Автоматизации производственных процессов




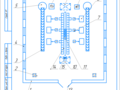
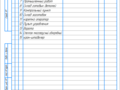
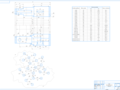
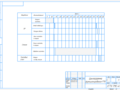
- Добавлен: 24.01.2023
- Размер: 634 KB
- Закачек: 1
Описание
Автоматизации производственных процессов
Состав проекта
![]() |
![]() ![]() ![]() ![]() |
![]() ![]() ![]() ![]() |
![]() ![]() ![]() |
![]() ![]() ![]() ![]() |
![]() ![]() ![]() |
Дополнительная информация
циклограмма.cdw

план автом.cdw

Автоматизация моя.doc
Конструкторский контроль чертежа и анализ технических условий на изделие4
Оценка степени подготовленности детали к автоматизированному производству5
Обоснование вида заготовки9
Выбор технологических баз и их обоснование11
Проектирование варианта технологического процесса автоматического производства и выбор технологического оборудования12
Размерный анализ технологического процесса13
Разработка окончательного варианта технологического процесса для автоматизированного производства13
Расчеты режимов обработки затрат времени на выполнение технологических переходов и синхронизация выполнения технологических переходов на позициях автоматизированного оборудования14
Разработка структуры автоматизированного производства и построение циклограммы работы комплекса20
Вспомогательное транспортно-загрузочное оборудование для компоновки автоматизированного комплекса20
Анализ установочных размерных связей на одной из позиций автоматизированного производственного комплекса22
Описание принципиальной схемы и принципа работы автоматизирующего устройства26
Описание компоновки и работы автоматической линии и циклограмма последовательности работы комплекса или отдельных его механизмов и узлов28
Выбор структуры системы управления автоматизированным комплексом30
Выводы и заключение30
Список используемой литературы31
Автоматизация производственных процессов - генеральное направление развития народного хозяйства одно из главных условий построения материально – технической базы страны.
Автоматизация открывает неограниченные возможности для повышения производительности общественного труда. Особое значение имеет автоматизация машиностроительного производства.
На основе развития машиностроения осуществляется механизация и автоматизация всей промышленности.
Современные тенденции развития машиностроительного производства ориентированного на коренное повышение качества машиностроительной продукции на широкое применение прогрессивных конструкционных и инструментальных материалов упрочняющей технологии на комплексную автоматизацию. На основе применения станков с ЧПУ и САПР требуют подготовки квалифицированных специалистов обладающих не только глубокими теоретическими знаниями но и способных практически их использовать в своей производственной деятельности
На механизацию и особенно автоматизацию машиностроительного производства необходимы значительные капитальные затраты. Если объект выбран удачно эти затраты окупаются быстро. В короткие сроки достигается высокая экономическая эффективность а если идти по пути «сплошной» автоматизации то вместо экономии можно получить убыток.
Данная курсовая работа заключается в создании автоматической станочной системы механообработки.
Служебное назначение детали и условие ее работы в изделии
Ползун № 387 входит в механизм штампа.
Назначение детали. Ползун № 387 – деталь служащая для передачи поступательного движения в штампе и закрепления в нем необходимого инструмента.
Нагрузки. Ползун №387 – деталь работающая под действием средних статических и динамических нагрузок. Дефекты: износ поверхности соединения в связи с попаданием пыли и грязи в область трения деталей необходимость частого смазывания.
Для изготовления заготовки рекомендуется сталь конструкционная легированная сталь 20Х ГОСТ 4543-71
В обозначение марки стали: первые цифры указывают массовую долю углерода; буква а – для горячей обработки давлением.
Табл. 1 Химический состав в % стали 20Х
Табл. 2 Механические свойства при Т=20oС Стали 20Х.
Твердость стали 20Х после отжига
Твердость стали 20Х калиброванного нагартованного
Конструкторский контроль чертежа и анализ технических условий на изделие
Деталь «Ползун №387 » изображена на рабочем чертеже форматав трех проекциях масштабе 1:1. На этих видах не указаны все размеры и предельные отклонения в соответствии с ГОСТ 2.305-68.
Все несоответствия сведены в нижеследующую таблицу.
Изображение на чертеже
Изображение в соответствии с ГОСТом
Табл. 3 Несоответствие обозначений
В общем чертеж составлен правильно. Имеется вся необходимая информация касающаяся видов разрезов технических требований отклонений шероховатости материала заготовки и т.д. Присутствуют все проекции виды четко объясняющие ее конфигурацию и возможные способы получения заготовки. Не хватает лишь одного размера – профрезерованного участка размером 70 мм.
Оценка степени подготовленности детали к автоматизированному производству
Операция 005 Токарная черновая:
) Асимметрия наружной конфигурации. Для металлической детали числовое значение кода – 1000000.
) Сцепляемые механически детали – 600000.
) Стержневая ферромагнитные имеют код – 10000.
) Круглые для прямых деталей код – 2000.
) Деталь имеет одну ось вращения одна ось симметрии – 100.
)Центральное отверстие сквозное форма детали гладкая - 20
) Деталь не имеет дополнительных признаков – 0.
Операция 010 Токарная черновая:
)Центральное отверстие отсутствуют - 10
Операция 015 Токарная чистовая:
Операция 020 Токарная чистовая:
Операция 025 Фрезерная:
) Паз на торце с одной стороны – 4.
Операция 030 Сверлильная:
Автоматизация средней сложности. Требуется отработка системы ориентации и загрузки детали в рабочие органы. Целесообразна экспериментальная проверка.
Обоснование вида заготовки
Заготовку для детали «Ползун №387» на базовом предприятии получают из проката. Данный метод получения заготовки не является рациональным так как при обработке детали требуются дополнительные затраты на снятие большого припуска для основного размера. Целесообразным вариантом получения заготовки будет штамповка.
Метод выполнения заготовки для данной детали будет определяться несколькими факторами: назначением детали конструкцией материалом техническими требованиями масштабом серийностью выпуска экономичностью изготовления.
Экономичность изготовления
Заготовка из сортового проката диаметром 55 мм.
Определим себестоимость заготовки получаемой способом характерным для данного предприятия. При расчетах экономичности изготовления данные берем из табл. 2.6 [1] (данные 1981 г.)
-технологическая себестоимость операций правки.
- приведенные затраты на рабочем месте (стр. 30 [1])
- штучное или штучно-калькуляционное время выполнения заготовительной операции т.е. резки.
М-затраты на материал.
Q – масса заготовки. Q=905 кг;
S – цена одного кг материала заготовки. S =011 руб.; (табл. 2.6 [1])
Q – масса готовой детали. q=235 кг;
Sотх– цена одной тонны отходов. Sотх.=0025руб. (табл. 2.7 [1]) руб.
Коэффициент использования материала:
Предлагаемый метод получения заготовки:
Заготовка получаемая штамповкой.
Стоимость заготовки по формуле:
=373руб-базовая стоимость 1т заготовок полученных на ГКМ (стр. 37 [1]).
Коэффициенты зависящие от класса точности группы сложности массы марки материала и объема производства заготовок:
=1 (нормальная точность).
= 1– для углеродистой стали
= 075 – для детали 1-й группы сложности. (табл. 2.12 [1] )
= 087 (табл. 2.12[1])
Массу заготовки Q определим по формуле:
Сравнивая методы получения заготовки существующий на заводе и предлагаемый можно установить значительное преимущество второго метода получения заготовки. Данные полученные в результате расчетов сведены в таблицу.
Наименование показателей
Альтернативный вариант
Годовой объем выпуска шт.
Коэффициент использования металла
Себестоимость заготовки руб.
Табл. 4 Экономичность изготовления
Выбор технологических баз и их обоснование
Одной из важнейших задач при проектировании технологических процессов механической обработки деталей является выбор технологических баз как для первых так и для последующих операций а так же соблюдение единства баз в процессе всей обработки детали с минимальным количеством переустановок.
При выборе базирующих поверхностей необходимо учитывать следующие обстоятельства:
)Базирующие поверхности должны быть выбраны так чтобы при установке детали и ее зажима деталь не смещалась с приданного ей положения и не деформировалась в недопустимых пределах под воздействием зажима и сил резания;
)Базирующие поверхности должны быть достаточной протяженности и расположены как можно ближе к месту возникновения сил резания;
)Неточность установки детали будет зависеть от неточности размеров и неправильной геометрической формы опорных установочных баз.
Выбирают две системы баз – основные базы и черновые используемые для базирования при обработке основных баз.
Проведя анализ технологического процесса можно сделать вывод:
- На всех операциях в качестве баз используются обработанные поверхности(кроме первой операции) что позволяет соблюсти довольно высокую точность обработки.
- Соблюдается принцип совмещения баз.
- Соблюдается принцип постоянства баз – т.е. на всех этапах механической обработки использованы одни и те же базовые поверхности обрабатываемой детали.
В данном случае выбор баз способствует тому что при установке детали в патроне она не будет смещаться с приданного положения. Поверхности обладают достаточной протяженностью по сравнению с общей длинной детали и расположены близко к источнику возникновения сил резания что уменьшает вероятность увеличения погрешности за счет деформаций. Опорные поверхности имеют правильную фору что облегчает закрепление детали и надежное удержание в процессе обработки. В данном случае все вышеуказанные обстоятельства учтены и можно сделать вывод что базовые поверхности выбраны правильно.
Проектирование варианта технологического процесса автоматического производства и выбор технологического оборудования
Наименование операции и перехода
Точить черн. Пов. 6101819
станок токарный патронно-центровой модели 16Б16Т1С1 с ЧПУ
Точить черн. пов. 543
Точить чист. Пов. 6101819
Точить чист. пов. 543
Фрезеровать шпоночный паз и поверхность 11 789
Станок фрезерный с ЧПУ 6Т13Ф3
Сверлить отверстия диаметром 12 4 и 2 мм.
обрабатывающий центр модели ИР320ПМФ4
Табл. 5 вариант технологического процесса
Размерный анализ технологического процесса
До недавнего времени расчет точности технологических процессов осуществлялся на основе методов построения и расчета размерных цепей. Однако в последнее время эти методы вытесняются более эффективными методами основанные на построении и расчете графов технологических процессов. При выполнении данного этапа целесообразно использовать данную методику. Расчет представлен в приложении (на чертеже).
Разработка окончательного варианта технологического процесса для автоматизированного производства
Наименование операции
Табл. 6 Окончательный вариант технологического процесса
Расчеты режимов обработки затрат времени на выполнение технологических переходов и синхронизация выполнения технологических переходов на позициях автоматизированного оборудования
Определяем оперативное время обработки:
где То –основное время Тхх-время холостых ходов Ттр- время на зажим и разжим а также на транспортирование заготовки.
5- токарная с ЧПУ (черновая)
По паспорту станка S0=06 мм.об.
Принимаем n=395 об.мин.
0- токарная с ЧПУ (черновая)
5- токарная с ЧПУ (чистовая)
0- токарная с ЧПУ (чистовая)
Lр.х.=10+105+3=235 мм.
Расчетное Sow=S*i=0.3*1.25=0.375
По паспорту Sow=0.32 ммоб.
Т=12+02+005=145 мин.
Расчет необходимого такта автоматической линии производится по формуле:
где - такт выпуска изделий на автоматической линии
Фд - действительный годовой фонд времени работы технологического оборудования в часах.
Q – годовой объем выпуска деталей в штуках.
Действительный годовой фонд времени определяется по формуле:
где Фн – номинальный годовой фонд времени оборудования в часах при 41- часовой рабочей неделе и двухсменной работе Фн =4140 часов; К- коэффициент учитывающий необходимые потери времени на профилактические работы и ремонт оборудования в процентах. Этот коэффициент принимается для металлообрабатывающего оборудования имеющего категорию сложности до 30- равным 3 свыше 30- равным 6.
Фд=4140·(1-)=38916 ч.
Одна автоматическая линия из выбранного оборудования.
Синхронизация имеет целью обеспечение равенства времени выполнения технологических переходов на каждой позиции автоматической линии с тактом автоматической линии.
Среднее оперативное время меньше такта автоматической линии следовательно требуется выполнить синхронизацию.
повышение режимов обработки за счет увеличения скорости резания
снижение режимов обработки за счет уменьшения скорости резания
Табл. 7 Синхронизация
Разработка структуры автоматизированного производства и построение циклограммы работы комплекса
Данная поточная линия механической обработки детали Ползун №387 состоит из 6 единиц оборудования. Имеется механизированная уборка стружки. Используется автоматизированная складская система с кареткой для автоматического адресования грузов и автоматическим кран-штабелером. Данный участок имеет площадь 180 м2. В результате выбора здания и сетки колон 18000х12000 и типовой секции 72000х72000 данная поточная линия находится в левом верхнем углу цеха механической обработки.
Вспомогательное транспортно-загрузочное оборудование для компоновки автоматизированного комплекса
Каретка-оператор представлена на рисунке.
Шасси тележки представляет собой сварную силовую раму 11 на кронштейнах которой смонтированы две оси с четырьмя ходовыми колесами 12. С одной стороны одной стороны рамы устанавливается подвижный бампер13 который в случае наезда тележки на посторонние предметы включает систему торможения и останова. Привод перемещения каретки-оператора состоит из электродвигателя постоянного тока 2 редуктора 1 на выходном валу которого установлено зубчатое колесо которое находится в зацепление с шестерней расположенной на ведущей оси ходовых колес. Платформа установки спутников представляет собой плиту 3на которой установлены направляющие планки с роликами 4 для базирования спутника и защелка предохраняющая спутник от смещения при движении тележки. Привод подачи спутника 5 обеспечивает его перемещение с платформы тележки по направляющим планкам к агрегату загрузки спутников либо к ячейке оперативного накопителя. Блок электроавтоматики установлен на стойке 6 шасси тележки к нему относятся чувствительные элементы 9 систем торможения и точного останова каретки-оператора состоит из электропривода и фиксатора который входит в отверстия в колодках расположенных в пунктах останова тележки.
Подвод электропитания к электрооборудованию обеспечивает кабеленесущую цепь 8. От наладочного пункта 7 возможно выполнение отдельных элементов цикла работы каретки-оператора.
Работа тележки осуществляется автоматически управление от ЭВМ. Тележка по команде поступающей от управляющей ЭВМ включает электродвигатель привод перемещения каретки-оператора и датчик позиционирования расположенной в пункте её требуемого останова. При подходе тележки к заданной позиции во взаимодействие с устройством позиционирования вступает вначале датчик системы торможения а затем датчик точного останова. Затем каретка-оператор фиксируется. После этого включается привод подачи спутника с платформы тележки на оборудование комплекса. На этом цикл работы тележки заканчивается. После поступления от ЭВМ новой информации каретка-оператор перемещается к пункту указанному в следующем адресе.
Ползун не имеет плоскости симметрии перпендикулярную к оси вращения поэтому необходимо двойное ориентирование в пространстве: ориентирование по отношению оси вращения и по отношению к плоскости перпендикулярной к оси вращения.
Применяем бункеро-ориентирующее устройство (рис.). Бункеро-ориентирующее устройство (БОУ) принимает заготовки “навалом” накапливает их и ориентирует в пространстве с помощью автоматических ориентирующих механизмов.
Рис. Схема устройства для вторичного ориентирования
Первичное ориентирование детали обеспечивается попаданием в простые карманы (зона 1) в дальнейшем вращающийся диск переносит детали в зону 2 где они зависают на перегородках карманов и в зависимости от положения центра тяжести поворачиваются так что проваливаются в окно 3 в одинаковом положении – происходит их вторичное ориентирование. Деталь из бункера подается на подводящий транспортер в свободное гнездо.
Между отводящими и подающими транспортерами также устанавливаются бункеро-ориентирующие устройства.
Анализ установочных размерных связей на одной из позиций автоматизированного производственного комплекса
Составляющими звеньями установочных размерных связей являются: размеры заготовки приспособлений которые выявляются при построении размерных цепей по общей методике размерного анализа конструкции. Выявление установочных размерных связей и их расчёт производится со следующим целями:
обеспечить работоспособность автоматической системы в течении требуемого времени эксплуатации в условиях действия различных факторов влияющих на стабильность составляющих размеров и размерных связей;
выбрать методы и средства автоматизации обеспечивающие требуемые размерные связи сформулированные требования к размерной точности автоматических устройств реализующих автоматическую установку;
выбрать методы и способы размерной наладки системы т.е. средства технического оснащения используемых в процессе наладки;
определить регламент обслуживания и профилактики автоматических загрузочных устройств;
определить допускаемые ограничения внешних воздействий при работе автоматических устройств.
Рассмотрим размерные связи возникающие при автоматической установки заготовки на станок во фрезерной операции:
Рис.3.Схема размерных связей
В- отклонение от соосности зажимного устройства станка и оси загружаемой заготовки
В1 – отклонение от соосности заготовки в схвате.
В2 – программируемые перемещения схвата.
В3 – расстояние от базы
В4 – расстояние между станком и роботом.
В5 – расстояние от оси зажимного устройства станка до основной базы станка.
Установку заготовки в патрон и съем детали осуществляет робот. Робот берет заготовку захватом вносит ее в рабочую зону станка так чтобы ось заготовки совпадала с осью раскрытых кулачков патрона и затем задвигает заготовку в патрон после чего подается команда на зажим кулачков патрона. Ввод заготовки в раскрытые кулачки патрона возможен если В не превышает значения:
Где D – диаметр раскрытой призмы зажимного устройства станка d – диаметр устанавливаемой в призму заготовки.
Кулачки сдвигающиеся к оси призмы при наличии отклонения от соосности будут стремиться переместить заготовку в новое положение. Заготовка пока еще закреплена в захвате робота. Следовательно возникнут силы при передаче заготовки от робота в патрон.
Где j – жесткость системы робот – заготовка – патрон.
Пусть j = 500 нм Р 100 н
тогда ВD = Р j = 100500 = 02 мм.
Размерная цепь ВD=В2 – В1 – В5 – В4 – В3
Метод достижения точности – метод полной взаимозаменяемости. При данном методе допуск замыкающего звена ТD = Т1+Т2+Т3+Т4+Т5
Допуск соосности ВD = ± 02 мм составил ТD =04 мм.
Очевидно обеспечить условие для автоматической установки практически нельзя. Возможно несколько путей решения поставленной задачи.
Сократить допуск размеров составляющих звеньев; использовать предварительно обработанные заготовки для уменьшения погрешности заготовки; расширить допуск замыкающего звена ТD.
Из формулы из которой было получено значение допуска следует что решение при той же допустимой силе может быть обеспечено снижение жесткости закрепления заготовки в захвате робота. Этот путь наиболее удобен и поэтому захват роботов делают подпружиненным. Однако чрезмерно уменьшать жесткость тоже вредно так как при установке изделия различной массы будут большие погрешности позиционирования оси заготовки в захвате по высоте.
Можно использовать робот с автоматической поисковой системой управления.
Для загрузки станков выбираем робот с погрешностью
позиционирования ± 1мм.
ТD 2 = 1+0325+0205+0235+0235
Описание принципиальной схемы и принципа работы автоматизирующего устройства
ОПИСАНИЕ РОБОТА М20П. 40. 01
Промышленный робот М20П. 40. 01 предназначен для автоматизации складирования погрузки деталей и смены инструмента на металлорежущих станках (1 или 2 станка) может работать в составе робототехнических комплексов и гибких автоматизированных производств.
В состав робота входят:
устройство программного управления промышленного робота
(УПУ ПР) «Контур 1».
Манипулятор робота М20П. 40. 01
Кинематическая схема манипулятора робота М20П. 40. 01 приведена на рис.4. Приводы звеньев Z q и R – электрические звена a и схвата – пневматические. В табл.7 приведены некоторые технические характеристики манипулятора робота М20П. 40. 01Ошибка! Источник ссылки не найден..
Кинематическая схема манипулятора робота 20П. 40. 01:
2 3 4 – степени подвижности; 5 – схват
Технические параметры
манипулятора робота М20П. 40. 01
Потребляемая мощность кВт
Максимальная скорость
Минимальная скорость
Устройство управления робота М20П. 40. 01
Промышленный робот М20П. 40. 01 оснащен устройством программного управления (УПУ ПР) «Контур 1».
Назначение и состав УПУ ПР «КОНТУР 1»
УПУ ПР «Контур 1» предназначен:
для управления манипулятором в ручном и автоматическом режимах;
для управления оборудованием робототехнического комплекса (РТК) в ручном и автоматическом режимах;
для приема сигналов от оборудования РТК в автоматическом режиме.
Укрупненная структурная схема УПУ ПР «Контур 1»приведена на рис.5.
Рис.5.Укрупненная структурная схема УПУ ПР «Контур 1»
Описание компоновки и работы автоматической линии и циклограмма последовательности работы комплекса или отдельных его механизмов и узлов
Данная автоматическая линия механической обработки детали «ползун» состоит из 6 единиц станочного оборудования 6 промышленных роботов модели М20П.40.01 предназначенных для загрузки станков 6 тактовых столов типа СТ220 на платформы которого с помощью каретки-оператора устанавливаются и снимаются в ориентированном виде заготовки и обработанные детали. Общая площадь занятая оборудованием составляет 180 м2.
Линия оснащена средствами механизированной уборки стружки (по типу шнекового конвейера). Заготовки поступают с общего склада заготовок при помощи каретки-оператора с платформы которого заготовки перегружаются в автоматическом режиме на платформу тактового стола далее промышленный робот берет заготовку устанавливает ее на станок. После окончания обработки робот снимает деталь со станка и устанавливает ее на тактовый стол после чего стол поворачивается на одну позицию.
Циклограмма представляет собой графическое изображение последовательности работы отдельных элементов и подсистем .
Расчет времени элементов цикла работы РТК.
Отвод руки из зоны обработки
Подвод руки в зону обработки
Зажим заготовки в призме
Разжим заготовки в призме
Перемещение заграждения
Поворот на одну позицию
Выбор структуры системы управления автоматизированным комплексом
Структура системы управления автоматизированным комплексом представлено в приложении.
В результате выполнения курсового проекта по разработке Т.П. крышки подшипника выполнено следующее:
- проведен анализ существующего на производстве Т.П. по действительной технологии и выявлены возможности его совершенствования;
- проведен конструкторский контроль чертежа детали выявлено его соответствие ГОСТам
- Т.П. на основе анализа маршрута разделен на черновые чистовые;
- спроектирована операционная технология использующая усовершенствованный вариант;
- выполнен расчет точности Т.П. с использованием теории графов;
- спроектирован ТП. удовлетворяющий всем условиям автоматизированного производства.
- спроектирована автоматическая линия для производства крышки подшипника.
Список используемой литературы
А.Ф. Горбацевич В.А. Шкред Курсовое проектирование по технологии машиностроения. 4-е издание переработанное и дополненное. Москва. Высшая школа 1985г. 658 стр.
Справочник технолога – машиностроителя в двух томах. Том 1 (под редакцией А.Г. косиловой и Р.А. Мещерикова – 4-е издание. Москва. Машиностроение 1985г. 656 стр.
Построение и расчет графов технологических процессов. Методические указания по и дипломному проектированию. (А.В. королев С.М. Болченко – Саратов 1981г. 14 стр.)
В.И. Анурьев. Справочник конструктора – машиностроителя. В трех томах том 1 издание пятое. Москва. Машиностроение 1979г. 728 стр.
Королев А.В. Гущин А.Ф. Шалунов В.З. Размерный анализ Т.П. механической обработки деталей. Учебное пособие Саратов 1998г.
А.В. Королев Н.А. Можаева. «Оптимизация Т.П.» Саратов 2001г.
Ю. Г. Козырев “Промышленные роботы” Справочник. М. Машиностроение. 1988г. 392с.
Г. П. Мельников В. П. Вороненко. “Проектирование механосборочных цехов” М. Машиностроение. 1990г. 352с.
А. Ф. Гущин П. Ю. Бочкарев. Обеспечение качества выпускаемых изделий в автоматизированном производстве на основе размерного анализа. Учебное пособие. СГТУ. 2000г. 78с.
В.П. Вороненко В.А. Егоров М.Г. Косов Д.Р. Попов и др. «Проектирование автоматизированных участков цехов» Высшая школа 2003. 272с.
Граф автом.cdw

СПЕЦа.CDW

Рекомендуемые чертежи
- 24.01.2023
- 20.06.2015