Автоматзация производственных процессов




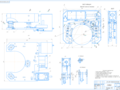
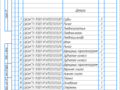
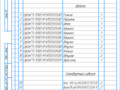
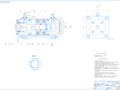
- Добавлен: 04.11.2022
- Размер: 512 KB
- Закачек: 0
Описание
Курсовой проект - Автоматзация производственных процессов
Состав проекта
![]() |
![]() |
![]() ![]() ![]() |
![]() ![]() ![]() |
![]() ![]() ![]() ![]() |
![]() ![]() ![]() ![]() |
![]() ![]() ![]() ![]() |
![]() ![]() ![]() |
Дополнительная информация
схват-спецификация.spw

Спецификация гидроцилиндр.spw

Чертеж циклограммы с временем.cdw

Гидроцилиндр.cdw

Схват.cdw

Рекомендуемые чертежи
- 20.06.2015
- 24.01.2023