Курсовой проект (колледж) - Разработка ТП обработки детали Тарель




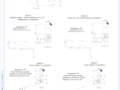
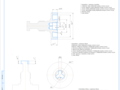
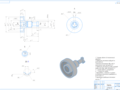
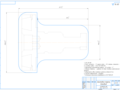
- Добавлен: 04.11.2022
- Размер: 5 MB
- Закачек: 0
Узнать, как скачать этот материал
Подписаться на ежедневные обновления каталога:
Описание
Курсовой проект (колледж) - Разработка ТП обработки детали Тарель
Состав проекта
![]() |
![]() |
![]() ![]() ![]() |
![]() ![]() ![]() ![]() |
![]() |
![]() ![]() ![]() |
![]() |
![]() ![]() ![]() ![]() |
![]() |
![]() ![]() ![]() |
Дополнительная информация
Контент чертежей
tarel_-_eskiz.cdw

tarel.cdw

Рекомендуемые чертежи
- 11.06.2017
- 18.10.2023
- 24.01.2023
- 04.11.2022
- 25.01.2023
- 04.11.2022
Свободное скачивание на сегодня
Обновление через: 50 минут