Спроектировать привод ленточного конвеера



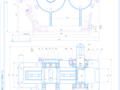

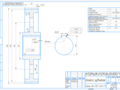
- Добавлен: 04.11.2022
- Размер: 440 KB
- Закачек: 0
Описание
Состав проекта
![]() |
![]() ![]() ![]() |
![]() ![]() ![]() ![]() |
![]() |
![]() ![]() ![]() |
![]() ![]() ![]() |
![]() ![]() ![]() |
![]() ![]() ![]() ![]() |
![]() ![]() ![]() |
Дополнительная информация
Содержание.docx
Выбор двигателя. Кинематический расчёт привода
Расчет клиноременной передачи
Конструирование шкивов клиноременной передачи
Расчет закрытой цилиндрической зубчатой передачи
1 Выбор материала колеса и шестерни
2 Определение допустимых напряжений
3 Допускаемые напряжения на изгиб
Расчет геометрических размеров цилиндрической зубчатой передачи
1 Проверочный расчёт
2 Конструирование цилиндрического колеса
Расчёт валов редуктора
1 Выбор материала для валов.
Определение реакций в опорах подшипников
Проверочный расчет подшипников
Расчет изгибающих моментов тихоходного вала.
Проверочный расчет муфты
Проверочный расчет тихоходного вала
Посадки зубчатого колеса и подшипников
Список использованной литературы
Редуктор А1.cdw

Spetsifikatsia.doc
КП.ДМиОК.01.09.02.00.000
КП.ДМиОК.01.09.03.00.000
Маслоуказатель жезловый
КП.ДМиОК.01.09.04.00.000.ГЧ
КП.ДМиОК.01.09.05.00.000
КП.ДМиОК.01.09.06.00.000.ГЧ
КП.ДМиОК.01.09.07.00.000
КП.ДМиОК.01.09.08.00.000
Крышка подшипника глухая
КП.ДМиОК.01.09.09.00.000
КП.ДМиОК.01.09.10.00.000
Крышка подшипника сквозная
КП.ДМиОК.01.09.11.00.000
КП.ДМиОК.01.09.12.00.000
КП.ДМиОК.01.09.13.00.000
КП.ДМиОК.01.09.14.00.000
КП.ДМиОК.01.09.15.00.000
КП.ДМиОК.01.09.00.00.000.СБ
Редуктор цилиндрический
КП.ДМиОК.10.04.00.00.000.ПЗ
Масло индустриальное И-Г-А-32
РГР ДМ Фаттахов.docx
Спроектировать привод ленточного конвеера данным таблицы и графика нагрузки
Рис. 14. Схема привода к ленточному конвейеру:
-Клиноремённая передача; 2-Редуктор; 3-Цепная муфта.
Тяговая сила ленты F кН
Диаметр барабана D мм
Допускаемое отклонение скорости ленты %
Выбор двигателя. Кинематический расчёт привода
Мощность на валу рабочей машины:
Pдв.= Ft*V=3*140875=48 кВт .
где 2- КПД ременной передачи 2 =095;
- КПД зубчатой цилиндрической передачи 3 =096 ;
под- КПД пары подшипников под = 0982;
муф.- КПД муфты муф=098 ;
По мощности двигателя и асинхронной частоте вращения выбираем подходящую модель: 4АМ112М4У3.
вых частота выходного вала
Общее передаточное число с учетом номинальной частоты вращения двигателя:
Uприв.=Uрем.*Uцил.з=1188
Пример стандартное значение для цилиндрического редуктора:
Расчет кинематических параметров валов:
Угловая скорость вала электродвигателя:
Угловая скорость первого вала:
Угловая скорость второго вала:
Момент на валу двигателя:
Момент на первом валу:
Момент на втором валу:
Т2= Tдв* Uрем.*= 36366*297*095*099=10158 Н*м.
Момент на третьем валу:
Т3= = T2*Uцил.з.* Н*м.
Расчет клиноременной передачи
Выбор сечения ремня и типа исходя из условий:
nдв.номин. =1445 обмин
Следовательно выбираем клиновый ремень сечение "A".
Определение минимально допустимого диаметра ведущего шкива d1 min
Выбираем ведущий шкив d1 большим диаметром чем d1 min : 100мм.
Определение диаметра ведомого шкива d2
d2= d1*Uрем.*(1-)=100*297*(1-002)=291 мм
Выбираем диаметр ведомого шкива d1 и d2 из стандартного ряда:
Определение фактического передаточного числа Uф и проверка его отклонения от заданного :
Ориентировочное межосевое расстояние a мм:
а=055*(d1+d2)+h=055*(100+280)+87=2177
Расчетная длина ремня мм :
=2a+*(d2+d1)+= 2*2177+05*314(280+100)+=10692 мм.
Выбираем из стандартного ряда:
Уточнение значения межосевого расстояния:
Угол обхвата ремнем ведущего шкива 1 град. 1 120.
=180-57* 120- условие выполняется.
Скорость ремня V мс :
V= ≤ [V] где [V] = 25 мс – допускаемая скорость для клиновых ремней
Частота пробегов ремня u с-1:
u= ≤ [u]; где [u] = 30 с-1 – допускаемая частота пробегов.
Допускаемая мощность передаваемая одним клиновым ремнем [Pп] кВт:
[Pп] = *Сα**Cz = *0.89*1*0.90=1165 кВт [3].
Количество клиновых ремней z:
Сила предварительного натяжения F0 Н:
Окружная сила передаваемая комплектом клиновых ремней Ft Н:
Ft = Pном.*= 22* =29092 Н.
Сила натяжения ведущей F1 и ведомой F2 ветвей Н:
F1 = F0 + = 130702 +29092(2*5)=15979 Н.
F2 = F0 - =130702 -=10161 Н.
Сила давления на вал Fоп. Н:
Fоп. = 2*F0*z*sin = 2*130702 *5*sin(2)= 1203.56 Н.
Максимальное напряжение в сечении ведущей ветви клинового ремня:
max= 1+u+V≤ []р A – площадь сечения мм2 [2]
где 1 - напряжение растяжения;
= + =130702 81+290922*5*81=1.97 МПа.
u = Eu *=90*87100=7.83 Нмм2 .
V - напряжение от центробежных сил ρ – плотность материала ремня
V = ρ * V2 * 10-6=1300*75622*10-6=0074 Нмм2
max= 1.97 +7.83 +0074 =9.874 МПа
87410–условие прочности выполняется
Конструирование шкивов клиноременной передачи
Наружный диаметр шкива мм:
de= dp+2t=100+2*33=1066
где dp - расчетный диаметр шкива.
=(z-1)*p+2f=(5-1)*15+2*10=80 мм
Толщина обода для чугунных шкивов клиноремнных передач мм
d=1.2(t+h)=1.2(33+87)=144
Значения коэффициентов t f r h выбираются по таблице 5.3
в соответствии с выбранным типом ремня.[2]
c=1.2*d=1.2*144=1728
Центральная часть шкива насаживаемая на вал называется ступицей.
d=1.6*d=1.6*144=2304
где d - диаметр отверстия.
Для ведущего шкива d равен диаметру выходного участка вала электродвигателя d=dдв. Для ведомого шкива определить диаметр d можно по формуле:
Где Т2 – крутящий момент на ведомом валу Нмм.
Расчет закрытой цилиндрической зубчатой передачи
1 Выбор материала колеса и шестерни
Для колес с твердостью активных поверхностей зубьев меньше 350 единиц по Бринелю (НВ≤350) применяют стали марок 40 45 50 50Г 35Х 40Х 45Х 40ХН 35ХМА З0ХНЗА 34ХМ и другие. Требуемую твердость активных поверхностей зубьев обеспечивают термообработкой нормализацией или улучшением. Эти стали позволяют изготовить колеса по упрощенной схеме с чистовой обработкой заготовки и зубьев после термообработки. [1]
Исходя из перечисленных условий зададимся материалом стали-45 . [3].
Заготовка шестерни Dпред=125мм;
Заготовка колеса Sпред=80мм
Твердость заготовки поверхности 235 262 НВ
а =780; =540; -1=335
2 Определение допустимых напряжений
Где - КHL = - коэффициент долговечности
NHE = 60*n*c* t0 - эквивалентное число циклов нагружения
где n – частота вращения зубчатого колеса обмин;
с – число зацеплений зуба за один оборот колеса (число колес
находящихся в зацеплении с рассчитываемым);
t0 = t2*365*24*Kгод * Kсут - расчетный срок службы передачи ч.
t0=3*365*24*04*03=3153.6 ч
NHE=60*121633*1*365*3*24 =1917909144
3 Допускаемые напряжения на изгиб
Допускаемые изгибные напряжения определяют:
где SF – коэффициент безопасности по изгибным напряжениям
Расчет геометрических размеров цилиндрической зубчатой передачи
Определяем межосевое расстояние аw мм:
аw= Ка*(U+1)*= 450*(41)*
примем аw = 140 мм . из стандартного ряда.
U - передаточное число ступени («+» для внешнего зацепления «-» для внутреннего зацепления);
KH - коэффициент нагрузки; в предварительных расчетах можно принять равным KH = 12 15 выбирая меньшие значения для более точных передач и при расположении зубчатых колес ближе к середине валов а большие значения - для менее точных передач при расположении у опор;
T - крутящий момент на ведомом валу ступени Нм;
[H] – допускаемые контактные напряжения МПа;
ba = ba – коэффициент ширины зубчатых колес выбираемый из ряда стандартных значений в соответствии с ГОСТ 2185–66
b2 = *аw= 0315*140=441 мм
ширина b1 - шестерни
Расчет нормального модуля m мм:
Минимальный модуль mmin определяется из условия прочности по следующей зависимости:
где Кm - коэффициент равный 34103 для прямозубых передач
КF - коэффициент нагрузки принимаемый равным КH
Нормальный модуль зубчатых колес определяют (с дальнейшим округлением по ГОСТ 9563-60) из следующих соотношений: m = b2 m; m ≥ mmin [1]
5≥0335 – Условие выполняется.
примем m=15 из стандартного ряда.
Определяем суммарное число зубьев шестерни и колеса:
для прямозубых колес z:
z= z1+z2 = 2*awm =2*
Определяем число зубьев шестерни z1:
Определяем число зубьев колеса z2:
z2 = z - z1 =186-37=149
Определяем основные геометрические параметры передачи мм :
делительный диаметр d1 – шестерни d2 – колеса:
d1 = m*z1 = 15*37=555мм ;
d2 = m*z2 = 15*149=2445мм ;
диаметр вершин зубьев da1 - шестерни da2 - колеса:
da1= m*(z1+2)=15*(37+2)=585мм ; принимаем 60 мм из стандартного ряда.
da2= m*(z2+2)=15*(149+2)=2465мм ; принимаем 250 мм из стандартного ряда.
диаметр впадин зубьев df1 - шестерни df2 - колеса:
df1= m*(z1-2.5)=15*(37-2.5)=5075 мм ; принимаем 50 мм из стандартного ряда.
df2= m*(z2-2.5)=15*(149-2.5)=23725мм ; принимаем 240 мм из стандартного ряда.
1 Проверочный расчёт
Окружную скорость колеса V мс определяют по формуле
Степень точности = 9
Проверочный расчет на контактную выносливость проводят по зависимости
где осредненные значения коэффициента zа равны 9600
КH - коэффициент нагрузки учитывающий неравномерность распределения нагрузки между зубьями по ширине венца а также возможные динамические нагрузки в зацеплении.
КH=1*1*1.05=1.05 где KHα - коэффициент распределения нагрузки;
KHα = KFa = 1 для прямозубых передач.
KH – коэффициент концентрации нагрузки для прирабатывающихся колес KH = 1.
Проверочный расчет на выносливость при изгибе проводят для зубьев шестерни и колеса:
где KF= KFαKFKF - коэффициент нагрузки учитывающий влияние динамических и дополнительных (внутренних) нагрузок
где Ft - окружная сила определяемая по формуле Н:
Ft=2*103*T1d1=2*103*36366555=1310
> F Условия прочности выполняются.
2 Конструирование цилиндрического колеса
С = (025..03) = 025504 = 126 мм. Округлим до 12 мм.
Внутренний диаметр ступицы мм:
D =+(10 12) = +10 = 5907 Примем d = 60 из стандартного ряда
Наружный диаметр ступицы мм:
dст = 155d = 155 60 = 93 мм.
Полученное значение округлим до 90 из ближайшего значения из ряда нормальных линейных размеров (Ra40)
Диаметр центров отверстий в диске колеса мм:
Диаметры отверстий в диске колеса мм:
Расчёт валов редуктора
1 Выбор материала для валов.
Марка стали : сталь 45
-я ступень. Диаметр первой ступени d1:
где Н*м - крутящий момент на быстроходном валу
= 10 - допускаемое напряжение на кручение для быстроходного вала.
Примем из стандартного ряда R40: d1 = 38 мм.
Длина первой ступени l1:
Примем из стандартного ряда R40: l1= 45 мм.
Диаметр второй ступени d2:
d2 = d1+5=38+5=43 мм .
Примем из стандартного ряда: d2= 42 мм ;
Длина второй ступени l2:
l2= 15*d2 = 15*42=63 мм.
Диаметр третей ступени d3:
d3 = d2+ 32*r =43+96=526 мм;
Длина третей ступени определяется графически.
Диаметр четвертой ступени d4:
Исходя из имеющихся условий выбираем для быстроходного вала радиальный однорядный шариковый подшипник 211 из легкой серии.
D=100 мм. - наружный диаметр подшипника ;
d= 55 мм.- внутренний диаметр подшипника ;
B=21 мм. - ширина подшипника ;
Длина четвертой ступени l4:
l4 = B+r= 21+25=235 мм.
Примем 24 мм изстандартного ряда.
Диаметр первой ступени d1 :
где Н*м - крутящий момент на тихоходном валу;
= 20 - допускаемое напряжение на кручение.
Примем: d1 = 45 мм .
l1 = 15*d1 =15*45=675 мм.
Выбираем 67 мм из стандартного ряда.
Диаметр второй ступени d2:
d2 = d1+2t=45+2*28=506 мм;
Выбираем 50 мм из стандартного ряда.
l2= 2*d2 = 2*50=100 мм.
Диаметр третей ступени d3:
d3 = d2+ 32*r = 50+96 = 596 мм.
Выбираем 60 мм из стандарного ряда.
Длина третей ступени l3 :
l3= b2+20 = 48+20 = 68 мм.
Примем 67 мм из стандартного ряда.
Исходя из имеющихся условий выбираем для тихоходного вала радиальный однорядный шариковый подшипник 212 .
D=110 мм. - наружный диаметр подшипника ;
d= 60 мм.- внутренний диаметр подшипника;
B=22 мм. - ширина подшипника ;
l4 = B+r= 22+25=245 мм.
Примем 25 мм из стандартного ряда.
Определение реакций в опорах подшипников
Окружная сила в зацеплении Ft Н:
Радиальная сила в зацеплении Fr Н:
Fr = Ft tg20 = 1298 0363 = 47145 Н.
Консольная сила муфты Fм Н:
Fм 125 = 125 = 24563 Н.
Составляем уравнение моментов всех сил относительно опоры А
Составляем уравнение моментов всех сил относительно опоры В
774 – 1298 – 29357 + 24563 = 0
Проверочный расчет подшипников
Предварительно был выбран радиальный однорядный подшипник 212.
Пригодность подшипника определяется сопоставлением расчетной динамической грузоподъемности Crр с базовой Сr или базовой долговечности L10h с требуемой Lh по условиям:
Сrp ≤ Cr – динамическая грузоподъемность
L10h > Lh – срок службы подшипников
m = 3 - модуль зацепления;
Re = V * Rr * K * KT - эквивалентная нагрузка;
V = 1 - коэффициент вращения при вращающемся внутреннем кольце подшипника [1];
K = 1 коэффициент безопасности;
KT = 1 - температурный коэффициент;
Rr = RC = 2927.75 Н - суммарная радиальная реакция на тихоходном валу.
Re = 1 * 2927.75 * 1 * 1 = 2927.75 H.
Условие Сrp ≤ Cr выполняется.
Условие L10h ≥Lh выполняется.
Расчет изгибающих моментов тихоходного вала.
Строим эпюру относительно оси Х в сечениях 1 4:
Строим эпюру относительно оси Y в сечениях 1 4:
Суммарные изгибающие моменты:
Выбираем втулочно-пальцевую упругую муфту.
nma D = 170; L= исполнение; I = 225 мм; II =169 мм; Dп = 130; dп =14;
Проверочный расчет муфты
D = D0 + (15 16) * d0
lвт = 82 zc = 6 dп = 18.
>см условие выполняется.
>и условие выполняется.
а) Параметры шпонки под муфту:
Рабочая длина шпонки со скругленными торцами:
Допускаемое напряжение на смятие:
cм условие выполняется шпонка обеспечивает надежное соединение.
б)Параметры шпонки под колесо:
cм[]см условие выполняется шпонка обеспечивает надежное соединение.
Проверочный расчет тихоходного вала
Нормальное напряжение:
Полярный момент инерции сопротивления сечения:
Касательное напряжение
Коэффициенты концентрации нормальных и касательных напряжений:
Пределы выносливости в данном сечении вала и пределы выносливости гладких образцов при симметричном цикле изгиба и кручения: 058 = 2378;
Коэффициенты запаса прочности по нормальным и касательным напряжениям:
Общий коэффициент запаса прочности:
Сопротивление усталости обеспечивается.
Нормальное напряжение :
Касательное напряжение
= 02 d3 = = 40250.55 мм3.
Смазывание редуктора производится картерным непроточным способом.
Подшипники смазываются разбрызгиванием масла колесом редуктора масленым туманом а также при растекании масла по валам.
Объем масляной ванны определяется из расчета 04 08 л на 1 кВт передаваемой мощности:
При контактных напряжениях Н = 515 ( ) и скорости v = 25 (мс) рекомендуемая вязкость масла должна быть равна 35 мм2 с.
Масла заливается до уровня обеспечивающего погружение зубчатого колеса на 12 мм.
Выбираем масло индустриальное И-Г-А-32 по ГОСТ 17479.4 - 87.
Посадки зубчатого колеса и подшипников
Посадки назначают в соответствии с ГОСТ 25347 – 82.
-посадка муфты на тихоходный вал : ;
-посадка зубчатого колеса на вал : ;
-посадка шкива ременной передачи на быстроходный вал: ;
-посадка подшипников качения:
-отклонение отверстия
-посадка распорных колец:;
-посадка шпоночных соединений: ;
-посадки крышек подшипников:
Сборку производят в соответствии со сборочным чертежом редуктора начиная с узлов валов.
Сборка редуктора осуществляется следующим образом:
-Установить корпус редуктора на стенд.
-Вручную установить предварительно собранный тихоходный вал.
-Вручную установить предварительно собранный быстроходный вал.
-Организовать зубчатое зацепление.
-Установить глухие крышки подшипников.
-Установить крышку редуктора.
-Далее проверить вращение колеса от руки проконтролировать биение выходного вала.
-Осуществить контроль болтовых соединений а также контроль герметичности.
Список использованной литературы
И.П.Талипова Р.Н.Тазмеева Учебное пособие «Расчет и проектирование передач с использованием систем автоматизированного проектирования»–Набережные Челны: изд-во НЧИ КФУ2017 . –104с
А.Е. Шейнблит. Курсовое проектирование деталей машин: учебное пособие
М изд. 3-е. Издательство АТП 2015 – 456 с.:ил.
titulnik.docx
Автомобильное отделение
Кафедра «Кафедра механики и конструирования»
Курсовая работа по дисциплине «Детали машин»
студент группы 1151113
Колесо А3.cdw

сопряжённого зубчатого колеса
Допуск торцового биения
Допуск на радиальное биение
Данные для контроля взаимного
расположения разноименных профилей
Степень точности по ГОСТ 1643-81
Коэффициент смещения
КП.ДМиОК.01.09.06.00.000.ГЧ
Сталь 40х ГОСТ 4543-71
Вал А3.cdw
Сталь 45 ГОСТ 8509-86
* Размер обеспечивает инструмент.