Привод ленточного конвеера


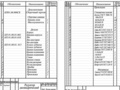
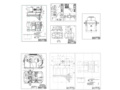
- Добавлен: 04.11.2022
- Размер: 1 MB
- Закачек: 0
Описание
Состав проекта
![]() |
![]() ![]() ![]() ![]() |
![]() ![]() ![]() |
![]() ![]() ![]() ![]() |
![]() ![]() ![]() |
![]() ![]() ![]() |
Дополнительная информация
спецификация редуктор.dwg

Подшипник 217 ГОСТ 8338-75
Штифт 6x70 ГОСТ 9464-79
Гайка М12 ГОСТ 2524-70
Шайба 10 65Г ГОСТ 6402-70
Шпонки ГОСТ 23360-78:
Манжета 1-85x65 ГОСТ 8752-79
Подшипник 309 ГОСТ 8338-75
Шайба 12 65Г ГОСТ 6402-70
Шайба 14 65Г ГОСТ 6402-70
Штифт 8x50 ГОСТ 3129-70
Герметик УТ-34 ГОСТ 24285-80
Масло И-Г-А-68 ТУ-38 101413-78
курс по ДМ (2007г)+редуктор.dwg

В редуктор залить масло марки И-Г-А-68
Перед сборкой на стыке разъема нанести пасту гермитик.
Технические требования.
Технические характеристики.
Вращающий момент на тихоходном валу 399 Н м
Частота вращения быстроходного вала 712
Общее передаточное число
Редуктор двухступенчатый
Сталь 40Х ГОСТ 4543-71
Направление линии зуба
Коэффициент смещения
По размерам в квадратных скобках обработать в сборе с корпусом
Неуказанные литейные радиусы 4мм.
Неуказанные предельные отклонения
Неуказанные литейные уклоны 3°
поверхностей : ±IT172.
ленточного конвейера
План размещения отверстий под фундаментальные болты
Технические требования
Допускаемые смещения валов электродвигателя и редуктора не более:
Вращающиеся детали оградить.
Техническая характеристика
Окружная сила на приводном барабане
Скорость движения ленточного конвейера
Общее передаточное число привода
Мощность электродвигателя
Частота вращения вала электродвигателя
Записка.doc
Государственное образовательное учреждение
высшего профессионального образования
Ульяновский Государственный Технический Университет
Кафедра «Основы Проектирования Машин»
ПОЯСНИТЕЛЬНАЯ ЗАПИСКА
к курсовому проекту по курсу «Детали машин»
Кинематический расчет привода 4.
1 Выбор электродвигателя .. ..4
2. Уточнение передаточных чисел ступеней редуктора .. ..5
3 Частота вращения валов редуктора . .6
4 Вращение моменты на волах редуктора . .6
5 Проверка двигателя на пуск . 6
6 Расчетный ресурс привода 6
2. Тихоходная косозубая цилиндрическая передача 7
1.1.Межосевое расстояние .. ..7
1.2. Предварительные размеры колеса .. ..10
1.3. Модуль передачи ..10
1.4. Суммарное число зубьев и угол наклона . 12
1.5 Число зубьев шестерни и колеса .. 13
1.6. Фактическое передаточное число ..13
1.7. Диаметры колес .. 13
1.8 Размеры заготовок .. 14
1.9 Проверка зубьев колес по контактным напряжениям . 14
1.10 Силы в зацеплении 14
1.11 Проверка зубьев колес по напряжениям изгиба. 15
1.12 Проверочный расчет на прочность зубьев при действии пиковой нагрузки.16
2. Быстроходная ступень редуктора 17
2.1.Межосевое расстояние .. ..17
2.2. Предварительные размеры колеса .. ..20
2.3. Модуль передачи ..20
2.4. Суммарное число зубьев и угол наклона . 22
2.5 Число зубьев шестерни и колеса .. 23
2.6. Фактическое передаточное число ..23
2.7. Диаметры колес .. 23
2.8 Размеры заготовок .. 24
2.9 Проверка зубьев колес по контактным напряжениям . 24
2.10 Силы в зацеплении 24
2.11 Проверка зубьев колес по напряжениям изгиба. 25
2.12 Проверочный расчет на прочность зубьев при действии пиковой нагрузки .26
3. Цепная передача 27
Эскизная компоновка редуктора 30
1. Предварительный расчет диаметров валов 30
1.1. Диаметры быстроходного вала 30
1.2. Диаметры промежуточного вала . 30
1.3. Диаметры тихоходного вала 30
2. Выбор подшипников .. 31
3.Основные размеры корпуса редуктора 31
Конструирование и расчет валов подшипников шпоночных соединений .. 32
1. Тихоходный вал .. .. 32
1.1. Построение эпюр изгибающих и крутящих моментов . . 33
1.2. Расчет вала на сопротивление пластическим деформациям . 35
1.3. расчет вала на сопротивление усталости 36
1.4. Расчет подшипников тихоходного вала .. 38
1.5. Расчет шпоночных соединений тихоходного вала 39
2. Промежуточный вал . 40
2.1. Расчет шпоночного соединения промежуточного вала с цилиндрическим колесом 47
3. Быстроходный вал 47
3.1. Построение эпюр изгибающих и крутящих моментов . 48
3.2. Расчет вала на сопротивление пластическим деформациям . 49
Конструкция и эксплуатация установки.
1. Конструкция редуктора. Смазка зубчатых передач подшипников. Для червячного редуктора - тепловой расчет. 55
2. Выбор стандартных муфт. 56
3. Конструкция рамы (плиты) выбор фундаментных болтов. 57
4.Эксплуатация установки. Техника безопасности. 57
Список используемой литературы 58
Кинематический расчет привода
Исходные данные: = 2.5 кН – окружное усилие на тяговых звёздочках;
=07 мс – окружная скорость звёздочек;
= 160 мм – шаг тяговых цепей;
=13 – число зубьев звёздочки .
1. Выбор электродвигателя
где = 097 – КПД зубчатой передачи [2 табл. 1.1];
= 093 – КПД цепной передачи.
= 099 – КПД подшипников;
= 4 - число пар подшипников.
Требуемая мощность электродвигателя
Частота вращения приводного вала
Требуемая частота вращения вала электродвигателя.
где – передаточное число цепной передачи [2 табл. 1.2];
и – передаточные числа тихоходной и быстроходной ступеней цилиндрического редуктора [2.т.1.2].
Выбираем электродвигатель [2 табл. 24.9] АИР 112 МА8: = 22 кВт . .
2. Уточнение передаточных чисел редуктора.
Общее передаточное число привода
Передаточное число цепной передачи = 225 тогда передаточное число редуктора
Передаточное число тихоходной ступени двухступенчатого соосного редуктора [ 2.т. 1.3].
Передаточное число быстроходной ступени двухступенчатого соосного редуктора [ 2.т. 1.3].
3. Вращающие моменты на валах редуктора
Вращающий момент на приводном валу
Момент на валу колеса тихоходной ступени редуктора
Вращающий момент на валу шестерни тихоходной ступени (на валу колеса быстроходной ступени редуктора)
Момент на валу шестерни быстроходной ступени
Частоты вращения валов
Частота вращения вала тихоходной ступени
Частота вращения вала шестерни тихоходной ступени (вала колеса быстроходной ступени двухступенчатого редуктора)
Частота вращения вала шестерни быстроходной ступени
5. Расчетный ресурс передачи
Суммарное время работы передачи [2 с.14]
где - число лет работы согласно заданию;
- коэффициент годового использования передачи;
- коэффициент суточного использования передачи.
1.Тихоходная ступень редуктора
Исходные данные: - вращающий момент на шестерне;
- частота вращения шестерни;
- передаточное число;
- время работы передачи;
- коэффициент перегрузки .
- термической обработки шестерни и колеса из стали 40Х – улучшение [2 табл. 2.1]: = 269 – 302 HB = 750 МПа; = 235 – 262 HB = 640 МПа; = 125 мм; = 125 мм.
1.1. Межосевое расстояние
Предварительное значение межосевого расстояния при и 350 HB [2 с.17].
Окружная скорость [2 с.18]
Степень точности косозубой цилиндрической передачи [2 табл. 2.5] при 4 мс .
Уточненное межосевое расстояние косозубой передачи
Коэффициент ширины при симметричном расположении колес относительно опор [2 с.18] .
Коэффициент нагрузки в расчетах на контактную прочность
Коэффициент учитывающий внутреннюю динамику нагружения [2 табл. 2.6] при и 350 HB: .
Ориентировочное значение коэффициента [2 с.19]
Коэффициент неравномерности распределения нагрузки после приработки
где = 1092 – коэффициент неравномерности распределения нагрузки в начальный период работы [2 табл. 2.7] для схемы передачи 4 и 350
= 026 – коэффициент учитывающий приработку зубьев [2 табл. 2.8] при и = 250 HB.
Начальное значение коэффициента распределения нагрузки между зубьями косозубой передачи при и 350 HB [2 с.21]
Принимаем по условию ограничения .
Значение коэффициента распределения нагрузки между зубьями после приработки [2 с.19]
Вычисление коэффициента нагрузки в расчетах на контактную прочность
Допускаемые контактные напряжения [2 с.13]
Предел контактной выносливости [2 табл. 2.2]
Число циклов соответствующее перелому кривой усталости [2 с.13]
Ресурс шестерни и колеса при одном вхождении в зацепление каждого зуба за оборот (=1)
Коэффициент эквивалентности [2 с.16]
Коэффициент долговечности при переменном режиме нагружении [2 с.13]
Коэффициент влияния шероховатости сопряженных поверхностей зубьев [2 с.14] при =125 мкм: =095.
Коэффициент влияния окружной скорости при =052 мс: =1.
Коэффициент запаса прочности для улучшенных зубчатых колес [2 с.13] =11.
Вычисление допускаемых контактных напряжений
Для цилиндрической косозубой передачи [2 с.14]
При условии что принимаем
Вычисление межосевого расстояния
Округляя по ряду размеров [2 табл. 24.1] =140.
1.2. Предварительные основные размеры колеса
Делительный диаметр [2 с.21]
1.3. Модуль передачи
Максимально допустимый модуль [2 с.21]
Минимальное значение модуля косозубой передачи
Коэффициент нагрузки при расчете по напряжениям изгиба
Коэффициент внутренней динамики нагружения [2 табл. 2.9] при = 9 = 052 мс и 350 HB: =101.
Коэффициент неравномерности распределения напряжений у основания зубьев по ширине зубчатого венца [2 с.22]
Коэффициент влияния погрешностей изготовления шестерни и колеса на распределение нагрузки между зубьями [2 с.22]
Вычисление коэффициента нагрузки при расчете по напряжениям изгиба
Допускаемые напряжения изгиба зубьев [2 с.15]
Предел выносливости при отнулевом цикле напряжений [2 табл. 2.3]
Число циклов соответствующее перелому кривой усталости [2 с.15] .
Коэффициент эквивалентности [2 с.16] при заданной циклограмме моментов q = 6
Коэффициент долговечности при переменном режиме нагружения [2 с.15]
Коэффициент влияния шероховатости переходной поверхности между зубьями [2 с.15] при 40 мкм: = 1.
Коэффициент влияния двустороннего приложения нагрузки [2 с.16] при одностороннем приложении нагрузки = 1.
Коэффициент запаса прочности для улучшенных колес [2 с.15] = 17.
Вычисление допускаемых напряжений изгиба зубьев
Вычисление минимального значения модуля косозубой передачи
Принимаем стандартный модуль [2 с.22] m = 125.
1.4. Суммарное число зубьев и угол наклона
Минимальный угол наклона зубьев косозубых колес [2 с.22]
Суммарное число зубьев
Округляем в меньшую сторону = 223.
Действительный угол наклона зубьев
1.5. Число зубьев шестерни и колеса
Число зубьев шестерни [2 с.23]
Округляем в большую сторону = 49.
Число зубьев колеса внешнего зацепления
1.6. Фактическое передаточное число
Делительные диаметры [2 с.23]
Диаметры окружностей вершин зубьев
Диаметры окружностей впадин зубьев
1.8. Размеры заготовок
Диаметр заготовки шестерни [2 с.24]
Толщина заготовки колеса
1.9. Проверка зубьев колес по контактным напряжениям
Контактное напряжение косозубых передач [2 с.24]
1.10. Силы в зацеплении
1.11. Проверка зубьев колес по напряжениям изгиба
Напряжение изгиба зубьев колеса [2 с.25]
Приведенное число зубьев колеса
Коэффициент формы зуба [2 табл. 2.10] при : .
Коэффициент угла наклона зуба в косозубой передачи.
Коэффициент перекрытия зубьев косозубой передачи [2 с.25] .
Вычисление напряжения изгиба зубьев колеса
Приведенное число зубьев шестерни
Напряжение изгиба зубьев шестерни [2 с.25]
1.12. Проверочный расчет на прочность зубьев при действии пиковой нагрузки
Допускаемое напряжение при пиковой нагрузке [2 с.26] при улучшении
Условие предотвращения повреждения поверхностного слоя зубьев
Допускаемое напряжение изгиба зубьев при пиковой нагрузке
Максимальное значение коэффициента долговечности для улучшенной стали [2 с.26] .
Коэффициент влияния частоты приложения пиковой нагрузки при многократном действии перегрузок .
Коэффициент запаса прочности .
Вычисление допускаемых напряжений изгиба зубьев при пиковой нагрузке
Условие предотвращения разрушения зубьев
2.Быстроходная ступень редуктора
2.1. Межосевое расстояние
где = 103 – коэффициент неравномерности распределения нагрузки в начальный период работы [2 табл. 2.7] для схемы передачи 4 и 350
= 027 – коэффициент учитывающий приработку зубьев [2 табл. 2.8] при и = 250 HB.
Коэффициент влияния окружной скорости при =193 мс: =1.
2.2. Предварительные основные размеры колеса
2.3. Модуль передачи
Коэффициент внутренней динамики нагружения [2 табл. 2.9] при = 9 = 193 мс и 350 HB: =1077.
Принимаем стандартный модуль [2 с.22] m = 1 мм.
2.4. Суммарное число зубьев и угол наклона
Округляем в меньшую сторону = 278.
2.5. Число зубьев шестерни и колеса
Округляем в большую сторону = 52.
2.6. Фактическое передаточное число
2.8. Размеры заготовок
2.9. Проверка зубьев колес по контактным напряжениям
2.10. Силы в зацеплении
2.11. Проверка зубьев колес по напряжениям изгиба
Коэффициент угла наклона зуба в косозубой передачи
2.12. Проверочный расчет на прочность зубьев при действии пиковой нагрузки
- вращающий момент на ведущей звездочке;
- частота вращения ведущей звездочки;
25- передаточное число.
КП=14 – коэффициент перегрузки.
Расположение цепи – горизонтальное; смазывание периодическое; регулирование цепи также периодическое.
Число зубьев ведущей звездочки
Число зубьев ведомой звездочки
Уточняем передаточное число
Определяем коэффициент учитывающий условия работы и установки.
где коэффициент изменения нагрузки равный КП ;
коэффициент учитывающий влияния межосевого расстояния при ;
коэффициент учитывающий угол наклона передачи к горизонту если он меньше ;
коэффициент учитывающий способ регулирования натяжения при периодическом регулировании;
коэффициент влияния способа смазывания цепной передачи при периодическом смазывании ;
коэффициент учитывающий режим работы при односменной работе.
Момент на валу ведущей звездочки
Определяем шаг цепи предварительно приняв ориентировочно допускаемое среднее давление [р] по нормам DIN 8195 [р] = 17 МПа[3 с. 283] полагаем что скорость цепи
Выбираем ближайшее стандартное значение [3 табл. 10.1]
Определяем скорость цепи
Уточняем значение [р] по DIN 8195: интерполируя находим
Проверяем расчетное давление
Условие выполняется
Подбираем цепь [3 табл. 10.1] приводную роликовую однорядную лёгкой серии: t = 381 мм; разрушающая нагрузка FB = 100 кН; масса 1 м цепи m = 55 кг; ее условное обозначение
Цепь ПР 381-127 ГОСТ 13568-75.
Определяем геометрические параметры передачи: межосевое расстояние
расчетная длина цепи
Проверяем цепь по числу ударов
Допускаемое значение ; условие выполнено.
Коэффициент запаса прочности цепи
Разрушающая нагрузка цепи
Нагрузка от центробежной силы
Сила от провисания цепи
Диаметр делительной окружности
Вычисляем коэффициент запаса прочности цепи
коэффициент запаса прочности [3 табл.10.2] должен быть [s] > 7.5 Следовательно условие s > [s] выполнено.
Расчет нагрузки на вал звездочки
Эскизная компоновка редуктора
1 Предварительный расчёт диаметров валов.
1.1. Диаметр быстроходного вала [2 с.45];
Согласуем с диаметром электродвигателя АИР 112МА8 [2 табл. 24.7];
Из диаметров отверстий полумуфт [3 табл. 15.5 15.6];
Диаметр вала под подшипник
Округляем до стандартного размера
Диаметр вала для базирования подшипника
Округляем до стандартного размера [2 табл. 24.1]
1.2. Диаметр промежуточного вала
Диаметр вала для базирования колеса
1.3. Диаметр тихоходного вала
Диаметр вала под колесо
2. Выбор подшипников
Для опор валов цилиндрических косозубых колес редуктора принимаем радиальные шарикоподшипники [2с.50] которые устанавливаем по схеме «враспор». Предварительно выбираем [2табл.2410] подшипники: для быстроходного вала 208: d=40мм D=80мм В=18мм r=2мм; для тихоходного вала 209: d=45мм D=85мм В=19мм r =2мм; для промежуточного вала 205: d=25мм D=52мм В=15мм r =15мм.
3. Основные размеры корпуса редуктора
Расстояние между внешними поверхностями зубчатых колес [2 рис. 3.3];
Зазор между поверхностью вращения колес и внутренние поверхности стенок корпуса
Расстояние между дном корпуса и поверхности колеса
Участок вала под уплотнение должен выступать за плоскость болта приверченных крышек [2 рис. 3.11(б)];
Расстояние между зубчатыми колёсами
Расчет толщины стенок редуктора
Радиусы скругления стенок редуктора
Выбор креплений крышки редуктора к корпусу:
Диаметр винтов крепления
Расстояния от края до оси винта
Конструирование крышек подшипников.
Привертные крышки конструируем по рис.82 [2с.168].
Крышка подшипника быстроходного вала.
Диаметр и число винтов крепления крышки к корпусу: d=8мм Z=4.
Диаметр крышки: ДФБ=D+4d=80+4×6=104мм; диаметр окружности расположения центров винтов: Д0=D+2d=80+2×6=92мм.
Размеры расточки под манжету [2табл.2426] быстроходного вала: D1=55мм h1=10мм.
Крышка подшипника тихоходного вала.
Диаметр крышки: ДФБ=D+4d=85+4×6=111мм; диаметр окружности расположения центров винтов: Д0=D+2d=85+2×6=97мм.
Размеры расточки под манжету [2табл.2426] быстроходного вала: D1=70мм h1=10мм.
Диаметр крышки: ДФБ=D+4d=52+4×6=76мм; диаметр окружности расположения центров винтов: Д0=D+2d=52+2×6=64мм.
Конструирование и расчет валов подшипников шпоночных соединений.
Механические характеристики стали 40ХН:
Вал с насаженными деталями изображаем в масштабе.
Под эскизом вала составляем его расчетную схему. Силы в зацеплении:Ft=3707H; Fr=1355H; Fa=350H;FЗВ=3617Н. Крутящий момент ТТ=399Н×м.
Размеры: а=50мм в=525мм с=80мм d2=2185мм.
1.1. Построение эпюр изгибающих и крутящих моментов
Реакции опор в плоскости Х:
Реакции опор в плоскости У:
Изгибающий момент в плоскости Х на левом и правом конце:
Изгибающие моменты в плоскости Y на левом и правом конце:
Суммарные изгибающие моменты на левом и правом конце:
Крутящий момент: на участке а Т=0;
На участке в и с Т=Тт=399 H×М.
Опасные сечения вала
На эскизе вала намечаем предположительно опасные сечения и сопоставляем их между собой используя эпюры моментов. Оставляем для расчета сечение 1 с наименьшим диаметром и наиболее нагруженное сечение 2. Из трех одинаковых сечений 236 исключаем менее нагруженные сечения 3 и 6. Сечение 5 исключаем т.к. оно не передает крутящего момента. Таким образом оставляем для дальнейшего расчета сечения 1 2 и 4.
1.2. Эквивалентные напряжения в сечениях вала
Изгибающие моменты находим по эпюре суммарных изгибающих моментов:
Крутящие моменты в намеченных сечениях вала определяем по эпюре крутящих моментов: Т1 = Т2 = Т4 = 399 Н*м.
Моменты сопротивления сечений вала при изгибе Wи и кручении Wк определяем по формулам:
в сечении 1 конец вала диаметром d = 36 мм ослаблен канавкой и глубиной h = 025 мм
в сечении 2 участок вала диаметром dп = 45 мм
в сечении 4 вал диаметром d4 = 56 мм ослаблен шпоночным пазом t1 = 6 мм и b = 16 мм.
Номинальные напряжения изгиба и кручения в сечениях вала:
Эквивалентные напряжения в сечениях вала по четвертой (энергетической) теории прочности:
Расчет вала на сопротивление пластическим деформациям
Расчет вала на сопротивление пластическим деформациям выполняем по сечению 1 в котором возникает наибольшее эквивалентное напряжение. Напряжение в опасном сечении вала при кратковременной перегрузке (Кпер = 14) по формуле:
Коэффициент запаса по пределу текучести материала вала по формуле 3.4 [4 c. 12]:
Допускаемое значение коэффициента запаса по пределу текучести определяем по пластичности материала вала применяя линейную интерполяцию:
Условие прочности вала по сопротивлению пластическим деформациям выполняется:
Опасные по усталости сечения вала
Для расчета вала на сопротивление усталости выбираем сечение 1. Выбор сечения 1 обусловлен тем что большие номинальные напряжения в нем сочетаются с концентрацией напряжений от ступенчатого перехода и от насаженной детали.
1.3. Расчет вала на сопротивление усталости по сечению 1
В сечении вала нереверсивного редуктора напряжения изгиба изменяются по симметричному циклу а напряжения кручения - по отнулевому циклу. Средние напряжения цикла и амплитуды напряжений по формулам 3.5 и 3.6 [5 c.29]:
Коэффициенты влияния абсолютного размера поперечного сечения проходящего по канавке диаметром dK = d – 2h = 36 – 2*025 = 35.5 мм вала из легированной стали при изгибе и кручении находим по табл. 3.4 [5 c.14] применяя линейную интерполяцию:
Эффективные коэффициенты концентрации напряжений в ступенчатом переходе с радиусом закругления r = 1 мм по табл. 3.5 [5 c.15] для бВ = 920 Мпа;
при изгибе ; при кручении
Отношение коэффициентов в ступенчатом переходе:
при изгибе при кручении
Отношение коэффициентов учитывающих снижение сопротивления усталости вала у торца насаженной с натягом полумуфты:
при изгибе по формуле 3.13 [4 c.17]:
где в соединении с посадочным диаметром 36 мм;
для материала вала с пределом прочности
для давления в посадке Р>25 МПа;
при кручении по формуле 3.14 [5 c.17]
В дальнейшем расчете учитываем тот концентратор напряжений у которого больше отношение коэффициентов а именно:
Коэффициенты влияния шероховатости поверхности канавки:
при изгибе по формуле 3.10 [5 c.14] для бВ = 920 Мпа; и Ra = 63 мкм
при кручении по формуле 3.11 [5 c.14]
Коэффициент влияния поверхностного упрочнения для участка вала без упрочнения KV = 1.
Коэффициенты влияния среднего напряжения цикла соответственно при изгибе и кручении по формулам 3.12 [5 c.14]:
Пределы выносливости гладких образцов из стали 40ХН при изгибе и кручения с симметричными циклами по табл. 3.1 [5 c.7]
Коэффициенты запаса прочности:
по нормальным напряжениям по формуле 3.8 [5 c.13]:
по касательным напряжениям по формуле 3.9 [5 c.13]:
Коэффициент запаса прочности по усталости при совместном действии напряжений изгиба и кручения по формуле 3.7 [5 c.13]:
Допускаемое значение коэффициента запаса прочности по усталости [S] = 15 1.8.
Условие прочности сечения 1 по сопротивлению усталости выполняется:
S = 1.86 > [S] = 18.
1.4. Выбор и расчет подшипников
Предварительно выбираем по каталогу радиальные шарикоподшипники легкой серии 209 у которых
Силы приложенные к подшипникам возьмем из уточненного расчета валов (п. 3.1.4.3.). Осевой нагрузки в этих расчетах нет поэтому на том же рисунке показываем осевую силу направляя ее в сторону противоположную направлению силы Fa4. Величина воспринимаемой подшипником осевой силы FАа = Fa4 = 350 Н. При данном направлении силы наихудшая комбинация сил для подшипника А.
Радиальная нагрузка на подшипник А:
Осевая нагрузка на подшипник:
Составим наихудшую комбинацию для опоры В для этого направим силу в другую сторону:
Реакции опор в горизонтальной плоскости:
Реакции опор в вертикальной плоскости:
Эквивалентные динамические нагрузки:
Эквивалентная динамическая нагрузка подшипника А по формуле [6 c.11]:
где V = 1 при вращении внутреннего кольца подшипника по отношению к направлению радиальной нагрузки;
KБ = 13 по табл. 5.4 [6 c.13] для редукторов;
X и Y выбраны по табл. 5.3 [6 c.12]:
параметр осевого нагружения равен
находим X = 1 и Y = 0.
Эквивалентная динамическая нагрузка подшипника B по формуле [6 c.12]:
Наиболее нагруженным является подшипник В и Pmax = 10729 Н.
Коэффициент эквивалентных динамических нагрузок по формуле 5.14 [6 c.15]:
Эквивалентная динамическая нагрузка подшипника Впри переменном режиме нагружения по формуле 5.10 [6 c.14]:
Расчетный ресурс подшипника А при вероятности безотказной работы 099 по формуле 5.4 [6 c.11]:
где т = 3 для шарикоподшипников;
а1 = 021 по табл. 5.1 [6 c.10] для вероятности безотказной работы 099;
а23 = 07 по табл. 5.2 [6 c.11] для обычных условий применения.
Это значение больше требуемого ресурса 16819 ч.
1.5. Расчет шпоночных соединений тихоходного вала.
Расчет шпоночного соединения тихоходного вала с колесом.
Исходные данные: Т=399Н×м – вращающий момент КП=14 – коэффициент перегрузки; Lсm=55мм – длин ступицы d=56мм посадка с натягом; материал колеса – сталь.
Выбираем призматическую шпонку с закругленными торцами. Допускаемая длина шпоночного паза [4с.5]
L`=Lсm-2S=55-2×4=47мм.
По диаметру d=56мм выбираем [4с.28] шпонку шириной в=16мм высотой h=10мм длиной L = 50мм с глубиной паза вала t1 =6мм.
Рабочая длина шпонки [4с.4] Lр=L-в=50-16=34мм.
Номинальное давление на поверхности контакта шпонки с пазом ступицы колеса [4с.6] =.
Допускаемые давления в соединении с натягом стальной ступицы на стальной вал [4табл.2.1]: []см=200МПа []изм=120МПа.
Условие износостойкости шпоночного соединения
=107МПа []изм=120МПа.
Условие прочности на смятие шпоночного соединения
max=×КП=99×14=138.6МПа []см=200МПа.
Расчет шпоночного соединения тихоходного вала со звёздочкой.
Исходные данные: Т=399Н×м КП=14; Lсm=80мм посадка переходная материал ступицы звёздочки – сталь d=36мм.
Выбираем призматическую шпонку с одним плоским и другим закругленным торцом. Допускаемая длина шпоночного паза L`=Lсm–S=80-4=76мм.
По диаметру d=36мм выбираем [4с.28] шпонку: в=10мм h=8мм L=70мм t1=5мм.
рабочая длина шпонки Lр=L-05×в=70-05×10=65мм.
Номинальное давление =.
Допускаемые давления в неподвижном соединении при переходной посадке стальной ступицы на стальной вал [4табл.2.1]: []cм=200МПа []изм=120МПа.
Условие износостойкости: =113МПа []изм=120МПа.
Условие прочности на смятие max=×КП=113×14=158МПа []см=200МПа.
2. Промежуточный вал.
Материал валаМеханические характеристики стали 40ХН:
. Эскиз и расчетная схема вала
Окружная сила Ft2 приложенная к колесу на радиусе d22 создает момент сопротивления направленный по вращению вала а окружная сила Ft3 приложенная к шестерне на радиусе d32 создает момент сопротивления направленный против вращения вала. Радиальные силы Fr2 и Fr3 направлены по радиусу к центру вала. Осевая сила Fa3 при правой винтовой линии нарезки зубьев ведущей шестерни и заданном вращении направлена от ведомого колеса быстроходной ступени а осевая сила Fa2 направлена в противоположную сторону.
Длину участков определяем по эскизу вала: a = 52 мм; b = 112 мм; c = 32 мм.
Силы в зацеплении:Ft3=3707H; Fr3=1355H; Fa3=350H;
Ft2=1031H; Fr2=378H; Fa2=125H;
Крутящий момент Т=114Н×м.
d2=227.62мм. d3=61.5мм. da=64мм. df=58.38мм.
2.1Построение эпюр изгибающих и крутящих моментов
Изгибающие моменты в горизонтальной плоскости на левом и правом конце:
Изгибающие моменты в вертикальной плоскости на левом и правом конце:
Крутящий момент в сечении вала равняется сумме внешних крутящих моментов крутящий момент направленный против часовой стрелки если смотреть на сечение со стороны внешней нормали. Крутящие моменты в сечениях вала:
на участках а и с - Т = 0; на участке b - Т = Тпром = 114 Н*м.
2.2.Расчёт вала на сопротивление пластическим деформациям по сечению в которых возникает наибольшее эквивалентное напряжение.
. Опасные сечения вала
На эскизе вала намечаем предположительно опасные сечения и сопоставляем их между собой используя эпюры моментов. Оставляем для расчета наиболее нагруженные сечения 3 и 6. Из двух сечений 4 и 5 выбираем для расчета сечение 4 т.к. оно ослаблено шпоночным пазом. Сечения 1278 исключаем т.к. они менее нагружены и не передают крутящего момента. Таким образом оставляем для дальнейшего расчета сечения 3 4 и 6.
Эквивалентные напряжения в сечениях вала
Крутящие моменты в намеченных сечениях вала определяем по эпюре крутящих моментов: Т3 = Т4 = Т6 = 114 Н*м.
Моменты сопротивления сечений вала при изгибе Wи и кручении Wк определяем по формулам
в сечении 3 участок вала диаметром dП = 25 мм
в сечении 4 вал диаметром dК = 32 мм ослаблен шпоночным пазом t1 = 5 мм и b =10 мм.
в сечении 6 шестерня с эвольвентными зубьями
Расчет вала на сопротивление пластическим деформациям выполняем по сечению 3 в котором возникает наибольшее эквивалентное напряжение. Напряжение в опасном сечении вала при кратковременной перегрузке (Кпер = 14) по формуле
Коэффициент запаса по пределу текучести материала вала по формуле
Для расчета вала на сопротивление усталости выбираем сечение 4. Выбор сечения 4 обусловлен тем что большие номинальные напряжения в нем сочетаются с концентрацией напряжений от шпоночного паза и от насаженной детали.
2.3. Расчет вала на сопротивление усталости по сечению 4
В сечении вала нереверсивного редуктора напряжения изгиба изменяются по симметричному циклу а напряжения кручения - по отнулевому циклу. Средние напряжения цикла и амплитуды напряжений по формулам 3.5 и 3.6
Коэффициенты влияния абсолютного размера поперечного сечения проходящего по шпоночному пазу глубиной t1 = 4 мм тогда dш = dк – h = 32 – 8 = 24 мм вала из легированной стали при изгибе и кручении находим применяя линейную интерполяцию:
Эффективные коэффициенты концентрации напряжений для концов участков валов со шпоночными пазами выполненными концевой фрезой для бВ = 920 МПа:
при изгибе по формуле
где в соединении с посадочным диаметром 24 мм;
при кручении по формуле
при изгибе по формуле для бВ = 920 Мпа; и Ra = 63 мкм
Коэффициенты влияния среднего напряжения цикла соответственно при изгибе и кручении по формулам
Пределы выносливости гладких образцов из стали 40ХН при изгибе и кручения с симметричными циклами по табл.
по нормальным напряжениям по формуле
по касательным напряжениям по формуле
Коэффициент запаса прочности по усталости при совместном действии напряжений изгиба и кручения по формуле
Условие прочности сечения 4 по сопротивлению усталости выполняется:
2.4. Выбор и расчет подшипников
Предварительно выбираем по каталогу радиальные шарикоподшипники лёгкой серии 205 у которых
Силы приложенные к подшипникам возьмем из уточненного расчета валов Осевой нагрузки в этих расчетах нет поэтому на том же рисунке показываем осевую силу направляя ее в сторону противоположную направлению равнодействующей сил Fa2 и Fa3. Величина воспринимаемой подшипником В осевой силы FВа = Fa3 – Fa2 = 350 – 125 = 225 Н.
Радиальные нагрузки на подшипники:
Осевые нагрузки на подшипники:
Эквивалентная динамическая нагрузка подшипника В по формуле
KБ = 13 по табл.] для редукторов;
X и Y выбраны по табл.
параметр осевого нагружения равен
Эквивалентная динамическая нагрузка подшипника А по формуле
Наиболее нагруженным является подшипник В и Pmax = 3585 Н.
Коэффициент эквивалентных динамических нагрузок по формуле
Эквивалентная динамическая нагрузка подшипника В при переменном режиме нагружения по формуле
Расчетный ресурс подшипника В при вероятности безотказной работы 09 по формуле
а1 = 1 по табл. для вероятности безотказной работы 09
а23 = 08 по табл. для обычных условий применения.
2.1. Расчет шпоночного соединения промежуточного вала с колесом.
Исходные данные: Т=114Н×м КП=14 Lсm=38мм d=32мм посадка с натягом материал колеса – сталь.
Выбираем призматическую шпонку с закругленными торцами. Допускаемая длина шпоночного паза L`=Lсm–2S=38-2×4=30мм.
По диаметру d=32мм выбираем шпонку: в=10мм h=8мм L=32мм t1=5мм.
Рабочая длина шпонки Lр=L-в=32-10=22мм.
Допускаемые давления в соединении с натягом стальной ступицы на стальной вал: []см=200МПа []изм=120МПа.
Условие износостойкости =107МПа []изм=120МПа.
Условие прочности на смятие max=×КП=107×14=150МПа []см=200МПа.
3. Быстроходный вал.
Под эскизом вала составляем его расчетную схему. Силы в зацеплении:Ft=1031H; Fr=378H; Fa=125H;Fм=125Н. Крутящий момент ТТ=27Н×м.
Размеры: а=31мм в=31мм с=63мм d1=5238мм.
3.1.Построение эпюр изгибающих и крутящих моментов.
Крутящий момент в сечении вала равняется сумме внешних крутящих моментов крутящий момент направленный против часовой стрелки если смотреть на сечение со сторона внешней нормали. Крутящие моменты в сечениях вала:
на участке а - Т = 0; на участках b и c - Т = Т1= 27 Н*м.
3.2.Расчёт вала на сопротивление пластическим деформациям по сечению в которых возникает наибольшее эквивалентное напряжение.
Крутящие моменты в намеченных сечениях вала определяем по эпюре крутящих моментов: Т1 = Т3 = Т4 = Т5 = 201 Н*м.
в сечении 1 конец вела диаметром d = 32 мм ослаблен канавкой и глубиной h = 025 мм
в сечении 3 участок вала диаметром dп = 40 мм
в сечении 4 участок вала диаметром dТ = 48 мм
в сечении 5 шестерня с эвольвентными зубьями
Коэффициент запаса по пределу текучести материала вала по формуле:
3.3. Расчет вала на сопротивление усталости
В сечении вала нереверсивного редуктора напряжения изгиба изменяются по симметричному циклу а напряжения кручения - по отнулевому циклу. Средние напряжения цикла и амплитуды напряжений по формулам 3.5 и 3.6 [5 c.13]:
Коэффициенты влияния абсолютного размера поперечного сечения проходящего по канавке диаметром dK = d – 2h = 32 – 2*025 = 315 мм вала из легированной стали при изгибе и кручении находим по табл. 3.4 [5 c.14] применяя линейную интерполяцию:
при изгибе ; при кручении .
при изгибе по формуле:
где в соединении с посадочным диаметром 14 мм;
Коэффициенты влияния среднего напряжения цикла соответственно при изгибе и кручении по формулам
Пределы выносливости гладких образцов из стали 40ХН при изгибе и кручения с симметричными циклами
3.4. Выбор и расчет подшипников
Предварительно выбираем по каталогу радиальные шарикоподшипники лёгкой серии 208 у которых
Силы приложенные к подшипникам возьмем из уточненного расчета валов Осевой нагрузки в этих расчетах нет поэтому на том же рисунке показываем осевую силу направляя ее в сторону противоположную направлению силы Fa4. Величина воспринимаемой подшипником осевой силы FАа = Fa1 = 125 Н. При данном направлении силы наихудшая комбинация сил для подшипника А.
KБ = 13 по табл. 5.4 для редукторов;
Эквивалентная динамическая нагрузка подшипника B по формуле
Наиболее нагруженным является подшипник В и Pmax = 1013 Н.
Расчетный ресурс подшипника В при вероятности безотказной работы 099 по формуле
а1 = 021] для вероятности безотказной работы 099;
а23 = 07 для обычных условий применения.
3.5 Расчет шпоночного соединения конца быстроходного вала с полумуфтой
Исходные данные : - вращающий момент ;
- коэффициент перегрузки
- посадка переходная
Выбираем призматическую шпонку с одним плоским а другим закругленным торцом.
Допустимая длина шпоночного паза:
По диаметру выбираем [4 с. 28];
С глубиной паза вала
Рабочая длина шпонки [4 с. 4].
Наименьшие давление на поверхность контакта шпонки с пазом ступени полу муфты [4 с. 6].
Допускаемые давления в неподвижном соединении при переходной посадки чугунной ступица на стольной вал [4 табл. 2.1];
Условие износостойкости шпоночного соединения
Условия прочности на смятие шпоночного соединения
Конструкция и эксплуатация установки
1. Конструкция редуктора смазка зубчатого зацепления и подшипников
В данном курсовом проекте представлен расчет привода цепного транспортера. Привод состоит из электродвигателя двухступенчатого цилиндрического соосного редуктора. Редуктор представляет собой двухступенчатую косозубую цилиндрическую передачу.
Рассчитываем основные размеры редуктора:
Толщина стенки редуктора
Толщина стенки крышки:
Болты для крепления крышки с корпусом:
принимаем d = 10 мм.
Диаметры болтов и их число для крепления редуктора к плите:
принимаем Межосевое расстояние тихоходной ступени: 140 мм тогда число фундаментных болтов – 6.
Для смазывания передачи применяется картерная система смазки. В корпус редуктора заливается масло так чтобы венец колеса был в него погружен на всю свою ширину. Колеса при вращении увлекают масло разбрызгивая его внутри корпуса. Масло попадает на внутренние стенки корпуса откуда стекает в нижнюю его часть. Внутри корпуса образуется взвесь частиц масла в воздухе которая покрывает поверхность расположенных внутри корпуса деталей. Для смазки шестерни тихоходного вала в данном редукторе установлено дополнительно смазывающее колесо изготовленное из полимера а также для смазки центральной опоры соосных валов в ней имеются отверстие и щель сквозь которые масло проникает к подшипниковому узлу.
Выбор смазочного материала основан на опыте эксплуатации. Принцип назначения масла следующий: чем выше окружная скорость колеса тем меньше должна быть вязкость масла и чем выше контактные давления в зацеплении тем большей вязкостью должно обладать масло. Поэтому требуемую вязкость масла определяют от контактного напряжения и окружной скорости колес выбирают марку масла для смазывания зубчатых передач. Для одноступенчатого конического редуктора при окружной скорости до 2 мс и контактных напряжениях 600 1000 МПа находим рекомендуемую вязкость 60 мм^с далее выбираем марку масла.
Используем масло марки: И-Г-А-68 [2 стр. 172-173]. Hm=b=32 мм
Объем масляной ванны
2. Выбор стандартных муфт.
Для передачи крутящего момента от двигателя редуктору выбираем муфту упругую с торообразной оболочкой. Муфты такого типа обладают большой крутильной радиальной и угловой податливостью.
Размеры муфты по заданному моменту подбирают по справочникам и атласам.
При выборе муфты должно выполняться условие:
Выбираем муфту Муфта 90-36-1У ГОСТ 20884-82.
Вращающий момент с полумуфт на оболочку передается силами трения созданными при затяжке винтом. При передаче момента в оболочке возникают касательные напряжения крутильного сдвига. Наибольшего значения они достигают в кольцевом сечении диаметром D1 [2 стр. 295-296]:
Полученный расчетом размер D необходимо округлить до стандартного ( ГОСТ 20884-82).
Оболочки диаметром D300 мм выполняют из резины. Для них принимают допускаемые касательные напряжения
Приняв число винтов z определяют трбуемую силу затяжки а по ней необходимый диаметр винтов. Затяжка винтов контролируется.
3. Конструкция рамы.
При монтаже приводов состоящих из электродвигателя и редуктора должны быть выдержаны определенные требования точности относительного положения узлов. Для этого узлы привода устанавливают на сварных рамах или литых плитах.
При единичном производстве экономически выгоднее применять рамы а при серийном выпуске изделий выгоднее применять плиты. В данном случае выпуск мелкосерийный однако требуемую высоту выходного вала редуктора невозможно обеспечить конструкцией плиты поэтому для данного привода изготавливается сварная рама.
Рамы изготавливают путем сваривания стального прокатного сортамента а именно: полос швеллеров уголков и пр. Размеры рамы определяются конструктивно руководствуясь компоновкой устанавливаемых на ней узлов.
Раму крепят к полу фундаментными болтами которые размещают на бобышках приваренных к полкам стоек. С целью повышения жесткости высоких рам бобышки выполняют высокими для жестких рам достаточно косых шайб.
4. Эксплуатация установки и техника безопасности
Данная установка предназначена для привода цепного транспортера. При эксплуатации установки необходимо:
-проверять уровень масла и при необходимости долить нужное количество;
-при выработке масла заменить его новым;
-периодически проверять крепеж агрегатов привода на случай отвинчивания болтов и винтов.
Для предотвращения растекания масла при его замене и сливе используется сливное отверстие с "бородой". Данная конструкция сливного отверстия не позволяет маслу растекаться по наружной поверхности корпуса. Это позволяет намного уменьшить возможность растекания масла.
Обеспечивать хорошее заземление редуктора.
Вращающиеся элементы закрыть кожухами.
Список используемой литературы.
Задание на контрольные работы и курсовой проект по деталям машин:
Методические указания сост. А.В.Олешкевич В.Н. Демокритов. – УлГТУ.2002
Дунаев П.Ф. Конструирование узлов и деталей машин: Учеб. Пособие для студ. Техн. Спец. Вузов П.Ф.Дунаев О.П.Леликов. – 8-е. изд. «Академия» 2003.
Проектирование механических передач: Учебно – справочное пособие для вузов С.А.Чернавский и др. – 5-е изд.1984.
Шпоночные и шлицевые соединения: Методические указания Сост. В.И.Тарханов - УлГТУ 1995.
Расчет и конструирование валов: Методические указания сост. В.И.Тарханов – УлПИ 1994.
Расчет и выбор подшипников качения: Методические указания сост. В.И.Тарханов – УлПИ 1993.
спецификация привод.dwg
Винт М10х14.56 ГОСТ 1478-75
М20х310.58 ГОСТ 24379.1-80
Редуктор цилиндрический
А132М8У3 ГОСТ 19523-81
Шайба 10 65Г ГОСТ 6402-70
Шайба 18 65Г ГОСТ 6402-70
Шайба 20 65Г ГОСТ 6402-70