Полноприводный коммерческий автомобиль 3,5 тонны




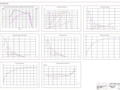
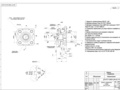
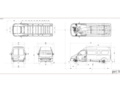
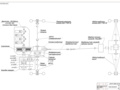
- Добавлен: 04.11.2022
- Размер: 41 MB
- Закачек: 0
Описание
Состав проекта
![]() |
![]() |
![]() ![]() ![]() |
![]() ![]() ![]() ![]() |
![]() ![]() ![]() ![]() |
![]() ![]() ![]() |
![]() ![]() ![]() |
![]() |
![]() ![]() ![]() |
![]() ![]() ![]() |
![]() |
![]() ![]() ![]() ![]() |
![]() ![]() ![]() ![]() |
![]() ![]() ![]() ![]() |
![]() ![]() ![]() ![]() |
![]() ![]() ![]() ![]() |
![]() ![]() ![]() ![]() |
![]() ![]() ![]() ![]() |
![]() ![]() ![]() ![]() |
![]() ![]() ![]() ![]() |
![]() |
![]() ![]() ![]() |
![]() ![]() ![]() |
![]() |
![]() ![]() ![]() |
![]() |
![]() |
![]() ![]() ![]() |
![]() |
![]() ![]() ![]() |
![]() ![]() ![]() |
![]() ![]() ![]() |
![]() |
![]() ![]() ![]() |
![]() ![]() ![]() |
![]() |
![]() ![]() ![]() |
![]() |
![]() ![]() ![]() |
![]() ![]() ![]() |
![]() ![]() ![]() |
![]() ![]() |
![]() |
![]() ![]() ![]() ![]() |
![]() ![]() ![]() |
![]() ![]() ![]() |
Дополнительная информация
Рессора_разм.dwg

ДП-НГТУ-190201-(АС-04)-02-2010
механическая операция по
Схема сборки задней ресоры
-Цилиндрическое отверстие
-Нижняя горизонтальная поверхность
-Верхняя горизонтальная поверхность
пробивка центрального отверстия
Агрегаттттт_разм.dwg

Линейная размерная цепь А
А1=120 мм - размер полного вала А2=2
мм - толщинапрокладки А3=6 мм - толщина фланца А4=11
мм- глубина отверстия под подшипник А5=18 мм - толщина регулировочного кольца А6=18
мм - размер подшипника А7=2
мм- толщина упорного кольца А8=66
мм длина конуса ведомой шестерни Аs=11
- смещение от вершины делительного конуса шестерни до оси колеса
Линейная размерная цепь Б
Б1=155 мм - размер полного вала Б2=66
мм - длина конуса ведомой шестерни Б3=2
мм- толщина упорного кольца Б4=18
мм - размер подшипника Б5=18 мм - толщина регулировочного кольца Б6=17
мм - размер подшипника Б7=6 мм- толщина мазеудерживающего кольца Б8=29 мм кожух крепления к карданной передаче Бs=2
- зазор между стопорным кольцоми фланцем вала (принимаем конструктивно)
Решение размерной цепи Б
N обрабатываемой поверхности
Термическая обработка
технологическая база
обрабатываемая поверхность
Схема механической обработки поверхностей шестерни
подготовка корпуса к сборке
контроль параллельности осей отверстий
контроль пятна контакта
контроль преднатяга
механическая операция по
подшипников шестерни
механическая операция по
завинчиванию гаек (болтов)
Кольцо регулировочное
Привод спидометра в сб.
Подшипник отключения сцепления в сб.
Схема сборки коробки передач с дифференциалом и угловым редуктором
Технология.doc
1.1. Анализ конструкции механизма
Назначение углового редуктора – преобразование крутящего момента и передача его через карданный вал на задний мост. Его конструкция должна быть компактной а работа бесшумной. Детали испытывают большие нагрузки поэтому необходима высокая точность при регулировки подшипников и зацепления зубчатых колес. Вал-шестерня углового редуктора вращается на двух подшипниках. Передней опорой является роликовый подшипник 7207 установленный в расточке вала-шестерни с посадкой внатяг обоих колец –35 L0к6 зазор в ролике равен 0015мм; задней опорой является роликовый подшипник 7206 внутреннее кольцо которого установлено с зазором 30 L0g6. Зазор равен 0013мм.
Для регулировки зацепления на валу-шестерни предусмотрено резьбовое соединение.
Шлицевое соединение предназначено для передачи крутящего момента.
Зазор между стопорным кольцом и фланцем вала равен 20-23 мм. В зубчатом зацеплении боковой зазор должен быть в пределах 012-025 мм. Одним из критериев работоспособности механизма является соблюдение всех перечисленных зазоров.
1.2. Разработка технических требований к точности обработки детали
Наиболее предпочтительным методом назначения технических требований к точности механической обработки детали является расчетный метод. Он позволяет установить наиболее обоснованные требования к точности детали на основании размерных цепей учитывающих и величину требуемых зазоров тип производства и другие факторы конструкции механизма.
Линейная размерная цепь определяющая допуск на размер звена на компенсирующее звено А2 для обеспечения смещения Аs
А1 =120 мм - размер полного вала
А2=23 мм – толщина комплекта регулировочных прокладок
А3 =6 мм – толщина фланца
А4=115 мм– глубина отверстия под подшипник
А5 =18 мм – толщина регулировочного кольца
А6 =182501 мм – размер подшипника
А7 =25 мм – толщина упорного кольца
А8 =661 мм – длина конуса ведомой шестерни
Аs =1195 мм – смещение от вершины делительного конуса шестерни до оси колеса
Аs = А1 + А2 + А3– А4– А5 – А6 – А7 – А8
Аs =120+23+6-115–18–1825–25–661=1195 мм
По нормам плавности работы конических и гипоидных зубчатых передач с m≥1 мм допуск на смещение зубчатого венца будет равен ±56 мкм
Таким образом звено Аs =1195±0056 мм
Определяем метод достижения необходимой точности замыкающего звена. Для этого вычисляем средний класс точности размерной цепи по формуле:
где - среднее геометрическое интервала размеров.
единиц допуска соответствуют примерно второму классу точности. Такая точность является очень высокой поэтому для расширения допусков на звенья в размерную цепь целесообразно ввести компенсатор а сборку механизма вести методом пригонки. В качестве компенсатора удобнее всего принять прокладку (А2).
Устанавливаем экономически целесообразные допуски на звенья цепи (кроме компенсирующего).
На звенья А1А4 А8 назначаем допуски по 12 квалитету:
На звенья А5 А7 назначаем допуски по 11 квалитету:
Определяем рассеивание размера замыкающего звена по формуле:
Наибольшую величину компенсации определяем из выражения:
Предельные отклонения замыкающего звена:
Предельные отклонения компенсирующего звена вычисляем по формуле:
Компенсация может проводиться набором прокладок разной толщины. При этом прокладки в наборе должны быть подобраны так чтобы путем их сочетания можно было получить любое значение кратное допуску зазора в пределах величины компенсации . Для этого толщина прокладок должна меняться в геометрической прогрессии знаменатель которой равен двум первый член – допуску смещения а последний – наименьшему числу превышающему половину величины компенсации .
Для нашей задачи прокладки в наборе должны иметь следующую толщину:
Всего потребуется четыре размера прокладок. Очевидно что сочетанием двух-трех прокладок можно получить любую нужную величину компенсации.
Линейная размерная цепь определяющая допуск на размер звена на звено Б2 для обеспечения зазора Бs ( рисунок 3.2.)
Б1 =155 мм – размер полного вала
Б2 =661 мм – длина конуса ведущей шестерни
Б3 =25 мм – толщина упорного кольца
Б4 =182501 мм – размер подшипника (левого)
Б5 =18 мм – толщина регулировочного кольца
Б6 =17201 мм – размер подшипника (правого)
Б7 =6 мм – толщина маслоотражательного кольца
Б8 =29 мм – кожух крепления к карданной передаче
Бs =20-23 мм – зазор между стопорным кольцом и фланцем вала (принимаем конструктивно)
Бs = Б2+ Б3+ Б4+ Б5 + Б6 + Б7+Б8–Б1
Бs =661+25+1825+18+172+6+29-155=205 мм
Таким образом звено Бs =205 мм
Кi - коэффициент относительного рассеивания
Qij23 соответствует единице допуска определяется по таблице 4
YT – допуск на размер
По таблице 2 для а=1511 ближайшие квалитеты 100 (11 квалитет) и 160 (12 квалитет)
Коэффициент относительной асимметрии звена Бs
где Р - передаточное отношение
Коэффициент относительного рассеивания звена Бs
Поле рассеивания звена Бs
Координата середины поля рассеивания звена Бs
Так как ms=-015 следовательно
Необходимо сместить середину поля допуска звенатаким образом чтобы получить
Предельные отклонения звена Б3:
Окончательно звено Б3 должно быть изготовлено в размер
1.3. Разработка технических требований к качеству обработки поверхностей детали.
Требования к качеству обработанных поверхностей детали назначаются в зависимости от точности обработки этих поверхностей от условий эксплуатации сборочной единицы или механизма и от назначения поверхностей детали.
Сначала назначают технические требования к качеству обработки поверхностей точность которых установлена расчетом размерных цепей. Затем качество обработки поверхностей (высота микронеровностей) может быть определено по следующим соотношениям:
где d- размер детали
YT – величина допуска на размер детали
На остальные поверхности детали требования к качеству обработанной поверхности можно назначить конструктивно.
Геометрическая форма
Внутренняя цилиндрич.
2. Проектирование технологического процесса механической обработки
2.1 Определение типа производства
Для определения типа производства необходимо рассчитать коэффициент закрепления операций Кзо. В настоящее время Кзо может быть определён двумя основными способами: расчётным и табличным.
Табличный метод определения типа производства применяется в том случае когда известны только программа выпуска и масса детали.
При программе выпуска N=150000и массе детали 155 кг тип производства будет массовый.
2.2. Анализ технологичности детали
Технологическая конструкция детали предусматривает:
)максимально широкое использование унифицированных сборочных единиц стандартизованных деталей и элементов деталей;
)возможно большую повторность деталей;
)Наличие на детали удобных базирующих поверхностей.
)Наиболее рациональный способ получения заготовок для деталей с размерами и формами возможно более близкими к готовым изделиям т.е обеспечивающими наиболее высокий коэффициент использования материала и наименьшую трудоёмкость механической обработки.
2.3. Выбор способа получения заготовки
Рекомендуется метод получения заготовки в штампах (лучшее использование металла меньшая стоимость и т.д.) а одним из типов штамповки рекомендуют штамповку на кривошипных прессах которая в 2-3 раза производительнее чем штамповка на молотах припуски и допуски уменьшаются на 20-30% расход металла снижается на 10-15%.
2.4 Разработка технологического процесса механической обработки
Определение комплектов технологических баз.
Точность детали во многом зависит от расположения поверхностей принятых за технологические базы. Следовательно фактическая точность размеров будет наивысшей при постановке размеров от поверхностей выбранных за технологические базы. Таким образом при разработке конструкции детали необходимо предусматривать возможность использования конструкторской базы в качестве технологической.
Рисунок 3.3. Размеры ведомой шестерни
Рисунок 3.4. Обрабатываемые поверхности ведущей шестерни
Учитывая это требование назначаем комплекты технологических баз.
Рисунок 3.5. Комплект технологических баз №1
Рисунок 3.6. Комплект технологических баз №2
Рисунок. 3.7. Комплект технологических баз №3
Разработка планов механической обработки типовых поверхностей.
Любая деталь входящая в конструкцию любого механизма может быть представлена в виде подбора простейших или элементарных поверхностей. К ним относятся:
-внутренние цилиндрические поверхности;
-наружные цилиндрические поверхности;
-зубчатые поверхности;
-шлицевые и шпоночные поверхности;
-поверхности сложной геометрической формы.
Наружные цилиндрические поверхности
Технологический метод
Шлифование окончательн.
Шлифование предварит.
Фрезирование чистовое
Фрезерование предварит
Нарезание гребенками
Фрезерование червячными фрезами
Разработка последовательности обработки заготовки (маршрутного технологического процесса)
Технологический маршрут обработки вала-шестерни 7-ой степени точности заготовка – штамповка из стали 20ХГНМ ГОСТ4543-71 представлен в таблице 3.8.
Фрезерование торцов и зацентровка
Фрезерно-центровальный станок
Токарная обработка по копиру с одной стороны:
получистовое точение
Токарный гидрокопировальный полуавтомат
Вертикально-Сверлильный станок
Нарезание резьбы на конце вала
Резьбонарезной станок
Фрезерование зубьев:
предварительное фрезерование
Чистовое фрезерование
Зубофрезерный полуавтомат
Фрезерование шлицев:
черновое фрезерование
получистовое фрезерование
Горизонтально фрезерный станок
Контроль (проверка пятна контакта)
Контрольно-обкатной станок
Термическая обработка
Предварительное шлифование опорных шеек и упорных торцов под подшипники качения с одной стороны
Кругло-шлифовальный станок
Искусственное старение
Чистовое шлифование шлицев
Чистовое шлифование опорных шеек и упорных торцов под подшипники качения с одной стороны
Предварительное шлифование зубьев
Зубо-шлифовальный станок повышенной точности
Чистовое шлифование зубьев Ra=125 мкм
Окончательный контроль проверка микротрещин на дефектоскопе подбор зубчатых колес в пары по пятну контакта
3.Проектирование технологического процесса сборки
3.1 Классификация соединений сборочных единиц
Соединение вала с задним подшипником.
Посадка назначена с натягом для нормальной работы подшипника причем посадка в корпус тоже с натягом чтобы избежать осевое перемещение подшипника.
Натяг подшипника регулируется (смотри ниже). Зазор в этом подшипнике для его вращения находится в ролике. Монтаж и демонтаж подшипника производится
специальными приспособлениями.
Соединение вала с регулировочным кольцом.
Регулировочное кольцо устанавливают для регулировки натяга подшипника для правильной работы узла.
Регулировочное кольцо устанавливается на валу с гарантированным зазором для упрощения замены колец и постановку кольца другого типоразмера для регулировки натяга подшипника.
Соединение вала-шестерни с передним подшипником.
Передний подшипник устанавливается с зазором на валу что обеспечивает сборку узла и возможность замены регулировочных колец для регулировки натяга подшипника заднего.
Посадка в корпус с натягом чтобы избежать осевое перемещение подшипника.
Монтаж и демонтаж подшипника производится специальными приспособлениями.
Соединение вала с фланцем карданного вала.
Соединение обеспечивается шлицевым соединением по шлицам же передается крутящий момент от карданного вала.
Установка производится специальным приспособлением.
Шайбу устанавливают для фиксации фланца карданного вала от осевого перемещения и биений возникающих при этом.
Резьбовое соединение здесь относится и к регулировочным и к крепежным.
К крепежным так как гайка закрепляет положение шайбы а следовательно и фланца карданного вала. Далее гайка фиксируется от проворачивания специальным пальцем.
К регулировочным так как с помощью осевого перемещения гайки регулируется зацепление зубчатой пары.
Данные этих соединений приведены в таблице 3.9.
Характеристика соединения
Краткие условия монтажа
Спец. приспособление
последующей затяжкой
3.2. Разработка процесса образования типовых сборочных соединений
Проводим группировку однотипных соединений. Затем для каждой группы соединений разрабатывается последовательность их образования дается описание регулировок их положения в сборочной единице и контроль.
Резьбовое соединение
с определенным моментом
Установка специальным приспособлением с
Регулировочным кольцом
опред. другим усилием
3.3. Разработка последовательности сборки механизма и сборочной единицы
На основании анализа сборочного чертежа выделяют сборочные единицы первого порядка и отдельные детали не вошедшие в состав сборочных единиц на которые этот механизм может быть разделен. Затем устанавливается очередность монтажа сборочных единиц и отдельных деталей. За базовую деталь принимаем корпус.
3.4 Проектирование основных сборочных операций
Обрабатываем содержание не только основных операций но и дополнительных операций связных с подготовкой детали к сборке применением операций механической обработки деталей в сборе и других операций влияющих на качество обработки.
Соединение вала-шестерни с роликовым радиально-упорным подшипником 7207.
Подшипник распаковать промыть от масла в специальной жидкости.
На вал-шестерню надеть подшипник с прессовой посадкой на валу специальным монтажным приспособлением с определенным усилием. Подшипник установить не весь а только внутреннее кольцо на вал-шестерню.
Соединение с кольцом.
Кольцо и регулировочные прокладки выбрать из набора в зависимости от требуемого натяга подшипника таким образом регулируя натяг подшипника. Проверку производить на стенде по рабочей температуре подшипника. Температура не должна превышать 100С.
Соединение вала-шестерни с роликовым радиально-упорным подшипником 7206.
На вал- шестерню надеть подшипник с зазором 002 мм на вал специальным монтажным приспособлением с определенным усилием. Зазор нужен для того чтобы можно было регулировать натяг подшипника 7207 снимая подшипник 7206.
В подшипник заложить графитовую смазку.
Соединение вала-шестерни с мазеудерживающим кольцом.
Мазеудерживающее кольцо служит для препятствия утечек графитовой смазки из-за увеличения температуры в подшипнике 7206. Мазеудерживающее кольцо надеть на шлицы впритык к подшипнику 7206 вручную или специальным приспособлением.
Соединение вала-шестерни с фланцем карданной передачи.
Фланец надеть на шлицы вала-шестерни с определенным усилием.
Соединение вала-шестерни с шайбой.
Шайбу надеть на вал- шестерню тем самым зафиксировать фланец карданной передачи от смещения в осевом направлении. Надеть вручную или специальным приспособлением.
Соединение вала-шестерни с корончатой гайкой.
На резьбовое соединение надеть гайку и завернуть ее на величину соответствующуюправильному зацеплению вала-шестерни с колесом. Для этого провести регулировку зацепления по пятну контакта. Гайку затянуть с крутящим моментом от 108 до 123 Нм гаечным ключом. Гайку застопорить штифтом который фиксирует гайку от разворачивания и соответственно от нарушения зацепления. Штифт вставить специальным приспособлением с натягом. Заканчивается процесс сборки сборочной единицы ее монтажом на базовую деталь – корпус и установкой всех деталей относящихся к ней согласно чертежу общего вида.
Вал-шестерню вставить в корпус таким образом чтобы внешние кольца подшипников с корпусом составили прессовую посадку.
Между фланцем карданного вала и корпуса поставить манжету специальным приспособлением. Перед установкой манжету смазать ЦИАТИМ 32.
Закрыть картер крышкой поставить шайбы и надеть болты. Болты затянуть крутящим моментом от 108 до 123 Нм гаечным ключом.
Провести контроль чтобы убедится что вал вращается в корпусе на специальном стенде провернув вал в собранном виде.
В картер залить масла определенной марки в объеме 35 литра.
Провести полное испытание на долговечность и работоспособность на специальных стендах.
Введение.doc
Современные автомобили обладают большим запасом мощности и на старте при резком нажатии на педаль газа сил сцепления одной пары колес с дорожным покрытием как правило не хватает. Ведущие колеса буксуют проскальзывают избыток тяги уходит вместе с дымом сгоревшей «резины». А распределение тягового усилия не на два а на четыре колеса и возможность использовать весь вес машины в качестве сцепного уменьшают вероятность пробуксовки вдвое и гарантируют впечатляющее стартовое ускорение. К тому же полный привод обеспечивает лучшую управляемость и курсовую устойчивость автомобиля в движении особенно на скользких дорогах позволяет водителю увереннее и быстрее проходить повороты. Однако трансмиссия 4х4 требует введения в конструкцию новых узлов что делает автомобиль более тяжелым шумным и вибронагруженным. Усложнение конструкции умножает производственные издержки что отражается на стоимости полноприводного автомобиля. В свою очередь потребуют больших затрат обслуживание и ремонт такой машины в эксплуатации. А еще при прочих равных условиях автомобили 4х4 потребляют больше горючего чем их аналоги с приводом на одну ось- сказываются увеличение общего веса машины и механические потери в дополнительных агрегатах трансмиссии.
Для автомобилей класса В в который зачислена и наша машина самая популярная схема - переднеприводная с поперечным расположением мотора. Примем ее как базовую: просто и потому относительно дешево привычно потребителям и ремонтникам.
Через сцепление с диафрагменной пружиной и беззазорным тросовым приводом крутящий момент передается на один из двух валов пятиступенчатой механической коробки передач. Дальше - главная пара обычный симметричный дифференциал и валы привода колес.
К главной передаче подсоединим угловой редуктор (место под него надо предусмотреть заранее). За ним установим валы с карданными шарнирами и промежуточной опорой муфту подключения заднего привода присоединенную к редуктору заднего моста.
Мы отказались от понижающей передачи в трансмиссии ради экономии места и денег - все-таки проектируем не внедорожник а коммерческий автомобиль. Пусть не вездеход но проходимость будет куда выше чем у машин 4х2. А на шоссе - почти такие же экономичность динамика комфорт.
Список литературы.doc
1.1.Основные схемы полного привода
1.2.Подключаемый полный привод
1.3.Постоянный полный привод
1.4.Постоянный по-требованию полный привод
3.Раздаточная коробка
4.Узел отбора мощности
Расчет продольной устойчивости автомобиля
1. Расчет продольной устойчивости переднеприводного автомобиля
2. Расчет продольной устойчивости полноприводного автомобиля
Графики_+НИЧ.dwg

Сетевой график.dwg

Сетевой график технологической подготовки производства коробки передач в сборе с дифференциалом и угловым редуктором
Агрегаттттт_разм.dwg

Линейная размерная цепь А
А1=120 мм - размер полного вала А2=2
мм - толщинапрокладки А3=6 мм - толщина фланца А4=11
мм- глубина отверстия под подшипник А5=18 мм - толщина регулировочного кольца А6=18
мм - размер подшипника А7=2
мм- толщина упорного кольца А8=66
мм длина конуса ведомой шестерни Аs=11
- смещение от вершины делительного конуса шестерни до оси колеса
Линейная размерная цепь Б
Б1=155 мм - размер полного вала Б2=66
мм - длина конуса ведомой шестерни Б3=2
мм- толщина упорного кольца Б4=18
мм - размер подшипника Б5=18 мм - толщина регулировочного кольца Б6=17
мм - размер подшипника Б7=6 мм- толщина мазеудерживающего кольца Б8=29 мм кожух крепления к карданной передаче Бs=2
- зазор между стопорным кольцоми фланцем вала (принимаем конструктивно)
Решение размерной цепи Б
N обрабатываемой поверхности
Термическая обработка
технологическая база
обрабатываемая поверхность
Схема механической обработки поверхностей шестерни
подготовка корпуса к сборке
контроль параллельности осей отверстий
контроль пятна контакта
контроль преднатяга
механическая операция по
подшипников шестерни
механическая операция по
завинчиванию гаек (болтов)
Кольцо регулировочное
Привод спидометра в сб.
Подшипник отключения сцепления в сб.
Схема сборки коробки передач с дифференциалом и угловым редуктором
Сборочный чертеж.dwg

Передаточные числа коробки передач
В коробку передач залить масло М10-ГИ или М8-ГИ ТУ 38-101-48-75 до уровня нидней кромки заливного отверстия. 2. Проверку коробки передач на шум и отсутствие течей производить последовательно с нагрузкой и без нагрузки на всех передачах при следующих частотах вращения первичного вала в обоих направлениях nIma nIIma nIII-IV-Vma nmax=2400 мин . 3. * Размеры для справок
Коробка передач с дифференциалом и угловым редуктором в сборе (Сборочный чертеж)
ДП-НГТУ-190201-(АС-04)-10-2010
фланец.dwg

Нормальный исходный контур
Коэффициент смещения
Обозначение чертежа сопряженного колеса
Толщина по хорде зуба
Допуск на погрешность направления зуба
Предельные отклонения
измерительного межосевого
Допуск на погрешность профиля зуба
Ускорение автомобиля
Плоская форма дна впадины
кафедра А и Т Гр. 04-АС
Фланец с отражателем в сборе (сборочный чертеж)
ДП-НГТУ-190201-(04-АС)-10-2010
сверлить базируясь по выточке Е
х45° зенковать с обеих сторон 4 овт.
Клеймить здесь размер клейма 10
Полировать на указанной длине
Поверхностная закалка на указанной длине
Твердость поковки фланца НВ 207 255. 2. Материал фланца Сталь 35 ГОСТ 1050-60. 3. Материал отражателя Сталь 08КПкатегория 4 ГОСТ 16523-70 толщ. 1
ГОСТ 3680-57. 4. Отражатель запрессовать до упора в буртик и приварить в 2 точках. 5. Биение относительно оси шлицевого отверстия для торца В не более 0
мм; для торцев Т и Г - 0
мм. 6. Биение поверхности Д и Е относительно оси шлицевого отверстия не более 0
мм. 7. Не плоскостность торца Т не более 0
мм. 8. Поверхность шейки Д подвергнуть поверхностной закалке ТВЧ на указанной длине. Глубина слоя 2
мм. Твердость НRC 53
не менее. 9. Относительное расположение отверстий и шлиц безразлично. 10. Неуказанные пред. откл. по ОСТ 37.001.246.-82.
Затупить острые кромки
КИН_схема.dwg

Муфта полного привода HALDEX
Карданный вал привода заднего моста
Промежуточный карданный вал
ДП-НГТУ-190201-(АС-04)-10-2010
LD100LWBLHD_черн_нов.dwg

Графики_без рамок.dwg

мен.dwg

КИЧ_2.doc
В качестве базового автомобиля в проекте рассмотрен коммерческий фургон MAXUS. В линейке английской марки присутствуют грузовые грузопассажирские и пассажирские автомобили в различных модификациях. Так существуют три исполнения по полной массе (28 32 и 35 тонны) два по колесной базе (3100 и 3850 мм) а также три варианта высоты крыши: низкая средняя и высокая (от пола до потолка внутри может быть 1505 1710 и 1925 мм соответственно).
А вот привод только на передние колеса и кузов только цельнометаллический несущий с распашной задней и сдвижной боковой дверями в грузовом отсеке или пассажирском салоне (боковая — в двух исполнениях по ширине и высоте).
Рассмотрим технические характеристики базового автомобиля полной массой 35 тонны с длинной базой (3850 мм) и супервысокой крышей (2540 мм).
Длинная база (3850 мм)
Ширина боковой двери
Высота боковой двери
Внутренняя длина кузова
Внутренняя ширина кузова
Внутренняя высота кузова
Расстояние между арками колес
Рисунок 2.1. Габаритная схема фургонов MAXUS с длинной базой с высокой и супервысокой крышей
Масса и грузоподъемность
Главная передача трансмиссии
Максимальная разрешенная масса
в том числе на переднюю ось
в том числе на заднюю ось
Вес в снаряженном состоянии
Полная масс с прицепом
Двигатель и трансмиссия
Дизельный 4-цилиндровый 16-клапанный с турбокомпрессором и промежуточным охладителем
Аккумуляторная система подачи топлива под высоким давлением фирмы "Бош" с прямым впрыском и электронным управлением.
Объем топливного бака
л (со стороны пассажира крышка бензобака с замком)
Система очистки выхлопных газов
Варианты мощности двигателя
л.с. при 3800 об.мин
0 Нм при 1800 об.мин
0 л.с. при 3800 об.мин
Гидравлическое диаметр диска 242 мм
Привод на передние колеса
Коробка передач в блоке с ведущим мостом
с ручным переключением 5 передач с синхронизатором
Независимая с амортизаторными стойками типа "McPherson" Стабилизатор поперечной устойчивости
Одиночные параболические листовые рессоры
Реечная передача с усилителем
От бордюра до бордюра (м)
От стены до стены (м)
Размещение запасного колеса
За задней колесной аркой или под полом
Конфигурация тормозной системы
Дисковые вентилируемые. Диаметр 294 мм
Плавающая тормозная скоба со спаренными поршнями
Тормозные барабаны с набегающей и задней тормозными колодками
Внутренний диаметр 280 мм
Привод к задним тормозам
3. Обзор известных решений проблемы
Необходимо кратко рассмотреть основные схемы реализации полного привода на автомобилях. Наиболее интересен для нас конечно вариант с поперечным расположением двигателя - о нем и пойдет речь.
3.1. Стандартная схема
Рисунок 2.2. Стандартная схема первого поколения
Рисунок 2.3. Стандартная схема второго поколения
Традиционный FullTime 4WD устанавливаемый на "исходно-переднеприводные" модели действительно когда-то был постоянным и полным с тремя дифференциалами (межосевой передний и задний межколесные) и равным распределением момента между передними и задними колесами (соотношение 5050). Но в настоящее время по этой схеме выпускается лишь небольшая часть автомобилей.
На машинах первого поколения применялась блокировка межосевого дифференциала многодисковой гидромеханической муфтой с электронным управлением (схема STD I). Нажатие кнопки "C.DIFF AUTO" на панели разрешает блоку управления автоматически выбирать коэффициент блокировки в зависимости от условий движения (при полной блокировке усилие принудительно будет почти поровну делиться между осями) при отжатой кнопке межосевой дифференциал остается постоянно свободным. Номинальным для повседневной езды является именно автоматический режим. Максимальный коэффициент блокировки реализуется системой управления при положениях селектора "L" и "R".
На большинстве моделей с коробкой A540H выпущенных после 94-96 гг. кнопка "C.DIFF AUTO" отсутствует - водитель полностью отстранен от управления блокировкой и автоматический режим задействован постоянно.
Следует отметить что схема STD I являлась наиболее совершенной надежной и эффективной среди всех вариантов полного привода автомобилей.
Во второй половине 90-ых начался переход к новым типам трансмиссий и теперь в стандартной схеме 4WD второго поколения блокировка межосевого дифференциала стала осуществляться "закрытой" вискомуфтой (схема STD II). Упрощение конструкции никак не отразилось на надежности но зато существенно ухудшило эксплуатационные характеристики - за счет слишком низкой эффективности вязкостной муфты по сравнению с гидромеханической.
Задний дифференциал при стандартной схеме остается свободным но "паркетные" джипы традиционно имеют комплектацию с самоблокирующимся дифференциалом Torsen.
Рисунок 2.4. Дифференциал Torsen (фрагмент)
Примечание. Необходимо пояснить - технический английский язык все самоблокирующиеся дифференциалы называет единым понятием LSD (Limited Slip Diff. - ограниченного проскальзывания или повышенного трения) однако на самом деле они разделяются как минимум на блокирующиеся с "закрытой" вискомуфтой с "открытой" вискомуфтой фрикционные и механические. "Закрытая" вискомуфта начинена силиконовой жидкостью но ее внутренняя полость не сообщается с картером редуктора. В "открытой" - диски и пластины муфты работают непосредственно в среде рабочей жидкости дифференциала. Во фрикционных частичная блокировка осуществляется за счет осевого перемещения шестеренок приводных валов и трения о корпус дифференциала (здесь как раз и используется LSD-масло). Дифференциалы Torsen работают на ином техническом принципе и используют обычное трансмиссионное масло.
С середины девяностых годов на автомобилях появился полный привод по схеме известной под общим названием V-Flex Fulltime 4WD. "Честным" его назвать нельзя - реально это схема с подключаемыми задними колесами. Межосевой дифференциал ушел в небытие а раздатка упростилась до простого углового редуктора через который момент отбирается от коробки передач и отправляется по кардану назад где перед задним редуктором установлена вязкостная муфта срабатывающая и соединяющая хвостовик кардана и входной вал редуктора только если передние колеса начинают "обгонять" задние (то есть при пробуксовке). В остальное время машина остается переднеприводной.
Подобная схема применялась и раньше - на моделях класса "B" тоже устанавлен упрощенный вариант с подключаемыми задними колесами без межосевого дифференциала вот только вискомуфта у них не закреплена на заднем редукторе а соединяет две части промежуточного карданного вала.
Иногда на моделях этой схемы устанавливается задний самоблокирующийся дифференциал типа Torsen.
Система ATC (Active Torque Control) в основном похожа на V-Flex но вместо вязкостной муфты для подключения заднего моста применена электромеханическая.
Рисунок 2.6. Схема ATC
Режим "разрешения" полного привода включается кнопкой "4WD AUTO" а само подключение автоматически осуществляет электронный блок управления в зависимости от условий движения (муфта позволяет также плавно распределять момент подавая на задние колеса до половины общего усилия). В выключенном состоянии привод осуществляется только на передние колеса.
4. Компоновочный расчет коммерческого автомобиля
В результате анализа известных схем реализации полного привода на автомобилях и конструкции и технических характеристик прототипа была выбрана схема с подключаемым полным приводом и поперечно расположенным двигателем. Такой вариант является наиболее целесообразным в данных условиях так как:
Сохраняется компоновка узлов и агрегатов в подкопотном пространстве;
Появляется возможность на базе уже существующей КПП спроектировать угловой редуктор вписывающийся ограниченное пространство между двигателем и поперечной тягой;
Потребуется незначительное изменение высоты подъема пола (а именно 100 мм) для того чтобы пропустить карданный вал и установить новый задний мост вместо задней оси;
для подключения заднего моста применена электромеханическая муфта HALDEX ввиду ее небольших габаритов и эффективности при использовании.
4.1. Оценка продольной и поперечной проходимости проектируемого автомобиля
Проходимость – это эксплуатационное свойство определяющее возможность движения автомобиля в ухудшенных дорожных условиях по бездорожью а также при преодолении единичных препятствий.
Профильная проходимость – характеризует возможность преодолевать неровности пути отдельные препятствия и вписываться в требуемую полосу движения
продольный радиус проходимости Rпр
наибольший угол преодолеваемого автомобилем подъема amax.
Поперечный радиус проходимости R поп.
4.1.1. Дородный просвет
h – это расстояние от опорной поверхности до одной из наиболее низко расположенных точек автомобиля.
В соответствии с категорией проектируемого транспортного средства hmin=200 мм.
Из рисунка 2.7. видно что получившийся дорожный просвет равен hmin=230 мм.
Свес L1 и L2 —это расстояние от крайней точки контура передней или задней выступающей части по длине автомобиля до плоскости перпендикулярной опорной поверхности и проходящей через центры передних или задних колес автомобиля.
Рисунок 2.8. параметры профильной проходимости автомобиля
γ1 и γ2 - угол свеса - это угол между опорной поверхностью и плоскостью касательной к окружности наружных диаметров передних или задних колес и проходящей через точки контура передней или задней части автомобиля таким образом чтобы все остальные точки контура оказались с внешней стороны названного угла.
4.1.4. Поперечный радиус проходимости R поп
Rпоп — радиус цилиндра являющийся касательным к колесам одного моста и проходящим через точку контура таким образом что все остальные точки лежат выше.
4.1.5. Продольный радиус проходимости Rпр
Rпр—это радиус цилиндра касательного к окружностям описанным свободными радиусами соседних колес наиболее разнесенных по базе и проходящего через точку контура нижней части автомобиля таким образом чтобы все остальные точки контура оказались с внешней сторона цилиндра.
4.1.6. Угол максимального преодолимого подъема amax
Угол максимального преодолимого подъема amax – угол подъема имеющий протяженность не менее двукратной длины автомобиля или автопоезда и ровную поверхность преодолеваемый автомобилем без использования сил инерции(скорость постоянная) нарушения режимов работы агрегатов и безопасности движения.
Угол зависит от положение центра масс автомобиля и типа дорожного покрытия.
4.2. Расчет положения центра масс проектируемого автомобиля
Так как при проектировании автомобиля в трансмиссии появились новые узлы и агрегаты то положение центра масс изменилось. Для расчета нам необходимо знать положение центра масс основных компонентов конструкции и их вес. В таблице 2.1. отражены координаты центров масс узлов и агрегатов преднеприводного автомобиля (прототипа) и полноприводного. Определим высоту и продольное положение центров масс автомобилей.
Вычислим координаты положения центра масс в спроектированном автомобиле и прототипе. Для этого составим уравнение моментов относительно точки О1 (ось переднего колеса рисунок 2.9.):
где - массы компонентов автомобиля центры масс которых находятся между осями;
- расстояние от центра передней оси автомобиля до центра масс
- массы компонентов автомобиля центры масс которых находятся перед передней осью;
- расстояние от центра передней оси автомобиля до центра масс j-го агрегата;
- реакция опоры приложенная к заднему колесу;
В результате расчета получили что центр масс полноприводного автомобиля опустился на 1142 мм относительно высоты центра масс прототипа. Продольное положение центра масс сместилось ближе к задней оси. В результате на переднюю ось теперь приходится 15813 кг а на заднюю – 19187 кг.
4.3.Определение геометрических параметров оптимальной посадки водителя транспортного средства
Вопросы проектирования рабочего моста водителя расположения органов управления машиной и контрольно-измерительных приборов влияющие на улучшение условий работы комфортабельность и безопасность занимаю одно из важных мест в процессе проектирования транспортного средства при проведении эргономического анализа. Эргономический анализ рабочего места водителя предусматривает мероприятия по созданию удобной посадки водителя позволяющей без напряжения и при малых затратах усилий управлять транспортным средством следить за дорогой за работой дополнительного оборудования машины. Все это в большой мере зависит от соответствия рабочего пространства (зоны) антропометрическим характеристикам человека (водителя) т.е. его размерам и массе. Антропометрические данные человека являются исходной информацией необходимой при компоновке (взаимном размещении отдельных алиментов) кузова и кабины. Основываясь на динамике изменения размеров тела человека при перемещения его отдельных частей в пространстве диапазоне движений рук ног головы и глаз правилах экономии движений конструктор выбирает оптимальную посадку водителя для данного транспортного средства. Проверим соответствует ли кабина прототипа требованиям предъявляемым к рабочему месту водителя (рисунок 2.10-2.11).
Основные углы посадки водителя:
Туловище – ребро А (педаль в нижнем положении)
Туловище – вертикаль В
Горизонталь – бедро С
Угол бедро – голень D
Посадка водителя соответствует основным нормам и требованиям предъявляемым к ней.
ГЛИСОН.doc
5.1. Определение параметров шестерен
направление смещения - вверх
Расчетная передаваемая мощность
Ширина зубчатого венца
Смещение оси шестерни гипоидной передачи
Угол и направление спирали
5.2. Определение элементов зубьев шестерен гипоидных передач по методике фирмы ГЛИСОН
Гипоидные передачи были введены фирмой Глисон в 1925 г.
Фирма Глисон пересматривала метод в 1947 1950 и 1954 гг. имея целью устранение случаев подрезания зубьев и введения специальных пропорций зубьев для двусторонней нарезки зубьев обеих сопряженных шестерен. Это позволяет увеличить производительность особенно за счет предварительной нарезки шестерни.
При специальных пропорциях зубьев применяемых при двусторонней нарезке зубьев сопряженных шестерен углы конусов впадин сопряженных шестерен выбираются так чтобы с помощью инструмента для предварительной нарезки получить необходимое сужение толщины зуба по длине; эти пропорции зубьев позволяют увеличить ширину развода резцов.
5.2.1. Основные положения
Метод охватывает передаточные отношения с числом зубьев шестерни не менее 6 и суммой чисел зубьев сопряженных шестерен не менее 40.
Исходное значение рабочей высоты зуба равно 19mNM где mNM - нормальный модуль в середине ширины зубчатого венца колеса.
Радиальный зазор равен 125% рабочей высоты зуба плюс 0051 мм.
Для шестерен гипоидных передач каждая сторона зуба имеет свою кривизну и свой угол зацепления.
Для главных передач легковых автомобилей и передач общего назначения с числом зубьев шестерни 8 и более исходный средний нормальный угол зацепления берется равным 21°15'.
Ширина зубчатого венца колеса должна быть равна 03 длины образующей делительного конуса колеса эквивалентной конической передачи или десяти торцовым модулям; принимается меньшая из двух величин.
Смещение оси шестерни для передач ведущих мостов легковых автомобилей и грузовых автомобилей малой грузоподъемности а также для передач общего назначения не должно быть более 40% длины образующей делительного конуса колеса эквивалентной конической передачи а для передач ведущих мостов грузовых автомобилей тягачей и автобусов а также передач локомотивов и мотовагонов — более 20%.
Направление спирали выбирается в зависимости от направления смещения оси шестерни относительно оси колеса. Для передач со смещением направленным вниз шестерня должна иметь левое направление спирали а для передач со смещением направленным вверх — правое.
5.2.2. Определение элементов зубьев
Для определения элементов зубьев шестерен гипоидных передач с межосевым углом 90° применяются два комплекта расчетных бланков. Бланки HI и Н2 или так называемые обычные бланки могут применяться для любых шестерен гипоидных передач. Расчетный бланк НЗ является общим для обоих комплектов.
Цифры в скобках обозначают номера позиций на бланках. Все углы берутся с точностью до минуты. Приведенные ниже замечания относятся к позициям (1) — (70) расчетных бланков обычных и специальных.
Ниже дан расчет определения элементов зубьев шестерен гипоидной передачи с числом зубьев 19 и 32 с шириной зубчатого венца колеса 286 мм со смещением оси шестерни вниз на 286 мм с диаметром делительной окружности колеса 163988 и углом спирали шестерни 45°.
Бланки HI и Н2 позиции (1) - (70)
(1)п — число зубьев шестерни.
(2) N — число зубьев колеса.
(4)F — ширина зубчатого венца колеса.
(5)Е — смещение оси шестерни.
(6)D — диаметр делительной окружности колеса.
(7)rс — радиус резцовой головки. Рекомендуются следующие радиусы резцовых головок в зависимости от диаметра делительной окружности колеса:
Диаметр делительной окружности колеса D в мм
Рекомендуемый радиус резцовой головки rс в мм
(8)P0 - желательный угол спирали шестерни.
(12) R0 - радиус делительной окружности колеса в середине ширины зубчатого венца.
(19) Q для первой попытки принимается постоянная 075.
Если подобный расчет уже делался ранее то рекомендуется взять величину tg1 [позиция (20)] из колонки «первая попытка» которая была получена при постоянной 075 и величину tg3 из колонки «третья попытка» и вместо постоянной 075 в позиции (19) для нового случая расчета применить:
(42) P1 - угол спирали шестерни. Он должен быть очень близок к желательному углу спирали позиция (8).
(44) G1 - угол спирали колеса.
(48) Г1 - угол делительного конуса колеса.
(65) r`C - радиус кривизны соответствующий углам делительных конусов γ1 позиция (36) и Г1 позиция (48). Полученный радиус кривизны не должен отличаться более чем на 3% от радиуса резцовой головки rC позиция (7). Если разница превышает 3% то необходимо сделать еще попытку.
Если позиция (65) меньше позиции (7) то tg позиция (20) уменьшается расчет повторяется снова и результаты вписываются во вторую колонку. Если позиция (65) больше позиции (7) то tg увеличивается. Значение поправки выбирается в зависимости от величины несовпадения радиусов кривизны. Если нет особых соображений то при второй попытке tg рекомендуется изменить на 10%. После второй попытки получается новая величина r`C которая тоже может оказаться недостаточно близкой к радиусу резцовой головки rC. При этом делается третья последняя попытка. В этом случае для tg можно принять
где индексы 1 2 3 указывают соответственно первую вторую и третью попытки.
Использование общего бланка
Бланк НЗ позиции (101) —(150)
(101) ГR - угол конуса впадин колеса.
(105) D0 - диаметр окружности выступов колеса.
(107) X0 - расстояние от наружной кромки венца колеса до оси шестерни.
(110) Z0 - расстояние от вершины конуса выступов колеса до оси шестерни. Знак плюс ( + ) означает что вершина конуса выступов лежит за осью шестерни; знак минус ( – ) означает что вершина конуса выступов лежит между колесом и осью шестерни.
(111) ZR - расстояние от вершины конуса впадин колеса до оси шестерни. Знак плюс ( + ) означает что вершина конуса впадин лежит за осью шестерни; знак минус (–) означает что вершина конуса впадин лежит между колесом и осью шестерни.
(117) γ0 - угол конуса выступов шестерни.
(121) G0 - расстояние от вершины конуса выступов шестерни до оси колеса. Знак плюс (+) означает что вершина конуса выступов лежит за осью колеса; знак минус (–) означает что вершина конуса выступов лежит между шестерней и осью колеса.
(131) B0 - расстояние от наружной кромки венца шестерни до оси колеса. Эта величина представляет собой величину В'о позиция (130) округленную до величины кратной 0127 мм.
(133) Bi - расстояние от внутренней кромки венца шестерни до оси колеса. Эта величина представляет собой величину В'i позиция (132) округленную до величины кратной 0127 мм.
(135) d0 - диаметр окружности выступов шестерни.
(141) GR - расстояние от вершины конуса впадин шестерни до оси колеса. Знак плюс ( + ) означает что вершина конуса впадин лежит за осью колеса; знак минус (–) означает что вершина конуса впадин лежит между шестерней и осью колеса.
(143) γR - угол конуса впадин шестерни.
(146) Bmin - минимальный боковой зазор.
(147) Bmax - максимальный боковой зазор.
(150) Ai - длина образующей делительного конуса колеса до внутренней кромки зубчатого венца.
sin1=(24)-(22) · (32)
a0G=(87)+(74) · (90)
b0G=(88)+(74) · (92)
X0=(106)-(93) · (49)
(12)-(50) · (75)+(50) · (87)
B=(114) · (126)+(74) · (125)
B0'=(127)+(113) · (128)
Bi'=(129)-(113) · (128)
5.3. Расчет шестерен на изгиб
Расчет проводится по следующей формуле:
коэффициент перегрузки
коэффициент перраспределения нагрузки
объедененный коэффициент формы зуба
коэффициент точности изготовления шестерни
коэффициент долговечности
температурный коэффициент
коэффициент надежности
5.3. Расчет шестерен на контактные напряжения
коэффициент зависящий от чистоты обработки зуба
[]'K=13500 17500 кГссм2
5.4. Определение нагрузок на подшипниках
Числа зубьев 19 и 32 торцовый модуль колеса 512464 ширина зубчатого венца 286 мм.
Колесо с двусторонним расположением опор шестерня с односторонним расположением опор.
Определим нагрузки подшипников.
5.4.1. Окружное усилие
PG=1432*103*N(Dm*nG)
nG=3700(4077*4188)= 2166977 обмин – число оборотов колеса в минуту
PG=1432*103*32(143303*2167)= 147565 кг
Окружное усилие шестерни гипоидной передачи определяется с помощью зависимости:
P – угол спирали шестерни
G– угол спирали колеса
PP=147565*0819209625=1255941 кг
5.4.2. Осевое усилие
Осевые усилия для колеса и шестерни при переднем ходе
PxG=P*(tgsinγ+sincosγ)cos=
PxP=P*(tgsinγ-sincosγ)cos=
5.4.2. Радиальное усилие
Распирающие усилия для колеса и шестерни при переднем ходе
P'rG=P*(tgcosγ-sinsinγ)cos=
P'rP=P*(tgcosγ+sinsinγ)cos=
Действующее усилие или момент
Шестерня (одностороннее расположение опор)
Распирающее усилие P'r
Момент от осевого усилия
Суммарная радиальная нагрузка на подшипник
PrA=(Pr22+(Pr1-Pr3)2)05=
PrB=(Pr52+(Pr4-Pr6)2)05=
Тяговый расчет1.doc
1.2.Исходные данные для выполнения расчета
1.2.1. Параметры заданные техническими условиями
Тип автомобиля выбираем в соответствии с принятой классификацией.
-по назначению: цельнометаллический фургон;
-по конструктивной схеме: одиночный;
Дизельный четырёхтактный.
Механическая ступенчатая.
Полноприводный автомобиль с колёсной формулой 4х4..
Малой грузоподъемности от 10 до 25 т.
Полная масса автомобиля
Максимальная скорость
Ориентировочно принимаем:
При максимальной скорости движения коэффициент сопротивления дороги:
где - коэффициент сопротивления качению при движении автомобиля со скоростью меньше 50 кмч по бетонному асфальтобетонному и асфальтовому покрытию;
- эмпирический коэффициент;
Максимальный коэффициент сопротивления дороги
Максимальный коэффициент сопротивления дороги преодолеваемый дорожными автомобилями на низшей передаче трансмиссии:
1.2.2. Выбираемые параметры
Собственная масса автомобиля в снаряженном состоянии
Фактор обтекаемости
Аэродинамические свойства автомобиля зависят от фактора обтекаемости:
где – коэффициент лобового сопротивления;
– плотность воздуха;
– площадь миделева сечения.
Распределение массы автомобиля по осям
У легковых автомобилей распределение массы по осям зависит от компоновочной схемы. Для расчета принимаем в снаряженном состоянии: ; при полной массе .
Частота вращения вала двигателя при максимальной мощности
neP = 3800 4500 мин-1
1.3.Выполнение тягового расчета
1.3.1. Определение полной массы автомобиля
(из исходных данных)
Максимальная и минимальная нагрузки на шину определяются по формулам:
где – часть полной массы автомобиля приходящейся на наиболее нагруженную переднюю (1) или заднюю (2) ось кг;
– часть массы автомобиля в снаряженном состоянии приходящейся на наименее нагруженную переднюю (1) или заднюю (2) ось кг;
– число шин на колесах наиболее нагруженной оси;
– число шин на колесах наименее нагруженной оси;
– ускорение свободного падения .
По ГОСТ 4754-97 шина с ближайшей большей грузоподъемностью: 20575 R16. Ее статический радиус rcт=0336 м.
1.3.3. Определение максимальной мощности двигателя
Для автотранспортных средств всех типов требуемую максимальную мощность двигателя выбирают из условия обеспечения заданной максимальной скорости .
При движении с максимальной скоростью ускорение автомобиля и мощность затрачиваемая на преодоление сопротивления разгону:
Принимая запишем уравнение мощностного баланса при движении автомобиля с максимальной скоростью:
где - мощность двигателя необходимая для движения автомобиля с максимальной скоростью кВт;
- мощность затрачиваемая на преодоление сопротивления дороги кВт;
- мощность затрачиваемая на преодоление сопротивления воздуха кВт;
- коэффициент сопротивления дороги при максимальной скорости движения;
- полная масса автомобиля кг;
- ускорение свободного падения ;
- фактор обтекаемости ;
- максимальная скорость движения автомобиля .
Необходим двигатель мощность которого с учетом подкапотных потерь составит 8766096=9131 кВт. В таблице 2.1. приведены параметры выбранного прототипа двигателя с учетом погрешности не превышающей 5%.
Таблица 2.1. Параметры двигателя
VM Motory 2.5 CDi 16V Common-Rail Diesel
Частота вращения при максимальной мощности радс (обмин)
Максимальный крутящий момент Нм
Частота вращения при максимальном моменте радс (обмин)
1.3.4. Определение передаточных чисел агрегатов трансмиссии
Определение максимального и минимального передаточных чисел трансмиссии
Максимальное передаточное число трансмиссии определяют из условия преодоления автомобилем максимального сопротивления дороги по формуле:
где rк – радиус качения ведущих колес автомобиля м (в данном случае и в дальнейшем принимаем что динамический радиус колеса равен его радиусу качения );
- максимальный крутящий момент двигателя Нм.
Проверяем полученное значение максимального передаточного числа трансмиссии по условию отсутствия буксования ведущих колес (по сцеплению ведущих колес с дорогой).
Условием отсутствия буксования ведущих колес служит неравенство .
Максимальное передаточное число трансмиссии также должно удовлетворять условию обеспечения минимальной устойчивой скорости движения необходимой в ряде случаев эксплуатации например при движении в колонне по участкам дорог со значительными неровностями и др. минимальная устойчивая скорость движения:
где - минимальная устойчивая угловая скорость вращения вала двигателя с-1;
- радиус качения колес м;
- минимальная устойчивая скорость движения принимаемая 15 2 мс.
Минимальное передаточное число трансмиссии определяется из условия обеспечения максимальной скорости движения по формуле:
где – угловая скорость вращения вала двигателя при максимальной скорости движения;
– радиус качения колес;
– максимальная скорость автомобиля.
где – угловая скорость вращения вала двигателя при максимальной мощности
Определение диапазона передаточных чисел трансмиссии
Диапазон передаточных чисел трансмиссии равен отношению максимального передаточного числа трансмиссии к минимальному передаточному числу трансмиссии:
Определение передаточных чисел ступеней агрегатов трансмиссии
Определение передаточного числа главной передачи.
Передаточное число главной передачи находят из выражения:
где - минимальное передаточное число трансмиссии;
- минимальное передаточное число коробки передач принятое
3.4.3.2. Определение передаточных чисел коробки передач.
максимальное передаточное число коробки передач.
Передаточные числа ступеней коробки передач находят из выражения:
передаточное число 2-ой передачи;
передаточное число 3-й передачи;
передаточное число 4-ой передачи (прямая передача);
передаточное число заднего хода.
- коэффициент коррекции.
Результаты расчета приведены в таблице 2.2.
Так как полученные передаточные числа сильно отличаются от исходных для приближения результатов к реальным показателям в дальнейших расчетах будем использовать реальные передаточные числа.
1.4.Тягово-динамические характеристики автомобиля
1.4.1. Тяговый баланс динамический фактор мощностной баланс и ускорение при разгоне автомобиля
Проведем необходимые расчеты для построения графиков тягового баланса динамической характеристики ускорений при разгоне и мощностного баланса автомобиля.
Пересчёт угловой скорости вращения коленчатого вала двигателя в скорость автомобиля:
где – передаточное число
– передаточное число главной передачи.
Сила сопротивления качению:
где – коэффициент сопротивления качения при малых скоростях.
Сила сопротивления воздуха:
Сила сопротивления движению:
где Кс=096 – коэффициент подкапотных потерь.
Сила тяги на колёсах:
Динамический фактор:
Ускорение при разгоне:
где f – коэффициент сопротивления качению при Va>15 мс; f=f0 при Va15 мс; g=981 мс – ускорение свободного падения;
– коэффициент учёта вращающихся масс
где Iе – момент инерции вращающихся частей двигателя;
Iкi – момент инерции i-го колеса.
Мощность на колёсах:
Мощность сопротивления воздуха:
Мощность сопротивления качению:
Полученные данные заносим в таблицы 2. 4. – 2.7.
Таблица 2.4. Баланс мощности автомобиля.
Таблица 2.5. Тяговый баланс автомобиля.
Таблица 2.6. Динамическая характеристика автомобиля.
Таблица 2.7. Ускорения автомобиля.
1.4.2.Определение времени и пути разгона автомобиля
Время разгона автомобиля на каждой передаче:
где V1 – скорость в начале разгона;
V2 – скорость в конце разгона;
ах – ускорение автомобиля.
Наиболее выгодно переключать передачи в точках пересечения графиков ускорений на разных передачах.
Представленный интеграл удобно вычислить численным методом. Для этого разобьем время разгона на каждой передаче на 12 интервалов. Обозначим:
axi – ускорение в конце i-ro интервала.
– изменение времени на
– изменение скорости на
– среднее ускорение на интервале.
Кроме того необходимо учесть время переключения передач которое примем равным 1 секунде. Тогда время разгона
где n – количество передач;
m=15 – количество интервалов разбиения времени.
Путь разгона автомобиля на каждой передаче
где t1 – время в начале разгона;
t2 – время в конце разгона;
V – скорость автомобиля.
Интеграл удобно вычислить численным методом. Для этого разобьём путь разгона на каждой передаче на 15 интервалов.
Si – путь в конце i-ro интервала.
где - изменение времени на ;
Также необходимо учесть путь пройденный автомобилем в период переключения передачи Sпj. Тогда путь разгона
где – средняя арифметическая скорость автомобиля в период переключения передачи.
По результатам расчетов построены графики времени и пути разгона автомобиля.
Полученные данные заносим в таблицы 2.8. -2. 9.
1.5.Определение показателей топливной экономичности автомобиля
Одним из показателей топливной экономичности автомобиля является контрольный расход топлива т.е. расход замеренный при движении полностью нагруженного автомобиля по ровной горизонтальной дороге при отсутствии ветра. Результатом расчета являются графики контрольного расхода топлива на всех передачах в зависимости от скорости движения.
Контрольный расход топлива определяется в следующем порядке:
Задается частота вращения коленчатого вала двигателя и определяется соответствующая ей скорость движения автомобиля
Определяется мощность двигателя. Определяются и о формулам:
Определяются коэффициенты И и Е по формулам:
- степень использования мощности;
- степень использования угловой скорости коленчатого вала;
Определяются коэффициенты и по формулам
Определяется удельный эффективный расход топлива ge по формуле:
Определяем путевой расход Qs (л100км) по формуле
где кгл – плотность топлива.
По результатам расчётов строятся графики контрольного расхода топлива на всех передачах в зависимости от скорости. Результаты расчетов заносим в таблицу 10.
Таблица 2.10. Определение расхода топлива
Титул.doc
«АНАЛИЗ КОНСТРУКЦИЙ ПРИВОДОВ ВЕДУЩИХ КОЛЕС СОВРЕМЕННЫХ АВТОМОБИЛЕЙ»
НИЧ.doc
Современные автомобили обладают большим запасом мощности и на старте при резком нажатии на педаль газа сил сцепления одной пары колес с дорожным покрытием как правило не хватает. Ведущие колеса буксуют проскальзывают избыток тяги уходит вместе с дымом сгоревшей «резины». А распределение тягового усилия не на два а на четыре колеса и возможность использовать весь вес машины в качестве сцепного уменьшают вероятность пробуксовки вдвое и гарантируют впечатляющее стартовое ускорение. К тому же полный привод обеспечивает лучшую управляемость и курсовую устойчивость автомобиля в движении особенно на скользких дорогах позволяет водителю увереннее и быстрее проходить повороты. Однако трансмиссия 4х4 требует введения в конструкцию новых узлов что делает автомобиль более тяжелым шумным и вибронагруженным. Усложнение конструкции умножает производственные издержки что отражается на стоимости полноприводного автомобиля. В свою очередь потребуют больших затрат обслуживание и ремонт такой машины в эксплуатации. А еще при прочих равных условиях автомобили 4х4 потребляют больше горючего чем их аналоги с приводом на одну ось- сказываются увеличение общего веса машины и механические потери в дополнительных агрегатах трансмиссии.
1. Основные схемы полного привода
Можно выделить три основных схемы полного привода: подключаемый полный привод (part-time) постоянный полный привод (full-time) и постоянный по-требованию полный привод (on-demand full-time).
1.1.Подключаемый полный привод
Самая простая и в то же время самая надежная схема полного привода: при нормальной эксплуатации момент передается только на одну ось а при необходимости подключается вторая ось — с помощью раздаточной коробки. При подключении оси жестко связываются между собой и колеса вращаются с одинаковой скоростью что создаёт некоторые ограничения: полный привод можно использовать только на покрытиях допускающих проскальзывание колес (грязь песок снег лед и т. п.).
При жесткой связи ведущих мостов в трансмиссии может возникнуть циркуляция мощности. При движении по хорошей горизонтальной дороге циркулирующая мощность (ЦМ) может быть значительной. ЦМ не используется для преодоления сил сопротивления движению автомобиля дополнительно нагружает механизмы трансмиссии и шины вызывая их повышенное изнашивание. Кроме того из-за увеличения суммарной мощности передаваемой через механизмы трансмиссии возрастают потери мощности в трансмиссии на буксование колес увеличивая расход топлива и изнашивание деталей двигателя. Поэтому ЦМ является вредной и ее часто называют паразитной мощностью. Чтобы уменьшить дополнительное изнашивание механизмов трансмиссии шин и расход топлива вызванных ЦМ и перераспределением крутящего момента при раздаточной коробке с блокированным приводом необходимо включать передний ведущий мост только для повышения проходимости и устойчивости автомобиля. При движении по хорошим дорогам необходимо принудительное отключение переднего ведущего моста для устранения циркуляции мощности или перераспределения крутящего момента.
1.2.Постоянный полный привод
Постоянный полный привод подразумевает постоянное подключение всех колес к двигателю для чего он подключается к осям через дифференциал. Некоторые модели автомобилей имеют принудительную блокировку межосевого дифференциала что позволяет им становиться аналогичным автомобилям с подключаемым полным приводом (в общем случае это повышает проходимость автомобиля). Некоторые современные автомобили имеют электронное управление межосевым дифференциалом позволяющее динамически менять соотношение передаваемого момента между осями. В основном это используется для уверенного движения по дорогам например в системах динамической стабилизации.
1.3.Постоянный по-требованию полный привод
Эту схему можно считать разновидностью постоянного полного привода. В ней одна ось подключена жестко а вторая (передняя или задняя чаще — задняя) подключается при проскальзывании первой через разнообразные муфты (вискомуфта(Гольф-3) Халдекс (Гольф-4) многодисковое сцепление(Субару с АКПП) ). Управление муфтой осуществляется электроникой или механико-гидравлическим образом за исключением вискомуфты. Недостатком такой схемы можно считать непредсказуемость поведения автомобиля в переходных состояниях — оно может за доли секунды меняться от выраженно переднеприводного до выраженно заднеприводного.
Конфигурация схемы трансмиссии определяется помимо прочих факторов в первую очередь расположением силового агрегата автомобиля. В зависимости от ориентации оси коленчатого вала относительно продольной оси машины различают продольное или поперечное расположение силового агрегата. По размещению двигателя относительно осей передних или задних колес различают компоновки: перед передней осью за передней осью перед задней осью (среднемоторная) за задней осью.
Расположение двигателя относительно осей передних или задних колес влияет на распределение массы по осям – развесовку а следовательно и на режим работы многодисковой фрикционной муфты с электронным управлением или на выбор конструкции межосевого дифференциала.
При поперечном расположении силового агрегата спереди двигатель всегда размещен перед передней осью. Это дает сильный дифферент на колеса передней оси. Кроме того возникает необходимость изменения направления вектора мощности на 90°. Для этого в конструкцию вводят гипоидную пару шестерен как правило имеющую передаточное число 1. Такая схема широко применяется на современных легковых автомобилях когда полноприводную трансмиссию создают дорабатывая трансмиссию перенеприводного автомобиля. Она также характерна для большинства кросссоверов. Отбор мощности к приводному валу заднего моста осуществляется с корпуса дифференциала переднего моста или с вала жестко связанного с корпусом дифференциала. То есть уже после того как снимаемый с выходного вала коробки передач момент был трансформирован главной передачей. Такая конструкция с одной стороны проста с другой – имеет два недостатка. Во-первых приводной вал на задний мост должен рассчитываться на передачу большего крутящего момента и соответственно иметь большую массу. Во-вторых гипоидная пара снижает коэффициент полезного действия трансмиссии.
При продольном расположении силового агрегата как спереди так и сзади для отбора мощности на один из мостов не требуется изменять направление вектора мощности. Стало быть можно обойтись либо зубчатой цепью либо цилиндрической зубчатой передачей коэффициент полезного действия которых выше. Вне зависимости от расположения двигателя относительно осей передних и задних колес отбор мощности производят с выходного вала коробки передач. Продольное расположение силового агрегата позволяет изготовить приводной вал к мосту на который отбирается мощность меньшим по массе поскольку он рассчитывается на передачу меньшего крутящего момента.
Когда силовой агрегат размещен спереди продольно двигатель редко удается расположить за осью передних колес. Ведь в этом случае приходится один из приводных валов колес проводить «сквозь» масляный поддон. Длину участка вала попадающего в поддон подбирают так чтобы приводные валы с шарнирами равных угловых скоростей обоих колес были одинаковыми. Если силовой агрегат размещен спереди продольно а двигатель оппозитный (с углом развала блока 180°) то его устанавливают перед передней осью. Причина проста: современные оппозитные двигатели имеют систему смазки с сухим поддоном картера и могут быть размещены ниже чем моторы классической компоновки. И это делается для уменьшения высоты центра тяжести автомобиля. Такое решение не всегда оправдано с позиций развесовки.
На автомобилях фирмы Audi с продольным расположением силового агрегата двигатель также устанавливают перед передней осью. Это связано с тем что на переднеприводных версиях с механической коробкой применена система «вал в вале»: приводной вал переднего моста расположен в выходном вале коробки а создавать специально для полноприводной версии оригинальную компоновку нецелесообразно.
На автомобилях малого класса (на рисунке 1.1. – F двигатель размещен перед передней осью. Для отбора мощности на приводной вал заднего моста в конструкцию вводят гипоидную пару шестерен: ее задача изменить направление вектора мощности на 90°.
На автомобилях средних размерных классов (на рисунке 1.2. – Volkswagen Passat относящийся к ё вал заднего моста в конструкцию вводят гипоидную пару шестерен: ее задача изменить направление вектора мощности на 90°.
Несколько производителей на автомобилях средних размерных классов (на рисунке 1.3. – Mercedes-Benz C-klasse относящийся к европейскому размерному классу D) размещают силовой агрегат продольно. Двигатель практически полностью размещен за передней осью однако приводной вал левого колеса проводят через поддон картера. Для отбора мощности на приводной вал переднего моста применяется цилиндрическая пара шестерен.
Некоторые производители на автомобилях средних размерных классов (на рисунке 1.4. – Audi A5 относящаяся к европейскому размерному классу D) размещают силовой агрегат продольно. Одним из недостатков схемы примененной на данном автомобиле является размещение двигателя перед передней осью.
На компактных и среднеразмерных кроссоверах (на рисунке 1.5 – Opel Frontera) как правило размещают силовой агрегат спереди поперечно. Двигатель устанавливают перед передней осью. Для отбора мощности на приводной вал заднего моста используется гипоидная пара шестерен.
На спорткарах (на рисунке 1.6. – Audi R8) часто применяют среднемоторную компоновку. В данном случае двигатель размещен перед задней осью коробка передач за задней осью. Для отбора мощности на приводной вал вязкостной муфты применяется цилиндрическая пара шестерен.
На некоторых спортивных автомобилях (на рисунке 1.7. – Porsche 911) часто применяют заднемоторную компоновку: двигатель размещен продольно за задней осью. Для отбора мощности на передний мост используется цилиндрическая пара шестерен.
двигатель; 2 коробка передач; 3 картер переднего моста; 4 карданный вал привода переднего колеса; 5 карданный вал привода заднего моста; 6 картер вязкостной муфты; 7 картер заднего моста; 8 карданный вал привода заднего колеса.
картер переднего моста; 2 карданный вал привода переднего колеса; 2 приводной вал заднего моста; 4 картер заднего моста; 5 карданный вал привода заднего колеса.
раздаточная коробка; 2 карданный вал привода заднего моста; 3 карданный вал привода переднего моста; 4 карданный вал привода заднего колеса; 5 картер заднего моста; 6 передний мост; 7 карданный вал привода переднего колеса.
двигатель; 2 коробка передач; 3 раздаточная коробка; 4 карданный вал привода переднего колеса; 5 приводной вал заднего моста; 6 картер заднего моста; 7 карданный вал привода заднего колеса.
двигатель; 2 коробка передач; 3 раздаточная коробка; 4 карданный вал привода переднего колеса; 5 карданный вал привода заднего моста; 6 картер заднего моста; 7 карданный вал привода заднего колеса.
двигатель; 2 коробка передач; 3 карданный вал привода заднего колеса; 4 приводной вал вязкостной муфты; 5 картер вязкостной муфты; 6 картер переднего моста; 7 карданный вал привода переднего колеса.
двигатель; 2 коробка передач; 3 карданный вал привода заднего колеса; 4 приводной вал к переднему мосту; 5 картер муфты; 6 картер переднего моста; 7 карданный вал привода переднего колеса.
двигатель; 2 коробка передач; 3 раздаточная коробка; 4 приводной вал переднего моста; 5 карданный вал привода заднего моста; 6 картер заднего моста; 7 карданный вал привода заднего колеса.
На автомобилях повышенной проходимости имеющих в качестве силового элемента раму (на рисунке 1.8. - Ford Explorer) силовой агрегат размещают спереди продольно. Из соображений компоновки двигатель не размещают за передней осью хотя никаких препятствий к этому нет. Для отбора мощности на приводной вал переднего моста в раздаточной коробке используется зубчатая цепь.
На полноразмерных кроссоверах (на рисунке – Cadillac Escalade) имеющих в качестве несущего элемента раму силовой агрегат размещают спереди продольно. Двигатель практически полностью располагают за передней осью. Отбор мощности на передний мост осуществляется зубчатой цепью.
двигатель; 2 коробка передач; 3 раздаточная коробка; 4 карданный вал привода переднего моста; 5 карданный вал привода переднего колеса; 6 карданный вал привода заднего моста; 7 картер заднего моста.
3.Раздаточная коробка
Раздаточная коробка (сокращенно РК) — это узел трансмиссии объединяющий раздаточный элемент и механизм отбора мощности на один из мостов. Кроме того в зависимости от назначения автомобиля раздаточная коробка может включать понижающую передачу (в нашем каталоге обозначается как ПП).
Надо заметить что автомобиль оборудованный понижающей передачей не обязательно обладает повышенными свойствами на бездорожье. Тем не менее этот критерий — наличие или отсутствие понижающей передачи — был выбран нами в качестве основного для определения принадлежности каждой модели к той или иной группе автомобилей. В подавляющем большинстве машины с понижающей передачей все-таки оказываются в разделе «Специальные автомобили». Но встречаются и исключения. Так модели Subaru на которых понижающая лишь в умеренных пределах увеличивает тяговые способности отнесены к разделам «Легковые автомобили» и «Кроссоверы». Впрочем разработчики Subaru сами рекомендуют использовать понижающую передачу на своих машинах либо для буксировки прицепа либо для получения максимального ускорения при разгоне. Активировать ПП на автомобилях Subaru можно двигаясь на любой скорости. Селектор включения понижающей передачи размещен на центральном тоннеле рядом с рычагом коробки передач.
Передаточное число понижающей передачи трансмиссии выбирается в зависимости от назначения автомобиля и согласовывается с величиной максимального крутящего момента двигателя передаточным числом первой передачи в коробке передач и передаточным числом главной передачи. При прочих равных условиях чем больше передаточное число ПП тем больший эффект дает ее использование в условиях бездорожья. Как правило на автомобилях предназначающихся для езды по бездорожью в раздаточной коробке устанавливается лишь одна понижающая передача. Однако на некоторых моделях например на Land Rover Defender предусмотрены две передачи с передаточным числом больше единицы. На сегодняшний день установка двух понижающих передач в раздаточной коробке — большая редкость.
В качестве раздаточного элемента трансмиссии в современных автомобилях применяются дифференциал или муфта. Оба этих узла обладают свойством разделять поток мощности на два потока. Соответственно еще одной конструктивной особенностью раздаточной коробки является наличие одного входного вала и двух выходных. При разнеени узла отбора и муфты раздаточная коробка включающая только муфту имеет один входной и один выходной вал. Если в автомобиле не предусмотрен раздаточный элемент трансмиссии или он разнесен с механизмом отбора мощности то по отношению к такому узлу включающему механизм отбора мощности и понижающую передачу более корректно употреблять термин «узел отбора мощности» а не «раздаточная коробка». Напротив раздаточный элемент размещенный в «отдельном» картере с полным правом можно назвать раздаточной коробкой. Более того если в РК размещен дифференциал который может тем или иным способом полностью блокироваться то на время действия блокировки раздаточная коробка превращается в полноценный узел отбора мощности: ведь в полностью заблокированном состоянии дифференциал не участвует в работе трансмиссии и на оба моста приходится 100% мощности. В общем для упрощения восприятия информации в каталоге «Полноприводные автомобили» узел отбора мощности включающий понижающую передачу называется раздаточной коробкой. В большинстве случаев картер раздаточной коробки стыкуют непосредственно с картером коробки передач. Однако встречаются исключения. Например на автомобиле Mercedes-Benz G-klasse или полноприводных машинах АвтоВАЗа коробка передач и РК разнесены: выходной вал КП и входной вал раздаточной коробки соединены карданным валом. Такое решение возможно в частности из соображений компоновки элементов трансмиссии или развесовки т.е. распределения массы по осям. На современных автомобилях к разнесению раздаточной коробки и коробки передач прибегают редко.
На полноприводных автомобилях с гибридным силовым агрегатом (на рисунке 1.11. — РК автомобиля Lexus LS 600h) раздаточная коробка ничем не отличается от РК автомобилей с классическим силовым агрегатом.
На автомобилях повышенной проходимости (на рисунке 1.13. - раздаточная коробка автомобиля Land Rover) устанавливают понижающую передачу.
Рисунок 1.10. Раздаточная коробка автомобиля BMW 5 серии
картер раздаточной коробки; 2 ведущая шестерня приводного механизма отбора мощности; 3 паразитная шестерня механизма отбора мощности; 4 ведомая шестерня механизма отбора мощности; 5 приводной карданный вал переднего моста; 6 многодисковая фрикционная муфта с электронным управлением; 7 вилка включения муфты; 8 электромеханический узел привода включения муфты; 9 упругая компенсирующая муфта; 10 приводной вал заднего моста.
картер раздаточной коробки; 2 ведущая шестерня приводного механизма отбора мощности; 3 паразитная шестерня механизма отбора мощности; 4 ведомая шестерня механизма отбора мощности; 5 фланец приводного вала переднего моста; 6 самоблокирующийся межосевой дифференциал с параллельными осями сателлитов и полуосевых шестерен; 7 фланец упругой муфты приводного вала заднего моста.
картер коробки передач; 2 картер раздаточной коробки; 3 зубчатая цепь являющаяся элементом механизма отбора мощности; 4 вилка включения понижающей передачи; 5 электрический управляющий разъем привода включения понижающей передачи; 6 фланец приводного вала заднего моста.
Рисунок 1.13. Раздаточная коробка установленная на полноразмерном кроссовере Audi Q7.
картер раздаточной коробки; 2 крышка картера раздаточной коробки; 3 входной вал раздаточной коробки; 4 несимметричный самоблокирующийся дифференциал; 5 ведущая шестеренка механизма отбора мощности; 6 цепь механизма отбора мощности; 7 ведомая шестеренка механизма отбора мощности; 8 приводной вал заднего моста; 9 приводной вал переднего моста.
4.Узел отбора мощности
В современных полноприводных легковых автомобилях очень часто разносят раздаточный элемент трансмиссии (муфту или дифференциал) от механизма отбора мощности на один из мостов. Кроме того раздаточный элемент может быть попросту не предусмотрен разработчиками. В этом случае узел объединяющий механизм отбора мощности и понижающую передачу более корректно называть узлом отбора мощности.
При продольном расположении силового агрегата картер узла объединяющего механизм отбора мощности и понижающую передачу стыкуют непосредственно с картером коробки передач. Как правило механизм отбора мощности в этом случае состоит из двух основных элементов: устройства обеспечивающего непосредственно отбор мощности и приводного элемента. Устройство отбора может быть исполнено в виде многодисковой фрикционной муфты либо в виде механического привода. В первом случае — инженеры могут предусмотреть возможность как автоматического срабатывания муфты так и возможность ее принудительного включения водителем. Во втором случае — подключение переднего моста производится только принудительно: на центральном тоннеле установлен дополнительный рычаг.
В качестве приводного элемента используют либо зубчатую цепь либо цилиндрическую зубчатую передачу. Зубчатая цепь обладает одним неоспоримым преимуществом перед прочими типами цепных передач — способностью выдерживать высокие нагрузки. По этому параметру данный вид цепи успешно соперничает с зубчатыми передачами ведь приводной элемент должен выдержать максимальный крутящий момент выдаваемый двигателем умноженный сначала на передаточное число первой передачи в коробке передач а затем и на передаточное число понижающей передачи.
Компоновка главной передачи (ГП) переднего моста (именно на приводной вал переднего моста передает мощность цепь при продольном расположении силового агрегата) определяет очень важный параметр а именно — требуемое направление вращения ведущей шестерни главной передачи. Цепь обеспечивает сонаправленное вращение ведущих передач обоих мостов. Еще одним преимуществом использования цепи является возможность соосной установки ведомой шестерни привода и ведущей шестерни главной передачи переднего моста без значительного увеличения массы и габаритов узла отбора мощности. Благодаря этому инженеры-конструкторы могут отказаться от использования карданных шарниров неравных угловых скоростей в приводном вале переднего моста.
В тех случаях когда требуется разнонаправленное вращение ведущих шестерен главных передач в качестве приводного элемента используется зубчатая передача. Поскольку пара шестерен постоянно находятся в зацеплении то зубья шестерен выполняются не прямыми а косыми. Это повышает способность передачи выдерживать нагрузки. Правда в качестве опоры валов на которые установлены шестеренки приходится использовать более дорогие конические упорные подшипники — тут шариковыми или роликовыми уже не обойтись.
При использовании в качестве приводного элемента зубчатой передачи можно добиться и сонаправленного вращения ведущих шестерен главных передач мостов: для этого в конструкцию вводят паразитное зубчатое колесо.
При поперечном расположении силового агрегата для передачи мощности к приводному валу раздаточного элемента приходится применять гипоидную передачу. Как правило ее передаточное число равно 10. Задача гипоидной пары состоит в изменении направления вектора мощности на 90°. В подавляющем большинстве случаев при таком исполнении приводного элемента отбор производится либо непосредственно с корпуса дифференциала переднего моста либо с вала жестко связанного с корпусом дифференциала. Для упрощения рассказывая о трансмиссии автомобилей с поперечно расположенным силовым агрегатом мы говорим об отборе мощности на приводной вал заднего моста хотя точнее было бы говорить о передаче мощности к раздаточному элементу.
Очень часто на автомобилях повышенной проходимости с принудительно подключаемым передним мостом не устанавливают межосевой дифференциал.
При продольном расположении силового агрегата отбор мощности производится с помощью цилиндрической пары шестерен. На рисунке 1.15. изображен механизм отбора мощности на передний мост автомобиля Audi R8.
При поперечном расположении силового агрегата (на рисунке 1.16. — узел отбора Audi TT) для передачи мощности на задний мост используют гипоидную передачу.
При поперечном расположении силового агрегата в силу особенностей компоновки приходится вводить дополнительные элементы отбора в данном случае на рисунке 1.17. помимо гипоидной пары в конструкцию включена и цилиндрическая.
Рисунок 1.14. Коробка отбора мощности
входной вал коробки; 2 ведущая шестерня механизма отбора мощности; 3 зубчатая цепь механизма отбора мощности; 4 ведомая шестерня механизма отбора мощности; 5 выходной вал коробки отбора мощности (на передний мост); 6 выходной вал коробки отбора мощности (на задний мост).
выходной вал коробки передач; 2 ведущая шестерня отбора мощности; 3 ведомая шестерня отбора мощности на задний мост; 4 ведомая шестерня отбора мощности на передний мост; 5 ведущая шестерня главной передачи заднего моста; 6 приводной вал на передний мост.
выходной вал коробки передач; 2 ведущая шестерня главной передачи переднего моста; 3 ведомая шестерня главной передачи переднего моста; 4корпус дифференциала переднего моста; 5 корпус дифференциала жестко соединенный с приводным валом механизма отбора мощности на задний мост; 5 гипоидная пара отбора мощности на задний мост.
ведомая шестерня главной передачи переднего моста; 2 приводной вал узла отбора; 3 ведомая шестерня цилиндрической пары; 4 ведущая шестерня гипоидной пары; 5 ведомая шестерня гипоидной пары.
Дифференциал (сокращенно Д) — это раздаточный элемент трансмиссии. По месту расположения дифференциалы бывают межколесные и межосевые. По соотношению крутящего момента на ведомых валах — с постоянным и непостоянным соотношением. По наличию блокировки различают дифференциалы свободные самоблокирующиеся и блокируемые дополнительным механизмом.
Между колесами устанавливаются симметричные дифференциалы. Между мостами могут устанавливаться как симметричные так и несимметричные: определяющим фактором тут является распределение массы по осям. Производители в последнее время часто используют несимметричные дифференциалы с распределением 40:60. То есть на передний мост приходится 40% крутящего момента снимаемого с выходного вала коробки передач на задний — 60%.
Конструктивно симметричные конические дифференциалы состоят из набора конических зубчатых колес-сателлитов размещенных на одной оси и полуосевых шестерен. Несимметричные дифференциалы устанавливаемые на современных автомобилях как правило представляют собой планетарную передачу.
Способность дифференциала разделять один поток мощности на два определяется наличием двух степеней свободы. Для того чтобы свободный дифференциал выполнял свои функции необходимо наложить две связи: это контакт каждого из колес на которые дифференциал распределяет крутящий момент с дорогой. Если одну из связей убрать например вывесить колесо то дифференциал перестает распределять крутящий момент. На практике причиной нарушения одной из связей становится разница в условиях по сцеплению колеса с дорогой. Через колесо находящееся на сухом асфальте можно реализовать в 4—5 раз больше тяги чем через колесо находящееся на скользком или влажном покрытии например на льду. То есть если при начале движения автомобиля одно из колес стоит на асфальте а второе — на льду то будет реализована лишь незначительная часть тягового усилия.
Самоблокирующиеся и блокируемые дифференциалы таким недостатком не обладают. Блокировка предусматривается для того чтобы реализовать тягу через колесо находящееся в лучших условиях по сцеплению. Блокировка свободных дифференциалов дополнительным механизмом заключается в жестком соединении корпуса дифференциала и одной из полуосевых шестерен. В этом случае дифференциал исключается из работы и крутящий момент не распределяется. То есть на каждое из колес приходится 100% тяги поступающей на задний мост. Соответственно при прочих равных условиях самыми лучшими свойствами на бездорожье будет обладать тот автомобиль у которого блокируются все три дифференциала трансмиссии.
Для того чтобы свободный конический дифференциал стал самоблокирующимся в конструкцию добавляют два пакета фрикционов срабатывающих при разнице скоростей колес. В этом случае водитель не может принудительно заблокировать дифференциал. Очень часто с дифференциалом устанавливают фрикционную муфту которой может управлять как электроника так и водитель.
Современные легковые автомобили комплектуются и самоблокирующимися дифференциалами в которых эффект самоблокировки обеспечивается конфигурацией зубьев шестерен нарезанных по винтовой линии. Различают степень блокировки и процент блокировки дифференциалов. Степень блокировки показывает — при какой разнице в угловых скоростях колес дифференциал начинает блокироваться а процент блокировки — какую часть тяги можно реализовать через колесо находящееся в лучших условиях по сцеплению. Конструкция современных самоблокирующихся дифференциалов устанавливаемых между мостами позволяет реализовывать различный процент через колеса передней и задней оси. Подобные механизмы в частности устанавливаются на некоторых моделях Audi.
На рисунке 1.19. изображено крайне редкое на сегодняшний день исполнение дифференциала переднего моста и межосевого дифференциала объединенных в двухрядной планетарной передачей.
Для блокировки свободного конического дифференциала часто используют два дополнительных пакета фрикционов в результате получают самоблокирующийся дифференциал реагирующий на разницу скоростей вращения ведущих колес (рисунок 1.20).
В переднем мосту легковых автомобилей часто используют самоблокирующиеся цилиндрические дифференциалы с параллельными осями сателлитов и полуосевых шестерен(рисунок 1.21) . Зубья шестерен нарезаны по винтовой линии.
Активный дифференциал заднего моста автомобиля BMW X6 (рисунок 1.22.). Данный механизм позволяет в динамическом режиме варьировать тягу на каждом колесе. Через любое из колес можно реализовать до 100% крутящего момента приходящего от раздаточной коробки.
Активный дифференциал заднего моста автомобиля Mitsubishi Lancer Evolution (рисунок 1.23.). Данный механизм позволяет в динамическом режиме варьировать тягу на каждом колесе. Через любое из колес можно реализовать до 100% крутящего момента приходящего от раздаточной коробки.
Рисунок 1.18. Передний мост автомобилей Mercedes-Benz с полноприводной трансмиссией; межколесный дифференциал — конический простой симметричный.
фланец вала-шестерни; 2 ведущая шестерня главной передачи переднего моста; 3 ведомая шестерня главной передачи; 4 корпус дифференциала; 5 сателлит; 6 ось сателлитов; 7 полуосевая шестерня; 8 карданный вал привода колеса.
Рисунок 1.19. Компоновка трансмиссии — Hyundai Santa Fe Classic
ведомая шестерня главной передачи переднего моста; 2 планетарная передача объединяющая в себе дифференциал переднего моста и межосевой дифференциал; 3 приводной вал левого колеса; 4 приводной вал правого колеса; 5 вязкостная муфта; 6 гипоидная передача привода вала заднего моста.
корпус дифференциала; 2 фрикционное кольцосвязанное с корпусом; 3 фрикционное кольцо связанное с полуосевой шестерней посредством приводного вала; 4 крышка корпуса; 5 сателлит; 6 ось сателлитов; 7 полуосевая шестерня.
корпус дифференциала; 2 обойма (полуосевая шестерня правого колеса); 3 сателлит; 4 центральная полуосевая шестерня (левого колеса); 5 крышка корпуса дифференциала.
Рисунок 1.22. Активный дифференциал заднего моста автомобиля BMW X6.
ведущая шестерня главной передачи; 2 ведомая шестерня главной передачи; 3 простой симметричный конический дифференциал; 4 планетарный редуктор; 5 пакет фрикционов.
Рисунок 1.23. Активный дифференциал заднего моста автомобиля Mitsubishi Lancer Evolution.
ведущая шестерня главной передачи; 2 ведомая шестерня главной передачи; 3 корпус дифференциала; 4 свободный планетарный дифференциал; 5 пакет фрикционов.
Муфты выполняют следующие функции: передача усилия с компенсацией неточности монтажа агрегатов трансмиссии отбор потока мощности блокировка свободного дифференциала.
Упругие компенсирующие муфты устанавливают в валах передающих мощность от коробки передач к заднему мосту. Силовой агрегат при этом может располагаться как продольно так и поперечно. Этот тип муфт еще называют упругим полукарданным шарниром. Устроен механизм достаточно просто: к упругому элементу с двух сторон крепятся фланцы приводных валов. Упругое звено может быть как резино-тканевым так и резиновым с армированием стальным тросом. В последнем случае муфта способна передавать большие нагрузки. Достоинством упругих муфт является их способность гасить динамические нагрузки возникающие например при резком включении или выключении сцепления. Муфты являющиеся раздаточными элементами трансмиссии бывают двух типов: многодисковые фрикционные с электронным управлением и вязкостные работающие в автоматическом режиме. Большее распространение получили многодисковые фрикционные муфты. Они устроены достаточно просто. На входном вале муфты установлено несколько фрикционных дисков между которыми размещены диски корпуса муфты жестко связанного с выходным валом. При замыкании дисков муфта начинает передавать мощность. Замыканием дисков управляет электронный блок: команда на срабатывание подается после того как одно из колес оси начинает проскальзывать то есть вращаться со скоростью большей чем может обеспечить подводимая к колесу мощность.
Муфты старого образца имеют электромеханический привод. На электрический разъем мотор-редуктора подается напряжение мотор начинает вращаться и мощность с выходного вала через приводной механизм передается на вилку которая и передвигает диски муфты. Довольно часто устанавливают гидравлический привод срабатывания. В этом случае исходным звеном также является электромотор от которого работает гидравлический насос. На поршень размещенный в корпусе муфты подается рабочая жидкость которая сжимает фрикционные диски. В этом случае диски муфты работают не всухую а в рабочей жидкости — специальном масле. Этот тип муфт имеет самое быстрое срабатывание. Все большее распространение получает исполнительный механизм работающий по принципу электромагнита: на обмотки подается напряжение сердечник перемещается и фрикционные диски смыкаются.
При проскальзывании одного из валов вязкостной муфты начинает меняться вязкость силиконовой жидкости которой заполнена муфта диски сжимаются и момент передается на колеса имеющие лучшие условия по сцеплению с дорогой.
Как правило вязкостные муфты и муфты с электронным управлением применяются в трансмиссии при поперечном расположении силового агрегата. Картер муфты стыкуют непосредственно с картером заднего моста.
Для блокировки свободного дифференциала применяют многодисковые фрикционные муфты с электронным управлением. Муфта жестко соединяет корпус дифференциала и одну из полуосевых шестерен. В таких конструкциях корпус муфты прифланцовывают к корпусу дифференциала. Дифференциалы с блокировкой дополнительным элементом относительно недороги в производстве и успешно конкурируют с самоблокирующимися дифференциалами. Во-первых муфтой достигается полная блокировка дифференциала а во-вторых есть возможность принудительной блокировки: в салоне размещают кнопку электропривода. То есть автомобили с таким механизмом обладают лучшими свойствами на бездорожье чем автомобили с самоблокирующимися межколесными дифференциалами.
При продольном расположении силового агрегата и отсутствии межосевого дифференциала в узле отбора мощности также устанавливают многодисковые фрикционные муфты. В этом случае муфта подключает механизм отбора мощности на передний мост. Подключение может осуществляться как в автоматическом режиме — по команде электронного блока управления так и принудительно когда в салоне устанавливают тумблер электропривода блокировки муфты.
Многодисковые фрикционные муфты с электронным управлением часто устанавливают на спортивные автомобили. В данном случае (на рисунке 1.24. — муфта привода переднего моста Porshe 911) муфта отбирает часть мощности на передний мост.
Многодисковая фрикционная муфта нашла самое широкое применение в трансмиссии как легковых автомобилей так и кроссоверов с силовым агрегатом расположенным спереди поперечно. Картер муфты как правило стыкуют с картером заднего моста (рисунок 1.25).
В трансмиссии современных легковых автомобилей вязкостные муфты (рисунок 1.26.) устанавливают не часто. Муфта не требует электронного управления и работает в автоматическом режиме реагируя на разницу во вращении колес одного из мостов.
Многодисковые фрикционные муфты (рисунок 1.27.) часто используют в качестве вспомогательного элемента для блокировки свободного дифференциала. Пакет фрикционов жестко соединяет полуосевую шестерню и корпус дифференциала.
входной вал; 2 шариковый подшипник; 3 пакет фрикционных дисков; 4 обойма муфты; 5 обмотка электромагнита; 6 приводной вал на передний мост.
карданный вал; 2 многодисковая фрикционная муфта с электронным управлением; 3 ведомая шестерня главной передачи заднего моста; 4 корпус дифференциала; 5 карданный вал привода заднего колеса.
вал-втулка вязкостной муфты; 2 фрикционный диск связанный шлицевым соединением с валом-втулкой; 3 фрикционный диск связанный шлицевым соединением с обоймой; 4 обойма; 5 уплотнитель.
корпус дифференциала; 2 полуосевая шестерня; 3 вал-втулка расположенная на приводном валу колеса; 4 пакет фрикционов; 5 поршень сжимающий пакет фрикционов.
Отдельно бы хотелось остановиться на конструкции и принципе работы муфты HALDEX.
Применение многодисковой фрикционной муфты фирмы Haldex с электрогидравлическим управлением позволило ввести электронное управление полным приводом автомобиля. Блок управления муфты фирмы Haldex учитывает не только пробуксовку колёс но и условия движения — движение на повороте скорость автомобиля а также движение на режиме принудительного холостого хода или в тяговом режиме.
Рисунок 1.28. Муфта Haldex
Рисунок 1.29. Муфта Haldex II
поколения 2004 модельного года
Рисунок 1.30. Муфта Haldex IV поколения
Принцип работы муфты Haldex
Впускной и напорный клапаны а также клапан с электронным управлением и блок управления регулируют давление сжимающее фрикционные диски муфты.
В муфтах Haldex первого и второго поколений разница скоростей вращения передней и задней осей автомобиля используется для работы насоса муфты создающего рабочее давление масла. Насос состоит из кулачкового диска приводного ролика и двух работающих параллельно поршней. Под действием давления масла поршень сжимает пакет фрикционных дисков. Величина усилия сжатия определяет передаваемый крутящий момент. Впускной и напорный клапаны а также клапан с электронным управлением и блок управления регулируют давление сжимающее фрикционные диски муфты.
Муфта полного привода IV поколения и предыдущая модель муфты Haldex имеют одинаковый принцип действия — передача крутящего момента с помощью пакета фрикционных дисков. Новым является то что давление в гидросистеме муфты создаётся электрическим насосом. Передаваемый крутящий момент корректируется блоком управления полного привода с помощью подачи сигнала на клапан управления
замыкания муфты. Разность скоростей вращения колёс передней и задней осей больше не является условием включения муфты полного привода.
Особенности конструкции
● Многодисковая фрикционная муфта с электрогидравлическим управлением
● Муфта встроена в картер задней главной передачи
● Упрощённая гидравлическая система (по сравнению с предыдущими моделями)
● Управление насосом оптимизированное в зависимости от давления необходимого в данный момент
● Управление муфтой вне зависимости от условий движения
● Быстрое увеличение крутящего момента с помощью упреждающего управления
● Задняя главная передача постоянно включена
● Совместима без ограничений с электронными системами управления тормозами (например ESP ABS)
Карданной называется передача в состав которой входит карданный шарнир. Карданные передачи применяются для силовой связи механизмов входной и выходной валы которых не соосны или расположены под углом друг к другу. В зависимости от схемы трансмиссии автомобиля карданные передачи могут включать один или несколько шарниров. Если шарниров больше двух значит в конструкцию вводится промежуточная опора корпус которой крепится к кузову или поперечине рамы.
В современных легковых автомобилях применяют два типа карданных шарниров: неравных (ШНУС) и равных угловых скоростей (ШРУС). У ШРУСов угловая скорость выходного вала меняется с изменением скорости входного и при постоянной скорости входного вала также постоянна. У шарниров неравных угловых скоростей при постоянной угловой скорости входного вала угловая скорость выходного меняется. Для компенсации этого эффекта в конструкцию вала вводится как минимум еще один шарнир неравных угловых скоростей.
ШНУСы в современных автомобилях применяют для передачи мощности: от выходного вала коробки передач к ведущей шестерне главной передачи заднего моста (при зависимой подвеске задних колес). Для компенсации взаимного перемещения коробки передач и моста в конструкцию карданного вала вводят шлицевое соединение допускающее осевое перемещение двух частей вала друг относительно друга. При независимой подвеске задних колес и следовательно жестком креплении картера моста к несущему элементу необходимости в использовании шарниров неравных угловых скоростей нет.
Крайне редко шарниры неравных угловых скоростей применяют для передачи мощности на управляемые колеса. Это делают в случае если передний мост подключается водителем а в РК не установлен межосевой дифференциал. Тогда производитель рекомендует подключать передние колеса только для преодоления участков бездорожья с малой скоростью. В нашем каталоге представлен автомобиль где в приводе к передним ведущим колесам используется карданный шарнир неравных угловых скоростей — это Jeep Wrangler.
Когда силовой агрегат размещен спереди продольно двигатель редко удается расположить за осью передних колес. В этом случае один из карданных валов проходит «сквозь» масляный поддон. Длину подбирают так чтобы оба вала с шарнирами равных угловых скоростей были одинаковыми. Если силовой агрегат размещен спереди продольно а двигатель оппозитный (с углом развала блока 180°) то его устанавливают перед передней осью. Причина проста: современные оппозитные двигатели имеют систему смазки с сухим поддоном картера и могут быть размещены ниже чем моторы классической компоновки. И это делается для уменьшения высоты центра тяжести автомобиля. Такое решение не всегда оправдано с позиций развесовки но избавляет от необходимости размещать в поддоне картера один из участков приводного вала.
Карданный шарнир неравных угловых скоростей (рисунок 1.31.) применяется в трансмиссии современных автомобилей в составе приводного вала между узлами трансмиссии — раздаточной коробкой и мостами (задним или передним). Основные достоинства узла: ремонтопригодность невысокая стоимость производства. В конструкцию шарнира входят помимо прочего четыре игольчатых подшипника которые размещены на крестовине. 1 входная вилка; 2 выходная вилка; 3 крестовина.
Карданный шарнир равных угловых скоростей (рисунок 1.32.) применяется для передачи мощности от моста к колесам с независимой подвеской. Поскольку и управляемые и неуправляемые колеса в процессе движения автомобиля меняют свое положение относительно картера моста в конструкцию карданного вала входит два шарнира. 1 вал; 2 кулак выполненный заодно с валом; 3 шарик; 4 защитный кожух.
Расчет продольной устойчивости автомобиля
1. Расчет продольной устойчивости переднеприводного автомобиля
Рассмотрим рисунок 2.1. Автомобиль движется вверх по склону с углом наклона α. Скорость автомобиля V=14 мс она постоянна.
Для схемы необходимо определить:
а)Условие устойчивости автомобиля по продольному опрокидыванию
б)Условие отсутсвия пробуксовки ведущих колес
в)Условие безопасности движения в подъем
а) Условие опрокидывания:
- суммарная сила сопротивления качению.
- критический угол по опрокидыванию.
б) Условие отсутствия пробуксовывания ведущих колес:
в) Условие безопасного движения в подъем:
Исходные данные для расчета:
Результаты расчета относительно коэффициента приведены в таблице 2.1.
2. Расчет продольной устойчивости полноприводного автомобиля
Рассмотрим рисунок 2. Автомобиль движется вверх по склону с углом наклона α. Скорость автомобиля V=14 мс она постоянна.
По результатам расчета построены сравнительные графики
Асфальтобетон в плохом состоянии
Булыжное в хорошем состоянии
Асфальтобетон в хорошем состоянии
В) Условие безопасного движения в подъем выполняется в обоих случаях
Вывод: из результатов видно что полноприводный автомобиль может преодолевать значительно большие углы подъема даже при низком коэффициенте сцепления колес с дорогой.
Тяговый расчет автомобиля. В.Н. Кравец. – Н. Новгород НГТУ 1983.
Тяговый расчет автомобиля. Составители: И.Н. Успенский В.Н. Кравец. – Горький: ГПИ им. А.А. Жданова 1983.
Расчет топливной экономичности автомобиля. Составители: В.Н. Кравец Б.В. Савинов. – Горький: ГПИ им. А.А. Жданова 1980.
Г.В. Мотовилен и др. Автомобильные материалы: Справочник. – М.: Транспорт 1989
Методические указания. Моделирование расчет анализ и оптимизация сетевых графиков. НГТУ 1988.
Справочник конструктора–машиностроителя.; т.2; В.И. Анурьев Москва «Машиностроение» 1978
Проектирование зубчатых конических и гипоидных передач. Инструкционные материалы фирмы Глисон. Под редакцией В.Ф. Родионова –М.:МАШГИЗ 1963.
Курсовое и дипломное проектирование колесных и гусеничных машин. Учебное пособиеНГТУ; Сост.: Л.В. Барахтанов А.А. Безруков В.В. Беляков и др. – Н. Новгород. 2000.
Богданович А.Б. и др. Художественное конструирование в машиностроении Киев 1976.
Родионов З.Ф. Фиттермак Б.М. Проектирование легковых автомобилей. - М.: Машиностроение 1980.
Высоцкий М.С. и др. Грузовые автомобили. - М.: Машиностроение
Спецвыпуск «За рулем». Полноприводные автомобили. №9 2008г. Варенов В. и др.
Вывод.doc
Для бездорожья лучше всего подойдет постоянный полный привод с полной блокировкой межосевого дифференциала и понижающей передачей. Неплох для таких целей подключаемый водителем полный привод. Повышают проходимость и самоблокирующиеся межколесные дифференциалы.
Любителям скоростной езды по автомагистралям предпочтительнее передний или постоянный полный привод без раздаточной коробки так как автомобили с такой трансмиссией в большинстве своем разрабатывались для этой цели.
Подключаемый автоматически полный привод вполне подойдет тем кто вынужден довольно часто съезжать на плохие дороги. Такие машины неплохо ведут себя на шоссе а проходимость по бездорожью у них выше чем у переднего и заднего приводов.
Многие потенциальные покупатели полноприводных автомобилей интересуются приводит ли большее количество "железа" к большим проблемам или значительному повышению расхода топлива. Мировая практика показывает что системы постоянного полного привода не приносят никаких специфических проблем. Вероятность отказа дополнительных приводных валов и шестерен не более вероятности того что восьмицилиндровый двигатель откажет только потому что в нем в два раза больше цилиндров чем в четырехцилиндровом. Это неплохая аналогия потому что при распределении тяги между четырьмя колесами нагрузки на трансмиссию меньше.
Те схемы которые основаны на использовании датчиков АБС для блокировки диффернциалов будут страдать от технических проблем не более чем любой другой автомобиль оснащенный АБС.
На самом деле недоверие к постоянному полному приводу вызвано использованием автомобилей с ручным подключением полного привода где делаются постоянные попытки упростить этот процесс при помощи различных автоматически блокирующихся ступиц иили разных дополнительных приспособлений. Системы постоянного полного привода проще по конструкции поскольку в нет необходимости в этих "упрощающих" приспособлениях и всех деталях связанных с ними.
Обвинения в том что автомобили с полным приводом расходуют много горючего справедливы только по отношению к системам с ручным подключением полного привода. Системы с постоянным полным приводом и центральным дифференциалом в отличие от систем с подключаемым полным приводом не приводят к чрезмерной деформации покрышек при повороте. Более того исследования Audi показали что потери на сопротивление качению у автомобиля с приводом на одну ось превосходят потери вызванные большим весом и инерцией автомобилей с постоянным полным приводом.
Использование в трансмиссии автомобиля ручного включения полного привода приводит к значительным трудностям в настройке подвески. Для автомобилей с управляемыми передними колесами передние колеса в повороте должны проходить большее расстояние чем задние. Из-за отсутствия центрального дифференциала задние колеса должны проскальзывать для выравнивания скоростей вращения и таким образом частично теряют сцепление с дорогой в повороте. При этом автомобиль получает излишнюю поворачиваемость что для среднестатистического водителя не является безопасным. Для корректировки этого передним колесам придается большой положительный угол развала. В результате передние колеса имеют меньшее пятно контакта с дорогой и соответственно меньшее сцепление в повороте. И все это только для того чтобы обеспечить автомобилю нейтральную поворачиваемость при включенном полном приводе. Когда полный привод отключен что в общем-то является более частой ситуацией автомобиль приобретает значительную недостаточную поворачиваемость поскольку тенденция к проскальзыванию задних колес в повороте уменьшается. АБС в режиме полного привода когда она бывает очень нужна тоже будет отключена.
Нет необходимости приводить дополнительные аргументы чтобы понять что подключаемый вручную полный привод имеет массу недостатков по сравнению с постоянным или автоматически подключаемым полным приводом которые способны динамически перераспределять тягу между осями в зависимости от того какая из них имеет худшее сцепление с дорогой. Системы постоянного и автоматически подключаемого полного привода полностью предсказуемы и могут быть настроены под каждый конкретный автомобиль для достижения максимального эффекта.
Средний потребитель обычно имеет тенденцию недооценивать необходимость высокой управляеости. Выражение "Я не собираюсь участвовать в гонках на моей машине" можно услышать довольно часто. Тем не менее если оценивать автомобиль как средство передвижения нельзя не оценить его управляемость. Автомобиль с хорошей управляемостью такой как перечисленные выше полноприводные модели снижает трудность прохождения поворотов делает этот процесс более предсказуемым. При этом среднестатистический водитель будет чувствовать себя более комфортабельно и уверенно будет меньше снижать скорость при прохождении поворотов что приведет к меньшим потерям крутящего момента и в свою очередь меньшим потерям энергии на очередное ускорение автомобиля. Другими словами такой автомобиль будет более энергетически эффективным.
Технико-экономическое обоснование.doc
К коммерческим автомобилям предъявляют самые жесткие требования. Как и любой другой грузовой транспорт они должны обладать достаточной грузоподъемностью отличаться высокой экономичностью и надежностью. В то же время городские машины должны быть компактными маневренными и иметь хорошую эргономику. Большинство современных машин данного класса представленных на российском рынке имеют схожие технические параметры: компактные размеры вместительный грузовой отсек бензиновые двигатели объемом 20 - 32 литра или дизельные моторы.
Разрабатываемый легкий коммерческий автомобиль согласно техническому заданию должен отвечать следующим требованиям:
Максимальная скорость — 120 кмч.
Масса автомобиля - 3500 кг.
Трансмиссия - подключаемый полный привод.
Для сравнения приведем некоторые технические характеристики аналогичных коммерческих автомобилей:
Масса в снаряженном состоянии
Мощность двигателя Ре кВт (л.с.)
(125) при 3700 обмин
3 (140) при 3500 обмин
Габаритная ширина мм
Габаритная высота не груженого автомобиля мм
Расстояние между колесными арками мм
Ширина грузового отсека мм
Расстояние от пола до потолка мм
Максимальная длина грузового отсека мм
Погрузочная высота мм
Из таблицы видно что из сравниваемых автомобилей MAXUS имеет наилучшие показатели по грузоподъемности объему багажного отсека и погрузочной высоте. Единственным его недостатком в данном случае будет тип привода неспособный обеспечить все требования предъявляемые к управляемости и проходимости в условиях нашего климата.
Компоновочная схема заднеприводных автомобилей достаточно проста надежна тщательно отработана и проверена на всем жизненном пути автомобиля. Плюс к этому задний привод еще и «работящий» - он позволяет без проблем буксировать прицеп.
Машины с задним приводом обладают наибольшей чувствительностью к управлению и довольно долго оставались на недосягаемой для переднеприводных конструкций высоте по поворачиваемости и информативности рулевого управления.
В теории автомобилей есть такое правило: Наличие тягового усилия на колесах (передних задних или на всех 4-х) уменьшает коэффициент сопротивления боковому уводу и коэффициент бокового трения что уменьшает величины действующих на них реакций боковых сил.
Согласно этому правилу автомобиль с задним приводом обладает излишней поворачиваемостью. При движении по дорогам с нормальным коэффициентом сцепления эта характеристика позволяет иметь большую маневренность однако когда дело доходит до движения по льду или снегу излишняя поворачиваемость становится причиной аварийноопасных заносов автомобиля.
Устранить «заносчивость» заднеприводных машин сегодня удалось благодаря созданию интеллектуальных электронных устройств — систем стабилизации движения которые исправляют ошибки водителя и помогают избежать потери контроля над управлением автомобилем активно вмешиваясь в работу тормозов и двигателя.
Преимущества заднего привода:
- прогнозируемое более естественное (соответствующее естественным рефлексам человека) поведение автомобиля на скользкой дороге. Если возникает опасная ситуация потери управления на дороге естественной реакцией человека является сброс газа - это стабилизирует курс заднеприводной машины;
-компоновка подкапотного пространства и разнесенные в пространстве
агрегаты удобнее для ремонта и ТО;
-развесовка автомобиля (двигатель впереди привод сзади). Кроме того
оптимально распределяется работа между передними и задними колесами:
передние поворачивают задние толкают машину вперед;
-при увеличении массы груза сцепление ведущих колес с покрытием только
нарастает и проходимость улучшается.
Недостатки заднего привода:
-меньший КПД трансмиссии из-за наличия карданной передачи;
-худшая управляемость и проходимость при некоторых режимах движения
(по сравнению с передним приводом) особенно по снегу и грязи.
- при резком старте ведущие задние колеса на скользком покрытии сразу буксуют.
-повышается расход топлива в зимних условиях.
Передние колеса являются одновременно ведущими и управляющими. В этом случае крутящий момент передается от коробки передач без дополнительных звеньев за счет полуосей. Водитель переднеприводного автомобиля чувствует себя на зимней скользкой дороге уверенно благодаря хорошей курсовой устойчивости и управляемости. Ведущие колеса переднеприводного автомобиля тянут за собой автомобиль и он менее склонен к заносам чем заднеприводной.
Но ведущие колеса переднеприводного автомобиля являются и направляющими то есть более перегруженными. Вследствие этого при движении в определенных условиях
ощущается нехватка сцепления ведущих колес с дорогой и проявляется главный недостаток переднеприводного автомобиля — плохая поворачиваемость и снос передней оси при движении с большой скоростью по скользкой дороге.
Занос задних колес переднеприводного автомобиля возникает крайне редко. На скользкой дороге чаще на спуске занос возникает иногда и при резком торможении и при переключении на низшую передачу в коробке передач.
Преимущества переднего привода:
-проще и безопаснее в управлении особенно он хорош для неопытного
водителя: прощает многие ошибки управления;
-высокий КПД трансмиссии за счет меньшей потери энергии при передаче
крутящего момента от двигателя к колесам;
-лучшая проходимость управляемость на заснеженных участках (по
сравнению с задним приводом).
Недостатки переднего привода:
-переход от полностью контролируемого движения к потере управления
происходит стремительнее чем у заднеприводного автомобиля и часто без
предварительных признаков. Водителям надо постоянно помнить об этом
свойстве переднеприводного автомобиля и управляя им всегда держать
рулевое колесо обеими руками;
-плотная компоновка моторного отсека;
-с увеличением загрузки ухудшается проходимость;
-самый нежный элемент трансмиссии - ШРУСы приводных валов.
Автоматически подключаемый полный привод
В нормальных дорожных условиях такая трансмиссия работает как передне- или заднеприводная. Это позволяет автомобилям сохранять «фамильные» черты свойственные тому или иному типу привода. А в экстремальных ситуациях когда одно или два ведущих колеса теряют сцепление с дорогой и начинают пробуксовывать крутящий момент перераспределяется и на колеса другой оси. Конструктивно это осуществляется таким образом. Вал который передает крутящий момент на ведущую ось через специальную муфту связан с колесами другой оси. Муфта обычно устанавливается вместо межосевого дифференциала или в непосредственной близости к заднему мосту. В нормальных условиях движения муфта разблокирована а в экстремальных ситуациях-блокирует и передает крутящий момент на колеса вспомогательной оси. В автомобилях с автоматически включаемым полным приводом применяются несколько типов муфт: вискомуфта электронно-управляемые фрикционные муфты гидравлические системы блокировки фрикционной муфты и так далее.
Таким образом подключаемый полный привод в варианте "4x2" обеспечивает комфортабельное движение по твердым дорогам (экономично тихо и "экономит" трансмиссию если отключить ступицы передних колес). Его жесткий вариант "4x4" обеспечивает максимальную проходимость. Создавая автомобиль с подключаемым полным приводом на базе переднего привода мы суммируем плюсы каждого из приводов и компенсируем их недостатки.
Для подтверждения приведем график сравнения углов начала пробуксовки ведущих колес передне- и полноприводного автомобилей.
Из диаграммы видно что полноприводный автомобиль практически в любых дорожных условиях способен преодолеть достаточно большие подъемы.
сборка для инженеров.doc
Государственное образовательное учреждение высшего профессионального образования
НИЖЕГОРОДСКИЙ ГОСУДАРСТВЕННЫЙ ТЕХНИЧЕСКИЙ УНИВЕРСИТЕТ им. Р.Е.Алексеева
ПОЯСНИТЕЛЬНАЯ ЗАПИСКА
к дипломному проекту
Сусленковой Веры Евгеньевны
(фамилия имя отчество)
Факультет: Автозаводская высшая школа управления и технологий
Кафедра: Автомобили и тракторы
Дата защиты « » 200__ г.
Кафедра «Автомобили и тракторы»
(подпись) (фамилия и. о.)
Полноприводный коммерческий автомобиль полной массой 35 тонны.
Компоновка. Угловой редуктор.
(наименование темы проекта)
По расчетно-конструкторской части
По экологичности и безопасности
По организационно-экономической части
По технологической части
по дипломному проектированию
студенту Сусленковой В. Е.
Тема проекта: Полноприводный коммерческий автомобиль полной массой 35 тонны. Компоновка. Угловой редуктор.
Срок сдачи студентом законченного проекта январь 2010 г.
Исходные данные к проекту: максимальная скорость ; коэффициент сопротивления качению ; максимальный коэффициент сопротивления дороги ; КПД трансмиссии ; коэффициент лобового сопротивления ; площадь миделева сечения ; 5-ти ступенчатая коробка передач.
Содержание расчетно-пояснительной записки (перечень вопросов подлежащих разработке):
1.Технико-экономическое обоснование
2.Конструкторско-исследовательская часть
2.2.Техническая характеристика коммерческого автомобиля
2.3.Обзор известных решений проблемы
2.4.Компоновочный расчет коммерческого автомобиля
2.5.Расчет углового редуктора
2.5.1.Определение параметров шестерен
2.5.2.Расчет зубьев шестерен на изгиб
2.5.3.Расчет зубьев шестерен на контактные напряжения
3.Технологическая часть
3.1.Размерный анализ механизма
3.2.Техпроцесс механической обработки детали
3.3.Техпроцесс сборки узла
4.Организационно-экономическая часть
5.Экологичность и безопасность
6.Научно-исследовательская часть
Список использованной литературы
Перечень графического (иллюстрационного) материала с точным указанием обязательных чертежей:
Графики тягового расчета лист А1;
Схема трансмиссии лист А1;
Компоновка автомобиля листа А1;
Главная передача и дифференциал в сборе с угловым редуктором лист А1;
Деталировка листа А1.
Консультации по проекту
Ф.И.О. преподавателя
конструкторская часть
экологичность и безопасность
организационно-экономическая часть
технологическая часть
Задание принял к исполнению
о дипломном проекте
( шифр и наименование )
В ОТЗЫВЕ НЕОБХОДИМО ОТМЕТИТЬ:
Объем и качество выполненой работы.
Положительные и отрицательные стороны проекта.
Характеристику работы студента над проектом (степень самостоятельности теоретическую подготовку умение решать практические вопросы и т.д.)
Общую оценку работы.
на дипломный проект студента
РЕЦЕНЗИЯ ДОЛЖНА ОБЯЗАТЕЛЬНО ВКЛЮЧАТЬ:
Заключение о степени соответствия выполненного дипломного проекта дипломному заданию.
Характеристику выполнения каждого раздела проекта степени использования дипломником последних достижений науки и техники и передовых методов работы.
Оценку качества выполнения графической части проекта и пояснительной записки к нему.
Перечень положительных качеств дипломного проекта и его основных недостатков (если последние имеют место).
Отзыв о проекте в целом и его общую оценку по пятибалльной системе.
к научно-исследовательской работе
г. Нижний Новгород ул. К.Минина24
СТУДЕНЧЕСКОЕ НАУЧНОЕ ОБЩЕСТВО
Факультет Автозаводская высшая школа управления и технологии
по научно-исследовательской работе
Анализ конструкций приводов ведущих колес современных автомобилей.
Расчет продольной устойчивости проектируемого автомобиля.
Анализ конструкций приводов ведущих колес современных автомобилей. Расчет продольной устойчивости проектируемого автомобиля.
Экологичность и безопасность проекта_мое.doc
Неправильные действия человека 60–70%;
Технические неисправности автомобиля и недостатки его конструкции 10–15%;
Плохое состояние дорог 20–30%.
Как видно из статистики основной причиной в происшествиях являются действия человека которые во многом зависят от условий труда водителя а так же состояние дорог. А долговечность дороги не в последнюю очередь зависит от того какое воздействие на нее оказывает передвигающийся по ней транспорт.
1 Экологичность проекта
Современные масштабы производства ДВС и их применение привели к тому что стало значительным их воздействие на окружающую среду. Условия существования жизни на нашей планете возможны в очень узких пределах изменения физических и химических характеристик окружающей среды. Размеры воздействия ДВС на окружающую среду таковы что концентрация химических веществ входящих в состав воздуха воды почвы становится опасной для жизни биологических существ и прежде всего для человека.
В настоящее время число поршневых ДВС в мире перевалило за миллиард. В это число кроме автомобильных входят судовые самолётные сельскохозяйственные дорожно-строительные стационарные и т. п. двигатели. Каждый из этих двигателей ежесекундно выбрасывает в атмосферу 10–100 литров отравленных газов.
Количество отравляемого воздуха всеми ДВС за одни только сутки составляет около 25 триллиона м3. И этот процесс идёт непрерывно. Природа частично устраняет эти последствия особенно лесной массив зелёные насаждения. В городах где вырубаются деревья под строительство различных сооружений эта проблема становится наиболее остро.
Это только одна из составляющих воздействия ДВС на окружающую среду. Кроме указанного выброса ДВС выбрасывают в атмосферу тепловую механическую (акустическое излучение) и лучистую энергию. Сюда следует добавить и экологическое воздействие оказываемое на природу при производстве и организации эксплуатации двигателей (добыча материалов отходы и т. д).
Поэтому знание материала по этой теме позволит современному инженеру более грамотно конструировать и эксплуатировать автомобильную технику.
Жидкие и твёрдые отходы являются обязательными негативными результатами эксплуатации автомобилей. Степень воздействия их на природу может быть уменьшена правильной организацией их переработки. Но при этом опять нужно учесть затраты энергии и выбросы в атмосферу при их переработке.
Тепловое воздействие ДВС на окружающую среду также является прямым и косвенным. Величина 1- э где э – эффективный кпд двигателя характеризует долю прямых тепловых выбросов. Вспомогательные потери складываются из работ трения деталей о детали гистерезисными потерями при качении шин трения шин о дорогу трением воздуха о поверхность автомобиля и т.д. Эти потери тоже повышают температуру атмосферы. Из этого следует что почти вся тепловая энергия сжигаемого в ДВС топлива выделяется в атмосферу. Нетрудно зная потребление различных видов топлив и их теплотворную способность определить выбросы теплоты от ДВС в глобальном масштабе. Это одна из причин глобального потепления на планете.
Электромагнитные излучения в основном создаются системами зажигания а также другими приборами. Это индукторный шум в генераторах стартерах различных индуктивностях и кроме того - прямое электромагнитное излучение создаваемое осветительными и нагревательными приборами и самим корпусом двигателя.
Вибрационное воздействие автомобиля на опорную поверхность и людей (эргономические показатели) рассматривается при изучении теории движения автомобиля.
Каждый ДВС при работе производит шум (акустическое излучение). Наличие большого количества автомобилей механизмов и машин с ДВС на улицах строительных площадках приводит к повышенному шуму мещает работе и отдыху людей. Шум вредно действует на органы слуха раздражает нервную систему снижает производительность труда.
При организации труда людей соприкасающихся с работающими машинами обязательно учитываются предельно допустимые нормы шума. Обычно нормируются внутренний и внешний шум машины. Общий уровень шума является одним из показателей качества машины применяемой технологии и культуры производства. Отдельные характеристики шума двигателя используются в качестве диагностических параметров.
Техногенное воздействие ДВС огромно. Сюда входят процессы разведки и добычи полезных ископаемых а также выбросы в окружающую среду вредных веществ в результате технологических процессов производства материалов и двигателей.
Из всего выше сказанного следует вывод что задача снижения токсичности отработавших газов является только частью общей задачи повышения экологической чистоты ДВС.
Снизить токсичность работы ДВС можно:
Совершенствованием рабочих процессов и смесеобразования то есть конструктивными мероприятиями;
Соблюдением правильных режимов эксплуатации двигателей то есть эксплуатационными мероприятиями.
Конструктивные и эксплуатационные мероприятия:
Повышение качества изготовления двигателей т. е. совершенствование технологических процессов: уменьшение технологических допусков на изготовление деталей формирующих камеры сгорания систему подачи топлива впускной тракт систему зажигания и др. В результате этого уменьшатся различия степени сжатия в отдельных цилиндрах будет лучшее приближение к оптимальным составам смеси и углам опережения зажигания и впрыска.
Совершенствование систем питания и зажигания. Применение электронных систем управления двигателем.
Нейтрализация отработавших газов.
Каталитические нейтрализаторы устанавливаемые в выпускной системе имеют специальные вещества (катализаторы) ускоряют протекание реакций окисления СО и СН а также восстанавливают NOx.
Каталитические нейтрализаторы применяемые для нейтрализации трёх компонентов (СО СН и NOx) называют трёхкомпонентными.
Установка фильтров и улавливателей сажи и твёрдых частиц в выпускных системах дизелей. Для этого применяются центрифуги электростатические улавливатели и другие различные фильтры. Для очистки фильтров от сажи применяются специальные горелки.
Для снижения концентрации NOx снижают максимальную температуру цикла. Для этого применяют:
рециркуляцию отработавших газов (10–15% по отношению к объёму свежего заряда;
водотопливную эмульсию;
впрыскивание воды во впускной трубопровод.
2 Безопасность проекта
2.1 Анализ опасных и вредных производственных факторов
Согласно ССБТ ГОСТ 12.0.003–74 «Опасные и вредные производственные факторы; классификация» существуют следующие основные вредные производственные факторы влияющие на работу водителя:
)движущиеся механизмы незащищенные подвижные элементы оборудования;
)повышенная запыленность и загазованность воздуха рабочей зоны;
)повышенный уровень шума на рабочем месте;
)повышенный уровень вибрации;
)повышенная яркость света;
)недостаточная освещенность рабочей зоны;
)повышенная или пониженная влажность воздуха;
)повышенная или пониженная температура воздуха рабочей зоны;
)опасный уровень напряжения в электрической цепи замыкание которой может произойти через тело человека;
) повышенная или пониженная подвижность воздуха.
Психофизиологические:
)физические перегрузки;
)нервно-психологические перегрузки.
2.2. Общие требования к безопасности конструкции автомобиля
Безопасность автомобиля – это совокупность его свойств и конструктивных особенностей характеризующих приспособленность к движению с минимальной вероятностью ДТП и сведения к минимуму возможных вредных последствий ДТП а так же безвредность его использования для людей и окружающей среды.
Активная безопасность автомобиля - это совокупность свойств и конструктивных особенностей автомобиля обеспечивающих снижение вероятности ДТП.
Свойства и конструктивные особенности определяющие активную безопасность:
эффективность системы освещения световой и звуковой сигнализации
эргономические свойства.
Пассивная безопасность автомобиля – это совокупность свойств и конструктивных особенностей автомобиля уменьшающих тяжесть последствий дорожно – транспортного проишествия.
Виды пассивной безопасности:
Внутренняя пассивная безопасность:
Конструктивные мероприятия:
создание жизненного пространства;
снижение инерционных нагрузок в процессе удара;
ограничение перемещений людей внутри автомобиля;
ограничение перемещений грузов и других предметов находящихся в автомобиле.
Жизненное пространство – это защитная зона вокруг человека сидящего в автомобиле внутрь которой не должны проникать предметы при аварии автомобиля.
ударно – прочностными свойствами кузова или кабины;
устранение возможности травмирования людей элементами интерьера.
Эргономические свойства:
Это свойства формируемые с целью повышения эффективности деятельности водителя сохранение здоровья водителя и пассажиров за счет создания конфигурации в которой учитываются характеристики пользователей.
Эргономические измерители подразделяются на:
) гигиенические свойства
) антропометрические свойства
) физиологические свойства
) психологические свойства
2.3 Микроклимат на рабочем месте
Факторы определяющие микроклимат в кабине нормируются ССБТ ОСТ 37.001.413–86 «Кабина. Рабочее место водителя».
Кабина должна быть оборудована системой принудительной вентиляции с подачей свежего воздуха в количестве не менее 30 м3ч на одного человека. Естественная вентиляция кабины в сочетании с ее теплоизоляцией должна обеспечивать на уровне головы водителя (при движении автомобиля со скоростью 30 кмч) перепад между внутренней и наружной температурой воздуха не более 3°С при наружной температуре +28°С и не более 5°С при наружной температуре +40°С. Подвижность воздуха в кабине при этом должна находиться в пределах 05 – 15 мс. Системы принудительной и естественной вентиляции должны обеспечивать возможность регулирования количества поступающего в кабину свежего воздуха.
Система отопления при движении автомобиля должна обеспечивать в зонах расположения ног пояса и головы водителя температуру не менее 15°С при наружной температуре –25°С. При этом температура в зоне головы водителя должна быть на 3–5°С ниже чем температура в зоне ног. Указанная температура должна устанавливаться не более чем за 30 мин. после начала движения автомобиля с прогретым двигателем. При наружной температуре до –40°С допускается снижение в указанных зонах до +10°С. Система отопления должна работать с притоком свежего воздуха и иметь устройства для регулировки производительности а так же для изменения количества теплого воздуха подаваемого в зону расположения ног и обогрева стекла ветрового окна.
Рабочее место водителя относится к категории постоянных. Поэтому оптимальные параметры по температуре влажности скорости движения воздуха должны поддерживаться во всем промежутке времени работы водителя. Данный режим поддерживается при помощи систем отопления и вентиляции. Отопление кабины осуществляется конвективным способом при принудительной прокачке воздуха либо электрическим вентилятором либо скоростным напором воздуха через радиатор отопителя использующего нагретую охлаждающую жидкость двигателя. Так же возможна установка и других отопителей салона независимого действия.
Циркуляция воздуха обеспечивается электрическим вентилятором и скоростным напором воздуха.
Пылезащищенность кабины обеспечивается ее достаточной герметичностью.
Для нормальной работы водителя необходимо обеспечить минимальную концентрацию вредных веществ в кабине согласно ГОСТ 12.1.005–88. ПДК вредных веществ в воздухе рабочей зоны должна быть не более:
Окись углерода–20 мгм3
Окислы азота в пересчете на NO2– 5 мгм3
Углеводороды– 300 мгм3
Для защиты водителя находящегося в кабине от вредных примесей в воздухе и пыли применяется герметизация кузова отделение моторного отсека от кабины водителя герметичной перегородкой предусматриваются резиновые уплотнения кабины ее стыков стен дверей. Еще больший эффект достигается при применении в машине фильтра поступающего в салон воздуха системы рециркуляции воздуха в салоне и системы кондиционирования. Для предотвращения попадания в кабину отработавших газов используется система выхлопа предусматривающая выброс этих газов в задней части машины.
2.4 Мероприятия по защите от вибрации
Вибрация возникает при движении гусеничной машины по неровностям дороги от неуравновешенности вращающихся частей движителя трансмиссии.
Согласно ССБТ ГОСТ 12.1.012–90 «Вибрационная безопасность. Общие требования» вибрация возникающая при движении автомобиля является транспортной и локальной. Транспортная вибрация возникает при движении транспортера по дороге передается через ходовую часть при движении по неровностям дороги и возникает при работе силовой установки. Локальная вибрация передается непосредственно водителю и пассажирам через органы управления например через рукоятку рычага управления коробкой передач.
Параметры вибрации нормируются по ГОСТ 12.1.012–90 «Вибрация. Общие требования». Нормируемые величины – логарифмический уровень виброускорений и среднеквадратичное виброускорение. Согласно ГОСТ предусматриваются следующие гигиенические нормы вибрации воздействующей на человека:
Направление по которому нормируется вибрация
Среднеквадратичное виброускорение мс2 .10-2; не более
Логарифмический уровень виброускорений дБ
Октавные полосы частот Гц
Основным средством борьбы с вибрацией является виброизоляция. Применение виброизоляторов – упругих элементов (пружины резиновые подушки гидроопоры магнитные подушки). Жесткость виброизоляторов выбирается в зависимости от частоты возмущающей силы т.е. чтобы частота собственных колебаний виброизоляторов была значительно меньше частоты возмущающей силы. Виброизоляция двигателя заключается в выборе размеров типа и количества упругих элементов. Для снижения локальной вибрации места контакта водителя с органами управления (рычагами педалями) покрыты виброизолирующими материалами.
Для снижения транспортных вибраций и выполнения норм плавности хода проводятся следующие мероприятия:
) крепление двигателя и силовых агрегатов (коробка передач бортовой редуктор карданная передача) которые могут стать источником вибраций кроме автомобиля осуществляется через резиновые виброизоляторы;
) тщательная балансировка вращающихся частей механизмов (карданной передачи сцепления);
) для снижения колебаний возникающих при движении по неровностям
дороги в проектируемом автомобиле применены амортизаторы со
специально подобранной скоростной характеристикой;
) сиденье водителя покрыто виброизолирующим материалом.
2.5. Мероприятия по защите от шума
Согласно классификации принятой ССБТ ГОСТ 12.1.003–83 «Шум. Общие требования безопасности» на рабочем месте водителя можно различать шум механический – от работающих механизмов: двигатель КПП главные – передачи и т.д. а также аэродинамический – всасывание воздуха выпуск отработавших газов и обтекание воздухом автомобиля при движении; аэродинамический – возникающий при всасывании воздуха двигателем выпуск отработавших газов и обтекание машины воздухом при ее движении.
Шумы подразделяются по характеру спектра: широкополосные обладающие непрерывным спектром шириной более одной октавы: по временной характеристике – постоянный шум уровень звука за 8–и часовой рабочий день изменяется во времени не более чем на 5Дб.
Уровни звука на рабочем месте водителя СН 2.2.42.1.8.562–96:
Уровень звукового давления дБ
Эквивалентные уровни звука на рабочем месте водителя и обслуживающего персонала 80 дБ(А).
Для снижения уровня звука применяют следующие конструктивные решения: двигатель оборудуют глушителем добиваются хорошей герметизации кабины применяют современные звукоизолирующие материалы.
Для снижения уровня шума в кабине используют различные капоты звукоизолирующие щиты из различных материалов. Проводят обработку кабины моторного отсека виброшумопоглощающими мастиками. Они способны заглушать шум на 10–20 дБ в зависимости от частоты колебаний. Также производят дополнительное капсулирование агрегатов проводят работы по улучшению герметичности кабины и силового агрегата путем уплотнения стыков панелей дверей перегородок резиновыми уплотнителями.
Так приведем некоторые звукоизолирующие способности листовой стали применяемой в конструкции машины:
Среднегеометрические частоты октавных полос Гц
Оценим уровень звуковой мощности двигателя на проектируемом транспорте. Для этого используем эмпирическую зависимость:
где : L – уровень звука в дБ(А);
n = 1000 – 4200 – число оборотов коленчатого вала обмин;
D = 0092; S=0094 – диаметр и рабочий ход поршня м;
z – коэффициент (при наличии клапанно–распределительного механизма z=l).
Результирующая формула принимает следующий вид:
L = 158 . lg (n . 0741) + 755
Уровень шума общий создаваемый двигателем с учетом звукоизоляции:
ΔL = 20–25 дБ шумоизоляция
В качестве шумоизолирующих материалов применяем листовую сталь и шумопоглощающий материал «шумоизол» которым изолируется моторный отсек. Звукоизолирующая способность стали толщиной 1мм равна 20дБ. А по ТУ 8714–055–00191–94 материал «шумоизол» снижает уровень шума на 15–20%.
Таким образом использование таких материалов очень эффективно снижает шум внутри салона и позволяет максимально приблизится к требованиям ССБТ ГОСТ 12.1.003–83 и международных правил. При этом следует отметить что на автомобиле присутствуют и другие источники шума поэтому дополнительно к перечисленным материалам применяют и другие. Это шумоизолирующие материалы: изотон липур полипропилен полидрев капровимор винилскожа листовая битумная мастика и комбинированные коврики типа «сэндвич».
2.6. Электробезопасность
На современных транспортных средствах применяется однопроводная схема электрооборудования с присоединением на «массу» (корпус) отрицательной клеммы аккумуляторной батареи. Напряжение в бортовой сети транспортера поддерживается в пределах 12В. Данное напряжение не является опасным для человека что исключает поражение электрическим током. Для предотвращения касания человеком токоведущих частей применяется надежная изоляция (сопротивление изоляции не менее 05МОм). Кроме этого проводка собирается в жгуты которые имеют дополнительную изоляцию. Проводка прокладывается в закрытых полостях тоннелях.
Для поддержания стабильного напряжения в бортовой сети применяется реле–регулятор РР–361. В электросети имеется блок плавких предохранителей обеспечивающих отключение цепей при превышении током номинальных значений.
2.7. Пожарная безопасность
Пожар в проектируемой гусеничной машине может возникнуть по следующим причинам:
)возгорание горюче–смазочных материалов от источников пламени лил тепла (искрение электропроводки попадание топлива на систему выпуска отработавших газов).
)самовозгорание промасленной ветоши.
Для предотвращения пожара согласно ГОСТ 12.1.004–91 «Пожарная безопасность. Общие требования» и быстрой его ликвидации проводятся следующие мероприятия:
в кабине находится огнетушитель ОУ–2;
сопротивление изоляции электропроводки не менее 05Мом;
вблизи с емкостями с ГСМ нет электропроводки и приборов электрооборудования;
герметизация соединений трубок системы питания двигателя с помощью применения хомутов и прокладок из бензостойкой резины;
глушитель выполняет роль пламегасителя;
заправка должна происходить закрытой струей;
промасленная ветошь не должна находиться вблизи приборов электрооборудования и в моторном отсеке.
В данном разделе определены общие требования к безопасности конструкции гусеничного транспортера дан анализ опасных и вредных производственных факторов касающихся работы водителя. Предусмотрены и проанализированы меры по обеспечению условий труда водителя разрабатываемого гусеничного транспортера.
Содержание.doc
Конструкторско-исследовательская часть
1.2.Исходные данные для выполнения расчета
1.3.Выполнение тягового расчета
1.4.Тягово-динамические характеристики автомобиля
1.5.Определение показателей топливной экономичности автомобиля
2. Техническая характеристика коммерческого автомобиля
3. Обзор известных решений проблемы
3.1. Стандартная схема
4. Компоновочный расчет коммерческого автомобиля
4.1. Оценка продольной и поперечной проходимости проектируемого автомобиля
4.2. Расчет положения центра масс проектируемого автомобиля
4.3. Определение геометрических параметров оптимальной посадки водителя транспортного средства
5. Расчет углового редуктор
5.1. Определение параметров шестерен
5.2. Определение элементов зубьев шестерен гипоидных передач по методике фирмы ГЛИСОН
5.3. Расчет шестерен на изгиб
5.4. Определение нагрузок на подшипниках
Технологическая часть
1.Разработка технических требований к качеству обработки детали
1.1. Анализ конструкции механизма
1.2. Разработка технических требований к точности обработки детали
1.3. Разработка технических требований к качеству обработки поверхностей детали
2. Проектирование технологического процесса механической обработки
2.1 Определение типа производства
2.2. Анализ технологичности детали
2.3. Выбор способа получения заготовки
2.4. Разработка технологического процесса механической обработки
3. Проектирование технологического процесса сборки
3.1. Классификация соединений сборочных единиц
3.2. Разработка процесса образования типовых сборочных соединений
3.3. Разработка последовательности сборки механизма и сборочной единицы
3.4. Проектирование основных сборочных операций
Организациогнно-экономическая часть
1 Обоснование применения механизма данного типа
2. Расчет увеличения стоимости проектируемого автомобиля
3. Расчет минимальной стоимости проектируемого автомобиля
4. Планирование подготовки производства углового редуктора
4.1 Сетевое планирование технологической подготовки производства
4.2. Расчет параметров сетевого графика
Экологичность и безопасность проекта
1 Экологичность проекта
2 Безопасность проекта
2.1 Анализ опасных и вредных производственных факторов
2.2. Общие требования к безопасности конструкции автомобиля
2.3 Микроклимат на рабочем месте
2.4 Мероприятия по защите от вибрации
2.5. Мероприятия по защите от шума
2.6. Электробезопасность
2.7. Пожарная безопасность
Научно-иследовательская часть
1. Устройство привода
1.1.Основные схемы полного привода
1.1.1. Подключаемый полный привод
1.1.2. Постоянный полный привод
1.1.3. Постоянный по-требованию полный привод
1.3.Раздаточная коробка
1.4.Узел отбора мощности
1.7.Карданный шарнир
2.Расчет продольной устойчивости автомобиля
2.1. Расчет продольной устойчивости переднеприводного автомобиля
2.2. Расчет продольной устойчивости полноприводного автомобиля
Сетевой график.dwg

Сетевой график технологической подготовки производства коробки передач в сборе с дифференциалом и угловым редуктором
Экономика.doc
Для повышения проходимости автомобиля в плохих дорожных условиях и увеличения угла подъема (угла начала пробуксовки ведущих колес) в конструкцию автомобиля были внесены некоторые изменения. А именно: модернизация коробки передач с установкой в ее корпусе углового редуктора установка заднего моста и карданной передачи. Все эти мероприятия направлены на преобразование переднеприводного коммерческого автомобиля в автомобиль с подключаемым полным приводом. Полный привод подключается автоматически благодаря установке в трансмиссию муфты HALDEX.
Подключаемый полный привод в варианте "4х2" обеспечивает комфортабельное движение по твердым дорогам (экономично тихо и "экономит" трансмиссию если отключить ступицы передних колес). Его жесткий вариант "4х4" обеспечивает максимальную проходимость. Создавая автомобиль с подключаемым полным приводом на базе переднего привода мы суммируем плюсы каждого из приводов и компенсируем их недостатки.
2. Расчет увеличения стоимости проектируемого автомобиля
Вычислим максимальную стоимость проектируемого автомобиля
Где - базовая стоимость автомобиля MAXUS с высокой крышей и длинной базой
3. Расчет минимальной стоимости проектируемого автомобиля
Рассчитаем минимальную стоимость проектируемого автомобиля.
Расчет стоимости дополнительных узлов и агрегатов представлен в таблице 4.1.
Средняя стоимость детали или узла руб
Количество на 1 машину
Крышка дифференциала
Колесо ведущее углового редуктора
Вал-шестерня углового редуктора
Крышка углового редуктора
Кольцо регулировочное
Прокладка крышки углового редуктора
Кольцо маслоотгонное
Дополнительные агрегаты в сборе
Установка заднего моста нового автомобиля производится вместо задней оси рыночная стоимость которой 9215 руб.
Получаем что стоимость проектируемого автомобиля будет получаться из рыночной стоимости уже существующего плюс стоимость новых узлов и агрегатов и минус стоимость задней оси:
Ц=640000+1021785-9215=7329635 руб.
Из полученных данных видно что ожидаемая цена нового автомобиля получилась значительно ниже ожидаемой максимальной цены. Данный расчет носит приблизительный характер так как цены на устанавливаемые на автомобиль узлы и агрегаты являются усредненными.
4. Планирование подготовки производства углового редуктора
4.1 Сетевое планирование технологической подготовки производства
Сетевое планирование управления - это метод основанный на графическом изображении определенного комплекса работ отражающих их логическую последовательность взаимосвязь и длительность.
Сетевые графики используются для контроля и текущего руководства работами выполнения технологической подготовки производства.
СПУ оперирует следующими терминами:
Работа – отражение связи между событиями во времени когда последующее событие может произойти лишь после совершения предыдущего через определенный промежуток времени.
Событие – момент завершения работы после чего наступает следующая работа.
Полный путь – путь от начального до завершающего события.
Критический путь – путь имеющий наибольшую протяженность.
Организация производства редуктора заднего моста требует тщательной подготовки начиная со стадии разработки узлов и заканчивая организацией производства.
Составим перечень событий которые необходимо совершить для организации производства. На основании перечня событий составим сетевой график организации производства учитывая логическую связь этих событий и очередность их совершения.
Таблица 4.4. Перечень работ необходимых для технологической подготовки производства и сборки коробки передач в сборе с дифференциалом и угловым редуктором
Продолжительность выполнения
Составление перечня комплектующих (подшипники и крепежные изделия)
Рассылка чертежей в цех механообработки деталей
Рассылка чертежей в цех сборки
Разработка технологического процесса изготовления литых заготовок
Разработка технологического процесса изготовления горячее-штампованных заготовок
Оформление и отправка заказа на поставку в цех сборки подшипников и крепежных деталей
Разработка технологического процесса механообработки литых деталей
Разработка технологического процесса механообработки горячее-штампованных деталей
Разработка технологического процесса сборки
Определение нормы расхода материала на литую корпусную заготовку
Определение нормы расхода материала на прочую литую заготовку
Определение нормы расхода материала на горячее-штампованную корпусную заготовку
Определение нормы расхода материала на прочую горячее-штампованную заготовку
Обеспечение цеха сборки подшипниками и крепежными изделиями
Проектирование специальной оснастки для механообработки литых деталей
Нормирование технологического процесса механообработки литых деталей
Проектирование специальной оснастки для механообработки горячее-штампованных деталей
Нормирование технологического процесса механообработки горячее-штампованных деталей
Оформление и отправка заказа на изготовление оборудование для сборки
Проектирование специальной оснастки для сборки коробки передач дифференциала и углового редуктора
Нормирование технологического процесса сборки
Проектирование специальной оснастки для изготовления литых корпусных заготовок
Нормирование технологического процесса изготовления литых корпусных заготовок
Проектирование специальной оснастки для изготовления прочих литых заготовок
Нормирование технологического процесса изготовления прочих литых заготовок
Проектирование специальной оснастки для изготовления горячее-штампованных корпусных заготовок
Нормирование технологического процесса изготовления горячее-штампованных корпусных заготовок
Проектирование специальной оснастки для изготовления прочих горячее-штампованных заготовок
Нормирование технологического процесса изготовления прочих горячее-штампованных заготовок
Изготовление специальной оснастки для механообработки литых деталей
Изготовление специальной оснастки для механообработки горячее-штампованных деталей
Поставка оборудования для сборки коробки передач дифференциала и углового редуктора в цех
Изготовление специальной оснастки для осуществления процесса сборки
Изготовление специальной оснастки для изготовления литых заготовок
Изготовление специальной оснастки для изготовления горячее-штампованных заготовок
Поставка специальной оснастки для механообработки литых деталей в цех механообработки
Поставка специальной оснастки для механообработки горячее-штампованных деталей в цех механообработки
Поставка специальной оснастки в литейный цех
Поставка специальной оснастки в кузнечный цех
Отладка и внедрение техпроцесса изготовления литых заготовок на пробной партии
Отладка и внедрение техпроцесса изготовления горячее-штампованных заготовок на пробной партии
Отладка технологических процессов механообработки литых деталей на пробной партии деталей
Отладка технологических процессов механообработки горячее-штампованных деталей на пробной партии деталей
Монтаж оборудования в цехе
Поставка специальной оснастки для сборки в цех сборки
Отладка и внедрение техпроцесса сборки коробки передач с дифференциалом и угловым редуктором
4.2. Расчет параметров сетевого графика
Расчет параметров сетевого графика имеет целью проанализировать насколько рационально выбрана последовательность работ и событий.
К основным параметрам сетевого графика относятся:
Lкр – критический путь – цепочка работ ведущая от начального события к завершающему и имеющая наибольшую протяженность.
Характеристика событий.
Трi – ранний срок совершения события i.
Tпi – поздний срок совершения события i.
Tпi = t(Lкр) – t[Lmax(i C)].
Ri – резерв времени события
Где Lmax – максимальный путь проходящий через событие
I – исходное событие.
С – завершающее событие.
Характеристики работ:
-раннее начало работы Трнij = Tpi
-позднее начало работы Tпнij = Tпj - ti
-раннее окончание работы Tроij = Tрi + tij
-позднее окончание работы Tпоij = Tпj
-полный резерв времени работы Rпij = Tпj - Tпi -tij
-полный резерв пути Rп(Li) = t(Lкр) – t(Li)
-свободный резерв времени работы Rcij = Tрj - Tрi -tij
Ожидаемое время выполнения работы Тож = Тро – Трн = Тпо - Тпн
Критический путь Lкр = 2+10+4+25+16+18=75
Результаты расчетов сведены в таблицу 4.5.
Таблица 4.5. Расчет параметров сетевого графика
Сетевой график технологической подготовки производства и сборки коробки передач в сборе с дифференциалом и угловым редуктором
Рекомендуемые чертежи
- 01.07.2014
- 25.10.2022