Дипломный проект (колледж) - Проект скраповых ножниц в условиях копрового цеха ЗАО СТАКС




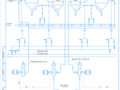
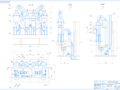
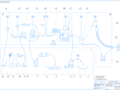
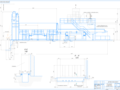
- Добавлен: 04.11.2022
- Размер: 16 MB
- Закачек: 0
Описание
Состав проекта
![]() |
![]() ![]() ![]() |
![]() |
![]() |
![]() |
![]() |
![]() |
![]() |
![]() |
![]() ![]() |
![]() |
![]() |
![]() |
![]() |
![]() |
![]() |
![]() |
![]() |
![]() |
![]() |
![]() |
![]() |
![]() |
![]() |
![]() |
![]() |
![]() |
![]() |
![]() |
![]() |
![]() |
![]() |
![]() |
![]() |
![]() |
![]() |
![]() |
![]() |
![]() |
![]() |
![]() |
![]() |
![]() |
![]() |
![]() |
![]() ![]() |
![]() ![]() |
![]() ![]() |
![]() |
![]() |
![]() |
![]() ![]() ![]() |
![]() ![]() ![]() |
![]() |
![]() ![]() ![]() |
![]() ![]() ![]() |
![]() |
![]() ![]() ![]() |
![]() ![]() ![]() |
![]() |
![]() ![]() ![]() |
![]() |
![]() ![]() ![]() |
Дополнительная информация
Diplom_Levchenko.doc
Технологическая часть21
1 Технологический процесс работы скраповых ножниц21
2 Контроль технологического процесса эксплуатации ножниц24
3 Технологическая операция «Включение и выключение
1 Конструкция функциональное описание скраповых
гидравлических ножниц32
2 Техническая характеристика скраповых гидравлических
3 Порядок ввода скраповых ножниц эксплуатацию45
4 Техническое обслуживание скраповых ножниц. Общие правила49
5 Интервалы технического обслуживания скраповых ножниц52
6 Порядок замены некоторых быстро изнашиваемых деталей56
7 Проверочный расчет лотка скраповых гидравлических ножниц65
8 Проверочный расчет цепи крепления лотка81
Охрана труда и промышленная безопасность83
1 Предохранительные устройства скраповых ножниц общее
их описание и порядок работы83
2 Действия обслуживающего персонала в экстремальных случаях инструкция85
3 Указания и предупреждения для обслуживающего персонала87
Экология и защита окружающей среды95
1 Описание факторов оказывающих загрязняющее действие
на окружающую среду при эксплуатации скраповых ножниц95
2 Классификация и эффективность работы пылеулавливающих
Экономическая часть114
1 Кадровая политика предприятия в современных условиях
рыночной экономики114
2 Определение численности промышленно – производствен -
3 Условия и факторы сокращения потерь рабочего времени121
Список использованных источников123
Завод представлял собой предприятие с полным металлургическим циклом. Первоначально - в 1872 году была задута доменная печь №1 рассчитанная для работы на антраците. В виду трудности ведения доменного производства на одном антраците печь была переделана для работы на смеси антрацита и кокса.
Первым начальником доменного цеха был известный металлург академик И. А. Павлов.
В 1895 году была пущена печь №2 и в 1902 году печь №3.
Мартеновский цех начал создаваться в 1892 году в 1893 году были построены печь №1 и №2. В 1896 - 1898 годах были построены еще 3 печи. В 1903 - 1904 годах была построена еще одна печь №6.
Прокатный цех был построен в 1872 году одновременно с доменным цехом. Вначале были установлены 2 стана: стан 500 и стан 230. Они прокатывали рельсы бандажи и частично пудлинговую болванку производство которой с 1875 - 1876 годах было организованно при прокатном цехе. Прокатный цех был расширен за счет установки станов 760 и 300. В 1887 году был установлен мелкосортный стан 230. В 1903 году произведено переоборудование станов заключавшееся в установке станов 240 и 400;
В настоящее время станы 230 300 500 демонтированы.
Одновременно с прокатным производством организованно костыльное производство выпускавшее рельсовые скрепления (накладки подкладки костыли болты и гайки). Производство рельсовых скреплений существовало до 1918 года затем было демонтировано а оборудование передано на один из заводов Донбасса.
Литейный цех открыт в 1872 году как вспомогательный цех для работ по обслуживанию открывающихся основных цехов. В 1885 году литейный цех значительно расширен и переоборудован в труболитейный а в 1893 - 1894 годах организован специальный труболитейный цех.
Механический цех был основан в 1876 году и обслуживал все основные цехи в своем составе имел токарный слесарный отделы котельную и кузнечную мастерскую.
Энергетический цех завода имел в своем составе: воздуходувки для воздуха в доменный цех котельную для подачи пара в цехи завода насосную и электростанцию.
Сулинский завод построен в расчете на использование железных руд и антрацита из месторождений вокруг завода и ближайших районов однако из-за малой мощности пластов завод отказался от использования местной руды и перешел на использование Криворожской руды уголь использовали из ближайших заводских шахт.
В1906 году в результате забастовки рабочих завод остановлен и было произведено массовое увольнение рабочих. Завод не работал около 1 года. В 1912 году завод перешел в ведение акционерного общества "Продамет".
В 1919 году завод был остановлен из-за нахождения завода в зоне военных действий в период гражданской войны.
Восстановительный период для Сулинского завода начался в 1926 - 1928 годах. Длительная консервация вызвана отсутствием у государства средств на восстановления всех предприятий Советской России.
По поручению рабочих завода в Москву выезжала делегация во главе с красным директором Янченко добиваться открытия завода.
Полностью завод восстановлен и начал работать с полной нагрузкой всех своих агрегатов в 1929 году.
С 1929 года на заводе работали: доменный цех (2 печи третья печь была остановлена на капитальный ремонт в 1911 году и после уже не была отремонтирована вследствие империалистической и гражданской войн). В 1935 году из-за нерентабельности доменный цех закрыт.
Мартеновский цех имел в своем составе 6 мартеновских печей.
В прокатном цехе начали работать 3 стана: 240 250 и 400 стан 760 был демонтирован в 1924 году и вывезен на один из заводов Донбасса. В 1933 году завод освоил выплавку и прокатку фосфористой стали для гаек ранее импортировавшуюся. В 1936 году произведена реконструкция стана 400 вместо морально и физически устаревших паровых машин установлены на обе линии мощные электродвигатели 1000 и 2000 л.с. На обжимной линии установлены: подъемный стол с задней стороны кантователь с передней стороны. В 1937 году также был реконструирован проволочный стан 250. На всех трех линиях вместо паровых машин установлены электродвигатели и дополнительно к имевшимся на данный момент еще 3 моталки.
Литейный цех был восстановлен полностью. Остальные цехи также пущены в работу полностью.
Завод до 1941 года выпускал:
полосу из мягкой стали;
полосовую сталь из низколегированной фосфористой стали;
полосу сельскохозяйственного профиля;
круг 16-50 мм квадрат 16-40 мм;
оконно - рамный профиль №35;
в 1940 году освоено производство профиля для оковки сапог.
Литейный цех выпускал трубы чугунные для водопроводов арматуру для промышленных печей изложницы.
Огнеупорный цех поставлял огнеупорный кирпич для футеровки топок паровозов.
Цех ширпотреба организованный в 1932 году выпускал из отходов производства прокатного цеха обручку строительные скобы мебельные пружины ромбические сетки для кроватей строительные железнодорожные костыли лодочные гвозди.
В сентябре 1941 года в связи с Великой Отечественной войной завод был остановлен основное оборудование было эвакуировано в город Нижние - Сергеи свердловской области. В период с сентября 1941 года по август 1942 года оставшееся оборудование работало на нужды обороны.
С августа 1942 года по февраль 1943 года город находился во временной оккупации.
В 1942 году по постановлению ГКО стан 400 был отправлен на Казахский металлургический завод в город Темир-Тау где он был установлен и на Сулинский завод не возвращен.
После освобождения города завод начал восстанавливаться. Первыми были пущены три мартеновских печи. В ноябре 1943 года в прокатном цехе начал работать стан 240. Начали работать механический цех литейный (за исключением труболитейного отдела который и не восстанавливался) железнодорожный огнеупорный. В 1946 году пущены 3 остальные мартеновские печи и стан 250. На полную мощность завод начал работать в 1947 году.
В 1948 - 1949 годах проведены работы по механизации трудоемких работ в литейном цехе: вместо работавших ранее кранов с ручным приводом установлены в двух пролетах электрические мостовые краны начали работать пневматические трамбовки на формовке и пневматические молотки на обработке что значительно облегчило труд работающих.
В 1948 - 1949 годах в мартеновском цехе на шихтовом дворе построена крановая эстакада и установлено 3 электрических мостовых крана в печном пролете установлен третий завалочный кран в литейном пролете установлен уборочный кран для ускорения разделки слитков - разделочный консольный кран механизирован подъем заслонок завалочных окон.
В прокатном цехе в 1948 - 1949 годах в пролете стана 250 установлен второй электрический мостовой кран для ускорения перевалок и ремонтов.
В вальцетокарной мастерской вместо крана с ручным приводом установлен мостовой электрический кран освободивший от тяжелого физического труда рабочих мастерской.
Установлен третий мостовой электрический кран на складе готовой продукции предназначенный вначале для разделки слитков а затем начиная с 1952 года используется для работы по погрузке готового металла. На посадке слитков в печь стана 240 электрифицирована ручная лебедка для погрузки слитков на тележку. Механизирован подъем заслонок на нагревательных печах прокатных станов.
В 1949 году было построено взамен устаревшего здание депо оснащенное новым оборудованием для ремонта вагонов и паровозов.
В копровом цехе погрузка шихты в мульды и выгрузка железнодорожных вагонов проводилась вручную в 1949 году построена двух пролетная скрапобаза для механизированной выгрузки из железнодорожных вагонов и погрузки в мульды железного лома.
На складе железнодорожного цеха для погрузки чугуна был в 1950 году установлен козловой электрический кран. В энергетическом цехе в 1948 - 1949 годах была построена химводоочистка для умягчения воды идущей в котлы.
В 1950 году на стане 240 освоено производство периодического профиля №16 и №18 для железобетона.
В 1951 году в огнеупорном цехе начато производство губчатого железа и железного порошка путем восстановления из железной руды и окалины.
Продолжая дальнейшее развитие завода в 1952 году в прокатном цехе на стане 240 взамен устаревшей физически и морально паровой машины установлен электрический двигатель мощностью 1500 кВт это позволило значительно улучшить работу прокатного стана.
В 1953 году в мартеновском цехе установлен 80-ти тонный разливочный кран в печном пролете установлены завалочные краны начат перевод печей на отопление мазутом. Эти мероприятия позволили увеличить вес плавки.
В прокатном цехе произведена частичная реконструкция нагревательных печей с переводом на отопление мазутом вместо отопления генераторным газом.
В 1954 - 1955 годах переведены все печи в мартеновском и прокатном цехах на отопление мазутом.
В 1956 - 1957 годах проведено в мартеновском цехе усиление здания печного пролета и построено здание для разделки слитков с установкой двух консольных кранов двух электрических кранов для механизированной погрузки слитков.
В прокатном цехе переведена на отопление природным газом нагревательная печь стана 250.
В 1956 году построен цех для производства промышленной сетки.
В 1958 году в связи с расформированием треста "Термоантрацит" заводу были переданы термоустановки №1 и №2.
Механизирована посадка слитков в печь стана 240 с помощью электротолкателей и рольгангов механизирована передача раскатов с передней стороны от первой обжимной ко второй обжимной клети и передача раскатов на чистовой линии с помощью обводных аппаратов.
Механизирована передача раската с задней стороны первой обжимной клети стана 240 с помощью установки подъемно - качающегося стола.
Механизирована кантовка слитков перед обжимной клетью №1 и уборка горячей обрези от обжимной клети №2 проволочного стана 250.
Реконструировано здание стана с улучшением аэрации и установлено два электромостовых крана.
Механизирована укладка в печи готового металла.
В литейном цехе построена обжиговая печь выплавка цветного литья переведена на газ механизированы погрузочные работы в обрубном отделе.
В 1962 году начато и в 1968 году закончено строительство крупнейшего в Союзе цеха по производству губчатого железа и железного порошка.
В 1963 году был запущен в эксплуатацию СПЦ.
В 1968 году введен в эксплуатацию электродный цех.
В 1981 году введен в действие цех металлокерамических изделий антифрикционного и конструкционного назначения на базе железного порошка (1-я очередь) 2-я очередь цеха пущена в эксплуатацию в 1988 году. Разработчик технологии - НИИ технологии машиностроения (город Ростов-на-Дону) генеральный проектировщик цеха - Гипросталь.
В механическом цехе организован участок по упрочнению деталей где производится полуавтоматическая наплавка прокатных валков наплавка плоских деталей вибродуговая наплавка поверхностная закалка ТВЧ хромирование деталей.
Кроме этого значительно обновлен станочный парк цеха.
В электродном цехе освоена технология производства универсальных низко токсичных высокопроизводительных электродов марок АНО - 3 АНО - 4 АНО - 6 установлен конвейер для упаковки электродов в потоке на всех прокалочных печах установлены сигнальные устройства с автоматическим отключением конвейеров печи при завале электродов.
В термоцехе №1 модернизирована печь по производству электродного термоантрацита освоена технология его производства на природном газе.
В железо-проволочном цехе осуществлен перевод волочильных станов на более прогрессивную технологию волочения проволоки в режиме гидравлического трения модернизированы волочильные станы АЗТМ ВС с шестикратного волочения на семикратное с помощью дополнительных блоков к станам введена в эксплуатацию станция нейтрализации.
В 1985 году введен в эксплуатацию крупнейший в стране цех по производству распыленного железного порошка. Проект цеха разработан Гипромезом (город Москва) и Гипросталью (город Харьков). В основу технологического процесса производства порошка положен метод распыления расплавленного металла водой высокого давления. Данный метод позволил получать порошки высокого качества заданного химического и гранулометрического состава с высокой прессуемостью. Проектная мощность цеха - 80 тыс. тонн в год.
В 1988 году в сталепроволочном цехе была пущена в эксплуатацию линия производства швейцарской фирмы "Манса Судаж АО" мощностью 7500 тонн сварочных электродов в год.
В 1990 - 1994 годах выполнен ряд работ по совершенствованию технологии и увеличению мощностей по переработке металлолома в копровом цехе. Установлены пакетировочный - пресс ПЛ - 450 усилием 450 те для пакетирования металлолома машина газокислородной резки МГР - 1 ножницы усилием 1000 т.с. для резки заготовки.
В сложных экономических условиях начиная с 1990 года заводу пришлось искать новые рынки сбыта и осваивать новые виды продукции.
В прокатном цехе освоены новые профилеразмеры проката сталь для армирования железобетонных конструкций диаметром 12 и 14 мм круг диаметром 12 14 16 18 20 28 мм квадрат 1414 мм катанка диаметром 10 мм.
В электродном цехе и на электродной линии СПЦ освоено производство новых марок сварочных электродов "Кубань - 1" и "Кубань - 2".
В цехе порошковых изделий организован и оборудован участок по производству строительных гвоздей шурупов и круглозвенных цепей.
В 1995 году в мартеновском цехе была введена в эксплуатацию МНЛЗГТ конструкции УкрНИИМета для отливки заготовки сечением 160 * 160 мм из сталей СтЗсп Ст5сп 35гс.
В 1995 году руководством завода было принято решение об организации ЭСПЦ на базе электросталеплавильного отделения ЦЖП №2. В этом же году там была построена и пущена в эксплуатацию трех ручьевая МНЛЗРТ изготовленная фирмами "Конкаст" и "Шлеманн" и приобретенная у фирмы "Иматра Стил" (Финляндия) производительностью 100000 тонн квадратной заготовки сечением 125 * 125 мм и 100 * 100 мм в год.
В 1997 году завершено строительство цеха обжига извести производительностью 90 т. тонн в год.
Программа модернизации электросталеплавильного производства на последние несколько лет включает в себя:
строительство агрегата внепечной обработки стали типа "печь - ковш" (АПК -30) фирмы "Фукс Системтехник Гмбх" (Германия) для повышения производительности технологической линии и качества металла;
реконструкция кислородного хозяйства завода со строительством кислородной станции большой производительности;
реконструкцию электросталеплавильных печей ДСП -25Н и замену их на ДСП-50;
модернизацию МНЛЗ увеличение числа ручьев.
Большинство пунктов данной программы на данный момент 06.2009 год выполнено. А именно:
- установлены электросталеплавильные печи ДСП-50;
- в дополнении к эксплуатируемой МНЛЗ монтируется пяти ручьевая МНЛЗ;
- в технологическом процессе производства стали активно используется печь-ковш;
- ведутся монтажные работы по сборке прокатного цеха.
Строительство прокатного цеха мощностью 250 т. тонн проката представляет собой установку нового универсального прокатного стана разработанного на основе новой гибкой модульной концепции специально для компактных мини - заводов типа М -250 для мелкосортного проката и катанки.
2 Электросталеплавильное производство этапы развития
Черная металлургия является базисной отраслью промышленности от уровня производства и качества черных металлов зависит развитие всех отраслей материального производства – промышленности строительства транспорта сельского хозяйства а также укрепление обороноспособности страны.
В настоящее время работа металлургических и машиностроительных заводов немыслима без использования печных агрегатов. Выплавка чугуна и стали нагрев металла перед прокаткой и ковкой нагрев металла для термической обработки – все эти операции выполняют в металлургических печах значение которых очень велико.
Основными направлениями технического прогресса электросталеплавильного производства являются увеличение единичной мощности дуговых электропечей совершенствование технологии и интенсификация технологического процесса механизация трудоемких процессом и автоматизация управления электросталеплавильным производством.
Новое поколение сверхмощных дуговых печей оборудуют водоохлаждаемыми устройствами для стен и сводов:
бросковыми машинами для загрузки шлакообразующих материалов;
раскислителей и ферросплавов;
газокислородными фурмами для подогрева скрапа и обезуглероживания жидкого металла в печи.
Для достижения требуемого высокого технического уровня работы дуговых печей предусматривается решение ряда неотложных проблем в частности снабжения печей высококачественными графитизированными электродами диаметром 550-700 мм с допустимой плотностью тока порядка 30-35 Асм2. Электропечные установки будут снабжаться новым электрооборудованием в том числе печными трансформаторами с первичным напряжением 220 кВ и минимальным индуктивным первичным напряжением. Вакуумная обработка в сочетании с электродуговой печью позволит успешно решать такие задачи сталеплавильного производства:
удаление водорода до уровня нефлокеночувствительности;
раскисление углеродом и другими элементами;
формирование в металле заданного типа неметаллических включений;
точное легирование стали на заданное содержание элементов с узкими пределами колебаний;
выравнивание температуры и состава металла во всем объеме ковша;
глубокое обезуглероживание обычных и легированных сталей.
Одним из перспективных направлений совершенствования технологии выплавки стали особенно в печах оснащенных мощными трансформаторами является выплавка стали скоростными методами:
сокращенным до 20-30 мин восстановительным периодом и минимальным индуктивным сопротивлением;
использованием высоковольтных печных выключателей с большим ресурсом работы;
применение специальных водоохлаждаемых кабелей сечением не менее 4000 мм2;
установкой оборудования для компенсации реактивной мощности.
Наряду с совершенствованием конструкции дуговых печей и использованием новых технических решений при строительстве крупных сталеплавильных цехов существенно изменяется технология выплавки и разливки высококачественной стали.
При такой технологии металл будет подвергаться интенсивной дефосфорации обезуглероживанию и нагреву до требуемой температуры.
Рисунок 1.2 – ДСП в работе
Важной в дальнейшем развитии технологического процесса выплавки стали в электродуговых печах является технология с частичной или полной заменой железного лома металлизованными окатышами при этом обеспечивается получение легированных сталей и сплавов более чистых по содержанию вредных примесей и цветных металлов.
Металлизованные окатыши – это продукт прямого получения железа из его оксидов в шахтных печах. Сырые окатыши получаются из смеси (в определенных соотношениях) концентрата железной руды (порошкообразной) измельченного твердого топлива и бентонита (глины) после чего они подвергаются восстановительному обжигу. Степень металлизации окатышей обычно составляет 90-95%. В нашей стране выплавка стали в 150-т. электродуговых печах с применением металлизованых окатышей осуществляется на Оскольском электрометаллургическом комбинате.
Автоматизация электросталеплавильного производства является важнейшим фактором технического прогресса. Комплексная автоматизация электросталеплавильного производства складывается из механизации трудоемких и тяжелых работ автоматизации управления тепловым и температурным режимом плавки автоматизация управления электрическим режимом плавки.
В настоящее время механизирована загрузка шихты внедрено электромагнитное перемешивание жидкого металла в ванне разрабатываются машины для очистки и заправки печи и полной механизации скачивания шлака применяются механизированные фурмы для подачи кислорода в ванну а также газокислородные горелки устройства для вдувания порошкообразных материалов. На многих электропечах используют установки непрерывного измерения температуры металла шлака футеровки печи квантометры для химического анализа металла и шлака экспресс - анализаторы для определения содержания углерода в металле и т. д.
Рисунок 1.3 – Новые электроды для ДСП
Все это позволило вплотную подойти к разработке систем автоматического управления технологическим процессом выплавки стали. Использование ЭВМ в электросталеплавильном производстве позволит осуществлять расчет шихты и расхода кислорода раскислителей легирующих и шлакообразующих материалов. Кроме того общецеховая ЭВМ будет выдавать и корректировать задания системы управления каждой печи контролировать основные технико-экономические показатели.
Рисунок 1.4 - Шлеппер2 Технологическая часть
1 Технологический процесс работы скраповых ножниц
1.1 Общее описание скраповых ножниц
Гидравлические скраповые ножницы предназначены для обработки металлического лома (скрапа). Металлические предметы прессуются при помощи прессовальной крышки бокового нажима и при необходимости ползуна в двух или трех измерениях а затем режутся на куски или ломаются.
При помощи ножниц ЕС 1240-15 можно:
прессовать и резать металлолом;
прессовать крупногабаритные части в штранг и затем резать;
разрезать штранги и профили;
пакетировать легкий лом;
дробить литье и кокили.
При помощи ножниц ЕС 1240-15 можно размельчать следующие материалы:
сборный и смешанный скрап;
ваграночный исходный материал;
кромкообрезной скрап;
арматурный и конструкционный скрап.
В ножницах ЕС 1240-15 можно размельчать куски прочностью 440 Нмм2 не превышающие следующие поперечные сечения:
Таблица 2.1 – Перечень исходных шихтовых материалов для скраповых ножниц
Максимальные размеры
Круглая форма материала
Прямоугольная форма материала
х 1400 или 6 х 1600 мм
1.2 Автоматический режим работы
Активированный автоматический режим сигнализируется зеленой лампой которая установлена снаружи на операторской кабине. При возникновении сбоя зажигается оранжевая лампа.
Рисунок 2.1 – исходная панель автоматического режима
При помощи кнопки справа внизу вызовите меню «Режимы эксплуатации». В этом меню Вы можете выбрать следующие установки:
Автоматические программы;
Настройки «Ползун» имеют значение только в автоматическом режиме:
«Без подпрессовки»: Процесс резки начинается сразу после зажатия штранга боковым нажимом и прессовальной крышкой;
«С подпрессовкой»: После зажатия штранга боковым нажимом и прессовальной крышкой ползун дополнительно прессует штранг в продольном направлении. Только после этого начинается процесс резки;
Для опции «Трамбовка» можно выбрать с каким усилием трамбовка подается вниз:
«Полное усилие»: Трамбовка опускается с большим усилием для прессования материала или размельчения литья;
«Сокращенное усилие»: Трамбовка опускается с достаточным усилием для прижатия материала перед резкой;
Опция «Длина резки» позволяет настроить длину отрезков штранга. Вы можете задать четыре значения длины отрезков которые часто используются в Ваших программах а затем выбирать необходимую длину резки.
Если требуется ввод какого-либо значения после прикасания к кнопке открывается окно похожее на цифровой блок клавиатуры компьютера позволяющее вводить цифры:
EscОтмена ввода значение не принимается системой;
EnterВведенное значение активируется в системе;
Стирание знака слева от курсора.
Опция «Выбор двигателей» позволяет отключать отдельные приводные двигатели. Как правило установка работает на всех приводных двигателях. Отключение двигателя может потребоваться если двигатель неисправен. В этом случае возможно что установка не будет работать в автоматическом режиме; разгрузите ее на ручном управлении.
Если при проведении технического обслуживания необходимо переместить агрегаты установки в другое положение в этом случае следует выбрать только один двигатель. В этом случае ножницы работают медленнее и точнее.
1.3 Выбор автоматического режима через систему управления
- Пуск автоматического режима
Нажмите световую кнопку «АВТОМАТИКА ВКЛ».
Кнопка зажигается и установка начинает выполнять запрограммированную Вами операцию.
Для повторного запуска операции снова нажмите кнопку «АВТОМА-ТИКА ВКЛ».
- Отменапрерывание автоматического режима.
По окончании автоматического процесса резки установка автоматически возвращается в режим ручного управления.
Чтобы прервать автоматический режим эксплуатации нажмите кнопку «АВТОМАТИКА ВЫКЛ». Сигнальная лампа гаснет. Все компоненты установки остаются в своем текущем положении.
2 Контроль технологического процесса эксплуатации ножниц
При помощи клавиши «Статус машины» можно получить информацию о положении цилиндров. Положение трамбовки резака ползуна прессовальной крышки и бокового нажима контролируется концевым выключателем или системой замера перемещений интегрированной в цилиндрах.
Рисунок 2.2 – Меню – статус машины
В меню «Статус машины» представлены положения цилиндров. При помощи клавиши «Статус машины» можно также получить информацию о коммутационном состоянии гидравлических клапанов (актуаторов) и точках переключения датчиков давления.
В меню «Статус машины» представлены также коммутационные состояния клапанов и реле давления.
Рисунок 2.3 – Последующее меню – статус машины
2.2 Тестирование насосов
Коснитесь справа внизу кнопки «Другие меню» чтобы вызвать перечень меню.
Коснитесь в разделе «Программы тестирования» опции «Тестирование насосов» чтобы открыть меню тестирования насосов.
Рисунок 2.4 – Меню контроля оборудования насосов
В меню «Тестирование насосов» можно выбрать для тестирования один гидравлический насос или провести автоматическое тестирование всех гидравлических насосов.
2.3 Тестирование насосов в ручном режиме
Выберите в нижней части окна «Единичный тест» привод и диапазон давления для тестирования.
Проводится тестирование.
2.4 Автоматическое тестирование насосов
В автоматическом режиме тестирования насосов проводится последовательное тестирование всех имеющихся приводов во всех диапазонах давления. При этом должны быть включены все приводы; если установка на данный момент работает с частью приводов Вам следует открыть меню «Режим эксплуатации» и изменить установку по приводам.
В таблице приводятся результаты последнего автоматического тестирования насосов.
Убедитесь в том что все приводы включены а затем запустите тестирование насосов коснувшись кнопки «Пуск».
Теперь установка проводит последовательное тестирование всех насосов и заносит новые результаты в таблицу.
Вы можете остановить текущее тестирование насосов коснувшись кнопки «Стоп».
2.5 Самотестирование
По истечении определенного числа часов эксплуатации запускается самотестирование оборудования. Для этого следует полностью опорожнить установку.
Рисунок 2.5 – Меню автоматического тестирования машины
Коснитесь кнопки «Пуск теста» чтобы запустить тестирование.
Если самотестирование игнорируется при помощи кнопки «Завершить» самотестирование запускается снова через 10 часов эксплуатации.
Тестирование можно в любой момент прервать кнопкой «СТОП».
Самотестирование может активироваться оператором.
Коснитесь в разделе «Программы тестирования» опции «Самотестирование».
Рисунок 2.6 – Подменю автоматического тестирования машины
2.6 Единичный контроль цилиндров
Коснитесь в меню «Программы тестирования» соответствующей кнопки «Контроль цилиндра ххх» чтобы вызвать меню контроля соответствующего цилиндра.
Рисунок 2.7 – Меню контроля цилиндра с ножом
По отдельности можно проверять цилиндры резаков трамбовки бокового нажима крышки и ползуна.
Коснитесь соответствующей кнопки чтобы запустить тестирование цилиндра.
3 Технологическая операция «Включение и выключение установки»
3.1 Включение установки
Разблокируйте основной выключатель на распределительном шкафу и поверните выключатель через «0» в положение «1». На пульте управления зажигается сигнальная лампа «Основной выключатель ВКЛ».
Поверните ключевой выключатель «Установка» на «1».
Подождите пока на дисплее появится меню «Статус датчиков».
Не касайтесь дисплея пока не появится «Статус датчиков»!
Рисунок 2.8 – Меню включения ножниц
Значения по отдельным сенсорам еще не считаны из установки и поэтому пока не отображены на дисплее.
Нажмите светящуюся кнопку «Система управления ВКЛ».
Запускаются циркуляционный насос и вентилятор активируется зажим резака.
Проводится опрос сенсоров и их значения появляются на дисплее.
Коснитесь кнопки «Режимы эксплуатации» справа внизу на дисплее чтобы открыть меню режимов эксплуатации.
Активируйте все три двигателя коснувшись кнопки «Да» справа под опцией «Выбор двигателей» для всех трех двигателей.
Выберите в опции «Автоматические программы» необходимую программу касанием соответствующей программы.
При помощи световой кнопки «Двигатели ВКЛ» включите двигатели.
В процессе запуска предварительно выбранных двигателей световая кнопка мигает. После запуска всех двигателей кнопка начинается светиться постоянно.
Рисунок 2.9 – Меню включения ножниц
считаны показания датчиков
Как только масло достигнет рабочей температуры установка готова к эксплуатации. Если масло еще слишком холодное следует разогреть его до температуры в соответствии с описанием в разделе технической документации «Подогрев масла».
3.2 Выключение установки
3.2.1 Общие действия
Существуют две возможности выключения установки:
Перед работами по техническому обслуживанию установка должна выключаться полностью.
Отключение в режиме ожидания который предотвращает остывание масла ниже 1 0С
Отключение в режиме ожидания используется при холодной погоде чтобы обеспечить быстрое включение установки на следующее утро.
3.2.2 Порядок операций
Перед выключением установки следует выполнить следующие действия:
Опорожните установку до полного выхода материала.
Отведите трамбовку и ножевые салазки вниз.
Отведите ползун и боковой нажим назад.
Полностью откройте прессовальную крышку.
3.2.3 Возникновение опасностей в процессе выключения
Опасность для жизни и угроза значительного повреждения установки при несанкционированном включении!
Защитите операторскую кабину и машинное отделение от доступа посторонних лиц. Вытаскивайте после выключения установки все ключи и храните их в недоступном для посторонних лиц месте. Запирайте операторскую кабину машинное отделение и доступы к установке.
3.2.4 Полное отключение
Нажмите кнопку «Двигатели ВЫКЛ».
Гидравлические насосы отключаются.
Поверните ключевой выключатель «Установка» на «0».
Выключите основной выключатель.
Сигнальная лампа «Основной выключатель ВКЛ» гаснет.
3.2.5 Отключение в режиме ожидания
Нажмите кнопку «Двигатели ВЫКЛ». Гидравлические насосы отключаются.
Оставьте систему управления и основной выключатель включенными и поверните ключевой выключатель «Подогрев масла» на «1».
Теперь система управления заблокирована; ввод установки в эксплуатацию невозможен. При охлаждении масла насосы включаются для его подогрева.
Чтобы снова ввести установку в эксплуатацию поверните ключевой выключатель «Нагрев масла» на «0».
1 Конструкция функциональное описание скраповых гидравлических ножниц
1.1 Конструкция установки
Рисунок 3.1 - гидравлические скраповые ножницы ЕС 1240-15
ЕС 1240-15 состоят из описанных ниже основных групп. Цифры в квадратных скобках относятся к рисунку 3.1
1.1.1 Прессовальная станина [3]
В прессовальной станине разрезаемый материал предварительно прессуется в двух или трех измерениях. Для этого используются боковой уплотнитель (боковой пресс) прессовальная крышка и загрузочный ползун. Прессовальная станина облицована сменными рабочими панелями на болтовых креплениях.
1.1.2 Стойка скраповых ножниц [1]
Стойка скраповых ножниц представляет собой тяжелую сварную конструкцию из стальных панелей с держателем для нижнего резака призменными направляющими для ножевых салазок и трамбовкой.
Направляющие планки для ножевых салазок регулируются снаружи и могут заменяться.
На ножевых салазках находятся верхний резак дробильная балка а также опускной стол который поддерживает материал в процессе подачи.
Ножи изготовлены из высокопрочного материала; резаки имеют по четыре режущих кромки и могут использоваться во всех положениях. Конструкция верхнего резака и нижнего резака идентична; они являются взаимозаменяемыми.
Трамбовка предназначена для уплотнения и удержания разрезаемого материала. Таким образом предотвращается отдача материала в процессе резки. Кроме того трамбовка может также применяться для ломки и размельчения литья.
1.1.3 Лоток (спускной желоб) [15]
Через лоток разрезанный лом выгружается из установки или передается на виброжелоб или ленточный транспортер.
1.1.4 Автоматическая смазка
Следующие направляющие и подшипники смазываются автоматически:
соединительные накладки между торсионным валом и боковым ползуном.
1.1.5 Гидравлический привод [7]
Необходимое для предварительного сжатия прессования трамбовки и резки усилие обеспечивается гидравлическим приводом. Гидравлический агрегат расположен в маслосборнике и состоит из следующих компонентов:
бак масла гидросистемы с радиатором и фильтрами
основной привод и вспомогательный привод.
Контроль рабочего давления делает возможным точное управление скраповыми ножницами.
Если в процессе контроля температуры масла и объема масла обнаруживается что температура масла слишком высока или уровень масла слишком низкий на панели управления появляется предупреждение. Если это предупреждение остается без внимания оператора происходит автоматическое отключение скраповых ножниц.
1.1.6 Гидравлический зажим резака [11]
Гидравлический зажим резака позволяет закрепить болты крепления резака на верхнем и нижнем резаке. Таким образом предотвращается неконтролируемое отсоединение болтов.
1.1.7 Электрооборудование [6]
Электрооборудование состоит из следующих компонентов:
распределительный шкаф с запираемым основным выключателем
электронная система управления SI- MATIC S7-300 для всех моторов и агрегатов а также
пульт управления с консолью управления и жидкокристаллическим дисплеем.
1.1.8 Операторская кабина [8]
Операторская кабина имеет двухконтурную конструкцию со звуко - и теплоизоляцией. Кабина остеклена с трех сторон безосколочным стеклом и оснащена запираемой двухстеночной дверью с окном. Плоская крыша оснащена вентиляционным отверстием.
К электрооборудованию операторской кабины относится однополюсный предохранитель и система отключения для наружного монтажа включая необходимые выключатели.
Операторская кабина поставляется с платформой высотой 1 м несущей сварной конструкции и посадочной лестницей для установки на насосную станцию.
1.1.9 Пульт управления [8]
Скраповые ножницы управляются через пульт управления расположенный в операторской кабине. Обработка команд управления проводится в автоматической системе управления (АСУ). АСУ передает команды через выходные модули на клапаны гидравлической системы.
Сам процесс резки происходит автоматически. Существует возможность управления установкой при помощи перекидных выключателей и тумблеров в ручном режиме; эти возможности используются в первую очередь для рабочих операций по предварительному сжатию материала.
На дисплее представлена вся важная информация по эксплуатационному состоянию.
Рисунок 3.2 - пульт управления ЕС 1240-15
В левой и нижней части пульта управления находятся выключатель ВКЛ ВЫКЛ дополнительные выключатели кнопки и контрольные лампы для некоторых основных функций а также аварийная кнопка.
Выше находится сенсорная панель через которую выбираются и обрабатываются все основные функции управления и настройки.
Вызов отдельных программ пунктов меню и настроек осуществляется касанием нужной функции.
-Управление через меню
Функции обслуживания ЕС 1240-15 представлены в меню. Из основного меню Вы выбираете отдельные субменю для выбора программ для запроса состояния тестирования насосов и т. д.
Рисунок 3.3 - обзор режимов эксплуатации
Меню или программы выбираются прикасанием. Если программа или настройка активирована кнопка изображается зеленым цветом.
EscОтмена ввода значение не принимается системой.
EnterВведенное значение активируется в системе.
- Сообщения о сбоях и кнопка «Помощь»
При возникновении сбоя в верхней части дисплея появляется сообщение о сбое. По сообщениям не содержащим разъяснительной информации можно получить дополнительную информацию нажав кнопку «Помощь» на дисплее слева внизу.
1.2 Функциональное описание скраповых гидравлических ножниц
Рисунок 3.4 - функциональная схема ЕС 1240-15
1.2.1 Загрузка и уплотнение
На первом этапе лом (скрап) загружается экскаватором или краном в прессовальную станину.
Рисунок 3.5 - крышка уплотняет материал
На втором этапе лом уплотняется боковым нажимом.
Рисунок 3.6 - боковой нажим уплотняет материал
Рисунок 3.7 – загрузка ножниц
При этом боковой уплотнитель подается либо настолько чтобы могла быть закрыта крышка либо подается с избыточным ходом иными словами уплотнитель проходит дальше и должен вернуться обратно до начала уплотнения материала крышкой и ее закрытия.
Работа бокового нажима с избыточным ходом зависит от выбора программы.
На третьем этапе лом уплотняется крышкой. При этом крышка подается либо настолько чтобы она прилегала к боковому нажиму и соответственно закрывала установку либо подается с избыточным ходом.
Рисунок 3.8 – установка закрыта ползун уплотняет материал
Работа крышки с избыточным ходом зависит от выбора программы.
Если боковой нажим и крышка работают без избыточного хода после этого установка считается закрытой.
Если боковой нажим и крышка работают с избыточным ходом крышка отводится назад настолько чтобы боковой нажим встал на свое место иными словами боковой нажим перемещается в положение в котором установка считается закрытой.
Затем крышка закрывает установку.
На четвертом этапе лом уплотняется ползуном сзади. Активация ползуна и настройка усилия ползуна зависят от выбранных программ.
1.2.2 Резание и выброс
- Дробление профилей
Рисунок 3.9 – резание и выброс профилей
Процесс резания и выталкивания зависит от выбранной программы.
При резке профилей трамбовка и верхний резак двигаются одновременно. Трамбовка и резак поднимаются только на высоту которая обусловлена толщиной материала (относительный ход). Когда трамбовка и верхний резак находятся сверху ползун смещает материал вперед. При движении вниз трамбовка удерживает материал а верхний резак разрезает материал.
При дроблении литья верхний резак не используется и остается наверху.
Рисунок 3.10 –дробление литья
Когда трамбовка находится сверху ползун смещает материал вперед. Трамбовка с полной силой подается вниз на литье и разбивает его. Опускной стол находится сверху и задерживает мелкие части материала.
- Легкий и тяжелый смешанный скрап
Рисунок 3.11 – Резание и выброс легкого
и тяжелого смешанного скрапа
При резке смешанного скрапа трамбовка и верхний резак опускаются одновременно. Трамбовка дополнительно уплотняет материал сверху а верхний резак разрезает материал. Затем ползун смещает материал дальше. При этом перемещение ползуна немного меньше ширины трамбовки.
- Легкий и тяжелый ваграночный скрап
При резке ваграночного скрапа сначала опускается трамбовка чтобы прижать материал как правило короткой длины. Только после этого опускается верхний резак и разрезает материал. Затем ползун смещает материал дальше.
Рисунок 3.12 – резание и выброс легкого
и тяжелого ваграночного скрапа
Опускной стол находится сверху и задерживает мелкие части материала.
- Пакетирование и трамбовка
При пакетировании верхний резак не используется и остается наверху. При пакетировании трамбовка сначала остается внизу а ползун уплотняет лом в прессовальной станине к трамбовке. Затем трамбовка поднимается а пакет скрапа выталкивается ползуном.
Рисунок 3.13 - пакетирование и трамбовка.
При пакетировании и трамбовке верхний резак не используется и остается наверху. При пакетировании и трамбовке трамбовка сначала остается внизу а ползун уплотняет лом в прессовальной станине к трамбовке. Затем трамбовка поднимается а пакет продвигается вперед. Трамбовка с полной силой подается вниз и дополнительно утрамбовывает материал сверху. При этом перемещение ползуна немного меньше ширины трамбовки. Опускной стол остается внизу и не используется.
2 Техническая характеристика скраповых гидравлических ножниц
2.1 Сводная характеристика
Таблица 3.1 - техническая характеристика установки
ЕС 1240-15 TD 100-25-23
Габариты (Д х Ш х В)
с корпусом и операторской кабиной
прибл. 28000 х 10000 х 8050 мм.
Продолжение таблицы 3.1
Рабочие характеристики
Стойка скраповых ножниц с ножевыми салазками
Максимальное усилие резания
Отверстие резака:макс. ширина
Автоматическая смазка
Число смазочных точек
Прессовальная станина
Длина прессовальной станины
Загрузочное отверстие (Ш х В)
Ширина загрузочного ползуна
Высота панели задвижки
Высота верхней кромки крышки
Высота верхней кромки станины
Усилие прессования бокового пресса
Усилие прессования крышки (центр)
Усилие прессования загрузочного ползуна
Внешние габариты (Д х Ш х В)
Высота в свету внутри
Люминесцентная лампа 58 Вт
Контакторное управляющее напряжение
Клапанное управляющее напряжение
Управляющее напряжение АСУ ТП
Кратковременная перегрузка
Гидравлический привод
Число шестеренных насосов с внутренними зубьями
Число регулируемых аксильно-поршневых насосов ВД
Потребная мощность на насосный агрегат (2 насоса)
Максимальное рабочее давление
Мощность привода:Основной привод
Вентилятор к радиатору
Масло (не входит в объем поставки)
Гидравлический зажим резака
2.2 Шумовая нагрузка
Шумовая нагрузка на оператора оценена по классу А эквивалентные продолжительные уровни шума на рабочих местах обслуживающего персонала.
Замеры проводились в соответствующих условиях при эксплуатации на номинальной нагрузке. Замеры проведены на аналогичной машинеустановке.
2.2.1 Методика измерения
Для замера уровня шума использовался калиброванный прецизионный шумометр настроенный на частотный класс «А» и хронирование «FAST». Уровень шума «Lрмакс» и «Lрмин» а также результирующийся из этих значений и оцененный по классу А энергоэквивалентный продолжительный уровень звука LрАd был считан и зарегистрирован непосредственно с шумометра.
Точка замера является рабочим местом оператора в операторской кабине. Воздействие других посторонних источников шума не учитывалось.
Таблица 3.2 - Значения уровня шума для определенного рабочего места в операторской кабине
Эквивалентный продолжительный уровень звука LрАd [дБ(А)]
3 Порядок ввода скраповых ножниц эксплуатацию
3.1 Состояние установки при приемке
Перед приемкой установка проходит обкатку и пробную эксплуатацию.
Установка находится в исходном положении в эксплуатационной готовности. Она передается в чистом состоянии и без загруженного материала.
Перед вводом в эксплуатацию гидравлическая система контролируется компанией Metso Lindemann или авторизованным экспертом. Система герметична. Цилиндры подлежат регулярной проверке на наличие масла на уплотнениях поршневого штока. Избыток снятого масла удаляется.
Система управления запрограммирована и проверена. Элементы пульта управления находятся в исходном положении. Индикаторы работают без сбоев.
В первый месяц эксплуатации техническое обслуживание проводится с сокращенными интервалами смотри пункт 3.4 пояснительной записки данного дипломного проекта;
3.2 Включение установки
Перед включением установки убедитесь в том что работы по ремонту и техническому обслуживанию не проводятся а в опасной зоне установки и в машинном отделении никто не находится. Убедитесь в том что платформа для замены резаков демонтирована и установлена отбойная стенка. Использование платформы для замены резаков во время работы установки категорически запрещается.
Во время работы установки доступ в опасную зону запрещен. Немедленно остановите установку или выключите (аварийный останов) если кто-нибудь оказывается в опасной зоне.
Рисунок 3.14 – общий вид панели управления
Порядок действий при включении:
- разблокируйте основной выключатель на распределительном шкафу и поверните выключатель через «0» в положение «1». На пульте управления зажигается сигнальная лампа «Основной выключатель ВКЛ»;
- поверните ключевой выключатель «Установка» на «1»;
- подождите пока на дисплее появится меню «Статус датчиков»;
- не касайтесь дисплея пока не появится «Статус датчиков»!
- нажмите светящуюся кнопку «Система управления ВКЛ».
Запускаются циркуляционный насос и вентилятор активируется зажим резака. Проводится опрос сенсоров и их значения появляются на дисплее.
- коснитесь кнопки «Режимы эксплуатации» справа внизу на дисплее чтобы открыть меню режимов эксплуатации;
- активируйте все три двигателя коснувшись кнопки «Да» справа под опцией «Выбор двигателей» для всех трех двигателей;
- выберите в опции «Автоматические программы» необходимую программу касанием соответствующей программы;
- при помощи световой кнопки «Двигатели ВКЛ» включите двигатели.
Как только масло достигнет рабочей температуры установка готова к эксплуатации. Если масло еще слишком холодное следует разогреть его в соответствии с ниже приведенным описанием.
При снижении температуры масла ниже 10°С система выдает сообщение о том что масло следует подогреть.
- установите ключевой выключатель «Подогрев масла» на «1» дисплей затемняется и проводится подогрев масла;
- по завершении процесса нагрева снова установите выключатель на «0» и снова запустите установку.
3.4 Ввод установки в эксплуатацию после аварийного останова
- убедитесь в том что опасность устранена и никто не находится в опасной зоне установки;
- разблокируйте нажатую аварийную кнопку вращением налево;
- нажмите кнопку «Квитирование сбоясообщения» чтобы квитировать сбой;
- квитируйте сбой на дисплее;
- включите систему управления и привод.
Аварийная кнопка используется только в экстренных случаях использование кнопки для включения или выключения установки в нормальном режиме эксплуатации не допускается.
3.5 Ручное управление
При включении установки она всегда находится сначала в режиме ручного управления. Установка также возвращается в режим ручного управления по завершении автоматического цикла или при возникновении сбоя автоматического цикла.
В режиме ручного управления движения установки управляются по отдельности кнопками расположенными в левой и нижней части пульта управления.
Боковой нажим прессовальная крышка и ползун управляются тумблерами трамбовка и резак управляются перекидными выключателями.
- удерживайте выключатели и тумблеры в требуемом положении переключения пока машина не достигнет нужного положения. Как только выключатели отпускаются они автоматически возвращаются в нулевую позицию; движение останавливается.
Движения установки прекращаются в том случае когда цилиндры достигают конечного положения; если Вы продолжаете удерживать элемент управления на дисплее появляется соответствующее сообщение.
Ручное управление используется в основном для прессовки крупногабаритных компонентов лома в штранг при помощи бокового нажима и прессовальной крышки.
Затем штранг разрезается в автоматическом режиме. Положение и движения всех компонентов установки можно отслеживать по дисплею.
3.6 Защита от перегрузки.
Если максимальное давление удерживается в гидравлической системе дольше 5 секунд - например если материал не разрезается или не прессуется - происходит открытие насосных клапанов и декомпрессия гидравлической системы. На дисплее пульта управления появляется сообщение о сбое.
Автоматический режим эксплуатации в ремонтном режиме невозможен. Кроме того нельзя проводить функциональные тесты компонентов установки.
Ремонтный режим позволяет перемещать трамбовку без закрытия крышки и бокового нажима. Кроме того можно перемещать резаки и трамбовку за конечные положения.
- установите ключевой выключатель «Ремонтный режим» в положение «1» вытащите ключ и держите при себе.
4 Техническое обслуживание скраповых ножниц. Общие правила
В процессе эксплуатации скраповых ножниц необходимо регулярное проведение профилактических работ по техническому обслуживанию с начала ввода оборудования в эксплуатацию.
Техническое обслуживание инспекции чистка и смазка а также контроль зазоров и износа проводятся через определенные интервалы.
Планируйте своевременное снабжение запасными частями. Использование фирменных запасных частей metso lindemann гарантирует соответствие этих деталей спецификациям. Это является важной предпосылкой для сохранения стоимости Вашей установки. На детали которые поставлены не от Metso Lindemann гарантийные обязательства компании Metso Lindemann не распространяются.
Все работы по ремонту и техническому обслуживанию должны проводиться в соответствии с нормами. В сомнительных случаях обратитесь на сервисную службу Metso Lindemann. Инспекции и работы по техническому обслуживанию Вы можете поручить Metso Lindemann на основании договора о техническом обслуживании. Это позволяет избежать требующих больших затрат времени работ и дает Вам гарантию правильного технического обслуживания установки.
По окончании работ по техническому обслуживанию и ремонту обеспечьте эксплуатационную готовность установки и надлежащий монтаж всех предохранительных устройств и защитных облицовок.
- перед началом инспекции или технического обслуживания опорожните установку до полного выхода материала;
- предохраните установку от доступа посторонних лиц;
- наладочные работы техническое обслуживание и чистка на установке и гидравлической системе могут проводиться только при отключенной системе управления. При необходимости переведите установку в положение технического обслуживания затем выключите основной выключатель и закройте его замком. Держите ключ при себе до окончания работ;
- использование платформы для замены резаков во время работы установки категорически запрещается. Убедитесь в том что платформа правильно подвешена и зафиксируйте ее стопорными болтами;
- перед вводом установки в эксплуатацию демонтируйте платформу для замены резаков и снова установите отбойную стенку;
- если техническое обслуживание установки проводится одновременно несколькими лицами между ними должна быть обеспечена связь. Если техническое обслуживание установки проводится одновременно несколькими лицами назначьте ответственного за техническое обслуживание;
- приступайте к поднятию груза только при отсутствии людей в секторе раскачивания;
- не заходите под подвешенный груз и следите за тем чтобы никто не находился под грузом;
- используйте только соответствующие и технически исправные подъемные устройства достаточной грузоподъемности которые соответствуют действующим нормам и правилам;
- крепление груза и руководство действиями оператора подъемных устройств могут осуществляться только авторизованными лицами которые должны находиться в поле зрения оператора или иметь с оператором голосовой контакт;
- сообщите о проведении сварочных и резательных работ на установке персоналу ответственному за технику безопасности и приступайте к работам только после принятия всех мер безопасности по предотвращению пожара. Сварочные работы могут выполняться только квалифицированными сварщиками;
- перед проведением технического обслуживания или поиска неисправностей в прессовальной станине завершите обработку всего загруженного материала или выгрузите материал при помощи крана;
- для проникновения в прессовальную станину используйте безопасную стремянку с нескользящими перекладинами. Предохраните стремянку от опрокидывания и соскальзывания;
- каска для защиты головы защитные очки при шлифовальных и резательных работах защитные ботинки со стальными вставками против сдавливания и с рифленой подошвой против подскальзывания защитные перчатки для защиты рук от острых кромок или осколков материала;
- выпрыскивающееся под давлением масло может привести к серьезным травмам. Подвижные детали могут отскочить или перевернуться и нанести телесные повреждения;
- во время эксплуатации масло гидросистемы нагревается; существует опасность ошпаривания;
- работы на гидравлической системе проводятся – при отсутствии других инструкций – только на декомпрессированной гидравлической системе. Убедитесь по индикатору на пульте управления что давление в системе отсутствует и температура масла не превышает 40°С.
5 Интервалы технического обслуживания скраповых ножниц
5.1 Сокращенные интервалы после ввода в эксплуатацию
В первый месяц после ввода в эксплуатацию действуют сокращенные интервалы технического обслуживания и инспекций. Эти работы проводятся дополнительно к обычному техобслуживанию.
После замены масла проинспектируйте остатки на фильтре. Крупная металлическая стружка означает дефект агрегата гидравлической системы.
проверьте состояние и функциональность резаков;
проверьте резьбовые соединения на прочность посадки при необходимости подтяните;
Ежедневно в первую неделю:
проверьте гидравлические соединения и разъемы на герметичность. Проверьте масляный поддон на утечку масла;
проверьте плавность хода электродвигателей и гидравлических насосов;
проверьте температуру масла и уровень масла в баке.
проверьте гидравлические соединения и разъемы на герметичность;
проверьте плавность хода электродвигателей и гидравлических насосов.
проверьте резьбовые соединения на прочность посадки при необходимости подтяните.
Интервалы при нормальном режиме эксплуатации.
интервалы указанные в планах контроля и технического обслуживания основаны на работе в одну смену при нормальной загрузке.
После ввода в эксплуатацию состояние гидравлической системы должно контролироваться авторизованным экспертом каждые пять лет.
Компания Metso Lindemann является лицензированной в соответствии с законом о водном хозяйстве специализированной фирмой по обслуживанию гидравлических систем которая имеет право устанавливать монтировать гидравлические системы а также проводить техническое обслуживание и чистку гидравлических установок.
Рисунок 3.15 - план технического обслуживания ЕС 1240-15
5.2 Перечень инспекций и технического обслуживания механики
Таблица 3.3 – Периодичность технического обслуживания механики
Переверните или замените резаки
Подтяните или замените уплотнение.
Заполируйте или при необходимости замените.
Стойка скраповых ножниц прессовальная станина.
Состояние (внешний осмотр).
Отремонтируйте или обратитесь в сервис Metso Lindemann
Рабочие панели в прессовальной станине на боковом нажиме и ползуне.
Болты ослаблены или отсутствуют.
Замените рабочие корпусные панели.
Подтяните знаменитые болты.
Направляющая ножевых салазок.
Внутренние и внешние направляющие планки на ножевых салазках.
Направляющие планки в стойке скраповых ножниц.
Замените резак и при необходимости отрегулируйте направляющую.
Замена проводится Metso Lindemann.
Направляющая трамбовки
Замените рабочие корпусные панели в трамбовочной камере.
Донная панель трамбовки заваривается Metso Lindemann.
Продолжение таблицы 3.2
Поверхности скольжения и кромки прессовальной крышки бокового нажима и ползуна.
Заварите электродом.
Крепления поршневой шток – ножевые салазки трамбовка прессовальная крышка боковой нажим ползун.
Геометричность (протечки не распознаются системой управления).
Наличие частей скрапа или грязи.
Замените трубопровод при необходимости обратитесь в сервисную службу Metso Lindemann.
Резьбовые соединения на двигателях насосах панелях управления трубопроводах гидравлических цилиндрах защитных устройствах быстроизнашивающихся частях резаках и т.д.; резьбовое соединение станина – стойка скраповых ножниц.
Моменты затяжки по агрегатной схеме.
Подшипник синхронного вала шарнирный рычаг бокового нажима (под нагрузкой).
Вкладыши подшипников заменяются Metso Lindemann.
Обратитесь в сервисную службу Metso Lindemann
Подвеска отбойной стенки.
Замените отбойную стенку.
Платформа для замены резаков включая подвеску и стопорные болты.
Трещины коррозия или прочие повреждения несущих компонентов.
М перед каждым использованием.
Система измерения перемещений.
Примечание: . Т = ежедневно W = еженедельно М = ежемесячно J = ежегодно.
5.3 Указания по контролю
все элементы установки типа отбойной панели и платформы для замены резаков могут перемещаться и устанавливаться только при помощи крана;
все крепежные болты отворачиваются и затягиваются динамометрическим ключом.
6 Порядок замены некоторых быстро изнашиваемых деталей
перед проведением технического обслуживания или поиска неисправностей в прессовальной станине завершите обработку всего загруженного материала или выгрузите материал при помощи крана;
для проникновения в прессовальную станину используйте безопасную стремянку с нескользящими перекладинами. Предохраните стремянку от опрокидывания и соскальзывания;
почистите прессовальную станину;
Рисунок 3.16 – Позиционирование резака
На резаках можно использовать только противоположные режущие кромки. Иначе не гарантируется достаточная плоскость прилегания резаков. Перед повторным монтажом плоскости прилегания изношенных сторон резака должны быть восстановлены надлежащей заваркой и последующей шлифовкой. Восстановление проводится так чтобы обеспечить изначальную геометрию (размеры ортогональность).
Регулярно контролируйте зазор резака и направляющей ножевых салазок. Переверните или замените резаки немедленно если режущие кромки.
имеют разломы > 25 мм
сильно затупились (R > 12 мм).
Слишком большой зазор резака и резаки с сильно затупленными и разломанными режущими кромками производят высокие динамические усилия (поперечные усилия) которые в несколько раз могут превысить усилие резания. Эти усилия могут привести к повреждениям гнезд резаков стойки ножевых салазок и направляющих.
Чтобы сократить время простоя скраповых пресс-ножниц рекомендуется всегда иметь в запасе 2-й комплект резаков.
6.2 Приведение оборудования в положение для замены резака и блокировка
Рисунок 3.17 – меню системы управления
включить основной выключатель и систему управления;
установить селектор с ключом «Ремонтный режим» на «ВКЛ» в этом случае машина работает медленнее и точнее;
выберать в меню «Режимы эксплуатации» в опции «Выбор двигателей» только один двигатель ответив «Да»;
включить гидравлический привод;
вызвать меню «Статус машины»;
подать трамбовку в верхнее конечное положение. Выше находится ремонтное положение;
нажать кнопку «Трамбовка наверх» до останова трамбовки;
для подачи трамбовки до верхнего упора нажать кнопку «Трамбовка наверх» и одновременно нажать кнопку «Резак разблокировка трамбовки»;
Рисунок 3.18 – схема установки стопорных пальцев
подать ножевые салазки немного выше положения В чтобы можно было вставить стопорный палец;
выключить гидравлический привод;
выключить машину выключатель с ключом «Установка» в поз. «0» основной выключатель «ВЫКЛ»;
закрыть основной выключатель навесным замком и держать все ключи при себе;
вставить оба стопорных пальца в отверстия А + В чтобы зафиксировать трамбовку (А) и ножевые салазки (В);
снимите нагрузку гидравлического агрегата на зажиме резака переключить красный воротковый выключатель С;
проверить по манометру отсутствие давления в гидравлической системе зажима резака гидравлический агрегат для зажима резака находится сбоку на стойке.
6.3 Подвеска платформы для замены резаков
перед работой проверить платформу для замены резаков на явные повреждения типа деформации трещин или коррозии;
проверить крепление на стойке скраповых пресс-ножниц. Использовать поврежденную или неправильно подвешенную платформу запрещается;
заблокировать подвешенную платформу для замены резаков стопорными болтами!;
снять отбойную панель;
подвесить платформу для замены резаков в крепление А отбойной панели;
заблокировать платформу для замены резаков стопорными болтами В;
приподнять лоток при помощи крана;
задвинуть блокировочный стержень С платформы для замены резаков под лоток;
опустить лоток чтобы он прилегал к блокировочному стержню.
Теперь лоток и платформа для замены резаков находятся на одном уровне и нижний резак свободен для доступа.
6.3 Демонтаж рабочих корпусных панелей в трамбовочной камере
Рисунок 3.19 – замена корпусных деталей
последовательность действий
Рабочая корпусная панель весит примерно 40 кг. При демонтаже работайте по двое чтобы исключить выскальзывание рабочей корпусной панели.
отвернуть болты и гайки А малых боковых рабочих корпусных панелей В слева и справа в трамбовочной камере при помощи импульсного винтоверта и насадки с удлинителем;
извлечь болты С внутрь и вставьте в отверстия металлические стержни;
выбить рабочую корпусную панель подходящим металлическим стержнем (например резьбовая штанга) через отверстие D в трамбовочную камеру и сместите рабочую корпусную панель на вставленные стержни;
снять рабочую корпусную панель.
6.4 Замена верхнего резака.
Присутствие под резаком во время демонтажа или монтажа категорически запрещается.
Рисунок 3.20 – замена верхнего резака
Для замены верхнего резака Вам потребуется наряду с инструментом еще деревянная доска и чистая ткань.
демонтировать защитную накладку на верхнем резаке;
отвернуть гайки зажима резака;
вытащить болт крепления резака А из держателя резака. Оставить второй болт крепления резака В в качестве предохранителя;
вставить в отверстие подходящий металлический стержень;
уложить в прессовальную станину деревянную доску на которую можно опустить верхний резак С;
вытащить второй болт крепления резака В из держателя резака;
отсоединить верхний резак С ударами по вставленному через отверстие D в ножевых салазках металлическому стержню. Теперь резак сидит на стержне вставленном спереди;
опустить верхний резак С на деревянные доски;
снять резак со стержня;
положить резак на чистое полотно;
почистить боковые плоскости прилегания резака и плоскость прилегания на ножевых салазках при этом почистить также гнезда для болтов.
Рисунок 3.21 – монтаж резака
восстановить резак перед монтажом;
проверить втулки Е на повреждение и при необходимости заменить;
проверьте элементы футеровки F на прочность посадки и при необходимости подтянуть болты G;
заварить сколы на элементах футеровки F чтобы достичь полной плоскости прилегания и соответственно оптимального восприятия усилия. Обработать выступающий наплавленный металл вручную (например при помощи углового шлифовального устройства) таким образом чтобы образовалась сплошная ровная поверхность с полным прилеганием;
снова поднять резак на деревянную доску и установить его на стержень;
установить верхний резак в обратной последовательности;
вставить болты крепления резака;
затянуть гайки от руки и убедитесь в том что плунжеры зажима резака полностью втянуты. Обратить внимание на правильную посадку плунжерного цилиндра и шлангов зажима резака. Прочность посадки резака достигается зажимом резака;
при монтаже обратить внимание чтобы резак прилегал в элементах футеровки без зазора.
6.5 Замена нижнего резака
- ставить подкладочные панели под нижний резак категорически запрещается!
- при необходимости изменить положение нижних резаков ставить подкладки под элементы футеровки.
Рисунок 3.22 – замена нижнего резака
Для замены верхнего резака Вам потребуется наряду с инструментом еще чистая ткань.
вытащить болт крепления резака А из держателя резака. Оставить второй болт В в качестве предохранителя;
вставить в отверстие подходящий металлический стержень.
вытащить второй болт крепления резака В из держателя резака.
отсоединить нижний резак С ударами по вставленному через отверстия D металлическому стержню спереди. Отверстия D доступны под станиной в положении стоя теперь резак сидит на стержне вставленном спереди;
почистить боковые плоскости прилегания резака и плоскость прилегания на ножевых салазках;
почистить также гнезда для болтов;
Проверьте втулки Е на повреждение и при необходимости замените.
проверить элементы футеровки F на прочность посадки и при необходимости подтяните болты G;
Рисунок 3.23 – порядок сборки при установке нижнего резака
заварить сколы на элементах футеровки F чтобы достичь полной плоскости прилегания и соответственно оптимального восприятия усилия;
обработать выступающий наплавленный металл вручную (например при помощи углового шлифовального устройства) таким образом чтобы образовалась сплошная ровная поверхность с полным прилеганием.
снова установить резак на стержень;
установите нижний резак в обратной последовательности;
затянуть гайки от руки и убедится в том что плунжеры зажима резака полностью втянуты обратите внимание на правильную посадку плунжерного цилиндра и шлангов зажима резака прочность посадки резака достигается зажимом резака;
7 Проверочный расчет лотка скраповых гидравлических ножниц
7.1 Описание системы конечно-элементного анализа механизмов
Система конечно-элементного анализа конструкций механизмов и приводов Пакет прикладных программ ZENIT 100 (П.П.П. ZENIT100)
Система реализована в виде пакета программ и включает в себя модули для подготовки данных проведения расчетов и вывода результатов по широкому классу задач статического и динамического анализа пространственных конструкций и плоских механизмов.
Система может быть использована для проведения проектных расчетов научных исследований и для обучения студентов по соответствующим специальностям.
Математическую основу системы составляет метод конечных элементов (МКЭ)- широко известный метод анализа механики сплошных сред - в форме метода возможных перемещений.
7.2 Основные возможности
В области статического и динамического анализа конструкций:
рассматриваются трехмерные пространственные конструкции произвольной формы состоящие из стержней пластин и объемных элементов;
материал предполагается изотропным и линейно-упругим;
конечно-элементная модель конструкции может содержать одновременно не более: - 100 узлов;
реализация суперэлементного подхода позволяет снять эти ограничения и исследовать конструкции гораздо большей размерности;
конструкция может быть выполненной из различных материалов нагруженной произвольным числом нагрузок и иметь произвольное число закреплений.
расчет деформаций и напряжений при различных видах статического нагружения;
расчет деформаций и напряжений под действием перепада температур;
расчет деформаций и напряжений под действием динамических нагрузок и кинематических возмущений произвольной формы и длительности;
расчет амплитудных значений деформаций и напряжений под действием вибрационных возмущений постоянной частоты;
расчет частот и форм собственных колебаний;
вычисление массы главных моментов инерции и координат центра масс конструкции.
В основу алгоритма решения задач заложен метод конечных элементов сущность которого заключается в представлении исследуемой конструкции в виде совокупности элементов простой конфигурации называемых конечными элементами (КЭ) стыкующихся в узловых точках. Для данной версии комплекса максимальное количество узлов в КЭ - модели - 100 количество КЭ - 200.
В рассматриваемом комплексе под термином "узловая точка" или "узел" понимается геометрическая точка конечно-элементной модели в которой стыкуются соседние КЭ или приложена внешняя сила и в которой определяются неизвестные описывающие состояние объекта (перемещения напряжения и т.п.).
Результаты представляются в таблично - текстовой форме с необходимыми краткими комментариями сгруппированными по виду результата а также в графическом виде.
В общем случае расчет статического напряженно - деформированного состояния металлоконструкции состоит из следующих этапов:
А) Построение конечно-элементной модели конструкции
На основании анализа чертежей или эскизов реальная конструкция представляется в виде идеализированной системы состоящей из конечных элементов которая и вычерчивается на отдельном листе в виде схемы или эскиза конечно-элементной модели.
При составлении схемы КЭ. - модели используются следующие виды конечных элементов (КЭ):
пространственная балка с двенадцатью степенями свободы (общее количество) испытывающая деформации растяжения - сжатия и изгиба в двух плоскостях а также кручения;
пространственный стержень с девятью степенями свободы (общее количество) испытывающий деформации растяжения - сжатия и изгиба в двух плоскостях (от предыдущего отличается шарнирным закреплением одного из концов стержня);
пространственный стержень с шестью степенями свободы (общее количество) испытывающий деформации растяжения - сжатия;
плоско - напряженный элемент произвольной четырехугольной формы (при необходимости вырождающейся в треугольную) произвольно ориентированный в пространстве испытывающий деформации растяжения-сжатия только в своей плоскости;
элемент плоской пластины произвольной четырехугольной формы (при необходимости вырождающейся в треугольную) произвольно ориентированный в пространстве испытывающий деформации растяжения-сжатия в плоскости и изгиба в двух плоскостях;
элемент гибкой нити (гибкий элемент имеющий в общем случае стрелу провисания и постоянное по длине сечение и испытывающий только деформации растяжения);
объемный элемент произвольной формы с количеством узлов от восьми до четырех - шестигранник общего вида (гексаэдр) при необходимости вырождающийся до четырехгранника (общего вида тетраэдра);
элемент рассматриваемый как твердое тело (элемент жесткостные характеристики которого значительно выше чем у смежных объектов);
элемент рассматриваемый как связь конечной жесткости между парой узлов;
элемент рассматриваемый как нелинейная неудерживающая связь между парой узлов с начальным зазором;
элемент рассматриваемый как абсолютно - жесткая связь между парой узлов;
П.П.П. предусматривает возможность расчета конструкции из разных материалов для отдельных частей;
геометрия всей системы описывается в глобальной (общей для всей конструкции) системе координат в качестве которой используется правая декартовая. Следовательно местоположение каждого узла фиксируется тремя координатами X Y Z.
В) В данной версии комплекса обеспечивается задание следующих видов нагрузок действующих на КЭ. - модель:
сосредоточенные силы и моменты действующие в узлах;
силы действующие в узлах по нормали к плоскости;
распределенные силы и моменты действующие на стержни по закону "трапеции" (частный случай - равномерно распределенная нагрузка);
силы равномерно распределенные по массе элементов;
статическая ветровая нагрузка действующая на стержни;
температурные нагрузки задаваемые в виде значений температуры в узлах.
Величины нагрузок имеют размерность Н Н*м Нм Н*мм.
7.5 Описание непосредственно расчета лотка
Лоток гидравлических скраповых ножниц разбиваем в соответствии с вышеописанным на конечные элементы (КЭ) и накладываем необходимые связи крепление лотка при помощи цепей и крепление лотка к станине ножниц прикладываем нагрузки из расчета действия груза пакета максимально возможной массы и учитываем массу самого лотка.
В результате расчета получены графические изображения КЭ модели тележки цветовое распределение напряжений в конструкции изображение ожидаемых деформаций (показаны в утрированном виде достоверные деформации даны в описании результатов расчета).
Весь расчет построен следующим образом:
текст исходных данных;
цветные изображения КЭ модели (разнообразные варианты);
результаты расчета выданные П.П.П. ZENIT100.
7.5.1 Исходные данные
габаритные размеры лотка м. замеры с действующего оборудования;
Дл х Вл х Шл – 2.26х1.16х1.5
материал лотка – сталь;
толщина стенок лотка мм. Sл=30;
угол наклона лотка к горизонту а=450;
максимальные размеры пакета при прессовании м. поперечное сечение;
коэффициент прессования пакета kп=0.7;
места крепления удерживающих цепей считать шарнирными;
места крепления лотка к станине скраповых ножниц считать жестко закрепленными.
7.5.2 Определение нагрузок действующих на лоток
Для расчета примем вариант максимальной нагрузки кг. т.е. размеры пакета будут максимальными длина пакета будет равна длине лотка поперечное сечение – максимально возможному.
Mп=(Дл*Вп*Шп)*ρстали*kп(3.1)
Мп=(2.26*1.4*0.8)*7800*0.7=13820 кг.
Нагрузку от пакета Нм2 будем считать равномерно распределенной по площади основания лотка при этом она будет равна:
Q=13820*9.81(2.26*1.5)=39992.4 Нм2 = 40 кНм2.
7.5.3 Исходные данные в формате П.П.П.Zenit100
Запись 1 Тип 0 Имя: Raschet_lotka
Запись 2 Тип 132 Имя: Koordinat tochek
Запись 3 Тип 800 Имя: Material lotka
Данные о механических свойствах материала:
Плотность кгм**3 = .780E+04
Модуль упругости МПa = .210E+06
Коэфф.Пуассона = .300
Модуль сдвига МПa = .800E+05
Коэфф. линейного расширения 1Град = .117E-04
Запись 4 Тип 504 Имя: Elementw plastin
Индексы элементов типа изгибаемых пластин
Толщина элементов мм = 30.0
Запись 5 Тип 49 Имя: Nagruz ves lotka
Данные о нагрузках распределенных по массе:
По оси OX Hкг = .000
По оси OY Hкг = -1.00
По оси OZ Hкг = .000
Запись 6 Тип 46 Имя: Raspred nagruzka
Данные о распределенных нагрузках
действующиих на стержни и ребра элементов
Номера Вид Интенсивность
узлов нагрузки По оси в узлах
4 2-усилиеНм OY -.4000E+05 -.4000E+05
5 2-усилиеНм OY -.4000E+05 -.4000E+05
6 2-усилиеНм OY -.4000E+05 -.4000E+05
7 2-усилиеНм OY -.4000E+05 -.4000E+05
8 2-усилиеНм OY -.4000E+05 -.4000E+05
14 2-усилиеНм OY -.4000E+05 -.4000E+05
15 2-усилиеНм OY -.4000E+05 -.4000E+05
16 2-усилиеНм OY -.4000E+05 -.4000E+05
17 2-усилиеНм OY -.4000E+05 -.4000E+05
18 2-усилиеНм OY -.4000E+05 -.4000E+05
24 2-усилиеНм OY -.4000E+05 -.4000E+05
25 2-усилиеНм OY -.4000E+05 -.4000E+05
26 2-усилиеНм OY -.4000E+05 -.4000E+05
27 2-усилиеНм OY -.4000E+05 -.4000E+05
28 2-усилиеНм OY -.4000E+05 -.4000E+05
34 2-усилиеНм OY -.4000E+05 -.4000E+05
35 2-усилиеНм OY -.4000E+05 -.4000E+05
36 2-усилиеНм OY -.4000E+05 -.4000E+05
37 2-усилиеНм OY -.4000E+05 -.4000E+05
38 2-усилиеНм OY -.4000E+05 -.4000E+05
44 2-усилиеНм OY -.4000E+05 -.4000E+05
45 2-усилиеНм OY -.4000E+05 -.4000E+05
46 2-усилиеНм OY -.4000E+05 -.4000E+05
47 2-усилиеНм OY -.4000E+05 -.4000E+05
48 2-усилиеНм OY -.4000E+05 -.4000E+05
54 2-усилиеНм OY -.4000E+05 -.4000E+05
55 2-усилиеНм OY -.4000E+05 -.4000E+05
56 2-усилиеНм OY -.4000E+05 -.4000E+05
57 2-усилиеНм OY -.4000E+05 -.4000E+05
58 2-усилиеНм OY -.4000E+05 -.4000E+05
64 2-усилиеНм OY -.4000E+05 -.4000E+05
65 2-усилиеНм OY -.4000E+05 -.4000E+05
66 2-усилиеНм OY -.4000E+05 -.4000E+05
67 2-усилиеНм OY -.4000E+05 -.4000E+05
68 2-усилиеНм OY -.4000E+05 -.4000E+05
74 2-усилиеНм OY -.4000E+05 -.4000E+05
75 2-усилиеНм OY -.4000E+05 -.4000E+05
76 2-усилиеНм OY -.4000E+05 -.4000E+05
77 2-усилиеНм OY -.4000E+05 -.4000E+05
78 2-усилиеНм OY -.4000E+05 -.4000E+05
84 2-усилиеНм OY -.4000E+05 -.4000E+05
85 2-усилиеНм OY -.4000E+05 -.4000E+05
86 2-усилиеНм OY -.4000E+05 -.4000E+05
87 2-усилиеНм OY -.4000E+05 -.4000E+05
88 2-усилиеНм OY -.4000E+05 -.4000E+05
Запись 7 Тип 50 Имя: Zakreplen lotka
Данные о кинематических граничных условиях
Номер Величина и вид Координатная
узла перемещения ось
8-жесткое закрепление
7-шарнирное закрепление
Запись 8 Тип 801 Имя: dopusk napryjen
Допускаемое напряжение МПа = 160.
7.5.4 Выходные данные в формате П.П.П.Zenit100
- математическая модель лотка
Рисунок 3.24 – вид математической модели по исходным данным
Рисунок 3.25 – Напряжения в лотке под действием нагрузок
Рисунок 3.26 – Деформации в лотке под действием нагрузок
Рисунок 3.27 – Деформации в лотке вид сбоку утрировано
7.5.5 Выходные данные в обычном текстовом формате П.П.П. Zenit100
Перемещения и углы поворота в узлах:
X-disp - перемещения м
XX-rot - углы поворота paд
N узла X-disp Y-disp Z-disp XX-rot YY-rot ZZ-rot
-.3389E-03 -.4117E-05 .5761E-06 -.4802E-04 .5886E-03 .4318E-02
.6157E-03 -.6052E-05 .1238E-05 -.4812E-04 -.1155E-02 .3164E-02
-.4631E-05 -.2246E-04 .2657E-05 -.4588E-04 -.5580E-02 -.5269E-02
-.4701E-05 -.2275E-02 .2249E-02 -.2364E-02 -.8208E-02 -.7943E-02
-.1847E-05 -.4143E-02 .4113E-02 -.4464E-02 -.3577E-02 -.3486E-02
.1853E-05 -.4143E-02 .4113E-02 -.4464E-02 .3577E-02 .3486E-02
.4707E-05 -.2275E-02 .2249E-02 -.2364E-02 .8208E-02 .7943E-02
.4636E-05 -.2246E-04 .2659E-05 -.4588E-04 .5580E-02 .5269E-02
-.6157E-03 -.6053E-05 .1238E-05 -.4812E-04 .1155E-02 -.3164E-02
.3389E-03 -.4118E-05 .5761E-06 -.4802E-04 -.5886E-03 -.4318E-02
-.6776E-03 -.1927E-05 .7632E-06 -.4796E-04 .3169E-02 .2333E-02
.0000 .0000 .0000 -.4799E-04 .1960E-02 .3368E-02
-.6215E-05 -.1713E-04 -.1716E-06 -.5062E-04 -.4121E-02 -.3586E-02
-.3946E-05 -.1839E-02 .1812E-02 -.1726E-02 -.7040E-02 -.6760E-02
-.1339E-05 -.3422E-02 .3391E-02 -.2736E-02 -.3095E-02 -.3004E-02
.1345E-05 -.3422E-02 .3391E-02 -.2736E-02 .3095E-02 .3003E-02
.3951E-05 -.1839E-02 .1812E-02 -.1726E-02 .7040E-02 .6760E-02
.6220E-05 -.1713E-04 -.1697E-06 -.5062E-04 .4121E-02 .3586E-02
.0000 .0000 .0000 -.4799E-04 -.1960E-02 -.3368E-02
.6776E-03 -.1926E-05 .7629E-06 -.4796E-04 -.3169E-02 -.2334E-02
-.3288E-03 -.9799E-05 .3079E-05 -.4819E-04 .3952E-02 .1483E-02
.8938E-04 -.8650E-05 .1501E-05 -.4746E-04 .3783E-02 .2293E-02
-.6414E-05 -.1643E-04 -.7506E-06 -.4532E-04 -.3250E-02 -.2703E-02
-.3372E-05 -.1576E-02 .1550E-02 -.8907E-03 -.6221E-02 -.5948E-02
-.1044E-05 -.2992E-02 .2961E-02 -.1564E-02 -.2762E-02 -.2677E-02
.1048E-05 -.2992E-02 .2961E-02 -.1564E-02 .2762E-02 .2677E-02
.3376E-05 -.1576E-02 .1550E-02 -.8908E-03 .6221E-02 .5948E-02
.6418E-05 -.1643E-04 -.7492E-06 -.4532E-04 .3250E-02 .2703E-02
-.8936E-04 -.8649E-05 .1500E-05 -.4747E-04 -.3783E-02 -.2293E-02
.3288E-03 -.9798E-05 .3078E-05 -.4820E-04 -.3952E-02 -.1483E-02
.9645E-04 -.1436E-04 .3083E-05 -.4982E-04 .2523E-02 .9295E-03
.3877E-03 -.1384E-04 .2759E-05 -.4847E-04 .2809E-02 .1552E-02
-.3347E-05 -.1836E-04 .8610E-06 -.4496E-04 -.3060E-02 -.2729E-02
-.1666E-05 -.1453E-02 .1428E-02 -.4738E-03 -.5605E-02 -.5393E-02
-.4954E-06 -.2734E-02 .2706E-02 -.1061E-02 -.2486E-02 -.2416E-02
.4988E-06 -.2734E-02 .2706E-02 -.1061E-02 .2486E-02 .2416E-02
.1669E-05 -.1453E-02 .1428E-02 -.4739E-03 .5605E-02 .5393E-02
.3350E-05 -.1836E-04 .8619E-06 -.4496E-04 .3060E-02 .2729E-02
-.3877E-03 -.1384E-04 .2759E-05 -.4847E-04 -.2809E-02 -.1552E-02
-.9640E-04 -.1436E-04 .3083E-05 -.4982E-04 -.2523E-02 -.9296E-03
.2534E-03 -.1568E-04 .1189E-05 -.5335E-04 .9497E-03 .1023E-02
.5267E-03 -.1565E-04 .2644E-05 -.5294E-04 .1339E-02 .1226E-02
-.2545E-06 -.1969E-04 .2878E-05 -.5127E-04 -.3028E-02 -.2809E-02
.7322E-07 -.1356E-02 .1333E-02 -.6299E-03 -.5007E-02 -.4859E-02
.6197E-07 -.2498E-02 .2472E-02 -.1370E-02 -.2185E-02 -.2134E-02
-.5952E-07 -.2498E-02 .2472E-02 -.1370E-02 .2185E-02 .2134E-02
-.7076E-07 -.1356E-02 .1333E-02 -.6299E-03 .5007E-02 .4859E-02
.2570E-06 -.1969E-04 .2879E-05 -.5127E-04 .3028E-02 .2809E-02
-.5267E-03 -.1565E-04 .2644E-05 -.5294E-04 -.1339E-02 -.1227E-02
-.2534E-03 -.1568E-04 .1189E-05 -.5335E-04 -.9497E-03 -.1023E-02
.9418E-04 -.1406E-04 -.2034E-05 -.5709E-04 -.7479E-04 .1419E-02
.4264E-03 -.1438E-04 .9455E-06 -.5887E-04 .2470E-03 .1306E-02
.1679E-05 -.1877E-04 .4104E-05 -.6159E-04 -.2736E-02 -.2575E-02
.1229E-05 -.1173E-02 .1154E-02 -.1270E-02 -.4162E-02 -.4059E-02
.4444E-06 -.2115E-02 .2093E-02 -.2452E-02 -.1771E-02 -.1735E-02
-.4429E-06 -.2115E-02 .2093E-02 -.2452E-02 .1771E-02 .1735E-02
-.1227E-05 -.1173E-02 .1154E-02 -.1270E-02 .4162E-02 .4059E-02
-.1677E-05 -.1877E-04 .4104E-05 -.6159E-04 .2736E-02 .2575E-02
-.4264E-03 -.1438E-04 .9454E-06 -.5887E-04 -.2471E-03 -.1306E-02
-.9413E-04 -.1406E-04 -.2034E-05 -.5709E-04 .7471E-04 -.1419E-02
-.2930E-03 -.1031E-04 -.5832E-05 -.5718E-04 -.4669E-03 .1873E-02
.1272E-03 -.1073E-04 -.1979E-05 -.6133E-04 -.2612E-03 .1601E-02
.2676E-05 -.1494E-04 .3905E-05 -.6966E-04 -.2052E-02 -.1939E-02
.1772E-05 -.8306E-03 .8167E-03 -.2148E-02 -.2834E-02 -.2765E-02
.6159E-06 -.1461E-02 .1445E-02 -.3888E-02 -.1169E-02 -.1146E-02
-.6151E-06 -.1461E-02 .1445E-02 -.3888E-02 .1169E-02 .1146E-02
-.1771E-05 -.8306E-03 .8166E-03 -.2148E-02 .2834E-02 .2765E-02
-.2675E-05 -.1494E-04 .3905E-05 -.6966E-04 .2052E-02 .1939E-02
-.1271E-03 -.1073E-04 -.1979E-05 -.6133E-04 .2611E-03 -.1601E-02
.2931E-03 -.1031E-04 -.5832E-05 -.5718E-04 .4668E-03 -.1873E-02
-.8144E-03 -.5838E-05 -.9494E-05 -.5246E-04 -.4807E-03 .2381E-02
-.2894E-03 -.5992E-05 -.5411E-05 -.5200E-04 -.2864E-03 .1970E-02
.2492E-05 -.8372E-05 .2284E-05 -.6829E-04 -.1087E-02 -.1014E-02
.1519E-05 -.3429E-03 .3354E-03 -.2491E-02 -.1188E-02 -.1151E-02
.5105E-06 -.5805E-03 .5723E-03 -.4265E-02 -.4709E-03 -.4589E-03
-.5101E-06 -.5805E-03 .5723E-03 -.4265E-02 .4709E-03 .4590E-03
-.1518E-05 -.3429E-03 .3354E-03 -.2491E-02 .1188E-02 .1151E-02
-.2491E-05 -.8372E-05 .2284E-05 -.6829E-04 .1086E-02 .1014E-02
.2894E-03 -.5992E-05 -.5411E-05 -.5200E-04 .2863E-03 -.1970E-02
.8144E-03 -.5838E-05 -.9494E-05 -.5246E-04 .4806E-03 -.2381E-02
-.1417E-02 -.2023E-05 -.1289E-04 -.4917E-04 -.4756E-03 .2646E-02
-.7952E-03 -.1944E-05 -.8591E-05 -.4306E-04 -.2636E-03 .2580E-02
.7952E-03 -.1944E-05 -.8591E-05 -.4306E-04 .2635E-03 -.2580E-02
.1417E-02 -.2023E-05 -.1289E-04 -.4917E-04 .4755E-03 -.2646E-02
Данные об усилиях в закреплениях
-.541E+05 1-усилие Н OX
-.125E+06 2-усилие Н OY
.451E+05 3-усилие Н OZ
-.122E+05 1-усилие Н OX
-.480E+05 2-усилие Н OY
-.987E+04 3-усилие Н OZ
-474. 4-моментН*м OX
-.555E+04 1-усилие Н OX
-.450E+05 2-усилие Н OY
-.188E+05 3-усилие Н OZ
-.268E+04 4-моментН*м OX
-.185E+04 1-усилие Н OX
-.523E+05 2-усилие Н OY
-.164E+05 3-усилие Н OZ
-.444E+04 4-моментН*м OX
.185E+04 1-усилие Н OX
-173. 5-моментН*м OY
-97.2 6-моментН*м OZ
.555E+04 1-усилие Н OX
-464. 5-моментН*м OY
-220. 6-моментН*м OZ
.122E+05 1-усилие Н OX
-994. 5-моментН*м OY
-896. 6-моментН*м OZ
.541E+05 1-усилие Н OX
конструкции кг = .147E+04
Моменты инерции конструкции
относительно центра масс кг*м**2:
Jxx= 727. Jyy= 834. Jzz= 941.
Jxy= -.176E-02 Jxz= -.120E-02 Jyz= 310.
Координаты центра масс мм:
X= 750. Y= .101E+04 Z= 800.
8 Проверочный расчет цепи крепления лотка
Проверку поддерживающих цепей проводим на основе выходных массово – инерционных характеристик подсчитанных в предыдущем расчете.
В соответствии с ним масса конструкции будет равна:
Q=14700 кг. учитывается масса самого лотка и его максимальная (теоретическая загрузка прессованным пакетом)
В расчет включаем вариант когда нагрузка всей конструкции приходиться только на две цепи наиболее тяжелый вариант
где кц=3.0 – коэффициент запаса в соответствии с нормами Госгортехнадзора;
На скраповых ножницах установлена цепь со следующими техническими характеристиками:
- разрушающее усилие - 266000 н.
- геометрия цепи получена в результате натурных замеров
d = 26 мм. t = 72 мм. b = 84 мм.
Фактический запас прочности цепи:
таким образом запас прочности цепей обеспечен.
Охрана труда и промышленная безопасность
1 Предохранительные устройства скраповых ножниц общее их описание и порядок работы
Рисунок 4.1 - Предохранительные устройства ножниц
Для защиты обслуживающего персонала окружающей среды а также механизмов гидравлики и электрики установка оснащена следующими предохранительными устройствами:
1.1 Скраповые ножницы
Отбойная панель за раствором ножей;
Система замера перемещений для контроля промежуточных положений ножевых салазок трамбовки загрузочного ползуна прессовальной крышки бокового нажима;
Стопорный палец ножевых салазок и трамбовки для проведения технического обслуживания.
1.2 Гидравлическая система
Маслосборник масляный поддон;
Сенсоры контроля давления уровня температуры масла и состояния фильтра;
Реле максимального давления для защиты от механических и электрических перегрузок.
1.3 Электрооборудование
Запираемое помещение с электрооборудованием;
Запираемый основной выключатель;
Автоматическая система управления (АСУ) анализирующая сигналы концевых выключателей системы замера перемещений и прерывающая работу установки в случае сбоев.
1.4 Операторская кабина
Шумоизолированная двухстеночная операторская кабина с безопасным стеклом.
1.5 Пульт управления
Элементы управления с запираемым выключателем системы управления и пультом управления разблокирующие кнопки при аварийном отключении и сообщениях о сбое контроллеры с автоматическим возвратом.
1.6 Аварийный останов ножниц
При нажатии аварийной кнопки прерывается подача тока и вся установка немедленно останавливается в текущем рабочем положении. Все настройки при этом сохраняются.
Рисунок 4.2 – Аварийная кнопка
Аварийная кнопка выполнена в красном цвете на желтой контрастной поверхности.
В базовой модификации установки на пульте управления установлена одна аварийная кнопка.
На распределительном шкафу установка отключается основным выключателем.
1.6.1 Ввод установки в эксплуатацию после аварийного останова
Убедитесь в том что опасность устранена и никто не находится в опасной зоне установки;
Разблокируйте нажатую аварийную кнопку вращением налево;
Включите систему управления и привод.
2 Действия обслуживающего персонала в экстремальных случаях инструкция
Загруженные в установку опасные вещества могут привести к пожару взрыву вспышке выбросу ядовитых и опасных для здоровья газов и испарений.
2.1 Действия при пожаре
Выключите установку.
Оповестите руководство.
Покиньте рабочие места.
Локализуйте очаг пожара.
Приступите к тушению пожара.
Небольшие возгорания тушатся огнетушителем. При значительных пожарах следует покинуть территорию установки тушение пожара проводится пожарной службой и координаторами.
Проверьте установку на повреждения.
После тушения опорожните установку в ручном режиме проверив при этом возможные очаги пожара на выходе материала чтобы исключить распространение пожара в зону хранения размельченного материала.
2.2 Действия при взрыве или вспышке
Локализуйте возможные очаги пожара.
Приступите к тушению пожара..
После тушения выключенная установка должна быть проверена специалистом по безопасности на наличие других взрывоопасных материалов.
Опорожните установку в ручном режиме эксплуатации или разгрузите при помощи вспомогательных средств.
Проверьте возможные очаги пожара на выходе материала чтобы исключить распространение пожара в зону хранения размельченного материала.
2.3 Действия при выбросах ядовитых опасных для здоровья газов или испарений
Выключенная установка должна быть проинспектирована специалистом по безопасности чтобы локализовать и устранить источник выхода газа или испарений. Доступ на установку разрешается только после отбоя тревоги уполномоченным лицом.
3 Указания и предупреждения для обслуживающего персонала
3.1 Загрузка опасных материалов
Рисунок 4.3 – Знак «Опасность!»
Опасно для жизни из-за опасных материалов! Если при проверке металлолома обнаруживаются боеприпасы взрывоопасные предметы или прочие опасные материалы или предметы и материалы не могут быть классифицированы как безопасные эти предметы следует отсортировать и утилизировать как опасные отходы.
Рисунок 4.4 – Знак «Особое внимание!»
Если опасные предметы или материалы обнаруживаются позже в прессовальной станине следует немедленно отключить установку. Предметы или материалы должны быть извлечены из установки.
Рисунок 4.5 – Знак «Внимание!
Обнаружен взрывоопасный предмет!»
Рисунок 4.6 – Знак «Внимание!
Взрывоопасный предмет!»
При обнаружении боеприпасов и взрывоопасных предметов следует обозначить место обнаружения изолировать от доступа и немедленно сообщить в соответствующие инстанции.
3.2 Эксплуатация установки
Рисунок 4.7 – Знак «Опасность!
Возможен вылет лома!»
Опасно для жизни из-за вылетающих частей установки или лома!
Рисунок 4.8 – Знак «Внимание! Люди в опасной зоне!»
Перед включением установки убедитесь в том что работы по ремонту и техническому обслуживанию не проводятся а в опасной зоне установки и в машинном отделении никто не находится.
Убедитесь в том что платформа для замены резаков демонтирована и установлена отбойная стенка.
Использование платформы для замены резаков во время работы установки категорически запрещается.
Рисунок 4.9 – Знак «Опасность! Недостаточный
объем защитных устройств»
Опасно для жизни из-за недостаточного объема защитных устройств!
Шунтирование или отключение предохранительных устройств запрещается.
Рисунок 4.10 – Знак «Внимание! Посторонним
лицам доступ закрыт!»
Нахождение людей на материале в прессовальной станине категорически запрещается. В случае перекашивания материала перекос устраняется краном или другими соответствующими инструментами.
Опасность пожара из-за легковоспламеняющихся материалов или пыли!
Не оставляйте работающую установку без присмотра. Следите за тем чтобы в установку не загружался пожароопасный материал. Постоянно контролируйте материал на очаги возгорания. В случае пожара немедленно примите меры по борьбе с огнем предусмотренные эксплуатационной организацией.
Соблюдайте планы чистки смазки и технического обслуживания чтобы не допустить повреждения установки и вытекающих из этого опасностей. При чистке обратите особое внимание на очистку ребер охлаждения двигателей от пыли которая может вызвать воспламенение приводов.
Рисунок 4.11 - Знак «Внимание! Опасность
получения травмы из-за подскальзывания!»
Рисунок 4.12 – Знак «Внимание!
Всегда носите защитную обувь»
При эксплуатации и обслуживании скраповых ножниц необходимо строго выполнять требования знака 4.12. - Всегда носите защитную обувь с ребристой подошвой чтобы не подскользнуться на мокрых или замасленных поверхностях.
Рисунок 4.13 – Знак «Внимание!
Тяжелый экологический ущерб!»
При работе с маслом для гидросистемы и прочими опасными для воды материалами следите за тем чтобы опасные для воды жидкости не попали в канализацию или почву. Загрязнение водоемов опасными для воды веществами не допускается.
3.3 Правила техники безопасности при техническом обслуживании и поиске неисправностей.
Предохраните установку от доступа посторонних лиц.
Наладочные работы техническое обслуживание и чистка на установке и гидравлической системе могут проводиться только при отключенной системе управления. При необходимости переведите установку в положение технического обслуживания затем выключите основной выключатель и закройте его замком. Держите ключ при себе до окончания работ.
Использование платформы для замены резаков во время работы установки категорически запрещается. Убедитесь в том что платформа правильно подвешена и зафиксируйте ее стопорными болтами.
Перед вводом установки в эксплуатацию демонтируйте платформу для замены резаков и снова установите отбойную стенкулоток.
Опасность в связи с непреднамеренным включением и отсутствием координации работ по техническому обслуживанию!
Если техническое обслуживание установки проводится одновременно несколькими лицами между ними должна быть обеспечена связь. Если техническое обслуживание установки проводится одновременно несколькими лицами назначьте ответственного за техническое обслуживание.
Рисунок 4.14 – Знак «Опасность! Опасность пожара
в связи со сварочными и резательными работами!»
Сообщите о проведении сварочных и резательных работ на установке персоналу ответственному за технику безопасности и приступайте к работам только после принятия всех мер безопасности по предотвращению пожара.
Сварочные работы могут выполняться только квалифицированными сварщиками.
Рисунок 4.15 – Знак «Опасность! Опасно для жизни из-за
недостаточного объема защитных устройств!»
По окончании профилактических работ предохранительные устройства и коммутаторы должны быть снова приведены в исходное состояние.
Рисунок 4.16 – Знак «Внимание! Опасность получения травмы
из-за падения в прессовальную станину!»
Перед проведением технического обслуживания или поиска неисправностей в прессовальной станине завершите обработку всего загруженного материала или выгрузите материал при помощи крана.
Для проникновения в прессовальную станину используйте безопасную стремянку с нескользящими перекладинами. Предохраните стремянку от опрокидывания и соскальзывания.
Рисунок 4.17 – Знак «Внимание! Опасность тяжелого увечья
из-за недостаточной защитной экипировки!»
Рисунок 4.18 – Знак «Использовать каску для защиты головы!»
Данным знаком отмечается следующие защитные приспособления - Защитные очки при шлифовальных и резательных работах.
Рисунок 4.19 - Знак «Использовать защитные ботинки!»
Защитные ботинки со стальными вставками против сдавливания и с рифленой подошвой против подскальзывания.
Рисунок 4.20 - Знак «Использовать защитные перчатки!»
Защитные перчатки для защиты рук от острых кромок или оскол-ков материала.
3.4 Техническое обслуживание электрооборудования
Рисунок 4.21 - Знак «Опасность!
Опасно для жизни из-за удара током!»
При работах на электрооборудовании основной выключатель на распределительном шкафу должен быть выключен и закрыт.
Предохраните основной выключатель от включения заприте основной выключатель и держите ключ при себе.
Проконтролируйте отсутствие напряжения при помощи вольтметра.
Заземлите место проведения работ и закоротите провода.
Закройте соседние находящиеся под напряжением компоненты.
Опасно для жизни из-за удара током!
Работы на электрооборудовании могут проводиться только квалифицированными электриками.
3.5 Техническое обслуживание гидравлики
Рисунок 4.22 - Знак «Внимание! Находящееся под
давлением масло гидросистемы опасно для жизни!»
Выпрыскивающееся под давлением масло может привести к серьезным травмам. Подвижные детали могут отскочить или перевернуться и нанести телесные повреждения.
Во время эксплуатации масло гидросистемы нагревается; существует опасность ошпаривания.
Работы на гидравлической системе проводятся - при отсутствии других инструкций только на декомпрессированной гидравлической системе. Убедитесь по индикатору на пульте управления что давление в системе отсутствует и температура масла не превышает 40 0С.
Рисунок 4.23 – Знак «Внимание!
Контроль гидравлической системы проводится только квалифицированным специалистом или специализированной фирмой.
Профилактические работы на гидравлической системе могут проводиться только специалисты фирмы производителя «Metso Lindemann» или другой уполномоченной специализированной фирмой по обслуживанию гидравлических систем.
Экология и защита окружающей среды
1 Описание факторов оказывающих загрязняющее действие на окружающую среду при эксплуатации скраповых ножниц
2.1 Загрязнение водной среды
Попадание гидравлической жидкости в водоемы может привести к тяжелым последствиям для экологии.
Эксплуатационная организация обязана проводить постоянный контроль герметичности и функциональности гидравлической системы.
Если эксплуатационная организация не располагает компетентным персоналом работы по контролю техническому обслуживанию и чистке системы должны проводиться авторизованной специализированной фирмой по обслуживанию гидравлических систем.
Фундамент установки должен быть спроектирован в соответствии с требованиями к размерам несущей способности и устойчивости. Кроме того если установка оснащена гидравлическими системами фундамент должен соответствовать требованиям по водоохране.
План фундамента и строительные нормативы по фундаменту компании Metso Lindemann содержат все необходимые данные для возведения фундамента.
В соответствии с законом о водном хозяйстве следует учитывать: Рабочая жидкость гидравлической системы классифицирована по классу опасности для воды 1.
Опасное вещество: Масло гидросистемы WGK1 прибл. 13 м3.
Таблица 5.1 – Содержание и объемы опасных веществ в скраповых ножницах
F1 Непроницаемая поверхность.
F2 Как F1 но со свидетельством.
R1 Сдерживающая способность объема опасных для воды жидкостей утечка которого допускается до принятия соответствующих мер безопасности (например блокировка негерметичного компонента установки или герметизация протечки).
R2 Сдерживающая способность объема опасных для воды жидкостей утечка которого допускается при эксплуатационных неполадках без учета профилактических мероприятий.
запись отклонений от нормального режима эксплуатации и принятие необходимых мер.
l2 План системы сигнализации и мероприятий описывающий эффективные мероприятия и меры предосторожности по предотвращению нанесения ущерба водным ресурсам и согласованный с включенными в план мероприятий участками.
Дополнительные условия соблюдения соответствующих водоохранных предписаний:
Вытекающее масло должно стекать в приемную камеру. Пол и боковые стенки приемной камеры должны быть выполнены маслонепроницаемыми до предельной высоты которая рассчитывается по максимально возможному уровню вытекшего масла при утечке из установки всего объема масла.
Приемные камеры выполняются без стока по которому масло может попасть в грунтовые воды или канализацию.
Строительство фундамента должно проводиться специализированной организацией работающей в соответствии со всеми основными нормативами и предписаниями. Уплотнения стыковых швов между отдельными сегментами фундамента на боковых стенках на выводах а также на прочих стыках также выполняются специализированной организацией.
2 Классификация и эффективность работы пылеулавливающих аппаратов
2.1 Общее описание принципа действия
Работа пылеулавливающих аппаратов основана на использовании разных механизмов осаждения частиц:
гравитационного под действием силы тяжести при прохождении частиц через аппарат;
осаждения под действием центробежной силы;
зацепления (эффект касания) происходящего если расстояние от частицы движущейся с газовым потоком до обтекаемого тела равно или меньше ее радиуса;
электрического в результате ионизации газа при которой частицы заряжаются и осаждаются на электродах
В основу классификации газоочистных аппаратов наиболее часто встречающихся на металлургическом предприятии может быть положена схема (смотри рисунок 5.1 далее в тексте).
Процесс очистки газов от твердых и капельных примесей в разных аппаратах характеризуется несколькими параметрами в том числе общей эффективностью очистки:
h=(Свх-Свых)Свх(5.1)
где - Свх и Свых - массовые концентрации примесей в газе соответственно до и после пылеуловителя
Эффективность очистки может быть определена как отношение количества уловленной пыли к количеству пыли поступающей в пылеуловитель:
h=DММ1=(М1 - М2)М1=1 - М2М1=DМ(DМ+М2)(5.2)
где - М2 - масса пыли выходящей из пылеуловителя.
Если очистка в системе последовательно соединенных аппаратов то общая эффективность очистки:
h=1- (1-h1) (1-h2) (1-hn)(5.3)
где h1 h2 h - n - эффективности очистки 1- 2- n-ного аппаратов.
В ряде случаев учитывают изменение фракционного состава пыли при переходе из аппарата в аппарат:
hi = (Cвхi - Свыхi)Свхi(5.4)
где Cвхi и Свыхi - массовые концентрации i-той фракции загрязнителя до и после пылеуловителя.
Гидравлическое сопротивление пылеуловителей DР определяют как разность давлений газового потока на входе Рвх и Рвых из аппарата. Величину DР находят экспериментально и рассчитывают по формуле:
DР= Рвх - Рвых = xrw22(5.5)
где r и w - соответственно плотность и скорость газа в расчетном сечении аппарата;
x - коэффициент гидравлического сопротивления.
Величина гидравлического сопротивления и объемный расход Q очищаемого газа определяют мощность привода устройства для подачи газа к пылеуловителю:
где К - коэффициент запаса мощности;
hм - КПД передачи мощности от электродвигателя к вентилятору - КПД вентилятора.
В процессах пылеулавливания весьма важны физико-химические характеристики пылей и туманов:
дисперсный (фракционный) состав;
адгезионные свойства;
электрическая заряженность частиц;
удельное электросопротивление слоев частиц и др.
Для правильного выбора пылеулавливающего аппарата необходимы прежде всего сведения о дисперсном составе пылей и туманов.
По дисперсности пыли классифицированы на 5 групп:
I- очень крупнодисперсная пыль d50 > 140 мкм;
II- крупнодисперсная пыль d50 = 40 140 мкм;
III- среднедисперсная пыль d50 = 10 40 мкм;
IV- мелкодисперсная пыль d50 = 1 10 мкм;
V- очень мелкодисперсная пыль d501 мкм (d50 - медианный размер частиц при котором доли частиц крупнее и мельче d50 равны).
Важная характеристика пыли - ее плотность. Различают истинную и кажущуюся плотность частиц пыли а также насыпную плотность слоя пыли. Кажущаяся плотность частиц - отношение ее массы к объему. Для сплошных (непористых) частиц кажущаяся плотность совпадает с истинной плотностью. Насыпная плотность слоя пыли равна отношению массы слоя к его объему и зависит не только от пористости частиц пыли но и от процесса формирования пылевого слоя. Насыпная плотность слоя необходима для вычисления объема пыли в бункерах.
2.2 Устройства для механической очистки газов от пыли
Основное достоинство этих устройств - простота конструкции и они рекомендуются в основном для грубой очистки. Пылеосадительная камера - это наиболее простое устройство для улавливания пыли. Она предназначена для предварительной очистки газов с улавливанием грубодисперсных частиц размер от 50 до 500 мкм. Взвешенная в потоке газа пыль осаждается под действием силы тяжести.
Камера представляет собой пустотелый или с горизонтальными полками во внутренней полости металлический прямоугольный короб с бункером внизу для сбора пыли (смотри рисунок 5.3). Площадь сечения короба значительно больше сечения подводящих газоходов. Вследствие этого скорость газового потока резко снижается и частицы пыли под действием силы тяжести оседают. Преимущества пылеосадительных камер - малое гидравлическое сопротивление простота и малая стоимость; недостатки - громоздкость небольшой коэффициент улавливания (не 40-45%). Этот коэффициент можно довести до 80-85% если в камерах установить горизонтальные полки увеличивающие длительность пребывания газа в камере. Однако такие камеры трудно очищаются и поэтому не нашли широкого применения.
Газоочистные аппараты
Осадительные камеры инерционные и центробежные аппараты
Волокнистые тканевые зернистые фильтры
Скрубберы форсуночные Вентури динамические газопромыватели
Центробежные ударно-инерционные тарельчатые аппараты
Сухие горизонтальные и вертикальные мокрые
Абсорберы адсорберы.
Рисунок 5.1 - Классификация пылеулавливающих аппаратов
Рисунок 5.2 - Пылеосадительная камера (а) и
инерционный пылеуловитель (б);
I - запыленный газ II - очищенный газ III пыль
Инерционные пылеуловители. В этих аппаратах резко изменяется направление газового потока частицы пыли по инерции сохраняют направление своего движения ударяются о поверхность и осаждаются в бункере. Наиболее простые пылеуловители (рисунок 5.2 б) способны задерживать только крупные частицы пыли размером более 25-30 мкм. Более мелкие частицы можно выделить из газового потока под действием инерционных сил при изменении направления движения газового потока с помощью жалюзийных пластин. Жалюзийный пылеуловитель (рисунок 5.3) состоит из двух частей: жалюзийной решетки и выносного пылеуловителя. При прохождении через жалюзийную решетку газовый поток разделяется на два: поток очищенный от пыли (80-90 % всего количества газа) и поток в котором сосредоточена основная масса пыли.
Рисунок 5.3 - Жалюзийный пылеуловитель.
I - запыленный газ II очищенный газ.
Центробежные обеспыливающие устройства (циклоны). Широкое применение для сухой очистки газов получили циклоны разных типов (рисунок 5.4). Газовый поток вводится в циклон через патрубок 2 по касательной к внутренней поверхности корпуса 1 и совершает вращательно-поступательное движение вдоль корпуса к бункеру 4. Под действием центробежной силы частицы пыли образуют на стенке циклона пылевой слой который вместе с частью газа поступает в бункер. Отделение частиц пыли от газа попавшего в бункер происходит при повороте газового потока в бункере на 1800. Освободившись от пыли газовый поток образует вихрь и выходит из бункера давая начало вихрю газа покидающему циклон через выходную трубу 3. Для нормальной работы циклона необходима герметичность бункера.
Рисунок 5.4 - Циклон
I - запыленный газ II - очищенный газ III - пыль
В промышленности используют циклоны рассчитанные на скорость газового потока от 5 до 20 мс. Так как в процессе работы установки скорость газового потока может изменяться то в последнее время широко применяют батареи циклонов в которых газовый поток определяется по нескольким параллельно работающим циклонам в зависимости от расхода газа действует то или иное число циклонов.
КПД циклонов зависит от концентрации пыли и размеров ее частиц и резко снижается при уменьшении этих показателей. Средняя эффективность обеспыливания газов в циклонах составляет 98% при размере частиц пыли 30-40 мкм 80% - при 10 мкм 60% - при 4-5мкм.
Преимущества циклонов - простота конструкции небольшие размеры отсутствие движущихся частей; недостаток - большой абразивный износ частей аппарата пылью.
2.3 Аппараты мокрой очистки газов от пыли
Аппараты мокрой очистки газов имеют широкое распространение так как характеризуются высокой эффективностью очистки от мелкодисперсных пылей с dч ³ (03 10) мкм а также возможностью очистки от пыли горячих и взрывоопасных газов. Однако мокрые пылеуловители обладают рядом недостатков:
образование в процессе очистки шлама требующее специальных систем для его переработки;
вынос влаги в атмосферу и образование отложений в отводящих газоходах при охлаждении газов до температуры точки росы;
необходимость создания оборотных систем подачи воды в пылеуловитель.
Аппараты мокрой очистки работают по принципу осаждения частиц пыли либо на капли либо на пленки жидкости под действием сил инерции и броуновского движения.
Силы инерции действуют на частицы пыли и капли жидкости при их сближении. Эти силы зависят от массы капель и частиц а также от скорости их движения. Мелкие ( 1 мкм) частицы пыли не обладают достаточной кинетической энергией и при сближении обычно огибают капли и не улавливаются жидкостью. Броуновское движение характерно для частиц малого размера. Для достижения высокой эффективности очистки газа от частиц примесей за счет броуновского движения необходимо уменьшить скорость движения газового потока в аппарате.
Кроме этих основных сил на процесс осаждения влияют:
турбулентная диффузия;
взаимодействие электрически заряженных частиц;
процессы конденсации;
Во всех случаях очистки газа в мокрых пылеуловителях важна смачиваемость частиц жидкостью.
Конструктивно мокрые пылеуловители разделяют на скрубберы Вентури форсуночные и центробежные ударно-инерционного типа барботажно-пенные и др.
Среди аппаратов мокрой очистки с осаждением частиц пыли на поверхность капель на практике более применимы скрубберы Вентури (рисунок 5.5). Основная часть скруббера - сопло Вентури 2 в конфузорную часть которого подводится запыленный поток газа и через центробежные форсунки 1 жидкость на орошение. В конфузорной части сопла газ разгоняется от входной скорости 15-20 мс до 30-200 мс в узком сечении сопла. Процесс осаждения частиц пыли на капли жидкости обусловлен массой жидкости развитой поверхностью капель и высокой относительной скоростью частиц жидкости и пыли в конфузорной части сопла. В диффузорной части сопла поток тормозится до скорости 15-20 мс и подается в каплеуловитель 3 обычно выполняемый в виде прямоточного циклона.
Рисунок 5.5 - Скруббер Вентури.
I - запыленный газ II - очищенный газ III - шлам.
Скрубберы Вентури обеспечивают высокую эффективность очистки аэрозолей со средним размером частиц 1-2 мкм при начальной концентрации примесей до 100 гм3 и удельном расходе воды на орошение 01-60 лм3.
Разновидностью аппаратов для улавливания пыли осаждением частиц на каплях жидкости являются форсуночные скрубберы (рисунок 5.6 а). Запыленный газовый поток поступает в скруббер по патрубку и направляется на зеркало воды где осаждаются наиболее крупные частицы пыли. Газовый поток и мелкодисперсная пыль распределяясь по всему сечению корпуса 1 поднимаются навстречу потоку капель подаваемых в скруббер через форсуночные пояса 2. Удельный расход воды в форсуночных скрубберах составляет 3.0 - б.0 лм3. Общая эффективность очистки получаемая на форсуночных скрубберах невысока и составляет 0.6-0.7 при очистке доменного газа. В форсуночных скрубберах эффективно улавливаются частицы > 10 мкм.
Рисунок 5.6 - Форсуночный (а) и центробежный (б) скрубберы.
В аппаратах центробежного типа (рисунок 5.8 б) частицы пыли отбрасываются на пленку жидкости 2 центробежными силами возникающими при вращении газового потока в аппарате за счет тангенциального расположения входного патрубка 5 в корпусе аппарата. Пленка жидкости толщиной 03 мкм создается подачей воды через сопла 1 и непрерывно стекает вниз увлекая в бункер 4 частицы пыли. Удельный расход воды в центробежных скрубберах составляет 0.09-0.18 лм3. Входная запыленность газового потока 20 гм3.
К мокрым пылеуловителям относят барботажно-пенные пылеуловители с провальной (рисунок 5.7 а) и переливной (рисунок 5.7 б) решетками. В таких аппаратах газ на очистку поступает под решетку 3 проходит через нее и барботируя через слой жидкости и пены 2 очищается от пыли в результате осаждения ее частиц на внутренней поверхности газовых пузырей. Режим работы аппаратов зависит от скорости подачи воздуха под решетку. Современные барботажно-пенные аппараты обеспечивают эффективность очистки газа от мелкодисперсной пыли около 095-096 при удельных расходах воды 04-05 лм3.
Эффективность мокрых пылеуловителей зависит в основном от смачиваемости пыли. Недостатки мокрых пылеуловителей - большой расход воды при отсутствии ее циркуляции необходимость иметь отстойники и периодически их очищать в случае циркуляции возможность щелочной и кислотной коррозии значительное ухудшение рассеивания газов после увлажнения через дымовые трубы.
Рисунок 5.7. - Барботажно-пенные пылеуловители с провальной (а) и
переливной 6 решетками.
– слой жидкости и пены;
Фильтрация через пористые материалы - один из наиболее совершенных методов очистки газов от твердых частиц. Газовый поток проходит через пористый материал разных плотностей и толщин в котором задерживается основная масса пыли. Для очистки газов применяют два вида промышленных фильтров: тканевые и зернистые.
Тканевые фильтры. В зависимости от формы фильтрующей поверхности различают рукавные и рамочные фильтры. Наиболее Распространены рукавные фильтры (рисунок 5.8) состоящие из ряда тканевых рукавов подвешенных в металлической камере.
Запыленный газ поступает в нижнюю часть аппарата и проходит через тканевые рукава. На поверхности ткани и в ее порах осаждается пыль. В качестве фильтрующих тканей используют синтетические ткани которые менее влагоемки по сравнению с натуральными не гниют стойки при > 150°С. термопластичны. От осевших частиц их очищают встряхиванием или обратной продувкой либо встряхиванием и обратной продувкой одновременно.
Рисунок 5.8 - Рукавный фильтр.
- корпус 2 - рукава 3 - дроссель 4 - пыль 5 - затвор 6- шнек.
I - запыленный воздух II - очищенный воздух.
Хорошие результаты достигнуты при внедрении тканевых фильтров из коррозионно- и термостойких материалов в том числе на металлической основе которые могут работать при 900°С.
Одним из распространенных фильтрующих материалов служат проволочные сетки из низкоуглеродистых или высоколегированных сталей меди латуни бронзы никеля и др. Фильтрующие элементы из сеток могут работать в широком диапазоне температур от 0 до 800°С в агрессивных и неагрессивных средах. Фильтрующие элементы из сеток обладая некоторыми преимуществами по сравнению с фильтрующими элементами из тканей и войлока уступают им по тонкости очистки.
Для ультратонкой очистки газов используют материалы типа ФП представляющие нанесенные на марлевую подложку слоя синтетических волокон диаметром 1-2 мкм. В качестве полимеров для ФП используют перхлорвинил (ФПП) фторполимеры и др. Материалы ФП характеризуются высокими свойствами и малой толщиной (от 02 до 1 мкм).
Зернистые фильтры могут работать при очень высоких температурах в агрессивных средах способны выдерживать большие механические нагрузки резкие перепады давления и температуры.
Различают насыпные и жесткие пористые зернистые фильтры. В насыпных фильтрах в качестве насадки используют песок гальку шлак дробленые горные породы древесные опилки крошку резины кокс пластмассы графит и другие материалы.
Жесткие пористые фильтры (керамические металлокерамические металлопористые и др.) отличаются повышенной устойчивостью к высокой температуре коррозии и механическим нагрузкам.
Расчет фильтров сводится к определению площади фильтровальных элементов гидравлического сопротивления фильтровального элемента и фильтра продолжительности работы фильтра до регенерации фильтровальных элементов и мощности привода вентилятора.
Электрическая очистка - один из наиболее совершенных видов очистки газов от взвешенных в них частиц пыли и тумана. Этот процесс основан на ударной ионизации газа в зоне коронирующего разряда передаче заряда ионов частицам примесей и осаждении последних на осадительных и коронирующих электродах.
Загрязненные газы поступающие в электрофильтр всегда оказываются частично ионизированными за счет внешних воздействий поэтому они способны проводить ток попадая в пространство между двумя электродами. При некотором достаточно большом напряжении движущиеся ионы и электроны настолько ускоряются что сталкиваясь с молекулами газа ионизируют их превращая нейтральные молекулы в ионы и электроны. Образовавшиеся новые ионы и электроны ускоряются электрическим полем и ионизируют новые молекулы газа.
Этот процесс названный ударной ионизацией газа протекает устойчиво лишь в неоднородном электрическом поле характерном для цилиндрического конденсатора (рисунок 5.9) В зазоре между коронирующим 1 и осадительным 2 электродами создается электрическое поле З с силовыми линиями направленными от осадительного к коронирующему электроду или наоборот. Напряжение к электродам подается от выпрямителя 4. Отрицательно заряженные аэрозольные частицы движутся к осадительному электроду под действием аэродинамических и электрических сил а положительно заряженные частицы оседают на отрицательном коронирующем электроде. Ввиду того что объем внешней зоны коронного разряда во много раз больше объема внутренней большинство частиц пыли получает заряд отрицательного знака. Поэтому основная масса пыли осаждается на положительном осадительном электроде и лишь относительно небольшая на отрицательном электроде.
По конструкции электрофильтры разделяют на трубчатые и пластинчатые. В трубчатых электрофильтрах запыленный газ пропускают по вертикальным трубам диаметром 200 - 250 мм по оси которых натянут коронирующий электрод диаметром 2 - 4 мкм.
Рисунок 5.9 - Схема расположения электродов в электрофильтре
Осадительным электродом служит труба на внутренней поверхности которой оседает пыль. В пластинчатых электрофильтрах коронирующие электроды натянуты между плоскими параллельными пластинами.
Осадительные электроды очищают встряхиванием ударом вибрацией или смыванием.
Для очистки вентиляционных выбросов от пыли туманов минеральных масел пластификаторов и т.п. разработан электрический туманоуловитель типа УУП (рисунок 5.10).
Рисунок 5.10 - Туманоуловитель УУП.
В корпусе 1 установлен электрический туманоуловитель 2 который питается от источника 4 напряжением 13 кВ. Подвод питания к электродам производится через высоковольтные электроизоляторы с клемами 3. Загрязненный воздух через входной патрубок распределительную решетку 8 и сетку 7 поступает к туманоуловителю очищается от примесей и пройдя каплеуловитель 5 подается на выход УУП. Жидкость собирается в воронках 6 а затем смывается через гидрозатворы.
Рисунок 5.10 - Магистральные трубопроводы газоочистки ЭСПЦ
Список использованных источников
Батищев А.Н. Голубев И.Г. Курчаткин В.В. «Монтаж эксплуатация и ремонт технологического оборудования» М.: КолосС 2007 – 424 с.
Гаевик Д.Т. « Смазка оборудования на металлургических предприятиях» М.: 1998 – 328 с.
Пономарёв А. Ф. Гедык П. К. «Смазка оборудования». М. Государственное научно-техническое издательство машиностроительной литературы. 1982.
Целиков А. И. «Машины и агрегаты металлургических заводов». Том 2 «Машины и агрегаты сталеплавильных цехов». М. Металлургия 1988.
Романенко Ю.А. Кудинова О.В. Требования к оформлению текстовых документов Красный Сулин ГОУ СПО "КМК" 2006- 45с
Эрдеди А.А. Эрдеди Н.А. Детали машин. - М.:Akadema2001-286 с
Иванов М.Н. Детали машин. Курсовое проектирование. М: Высшая школа 1985-550 с.
Кнышнова Е. Н. Панфилова Е. Е. Экономика организации: Учебник. - М.: ФОРУМ: ИНФРА-М 2005.-336 с.
Микроэкономика: Учебебное пособие для студентов средних профессиональных учебных заведений. Н. П.Котерова. - М.: Издательский центр «Академия» 2003. - 208с.
Экономика предприятия: Учебник Под ред. А.Е.Карелика М.Л.Шухгальтер. - М.: ИНФРА - М 2001.- 432с.
Волков О.И. Скляренко В.К. Экономика предприятия: Курс лекций. - М.: ИНФРА - М 2004. - 280 с
Зайцев Н.Л.Экономика промышленного предприятия: Учебник. - М.: ИНФРА-М 2002.-384 с.
Per_Blok_gazoochistok.doc
Система водораспределения
ДП.1150411.05.23.00.
Oborudovanie_ESPC_Staks.doc
Корзина загрузочная ДСП
Тележка с весовым устройством Q = 40 т.
Устройство для свинчивания электродов
Кран мостовой Q = 5010 т.
Печной трансформатор ЭТЦНК-200010-7643
Кран однобалочный Q = 3.2 т. L=9.0 м.
Дуговая сталеплавильная печь ДСП-50 №1
Фурма для вдувания карбюризатора в ДСП-50
Устройство подачи ферросплавов в ковш
Опора траверсы Q = 20 т. для шлаковой чаши
Чаша шлаковая V = 3.5 м3
Стенд для разливочного ковша V = 50 т.
Устройство для сушки разливочных ковшей
Дуговая сталеплавильная печь ДСП-50 №2
Тележка сталевозная Q = 50 т.
Тележка для транспортировки шлаковой чаши
Система хранения и подачи футеровочной массы
Установка набивной футеровки разливочных
Стенд для сборки стопоров
Стенд для замены футеровки металлоприемников
Электросушилка для продувочных фурм
ДП.1150411.05.23.00.
электросталеплавильного
Кран консольный Q = 5 т.
Стенд для установки металлоприемников
Кран мостовой Q = 5010 т. Для транспортиров-
Тележка передаточная
Короб для мусора V = 5.6 м3
Стенд механизированный для ковша V = 50 т.
Опора траверсы для Q = 50т. Для ковша V = 50т
Машина непрерывного литья заготовок
Насосная автоматического пожаротушения
Место для выбивки сводов ДСП-50
Служебные помещения диспетчерская комната
мастера комната отдыха помещение связи.
Место установки контейнеров
Per_gruzopotoki_ZAO_Staks.doc
Бадья саморазгрузочная
Приемные переносные бункера
Бункера боя электродов и кокса
Бункера ферросплавов
Весы для взвешивания ферросплавов
Кран мульдозавалочный
Кран с загрузочной бадьей
Ковш сталеразливочный
Прокатный цех в перспективе
ДП.1150411.05.23.00.
электросталеплавильного
Gruzopotoki.cdw
III - Разливочный пролет.
электросталеплавильного
ДП.150411.05.23.00.С1.
Chema_nagruzok_i_podkluchenij.cdw
От распредшкафа к двигателям
Безусадочная заливка
Указание: подкрановый рельс над
моторами обеспечивается заказчиком
Лестницы и ограждения - обеспечивает заказчик
ДП.150411.05.23.00.С5
Princip_chema_gazoochistki.cdw
Дымосос ВМ-751200-1Б
охлаждения подшипников
УСЛОВНЫЕ ОБОЗНАЧЕНИЯ
Измерительная диафрагма
Водовод оборотной воды
Фланцевое соединение
Дроссель регулирующий
ДП.150411.05.23.00.С3.
Принципиальная схема
Рекомендуемые чертежи
- 29.07.2014
- 04.11.2022
- 04.11.2022
- 24.01.2023
- 24.01.2023
- 04.11.2022