Проектирование технологического процесса производства гайки М1110



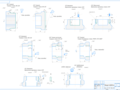
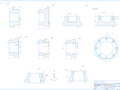
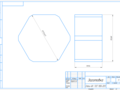
- Добавлен: 04.11.2022
- Размер: 446 KB
- Закачек: 0
Узнать, как скачать этот материал
Подписаться на ежедневные обновления каталога:
Описание
Курсовая работа - Проектирование технологического процесса производства гайки М1110
Состав проекта
![]() |
![]() ![]() ![]() |
![]() ![]() ![]() ![]() |
![]() ![]() ![]() ![]() |
![]() ![]() ![]() |
Дополнительная информация
Контент чертежей
Пояснительная.docx
1 Назначение и конструкция детали
2 Анализ технологичности детали
3 Определение типа производства
4 Разработка маршрута обработки детали
5 Выбор и обоснование метода получения заготовки
6 Расчет припусков по таблице
7 Расчет режимов резания
8 Расчет технической нормы времени
Машиностроение поставляющее необходимую и новую технику всем отраслям хозяйства определяет технический прогресс страны и оказывает решающее влияние на создание материальной базы нового общества. В связи с этим его развитию придавалось и придается первостепенное значение.
Темпы развития машиностроения характеризуются не только улучшением конструкции машин но и непрерывным совершенствованием технологии их производства. В настоящее время важно качественно дешево и в заданные плановые сроки с минимальными затратами живого и общественного труда получить изделие применив современное высокопроизводительное оборудование инструмент технологическую оснастку средства механизации и автоматизации производства.
В условиях развивающегося машиностроения автоматизация является средством повышения эффективности общественного производства и как следствие этого повышения технологического уровня производства.
Автоматизация производственных процессов есть комплекс мероприятий по разработке новых прогрессивных технологических процессов и проектированию на их основе высокопроизводительного технологического оборудования осуществляющего рабочие и вспомогательные процессы без непосредственного участия человека.
На первых этапах своего развития автоматизация охватывала главным образом процессы механической обработки таких массовых изделий как блоки цилиндров двигателей кольца подшипников поршни и т.д. В настоящее время широким фронтом развернулась автоматизация не только механической обработки но и литейного производства штамповочного производства термической и термохимической обработок контроля сборки и т.д.
Технический прогресс в машиностроении связан главным образом с заменой устаревшего металлорежущего оборудования новым обеспечивающим более высокую степень механизации и автоматизации. Автоматизация металлорежущего оборудования приобрела большое значение так как на предприятиях страны эксплуатируются в настоящее время большое количество станков требующих переналадки при переходе на обработку новых деталей что в свою очередь требует проектирования большого количества новых технологических процессов и оснастки.
За последние десятилетия в серийном производстве наблюдалось два этапа технического перевооружения.
Первый этап состоял в замене универсального оборудования с ручным управлением обслуживаемого рабочими-универсалами высокой квалификации оборудованием с автоматическим циклом обработки то есть настроенном на автоматическое обеспечение качества (главным образом точности) обработки позволяющим организовать многостаночное обслуживание рабочими-операторами а переналадку станков на разные детали осуществлять наладчиками по тщательно разработанным операционным и наладочным картам.
Второй этап (наиболее перспективный и продолжающийся в данное время) связан с внедрением станков с числовым программным управлением (токарных расточных фрезерных шлифовальных сверлильных и т.д.) имеющих технологические преимущества перед оборудованием с “жестким” управлением требующим больших затрат подготовительно-заключительного времени на ручную переналадку его для обработки разных деталей. Станки с ЧПУ и особенно многооперационные (типа обрабатывающих центров) с оперативными системами управления от микроЭВМ и ПК обладают высокой универсальностью а смена программ обработки и автоматическая переналадка станка занимает в десятки раз меньше подготовительно-заключительного времени чем при ручной наладке. Такая гибкость в переналадках помимо сокращения рабочих мест является ценным технологическим и экономическим качеством в современных условиях все большего сокращения сроков изготовления машин неизменной конструкции. Наиболее развивающимся направлением является объединение станков с ЧПУ с промышленными роботами автоматическими переналаживаемыми средствами межоперационного транспорта складами и измерительно-наладочными устройствами. Такое объединение образует гибкие производственные системы (ГПС) роботизированные технологические комплексы (РТК) управляемые от ЭВМ.
Такое техническое перевооружение производства требует разработки многочисленных систем автоматизированного проектирования технологической подготовки производства (САПРТПП) а в первую очередь технологических процессов обработки затем вытекающих из них этапов проектирования специальных режущих измерительных вспомогательных инструментов приспособлений а также определения планово-экономических показателей обработки. Автоматизация технологической подготовки значительно сокращает сроки подготовки производства за счет автоматизации инженерного труда. Современные гибкие производственные системы не могут быть спроектированы организованы и запущены в работу без автоматизированного проектирования систем управления технологическим процессов и его подготовки. На базе ПК в настоящее время создаются автоматизированные рабочие места (АРМ) специализированные для технологов конструкторов экономистов и других специальностей соединенных между собой и центральной вычислительной машиной (ЦВМ) сетью.
В данное время для автоматизации подготовки производства наиболее широко применяются высоко развитые мощные системы САD(Computer Aided Disign-компьютерная помощь проектировщику)CAM(Computer Aided Manufacturing-компьютерная помощь производству) такие как КОМПАС-ГРАФИК AutoCAD SolidWorks ProE + различные модули и библиотеки к этим программам.
Вследствие широкого внедрения и характерных особенностей станков с ЧПУ (одна из основных - их высокая точность) потребовалась специальная технологическая оснастка. Режущий инструмент является составной частью комплексной автоматизированной системы станка с ЧПУ обеспечивающей его эффективную эксплуатацию. От выбора и подготовки инструмента зависят производительность станка и точность обработки. В связи с этим режущий инструмент станков с ЧПУ должен обладать: стабильными режущими свойствами хорошо формировать и отводить стружку обеспечивать заданную точность обработки обладать универсальностью быть быстросменным. Приспособления к станкам с ЧПУ должны обеспечивать: высокую точность установки заготовок не снижать жесткости системы СПИД быть быстропереналаживаемыми не препятствовать перемещению режущего инструмента в процессе работы иметь простые установочно-зажимные элементы.
Применение различных средств автоматизации производства имеет существенные особенности и создает определенные преимущества в частности следующие: сокращение сроков подготовки производства сокращение общей продолжительности цикла изготовления продукции экономию средств на проектирование и изготовление продукции и технологической оснастки и многое другое.
1Назначение и конструкция детали
Деталь представляет собой гайку внутри которой два совмещённых цилиндра разных диаметров между которыми технологическая канавка радиусом R10.5. Гайка 81.26.326 - М110 (8 отв) - Зубчатая гайка для крепления шкива на торце оси колесной пары пассажирских вагонов. На внутренней стороне меньшего цилиндра расположен зубчатый венец (делительный диаметр которого ø90H11(+022)) для передачи крутящего момента на зубчатый венец. Внутренняя сторона большего цилиндра представляет собой резьбу М110х4-5H6H. Также на внешней стороне меньшего цилиндра (представляет конус) располагается шпоночный паз под призматическую шпонку. На правом торце расположены 8 отверстия М12-7Н.
Хим. состав и механические свойства стали приведем в таблице 1.1
Таблица 1.1 – Химический состав материала
Массовая доля элементов %
Таблица 1.2 – Механические свойства материала
Предел прочности при растяжении в НММ2
Предел текучести НММ2
Сталь 40Х – сталь конструкционная углеродистая качественная. Прочность у данного материала повышенная. Относится к трудно свариваемым материалам поверхности можно подвергать термической обработке. Использование в промышленности: вал-шестерни коленчатые и распределительные валы шестерни шпиндели цилиндры бандажи и др.
Анализ технологичности детали
Деталь – гайка – изготовляется из конструкционной легированной стали 40Х прокатом поэтому конфигурация поверхностей не вызывает значительных трудностей при получении заготовки.
Деталь представляет собой тело вращения – два цилиндра разных диаметров. Максимальный диаметр детали ø172 при длине 90h14. В торце со стороны меньшего наружного диаметра ø145 расположены восемь резьбовых отверстия М12-7Н по ø125. На внутреннем диаметре ø90Н11 нарезаны зубья модулем m=3. В отверстии ø110 нарезана резьба М110х4-5Н6Н. Для выхода долбяка предусмотрена канавка в месте перехода внутренних диаметров ø90Н11 и ø110 радиусом R10.5 шириной 19.
Боковые поверхности зубьев (эвольвенты) зубчатого венца модуля m=3 – Rz20. Квалитеты допусков на размеры проставлены в соответствии со служебным назначение поверхностей.
Базовым отверстием является отверстие ø110 (базовая поверхность В). Относительно базы В у детали имеются допуски на расположение ( перпендикулярность) правой торцевой поверхности не более 02 а также радиальное биение зубчатых венцов модуля m=3 не более 03.
В результате анализа чертежа детали на технологичность делаю вывод что деталь в целом является технологичной т.к. не требует специального оборудования и уникальной оснастки позволяет использовать установившиеся приёмы обработки.
Коэффициент точности обработки детали
где Qтч.н - число размеров необоснованной степени точности обработки;
Qтч.о. – общее число размеров подлежащих обработки.
Ктч. 01т.к. размеры точности обработки обоснованы
Коэффициент шероховатости поверхности детали
где Ош.н.- число поверхностей детали необоснованной шероховатости;
Ош.о.- общее число поверхностей детали подлежащих обработке.
Кш 01т.к. поверхности детали обоснованной шереховатости
Коэффициент использования материала
Ки.м. = 1014.2 = 07.
Показатель высокий - технологична.
Минимальное значение параметра шероховатости обрабатываемых поверхностей Ra 63 мкм
3 Определение типа производства выбор формы организации технологического процесса
Типы производств и формы организации труда определяют характер технологического процесса и его построение. Тип производства определяется для данной детали объемом выпуска (годовой производственной программой их массой и габаритными размерами). Пользуясь условиями классификации отнесем детали к средним по массе (М=10 кг). К средним относят детали 1М50. С учетом годовой программы N=1000по таблице 1 [16 с.23] примем тип производства крупносерийным
где n – количество деталей в партии шт.;
N – количество деталей одного наименования и размера по годовой программе выпуска изделий шт.;
t – необходимый запас деталей на складе в днях: для средних деталей 10 дней;
Фу – число рабочих дней в году Фу=255 дня при двух днях отдыха и продолжительности рабочего дня 8ч.
Для дальнейших расчетов примем n=39 шт
Такое количество позволяет каждый месяц запускать в производство по пять партий. (12·39·2 =936).
По данным таблицы 2 [16 с.20] при n=39будем считать производство крупносерийным. И дальше технологический процесс будем проектировать для условий такого производства.
Данный тип производства характеризуется ограниченной номенклатурой и сравнительно большим объемом выпуска изделий изготавливаемых периодически повторяющимися партиями.; используются автоматы оснащенные как специальными так и универсальными и универсально – сборными приспособлениями что позволяет снизить трудоемкость и себестоимость изготовления детали.
Для 1000применяем несколько видов станков Токарный станок ИЖ-250 предназначен для выполнения разнообразных токарных работ в центрах цанговых или кулачковых патронах; Вертикально фрезерный станок 6Н10 предназначен для сверления и выполнения расточных работ с заготовками любых форм и из любых материалов - от чугуна до сплавов цветных металлов; Универсальный токарный станок PROMA SPD-1000P предназначен для обработки тел вращения путём снятия с них стружки при обточке. На станке можно выполнять различные виды токарной обработки; Зубодолбежный станок модели 5М150ПФ3 модернизированный станок с механическими связями и предназначен для нарезания зубьев на цилиндрических шестернях внутреннего и наружного зацепления
Минимальный размер партии деталей запускаемый в производство:
Nmin= (Nгод*a*d*8)Fд= (1000*4*2*8)3940= 16 шт.
где а=5 дн. – периодичность запуска деталей; d=2 дн. – количество смен; – действительный фонд времени.
Целое число запусков в производство:
Nзап= NмесNmin= 8316=5.
Размер партии деталей:
N=NмесNзап=835=16 шт
4 Разработка маршрутного технологического процесса
Таблица 1.4 Маршрутный технологический процесс
Наименование и краткое содержание
Продолжение таблицы 1.4
Продолжение таблицы 1.4
Сверлильная (8 отв.)
Нарезаем резьбу М110
Вытачиваем шпоночный паз
Для данной детали массой 10 кг мы используем прокат так как это рационально для 1000шт. Вид проката или профиль: сортовой шестигранный горячекатаный повышенной и нормальной точности ГОСТ 2590-71.
6 Расчет припусков и межоперационных размеров
6.1 Расчет припусков табличным методом
) В соответствии с квалитетами переходов определяются допуски. Допуск берется в соответствие с ГОСТом 7505-89
) По чертежу детали определяются минимальный и максимальный размер поверхности
dmах = dном + dmin =dном+ei
) По справочникам определяются минимальные припуски по переходам.
) Определяются минимальные размеры заготовки для валов или максимальные для отверстий по переходам:
Для валов dmin i-1 = dmin i+2Zmin i
Для отверстий Dmax i-1- Dmax i + 2Zmin
) Определяются максимальные размеры деталей для валов или минимальные для отверстий:
dmax i-1 = dmin i-1 + Tdi-1
Dmin i-1 = Dmax i-1 – TDi-1
) Определяются максимальные припуски
Для валов 2Zmax i-1 = dmax i-1 – dmax i
Для отверстий 2Zmax i = Dmin i – Dmin i-1
) Определяем операционные размеры по переходам
Таблица 1.6.1 Карта расчета припусков на обработку
Наименован.поверхности
Операционный размер мм
Приведем расчет режимов резания для одной операций. Для остальных операций расчет в пояснительной записке не приводиться так как они рассчитываются по той же методике и результаты этих расчетов представлены в таблице 1.7.1.
7.1 Операция Сверлильная
) Глубина резания t= = = 35 мм.
) Подача на оборот So = 041 ммоб. [6 с.278 табл. 25].
) Скорость главного движения резания допускаемая режущими свойствами инструмента
KMV - коэффициент на обрабатывающий материал
KMV= = = 08 [6 с. 261 табл. 1];
KИv – коэффициент на инструментальный материал KИv=1 [6 с. 263 табл. 6];
Kпv =1 [6 с. 263 табл. 5].
Сv = 70; q = 0.4; y =0.7; m=0.20 [6 с. 278 табл. 28].
) Частота вращения соответствующая расчетной скорости
n = = = 146.5 обмин.
Корректирование частоты вращения по паспортным данным станка
nст обмин. Принимается ближайшее меньшее если большее но не
более чем на 5-10%. nст = 145 обмин.
) Действительная скорость главного движения
) Проверка достаточности мощности электродвигателя станка.
1. Мощность потребная на резание Npeз = кВт где:
Po=10·Cp·Dq·Sy-Kp H
где Ср = 68; q=10; y=070 [6 с. 281 табл. 32].
Po=10·68·3510·027070·069 = 6567 Н.
Мкр=10 ·См ·Dq ·Sy Кр Н·м
где СМ = 00345; q=20; y=080 [1 с. 281 табл. 32].
Мкр=10 ·00345 ·3520 ·02708 ·069 = 102 Н·м.
2. Мощность на шпинделе станка
Nшп.= Nдв · = 50·085 = 425 кВт (по паспортным данным станка) Должно быть выполнено условие Npeз Nшп (194 425).
) Определение основного времени
где L - длина рабочего хода инструмента L = l+y+y1(Δ)мм
где 1 - длина резания;
y1(Δ)= - величина перебега y1(Δ)= 1÷3 мм y1(Δ) = 0 - для глухих отверстий.
То==32мин.1.8 Расчет норм времени
8.1 Операция Токарная
Кtв – поправляемый коэффициент на ручное вспомогательное время Кtв=1 [7с. 35 карта 1]
t уст = 028 мин [7 с.39 карта 3]
Вспомогательное ручное время связанное с выполнением операции на приемы управления станком
-включить станок выключить – 005 мин;
-открыть заградительный щиток закрыть – 003 мин;
tв.оп = 005+003 = 008 мин. [7 с.50 карта 8]
tвр = 028·2+008 = 064 мин.
Вспомогательное автоматическое время на каждый переход составит:
-на одновременное ускоренное перемещение рабочих органов станка по осям координат Z и Х – 003 мин;
-на одновременное установочное перемещение рабочих органов станка по осям координат Z и Х – 008 мин;
-установочное перемещение в зоне резания – 005 мин;
-поворот резцедержателя на одну позицию – 007 мин.
tв.а = 003+008+005+008= 024 мин (на каждый переход)
Тв = 0631+0239 + 016 = 3мин.
) Оперативное время на операцию
Топер. = Тв+ То = 3+2566 = 2866 мин.
) Время на обслуживание и технические надобности
Тобсл.= 10% Топер. [7 с.65 карта 10]
Тшт. = (1+) = (1+) = 2976 мин.
где q – число одновременно обрабатываемых деталей q=1
)Подготовительно – заключительное время на операцию
Тп.з. = 16 мин – время на организационную подготовку станка [7 стр. 56-57 карта 2].
)Штучно-калькуляционное время
Тшк = Тшт + = 2976 + = 3005 мин.
8.2 Операция 020 Сверлильная
) Вспомогательное время на операцию
Тв = Ту + Тпер + Тизм
tу = 15 мин. [7 карта 12 с. 48-49]
tпер1 = 006 мин. [7 карта 27 с. 95]
Тпер = 6·006 = 036 мин.
Тизм = tизм1 + tизм2 = 009 + 013 = 022 мин.
tизм1 = 009 мин. [7 карта 86 с. 188 п. 68]
tизм2 = 013 мин. [7 карта 86 с. 191 п. 158]
Время на приемы связанные с переходом не вошедшие в комплекс:
время на прием «вкл» или «выкл» вращения шпинделя предусматриваем 2 раз; tв1 = 2 · 003 = 006 мин.;
Тв = 15 + 036 + 022 + 006 = 214 мин.
Топер. = То + Тв = 24 + 214 = 454 мин.
)Время на техническое обслуживание и технические надобности
Тшт. = Топер = 508 мин.
)Подготовительно-заключительное время на операцию
Определяем штучно-калькуляционное время на партию деталей
Тшк. = Тшт. + = 508 + = 535 мин.
Глубина резания t = h = 22 m = 22 8 = 176 (мм)
Подачана один оборот детали: sо.т= 26ммоб. (табл. 4).
Поправочные коэффициенты: Кs=12 sо=2612=312 ммоб. Корректируем по паспорту станка sо.ст=31ммоб.
Скорость резания определяется по формуле: vт=35ммин. (табл. 5).
Поправочные коэффициенты:К1=11; К2=12.v=351112=462 ммин. Частота вращения фрезы определяется по формуле.
По станку принимаем nст=100 об.мин.
Фактическая скорость резания определяется по формуле:
Таблица 1.8.1 Нормы времени
) Справочник технолога машиностроителя Под ред. А.Г. Косиловой и Р.К. Мещерякова. – М.: Машиностроение 1985;
) Гусев Беспалов Ковальчюк и др. «Технология машиностроения»;
) А.Ф. Горбацевич В.А.Шкред «Курсовое проектирование по Технологии машиностроения»;
) Балакшин Б.С. «Основы технологии машиностроения»;
) Егоров «Технология машиностроения»;
) Кузнецов Ю.И. Оснастка для станков с ЧПУ: Справочник.- М. Машиностроение 1982
Маршрут15(2).cdw

Токарный стонок ИЖ-250
Токарный станок ИЖ-250
Токарно-винторезный станок PROMA SPD-1000P
Вертикально-фрезерный станок 6Н10
Сталь 40Х ГОСТ 1050-2013
Операционные15(2).cdw

Рекомендуемые чертежи
- 24.01.2023
- 18.10.2023
- 24.01.2023
- 17.05.2023
Свободное скачивание на сегодня
Обновление через: 18 часов 32 минуты