Линия производство кормовой муки с расчетом барабанной сушилки


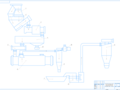
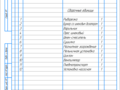
- Добавлен: 04.11.2022
- Размер: 1 MB
- Закачек: 2
Описание
Курсовая работа - Линия производство кормовой муки с расчетом барабанной сушилки
Состав проекта
![]() |
![]() ![]() ![]() ![]() |
![]() ![]() ![]() |
![]() ![]() ![]() ![]() |
Дополнительная информация
Спецификация мука.spw

кормовой муки с жомом
Линия по производству кормовой муки
Бункер со шнековым дозатором
Магнитное заграждение
Мельничная установка
Курсач !!!!!!.doc
Агрегатно-технологическая линия производства10
Описание конструкции сушильной установки барабанного типа18
Обоснование процесса сушки21
Расчет барабанной сушилки25
Пути интенсификации процесса протекающего в аппарате29
Список используемой литературы31
Основная цель рыбной отрасли - обеспечение населения качественными продуктами питания такими как: рыба продукты из гидробионтов консервы и полуфабрикаты. Кроме основных пищевых продуктов выпускают кормовые продукты полуфабрикаты ветеринарные и медицинские препараты;
Производство продукции кормового назначения основано на переработке малоценного в пищевом отношении сырья и пищевых отходов. Их переработке уделяют большое внимание потому что отходы переработки гидробионтов содержат полноценные белки жиры фосфорные и кальциевые соли витамины микроэлементы.
Различные рыбные отходы и рыба малоценные в пищевом отношении издавна применяли для подкорма животных и птиц. Мировая годовая потребность в кормовой рыбной муке составляет около 10 млн. т. при объемах производства 5 млн. т. по оценкам ФАО. Так для сельскохозяйственных предприятий России необходимо более 1 млн. т. продукции в год. Что совершенно не удовлетворяется рыбной отраслью. На промышленных и научно-исследовательских предприятиях проводится большая работа по повышению качества улучшению и расширению ассортимента выпускаемых продуктов созданию новых прогрессивных и высокорентабельных технологий.
На сегодняшний день технологии переработки гидробионтов не обеспечивают их безотходное экологически чистое и экономически оправданное использование. Приготовление большинства известных кормовых продуктов из отходов переработки гидробионтов базируется на относительно жестких технологических режимах нормативная документация не всегда регламентирует необходимый уровень качества что не позволяет получить продукцию высокой биологической ценности.
Существующее промышленное производство кормовых продуктов из гидробионтов не всегда эффективно а возможность регулирования технологии кормовых продуктов для их использования в сельском хозяйстве и аквакультуре изучена недостаточно. Часть отходов гидробионтов не используется а их уничтожение технически сложно ведет к загрязнению окружающей среды и является энергоемким.
Разрешить конкретные задачи промышленности быстро реализовать их на имеющемся оборудовании позволит совершенствование технологии традиционных кормовых продуктов из гидробионтов. Это применимо к производству компонентов комбикормов на основе отходов переработки гидробионтов. Химический состав и технологические свойства гидробионтов предполагает рассматривать их как ценное сырье не только для производства пищевых продуктов медицинских профилактических лечебных препаратов но и для кормовых продуктов и выделения комплекса ценных биологически активных соединений.
Разработка технологии приготовления кормовых продуктов является эффективным безотходным экологически чистым производством. Аминокислотный и жиро-кислотный состав растительных и животных отходов различны поэтому при одновременной тепловой обработке будут образовываться новые соединения которые обладают более высокой биологической активностью чем в случае механического смешивания различных компонентов как это имеет место в традиционном производстве комбикормов. Также эффективности компонентов комбикормов способствует стабилизация антиокислителем липидной фракции. Рыбную кормовую муку можно использовать не только для добавки к рациону сельскохозяйственных животных но и аквакультуре рыб.
ПИЩЕВАЯ ЦЕННОСТЬ ПЕРЕРАБАТЫВАЕМОГО РЫБНОГО СЫРЬЯ И КОРМОВОЙ МУКИ
На производство кормовой муки идут в основном отходы получаемые при разделки рыбы такие как мясо кожа голова кости плавники молоки икра печень.
Таблица 1 -Химический состав частей тела рыбы %
Минеральные вещества
Содержание белковых веществ в рыбе и отходах ее переработки колеблется в пределах 16 - 20% и зависит от ряда факторов среди которых наиболее важными являются вид рыбы и период лова. Липиды рыб имеют ряд особенностей которые обуславливают их существенное отличие от липидов животных и растений.
Основную массу липидов отходов триглицериды и фосфолипиды но иногда доминируют липиды непищевого значения (алкоксидиглицериды воска углеводы). Кроме этого могут присутствовать свободные жирные кислоты ди- и моноглицериды фосфолипиды (1 - 2%). Для жиров рыб характерно наличие жирных кислот с числом атомов углерода от С12 до С24 но доминирующими являются С14 С18 С20 С22.
Жиры содержат насыщенные и ненасыщенные жирные кислоты. В теле теплокровных животных преобладают жирные насыщенные кислоты с твердой консистенцией (пальмитиновая стеариновая). Особое значение с биологической точки зрения имеют ненасыщенные жирные кислоты (линолевая линоленовая и арахидоновая). Важную часть рыбных жиров составляют полиненасыщенные жирные кислоты являющиеся необходимыми компонентами пищи для животного организма при их отсутствии нарушается устойчивость правильное функционирование организма. По содержанию липидов сырьё предназначенное для производства рыбное муки подразделяется на три группы: тощее (содержание липидов менее 5%) средней жирности (до 10%) и жирное (более 10%). В зависимости от содержания липидов в сырье определяются технологии его переработки параметры технологического процесса. Например тощее сырьё может быть переработано способом прямой сушки без выделения жира сырьё средней и высокой жирности - прессово-сушильным способом с применением различных технологических приемов его обработки [3].
Углеводы представлены в основном гликогеном. Его содержание в сырье зависит от упитанности и физиологического состояния объекта. С целью сохранения углеводов целесообразно рыбу и отходы её переработки направлять на производство кормовых продуктов сразу после вылова.
Ферменты обуславливают характер и интенсивность протекания посмертных изменений в сырье. В мышечной ткани рыб обнаружено более 50 ферментов несущих ответственность за изменение органических веществ рыбы после вылова. Активность ферментных систем рыб не одинаково и зависти от вида рыбы сезона вылова. Наибольшей активностью отличаются сельдевые лососевые скумбриевые наименышей-минтай треска. Повышение температуры способствует активизации ферментных систем и в результате - снижению качества сырья и готовой продукции.
Для получения рыбной муки высокого качества необходимо использовать безупречно свежее сырьё. Автолитические процессы оказывают существенное влияние на качество сырья. Особо важную роль играют протеазы и амилазы. Наибольшей активностью обладают ферментные системы рыб в преднерестовый и нагульный периоды. Повышение температуры способствует активизации ферментов низкие температуры хлориды натрия магний уксусная и соляная кислоты ингибируют их.
Рыбное сырье предназначенное для производства рыбной кормовой продукции может храниться без охлаждения 12-24 часа. Если оно храниться дольше необходимо охлаждать его дробленым льдом или охлажденной морской водой. Однако охлаждение довольно дорогостоящий процесс поэтому для сохранения качества сырья используют консерванты такие как нитрит натрия и формальдегид. Добавления 25 г NaNO2 на 100 кг свежей рыбы увеличивает продолжительность её хранения до 22 суток. Внесение 01% формалина в виде раствора предохраняет рыбу от порчи уплотняет ткани. Дозировка выбирается таким образом чтобы содержание консервантов в рыбной муке не превышало 002%.
Ценность рыбного сырья во многом определяется и наличием в нем витаминов играющих важную роль в регулировании процесса обмена веществ в организме. В рыбе обнаружены водорастворимые (В1 В2 В6 В8 В12 РР и пантотеновая кислота) и жирорастворимые (А Д3 Е) витамины. Наибольшее содержание отмечается во внутренних органах что во многом определяет кормовую ценность рыбной продукции. Витамины группы В достаточно устойчивы к термическому воздействию и в процессе приготовления рыбной муки сохраняются. Большую ценность представляет витамин Р (группа незаменимых ненасыщенных алифатических жирных кислот с 18-20 атомами углерода имеющими 2 3 и 4 двойных связи: линоленовая линолевая и арахидоновая обладающие биокаталитическими функциями).
Особое место в составе рыбного сырья занимает вода находящаяся в частично связанном и частично (около 80%) свободном состоянии.
Минеральные вещества в сырье представлены макро- и микроэлементами характерными для среды обитания (Са Р Мg J А1 Cu Fe Co и др.).
В качестве сырья используют отходы целую рыбу неблагополучную в паразитарном отношении и рыбу любой жирности свежую соленую мороженную [1].
Свежее сырьё направляют на переработку в течении 1 суток с момента поступления. Если невозможно переработать в течении 1 суток его охлаждают льдом. Мороженое сырьё предварительно размораживают а солёное - отмачивают.
При поступлении на переработку очень жирного сырья (более 50%) его смешивают с тощим в отношении 1:3 или 1:4 для того чтобы улучшить процесс прессования отваренной массы с целью лучшего удаления из сырья влаги и жира.
АГРЕГАТНО-ТЕХНОЛОГИЧЕСКАЯ ЛИНИЯ ПРОИЗВОДСТВА
Технологическая схема предоставлена на рис. 1:
Рисунок 1 – Технологическая схема получения кормовой муки прессово-сушильным способом
- рыборезка 2 - бункер со шнековым дозатором 3- варильник 4 – пресс шнековый 5 - шнек-смеситель 6 – сушилка 7 - магнитное заграждение 8 - мельничная установка 9 – циклон 10 – вентилятор 11 – пневмотранспорт 12 - установка насосная.
Рисунок 2- Схема получения кормовой муки прессово-сушильным способом
Степень измельчения зависит от: вида сырья и способности разваривания.
При переработке крупных кусков сырья (головы позвоночник) их измельчают на кусочки 1 -3 см;
При переработке целой рыбы - на кусочки 1-5 см;
При переработке мелкой рыбы и отходов их не измельчают.
Измельчение осуществляется на рыборезке которая состоит из чугунного корпуса с открывающейся на шарнире. В корпусе вращается ротор изготовленный в виде двух усеченных конусов сопряженных малыми основаниями. Вдоль образующих конусов в гнездах установлены три пары ножей вращающихся вместе с ротором. Ротор закреплен на валу который вращается в подшипниках корпуса. Верхней части последнего укреплен клинообразный опорный нож совершающий поступательное движение вдоль направляющих параллелей. Перемещая опорный нож регулирует зазор определяющий измельчение сырья. Оптимальная величина зазора 8 мм.
Процесс разваривания - наиболее важный при производстве кормовой муки так как на этом этапе белки коагулируют а жиросодержащие клетки разрушаются и высвобождается жир.
Дробленое сырьё поступает в варильник. Варка сырья предусматривает стерилизацию разваривание костей для облегчения в дальнейшем их сушки и измельчения.
Из бункера сырье шнековым дозатором загружается в секционный варильник. Процесс варки управляется пропорциональными регуляторами температуры в комплект которых входит термопреобразователь сопротивления автоматический самопишущий мост с реостатным
задатчиком балансное реле электрический исполнительный механизм переключатель и ключ управления.
В варильнике сырьё нагревается одновременно глухим паром через паровую рубашку и острым паром.
В зависимости от вида сырья устанавливают режим варки который определяется температурой давлением пара в рубашке и количеством подаваемого острого пара. В среднем температура стерилизации около 100 °С.
Оптимальный режим варки сырья определяют по качеству жома который выходит из пресса.
При поступлении большого количества острого пара в варильник жом при прессовании будет содержать высокий процент влаги которую нельзя удалить даже при дополнительной регулировке шнека пресса а при поступлении пара в недостаточном количестве сырьё разваривается не полностью и жом будет содержать высокий процент жира.
Варильник состоит из сварного горизонтально расположенного цилиндра закрытого с двух сторон щеками. Боковые щеки цилиндра укреплены на металлическом каркасе на котором смонтированы приводные устройства варильника и площадка для его обслуживания. В нижней части цилиндра имеется паровая рубашка и несколько штуцеров для подачи острого пара непосредственно во внутреннюю полость цилиндра. Конденсат из рубашки удаляется через конденсационный горшок.
Назначение этой операции - максимальное удаление из разваренного сырья воды и жира. Производят на непрерывно-действующих прессах (шнековых или гидравлических).
Шнековый пресс предназначен для отжима бульона из разваренного сырья. Состоит из сварной станины шнекового вала зеерного цилиндра загрузочной и разгрузочной течек поддона для сбора бульона и привода состоящего из электродвигателя вариатора скорости клиноременной передачи и червячного редуктора.
Из варильника масса поступает на шнековый пресс с зеером. Прессование предусматривает разделение разваренной массы на твёрдую и жидкую фазу.
Твёрдую фазу - жом из пресса направляют на сушку. При правильной работе пресса жом должен содержать 50-60% влаги.
Бульон из-под пресса направляют на горизонтальную осадительную центрифугу где отделяются твёрдые взвешенные частицы.
Твёрдые частицы отделяемые на центрифуге смешиваются с жомом и поступают на сушку.
Жом предварительно разрыхляют для облегчения процесса сушки. Режим сушки определяется скоростью испарения влаги.
Сушку жома ведут в 1 или 2-х аппаратах в зависимости от этого сушку называют: одноступенчатой или двухступенчатой сушкой.
При двухступенчатом режиме вначале ведут предварительную сушку затем окончательную.
Продолжительность сушки составляет от 30 минут до 2 часов. Зависит от многих факторов.
Работа в сушилке автоматизирована путем стабилизации температурного режима. Для этого в сушильном барабане установлена термопара являющаяся измерительным преобразователем регулятора температуры. При изменении температуры регулятор с помощью клапана с электроприводом соответствующим образом меняют подачу пара в за рубашечное пространство барабаносушилки. Смесь жома с упаренным бульоном по шнекам поступает на вход в сушилку. Система автоматического регулирования температуры сушки рыбой муки поддерживает постоянную температуру в сушилке порядка 100° С. По прохождении определенного времени по готовности (высушенная) смесь двигается по шнекам к выходу для дальнейшего дробления.
Интенсивность сушки рыбной муки прямо пропорциональна скорости движения воздуха относительно высушиваемого продукта. Выбор оптимальной скорости воздуха а следовательно расхода воздуха поступающего на сушку является одной из основных задач для экономичной работы сушильных установок.
Цель операции - удаление металломагнитных примесей которые могут попасть в продукт при измельчении прессовании или других операциях.
Для удаления метало-примесей сушенку пропускают через магнитные сепараторы которые в зависимости от конструкции устанавливают перед измельчением сушенки или перед охлаждением продукта и упаковыванием.
Корпус сепаратора служит опорой всех узлов аппарата. Измельченная мука из мельницы по течке поступает в ворошитель который разрыхляет муку и не дает ей слеживаться. При помощи питающего валика и примыкающей к нему наклонной заслонки регулируется толщина слоя муки поступающей на сепарацию а следовательно и производительность аппарата. Заслонка перемещается в направляющих пазах механизмом. Электромагнитная система состоит из катушек над сердечниками которых расположена ступенчатая поверхность. По этой поверхности перемещается мука. Металлические примеси снимаются при помощи скребка совершающего возвратно-поступательное движение. Примеси удаляются из машины через каналы расположенные по бокам сепаратора.
В нижней части сепаратора предусмотрен клапан для изменения направления движения продукта (муки) во время случайного прекращения питания катушки током. На сепараторе смонтирована сигнально-защитная лампа предназначенная для предохранения катушки электромагнита от пробоя и сигнализирующая о прекращении подачи тока в систему.
Измельченную сушенку просеивают через вибросито с размером отверстий не более 3 мм. В результате получают муку равномерного помола размер частиц не более 3 мм.
Вибрационное сито состоит из сварной станины горизонтального сита и привода состоящего из электродвигателя и клиноременной передачи. Сито разделено на несколько секций в каждой из которых на сетке лежат шары предотвращающие прилипание муки к металлической сетке. Сито закрыто кожухом. Мука из бункера поступает на сито. Просеянная мука собирается в бункере имеющем задвижку через которую мука высыпается в мешок. Отсев муки отводиться от вибрационного сита по течке. Возвратно-поступательное движение сито совершает от воздействия эксцентрикового вала. Сито покоится на подвесках. Мощность электродвигателя 06 кВт ход сита 50 мм число двойных ходов сита в минуту в 350 размеры сита 1215x485 мм масса 450 кг.
Цель - для предупреждения саморазогревания и самовозгорания муки. Охлаждают до t = 30°С. Охлаждают муку или перед второй магнитной сепарацией или перед направлением на упаковывание.
Охладитель муки марки Т1-ИЖС-12 состоит из горизонтального и вертикального шнеков цилиндрической формы с рубашками в которые подается соляной раствор температурой 5°С.
Упаковывание маркирование хранение
Упаковывание муки с температурой более 30°С на разрешается. Упаковывают кормовую муку в многослойные бумажные с полимерным покрытием - мешки в джутовые мешки в мешки с полиэтиленовыми вкладышами.
Маркирование производят по ГОСТу 7630.
Хранят кормовую муку в помещениях с температурой не более 30°С. Оптимальная tхран - 0 - 5°С. Срок хранения - 1 год. При хранении муки из неё выделяются токсичные газы в виде оксида углерода СО N0 которые могут вызывать летальный исход при разгрузочных работах [2].
ОПИСАНИЕ КОНСТРУКЦИИ СУШИЛЬНОЙ УСТАНОВКИ БАРАБАННОГО ТИПА
Сушильная установка включает: сушильную камеру устройство для подготовки и транспортирования тепловлагоносителя устройства для отчистки воздуха или дымовоздушной смеси перед поступлением в сушилку и на выходе из нее устройства для подачи сырья и отвода готовой продукции для обеспечения заданного режима и регулирования хода процесса.
Барабанные сушилки применяют для переработки водорослей обезвоживания жома в производстве рыбной муки. Сушка в барабанных сушилках происходит при атмосферном давлении. Теплоносителем являются воздух или топочные газы [1].
Барабанные сушилки имеют цилиндрический полый горизонтальный барабан установленный под небольшим углом (4°) к горизонту (рис 1). Барабан снабжен бандажами каждый из которых катится по двум опорным роликам и фиксируется упорными роликами. Барабан приводится во вращение от электропривода с помощью насаженного на барабан зубчатого колеса. Частота вращения барабана не превышает 5-8 мин-1. Влажный материал поступает в сушилку через питатель. При вращении барабана высушиваемый материал перекатывается и движется к разгрузочному отверстию. За время пребывания материала в барабане происходит его высушивание при взаимодействии с теплоносителем - в данном случае с топочными газами которые поступают в барабан из топки.
Для улучшения контакта материала с сушильным агентом в барабане устанавливают внутреннюю насадку которая при вращении барабана способствует перемешиванию материала и улучшает обтекание его сушильным агентом. Тип насадки выбирается в зависимости от свойств материала. В данном случае используется подъемно-лопастная насадка (предназначена для сушки крупнокусковых материалов). Газы и материал
могут двигаться прямотоком и противотоком. При прямотоке удается избежать перегрева материала так как при этом горячие газы взаимодействуют с материалом с высокой влажностью. Чтобы исключить большой унос пыли газы просасываются через барабан вентилятором со скоростью 2-3 мс. Перед выбросом в атмосферу отработанные газы очищаются в циклоне [5].
Рисунок 3 – Барабанная сушилка
Для улучшения контакта материала с сушильным агентом в барабане устанавливают внутреннюю насадку которая при вращении барабана способствует перемешиванию материала и улучшает обтекание его сушильным агентом. Тип насадки выбирается в зависимости от свойств материала.
На рисунке показаны некоторые типы внутренних насадок.
Рисунок 4 - Внутренние распределительные насадки барабанов:
а - подъемно-лопастная б - распределительная (полочная)
в - перевалочная (ячейковая)
Подъемно - лопастная насадка используется для сушки крупнокусковых и склонных к налипанию материалов. Для мелкокусковых хорошо сыпучих материалов применяется распределительная насадка. Сушка пылящих тонкодисперсных материалов производится в барабанах снабженных перевалочной (ячейковой) насадкой.
Газы и материал могут двигаться прямотоком и противотоком. При прямотоке удается избежать перегрева материала так как при этом горячие газы взаимодействуют с материалом с высокой влажностью. Чтобы исключить большой унос пыли газы просасываются через барабан вентилятором со скоростью 2-3 мс. Перед выбросом в атмосферу отработанные газы очищаются в циклоне [6].
ОБОСНОВАНИЕ ПРОЦЕССА СУШКИ
Сушка - сложный физико-химический процесс который заключается в переводе влаги находящейся в продукте в парообразное состояние путем подведения к нему теплоты и в удалении образовавшегося пара во внешнюю окружающую тело среду. Кроме этого при сушке в продукте происходит комплекс взаимосвязанных химических физико-химических биохимических микробиологических ферментативных и реологических процессов формирующих качественные и структурные свойства продукта.
Способы сушки гидробионтов определяются их геометрическими размерами формой физико-химическими биохимическими реологическими теплофизическими свойствами видом подводимой к ним теплоты формой связи и конечным значением массовой доли влаги в готовом изделии. В зависимости от вида подводимой к продукту теплоты различают сушку: конвективную кондуктивную (контактную) под действием энергетических полей (терморадиационная инфракрасными лучами; в электрическом поле высокой и сверхвысокой частоты; в акустическом поле) и комбинированную с применением указанных выше видов подвода теплоты.
Сушка может происходить при атмосферном и пониженном давлении. В последнем случае теплота подводится только в результате контакта высушиваемого продукта с нагретой поверхностью путем теплового излучения. Высушивание при пониженном давлении применяют для термолабильных продуктов не выдерживающих интенсивного теплового воздействия.
Процесс обезвоживания продуктов в сушилках представляет собой комплекс одновременно протекающих и влияющих друг на друга явлений. К ним относятся перенос тепла от нагретого воздуха к высушиваемому продукту через его поверхность; испарение влаги; перенос влаги с поверхности продукта в среду сушильной камеры; перенос влаги внутри продукта.
При испарении влаги с поверхности продукта возникает перепад влагосодержания между его наружным или внутренним слоями что и обеспечивает дальнейшее перемещение влаги из внутренних более влажных участков к его поверхности имеющей меньшую влажность. На перемещение влаги внутри продукта оказывает влияние перепад температуры. На поверхности продукта она больше чем в центральных слоях. Процесс сушки протекает со скоростью зависящей от формы связи влаги с сухим веществом продукта и механизма перемещения в нем влаги. Если продукт поместить в сушильную камеру через которую продувается предварительно подогретый воздух то продукт начнет тоже подогреваться. В начале когда начинают прогреваться только наружные слои образца вода из этих слоев начнет испаряться и в виде пара уходить в воздух. Затем следует период постоянно: скорости сушки называемый первым периодом сушки. Этот период характеризуете постоянной скоростью уменьшения влажности и температуры продукта. В первый период сушки происходит интенсивное поверхностное испарение свободной влаги. Он продолжается до наступления критической влажности. Критическая влажность является границей между периодом постоянной и падающей скоростями сушки [6].
В период постоянной скорости сушки интенсивность процесса определяются только параметрами сушильного агента. Продолжительность периода постоянной скорости сушки увеличивается с повышением температуры потенциала сушки сушильного агента.
В период падающей скорости сушки (второй период) скорость обезвоживания уменьшается по мере уменьшения влажности продукта; температура его постепенно увеличивается приближаясь к температуре сушильного агента. Процесс сушки происходит правильно если скорость испарения влаги с поверхности продукта равно скорости перемещения влаги из глубины слоев. Чем больше скорость движения воздуха в сушилке тем скорее он уносит испарившуюся влагу препятствуя повышению парциального давления водяного пара. Скорость испарения тем больше; чем выше температура воздуха в сушилке [5].
Влажностью материала W называется содержание влаги в процентах массы влажного материала:
где mвл - масса воды кг;
m - общая масса материала кг.
Материальный баланс сушки выражается уравнением:
где G1 – количество влажного материала кгч;
Gк - количество высушенного материала кгч;
W - количество влаги удаляемой из материала при сушке кгч;
Тепловой баланс сушки выражается уравнением:
где I1 - энтальпия влажного воздуха после калорифера Джкг;
I2 - энтальпия влажного воздуха после сушилки Джкг;
х2 - влагосодержание воздуха после сушилки гкг;
Удельное количество теплоты Δ (в кДжкг испаряемой влаги) вносимой в сушильную камеру или теряемой ею определяем по формуле:
= qдоб +1 – (qм + qтр + qб) кДжкг(4.3)
где Δ - коэффициент испарения влаги кДжкг;
qдоб - добавочные тепловыделения вносимые в сушильную камеру кДжкг испаряемой влаги;
cв1 - теплота вносимая в сушилку с влагой материала;
св - теплоемкость влаги кДж(кг-К) ;
- температура материала на входе в сушилку °С;
qм - количество теплоты (в кДжкг испаряемой влаги) необходимой для нагревания материала от 1 до 2;
qтр - количество теплоты необходимой для нагревания транспортных устройств кДжкг испаряемой влаги;
qПОТ - потери тепла от транспортера сушилки кДжкг [8].
РАСЧЕТ БАРАБАННОЙ СУШИЛКИ
Производительность установки G = 270 кгч;
Влажность продукта: начальная н= 32 %;
Влажность продукта: конечная к = 10 %.
Масса транспортного устройства Gк =1260
Теплоемкость транспортного устройства Cтр=168 кДжкг Сº;
Температура транспортного устройства на входе в сушилку t1тр =23°С;
Температура транспортного устройства на выходе из сушилки t2тр =60°С;
Тепловые потери в окружающую среду от суммы всех остальных слогагаемых теплового баланса qпот = 12%
Температура материала перед входом в сушилку 1 = 23°С;
Температура материала на выходе из сушилки 2 = 60°С;
Относительная влажность воздуха на входе в калорифер φо=65%
Температура воздуха после калорифера t1= 80 Cº;
Температура наружного воздуха t0 = 21°С;
Решение. Количество влаги W (кгс) выделившейся из дрожжей в сушилке рассчитывают по формуле:
Производительность сушилки по высушенному продукту
G2 = G1 – W = 0.0183 – 0.075 = 0.056 кгс.
Рассчитывают потери теплоты на 1 кг испаренной влаги:
а) расход теплоты qдр на подогрев дрожжей от 1 = 23°С до 2 = 60°С составит: :
Где Cж =168 кДжкг Кº
Расход теплоты на подогрев транспортного устройства от t1тр =23°С до t2тр =60°С:
Теплота вносимая в сушилку с влагой материала:
qw=сw×=4.187×23=963 кДжкг влаги
Так как подогрев воздуха в сушильной камере не предусматривается величина qд=0:
Приняв тепловые потери 12 % от подведенной полезной теплоты величину их определяют по формуле
qп=(qж+qт-qw)012=(1902+1188-963)×012=153 кДж
Определим суммарные тепловые потери:
= qдоб +1 – (qм + qтр + qб) кДжкг испаренной влаги.
По диаграмме -i x1 = х0 = 001 кгкг сухого воздуха и i1 = 110 кДжкг сухого воздуха (точка В).
Из точки В проводят линию постоянного теплосодержания воздуха i1= 72 кДжкг сухого воздуха до пересечения с заданной изотермой t2= 27 °С.
Рисунок 5 - Диаграмма Рамзина i-X (d).
Полученная при этом точка С соответствует состоянию воздуха после сушильной камеры для теоретического процесса. Затем на линии ВС теоретического процесса произвольно принимают точку е проводят через нее вертикаль и горизонталь до пересечения с линией АВ (точка f). Измеряют величину отрезка ef.
На взятой для расчета ix-диаграмме с масштабом m=MiMx=0125×1000025=500
отрезок ef = 6 мм. Находят величину отрезка Ее определяющего отклонение действительного процесса от теоретического по формуле
Так как Ее 1 откладывают отрезок Ее = -135 мм вниз от точки е. Затем из точки В через точку Е проводим прямую до пересечения с изотермой t2 = 60 °С; получают точку С' характеризующую состояние воздуха после сушилки при действительном процессе сушки. Этой точке соответствуют: влагосодержание х2 = 00175 кгкг сухого воздуха теплосодержание i2 = 72 кДжкг и относительная влажность φ2 = 72 %.
1 Расчет расхода воздуха на сушку продукта
Удельный расход воздуха:
кгкг испаренной влаги
Затем находим полный расход смеси воздуха
L= 75×00183=0137 кгс
Пользуясь формулой узнаем удельный расход теплоты.
q=L1×(i1-i0)=75(110-48)=465кДжкг
Полный расход теплоты в калорифере кДжкг
Q=465×00183=8.5 кДжкг
ПУТИ ИНТЕНСИФИКАЦИИ ПРОЦЕССА ПРОТЕКАЮЩЕГО
Решение о путях повышения эффективности сушильных установок следует принимать на основе совместного энергетического и экономического анализа в результате которого будут получены данные о наиболее низкой стоимости оборудования установки и организации процесса сушки.
Для интенсификации процесса сушки в барабанной сушилке устанавливают внутренние насадки (для улучшения контакта материала с сушильным агентом) которая при вращение барабана способствует перемешиванию
материала и улучшает обтекание его сушильным агентом также можно произвести предварительный подогрев материала перед входом в сушилку уменьшить относительную влажность воздуха на входе в калорифер.
Можно несколько повысить скорость потока воздуха (до 2 мс) и как следствие более интенсивную циркуляцию влаги с поверхности материала.
Предварительный подогрев материала перед входом в сушилку уменьшение относительной влажности воздуха на входе в калорифер.
Однако не следует превышать возможно более высокую температуру воздуха что приводит к необратимой порче продукта и поддерживать относительную влажность не более 65% [6].
В результате расчета барабанной сушильной установки определены следующие основные параметры: Количество влаги испаряющейся в сушилке W = 00183кгс;
Количество материала выходящего из сушилки G2 =0056 кгс;
Расход воздуха в сушилке L =1370 кгc;
Расход теплоты в сушилке Q =8.5 кДжкг
Для интенсификации процесса сушки в барабанной сушилке устанавливают внутренние насадки (для улучшения контакта материала с сушильным агентом) которая при вращение барабана способствует перемешиванию материала и улучшает обтекание его сушильным агентом также можно произвести предварительный подогрев материала перед входом в сушилку уменьшить относительную влажность воздуха на входе в калорифер.
СПИСОК ИСПОЛЬЗУЕМОЙ ЛИТЕРАТУРЫ
Гинзбург А.С. Технология сушки пищевых продуктов - М.: Пищевая промышленность 1976
Чупахин В.М.Технология оборудование рыбообрабатывающих предприятий - М: Пищевая промышленность 1968
Сафронова Т.М. Богданов В.Д. Бойцова Т.М. и др. Технология комплексной переработки гидробионтов: Уч. пособие. Владивосток: Дальрыбвтуз 2002.-512 с.
Баранцев В.И.Сборник задач по процессам и аппаратам пищевых производств. -М.: Агропромиздат 1985. - 136 с.
Доронин А.Н. Перебейнос А.В. Угрюмова С.Д. ПАПП часть 1 -сушильные агрегаты типы конструкций и основы расчёта - Владивосток Дальрыбвтуз 2003
Кавецкий Г.Д. Королев А.В. Процессы и аппараты пищевых производств-Пути интенсификации процесса протекающие в аппарате.
Стабников В.Н.Процессы и аппараты пищевых производств. - М.: Агро-промиздат 1985.-503 с.
Ткаченко Т.И. Угрюмова С.Д. Курсовое проектирование «Процессы и аппараты пищевых производств» - Владивосток Дальрыбвтуз 2007. - 155 с.
схема мука ред.cdw

Рекомендуемые чертежи
- 28.02.2014
- 13.02.2022
- 29.07.2014
- 02.06.2020
Свободное скачивание на сегодня
Другие проекты
- 24.04.2014