масштабе на кинематической схеме.
Таблица 13.3 – Размеры зубчатых колес редуктора
Действительный диаметр колеса м
Размер диаметра на схеме мм
Рисунок 10.1 – Кинематическая схема зацеплений редуктора
Таким образом смазка редуктора будет осуществляется окунанием не меньше чем половины длины зубьев конического колеса 2.
Высота уровня масла в картере редуктора
Вязкость масла выбираем в зависимости от окружной скорости колес и величин контактных напряжений.
Для быстроходной косозубой передачи МПа; мс.
Для тихоходной прямозубой передачи МПа; мс.
По величинам вязкости 10409 и 18074 из таблицы 13.4 назначаем соответствующие кинематические вязкости:
Среднее значение кинематической вязкости
По величине среднего значения вязкости сст и таблице 13.5 назначаем марку масла ИРП – 75 (ТУ 38 - 101451-78) с вязкостью сст.
Таблица 10.1 – Рекомендации к выбору вязкости масел для редукторов
Виды зубчатых редукторов
Цилиндрические и конические
Таблица 10.2 – Марки масел и их кинематическая вязкост
Кинематическая вязкость
ИРП-75 (ТУ 38 – 101451 – 78)
ИРП-150 (ТУ 38 – 101451 – 78)
И-40А (ГОСТ 20799 – 88)
И-50А (ГОСТ 20799 – 88)
ТАП 15В (ГОСТ 23652 – 79)
ИТП-200 (ТУ38 – 101292 – 79)
ИГП-114 (ТУ 38 – 101413 – 78)
ИГП-152 (ТУ 38 – 101413 – 78)
АСЗП-6 (ТУ 38 – 10111 – 75)
МС-20 (ГОСТ 21743 – 76)
Необходимый объем масла
Источники.docx
Баласанян Р.А. " Атлас деталей машин: Навч. поciбник для техн. вузiв. - X.: Основа 1996. - 256 с.
Шейнблинт А.Е. Курсовое проектирования деталей машин: Учеб. пособие для техникумов. – М.: Высш.шк. 1991.
Детали машин в примерах и задачах: Учеб. пособие С.Н. Ничипорчик М.И. Корженцевский В.Ф. Калачев и др.; Под общ.ред. С.Н. Ничипорчика. – Мн.:Выш.шк. 1981 г.
Детали машин и основы конструирования: учеб.А.Т.Скойбеда А.В.Кузьмин Н.Н.Макейчик; под общ. ред. А.Т.Скойбеды. – Мн.: Высш.шк. 2000 г
Титул.docx
«Автомобильный транспорт» машины и детали машин»
ПРИВОД ТРАНСПОРТЕРА С ДВУХСТУПЕНЧАТЫМ ЦИЛИНДРИЧЕСКИМ РЕДУКТОРОМ
ДМ 15-007.00.00.00.00.ПЗ
Пояснительная записка курсовому проекту
по дисциплине «Детали машин»
Зачетная книжка № 14 – 145
Факультет «Автомобильный Кафедра «Строительно-дорожные
транспорт» машины и детали машин»
на курсовой проект по деталям машин
Тема: спроектировать привод транспортера с цилиндрическим двухступенчатым редуктором.
Кинематическая схема транспортера.
Окружная тангенциальная сила Н.
Окружная скорость мс.
Срок службы транспортера год.
Годовой коэффициент использования .
Дневной коэффициент использования .
Диаграмма нагружения транспортера.
Рекомендуемые чертежи
- 15.02.2021